- 1Key Laboratory of Energy Thermal Conversion and Control of Ministry of Education, School of Energy and Environment, Southeast University, Nanjing, China
- 2Jiangsu Key Laboratory of Micro and Nano Heat Fluid Flow Technology and Energy Application, School of Physical Science and Technology, Suzhou University of Science and Technology, Suzhou, China
Introduction
With the advent of the Information Age, the requirements for data processing have been on the rise. However, the miniaturization and integration of electronic components lead to increased heat generation. This huge energy consumption in cooling and heat transfer performance of existing coolants limits the development of electronic devices. An important solution is to enhance the heat absorption capacity of coolants. Phase change materials (PCMs) absorb and release a large amount of latent heat through a phase change, which is advantageous in preventing overheating of electronic components (Zhang et al., 2020). However, PCMs leak easily and are mostly corrosive (Moreno et al., 2014). Adding encapsulated phase change materials (EPCMs) into a base working fluid forms a PCM slurry (PCMS), which circumvents the defects of PCM and offers a feasible approach to thermal management. The invariant temperature during the phase change makes PCMS more competitive than conventional coolants in many cooling technologies, such as microchannel (Wang et al., 2016), jet and spray cooling (Wan et al., 2021), heat pipes (Heydarian et al., 2019), etc. In particular, when the heat flux is high, up to a 40% decrement in the internal wall temperature, a 50% increase in heat transfer coefficient (Sabbah et al., 2012), and a 67.5% decrement in the pumping power (Chen et al., 2008) can be achieved by the application of EPCM. However, encapsulation brings about additional heat resistance, which may weaken the heat transfer performance of PCMS or even deteriorate the cooling process. Furthermore, the high viscosity of PCMS leads to high pumping power, especially in conditions with a high concentration of EPCM, a low Re number, or narrow channels (Ghoghaei et al., 2020). Supercooling is another drawback of PCMS in that phase change is triggered at a higher temperature than pure PCM, resulting in uncertainty of heat transfer and increasing energy consumption. To improve the performance of PCMS, various attempts have been made and can be classified into two categories as improving the fabrication of PCM microcapsules (Hao et al., 2022) and coupling PCMS with other materials (Rajabifar, 2015).
Thus, given the urgent need for electronic cooling and the favorable heat transfer performance of PCMS, this opinion briefly expounds on the prospect and challenges of PCMS in thermal management. The fabrication of EPCM and the application of common cooling technology with typical optimization methods are summarized here, aiming to provide a quick and preliminary understanding of PCMS.
Fabrication of Encapsulated Phase Change Materials
Traditionally, EPCMs are produced through polymerization, coacervation, etc. Microfluidics with high capsulation efficiency provide an alternative approach to producing highly monodispersed EPCM in a controllable way. EPCMs produced by polymerization, complex coacervation, and microfluidics are shown in Figure 1.
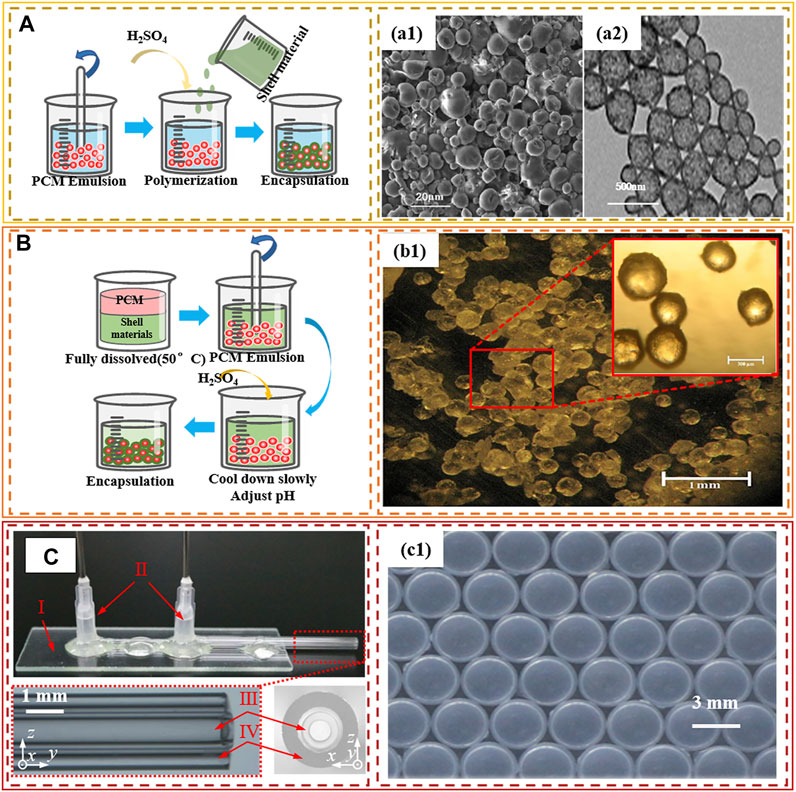
FIGURE 1. Encapsulation methods: (A) polymerization, (a1) and (a2) are EPCM produced by in situ polymerization (Srinivasaraonaik et al., 2020) and interfacial polymerization (Zhao and Luo, 2022), respectively, (B) coacervation (Malekipirbazari et al., 2014), (C) microfluidic EPCM production (I: glass slide, II: dispensing needles, III: inner capillary, IV: outer capillary) (Hao et al., 2022).
Polymerization
Polymerization generally refers to in situ polymerization and interfacial polymerization, as shown in Figure 1 A. In the in situ polymerization, monomers of the shell material and catalyst are dissolved in the preemulsified core solution. When the environmental conditions, such as pH value or temperature, vary, a high molecular polymer of the shell, which is insoluble in the continuous phase, forms at the surface of the core emulsions that encapsulates the core materials into capsules (Srinivasaraonaik et al., 2020). The interfacial polymerization is similar to in situ polymerization where the polymerization occurs at the interface of core material emulsion. The formation of a shell is caused by the polymerization of reactants inside and outside the interface (Zhao and Luo, 2022). Polymerization methods have the advantages of rapid reaction, mild conditions, and simple operation. But, impurities in the products are inevitable.
Complex Coacervation
Complex coacervation, as shown in Figure 1B, uses two or more types of polymers with opposite charges as the composite of shell. Under certain temperature and salinity, the electrostatic attraction between polymers leads to polymerization at the surface of dispersed core material. Phase separation occurs spontaneously with decreasing solubility, and microcapsules form eventually (Malekipirbazari et al., 2014). The coacervation is easy to operate with the advantage of high throughput. However, the selection of the shell materials is tricky, and impurities are inevitable.
Microfluidic
Studies have proven the significance of accurate and controllable encapsulation of EPCM for the cooling performance of PCMS (Li et al., 2019). Based on microfluidic chips, micro/nanoscale single and double emulsions with perfect sphericity can be prepared, and the capsule size can be controlled easily by changing the flow rate of phases, which has drawn extensive attention. Axisymmetric microfluidic chips, such as flow focusing (Akamatsu et al., 2019) and coflowing (Fu et al., 2014) are usually used for preparing EPCM. The liquid-state core and shell materials are injected as the innermost and the middle phase, respectively, during the formation of double emulsions in microfluidics. Subsequently, EPCM with smooth surface and regular size are obtained by curing the emulsion templates. The EPCM produced by Hao et al. (2022) with coflowing microfluidic device is shown in Figure 1C1, which suggests that EPCM prepared by microfluidic have significantly higher monodispersity than those prepared by other methods.
A 100% encapsulation efficiency and controllability make microfluidic a promising fabrication method for EPCM. However, there are several issues limiting the industrial application of microfluidic: 1) The controllability of microfluidic relies on fully understanding the hydrodynamic mechanism of droplet formation (Chen et al., 2013; Chen and Deng, 2017; Wang et al., 2022). 2) The fluid to be emulsified is determined by the wettability of the chip; hence, surface modification is usually required (Wang et al., 2018). 3) The throughput of microfluidic is relatively low in a single microfluidic channel. Recently, step emulsification (Shi et al., 2020), parallel microchannel (Eberhardt et al., 2019), and droplet splitting (Park et al., 2018) are proposed to facilitate the throughput of microfluidics. However, complex hydrodynamics are inevitable in high-throughput microfluidics that the monodispersity is slightly worse than a single-channel microfluidic.
Applications in Electronic Cooling
EPCM shows great potential in effective cooling with reduced energy consumption attributable to its high specific surface area and favorable characteristic of constant temperature during the phase transition process. However, there are some unsolved problems that limit the prevalence of EPCM in cooling technologies.
Microchannel
Microchannel is one of the most commonly used liquid cooling devices. Compared with traditional coolant, PCMS has been proven to have enhanced cooling performance. Adding 0.7% EPCM can achieve a 37% increment in heat transfer efficiency compared to single-phase coolant (deionized water). However, when the concentration of EPCM increases from 0.25% to 1.5%, the viscosity increases by 15%–22%, which directly leads to high pressure drop and pumping power (Joseph and Sajith, 2019). To optimize the performance of PCMS, some methods aiming to enhance the heat transfer are proposed, such as adding nanoparticles in the slurry (Rajabifar, 2015), using carbon nanotubes as the shell to increase the thermal conductivity, and adding liquidity-enhancing active agent (Sinha-Ray et al., 2014). The applicable temperature of PCMS can be extended from 40°C–80°C to 40°C–120°C with carbon nanotube shells and active agent, which is of great significance for cooling in high-heat flux narrow channels.
Jet Impingement Cooling
The heat transfer coefficient of jet impingement cooling increases by 50%–70% after the working fluid is loaded with EPCM, and the capsules can maintain complete structure after multiple cycles (Wu et al., 2011). However, a high pressure drop and heat transfer resistance of EPCM were also observed (Wan et al., 2021). What is more, the PCMS exhibit greater cooling efficiency than single-phase coolants only when the jet inlet temperature is in a certain range related to the PCM melting point. Although the disadvantage of PCMS can be counteracted by increasing the flow rate, excessive flow velocity causes incomplete phase transition and invalidity of PCMS.
Heat Pipe
The PCMS is also utilized in pulsating heat pipes. The PCM melts and solidifies when it passes through the heating and cooling section, respectively. The experiments of Heydarian et al. show that the PCMS can enhance heat transfer by 6%–44%, thus contributing to its large latent heat and disturbance to the fluid flow (Heydarian et al., 2019). Moreover, PCMS can effectively prevent the dry-out compared to single-phase coolants, which stabilizes the operation of heat pipes under the high heat flux. However, the EPCM leads to higher thermal resistance and viscosity, so there is an optimal concentration at which the thermal resistance of the slurry is the highest. Once the concentration exceeds this optimal concentration, boiling deterioration is observed.
Flow in Pipe
As an important component of numerous heat exchangers, enhancing the heat transfer of flow in the pipe/tube by PCMS is of great potential. By comparing the heat transfer of PCMS and water in tubes under different working conditions, Zhang et al. found that the disadvantage of PCMS’s high viscosity plays a dominant role in the laminar flow condition. Thus, the heat transfer coefficient of PCMS in the pipe is even lower than that of single-phase coolant at the low Re number. In the turbulent flow, although the heat transfer can be improved by PCMS, the enhancement shows a strong correlation with the flow rate, which is dominated by the heat load. Although the high viscosity increases the pumping power required for pipe flow, the required flow rate is reduced, the pump energy can be reduced by more than 60% (Chen et al., 2008). However, with the continuous increase of Re, insufficient time for phase transition of PCM is observed, and the heat absorption capacity of PCMS is weakened (Zhang et al., 2018; Zhang et al., 2021).
Summary
The PCMS shows great potential in effective cooling having a huge advantage of maintaining a stable temperature. Some advantages and common challenges of PCMS for liquid cooling can be summed up according to the present literature. The PCMS can thus enhance the heat transfer greatly by storing the absorbed energy as latent heat, especially under high heat flux conditions. But, the performance is limited by the working condition. On the one hand, the competition among high specific surface area, high thermal resistance, and high viscosity attributing to encapsulation lead to an optimum concentration of EPCM in the base fluid. Although the optimal value is mainly determined by experiments, further theoretical studies are needed. Moreover, the application of PCMS in narrow channels and laminar flow is hindered by high thermal resistance and high viscosity, and the heat transfer deteriorates in some conditions. Although the thermal conductivity and fluidity of PCMS can be improved by nanoparticles and active agents, this approach is limited because nanoparticles also increase the viscosity of the slurry (Zhang et al., 2018). On the other hand, the heat absorption of EPCM depends on the phase change process that occurs only under certain temperature conditions. Thus, the choice of PCMS depends on specific working conditions, and the prediction of the heat transfer coefficient is a challenge.
Conclusion
Current studies have proven that PCMS can achieve higher efficiency than single-phase coolants in heat dissipation, especially under high heat flux conditions, which is of great significance in solving the problem of heat dissipation of electronic devices while reducing the energy consumption. However, PCMS is valid only under a certain range of flow velocity, temperature, and concentration due to additional thermal resistance, high viscosity, and supercooling. Several approaches have been proposed to enhance the performance of PCMS. From the aspect of fabrication, microfluidics with a 100% encapsulation efficiency represents a promising route for producing high quality EPCM in a controllable way. From the aspect of an application, nanoparticles and an active agent can improve the thermal conductivity and fluidity of PCMS, respectively. There are three possible directions for the future development of PCMS. First, a high-throughput and controllable microfluidic method for the fabrication of EPCM can improve the quality and stability of PCMS. Second, an efficient and compatible base fluid with high thermal conductivity and liquidity is beneficial in the extensive application of PCMS. Finally, the prediction of an optimal working condition based on experimental tests and theoretical analysis is essential for the design of cooling devices utilizing PCMS.
Author Contributions
FY contributed to the conception of the study. HC wrote the first draft of the manuscript. All authors contributed to the manuscript revision, and have read and approved the submitted version.
Funding
This work is supported by the National Natural Science Foundation of China (No. 51906170).
Conflict of Interest
The authors declare that the research was conducted in the absence of any commercial or financial relationships that could be construed as a potential conflict of interest.
Publisher’s Note
All claims expressed in this article are solely those of the authors and do not necessarily represent those of their affiliated organizations, or those of the publisher, the editors, and the reviewers. Any product that may be evaluated in this article, or claim that may be made by its manufacturer, is not guaranteed or endorsed by the publisher.
References
Akamatsu, K., Ogawa, M., Katayama, R., Yonemura, K., and Nakao, S.-i. (2019). A Facile Microencapsulation of Phase Change Materials within Silicone-Based Shells by Using Glass Capillary Devices. Colloids Surfaces A Physicochem. Eng. Aspects 567, 297–303. doi:10.1016/j.colsurfa.2019.01.076
Chen, B., Wang, X., Zeng, R., Zhang, Y., Wang, X., Niu, J., et al. (2008). An Experimental Study of Convective Heat Transfer with Microencapsulated Phase Change Material Suspension: Laminar Flow in a Circular Tube under Constant Heat Flux. Exp. Therm. Fluid Sci. 32 (8), 1638–1646. doi:10.1016/j.expthermflusci.2008.05.008
Chen, Y., and Deng, Z. (2017). Hydrodynamics of a Droplet Passing Through a Microfluidic T-Junction. J. Fluid Mech. 819, 401–434. doi:10.1017/jfm.2017.181
Chen, Y., Liu, X., and Shi, M. (2013). Hydrodynamics of Double Emulsion Droplet in Shear Flow. Appl. Phys. Lett. 102 (5), 051609. doi:10.1063/1.4789865
Eberhardt, A., Bošković, D., Loebbecke, S., Panić, S., and Winter, Y. (2019). Customized Design of Scalable Microfluidic Droplet Generators Using Step‐Emulsification Methods. Chem. Eng. Technol. 42 (10), 2195–2201. doi:10.1002/ceat.201900143
Fu, Z., Su, L., Li, J., Yang, R., Zhang, Z., Liu, M., et al. (2014). Elastic Silicone Encapsulation of N-Hexadecyl Bromide by Microfluidic Approach as Novel Microencapsulated Phase Change Materials. Thermochim. Acta 590, 24–29. doi:10.1016/j.tca.2014.06.008
Ghoghaei, M. S., Mahmoudian, A., Mohammadi, O., Shafii, M. B., Jafari Mosleh, H., Zandieh, M., et al. (2020). A Review on the Applications of Micro-/Nano-encapsulated Phase Change Material Slurry in Heat Transfer and Thermal Storage Systems. J. Therm. Anal. Calorim. 145 (2), 245–268. doi:10.1007/s10973-020-09697-6
Hao, G., Yu, C., Chen, Y., Liu, X., and Chen, Y. (2022). Controlled Microfluidic Encapsulation of Phase Change Material for Thermo-Regulation. Int. J. Heat Mass Transf. 190, 122738. doi:10.1016/j.ijheatmasstransfer.2022.122738
Heydarian, R., Shafii, M. B., Rezaee Shirin-Abadi, A., Ghasempour, R., and Alhuyi Nazari, M. (2019). Experimental Investigation of Paraffin Nano-Encapsulated Phase Change Material on Heat Transfer Enhancement of Pulsating Heat Pipe. J. Therm. Anal. Calorim. 137 (5), 1603–1613. doi:10.1007/s10973-019-08062-6
Joseph, M., and Sajith, V. (2019). An Investigation on Heat Transfer Performance of Polystyrene Encapsulated N-Octadecane Based Nanofluid in Square Channel. Appl. Therm. Eng. 147, 756–769. doi:10.1016/j.applthermaleng.2018.10.120
Li, S., Zhang, H., Cheng, J., Li, X., Cai, W., Li, Z., et al. (2019). A State-Of-The-Art Overview on the Developing Trend of Heat Transfer Enhancement by Single-phase Flow at Micro Scale. Int. J. Heat Mass Transf. 143, 118476. doi:10.1016/j.ijheatmasstransfer.2019.118476
Malekipirbazari, M., Sadrameli, S. M., Dorkoosh, F., and Sharifi, H. (2014). Synthetic and Physical Characterization of Phase Change Materials Microencapsulated by Complex Coacervation for Thermal Energy Storage Applications. Int. J. Energy Res. 38 (11), 1492–1500. doi:10.1002/er.3153
Moreno, P., Miró, L., Solé, A., Barreneche, C., Solé, C., and Martorell, I. (2014). Corrosion of Metal and Metal Alloy Containers in Contact with Phase Change Materials (PCM) for Potential Heating and Cooling Applications. Appl. Energy 125, 238-245. doi:10.1016/j.apenergy.2014.03.022
Park, J., Jung, J. H., Park, K., Destgeer, G., Ahmed, H., Ahmad, R., et al. (2018). On-Demand Acoustic Droplet Splitting and Steering in a Disposable Microfluidic Chip. Lab. Chip 18 (3), 422–432. doi:10.1039/c7lc01083d
Rajabifar, B. (2015). Enhancement of the Performance of a Double Layered Microchannel Heatsink Using PCM Slurry and Nanofluid Coolants. Int. J. Heat Mass Transf. 88, 627–635. doi:10.1016/j.ijheatmasstransfer.2015.05.007
Sabbah, R., Seyed-Yagoobi, J., and Al-Hallaj, S. (2012). Heat Transfer Characteristics of Liquid Flow with Micro-encapsulated Phase Change Material: Experimental Study. J. Heat Transf. 134 (4), 044501. doi:10.1115/1.4005311
Shi, Z., Lai, X., Sun, C., Zhang, X., Zhang, L., Pu, Z., et al. (2020). Step Emulsification in Microfluidic Droplet Generation: Mechanisms and Structures. Chem. Commun. 56 (64), 9056–9066. doi:10.1039/d0cc03628e
Sinha-Ray, S., Sinha-Ray, S., Sriram, H., and Yarin, A. L. (2014). Flow of Suspensions of Carbon Nanotubes Carrying Phase Change Materials through Microchannels and Heat Transfer Enhancement. Lab. Chip 14 (3), 494–508. doi:10.1039/c3lc50949d
Srinivasaraonaik, B., Singh, L. P., Tyagi, I., Rawat, A., and Sinha, S. (2020). Microencapsulation of a Eutectic PCM Using In Situ Polymerization Technique for Thermal Energy Storage. Int. J. Energy Res. 44 (5), 3854–3864. doi:10.1002/er.5182
Wan, H., He, G. Q., Xue, Z. R., and Li, W. Q. (2021). Numerical Study and Experimental Verification on Spray Cooling with Nanoencapsulated Phase-Change Material Slurry (NPCMS). Int. Commun. Heat Mass Transf. 123, 105187. doi:10.1016/j.icheatmasstransfer.2021.105187
Wang, J.-X., Yu, W., Wu, Z., Liu, X., and Chen, Y. (2022). Physics-Based Statistical Learning Perspectives on Droplet Formation Characteristics in Microfluidic Cross-Junctions. Appl. Phys. Lett. 120 (20), 204101. doi:10.1063/5.0086933
Wang, J., Gao, W., Zhang, H., Zou, M., Chen, Y., and Zhao, Y. (2018). Programmable Wettability on Photocontrolled Graphene Film. Sci. Adv. 4 (9), eaat7392. doi:10.1126/sciadv.aat7392
Wang, Y., Chen, Z., and Ling, X. (2016). An Experimental Study of the Latent Functionally Thermal Fluid with Micro-encapsulated Phase Change Material Particles Flowing in Microchannels. Appl. Therm. Eng. 105, 209–216. doi:10.1016/j.applthermaleng.2016.05.159
Wu, W., Bostanci, H., Chow, L. C., Ding, S. J., Hong, Y., Su, M., et al. (2011). Jet Impingement and Spray Cooling Using Slurry of Nanoencapsulated Phase Change Materials. Int. J. Heat Mass Transf. 54 (13-14), 2715–2723. doi:10.1016/j.ijheatmasstransfer.2011.03.022
Zhang, C., Li, J., and Chen, Y. (2020). Improving the Energy Discharging Performance of a Latent Heat Storage (LHS) Unit Using Fractal-Tree-Shaped Fins. Appl. Energy 259, 114102. doi:10.1016/j.apenergy.2019.114102
Zhang, G., Cui, G., Dou, B., Wang, Z., and Goula, M. A. (2018). An Experimental Investigation of Forced Convection Heat Transfer with Novel Microencapsulated Phase Change Material Slurries in a Circular Tube under Constant Heat Flux. Energy Convers. Manag. 171, 699–709. doi:10.1016/j.enconman.2018.06.029
Zhang, J. J., Yang, C. H., Jin, Z. G., Ma, S. X., Zhang, J. S., and Pang, X. M. (2021). Experimental Study of Jet Impingement Heat Transfer with Microencapsulated Phase Change Material Slurry. Appl. Therm. Eng. 188, 116588. doi:10.1016/j.applthermaleng.2021.116588
Keywords: PCM, encapsulation, phase change microcapsule slurry, microfluidic, electronic cooling
Citation: Cao H and Yao F (2022) Opinions on Fabrication of Phase Change Microcapsule Slurry and Its Application in Electronic Cooling. Front. Energy Res. 10:945360. doi: 10.3389/fenrg.2022.945360
Received: 16 May 2022; Accepted: 03 June 2022;
Published: 14 July 2022.
Edited by:
Xiao Chen, Beijing Normal University, ChinaReviewed by:
Takaichi Watanabe, Okayama University, JapanCopyright © 2022 Cao and Yao. This is an open-access article distributed under the terms of the Creative Commons Attribution License (CC BY). The use, distribution or reproduction in other forums is permitted, provided the original author(s) and the copyright owner(s) are credited and that the original publication in this journal is cited, in accordance with accepted academic practice. No use, distribution or reproduction is permitted which does not comply with these terms.
*Correspondence: Feng Yao, eWFvZmVuZ0B1c3RzLmVkdS5jbg==