- 1School of Chemistry and Chemical Engineering, South China University of Technology, Guangzhou, China
- 2State Key Laboratory of Automotive Safety and Energy, Tsinghua University, Beijing, China
- 3State Key Laboratory of Fire Science, University of Science and Technology of China, Hefei, China
- 4Lee Kong Chian Faculty of Engineering and Science, UTAR, Kajang, Malaysia
Editorial on the Research Topic
Advanced Battery Thermal Management Systems
A massive number of lithium ion (Li-ion) batteries are used in electric vehicles and the number is still growing rapidly. Li-ion batteries are sensitive to temperature—they likely degrade in an over-cold or an over-hot environment. Battery thermal management systems (BTMSs) are designed to control the battery temperature within the optimal range between 20 and 55°C. Thermal management is one important part of battery management systems. A good BTMS allows researchers to improve the performance, extend the life, and enhance the safety of a battery. We launch this Research Topic to collect the latest technologies and design methodology on BTMSs.
Three papers have been published in this issue.
Yang et al. designed a semiconductor refrigeration system for a 48 V Li-ion battery pack which often operates at high discharge/charge rates, as shown in Figure 1A. A thermal model of the BTMS was also developed for this semiconductor-based BTMS. This BTMS is integrated with air cooling, limiting the maximum temperature to less than 40°C, as long as the temperature difference is less than 1.6°C. The semiconductor-based BTMS is effective when the battery temperature and discharge rate are high.
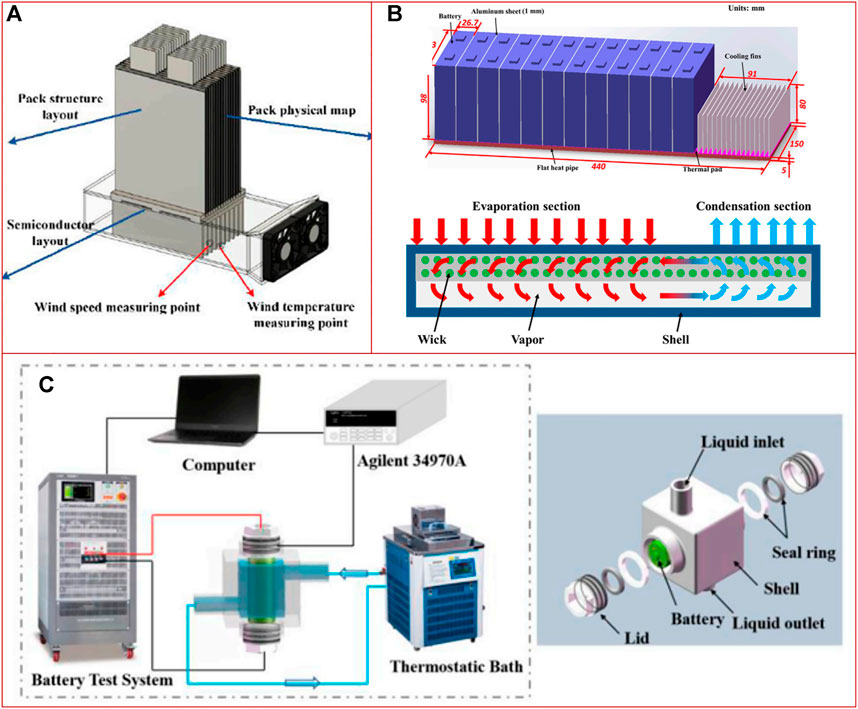
FIGURE 1. Illustrations of a BTMS structure. (A) A semiconductor and air cooling by Yang et al.; (B) A flat heat pipe and air cooling by Wang et al.; (C) Immersion water cooling by Luo et al.
Wang et al. applied a flat heat pipe (FHP) to a BTMS, utilizing the extremely high thermal dissipation ability of the FHP to remove the heat from the battery, as well as to improve the temperature homogeneity among battery cells. The BTMS structure is presented in Figure 1B. A thermal network model was also developed for this BTMS and the simulation agreed with the experiment data. The thickness, porosity, and particle diameter of a sintered wick on the thermal performance of the battery was investigated and the FHP was optimized. An FHP allows a radiator to be placed aside the battery pack as a condensation sector, making the battery pack compact.
Luo et al. designed a novel direct liquid cooling BTMS. With a unique structure shown in Figure 1C, the BTMS can be used for cylindrical battery cells with water as the thermal fluid, without worrying about the potential risks of the electric conductivities of water. A numerical model was developed and validated with the system. They investigated the effects of the coolant flowrate and suggested a high flowrate (>500 mL/min) is needed for the discharge at a rate above 3C of a 20-cell module. Multiple inlets were also suggested to improve the temperature uniformity.
These studies have shown new prototypes of battery cooling with semiconductors, heat pipes, and direct liquid cooling, which could provide alternatives for thermal management in commercial battery modules.
Author Contributions
All authors listed have made a substantial, direct, and intellectual contribution to the work and approved it for publication.
Conflict of Interest
The authors declare that the research was conducted in the absence of any commercial or financial relationships that could be construed as a potential conflict of interest.
Publisher’s Note
All claims expressed in this article are solely those of the authors and do not necessarily represent those of their affiliated organizations, or those of the publisher, the editors and the reviewers. Any product that may be evaluated in this article, or claim that may be made by its manufacturer, is not guaranteed or endorsed by the publisher.
Keywords: battery thermal management, semiconductor cooling, flat heat pipe, immersion cooling, summary
Citation: Ling Z, Feng X, Wang Q and Saw LH (2022) Editorial: Advanced Battery Thermal Management Systems. Front. Energy Res. 10:901083. doi: 10.3389/fenrg.2022.901083
Received: 21 March 2022; Accepted: 04 April 2022;
Published: 02 May 2022.
Edited and reviewed by:
Sheng S. Zhang, United States Army Research Laboratory, United StatesCopyright © 2022 Ling, Feng, Wang and Saw. This is an open-access article distributed under the terms of the Creative Commons Attribution License (CC BY). The use, distribution or reproduction in other forums is permitted, provided the original author(s) and the copyright owner(s) are credited and that the original publication in this journal is cited, in accordance with accepted academic practice. No use, distribution or reproduction is permitted which does not comply with these terms.
*Correspondence: Ziye Ling, enlsaW5nQHNjdXQuZWR1LmNu