- 1Laboratory of Environmental and Thermal Engineering, Department of Mechanical Engineering, Polytechnic School, University of Sao Paulo, Sao Paulo, Brazil
- 2Bioprocesses and Reactive Flow Group, Department of Processes and Energy, Faculty of Minas, National University of Colombia, Medellin, Colombia
- 3Industrial Process and Energy Systems Engineering, Department of Process Engineering, Federal Polytechnic School of Lausanne, Sion, Switzerland
This work evaluates the potential to produce synthetic nitrogen fertilizers by using sugarcane bagasse gasification in the São Paulo state, Brazil, aiming to increase the economic revenues and to decarbonize a chemical sector traditionally based on natural gas. The partial or total substitution of natural gas by consuming bagasse and enabling an intensive import of electricity from the Brazilian electricity mix is studied. The comparative assessment of the alternative production routes considers a reference case in which the residual bagasse is used only to generate surplus power at the cogeneration unit of the sugarcane mill, whereas ammonia is typically produced by consuming only natural gas. Unlike the conventional scenario, the proposed alternative routes employ surplus bagasse to produce ammonia. Regarding the unit exergy cost of ammonia, an increase between 50% and 100% is expected for the biomass-based routes (2.4498–3.1780 kJ/kJNH3) when compared to the conventional case (1.5866 kJ/kJNH3). In contrast, the net CO2 emissions balance of the alternative scenario achieve negative values (−2.5017 tCO2/tNH3), in comparison to the net CO2 positive emissions (1.75 tCO2/tNH3) of the conventional scenario. Additionally, the best location of the ammonia plant is nearby a sugarcane mill with a milling capacity of 10 Mt/y and 20 km far from another smaller sugarcane mill, in order to achieve an ammonia production potential of 1,200 tNH3/day. Concerning the economic analysis, if no carbon taxes are considered, the net present value (NPV) of the alternative scenarios drops up to 52%, compared to the conventional scenario. Finally, since 1.6 MtCO2/y can be avoided by using the residual bagasse as feedstock in the ammonia plant, the alternative scenarios become competitive vis-à-vis the conventional scenario in terms of NPV when carbon taxes of 40–50 USD/tCO2 are adopted. In the absence of carbon taxes, the drawback of the seasonality of the sugarcane crops (240 days of operation compared to 340 days for the conventional scenario) contributes to the decrease (39%–51%) of the NPV for the alternative scenarios.
Introduction
The fertilizer industry is crucial for sustaining the growing population (ABISOLO, 2017). Brazil is one of the largest importers of nitrogen-based fertilizers, with a share of 80% of its domestic demand (Manente and Marino, 2020). This dependency leaves the country more susceptible to the variation of the prices of the non-renewable energy resources, such as oil and gas, not to mention the issues related to logistical and transportation costs (Hernandez and Torero, 2011). Accordingly, some authors have worked out new paths and technologies aimed to produce ammonia in Brazil from different energy resources. Flórez-Orrego (2018) studied the production of ammonia via gasification of sugarcane bagasse residues and compared its performance with the conventional process based on steam reforming of natural gas. Both the electricity from the grid and the syngas produced from the gasification process have been considered as alternative input to provide the energy requirements of the alternative ammonia plant. Rivarolo et al. (2019) considered the ammonia production route based on a water electrolysis (200 t/day of NH3). The electrolyzer is fed by the electricity generated at the Itaupu hydropower plant and by the nitrogen produced in an air separation unit. The large amount of power consumed to produce ammonia at a small scale reportedly led to increased prices of ammonia, when compared to the use of residual bagasse. Esteves et al. (2015) also estimated the potential to produce ammonia in Ceará state, using renewable hydrogen produced from wind and solar technologies. A potential above 1,300 tNH3/km2/year for almost all the municipalities of Ceará state has been determined.
Biomass gasification has gained renewed attention as an approach to reduce the environmental impact of the chemical sector. According to Gilbert et al., 2014, the gasification of woody biomass may reduce by 65% the worldwide greenhouse gas emissions. In fact, depending on the use of the syngas produced, it could even offer negative rates of net CO2 emissions (Arora et al., 2017). More recent works performed by Arora et al. (2017) and Flórez-Orrego (2018) suggested the use of inexpensive biomass residues, such as sugarcane bagasse and straw, in order to enhance the financial attractiveness of unconventional ammonia production routes. Nakashima et al. (2019) also studied the advantages of integrating the anaerobic digestion to the gasification process in order to capitalize on the conversion of the vinasse and the residual bagasse from biorefineries. This work analyzed three production routes aiming to produce electricity, biomethane and hydrogen for the market. The highest exergy efficiency corresponded to the production of biomethane (48%) due to the fewer chemical processes units involved, whereas the highest revenues corresponded to the hydrogen exportation. Ribeiro Domingos et al. (2021) studied the alternative production of ammonia via black liquor gasification in a kraft pulp mill. Exergy efficiencies of up to 42% are reported for the integrated kraft pulp mill and ammonia production facilities. The negative CO2 emissions for the integrated scenario (−0.69 tCO2/tPulp) suggested the potential of biomass for decarbonizing bulk chemicals production. Frattini et al. (2016) studied three scenarios based on Haber-Bosch process to produce ammonia by means of 1) a biomass gasification system; 2) an electrolyzer and air separation unit powered via wind and solar farms; and 3) a steam reformer consuming biogas. The authors found that the overall energy consumption is similar for all the scenarios. However, the scenarios 1), 2), and 3) emit 3.82, 0.00, and 3.59 tCO2/tNH3, respectively, while the reference scenario based on natural gas steam reforming releases 2.05 tCO2/tNH3. Ajiwibowo et al. (2019) proposed the gasification of palm oil mill residues (empty fruit brunches) in an energy intensive supercritical water gasifier (SWG) in order to produce ammonia. The process employs syngas chemical looping to produce hydrogen, leading to a virtually emissions-free ammonia production route. Xu et al. (2021) proposed a system for simultaneous power and ammonia production, coupled to an Allam power cycle. Cotton stalk is used as biomass feedstock in the gasification process. Andersson and Lundgren (2014) studied the integration of a pulp mill to an ammonia production plant in order to upgrade the residues of the former facility. An increase of 10% in the energy efficiency has been calculated for the integrated operation, compared to the standalone pulp mill and ammonia plant. Consequently, the valorization of the biomass residues to produce value-added fuels and chemical has been recognized as an effort to mitigate the environmental impact of the chemical sector.
Meanwhile, in the Brazilian sugarcane mills, the residual bagasse is generally burnt in cogeneration units with low conversion efficiencies in order to supply the internal mill demands and to export surplus electricity to the grid. Some works aimed to increase the performance of those utility systems. Pellegrini (2009) assessed the extent of energy integration of the sugarcane mill and its cogeneration plant. The author reported a sharp reduction of the steam demand from 490 to 392 kgsteam/tsugarcane when energy integration is performed. Pina et al. (2017) evaluated the potential reduction in steam demand for an autonomous distillery (i.e., where only ethanol is produced) and an annexed plant (i.e., where both sugar and ethanol are produced). A reduction in 35% of steam consumption is reported when energy integration is adopted. Silva Ortiz et al. (2019) performed an exergy analysis on the production of first generation ethanol (1G ethanol) for similar scenarios in Pina et al. (2017). A higher overall exergy efficiency is reported for the annexed plant (41.39%), despite their highest capital expenditures. Burin et al. (2015) studied the integration of a concentrated solar panel (CSP) in the feedwater-heating scheme of the sugarcane cogeneration plant. An increase of 1.5% in the electricity output has been reported when compared to the reference scenario. On the other hand, the utilization of residual bagasse to produce value-added products and to partially or totally replace the use of fossil energy resources in the chemical and agricultural sectors may help not only reducing the inefficiency occurring in oversized cogeneration systems, but may also reveal business opportunities, envisaging more stringent carbon markets. However, since biomass residues are relatively dispersed, the choice of a strategic location for the waste-to-energy plant is essential to avoid excessive transportation costs. Hamelinck et al. (2005) recommended distances lower than 100 km, whereas Suurs (2002) correlated transportation costs and distance (50–200 km). Meanwhile, Selkimäki et al. (2010) calculated a limit for the radius of transportation (300 km) for Swedish and Finnish scenarios. Jäppinen et al. (2011) considered 50 km radius of transportation for woody biomass in Finland, as distances lower than 100 km for truck transportation could raise the transportation costs. The aforementioned works have the shortcoming of not reporting crop data from a specific geographic region (e.g., actual yearly sugarcane milling rate), and only few works deal with the collection of biomass into a specific location. Carbon taxation is also not considered in the previous works, which may shed light on the hidden advantages of the alternative scenarios over the conventional natural gas-based ammonia production route.
In view of 1) the benefit of upgrading bagasse to value-added products and 2) promoting negative carbon emissions, and bearing in mind 3) the inefficient conversion of bagasse in sugarcane mill cogeneration systems, as well as 4) the limitation for transporting biomass over long distances, a techno-economic analysis is necessary to elucidate the feasibility of using bagasse as an alternative input to produce fertilizers in Sao Paulo state. Although this state is the largest producer of sugarcane-derived products in Brazil, it mostly imports inexpensive natural gas from Bolivia to drive fertilizer production, thus entailing higher environmental burden to the chemical sector. In this regard, this work performs a comparative incremental assessment of six biomass-based ammonia production routes. The technical and economic analyses compare those routes to a conventional scenario in which ammonia is produced by steam methane reforming, whereas the residual bagasse is used to generate surplus electricity to the grid. Since different energy inputs (e.g., syngas, electricity and natural gas) can be used in the utility system of the ammonia production plant, the advantage of a transitional operation using alternative production routes is demonstrated. This approach reveals a more realistic energy transition path than that adopted in previous works, since fully renewable feedstock plants for ammonia production may not be considered either economically or technically viable in the short-to-mid-term. This analysis also differs from other approaches as it includes economic and environmental aspects of the transportation step, the ammonia production potential is assessed considering the restrictions on the sugarcane harvest period.
Materials and Methods
In this section, the cogeneration systems used either in the standalone or in the integrated sugarcane mill and ammonia plant are defined. Next, some assumptions related to the transportation processes of residual bagasse from the sugarcane mill to the location where the ammonia plant settles are stated. The characteristics of the alternative ammonia production plants, including the profile of the energy demands and the ammonia yield, are also discussed. Finally, the main parameters considered in economic analysis are discussed.
Standalone and Integrated Setups of Sugarcane Mill and Ammonia Plant
The standalone sugarcane mill shown in the right upper portion of Figure 1 refines sugarcane into sugar and hydrated ethanol, and produces bagasse as a byproduct. The bagasse is typically consumed in the cogeneration system in order to meet the internal energy demands of the mill, as well as to generate surplus electricity exported to the grid. The biogenic emissions derived from the fermentation process and bagasse combustion are usually not captured. Meanwhile, in the standalone ammonia production plant (Figure 1, right), a large amount of natural gas is consumed as feedstock and fuel in order to drive the reforming reactions and produce the utilities required by the chemical plant. In the conventional ammonia plant, a fraction of the fossil CO2 emissions is avoided thanks to the implementation of a syngas purification unit, whereas those derived from the combustion of natural gas are generally vented to the atmosphere.
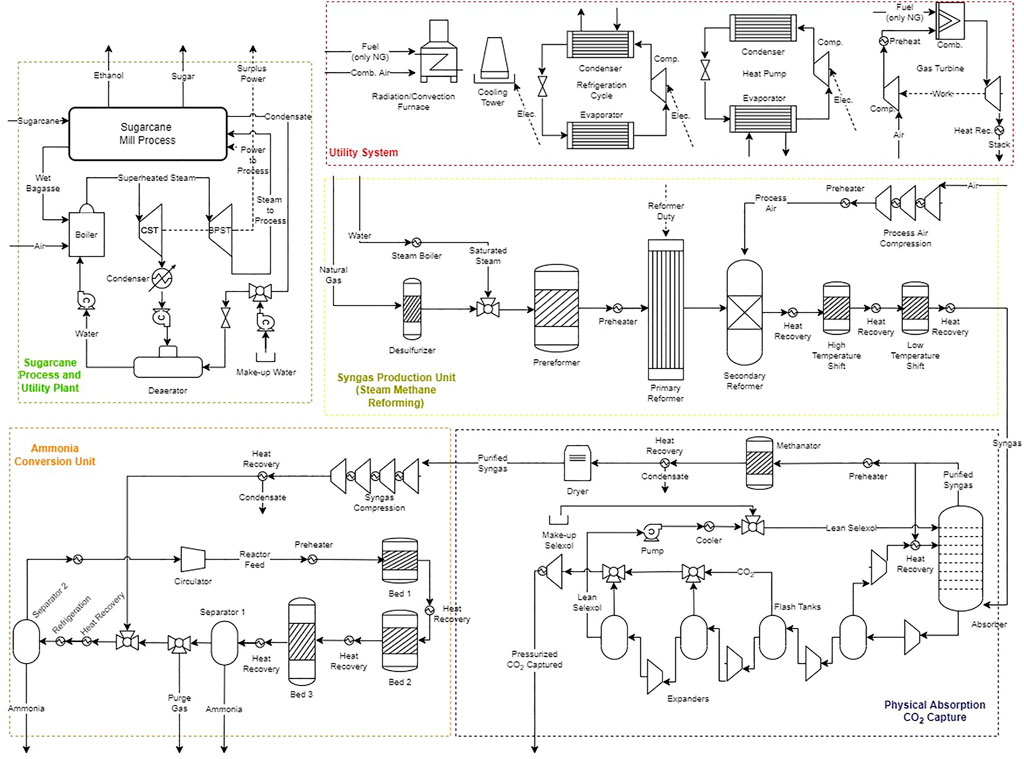
FIGURE 1. Flowsheet of the conventional scenario, considering a standalone sugarcane mill and a conventional ammonia plant. BPST, Backpressure steam turbine; CST, Condensing steam turbine.
Figure 2 shows the flowsheet of the integrated production route. Therein, the residual bagasse leaving the sugarcane mill is fed to the gasification unit of the ammonia plant. In this case, less bagasse is burnt in the cogeneration unit of the sugarcane mill, which entails less surplus electricity to the grid when compared to the conventional scenario described in Figure 1. Evidently, the integration of a bagasse gasification unit into an ammonia production plant affects the energy balance of the ammonia plant itself, as well as the sugarcane mill that provides the residual bagasse. Thus, the new utility systems must be suitably redesigned whenever a total or partial substitution of natural gas using biomass for decarbonization purposes is considered. In both Figures 1, 2, the size and use of the utility systems (e.g., furnaces, cooling tower, refrigeration system, heat pump, and gas turbine) have been previously optimized to achieve the minimum amount of energy consumption in the ammonia plant (Florez-Orrego, 2018).
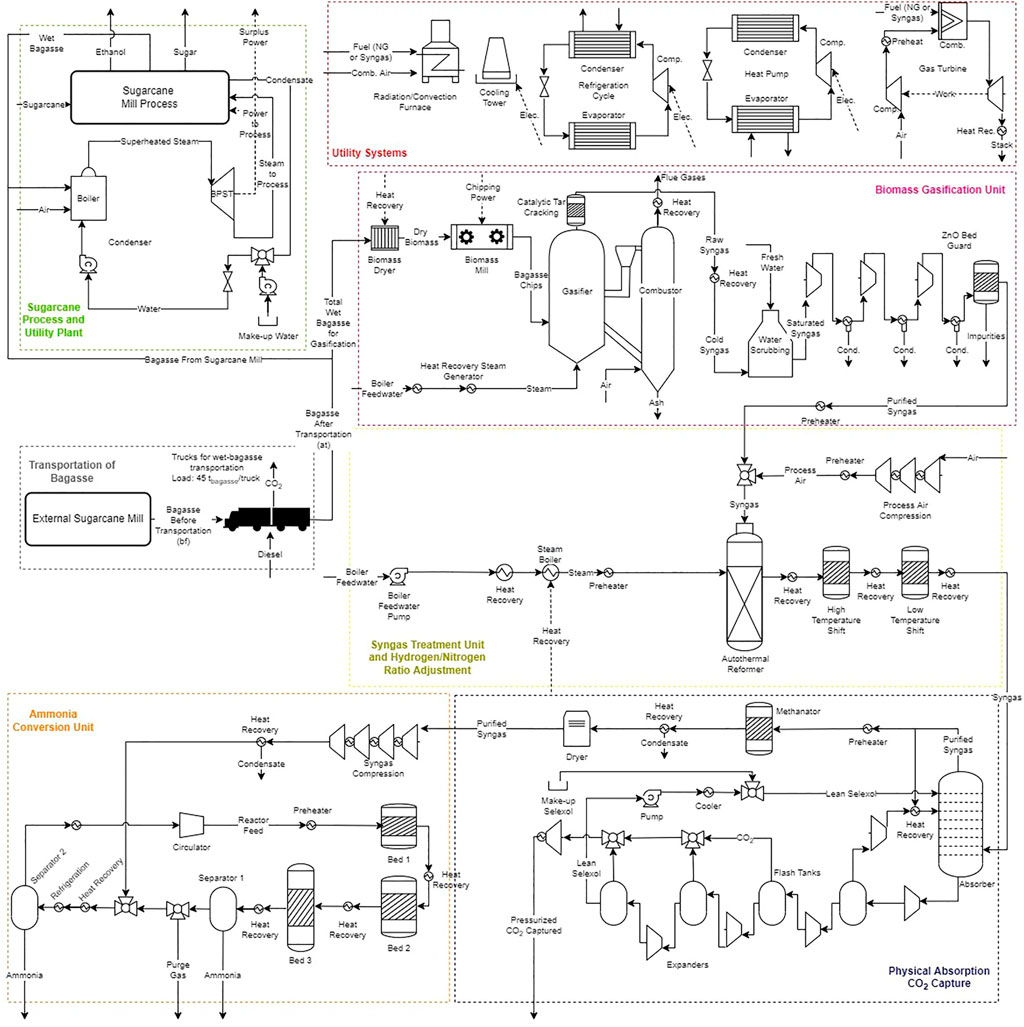
FIGURE 2. Flowsheet of the alternative scenarios considering an integrated sugarcane mill and an ammonia production plant. BPST, Backpressure steam turbine; CST, Condensing steam turbine.
Milling Rate and Geographical Localization of the Sugarcane Mills in São Paulo State.
Data about the milling rate and geographical localization of the main sugarcane mills across São Paulo state is used to determine the ammonia production potential and propose enhanced cogeneration units for the integrated facilities. In this work, data of the crop year 2018–2019 is considered according to RCGI & GBIO (2020), and the location and number of sugarcane mills is obtained from PROCANA (2016). Those figures are summarized in Supplementary Appendix A. Based on this data, the average sugarcane milling rate (ascmr) per city (i) is calculated, according to Eq. 1:
Meanwhile, the total wet bagasse (twb) available per city is estimated as the product of the ascmr and the ratio between the total bagasse production and the sugarcane milling rate in a typical mill (κ), assumed as 0.28 (Flórez-Orrego et al., 2015), Eq. 2.
Next, the average sugarcane milling rates are classified into ten groups according to the range of milling capacity. The twb is used as an input to SteamPro® suite of Thermoflow® software (Thermoflow Inc., 2020) in order to simulate the performance of the cogeneration unit of the sugarcane mills when they operate either in standalone or integrated mode.
Configurations and Operating Parameters of the Cogeneration Units in the Sugarcane Mills.
Aside from the total wet bagasse available (twb), other inputs required by the SteamPro® simulator are the features of the cogeneration system of the sugarcane mill, including the operating conditions (e.g., levels of steam pressure, superheated steam conditions, and energy demands) and the structure (i.e., backpressure and extraction-condensing steam turbine designs) of the steam network. As for the energy demands of the sugarcane mill, when enhanced thermal integration is considered, steam consumption achieves 392 kg per t of cane (tc). The power consumption of the mechanically-driven components (i.e., without electrification) reaches 30 kWh/t of processed cane (Pellegrini, 2009). A large amount of low pressure steam at 2.5 bar (∼196–250 t/h of steam for a 500 t/h sugar cane milling capacity) is also required in order to meet the heating demands of the sugarcane mill (Pellegrini, 2009). The properties of the superheated steam produced in the cogeneration system of a sugarcane mill may vary from 22 bar/300°C, up to supercritical water conditions. According to CALDEMA (2020), most of the boilers in operation in the sugarcane mills located in the Sao Paulo state operates at pressures varying between 42 and 67 bar, whereas the superheated steam temperatures range from 420 to 530°C. Yet, superheated steam conditions as high as 100 bar and 520°C have been reported as representative values of advanced cogeneration systems (Pellegrini, 2009). In this work, two cogeneration plant layouts are implemented, depending on the operative goals of the sugarcane mill. In the first setup, a backpressure steam turbine (BPST) operates in parallel with a condensing steam turbine (CST) in order to maximize the surplus electricity exported to the grid (Figure 3A). The internal energy demands of the sugarcane mill must be supplied (392 kgsteam/tc and 30 kWh/tc) and no residual bagasse is left for export. A bubbling fluidized bed biomass boiler (BFBBB) fueled with 50% wet sugarcane bagasse is used to generate superheated steam at 67 bar/480°C. Since no residual bagasse is exported, the standalone sugarcane mill is not integrated to the conventional ammonia plant (Figure 1). In the second setup (Figure 3B), the boiler consumes just the bagasse needed for attending the internal energy demands of the sugarcane mill, whereas the remainder (i.e. residual bagasse) is exported for ammonia production purposes (Figure 2). In this scenario, a backpressure steam turbine system is employed and the superheated steam properties after the BFBBB remain the same as in the previous scenario. Figures 3A,B summarizes the states of the streams involved in the two cogeneration systems. The main operating parameters calculated using SteamPro® are the residual sugarcane bagasse, the surplus electricity generation and the biogenic CO2 emissions from the BFBBB. It is worth noticing that the amount of residual wet bagasse is the difference between the total amount of wet bagasse (twb) and the amount of bagasse used to supply the power and heat demands of the sugarcane mill, which depends on the scale and efficiency of the cogeneration plant adopted and the milling capacity of the sugar cane mill.
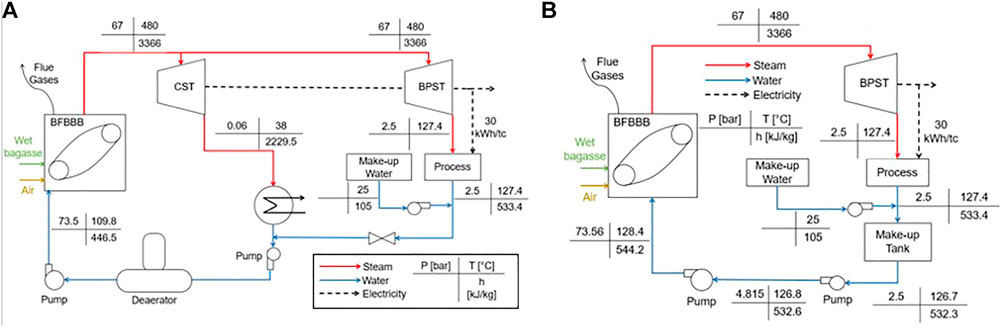
FIGURE 3. Sugarcane mill cogeneration systems based on: (A) a condensing steam turbine (CST) and a backpressure steam turbine (BPST) with superheated steam conditions at 67 bar/480°C, employed in the scenario with no residual bagasse; (B) backpressure steam turbine (BPST) with superheated steam conditions at 67 bar/480°C, employed in the scenario with residual bagasse sent to the ammonia plant.
Residual Bagasse Transportation
Since the residual bagasse coming only from one sugarcane mill is not enough to produce about 1,000 tNH3/day of ammonia in the alternative scenarios, an additional source of bagasse must be considered. The transportation of this additional residual bagasse entails an extra amount of fuel consumption by trucks, as well as increased CO2 emissions. Maximum transportation load of 45 t and gross weight load of 57 t per truck are adopted (Dantas Filho, 2009). Fuel consumption of 27 Ldiesel per 100 km for a heavy truck with gross combined weight load over 40 is based on data from Novo (2016). A maximum radius of biomass transportation of 20 km is assumed, according to current highway infrastructure in Sao Paulo state (Dantas Filho, 2009). The interactive tools of Google Maps aid determining the distance between two geographic coordinates according to the Haversine equation (Sanches, 2012).
Figure 4 shows the control volume considered for calculating the unit exergy cost of the transported bagasse; c stands for unit exergy cost, defined as the amount of exergy required to produce one unit of exergy of substance or energy flow (kJ/kJ). Subscript b refers to the state of bagasse before (bt) and after (at) the transportation stage, whereas B is the exergy flow rate of the residual bagasse transported or the diesel consumed (kW).
By applying a exergoeconomy cost balance to the transportation stage, and recognizing that the useful exergy of the transported biomass does not virtually change with the transportation service (i.e., Bb,at ≈ Bb,bt), all the terms at both sides of the cost balance can be divided by Bb,at, so that the unit exergy cost of the transported bagasse (cb,at) can be calculated according to Eq. 3:
where the ratio (Bdiesel/Bb,at) is defined as the specific exergy consumption (rc) (Flórez-Orrego et al., 2015). This latter magnitude can be calculated by considering data of the truck, namely the load, the specific fuel consumption (Spec_Cons), the number of necessary travels (Ntravel), the number of trucks per travel (NTruck), the chemical exergy of the diesel and bagasse transported (bich), and the distances from the i-th city to the ammonia power plant location, according to Eq. 4.
Based on the bagasse ultimate composition (46.7% C; 44.95% O; 6.02% H; 0.17% N and 0.02% S) and 50% moisture content (Flórez-Orrego, 2018), the chemical exergy of bagasse can be calculated using the correlations for estimating the lower heating value (LHV) (Parikh et al., 2005) and the ratio of the specific chemical exergy to the lower heating value (ϕ = bCH/LHV) (Szargut et al., 1988).
Ammonia Plant Setups
The standalone ammonia plant based on the conventional steam methane reforming process (Figure 1) has been thoroughly studied and more details can be found elsewhere (Flórez-Orrego and Oliveira, 2016; Flórez-Orrego et al., 2020). The current work rather focuses on the potential to partially or totally decarbonize the ammonia production by integrating a bagasse gasification unit, as it is shown in Figure 2. To this end, the bagasse is firstly dried up to about 10% wt. of moisture content and chipped, so that it can be fed to an indirectly heated, twin bed gasifier operating at atmospheric pressure. The raw syngas produced is water-scrubbed and compressed (30 bar), and goes through an autothermal reformer and two water gas shift reactors to adjust the hydrogen to nitrogen ratio (N2:H2:1:3), suitable for ammonia production. An additional purification process based on the physical absorption of the CO2 in the syngas by a solution of dimethyl ether polyethylene glycols (DEPGs) is used along with a methanator for removing the carbon oxide compounds that are poisonous for the ammonia synthesis catalyst. The CO2 captured is exported, whereas the purified syngas is further compressed up to 200 bar and enters the ammonia loop. Ammonia is produced via Haber-Bosch process, in which hydrogen and nitrogen in the syngas react in a series of catalytic reactor beds with intercooling until a nitrogen conversion of about 30% is attained (Flórez-Orrego and Oliveira, 2016). A purge gas stream is continuously withdrawn, so that the inert content in the loop is keep at adequate levels. Finally, the ammonia produced is condensed using cooling water and a vapor compression refrigeration system. The energy demands (i.e., heating, cooling and power requirements) of the alternative ammonia plant shown in Figure 2 could be supplied by a variety of utility systems, namely a refrigeration cycle, a cooling water system, syngas or natural gas furnaces, a gas turbine system, a Rankine cycle or even a combined cycle. It is worthy to notice that an appreciable amount of electricity from the grid can be also imported, instead of self-generating all the power in the utility system of the ammonia plant. In this way, the major difference between the conventional and the alternative ammonia production plants lies on the use of bagasse as the main source of syngas for ammonia synthesis and the opportunity to diversify the energy input to the utility systems. This approach allows for a substantial drop in the CO2 emissions and enables the partial or total substitution of the natural gas consumption, which has traditionally dominated the ammonia manufacturing sector.
Figures 5A–D schematize all the configurations of ammonia plant studied as a function of the energy input (e.g., natural gas, electricity, and bagasse) and the utility system adopted (i.e., either a Rankine or a combined cycle). The conventional scenario (Figure 5A), based on the steam methane reforming process, uses only natural gas as both fuel and feedstock and depends on a Rankine cycle to supply the utility demands to the chemical plant. Meanwhile, the electricity imported from the grid could be also used to balance the power generated by a Rankine cycle integrated to the ammonia plant (Figure 5B). In this case, bagasse is mainly consumed as feedstock in the gasification unit for syngas production. Other scenarios (Figure 5C) may admit bagasse as the only energy input. Thus, the syngas produced could be partly consumed as feedstock in an ammonia plant, as well as fuel either in a Rankine or a combined cycle. Lastly, the use of bagasse as feedstock and the consumption of natural gas either in a Rankine or a combined cycle represents the most likely pathway towards short-term decarbonization (Figure 5D). According to Figures 5A–D, although ammonia is regarded as the main product of the chemical plant, carbon dioxide can be also marketed for producing other chemicals (e.g., methanol, urea, food, polymers or even enhanced oil recovery). Meanwhile, the purge gas stream, rich in hydrogen, nitrogen and methane could be further processed, flared or consumed as fuel.
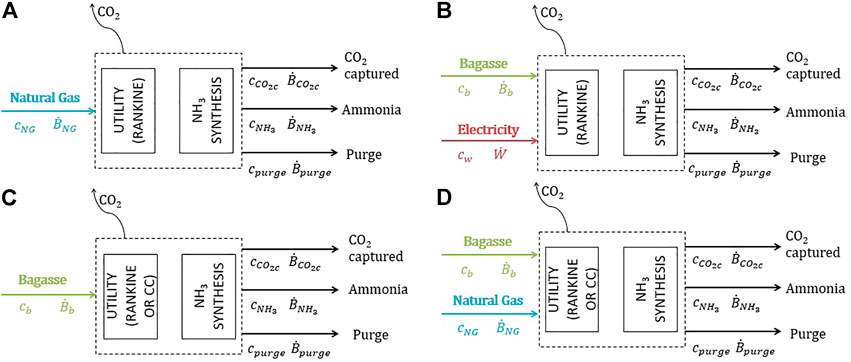
FIGURE 5. Different scenarios of ammonia chemical plants and their utility systems depending on the feedstock and fuel energy resources used: (A) natural gas only; (B) bagasse and electricity; (C) bagasse only; (D) bagasse and natural gas.
The average unit exergy costs of the products of the ammonia plant are calculated bearing in mind the equality partition criterion (Oliveira, 2013), which assigns the same unit exergy cost to the main product (ammonia) and by-products (marketable CO2 captured and purge gas), according to Eqs 5–8, Table 1.
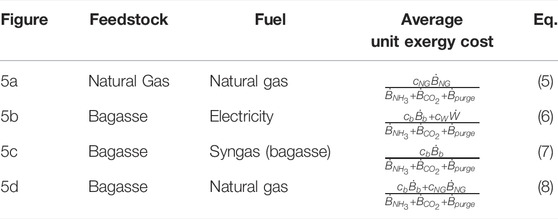
TABLE 1. Average unit exergy cost of the ammonia plant products for the different studied scenarios shown in Figure 5.
The rational exergy efficiency of the ammonia plant is calculated in terms of the exergy consumed, namely bagasse, electricity and/or natural gas, and the exergy of the ammonia plant products and by-products, as shown in Eq. 9.
Economic Analysis
In order to estimate the feasibility of installing an alternative ammonia production plant nearby the sugarcane mill, an incremental financial analysis over 20 years is performed. The net present value (NPV) is evaluated according to the main hypotheses shown in the Table 2. Moreover, it is assumed that in the first year of operation, the load factor of the ammonia plant is considerably lower than for the rest of the project lifetime.
The capital expenditure, operation and maintenance (O&M) and overall costs, as well as other economic considerations adopted are discussed next. Bartels (2008) and Appl (1999) reported the capital costs of an ammonia plant based on steam methane reforming as ranging between 72.79 and 81.53 USD per tNH3 for a 2,000 tNH3/day plant, and 85.58 USD/tNH3 for an 1,800 tNH3/day plant. Maung et al. (2012) considered the overall ammonia plant cost ranging between 400–600 USD/tNH3 when using both flared and conventional natural gas as feedstock. According to the authors, the O&M costs range between 30–40 USD per tNH3. As for the biomass-based ammonia plants, some studies evidenced that the biomass price strongly influence the economic viability of the project (Bartels, 2008; Arora et al., 2017; Flórez-Orrego, 2018). A typical value adopted for sugarcane bagasse in Brazil is 20 USD per tbagasse (Arora et al., 2017), which is an advantageous price compared to other biomass resources, such as australian eucalyptus (100 USD/t) and indian straw (30 USD/t). Arora et al. (2017) reported capital costs for small scale alternative ammonia plants (120 tNH3/day) varying from 127.66 to 237.09 USD per tNH3. Larger biomass-based ammonia production plants (194.67-736 tNH3/day) reportedly exhibit similar overall production costs (194.67–241.98 USD/tNH3), while Gilbert et al. (2014) reported an overall cost of about 500 USD/tNH3 when a woody biomass price of 60 USD/t and a production rate of 1,200 tNH3/day are considered. Thus, in this work, the capital cost (CAPEX) for a conventional ammonia plant is set as 160 USD/tNH3, whereas for the bagasse gasification scenarios, a CAPEX of 300 USD/tNH3 is adopted. The O&M cost of the conventional and alternative ammonia plants are assumed as 30 USD/tNH3 and 300 USD/tNH3, respectively. Meanwhile, the O&M cost for the cogeneration plant of the sugarcane mill is divided into fixed and variable costs, assumed as 123 USD/kW-year and 5 USD/MWh, respectively (NREL (National Renewable Energy Laboratory), 2020). The O&M cost adopted for the sugarcane mill are set as 0.34 USD/kgsugar (Cheng et al., 2019) and 0.257 USD/m³ethanol (or 1,377 BRL/m³) (Castro, 2020). Other relevant values considered in this analysis are the freight, assumed as 0.41 USD/km (or 2.19 BRL/km) according to the Resolution Nº 5.842 of the Brazilian National Agency of Terrestrial Transport (ANTT in Portuguese) (ANTT, 2019) and the state and federal taxes for producing sugar and ethanol, taken from CEPEA (2021). The specific capital (CAPEX) and operational (OPEX) expenditures are taken from literature (Bartels, 2008; Appl, 1999; Maung et al., 2012; Arora et al., 2017; Flórez-Orrego, 2018; Cheng et al., 2019; NREL (National Renewable Energy Laboratory), 2020).
Environmental Analysis of the Standalone and Integrated Sugarcane Mill and Ammonia Production Plant
An environmental analysis (CO2 emissions accounting) is performed based on the emissions of the cogeneration system of the sugarcane mill, the residual bagasse transportation and the emissions in the ammonia plant. The emissions are divided into two main groups, namely the direct (i.e., from combustion processes) and indirect (i.e., from supply chain) emissions. At the ammonia plant, the CO2 emissions avoided are also classified in biogenic and fossil emissions. The biogenic CO2 emissions avoided refer to the CO2 emissions captured in the syngas purification unit in the ammonia plant. Since those emissions can be considered circular due to the CO2 absorption during the plant growth and the release to the atmosphere during the plant decay or combustion, the biogenic CO2 emissions do not have a net contribution to the atmospheric emissions. However, since they can be captured and stored, a net negative emission may be found when the biogenic CO2 is sequestrated in the syngas purification process. On the other hand, since the fossil CO2 avoided derives from the combustion of natural gas, its capture and storage do not contribute to the depletion of the CO2 present in the atmosphere (Flórez-Orrego, 2018). Figure 6 summarizes the useful definitions required for the calculation of the CO2 emissions balance. The CO2 emitted from the cogeneration system of the sugarcane mill are calculated using the SteamPro® suite of Thermoflow® software (Thermoflow Inc., 2020). The ammonia plant direct and indirect emissions are estimated based on (Flórez-Orrego, 2018). Finally, the direct CO2 emissions from the trucks are estimated based on the methodology of Cancelli and Dias (2014), Eq. 10:
where E stands for the total emissions in kg; Fr,j is the number of vehicles from category j using the road during a certain period; Fe,j is the emission factor of the pollutant in g/km and L is the total length travelled by the truck. The emission factors are obtained from default tables according to the vehicle category, the fuel consumed, the year of production and the type of pollutant emitted (CETESB, 2018).
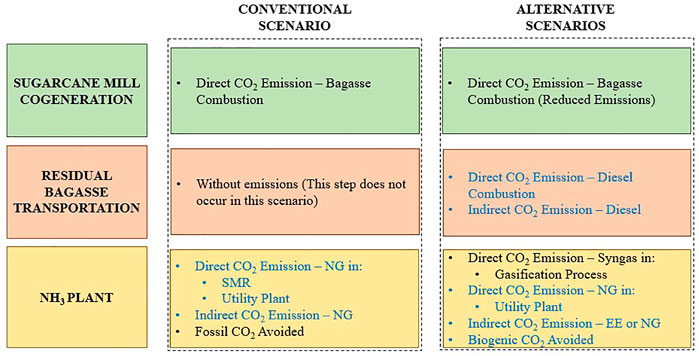
FIGURE 6. Summary of the CO2 emissions evaluated for the different control volumes presented in Figures 1, 2. The blue font color spotlights the emissions considered in the net CO2 emissions balance.
Meanwhile, the renewability performance indicator (λ) aims to evaluate if a process is environmentally favorable, Eq. 11, i.e., if the exergy of the products can offset the sum of the exergy consumed from fossil resources, the exergy destroyed in the production process, the consumption of exergy for waste deactivation, as well as the exergy of the emissions (Velasquez et al., 2009).
If this indicator is lower than one, the process is environmentally unfavorable. If it is equal to one, it is internally and externally reversible. As λ becomes larger than one, the process is environmentally favorable. For a hypothetic reversible process with only renewable inputs and no wastes, λ →∞.
Results and Discussions
Based on the data of sugarcane milling rate and residual bagasse availability, the performance of the cogeneration unit of different sugarcane mills is evaluated at various scales using SteamPro®. As a result, the cogeneration plants based only on BPST systems, aiming to generate just the internal energy demands with minimum electricity surplus, present exergy efficiencies up to 2.2 percentage points higher than those of the setups aimed to maximize the surplus electricity (i.e., the BPST + CST system). This result can be explained by the fact that the residual bagasse is upgraded to syngas in the alternative ammonia production plants, instead of being directly burned. In this way, the percentage of residual bagasse available for gasification is about 12% of the total sugarcane milling rate when no surplus electricity is generated. This value is almost double than that reported in Flórez-Orrego et al. (2015), where only 5.3% of the sugarcane milling rate was available as residual bagasse. The reason is that in that work, less efficient cogeneration systems were integrated, as superheated steam conditions only achieved 22 bar and 300°C. Thus, enhancing the superheated steam conditions to 67 bar and 480°C seemingly has a significant impact on the residual bagasse availability and, thus, the ammonia production potential. It is worthy to notice that, even if all the residual bagasse is exported, a small surplus electricity is incidentally generated (36.9 kWh/tc). Yet, this value is much lower than the maximum power generated when no bagasse is sent to gasification (102.8 kWh/tc). Also, since there are no modifications in the processing units of the sugarcane mill, the sugar and ethanol yields remain 2,446 tsugar/day and 1,550 m³/day, respectively, for all scenarios. Concerning the bagasse availability, an increase of the radius of biomass transportation also increases the number of sugarcane bagasse suppliers. Thus, for the alternative ammonia production scenarios, it is considered that the ammonia plant is located in the city of Pradópolis, in Sao Paulo state. Therein is also located the world’s largest sugarcane mill (São Martinho, 2020). Considering a maximum radius of 20 km from this city, there is an additional sugarcane mill that may help providing the amount of biomass required to produce up to 1,235 tNH3/day. The bagasse transportation from this second sugarcane mill to the alternative ammonia plant entails an increase of only 0.03% in the unit exergy cost of the bagasse. Figure 7 illustrates the impact of the radius of transportation on the ammonia production potential and on the unit exergy cost of the transported bagasse. As a result, for a radius of 100 km, the unit exergy cost of bagasse after transportation only increases 1%. However, when radiuses above 100 km are considered, increments of unit exergy cost above 5% can be obtained. Bearing in mind that typical ammonia production plants have a nominal capacity of 1,000 tNH3/day, the selected radius (20 km) is used as a rational choice for these analyses.
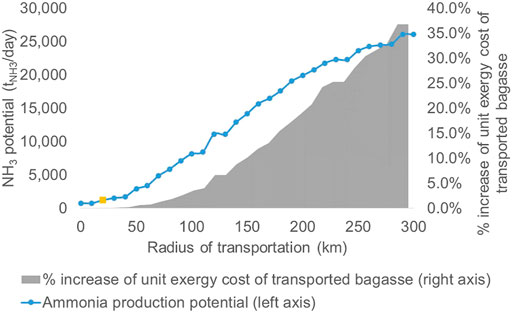
FIGURE 7. Variation of the ammonia production potential and the unit exergy cost of the transported bagasse as a function of the radius of transportation. Ammonia plant is located in Pradópolis city. The yellow squared point refers to the radius of transportation adopted in this work (20 km).
Based on the exergy costs calculated for the transported bagasse, the unit exergy costs of the main product and byproducts of the ammonia plant are determined. These values, along with other performance indicators, such as the rational exergy efficiency, the ammonia production rate and the CO2 captured are reported in Figure 8. It is worth recalling that those values depend on the different integration alternatives adopted between the ammonia plant and its utility systems, as well as on the energy inputs considered for each scenario in Figure 5.
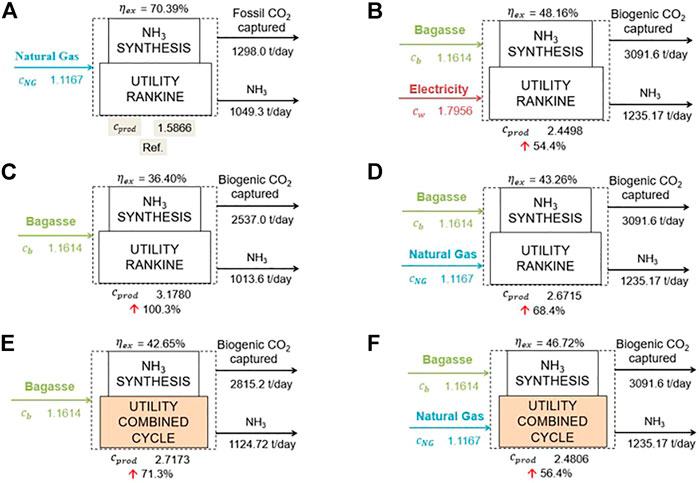
FIGURE 8. Unit exergy costs of the ammonia plant products and its percentage increment compared to the conventional scenario, (A). Other variables such as the amount of ammonia produced and the CO2 captured are reported for the alternative ammonia production (B–F).
According to Figure 8, the highest unit exergy cost of the ammonia plant products corresponds to the scenario in which only bagasse is used as both feedstock and fuel (i.e., gasification-derived syngas is used in the utility systems). Moreover, the use of a utility system based on a Rankine cycle instead of a combined cycle leads to an increment of the average unit exergy cost of the products of the alternative ammonia production plant (7.7% when comparing Figures 8D–F, and 16.9% when comparing Figures 8C–E). On the other hand, the lowest average unit exergy cost of the products of the alternative ammonia plant is found for the scenario shown in Figure 8B. In that case, the electricity import is increased to reduce the import of utility fuel. Thus, the use of electricity produced in the highly renewable Brazilian electricity mix leads to a reduction of the overall energy consumption in the ammonia plant. Despite this relative thermodynamic and environmental advantage, the average unit exergy cost of the products of the ammonia plant for the scenario shown in Figure 8B is still 54% higher than that obtained when the ammonia plant operates under the conventional scenario. These results are in agreement with the exergy efficiency indicator, which is up to 34% higher for the conventional scenario, if compared to the alternative scenarios. This difference occurs due to the increased exergy consumption in the biomass-based routes, compared to more mature and efficient conversion processes in the conventional ammonia plant. Actually, the alternative production routes based on bagasse gasification comprise energy-intensive bagasse drying and more stringent syngas compression and purification processes. Yet, regarding the amount of CO2 captured, the alternative ammonia production routes sequestrate two times more CO2 compared to the conventional scenario. This fact reveals opportunities of net negative CO2 emissions for the biomass-based ammonia production routes, which becomes relevant in scenarios involving with carbon taxes.
Regarding the financial analysis, the main parameter evaluated is the net present value (NPV) of the conventional and integrated setups. The values reported in Figure 9 do not consider any carbon taxes yet. Notably, the conventional scenario exhibits the highest NPV due to the highest number of days of ammonia production using natural gas (340 days), compared to the 200 days adopted for the sugarcane harvesting season. Accordingly, the seasonality of biomass growth hampers the NPV of the alternative ammonia production routes, which is 39%–53% lower than in the conventional case. Higher CAPEX and OPEX associated to the alternative production routes further impair their economic performance. This circumstance presents technical and financial challenges for the bagasse-based ammonia plants if they aim to become competitive vis-à-vis the conventional production route.
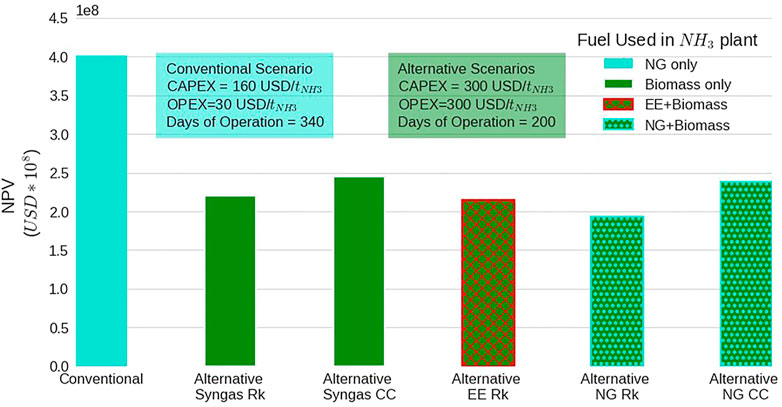
FIGURE 9. Net present value (NPV) for the conventional and integrated ammonia production scenarios without considering carbon taxes. Rk, Rankine cycle; CC, combined cycle; NG, natural gas; EE, electricity. “Syngas” represents the production routes that only consume bagasse and produce their own utilities consuming a fraction of the syngas produced.
Meanwhile, due to growing awareness of the impact of the fertilizers production in the environment, these apparent disadvantages must be weighed against the benefits of the alternative production routes to mitigate the CO2 emissions. Moreover, there could be an opportunity of earning additional revenues in new markets with more stringent environmental regulations. For this reason, an additional analysis is carried out in order to compare the financial performance of all the production routes considering a future scenario of carbon taxation. In the case of the alternative ammonia production routes, the carbon tax is favorable, since there is an overall negative carbon emission rate due to the biogenic CO2 carbon capture process in the syngas purification unit (Figure 10). On the other hand, due to the net positive fossil CO2 emissions from the natural gas combustion, the NPV of the conventional scenario drops as the carbon tax increases. Figure 11 presents the incremental NPV calculated as the difference between the NPV of the alternative configurations and the conventional setup. Unlike Figure 10, the Figure 11 shows the carbon tax at which the integrated production plants become equal or more economically attractive than the conventional scenario. Notably, the integrated production routes become more favorable when the carbon tax increases above 45 USD/tCO2, especially when the utility system of the ammonia plant is based on the combined cycle technology. Moreover, when a substantial import of electricity to the ammonia production plant is enabled, higher carbon taxes (>55 USD/tCO2) would be necessary to compensate for a higher price of the electricity consumed. In fact, the solution based on intensive electricity import results less favorable than those based on combined cycles, unless the carbon tax is increased above 120 USD/tCO2. Hence, as long as lower electricity prices may be accomplished, the integrated production route reliant on electricity would be even more favorable than the one consuming natural gas or syngas as fuel. This parametric analysis demonstrates the interdependence between the financial and thermodynamic parameters of the integrated production routes.
The renewability indexes for the different scenarios are summarized in Table 3. As it can be seen, the highest renewability index corresponds to the alternative scenario consuming electricity from the Brazilian electricity grid and using a Rankine cycle. This value is 62.2% higher than the renewability index of the conventional scenario. Actually, as it goes from a control volume encompassing only the ammonia plant to a control volume including all the production route, the renewability index increases for all the studied scenarios except for the conventional one. It indicates a deterioration in the exergy and environmental performance of the standalone sugarcane and ammonia production plant when the supply chain of the resources is considered. On the other hand, the integration of the sugarcane mill and the ammonia production routes may help offsetting the disadvantages of the lower conversion efficiencies in the alternative routes and the increased emissions due to bagasse transportation.
Regarding the balance of CO2 emissions, the direct, indirect emissions, as well as the biogenic CO2 avoided, are shown in Table 4. The conventional scenario is the only with positive CO2 emissions, due to intensive natural gas consumption. On the other hand, the alternative scenarios based on biomass gasification exhibit a drastic drop on the net CO2 emissions, thanks to the use of syngas derived from residual sugarcane bagasse. However, these scenarios still present some indirect fossil CO2 emissions, due to the bagasse transportation from sugarcane mills to the ammonia plant. Anyhow, the direct and indirect CO2 emissions derived from the diesel consumption are not as representative as those derived from the energy conversion processes in the chemical plant and the supply chains of other energy resources (e.g., natural gas and electricity, see Table 4). The use of electricity as an energy resource may also cut down the CO2 emissions in the alternative ammonia production routes (Flórez-Orrego, 2018), however it will depend on how electricity is generated. In this way, an upgraded gasification of bagasse in the ammonia plant may help dropping the CO2 emissions by 1.6 MtCO2/year, compared to the case when bagasse is entirely burnt to generate surplus electricity to the grid.
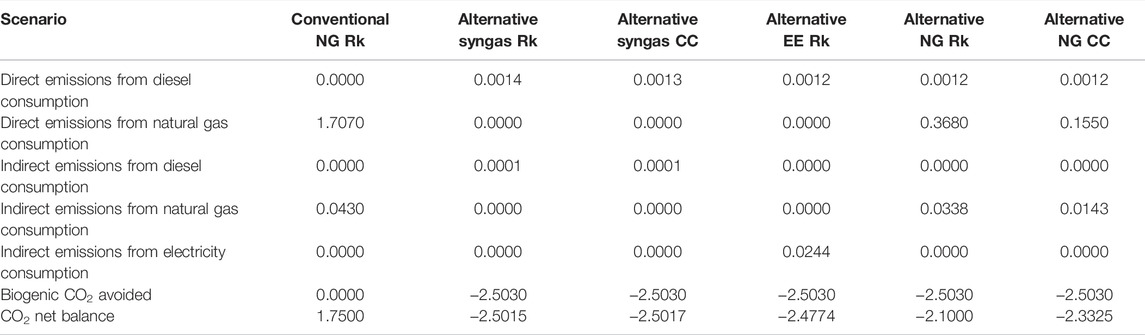
TABLE 4. Direct and indirect emissions for diesel, natural gas (NG) and Electricity (EE). The net CO2 emissions balance of the scenarios studied is also reported (tCO2/tNH3).
Conclusion
In this work, the potential to produce ammonia from inexpensive biomass residues, namely, residual bagasse from sugar cane mills, is compared to the conventional case (i.e., standalone sugar and ethanol mill and ammonia plant). This comparison is performed in terms of: 1) the average unit exergy costs of the marketable products, 2) financial performance indicators, 3) the net CO2 emission balance and 4) the renewability index. The average unit exergy cost of the ammonia plant products (i.e., ammonia, CO2 and purge gas) and the associated CO2 emissions are reduced if electricity is imported from the greener Brazilian electricity mix. The financial analysis showed that using syngas derived from bagasse gasification as fuel in the utility systems (e.g., combined cycle) of the ammonia plant may help reducing the dependency on fossil resources. Indeed, a net balance of CO2 emissions demonstrated that the alternative ammonia production routes promote the depletion of CO2 in the atmosphere, unlike the conventional scenario of ammonia production, based on natural gas. Additionally, the renewability index is higher for all alternative ammonia production scenarios compared to the conventional case. The alternative scenario relying on substantial electricity import proved to be the most renewable one. The challenge of the alternative production routes remains the improvement of the financial indicators, such as the NPV, to levels comparable to those of conventional scenario. The energy intensive bagasse pre-treatment and syngas conditioning processes, along with the seasonality of the sugarcane mill operation and the technological gaps of the biomass gasification systems are key factors to enhance the thermodynamic and the economic performances of the integrated sugarcane mill and ammonia plant. An approach that could be further evaluated is the possibility of using different biomass resources or biogas to tackle the seasonality issue. Anyhow, these breakthrough approaches for producing nitrogen fertilizers constitute important pathways to cut down greenhouse gas emissions and to promote the sustainable use of energy. Biomass gasification is a promising energy conversion route, especially for tropical countries, which have a largely underexploited biomass potential.
Data Availability Statement
The datasets presented in this study can be found in online repositories. The names of the repository/repositories and accession number(s) can be found in the article/Supplementary Material.
Author Contributions
RT was responsible for research conceptualization, data obtainment and organization, results discussion, and draft manuscript preparation. DF-O and SO were responsible for research conceptualization, results discussion, and revision of the manuscript.
Funding
Fundação de Apoio à Universidade de São Paulo (FUSP) and Virtual University of the Sao Paulo State (UNIVESP)—RT MSc grant. Colombian Administrative Department of Science, Technology and Innovation—Minciencias (COLCIENCIAS Grant 1.128.416.066-646/2014)—DF-O grant. Brazilian National Council for Scientific and Technological Development (CNPq), grant 306484/2020-0—SO grant.
Conflict of Interest
The authors declare that the research was conducted in the absence of any commercial or financial relationships that could be construed as a potential conflict of interest.
Publisher’s Note
All claims expressed in this article are solely those of the authors and do not necessarily represent those of their affiliated organizations, or those of the publisher, the editors and the reviewers. Any product that may be evaluated in this article, or claim that may be made by its manufacturer, is not guaranteed or endorsed by the publisher.
Acknowledgments
The first author would like to thank Fundação de Apoio à Universidade de São Paulo (FUSP) and Virtual University of the Sao Paulo State (UNIVESP) for his MSc grant. The second author would like to thank the Colombian Administrative Department of Science, Technology and Innovation—Minciencias (COLCIENCIAS Grant 1.128.416.066-646/2014). The last author thanks the Brazilian National Council for Scientific and Technological Development (CNPq), grant 306484/2020-0.
Supplementary Material
The Supplementary Material for this article can be found online at: https://www.frontiersin.org/articles/10.3389/fenrg.2022.881263/full#supplementary-material
References
ABISOLO (2017). Brazilian Yearbook of Technology in Plant Nutrition. Sao Paulo. Available at: https://abisolo.com.br/anuario-edicoes-anteriores/ (accessed 09 24, 2019).
Ajiwibowo, M. W., Darmawan, A., and Aziz, M. (2019). Towards Clean Palm Oil Processing: Integrated Ammonia Production from Empty Fruit Bunch and Palm Oil Effluent. J. Clean. Prod. 236, 117680. doi:10.1016/j.jclepro.2019.117680
Andersson, J., and Lundgren, J. (2014). Techno-Economic Analysis of Ammonia Production via Integrated Biomass Gasification. Appl. Energy 130, 484–490. doi:10.1016/j.apenergy.2014.02.029
ANTT (2019). Resolution Nº 5.842. Available at: https://anttlegis.datalegis.inf.br/action/UrlPublicasAction.php?acao=abrirAtoPublico&sgl_tipo=RES&num_ato=00005842&seq_ato=000&vlr_ano=2019&sgl_orgao=DG/ANTT/MI (accessed 01 05, 2021).
Arora, P., Hoadley, A. F. A., Mahajani, S. M., and Ganesh, A. (2017). Multi-Objective Optimization of Biomass Based Ammonia Production - Potential and Perspective in Different Countries. J. Clean. Prod. 148, 363–374. doi:10.1016/j.jclepro.2017.01.148
Bartels, J. R. (2008). A Feasibility Study of Implementing an Ammonia Economy. [dissertation]. Iowa, USA: Iowa State University.
Burin, E. K., Buranello, L., Giudice, P. L., Vogel, T., Görner, K., and Bazzo, E. (2015). Boosting Power Output of a Sugarcane Bagasse Cogeneration Plant Using Parabolic Trough Collectors in a Feedwater Heating Scheme. Appl. Energy 154, 232–241. doi:10.1016/j.apenergy.2015.04.100
CALDEMA (2020). Caldema Supply List. Available at: https://www.caldema.com.br/fornecimentos (accessed 05 14, 20).
Cancelli, D. M., and Dias, N. L. (2014). BRevê: An Objective Approach to Calculate Emission Rates for the Brazilian Vehicle Fleet Characteristics. Eng. Sanit. Ambient. 19, 13–20. doi:10.1590/s1413-41522014019010000284
Castro, N. M. D. (2020). Hydrated Ethanol is Traded at below Production Cost. Available at: https://www.novacana.com/n/etanol/mercado/precos/etanol-hidratado-negociado-valores-abaixo-custo-producao-230420#:∼:text=O%20custo%20de%20produ%C3%A7%C3%A3o%20de,em%20R%24%201.377%2Fm%C2%B3.&text=De%20acordo%20com%20o%20presidente,de%20quase%20R%24%209%20bilh%C3%B5es (accessed 01 06, 2021).
CEPEA (2021). Agricultural Prices. Available at: https://cepea.esalq.usp.br/en (accessed 01 05, 2021).
CETESB (2018). Emission Factors 2018. Available at: https://cetesb.sp.gov.br/page/2/?s=fator+de+emiss%C3%A3o (accessed 03 16, 2021).
Cheng, M. H., Huang, H., Dien, B. S., and Singh, V. (2019). The Costs of Sugar Production from Different Feedstocks and Processing Technologies. Biofuels, Bioprod. Bioref. 13 (3), 723–739. doi:10.1002/bbb.1976
Dantas Filho, P. L. (2009). Cost Analysis in Power Generation with Sugar Cane Bagasse: A Case Study in Four Mills in São Paulo. [MSc dissertation]. Sao Paulo, Brazil: University of Sao Paulo.
EPE (2019). Technical Report - Natural Gas Competitiveness: Case Study in the Nitrogen Fertilizer Industry. Brasilia, Brazil: Empresa de Pesquisa Energética (EPE). Technical Report No.: EPE-DEA-IT-001/2019.
Esteves, N. B., Sigal, A., Leiva, E. P. M., Rodríguez, C. R., Cavalcante, F. S. A., and de Lima, L. C. (2015). Wind and Solar Hydrogen for the Potential Production of Ammonia in the State of Ceará - Brazil. Int. J. Hydrog. Energy 40 (32), 9917–9923. ISSN 0360-3199. doi:10.1016/j.ijhydene.2015.06.044
Flórez-Orrego, D., Sharma, S., Oliveira, S., and Marechal, F. (2020). Combined Exergy Analysis, Energy Integration and Optimization of Syngas and Ammonia Production Plants: A Cogeneration and Syngas Purification Perspective. J. Clean. Prod. 244, 118647. doi:10.1016/j.jclepro.2019.118647
Flórez-Orrego, D. A. (2018). Process Synthesis and Optimization of Syngas and Ammonia Production in Nitrogen Fertilizers Complexes: Exergy, Energy Integration and CO2 Emissions Assessments. [DSc thesis]. Sao Paulo, Brazil: University of Sao Paulo.
Flórez-Orrego, D., da Silva, J. A. M., Velásquez, H., and de Oliveira, S. (2015). Renewable and Non-Renewable Exergy Costs and CO2 Emissions in the Production of Fuels for Brazilian Transportation Sector. Energy 88, 18–36. doi:10.1016/j.energy.2015.05.031
Flórez-Orrego, D., and Oliveira, S. (2016). On the Efficiency, Exergy Costs and CO2 Emission Cost Allocation for an Integrated Syngas and Ammonia Production Plant. Energy 117 (Part 2), 341–360. doi:10.1016/j.energy.2016.05.096
Frattini, D., Cinti, G., Bidini, G., Desideri, U., Cioffi, R., and Jannelli, E. (2016). A System Approach in Energy Evaluation of Different Renewable Energies Sources Integration in Ammonia Production Plants. Renew. Energy 99, 472–482. doi:10.1016/j.renene.2016.07.040
Gilbert, P., Alexander, S., Thornley, P., and Brammer, J. (2014). Assessing Economically Viable Carbon Reductions for the Production of Ammonia from Biomass Gasification. J. Clean. Prod. 64, 581–589. doi:10.1016/j.jclepro.2013.09.011
Hamelinck, C. N., Suurs, R. A. A., and Faaij, A. P. C. (2005). International Bioenergy Transport Costs and Energy Balance. Biomass Bioenergy 29 (2), 114–134. doi:10.1016/j.biombioe.2005.04.002
Hernandez, M., and Torero, M. (2011). Fertilizer Market Situation: Market Structure, Consumption and Trade Patterns, and Pricing Behavior. Washington, DC: International Food Policy Research Institute. Discussion Paper 01058.
Jäppinen, E., Korpinen, O.-J., and Ranta, T. (2011). Effects of Local Biomass Availability and Road Network Properties on the Greenhouse Gas Emissions of Biomass Supply Chain. ISRN Renew. Energy 2011, 1–6. doi:10.5402/2011/189734
Manente, A., and Marino, C. (2020). The Gas Bill and the Restoration of Competitiveness in Brazilian Industry. Available at: https://abiquim.org.br/comunicacao/noticia/9080 (Accessed 03 23, 2021).
Maung, T., Ripplinger, D., McKee, G., and Saxowsky, D. (2012). Economics of Using Flared vs. Conventional Natural Gas to Produce Nitrogen Fertilizer: A Feasibility Analysis. Agribusiness and Applied Economics Report 133410. Fargo, North Dakota: North Dakota State University, Department of Agribusiness and Applied Economics.
Nakashima, R., Flórez-Orrego, D., and Oliveira, S. (2019). Integrated Anaerobic Digestion and Gasification Processes for Upgrade of Ethanol Biorefinery Residues. J. Power Technol. 99 (2), 104–114.
Novo, A. L. A. (2016). Perspectives for Fuel Consumption in Freight Transport in Brazil - A Comparison between the Structure and Intensity Effects on the Sector's Final Energy Use. [MSc dissertation]. Rio de Janeiro, Brazil: Federal University of Rio de Janeiro.
NREL (National Renewable Energy Laboratory) (2020). 2020 Annual Technology Baseline. Colarado, USA: National Renewable Energy Laboratory.
Paixão, V. P. (2018). Retro-Techno-Economic Analysis of an Ammonia Production Plant Based on Urban Solid Waste Gasification. [MSc dissertation]. Rio de Janeiro, Brazil: Federal University of Rio de Janeiro.
Parikh, J., Channiwala, S., and Ghosal, G. (2005). A Correlation for Calculating HHV from Proximate Analysis of Solid Fuels. Fuel 84 (5), 487–494. doi:10.1016/j.fuel.2004.10.010
Pellegrini, L. F. (2009). Thermo-Economic-Environmental Analysis and Optimization Applied to the Combined Production of Sugar, Alcohol and Electricity. [DSc thesis]. Sao Paulo, Brazil: University of Sao Paulo.
Pina, E. A., Palacios-Bereche, R., Chavez-Rodriguez, M. F., Ensinas, A. V., Modesto, M., and Nebra, S. A. (2017). Reduction of Process Steam Demand and Water-Usage through Heat Integration in Sugar and Ethanol Production from Sugarcane - Evaluation of Different Plant Configurations. Energy 138 (1), 1263–1280. doi:10.1016/j.energy.2015.06.054
RCGI & GBIO (2020). Biogas, Biomethane and Electric Power in São Paulo. Available at: https://www.arcgis.com/apps/View/index.html?appid=280ffdedd6e74724903ff161803a1462&extent=-53.9090,-25.0137,-43.3621,-20.1000 (accessed 01 24, 2020).
Ribeiro Domingos, M. E. G., Flórez-Orrego, D., Teles Dos Santos, M., and Oliveira, S. (2021). Exergy and Environmental Analysis of Black Liquor Upgrading Gasification in an Integrated Kraft Pulp and Ammonia Production Plant. Int. J. Exergy 35 (1), 35–64. doi:10.1504/ijex.2021.10032908
Rivarolo, M., Riveros-Godoy, G., Magistri, L., and Massardo, A. F. (2019). Clean Hydrogen and Ammonia Synthesis in Paraguay from the Itaipu 14 GW Hydroelectric Plant. ChemEngineering 3, 87. doi:10.3390/chemengineering3040087
Sanches, R. M. (2012). Development of a Trajectory Planning System for Autonomous Agricultural Vehicles. [MSc dissertation]. Sao Carlos, Brazil: University of Sao Paulo.
São Martinho (2020). Businesses and Units. Available at: https://www.saomartinho.com.br/show.aspx?idMateria=rk2CGXH5SOIFTobanx1b+g== (Accessed 07 06, 2020).
Selkimäki, M., Mola-Yudego, B., Röser, D., Prinz, R., and Sikanen, L. (2010). Present and Future Trends in Pellet Markets, Raw Materials, and Supply Logistics in Sweden and Finland. Renew. Sust. Energ. Rev. 14 (9), 3068–75. doi:10.1016/j.rser.2010.06.009
Silva Ortiz, P., Flórez-Orrego, D., Oliveira Junior, S., Maréchal, F., and Maciel Filho, R. (2019). Exergetic, Environmental and Economic Assessment of Sugarcane First-Generation Biorefineries. J. Power Technol. 99 (2), 67–81.
Suurs, R. (2002). Long Distance Bioenergy Logistics - An Assessment of Costs and Energy Consumption for Various Biomass Energy Transport Chains. Utrecht: Universiteit Utrecht – Copernicus Institute.
Szargut, J., Morris, D. R., and Steward, F. R. (1988). Exergy Analysis of Thermal, Chemical and Metallurgical Processes. Berlin, Germany: Hemisphere Publishing Corporation.
Thermoflow Inc. (2020). Thermoflow Software. Jacksonville, USA: Thermoflow Incorporated. Available at: https://www.thermoflow.com/thermoflow_overview.html (Accessed June 03, 2022).
Velásquez, H. I., Colorado, A. R., and Oliveira, S. (2009). Ethanol Production from Banana Fruit and its Lignocellulosic Residues: Exergy and Renewability Analysis. Int. J. Thermodyn. 12, 155–162. doi:10.5541/ijot.251
Keywords: ammonia, bagasse, gasification, exergy, carbon credit, economics
Citation: Telini RO, Flórez-Orrego D and de Oliveira Junior S (2022) Techno-Economic and Environmental Assessment of Ammonia Production From Residual Bagasse Gasification: A Decarbonization Pathway for Nitrogen Fertilizers. Front. Energy Res. 10:881263. doi: 10.3389/fenrg.2022.881263
Received: 22 February 2022; Accepted: 30 May 2022;
Published: 15 June 2022.
Edited by:
Yoshiharu Amano, Waseda University, JapanReviewed by:
Muhammad Aziz, The University of Tokyo, JapanClaudia Gutiérrez-Antonio, Universidad Autónoma de Querétaro, Mexico
Copyright © 2022 Telini, Flórez-Orrego and de Oliveira Junior. This is an open-access article distributed under the terms of the Creative Commons Attribution License (CC BY). The use, distribution or reproduction in other forums is permitted, provided the original author(s) and the copyright owner(s) are credited and that the original publication in this journal is cited, in accordance with accepted academic practice. No use, distribution or reproduction is permitted which does not comply with these terms.
*Correspondence: Rodrigo Oliveira Telini, cm9kcmlnb3RlbGluaUBhbHVtbmkudXNwLmJy