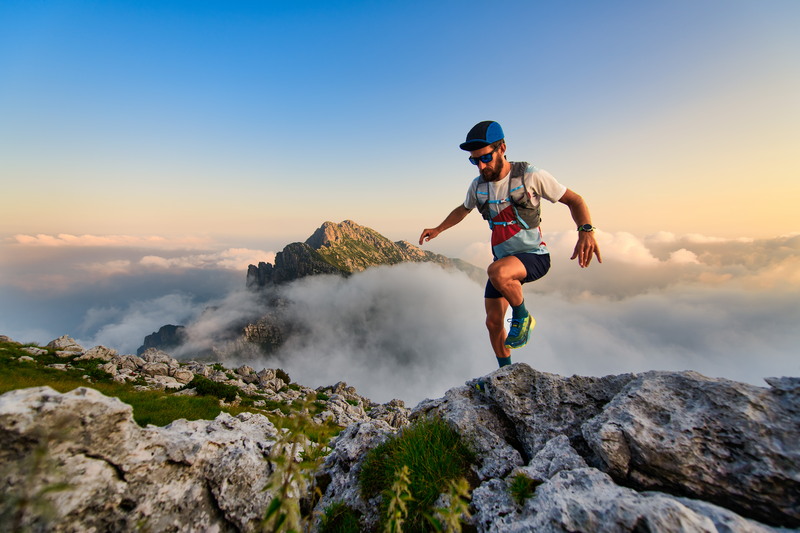
95% of researchers rate our articles as excellent or good
Learn more about the work of our research integrity team to safeguard the quality of each article we publish.
Find out more
ORIGINAL RESEARCH article
Front. Energy Res. , 18 July 2022
Sec. Nuclear Energy
Volume 10 - 2022 | https://doi.org/10.3389/fenrg.2022.928693
This article is part of the Research Topic Experimental and Numerical Studies on Liquid Metal Cooled Fast Reactors View all 17 articles
Because of their high molecular heat conductivity, low-Prandtl number liquid metal is a promising candidate coolant for various designs of advanced nuclear systems such as liquid metal–cooled fast reactors and accelerator-driven sub-critical system (ADS). With the fast-growing computational capacity, more and more attention has been paid to applying computational fluid dynamics (CFD) methods in thermal design and safety assessment of such systems for a detailed analysis of three-dimensional thermal–hydraulic behaviors. However, numerical modeling of turbulent heat transfer for low-Prandtl number liquid metal remains a challenging task. Numerical approaches such as wall-resolved large eddy simulation (LES) or direct numerical simulation (DNS), which can provide detailed insight into the physics of the liquid metal flow and the associated heat transfer, were widely applied to investigate the turbulent heat transfer phenomenon. However, these approaches suffer from the enormous computational consumption and are hence limited only to simple geometrical configurations with low to moderate Reynolds numbers. The Reynolds-averaged Navier–Stokes (RANS) approach associated with a turbulent Prandtl number
1) Proposal of a new model for the turbulent Prandtl number in the RANS approach for engineering applications.
2) Validation of the proposed model with available LES/DNS results of the local temperature profile in the concentric annulus and bare rod bundle.
3) Validation of the proposed model with experimental correlations on the Nusselt number in a circular tube and bare rod bundle.
Low-Prandtl number liquid metals are considered as promising candidate coolants in various innovative nuclear systems, such as the sodium-cooled fast reactor (SFR), the liquid lead–cooled fast reactor (LFR), and the accelerator-driven sub-critical system (ADS), due to their high molecular heat conductivity in favor of the reactors’ reliability and safety (Roelofs, 2019). With the fast development of computational power, more and more attention has been paid to applying the computational fluid dynamics (CFD) methods for detailed analysis of three-dimensional thermal–hydraulic behavior, especially in nuclear fuel assembly design (Cheng and Tak, 2006b; Marinari et al., 2019; Chai et al., 2019). However, modeling of turbulent heat flux in low-Prandtl number liquid metal flow remains a challenging task when using CFD methods to solve the turbulent flow heat transfer behavior (Shams, 2019). Advanced high-fidelity numerical approaches represented by the wall-resolved large eddy simulation (LES) method and the direct numerical simulation (DNS) method can provide detailed insight into the physics of the flow and the associated heat transfer (Tiselj et al., 2019). However, these approaches are limited to simple flow configurations and low to moderate Reynolds numbers due to their rather high requirement of computational capacities. Hence, Reynolds-averaged Navier–Stokes (RANS) method is still at least in the current state, in most cases, the only practically feasible approach to deal with high Reynolds industrial flows, especially those in complex geometries such as those encountered in typical nuclear fuel assemblies (Shams et al., 2019). It is thus important to assess and improve the accuracy of the RANS approach and the associated models for turbulent heat transfer. With this objective in mind, simulation results of the velocity and temperature field obtained by LES or DNS are, hence, very valuable references to which RANS models can be compared and calibrated.
Compared to conventional fluids with the Prandtl number in the order of unity, such as water or air, heat transfer in the low-Prandtl number liquid metal is characterized by the high contribution of molecular heat conduction even in high turbulent flow. Consequently, temperature change in the boundary layer is much smoother, even in the very thin laminar sub-layer. In the classical RANS approach with conventional turbulence models, turbulent heat transfer is often predicted solely from the knowledge of turbulent momentum transfer based on the concept of the so-called Reynolds analogy (Cheng and Tak, 2006a), in which the turbulent heat conductivity
It is well acknowledged that an accurate prediction of
In the past, extensive studies were carried out to derive appropriate expressions for
The models of Reynolds (1975).
Also, the model of Jischa and Rieke (1979).
The model by Cheng and Tak (2006b).
in which the constant A is given as:
The second type gives
where the turbulent Peclet number Pet is defined as:
Figure 1 compares the
FIGURE 1. Comparison of turbulent Prandtl numbers obtained with different models (molecular Prandtl Pr = 0.01).
With the fast-growing computational capacities, advanced high-fidelity numerical approaches such as wall-resolved LES method and DNS method become more and more attractive to provide detailed insight into the physics of the flow and the associated heat transfer. Due to their high demands of computational capacities, LES and DNS simulations are often, at least in the current state, limited to rather simple geometrical configurations. Nevertheless, simulation results of LES and DNS are very valuable references to which RANS models can be compared and calibrated. In the current study, LES and DNS results of a simple fully developed forced turbulent channel flow of low-Prandtl number fluid
As depicted in Figure 2, a fully developed forced turbulent channel flow of low-Prandtl number fluid heated by a uniform heat flux
FIGURE 2. Sketch of the fully developed forced turbulent channel flow heated by a uniform heat flux
TABLE 1. Summary of LES/DNS simulation on fully developed turbulent channel flow for low-Prandtl number fluid.
in which the friction velocity
where
which is then used to define the bulk Reynolds number
The bulk Peclet number
Also included in Table 1 is the global heat transfer performance characterized by the bulk Nusselt number
where the bulk temperature
For the purpose of assessing RANS approach, DNS results of Kawamura et al. (1999) with
As depicted in Figure 3, a quasi-2D RANS simulation of the fully developed channel flow was performed in the current study with the commercial CFD software package Ansys CFX. An arbitrary channel half height
FIGURE 3. Sketch of the mesh structure and boundary conditions used in RANS simulation of the fully developed forced turbulent channel flow.
Table 2 summarizes the most important boundary parameters of the RANS simulations performed in the current study. The flow is assumed to be incompressible with constant thermal–physical properties as in consistency with the LES/DNS settings. The governing equations are the RANS equations for incompressible flow with constant thermal–physical properties and the energy conservation equation for temperature. Due to the periodic boundary condition in the streamwise direction and the constant wall heat flux on the top and bottom walls, the temperature will continuously increase in the streamwise direction and a fully developed flow condition will never be achieved. Therefore, a negative volumetric heat source was specified in the RANS simulation, which takes exactly the same amount of energy away as given to the domain by the heat flux on the top and bottom walls. High-resolution advection scheme and turbulence numerics were chosen to ensure a second order accuracy. The buoyancy effect due to the temperature difference in the channel height direction (y-direction) is negligibly small, hence not considered in the RANS simulations. This is justified by the fact that the bulk Richardson number
TABLE 2. Summary of boundary parameters for RANS simulations of fully developed forced turbulent channel flow for low-Prandtl number fluid.
where
The mean streamwise velocity profile and mean temperature profile in the channel height direction (y-direction) are normalized with the friction velocity
where
The mean streamwise velocity profile is hence characterized by the normalized dimensionless mean velocity
The mean temperature profile is characterized by the normalized dimensionless mean temperature
where
where y is the actual distance to the wall.
As also included in Figure 3, a block-structured mesh consisting of only hexahedra was used in RANS simulations. The mesh nodes are uniformly distributed among the streamwise direction (x-direction), while local refinement was specified in the y-direction when approaching the top and bottom wall, in order to ensure at least a dimensionless universal wall distance of the first interior node
Figure 4 compares the normalized mean streamwise velocity profile (
FIGURE 4. Mesh sensitivity study: comparison of the (A) mean velocity profile and (B) mean temperature profile normalized in a friction unit obtained with different meshes.
Two types of turbulence models are available in CFX, that is, the wall-resolved low-Reynolds number turbulence model with which the boundary layer is fully resolved, and the wall-unresolved high-Reynolds number turbulence model with which the boundary layer is approximated relying on a logarithmic wall function. For the present analysis, the wall-resolved
FIGURE 5. Effect of different turbulence models on (A) mean velocity and, (B) mean temperature profile in friction unit.
To study the effect of the turbulent Prandtl number
1) Compared to conventional fluid with the Prandtl number in the order of unity, for which the linear law is valid only in the very thin laminar sub-layer of
2) As
FIGURE 6. RANS approach with varying turbulent Prandtl numbers: (A) effect on normalized mean temperature; (B) effect on bulk Nusselt number.
In order to obtain the optimum value of
The aforementioned approach to determine the optimum value of
FIGURE 7. Development of a new model of the turbulent Prandtl number for RANS with LES/DNS results in turbulent channel flow as a reference.
It is observed that
1) Apparently, the turbulent Prandtl number
2) Furthermore,
3) More importantly, the fact that
4) Therefore, the following simple model for
5) Since the proposed new model in Eq. 21 was derived based on LES/DNS results, the validity range of the new model should be limited to the range as specified in LES/DNS simulations as summarized in Table 1. Therefore, the validity range of
For assessment of the proposed model for the turbulent Prandtl number, RANS simulation was performed with
FIGURE 8. Assessment of the proposed model for the turbulent Prandtl number with DNS results for Pr = 0.025 at Reτ = 395, and for Pr = 0.01 at Reτ = 180: comparison of the mean temperature profile normalized in a friction unit.
The general strategy for validation of the proposed new model for the turbulent Prandtl number for the RANS approach is divided into the following two phases:
1) Phase I: taking LES/DNS results on the local temperature profile in the concentric annulus and bare rod bundle heated by constant uniform heat flux as a reference, with which RANS simulations results with the new model for
2) Phase II: LES/DNS simulations in the concentric annulus and bare rod bundle can provide detailed information about the local temperature profile, but are only available to a rather low-Reynolds number and Peclet number due to the enormous computational requirement. From the engineering point of view, the most important parameter to be considered is the heat transfer behavior in terms of the bulk Nusselt number
As the first step of the validation process phase I, a concentric annular channel heated on both walls as depicted in Figure 9A was considered due to its closeness to the sub-channel in a bare rod bundle (Ma et al., 2012). LES/DNS simulations on the fully developed state of turbulent heat transfer in the annular channel were performed at
FIGURE 9. (A) Sketch of a concentric annular channel heated uniformly on both walls and (B) mesh used in the RANS simulations.
Following the LES setting, RANS simulation was performed with the
Figure 10 shows the fully developed normalized mean temperature profile in the radial direction of the annular channel. The wall distance was determined relative to the inner wall and the mean temperature was also normalized with friction temperature and wall temperature on the inner wall. It is observed that the temperature profile obtained by the RANS simulation with the new model for
FIGURE 10. Validation of the proposed model on turbulent Prandtl number: a heated concentric annular channel.
A further validation of the proposed new model for the turbulent Prandtl number was performed in a loosely spaced bare rod bundle, for which wall-resolved large eddy simulation (LES) on the fully developed state of turbulent heat transfer with liquid lead at an operating temperature of 440°C (corresponding to a
FIGURE 11. (A) Sketch of a hexagonal rod bundle heated uniformly on walls and (B) mesh used in the RANS simulations.
Figure 12 compares, then, the fully developed temperature profile in the gap region of the two sub-channels (as indicated with a red arrow in Figure 11A). It is observed that the temperature profile obtained by RANS simulation with the new model for
FIGURE 12. Validation of the proposed model on the turbulent Prandtl number: a hexagonal rod bundle.
The first step of validation phase II was performed in a circular tube, for this geometry has been studied intensively from an experimental point of view. Many correlations on the turbulent heat transfer behavior (in terms of the bulk Nusselt number
1) Correlation of Lyon (1949), Lyon (1951) as an upper limit for the bulk Nusselt number.
2) Correlation of Kutateladze et al. (1959) as a lower limit for the bulk Nusselt number.
3) Correlation of Notter and Sleicher (1972) as the best general applicable correlation for all the investigated liquid metals including sodium (Na) and sodium–potassium alloys (NaK), pure lead (Pb), and lead–bismuth eutectic (LBE) as well as pure mercury (Hg).
It should be noted that all the aforementioned correlations were proposed for the thermal boundary condition of the uniform wall heat flux and have been developed for fully developed turbulent flow conditions with bulk Reynolds numbers
FIGURE 13. (A) Sketch of a tube heated uniformly on the wall; (B) and (C) mesh used in the RANS simulations.
Figure 14 compares then the bulk Nusselt number
In the second step of validation phase II, a bare rod bundle in the hexagonal arrangement was investigated, for which most of the experiments were performed in hexagonal arrays or bundles (OECD, 2015). Based on a review of available experimental data, the following three correlations were chosen as references. All the correlations express the bulk Nusselt number
1) Correlation of Gräber and Rieger (1972).
2) Correlation of Ushakov et al. (1977).
3) Correlation of Mikityuk (2009).
It should be noted, that the aforementioned Eqs. 25–27 were developed based on the experimental data of alkali metals such as liquid sodium (Na) or sodium–potassium alloy (NaK). However, as reviewed by Mikityuk (2009), the three correlations were recommended in the OECD Handbook on the heavy liquid metal (OECD, 2015) as the most relevant engineering heat transfer correlations for heavy liquid metal flows, that is, LBE or liquid lead. Similar to the correlations proposed for a circular tube, the aforementioned three correlations for the bare rod bundle are defined for the fully developed state. Table 3 summarizes the validity range of the respective correlations in terms of the pitch-to-diameter ratio and bulk Peclet number. However, it should be noted that in the review conducted by Mikityuk (2009), all the three correlations were recommended for use in the range of
TABLE 3. Summary of experimental correlations on the bulk Nusselt number in a bare rod bundle of the hexagonal arrangement for the low-Prandtl number liquid metal.
Figure 15A defines the geometry investigated in the current study, where a triangular bundle configuration is shown. One-sixth of a sub-channel (a colored region in the figure) was defined as a computational domain, in which a block-structured hexahedral mesh was defined (Figure 15B). The definition of the boundary conditions was specified in Figure 15C. The rod was defined as a no-slip wall with a constant uniform heat flux, while the symmetry boundary condition was imposed on the other three side planes. In order to achieve a fully developed state, a domain length of 300 times of the hydraulic diameter was given in the flow direction. Constant uniform velocity and temperature were specified in the inlet boundary and a constant pressure condition was defined at the outlet boundary. LBE with constant thermal–physical properties (corresponding Prandtl number is 0.025) was chosen as a working fluid. In the current study, four pitch-to-diameter ratios
FIGURE 15. (A) Sketch of a bare rod bundle uniformly on the wall; (B) mesh used in the RANS simulations. (C) boundary conditions is the RNAS simulations; (D) sketch of the streamwise domain length.
Figures 16A–D compare, then, the bulk Nusselt number obtained by RANS simulations with that given by the experimental correlations Eqs. 25–27 for
1) The same trend of the bulk Nusselt number
2) For the tight-spaced bundle of
3) However, the situation is much different for the loosely spaced rod bundle of
FIGURE 16. Validation of the proposed model on turbulent Prandtl number: bare rod bundle of P/D ratio equals (A) 1.1; (B) 1.2; (C) 1.3 and (D) 1.5.
In this study, LES/DNS simulation results of a fully developed forced turbulent channel flow up to
1) Heat transfer characteristics of the low-Prandtl number liquid metal depend strongly on the turbulent Prandtl number
2) Taking the LES/DNS simulation results of the fully developed forced turbulent channel flow as a reference, the RANS approach with the turbulent Prandtl number concept was assessed. It was found that the optimum value of
3) Based on the aforementioned relation between
4) To summarize, it could be concluded that the RANS approach with the simple concept of a constant global turbulent Prandtl number
The raw data supporting the conclusions of this article will be made available by the authors, without undue reservation.
XH—writing–original draft preparation; methodology; investigation; data curation; visualization. BP—conceptualization; methodology; investigation; writing–original draft preparation; writing–review and editing; project administration; funding acquisition. XC—software; investigation; writing–review and editing YY—methodology; project administration; writing–review and editing.
This work was financially supported by the Natural Science Foundation of Guangdong Province (2021A1515010391).
The authors declare that the research was conducted in the absence of any commercial or financial relationships that could be construed as a potential conflict of interest.
All claims expressed in this article are solely those of the authors and do not necessarily represent those of their affiliated organizations, or those of the publisher, the editors, and the reviewers. Any product that may be evaluated in this article, or claim that may be made by its manufacturer, is not guaranteed or endorsed by the publisher.
Abe, H., Kawamura, H., and Matsuo, Y. (2004). Surface Heat-Flux Fluctuations in a Turbulent Channel Flow up to Reτ=1020 with Pr=0.025 and 0.71. Int. J. Heat Fluid Flow 25 (3), 404–419. doi:10.1016/j.ijheatfluidflow.2004.02.010
Aoki, S. (1963). A Consideration on the Heat Transfer in Liquid Metal. Tokyo, Japan: Bulletin of the Tokyo Institute of Technology, 63–73.
Bricteux, L., Duponcheel, M., Winckelmans, G., Tiselj, I., and Bartosiewicz, Y. (2012). Direct and Large Eddy Simulation of Turbulent Heat Transfer at Very Low Prandtl Number: Application to Lead-Bismuth Flows. Nucl. Eng. Des. 246, 91–97. doi:10.1016/j.nucengdes.2011.07.010
Chai, X., Liu, X., Xiong, J., and Cheng, X. (2019). Numerical Investigation of Thermal-Hydraulic Behaviors in a LBE-Cooled 19-pin Wire-Wrapped Rod Bundle. Prog. Nucl. Energy 119, 103044. In press, corrected proof, Available online 1 May 2019, Article 103044. doi:10.1016/j.pnucene.2019.103044
Cheng, X., and Tak, N.-I. (2006). Investigation on Turbulent Heat Transfer to Lead-Bismuth Eutectic Flows in Circular Tubes for Nuclear Applications. Nucl. Eng. Des. 236, 385–393. doi:10.1016/j.nucengdes.2005.09.006
Duponcheel, M., Bricteux, L., Manconi, M., Winckelmans, G., and Bartosiewicz, Y. (2014). Assessment of RANS and Improved Near-Wall Modeling for Forced Convection at Low Prandtl Numbers Based on LES up to Reτ=2000. Int. J. Heat Mass Transf. 75, 470–482. doi:10.1016/j.ijheatmasstransfer.2014.03.080
Graber, H., and Rieger, M. (1972). Experimentelle Untersuchung des Wärmebergangs an Flüssigmetalle (NaK) in parallel durchströmten Rohrbündeln bei konstanter und exponentieller Wärmeflussdichteverteilung. Atomkernenergie 19 (1), 23–40.
Jischa, M., and Rieke, H. B. (1979). About the Prediction of Turbulent Prandtl and Schmidt Numbers from Modeled Transport Equations. Int. J. Heat Mass Transf. 22, 1547–1555. doi:10.1016/0017-9310(79)90134-0
Kader, B. A. (1981). Temperature and Concentration Profiles in Fully Turbulent Boundary Layers. Int. J. Heat Mass Transf. 24, 1541–1544. doi:10.1016/0017-9310(81)90220-9
Kawamura, H., Abe, H., and Matsuo, Y. (1999). DNS of Turbulent Heat Transfer in Channel Flow with Respect to Reynolds and Prandtl Number Effects. Int. J. Heat Fluid Flow 20, 196–207. doi:10.1016/s0142-727x(99)00014-4
Kays, W. M. (1994). Turbulent Prandtl Number-Where Are We? J. Heat Transf. 116, 284–295. doi:10.1115/1.2911398
Kirillov, P., and Ushakov, P. A. (2001). Heat Transfer to Liquid Metals: Specific Features, Methods of Investigation, and Main Relationships. Therm. Eng. 48 (1), 50–59.
Kutateladze, S., Borishanskii, V., and Novikov, I. (1959). Heat Transfer in Liquid Metals. J. Nucl. Energy, Part B, React. Technol. 9 (1-4), 214–229. doi:10.1016/0368-3265(59)90177-x
Lyon, R. (1949). Forced Convection Heat Transfer Theory and Experiments with Liquid Metals. Oak Ridge, Tennessee: Oak Ridge National Laboratory.
Lyon, R. (1951). Liquid Metal Heat-Transfer Coefficients. Chem. Eng. Prog. 47 (2), 75–79. doi:10.1080/00223131.2014.980349
Lyu, Y., Ge, Z., and Zhao, P. (2015). Large Eddy Simulation for the Turbulent Heat Transfer of Liquid Metal in an Annulus. J. Univ. Sci. Technol. China 45 (11), 917–922. doi:10.3969/j.issn.0253-2778.2015.11.006
Ma, Z., Wu, Y., Qiu, Z., Tian, W., Su, G., and Qiu, S. (2012). An Innovative Method for Prediction of Liquid Metal Heat Transfer Rate for Rod Bundles Based on Annuli. Ann. Nucl. Energy 47, 91–97. doi:10.1016/j.anucene.2012.04.023
Marinari, R., Di Piazza, I., Tarantino, M., Angelucci, M., and Martelli, D. (2019). Experimental Tests and Post-test Analysis of Non-uniformly Heated 19-pins Fuel Bundle Cooled by Heavy Liquid Metal. Nucl. Eng. Des. 343, 166–177. doi:10.1016/j.nucengdes.2018.12.024
Marocco, L. (2018). Hybrid LES/DNS of Turbulent Forced and Aided Mixed Convection to a Liquid Metal Flowing in a Vertical Concentric Annulus. Int. J. Heat Mass Transf. 121, 488–502. doi:10.1016/j.ijheatmasstransfer.2018.01.006
Mikityuk, K. (2009). Heat Transfer to Liquid Metal: Review of Data and Correlations for Tube Bundles. Nucl. Eng. Des. 239 (4), 680–687. doi:10.1016/j.nucengdes.2008.12.014
Notter, R. H., and Sleicher, C. A. (1972). A Solution to the Turbulent Graetz Problem-III Fully Developed and Entry Region Heat Transfer Rates. Chem. Eng. Sci. 27 (11), 2073–2093. doi:10.1016/0009-2509(72)87065-9
OECD (2015). Handbook on Lead-Bismuth Eutectic Alloy and Lead Properties, Materials Compatibility, Thermal-hydraulics and Technologies. Paris, France No: OECD/NEA, 7268.
Reynolds, A. J. (1975). The Prediction of Turbulent Prandtl and Schmidt Numbers. Int. J. Heat Mass Transf. 18, 1055–1069. doi:10.1016/0017-9310(75)90223-9
Roelofs, F. (2019). “Chapter 1: Introduction to Liquid Metal Cooled Reactors,” in Thermal Hydraulics Aspects of Liquid Metal Cooled Nuclear Reactors. Editor F. Roelofs (Cambridge: Woodhead Publishing, Elsevier Ltd).
Shams, A. (2019). “Chapter 6.2.1 Turbulent Heat Transport,” in Thermal Hydraulics Aspects of Liquid Metal Cooled Nuclear Reactors. Editor F. Roelofs (Cambridge: Woodhead Publishing, Elsevier Ltd).
Shams, A., De Santis, A., Koloszar, L. K., Villa Oritz, A., and Narayanan, C. (2019). Status and Perspectives of Turbulent Heat Transfer Modelling in Low-Prandtl Number Fluids. Nucl. Eng. Des. 353, 110220. doi:10.1016/j.nucengdes.2019.110220
Shams, A., Mikuž, B., and Roelofs, F. (2018). Numerical Prediction of Flow and Heat Transfer in a Loosely Spaced Bare Rod Bundle. Int. J. Heat Fluid Flow 73, 42–62. doi:10.1016/j.ijheatfluidflow.2018.07.006
Tiselj, I., Flageul, C., and Oder, J. (2019). Direct Numerical Simulation and Wall-Resolved Large Eddy Simulation in Nuclear Thermal Hydraulics. Nucl. Technol. 206, 164–178. doi:10.1080/00295450.2019.1614381
Keywords: low-Prandtl number liquid metal, turbulent heat transfer, turbulent Prandtl number, RANS, CFD
Citation: Huang X, Pang B, Chai X and Yin Y (2022) Proposal of a turbulent Prandtl number model for Reynolds-averaged Navier–Stokes approach on the modeling of turbulent heat transfer of low-Prandtl number liquid metal. Front. Energy Res. 10:928693. doi: 10.3389/fenrg.2022.928693
Received: 26 April 2022; Accepted: 27 June 2022;
Published: 18 July 2022.
Edited by:
Wenzhong Zhou, Sun Yat-sen University, ChinaReviewed by:
Yaou Shen, Laboratory of Reactor System Design Technology (LRSDT), ChinaCopyright © 2022 Huang, Pang, Chai and Yin. This is an open-access article distributed under the terms of the Creative Commons Attribution License (CC BY). The use, distribution or reproduction in other forums is permitted, provided the original author(s) and the copyright owner(s) are credited and that the original publication in this journal is cited, in accordance with accepted academic practice. No use, distribution or reproduction is permitted which does not comply with these terms.
*Correspondence: Bo Pang, Ym8ucGFuZ0BzenUuZWR1LmNu
Disclaimer: All claims expressed in this article are solely those of the authors and do not necessarily represent those of their affiliated organizations, or those of the publisher, the editors and the reviewers. Any product that may be evaluated in this article or claim that may be made by its manufacturer is not guaranteed or endorsed by the publisher.
Research integrity at Frontiers
Learn more about the work of our research integrity team to safeguard the quality of each article we publish.