- Chemical and Petroleum Engineering, Schulich school of Engineering, University of Calgary, Calgary, AB, Canada
The decreasing abundance of conventional energy resources of nature, such as crude oil, natural gas, and coal, is putting forward the issues of energy shortcoming for the future. With a sentiment of this, most researchers are now directing either on non-conventional resources that already prevail or invent it. The most promising non-conventional energy resource is the hydrogen energy, which can be used in fuel cell to get electricity. Therefore, a number of researchers are putting a light on developing the most efficient and affordable fuel cell. This review is mainly focused on the developments of proton exchange membranes (PEMs) in two parts as low and high temperature PEMs for proton exchange membrane fuel cell (PEMFC) and based on that some outperformed PEMs are mentioned in the respective tables. Most of the energy and automobile industries are concentrating to apply PEMFCs for power generation and to apply in vehicles. The cost of PEMFCs is higher due to the manufacturing cost of PEM. Therefore, research works in PEMs are now in trend to reduce the cost, to improve efficiency, and to withstand particular operating conditions. In this review article, recent developments in PEM by number of researchers and the importance of it in near future have been elicited.
Introduction
Energy is the essential need in this modern world. Every sector requires energy to get growth rapidly. There are several energy sources available today. Energy sources are classified into two main categories such as renewable and non-renewable. The renewable energy source consists solar energy, wind energy, hydrothermal energy, geothermal energy, and hydrogen energy, and the non-renewable energy resources are from coal, oil, natural gas, and nuclear. In this day and age, most of the sectors prefer renewable energy sources to meet the world’s requirements due to uncertain quantity of non-renewable energy sources. Currently, hydrogen energy is in trend because of its zero emission rate, higher efficiency, more flexibility, less noise, and compact structure. The history of today’s all types of fuel cells has come a long way, which is about two centuries, starting from the 18th century with Alessandro Volta’s Voltaic Pile to Francis Thomas Bacon’s Alkaline Fuel Cell (Nicholsan and Cruickshank, 1800; Williams, 1994). During that time and then, a number of other renowned scientists also had contributed such as Sir William Grove, Ludwig Mond, Carl Langer, Charles Wright, C. Thompson, Friedrich Wilhelm Ostwald, William W. Jacques, E. Baur, H. Ehrenberg, J. Broers, and J. Ketelaar (Grove, 1839; Grove, 1842; Grove, 1874; Appleby, 1990; Hoogers, 2003; Andujar and Segura, 2009; Kragh, 2015). Oil shortage in near future for transportation can be possibly dealt in two ways. The first one is by changing conventional fuel to regenerative fuel or by enhancing the efficiency of conventional fuel; the second way is by boosting current engine technology (Alaswad et al., 2016). Today, all kinds of fuel cells are available with the features of different power capacity, compactness, higher durability, etc. There are many fuel cells available such as solid oxide fuel cell (SOFC), phosphoric acid fuel cell (PAFC), alkaline fuel cell (AFC), molten carbonate fuel cell (MCFC), microbial fuel cell (MFC), and proton exchange membrane fuel cell (PEMFC). Among all of these, PEMFC is the most attractive fuel cell because of its enhancing developments in recent years as shown in Figure 1. In addition to this, strong points of this fuel cell are lightweight, high efficiency (>60%), low operating temperature (80°C), zero-emission of greenhouse gases (CO or CO2), the byproduct of the reaction is environmentally free (H2O or water), and it is suitable for both heavy- and light-duty operations. As shown in Figure 2, PEMFC is mainly composed of end plates, current collectors, bipolar plates (BP), gaskets, gas diffusion layers (GDL), catalyst, and membrane. End plates establish the strength to maintain the structure of fuel cell and prevent leakage of gases to the environment; it is constructed with unique flow channels such as single serpentine, double serpentine, and four serpentine (Boddu et al., 2009). Current collector collects the electricity and transmits from the fuel cell to the outer side. Bipolar plate enables to connect one membrane electrode assembly (MEA) to another to increase voltage, and it discharges water. Gaskets are generally made of rubbery material, and it is used to avoid leakage of reactant gases within the fuel cell. MEA is the major component of PEMFC, and the fabrication is challenging.
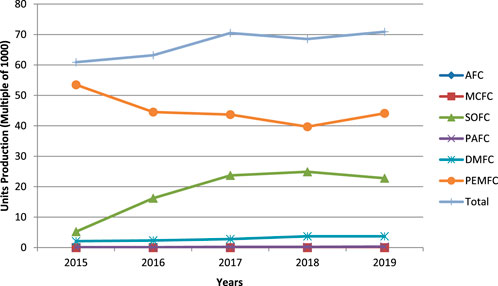
FIGURE 1. Yearly fuel cell’s production (1000 units) by type (E4tech, 2019).
For MEA, there are ample of fabrication methods that are available such as catalyst-coated membrane (CCM), catalyst-coated substrate (CCS), and catalyst-coated electrode (CCE). From these methods, CCE is the most effective and efficient method compared to others as per recent the article by Bhosale et al. (2020). However, Shahgaldi et al. (2018) performed an experiment on every MEA manufacturing method and showed that the CCM method is showing high performance. In addition, CCM is the overall best method, which is supported by many researchers as per a review by Huah et al. (2020). MEA is divided in three parts. First, the gas diffusion layer mainly made of carbon paper, which is covered with polytetra fluoro ethylene (PTFE); both reactant gases diffuse on its pores, and then they flow to catalyst layer. In addition to this, it also maintains water retention and water release to maintain membrane working efficiently. Second, fine nano particles of platinum (Pt) catalyst are uniformly dispersed on both the anode and cathode sides of either membrane or GDL; catalyst ionizes hydrogen ion (H+) from hydrogen gas and oxygen ion (O2-) from oxygen gas. Last, membrane is the heart and costliest part of the fuel cell. The protons (H+) which are generated by the catalyst layer flow through this membrane from one side to another and form water as a byproduct and as a product that produces electricity through the outer circuit. Therefore, it is a passage for these ions. As the interest of people in fuel cell increases, the research, development, and market size also increase. According to the international newsletter, the market value of the fuel cell industries will be $24.8 billion by 2025 (Degnan, 2018). Today, several firms such as Bloom Energy, Ballard Power, Posco Energy, Plug Power, SFC Energy, Hydrogenics, and FuelCell Energy are manufacturing different types of fuel cells for power plants, commercialization, and automobile applications. Automobile companies such as General Motors, Toyota, Tesla, Honda, Ford, Mazda, Hyundai, Fiat, and Mercedes are manufacturing fuel cell cars, trucks, and buses for transportation (Sharaf and Orhan, 2014); the world’s first fuel-cell car Electrovan was developed by General Motors for the United States president John F. Kennedy in 1966 (Barret, 2016).
Several pieces of research and review articles have been published in the past few years. Song et al. (E4tech Ltd, 2019) published a review on developments of materials, fabrication, and applications of PEMFC in the past few years along with a comparison with each other. Devanathan (2008) elicited the developments in the proton exchange membrane in recent years with its thorough chemistry. Polymer type membrane is installed in the fuel cell as an electrolyte. There are some limitations for PEMFC, first it cannot work efficiently above 80°C because high operating temperature creates over humidification and it condenses inside the fuel cell; second, CO tolerance reduces as the operating temperature decreases (Zhang, 2012); third, the cost of the whole assembly is higher than the other fuel cells as the PEM is the costliest part; fourth, PEMFC engine start-up under cold condition such as −20°C to -5°C can result in power degradation (Lin et al., 2019). It can be avoided using antifreezing agent such as methanol, but residual methanol in the stack can result in performance degradation (Knorr et al., 2019). Mostly, the Nafion membrane is used, which was made by DuPont, and it is costly. Therefore, many researchers are focusing on the development of PEMFC and reduction of cost of PEM by modifying it.
Based on the current scenario of carbon dioxide emission from vehicles, several countries’ governments have prioritized the initiatives to develop a carbon-free environment by giving preference to fuel cell electric vehicles (FCEVs). This list of countries includes European countries, United States, Canada, Japan, South Korea, and China. These countries are the major manufacturers of the fuel cells for stationary use, transportation, and power plants. Most of the fuel cell manufacturers are focusing on developing PEMFC for vehicles such as Ballard Power System, Nuvera Fuel Cells, SFC Energy, Altergy Systems, Ceres Power, and Doosan. However, the cost of manufacturing PEMFC is extravagant due to its proton exchange membrane’s cost, and it directly impacts the cost of its applications. Every fuel cell’s developers are focusing on to modify the existing PEM or invent a new one to reduce the price. According to a report of the Department of Energy (DOE), United States set targets for fuel cell developments for the future to apply at automotive applications. The mission of this organization is to meet the requirements of the United States for innovation in vehicles and energy alternatives. Here, some of the targets and current status of the fuel cell characteristics are described in Table 1 (Drive, 2013).
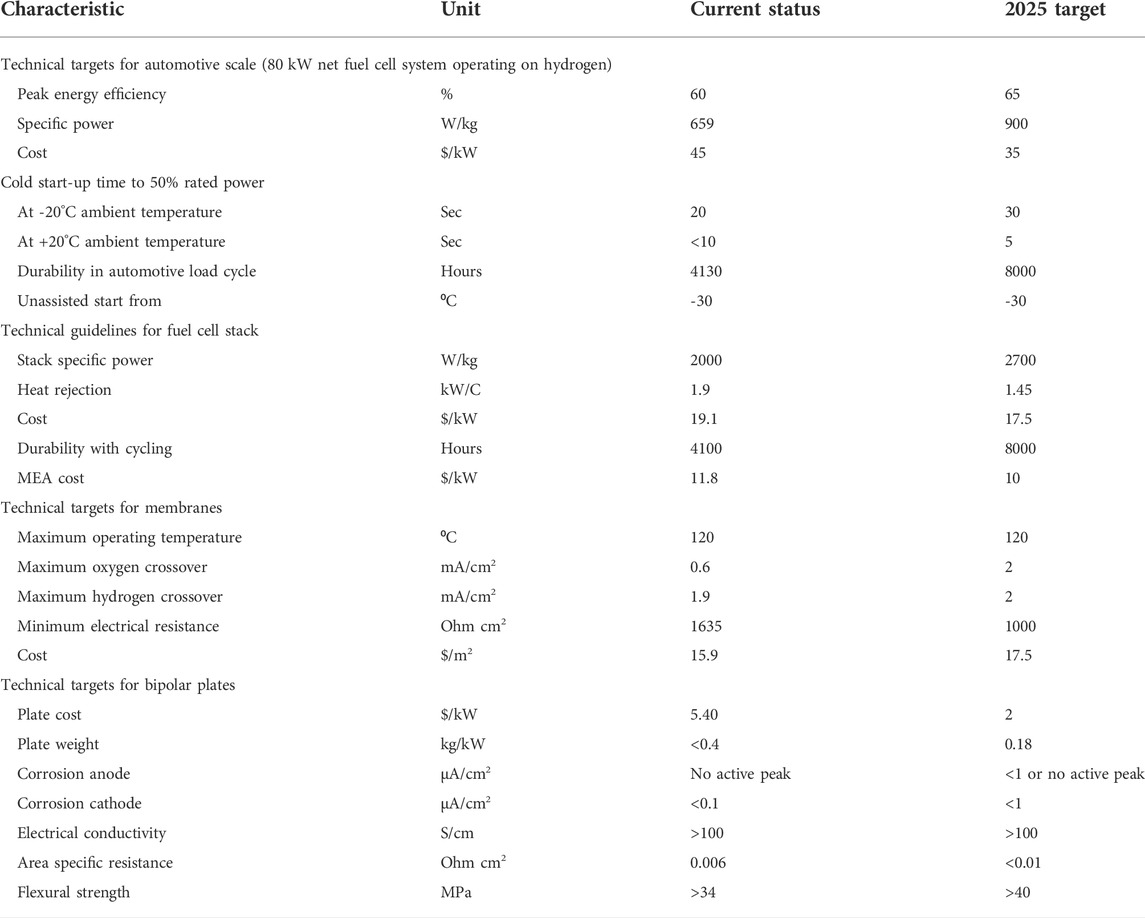
TABLE 1. Targets and current status of fuel cell characteristics as per DOE, United States (Drive U, 2013).
Based on the fuel cell industry review 2019 by E4tech Ltd (Song, 2019), the usage of fuel cells is dominating in stationary category and gradually increasing in the transportation field year by year as shown in Figure 3. Apart from the usage of fuel cell in the transportation field, the power generation capacity in it is also steeply increasing as shown in Figure 4. The most increasing fact in it is the production and power generation capacity of PEMFC are the highest. Because of these reasons, PEMFC has broad scope in the future.
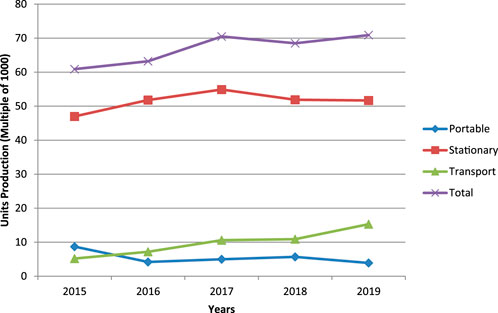
FIGURE 3. Yearly fuel cell’s production (1000 units) by application (E4tech, 2019).
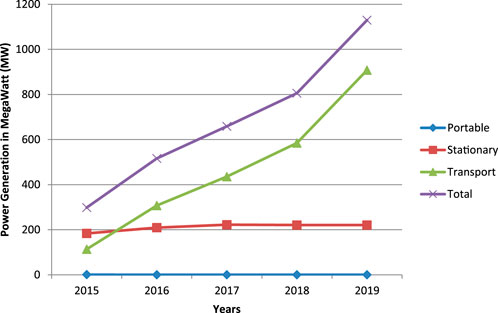
FIGURE 4. Yearly power generation in megawatts (MW) by application (E4tech, 2019).
U.S. DRIVE fuel cell tech team’s goal is to make a direct hydrogen fuel cell power system for the application of transportation with 8000 h durability and mass production at cost of $35/kW by 2025 (Trabia et al., 2016). On the other hand, the fuel cell stack developed by Imperial college of London declared their cost would be $26/kW (Costamagna and Srinivasan, 2001).
Recent developments in proton exchange membranes
The most common proton exchange membrane for fuel cells is the perfluoro sulfonic acid (PFSA) membrane, and it is mainly known as Nafion, which was invented by DuPont. It is also one of the costliest parts of membrane electrode assembly (MEA). Therefore, many researchers are focusing on reducing their costs and to increase efficiency.
Most common catalyst for PEM is Pt, and it is also the costliest and rarest element on earth. Therefore, the usage of Pt should be carried out more carefully and more efficiently. The most important reaction in PEMFC is the oxygen reduction reaction (ORR), and it depends on Pt catalyst. Therefore, if the Pt loading increases then ORR rate increases and gives more power output; if there is low loading of Pt then power output will decrease. However, number of studies have been conducted, and still going on to increase the ORR rate in PEMFC through low Pt catalyst loading by either modifying Pt with other metals to make an alloy or replacing Pt with other potential metal. Lin et al. have illustrated the capacity of different nanostructures of Pt catalyst such as nanopolyhedra, nanoframes and, nanowires/nanotubes and compared them with each other with the help of advantages and disadvantages. Scientists are also searching for better alternative of costliest Pt. However, they are far away from the result (Lin et al., 2018). There are other parameters that can make a difference on performance of PEMFC such as back pressure, relative humidity, and air stoichiometry; as they increase the performance also increases. But, they can also degrade performance in the long run (Zhang et al., 2016; Wang B. et al., 2019; Lui et al., 2019). Apart from this, development in MEA is also required, and it is briefly described in Section 3.1. Detailed information about different types of manufacturing processes of MEAs, membranes, GDLs, and bipolar plates are included in the review article of Mehta and Cooper (2003). The review of Wong et al. elaborated about the additives, which were used in PEMs in past few years to improve the efficiency of fuel cells. In that review, the category of additives was divided into low temperature and high temperature proton exchange membranes along with their results (Wong et al., 2019). Different kinds of PEMs are categorized into low temperature and high temperature PEMs.
Low temperature PEMs
Low temperature PEMs work below 100°C operating temperature. They generally show high proton conductivity, high limiting current density, and power. But, they have low mechanical strength. The membranes generally used in low temperature PEMFCs are fluorinated (also known as PFSA) such as Nafion by DuPont, Aciplex by Asahi Kasei, and Flemion by Asahi Glass and non-fluorinated such as sulfonated poly arylene ether ketone (S-PEEK) and sulfonated polyether sulfone (S-PES) (Bruijin et al., 2007). These low-temperature PEMs can be modified by reinforced material to increase the strength and durability. These membranes are called as reinforced PFSA or fluorinated membranes. For example, Gore-Select is the most known reinforced PFSA membrane with PTFE coating (polytetrafluoroethylene), which was invented by W. L. Gore (Bruijin et al., 2007). Apart from that, sulfonated polyphenylene (SPP-QP-PE) which is made of phenylene ionomer along with polyethylene (PE) support layer is an example of non-fluorinated reinforced membrane (Miyake et al., 2021). In this section, several reinforced, modified, or innovative membrane have been discussed for LT-PEMFC.
To modify Nafion 117, Tricoli did an experiment to overcome the issue of methanol diffusion from anode to cathode through the polymer electrolyte membrane for DMFC. He exchanged the hydrogen ion (H+) with cesium ion (Cs+ from CsOH) at several degrees, and he reduced the methanol permeability and increased the power density and efficiency to a great extent (Tricoli, 1998). Moreover, Kim et al. (2004) reported that biphenol sulfonated acidified membrane’s (BPSH) methanol permeability highly depends on morphologically closed regime. Roy et al. had proposed a novel way to manufacture the PEM, and it was the concept of multi-block copolymers. In this concept, the main focus was on block length of the hydrophobic and hydrophilic regions. Based on this, they did the experiments and measured characteristics of the membrane such as water uptake, proton conductivity, self-diffusion coefficient, ion exchange capacity (IEC), and water volume fraction for DMFC. Based on the results, they concluded that proton and water transport increased greatly as the block length increased, and methanol permeability increases as the IEC, water uptake, and self-diffusion coefficient increase (Roy et al., 2006; Roy et al., 2008). The same concept was also used by Liu D. et al. (2020),but for PEMFC and their work show that as the hydrophilic segment’s length increases the morphology of hydrophilic–hydrophobic and macroscopic characteristics escalate so does the performance of PEMFC. Sarah trabia et al. developed a new method for the fabrication of the PFSA membrane using 5% wt. PFSA solution also known as Nafion solution. This method can create unique shapes of the Nafion membrane using water dispersion by means of painting. First, the dispersion is sprayed on a weighing dish and creates the first layer then sprays the second layer and it continues without letting them dry. When it reaches 300 microns, they cut the membrane in the desired shape by Silhouette Cameo. After comparison with the traditional Nafion membrane, they nearly achieved equal results (Trabia et al., 2016).
PFSA membrane can also be modified by fillers, metals, metal oxides, or ILs (ionic liquids). The most recommendable is the metal oxides because they can prevent membrane degradation to some extent and extends the durability of it. Number of oxides have been used to get the notable performance, one of them is the ceria (Ce) added because Ce has the ability to possess reversible redox reaction (Yurova et al., 2021). For instance, Velayutham et al. performed an experiment on modifying Nafion with CeO2 for DMFC and Baker et al. developed for PEMFC; both the PEMs showed exceptional performance (Baker et al., 2014; Velayutham et al., 2017).
For sulfonated type PEMs, degree of sulfonation and disulfonation reaction are the primary factors to consider before manufacturing. The disulfonation reaction for the manufacturing of PEM was modified and optimized by M. Sankir et al. In their modified synthesis process, they eliminated the re-crystallization step and achieved the same quality of the product as it was in the former process. Therefore, it is advantageous in terms of process economics (Sankir et al., 2006). Zaidi et al. published their research on a partially sulfonated PEEK (polyether ether ketone) membrane by tungstophosphoric acid and molybdophosphoric acid. The membranes are thermally and mechanically stable, and the manufacturing process of this membrane is also cheaper (Zaidi et al., 2000). After 1 year, the sulfonated polyether ether ketone (SPEEK) membrane was modified with the help of BPO4 fine powder by Mikhailenko et al. (2001) and the conductivity of pure SPEEK is less than the modified SPEEK/BPO4. Another research on the SPEEK membrane was published by Li et al. [45] and Zhou et al. (2020) along with its detailed manufacturing process, testing, and results. However, Li et al. developed the SPEEK membrane for DMFC to operate at 80°C and compared it with Nafion 155, but it can be applicable for PEMFC. Further recent development in this field of PEEK membrane was carried out by Guo et al., Trindade, L. G. et al. and Geng et al. All research teams have made AP6FSPEEK (aminated/sulfonated copolymer of poly(aryl ether ketone)), SPEEK/MOF, and SPEEK/NIMs-SiO2 composite membranes, which unveil proton conductivities, and among them SPEEK/NIMs-SiO2 shows a highest proton conductivity of 0.22Scm−1 (Guo et al., 2009; Trindade et al., 2019; Geng et al., 2020). The performance of PEM can be enhanced in two ways, they are sulfonation of aromatic polymer and cross-linking of the membrane. Based on the study, if the degree of sulfonation and cross-linking increases then performance also increases; however, they could also lead to deformation in mechanical properties so does affects efficiency (Khomein et al., 2020).
Physical properties such as mechanical strength can be improved in ferroxane type membranes by adding polyvinyl alcohol (PVA), but proton conductivity decreases as the relative humidity decreases (Zhang et al., 2012). To modify the PFSA membrane, two methods are encountered mostly and those are impregnation and casting. However, the casting process showed better result, which was studied and compared by Fatima et al. They doped membranes with different compositions of phosphonic acid (PA) and biphosphonates (BA). The membrane doped with two biphosphonic acid groups (BA2) generated 87.3mScm−1 proton conductivity (Teixeira et al., 2019). The performance of PEMFC could be decreased by adding MgSO4 (magnesium sulfate solution). As the concentration of Mg+2 (magnesium ion) increases the contamination and degradation, power density decreases (Zhu J. et al., 2019). The membrane based on metal organic frameworks (MOF) is now modern choice. It is a mixture of organic and inorganic materials, which show high chemical and physical stability along with high conductivity. Imidazole@MOF-801, imidazole-MOF-801 and UiO-66-NH2 are the examples of it (Wang L. et al., 2020; Zhang et al., 2020). Moreover, the bio-inspired proton exchange membrane also shows high strength and conductivity and low weight (Cai et al., 2020). Until now, SPAES50’s performance has been the highest in the category of hydrocarbon-based PEM with 1069 mA/cm2 current density, which is synthesized by 50 mol% degree of sulfonation (Park et al., 2020).
Apart from modifying membrane methods, there are certain methods to improve overall performance of MEA for low temperature PEMFC such as electro-less plating of electrodes, which can decrease the surface resistance (Chung et al., 2007). A new type of ionic polymer-metal composite membranes (IPMC) made of the mixture of PFSA solution and poly(vinyl alcohol-co-ethylene), and they are also based on electro-less plating. This method of fabrication significantly reduced the PFSA composition by 30% and the material cost to some extent (Hwang et al., 2015). Based on the catalyst ink spray to complete MEA, there are three types of methods in trend for development of PEMFC’s performance and they are (1) low temperature decal method (LMTD), (2) catalyst-coated substrate (CCS), and (3) catalyst-coated membrane (CCM) (Shahgaldi et al., 2018). The method of LMTD is known for the complete catalyst transfer from decal substrate (fluorinated ethylene propylene) to the membrane without the skin layer of PFSA (Shahgaldi et al., 2017). In detail, the CCM technique to improve PEMFC performance along with experiments using Pt catalyst ink with isopropyl alcohol on the soaked membrane of ethylene glycol explained by Sun et al. (2008).
The Table 2 clearly shows the comparison of some low temperature PEMs by comparing some of the characteristics. Among these, the SPEEK/PSSA-g-PVDF membrane shows high power density along with high proton conductivity, which is essential for the PEMFC. However, other parameters such as water uptake and membrane thickness are also important. Water uptake is a function to measure the capacity of absorbance of water by the membrane because that absorbed water can help the membrane to deionize the protons. On the other side, thickness of the membrane gives the strength to face the pressure of hydrogen and oxygen gases. This membrane lacks in these two parameters. Although, research is still going on to improve low temperature PEMs. Based on the targets set by DOE, still a lot of work is required in this area.
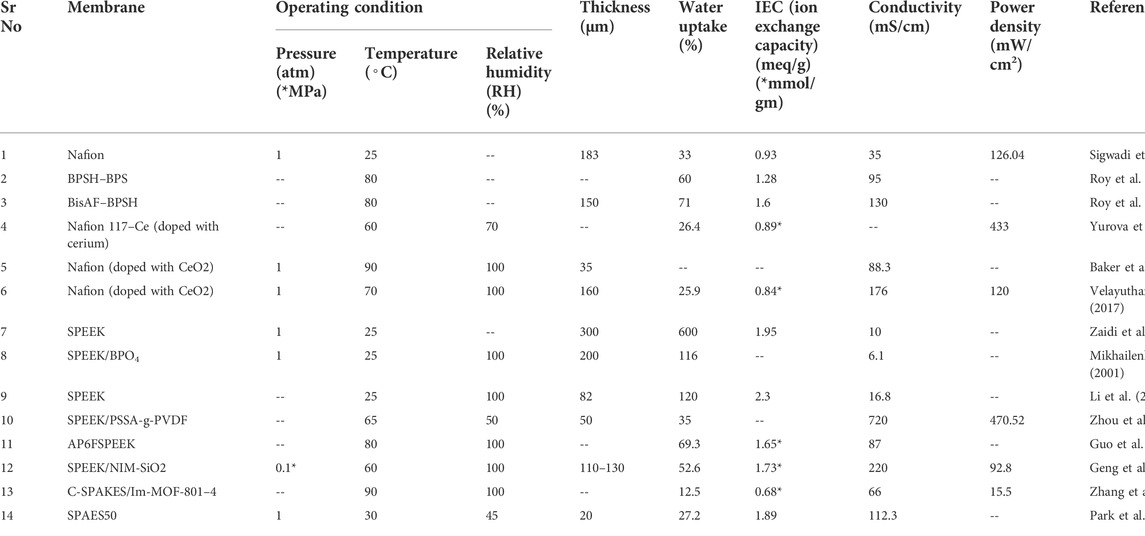
TABLE 2. Comparison of low-temperature PEMs based on thickness, water uptake, IEC, proton conductivity, and power density.
High temperature PEMs
High temperature PEMs are operating above 100°C. They have high mechanical strength, but power output, current density, and proton conductivity are less. As Nafion is notable for low temperature PEMFC then Hyflon is for high temperature PEMFC, and it was developed by Solvay Solexis; Hyflon is generally made of perfluoroalkoxy (PFA). Arcella et al. made the Hyflon membrane using a copolymer of tetrafluoroethylene (TFE) and sulfonylfluoridevinyl ether (SFVE) for the fuel cell to operate at high temperature. They observed that the fuel cell performance depends on the equivalent weight of Hyflon ion polymers, and they have higher thermal stability. In addition to this, this type of membrane showed higher conductivity, higher ionic glass transition temperature, higher mechanical properties, and long durability (Arcella et al., 2005). After this, Merlo et al. conducted an experiment on Hyflon ion polymer with the fuel cell and compared it with the Nafion membrane. They found that hydrogen permeability could occur below −40°C, and there was no degradation in the range of 70–90°C. The degradation happened due to the –OH species of H2O2 decomposition on the anode and the cathode. They have elaborated an entire membrane synthesis and modified MEA assembly along with its results in their article. They also observed that the rate of degradation in membrane increases as the humidity of reactants decreases; however, it does not depend on operating temperature (Merlo et al., 2007). Like Roy et al. and Liu et al., multi-block copolymer concept is also prominent for high temperature PEMs; work by Ghassemi et al. reported that poly(arylene ether sulfone) multi-block PEM has higher proton conductivity than the commercial types. In this multi-block copolymer, as a hydrophobic segment poly(arylene ether) and as a hydrophilic segment poly(arylene ether sulfone) are used, and ample of experiments based on different multi-block are described and those multi-block PEMs have proton conductivity up to 0.32S/cm (Ghassemi et al., 2006). Several high temperature PEM’s reactants such as polysulfone, poly(ether ketone), poly(aryl ether ketone sulfone), poly(propylene oxide), and poly(vinyl chloride) are renowned by reason of straightforward fabrication. However, their proton conductivity is less. Although, aminopropyl imidazole functionalized high temperature PEM showed acceptable proton conductivity at 180°C (Liu et al., 2020b; Xu et al., 2019; Tang et al., 2020).
Ceramic types of PEMs are also in trend along with the polymeric and composite types due to its high mechanical and thermal tolerance. Tsui et al. (2007) had reported ceramic PEM membrane fabricated using ferroxane and alumoxane as a precursor for DMFC and PEMFC applications. They had found a comparable alternative of Nafion 117 that was ferroxane-derived ceramics, which had lower methanol permeability, lower costs, and higher conductivity in less humidity.
To overcome CO tolerance and water uptake of the traditional Nafion membrane, a low volatile acid solution could be helpful to modify it (Malhotra and Datta, 1997). Apart from that, Nafion could also be modified by metal oxides such as ZrO2, SiO2, TiO2, and CO3O4 using the sol–gel method. These doped membranes showed high conductivity, high water uptake, and high degradation temperature compared to the traditional one (Jalani et al., 2005; Pourzare et al., 2020). The experiments with the Nafion–ZrO2 membrane had also been carried out by Thampan et al. (2005). Similarly, the Nafion–SiO2–PWA (phosphotungstic acid) composite membrane revealed higher current density at 110°C (540 mA/cm2) than Nafion 115 (95 mA/cm2) at 70% relative humidity (Shao et al., 2004).
Apart from novel LMTD for catalyst transfer, there are two unique procedures applied on the polybenzimidazole membrane; first, automatic catalyst spraying under irradiation (ACSUI) developed by Su et al. (2013) to build gas diffusion electrodes (GDEs). Second, branching structure of membrane is customized using special cross-linker, which resists sacrifice of N-H sites in the membrane (Wang J. et al., 2019) for high temperature PEMFCs; other researchers such as Guo et al. (2020), Tao et al. (2020), Imran et al. (2020), Wang S. et al. (2020), and Koyilapu et al. (2020) also have worked on the polybenzimidazole membrane to improve its performance. Another benzimidazole group’s membrane made by chloromethylated polysulfone (CMPSU) and zirconium phylate (ZrPA), with a cross-linking structure for high temperature PEM (Lv et al., 2019). As polybenzimidazole is used for high temperature PEMFC, then polytriazoles is used for low temperature PEMFC (Roy et al., 2020).
Xi et al. have developed high temperature proton exchange membrane, which they named HTM-X. This membrane synthesized from amino trimethylene phosphonic acid (ATMP), aminopropyltriethoxysilane (APTES), and cross-linked structure of PPO (poly(2,6-dimethyl-1,4-phenylene oxide)). From all membranes, HTM-15 showed a significant proton conductivity of 0.0848Scm−1 under 120°C and 5% relative humidity. In addition, all those membranes could be thermally stable of up to 210°C (Zhu X. et al., 2019). The sulfonated polyphenylsulfone (SPPSU) crosslink with carbon nanodots (CCD) can give outstanding conductivity at both low and high relative humidity. The notable conductivity of the membrane was 56.3mS/cm with 3% CND, and the flexibility of membrane and reduction in membrane cracking also improved (Mohamad Nor et al., 2020). Apart from CND, carbon nano tubes (CNTs) have also been applied more recently with chitosan (CS) in a simplistic way and layer-by-layer technique in a tedious way to enhance PEM for high temperature PEMFCs (Wang L. et al., 2019; Jia et al., 2020). Not only in PEMFC, this concept of using CS with polymer solution has also been applied in DMFC (Abu-saied et al., 2020). Therefore, this renowned concept is meaningful for future developments. As mentioned in the low temperature PEM section, Sanchez-Ballester et al. (2020) have also performed the research to improve physical properties along with proton conductivity by bisulfonated poly(vinyl alcohol) with graphene oxide as an inorganic filler. For intermediate or high temperature PEMFCs, the overview by Xiao et al. (2020) shows three categories of electrolyte membrane such as perfluorosulfonic, non-fluorinated arylene, and inorganic, which are currently in trend and used by number of industries.
Ballard Power Company has invented a new material for MEAs to apply in automobiles and electrochemical applications, which is named Ballard Advanced Materials (BAMs). These materials consist of copolymers of α,β,β-trifluorostyrene, and they compared it with Nafion 117 and DOW membrane. From BAMs, BAM3G01 showed a higher performance of 1300Amps/ft2 (Wei et al., 1995). Apart from Ballard, other power companies have also developed their own membrane material such as Gore select of Gore & Associates, Flemion of Asahi Glass, Aquivion of Solvay-Solexis, and Aciplex of Asahi Chemical.
High temperature membrane is unusual in usage in PEMFC due to number of factors. First, a cost of type of membrane requires a lot of costly materials and processes. Second, they are not flexible with feed’s composition. Last, the membrane thickness has become an issue for proton transportation. However, there are some advantages of it such as more power density, more stability, and flexibility in temperature and pressure of the feed. High temperature PEMs show immense performance but the overall cost is the ultimate issue. From the comparison shown in Table 3, SiO2-doped Nafion membrane showed high power density. However, the membrane is not much useful for long run due to aforementioned factors.
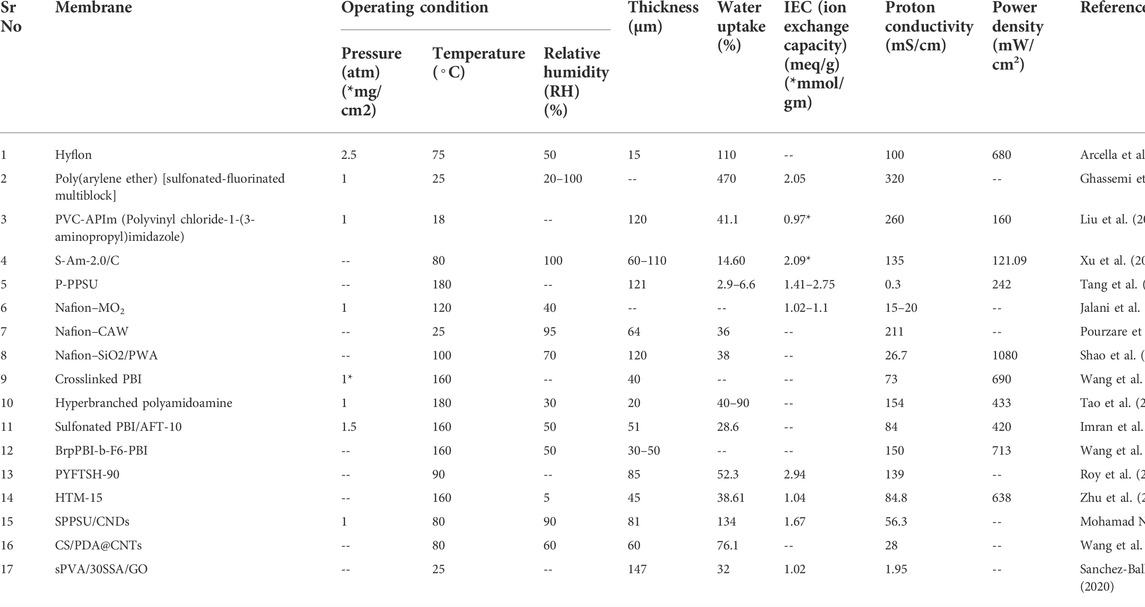
TABLE 3. Comparison of high-temperature PEMs based on thickness, water uptake, IEC, proton conductivity, and power density.
Future scope
PEMFC technology has wide range of future aspects and applications. Therefore, most of researchers and automobile industries are now focusing on development of PEMFC to use it commercially and industrially. Their center of attention is reducing the cost and improving performance of this fuel cell as well. They are doing this by either substituting Pt catalyst with low cost noble catalyst or by modifying the PEM with several methods. Until now, the Pt loading on PEM is nearly cut down to 50% in past decade, and efficiency of PEMs increased drastically (Prykhodko et al., 2020). Due to global warming situation, whole world is coming together to battle with it by putting strict policies on usage of renewable resources and restrictions on conventional fuels. America, Japan, South Korea, the United Kingdom, Canada, China, and Germany are diverting their energy policies toward more usage on hydrogen fuel for mainly in automobile industry. For instance, the United Kingdom has imposed a ban on sale of petrol and diesel vehicles after 2030 under “The Green Industrial Revolution” (HM government, 2020). In addition, Canada is also set to adopt “Net-Zero Emissions plan” by 2050 to eliminate carbon monoxide emission from industries and vehicles (Kim, 2019). By understanding the importance of green environment, there are more footprints in PEMFC in near upcoming decades. Because of this, more research works in this field are required to compete with the internal combustion engines to fulfill the requirements of government policies as mentioned. More achievements and government policies are briefly described in review of Ogungbemi et al. As a result, there is a wide scope of PEMFCs in land, air, and water transportation and so does in development of affordable and efficient PEMs (Ogungbemi et al., 2020). Major players in the fuel cell industry such as Ballard Power, Plug Power, Bloom Energy Corporation, FuelCell Energy, and Nikola, are currently on projects to build carbon-free transportation by building fuel cell truck, trains, tractors, cars, buses, and even small jets. In upcoming years, submarines, ships, aircrafts, spaceships, and generators will also run on hydrogen energy by fuel cells. Some future projects are in the development phase such as catalyst development and MEA compactness. In near future, only electrical, solar, and hydrogen energy will dominate to make the world a better place to live.
Conclusion
The discovery of fuel cells come a long way of two centuries, from Volta had discovered Voltaic Pile, which separates hydrogen and oxygen gases by giving electricity to the reverse reaction of it to generate electricity from those gases. Several fuel cells had been invented such as SOFC, MCFC, DMFC, PAFC, AFC, and PEMFC, but only PEMFC shows the potential to apply in both commercial and transportation because of its higher efficiency, low operating temperature, more flexibility, higher current density, etc. On the other hand, the number of PEMs are made to compete with the costliest Nafion series such as Nafion 112, 115, 117, and 1110, and those are the modified membranes such as Hyflon, multiblock polymers, PEEK, SPEEK, AP6FSPEEK, ferroxane-derived polymer, Nafion-SiO2/ZrO2/TiO2, Nafion-SiO2-PWA, IPMC, PA and BA doped Nafion, HTM-X, and SPPSU-CND/CNT with improved characteristics. This review generally classifies PEMs in two parts with low and high temperature PEMs. This classification is based on the application of PEM; low-temperature PEMs are used for commercial applications such as automobile or stationary power applications; high-temperature PEMs are used for industrial applications. Low-temperature PEMs have high efficiency along with great power and current density, the only drawback is that it could not work on high pressurized feed gas and high working temperature. In addition, it will gradually decay in long run. Nafion is low-temperature PEM with the power density around 120–150 mW/cm2. Based on study, the best alternative of the Nafion membrane is modified SPEEK membranes, as the SPEEK membranes show great potential with high power density, which could exceed 450 mW/cm2. As the degree of sulfonation increases in SPEEK, the power density increases; however, the chemical and mechanical instabilities also increase, which could lead to SO2 formation, and the membrane will decay drastically. Therefore, maintaining optimum degree of sulfonation is the primary goal for the SPEEK membrane by using different combinations of precursors, reactants, or treatment methods. On the other hand, high-temperature PEMs have high strength and can withstand high pressure of feed gases, but the energy efficiency is quite low. From the literature study, Nafion doped with silica shows high tensile and compression strength along with a high power density of 1080 mW/cm2. However, the process to make this membrane is complex and it is not cost-effective. Although, research works are going on to innovate a new membrane and develop an existing one. In the future, all vehicles may run on fuel cells with zero carbon monoxide emissions as mentioned in Future Scope. Automobile companies like Tesla, Honda, Ford, and Toyota launched their FCEV in the market to test. Therefore, scientists and researchers are putting their efforts to achieve the cheapest materials and parts for fuel cells to make it commercially available and affordable.
Author contributions
The author confirms being the sole contributor of this work and has approved it for publication.
Conflict of interest
The authors declare that the research was conducted in the absence of any commercial or financial relationships that could be construed as a potential conflict of interest.
Publisher’s note
All claims expressed in this article are solely those of the authors and do not necessarily represent those of their affiliated organizations, or those of the publisher, the editors, and the reviewers. Any product that may be evaluated in this article, or claim that may be made by its manufacturer, is not guaranteed or endorsed by the publisher.
References
Abu-Saied, M. A., Soliman, E. A., and Desouki, E. A. A. (2020). Development of proton exchange membranes based on chitosan blended with poly(2-acrylamido-2-methylpropane sulfonic acid) for fuel cells applications. Mater. Today Commun. 25, 101536. doi:10.1016/j.mtcomm.2020.101536 |
Alaswad, A., Baroutaji, A., Anchour, H., Carton, J., Makky, A., and Olabi, A. G. (2016). Developments in fuel cell technologies in the transport sector. Int. J. Hydrogen Energy 41 (37), 16499–16508. doi:10.1016/j.ijhydene.2016.03.164 |
Andujar, J. M., and Segura, F. (2009). Fuel cells: History and updating. A walk along two centuries. Renew. Sustain. Energy Rev. 13, 2309–2322. doi:10.1016/j.rser.2009.03.015 |
Appleby, A. J. (1990). From sir william grove to today: Fuel cells and the future. J. Power Sources 29, 3–11. doi:10.1016/0378-7753(90)80002-U |
Arcella, V., Troglia, C., and Ghielmi, A. (2005). Hyflon ion membranes for fuel cells. Ind. Eng. Chem. Res. 44 (20), 7646–7651. doi:10.1021/ie058008a |
Baker, A., Wang, L., Johnson, W., Prasad, A. K., and Advani, S. (2014). Nafion membranes reinforced with ceria-coated multiwall carbon nanotubes for improved mechanical and chemical durability in polymer electrolyte membrane fuel cells. J. Phys. Chem. C 118 (46), 26796–26802. doi:10.1021/jp5078399 |
Barrett, S. (2016). GM marks 50 years of FCEV development, from Electrovan to Chevrolet Colorado ZH2. Fuel Cells Bull. 2016 (11), 14–15. doi:10.1016/s1464-2859(16)30330-3 |
Bhosale, A. C., Ghosh, P. C., and Assaud, L. (2020). Preparation methods of membrane electrode assemblies for proton exchange membrane fuel cells and unitized regenerative fuel cells: A review. Renew. Sustain. Energy Rev. 133, 110286. doi:10.1016/j.rser.2020.110286 |
Boddu, R., Marupakula, U., Summers, B., and Majumdar, P. (2009). Development of bipolar plates with different flow channel configurations for fuel cells. J. Power Sources 189 (2), 1083–1092. doi:10.1016/j.jpowsour.2008.12.156 |
Bruijin, F. A., Makkus, R. C., Mallant, R. K. A. M., and Janssen, G. J. M. (2007). Chapter five-materials for state-of-the-art PEM fuel cells, and their suitability for operation above 100C. Adv. Fuel Cells 1, 235–336. doi:10.1016/51752-301X(07)80010-X |
Cai, Y., Yang, Q., Sun, L. X., Zhu, Z. Y., Zhang, Q. G., Zhu, A. M., et al. (2020). Bioinspired layered proton-exchange membranes with high strength and proton conductivity. Int. J. Hydrogen Energy 46, 4087–4099. doi:10.1016/j.ijhydene.2020.10.198( |
Chung, R., Chin, T., Chen, L., and Hsieh, M. (2007). Preparation of gradually componential metal electrode on solution-casted Nafion™ membrane. Biomol. Eng. 24 (5), 434–437. doi:10.1016/j.bioeng.2007.07.003 | |
Costamagna, P., and Srinivasan, S. (2001). Quantum jumps in the PEMFC science and technology from the 1960s to the year 2000. J. Power Sources 102 (1-2), 242–252. doi:10.1016/S0378-7753(01)00807-2 |
Degnan, T. (2018). Fuel cell market size worth $24.8 bn by 2025 | CAGR: 21%: Grand view research inc. Focus Catal. 2018 (12), 1–2. doi:10.1016/j.focat.2018.11.058 |
Devanathan, R. (2008). Recent developments in proton exchange membranes for fuel cells. Energy Environ. Sci. 1, 101–119. doi:10.1039/b808149m |
Drive, U. (2013). Fuel cell technical roadmap. New York: US Drive Partnership, 1–34. Available at: https://www.energy.gov/sites/prod/files/2017/11/f46/FCTT_Roadmap_Nov_2017_FINAL.pdf.
E4tech Ltd (2019). The fuel cell industry review 2019. Available at: https://www.afhypac.org/documents/publications/rapports/TheFuelCellIndustryReview2019.pdf.
Geng, H., Wu, H., Li, J., He, X., Shi, B., Fan, C., et al. (2020). Preparing proton exchange membranes via incorporating silica-based nanoscale ionic materials for the enhanced proton conductivity. Solid State Ionics 349, 115294. doi:10.1016/j.ssi.2020.115294 |
Ghassemi, H., McGrath, J. E., and Zawodzinski, T. A. (2006). Multiblock sulfonated–fluorinated poly(arylene ether)s for a proton exchange membrane fuel cell. Polymer 47 (11), 4132–4139. doi:10.1016/j.polymer.2006.02.038 |
Grove, W. (1842). LXXII. On a gaseous voltaic battery. Lond. Edinb. Dublin Philosophical Mag. J. Sci. 3 (21), 417–420. doi:10.1080/14786444208621600 |
Grove, W. (1874). The correlation of physical forces. London, England: Longmans Green & Co. doi:10.5962/bhl.title.19475 |
Grove, W. (1839). XXIV. On voltaic series and the combination of gases by platinum. Lond. Edinb. Dublin Philosophical Mag. J. Sci. 14, 127–130. doi:10.1080/14786443908649684 |
Guo, M., Liu, B., Liu, Z., Wang, L., and Jiang, Z. (2009). Novel acid–base molecule-enhanced blends/copolymers for fuel cell applications. J. Power Sources 189 (2), 894–901. doi:10.1016/j.jpowsour.2008.12.137 |
Guo, Y., Guo, X., Zhang, H., and Hou, S. (2020). Energetic, exergetic and ecological analyses of a high-temperature proton exchange membrane fuel cell based on a phosphoric-acid-doped polybenzimidazole membrane. Sustain. Energy Technol. Assessments 38, 100671. doi:10.1016/j.seta.2020.100671 |
HM Government, (2020). The ten point plan for a green industrial revolution. London: Government of UK. https://assets.publishing.service.gov.uk/government/uploads/system/uploads/attachment_data/file/936567/10_POINT_PLAN_BOOKLET.pdf.
Huah, L. B., Majlan, E. H., Tajuddin, A., Husaini, T., Daud, W. R. W., Radzuan, N. A. M., et al. (2020). Comparison of catalyst-coated membranes and catalyst-coated substrate for PEMFC membrane electrode assembly: A review. Chin. J. Chem. Eng. 33, 1–16. doi:10.1016/j.cjche.2020.07.044 |
Hwang, T., Palmre, V., Nam, J., Lee, D., and Kin, K. J. (2015). A new ionic polymer-metal composite based on Nafion/poly(vinyl alcohol-co-ethylene) blends. Smart Mat. Struct. 24 (10), 105011. doi:10.1088/0964-1726/24/10/105011 |
Imran, M. A., Li, T., Wu, X., Yan, X., Khan, A., and He, G. (2020). Sulfonated polybenzimidazole/amine functionalized titanium dioxide (sPBI/AFT) composite electrolyte membranes for high temperature proton exchange membrane fuel cells usage. Chin. J. Chem. Eng. 28 (9), 2425–2437. doi:10.1016/j.cjche.2020.05.016 |
Jalani, N. H., Dunn, K., and Datta, R. (2005). Synthesis and characterization of Nafion-MO2 (M=Zr, Si, Ti) nanocomposite membranes for higher temperature PEM fuel cells. Electrochimica Acta 51 (3), 553–560. doi:10.1016/j.electacta.2005.05.016 |
Jia, T., Shen, S., Zhao, J., Jin, J., Pan, B., Duan, X., et al. (2020). Ultrathin membranes formation via the layer by layer self-assembly of carbon nanotubes-based inorganics as high temperature proton exchange membranes. Int. J. Hydrogen Energy 45 (28), 14517–14527. doi:10.1016/j.ijhydene.2020.03.175 |
Khomein, P., Ketelaars, W., Lap, T., and Liu, G. (2020). Sulfonated aromatic polymer as a future proton exchange membrane: A review of sulfonation and crosslinking methods. Renew. Sustain. Energy Rev. 173, 110471. (In press). doi:10.1016/j.rser.2020.110471 |
Kim, S. (2019). Government of Canada releases emissions projections, showing progress towards climate target, Environment and Climate Change Canada. Ottawa: Government of Canada. Available at: https://www.canada.ca/en/environment-climate-change/news/2019/12/government-of-canada-releases-emissions-projections-showing-progress-towards-climate-target.html.
Kim, Y. S., Hickner, M. A., Dong, L., Pivovar, B. S., and McGrath, J. E. (2004). Sulfonated poly(arylene ether sulfone) copolymer proton exchange membranes: Composition and morphology effects on the methanol permeability. J. Membr. Sci. 243 (1-2), 317–326. doi:10.1016/j.memsci.2004.06.035 |
Knorr, F., Sanchez, D. G., Schirmer, J., Gazdzicki, P., and Friedrich, K. A. (2019). Methanol as antifreeze agent for cold start of automotive polymer electrolyte membrane fuel cells. Appl. Energy 238, 1–10. doi:10.1016/j.apenergy.2019.01.036 |
Koyilapu, R., Singha, S., Sana, B., and Jana, T. (2020). Proton exchange membrane prepared by blending polybenzimidazole with poly (aminophosphonate ester). Polym. Test. 85, 106414. doi:10.1016/j.polymertesting.2020.106414 |
Kragh, H. (2015). From cosmochemistry to fuel cells: Notes on Emil Baur, physical chemist. Bull. Hist. Chem. 40 (2), 74–85. Available at: http://acshist.scs.illinois.edu/bulletin_open_access/FullIssues/vol40-2.pdf.
Li, L., Zhang, J., and Wang, Y. (2003). Sulfonated poly(ether ether ketone) membranes for direct methanol fuel cell. J. Membr. Sci. 226 (1-2), 159–167. doi:10.1016/j.memsci.2003.08.018 |
Lin, R., Cai, X., Zeng, H., and Yu, Z. (2018). Stability of high-performance Pt-based catalysts for oxygen reduction reactions. Adv. Mat. 30 (17), 1705332. doi:10.1002/adma.201705332 |
Lin, R., Zhu, Y., Ni, M., Jiang, Z., Lou, D., Han, L., et al. (2019). Consistency analysis of polymer electrolyte membrane fuel cell stack during cold start. Appl. Energy 241, 420–432. doi:10.1016/j.apenergy.2019.03.091 |
Liu, D., Xie, Y., Cui, N., Han, X., Zhang, J., Pang, J., et al. (2020a). Structure and properties of sulfonated poly(arylene ether)s with densely sulfonated segments containing mono-di- and tri-tetraphenylmethane as proton exchange membrane. J. Membr. Sci. 620, 118856. (In press). doi:10.1016/j.memsci.2020.118856 |
Liu, R., Dai, Y., Li, J., Chen, X., Pan, C., Yang, J., et al. (2020b). 1-(3-Aminopropyl)imidazole functionalized poly(vinyl chloride) for high temperature proton exchange membrane fuel cell applications. J. Membr. Sci. 620, 118873. (In press). doi:10.1016/j.memsci.2020.118873 |
Lui, D., Lin, R., Feng, B., and Yang, Z. (2019). Investigation of the effect of cathode stoichiometry of proton exchange membrane fuel cell using localized electrochemical impedance spectroscopy based on print circuit board. Int. J. hydrogen energy 44, 7564–7573. doi:10.1016/j.ijhydene.2019.01.095 |
Lv, Y., Li, Z., Song, M., Sun, P., Yin, X., and Wang, S. (2019). Preparation and properties of ZrPA doped CMPSU cross-linked PBI based high temperature and low humidity proton exchange membranes. React. Funct. Polym. 137, 57–70. doi:10.1016/j.reactfunctpolym.2019.01.014 |
Malhotra, S., and Datta, R. (1997). Membrane-supported nonvolatile acidic electrolytes allow higher temperature operation of proton-exchange membrane fuel cells. J. Electrochem. Soc. 144 (2), L23–L26. doi:10.1149/1.1837420 |
Mehta, V., and Cooper, J. S. (2003). Review and analysis of PEM fuel cell design and manufacturing. J. Power Sources 114 (1), 32–53. doi:10.1016/s0378-7753(02)00542-6 |
Merlo, L., Ghielmi, A., Cirillo, L., Gebert, M., and Arcella, V. (2007). Membrane electrode assemblies based on HYFLON®Ion for an evolving fuel cell technology. Sep. Sci. Technol. 42 (13), 2891–2908. doi:10.1080/01496390701558334 |
Mikhailenko, S. D., Zaidi, S. M. J., and Kaliaguine, S. (2001). Sulfonated polyether ether ketone based composite polymer electrolyte membranes. Catal. Today 67 (1-3), 225–236. doi:10.1016/s0920-5861(01)00290-5 |
Miyake, J., Watanabe, T., Shintani, H., Sugawara, Y., Uchida, M., and Miyatake, K. (2021). Reinforced polyphenylene ionomer membranes exhibiting high fuel cell performance and mechanical durability. ACS Mat. Au 1 (1), 81–88. doi:10.1021/acsmaterialsau.1c00002 |
Mohamad Nor, N. A., Nakao, H., Jaafar, J., and Kim, J. (2020). Crosslinked carbon nanodots with highly sulfonated polyphenylsulfone as proton exchange membrane for fuel cell applications. Int. J. Hydrogen Energy 45, 9979–9988. doi:10.1016/j.ijhydene.2020.01.142 |
Nicholson, Carlisle, and Cruickshank, M (1800). IV. Experiments in galvanic electricity. Philosophical Mag. 7, 337–347. doi:10.1080/14786440008562593 |
Ogungbemi, E., Wilberforce, T., Ijaodola, O., Thompson, J., and Olabi, A. G. (2020). Selection of proton exchange membrane fuel cell for transportation. Int. J. Hydrogen Energy 46, 30625–30640. (In press). doi:10.1016/j.ijhydene.2020.06.147 |
Park, J. E., Kim, J., Han, J., Kim, K., Park, S., Kim, S., et al. (2020). High-performance proton-exchange membrane water electrolysis using a sulfonated poly(arylene ether sulfone) membrane and ionomer. J. Membr. Sci. 620, 118871. doi:10.1016/j.memsci.2020.118871 |
Pourzare, K., Mansourpanah, Y., Farhadi, S., Hasani Sadrabadi, M. M., Frost, I., and Ulbricht, M. (2020). Improving the efficiency of Nafion-based proton exchange membranes embedded with magnetically aligned silica-coated Co3O4 nanoparticles. Solid State Ionics 351, 115343. doi:10.1016/j.ssi.2020.115343 |
Prykhodko, Y., Fatyeyeva, K., Hespel, L., and Marais, S. (2020). Progress in hybrid composite Nafion®-based membranes for proton exchange fuel cell application. Chem. Eng. J. 409, 127329. (In press). doi:10.1016/j.cej.2020.127329 |
Roy, A., Hickner, M. A., Yu, X., Li, Y., Glass, T. E., and McGrath, J. E. (2006). Influence of chemical composition and sequence length on the transport properties of proton exchange membranes. J. Polym. Sci. B. Polym. Phys. 44 (16), 2226–2239. doi:10.1002/polb.20859 |
Roy, A., Lee, H. S., and McGrath, J. E. (2008). Hydrophilic–hydrophobic multiblock copolymers based on poly(arylene ether sulfone)s as novel proton exchange membranes – Part B. Polymer 49 (23), 5037–5044. doi:10.1016/j.polymer.2008.08.046 |
Roy, S., Ghorai, A., Komber, H., Voit, B., and Banerjee, S. (2020). Synthesis of 2, 2́-hindered pyridine containing semifluorinated polytriazoles and investigation for low-temperature proton exchange membrane application with enhanced oxidative stability. Eur. Polym. J. 136, 109898. doi:10.1016/j.eurpolymj.2020.109898 |
Sánchez-Ballester, S. C., Soria, V., Rydzek, G., Ariga, K., and Ribes-Greus, A. (2020). Synthesis and characterization of bisulfonated poly(vinyl alcohol)/graphene oxide composite membranes with improved proton exchange capabilities. Polym. Test. 91, 106752. doi:10.1016/j.polymertesting.2020.106752 |
Sankir, M., Bhanu, V. A., Harrison, W. L., Ghassemi, H., Wiles, K. B., Glass, T. E., et al. (2006). Synthesis and characterization of 3, 3′-disulfonated-4, 4′-dichlorodiphenyl sulfone (SDCDPS) monomer for proton exchange membranes (PEM) in fuel cell applications. J. Appl. Polym. Sci. 100 (6), 4595–4602. doi:10.1002/app.22803 |
Shahgaldi, S., Alaefour, I., and Li, X. (2018). Impact of manufacturing processes on proton exchange membrane fuel cell performance. Appl. Energy 225, 1022–1032. doi:10.1016/j.apenergy.2018.05.086 |
Shahgaldi, S., Alaefour, I., Unsworth, G., and Li, X. (2017). Development of a low temperature decal transfer method for the fabrication of proton exchange membrane fuel cells. Int. J. Hydrogen Energy 42 (16), 11813–11822. doi:10.1016/j.ijhydene.2017.02.127 |
Shao, Z. G., Joghee, P., and Hsing, I. M. (2004). Preparation and characterization of hybrid Nafion–silica membrane doped with phosphotungstic acid for high temperature operation of proton exchange membrane fuel cells. J. Membr. Sci. 229 (1-2), 43–51. doi:10.1016/j.memsci.2003.09.014 |
Sharaf, O., and Orhan, M. (2014). An overview of fuel cell technology: Fundamentals and applications. Renew. Sustain. Energy Rev. 32, 810–853. doi:10.1016/j.rser.2014.01.012 |
Sigwadi, R., Dhlamini, M. S., Mokrani, T., Nemavhola, F., Nonjola, P. F., and Msomi, P. F. (2019). The proton conductivity and mechanical properties of nafion/Zrp nanocomposite membrane. Heliyon 5, e02240. doi:10.1016/j.heliyon.2019.e02240 | |
Song, Y., Zhang, C., Ling, C. Y., Han, M., Yong, R. Y., Sun, D., et al. (2019). Review on current research of materials, fabrication and application for bipolar plate in proton exchange membrane fuel cell. Int. J. Hydrogen Energy 45 (54), 29832–29847. doi:10.1016/j.ijhydene.2019.07.231 |
Su, H., Pasupathi, S., Bladergroen, B. J., Linkov, V., and Pollet, B. G. (2013). Enhanced performance of polybenzimidazole-based high temperature proton exchange membrane fuel cell with gas diffusion electrodes prepared by automatic catalyst spraying under irradiation technique. J. Power Sources 242, 510–519. doi:10.1016/j.jpowsour.2013.05.128 |
Sun, L., Ran, R., Wang, G., and Shao, Z. (2008). Fabrication and performance test of a catalyst-coated membrane from direct spray deposition. Solid State Ionics 179, 960–965. doi:10.1016/j.ssi.2008.01.081 |
Tang, H., Geng, K., Hu, Y., and Li, N. (2020). Synthesis and properties of phosphonated polysulfones for durable high-temperature proton exchange membranes fuel cell. J. Membr. Sci. 605, 118107. doi:10.1016/j.memsci.2020.118107 |
Tao, P., Dai, Y., Chen, S., Wang, J., and He, R. (2020). Hyperbranched polyamidoamine modified high temperature proton exchange membranes based on PTFE reinforced blended polymers. J. Membr. Sci. 604, 118004. doi:10.1016/j.memsci.2020.118004 |
Teixeira, F. C., Sa, A., Teixeira, A. P. S., and Rangel, C. M. (2019). Nafion phosphonic acid composite membranes for proton exchange membranes fuel cells. Appl. Surf. Sci. 487, 889–897. doi:10.1016/j.apsusc.2019.05.078 |
Thampan, T. M., Jalani, N. H., Choi, P., and Datta, R. (2005). Systematic approach to design higher temperature composite PEMs. J. Electrochem. Soc. 152 (2), A316–A325. doi:10.1149/1.1843771 |
Trabia, S., Hwang, T., and Kim, K. J. (2016). A fabrication method of unique nafion shapes by painting for ionic polymer-metal composites. Smart Mat. Struct. 25, 085006–085021. doi:10.1088/0964-1726/25/8/085006 |
Tricoli, V. (1998). Proton and methanol transport in poly(perfluorosulfonate) membranes containing Cs+ and H+ cations. J. Electrochem. Soc. 145 (11), 3798–3801. doi:10.1149/1.1838876 |
Trindade, L. G., Borba, K. M. N., Zanchet, L., Lima, D. W., Trench, A. B., Rey, F., et al. (2019). SPEEK based proton exchange membranes modified with MOF-encapsulated ionic liquid. Mat. Chem. Phys. 236, 121792. doi:10.1016/j.matchemphys.2019.121792 |
Tsui, E. M., Cortalezzi, M. M., and Wiesner, M. R. (2007). Proton conductivity and methanol rejection by ceramic membranes derived from ferroxane and alumoxane precursors. J. Membr. Sci. 306 (1-2), 8–15. doi:10.1016/j.memsci.2007.03.026 |
Velayutham, P., Sahu, A. K., and Parthasarathy, S. (2017). A nafion-ceria composite membrane electrolyte for reduced methanol crossover in direct methanol fuel cells. Energies 10 (2), 259. doi:10.3390/en10020259 |
Wang, B., Lin, R., Liu, D., Xu, J., and Feng, B. (2019a). Investigation of the effect of humidity at both electrode on the performance of PEMFC using orthogonal test method. Int. J. Hydrogen Energy 44 (26), 13737–13743. doi:10.1016/j.ijhydene.2019.03.139 |
Wang, J., Gong, C., Wen, S., Liu, H., Qin, C., Xiong, C., et al. (2019b). A facile approach of fabricating proton exchange membranes by incorporating polydopamine-functionalized carbon nanotubes into chitosan. Int. J. Hydrogen Energy 44, 6909–6918. doi:10.1016/j.ijhydene.2019.01.194 |
Wang, L., Liu, Z., Liu, Y., and Wang, L. (2019c). Crosslinked polybenzimidazole containing branching structure with no sacrifice of effective N-H sites: Towards high-performance high-temperature proton exchange membranes for fuel cells. J. Membr. Sci. 583, 110–117. doi:10.1016/j.memsci.2019.04.030 |
Wang, L., Wu, Y., Fang, M., Chen, J., Liu, X., Yin, B., et al. (2020a). Synthesis and preparation of branched block polybenzimidazole membranes with high proton conductivity and single-cell performance for use in high temperature proton exchange membrane fuel cells. J. Membr. Sci. 62, 117981. doi:10.1016/j.memsci.2020.117981 |
Wang, S., Luo, H., Li, X., Shi, L., Cheng, B., Zhuang, X., et al. (2020b). Amino acid-functionalized metal organic framework with excellent proton conductivity for proton exchange membranes. Int. J. Hydrogen Energy 46, 1163–1173. (In press). doi:10.1016/j.ijhydene.2020.09.235 ( |
Wei, J., Stone, C., and Steck, A. E. (1995). Trifluorostyrene and substituted trifluorostryrene copolymeric compositions and ion-exchange membranes formed therefromU.S. Patent No. 5. Washington, DC: U.S. Patent and Trademark Office, 411.
Williams, K. R. (1994). Francis Thomas Bacon 21 december 1904 -24 may 1992. Biogr. Memoirs Fellows R. Soc. 39, 2–9. doi:10.1098/rsbm.1994.0001 |
Wong, C. Y., Wong, W. Y., Ramya, K., Khalid, M., Loh, K. S., Daud, W. R. W., et al. (2019). Additives in proton exchange membranes for low- and high-temperature fuel cell applications: A review. Int. J. Hydrogen Energy 44 (12), 6116–6135. doi:10.1016/j.ijhydene.2019.01.084 |
Xiao, T., Wang, R., Chang, Z., Fang, Z., Zhu, Z., Xu, C., et al. (2020). Electrolyte membranes for intermediate temperature proton exchange membrane fuel cell. Prog. Nat. Sci. Mater. Int. 30, 743–750. doi:10.1016/j.pnsc.2020.08.014 |
Xu, J., Zhang, Z., Yang, K., Zhang, H., and Wang, Z. (2019). Synthesis and properties of novel cross-linked composite sulfonated poly(aryl ether ketone sulfone) containing multiple sulfonic side chains for high-performance proton exchange membranes. Renew. Energy 138, 1104–1113. doi:10.1016/j.renene.2019.02.042 |
Yurova, P. A., Malakhova, V. R., Gerasimova, E. V., Stenina, I. A., and Yaroslavtsev, A. B. (2021). Nafion/surface modified ceria hybrid membranes for fuel cell application. Polymers 13, 2513. doi:10.3390/polym13152513 | |
Zaidi, S. M., Mikhailenko, S. D., Robertson, G. P., Guiver, M. D., and Kaliaguine, S. (2000). Proton conducting composite membranes from polyether ether ketone and heteropolyacids for fuel cell applications. J. Membr. Sci. 173 (1), 17–34. doi:10.1016/s0376-7388(00)00345-8 |
Zhang, L., Chae, S. R., Hendren, Z., Park, J. S., and Wiesner, M. R. (2012). Recent advances in proton exchange membranes for fuel cell applications. Chem. Eng. J. 204-206, 87–97. doi:10.1016/j.cej.2012.07.103 |
Zhang, L., Chae, S. R., Lin, S., and Weisner, M. R. (2012). Proton-conducting composite membranes derived from ferroxane-polyvinyl alcohol complex. Environ. Eng. Sci. 29 (2), 124–132. doi:10.1089/ees.2011.0270 |
Zhang, Q., Lin, R., Techer, L., and Cui, X. (2016). Experimental study of variable operating parameters effects on overall PEMFC performance and spatial performance distribution. Energy 115, 550–560. doi:10.1016/j.energy.2016.08.086 |
Zhang, Z., Ren, J., Xu, J., Wang, Z., He, W., Wang, S., et al. (2020). Adjust the arrangement of imidazole on the metal-organic framework to obtain hybrid proton exchange membrane with long-term stable high proton conductivity. J. Membr. Sci. 607, 118194. doi:10.1016/j.memsci.2020.118194 |
Zhou, X., Zhu, B., Zhu, X., Miao, J., Sun, X., and Zhou, Q. (2020). Novel nanofiber-enhanced SPEEK proton-exchange membranes with high conductivity and stability. Polymer 210, 123016. doi:10.1016/j.polymer.2020.123016 |
Zhu, J., Tan, J., Pan, Q., Liu, Z., and Hou, Q. (2019a). Effects of Mg2+ contamination on the performance of proton exchange membrane fuel cell. Energy 189, 116135. doi:10.1016/j.energy.2019.116135 |
Zhu, X., Shen, C., Gao, S., Jin, H., Cheng, X., and Gong, C. (2019b). High-temperature proton exchange membrane with dual proton transfer channels by incorporating phosphonic acid functionalized siloxane into poly(2, 6-dimethyl-1, 4-phenyleneoxide) (PPO). Solid State Ionics 337, 193–204. doi:10.1016/j.ssi.2019.04.027 |
Keywords: PEMFC, recent developments, renewable energy, proton exchange membrane, high temperature PEM, low temperature PEM
Citation: Parekh A (2022) Recent developments of proton exchange membranes for PEMFC: A review. Front. Energy Res. 10:956132. doi: 10.3389/fenrg.2022.956132
Received: 29 May 2022; Accepted: 21 July 2022;
Published: 16 September 2022.
Edited by:
Shijun Liao, South China University of Technology, ChinaReviewed by:
Zhefei Pan, Hong Kong Polytechnic University, Hong Kong SAR, ChinaCopyright © 2022 Parekh. This is an open-access article distributed under the terms of the Creative Commons Attribution License (CC BY). The use, distribution or reproduction in other forums is permitted, provided the original author(s) and the copyright owner(s) are credited and that the original publication in this journal is cited, in accordance with accepted academic practice. No use, distribution or reproduction is permitted which does not comply with these terms.
*Correspondence: Abhi Parekh, YWJoaWNoZXRhbmt1bWFyLnBhcmVAdWNhbGdhcnkuY2E=