- Key Laboratory of Energy Thermal Conversion and Control of Ministry of Education, School of Energy and Environment, Southeast University, Nanjing, China
1 Introduction
OTEC originates from the conversion of thermal energy generated by the temperature gradient in the vertical direction in the ocean (Jin, Z. J., 2017). Despite the presence of major shortcomings (limited temperature difference, high initial investment cost and maintenance costs, etc.), as one of the sources of green and renewable energy, OTEC is superior to wind and solar energy in stability, given that the temperature difference and temperature, especially in deep cold seawater (DCS), remain constant except for ocean currents and seasonal variations. Global net electricity production from OTEC is approximately 30 TW, according to a fully three-dimensional ocean general circulation model (Krishnakumar R., 2013). The regions with high OTEC potential are mainly small islands and coastal areas in the tropics (between 20° north and 20° south); in these areas, the steep seabed or no-continental shelf is accessible, meaning that deep seawater (at depths exceeding 1000 m) can be accessed within 10 km of the coastline in the former case and near the coastline in the latter (Dan, G., 2022). Furthermore, a suitable marine environment is another advantage of these regions; for example, the equatorial waters of the Pacific Ocean are not substantially affected by adverse events in the external environment, such as typhoons and waves (Kim, H. J., 2021).
It is worth noting that the global distribution of seawater temperature difference is not linear or symmetrical. The surface seawater temperature in the sea area between 30° N and 20° S can exceed 28.8°C, even exceeding 32°C in the region between 5° N and the equator. The temperature difference is 24.8°C–28 °C when the deep seawater (at about 1000 m) is at 4°C. Below this, temperature differences of 17.6°C–24.8°C are available at latitudes between 30° and 45° N, where surface seawater temperatures range between 21.6°C and 28.8°C, meeting the requirements for OTEC operation in summer. However, the operation of OTEC is difficult in the areas at latitudes exceeding 50° N or 30° S latitude, where the surface seawater temperature is generally below 18°C (Hall, K., 2022).
Based on these advantages, several modes have been proposed for utilization of OTEC, such as OTEC-based power generation, OTEC refrigeration (HU, Z., 2022), and desalination. Furthermore, in terms of carbon neutralization benefits, there exist certain proposals for OTEC power generation that would produce considerable amounts of electricity. In 1930, the first OTEC factory was built in Cuba by Georges Claude, a student of d’Arsonval. The plant employed open-cycle OTEC with seawater itself as the working fluid. During the operation process, warm surface seawater was pumped into a low-pressure tank to generate steam, which drove the turbine generator and then condensed into liquid in a chamber with cooling water (Claude, G., 1930). Since then, a range of OTEC plants have been established. The closed-cycle Mini-OTEC unit, constructed by the United States, is capable of producing a net 18.8 kW of electricity (Trimble, L. C., 1980). Additionally, a 100-kW OTEC experimental plant has been designed in the Republic of Nauru by a Japanese electricity enterprise, through which electricity is supplied to the local grid and the validity of the system has been tested (Mitsui, T., 1983). Another example is a 210-kW OTEC power plant located in Hawaii, which has been established to validate the feasibility of this energy source (Uehara, H., 1995). Additionally, a 255-kW OTEC power plant was put into operation at Keahole Point in 1993 and operated continuously for 6 years. Based on the experience of these projects, a new 105-kW platform was constructed in 2013, electricity from which was connected to the grid, although the power of this platform was lower than that of the former system. These cases are expected to contribute to the realization of energy independence in Hawaii in 2045, and the next step is a 10–20-MW device (Dan, G., 2022). In addition, a 1.5-MW OTEC barge underwent temporary testing at the 7th International OTEC Symposium in Busan, South Korea, to explore the large-scale operation of an OTEC plant (Dan, G., 2022).
Although a long time has elapsed since OTEC was first proposed, the situation in terms of theoretical and pilot studies has evolved, if slowly. The considerable costs and low rewards, probably due to low thermal efficiency, underdeveloped cycles, and highly corrosive operating environment, among other factors, are the primary restrictions on the large-scale application of OTEC power generation.
Against this backdrop, this opinion article mainly sheds light on improvements to OTEC power cycles, with a partial focus on future prospects.
2 Progress in and development of OTEC
2.1 Forms of OTEC cycle
The elementary notion of OTEC can be traced back to an 1881 publication by D'Arsonval J. A. (1881). One of the early forms in which OTEC was utilized was that of the mist flow OTEC plant (Figure 1A) (Ridgway, S. L., 1977), in which steam produced by warm surface seawater acts as the working fluid instead of other chemical substances. The steam, generated via large quantities of warm seawater in a tank at an internal pressure of exactly the saturation pressure of seawater at the corresponding temperature, is converted back to liquid at an elevation, through which latent heat is exhausted to the cold seawater and the height of the liquid is elevated. Meanwhile, a hydraulic turbine converts the gravitational potential energy extracted from the warm seawater to rotating mechanical energy and then to electricity via an alternator. In 1926, experiments with open-cycle OTEC power generation was conducted in a laboratory and the electricity produced during the experiments lit bulbs; following this experimentation, a 210-kW open-cycle OTEC system was completed in Hawaii, in which warm water in the evaporator was turned into steam at low pressure, and a nozzle sprayed the steam to drive the turbine to generate electricity (Kobayashi, H., 2001).
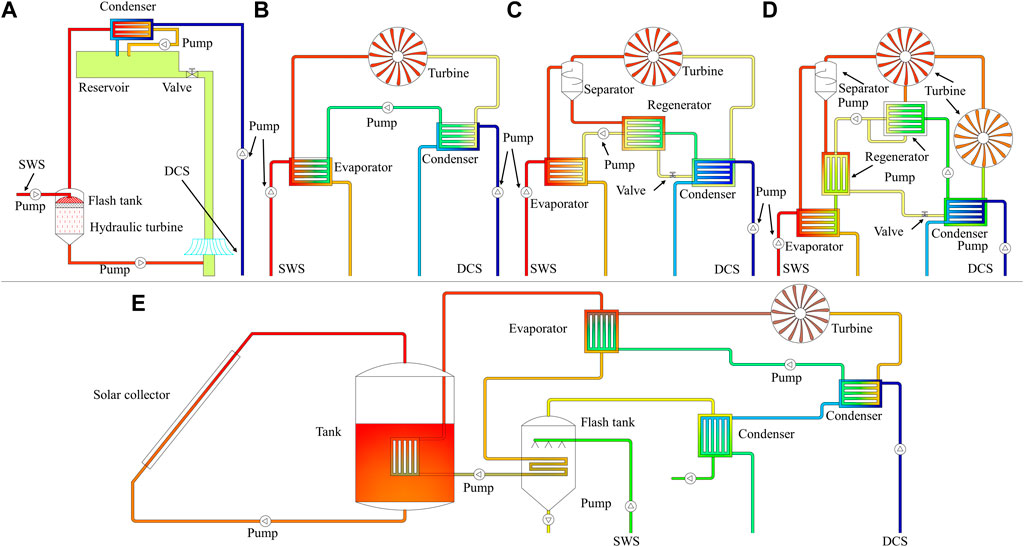
FIGURE 1. Different forms of cycle in OTEC power generation: (A) mist flow OTEC plant (Ridgway, S.L., 1977), (B) organic Rankine cycle, (Cao, H., 2010), (C) Kalina cycle (Kalina, A. I., 1984), (D) Uehara cycle (Uehara, H., 1998), and (E) hybrid solar–OTEC system (Park, S., 2017).
Compared with the method in which water is used directly as the medium, the most universal form of conversion is closed-cycle OTEC, where an intermediate working fluid is developed as the conversion carrier (D'Arsonval J. A., 1881). Since the original development of this approach, many scholars have devoted efforts to improving the performance of OTEC power cycles. The most basic power generation cycle, the Rankine cycle, is widely used in modern industry, especially in power production (Figure 1B) (Cao, H., 2010). Combined with the rapid development of low-boiling-point refrigerants, the Rankine cycle (RC) has been widely studied in context of the OTEC system to establish the appropriate evaporation pressure and low-temperature energy conversion. For example, R717 was used as the working fluid in one RC system, with 28
To improve performance, a separator and regenerator were adopted to configure novel high-efficiency OTEC power cycles, through which the average temperature difference between the working fluid and the external fluid (i.e., the warm surface seawater and cold deep seawater) in the condenser or evaporator was reduced (Kalina, A. I., 1984). This modified cycle, the Kalina cycle (Figure 1C), has been operated effectively with an ammonia–water mixture, with an ammonia-poor mixture delivering heat to the working fluid instead of cooling water to increase the efficiency (from about 3% in the RC to 5% in the Kalina cycle under the same conditions) (Dhanak, M. R., 2016). The decrease in heat transfer temperature difference and the exhaustion of heat to cold seawater played a major role in further improvements; a two-stage turbine with an intermediate extraction and steam regeneration cycle was proposed (Figure 1D), which ultimately resulted in thermal efficiencies of 5.22% and 5.30% for the Kalina cycle and the current cycle (the Uehara cycle), respectively (with an ammonia–water mixture as the working fluid) (Uehara, H., 1998). Compared to the Kalina cycle, the priority of the Uehara cycle is to ensure that amount of heat being released to the cold seawater is decreased by reducing the quantity of exhaust steam through extraction of the steam. With a cooler and a two-stage turbine, 2.40% efficiency was achieved in the novel R717 system, compared with 2.36% and 2.37% for the Kalina and Uehara cycles, respectively, in the same environment (Yoon, J. I., 2014).
2.2 Reinforcement of the OTEC cycle
Despite the aforementioned improvements to the OTEC system, the energy efficiency of OTEC is still considerably low (less than 5.4%) compared with geothermal energy (which exceeds 15% when the heat source temperature is more than 150
2.2.1 Ejectors
The ejector, a consumption-free machine, is widely used in industrial processes, e.g., in the EP-OTEC cycle, where a fluid–vapor ejector and a pressure motive pump have been enrolled in order to lower the turbine outlet pressure. The result was a 38% enhancement compared with the basic OTEC cycle, achieving 4.0% system efficiency along with only a slight increase in the consumption of the whole system at the same gross turbine power (Yoon J. I., 2017).
2.2.2 Heat exchangers
As one of the most significant devices in industrial processes, the heat exchanger plays a decisive role not only in system efficiency but also in cost. The cost of the heat exchanger represents close to 30%–50% of the cost of an OTEC power system, and the heat exchange surface required by the evaporator and condenser is close to 7–8 m2/kW (Dhanak, M. R., 2016). Compared with a conventional shell and tube heat exchanger and a double-fluted-type exchanger, the use of a plate heat exchanger reduces the area by 40%–47% and 33%, respectively, which helps to reduce the cost. In addition, manufacturing costs can be significantly reduced by the use of leak-tolerant systems instead of leak-intolerant systems. In addition, the total heat transfer coefficient of a high-angle plate heat exchanger is about 33% higher than that of a lower-angle one; unfortunately, the pressure drop in the former case is almost four times that of the latter. Furthermore, use of a special coating (applied by spraying molten stainless steel onto the surface of the sandblasting plate with compressed air) on the ammonia side (increasing the K-value by 30%–40%), as well as tiny cavities (which function as nucleation points and thereby improve the evolution), can considerably upgrade the performance of the heat exchanger (Avery, W., 1994) (Dhanak, M. R., 2016). In order to choose an appropriate heat exchanger for OTEC, several heat exchangers have been tested in the Argonne National Laboratory (listed in Table 1). In terms of the results, the Trane plate-fin heat exchanger showed the best performance, with an overall heat transfer coefficient of 7003 W/m2K and ammonia-side and water-side pressure drop of 11 and 21 kPa, respectively (Lewis, L. G., 1978) (Yung, D. T., 1979) (Hillis, D. L., 1979) (Lewis, L. G., 1979) (Lorenz, J. J., 1979) (Panchal, C. B., 1981). In addition, biofouling is another issue that exerts a negative influence on heat transfer performance in OTEC, and there a range of measures have been proposed to control this issue, including NaOCl, the use of Amertrap rubber sponges, a silica particle slurry, liquid sodium hypochlorite, and an intermittent chlorination system of 1.2 mg / 1 residue (interval of 2 hours) for controlling coal slime (Dhanak, M. R., 2016).
2.2.3 Seawater pumps
Given the specific nature of the working environment (high salt corrosion), not only can long-term, efficient operation of the seawater pump (overall seawater pump efficiency can reach 85%) (Geng, D., 2022) reduce the operation and maintenance costs of the system, but it can also increase the annual operation time of the system. OTEC requires a pump with a large flow rate and a low head, and due to the high seawater flow rates, the power consumption of a seawater pump represents a considerable portion of the electricity consumed. The net power is about 65% (Vega, L., 1999) of the total electricity generated in OTEC; the seawater pump, the vacuum pump, and the working medium pump are the main sources of equipment power consumption. In the case of the open-cycle system, the power consumption of the seawater pump, the vacuum pump, and other devices accounts for approximately 61%, 38%, and 1% of the system power consumption, respectively. For the closed-cycle system, the power consumption of the seawater pump and the working fluid pump accounts for approximately 70% and 30% of the system power consumption, respectively. However, under the same system capacity, the power consumption of the latter type of cycle is generally lower than that of the former (Seungtaek, L., 2020). In addition, seawater pumps face a series of issues, such as ship movement (in the case of an off-shore platform) (Ravindran, M., 2022), immersion fluctuation, and seawater corrosion. Taking an optimistic view, with the development of the relevant engineering discipline, a few problems have been solved. For example, stainless steel and nickel cast iron are used to make impellers and housings, respectively, because of their excellent corrosion resistance and stability in salt water. Additionally, improvements to the mechanical structure, such as a special roller thrust bearing, have resolved the pitching motion (about 5%) of the off-shore platform. Furthermore, decreasing the potential of dual-phase steel can significantly reduce the probability of pitting corrosion (Dhanak, M. R., 2016). Most importantly, a considerable range of suggestions to improve the safety of OTEC components have been put forward. These have involved the development of novel superhydrophobic/hydrophobic and slippery surface coatings, inhibiting direct contact with high-salinity seawater and enhancing corrosion resistance (Gulfam, R., 2019).
2.2.4 Auxiliary energy
Even keeping up to date with certain improvements to OTEC, as described previously, the efficiency of the OTEC cycle remains unsatisfactory in relation to Carnot’s theorem (8.27% when the surface seawater is at 29°C and deep seawater is at 4°C). It is clear that industrial waste heat and renewable energy exist as, namely, the geothermal energy and the solar energy, which can be coupled with OTEC through certain arrangements. For proper design, a higher temperature can be achieved in the heating phase of the OTEC cycle through use of an auxiliary heat source in order to improve performance.
Several coupling systems have been successfully proposed that significantly elevate the performance of OTEC systems. For instance, cooling water released from the condensers of three nuclear plants, namely the Kori (30.82°C), Wolsong (29.24°C), and Uljin (30.55°C) nuclear plants in South Korea, has been utilized as a heat source instead of surface seawater. In these three regions, performance metrics for different forms of cycle (closed, regenerative, Kalina, open-ended, and comprehensive cycles), with various working fluids, have been calculated for each plant under equivalent conditions. In these calculations, the regenerative cycle with R-134a stood out, with efficiencies of 5.21%, 5.15%, and 4.83% in each of the regions, respectively (Park, S. S., 2015). Moreover, a novel GeOTEC cycle combining geothermal waste energy (as a heat source for the super heater) with OTEC has been suggested (Mohd I., 2017). The highest efficiency was found to be 4.60% under operation with different superheated ammonia temperatures. Additionally, several united OTEC processes combined with solar power systems have been analyzed in different temperatures and flash pressures. This type of solar-hybrid OTEC system (Figure 1E) has been found to operate at approximately 12.65% efficiency, which is 3.5 times greater than basic hybrid OTEC system, at 80°C with R134a as the working fluid (Park, S., 2017).
Additionally, the use of an auxiliary heat source is not the only way to improve OTEC performance. For example, demonstration has been provided of a combination of wind power generation with an OTEC system to satisfy the electricity consumption of a gasoline station located on the shore of the Mediterranean Sea in Turkey. Based on R600a, the overall system performed with 4.49% energy efficiency and 14.84% exergy efficiency. Furthermore, performance was 12.27% energy efficiency and 23.34% exergy efficiency in the component of the system that was converted into shaft work, which represents the percentage of the maximum theoretical shaft work (Bejan, A., 1995). In total, 2553 kWh/day net electricity was produced, with a cost rate of 3.03$/hr, which could cater for the electricity demands of eight gas stations (Fatih Y., 2019).
2.3 Economics of OTEC power generation
With an increase in capacity, a competitive levelized cost of energy (LCoE) of 0.029$/kWh for a 100-MW scale off-shore OTEC plant can be achieved, according to cost analysis (Langer, J., 2020), compared with average operation costs
2.4 Comparison of offshore and onshore OTEC platforms
Most of the equipment for onshore OTEC is located on the shore. Complex mooring systems or interfaces between the cold water pipe (CWP) and ships are not necessary, and long cables (possibly more than 10 km) for power transmission between the shore and the power generation platform are not required. At the same time, this arrangement is more convenient for export of desalinated seawater and deep-seawater nutrients. However, there are several disadvantages. For instance, longer water pipes and the need to protect pipes passing through the surf zone can increase the initial investment and maintenance costs. In contrast, all equipment for offshore OTEC is installed on the floating platform; thus, it does not occupy limited land space. The length and diameter of the seawater pipes are greatly reduced due to their vertical installation. Nevertheless, floating platforms also have some disadvantages, including the need for complex offshore technical operations during the construction process (Dan, G., 2022). One of the greatest engineering challenges of offshore OTEC is the design of the CWP. In addition to the stress at the connection point, it is also affected by a variety of forces, including water flow resistance, oscillation force caused by vortex shedding, force attributed to harmonic motion of the platform, force produced by the platform drift, and the dead weight of the pipeline (Doorga, J. R. S., 2018).
2.5 Impact of global warming on OTEC
The 196 signatories of the Paris Agreement recognized that climate change may have a negative impact on Earth and decided to control the global temperature rise, keeping it within 2°C by the end of the 21st century. Furthermore, at the 2021 United Nations Climate Change Conference (COP26) (Hall, K., 2022), the delegates determined to make efforts to limit the temperature rise to below 1.5°C, in recognition of the fact that the impact of climate change can be greatly reduced if the temperature rises only by 1.5°C. The possible rise in surface seawater temperatures increases the available temperature difference, which may improve OTEC performance. However, global warming is not uniform in the northern and southern hemispheres, and the former is deemed to be undergoing a larger temperature rise. Consequently, it is anticipated that thermohaline circulation will be altered or even reversed, meaning that the altitude difference required to access a 20 °C temperature difference will be 2100–2300 m. As a result, the power consumption of OTEC systems required to obtain seawater may increase, causing the method to lose its practical value (Nilhous, G. C., 2022). In addition, there are a number of other negative influences, such as enhancement of cyanobacteria disasters in spring (which affects the operation of OTEC power station) (Zhang, M., 2022), and the disappearance of small islands due to the rising sea level (reducing on-shore OTEC sites) (Hall, K., 2022).
2.6 Off-design behavior of OTEC plants
There is no doubt that the temperature of seawater varies with seasons and ocean currents, especially surface seawater. When the temperature difference decreases from 24°C to 17°C, even with a 70% load change, the turbine still shows only a slight isentropic efficiency decrease (from 89% to 87.8%), while the system efficiency decreases from 2.35% to 0.85%. Analysis using data on the annual distribution of sea water temperatures in Hawaii indicates that, under off-design conditions, the net power generation of 8000 equivalent hours is 15.96 GWh, which is 18% less than the value obtained by assuming a constant surface seawater temperature of 28°C. Therefore, when calculating OTEC power generation, it is necessary to consider off-design conditions (Giostri, A., 2021).
3 Outlook
With improvements to the circulation system, the application of novel components, and combination with other renewable energy sources, the use of OTEC systems is a feasible way to address the challenges imposed by the need for carbon neutralization. However, several challenges in the practical application of OTEC still need to be properly resolved, such as the need for advanced specialized ammonia turbines, more efficient heat exchangers, and novel conversion cycles. The specific challenges are as follows.
1) It is clear that low efficiency and the considerable costs are the primary obstacles to the large-scale application of OTEC. Owing to the considerable heat transfer area, heat exchangers for OTEC systems are very costly. Therefore, efficient heat exchangers are needed in order to improve the efficiency and reduce the investment costs of OTEC.
2) Novel working fluids, including pure substances and mixtures, should be proposed to improve the performance of OTEC cycles. However, the downsides associated with the use of a mixture as the working fluid are multifaceted; they include a general increase in the complexity of the system, the need for a separator in the case of an ammonia–water system, and weak thermal stability (R1234yf). For example, the application of ammonia significantly improves the performance of a subcritical OTEC system, through which 19.29% and 12.39% increases in thermal efficiency have been achieved in comparison with R744 and R404A, respectively, under the same fixed conditions. In a comparison of the thermodynamic properties of these three refrigerants, the specific heat capacity and thermal conductivity of ammonia exceeds those of the other two under the same temperature and phase conditions (with thermal conductivity being more than five times that of the other two at 10°C). Thus, superior mediums with higher thermal conductivity and latent heat are required to improve the performance of OTEC systems. In addition, the development of revolutionary thermodynamic cycles (such as semiconductor thermoelectric power generation, which achieves an efficiency of 8.27% when the surface seawater is at 29°C and deep seawater is at 4°C) may help to maximize efficiency.
3) Optimization is another way to improve the performance of OTEC. There are a considerable number of OTEC systems that operate under suboptimal parameters, such as temperature conditions, working fluids, and forms of cycle. Thus, different cases have different optimum operation parameters, and better performance could be achieved through optimization.
4) It is clear that the temperature increment of deep seawater has a significant impact on the utilization of the finite temperature difference. Several different materials have been used in seawater intake, such as steel, concrete, and HDPE. However, low thermal conductivity and excellent mechanical properties have so far been incompatible with the marine environment. Consequently, future research is expected to explore novel materials that can perform appropriately in terms of their mechanical properties, thermodynamic properties (such as pressure drop and cooling loss), and economic properties (investment required). We hereby also recommend using novel surface fabrication techniques, such as superhydrophobic and slippery coatings that can reduce drag, and examining whether they can help in improving the performance by affecting the pressure drop. However, it is still challenging to advance an opinion on how to balance the cost and performance of OTEC systems, and it may be much too early to do so (Zhang M. et al., 2022).
Author contributions
CX wrote the first draft of the manuscript. RG contributed to review, writing, and funding. Both authors contributed by revising, reading, and approving the submitted version.
Funding
This work was supported by the Research Fund for International Scientists under the National Science Foundation of China (grant number 5221101369), and the 72nd Batch of General Funding under the China Postdoctoral Science Foundation (grant number 2022M720711).
Conflict of interest
The authors declare that the research was conducted in the absence of any commercial or financial relationships that could be construed as a potential conflict of interest.
Publisher’s note
All claims expressed in this article are solely those of the authors and do not necessarily represent those of their affiliated organizations, or those of the publisher, the editors, and the reviewers. Any product that may be evaluated in this article, or claim that may be made by its manufacturer, is not guaranteed or endorsed by the publisher.
References
Avery, W., and Wu, C. (1994). Renewable energy from the ocean: A guide to OTEC. Oxford, UK: Oxford University Press.
Bejan, A., Tsatsaronis, G., and Moran, M. J. (1995). Thermal design and optimization.Wiley , Hoboken, NJ, USA.
Bernardoni, C., Binotti, M., and Giostri, A. (2019). Techno-economic analysis of closed OTEC cycles for power generation. Renew. Energy 132, 1018–1033. doi:10.1016/j.renene.2018.08.007
Binger, A. (2004). Potential and future prospects for ocean thermal energy conversion (OTEC) in small islands developing States (SIDS). University of the West Indies Centre for Environment and Development.Kingston, Jamaica
Cao, H., Liu, H., and Dömling, A. (2010). Efficient multicomponent reaction synthesis of the schistosomiasis drug praziquantel. Chemistry 16 (41), 12296–12298. doi:10.1002/chem.201002046
D'Arsonval, J. A. (1881). Utilization des Forces Naturelles, Avenir de L'electricite. Le. Revenue Sci. 17, 370–372.
Dan, G., and Max, C. (2022). 8.04 - ocean Thermal energy conversion (OTEC). 2. Comprehensive Renewable Energy, 40–49. doi:10.1016/B978-0-12-819727-1.00114-X
Dhanak, M. R., and Xiros, N. I. (2016). Springer handbook of ocean engineering.Springer International Publishing Berlin, Germany, doi:10.1007/978-3-319-16649-0
Doorga, J. R. S., Gooroochurn, O., Motah, B., Ramchandur, V., and Sunassee, S. (2018). A novel modelling approach to the identification of optimum sites for the placement of ocean thermal energy conversion (OTEC) power plant: Application to the tropical island climate of Mauritius. Int. J. Energy Environ. Eng. 9, 363–382. doi:10.1007/s40095-018-0278-4
Fatih, Y. (2019). Energy, exergy and economic analyses of a novel hybrid ocean thermal energy conversion system for clean power production. Energy Convers. Manag. 196, 557–566. doi:10.1016/j.enconman.2019.06.028
Geng, D., and Gao, X. (2022). Thermodynamic and exergoeconomic optimization of a novel cooling, desalination and power multigeneration system based on ocean thermal energy. Renew. Energy 202, 17–39. doi:10.1016/j.renene.2022.11.088
Giostri, A., Romei, A., and Binotti, M. (2021). Off-design performance of closed OTEC cycles for power generation. Renew. Energy 170, 1353–1366. doi:10.1016/j.renene.2021.02.047
Gulfam, R., and Zhang, P. (2019). Power generation and longevity improvement of renewable energy systems via slippery surfaces – a review. Renew. Energy 143, 922–938. doi:10.1016/J.RENENE.2019.05.055
Hall, K., Kelly, S., and Henry, L. (2022). Site selection of ocean thermal energy conversion (OTEC) plants for Barbados. Renew. Energy 201, 60–69. doi:10.1016/j.renene.2022.11.049
Hillis, D. L., (1979). OTEC performance tests of the union carbide sprayed-bundle evaporator. Argonne National Laboratory Report ANL/OTEC. Illinois. 10.2172/5926524.
Hu, Z., Wan, Y., Zhang, C., and Chen, Y. (2022). Compression-assisted absorption refrigeration using ocean thermal energy. Renew. Energy 186, 755–768. doi:10.1016/j.renene.2022.01.036
JinYeWangLiQian, Z. J. H. H. H. J. Y. (2017). Thermodynamic analysis of siphon flash evaporation desalination system using ocean thermal energy. Energy Convers. Manag. 136, 66–77. doi:10.1016/j.enconman.2017.01.002
Kalina, A. I. (1984). Combined-cycle system with novel bottoming cycle. J. Eng. Gas Turbines Power 106 (4), 737–742. doi:10.1115/1.3239632
Kim, H. J., Lee, H.-S., Lim, S.-T., and Petterson, M. (2021). The suitability of the pacific islands for harnessing ocean thermal energy and the feasibility of OTEC plants for onshore or offshore processing. Geosciences 11, 407. doi:10.3390/geosciences11100407
Kobayashi, H., Jitsuhara, S., and Uehara, H. (2001). The present status and features of OTEC and recent aspects of thermal energy conversion technologies. 24th Meet. UJNR Mar. Facil. Panel,Saga University , Saga, Japan.
Krishnakumar, R., and Gérard, C. N. (2013). Estimates of global Ocean Thermal Energy Conversion (OTEC) resources using an ocean general circulation model. Renew. Energy 50, 532–540. doi:10.1016/j.renene.2012.07.014
Kumar, C. M., Singh, S. K., Gupta, M. K., Nimdeo, Y. M., Raushan, R., and Deorankar, A. V., (2023). Solar energy: A promising renewable source for meeting energy demand in Indian agriculture applications. 102905, 55, doi:10.1016/j.seta.2022.102905Sustain. Energy Technol. Assessments,
Langer, J., Quist, J., and Blok, K. (2020). Recent progress in the economics of ocean thermal energy conversion: Critical review and research agenda. Renew. Sustain. Energy Rev. 130, 109960. . doi:10.1016/j.rser.2020.109960
Lewis, L. G., and Sather, N. F. (1978). OTEC Performance Tests of the Union Carbide Flooded-Bundle Evaporator, 1. Argonne National Laboratory Report ANL/OTECPS. Illinois.
Lewis, L. G., and Sather, N. F. (1979). OTEC performance tests of the camegie-mellon university vertical fluted-tube condenser. Argonne National Laboratory Report ANL/OTEC. Illinois.
Lorenz, J. J., (1979). OTEC performance tests of the camegie-mellon university vertical fluted-tube evaporator. Argonne National Laboratory Report ANL/OTEC. Illinois.
Mitsui, T., ItoSeya, Y., and Nakamoto, Y. (1983). Outline of the 100 kw otec pilot plant in the republic of naure. IEEE Trans. PAS- 102 (9), 3167–3171. doi:10.1109/TPAS.1983.318124
Mohd, I., N. H., Musa, M. N., Yahya, W. J., and Ithnin, A. M. (2017). Geo-ocean thermal energy conversion (GeOTEC) power cycle/plant. Renew. Energy 111 (), 372–380. doi:10.1016/j.renene.2017.03.086
NamKim, J., Kim, C. N., and Wongee, C. (2009). Using the condenser effluent from a nuclear power plant for Ocean Thermal Energy Conversion (OTEC). Int. Commun. Heat Mass Transf. 36, 1008–1013. doi:10.1016/j.icheatmasstransfer.2009.08.001
Nilhous, G. C. (2007). An estimate of Atlantic Ocean thermal energy conversion (OTEC) resources. Ocean. Eng. 34, 2210–2221. doi:10.1016/j.oceaneng.2007.06.004
Panchal, C. B., Lorenz, J. J., and Hillis, D. L. (1981). The effects of ammonia contamination by water on OTEC power-system performance. Argonne National Laboratory Report ANL/OTEC. Illinois. doi:10.2172/5989233
Park, S., Chun, W., and Kim, N. (2017). Simulated production of electric power and desalination using Solar-OTEC hybrid system. Int. J. Energy Res. 41, 637–649. doi:10.1002/er.3641
Park, S. S., Kim, W. j., Kim, Y. H., Hwang, J. D., and Kim, N. J. (2015). Regenerative OTEC systems using condenser effluents discharged from three nuclear power plants in South Korea. Int. J. Energy Res. 39, 397–405. doi:10.1002/er.3251
Ravindran, M., and Abraham, R. (2002). The Indian 1 MW demonstration OTEC plant and the development activities, 3. Biloxi, MI, USA: OCEANS '02 MTS/IEEE, 1622–1628. 10.1109/OCEANS.2002.1191877.
Ridgway, S. L. (1977). “The mist flow OTEC plant,” in Annual conference on ocean thermal energy conversion. 4 (New Orleans, La: University of New Orleans), A78VIII–37. March 22-24, 1977, Proceedingsto VIII-41 https://ui.adsabs.harvard.edu/abs/1977otec.confU.R/abstract.-33301 13-44) New Orleans.
Seungtaek, L., Hosaeng, L., Junghyun, M., and Hyeonju, K. (2020). Simulation data of regional economic analysis of OTEC for applicable area. Processes 8 (9), 1107. doi:10.3390/pr8091107
Trimble, L. C., and Owens, W. L. (1980). “Review of mini-OTEC performance,” in Energy to the 21st century; proceedings of the fifteenth intersociety energy conversion engineering conference (Seattle, WashNew York: American Institute of Aeronautics and Astronautics, Inc.), 2, 1331–1338. August 18-22.A80-48165 21-44.
Uehara, H., Ikegami, Y., and Nishida, T. (1998)., 64. Transactions of the Japan Society of Mechanical Engineers.B, 2750–2755. doi:10.1299/kikaib.64.2750Performance analysis of OTEC system using a cycle with absorption and extraction processes,
Uehara, H. (1995). The present status and future of ocean thermal energy conversion. Int. J. Sol. Energy 16 (4), 217–231. doi:10.1080/01425919508914278
Vega, L. (1999). ocean thermal energy conversion (OTEC) – OTEC overview., Science Direct, Amsterdam, The Netherlands.
Yoon, J. I., Seol, S., Son, C., Jung, S., Kim, Y., Lee, H., et al. (2017). Analysis of the high-efficiency EP-OTEC cycle using R152a. Renew. Energy 105, 366–373. doi:10.1016/j.renene.2016.12.019
Yoon, J. I., Son, C., Baek, S., Ye, B., Kim, H., and Lee, H. (2014). Performance characteristics of a high-efficiency R717 OTEC power cycle. Appl. Therm. Eng. 72, 304–308. doi:10.1016/j.applthermaleng.2014.05.103
Yung, D. T., (1979). OTEC performance tests of the union carbide enhanced-tube condenser. Argonne National Laboratory Report ANL/OTEC. Illinois. doi:10.2172/5963405
Zhang, C. B., Wu, Z., Wang, J. D., Ding, C., Gao, T. Y., and Chen, Y. P. (2022). Thermodynamic performance of a radial-inflow turbine for ocean thermal energy conversion using ammonia. Renew. Energy 202, 907–920. doi:10.1016/j.renene.2022.12.024
Keywords: ocean thermal energy conversion (OTEC), mist flow OTEC plant, improvements of OTEC power cycles, ejectors, auxiliary heat source
Citation: Xiao C and Gulfam R (2023) Opinion on ocean thermal energy conversion (OTEC). Front. Energy Res. 11:1115695. doi: 10.3389/fenrg.2023.1115695
Received: 05 December 2022; Accepted: 08 February 2023;
Published: 27 February 2023.
Edited by:
Anna Stoppato, University of Padua, ItalyReviewed by:
Andrea Giostri, Politecnico di Milano, ItalyM. Rafiuddin Ahmed, University of the South Pacific, Fiji
Copyright © 2023 Xiao and Gulfam. This is an open-access article distributed under the terms of the Creative Commons Attribution License (CC BY). The use, distribution or reproduction in other forums is permitted, provided the original author(s) and the copyright owner(s) are credited and that the original publication in this journal is cited, in accordance with accepted academic practice. No use, distribution or reproduction is permitted which does not comply with these terms.
*Correspondence: Raza Gulfam, Z3VsZmFtQHNldS5lZHUuY24=, Z3VsZmFtcmF6YWhhaWRlcnlAaG90bWFpbC5jb20=