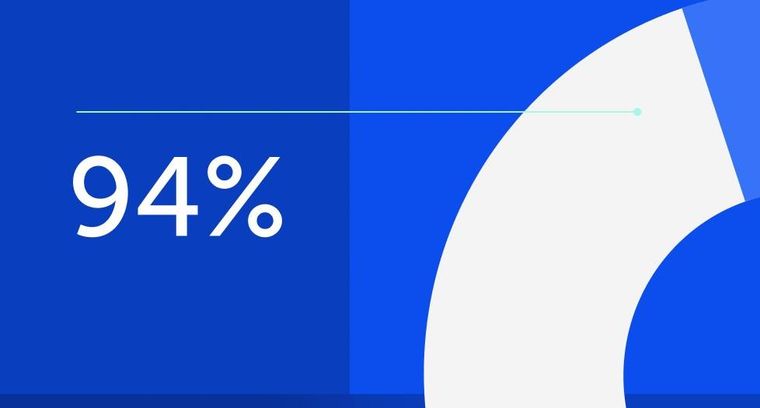
94% of researchers rate our articles as excellent or good
Learn more about the work of our research integrity team to safeguard the quality of each article we publish.
Find out more
ORIGINAL RESEARCH article
Front. Energy Res., 26 September 2022
Sec. Smart Grids
Volume 10 - 2022 | https://doi.org/10.3389/fenrg.2022.927048
This article is part of the Research TopicCondition Monitoring for Renewable Energy SystemsView all 13 articles
At present, it is difficult to bring centralized heating to rural areas owing to factors such as scattered distribution, distance from towns and cities, and difficulty in laying public pipes. According to research, most rural residents use inefficient household heating facilities, thereby resulting in serious environmental pollution and a decline in the quality of life of residents. In order to alleviate environmental pollution, the use of solar energy, air energy, and other renewable energy for rural heating of such decentralized buildings is of profound significance. This study analyzed the distribution characteristics of solar energy resources and solar combined air energy greenhouse heating system, established and solved a mathematical model of the solar combined air energy greenhouse heating system, calculated solar heat collection and solar heating energy consumption. From the data analysis, the relationship among heat gain power, heating power, and the water temperature of the water storage tank of the heat pump system was obtained. The mathematical model of the storage tank of the solar combined air energy greenhouse heating system was solved, and the operating conditions and volume of the storage tank of the solar combined air energy greenhouse heating system were determined. The study also analyzed the solar heat collection and solar heating energy consumption in Qingdao, thereby pointing out the advantages of the solar combined air energy greenhouse heating system, and finally obtained the best heating scheme.
Greenhouses are an important infrastructure of modern agriculture. The development direction of modern greenhouse is large-scale, high-tech, factory, greenhouse product diversification, characteristic, low energy consumption and environmental protection (Wei, 1999). In the cold areas of north China, the energy consumption of the greenhouse heating load during winter is quite large, thereby accounting for 60–74% of the operating cost of greenhouses (Zhu, 2005). The average winter temperature in northern China is 5°C, and the negative accumulated temperature is 1–4 times higher than that in the same latitude around the world (Liao et al., 1998). Due to the high heat transfer coefficient of greenhouse covering materials and the inability of plants in the greenhouse to store a lot of heat, greenhouse heating is quite different from that of ordinary buildings. The most important characteristic of the greenhouse are the poor thermal inertia of the envelope and the huge temperature difference between day and night (Gao, 2012). These are the temperature regulation methods that are mainly followed for greenhouses in China (Zhou, 2003): (1) adding cover; (2) hot-water heating method; (3) wood heating method; (4) heating coal-fired hot blast stove temperature raising method; (5) electric heating; and (6) solar thermal storage pool, which is mainly used to collect and store solar energy. In recent years, solar energy technology has been widely applied at home and abroad (Ma, 2003). At the same time, as a type of green technology of energy saving, heat pumps are highly efficient, provide environmental protection, and have been increasingly applied in the field of facility agriculture (Mao et al., 2004).
There is a serious lack of energy in rural areas in China, remote and isolated areas are in urgent need of energy supply, and the use of solar energy is one of the main ways to solve the heating needs of greenhouses in these areas (Wang and Cheng, 2007). The use of solar energy for greenhouse heating, although energy saving and environmentally friendly, is subject to the weather and meets the needs of all-weather heating with difficulty (Zhang and Chen, 2008). With the rapid development of modern agriculture in China, energy saving, high efficiency, and environmental protection have become the development themes of facility agriculture, and greenhouse heating equipment and heating methods have also been developed in that direction (Liu et al., 2008). In recent years, solar energy technology has been widely used at home and abroad (Luo et al., 2007). Meanwhile, heat pumps, as an energy-saving, high-efficiency, and environmentally friendly green technology, are also being increasingly used in the field of facility agriculture (Luo et al., 2007; Fang et al., 2008). The traditional heating equipment relies on conventional energy to heat up during the day and most nights during winter, which can meet the heating requirements, but it produces problems, such as high heating cost, low efficiency, and environmental pollution. To improve the propane refrigeration system of the natural gas shallow cooling unit, the factors affecting the energy consumption of the propane compressor were analyzed, and it was found that reducing the condensing temperature of the propane at the outlet of the compressor could ensure that the grade and quantity of the cold quantity provided by the refrigeration system would not decrease and effectively reduce the energy consumption of the propane compressor (Fang and Zhuang, 2014). The cooling capacity of the cryogenic methane washing process is provided by a refrigeration cycle using the product gas CO as the working mass, which has high energy consumption (Li et al., 2013). The ternary hybrid refrigeration system provides the cooling capacity for the separation system to meet the heating demand of some low-temperature-distillation tower reboilers and effectively recovers the cooling capacity of the process logistics through precooling and subcooling of the refrigerant (Di, 2003). Process model of separation refrigeration system using demethanizer, Process simulation, parameter sensitivity analysis and process optimization of old refrigeration system in Yangzi ethylene plant (Xu and Gong, 2010).
The refrigerant R134a is used in the solar air greenhouse combined heating system, and the compressor used is the Bizell piston compressor. The compressor compresses the refrigerant to high temperature pressure and transfers the refrigerant to a condensing coil, which then condenses it to a liquid state. The condensing coil is placed in the hot water storage bucket, and the water in the bucket is heated using the condensing coil. Liquid refrigerant passes through a liquid storage device, liquid mirror, and filter dryer, which is throttled by the expansion valve, becomes a low-pressure and low-temperature liquid refrigerant, and enters the solar plate collector to evaporate and absorb heat. The vaporized refrigerant is separated from the superheated gas by the gas–liquid separator into the low-pressure end of the compressor and compressed into a high-temperature and high-pressure liquid refrigerant. The hot water in the hot water storage tank is pumped into the fan coil unit in the greenhouse. The fan coil emits heat inside the greenhouse to maintain the temperature inside the greenhouse. The hot water is returned to the hot bucket to complete the hot water circulation. The solar plate collector in this system is processed from an aluminum plate, and its surface is painted black to absorb sunlight (Li, 2022a; Li, 2022b).
The greenhouse heating loss is mainly composed of heating loss of the envelope, cold air infiltration, and cold air invasion. The calculation formula of heat load (Zhang and Chen, 2011) is as follows:
Here, Q1 is the heat loss of the envelope structure; —Cold air permeates heat loss; —Ground heat loss; —Heat transfer coefficient of greenhouse envelope at n floor, W/(m2∙K), = 3 W/(m2∙K); —Surface area of the n greenhouse envelope, m2; —Wind power factor, = 1; —Greenhouse air volume, m3; —Number of chamber air changes, h-1, Greenhouse once/12 h; —Ground heat transfer coefficient in zone i, W/(m2∙K); —Area of block i, m2; —The n greenhouse indoor heating design temperature, K = 18°C; —The n greenhouse outdoor heating design temperature, K. = 2°C.
For small rolling-rotor compressors, the refrigerant flow rate and compressor power can be calculated using the following equation.
1 Refrigerant mass flow rate
where vi is the compressor suction specific volume expressed as m3/kg; n is the heat loss of envelope structure, taking the value of 2880 r/min; C is compressor speed, taking the value of 0.91; and Vd is the compressor theoretical discharge volume, taking the value of 13.40 cm3/r.
2 Compressor power
The compressor input electrical power is:
where λcm is the total efficiency of the compressor; Pc is the evaporation pressure and condensation pressure, Pa; and k is the compression process multivariate index.
Experimental study of direct expansion solar heat pump water heater.
Solar water supply systems require temperatures lower than 60°C and the use of collectors with glass cover. According to the energy balance can be obtained that as the design conditions under the pressure drop is small, you can ignore the pressure drop of the refrigerant in the tube.
1 Refrigerant side flow heat transfer equation (Chai et al., 2008; Chen et al., 2011; Kuang and Wang, 2005):
The formula, Qr—Heat absorbed by Refrigerant, W; mr—Refrigerant mass flow, kg/s; αi—Convective heat transfer coefficient on refrigerant side surface, W/(m2·K); Ai—Tube surface area, m2; Tp—Tube wall temperature, K; Trm—Average inlet and outlet temperature of refrigerant, K.
2 Compressor power
The formula, Qd—Effective heat gain of heat collector plate, W; Ad—Micro-element length heat collection area on the upper surface of trace element heat collecting plate, m2; S—The difference between absorbed and emitted radiation from the heat collector plate, W/m2; ULC—Total heat loss coefficient of heat collector plate, m2, W/(m2·K); —Heat collection efficiency factor of collector plate; T0—Ambient temperature, K.
where ambient temperature is K, Boltzmann constant (blackbody radiation constant) is 5.67 × 10 − 8W/(m2∙K4), the outdoor wind speed and the calculated outdoor wind speed in winter in the Chengyang area are taken in this paper, and T0 is the ambient temperature, K, which is the unit of measurement of standard error in the total number.
Taking into account the installation angle and direct sunlight, sky radiation, and reflection of solar radiation from the ground, the total solar radiation is calculated as follows:
The formula, —Indicates the intensity of radiation projected on a horizontal surface; —Indicates the intensity of diffuse reflection projected on a horizontal surface; —Indicates the angle of projection of direct sunlight on inclined and horizontal surfaces; —Indicates the tilt angle of the collector plate installation; —Indicates the reflectivity of the ground to the total solar radiation, in engineering calculations, we usually take the average value as 0.2.
For an inclined surface facing due south, formula for calculating the .
For an inclined surface facing due south formula for calculating the formula, —Hour Angle; —Angle of incidence; —Local latitude; —Angle of declination; —inclination of collector surface (Duffie J.A. et al., 1991).
3 Heat balance equation inside and outside the tube:
Here, the coefficient introduced by considering impurities, such as oil, in the refrigerant takes a value of 0.9 in the model.
Condenser (tank) uses immersion condensing spiral coil, and collectors are similar to the enthalpy difference in the direction of the length of the equal division of a number of microelements. When the enthalpy difference is small, the length of each microelement is also very small, which can be approximated by straight pipe section to deal with, and corrected using the spiral tube correction factor. For each microelement, the following control equation can be established.
1 Refrigerant side flow heat transfer equation:
2 Water-side heat transfer equation:
where hot water heating power is expressed in W; total mass of water in the tank is expressed in kg; specific heat of water is expressed in kJ/(kgK); water temperature is expressed in K; and time is expressed in s.
3 Heat balance equation inside and outside the tube:
4 Microelement thermal conductivity equation:
The formula, —Heat transfer coefficient of overall on external surface area, W/(m2·K); —Heat transfer area between condensing coil and water, here is the exterior area of the condensing coil, m2; —Average temperature of water, K。
The heat transfer coefficient of the condensing coil to water can be calculated according to the formula:
where metal tube wall thickness is m; thermal conductivity of metal pipe wall is expressed by W/(m2·K); surface heat transfer coefficient of the refrigerant in the condensing coil is expressed by W/(m2·K); water-side surface heat transfer coefficient is expressed by W/(m2·K); inside and outside areas of condensing coils is expressed in m2; and average surface area of condensing coils is expressed in m2.
The thermal expansion valve model includes the following control equations:
Flow characteristic equation
The refrigerant flow rate through the thermal expansion valve can be calculated according to the following formula:
The formula, —Expansion valve inlet and outlet enthalpy, J/kg —Differential pressure before and after the valve hole, Pa —Flow coefficients, using empirical formulas from the literature —Minimum flow area of valve orifice, m2—Inlet liquid refrigerant density, kg/m3—Outlet refrigerant specific volume, m3/kg.
On rainy days and at night, the evaporator gains heat from the surrounding air through the spiral finned tubes and collector plates, and the heat pump works as an air source:
The formula—Refrigerant flow rate, —Refrigerant enthalpy at evaporator outlet; —The refrigerant enthalpy of the evaporator inlet.
1 Chilled water heat balance equation
2 Coil heat exchanger coil wall heat balance equation
3 Air-side humidity equilibrium equation
4 Energy equation
The formula represents heat transfer coefficient, which is expressed as W/(m2·K); cross-sectional area of air passing through the coil heat exchanger is expressed as m2; specific heat capacity of guest product is expressed as J/(m3·K); moisture content, based on 1 kg of dry air, is expressed as g/kg; heat transfer area per unit volume of fluid is expressed as m2/m3; enthalpy is expressed as J/kg; mass transfer coefficient between air and the outer surface of the coil is expressed as kg/(m2·s); coil heat exchange is expressed as W; temperature is expressed as K; fluid flow rate is expressed as m/s; coefficient of heat transfer between air and the outer surface of the coil is expressed as kg/(m2·s); fluid density is expressed as kg/m3; and duration of a single stay is expressed as s.
Subscript, —Wet air; —Coil wall surface; —Between the chilled water and the inner surface of the coil; —Between the air flow and the outer surface of the coil; —Coil heat exchanger outer surface saturated with air; —Import; —The entire coil; —Export; —Frozen water.
Heat exchange of primary heat exchanger at dry working conditions.
The air on the outside of the evaporator tube in winter is an exothermic cooling process from the inlet to the outlet, and according to the state parameters of the air, its cooling process have three conditions: dry condition and wet condition.
The heat exchange volume in the dry condition is calculated by the following formula (Sun, 2008):
The formula, —Air-side heat transfer coefficient, W/(m2·K); —Fin efficiency; —Fin area, m2; —Base tube area, m2; —Temperature, K.
Subscript, —Air; —Frosting; —Ribs; —Pipe Wall; —Base Management;
The fin efficiency is calculated using the following formula.
The formula represents thermal conductivity of rib material, which is expressed as W/(m2·K) and the average thickness of ribs is expressed as m.
The heat exchange coefficient on the air side was used from the literature (Kong et al., 2010).
The heat exchange volume at wet working conditions is calculated using the following equation (Hikari, 1983):
The formula—Moisture dispersion coefficient —Fin efficiency under wet working conditions;
Moisture dispersion coefficient, the calculation of fin efficiency under wet working conditions is referred to literature 22.
The project is located in Qingdao, Shandong province, the southern tip of Shandong Peninsula, at the longitude 119°30′E–121°00′E and latitude 35°35′N–37°09′ N. The terrain is high in the east and low in the west, uplifted on both sides of the north and south, and concave in the middle. Located in the warm temperature difference between day and night on January 28 sunrise at 7:03 and sunset at 17:20. Cloudy, RH 39%, no continuous wind direction and light breeze.
Figure 1 shows the COP variation with solar radiation intensity. As it can be seen from Figure 2, COP of the system increases with the solar radiation intensity. The solar combined air energy greenhouse heating system’s biggest characteristic in solar panels is that the refrigerant directly absorbs heat from the environment and evaporation, the main source of energy is radiation from the sun, evaporation temperature increases with an increase in the radiation from the sun, and refrigerant phase-change heat absorption unit, which is the process of quality, is also increased. Thus, the system’s COP also increases. By the same token, COP increases with ambient temperature. In the numerical simulation results, the maximum error of heating time is 11.02%, the average error is 5.43%, the maximum error of COP is 13.40%, and the average error is 4.12%. The error is acceptable in the engineering application range, and the simulation results are in good agreement with the test results.
Figure 3 shows the simulation comparison of the transient COP experiment of the system. As the temperature of condensed water increases, the COP of the system decreases due to the deterioration of condensation conditions. At the same time, solar radiation intensity changes due to cloud shielding when the system runs up to 16 min and 46 min, and the COP of the system also changes, which is consistent with the conclusion drawn in Figure 3. When the weather conditions change, in order to maintain a higher COP and a shorter system running time as much as possible, frequency conversion adjustment can be carried out on the heat pump system and the evaporation temperature can still be maintained in a reasonable range when solar radiation changes significantly. About the compressor running frequency effect on the COP of the system, the frequency and refrigerating capacity decrease, but the power reduction rate is greater than the heat; thus, the system COP in the reduced frequency is increased. Thus, we specially selected two days’ climate conditions, which were close to the experimental data, to compare, and the final measurements for the two groups’ experiment system’ COP was 4.87 and 5.3.
Figure 4 shows the power consumption of the compressor in this group of experiments. The power consumption of the compressor at 70 Hz increases significantly faster than that of the compressor at 50Hz; thus, the COP of the latter is greater. In addition, when the solar radiation intensity decreases and the heating time is prolonged, the system operating at high frequencies will decline rapidly due to increased power consumption of the compressor. However, in contrast, it takes 52 min to heat the water in the water tank from 27 to 50°C at 70 Hz and 78 min at 50 Hz. Therefore, it can be considered appropriately to increase the frequency of the compressor when the hot water is expected to be heated quickly. The frequency of the compressor has an extremely important influence on COP and the speed of hot water. The frequency of the compressor should be adjusted according to the climatic conditions and user needs.
The centralized parameter model has satisfactory accuracy for the calculation of the transient process and the overall operation parameters of the solar air greenhouse combined heating system, and the calculation results have reference significance for guiding the experimental direction. It is evident that the COP increases with increasing ambient temperature. The results of the numerical simulation showed that the maximum error of heating time was 11.02% and the average error was 5.43%, whereas the maximum error of COP was 13.40% and the average error was 4.12%. The error is acceptable in the engineering application range, and the simulation results agree well with the test results.
The raw data supporting the conclusion of this article will be made available by the authors, without undue reservation.
WH conceived the idea and designed the experiments. The experiments were led by XZ, while WJ contributed to data analysis and interpretation along with writing paper. All authors read and approved the final manuscript.
The authors declare that the research was conducted in the absence of any commercial or financial relationships that could be construed as a potential conflict of interest.
All claims expressed in this article are solely those of the authors and do not necessarily represent those of their affiliated organizations, or those of the publisher, the editors, and the reviewers. Any product that may be evaluated in this article, or claim that may be made by its manufacturer, is not guaranteed or endorsed by the publisher.
Chai, L., Ma, C., and Zhang, X. (2008). Experimental Research and Performance Analysis of Ground Source Heat Pump Greenhouse Cooling System. J. Agric. Eng. 24 (12), 150–154.
Chen, B., Luo, X., Bi, F., and Li, J. (2011). Experiment of Combined Solar and Air Source Heat Pump Heating System for Greenhouse. China Agric. Sci. Technol. Her. 13 (1), 55–59.
Di, X. (2013). Optimization of Combined Operation of De-ethanizer Tower and Refrigeration System in Ethylene Plant. China Foreign Energy 18 (10), 84–89.
Du, J., Wang, H., and YangDan, L. (2000). New Field of Heating Technology a Greenhouse Heating. Energy Sav. Technol. 18 (10), 22–23.
Duffie, J. A., and Beckman, W. A. (1991). Solar Engineering of Thermal Processes. Second Edition. New York: John Willy & Sons, Inc., 28–143.
Fang, X., and Zhuang, X. (2014). Application and Effect Analysis of Energy-Saving Technology for Propane Refrigeration System. Petroleum Petrochem. Energy Conservation 4 (08), 12–14.
Gao, L. (2012). Analysis of Air-Source Heat Storage Soil-Source Heat Pump for Heating and Cooling of Sunlight Greenhouses in Severe Cold Areas, Master's Thesis, 6. Harbin Institute of Technology.
Hikari .Q (Editor) (1983). Cooling Technology for Air Conditioning (China Construction Industry Press).
Hui, F., Yang, Q., and Sun, A. (2008). Application of Ground-Source Heat Pump-Floor Heat Dissipation System in Greenhouse Winter Heating. J. Agric. Eng. 24 (12), 145.
Jordan, R. C., and Priester, G. B. (1948). Refrigeration and Air Conditioning. New York: Prentic-Hall, Inc., 82–98.
Kong, X., Zhang, D., Ying, L., and Yang, Q. (2010). Simulation Study of Direct Expansion Solar Heat Pump Water Heater. J. Sol. Energy 12 (3112), 1574–1579.
Kuang, Y. H., and Wang, R. Z. (2005). Experimental Study of Direct Expansion Solar Heat Pump Water Heater. J. Eng. Thermophys. (3), 379–381.
Le, S., Wu, Y., Guo, Y., and Del Vecchio, C. (2021). Game Theoretic Approach for a Service Function Chain Routing in NFV with Coupled Constraints. IEEE Transactions on Circuits and Systems II. Published online.
Li, G., Zhang, X. W., Li, Y., and Guan, F. B. (2013). Design and Energy Saving Research of Refrigeration Cycle in Low Temperature Methane Washing Process. Chem. Des. Commun. 39 (06), 40–43.
Li, H., Deng, J., Feng, P., Pu, C., Arachchige, D. D. K., and Cheng, Q. (2021). Short-Term Nacelle Orientation Forecasting Using Bilinear Transformation and ICEEMDAN Framework. Front. Energy Res. 9, 780928–782021. doi:10.3389/fenrg.2021.780928
Li, H., Deng, J., Yuan, S., Feng, P., and Arachchige, D. D. K. (2021). Monitoring and Identifying Wind Turbine Generator Bearing Faults Using Deep Belief Network and EWMA Control Charts. Front. Energy Res. 9, 799039. doi:10.3389/fenrg.2021.799039
Li, H. (2022b). SCADA Data Based Wind Power Interval Prediction Using LUBE-Based Deep Residual Networks. Front. Energy Res. 10, 920837. doi:10.3389/fenrg.2022.920837
Li, H. (2022a). Short-term Wind Power Prediction via Spatial Temporal Analysis and Deep Residual Networks. Front. Energy Res. 10, 920407. doi:10.3389/fenrg.2022.920407
Liao, Y., Wang, L., and Wen, X. (1998). Facility Agriculture-An Important Way for Efficient Utilization of Agricultural Resources in China. Resour. Sci. 20 (3), 20–25.
Liu, S. Y., Zhang, J., and Zhang, B. L. (2008). Experimental Study of Solar Thermal Storage System to Increase the Ground Temperature of Greenhouse. J. Sol. Energy 3, 461–465.
Luo, Y., Jiang, L., and Xu, L. (2007). Research on the Application of Ground Source Heat Pump Greenhouse System. Agric. Mech. Res. 4, 59–61.
Ma, C. (2003). Research on Active Greenhouse Solar Underground Heat Storage System. Nanchang: Shanxi Agricultural University, 2–5.
Mao, H., Wang, X., and Wang, D. (2004). Design and Experimental Study of Greenhouse Solar Heating System. J. Sol. Energy 25 (3), 305–309.
Sun, Z. H. (2008). Performance Improvement and Experimental Study of Direct Expansion Solar Heat Pump Water Heater. Master's thesis 1, 41–42.
Toyoda, M., and Wu, Y. (2021). Mayer-type Optimal Control of Probabilistic Boolean Control Network with Uncertain Selection Probabilities. IEEE Trans. Cybern. 51, 3079–3092. doi:10.1109/tcyb.2019.2954849
Wang, S-S., and Cheng-wei, M. (2007). Experimental Study on Built-In Solar Thermal Collector and Thermoregulation Device for Solar Greenhouse. Agric. Mech. Res. 2, 130–133.
Wei, Q. (1999). The Development Status and Prospect of Factory Farming. Rural. Pract. Eng. Technol. (8), 2–3.
Wu, Y., Guo, Y., and Toyoda, M. (2021). Policy Iteration Approach to the Infinite Horizon Average Optimal Control of Probabilistic Boolean Networks. IEEE Trans. Neural Netw. Learn Syst. 32 (6), 2910–2924. doi:10.1109/TNNLS.2020.3008960
Xu, Y., and Gong, B. (2010). Simulation and Optimization of Ethylene Plant Refrigeration System. Ethyl. Ind. 22 (04), 3–9+25.
Zhang, X., and Chen, Q. (2008). Heating Effect of Ground Source Heat Pump Air Conditioning System in Solar Greenhouse. J. Shanghai Jiaot. Univ. 5, 436–439.
Zhang, X., and Chen, W. (2011). Energy Saving Analysis of Greenhouse Solar Thermal Storage Pool. Agric. Mech. Res. 8–8.
Zhou, C. (Editor) (2003). Modern Greenhouse Engineering (Beijing: Chemical Industryd Press), 2, 38–139.
Keywords: greenhouse, solar energy, air energy, COP, heating system
Citation: Hao W, Jintao W, Ruifeng Z and Zhenjun X (2022) Study of Solar Combined Air Energy Greenhouse Heating System Model. Front. Energy Res. 10:927048. doi: 10.3389/fenrg.2022.927048
Received: 23 April 2022; Accepted: 13 May 2022;
Published: 26 September 2022.
Edited by:
Yusen He, The University of Iowa, United StatesReviewed by:
Hardeep Singh, Sophia University, JapanCopyright © 2022 Hao, Jintao, Ruifeng and Zhenjun. This is an open-access article distributed under the terms of the Creative Commons Attribution License (CC BY). The use, distribution or reproduction in other forums is permitted, provided the original author(s) and the copyright owner(s) are credited and that the original publication in this journal is cited, in accordance with accepted academic practice. No use, distribution or reproduction is permitted which does not comply with these terms.
*Correspondence: Xu Zhenjun, eHV6aGVuanVuQHFhdS5lZHUuY24=
Disclaimer: All claims expressed in this article are solely those of the authors and do not necessarily represent those of their affiliated organizations, or those of the publisher, the editors and the reviewers. Any product that may be evaluated in this article or claim that may be made by its manufacturer is not guaranteed or endorsed by the publisher.
Research integrity at Frontiers
Learn more about the work of our research integrity team to safeguard the quality of each article we publish.