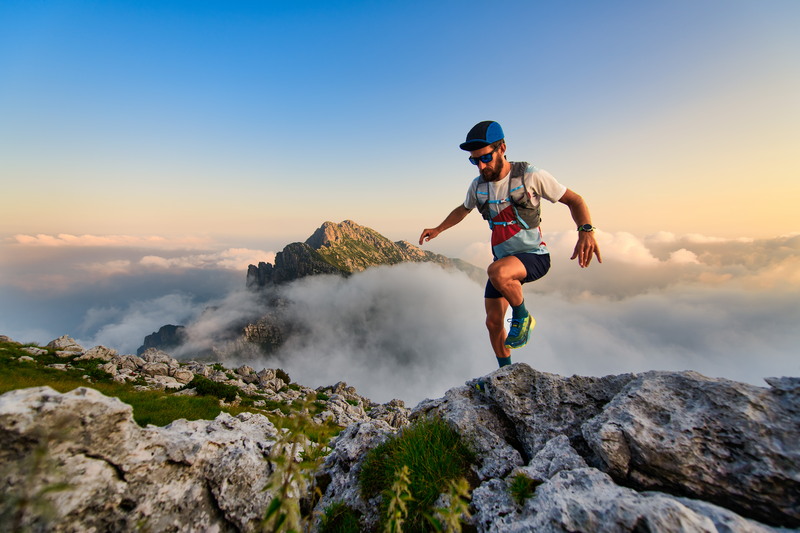
95% of researchers rate our articles as excellent or good
Learn more about the work of our research integrity team to safeguard the quality of each article we publish.
Find out more
ORIGINAL RESEARCH article
Front. Energy Res. , 25 August 2022
Sec. Bioenergy and Biofuels
Volume 10 - 2022 | https://doi.org/10.3389/fenrg.2022.919415
Biofuels are playing an increasingly important role since they are an attractive alternative to fossil fuels, access to which has been limited. Moreover, they can help the European Union countries meet their climate and energy objectives. There is a growing interest in the production of biofuels from the organic fraction of municipal solid wastes as second-generation biofuels. Such a solution supports a circular economy as an example of an effective approach in terms of effective waste management. The study presents a review of different biofuels with an emphasis on second-generation biofuels from lignocellulose biomass, highlighting the BioRen process, which is one of the waste-to-fuel conversion technologies. It allows for maintaining the value of materials within the economy. All stages of the process are described and material flow is presented. The framework of the BioRen project includes the bio-fermentation of the organic fraction by a two-stage enzymatic process simultaneously into bioethanol and isobutanol, which are then used to produce glycerol tertiary butyl ether. The post-fermentation sludge is treated by the hydrothermal carbonization method increasing the efficiency of the whole waste treatment process and closing the loop. The bio-coal resulting from the process of carbonization can be used as a fuel with a high-calorific value. The remaining fraction undergoes a physical–chemical and catalytic conversion of inorganic particles into their clean, dry, and inert components. The results show that in the BioRen project 78% of the heat that is produced during the process is recovered and used for electricity production. Moreover, 53% of waste is recovered and re-used, because the process is profitable, efficient, environmentally friendly, and maintains high-security standards. Such an example of advanced technology, with a high readiness level, obtained results, and experience may encourage European countries and facilities to implement such an effective solution, which supports the development of bioenergy.
Lignocellulose biomass feedstock used as a raw material for the production of bioenergy and bio-based resources delivers benefits both socially and economically. Biomass, also from the organic part of municipal solid waste (OFMSW), is a recyclable product competing with grains grown for food production. It indirectly reduces CO2 emissions to the air by reducing the burning of fossil fuels. Its use supports local economic development, generating new chances for the development of biochemical and bioenergetics and offering increased fuel security for oil and fossil fuel–dependent countries (Ganguly et al., 2021).
Biomass from lignocellulose and aquatic material is seen as an interesting source of raw material for conversion into biofuels, biochemical, and biomaterials. The biorefinery, integration of processes and technologies for biomass conversion, demands efficient utilization of all components. Although originally developed mainly for cellulose-to-ethanol processes, these various hydrothermal pretreatment methods are now being adapted to various lignocellulosic biorefinery processes, which is why their differentiated influence on the biomass composition is of critical significance. The hydrothermal process as a fundamental step in biorefinery covers the use of both marine and lignocellulosic biomass (Ruiz et al., 2017). Hydrothermal pretreatment of lignocellulose biomass is used at different scales in the processing of biomass for fractionation and structural modification for the development of integrated, sustainable biorefineries to advance this technology to a commercial application for second-generation biorefineries in the production of high-added value compounds and biofuels (Ruiz et al., 2020). Hydrothermal pretreatment methods are now being adapted to various lignocellulosic biorefinery processes, resulting in partial fractionation of the biomass due to solubilization of hemicellulose (main xylan) and redistribution of lignin. Hydrothermal processing is an efficient pretreatment for wheat straw biomass. S. cerevisiae CA11 has the potential to be used for ethanol production. The highest ethanol conversion yield obtained was 85.7% (Pedersen et al., 2010; Ruiz et al., 2012). Hydrothermal pretreatment is intended to improve the enzymatic cellulose saccharification. Despite the enhanced formation of inhibitors, overall, at higher severity, more hemicellulose is solubilized, and the enzymatic cellulose hydrolysis is generally improved (Yang and Wyman, 2004; Pedersen and Meyer, 2010).
First-generation biofuels (conventional biofuels) are obtained from traditional crop-based feedstock such as vegetable oil, sugar, corn, wheat, and starch. Production of the oil is on a commercial scale and encompasses conventional techniques–for example, vegetable oil is used for biodiesel via esterification and sugar crops for bioethanol via fermentation. The resultant fuels are distinctive and of high quality. Most of the most common first-generation biofuels are biogas, biodiesel, and bio-based alcohol. A summary of the numerous biological processes of ethanol production from algal biomass, lignocellulose, and crops is presented by Devarapalli and Atiyeh (2015). Some studies proposed different technological solutions, that is, ethanol from residual biomass of fruit and vegetable waste (Plazzotta et al., 2017). An overview of the conversion of various lipid sources (edible and non-edible) into biodiesel using traditional and new technologies emphasizing the quality standards mainly dependent on the used feedstock and technology, processing, and purification was presented by Verhe et al. (2011).
Lignocellulose is the key biomass for the creation of second-generation fuels (Viguie et al., 2013; Ayodele et al., 2019). These biofuels involve a wide range of fuel pathways that offer advantages over first-generation biofuels. The distinguishing characteristics of second-generation biofuels are that they use a non-food feedstock (lignocellulose biomass, field crop residues, forest product residues, or fast-growing dedicated energy crops). The fuel obtained is a “drop-in” replacement for classic petroleum-based fuels, meaning there are no limits on blending, or they can be used as is (without blending) in existing vehicles. The main type of second-generation biofuel in use or under development is cellulosic ethanol which is produced via the fermentation of sugars derived from the cellulose and hemicellulose fractions of lignocellulose biomass. Currently, the fuel yield is lower than that with ethanol, but bio-butanol can be used as a drop-in replacement for petrol without blending limits. Research on the production of biofuels and bioenergy from the organic fraction of municipal solid waste and refuse-derived fuel was presented by Verhe et al. (2020).
The updated research trends, challenges, and future outlooks supporting the circular economy model have been analyzed by Jain et al. (2022) underlying that valorization of bio-waste into other value-added products such as biofuel is essential. However, there are still numerous constraints and challenges to closing the loop, especially in lignocellulose and transferring the technology to full-scale operation.
Technologies for the conversion of lignocellulose biomass including municipal solid wastes are still not technologically mature and cost-competitive. Most of the projects are under research and development at different technology readiness levels (TRLs). According to Figure 1, the majority of advanced biofuel production technologies are at the prototype (TRLs 4, 5) and demonstration (TRLs 6, 7) level. Only lignocellulose ethanol, gasification + methanol, and methanol/dimethyl ether (DME) to gasoline are being prepared for commercialization. Nevertheless, they are at the beginning of the implementation process. Therefore, technologies at lower TRL levels would require more attention and research (Benetti, 2018).
FIGURE 1. Technology readiness level (TRL) of available advanced biofuel technologies (Kargbo et al., 2021).
This scientific know-how is constantly developing, because the topic is very promising in terms of GHG reduction, mainly in the transport sector. Moreover, the production of second-generation biofuels is more sustainable than that of first generation, because they can be treated as an effective waste management solution, and contributes to the diversification of energy sources and reduce dependence on fossil fuels.
In this study, different generations of biofuels are being characterized, highlighting the role of the second-generation biofuels produced from the organic fraction of municipal solid waste. The main goal of the BioRen research is to make a progress in the developed advanced smart chain processing which consists of the recycling and reuse of selected municipal waste and the processing of non-recycled municipal solid waste (MSW) streams into biodiesel and bio-coal pellets. The next step is hydrolysis and bio-fermentation of OFMSW enabling the appropriate production of isobutanol and following this the chemical conversion of isobutanol to isobutene which reacts with glycerol to produce glycerol tertiary butyl ether (GTBE), which is a higher value fuel, seems to be a beneficial new green additive to both diesel and petrol. Additive in diesel GTBE should result in an increase in cetane number, reduction in fine particles, and NOx. The resulting fuels (isobutanol and GTBE) will be tested in engine tests to provide feedback regarding their performance, emission results, and fuel use. Bio-coal pellets are also produced from fermentation residue.
This is an example of the technology that has reached a high level of TRL and the project is achieving satisfactory results that will allow for full commercial deployment. The developed processes are integrated into an innovative MSW treatment plant located in Ostend, Belgium, which combines the most efficient technologies of material reuse, and is currently looking into optimizing the profitability of its organic waste fraction. In addition, the results show that the BioRen project is economically feasible, environmentally friendly, and maintains high-security standards that could have a great potential to be widely used in many European markets. The high quality of the technology is proven by different certification systems such as ISCC (International Sustainability & Carbon Certification) or REDcert (Renewable Energy Directive Certification).
The amount of municipal waste generated is 2000 Mt/y worldwide, 240 Mt/y in Europe, and 3.17 Mt/y in Flanders. These amounts will become even greater with population growth, urbanization, and prosperity. Global waste production in urban centers is estimated to increase by 70% by 2025. The largest increase in municipal waste production is occurring in upper and lower-middle-income countries (Trends in Solid Waste Management, 2021).
The contributions of municipal solid waste and refuse-derived fuel (RDF) to the material recovered in mechanical–biological treatment plants (MBT) are analyzed below. The main goal of this analysis was to compare the efficiency of their incineration. RDF is an alternative fuel resulting from the sorting and preparation of waste fractions and is characterized by the high heat of combustion. The RDF formulation refers to fuels covering a wide spectrum of waste processed to meet regulations or industrial requirements, in terms of suitability for energy recovery (BioRen, 2020).
RDF obtained in MBT units constitutes about 67% of the MSW processed and is usually landfilled, but combustion of RDF with energy recovery has been proposed. MSW and RDF contain high percentages of flammable materials such as plastics or cellulose, and their calorific values are 10.160 MJ/kg for MSW and 18.281 MJ/kg for RDF. The calorific value of RDF is similar to certain types of wood, so burning it seems to be more economically advantageous than using MSW as a fuel (Montejo et al., 2011). Its composition is shown in Table 1.
Due to their energy contents, MSW and RDF having a lower calorific value (LCV), which is higher than 7.0 MJ/kg, can be used for combustion (Cherubini et al., 2009). The burning of RDF seems to be more efficient in economic terms as RDF has greater water content and a LCV value of 79.9% which is higher than MSW. Analyzing dry waste, the LCV of RDF is 23.6% higher than MSW. This is possible due to the large content of materials with a high LCV such as plastic, paper, organics, and cellulose in RDF waste. The LCV of RDF, 16.661 MJ/kg, is certainly higher than LCV, 10.11 MJ/kg, of MSW processed in Italian mechanical–biological treatment units. The reason for these differences results from the varying compositions of MSW and RDF is investigated. Thus, RDF is more flammable than MSW since its LCV is much higher. In addition, an increase in the energy recovery from RDF can be achieved by upgrading the systems for the removal of organic materials in the MBT units, as this fraction has one of the lowest LCVs containing ∼50% water. This confirms that RDF is more suitable for burning than MSW (Cherubini et al., 2009).
Cherubini et al. (2009) undertook a life cycle assessment of MSW management options for Rome: storage; storage with biogas incineration for electricity production; a separation plant that separates the inorganic waste fraction from RDF (following use for electricity generation) and OFMSW for biogas generation through anaerobic digestion and direct burning of MSW. The results indicated waste storage systems as the worst solution and show the essential ecological effects on a worldwide scale that resulted from energy recycling.
Analysis of the environmental impact of incineration of MSW and RDF indicated that the pollution content in the flue gases can meet European standards. When it comes to the most harmful pollutants, such as dioxins and furans, such compounds could be eliminated by proper plant design and the treatment of emissions in the flue gas (Cherubini et al., 2009). In addition, energy recovered in burning waste may be a factor in reducing the emission of greenhouse gases when compared to the quantities emitted during the combustion of primary energy. If environmental standards are going to be met, the quality of flue gas after RDF combustion would be higher than it would be in the case of MSW, due to the lower heavy metal content in RDF fly ash. This is the reason why RDF combustion can be considered a more favorable solution for managing RDF than storing it.
Nowadays biofuels are a principal source of renewable energy. Biofuels offer an opportunity to reduce greenhouse gas emissions when compared to petroleum-based fuels, as well as to store CO2 emissions in the soil or decrease them. This depends on the methods used for obtaining biofuels and their co-products. The strategy for maintaining soil organic carbon at an early stage of developing a biofuel restricts climate change. This could guide farmers’ proper management of soil carbon during the life cycle of biofuel production (Pourhashem et al., 2016).
Biofuels could be made also from organic fractions of waste. Most of the biofuels that are called conventional or first-generation biofuels are produced from crops. Ethanol commonly produced by fermentation of sugars derived either from starch-based raw material such as corn, wheat, maize, sugarcane, or lignocellulose biomass is an established fuel decarbonizing the transport sector. It is usually added to petrol to produce blended fuels or added to ordinary vehicles (up to 10%) as well as being used in higher concentrations in flex-fuel cars, which are designed to use both ethanol and petrol. Melin et al. (2022) presented a novel selective and flexible process concept for the production of ethanol with electricity and lignocellulose biomass as main inputs.
However, fermentation, known as the biochemical pathway to drop-in fuels, is in the early phases of development and therefore needs further research and pilot-scale tests to develop cost-effective and sustainable ways to put such methods into practice. It has been stated that ethanol and biodiesel will be basic biofuels in the future. Singh et al. (2019) assessed the different raw materials used in the production of biodiesel of different generations, along with their advantages and disadvantages. This is because it produces biodiesel with high efficiency and is comparable in properties to diesel fuel. Biodiesel is made from vegetable oils or fats. In the production process, it is mixed with small amounts of diesel fuel (up to 7%). As for the processes of biodiesel production, transesterification is indicated as the most appropriate process. The difference between hydrotreated vegetable oil (HVO) and biodiesel results from the method of production, as well as the quality of the final product. HVO, obtained using the hydroprocessing of oils and fats, is commonly referred to as renewable diesel. It can be mixed with diesel fuel and there is no specific proportion used in mixing.
The production of second-generation 2G biofuels allows the use of crops of raw materials that mainly contain cellulose. However, cellulosic biofuels are still in the research phase and commercially profitable methods that could be implemented on an industrial scale are anticipated to require another decade of experiment and development, despite their attractiveness (Schnoor, 2011).
Lignocellulose biomass (LCB) is the most abundantly available bioresource amounting to about a global yield of up to 1.3 billion tons per year. This is one of the key carbon feedstocks to supply energy to the transportation sector for light and heavy-duty fuels. Utilization of LCB supports improved energy security by reducing the demand for petroleum imports, agricultural development, and reducing greenhouse gas emissions The hydrolysis of LCB results in the release of various reducing sugars which are highly valued in the production of biofuels such as bioethanol and biogas (Baruah et al., 2018; Resch and Emme, 2022).
A review of the techno-economic possibilities for implementation and a versatile evaluation of activities used for a high-quality “drop-in” fuel obtained from lignocellulose materials (Kargbo et al., 2021) indicate that the actual production cost of “drop-in” fuel is 100% higher than that of fossil fuels (11.5 $/L) if a second-generation feedstock is used. Most importantly, the proper development of biofuels depends on the sustainable use of biomass. It should be emphasized that second-generation raw materials are more sustainable than first-generation.
Commercially produced fermentation ethanol based on cellulosic biomass was first obtained in the United States. Nowadays, technologies for the production of ethanol from cellulose (EFC) that are economically viable have begun to appear in some countries. Three basic types of EFC methods that are used are acid, enzymatic, and thermochemical hydrolysis—with different options for each. The most popular, however, is acid hydrolysis because virtually any acid can be used in this process. Due to economic reasons, sulfuric acid is the one that is most commonly used (Badger, 2002).
Havlik et al. (2011) proved that 2G biofuel production using wood from properly managed existing forests could result in a negative indirect change factor in the use of the land (iLUC), indicating that total emissions are 27% lower than they would be with the ‘‘No biofuel’’ variant by 2030. Also, 2G biofuels achieve better results concerning the other criteria evaluated; provided that the biomass does not come from fields intended for this purpose in direct competition with agricultural land.
Daylan and Ciliz (2016) presented LCA and ELCC—Environmental Life Cycle Costing research for the lignocellulose bioethanol blends E10 and E85—10% and 85% v/v of bioethanol with conventional petrol (CG). ELCC calculations of E85 fuel use, provide a 23% lower cost with concern to CG based on driving a distance of 1 km. The results proved E85 to be the better option for decreasing emissions and the cost of fuel manufacture.
The techno-economic analysis of manufacturing methods for producing first- and second-generation bio-jet fuels from sugars and biomass, which are found in Santos et al. (2018), included the minimum jet fuel selling price (MJSP) and its environmental impact (i.e., GHG emissions and use of non-renewable energy (NREU). Although the MJSPs estimated for all scenarios are higher than those in the case of typical jet fuel, the large potential decrease in environmental impacts (in terms of GHG emissions and primary energy use) are promising for further experiments on achieving cost reductions and technological development.
The efficiency of cellulose conversion is the most important problem for cellulosic biofuels. Enzymes can transform sugars into ethanol with a 90% yield, but the production of ethanol by transforming cellulose has an efficiency of only ∼40% (Devarapalli and Atiyeh, 2015). Therefore, the transformation of cellulose biomass to ethanol requires much larger quantities of raw materials to be manufactured to obtain the same quantity of biofuel as with first-generation biofuels. In a temperate climate, 20 t of cellulosic biomass and 30 t of grass can be obtained per ha. In the most efficient cellulose transformation, 180 L ethanol is obtained from 1 t of raw material (Badger, 2002).
Commercial systems using second-generation biofuels are still under evaluation to meet government requirements concerning biofuels because classic biofuels are still cheaper. Hence, there are worries that the cost attractiveness of the second-generation biofuels will remain behind that of conventional biofuels.
Third-generation biofuels are less developed than 2G biofuels but offer some potential advantages. Two examples are algal biofuels and synthetic biology. Algal biofuel production is at the early stages of commercialization and scale-up. Their superiority is due to their high energy and oil content, as well as lower pollution content. The fourth generation of biodiesel is obtained from synthetic biology, which will enhance the physicochemical properties of biodiesel and has allowed carbon-neutral technology to be developed.
The objective of BioRen is to develop techno-economical competitive drop-in biofuels for road transport from OFMSW. The project will develop a pretreatment method for the organic fraction of MSW, industrial 2G Saccharomyces strains that produce isobutanol, chemical dehydration of isobutanol into isobutene, and conversion of isobutene into GTBE by adding category 1 glycerol. The developed processes will be integrated into an innovative waste treatment plant that combines the most efficient technologies of material reuse and is currently looking into optimizing the profitability of its organic waste fraction. Developed research allows making a progress in the development of technology drop-in biofuels for cars using the organic fraction of municipal solid waste as shown in Figure 2.
FIGURE 2. Objective of the BioRen process (BioRen, 2020).
The BioRen strategy is focused on the development of a pretreatment method, hydrolysis, and fermentation appropriate for application to biomass thus enabling the appropriate production of isobutanol and glycerol tertiary butyl ether. A pretreatment stage developed in the process, which includes an industrial saccharification process, allows isobutanol to be obtained and the chemical dehydration of isobutanol into isobutene. The isobutene is transformed into GTBE by adding glycerol. Obtained biofuels, such as isobutanol and GTBE, a beneficial additive to both diesel and petrol, which can improve engine performance and additionally decrease harmful exhaust emissions, will be tested via engine trials, which determine their impact on efficiency, emissions data, and fuel consumption (BioRen, 2020).
Renasci Smart Chain Processing (SCP) processing was implemented in the first stage of the BioRen project realization (Verhe et al., 2020). This innovative process combines waste processing technologies in a chain process producing products and energy. Renasci installation in Ostend (Belgium) converts 102,000 t/y of refuse-derived fuels RDF and 18,000 t/y of mixed plastics into reusable products (BioRen, 2020; Redant et al., 2022).
The flow sheet of the Renasci Smart Chain Processing is shown in Figure 3.
FIGURE 3. Flow sheet of Renasci Smart Chain Processing in Ostend. PET— polyethylene-terephthalate, PVC—polyvinyl chloride. P2C—plastic-to-chemicals, HTC—hydrothermal carbonization, PCC—physic-chemical combustion (Verhe et al., 2020).
Renasci SCP allowed realizing innovative technologies, sustainable, salable, and adaptable, enabling the processing of mixed waste streams continuously improved through collaboration with various acclaimed knowledge institutions. SCP is the combination of proven following technologies: high-end selective separation and sorting, plastics-2-chemicals (P2C), hydrothermal carbonization (HTC), and physical–chemical catalysis (PCC). Developed SCP processing is customizable to local waste management challenges and the modular plant can be adjusted to different waste compositions and the desired products. Developed technologies resulted in the production of best-in-class materials and energy recovery. All incoming waste is processed, and no residual waste is generated. Technologies have a minimal ecological footprint and are self-sustaining in terms of energy consumption (Verhe et al., 2020).
The first stage of the Renasci SCP process is the separation of RDF and plastic waste into partial streams: bio-organic materials, paper, and cardboard, plastics, textiles, ferrous/non-ferrous components, and inert materials. These are converted into recycling materials, products, and energy. The modern separation unit sorts MSW into recyclable and non-recyclable fractions. Each stream is separated based on its physical characteristics such as magnetism, mass, and density. The recyclable fraction of waste is cleaned, upgraded, and re-entered in the market. The non-recyclable waste fraction is processed and treated to obtain new products.
The separation unit sorts the recyclable and the non-recyclable plastics. The non-recyclable plastics are converted into hydrocarbons using the P2C method. According to P2C end of life, plastics are processed by pyrolysis (non-catalytic) and obtained vapors are condensed to obtain 75% heavy BP pyoil and 10% light BP pyoil). Non-condensable gases (7.5% of products) are incinerated and obtained heat is used in the pyrolysis process (in-process energy recycling). Heavy pyoil contains [in %] 67 linear alkenes, seven branched alkenes, 19 alkenes, six cyclic compounds, and one aromatic compound (Verhe et al., 2020).
The good quality paper/cardboard re-enters the market. The non-recyclable organic fraction is processed by hydrothermal carbonization (HTC) into bio-coal pellets. HTC is a recognized method for converting waste into a product (Hitzl et al., 2015; Zhai et al., 2017). The high calorific value of bio-coal pellets allows them to be used as a substitute for fossil fuels. Despite the raw materials, the quality of the bio-coal obtained remains in the range of caloric value of 20–24 MJ/kg which is similar to a coal energy source. The by-product of the process could be added to the soil as a conditioner.
The remaining fraction, which is too small to be separated, is treated by physicochemical and catalytic conversion (PCC). It is added to the reactor, the water is evaporated and the inorganic particles are transformed into their clean, dry, and inert ingredients. The steam and heat obtained are used to generate electricity and provide power to the facility.
The second stage of the BioRen project realization provided bio-fermentation of recycled and non-recycled parts OFMSW fractions. In the analyzed case (Table 1), processed RDF contained 44% non-recyclable organic compounds and 28% of recyclable paper/cardboard. The flow sheet of the modernized Renasci SCP processing providing bio-fermentation of all OFMSW fractions to obtain biofuels and bio-coal pellets produced from post-fermentation sludge using the HTC method is presented in Figure 4 (BioRen, 2020). So only separated ferrous, non-ferrous metal, PET/PVC, and granulated plastics will be recycled and reused on the market.
FIGURE 4. Flow sheet of Renasci innovative SCP (BioRen, 2020).
Non-recyclable organics and paper/cardboard should be pre-treated before starting the bio-fermentation process. The organic fraction of municipal solid waste (OFMSW) consisting typically 35–40% of waste paper and cardboard (WPC) fiber is a very interesting second-generation (2G) feedstock. WPC is further pre-treated with mild acid, which considerably reduced ash content to below 4% (Varghese et al., 2022). The next phase of the process is the saccharification/fermentation (SSF) set-up for isobutanol production using solid OFMSW (organics, paper, and cardboard waste) as feedstock.
The cardboard and paper wastes used to demonstrate the developed saccharification and simultaneous fermentation (SSF) process at a pilot scale were pre-treated at a Bio Base Europe Pilot Plant (BBEPP) before starting the SSF process. The paper and cardboard wastes were first pulped to a dry matter consistency of 10% w/w and heated to 50°C to increase slurry homogeneity and specific fiber surface area. The pulp was subsequently diluted to a 5% dry mass and circulated through a magnetic sieve and plastic sieve to remove ferromagnetic metal particles and plastic particles. A pasteurization step was carried out after removing the undesired particles in the pulp to kill off potential contaminants in the waste stream. A decanter centrifuge was then used to dewater the pulp. This dewatered material (>30% dry mass) was repulped to 5% and calcium carbonate was neutralized by adding nitric acid. The Ca(NO3)2 obtained is soluble in the water phase of the sludge. The pulp was finally dewatered again by applying a second decantation step. These resulted in the sludge deashing. The pretreatment process allowed obtaining homogeneous sludge, free from the undesired particles (metals and plastic) and with an increased specific fiber surface area.
Figure 5 presents isobutanol production by a fermentation process.
FIGURE 5. Flow sheet of isobutanol production; SHF enzymatic hydrolysis and saccharification; SSF —saccharification and simultaneous fermentation; CBP—consolidated bioprocessing.
In the next step, a sample of pre-treated paper/cardboard waste was subjected to a hydrolysis process providing hydrolysis of cellulose and hemicellulose by chemicals or enzymes, production of a sugar solution, and fermentation of a sugar solution into isobutanol. The organic fraction of municipal solid waste (OFMSW) consisting typically 35–40% waste paper and cardboard (WPC) fiber is a very interesting second-generation (2G) feedstock. These are further pre-treated with mild acid, which considerably reduced ash content to below 4%. The pre-treated cardboard pulp was transferred into a continuously stirred tank reactor (CSTR). The broth was directly cooled down from 50–55°C to 35°C. Before pitching the broth with yeast, urea was added to the fermenter to have a urea concentration of 2 g/kg into the liquefied cardboard pulp. Process conditions such as pH, dissolved oxygen, temperature, and feeding of sugars were controlled in the propagation step to optimize the growth of the yeast. The pH value and temperature were in an acceptable range for optimal enzyme activity (pH = 4.75–5.25, T = 50–55°C). Renasci developed an enzymatic hydrolysis process to valorize organic MSW fractions. This process produces second-generation sugars (85% glucose) that can be used as a feedstock for bio-based chemistry. Due to the mild pretreatment and enzymatically hydrolysis processes, the sugar contains practically no inhibitors, making it especially suitable for a fermentation feedstock (Redant et al., 2022). The glucan and xylan present in the pre-treated feedstock (65–70%) are easily amendable to enzymatic saccharification and can be further fermented with industrial xylose–fermenting yeast to produce 2G bioethanol. CBHI-I was identified as the most limiting cellulose enzyme during simultaneous saccharification and co-fermentation (SSCF) of the WPC pulp. To further reduce the commercial enzyme dosage and accelerate the SSCF, the secretary expression of a heterogeneous codon–optimized CBH-I gene from Talaromyce emersonii into industrial xylose–fermenting yeast strain BMD44 was engineered. Under SSCF conditions, these strains are allowed for producing the highest titer of ethanol at 6,22% (v/v) with a yield of 93.3% (Varghese et al., 2022).
A decanter centrifuge in the last stage of the fermentation process is used, the remaining solids in the fermentation slurry were separated from the broth and post-fermentation residues can be converted into bio-coal pellets using hydrothermal carbonization (HTC) (Verhe et al., 2020).
The fermentative production of isobutanol remains a challenge due to isobutanol inhibits the growth of microorganisms at concentrations of 1–2% w/w. In situ product recovery (ISPR) needs to be developed to solve this problem. From reviewed ISPR methods, technological and economic performance of sol that can be used for vent extraction and pervaporation was assessed (Vandercruysse, 2022). An isobutanol concentration of 200 g/L was reached after 57 h of fermentation. After heterogeneous azeotropic isobutanol–water distillation (Figure 5), the product obtained was isobutanol. In the production of isobutanol, the maximum yield is 1 moll of isobutanol/moll of glucose, and 411 kg of isobutanol is obtained from 1 t of glucose. A measure of 1,000 kg of biomass (25% water) gives 308 kg of isobutanol. With the expected yield of 80%, 246 kg of isobutanol can be obtained from 1 ton of biomass (25% water). The remaining 20% (200 kg) is converted into HTC. The diagram of isobutanol concentration is shown in Figure 6.
Finally, glycerol tertiary butyl ether (GTBE) is produced which is a promising fuel additive that substitutes the use of fossil fuels (reduction in CO2 emissions). It is usable in both diesel and gasoline engines and improves engine performance and cuts harmful exhaust emissions (e.g., fine dust). It can be blended in higher amounts than ethanol, without having to change the engine. The surplus of crude glycerol generated by biodiesel production is used in the production of GTBE (Verhe et al., 2020).
Hydrothermal carbonization is a method in which waste organic materials are transformed into a bio-coal and an aqueous hydrothermal carbonization liquid AHL, a fertilizer solution containing N, P, and K (Gao et al., 2019). Bio-coal pellets are usually combusted for energy recovery. Maniscalco et al. (2020) studied different methods of using bio-coal obtained from various types of waste biomass. Zhai et al. (2017) studied the implementation of hydrothermal carbonization for energy-efficient production of char pellets from sewage sludge.
The process of OFMSW hydrothermal carbonization is an effective MSW management strategy combined with the production of sustainable solid fuel. In the study of Lucian et al. (2018), processing conditions affecting the formation and composition of hydro chars obtained from OFMSW were analyzed. The study showed that the increased parameters (higher temperature, and longer reaction time) resulted in lower solid efficiency, but an increased calorific value, and content of fixed and elemental carbon.
Gupta et al. (2019) indicated that the HTC process has the greatest energy recovery potential for paper and food waste FW having a calorific value of 2.95 MJ/kg FW. Incineration tests indicated that the hydro char produced from FW has high energy productivity (2.95 MJ/kg FW) concerning combustion (2.217 MJ/kg FW) and anaerobic digestion (2.605 MJ/kg).
Roman et al. (2021) investigated the process of producing catalytic hydro char by HTC from MSW compost. The influence of individual parameters on the reaction was examined, that is, hydro treatment time (1–5 h) and amount of compost (30–120 kg/1000 L and temperature 150–230°C). Several factors were assessed for the liquid phase (TOC, conductivity, and volume recovered) and for the solid phase (mass and amount of carbon). The hydro char obtained had high catalytic activity in hydrogen breakdown (100% decomposition after 6 h of processing).
The Ingelia Company has optimized its HTC process (Hitzl et al., 2015; Burguette et al., 2016) for a wide range of feedstock. According to the laboratory tests, fermentation residue from isobutanol can be transformed into biochar using the HTC method. The carbonization degree was slightly increased with reaction time. The HTC yield increased when the dry matter concentration was increased. An optimum value for solid recovery using HTC has been detected with 80% of humidity in the feedstock. This would also be an optimum point for pumping operations. It was possible to transform the waste stream into a solid bio-coal and a liquid effluent, recovering water and nutrients. The reaction is carried out in aqueous media under a pressure of 18.7 Talaromyce emersonii—19.5 bar and a temperature of 210°C. The separation of post-treatment sludge has been satisfactory, achieved by physical, gravitational means, separating sand with silica, and calcium sulfate from hydro char. The process yield was 56.8% to bio-coal. Nitrogen, potassium, and organic matter are the main nutrients in the obtained processed water. A schematic diagram of the HTC process is given in Figure 7.
The composition of bio-coal pellets and liquid fertilizer obtained after HTC processing of post-fermentation sludge is presented in Table 2.
Material and energy consumption data for raw material, electricity, and energy and figures for assessments of the amounts of products obtained and energy utilized are presented in Table 3.
BioRen project research results in an increased value of selected municipal and industrial waste streams feeding into biofuels and bio-coal and the development of technology for the production of effective drop-in fuel additives derived from the processing of the organic solid fraction of municipal wastes. The proposed Renasci/BioRen SCP of municipal solid waste is much more environmentally friendly than that of the municipal waste incineration energy system. Process products are electricity, bio-coal pellets, biodiesel, inerts used as fillers in building materials, and second-generation GTBE biofuel. Glycerol tertiary butyl ether is the end product, which is used as a fuel additive that can be mixed with petrol or diesel in high proportions. The environmental impact of Renasci technologies is highly beneficial, especially for the production of biofuels and biochar. In the Renasci/BioRen method, 53% of waste is recovered and used for utility purposes. More than 78% of energy from waste is also recovered. The integrated production system, with a highly flexible modular configuration, is very well suited to the processing of complex waste streams. The project meets the requirements of all European regulations and directives.
The original contributions presented in the study are included in the article/Supplementary Material; further inquiries can be directed to the corresponding author.
•ZK: conception and design of the work, original draft preparation, data analysis, and conclusions. •JK: methodology, evaluation and critical review, and conclusions. •RV: concept of the bioethanol production process from the organic fraction of waste, BioRen technology development. •LD: BioRen technology development. •GD: BioRen technology development. •AM: analysis and interpretation of data and assessment of technology. •NG: literature review on biofuel generations, visualization and editing. •PH: literature review on biofuel generations, visualization, preparation, and editing.
The work is supported by the BioRen H2020 project (Grant agreement number — 818310) granted by the Innovation and Networks Executive Agency (INEA), under the powers delegated by the European Commission.
Authors LD and GDC were employed by the company Renasci.
The remaining authors declare that the research was conducted in the absence of any commercial or financial relationships that could be construed as a potential conflict of interest.
All claims expressed in this article are solely those of the authors and do not necessarily represent those of their affiliated organizations, or those of the publisher, the editors, and the reviewers. Any product that may be evaluated in this article, or claim that may be made by its manufacturer, is not guaranteed or endorsed by the publisher.
Asdrubali, F., Baldinelli, G., D’Alessandro, F., and Scrucca, F. (2015). Life cycle assessment of electricity production from renewable energies: Review and results harmonization. Renew. Sustain. Energy Rev. 42, 1113–1122. doi:10.1016/j.rser.2014.10.082
Ayodele, B. V., Alsaffar, M. A., and Mustapa, S. I. (2019). An overview of integration opportunities for sustainable bioethanol production from first- and second-generation sugar-based feedstocks. J. Clean. Prod. 245 (22), 118857. doi:10.1016/j.jclepro.2019.118857
Badger, P. C. (2002). “Ethanol from cellulose: A general review. P. 17–21,” in Trends in new crops and new uses. Editors J. Janick, and A. Whipkey (Alexandria, VA: ASHS Press).
Baruah, J., Nath, B. K., Sharma, R., Kumar, S., Deka, R. C., Baruah, D,C., et al. (2018). Recent trends in the pretreatment of lignocellulosic biomass for value-added products. Front. Energy Res. 6, 1–19. doi:10.3389/fenrg.2018.00141
Benetti, C. (2018). Low TRL biofuel technologies. Florence: ETA-Florence Renewable Energies. AvaliableAt: https://www.besustainablemagazine.com/cms2/low-trl-biofuel-technologies/.
BioRen. (2020). Deliverable report D 3.1 process conditions (ethanol production), WP9. Grant Agreement no. 818310 (unpublished report).
Burguette, P., Corma, A., Hitzl, M., Modrego, R., Ponceb, E., and Renz, M. (2016). Fuel and chemicals from wet lignocellulosic biomass waste streams by hydrothermal carbonization. Green Chem. 18, 1051–1060. doi:10.1039/c5gc02296g
Cherubini, F., Bargigli, S., and Ulgiati, S. (2009). Life Cycle Assessment (LCA) of waste management strategies: Landfilling, sorting plant and incineration. Energy 34, 2116–2123. doi:10.1016/j.energy.2008.08.023
Daylan, B., and Ciliz, N. (2016). Life cycle assessment and environmental life cycle costing analysis of lignocellulosic bioethanol as an alternative transportation fuel. Renew. Energy 89, 578–587. doi:10.1016/j.renene.2015.11.059
Devarapalli, M., and Atiyeh, H. K. (2015). A review of conversion processes for bioethanol production with a focus on syngas fermentation. Biofuel Res. J. 7, 268–280. doi:10.18331/BRJ2015.2.3.5
Ganguly, P., Sarkhel, R., and Das, P. (2021). The second- and third-generation biofuel technologies: Comparative perspectives. Sustain. Fuel Technol. Handb. 29, 29–50. doi:10.1016/b978-0-12-822989-7.00002-0
Gao, L., Volpe, M., Lucian, M., Fiori, L., and Goldfarb, J. L. (2019). Does hydrothermal carbonization as a biomass pretreatment reduce fuel segregation of coal-biomass blends during oxidation? Energy Convers. Manag. 181, 93–104. doi:10.1016/j.enconman.2018.12.009
Gupta, D., Mahajani, S. M., and Garg, A. (2019). Effect of hydrothermal carbonization as pretreatment on energy recovery from food and paper wastes. Bioresour. Technol. 285, 121329. doi:10.1016/j.biortech.2019.121329
Havlik, P., Schneider, U. A., Schmid, E., Böttcher, H., Fritz, S., Skalský, R., et al. (2011). Global land-use implications of first and second generation biofuel targets. Energy Policy 39 (10), 5690–5702. doi:10.1016/j.enpol.2010.03.030
Hitzl, M., Corma, A., Pomares, F., and Renz, M. (2015). The hydrothermal carbonization (HTC) plant as a decentral biorefinery for wet biomass. Catal. Today 257 (2), 154–159. doi:10.1016/j.cattod.2014.09.024
Jain, A., Sarsaiya, S., Awasthi, M. K., Singh, R., Rajput, R., Mishra, U. M., et al. (2022). Bioenergy and bio-products from bio-waste and its associated modern circular economy: Current research trends, challenges, and future outlooks. Fuel 307, 121859. doi:10.1016/j.fuel.2021.121859
Kargbo, H., Harris, J., and Phan, S., N. (2021). Drop-in” fuel production from biomass: Critical review on techno-economic feasibility and sustainability. Renew. Sustain. Energy Rev. 135, 110168. doi:10.1016/j.rser.2020.110168
Lucian, M., Volpe, M., Gao, L., Piro, G., Goldfarb, J. L., and Fiori, L. (2018). Impact of hydrothermal carbonization conditions on the formation of hydro chars and secondary chars from the organic fraction of municipal solid waste. Fuel 233, 257–268. doi:10.1016/j.fuel.2018.06.060
Maniscalco, M. P., Volpe, M., and Messineo, A. (2020). Hydrothermal carbonization as a valuable tool for energy and environmental applications: A review. Energies 13 (16), 4098. doi:10.3390/en13164098
Melin, K., Nieminen, H., Klueh, D., Laari, A., Koiranen, T., and Gaderer, M. (2022). Techno-economic evaluation of novel hybrid biomass and electricity-based ethanol fuel production. Front. Energy Res. 10, 1–17. doi:10.3389/fenrg.2022.796104
Meng, W., Bai, X., Wang, B., Liu, Z., Lu, S., and Yang, B. (2019). Biomass-derived carbon dots and their applications. Energy Environ. Mater. 2 (3), 172–192. doi:10.1002/eem2.12038
Montejo, C., Costa, C., Ramos, P., and Marquez, M. (2011). Analysis and comparison of municipal solid waste and reject fraction as fuels for incineration plants. Appl. Therm. Eng. 31 (13), 2135–2140. doi:10.1016/j.applthermaleng.2011.03.041
Pedersen, M., and Meyer, A. S. (2010). Lignocellulose pretreatment severity - relating pH to biomatrix opening. New Biotechnol. 27, 739–750. doi:10.1016/j.nbt.2010.05.003
Pedersen, M., Viksø-Nielsen, A., and Meyer, A. S. (2010). Monosaccharide yields and lignin removal from wheat straw in response to catalyst type and pH during mild thermalpretreatment. Process. Biochem. 45, 1181–1186. doi:10.1016/j.biombioe.2009.01.004
Plazzotta, S., Manzocco, L., and Nicoli, M. C. (2017). Fruit and vegetable waste management and the challenge of fresh-cut salad. Trends Food Sci. Technol. 63, 51–59. doi:10.1016/j.tifs.2017.02.013
Pourhashem, G., Adler, P. R., and Spatari, S. (2016). Time effects of climate change mitigation strategies for second generation biofuels and co-products with temporary carbon storage. J. Clean. Prod. 112, 2642–2653. doi:10.1016/j.jclepro.2015.09.135
Redant, E., Desender, B. G., and Verhe, R. (2022). “Waste-to-sugars; a sustainable feedstock for biobased chemistry,” in procedia, 18th International Conference on Renewable Resources and Biorefineries RRB 2022 (Bruges Belgium: Ghent University), 38.
Resch, M. G., and Emme, B. (2022). Using incremental changes to convert lignocellulosic feedstocks to cellulosic ethanol. Front. Energy Res. 10, 1–6. doi:10.3389/fenrg.2022.835714
Roman, F. F., Diaz de Tuesta, J. L., Praça, P., Silva, A. M. T., Faria, J. L., and Gomes, H. T. (2021). Hydrochars from compost derived from municipal solid waste: Production process optimization and catalytic applications. J. Environ. Chem. Eng. 9 (1), 104888. doi:10.1016/j.jece.2020.104888
Ruiz, H. A., Conrad, M., Sun, S., Sanchez, A., Rocha, G. J. M., Romaní, A., et al. (2020). Engineering aspects of hydrothermal pretreatment: From batch to continuous operation, scale-up and pilot reactor under biorefinery concept. Bioresour. Technol. 299, 122685. doi:10.1016/j.biortech.2019.122685
Ruiz, H. A., Silva, P. D., Ruzene, D. S., Lime, L. F., Vicente, A. A., and Teixeira, J. A. (2012). Bioethanol production from hydrothermal pretreatment wheat straw by flocculating Saccharomyces cerevisiae strain- Effect of process conditions. Fuel 95, 528–536. doi:10.1016/j.fuel.2011.10.060
Ruiz, H. A., Thomsen, M. H., and Trajano, H. L. (2017). Hydrothermal processing in biorefineries. Production of bioethanol and high added-value compounds of second and third generation biomass (Cham, Switzerland: Springer International Publishing).
Santos, C. I., Silva, C. C., Mussatto, S. I., Osseweijer, P., van der Wielen, L. A. M., and Posada, J. A. (2018). Integrated 1st and 2nd generation sugarcane bio-refinery for jet fuel production in Brazil: Techno-economic and greenhouse gas emissions assessment. Renew. Energy 129, 733–747. doi:10.1016/j.renene.2017.05.011
Schnoor, J. L. (2011). Cellulosic biofuels disappoint. Environ Sci. Technol. 45 (17), 7099. doi:10.1021/es2026032
Singh, D., Sharma, D., Soni, S. L., Sharma, S., Kumar Sharma, P., and Jhalani, A. (2019). A review on feedstocks, production processes, and yield for different generations of biodiesel. Fuel 262, 116553. doi:10.1016/j.fuel.2019.116553
Tao, F., Zuo, Y., Xu, L. D., Lv, L., and Zhang, L. (2014). Internet of things and BOM-Based life cycle assessment of energy-saving and emission-reduction of products. IEEE Trans. Ind. Inf. 10 (2), 1252–1261. doi:10.1109/tii.2014.2306771
Trends in Solid Waste Management (2021). worldbank. AvaliableAt: https://datatopics.worldbank.org/what-a-waste/trends_in_solid_waste_management.html(accessed 10 10, 2021).doi:10.1016/j.jclepro.2006.06.012
Vandercruysse, C. (2022). “Fermentative isobutanol production from paper and cardboard waste derived sugar applying different in situ recovery techniques,” in procedia, 18th International Conference on Renewable Resources and Biorefineries RRB 2022 (Bruges Belgium: Ghent University), 39.
Varghese, S., Demeke, M,M., and Thevelein, J. M. (2022). “Secretary-expression of heterogenous celluloniobiohydrolase- I and endoglucanae improves the simultaneous saccharification and co-fermentation of pre-treated wastepaper and cardboard fiber to ethanol,” in procedia, 18th International Conference on Renewable Resources and Biorefineries RRB 2022 June 1–3, 2022 (Bruges Belgium: Ghent University), 38.
Verhe, R., De Clercq, G., Redant, E., and Desender, L. (2020). Production of biofuels and bioenergy from the organic fraction of municipal solid waste and refuse derived fuel. AvaliableAt: www.circularhotspot.pl/userfiles/Gilles%20De%20Clercq.pdf (accessed 12 01, 2021).
Verhé, R., Echim, C., De Greyt, W., and Stevens, C. (2011). “Production of biodiesel via chemical catalytic conversion,” in Handbook of biofuels production : Processes and technologies. Editors R. Luque, J. Campelo, and J. Clark (Philadelphia: Woodhead Publishing), 97–133. doi:10.1533/9780857090492.2.97
Viguie, J., Ullrich, N., Porot, P., Bournay, L., Hecquet, M., and Rousseau, J. (2013). BioTfueL project: Targeting the development of second-generation biodiesel and biojet fuels. Oil Gas Sci. Technol. 68, 935–946.
Yang, B., and Wyman, C. E. (2004). Effect of xylan and lignin removal by batch and flow-through pretreatment on the enzymatic digestibility of corn stover cellulose. Biotechnol. Bioeng. 86, 88–98. doi:10.1002/bit.20043
Keywords: biofuels, waste management, bioethanol, fermentation, management, municipal solid waste
Citation: Kowalski Z, Kulczycka J, Verhé R, Desender L, De Clercq G, Makara A, Generowicz N and Harazin P (2022) Second-generation biofuel production from the organic fraction of municipal solid waste. Front. Energy Res. 10:919415. doi: 10.3389/fenrg.2022.919415
Received: 13 April 2022; Accepted: 21 July 2022;
Published: 25 August 2022.
Edited by:
Anuj Kumar Chandel, Lorena School of Engineering, University of São Paulo, BrazilReviewed by:
Rahmath Abdulla, Universiti Malaysia Sabah, MalaysiaCopyright © 2022 Kowalski, Kulczycka, Verhé, Desender, De Clercq, Makara, Generowicz and Harazin. This is an open-access article distributed under the terms of the Creative Commons Attribution License (CC BY). The use, distribution or reproduction in other forums is permitted, provided the original author(s) and the copyright owner(s) are credited and that the original publication in this journal is cited, in accordance with accepted academic practice. No use, distribution or reproduction is permitted which does not comply with these terms.
*Correspondence: Joanna Kulczycka, a3VsY3p5Y2thQGFnaC5lZHUucGw=
Disclaimer: All claims expressed in this article are solely those of the authors and do not necessarily represent those of their affiliated organizations, or those of the publisher, the editors and the reviewers. Any product that may be evaluated in this article or claim that may be made by its manufacturer is not guaranteed or endorsed by the publisher.
Research integrity at Frontiers
Learn more about the work of our research integrity team to safeguard the quality of each article we publish.