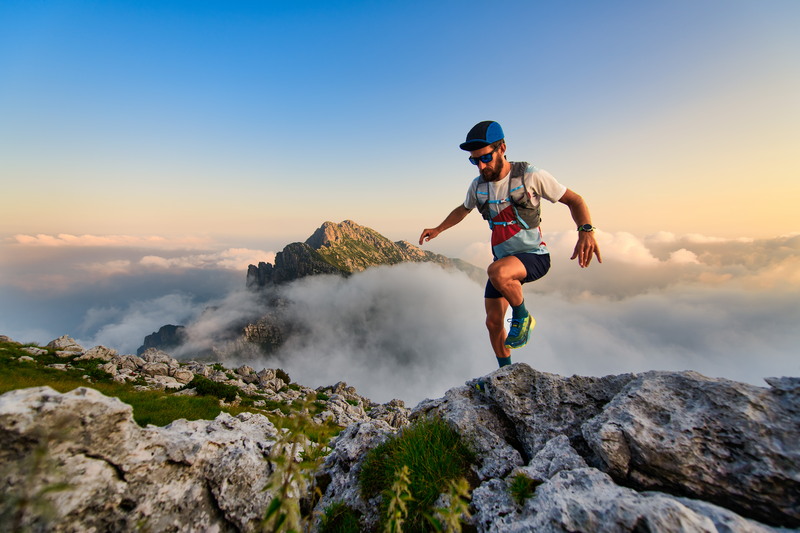
94% of researchers rate our articles as excellent or good
Learn more about the work of our research integrity team to safeguard the quality of each article we publish.
Find out more
MINI REVIEW article
Front. Energy Res. , 05 August 2022
Sec. Process and Energy Systems Engineering
Volume 10 - 2022 | https://doi.org/10.3389/fenrg.2022.915893
This article is part of the Research Topic Green and Sustainable LNG Supply Chain: A Bridge to a Low Carbon Energy Society View all 5 articles
Liquefied natural gas (LNG) has become an important part in the energy industry on account of its high energy density, low carbon emission, and convenient transportation. In recent years, with the discovery of unconventional natural gas resources, the situation of the world’s natural gas liquefaction plants using conventional natural gas as feedstock is changing. Unlike traditional LNG plants, unconventional natural gas liquefaction processes require special considerations in design and manufacturing. This review summarizes and analyzes the characteristics and differences of several typical unconventional natural gas liquefaction processes compared to traditional natural gas liquefaction processes, including coalbed methane liquefaction, synthetic natural gas liquefaction, LNG-FPSO, and PLNG (pressurized liquefied natural gas). Moreover, a state-of-the-art review of the recent progress on design and optimization of unconventional natural gas liquefaction processes is presented.
Natural gas is a kind of high quality and clean fossil energy. It will play an important role in a long historical period before the human society reaches the stage where renewable energy is the main form of energy. Currently, natural gas accounts for about 23% of the world’s energy structure, which is a key to unlocking access to secure, clean, and modern energy. It can immediately reduce emissions and improve the quality of clean air by replacing coal, oil, and conventional biomass. According to the forecasts of BP, the International Energy Agency (IEA), and other agencies, natural gas consumption will surpass oil consumption to become the world’s second largest energy around 2035. In order to achieve high-density storage and long-distance transport, natural gas is usually liquefied into a cryogenic liquid called liquefied natural gas (LNG) near gas reservoirs in a large based-load plant, thereby reducing its volume by a factor of 600. Nowadays, as an important means of natural gas development and utilization, LNG has already become an important part of the energy industry.
From 2007 to 2017, world natural gas consumption increased from 2.96 × 1012 m3 to 3.67 × 1012 m3, with an average annual growth rate of 2.2%. At the same time, the international trade volume of LNG increased from 2.26 × 1011 m3 to 3.93 × 1011 m3, with an average annual growth rate of 5.7%, much higher than the growth rate of world GDP. In 2020, global LNG trade increased to 356.1 MT, a small increase by 1.4 MT versus 2019, but another year of consecutive growth in LNG trade despite COVID-19-related impacts on the supply and demand sides (IGU. 2021 World LNG Report, 2021).
After decades of development and application, liquefied natural gas technology has formed a variety of liquefaction processes. Also, further effort still continues for the purpose of improving the processes in efficiency, capacity, and reliability. Natural gas liquefaction is a kind of typical energy-intensive process. Many researchers have been devoted to the design of novel liquefaction processes and the optimization of existing liquefaction processes to minimize energy consumption (He and Ju, 2014a; He et al., 2018). In terms of refrigeration cycles, there are mainly three conventional LNG processes: cascade liquefaction process, mixed refrigerant liquefaction process, and liquefaction process with the expander. Natural gas is composed of different kinds of hydrocarbons and secondary gases. In the process of liquefaction, its specific heat varies significantly over temperature, depending on the pressure and composition. Unconventional gas sources are often quite different in composition from conventional gas. For example, coal-bed methane and shale gas are both poor gases with high methane content. As a result, unconventional natural gas liquefaction processes often need to be improved upon basic processes, which can also be a composite process using different combinations of parts of processes.
The mixed refrigerant (MR) liquefaction process is widely utilized in LNG plants. One dominant process (widely called C3-MR or propane-precooled mixed-refrigerant process) has been considered the reasonable choice for large-scale liquefaction. The variable temperature evaporation characteristics of the mixed refrigerant can match the distributed load in the cooling process of natural gas well, which has great reference significance for the design and optimization of unconventional natural gas liquefaction processes. The optimization of the mixed refrigerant composition is a multi-variable, nonlinear, and strong coupling issue, which can reach high exergy efficiency by making the heat exchange curves match rationally. Cao et al. (2016) carried out robustness analysis of the mixed refrigerant composition employed in the single mixed refrigerant (SMR) LNG process. The results showed that the robustness of the mixed refrigerant composition was very strong because the exergy efficiency was maintained at about 0.40, even though the ratio of the mixed refrigerant was restrained. Xu et al. (2013) and Xu et al. (2014) investigated the performance diagnosis mechanism for the single mixed refrigerant (SMR) process. A control strategy was then proposed to control the changes in the working refrigerant composition under different working conditions. By adjusting the flow rates, it is easy to decouple the control variables and automate the system. Finally, this approach was validated by process simulation and shown to be highly adaptive and exergy efficient in response to changing working conditions. He and Ju (2014b), He and Ju (2014c), He and Ju (2015), He and Ju (2016), and He et al. (2019) presented various natural gas liquefaction processes for small-scale LNG plants in skid-mount packages. Optimization analysis was carried out on the basis of the mixed refrigerant process and parallel nitrogen expansion process, along with dynamic simulation. In addition to the MR processes, the nitrogen expansion system is a commonly utilized process in the small-scale LNG plant. Yuan et al. (2014) presented a novel small-scale liquefaction process adopting single nitrogen expansion with carbon dioxide pre-cooling. The process can achieve a liquefaction rate of 0.77 with a unit energy consumption of 9.90 kW/kmol/h.
Several review articles (Khan et al., 2017; He et al., 2018; Zhang et al., 2020; Yin and Ju, 2022) on LNG technology have been published in recent years. Zhang et al. (2020) presented a quantitative technical and economic review of the status of LNG processes for onshore large-scale, onshore small-scale, and offshore applications based on industrial practices in optimization results in academic literature works and technical reports. Khan et al. (2017) provided a retrospective review of natural gas liquefaction technologies and optimization methodologies. He et al. (2018) summarized natural gas liquefaction progresses on the design and optimization in recent years for onshore and offshore LNG devices. Yin and Ju, (2022) presented an overview of recent progresses on the design and optimization of BOG re-liquefaction processes, which are classified into indirect re-liquefaction processes and direct re-liquefaction processes. In recent years, many researchers have paid attention to the study of the unconventional natural gas liquefaction process. This article reviews the liquefaction process of unconventional natural gas sources, including coalbed methane liquefaction, synthetic natural gas liquefaction, LNG-FPSO, and PLNG (pressurized liquefied natural gas). Otherwise, the characteristics and differences of unconventional natural gas liquefaction processes compared to traditional natural gas liquefaction processes are summarized and analyzed.
Coalbed methane (CBM) is a primary type of unconventional natural gas adsorbed in coal seams. Its amount around the world is estimated to be 26 × 1012 m3 (Flores, 1998). Different from conventional natural gas, CBM usually has a low concentration of methane and contains a high proportion of nitrogen, which cannot be removed by purification procedures applied in conventional LNG processes. As a result, for the liquefaction of coalbed methane with low-methane concentration, the key is the extraction process. At present, the main extraction methods are cryogenic distillation and pressure swing adsorption (PSA).
Cryogenic distillation separation technology uses boiling point difference to separate methane and nitrogen/oxygen. This is the most efficient technology to achieve the separation of methane from oxygen and nitrogen from the perspective of thermodynamics. PSA technology has the advantages of low-energy consumption, flexible and convenient operation, and continuous operation at room temperature. At present, the separation effect is the main factor restricting the practical application of PSA.
The safety of oxygen is also an important problem in the process of low-methane concentration coalbed methane liquefaction. No matter the extraction is carried out by cryogenic distillation or PSA, the safety problems faced by methane, oxygen, and nitrogen separation could not be fundamentally avoided because the concentration in local space could not be controlled. Some researchers believe that oxygen in CBM must be removed safely at the beginning of the process (such as combustion deoxygenation) and not in subsequent adsorption, liquefaction, or distillation processes to ensure the safety of actual industrial plants. To this end, they focused on methane concentration and liquefaction of deoxygenated coalbed methane (CH4/N2 mixture). The liquefaction system performance and the heat transfer characteristics differ from those of conventional natural gas liquefaction processes and depend on the nitrogen content.
Gao et al. (2010), Gao et al. (2011a), Gao et al. (2011b), and Lin et al. (2018a) established, optimized, and evaluated liquefaction processes for the nitrogen/methane mixture with the nitrogen mole fraction ranging between 0 and 70%. Two separation technology schemes, adsorption–liquefaction and distillation–liquefaction, were considered in the processes, and the effects of different nitrogen content on the separation–liquefaction processes were investigated. Considering that the presence of a large amount of nitrogen may affect the solubility of CO2 in LNG, Gao et al. (2012) and Shen et al. (2012) conducted experimental tests and theoretical calculations on the cryogenic solubility of CO2 in the CH4–N2 mixture, and the results are of practical value for considering the CO2 removal index in high-nitrogen-content natural gas liquefaction engineering. Li et al. (2010) and Li et al. (2011) proposed a liquefaction process designed for the specified oxygen-bearing CBM and analyzed the flammability limits for the liquefaction process. In the process, oxygen and nitrogen are nearly removed completely, achieving a high-purity liquefied natural gas product with a high methane recovery rate. The applicability and safety of the liquefaction process were also analyzed. Du et al. (2011) explored the heat transfer characteristics of supercritical cooling in the process of coalbed methane liquefaction.
In the industrial production process, mixed gas products or by-products with methane–hydrogen as the main active ingredient are often obtained, such as synthetic natural gas (SNG), coke oven gas (COG), and synthetic ammonia tail gas. The separation and liquefaction of the mixture into LNG is convenient for storage and transportation and can improve economic benefits. However, the presence of hydrogen has a significant effect on SNG and COG liquefaction processes.
Lin et al. (2017) proposed a separation method combining rectification and flash distillation to separate hydrogen from SNG to produce LNG. Under the same operating parameters, the liquefaction rate of this method is higher than that of distillation–separation alone, and the unit energy consumption is 7%–10% lower than that of other conventional processes. The influence of hydrogen content on the liquefied process of COG is also discussed in the article (Lin et al., 2014). An improved nitrogen expansion refrigeration cycle is proposed and optimized to produce LNG from COG. With the increase of hydrogen content in COG and the improvement of methane recovery, the energy consumption increases. The unit energy consumption of the distillation process is about 10% lower than that of the non-distillation process.
Gu et al. (2019) developed a coal-based coproduction process of liquefied natural gas and methanol (CTLNG-M), and key units are simulated. The simulation results show that the CTLNG-M process can obtain a carbon utilization efficiency of 39.6%, bringing about a reduction of CO2 emission by 130,000 tons/a compared to the CTSNG process. However, the energy consumption of the new process increased by 9.3% after detailed analysis of energy consumption.
Xu et al. (2018), Xu and Lin (2021a), and Xu and Lin (2021b) constructed and optimized cryogenic processes to produce LNG and liquid hydrogen at the same time from COG. Methane and hydrogen were separated through the distillation column, and the different refrigeration cycles were simulated to provide the cooling capacity for the cooling and liquefaction process before and after the rectification. Thus, high-purity LNG and liquid hydrogen were obtained. The recoveries of LNG and hydrogen are both greater than 97%.
The sea is rich in oil and gas resources. However, for the natural gas resources in the deep sea, the cost of LNG production is too high, whether it is delivered by submarine pipelines or the construction of large permanent offshore platforms. A more practical solution is to produce LNG on floating platforms such as FPSO. The small and shaky space presents many special challenges to the production of FLNG: 1) rocking caused by waves and wind must be considered in the design of process equipment. On the one hand, the strength and fatigue resistance required depends on the severity of the shaking. On the other hand, process equipment with two-phase flow may be affected by the swaying of the hull, resulting in performance degradation. 2) Compared with onshore installations, the narrow space on board also presents difficulties in the equipment design and layout. 3) It is difficult to strictly separate the fuel storage area from the personnel activity area. Therefore, the storage of fuel on board should be reduced as much as possible. Proper process selection can reduce the space required for storing combustible materials. 4) More corrosion-resistant materials are required for offshore installations.
From the perspective of the liquefaction process, the C3MR process, which performs well in onshore installations, was ruled out first because it requires large quantities of propane storage, which is highly hazardous. The nitrogen expansion process, which is rarely considered in large- or medium-scale onshore plants due to its low energy efficiency, is considered to be a reasonable choice for FLNG installations with a capacity of less than 1.5 Mt/a because of the inherent safety of nitrogen refrigerant. The AP-N process is the nitrogen expansion process for FLNG developed by APCI, which has two pressure levels and three expander temperatures. In addition, if the hydrofluorocarbon (HFC)-class refrigerant is used for pre-cooling, it evolves into the AP-HN process, which can increase the suitable capacity of the nitrogen expansion process to 2.0 Mt/a. For large-scale FLNG units above 3 Mt/a, DMR is the best choice. For small-scale FLNG devices, SMR is a better choice if high efficiency and few devices are preferred. In terms of safety, the nitrogen expansion cycle shows the best performance.
Zhao et al. (2012) and Zhao et al. (2013) carried out an experimental and numerical investigation of the hydrodynamic interaction and the response of a single point turret-moored floating liquefied natural gas (FLNG) system, which is a new type of a floating LNG (liquid natural gas) platform that consists of a ship-type FPSO hull equipped with LNG storage tanks and liquefaction plants. Chen et al. (2015) developed liquefaction technology and a key device of FLNG topside for the South China Sea with an appropriate capacity of 2 million ton/year. It contains the new process of twin columns and two circulations of amine solution, the improved DMR liquefaction process, particularly for FLNG, uses the aviation derivative gas turbine to drive the refrigerant compressor and power generation. The self-developed FLNG aluminum coil-wound heat exchanger (CWHE) is used as the pre-cooling and cryogenic main heat exchanger.
Yan and Gu, (2010) and Gu and Ju, (2011) studied the effect of parameters on the performance of the LNG-FPSO offloading system in offshore-associated gas fields. The offloading system for LNG transportation from LNG-FPSO to LNG carriers is one of the most important parts in LNG-FPSO. The results showed that there was an economic mass flow rate for the practical design on the balance of the cost in pump head and BOG. The height difference of the pipeline must be considered for the increase of required pump head and harms from pressure changes. The effects of LNG-tank sloshing on the FLNG system and on shell-side pressure drop and offshore adaptability of the LNG-FPSO spiral-wound heat exchanger have also been investigated by researchers (Hu et al., 2017; Sun et al., 2019a; Sun et al., 2019b).
Pressurized liquefied natural gas (PLNG) is a liquefied natural gas stored at a higher pressure (1 MPa–2 MPa). The liquefaction temperature is about −100°C to −120°C. The higher liquefaction temperature not only reduces the energy consumption of the liquefaction process but also greatly increases the solubility of CO2 in LNG (the solubility of CO2 in LNG is less than 100 ppm under atmospheric pressure but can increase to 3%–6% under PLNG conditions). The increase of CO2 solubility makes it possible to remove pretreatment equipment, which occupies a large area in the LNG process, making it possible to implement LNG on offshore platforms with very limited sites. Xiong et al. (2015), Xiong et al. (2016) and Lin et al. (2018b), Lin et al. (2018c) studied the optimization of PLNG processes and proposed a novel PLNG process combining CO2 condensation–separation, which made the PLNG process completely break through the limitation of CO2 content and realized zero CO2 emission in the LNG process.
With the exploitation and application of unconventional natural gas sources, research on unconventional natural gas liquefaction will be an important development direction in the future. Several potential developments in the unconventional natural gas liquefaction process design and optimization in the future may include:
1) Research on heavy hydrocarbon separation technology suitable for lean gas; study on safety characteristics of oxygen-containing coalbed methane; safe and efficient removal of oxygen from coalbed methane; efficient separation of methane/nitrogen (adsorption, distillation); efficient separation of methane/hydrogen; research and development of unconventional natural gas liquefaction processes to realize the overall energy optimization of separation and liquefaction processes.
2) Offshore natural gas liquefaction mainly needs to face problems such as narrow site and platform shaking, and its development direction includes: safe and compact process design suitable under offshore shaking conditions; study on the influence of sloshing conditions on the performance of the liquefaction unit; research and development of key equipment of the liquefaction unit suitable for sloshing conditions; study on transportation characteristics of LNG in sloshing hose.
3) Development directions of basic research related to natural gas liquefaction include: gas–liquid equilibrium, solubility, condensation heat transfer characteristics, and supercritical fluid cooling heat transfer characteristics of different components of natural gas; study on the gas–liquid equilibrium and condensing and evaporating heat transfer characteristics of different refrigerant mixtures.
JX and WL contributed to the conception, design, investigation, and analysis of the study. XC and HZ wrote sections of the manuscript. All authors contributed to manuscript revision and read and approved the submitted version.
The authors declare that the research was conducted in the absence of any commercial or financial relationships that could be construed as a potential conflict of interest.
All claims expressed in this article are solely those of the authors and do not necessarily represent those of their affiliated organizations, or those of the publisher, the editors, and the reviewers. Any product that may be evaluated in this article, or claim that may be made by its manufacturer, is not guaranteed or endorsed by the publisher.
The authors gratefully acknowledge the support from the State Key Laboratory of Clean Energy Utilization (Open Fund Project No. ZJUCEU2021014) and the Central Guidance on Local Science and Technology Development Fund of Shanghai City (No. YDZX20213100003002)
Cao, L., Liu, J., and Xu, X. (2016). Robustness Analysis of the Mixed Refrigerant Composition Employed in the Single Mixed Refrigerant (SMR) Liquefied Natural Gas (LNG) Process. Appl. Therm. Eng. 93, 1155–1163. doi:10.1016/j.applthermaleng.2015.10.072
Chen, J., Center, R. D., Amp, C. G., and Group, P. (2015). Scheme Research of FLNG Liquefaction Technology and Key Device in the South China Sea. Ciesc J.
Du, Z., Lin, W., and Gu, A. (2011). Prediction of Turbulent Convective Heat Transfer to Supercritical CH4/N2 in a Vertical Circular Tube. J. Heat Transfer-Transactions Asme 133 (11). doi:10.1115/1.4004433
Flores, R. M. (1998). Coalbed Methane: From Hazard to Resource. Int. J. Coal Geol. 35 (1), 3–26. doi:10.1016/s0166-5162(97)00043-8
Gao, T., Lin, W., Gu, A., and Gu, M. (2010). Coalbed Methane Liquefaction Adopting a Nitrogen Expansion Process with Propane Pre-Cooling. Appl. Energy 87 (7), 2142–2147. doi:10.1016/j.apenergy.2009.12.010
Gao, T., Lin, W., and Gu, A. (2011). Improved Processes of Light Hydrocarbon Separation from LNG with its Cryogenic Energy Utilized. Energy Convers. Manag. 52 (6), 2401–2404. doi:10.1016/j.enconman.2010.12.040
Gao, T., Lin, W., Liu, W., Gu, A., and Qi, Y. (2011). CBM Liquefaction Process Integrated with Distillation Separation of Nitrogen. J. Chem. Eng. Jpn. 44 (8), 555–560. doi:10.1252/jcej.10we032
Gao, T., Shen, T., Lin, W., Gu, A., and Ju, Y. (2012). Experimental Determination of CO2 Solubility in Liquid CH4/N2 Mixtures at Cryogenic Temperatures. Ind. Eng. Chem. Res. 51 (27), 9403–9408. doi:10.1021/ie3002815
Gu, J., Yang, S., and Kokossis, A. (2019). Modeling and Analysis of Coal-Based Lurgi Gasification for LNG and Methanol Coproduction Process. Processes 7 (10). doi:10.3390/pr7100688
Gu, Y., and Ju, Y. L. (2011). Corrigendum to “Effect of Parameters on Performance of LNG-FPSO Offloading System in Offshore Associated Gas Fields” [Appl. Energy 87 (11) (2010) 3393-3400]. Appl. Energy 88 (1), 417. doi:10.1016/j.apenergy.2010.07.027
He, T. B., and Ju, Y. L. (2014). A Novel Process for Small-Scale Pipeline Natural Gas Liquefaction. Appl. Energy 115, 17–24. doi:10.1016/j.apenergy.2013.11.016
He, T., Chong, Z. R., Zheng, J., Ju, Y., and Linga, P. (2019). LNG Cold Energy Utilization: Prospects and Challenges. Energy 170, 557–568. doi:10.1016/j.energy.2018.12.170
He, T., and Ju, Y. (2014). A Novel Conceptual Design of Parallel Nitrogen Expansion Liquefaction Process for Small-Scale LNG (Liquefied Natural Gas) Plant in Skid-Mount Packages. Energy 75, 349–359. doi:10.1016/j.energy.2014.07.084
He, T., and Ju, Y. (2014). Design and Optimization of a Novel Mixed Refrigerant Cycle Integrated with NGL Recovery Process for Small-Scale LNG Plant. Ind. Eng. Chem. Res. 53 (13), 5545–5553. doi:10.1021/ie4040384
He, T., and Ju, Y. (2016). Dynamic Simulation of Mixed Refrigerant Process for Small-Scale LNG Plant in Skid Mount Packages. Energy 97, 350–358. doi:10.1016/j.energy.2016.01.001
He, T., and Ju, Y. (2015). Optimal Synthesis of Expansion Liquefaction Cycle for Distributed-Scale LNG (Liquefied Natural Gas) Plant. Energy 88, 268–280. doi:10.1016/j.energy.2015.05.046
He, T., Karimi, I. A., and Ju, Y. (2018). Review on the Design and Optimization of Natural Gas Liquefaction Processes for Onshore and Offshore Applications. Chem. Eng. Res. Des. 132, 89–114. doi:10.1016/j.cherd.2018.01.002
Hu, Z.-Q., Wang, S.-Y., Chen, G., Chai, S.-H., and Jin, Y.-T. (2017). The Effects of LNG-Tank Sloshing on the Global Motions of FLNG System. Int. J. Nav. Archit. Ocean Eng. 9 (1), 114–125. doi:10.1016/j.ijnaoe.2016.09.007
Khan, M. S., Karimi, I. A., and Wood, D. A. (2017). Retrospective and Future Perspective of Natural Gas Liquefaction and Optimization Technologies Contributing to Efficient LNG Supply: A Review. J. Nat. Gas Sci. Eng. 45, 165–188. doi:10.1016/j.jngse.2017.04.035
Li, Q., Wang, L., and Ju, Y. (2010). Liquefaction and Impurity Separation of Oxygen-Bearing Coal-Bed Methane. Front. Energy Power Eng. China 4 (3), 319–325. doi:10.1007/s11708-010-0115-9
Li, Q. Y., Wang, L., and Ju, Y. L. (2011). Analysis of Flammability Limits for the Liquefaction Process of Oxygen-Bearing Coal-Bed Methane. Appl. Energy 88 (9), 2934–2939. doi:10.1016/j.apenergy.2011.02.035
Lin, W., Xiong, X., and Gu, A. (2018). Optimization and Thermodynamic Analysis of a Cascade PLNG (Pressurized Liquefied Natural Gas) Process with CO2 Cryogenic Removal. Energy 161, 870–877. doi:10.1016/j.energy.2018.07.051
Lin, W., Xiong, X., Spitoni, M., and Gu, A. (2018). Design and Optimization of Pressurized Liquefaction Processes for Offshore Natural Gas Using Two-Stage Cascade Refrigeration Cycles. Ind. Eng. Chem. Res. 57 (17), 5858–5867. doi:10.1021/acs.iecr.7b04080
Lin, W., Xu, J., Gao, T., and Gu, A. (2018). Analysis of Heat Transfer Irreversibility in Processes for Liquefaction of Coalbed Methane with Nitrogen. Ind. Eng. Chem. Res. 57 (17), 5895–5902. doi:10.1021/acs.iecr.7b04083
Lin, W., Xu, J., Zhang, L., and Gu, A. (2017). Synthetic Natural Gas (SNG) Liquefaction Processes with Hydrogen Separation. Int. J. Hydrogen Energy 42 (29), 18417–18424. doi:10.1016/j.ijhydene.2017.04.141
Lin, W., Zhang, L., and Gu, A. (2014). Effects of Hydrogen Content on Nitrogen Expansion Liquefaction Process of Coke Oven Gas. Cryogenics 61, 149–153. doi:10.1016/j.cryogenics.2014.01.006
Shen, T., Gao, T., Lin, W., and Gu, A. (2012). Determination of CO2 Solubility in Saturated Liquid CH4 + N2 and CH4 + C2H6 Mixtures Above Atmospheric Pressure. J. Chem. Eng. Data 57 (8), 2296–2303. doi:10.1021/je3002859
Sun, C., Li, Y., Han, H., Zhu, J., Qin, Y., Wang, S., et al. (2019). Experimental Study on Shell-Side Pressure Drop and Offshore Adaptability of LNG-FPSO Spiral Wound Heat Exchanger. Exp. Therm. Fluid Sci. 109. doi:10.1016/j.expthermflusci.2019.109874
Sun, C., Li, Y., Han, H., Zhu, J., Wang, S., and Liu, L. (2019). Experimental and Numerical Simulation Study on the Offshore Adaptability of Spiral Wound Heat Exchanger in LNG-FPSO DMR Natural Gas Liquefaction Process. Energy 189. doi:10.1016/j.energy.2019.116178
Xiong, X., Lin, W., and Gu, A. (2016). Design and Optimization of Offshore Natural Gas Liquefaction Processes Adopting PLNG (Pressurized Liquefied Natural Gas) Technology. J. Nat. Gas Sci. Eng. 30, 379–387. doi:10.1016/j.jngse.2016.02.046
Xiong, X., Lin, W., and Gu, A. (2015). Integration of CO2 Cryogenic Removal with a Natural Gas Pressurized Liquefaction Process Using Gas Expansion Refrigeration. Energy 93, 1–9. doi:10.1016/j.energy.2015.09.022
Xu, J., and Lin, W. (2021). Research on Systems for Producing Liquid Hydrogen and LNG from Hydrogen-Methane Mixtures with Hydrogen Expansion Refrigeration. Int. J. Hydrogen Energy 46 (57), 29243–29260.
Xu, J., and Lin, W. (2021). Integrated Hydrogen Liquefaction Processes with LNG Production by Two-Stage Helium Reverse Brayton Cycles Taking Industrial By-Products as Feedstock Gas. Energy 227, 120443. doi:10.1016/j.energy.2021.120443
Xu, J., Lin, W., and Xu, S. (2018). Hydrogen and LNG Production from Coke Oven Gas with Multi-Stage Helium Expansion Refrigeration. Int. J. Hydrogen Energy 43 (28), 12680–12687. doi:10.1016/j.ijhydene.2018.05.137
Xu, X., Liu, J., Cao, L., and Pang, W. (2014). Automatically Varying the Composition of a Mixed Refrigerant Solution for Single Mixed Refrigerant LNG (Liquefied Natural Gas) Process at Changing Working Conditions. Energy 64, 931–941. doi:10.1016/j.energy.2013.10.040
Xu, X., Liu, J., Jiang, C., and Cao, L. (2013). The Correlation Between Mixed Refrigerant Composition and Ambient Conditions in the PRICO LNG Process. Appl. Energy 102, 1127–1136. doi:10.1016/j.apenergy.2012.06.031
Yan, G., and Gu, Y. (2010). Effect of Parameters on Performance of LNG-FPSO Offloading System in Offshore Associated Gas Fields. Appl. Energy 87 (11), 3393–3400. doi:10.1016/j.apenergy.2010.04.032
Yin, L., and Ju, Y. (2022). Review on the Design and Optimization of BOG Re-Liquefaction Process in LNG Ship. Energy 244, 123065. doi:10.1016/j.energy.2021.123065
Yuan, Z., Cui, M., Xie, Y., and Li, C. (2014). Design and Analysis of a Small-Scale Natural Gas Liquefaction Process Adopting Single Nitrogen Expansion with Carbon Dioxide Pre-Cooling. Appl. Therm. Eng. 64 (1-2), 139–146. doi:10.1016/j.applthermaleng.2013.12.011
Zhang, J., Meerman, H., Benders, R., and Faaij, A. (2020). Comprehensive Review of Current Natural Gas Liquefaction Processes on Technical and Economic Performance. Appl. Therm. Eng. 166, 114736. doi:10.1016/j.applthermaleng.2019.114736
Zhao, W.-h., Yang, J.-m., and Hu, Z.-q. (2012). Hydrodynamic Interaction Between FLNG Vessel and LNG Carrier in Side by Side Configuration. J. Hydrodyn. 24 (5), 648–657. doi:10.1016/s1001-6058(11)60288-6
Keywords: LNG, unconventional natural gas, coalbed methane, synthetic natural gas, LNG-FPSO, PLNG
Citation: Xu J, Lin W, Chen X and Zhang H (2022) Review of Unconventional Natural Gas Liquefaction Processes. Front. Energy Res. 10:915893. doi: 10.3389/fenrg.2022.915893
Received: 08 April 2022; Accepted: 19 May 2022;
Published: 05 August 2022.
Edited by:
Tianbiao He, China University of Petroleum (East China), ChinaReviewed by:
Zhen Tian, Shanghai Maritime University, ChinaCopyright © 2022 Xu, Lin, Chen and Zhang. This is an open-access article distributed under the terms of the Creative Commons Attribution License (CC BY). The use, distribution or reproduction in other forums is permitted, provided the original author(s) and the copyright owner(s) are credited and that the original publication in this journal is cited, in accordance with accepted academic practice. No use, distribution or reproduction is permitted which does not comply with these terms.
*Correspondence: Jingxuan Xu, eHVqaW5neHVhbkB1c3N0LmVkdS5jbg==
Disclaimer: All claims expressed in this article are solely those of the authors and do not necessarily represent those of their affiliated organizations, or those of the publisher, the editors and the reviewers. Any product that may be evaluated in this article or claim that may be made by its manufacturer is not guaranteed or endorsed by the publisher.
Research integrity at Frontiers
Learn more about the work of our research integrity team to safeguard the quality of each article we publish.