- Chongqing Industry Polytechnic College, Chongqing, China
The use of corrosion inhibitors can effectively avoid the corrosion of metals and alloys, but the conventional organic/inorganic corrosion inhibitors have certain toxic and side effects and environmental pollution problems (including some expensive toxic reagents and catalysts), prompting researchers to turn their attention to the research of water-soluble polymer corrosion inhibitors with green environment friendly and low pollution. This paper reviews the action mechanism of polymer inhibitors, the research status of natural polymer inhibitors (chitosan-based inhibitors, cellulose and its derivatives inhibitors, other carbohydrate inhibitors, protein inhibitors) and synthetic polymer inhibitors (epoxy resin inhibitors, polyethylene glycol inhibitors, conductive polymer inhibitors), The purpose is to provide some reference for the development of eco-friendly metal coatings.
Introduction
Carbon steel, alloys (magnesium, aluminum alloys) and other metal materials are widely used in industry, agriculture, transportation, daily life and other fields because of their good plasticity, easy processability and excellent mechanical properties (Pludek, 1977; Bardal et al., 1993; Musa et al., 2012). However, under natural conditions, metal materials usually react with corrosive media such as water, Cl−, SO42−, O2 in the surrounding environment, which changes their chemical properties, resulting in a large amount of metal components peeling off with the corrosive media. The essence of metal corrosion is the process of metal atoms losing electrons and being oxidized. Metal corrosion can be generally divided into chemical corrosion and electrochemical corrosion. Electrochemical corrosion is the most common and important type of metal corrosion. The corrosion of steel in humid air is the most prominent example of electrochemical corrosion. In the humid air, a thin water film will be adsorbed on the steel surface. If the water film is strongly acidic, hydrogen will be released from the electrons of H+, and this electrochemical corrosion is called hydrogen evolution corrosion; If the water film is weakly acidic or neutral, more oxygen can be dissolved. At this time, O2 gets electrons and precipitates OH−. This electrochemical corrosion is called oxygen absorption corrosion and is the main cause of steel corrosion. According to the National Association of Corrosion Engineers (NACE), up to now, the global loss caused by corrosion is equivalent to about 3.4% of the world GDP, and safety accidents caused by corrosion continue to occur (Sheikh et al., 2021; Guo et al., 2020). In order to reduce the loss caused by metal corrosion, metal corrosion prevention methods such as surface modification, anodic oxidation, electroless plating or electroplating, and chemical coating have been developed in succession (Vijayan and Al-Maadeed, 2019; Grundmeier et al., 2000). The method of using heterocyclic compound organic coating to protect metal substrates has the advantages of low cost, fast construction, and excellent corrosion resistance. It is one of the fastest-growing anti-corrosion methods in recent decades, and is widely used in the field of metal protection. However, there are still many defects in the use of these compounds as corrosion inhibitors. The first is that these compounds are not environmentally friendly. Because most of the compound raw materials, solvents and catalysts are expensive and have toxic side effects, their application is greatly limited (Balgude and Sabnis, 2012; Guo et al., 2020; Tan et al., 2022). Polymer has the advantages of low cost, stable properties, non-toxic and so on. In recent years, it has gradually become an environmental protection inhibitor to replace the conventional heterocyclic inhibitor (Figure 1). Because the polymer contains various macromolecules and functional groups (–N=N–, R–NH2, R–COOH, etc.), it can be used as both an anti-corrosion coating and a corrosion inhibitor (Table 1). Among them, amine, imine, amide polymers, vinyl and vinyl polymers account for 76.08% of polymer corrosion inhibitors (Fathima Sabirneeza et al., 2015). In addition, there are heteroatoms in biopolymers or macromolecules formed by the degradation of active organisms (animals, plants, bacteria, microorganisms, etc.), which show a certain adsorption capacity, so as to achieve the purpose of preventing metal surface corrosion (Sushmitha and Rao, 2019). Therefore, this paper reviews the action mechanism of polymer inhibitors, the application status of biopolymer inhibitors (chitosan-based inhibitors, cellulose and its derivatives inhibitors, other carbohydrate inhibitors, protein inhibitors) and synthetic polymer inhibitors (epoxy resin inhibitors, polyethylene glycol inhibitors, conductive polymer inhibitors), The purpose is to provide some reference for the development of eco-friendly metal coatings.
Mechanism of polymer corrosion inhibitor
Metal corrosion is the result of galvanic cell reaction on the metal surface, which is the main cause of corrosion. Galvanic cell reaction usually includes anode reaction and cathode reaction. If corrosion inhibitor can inhibit either anode or cathode reaction, it will slow down the galvanic cell reaction process and weaken the corrosion rate of metal (Zeng and Chen, 2012; Jevremović et al., 2020). At present, the mechanism of corrosion inhibitor has not been fully understood, but the main corrosion inhibition principles are as follows:
(1) Physical/chemical adsorption at the metal/electrolyte interface;
(2) Electrostatic interaction of the protonated groups existing in corrosion inhibitor molecules and cations on surface of the metal matrix;
(3) Chemical interaction between unshared electrons (electrons on N, S, O atoms) and empty d orbitals in the electronic structure of metal atoms;
(4) By forming stable metal corrosion inhibitor complexes.
The action mechanism of polymer inhibitor is similar to heterocyclic inhibitor. It mainly forms a protective film for blocking aqueous medium by adsorbing on the surface of metal matrix. The stability and blocking effect of the protective film depend on the hydrophilicity and hydrophobicity of the polymer, which directly determines the adhesion ability of the polymer film. Polymer adsorption can be divided into physical adsorption, chemical adsorption and mixed adsorption. Among them, physical adsorption is mainly caused by the van der Waals force between the polymer inhibitor molecules and the surface of the metal matrix, while chemical adsorption uses the electron transfer and exchange between the polymer inhibitor and the surface atoms of the metal matrix to form the adsorption of chemical bonds. In addition, there are also mixed adsorption methods covering two adsorption characteristics (Hui et al., 2020; Verma et al., 2022). The adsorption process of polymer corrosion inhibitor can be divided into the following steps:
(1) Polymer molecules replace acid ions and water molecules on the metal surface;
(2) Polymer molecules and acid ions form flocs;
(3) Polymer molecules use the hydroxyl, carboxyl and other organic functional groups contained in them to provide electrons to the empty orbit of the metal, form chelates with metal ions, and adsorb on the metal surface to form a hydrophobic protective film.
At the same time, in the process of polymer corrosion inhibitor, the metal corrosion efficiency will also be related to the chemical stability, coating uniformity and adsorption effect of the polymer. In addition, the density of donor electrons, electrolyte composition, pH value, apparent morphology of metal matrix, charge characteristics, etc. will also affect the effect of polymer corrosion inhibitor (Dariva and Galio, 2014).
Aqueous polymer inhibitor
Chitosan based corrosion inhibitor
As a linear polysaccharide, chitosan (Cht) contains various polar functional groups (amino, hydroxyl, acetyl, hydroxymethyl, etc.) on its linear polymer chain (Figure 2). These functional groups help to improve the solubility of chitosan in polar electrolytes and make chitosan easy to adsorb on metal surfaces. And because the acidity coefficient (pKa) value of amino group in chitosan is 6.5, it has a high degree of protonation in neutral and acidic environment. This property makes chitosan water-soluble and can form a good adhesion with negatively charged metal surfaces. In addition, chitosan can be modified to improve its biological tolerance and corrosion resistance. It is because chitosan and its derivatives have the characteristics of non-toxic, environmental protection, non-sensitization, biocompatibility and degradability that they have been widely concerned in food, biomedicine, agriculture, environment, pharmaceutical and other industries.
Blanda et al. (2019) deposited a thin chitosan gel layer on the surface of 304 stainless steel sample through galvanic displacement reaction, and measured that the Icorr of steel before and after chitosan coating were 24.5 and 1.14 respectively μA cm−2, while Ecorr values were -0.161 and 0.0045 V respectively. The deposited chitosan coating successfully slowed down the corrosion rate of the matrix. It is found that the adhesion strength of chitosan coating is related to the type of solution, potential and other factors. For example, the adhesion of chitosan in the solution system is: methanol < isopropanol < ethanol solution. In addition, the thickness of chitosan coating is proportional to the potential. In order to improve the adhesion between chitosan and steel surface, polar functional groups can also be added to the main chain of chitosan for modification to strengthen its corrosion inhibition ability. Chauhan et al. (2019) used 4-amino-5-methyl-1,2,4-triazole-3-mercaptan for the first time to chemically modify chitosan corrosion inhibitor. Through the evaluation of its corrosion inhibition performance on the surface of carbon steel in 1 M HCl solution, it was found that the adsorption of the modified corrosion inhibitor conformed to the Langmuir isotherm, which showed physical adsorption and chemical adsorption. In addition, with the increase of inhibitor concentration, its polarization resistance gradually increases, which is a mixed inhibitor with cathode advantage, and the purpose of enhancing the corrosion inhibition effect can be achieved by improving the combination of Fe inhibitor system. Farhadian et al. (2020) used 1,3-propanesulfonic acid to sulfonate chitosan with different molecular weights to improve its solubility and overcome the incompatibility between hydrate inhibitor (HHIs) and inhibitor. The test shows that low molecular weight sulfonated modified chitosan (SCS) has obvious inhibition effect on metal corrosion in 2 M HCl solution, and the inhibition rate is close to 95.6 ± 0.1%. In addition, chitosan derivatives can also be used as metal corrosion inhibitors. Suyanto et al. (2015) synthesized two chitosan derivatives, carboxymethyl chitosan benzaldehyde (CMChi-B) and carboxymethyl chitosan urea glutaric acid (CMChi-UGLU), using chitosan as raw materials. By using NaCl 2% solution as the corrosion medium, the maximum corrosion inhibition rates of CMChi-B and CMChi-UGLU on steel are 80.8% and 80.6% respectively. Both inhibitors show strong corrosion inhibition ability.
Chitosan and its derivatives have a wide range of sources and low cost. By adjusting the parameters of the coating solution and introducing polar functional groups, the adhesion strength can be effectively improved, showing good application potential.
Corrosion inhibitor of cellulose and its derivatives
Cellulose is a natural polymer rich in carbohydrates, which is widely distributed in cotton, wood, hemp and other animal and plant raw materials (Figure 3). Due to the environmental protection of its source, it is currently one of the main sources of compounds as eco-friendly metal corrosion inhibitors (Rajeswari et al., 2013).
Nwanonenyi et al. (2019) studied the adsorption and corrosion inhibition properties of hydroxypropyl cellulose (HPC) for aluminum in 0.5 M HCl and 2 M H2SO4 media. The results show that HPC has strong anodic effect in both corrosion solutions and is a mixed inhibitor. The sustained release rate increases with the increase of concentration, but its sustainability decreases with the increase of temperature. Hassan and Ibrahim. (2021) studied the corrosion inhibition effect of methylcellulose (MC) on magnesium (Mg) metal in hydrochloric acid. The results show that the corrosion inhibition rate of Mg metal surface increases with the increase of inhibitor concentration and decreases with the increase of temperature. Its adsorption conforms to the Langmuir and Freundlich isotherm model. This is because MC inhibitor can form OH− bridging on the metal surface and adsorb on the Mg metal surface, thus delaying the corrosion of the metal surface. Sobhi and Eid (2018) studied the corrosion inhibition effect of methyl hydroxyethyl cellulose (MHEC) on metal copper in 1 m HCl. The results showed that the adsorption of MHEC on the copper surface followed the Langmuir isotherm, mainly physical adsorption. Its corrosion inhibition depends on the concentration of inhibitor. This inhibition is due to the adsorption of MHEC on the surface of copper, which hinders the charge transfer on the surface of copper, so as to protect the copper surface from aggressive ions. Manimaran et al. (2013) evaluated the corrosion inhibition rate of carboxymethyl cellulose (CMC)-Zn2+ system on carbon steel in formation water with or without Zn2+ by weight loss method. The results show that the corrosion inhibition rate of the formula composed of 250ppm CMC and 50 ppm Zn2+ is as high as 98%. It is pointed out that the corrosion inhibition mechanism of CMC is due to the formation of protective film between Fe2+-CMC complex and Zn(OH)2, and CMC-Zn2+ system has synergistic effect. In addition, conventional cellulose can be modified or cellulose derivatives can be selected to avoid the limited solubility of conventional cellulose. Farhadian et al. (2021) developed a chemically modified hydroxyethyl cellulose (CHEC) and evaluated the anti-corrosion effect of CHEC in low carbon steel. The results show that CHEC can effectively maintain its anti-corrosion activity in the temperature range of 20–80°C, and the corrosion inhibition rate is as high as 93% at 80°C. In terms of mechanism analysis, CHEC inhibits the metal dissolution of the anode and the hydrogen evolution reaction of the cathode by generating chemical adsorption on the surface of the corroded metal. Its adsorption conforms to the Langmuir adsorption isotherm model.
Because cellulose has various electron rich polar functional groups, but its solubility in polar solvents is limited, it is often necessary to introduce polar substituents into the molecular structure of cellulose for chemical modification. These polar functional groups can improve the corrosion inhibition effect of inhibitors by increasing the molecular size and solubility of cellulose.
Starch corrosion inhibitor
As a natural renewable polymer carbohydrate, starch has the characteristics of low cost, non-toxic, degradable and so on. It is widely used in food industry, pharmaceutical, papermaking and other fields. It mainly exists in corn, potatoes, wheat and other grains, and is composed of various glucose units. However, natural starch is easy to stick together, there are problems of aging and biological corruption, and because of its poor corrosion inhibition ability and low water solubility, it is rarely used as a corrosion inhibitor directly. However, due to the existence of amylose (20–25%) and amylopectin (75–80%), there is a large space for modification (Figure 4).
Nwanonenyi et al. (2017) studied the corrosion inhibition performance of millet starch (MS) in 30 ± 1°C and 0.5 M HCl solution. The results show that MS has obvious inhibition effect on the corrosion of low carbon steel in acid solution, and the inhibition effect is proportional to the concentration of MS. Wu et al. (2016) studied the corrosion inhibition performance of carboxymethyl starch (CMS) on low carbon steel in hydrochloric acid solution. The results show that CMS has good corrosion inhibition effect in 5% HCl solution at 24–60°C. When the concentration of CMS increases to 2 g/L, the corrosion rate of low carbon steel decreases to 11.19 mm/year, and the corrosion inhibition rate is 80.61%. CMS acts as a cathodic inhibitor, and its corrosion inhibition rate increases with the increase of CMS concentration, and the corrosion inhibition effect at room temperature is the best. However, conventional starch has poor corrosion inhibition ability and low water solubility, so it cannot be directly used as a metal corrosion inhibitor, so it often needs to be modified. Ochoa et al. (2013) studied the corrosion inhibition effect of activated carboxymethylated cassava starch derivatives (CMS) on carbon steel XC35 in 200 mg L−1 NaCl solution. The results showed that activated starch was a mixed inhibitor, while carboxymethylated cassava starch mainly inhibited the anodic reaction. The slow-release rate of the two corrosion inhibitors increases with the increase of concentration. Activated starch can form a more stable and dense protective film than CMS, because the alkoxy and carboxylic groups in starch can form chelates with the surface of oxidized metal to block its active sites. Anyiam et al. (2020) modified sweet potato starch (NS) extract by alkali treatment to obtain alkali modified starch (AMS), and evaluated its corrosion inhibition performance under acidic conditions. The results show that AMS has high corrosion inhibition effect, and the corrosion inhibition effect tends to be stable with the extension of time. In addition, the synergistic use of potassium iodide (KI) can also improve the corrosion inhibition effect of AMS. Li et al. (2020) synthesized cassava starch sodium allyl sulfonate acrylamide graft copolymer (CS-SAS-AAGC) ternary graft copolymer by chemically modifying cassava starch (CS) and grafting with sodium allyl sulfonate (SAS) and acrylamide (AA). The corrosion inhibition performance of CS-SAS-AAGC on cold rolled steel (CRS) in 1.0 M HCl solution was studied. The results show that the best corrosion inhibition rate of CS-SAS-AAGC at 50 mg L−1 is 97.2%, and its corrosion inhibition ability is stronger than CS, SAS and AA. Lahrour et al. (2019) used glycerol grafted starch as a metal corrosion inhibitor, grafted glycerol molecules on amylopectin, and then evaluated its corrosion inhibition effect in 1 m HCl solution and C-Mn steel. The results show that the inhibitor may be of cathode type. With the increase of inhibitor concentration, the corrosion current density decreases, and the inhibition effect of the inhibitor gradually increases. When the concentration of inhibitor is increased to 300 mg L−1, the inhibition rate can reach 94.25%.
Starch has a large space for modification. Starch corrosion inhibitor based on certain activation and modification of starch raw materials is also an effective choice for metal corrosion prevention.
Protein inhibitor
As a kind of biological macromolecule (or biopolymer), protein is composed of one or more amino acid (AAS) residue polymerization chains. It plays a role in DNA replication and catalytic metabolism in organisms (Figure 5). Because of its wide source, easy degradation and low cost, it is widely used in industrial and biological fields. At present, studies have shown that proteins have specific amino acid functional sites. Through protonation, molecules can interact with metal surfaces to produce colloidal organometallic complexes. In addition, protein denaturation will also form a corrosion inhibition film on the metal surface, thereby delaying the corrosion process of metal (Talha et al., 2019).
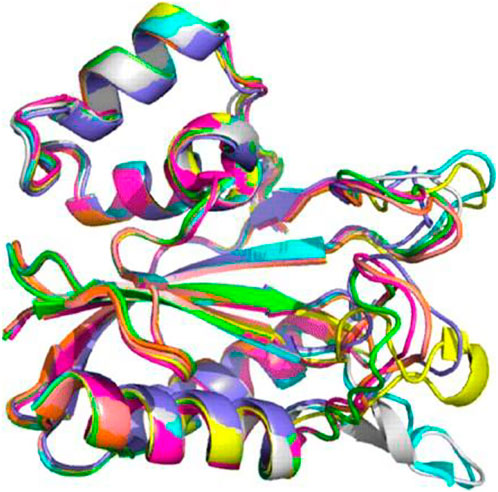
FIGURE 5. Molecular structure of protein-conformational state (Burra et al., 2009)
Ma et al. (2021) studied the corrosion behavior of AZ31 magnesium alloy under the action of different concentrations of bovine serum albumin (BSA). The results showed that the corrosion resistance of BSA to AZ31 increased with the increase of its concentration in the range of 0–2.0 g/L. Among them, BSA mainly delays the process of metal corrosion by physical adsorption, but continue to increase the concentration of BSA to 5.0 g/L. BSA will chelate with dissolved Mg2+, Ni2+ and other metal ions to form a soluble complex, which will increase the surface roughness of the metal and accelerate its corrosion process. Höhn et al. (2019) also confirmed the view that protein can be used as both a corrosion promoter and a corrosion inhibitor for magnesium alloys, which depends on the selected corrosion inhibitor system, protein concentration, protein size, protein surface interaction (surface charge), medium and protein-protein interaction. Farag et al. (2018) deproteinized the chitin in shrimp shell with acetic acid and sodium carbonate to obtain shrimp shell waste protein (RSWP) with low extraction cost and environmental friendliness, and explored the corrosion inhibition effect of RSWP as a carbon steel inhibitor in 1 M HCl solution. The results show that RSWP, as a mixed corrosion inhibitor, its corrosion inhibition depends on its adsorption on the steel surface, which follows the Langmuir adsorption isotherm and is a spontaneous chemical adsorption mode. The inhibition rate increased with the increase of RSWP concentration, and its inhibition effect was determined by the number of donor atoms in amino acids in protein. Rabizadeh and Asl (2019) studied the effect of bovine cheese protein on the corrosion behavior of low carbon steel in 0.1 M HCl, and found that casein can act on the metal surface by physical or chemical adsorption, and its selective adsorption conforms to the Langmuir adsorption isotherm. In addition, this process is accompanied by the increase of activation energy and activation enthalpy of corrosion process, and the increase of casein concentration will also lead to the decrease of corrosion current density.
In addition to the corrosion inhibition performance of animal protein extracts, researchers have also conducted relevant research on the corrosion inhibition effect of plant proteins. Zunita et al. (2022) separated proteins and their amino acids (Glycine, methionine, proline, threonine, tryptophan, etc.) from tofu pulp, and evaluated their corrosion inhibition in brackish water medium. The results showed that the corrosion inhibition rate of the separated protein was 92% at the concentration of 80 ppm and 25°C, and its adsorption process followed the Langmuir isotherm curve ΔGads is −33.5 kJ/mol. Zhang et al. (2019) studied the corrosion inhibition effect of corn gluten powder extract on reinforcement in 3.0 wt% NaCl solution. The results show that the amide bond structure of the main components in the extract is conducive to the adhesion of the steel surface. The corrosion inhibition rate of the extract to the steel is 62.7%–88.1%. Its adsorption process follows the Langmuir isotherm curve and is mainly controlled by physical adsorption.
Animal/plant proteins are supplied from a wider range of sources. By changing protein concentration, protein size, protein surface interaction (surface charge), medium and protein-protein interaction, the corrosion rate of metals can be effectively reduced. However, at present, the mechanism of protein corrosion inhibition needs to be further studied.
Arabic gum inhibitor
Arabic gum (GA) is a common natural gum. Because of its low cost, non-toxic and good biocompatibility, it is widely used in the food and coating industry as a stabilizer, film-forming agent, emulsifier and viscosity control agent. GA is a complex mixture of arabinogalactan, oligosaccharides, polysaccharides and glycoproteins. It has a highly branched complex polysaccharide structure, which makes it have a relatively small hydrodynamic volume, thus allowing more functional groups to be adsorbed on the metal surface (Figure 6), showing a certain corrosion inhibition potential (Ali et al., 2009).
Shen et al. (2019) studied the corrosion inhibition performance of GA on 1018 carbon steel in brine. The results show that GA surface mainly improves the corrosion inhibition ability of metals by chemical adsorption, and the corrosion inhibition rate increases with the increase of GA concentration. Its adsorption follows the Langmuir isotherm, and the corrosion inhibition rate at room temperature is up to 94%. Palumbo et al. (2020) studied the corrosion inhibition effect of GA on N80 carbon steel in high-pressure CO2 salt water environment. The results show that the corrosion inhibition rate of N80 carbon steel increases with the increase of inhibitor concentration and CO2 partial pressure. After soaking for 24 h, the maximum corrosion inhibition rate when PCO2 = 4 MPa is 84.53%. The partial pressure was maintained for 168h, and the corrosion inhibition rate of GA was 74.41%. In addition to investigating the corrosion inhibition effect of GA on different types of corrosive media and materials, halide ions are also one of the important parameters affecting the corrosion inhibition performance of GA. Djellab et al. (2018) explored the corrosion inhibition effect of halide ions (KI, KCl, and KBr) on the surface of API5L X70 pipeline steel in 30°C and 0.5 m H2SO4 solution. The results show that the synergistic effect of 2 g·L−1 GA and 0.5 M KI can obtain significant corrosion inhibition effect (the inhibition rate is 99%), and its adsorption follows the Langmuir adsorption isotherm. In addition, the order of inhibition gain effect between GA and halide is: I > Cl > Br. In addition to halides, nanoparticles are also an important component that affects the corrosion inhibition performance of GA. Asaad et al. (2021) studied the corrosion inhibition effect of nanoparticles Arabic gum (GA-NPs) on reinforced concrete exposed to CO2 for 180 days. The results show that in the concrete mixed with 3% GA-NPs, the corrosion inhibitor molecules form a protective layer by adsorption on the surface of the reinforcement, the corrosion inhibition rate is increased to 94.5%, and the corrosion rate is reduced to 0.57 × 10−3mm/year. In addition, due to the consumption of Ca(OH)2, GA-NPs reduced Ca/Si to 3.72% and 0.69% respectively. Nawaz et al. (2021) added about 30.0wt% GA to cerium oxide nanoparticles (CONPs) anti-corrosion coatings, and developed an environment-friendly anti-corrosion additive for coated steel in marine environment. The inhibitor combination can effectively reduce the corrosion active area by releasing Ga from CONPs and adsorbing it on the steel surface, thus playing a corrosion inhibition role.
Similarly, as a biological corrosion inhibitor, the corrosion inhibition performance of Arabic gum is relatively insufficient. At present, the research on Arabic gum inhibitor mainly focuses on auxiliary corrosion inhibition, but the complex polysaccharide structure of Arabic gum provides the basis for its modification and enhancement.
Other plant corrosion inhibitors
At present, the selection of low-cost and environment-friendly biological corrosion inhibitors has become the current mainstream development trend. Many plant extracts contain heteroatoms such as N and P, conjugated double bonds and polar functional groups (Tan et al., 2020). Their electronegativity makes this kind of corrosion inhibitor can form a barrier diaphragm to isolate corrosive media by adsorption on the metal surface.
Guo et al. (2021) found that banana leaves contain a large number of organic compounds containing heteroatoms (N, O, etc.), which can form coordination bonds with the three-dimensional empty orbital of iron atoms, thus forming stable chemical adsorption on the surface of X70 steel. Hu et al. (2020) found that durian pulp skin/core extract (DPSE) contains rich terminal hydroxyl, amino, carboxylic acid and amide groups. Through the corrosion inhibition performance test of DPSE on copper in 0.5 mol/L H2SO4 solution, DPSE can effectively adsorb on the copper surface to slow down corrosion, and the corrosion inhibition rate can reach 92.6%, which is in line with Langmuir isotherm. Chen et al. (2022) explored the corrosion inhibition performance of Ginkgo biloba extract on X70 Steel in 1mol/L HCl solution, and found that the main components of the extract form a dense and stable adsorption film on the surface of × 70 steel, which can effectively prevent the attack of corrosive species on the steel substrate. Tan et al. (2022) explored the corrosion inhibition effect of areca leaf extract (BLE) on Q235 steel and found that BLE could inhibit the cathodic and anodic reactions of Q235 steel. When BLE concentration is 400 mg/l, the anti-corrosion efficiency is close to 94%.
Recent studies have proved the effectiveness of plant extracts as metal corrosion inhibitors, but it is also necessary to ensure that the extraction solvent used in the extraction process should meet the basic requirements of environmental friendliness, low price, good solubility and so on. At the same time, the final extract must be non bioaccumulative, non-toxic and biodegradable.
Synthetic polymer corrosion inhibitor
Synthetic polymers usually refer to polymers synthesized under laboratory conditions. Because of their high molecular weight, they can still maintain good coating effect even at low concentration, thus playing a certain anti-corrosion effect. Therefore, the application status of resin-based corrosion inhibitor, polyethylene glycol corrosion inhibitor and conductive polymer corrosion inhibitor which are widely used at present are introduced respectively.
Resin based corrosion inhibitor
Epoxy resin, also known as epoxy polymer, has the advantages of many varieties, large curing/modification space, strong adhesion of peripheral polar substituents, low curing shrinkage, high mechanical strength, strong acid and alkali resistance, etc. Due to the polymer characteristics of epoxy resin, it can form excellent surface coverage and strong adsorption capacity on the metal surface, and heteroatoms such as O, N and s in epoxy resin are easy to protonate, which is conducive to the dissolution of epoxy polymer in polar electrolyte (Jin et al., 2015). In addition, epoxy ring can also be protonated in strong acidic solution and undergo ring opening reaction to form -OH substituents with strong polarity and interaction with water (Figure 7). However, due to the high molecular weight of most epoxy resins, the solubility in polar electrolytes is still limited, so at present, waterborne epoxy resins are mainly used as metal corrosion inhibitors.
Hsissou et al. (2020) studied the corrosion inhibition effect of diglycidyl aminobenzene (DGAB) epoxy prepolymer on acid corrosion of carbon steel. The results show that DGAB has good metal adsorption and corrosion barrier ability. Its adsorption process conforms to the Langmuir adsorption isotherm, and the corrosion inhibition rate is as high as 95.9% at the concentration of 10−3 M. Dagdag et al. (2020) used methylene diphenylamine (MDA) as curing agent to build a macromolecular epoxy coating (DGEDDS-MDA) based on bisphenol s diglycidyl ether (DGEDDS). It was found that the electron rich center of DGEDDS-MDA showed strong adsorption capacity with Fe (110) metal surface, and its adsorption energy was-300.67 kJ/mol. In addition to exploring the influence of the type of epoxy resin on metal corrosion, researchers also modified the resin-based materials to obtain better corrosion inhibition effect.
In addition to using different types of epoxy resins for metal corrosion inhibition experiments, researchers also improved the corrosion inhibition effect of conventional resin materials by doping silicon and carbon nanoparticles or using chemical reagents. Joseph et al. (2020) synthesized ceria zirconia solid solution (CexZr1-xO2 nanoparticles) with different doping concentrations by co deposition method, and prepared CexZr1-xO2 nanoparticles waterborne epoxy resin coating on low carbon steel substrate by spin coating technology. The results showed that CexZr1-xO2 nanoparticles effectively improved the corrosion resistance of waterborne resin. In CE rich Ce−Zr solid solution (0.6 ≤ × ≤ 0.8), with the increase of Zr doping concentration, the corrosion resistance of CexZr1-xO2 nanoparticles waterborne epoxy resin is enhanced, because a large amount of oxygen vacancies improves the redox performance of the resin-based system. Sharma et al. (2022) used carbon nanotubes/reduced graphene oxide (CNT/rGO) to modify the epoxy resin corrosion inhibition coating, and found that CNT/rGO can effectively improve the mechanical strength of the coating matrix, and can effectively improve the dispersion and bonding characteristics of nano fillers by cooperating with silane agents. The corrosion results show that CNT/rGO modified epoxy coating can form a dense, impermeable and durable coating on the surface of reinforcement. This is because the functional groups on the rGO sheet provide a dense network structure, and the rGO sheet also has a certain hydrophobicity, which can effectively reduce the infiltration ability of corrosive media. Karaxi et al. (2019) studied the modification effect of liquid rubber polymer on epoxy resin. The experimental results show that the corrosion inhibition coating can form a stable chelate on the surface of galvanized steel, has strong barrier performance, and the coating shows a certain self-reaction and self-healing effect on corrosion damage. Rahman et al. (2019) found that the use of indole butyric acid (IBA) modified gypsum can effectively improve the corrosion resistance of epoxy coating to reinforcement, and the coating has no adverse effect on the bond strength between embedded reinforcement and concrete. The reason is related to the healing effect of metal surface passivation in corrosive environment; On the other hand, it is attributed to the adhesion and good isolation ability of the resin. Dagdag et al. (2019) explored the corrosion inhibition effect of zinc phosphate on the surface of aa7075-t6 aluminum plate substrate with bisphenol epoxy resin coating in NaCl solution (3wt%). The results showed that the addition of zinc phosphate promoted the formation of the coating barrier layer and effectively delayed the penetration rate of corrosive ions on the surface of the coating in the epoxy resin polyamide anticorrosive system.
Resin based corrosion inhibitor is the mainstream metal corrosion inhibitor at present because of its good acid, alkali and salt resistance. And the epoxy resin has a large modification space, which can further improve its corrosion inhibition performance by doping various functional nano materials.
Polyethylene glycol corrosion inhibitor
Polyethylene glycol (PEG) as a high molecular polymer, its molecular weight ranges from 200 to 10 of thousands (Figure 8). Due to its good dispersion, solubility, adhesion and low raw material cost, peg is widely used in chemical, pharmaceutical, food and other fields (Chen et al., 2005). In recent years, PEG and its derivatives have been used as metal corrosion inhibitors because of its good thermal stability, chemical stability and recyclability.
Deyab and Abd El-Rehim (2013) used peg with different average molecular weights (mw = 1200, 4,000 and 6,000) as corrosion inhibitor to explore the corrosion inhibition effect of PEG on carbon steel in 1.0 M butyric acid medium. The results show that the corrosion rate of carbon steel in butyric acid decreases with the increase of PEG concentration and molecular weight, and intensifies with the increase of temperature. Peg retards the corrosion of carbon steel by physical adsorption, which follows the Temkin adsorption isotherm. Awad (2013) studied the correlation between the molecular structure of PEG and the corresponding corrosion inhibition rate. Quantum chemical calculation shows that there is a good correlation between the quantum chemical parameters of the studied compound and the corrosion inhibition rate of its corrosion process. The function △E of its reaction activity is related to the corrosion inhibition rate of the inhibitor. With the decrease of △E, the reactivity of the inhibitor to the metal surface increases. Similarly, the higher the adsorption energy, the higher the stability of the formed complex, and the higher the corrosion inhibition rate.
Like other corrosion inhibitors, the corrosion inhibition effect of PEG is also affected by some common surfactants, catalysts, emulsifiers and other additives. Mobin and Khan (2014) studied the adsorption and corrosion inhibition behavior of PEG with sodium dodecylbenzene sulfonate (SDBS) and cetyltrimethylammonium bromide (CTAB) on low carbon steel in 0.1 M H2SO4 solution and 30–60°C. The results show that the addition of a small amount of surfactant can synergistically enhance the corrosion inhibition of PEG. The adsorption process is completely spontaneous and conforms to the Langmuir adsorption isotherm. Hamlaoui et al. (2013) studied the effect of PEG and cerium nitrate solution on galvanized steel. The results show that adding peg to cerium nitrate solution can effectively weaken the hydrogen reduction reaction, reduce the thickness of the coating, reduce the formation of cracks, and then improve the corrosion resistance of the coating. Umoren et al. (2009) studied the effect of halides (KCl, KBr and KI) on the corrosion inhibition of PEG. The results show that PEG can slow down the corrosion of aluminum in alkaline medium, and its corrosion inhibition rate increases with the increase of inhibitor concentration. The adsorption of PEG on aluminum surface conforms to Flory Huggins and Temkin adsorption isotherms. The addition of halides has obvious synergistic effect on the corrosion inhibition rate of PEG, and the order is: I− > Br− > Cl−. El-Lateef and Hany (2016) studied the corrosion inhibition of carbon steel in 0.1 M H2SO4 solution when two kinds of PEG with different molecular weight cooperated with rare earth Ce4+. The results show that the synergistic use of PEG and Ce4+ ions can significantly improve the corrosion inhibition of carbon steel surface when used alone.
Polyethylene glycol has poor performance when used as a metal corrosion inhibitor. It is often used together with other chemical reagents in the form of additives, and can improve the corrosion resistance of the coating by weakening the hydrogen reduction reaction in the process of metal corrosion.
Conductive polymer inhibitor
Conductive polymer (CPS) is a special type of polymer. Because its main chain has extensive π electron delocalization, it shows good conductivity during oxidation and reduction. Because of the electronic properties of semiconductors and the ease of processing of conventional polymers, they are widely used in daily production and life. In addition, because of its large structural units and good coating effect, conductive polymers are also efficient corrosion inhibitors for metal corrosion prevention. The commonly used conductive polymer corrosion inhibitors include polyaniline (PANI), polypyrrole (PPy), polyindole (PIN), polythiophene (PTh) and polyaniline (PPD). Because the conductive polymer coating has good barrier performance, it can effectively inhibit the corrosion diffusion of corrosion medium and firmly adhere to the metal surface (Advincula, 2015; Namsheer and Rout, 2021).
Danaee et al. (2020) studied 2,2′-(2-hydroxyethylimino) bis [N-(α-Corrosion inhibition effect of dimethyl phenylethyl) -n-methylacetamide] on low carbon steel in 1 m HCl solution. The results show that the corrosion inhibitor is mainly adsorption, and its adsorption process conforms to the Langmuir adsorption isotherm. It is a mixed corrosion inhibitor, and its slow-release rate is directly proportional to the corrosion concentration. Ali Fathima Sabirneeza and Subhashini (2013) prepared a new water-soluble conductive polymer poly (vinyl alcohol histidine) composite with persulfate as raw material by free radical condensation method, and explored the corrosion inhibition effect of the material on the corrosion behavior of low carbon steel in 1 M HCl. The results show that when the mass fraction of the composite is 0.6%, the corrosion inhibition rate can reach more than 95%. As a mixed inhibitor, the adsorption of the inhibitor conforms to the Temkin adsorption isotherm. Duan et al. (2022) obtained a new polymer poly [n-alkyl—(4-hydroxybutyl-2-alkynyl) pyridine bromide] by radical polymerization of n-alkyl—(4-hydroxybutyl-2-alkynyl) pyridine bromide under the catalysis of Pd-C catalyst, and then verified its corrosion inhibition effect on × 70 Steel in HCl solution. The results show that the optimum corrosion inhibition concentration of the polymer is 60 ppm, and the increase of acid concentration and soaking time can enhance the adsorption and barrier effect of the polymer.
In addition, Awuzie (2017) found that conductive polymers can improve their conductivity, mechanical flexibility and high thermal stability by doping. Aly et al. (2019a) studied the effect of sodium bentonite on the solubility, thermal stability and corrosion inhibition of CoPm conductive polymer coating. The results show that the corrosion inhibition rate of the blend polymer to low carbon steel in acidic environment is 97%, which is much higher than that of the same copolymer. Shukla et al. (2008) synthesized water-soluble self-doped poly (o-aminobenzoic acid) corrosion inhibitor with different oxidants at different polymerization times, and studied the corrosion inhibition effect of the inhibitor on low carbon steel in 0.5 M HCl. The results show that the inhibitor is mainly in the form of adsorption inhibition. When the concentration of inhibitor is 60 mg/l, the maximum inhibition rate is 92%.
In the process of metal corrosion, some CPS charges will be consumed due to corrosion, and anion exchange will occur to form a passive oxide layer, reducing the adhesion between CPS and metal. Therefore, researchers proposed to use nano inorganic materials in conjunction with CPS to improve the corrosion inhibition ability of metal materials. Aly et al. (2019b) prepared cycloalkanone nano clay CPS composites by in-situ polymerization, and compared them with CPS polymers without nano clay. The results show that CPS modified by cyclohexanone has better shielding and protection ability, and its corrosion inhibition rate is as high as 95.9%, indicating that increasing the molecular weight of the polymer (the larger the molecular weight is, the larger the metal area can be covered) or using modified nano clay can effectively enhance the corrosion inhibition ability of CPS. Elhalawany et al. (2014) prepared a kind of conductive polymer nanoparticles (CPNs) by using micro lotion polymerization technology, and added the prepared CPNs and polymethylaniline (PAns) - polyaniline (PTol) copolymer (CCPNs) dispersed in aqueous medium to the aqueous coating for corrosion performance evaluation. The results show that the composite inhibitor system has stronger barrier effect and is easier to participate in the formation of oxide film. Through the dual redox catalysis of CCPNs, the corrosion resistance of metal surface is significantly improved.
There are many kinds of conductive polymer corrosion inhibitors, which have strong corrosion resistance to corrosive media, good adhesion, and can be used together with similar conductive polymers, but too many doping methods have brought challenges to its mechanism research.
Composite polymer inhibitor
In order to obtain better anticorrosion performance of metal materials, at present, the combination of inhibitors is often used to balance the advantages and disadvantages of each inhibitor and maximize the anticorrosion effect of the coating. Abd El-Ghaffar et al. (2020) used ammonium persulfate as initiator, used toluidine and phenylenediamine monomers to carry out in-situ chemical oxidation polymerization in the presence of barium sulfate to prepare a new intelligent and eco-friendly polymer conductive polymer inhibitor. Based on the synergistic epoxy polyester coating formula, they carried out a salt spray test of soaking in 3.5% NaCl solution for 1,500 h, and obtained good corrosion resistance. Alva et al. (2018) explored the corrosion inhibition effect of GA cooperating with cellulose acetate on the surface of aluminum plate. It was found that in high concentration of strong acid, the water solubility of GA and cellulose acetate was enhanced, which was due to the increase of solution polarity by the polysaccharide components in the two biological corrosion inhibitors. In addition, the two polymers can also hinder the chemical reaction between aluminum and other substituents by forming an organic coating, and the N, O, S, etc. in the two polymers play an important role in reducing the formation of aluminum surface by-products. Chauhan et al. (2018) explored the effect of PEG crosslinked chitosan (Cht-PEG) on the corrosion performance of carbon steel in 1 M sulfamic acid solution. The results show that the adsorption of Cht-PEG on the surface of low carbon steel conforms to the Langmuir isotherm, and the corrosion inhibition rate can reach 93.9% at the optimal concentration of 200ppm. As a mixed corrosion inhibitor with cathode advantages, it can effectively inhibit the anodic and cathodic corrosion processes. Kong et al. (2019) explored the effect of polyaniline (PANI)/chitosan (CTS) on the corrosion properties of Q235 steel in 0.5 M HCl medium. The results show that polyaniline/CTS is essentially a mixed corrosion inhibitor because it can provide N, O, −C = N and other groups. In the corrosion test, the increase of its concentration can effectively delay the cathodic reaction, resulting in the increase of charge transfer resistance, thus delaying the corrosion process of Q235 steel. Sabirneeza et al. (2013) synthesized a new corrosion inhibitor polyvinyl alcohol leucine composite inhibitor (PVAL), and studied the corrosion inhibition effect of PVAL on low carbon steel in 1 M HCl solution. The results show that PVAL is a mixed inhibitor, which exhibits spontaneous adsorption on the surface of low carbon steel. It inhibits the corrosion of low carbon steel by blocking the active sites of metals. When its concentration increases to 0.6%, the inhibition rate can reach more than 95%. Yang et al. (2018) synthesized a new clam shaped adhesive polymer (PHEA-DOPA) containing 3,4-dihydroxyphenylalanine (DOPA) functional group based on polyasparagine derivatives, and explored the corrosion inhibition performance of the polymer on waterborne epoxy coatings. The results show that PHEA-DOPA can effectively delay the corrosion process of the metal solution interface by forming an insoluble DOPA-Fe complex passivation layer on the surface of carbon steel to improve the cross-linking density of the coating.
Conclusion
Through the systematic development of aqueous polymer corrosion inhibitors, it can be seen that in water-soluble polymers, such as chitosan, cellulose, animal and plant proteins and their derivatives have the characteristics of wide source, easy degradation and low cost, but these materials are often used in large amounts and have poor solubility, and will be affected by the pH value of the solution, and the understanding of the mechanism is still not clear; In synthetic polymers, epoxy resin, polyethylene glycol, conductive polymers, etc. have the advantages of low dosage, containing multiple adsorption sites, high corrosion inhibition rate, long action time limit, high temperature resistance, large modification space, etc., but the disadvantages are that it is difficult to analyze the corrosion inhibition mechanism of synthetic polymers, containing certain biological toxicity, and difficult to control the molecular weight; The composite polymer inhibitor effectively takes into account the balance between natural polymers and synthetic polymers, which can not only play a synergistic corrosion inhibition effect, but also improve other properties required by the metal matrix (such as wear, lubrication, hydrophilic or hydrophobic properties, etc.). However, the composition of the composite polymer is miscellaneous, and the analysis of its corrosion inhibition mechanism is more difficult, but this uncertainty provides infinite possibilities for future exploration. It is believed that with the continuous advancement of relevant research work and the development of technology, the corrosion inhibition mechanism of various polymers will become more and more clear. By reasonably controlling the cost of polymer corrosion inhibitor, it will become the mainstream development trend of metal corrosion protection in the future.
Author contributions
ZY investigated and processed the data, pointed out the framework of the paper, made a summary and analysis, and completed the writing of the paper. ZY reviewed the paper and supported the project.
Author Contributions
All authors listed have made a substantial, direct, and intellectual contribution to the work and approved it for publication.
Funding
This work was supported by The Doctoral Fund Project of Chongqing Institute of Industry and Technology (Grant No. 2022G2YBS2K2-12).
Conflict of interest
The authors declare that the research was conducted in the absence of any commercial or financial relationships that could be construed as a potential conflict of interest.
Publisher’s note
All claims expressed in this article are solely those of the authors and do not necessarily represent those of their affiliated organizations, or those of the publisher, the editors and the reviewers. Any product that may be evaluated in this article, or claim that may be made by its manufacturer, is not guaranteed or endorsed by the publisher.
References
Abd El-Ghaffar, M., Abdelwahab, N., Fekry, A., Sanad, M., Sabaa, M., and Soliman, S. (2020). Polyester-epoxy resin/conducting polymer/barium sulfate hybrid composite as a smart eco-friendly anti-corrosive powder coating. Prog. Org. Coatings 144 (7), 105664–105711. doi:10.1016/j.porgcoat.2020.105664
Advincula, R. (2015). “Conducting polymers with superhydrophobic effects as anticorrosion coating,” in Intelligent coatings for corrosion control (Oxford: Butterworth-Heinemann), 409–430. doi:10.1016/B978-0-12-411467-8.00011-8
Ali, B., Ziada, A., and Blunden, G. (2009). Biological effects of gum Arabic: A review of some recent research. Food Chem. Toxicol. 47 (1), 1–8. doi:10.1016/j.fct.2008.07.001
Ali Fathima Sabirneeza, A., and Subhashini, S. (2013). A novel water‐soluble, conducting polymer composite for mild steel acid corrosion inhibition. J. Appl. Polym. Sci. 127 (4), 3084–3092. doi:10.1002/app.37661
Alva, S., Sundari, R., Rahmatullah, A., and Wahyudi, H. (2018). Inhibition effect of Arabic gum and cellulose acetate coatings on aluminium in acid/base media//IOP Conference Series: Materials Science and Engineering. IOP Conf. Ser. Mat. Sci. Eng. 324 (1), 012070–8. doi:10.1088/1757-899X/324/1/012070
Aly, K., Younis, O., Mahross, M., Orabi, E. A., Abdel-Hakim, M., Tsutsumi, O., et al. (2019a). Conducting copolymers nanocomposite coatings with aggregation-controlled luminescence and efficient corrosion inhibition properties. Prog. Org. Coatings 135 (10), 525–535. doi:10.1016/j.porgcoat.2019.06.001
Aly, K., Younis, O., Mahross, M., Tsutsumi, O., Mohamed, M. G., and Sayed, M. M. (2019b). Novel conducting polymeric nanocomposites embedded with nanoclay: synthesis, photoluminescence, and corrosion protection performance. Polym. J. 51 (1), 77–90. doi:10.1038/s41428-018-0119-6
Anyiam, C., Ogbobe, O., Oguzie, E., and Madufor, I. C. (2020). Synergistic study of modified sweet potato starch and KI for corrosion protection of mild steel in acidic media. J. Bio. Tribocorros. 6 (3), 70–10. doi:10.1007/s40735-020-00362-x
Asaad, M., Huseien, G., Baghban, M., Raja, P. B., Fediuk, R., Faridmehr, I., et al. (2021). Gum Arabic nanoparticles as green corrosion inhibitor for reinforced concrete exposed to carbon dioxide environment. Materials 14 (24), 7867–7925. doi:10.3390/ma14247867
Awad, M. K. (2013). Quantum chemical studies and molecular modeling of the effect of polyethylene glycol as corrosion inhibitors of an aluminum surface. Can. J. Chem. 91 (4), 283–291. doi:10.1139/cjc-2012-0354
Awuzie, C. (2017). Conducting polymers. Mater. Today Proc. 4 (4), 5721–5726. doi:10.1016/j.matpr.2017.06.036
Balgude, D., and Sabnis, A. (2012). Sol–gel derived hybrid coatings as an environment friendly surface treatment for corrosion protection of metals and their alloys. J. Solgel. Sci. Technol. 64 (1), 124–134. doi:10.1007/s10971-012-2838-z
Bardal, E., Drugli, J., and Gartland, P. (1993). The behaviour of corrosion resistant steels in seawater. A review. Corros. Sci. 35 (1-4), 257–267. doi:10.1016/0010-938X(93)90157-C
Blanda, G., Brucato, V., Carfì, F., Conoscenti, G., La Carrubba, V., Piazza, S., et al. (2019). Chitosan-coating deposition via galvanic coupling. ACS Biomater. Sci. Eng. 5 (4), 1715–1724. doi:10.1021/acsbiomaterials.8b01548
Burra, P., Zhang, Y., Godzik, A., and Stec, B. (2009). Global distribution of conformational states derived from redundant models in the PDB points to non-uniqueness of the protein structure. Proc. Natl. Acad. Sci. U. S. A. 106 (26), 10505–10510. doi:10.1073/pnas.0812152106
Chauhan, D., Quraishi, M., Sorour, A., Saha, S. K., and Banerjee, P. (2019). Triazole-modified chitosan: A biomacromolecule as a new environmentally benign corrosion inhibitor for carbon steel in a hydrochloric acid solution. RSC Adv. 9 (26), 14990–15003. doi:10.1039/C9RA00986H
Chauhan, D., Srivastava, V., Joshi, P., and Quraishi, M. A. (2018). PEG cross-linked chitosan: A biomacromolecule as corrosion inhibitor for sugar industry. Int. J. Ind. Chem. 9 (4), 363–377. doi:10.1007/s40090-018-0165-0
Chen, J., Spear, S., Huddleston, J., and Rogers, R. D. (2005). Polyethylene glycol and solutions of polyethylene glycol as green reaction media. Green Chem. 7 (2), 64–82. doi:10.1039/B413546F
Chen, L., Shi, Y., and Li, H. (2022). Research progress of plant extract-based green corrosion inhibitors in aggressive media. J. Chongqing Univ. 25 (4), 1–25. doi:10.11835/j.issn.1000-582X.2021.114
Dagdag, O., Berisha, A., Safi, Z., Dagdag, S., Berrani, M., Jodeh, S., et al. (2020). Highly durable macromolecular epoxy resin as anticorrosive coating material for carbon steel in 3% NaCl: Computational supported experimental studies. J. Appl. Polym. Sci. 137 (34), 49003–49012. doi:10.1002/app.49003
Dagdag, O., El Gana, L., Hamed, O., Jodeh, S., and El Harfi, A. (2019). Anticorrosive formulation based of the epoxy resin–polyaminoamide containing zinc phosphate inhibitive pigment applied on sulfo-tartaric anodized AA 7075-T6 in NaCl medium. J. Bio. Tribocorros. 5 (1), 25–29. doi:10.1007/s40735-019-0218-8
Danaee, I., RameshKumar, S., RashvandAvei, M., and Vijayan, M. (2020). Electrochemical and quantum chemical studies on corrosion inhibition performance of 2, 2'-(2-hydroxyethylimino) bis [N-(alphaalpha-dimethylphenethyl)-N-methylacetamide] on mild steel corrosion in 1M HCl solution. Mat. Res. 23 (2), 1–16. doi:10.1590/1980-5373-MR-2018-0610
Dariva, C., and Galio, A. (2014). Corrosion inhibitors–principles, mechanisms and applications. Dev. Corros. Prot. 16 (2), 365–378. doi:10.5772/57255
Deyab, M., and Abd El-Rehim, S. (2013). Influence of polyethylene glycols on the corrosion inhibition of carbon steel in butyric acid solution: weight loss, EIS and theoretical studies. Int. J. Electrochem. Sci. 8 (12), 12613–12627. doi:10.1007/s10008-013-2231-z
Djellab, M., Bentrah, H., Chala, A., and Taoui, H. (2018). Synergistic effect of halide ions and gum Arabic for the corrosion inhibition of API5L X70 pipeline steel in H2SO4. Mater. Corros. 70 (1), 149–160. doi:10.1002/maco.201810203
Duan, M., Wu, G., Gu, T., Jiang, X., Zhao, L., Zhou, L., et al. (2022). Conductive and anticorrosive poly (N‐alkyl‐2‐(4‐hydroxybut‐2‐ynyl) pyridinium bromides): Synthesis and characterization. J. Polym. Sci. 60 (12), 1468–1479. doi:10.1002/pol.20210672
El-Lateef, A., and Hany, M. (2016). Synergistic effect of polyethylene glycols and rare Earth Ce4+ on the corrosion inhibition of carbon steel in sulfuric acid solution: electrochemical, computational, and surface morphology studies. Res. Chem. Intermed. 42 (4), 3219–3240. doi:10.1007/s11164-015-2207-y
Elhalawany, N., Mossad, M., and Zahran, M. (2014). Novel water-based coatings containing some conducting polymers nanoparticles (CPNs) as corrosion inhibitors. Prog. Org. Coatings 77 (3), 725–732. doi:10.1016/j.porgcoat.2013.12.017
Farag, A., Ismail, A., and Migahed, M. (2018). Environmental-friendly shrimp waste protein corrosion inhibitor for carbon steel in 1 M HCl solution. Egypt. J. petroleum 27 (4), 1187–1194. doi:10.1016/j.ejpe.2018.05.001
Farhadian, A., Kashani, S., Rahimi, A., Oguzie, E. E., Javidparvar, A. A., Nwanonenyi, S. C., et al. (2021). Modified hydroxyethyl cellulose as a highly efficient eco-friendly inhibitor for suppression of mild steel corrosion in a 15% HCl solution at elevated temperatures. J. Mol. Liq. 338 (9), 116607–116616. doi:10.1016/j.molliq.2021.116607
Farhadian, A., Varfolomeev, M., Shaabani, A., Nasiri, S., Vakhitov, I., Zaripova, Y. F., et al. (2020). Sulfonated chitosan as green and high cloud point kinetic methane hydrate and corrosion inhibitor: Experimental and theoretical studies. Carbohydr. Polym. 236 (5), 116035–116112. doi:10.1016/j.carbpol.2020.116035
Fathima Sabirneeza, A., Geethanjali, R., and Subhashini, S. (2015). Polymeric corrosion inhibitors for iron and its alloys: A review. Chem. Eng. Commun. 202 (2), 232–244. doi:10.1080/00986445.2014.934448
Grundmeier, G., Schmidt, W., and Stratmann, M. (2000). Corrosion protection by organic coatings: electrochemical mechanism and novel methods of investigation. Electrochimica Acta 45 (15-16), 2515–2533. doi:10.1016/s0013-4686(00)00348-0
Guo, L., Tan, B., Li, W., Li, Q., Zheng, X., and Obot, I. B. (2021). Banana leaves water extracts as inhibitor for X70 steel corrosion in HCl medium. J. Mol. Liq. 327 (11), 114828–114911. doi:10.1016/j.molliq.2020.114828
Guo, L., Tan, J., Kaya, S., Leng, S., Li, Q., and Zhang, F. (2020). Multidimensional insights into the corrosion inhibition of 3, 3-dithiodipropionic acid on Q235 steel in H2SO4 medium: A combined experimental and in silico investigation. J. colloid interface Sci. 570 (6), 116–124. doi:10.1016/j.jcis.2020.03.001
Hamlaoui, Y., Tifouti, L., and Pedraza, F. (2013). Corrosion protection of electro-galvanized steel by ceria-based coatings: effect of polyethylene glycol (PEG) addition. J. Mat. Eng. Perform. 22 (9), 2706–2715. doi:10.1007/s11665-013-0574-3
Hassan, R., and Ibrahim, S. (2021). Performance and efficiency of methyl-cellulose polysaccharide as a green promising inhibitor for inhibition of corrosion of magnesium in acidic solutions. J. Mol. Struct. 1246 (101), 131180–131187. doi:10.1016/j.molstruc.2021.131180
Höhn, S., Virtanen, S., and Boccaccini, A. (2019). Protein adsorption on magnesium and its alloys: A review. Appl. Surf. Sci. 464 (1), 212–219. doi:10.1016/j.apsusc.2018.08.173
Hsissou, R., Benhiba, F., Dagdag, O., El Bouchti, M., Nouneh, K., Assouag, M., et al. (2020). Development and potential performance of prepolymer in corrosion inhibition for carbon steel in 1.0 M HCl: outlooks from experimental and computational investigations. J. colloid interface Sci. 574 (8), 43–60. doi:10.1016/j.jcis.2020.04.022
Hu, Y., Fan, B., and Liu, H. (2020). Corrosion inhibition mechanism of durian peel and stone extract for copper in Sulphuric solution. Corros. Prot. 41 (7), 17–24. doi:10.11973/fsyfh-202007003
Hui, X., Guo, N., and Liu, T. (2020). Slow release mechanism and application progress of cellulose based corrosion inhibitors. Equip. Environ. Eng. 17 (12), 47–53. doi:10.7643/issn.1672-9242.2020.12.008
Jevremović, I., Chen, Y., and Altin, A. (2020). “Mechanisms of inhibitor action,” in Corrosion inhibitors in the oil and gas industry (New Jersey: Wiley).
Jin, F., Li, X., and Park, S. (2015). Synthesis and application of epoxy resins: A review. J. Industrial Eng. Chem. 29 (9), 1–11. doi:10.1016/j.jiec.2015.03.026
Joseph, A., John Mathew, K., and Vandana, S. (2020). Zirconium-doped ceria nanoparticles as anticorrosion pigments in waterborne epoxy–polymer coatings. ACS Appl. Nano Mat. 4 (1), 834–849. doi:10.1021/acsanm.0c03162
Karaxi, E., Kartsonakis, I., and Charitidis, C. (2019). Assessment of self-healing epoxy-based coatings containing microcapsules applied on hot dipped galvanized steel. Front. Mat. 222 (9), 1–17. doi:10.3389/fmats.2019.00222
Kong, P., Feng, H., Chen, N., Lu, Y., Li, S., and Wang, P. (2019). Polyaniline/chitosan as a corrosion inhibitor for mild steel in acidic medium. RSC Adv. 9 (16), 9211–9217. doi:10.1039/C9RA00029A
Lahrour, S., Benmoussat, A., Bouras, B., Mansri, A., Tannouga, L., and Marzorati, S. (2019). Glycerin-grafted starch as corrosion inhibitor of C-Mn steel in 1 M HCl solution. Appl. Sci. 9 (21), 4684–4718. doi:10.3390/app9214684
Li, X., Deng, S., Lin, T., Xie, X., and Du, G. (2020). Cassava starch ternary graft copolymer as a corrosion inhibitor for steel in HCl solution. J. Mater. Res. Technol. 9 (2), 2196–2207. doi:10.1016/j.jmrt.2019.12.050
Ma, Y., Talha, M., Wang, Q., Li, Z., and Lin, Y. (2021). Evaluation of the corrosion behavior of AZ31 magnesium alloy with different protein concentrations. Anti-Corrosion Methods Mater. 69 (1), 47–54. doi:10.1108/ACMM-08-2021-2524
Manimaran, N., Rajendran, S., Manivannan, M., et al. (2013). Corrosion inhibition by carboxymethyl cellulose. Eur. Chem. Bull. 2 (7), 494–498. doi:10.1016/S0956-5663(01)00286-X
Mobin, M., and Khan, M. (2014). Adsorption and corrosion inhibition behavior of polyethylene glycol and surfactants additives on mild steel in H2SO4. J. Mat. Eng. Perform. 23 (1), 222–229. doi:10.1007/s11665-013-0767-9
Musa, A., Mohamad, A., Al-Amiery, A., and Tien, L. T. (2012). Galvanic corrosion of aluminum alloy (Al2024) and copper in 1.0M hydrochloric acid solution. Korean J. Chem. Eng. 29 (6), 818–822. doi:10.1007/s11814-011-0233-z
Namsheer, K., and Rout, C. (2021). Conducting polymers: A comprehensive review on recent advances in synthesis, properties and applications. RSC Adv. 11 (10), 5659–5697. doi:10.1039/d0ra07800j
Nawaz, M., Shakoor, R., Kahraman, R., and Montemor, M. (2021). Cerium oxide loaded with gum Arabic as environmentally friendly anti-corrosion additive for protection of coated steel. Mater. Des. 198 (1), 109361–109412. doi:10.1016/j.matdes.2020.109361
Nwanonenyi, S., Arukalam, I., Obasi, H., Ezeamaku, U. L., Eze, I. O., Chukwujike, I. C., et al. (2017). Corrosion inhibitive behavior and adsorption of millet (Panicum miliaceum) starch on mild steel in hydrochloric acid environment. J. Bio. Tribocorros. 3 (4), 54–11. doi:10.1007/s40735-017-0115-y
Nwanonenyi, S., Obasi, H., and Eze, I. O. (2019). Hydroxypropyl cellulose as an efficient corrosion inhibitor for aluminium in acidic environments: Experimental and theoretical approach. Chem. Afr. 2 (3), 471–482. doi:10.1007/s42250-019-00062-1
Ochoa, N., Bello, M., Sancristóbal, J., Balsamo, V., Albornoz, A., and Brito, J. L. (2013). Modified cassava starches as potential corrosion inhibitors for sustainable development. Mat. Res. 16, 1209–1219. doi:10.1590/S1516-14392013005000126
Palumbo, G., Kollbek, K., Wirecka, R., Bernasik, A., and Gorny, M. (2020). Effect of CO2 partial pressure on the corrosion inhibition of N80 carbon steel by gum Arabic in a CO2-water saline environment for shale oil and gas industry. Materials 13 (19), 4245–4324. doi:10.3390/ma13194245
Pludek, V. (1977). Design and corrosion control. London: The Macmillan Press. ISBN-13: 978-1349027897.
Rabizadeh, T., and Asl, S. (2019). Casein as a natural protein to inhibit the corrosion of mild steel in HCl solution. J. Mol. Liq. 276 (2), 694–704. doi:10.1016/j.molliq.2018.11.162
Rahman, M., Islam, M., Khan, M., Ong, H. R., and Uddin, M. T. (2019). IBA-modified gypsum-containing epoxy resin coating for rebar: corrosion performance and bonding characteristics. Int. J. Plast. Technol. 23 (1), 20–28. doi:10.1007/s12588-019-09238-3
Rajeswari, V., Kesavan, D., Gopiraman, M., and Viswanathamurthi, P. (2013). Physicochemical studies of glucose, gellan gum, and hydroxypropyl cellulose—inhibition of cast iron corrosion. Carbohydr. Polym. 95 (1), 288–294. doi:10.1016/j.carbpol.2013.02.069
Sabirneeza, A., Subhashini, S., and Rajalakshmi, R. (2013). Water soluble conducting polymer composite of polyvinyl alcohol and leucine: An effective acid corrosion inhibitor for mild steel. Mater. Corros. 64 (1), 74–82. doi:10.1002/maco.201106096
Sharma, N., Sharma, S., Sharma, S. K., Mahajan, R. L., and Mehta, R. (2022). Evaluation of corrosion inhibition capability of graphene modified epoxy coatings on reinforcing bars in concrete. Constr. Build. Mater. 322 (3), 126495–126521. doi:10.1016/j.conbuildmat.2022.126495
Sheikh, M., Kamal, K., Rafique, F., Sabir, S., Zaheer, H., and Khan, K. (2021). Corrosion detection and severity level prediction using acoustic emission and machine learning based approach. Ain Shams Eng. J. 12 (4), 3891–3903. doi:10.1016/j.asej.2021.03.024
Shen, C., Alvarez, V., Koenig, J., and Luo, J. L. (2019). Gum Arabic as corrosion inhibitor in the oil industry: experimental and theoretical studies. Corros. Eng. Sci. Technol. 2019 (4), 444–454. doi:10.1080/1478422X.2019.1613780
Shukla, S., Quraishi, M., and Prakash, R. (2008). A self-doped conducting polymer “polyanthranilic acid”: An efficient corrosion inhibitor for mild steel in acidic solution. Corros. Sci. 50 (10), 2867–2872. doi:10.1016/j.corsci.2008.07.025
Sobhi, M., and Eid, S. (2018). Chemical, electrochemical and morphology studies on methyl hydroxyethyl cellulose as green inhibitor for corrosion of copper in hydrochloric acid solutions. Prot. Met. Phys. Chem. Surf. 54 (5), 893–898. doi:10.1134/S2070205118050210
Sushmitha, Y., and Rao, P. (2019). Material conservation and surface coating enhancement with starch-pectin biopolymer blend: A way towards green. Surfaces Interfaces 16 (9), 67–75. doi:10.1016/j.surfin.2019.04.011
Suyanto, H., Ratih, R., and Leo, S. (2015). Application chitosan derivatives as inhibitor corrosion on steel with fluidization method. J. Chem. Pharm. Res. 7 (2), 260–267. Available at: http://repository.unair.ac.id/id/eprint/49764.
Talha, M., Ma, Y., Kumar, P., Lin, Y., and Singh, A. (2019). Role of protein adsorption in the bio corrosion of metallic implants–A review. Colloids Surfaces B Biointerfaces 176 (4), 494–506. doi:10.1016/j.colsurfb.2019.01.038
Tan, B., Zhang, S., Cao, X., Fu, A., Guo, L., Marzouki, R., et al. (2022). Insight into the anti-corrosion performance of two food flavors as eco-friendly and ultra-high performance inhibitors for copper in sulfuric acid medium. J. Colloid Interface Sci. 609 (11), 838–851. doi:10.1016/j.jcis.2021.11.085
Tan, B., Zhang, S., Qiang, Y., Li, W., Li, H., Feng, L., et al. (2020). Experimental and theoretical studies on the inhibition properties of three diphenyl disulfide derivatives on copper corrosion in acid medium. J. Mol. Liq. 298 (1), 111975–112013. doi:10.1016/j.molliq.2019.111975
Umoren, S., Ebenso, E., and Ogbobe, O. (2009). Synergistic effect of halide ions and polyethylene glycol on the corrosion inhibition of aluminium in alkaline medium. J. Appl. Polym. Sci. 113 (6), 3533–3543. doi:10.1002/app.30258
Verma, C., Quraishi, M., and Rhee, K. (2022). Aqueous phase polymeric corrosion inhibitors: Recent advancements and future opportunities. J. Mol. Liq. 348 (2), 118387–118422. doi:10.1016/j.molliq.2021.118387
Vijayan, P., and Al-Maadeed, M. (2019). Self-repairing composites for corrosion protection: A review on recent strategies and evaluation methods. Materials 12 (17), 2754–2817. doi:10.3390/ma12172754
Wu, W., Chen, T., Du, H., Li, D., and Liu, J. (2016). Carboxymethyl starch as corrosion inhibitor for mild steel. Emerg. Mater. Res. 5 (2), 277–283. doi:10.1680/jemmr.15.00037
Yang, M., Wu, J., Fang, D., Li, B., and Yang, Y. (2018). Corrosion protection of waterborne epoxy coatings containing mussel-inspired adhesive polymers based on polyaspartamide derivatives on carbon steel. J. Mat. Sci. Technol. 34 (12), 2464–2471. doi:10.1016/j.jmst.2018.05.009
Zeng, J., Chen, H., Li, S. L., and Wang, Y. Z. (2012). Chitin whiskers: An overview. Biomacromolecules 025 (03), 1–11. doi:10.1021/bm201564a
Zhang, Z., Ba, H., and Wu, Z. (2019). Sustainable corrosion inhibitor for steel in simulated concrete pore solution by maize gluten meal extract: Electrochemical and adsorption behavior studies. Constr. Build. Mater. 227 (12), 117080. doi:10.1016/j.conbuildmat.2019.117080
Keywords: corrosion, inhibitor, polymer, mechanism, review
Citation: Yihang Z (2022) Application of water-soluble polymer inhibitor in metal corrosion protection: Progress and challenges. Front. Energy Res. 10:997107. doi: 10.3389/fenrg.2022.997107
Received: 18 July 2022; Accepted: 29 August 2022;
Published: 20 September 2022.
Edited by:
Zhiqiang Geng, Beijing University of Chemical Technology, ChinaReviewed by:
Lei Guo, Tongren University, ChinaCopyright © 2022 Yihang. This is an open-access article distributed under the terms of the Creative Commons Attribution License (CC BY). The use, distribution or reproduction in other forums is permitted, provided the original author(s) and the copyright owner(s) are credited and that the original publication in this journal is cited, in accordance with accepted academic practice. No use, distribution or reproduction is permitted which does not comply with these terms.
*Correspondence: Zhang Yihang, THVja3l6aGFuZ3loQGZveG1haWwuY29t