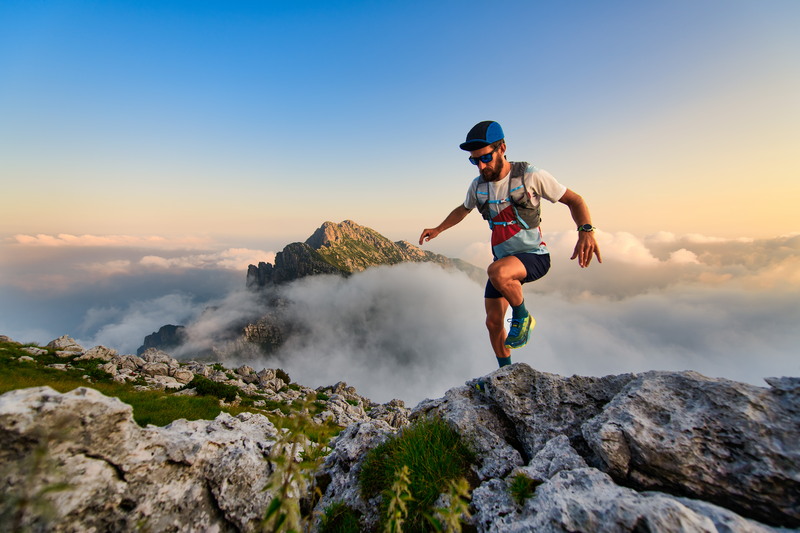
95% of researchers rate our articles as excellent or good
Learn more about the work of our research integrity team to safeguard the quality of each article we publish.
Find out more
EDITORIAL article
Front. Energy Res. , 26 September 2022
Sec. Process and Energy Systems Engineering
Volume 10 - 2022 | https://doi.org/10.3389/fenrg.2022.971870
This article is part of the Research Topic Design, Simulation and Optimization of Hydraulic Machinery View all 25 articles
Editorial on the Research Topic
Design, simulation and optimization of hydraulic machinery
With the increasing pressure of energy crisis and carbon emission, the energy-saving technology of industrial processes has attracted worldwide attention. Hydraulic machinery and its systems are the key components for the sustainable development of engineering, energy transformation in hydraulic systems, water resources, and chemical industry including various transport of liquids or mixtures. The growing demands for the increase of processes operation efficiency have encouraged and indicated the development and implementation of the optimization at the design stages for pumps and pump systems based on mathematical and physical models, advanced numerical simulation, or data-driven techniques.Recently, an increasing number of papers have discussed the design and optimization for the improvement of pumps, turbines, valves, and other flow components. Many new theories and methods have been proposed and applied to improve hydraulic performance. For more efficient utilization of hydraulic machinery, it is important to collect up-to-date information on this topic.
In the first article, Li et al. simplified the reactor primary circuit system of HPR1000. Meanwhile, the RCP shutdown accident in a single circuit of the reactor is numerically simulated. Results show that the pressure in the pipeline system has changed greatly compared. The torque drops sharply, and then rises slowly to zero. The pressure at the inlet and outlet of the impeller changes dramatically which leads to the change of blade load. The pressure and velocity in the guide vane continue to decrease.
Based on performance test and Pumplinx simulation, Chao et al. investigated the effect of blade inlet width on cavitation performance. The results show that the method of twisting the centrifugal impeller of the suspended forward-extended blade shows a significant effect in preventing cavitation performance under such working conditions of high speed and negative pressure. Its application in aerospace power systems can significantly improve the cavitation performance.
The third article (Liu et al.) studied the energy loss of bi-directional hydraulic machinery under cavitation conditions, they used high-speed photography combined with six-axis force and torque sensors to collect cavitating flow images and lift signals of S-shaped hydrofoils simultaneously in a cavitation tunnel. The fast Fourier analysis reveals that the fluctuations of the lift signals under cloud cavitation are significantly higher than those under non-cavitation, and the main frequencies of the lift signals under cloud cavitation were all twice the frequency of the cloud cavitation shedding.
The article by Xu et al. proposed a new hard hose traveler with the function of electric drive and self-propelled. A calculation model for the dynamic change of the pulling force and energy consumption of the reel and tube operation is proposed in this study. The difference between the calculated and the measured values of the total winding length of each tube layer was not more than 0.4 m, with the deviation rate being approximately equal to 0.5%. This investigation can help solve the problems of higher energy consumption and lower intelligence of traditional hard hose travelers.
Tian et al. summarized the scientific research results of submersible mixer in recent years from four aspects: structure and energy characteristics of submersible mixer, numerical simulation calculation method, flow field characteristics, and factors affecting the flow field characteristics. Few experimental studies are conducted, and mostly numerical calculations are based on clear water as the medium. Many factors affect the mixing effect of a submersible mixer, such as installation factors and impeller design parameters. Meanwhile, the development and trends of submersible mixer technology are prospected, and the future directions of further research are proposed.
Chen et al. used time-resolved particle image velocimetry (TR-PIV) measurements to investigate the flow structures in the impeller passage under different flow rates. Through the study of the first few proper orthogonal decomposition (POD) modes of the flow field, the coherent flow structures under several flow rates were revealed, consequently, the flow fields were reconstructed by the POD modes. The flow structures that were reflected by the several modes change as the decrease of flow rate, especially, at the extreme part-load condition, not only the shapes of the flow structures changed, but also the flow direction is reversed. This indicates that the generation mechanism of turbulent kinetic energy in the flow passage changed at the extreme part-load conditions.
Lin et al. studied the flow characteristics of the centrifugal pump with different offset angles of inlet guide vanes (IGVs). In terms of external characteristics, the pump with 25°IGVs has the best head and efficiency improvement. Under three small operating points, the pump with 25°IGVs increased the head by 2.11, 0.95, and 0.73% and the efficiency by 2.51, 1.67, and 1.25%, respectively, compared with the pump with 0°IGVs. The research in this paper contributes to the performance improvement of centrifugal pumps operating at low flow conditions.
Meng et al. adopts the method of experimental and numerical simulation in the pump and studies the variation of the vibration characteristics in the operation process to improve the stability of the pump. The vibration characteristics of the pumps have been significantly improved by adding special trash barriers. In the experiment, the cavitation did occur in the actual operation process. This is the main reason that causes the centrifugal pump performance and pump flow to drop.
The characteristic of steady-state flow force on the cone valve was investigated by Liu et al. the geometric parameters and operating conditions in the steady-state flow force were optimized by the orthogonal test-optimization method. The results show that the greater the pressure differential is, the greater the steady-state flow force is. The steady-state flow force does not increase linearly, but increases first and then decreases with the increase of the opening. The study will lay the foundation to precise axial flow force prediction and reference for design optimization of the valve.
The article by Yan et al. regarded the three fish-type leading-edge structures of mackerel, sturgeon and small yellow croaker as the research objects and use high-precision non-contact 3D scanners to establish three bionic hydrofoils. They used large eddy simulation to simulate the transient cavitating flow of hydrofoils numerically. The numerical simulation results are in good agreement with the experimental results. This study revealed the mechanism of the change in the hydrofoil leading-edge structure in transient cavitating flow and provides a reference for the subsequent optimal design of hydraulic machinery blades.
The transient flow in a new type of dishwasher pump is investigated numerically by Ning et al. The simulation results agree well with the experiment. Three schemes, 0 rpm/30 rpm/60 rpm, of volute speeds are investigated. After comparing the three schemes with respect to the radial force, the shape of the vector distribution is most regular for the 30 rpm scheme, which indicates that the stability of the pump is the highest. This paper can be used to improve both the control and selection of volute speeds.
The hydraulic characteristics of vertical axial flow pump devices with different guide vane inlet angles were studied by Xu et al. using computational fluid dynamics (CFD) and model test methods. The results showed that the pump device efficiency under low-head and large-discharge conditions was improved when the guide vane inlet angle was rotated in the clockwise direction. When the operational conditions of the pump device deviate from its high-efficiency zone, the application of these results could improve its hydraulic performance, which is of great significance to the design and application of low-head pump devices.
Yang et al. fabricated the prototypes of conical tube valveless piezoelectric pump and hyperbolic tubes valveless piezoelectric pump. The size and position of entropy production of the hyperbolic tube and the conical tube were numerically calculated based on entropy production theory. The results show that the entropy production rate of the hyperbolic tube was significantly lower than that of the conical tube, which is consistent with the experimental results. This research provided a new design and research method for improving the output performance of the valveless piezoelectric pump in the future.
Xie et al. established a mathematical model of damping characteristics of the valve-controlled damping adjustable damper and designed the experiment of the damping characteristics of the compression stroke and the recovery stroke. Through simulation and experiment, the accuracy of the mathematical model was verified, and the damping contribution rate of different key parameters under different excitation speeds was analyzed. The research results can screen out the key parameters, improve the development efficiency of the damper, and provide guidance for the damper design and optimization.
Formed with a low-specific-speed centrifugal pump as the study object, unsteady flow calculation and fluid-structure interaction calculation were performed by Jia et al. on centrifugal pumps with different wear-ring clearances. The effect of the incident angle of the wear-ring clearance on the distribution of pressure pulsation and vibration performance of centrifugal pump was analyzed. The results showed that the improved efflux angle of the wear-ring clearance could effectively weaken the impact disturbance of the leakage flow in the wear-ring clearance to the main flow at the inlet. Meanwhile, the efficiency of the centrifugal pump was improved, and the vibration amplitude and vibration energy of the pump were also reduced.
The article by Yu et al. proposed a numerical analysis method based on the computer simulation and the Monte Carlo (MC) method. First, the unit’s life simulation values were simulated using the MC method. Next, the CEMS life simulation value can be obtained based on the CEMS reliability model. Then, simulation data were analyzed, and the distribution of the CEMS life was deduced. The goodness-of-fit test, point estimation and confidence interval of the parameters, and reliability measure were estimated. Finally, as a test example of the wind turbine, the practicability and effectiveness of the method proposed in this paper were verified.
Zhao et al. studied the effect of adding non-connected forms of tiny blades with different parameters of radial position, width, and length to the shroud of the impeller on the cavitation performance of a centrifugal pump. A modified SST k-ω turbulence model combined with the Zwart-Gerber-Belamri cavitation model is used for numerical simulation of the model pump. The results show that the numerical prediction of the original pump agrees well with the experimental results. The existence of tiny blades reduces the overall pressure pulsation main frequency amplitude during pump operation, making its operation more stable.
Jia et al. performed external characteristics, dynamic pressure, and vibration tests on the closed impeller model, semi-open type impeller model, and open impeller model to study the influence of the impeller structure on the operational stability of the pump. According to the research findings, the external characteristic curves and the pressure pulsation in the casing tongue area of the three impellers enjoyed the poorest stability can be observed in the open impeller, while the enclosed impeller has the best stability. In addition, the optimum stability of rotor vibration can be observed in the closed impeller, semi-open impeller, and open impeller with similar stability of rotor vibration.
Xi et al. selected four commonly used operating conditions with opening angles to perform simulation calculations on the flow pattern of the water behind the valves at different flow rates. The flow pattern of the water flow is analyzed by three indicators: the streamline of the water flow, the uniformity of the flow velocity, and the head loss in the culvert. The result shows that the larger the opening angle of the flap valve, the less the head loss of the water flow in the outlet culvert, and the flow pattern of the water flow in the culvert gradually becomes better.
Chang et al. employed the Population Balance Model (PBM) to investigate the influence of different air voids and flow conditions on the performance self-priming centrifugal pumps. The result shows that the frequency of bubble coalescence at the shroud is higher. Meanwhile, the increment of flow conditions has a significant effect on reducing the pressure pulsation of the gas-liquid two-phase flow, while the improvement of the air voids destroys the instability and asymmetry of the internal flow of the two-phase flow. Therefore, this article can provide a certain theoretical reference for the study of air-liquid two-phase flow characteristics of self-priming centrifugal pumps.
Zhang et al. use a high-speed camera to visualize the flow field in a rotational hydrodynamic cavitation reactor (RHCR) in a closed cycle test rig, and the numerical simulation is carried out based on the RNG k-ε turbulence model and the Zwart-Gerber-Belamri (ZGB) cavitation model. Influence of hole diameter, hole height and hole cone bottom length on performance of RHCR are comprehensively investigated. The results show that the numerical results are in good agreement with the experimental data, which verifies the accuracy and reliability of the numerical method.
Jinwei et al. analyzes the jet characteristics of the jet mechanism with different openings (20, 40, 60, 80, 100%) under 4.8% eccentricity to study the effect of jet needle eccentricity on the jet, and verify the reliability of the research method. Then the focus is on the jet characteristics of the jet mechanism at different eccentricities (0, 1, 2.1, 4.8, 8, and 14%) at 40% opening. The results show that as the eccentricity of the nozzle increases, the jet appears to be asymmetrical. The eccentricity of the water jet increases with the increase of the eccentricity of the needle; the efficiency of the injection mechanism gradually decreases, and the energy loss gradually increases.
Li et al. analyzed the internal flow field and particle motion law of a two-stage deep-sea lifting pump at different rotational speeds Through discrete element method-computational fluid dynamics. In addition, the physical phenomena, such as flow field velocity, secondary flow, and particle flow, were studied. The relationship between the rotational speed of the lifting pump and solid–liquid two-phase flow was investigated. An experiment on the hydraulic performance of the lift pump showed that the resulting lift and efficiency were consistent with the numerical simulation data.
Zhou et al. introduce three conventional unit startup processes. Combined with the optimal impulse control strategy, an optimized unit startup method is proposed. Though the CFD simulation and the dynamic stress tests, the equivalent stress characteristics and the peak value of the dynamic and static stresses of the blade under different startup processes is obtained. The validity of the model analysis is proved by the comparison between the simulation calculation and the measured results, and the effectiveness of the startup control strategy is proved. The optimization method of the startup process proposed can provide a basis for long-term stable operation of the hydropower unit.
In conclusion, this Research Topic provides an overview of the design and optimization for the improvement of pumps, turbines, valves, and other flow components. Many new theories and methods have been proposed and applied to improve hydraulic performance under this Research Topic through numerical simulations and experimental studies. We hope readers can find from this Research Topic some useful references for better understanding the research status of design, simulation and optimization of hydraulic machinery. Further development of new energy-saving technologies for hydraulic machinery is an inevitable trend for future industry.
All authors listed have made a substantial, direct, and intellectual contribution to the work and approved it for publication.
The authors declare that the research was conducted in the absence of any commercial or financial relationships that could be construed as a potential conflict of interest.
All claims expressed in this article are solely those of the authors and do not necessarily represent those of their affiliated organizations, or those of the publisher, the editors and the reviewers. Any product that may be evaluated in this article, or claim that may be made by its manufacturer, is not guaranteed or endorsed by the publisher.
Keywords: energy characteristics, energy conversion, hydraulic losses, optimal design, numerical simulation, fluid control, fault diagnosis
Citation: Zhou L, Kim J-H, Tan L and Li X (2022) Editorial: Design, simulation and optimization of hydraulic machinery. Front. Energy Res. 10:971870. doi: 10.3389/fenrg.2022.971870
Received: 17 June 2022; Accepted: 08 September 2022;
Published: 26 September 2022.
Edited and reviewed by:
Francois M. A. Marechal, Swiss Federal Institute of Technology Lausanne, SwitzerlandCopyright © 2022 Zhou, Kim, Tan and Li. This is an open-access article distributed under the terms of the Creative Commons Attribution License (CC BY). The use, distribution or reproduction in other forums is permitted, provided the original author(s) and the copyright owner(s) are credited and that the original publication in this journal is cited, in accordance with accepted academic practice. No use, distribution or reproduction is permitted which does not comply with these terms.
*Correspondence: Ling Zhou, bGluZ3pob3VAdWpzLmVkdS5jbg==
Disclaimer: All claims expressed in this article are solely those of the authors and do not necessarily represent those of their affiliated organizations, or those of the publisher, the editors and the reviewers. Any product that may be evaluated in this article or claim that may be made by its manufacturer is not guaranteed or endorsed by the publisher.
Research integrity at Frontiers
Learn more about the work of our research integrity team to safeguard the quality of each article we publish.