- 1Department of Chemical Engineering, Faculty of Engineering, University of Benin, Benin City, Nigeria
- 2Department of Chemical Engineering, Faculty of Engineering, Edo State University, Uzairue, Nigeria
- 3Department of Chemistry, Faculty of Physical Sciences, Ambrose Alli University, Ekpoma, Nigeria
The use of organic waste materials conjugated with inorganic sources as a bifunctional catalyst for one-step biodiesel production is currently under-utilized. In this study, a bifunctional catalyst for biodiesel production was developed from poultry droppings doped with ferric sulphate (FSPD). Its catalytic activity was investigated in simultaneous esterification and transesterification of neem seed oil (NSO) using methanol. Response Surface Methodology was employed in modelling and optimizing the reaction conditions. The characterization of the catalyst was done using Scanning Electron Microscopy equipped with Energy-Dispersive X-ray Spectroscopy, Fourier Transform Infrared Spectroscopy and X-ray Diffractometer. Fe (46.08 wt. %), S (22.31 wt. %), and Ca (11.82 wt. %) were the major elements present in the FSPD and the other results revealed that it is bifunctionally active. A biodiesel yield of 97.21% and acid value (AV) of 0.5 mg KOH/g were obtained at the optimum conditions of 21:1 methanol/oil ratio, 5 wt. %, catalyst loading and reaction temperature of 65°C after 180 min. The biodiesel produced using FSPD catalyst meets both the ASTM D6751 and the EN 14214 biodiesel standards. Reusability investigation of the FSPD showed remarkable stability up to the third reuse cycle with a slight decrease in biodiesel yield and a corresponding increase in acid value from 97.21% to 90.05% and 0.5–0.81 mg KOH/g respectively. The utilization of FSPD as a bifunctional catalyst is significant for improving the biodiesel output of high FFA oil and overall biodiesel production time.
1 Introduction
The global use of fossil fuels as a source of energy over the years has raised concerns due to its adverse effects on the environment and sustainability development goals. Biofuel currently being produced at an increasing rate is the best replacement for these fossil fuels (Shelke et al., 2016; Zareh et al., 2017; Ogunkunle and Ahmed, 2019; Anwar, 2021). Biofuels which are mainly biodiesel, bioethanol and biogas are fuels derived from organic matter or biomass. According to Sharma et al. (2008), these fuels are considered environmentally friendly due to a good number of reasons such as low pollutant emissions, easy biodegradability, and renewability.
Biodiesel is an alternative to petroleum-based diesel fuel and it is derived from the transesterification of vegetable oils or animal fats in the presence of an acidic or alkaline catalyst (Sekhar et al., 2009; Ogunkunle and Ahmed, 2019; Akhabue and Okwundu, 2019). Vegetable oils which are the major feedstock in biodiesel production are obtained from both edible and non-edible seed oils (Chhetri et al., 2008; Atabani et al., 2012). The use of edible oils for biodiesel production has posed serious concerns as it competes with food for man and animals, resulting in the projection of non-edible oils as a sustainable feedstock for biodiesel production (Mofijur et al., 2013a; Mofijur et al., 2013b; Mueanmas et al., 2019; Aarathi et al., 2019; Chang et al., 2020).
Recently, researchers have found that biodiesel derived from non-edible oils which are also called second-generation feedstock is a potential eco-friendly substitute for petroleum-based diesel fuel. It is much more cost-friendly and less food competitive compared to the biodiesel obtained from edible oils (Taufiq-Yap et al., 2011). One such non-edible oil is neem seed oil (NSO). NSO is extracted from the seeds of the neem plant (Azadirachta indica) and it contains about 30% oil content per seed (Karmakar et al., 2012; Demirbas et al., 2016).
One of the reasons why non-edible oils have not been extensively used for the production of biodiesel is because of the free fatty acid (FFA) content of these oils. Oils having an FFA content of more than 1% will require esterification (pretreatment) step before it is used for biodiesel production. This additional step has given rise to increased biodiesel production costs.
H2SO4 and ferric sulphate are very effective in reducing the high FFA of oil as homogeneous and heterogeneous acid catalysts respectively. While the H2SO4 catalyst has great efficiency in catalyzing the esterification reaction faster than the ferric sulphate counterpart, the ferric sulphate is preferred due to its ease of separation, corrosion mitigation, and ability to be used in mild conditions, (Wang et al., 2007).
Ferric sulphate, a non-organic material has been used as a conventional heterogeneous acid catalyst for biodiesel production by many researchers (Gan et al., 2010; Patil et al., 2010; Alhassan et al., 2013; Ganesan et al., 2020) and has been proven to be very effective over the years. Wang et al. (2007) studied the catalytic activity of ferric sulphate in a two-step biodiesel production from waste cooking oil having an acid value of 75.92 ± 0.036 mg KOH/g. The ferric sulphate catalyst was used in the first step, and the triglycerides (TGs) in WCO were transesterified in the second step using potassium hydroxide. The results showed that a 97.22% conversion rate of FFA was obtained when 2 wt. % of ferric sulphate was added to the reaction system containing a 10:1 methanol/oil ratio at the reaction temperature of 95°C for 4 h. This shows the high catalytic activity of ferric sulphate catalyst in esterifying the high free fatty acids content of the waste cooking oil. Ferric sulphate has also been reportedly used with supercritical methanol in the conversion of waste cooking oil to biodiesel (Patil et al., 2010). Falowo et al. (2019), successfully reduced the FFA of a neem/rubber seed oil blend (60:40) from 17.76% to 0.67% using ferric sulphate catalyst before microwave irradiation-assisted transesterification using nanoparticles from elephant-ear tree pod husk at the reaction conditions of 25:1 methanol/oil blend ratio, 10 wt. % catalyst dosage, 120 min reaction time and 65°C reaction temperature. This shows the efficiency of ferric sulphate in reducing the high FFA of oils for biodiesel production.
On the other hand, poultry droppings-derived catalyst has been proven to be very efficient in biodiesel production through transesterification and simultaneous esterification and transesterification respectively (Maneerung et al., 2016; Akhabue et al., 2020).
Sekhar et al. (2009), Akhabue et al. (2020) found the percentage of free fatty acid (FFA) in NSO to be high. While the former suggested esterification of the oil to reduce its FFA content, the latter developed a catalyst which could simultaneously reduce the FFA content of the oil as well as produce biodiesel from the oil. In simultaneous esterification and transesterification for biodiesel production, specific types of catalysts with both acid and base properties are used (Chaveanghong et al., 2018; Loures et al., 2018; Al-Saadi et al., 2020; Elias et al., 2020). Although several bifunctional catalysts have been used for simultaneous esterification and transesterification of oils, these catalysts are mainly synthesized from non-organic materials solely, and the processes of synthesizing these catalysts are complex (Zhang et al., 2013; Chaveanghong et al., 2018; Al-Saadin et al., 2020; Chang et al., 2020).
In this study, the catalytic activity of a dual organic and inorganic bifunctional catalyst in which the alkaline precursor was originally synthesized from poultry droppings and the acid precursor from ferric sulphate was investigated. The use of environmental wastes such as poultry droppings as raw materials for the synthesis of biodiesel catalysts checkmates the cost of purchasing expensive catalysts for biodiesel production since the only cost involved is that of calcination (Maneerung et al., 2016). Factors such as methanol/oil ratio, catalyst loading, reaction temperature and time which affect the output of biodiesel production processes were optimized using response surface methodology conjugated with central composite design (RSM-CCD) on Design-Expert software version 12.
RSM is a collection of mathematical and statistical techniques that is useful for the modelling and analysis of problems in which a response is influenced by several factors. In the last decades, it has been used by researchers for analysing and completing the optimization of processes from statistically designed experiments (Betiku, et al., 2014; Nayebzadeh et al., 2016; Moyo et al., 2021). It can explain the interaction of independent factors and their effects on the response(s).
Most works that have been carried out on the reusability of heterogeneous catalysts only consider the biodiesel yield with little or no mention of the acid value of the biodiesel produced using the recovered catalyst (Yin et al., 2016; Yusuff, 2019; Gnanaserkhar et al., 2020; Qu et al., 2021). The reusability of the FSPD was also investigated by monitoring the biodiesel yield and also measuring the acid values for four reused cycles.
2 Materials and Methods
2.1 Materials
The materials used include NSO, obtained from Nigeria Research Institute for Chemical Technology, Zaria, Nigeria. The physicochemical properties of the oil have previously been reported in the work conducted by Akhabue et al. (2020). Poultry droppings were obtained from a farmhouse near Benin City, Nigeria. The chemicals used in this study include ferric sulphate, methanol, benzene, chloroform, acetic acid, Wij’s solution, potassium hydroxide, ethanol, sodium sulphate, hydrochloric acid, phenolphthalein, potassium iodide, sulphuric acid, and phosphoric acid. All the chemicals used were of analytical grade and were obtained from Pyrex Chemicals in Benin City, Nigeria.
2.2 Preparation of Organic Alkaline Precursor From Poultry Droppings
The method used for the preparation of the organic alkaline precursor is a modified procedure described by Maneerung et al. (2016). The fresh poultry droppings collected were sundried for several days. It was then ground to a fine powder and carbonised at 280°C. The carbonised sample was later calcined in the muffle furnace for 6 h at a temperature of 900°C. The resultant solid was then removed and allowed to cool in the desiccator after which it was ground and kept in an air-tight container awaiting further use.
2.3 Synthesis of Ferric Sulphate Doped With Poultry Droppings Catalyst
To achieve the bi-functionality of the FSPD, the wet impregnation method used by Akhabue et al. (2020) for the synthesis of the bio-based bifunctional catalyst (BBFC) was adopted. The acid precursor (ferric sulphate) was impregnated with the organic alkaline precursor (poultry droppings) in a ratio of 2:3 by weight. Twenty grams (20 g) of the alkaline precursor was dissolved in a small quantity of distilled water and 30 g of ferric sulphate was added to the aqueous solution and stirred for several minutes until there was a complete mixing. The resultant slurry was placed on a magnetic stirrer with heat supplied at 100°C while stirring continuously until there was free evaporation of the distilled water leaving behind a solid mixture. The solid mixture was then oven-dried at 110°C. A preliminary investigation was carried out on the use of this catalyst for biodiesel production. The FSPD catalyst was divided into six parts. Five samples were thermally activated in the furnace at 100°C, 200°C, 300°C, 400°C, and 500°C while the remaining sample was not activated. After, activation, the catalysts were used for simultaneous esterification and transesterification of NSO. The maximum biodiesel yield was obtained from the reaction catalyzed by the catalyst that was not thermally activated as the rest gave low biodiesel yields and higher acid values. The non-thermally activated FSPD catalyst was subsequently used to catalyse the reaction.
2.4 Characterization of the Catalyst
The FSPD catalyst was characterised to determine its catalytic potential. The morphology of the catalyst and elemental compositions were determined using Scanning Electron Microscopy equipped with Energy Dispersive X-ray (SEM EDX) spectrometer (Phenom ProX). The SEM images were taken at a voltage of 15 kV. Fourier Transform Infrared (FTIR) measurements were also carried out on the catalyst in the absorbance mode ranging from 4,000 to 600 cm−1 to determine functional groups present in the catalyst. The crystalline compounds in the catalyst were determined using the PANanalytical Model Empyrean X-ray diffractometer (XRD) operated at 45 kV and 40 mA.
2.5 Experimental Design, Modelling and Optimization of Simultaneous Esterification and Transesterification Process
The effect of process factors; methanol/oil molar ratio
From the experimental results obtained, a mathematical model was developed by response surface regression by the use of the second-order polynomial shown in Eq. 1.
Where
The quality of fit of the mathematical model was checked using analysis of variance (ANOVA). The mathematical model was considered satisfactorily when the ANOVA data exhibited a high level of statistical significance. The contribution of the factors to the biodiesel yield was determined using the p-value from the ANOVA results. Further tests were also carried out to determine the suitability of the model and these tests include the coefficient of determination
2.6 Simultaneous Esterification and Transesterification of Neem Seed Oil
The simultaneous esterification and transesterification of NSO were carried out in a 500 ml two-neck round bottom flask that was equipped with a reflux condenser and a temperature probe, placed on a constant temperature magnetic stirrer (B. BRAN SCIENTIFIC & INSTRUMENT COMPANY, ENGLAND). A measured amount of the catalyst was added to a preheated 50 g NSO in the flask. The required amount of methanol containing the catalyst was then added to the NSO. In other to prevent the loss of methanol, the reflux condenser was used to prevent and re-condense any methanol escaping from the reacting mixture at higher temperatures close to and above 64.7°C back to the reacting mixture. The reaction time was set according to values generated by the CCD. The resulting product mixture was separated from the catalyst at the end of each run using a centrifuge machine (Jinotech Instruments 800D Centrifuge). Thereafter, the biodiesel was separated from the glycerol and the excess methanol from the reaction. After separation, the biodiesel was washed, dried and stored in an air-tight container according to the method used by Falowo et al. (2019). The biodiesel yield was determined using Eq. 2, while the acid value was determined using Eq. 3 (Gaurav et al., 2019).
Where
2.7 Catalyst Recovery and Reusability
At the end of the experimental runs, the optimum conditions for maximum biodiesel yield and the minimum acid value were obtained using numerical optimization. These conditions were later used for the production of biodiesel. After the reaction, the catalyst was separated from the product mixture by centrifuging. Ethanol and water were used to wash the recovered catalyst after which it was dried in an oven at 110°C overnight and it was ready to be reused.
3 Results and Discussion
3.1 Characterization of the Synthesized Catalyst
3.1.1 Surface Morphology and Elemental Composition of the Catalyst
The SEM image of the FSPD catalyst is shown in Figure 1. The FSPD possess fine pore spaces with an uneven distribution of internal porous spaces of a circular shaped network containing its active site. This uneven porous space distribution restricted the aggregation of the FSPD particles. The major metallic elements present in the FSPD and their compositions as shown in the EDX images (Figure 2) include Fe (46.08 wt. %), Ca (11.82 wt. %), and K (9.58 wt. %). Also noticed is the presence of the major non-metallic element S (22.31%) in high proportion. Silicon was also found to be present in the catalyst.
3.1.2 Functional Groups in the Catalyst
The FTIR spectra of the catalyst are presented in Figure 3. The weak peak at 3,608.1 cm−1 indicates the presence of a non-bonded hydroxyl (OH) group, while the medium peaks at 1,617.7 cm−1 can be attributed to the presence of a carbonyl (CO) group. The FTIR spectra for the catalyst also indicate the presence of a strong peak at 1,080.9 cm−1 which indicates the presence of a silicon-oxy group arising from Si-O-Si stretching. This further confirms the results obtained from the elemental composition of the catalyst.
3.1.3 Crystalline Compounds Present in the Catalyst
The XRD pattern for the catalyst as shown in Figure 4 was used to identify the crystalline compounds present in the FSPD. The peaks obtained at 11.57, 21.00, 28.61, 31.02, 33.4, 35.2, 40.43, 49.82, and 61.4 indicates the presence of Gypsum (CaSO4.2H2O). Jarosite (KFe3(SO4)2(OH)6) was also observed at 14.84, 17.35, 45.77, and 60.10.
3.2 Design of Experiments and Statistical Analysis by Response Surface Methodology
The statistical analysis of simultaneous transesterification and esterification of NSO catalysed with FSPD catalyst was carried out using the responses (biodiesel yield and acid value) inputted into the runs generated by the CCD. The experimental design matrix with the biodiesel yield and acid value obtained from the simultaneous esterification and transesterification of NSO catalysed with FSPD catalyst are shown in Table 2. From the results obtained, the range of biodiesel yield was 68.8%–97.99% and the minimum acid value obtained was
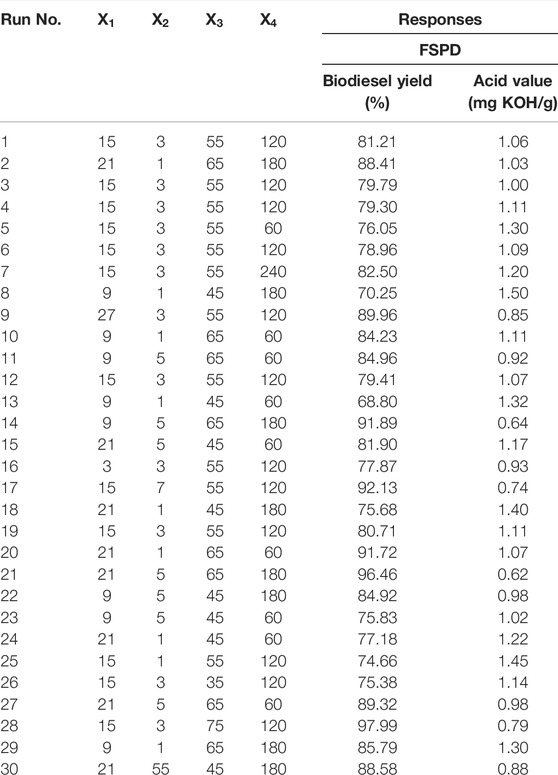
TABLE 2. Experimental design matrix for the simultaneous transesterification and esterification of NSO.
The statistical significance of the developed model was evaluated using the ANOVA for the response surface quadratic model and the results are presented in Table 3. The model was significant with an F value of 104.91. It was also observed that individual factors were significant based on their p-value < 0.0001. The temperature was found to have the greatest influence on the biodiesel yield based on the high F value (702.10). Based on the p-values shown on the ANOVA table, it was observed also that catalyst loading and temperature with catalyst loading and time were the significant interacting terms in the developed model. The model showed a “Lack of Fit F-value” of 1.50 indicating that the Lack of Fit is not significant relative to the pure error.
The fitness of the model was analysed using the fit statistics shown in Table 4. The obtained coefficient of determination
3.3 Effect of the Significant Interacting Variables on the Biodiesel Yield
The effect of the significant interacting variables on the biodiesel yield was investigated using the response surface plots shown in Figure 5. Figure 5A shows the interaction effect between the methanol: oil and catalyst loading. An increase in catalyst loading from 1 wt. % to 5 wt. % at constant temperature and time led to a corresponding increase in the biodiesel yield at methanol: oil of 9 mol/mol and 21 mol/mol respectively. This is a result of the availability of excess methanol in the reacting system to drive the reaction to completion, which in other words, gave way for unhindered penetration of the reactant into the active sites of the catalyst. A similar trend was observed for the interaction between methanol: oil and reaction temperature Figure 5B, and the interaction between methanol: oil and reaction time Figure 5C. This justifies the fact that excess of the limiting reactant (methanol) is required for the complete conversion of the neem seed oil to biodiesel. Figure 5D shows the effect of interaction between catalyst loading and reaction temperature on biodiesel yield. From the plots, it was observed that at the catalyst loading of 1 wt. %, increasing temperature from 45 to 65°C at constant methanol: oil and reaction time increases biodiesel yield. This could be attributed to the fact that increasing reaction temperature increases reaction rates. A similar increase in biodiesel yield was also observed when catalyst loading was increased from 1 wt. % to 5 wt. % and a significant increase in the biodiesel yield when both catalyst loading and temperature were simultaneously increased. This is attributable to the fact that an increase in temperature results in a corresponding increase in the energy of the reacting system thereby leading to the excitement of the catalytic active sites of the catalyst available for the reaction to take place. The interactive effects between catalyst loading and reaction time as shown in the response surface plots in Figure 5E show that increase in reaction time from 60 to 180 min while keeping the catalyst loading constant did not have a significant effect on the biodiesel yield. Increasing catalyst loading from 1 wt. % to 5 wt. % with reaction time kept constant resulted in a minimal increase in biodiesel yield. Furthermore, a significant increase in the biodiesel yield was observed with an increase in reaction temperature and reaction time respectively Figure 5F.
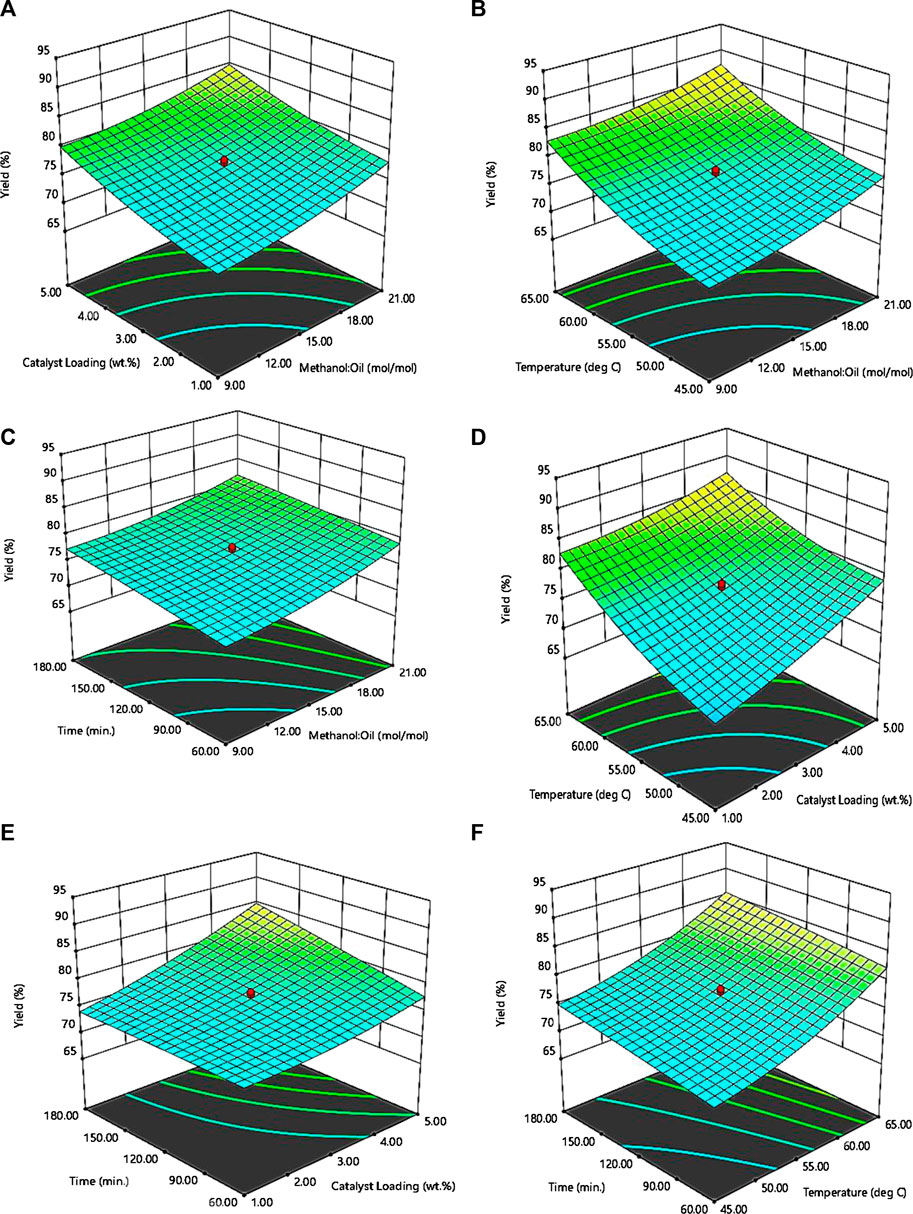
FIGURE 5. Response surface plots for biodiesel yield as a function of (A) methanol: oil and catalyst loading (B) methanol: oil and reaction temperature (C) methanol: oil and reaction time (D) catalyst loading and reaction temperature (E) catalyst loading and reaction time (F) reaction temperature and reaction time.
3.4 Optimization of the Reaction Conditions
Numerical optimization was used in optimizing the reaction conditions by maximizing the biodiesel yield as well as minimizing the acid value obtained. The reaction conditions that gave the maximum biodiesel yield of 96.08% and a maximum acid value of 0.61 mg KOH/g were 21:1 methanol:oil, 5 wt. % catalyst loading, 65°C reaction temperature with a reaction time of 180 min. Based on these optimal conditions, experimental runs were carried out in triplicate to validate the results, an average biodiesel yield of 97.21% and an acid value of 0.50 mg KOH/g were obtained. Table 4 shows a comparison between different catalysts used for simultaneous esterification and transesterification of different oils and their biodiesel yields.
3.5 Physicochemical Properties of the Biodiesel
The biodiesel produced at optimum reaction conditions was analysed for its physicochemical and fuel properties and the results obtained are shown in Table 5. From the results obtained, the properties of the biodiesel produced from both catalysed reactions were within the ASTM D6751 and EN 14214 biodiesel specifications.
The density and viscosity of 894 kg/m3 and 5.35 mm2/s of the produced biodiesel from neem seed oil using FSPD meets the required biodiesel standards. Similar results have been obtained by Betiku et al. (2014) (897 kg/m3 and 5.940 mm2/s), Policano et al. (2016) (897 kg/m3 and 5.9 mm2/s), Chaveanghong et al. (2018) (1.9–6.0 mm2/s), and Akhabue et al. (2020) (892 kg/m3 and 4.25 mm2/s). Similarly, the optimum acid value of the produced biodiesel using FSPD is reasonably low compared to other previous methods studied (Table 5).
3.6 Reusability of the Recovered Ferric Sulphate Doped With Poultry Droppings
The recovered catalyst was reused to ascertain its reusability and activity. The biodiesel yield and the acid value from each cycle of use are shown in Figure 6. From the results, there was a decrease in biodiesel yield from 97.21% to 90.78% after the first cycle of use. In subsequent use, the biodiesel yield experienced a slight insignificant decrease. The acid value show increase from the initial value of 0.50 mg KOH/g–0.81 mg KOH/g after the third cycle of use. Although the biodiesel yield obtained from the reuse of the recovered FSPD after three cycles were higher than 90%, the acid value however exceeded the biodiesel standard.
4 Conclusion
In this study, a ferric sulphate doped poultry droppings bifunctional catalyst (FSPD) for the simultaneous esterification and transesterification of high free fatty acid neem oil. Gypsum and jarosite were identified in the FSPD while the major element present are iron, calcium and sulphur (more than 20%). At optimum reaction conditions of 21:1 methanol/oil, 5 wt. % catalyst loading and 65°C reaction temperature after 180 min, an average biodiesel yield and an acid value of 97.21% and 0.50 mg KOH/g was obtained respectively. The physicochemical properties of the biodiesel produced using the synthesized catalyst were within the biodiesel ASTM and EN specifications. The reusability of the FSPD catalyst showed a slight decrease in biodiesel yield and a slight increase in acid value after three successive reuse. It can be concluded that the FSPD is efficient for biodiesel production from high free fatty acid oil and the reusability of the catalyst is effectively reliable.
Data Availability Statement
The original contributions presented in the study are included in the article/Supplementary Material, further inquiries can be directed to the corresponding author.
Author Contributions
Conception or design of the work: UU, EO-B, and CA. Data collection: CA, UU, and EO-B. Data analysis and interpretation: CA, UU, EO-B, SO, OI, and EO. Drafting the article: EO-B and CA. Critical revision of the article: CA, EO-B, SO, UU, OI, and EO. Final approval of the version to be published: CA, EO-B, UU, SO, OI, and EO.
Conflict of Interest
The authors declare that the research was conducted in the absence of any commercial or financial relationships that could be construed as a potential conflict of interest.
Publisher’s Note
All claims expressed in this article are solely those of the authors and do not necessarily represent those of their affiliated organizations, or those of the publisher, the editors and the reviewers. Any product that may be evaluated in this article, or claim that may be made by its manufacturer, is not guaranteed or endorsed by the publisher.
Supplementary Material
The Supplementary Material for this article can be found online at: https://www.frontiersin.org/articles/10.3389/fenrg.2022.927467/full#supplementary-material
References
Aarathi, V., Harshita, E., Nalinashan, A., Ashok, S., and Prasad, R. K. (2019). Synthesis and Characterisation of Rubber Seed Oil Trans-esterified Biodiesel Using Cement Clinker Catalysts. Int. J. Sustain. Energy 38 (4), 333–347. doi:10.1080/14786451.2017.1414052
Akhabue, C. E., and Okwundu, O. S. (2019). Monitoring the Transesterification Reaction of castor Oil and Methanol by Ultraviolet Visible Spectroscopy. Biofuels 10 (6), 729–736. doi:10.1080/17597269.2017.1338128
Akhabue, C. E., Osa-Benedict, E. O., Oyedoh, E. A., and Otoikhian, S. K. (2020). Development of a Bio-Based Bifunctional Catalyst for Simultaneous Esterification and Transesterification of Neem Seed Oil: Modeling and Optimization Studies. Renew. Energy 152, 724–735. doi:10.1016/j.renene.2020.01.103
Al-Saadi, A., Mathan, B., and He, Y. (2020). Biodiesel Production via Simultaneous Transesterification and Esterification Reactions over SrO-ZnO/Al2O3 as a Bifunctional Catalyst Using High Acidic Waste Cooking Oil. Chem. Eng. Res. Des. 162, 238–248. doi:10.1016/j.cherd.2020.08.018
Alhassan, F. H., Yunus, R., Rashid, U., Sirat, K., Islam, A., Lee, H. V., et al. (2013). Production of Biodiesel from Mixed Waste Vegetable Oils Using Ferric Hydrogen Sulphate as an Effective Reusable Heterogeneous Solid Acid Catalyst. Appl. Catal. A General 456, 182–187. doi:10.1016/j.apcata.2013.02.019
Anwar, M. (2021). Biodiesel Feedstocks Selection Strategies Based on Economic, Technical, and Sustainable Aspects. Fuel 283, 119204. doi:10.1016/j.fuel.2020.119204
Atabani, A. E., Silitonga, A. S., Badruddin, I. A., Mahlia, T. M. I., Masjuki, H. H., and Mekhilef, S. (2012). A Comprehensive Review on Biodiesel as an Alternative Energy Resource and its Characteristics. Renew. Sustain. Energy Rev. 16 (4), 2070–2093. doi:10.1016/j.rser.2012.01.003
Baroi, C., and Dalai, A. K. (2013). Simultaneous Esterification, Transesterification and Chlorophyll Removal from Green Seed Canola Oil Using Solid Acid Catalysts. Catal. Today 207, 74–85. doi:10.1016/j.cattod.2012.07.003
Betiku, E., Omilakin, O. R., Ajala, S. O., Okeleye, A. A., Taiwo, A. E., and Solomon, B. O. (2014). Mathematical Modeling and Process Parameters Optimization Studies by Artificial Neural Network and Response Surface Methodology: A Case of Non-edible Neem (Azadirachta indica) Seed Oil Biodiesel Synthesis. Energy 72, 266–273. doi:10.1016/j.energy.2014.05.033
Bojan, S. G., Chelladurai, S., Durairaj, S. K., and Kumaran, S. (2011). Response Surface Methodology for Optimization of Biodiesel Production from High FFA Jatropha Curcas Oil. Int. J. Green Energy 8 (6), 607–617. doi:10.1080/15435075.2011.600373
Chang, A., Pan, J.-H., Lai, N.-C., Tsai, M.-C., Mochizuki, T., Toba, M., et al. (2020). Efficient Simultaneous Esterification/transesterification of Non-edible Jatropha Oil for Biodiesel Fuel Production by Template-free Synthesized Nanoporous Titanosilicates. Catal. Today 356, 56–63. doi:10.1016/j.cattod.2019.10.006
Chaveanghong, S., Smith, S. M., Smith, C. B., Luengnaruemitchai, A., and Boonyuen, S. (2018). Simultaneous Transesterification and Esterification of Acidic Oil Feedstocks Catalyzed by Heterogeneous Tungsten Loaded Bovine Bone under Mild Conditions. Renew. Energy 126, 156–162. doi:10.1016/j.renene.2018.03.036
Chellappan, S., Nair, V., V., S., and K., A. (2018). Synthesis, Optimization and Characterization of Biochar Based Catalyst from Sawdust for Simultaneous Esterification and Transesterification. Chin. J. Chem. Eng. 26 (12), 2654–2663. doi:10.1016/j.cjche.2018.02.034
Chhetri, A., Tango, M., Budge, S., Watts, K., and Islam, M. (2008). Non-edible Plant Oils as New Sources for Biodiesel Production. Ijms 9 (2), 169–180. doi:10.3390/ijms9020169
Demirbas, A., Bafail, A., Ahmad, W., and Sheikh, M. (2016). Biodiesel Production from Non-edible Plant Oils. Energy Explor. Exploitation 34 (2), 290–318. doi:10.1177/0144598716630166
Elias, S., Rabiu, A. M., Okeleye, B. I., Okudoh, V., and Oyekola, O. (2020). Bifunctional Heterogeneous Catalyst for Biodiesel Production from Waste Vegetable Oil. Appl. Sci. 10, 3153. doi:10.3390/app10093153
Falowo, O. A., Oloko-Oba, M. I., and Betiku, E. (2019). Biodiesel Production Intensification via Microwave Irradiation-Assisted Transesterification of Oil Blend Using Nanoparticles from Elephant-Ear Tree Pod Husk as a Base Heterogeneous Catalyst. Chem. Eng. Process. - Process Intensif. 140, 157–170. doi:10.1016/j.cep.2019.04.010
Gan, S., Ng, H. K., Ooi, C. W., Motala, N. O., and Ismail, M. A. F. (2010). Ferric Sulphate Catalysed Esterification of Free Fatty Acids in Waste Cooking Oil. Bioresour. Technol. 101, 7338–7343. doi:10.1016/j.biortech.2010.04.028
Ganesan, S., Nadarajah, S., Chee, X. Y., Khairuddean, M., and Teh, G. B. (2020). Esterification of Free Fatty Acids Using Ammonium Ferric Sulphate-Calcium Silicate as a Heterogeneous Catalyst. Renew. Energy 153, 1406–1417. doi:10.1016/j.renene.2020.02.094
Gaurav, A., Dumas, S., Mai, C. T. Q., and Ng, F. T. T. (2019). A Kinetic Model for a Single Step Biodiesel Production from a High Free Fatty Acid (FFA) Biodiesel Feedstock over a Solid Heteropolyacid Catalyst. Green Energy & Environ. 4, 328–341. doi:10.1016/j.gee.2019.03.004
Gnanaserkhar, S., Asikin-Mijan, N., AbdulKareem-Alsultan, , Seenivasagam-Sivasangar, , Izham, S. M., and Taufiq-Yap, Y. (2020). Biodiesel Production via Simultaneous Esterification and Transesterification of Chicken Fat Oil by Mesoporous Sulfated Ce Supported Activated Carbon. Biomass Bioenergy 141, 10571.
Karmakar, A., Karmakar, S., and Mukherjee, S. (2012). Biodiesel Production from Neem towards Feedstock Diversification: Indian Perspective. Renew. Sustain. Energy Rev. 16, 1050–1060. doi:10.1016/j.rser.2011.10.001
Kumar, A., and Sharma, S. (2008). An Evaluation of Multipurpose Oil Seed Crop for Industrial Uses (Jatropha Curcas L): A Review. Industrial Crops Prod. 28, 1–10. doi:10.1016/j.indcrop.2008.01.001
Kurniati, S., Soeparman, S., Setyo Yuwono, S., Hakim, L., and Syam, S. (2019). A Novel Process for Production of Calophyllum inophyllum Biodiesel with Electromagnetic Induction. Energies 12 (3), 383. doi:10.3390/en12030383
Loures, C. C., Da Ros, P. C., Zorn, S. M., de Castro, H. F., and Silva, M. (2018). Simultaneous Esterification and Transesterification of Microbial Oil from Chlorella Minutissima by Acid Catalysis Route: A Comparison between Homogeneous and Heterogeneous Catalysts. Fuel 211, 261–268. doi:10.1016/j.fuel.2017.09.073
Malhotra, R., and Ali, A. (2018). Lithium-doped Ceria Supported SBA−15 as Mesoporous Solid Reusable and Heterogeneous Catalyst for Biodiesel Production via Simultaneous Esterification and Transesterification of Waste Cottonseed Oil. Renew. Energy 119, 32–44. doi:10.1016/j.renene.2017.12.001
Maneerung, T., Kawi, S., Dai, Y., and Wang, C.-H. (2016). Sustainable Biodiesel Production via Transesterification of Waste Cooking Oil by Using CaO Catalysts Prepared from Chicken Manure. Energy Convers. Manag. 123, 487–497. doi:10.1016/j.enconman.2016.06.071
Mofijur, M., Atabani, A. E., Masjuki, H. H., Kalam, M. A., and Masum, B. M. (2013a). A Study on the Effects of Promising Edible and Non-edible Biodiesel Feedstocks on Engine Performance and Emissions Production: A Comparative Evaluation. Renew. Sustain. Energy Rev. 23, 391–404. doi:10.1016/j.rser.2013.03.009
Mofijur, M., Masjuki, H. H., Kalam, M. A., and Atabani, A. E. (2013b). Evaluation of Biodiesel Blending, Engine Performance and Emissions Characteristics of Jatropha Curcas Methyl Ester: Malaysian Perspective. Energy 55, 879–887. doi:10.1016/j.energy.2013.02.059
Moyo, L. B., Iyuke, S. E., Muvhiiwa, R. F., Simate, G. S., and Hlabangana, N. (2021). Application of Response Surface Methodology for Optimization of Biodiesel Production Parameters from Waste Cooking Oil Using a Membrane Reactor. South Afr. J. Chem. Eng. 35, 1–7. doi:10.1016/j.sajce.2020.10.002
Mueanmas, C., Nikhom, R., Petchkaew, A., Iewkittayakorn, J., and Prasertsit, K. (2019). Extraction and Esterification of Waste Coffee Grounds Oil as Non-edible Feedstock for Biodiesel Production. Renew. Energy 133, 1414–1425. doi:10.1016/j.renene.2018.08.102
Nayebzadeh, H., Saghatoleslami, N., and Tabasizadeh, M. (2016). Optimization of the Activity of KOH/calcium Aluminate Nanocatalyst for Biodiesel Production Using Response Surface Methodology. J. Taiwan Inst. Chem. Eng. 68, 379–386. doi:10.1016/j.jtice.2016.09.041
Ogunkunle, O., and Ahmed, N. A. (2019). A Review of Global Current Scenario of Biodiesel Adoption and Combustion in Vehicular Diesel Engines. Energy Rep. 5, 1560–1579. doi:10.1016/j.egyr.2019.10.028
Patil, P., Deng, S., Isaac Rhodes, J., and Lammers, P. J. (2010). Conversion of Waste Cooking Oil to Biodiesel Using Ferric Sulfate and Supercritical Methanol Processes. Fuel 89, 360–364. doi:10.1016/j.fuel.2009.05.024
Policano, M., Rivaldi, J., deCastro, H., and Carneiro, L. (2016). Simultaneous Esterification and Transesterification of Andiroba Oil Using Niobium Oxide-Sulfate as Catalyst. Int. J. Eng. Res. Sci. 2 (10), 175–184.
Qu, T., Niu, S., Zhang, X., Han, K., and Lu, C. L. (2021). Preparation of Calcium Modified Zn-Ce/Al2O3 Heterogeneous Catalyst for Biodiesel Production through Transesterification of Palm Oil with Methanol Optimized by Response Surface Methodology. Fuel 284, 11898. doi:10.1016/j.fuel.2020.118986
Sekhar, M. C., Mamilla, V. R., Mallikarjun, M., and Reddy, K. (2009). Production of Biodiesel from Neem Oil. J. Eng. Stud. 1 (4), 295–302.
Sharma, Y. C., Singh, B., and Upadhyay, S. N. (2008). Advancements in Development and Characterization of Biodiesel: A Review. Fuel 87 (12), 2355–2373. doi:10.1016/j.fuel.2008.01.014
Shelke, P. S., Sakhare, N. M., and Lahane, S. (2016). Investigation of Combustion Characteristics of a Cottonseed Biodiesel Fuelled Diesel Engine. Procedia Technol. 25, 1049–1055. doi:10.1016/j.protcy.2016.08.205
Taufiq-Yap, Y. H., Lee, H. V., Yunus, R., and Juan, J. C. (2011). Transesterification of Non-edible Jatropha Curcas Oil to Biodiesel Using Binary Ca-Mg Mixed Oxide Catalyst: Effect of Stoichiometric Composition. Chem. Eng. J. 178, 342–347. doi:10.1016/j.cej.2011.10.019
Wang, Y., Liu, P., and Zhang, Z. (2007). Preparation of Biodiesel from Wastes Cooking Oil via Two-Step Catalyzed Process. Energy Convers. Manag. 48, 184–188. doi:10.1016/j.enconman.2006.04.016
Yin, X., Duan, X., You, Q., Dai, C., Tan, Z., and Zhu, X. (2016). Biodiesel Production from Soybean Oil Deodorizer Distillate Usingcalcined Duck Eggshell as Catalyst. Energy Convers. Manag. 112, 199–207. doi:10.1016/j.enconman.2016.01.026
Yusuff, A. S. (2019). Characterization of Alkaline Modified Anthill and Investigation of its Catalytic Behaviour in Transesterification of Chrysophyllum Albidium Seed Oil. South Afr. J. Chem. Eng. 29, 2–32. doi:10.1016/j.sajce.2019.05.001
Zareh, P., Zare, A. A., and Ghobadian, B. (2017). Comparative Assessment of Performance and Emission Characteristics of castor, Coconut and Waste Cooking Based Biodiesel as Fuel in a Diesel Engine. Energy 139, 883–894. doi:10.1016/j.energy.2017.08.040
Keywords: neem seed oil, bifunctional catalyst, simultaneous, esterification, transesterification
Citation: Akhabue CE, Ukponahiusi UJ, Osa-Benedict EO, Otoikhian SK, Inetianbor OC and Oyedoh EA (2022) Simultaneous Esterification and Transesterification of Neem Seed Oil Using Ferric Sulphate Doped With Poultry Droppings as a Bifunctional Catalyst. Front. Energy Res. 10:927467. doi: 10.3389/fenrg.2022.927467
Received: 24 April 2022; Accepted: 23 June 2022;
Published: 25 July 2022.
Edited by:
Md Mofijur Rahman, University of Technology Sydney, AustraliaReviewed by:
S. M. Ashrafur Rahman, Queensland University of Technology, AustraliaAwais Bokhari, COMSATS University Islamabad, Lahore Campus, Pakistan
Copyright © 2022 Akhabue, Ukponahiusi, Osa-Benedict, Otoikhian, Inetianbor and Oyedoh. This is an open-access article distributed under the terms of the Creative Commons Attribution License (CC BY). The use, distribution or reproduction in other forums is permitted, provided the original author(s) and the copyright owner(s) are credited and that the original publication in this journal is cited, in accordance with accepted academic practice. No use, distribution or reproduction is permitted which does not comply with these terms.
*Correspondence: Christopher Ehiaguina Akhabue, Y2hyaXN0b3BoZXIuYWtoYWJ1ZUB1bmliZW4uZWR1; Evidence Osayi Osa-Benedict, ZXZpZGVuY2Vvc2FiZW5lZGljdEBnbWFpbC5jb20=