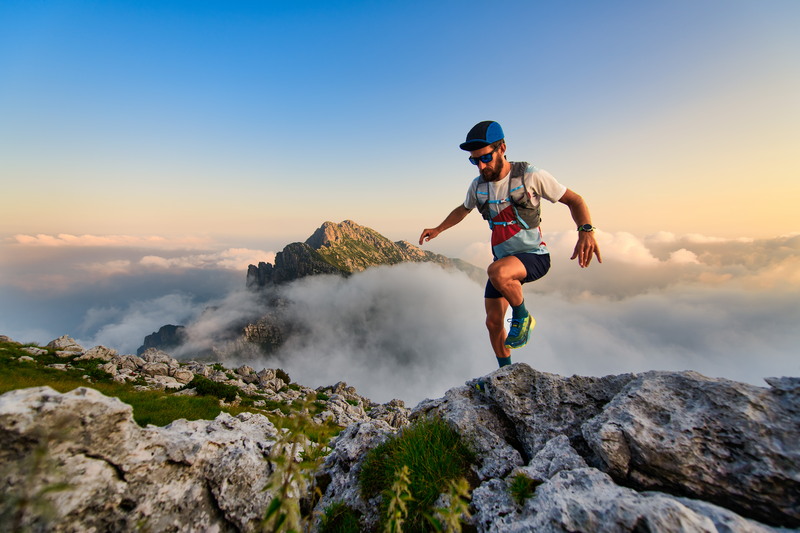
95% of researchers rate our articles as excellent or good
Learn more about the work of our research integrity team to safeguard the quality of each article we publish.
Find out more
REVIEW article
Front. Energy Res. , 24 March 2023
Sec. Smart Grids
Volume 11 - 2023 | https://doi.org/10.3389/fenrg.2023.1142243
This article is part of the Research Topic Advances in Artificial Intelligence Application in Data Analysis and Control of Smart Grid View all 20 articles
In order to break through the existing battery technology of electric vehicles, this paper proposes to use heat pump air conditioning instead of the original PTC heating system potential. First, the advantages and disadvantages of different heat pump models for new energy vehicles are analyzed and compared. Second, a fuzzy inference system is constructed based on the machine learning model to observe the temperature of the passenger compartment using the temperature sensor inside the tram and to determine the need for the air conditioning system to be turned on in the heating/cooling mode by comparing it with the set temperature. Finally, the results show that the machine learning algorithm is able to monitor and adaptively adjust the interior temperature to further enhance the adaptability of the system with low volatility and high accuracy. The proposed research study can lay the foundation for further optimizing the design of heat pump air conditioners for electric vehicles.
Automotive air conditioning technology has been developed for nearly 70 years since the 1950s, when General Motors first designed and installed the first integrated heating and cooling air conditioner in a car in the United States (Sharif et al., 2017; Bentrcia et al., 2018; Wang et al., 2020). During this period, although the components within the automotive air conditioning system have been continuously updated, its entire system based on mechanical compression for cooling and the use of waste heat from fuel vehicles for heating has remained almost unchanged (Ahn et al., 2016; Kalinichenko et al., 2018; Lee et al., 2022). With the rising awareness of environmental protection in various countries and the rapid development of technology in the new energy vehicle industry, it is the trend for vehicles to develop from traditional fuel vehicles to new energy. Therefore, the automotive air conditioning industry is facing a shift and challenge from a single indicator of comfort to comprehensive energy saving and emission reduction. Under the pressure of energy crisis and environmental pollution, new energy vehicles came into being. Among them, pure electric vehicles, with their characteristics of no pollution, low noise, and high efficiency, have received wide attention from automobile manufacturers and consumers and have gradually become an important research direction for the transformation and upgrading of the automobile industry (Wang et al., 2016; Li et al., 2019). Although electric vehicles have great potential for development, shortcomings such as short range and long charging time limit the popularity of pure electric vehicles.
Both new energy vehicles and conventional vehicles require a comfortable driving environment. Air conditioning systems can provide a comfortable interior environment for the driver and occupants under complex and changing driving conditions (Sharif et al., 2016). Pure electric vehicles have limited battery capacity and short range, so there are strict requirements for the energy consumption and efficiency of the air conditioning system. Among them, in the design of the whole vehicle thermal management system, the cooling system medium of electric drive and accessory thermal management is the coolant, and the structure is basically independent. The interior thermal management and battery thermal management are realized by the coupling of air conditioning system, and the cooling medium is an R134a refrigerant. The interior thermal management mainly includes interior cooling, interior heating, and remote control of air conditioning. The strongest coupling between the battery thermal management and air conditioning system is battery cooling, and battery heating is generally realized independently through the battery heater, which is basically not coupled with the air conditioning system.
Recently, artificial intelligence has become a socially recognized future development trend (Athey, 2018; Bi et al., 2019). By mining the implied laws from a large amount of historical data and applying them to the prediction of the system, machine learning improves the accuracy and precision of the system. With decades of research and development, automotive air conditioners have accumulated a sufficient amount of historical data and are a representative applicable object for machine learning. Most of the air conditioning systems of electric vehicles currently in circulation are used for winter heating through PTC, but according to the relevant electric vehicle regulations, if the car is to have the function of heating and defrosting, then the PTC electric heating power needs to be more than 3000 W (Park and Kim, 2017; Park and Kim, 2019). The PTC electric heating method of heating consumes a lot of power and has a large impact on the battery, and the coefficient of performance of the system is maximum 1, there is certain of energy waste. The heat cannot be propagated in the reverse direction without the interference of external forces, and heat can only be radiated from high temperature to low temperature. The working principle of the heat pump is to consume less energy and realize the propagation of heat from the low-temperature object to high-temperature object by reversing the cycle, so as to obtain a larger amount of heat. This way of consuming less energy and obtaining more heat can achieve the purpose of energy saving.
Heat pumps have a proven product history of over 20 years as a solution for home and commercial air conditioning. Although, their use of electrical energy can achieve 2–3 times of heat output. However, limited by cost and technical maturity, they have been slow to develop in the automotive air conditioning industry. However, with the imperative to address the range of electric vehicles, heat pump systems are the most promising and efficient solution available. At present, a lot of research studies have been performed by scholars in various countries on the design and application of heat pump air conditioning control systems in the context of machine learning. In this paper, we will systematically review the current research status of the electric vehicle heat pump air conditioning control system based on machine learning, summarize and conclude the technical principles of heat pump air conditioning, types of heat pumps, environmental protection work material substitution, and compressor control strategy and electric vehicle heat pump defrost system based on machine learning, and analyze the current difficulties in electric vehicle heat pump air conditioning on this basis.
The working principle of the electric vehicle heat pump air conditioning system is shown in Figure 1, which mainly consists of an electric compressor, a four-way reversing valve, an external heat exchanger, a liquid storage dryer, a capillary tube, an internal heat exchanger, and a fan (Zhou et al., 2017; Peng et al., 2021; Ning et al., 2023). The cooling cycle is similar to the heating cycle in that the direction of the mass flow can be changed simply by a four-way reversing valve.
T and P denote pressure and temperature, respectively. As can be seen from Figure 1, the electric air conditioning compressor will be a high-temperature and low-pressure gaseous refrigerant, compressed into a high-temperature and high-pressure liquid refrigerant; through the car heat exchanger condensation, heat exchanges with the air inside the car, the air temperature inside the car rises, and the refrigerant temperature drops, becoming a low-temperature and high-pressure liquid refrigerant; and then, through the electronic expansion valve, it becomes a low-temperature and low-pressure gaseous refrigerant; through the car heat exchanger, heat exchanges with the gas outside the car, the air temperature outside the car drops, and the refrigerant temperature rises, becoming a high-temperature and low-pressure gaseous refrigerant, into the next round of the refrigeration cycle. In this way, the heat exchange between the inside and outside of the car can be realized, so as to achieve the effect of heating the inside of the car.
Automotive air conditioning systems with heat pump functions are more complex than conventional automotive air conditioning systems, and the functionality and reliability of the components are correspondingly higher. Junqi et al. (2021) pointed out that the existing four-way reversing valve design is a copper reversing valve for domestic air conditioners, and an aluminum reversing valve for automotive air conditioners has poor solderability, low reliability, and vibration resistance and, thus, has the disadvantage of being unsuitable for frequent switching and leakage between high and low pressures. Therefore, major automotive companies and system suppliers can now arrange a dual heat exchanger on the indoor side to take care of the cooling and heating needs (Han et al., 2021; Wang et al., 2022a). For the direct heat pump system, an internal condenser is arranged directly on the rear side of the evaporator inside the air conditioning box to replace the conventional warm air core. At the same time, since the outdoor heat exchanger has to take on additional heat absorption demand in winter, it is necessary to add an additional heat making valve set or throttling short pipe valve set at its inlet in the heat pump mode. The function is to realize the fine adjustment of the flow rate of outdoor heat exchanger to maintain the stable operation and heat output of the system in the heating mode. At the same time, the battery cooler and indoor evaporator also need to use solenoid valve set to cut off and bypass to the gas–liquid separator.
Unlike the direct heat pump, the indirect heat pump system uses a plate heat exchanger to realize the heat exchange between the compressor high-pressure high-temperature refrigerant gas and the coolant of the cooling circuit, and the heat exchanged high-temperature coolant then flows through the warm air core in the air conditioning box via the secondary circuit, so as to conduct secondary heat exchange with the circulating air in the air conditioning box again. After the secondary heat exchange, the air temperature of the warm air core reaches the set target air temperature (Zhou et al., 2022). It can be seen that the arrangement inside the air conditioning box is still the same as that of the conventional air conditioning box, with the evaporator and the warm air core. The air conditioning box does not need to be redesigned again, which can reduce most of the design and verification and tooling costs and save the development cycle. Meanwhile, the indirect heat pump with secondary loop design can realize the coupling relationship between the coolant system and the heat pump system through the plate water-cooled condenser (Malinowski et al., 2017). The high-pressure water PTC of the cooling system can achieve rapid warming of the battery system in winter and can also be used as a supplementary heat source to compensate for the risk of heat deficiency of the heat pump system under severe low-temperature conditions. It also reduces the risk and cost of the high-pressure PTC in the air conditioning box. The use of electrical energy regulation not only keeps the structure design simple but also controls the current size and heat and the use of temperature models, reduces the heat loss during the operation of the air conditioning system, and increases the speed of the car’s internal temperature.
Although the heat pump system can output 2 to 3 times the electrical power of the heat and the energy efficiency is high, it relies on the external heat exchanger at low-temperature air and refrigerant heat transfer. When the external heat exchanger is in evaporating condition and the surface temperature is lower than the dew point temperature of the incoming air, the heat exchanger surface is in wet condition and the heat exchanger surface will condense or even frost. Therefore, the traditional air source heat pump, in the low-temperature and high-humidity environment will quickly frost and, thus, affect the stable output of system heat and system pressure loss. For this reason, many scholars have considered dual heat source heat pump systems that operate by using the waste heat from the coolant of electrical components such as motors.
A new heat pump system for electric vehicles is proposed in the literature (Singh and Sharif, 2019; Wang et al., 2021a), which takes the form of an additional external heat source in the system. A special device, called a bi-directional reservoir, was also designed. This device performs the filtering and drying function of the reservoir inside a conventional vehicle air conditioner and can be used in the cooling or heating mode. This replaces the original need for two expansion valves, two check valves, and two liquid storage electric compressor control tanks. The results of the improved heat pump bench test show that at an ambient temperature of −10°C, the air side absorbs 2.5 kW of heat exchange and the battery and motor recover 0.5 kW of heat. In comparison with the PTC system, the whole vehicle saves 15% of electricity consumption. It also improves the stability of the system for external heat exchanger frost.
Rajbongshi and Saikia (2018) proposed a thermal management method called the thermal link system, in which the waste heat recovery heat exchanger is connected in series with the outdoor heat exchanger. In the heating mode, the power consumption can be reduced to 580 W and a heating capacity of more than 2000 W can be obtained. As a result, the COP of the heat pump system exceeds 3.3.
In the study of Liu et al. (2019), a waste heat recovery heat pump system connected in parallel with an external heat exchanger was investigated. The performance of the winter EV thermal management system was enhanced by recovering the automotive waste heat, and the heating COP was improved by about 25.5% when the ambient temperature was −7°C and the waste heat was boosted from 0 W to 1000 w. At the same time, the waste heat generated by the circuit helps to increase the compressor suction pressure and outlet pressure, which in turn increases the outlet air temperature. In comparison with the PTC heating system, the remaining power of the whole vehicle is improved by about 53%.
Karnik et al (2016) noted in an SAE workshop that the I-pace heat pump system can recover 2.5 kW of heat from the motor circuit at an ambient temperature of 0°C. At the same time, only 0.3 kW of compressor power consumption is required to deliver an overall 2.8 kW of heat to the passenger compartment. Menken et al (2018) evaluated that the Audi Q7 e-tron heat pump can deliver 3.4 kW of heat with 2.5 kW of power in the waste heat recovery heat pump mode at an ambient temperature of 5°C.
Currently, R134a is the main working fluid in automotive air conditioning systems, while R407C, R410A, R1234yf, and CO2 are also used in a few automotive air conditioning systems.
R134a is non-toxic, non-combustible, and has good heat transfer performance, but its boiling point is relatively low (−26.5°C) and the amount of refrigerant vaporization decreases significantly when the ambient temperature decreases, resulting in a decrease in heating efficiency, insufficient low-temperature heat production, and high energy consumption, which cannot meet the load requirements of automotive air conditioners at low ambient temperatures; its GWP (1600) value is high, and it is a restricted process in the EU and the Kyoto Protocol. R407C is a ternary non-azeotropic blend of R32, R125, and R134a, with a GWP value of 1980. R134a, R407C, and R410A are three mainstream automotive air conditioning process agents whose use has been restricted due to their high GWP values. R1234yf (ODP = 0, GWP = 4) is an environment-friendly process agent for automotive air conditioners jointly introduced by Honeywell and DuPont, which can meet the requirements of EU regulations and has similar thermodynamic and heat transfer characteristics to R134a. It is one of the best alternatives to R134a for automotive air conditioners because of its low cost (Altinkaynak et al., 2019; Pabon et al., 2020; Adrian et al., 2021; Yadav et al., 2022). However, there is a 10% decrease in performance compared with R134a systems, and the performance decrease is more prominent at low-temperature heating. Meng et al. (2018) and Yang et al. (2019) applied R1234yf/R134a hybrid work gases with different mixing ratios in automotive heat pump air conditioning systems, and the COP is slightly lower than that of R134a systems, but the difference does not exceed 7%, which is feasible.
The natural work gas CO2 (ODP = 0 and GWP = 1) has the advantages of good low-temperature heating performance and high cooling capacity per unit and is considered as one of the best choices for the new generation of work gas for automotive air conditioning (Lee et al., 2014). Mercedes-Benz of Germany was the first to launch a vehicle equipped with a CO2 air conditioning system in 2017, and Toyota and others have started to apply it on a large scale. The CO2 heat pump system developed by Valeo can increase the driving range by 15% at −15°C and 30% at 20°C. The CO2 transcritical automotive heat pump air conditioning system proposed in the literature (Zheng et al., 2020; Wang et al., 2022b) can achieve an outlet air temperature of 40.4°C and a COP of 1.8 at −20°C in a fully fresh air environment, with obvious advantages of low-temperature heating effect. However, the critical temperature of CO2 work material is low (31°C), and the system must work in the transcritical cycle (pressure >7.4 MPa), and the operating pressure is much higher than that of the R134 a automotive air conditioning system, and the existing components cannot meet the requirements of system reliability and safety.
A temperature sensor in the passenger compartment of the electric vehicle observes the temperature of the passenger compartment and determines that the air conditioning system needs to be turned on in the heating/cooling mode by comparing it with the set temperature. The automatically controlled air conditioning system features low volatility and high accuracy, avoiding the driving safety hazards for drivers caused by manually adjusting the air conditioning knob. Scholars at home and abroad have found that the compressor is a key part of the air conditioning control system through research on air conditioning systems. Scroll compressors can even reduce the power of the air conditioning system by avoiding the compressor to always run at very high speed.
The scroll compressor is driven by a DC motor. By adjusting the duty cycle of the voltage applied to the DC motor, the speed of the compressor can be effectively controlled to achieve effective and precise control of the occupant compartment temperature. At the same time, it can reduce the power of the air conditioning system by avoiding the compressor from running at very high speed all the time. By introducing machine learning (Agarwal et al., 2020) and combining neural networks with fuzzy control, researchers designed a fuzzy neural network compressor controller and compared it with the control effects of PID and fuzzy control to derive the best compressor control system.
In this paper, the control strategy of the heat pump air conditioning system is studied from the power of the air conditioning system by combining the heat transfer mechanism of the heat pump air conditioning system and components and relevant algorithms in machine learning with current popular control methods as the starting point. Based on the thermodynamic principle, the remaining components of the heat pump air conditioning system are modeled, and the coupling of each component is proposed to build a heat pump air conditioning system construction strategy. The deficiency of fuzzy control which relies heavily on expert experience is remedied.
PID control as a linear controller is widely used in the field of mechanical control due to its excellent robustness, high reliability, simple principle, and easy implementation (Xie et al., 2022). PID achieves the control of the control target by establishing an accurate mathematical model. However, for the automotive air conditioning system, the dynamic changes of its driving state and environment make it a non-linear and time-varying strong controlled object. Therefore, it is difficult to meet the precise control of the air conditioning system by using the PID controller, a classical control algorithm that regulates by linear superposition of three items: proportional, differential, and integral. At the same time, there are also applications for the actual control object, after simplifying the PID controller, such as the PI controller.
The PID control system for the automatic air conditioning compressor was determined based on the principle of the PID control system combined with the compressor control system. The researchers found that if the set temperature of the passenger compartment is 25 °C, the compressors all run at the highest speed when the temperature difference exceeds the upper and lower limits to ensure that the set temperature is reached as soon as possible (Chunyue, 2017).
Fuzzy control based on fuzzy sets, fuzzy logic, and fuzzy language is a popular research topic in the field of artificial intelligence control in recent years and has been widely used in various fields of industry. The automotive heat pump air conditioning system is easily limited by the driving status of the car and the changing heat load. Also, fuzzy control, as an important part of intelligent control, uses set fuzzy rules for effective control of the control target without the need for precise mathematical models (Nguyen et al., 2019). Yordanova et al. (2014) argued that the introduction of fuzzy control into the field of air conditioning control avoids most of the ineffective control and allows the power of the air conditioning system to be reduced.
The EV obtains the exact value of the controlled quantity by interrupt sampling and then compares this quantity with the given quantity to obtain the error signal
In order to exert precise control on the controlled object, it is also necessary to convert the fuzzy quantity
Machine learning is centered on parsing data and finding patterns, learning by writing algorithms, and making decisions and predictions of relevant events based on the learned algorithms. In contrast to the traditional idea of explicitly writing programs to perform a solidified task, machine learning enables computers to perform tasks by developing learning algorithms (Durur and Yokuş, 2021). Depending on the learning method, there are three categories: supervised learning, unsupervised learning, and reinforcement learning. Different types of machine learning methods have specific advantages, disadvantages, and applications. An overview of current machine learning methods and classical applications is shown in Table 1.
Machine learning is a method of giving machines and humans the same level of intelligence (artificial intelligence). Machine learning contains a variety of algorithms that are applicable indifferent situations such as clustering and classification. Artificial neural networks are the current research hotspot and focus in machine learning. Artificial neural networks are based on the structure of biological neural networks. One or more outputs are produced by many inputs that pass through several implicit layers. These connections form specific loops that mimic the way the human brain processes information and logical connections. As the algorithm continues, the hidden layers tend to be smaller and more subtle. By using the generalized multi-feature subspace framework to learn the structural features of noisy and anomalous pixels, a unique approximate solution is computed by using the L1 sphere theory, and the complex computation of large-scale data is avoided by using the filtering technique, thus reducing the time and space complexity. Finally, machine learning provides better recognition results compared to other sparse coding methods.
Fuzzy systems and artificial neural networks belong to the same characteristic-free mathematical models and non-linear systems, and both are important tools for dealing with uncertainty problems, uncertainty, and non-linearity. Salleh et al. (2017) studied that the inference rules of fuzzy systems rely on expert experience or skilled operators to write them, and they do not have adaptive and self-learning capabilities themselves, which makes fuzzy systems have certain limitations. Moreover, the reliability of expert experience determines the reliability of fuzzy systems. Neural networks have the ability of adaptive learning, fault tolerance, parallelizable computation, and distributed information storage. However, Alashkar et al. (2017) pointed out that neural networks themselves do not make good use of empirical knowledge and are often assigned initial values and weights in the form of 0 or random numbers, which makes neural networks show poor performance when applied to express rule-based knowledge. Also, it makes the neural network prone to fall into local extremes and increases the training time of the neural network. In conclusion, fuzzy systems are suitable for dealing with structured knowledge, while neural networks are more effective for unstructured knowledge. Fuzzy neural network systems are modeled according to their fuzzy systems and given physical meaning to the corresponding network nodes. In contrast to neural networks, fuzzy neural networks can determine the initial values of the system. Also, compared to fuzzy systems, fuzzy neural networks have high adaptive and learning capabilities due to their neural network structure (Marín et al., 2019; Zheng et al., 2021).
Fuzzy neural networks are essentially conventional neural networks that are given fuzzy input signals and fuzzy weights, and their learning algorithms are usually neural network learning algorithms or generalization algorithms. The inference rules of Mamdani-type fuzzy neural networks conform to the normal human thinking habits and, therefore, can represent human knowledge more accurately (Yucel et al., 2017; Zhang et al., 2018a; Lucchese et al., 2021; Mohammed and Hussain, 2021). However, their computations are generally complex and are not conducive to mathematical analysis.
The frost suppression design is mainly designed to reduce the frost rate and frost volume by changing the geometrical structure parameters and surface interface properties of the heat exchanger. The literature (Hu et al., 2020) analyzed the characteristics of frost growth in a four-process heat exchanger: the ratio of gas–liquid refrigerant differs in different processes and is influenced by gravity, the frost layer is uniformly distributed in the first process, while it is non-uniformly distributed in the second, third and fourth processes, and there is a linkage between surface frost growth and surface temperature drop. There is a lack of research on the optimization of frost suppression for this phenomenon, but in the study of improving the air inlet conditions of electric vehicle heat exchangers (Zhang et al., 2018b), the four processes were improved to six processes with more uniform air inlet, and the study provided ideas for heat exchanger frost suppression. Combining these two studies, it can be foreseen that improving the refrigerant side process has some potential in the design of heat exchanger frost suppression.
The outdoor heat exchanger of the heat pump system has two spatial arrangements, horizontal and vertical, and the conventional fuel car heat pump system mostly uses the horizontal arrangement with the reservoir function, while the electric car microchannel heat exchanger mostly uses the vertical arrangement that helps drainage. Gillet et al. (2018) studied the heat production and air outlet temperature variation of horizontal and vertical arrangement methods under evaporator conditions in high cold, high humidity, and cold and wet conditions. The performance of the horizontal arrangement is better than that of the vertical arrangement under frost conditions, mainly because the vertical arrangement leads to uneven refrigerant distribution and severe frosting at local locations, while defrosting will not be complete. This shows that the vertical arrangement of the heat exchanger, although conducive to frost water drainage, but not conducive to frost suppression. In the work of Mahvi et al. (2021), a superhydrophobic heat exchanger was studied, which was able to significantly reduce the amount of frost and keep the thermal conductivity above 50% of the maximum value and reduce the time and energy required for defrosting.
Surface treatment can reduce the amount and speed of frosting, but the high cost of the surface treatment and the complexity of the process make it difficult to spread, so reducing costs and simplifying the process are the key points of whether this type of technology can be applied. Considering the long-time operation of the electric vehicle heat exchanger, surface treatment cannot fundamentally solve the frosting problem, and we still need to rely on the defrosting equipment and system, but surface treatment has a positive effect in extending the defrosting cycle and reducing defrosting energy consumption, as shown in Table 2.
In order to reduce the energy consumption, the air conditioning system works at the optimal working condition and achieves the economic performance index; the machine learns and makes calculations based on the input command and operation status and adjusts the action of relevant actuators, especially the speed of electric compressor, in time. To achieve the aforementioned control objectives, the air conditioning controller needs to collect information on the operating status of the air conditioning system and the environment, including the temperature inside and outside the vehicle, sunlight intensity, cooling water temperature, and compressor speed, and then output the corresponding control signals through the microprocessor to adjust the corresponding actuators to meet the requirements of the occupants. Based on the aforementioned conditions, unnecessary calculations are reduced.
The common defrosting methods of heat pump systems include manual defrosting, water flushing, compressed air defrosting, electric defrosting, and hot air defrosting. For electric vehicles, hot air defrosts is valued because it does not require auxiliary equipment and has high energy efficiency. The following is the main introduction of hot air defrost technology; there are two forms of hot air defrost: the hot air bypass method and reverse cycle method:
1) The hot gas bypass method refers to the direct introduction of high-pressure high-temperature exhaust from the compressor into the heat exchanger to melt the frost, which has the advantages of short bypass piping, low resistance, and small temperature fluctuations inside the vehicle during defrosting (Xi et al., 2021). The defrosting time and energy consumption of the four defrosting modes are shown in Table 3. Among them, the thawing performance of the high-pressure hot gas bypass is the most satisfactory.
Hu et al. (2014) systematically studied the hot gas bypass method and obtained the optimal opening of the bypass valve and the optimal defrost cycle for the studied heat pump system. The optimal defrost cycle is based on the basic complete defrost, while the residual frost at the edges where the heat exchange is small can be neglected. In addition, Wang et al. (2018) introduced the method of refrigerant subcooling defrosting, which is similar to the hot gas bypass method and uses the refrigerant liquid just coming out from the condenser to the evaporator for defrosting; the characteristics of this method are similar to those of the hot gas bypass method, which does not affect the heating, but requires a long operation time and is suitable for defrosting out the frost in the case of microfrost to prevent further frost generation. The condenser has the following advantages over conventional hot air corps: First, it has low system operating costs. Condensing temperatures within 8.3°C of the wet bulb design temperature are very practical and economical, with the result that compressor power saves at least 10% of the power consumption of other cooling tower/condenser systems and saves 30% of the power consumed by the fan, which is comparable to the power consumed by the fan of a cooling tower/condenser system and is approximately 1/3 of the power of an air-cooled condenser fan of the same size. Second, the condenser requires only approximately 50% of the windward area of the same size.
2) Circular method
The advantage of reverse cycle defrosting is fast defrosting and low energy consumption, but the disadvantage is that the heating stops when defrosting, which has a greater impact on the vehicle temperature. Minglu et al (2020) pointed out the mechanism by which reverse cycle reduces the circulation efficiency of the system. In the work of Wang et al. (2021b), a reverse cycle defrost system with CO2 as the working fluid was investigated, the parameters in the defrost process were optimized, and a reverse cycle defrost model with CO2 working fluid was established, and the optimal time point and duration of defrost were studied on this basis. Zhou Guanghui et al. proposed a combined reverse cycle defrost-based defrost technology, the core of which is to enhance the temperature and enthalpy of airflow during defrosting, to achieve rapid defrosting by controlling the external air speed, controlling the compressor speed, and enhancing the interior temperature, and to reduce the impact on the interior temperature during reverse cycle defrosting. Li et al. (2022) built a platform for frost defrosting the heat exchanger outside the real vehicle and concluded that the degree of heat exchanger frosting can be indirectly characterized by the change of suction temperature or suction pressure relative to the frost-free state, and the large-diameter electronic expansion valve combined with intelligent control can achieve effective defrosting. The continuous frosting–defrosting experiment was studied by frost time recording and real-time shooting of the frost layer, and the results showed that after continuous operation of frosting for 150 min, the heating capacity decreased by 22.6% and 15.6% respectively, and the second frosting time was only 28.5% of the first frosting time, and the reverse cycle defrosting effect was obvious.
In the defrost system control, the timing control method only needs to confirm the defrost cycle and defrost duration based on experience or experiment, but this defrost method is more suitable for areas with relatively high ambient humidity, while in areas with low ambient humidity, there will be no frost and defrost phenomenon. When the timing module in the air conditioner controller detects that the heat pump air conditioning system is running continuously for a certain value, the heat pump air conditioning system automatically enters defrost mode, which outputs the speed of the compressor and the time for the defrost function to run. In the actual experimental process, the control strategy is verified, when the ambient humidity is above 50%, the air conditioning system continuous heating for a certain period of time, the outdoor heat exchanger will appear frost phenomenon, and the control strategy can complete the defrost function. However, when the ambient humidity is lower than 50%, the heat pump air conditioning system does not have frost in the continuous heating for a certain period of time, but the control strategy will still perform defrosting action, so there will be an unnecessary defrosting process, thus increasing the energy consumption.
The time–temperature control method is a common method in which the air conditioning system defrosts for a certain period of time when the ambient temperature and ambient humidity are relatively high (Liang et al., 2019). When the air conditioning controller detects that the ambient temperature reaches the ambient temperature value set in the defrost control strategy, the CCM will control the air conditioning system to automatically enter the defrost function and then control the corresponding components to complete the corresponding action, i.e., output the speed of the electric compressor and the time for which the defrost function runs. In the actual experimental process, when the ambient temperature reaches below 3°C and the ambient humidity is above 50%, the outdoor heat exchanger will frost for a certain period of time when the air conditioning system is heating continuously, and the control strategy can achieve the defrost function. However, when the ambient temperature is higher than 3°C and the ambient humidity is lower than 50%, the outdoor heat exchanger will be frosted when the air conditioning system heats up continuously for a certain period of time, and at this time, the air conditioning controller will not defrost by judging that the ambient temperature has not reached the condition, so there will be no defrosting action when defrosting is needed.
The air and heat exchanger surface temperature difference control method uses the difference between the heat exchanger outlet temperature and the ambient temperature for defrost control (Nilpueng et al., 2019; Su et al., 2021; Yi, 2021). It can be said that assuming that the ambient temperature remains unchanged and the heat exchanger surface does not reach the condition of frost, the heat exchanger surface temperature is basically unchanged at this time, so the difference with the ambient temperature is unchanged, but when the heat exchanger surface reaches the condition of frost, that is, when it starts to frost, the difference between the two will show significant changes (Juárez et al., 2021; Singh and y Sora, 2021). So, you only need to determine the appropriate temperature difference value; it is good to determine whether the outdoor heat exchanger surface has been frosted and a certain defrost time can be, but the defrost method is only suitable for specific situations because different systems need to determine other temperature difference values and different defrost time, and the heat pump air conditioning system is more sensitive to changes in load, such as changes in ambient temperature will cause excess defrost action. When the air conditioner controller detects the ambient temperature and the heat exchanger surface temperature and determines that the difference between the two changes, the air conditioner controller will control the heat pump air conditioning system to automatically enter the defrost function and output the corresponding electric compressor speed and defrost function running time. In the actual experimental verification process, because the ambient temperature will be affected by the speed of the vehicle and other factors, when using this control strategy at this time, due to changes in ambient temperature, there will be defrost action when the defrost should be carried out, or when there is no need to carry out defrost, there is a redundant defrost action (Mohammed et al., 2022).
In a comprehensive view, researchers in various countries have explored a lot in compressor control strategy optimization and heat pump defrost technology, but the combination with emerging technologies such as machine learning is not close enough. As the application of new energy technology, some basic work and key technologies of heat pump air conditioning for electric vehicles still need to be broken through.
1) Development of heat pump air conditioners toward environmental protection, full-scene energy saving, and extreme environmental applicability: Research and development of new alternative masses, high-efficiency heat pump air conditioning systems and their components, such as supercritical CO2 heat pump air conditioners, new high-efficiency make-up gas compressors, and high-efficiency microchannel heat exchangers should be carried out to solve the problems of high energy consumption and insufficient capacity for heat production. Research and development of new heat pump air conditioners for extreme environments (extreme cold, extreme heat, high humidity, and high salt) and other areas should be carried out to improve the applicability of the whole vehicle.
2) The heat pump system has great potential and advantages in solving the heat and cold management of the passenger compartment, and further research on the enthalpy charge technology, new defrosting method, multiple heat sources for heating at low temperature, and new alternative refrigerants can allow the heat pump system to be applied and promoted in a low-temperature environment.
3) In the optimization of the compressor control strategy, the existing algorithm can be further improved to accelerate the global convergence rate by combining techniques such as small habitats under machine learning models (classifying individuals of each generation and selecting individuals with high fitness from the classification to form a population and re-hybridize).
4) Most of the studies on the defrosting of EV heat pumps only consider that the frosting of the heat exchanger affects its effective area for heat exchange. At present, further research is needed on the actual frost area of the heat exchanger and the extent of the effect of heat exchange.
5) Based on machine learning models, the heat pump air conditioner monitors and adaptively adjusts ambient temperature and humidity, indoor temperature and humidity, air outlet temperature, battery temperature, water temperature, mass temperature and pressure, indoor CO2 concentration, and PM2.5 to further enhance the system’s adaptability.
Good progress has been made in the research of the heat pump air conditioning control system for electric vehicles in the context of machine learning. Although the heat pump air conditioning system has many advantages and is one of the ideal solutions for electric vehicle air conditioning systems, the system also has defects such as low heating efficiency under low-temperature conditions, slow heating speed, and frosting of the heat exchanger outside the vehicle. In this paper, the advantages and disadvantages of various new energy vehicle heat pump systems are first described separately, and the system performance under different heat pumps is compared and analyzed. Second, in terms of electric vehicle design, the focus of attention is elaborated on the system cooling and heating under the charge volume, compressor oil return, winter frosting, and different electronic expansion valve control. In the future, a commercial CO2 vehicle heat pump air conditioning system can be used to make the performance of the new energy vehicle heat pump system more superior, thus solving the problem of electric vehicle range.
ZM carried out all the work on the article independently.
The author declares that the research was conducted in the absence of any commercial or financial relationships that could be construed as a potential conflict of interest.
All claims expressed in this article are solely those of the authors and do not necessarily represent those of their affiliated organizations, or those of the publisher, the editors, and the reviewers. Any product that may be evaluated in this article, or claim that may be made by its manufacturer, is not guaranteed or endorsed by the publisher.
Adrian, Ł., Szufa, S., Piersa, P., Kuryło, P., Mikołajczyk, F., Kurowski, K., et al. (2021). Analysis and evaluation of heat pipe efficiency to reduce low emission with the use of working agents R134A, R404A and R407C, R410A. Energies 14 (7), 1926. doi:10.3390/en14071926
Agarwal, P., Rakshit, M., and Chand, M. (2020). Fractional calculus involving (p, q)-mathieu type series. Appl. Math. Nonlinear Sci. 5 (2), 15–34. doi:10.2478/amns.2020.2.00011
Ahn, J. H., Lee, J. S., Baek, C., and Kim, Y. (2016). Performance improvement of a dehumidifying heat pump using an additional waste heat source in electric vehicles with low occupancy. Energy 115, 67–75. doi:10.1016/j.energy.2016.08.104
Alashkar, T., Jiang, S., Wang, S., and Fu, Y. (2017). “Examples-rules guided deep neural network for makeup recommendation,” in Thirty-First AAAI Conference on Artificial Intelligence (AAAI-17), San Francisco, California, USA, February 2017. doi:10.1609/aaai.v31i1.10626
Altinkaynak, M., Olgun, E., and Şahi̇n, A. Ş. (2019). Comparative evaluation of energy and exergy performances of R22 and its alternative R407C, R410A and R448A refrigerants in vapor compression refrigeration systems. El-Cezeri 6 (3), 659–667.
Athey, S. (2018). “The impact of machine learning on economics,” in The economics of artificial intelligence: An agenda (University of Chicago Press), 507–547.
Bentrcia, M., Alshitawi, M., and Omar, H. (2018). Developmens of alternative systems for automotive air conditioning-A review. J. Mech. Sci. Technol. 32 (4), 1857–1867. doi:10.1007/s12206-018-0342-2
Bi, Q., Goodman, K. E., Kaminsky, J., and Lessler, J. (2019). What is machine learning? A primer for the epidemiologist. Am. J. Epidemiol. 188 (12), 2222–2239. doi:10.1093/aje/kwz189
Chunyue, P. A. N. (2017). “Air compressor pressure control system based on gearshift integral PID controller,” in MATEC Web of Conferences (EDP Sciences), 00199.
Durur, H., and Yokuş, A. (2021). Exact solutions of (2 + 1)-Ablowitz-Kaup-Newell-Segur equation. Appl. Math. Nonlinear Sci. 6 (2), 381–386. doi:10.2478/amns.2020.2.00074
Gillet, T., Andres, E., El-Bakkali, A., Lemort, V., Rulliere, R., and Haberschill, P. (2018). Sleeping evaporator and refrigerant maldistribution: An experimental investigation in an automotive multi-evaporator air-conditioning and battery cooling system. Int. J. Refrig. 90, 119–131. doi:10.1016/j.ijrefrig.2018.04.004
Han, Z., Guo, J., Zhang, H., Chen, J., Huai, X., and Cui, X. (2021). Experimental and numerical studies on novel airfoil fins heat exchanger in flue gas heat recovery system. Appl. Therm. Eng. 192, 116939. doi:10.1016/j.applthermaleng.2021.116939
Hu, B., Wang, X., Cao, F., He, Z., and Xing, Z. (2014). Experimental analysis of an air-source transcritical CO2 heat pump water heater using the hot gas bypass defrosting method. Appl. Therm. Eng. 71 (1), 528–535. doi:10.1016/j.applthermaleng.2014.07.017
Hu, Y., Yuill, D. P., and Ebrahimifakhar, A. (2020). The effects of outdoor air-side fouling on frost growth and heat transfer characteristics of a microchannel heat exchanger: An experimental study. Int. J. heat mass Transf. 151, 119423. doi:10.1016/j.ijheatmasstransfer.2020.119423
Juárez, F. F., Esenarro, D., Díaz, M., and y Frayssinet, M. (2021). Model based on balanced scorecard applied to the strategic plan of a peruvian public entity. Investig. Pensam. crítico 10 (4), 127–147. doi:10.17993/3cemp.2021.100448.127-147
Junqi, D., Yibiao, W., Shiwei, J., Xianhui, Z., and Linjie, H. (2021). Experimental study of R744 heat pump system for electric vehicle application. Appl. Therm. Eng. 183, 116191. doi:10.1016/j.applthermaleng.2020.116191
Kalinichenko, A., Havrysh, V., and Hruban, V. (2018). Heat recovery systems for agricultural vehicles: Utilization ways and their efficiency. Agriculture 8 (12), 199. doi:10.3390/agriculture8120199
Karnik, A. Y., Fuxman, A., Bonkoski, P., Jankovic, M., and Pekar, J. (2016). Vehicle powertrain thermal management system using model predictive control. SAE Int. J. Mater. Manuf. 9 (3), 525–533. doi:10.4271/2016-01-0215
Lee, H., Lee, D., and Kim, Y. (2022). Heating performance of a coolant-source heat pump using waste heat from stack and electric devices in fuel cell electric vehicles under cold conditions. Energy Convers. Manag. 252, 115092. doi:10.1016/j.enconman.2021.115092
Lee, J. S., Kim, M. S., and Kim, M. S. (2014). Studies on the performance of a CO2 air conditioning system using an ejector as an expansion device. Int. J. Refrig. 38, 140–152. doi:10.1016/j.ijrefrig.2013.08.019
Li, K., Xia, D., Luo, S., Zhao, Y., Tu, R., Zhou, X., et al. (2022). An experimental investigation on the frosting and defrosting process of an outdoor heat exchanger in an air conditioning heat pump system for electric vehicles. Appl. Therm. Eng. 201, 117766. doi:10.1016/j.applthermaleng.2021.117766
Li, Z., Khajepour, A., and Song, J. (2019). A comprehensive review of the key technologies for pure electric vehicles. Energy 182, 824–839. doi:10.1016/j.energy.2019.06.077
Liang, L., Guo, L., Wang, Y., and Li, X. (2019). Towards an intelligent FE simulation for real-time temperature-controlled radial-axial ring rolling process. J. Manuf. Process. 48, 1–11. doi:10.1016/j.jmapro.2019.09.032
Liu, Y., Wang, X., Meng, X., and Wang, D. (2019). A review on tube external heat transfer for passive residual heat removal heat exchanger in nuclear power plant. Appl. Therm. Eng. 149, 1476–1491. doi:10.1016/j.applthermaleng.2018.11.114
Lucchese, L. V., de Oliveira, G. G., and Pedrollo, O. C. (2021). Mamdani fuzzy inference systems and artificial neural networks for landslide susceptibility mapping. Nat. Hazards 106 (3), 2381–2405. doi:10.1007/s11069-021-04547-6
Mahvi, A. J., Boyina, K., Musser, A., Elbel, S., and Miljkovic, N. (2021). Superhydrophobic heat exchangers delay frost formation and enhance efficency of electric vehicle heat pumps. Int. J. Heat Mass Transf. 172, 121162. doi:10.1016/j.ijheatmasstransfer.2021.121162
Malinowski, L., Lewandowska, M., and Giannetti, F. (2017). Analysis of the secondary circuit of the DEMO fusion power plant using GateCycle. Fusion Eng. Des. 124, 1237–1240. doi:10.1016/j.fusengdes.2017.03.026
Marín, L. G., Cruz, N., Sáez, D., Sumner, M., and Núñez, A. (2019). Prediction interval methodology based on fuzzy numbers and its extension to fuzzy systems and neural networks. Expert Syst. Appl. 119, 128–141. doi:10.1016/j.eswa.2018.10.043
Meng, Z., Zhang, H., Lei, M., Qin, Y., and Qiu, J. (2018). Performance of low GWP R1234yf/R134a mixture as a replacement for R134a in automotive air conditioning systems. Int. J. Heat Mass Transf. 116, 362–370. doi:10.1016/j.ijheatmasstransfer.2017.09.049
Menken, J. C., Strasser, K., Anzenberger, T., and Rebinger, C. (2018). Evaluation of the energy consumption of a thermal management system of a plug-in hybrid electric vehicle using the example of the Audi Q7 e-tron. SAE Int. J. Passeng. Cars-Mechanical Syst. 11 (3), 203–212. doi:10.4271/06-11-03-0017
Minglu, Q., Rao, Z., Jianbo, C., Yuanda, C., Xudong, Z., Tongyao, Z., et al. (2020). Experimental analysis of heat coupling during TES based reverse cycle defrosting method for cascade air source heat pumps. Renew. Energy 147, 35–42. doi:10.1016/j.renene.2019.08.120
Mohammed, H. R., and Hussain, Z. M. (2021). Hybrid mamdani fuzzy rules and convolutional neural networks for analysis and identification of animal images. Computation 9 (3), 35. doi:10.3390/computation9030035
Mohammed, S., Hafizah, H. N., Sahnius, U., Shadab, A., Surbhi, B., Arwa, M., et al. (2022). Self-sovereign identity solution for blockchain-based land registry system: A comparison. Mob. Inf. Syst. 2022, 1–17. doi:10.1155/2022/8930472
Nguyen, A. T., Taniguchi, T., Eciolaza, L., Campos, V., Palhares, R., and Sugeno, M. (2019). Fuzzy control systems: Past, present and future. IEEE Comput. Intell. Mag. 14 (1), 56–68. doi:10.1109/mci.2018.2881644
Nilpueng, K., Ahn, H. S., Jerng, D. W., and Wongwises, S. (2019). Heat transfer and flow characteristics of sinusoidal wavy plate fin heat sink with and without crosscut flow control. Int. J. Heat Mass Transf. 137, 565–572. doi:10.1016/j.ijheatmasstransfer.2019.03.114
Ning, X., Tian, W., He, F., Bai, X., Sun, L., and Li, W. (2023). Hyper-sausage coverage function neuron model and learning algorithm for image classification. Pattern Recognit. 136, 109216. doi:10.1016/j.patcog.2022.109216
Pabon, J. J., Khosravi, A., Belman-Flores, J. M., Machado, L., and Revellin, R. (2020). Applications of refrigerant R1234yf in heating, air conditioning and refrigeration systems: A decade of researches. Int. J. Refrig. 118, 104–113. doi:10.1016/j.ijrefrig.2020.06.014
Park, M. H., and Kim, S. C. (2017). Heating performance characteristics of high-voltage PTC heater for an electric vehicle. Energies 10 (10), 1494. doi:10.3390/en10101494
Park, M. H., and Kim, S. C. (2019). Heating performance enhancement of high capacity PTC heater with modified louver fin for electric vehicles. Energies 12 (15), 2900. doi:10.3390/en12152900
Peng, B., Zhang, Y., Zhang, P., and Ullah, H. (2021). Recent advances on the electric vehicle heat pump air conditioning system. Recent Pat. Mech. Eng. 14 (3), 354–365. doi:10.2174/2212797614666210125142854
Rajbongshi, R., and Saikia, L. C. (2018). Combined voltage and frequency control of a multi-area multisource system incorporating dish-Stirling solar thermal and HVDC link. IET Renew. Power Gener. 12 (3), 323–334. doi:10.1049/iet-rpg.2017.0121
Salleh, M. N. M., Talpur, N., and Hussain, K. (2017). “Adaptive neuro-fuzzy inference system: Overview, strengths, limitations, and solutions,” in International conference on data mining and big data (Cham: Springer), 527–535.
Sharif, M. Z., Azmi, W. H., Redhwan, A. A. M., and Mamat, R. (2016). Investigation of thermal conductivity and viscosity of Al2O3/PAG nanolubricant for application in automotive air conditioning system. Int. J. Refrig. 70, 93–102. doi:10.1016/j.ijrefrig.2016.06.025
Sharif, M. Z., Azmi, W. H., Redhwan, A. A. M., Mamat, R., and Yusof, T. M. (2017). Performance analysis of SiO2/PAG nanolubricant in automotive air conditioning system. Int. J. Refrig. 75, 204–216. doi:10.1016/j.ijrefrig.2017.01.004
Singh, A. D., and Sharif, M. (2019). Bi-Directional storage capacity and elevation level calculator for reservoir operation management. Am. J. Water Resour. 7 (3), 121–127.
Singh, A. K., and y Sora, M. (2021). An optimized deep neural network-based financial statement fraud detection in text mining. Investig. Pensam. crítico 10 (4), 77–105. doi:10.17993/3cemp.2021.100448.77-105
Su, J., Yuan, S., and Rita, J. N. (2021). Mathematical simulation experiment based on optimisation of heat treatment process of aluminium alloy materials. Appl. Math. Nonlinear Sci. 7, 609–616. doi:10.2478/AMNS.2021.1.00083
Wang, A., Cao, F., Fang, J., Jia, F., Yin, X., and Wang, X. (2022). Research on efficient defrosting control logic for transcritical CO2 electric vehicle heat pump air-conditioning system. Int. J. Refrig. 138, 13–22. doi:10.1016/j.ijrefrig.2022.03.028
Wang, C., Ning, X., Sun, L., Zhang, L., Li, W., and Bai, X. (2022). Learning discriminative features by covering local geometric space for point cloud analysis. IEEE Trans. Geoscience Remote Sens. 60, 1–15. doi:10.1109/TGRS.2022.3170493
Wang, H., Amini, M. R., Hu, Q., Kolmanovsky, I., and Sun, J. (2020). Eco-cooling control strategy for automotive air-conditioning system: Design and experimental validation. IEEE Trans. Control Syst. Technol. 29 (6), 2339–2350. doi:10.1109/tcst.2020.3038746
Wang, J., Cao, J., and Yuan, S. (2021). Deep learning reservoir porosity prediction method based on a spatiotemporal convolution bi-directional long short-term memory neural network model. Geomechanics Energy Environ. 32, 100282. doi:10.1016/j.gete.2021.100282
Wang, M., Zang, R., Hu, E., and Ezzat, A. W. (2018). Investigation of air cooler fan start-up delay in liquid refrigerant defrosting system. Appl. Therm. Eng. 143, 302–307. doi:10.1016/j.applthermaleng.2018.07.066
Wang, Q., Jiang, B., Li, B., and Yan, Y. (2016). A critical review of thermal management models and solutions of lithium-ion batteries for the development of pure electric vehicles. Renew. Sustain. Energy Rev. 64, 106–128. doi:10.1016/j.rser.2016.05.033
Wang, Y., Ye, Z., Song, Y., Yin, X., and Cao, F. (2021). Experimental analysis of reverse cycle defrosting and control strategy optimization for transcritical carbon dioxide heat pump water heater. Appl. Therm. Eng. 183, 116213. doi:10.1016/j.applthermaleng.2020.116213
Xi, Z., Yao, R., Li, J., Du, C., Yu, Z., and Li, B. (2021). Experimental studies on hot gas bypass defrosting control strategies for air source heat pumps. J. Build. Eng. 43, 103165. doi:10.1016/j.jobe.2021.103165
Xie, Y., Yang, P., Qian, Y., Zhang, Y., Li, K., and Zhou, Y. (2022). A two-layered eco-cooling control strategy for electric car air conditioning systems with integration of dynamic programming and fuzzy PID. Appl. Therm. Eng. 211, 118488. doi:10.1016/j.applthermaleng.2022.118488
Yadav, S., Liu, J., and Kim, S. C. (2022). A comprehensive study on 21st-century refrigerants-r290 and R1234yf: A review. Int. J. Heat Mass Transf. 182, 121947. doi:10.1016/j.ijheatmasstransfer.2021.121947
Yang, M., Zhang, H., Meng, Z., and Qin, Y. (2019). Experimental study on R1234yf/R134a mixture (R513A) as R134a replacement in a domestic refrigerator. Appl. Therm. Eng. 146, 540–547. doi:10.1016/j.applthermaleng.2018.09.122
Yi, Q. (2021). Radar system simulation and non-Gaussian mathematical model under virtual reality technology. Appl. Math. Nonlinear Sci. 7, 573–580. doi:10.2478/AMNS.2021.1.00079
Yordanova, S., Merazchiev, D., and Jain, L. (2014). A two-variable fuzzy control design with application to an air-conditioning system. IEEE Trans. fuzzy Syst. 23 (2), 474–481. doi:10.1109/tfuzz.2014.2312979
Yucel, E., Ali, M. S., Gunasekaran, N., and Arik, S. (2017). Sampled-data filtering of Takagi–Sugeno fuzzy neural networks with interval time-varying delays. Fuzzy sets Syst. 316, 69–81. doi:10.1016/j.fss.2016.04.014
Zhang, S., Jiang, H., Yin, Y., Xiao, W., and Zhao, B. (2018). The prediction of the gas utilization ratio based on TS fuzzy neural network and particle swarm optimization. Sensors 18 (2), 625. doi:10.3390/s18020625
Zhang, Z., Wang, D., Zhang, C., and Chen, J. (2018). Electric vehicle range extension strategies based on improved AC system in cold climate–A review. Int. J. Refrig. 88, 141–150. doi:10.1016/j.ijrefrig.2017.12.018
Zheng, K., Zhang, Q., Hu, Y., and Wu, B. (2021). Design of fuzzy system-fuzzy neural network-backstepping control for complex robot system. Inf. Sci. 546, 1230–1255. doi:10.1016/j.ins.2020.08.110
Zheng, S., Wei, M., Song, P., Hu, C., and Tian, R. (2020). Thermodynamics and flow unsteadiness analysis of trans-critical CO2 in a scroll compressor for mobile heat pump air-conditioning system. Appl. Therm. Eng. 175, 115368. doi:10.1016/j.applthermaleng.2020.115368
Zhou, G., Li, H., Liu, E., Li, B., Yan, Y., Chen, T., et al. (2017). Experimental study on combined defrosting performance of heat pump air conditioning system for pure electric vehicle in low temperature. Appl. Therm. Eng. 116, 677–684. doi:10.1016/j.applthermaleng.2017.01.088
Keywords: machine learning, electric vehicle, heat pump air conditioning, control system, defrost
Citation: Miao Z (2023) Intelligent control system for the electric vehicle heat pump air conditioner based on machine learning. Front. Energy Res. 11:1142243. doi: 10.3389/fenrg.2023.1142243
Received: 11 January 2023; Accepted: 03 March 2023;
Published: 24 March 2023.
Edited by:
Xin Ning, Institute of Semiconductors (CAS), ChinaReviewed by:
Juan Manuel Belman-Flores, University of Guanajuato, MexicoCopyright © 2023 Miao. This is an open-access article distributed under the terms of the Creative Commons Attribution License (CC BY). The use, distribution or reproduction in other forums is permitted, provided the original author(s) and the copyright owner(s) are credited and that the original publication in this journal is cited, in accordance with accepted academic practice. No use, distribution or reproduction is permitted which does not comply with these terms.
*Correspondence: Zehua Miao, ZXpyYW1pYW9Ab3V0bG9vay5jb20=
Disclaimer: All claims expressed in this article are solely those of the authors and do not necessarily represent those of their affiliated organizations, or those of the publisher, the editors and the reviewers. Any product that may be evaluated in this article or claim that may be made by its manufacturer is not guaranteed or endorsed by the publisher.
Research integrity at Frontiers
Learn more about the work of our research integrity team to safeguard the quality of each article we publish.