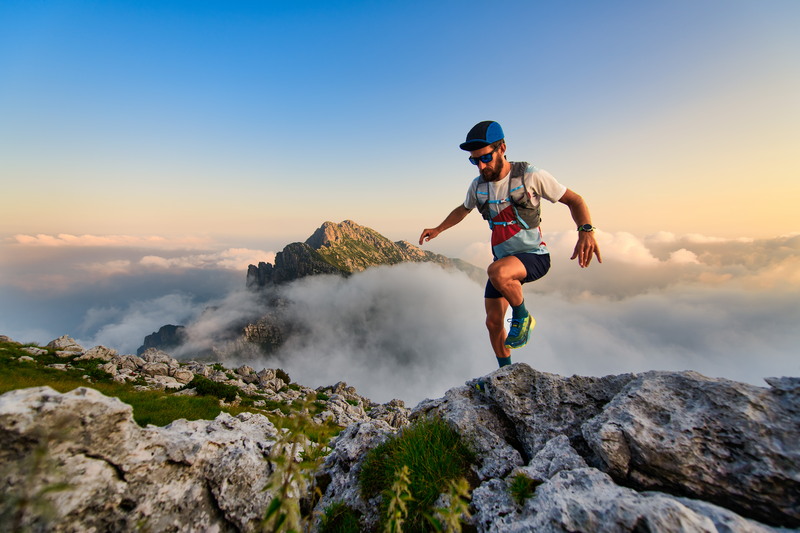
95% of researchers rate our articles as excellent or good
Learn more about the work of our research integrity team to safeguard the quality of each article we publish.
Find out more
METHODS article
Front. Energy Res. , 26 May 2022
Sec. Process and Energy Systems Engineering
Volume 10 - 2022 | https://doi.org/10.3389/fenrg.2022.871604
This article is part of the Research Topic Advanced Water Splitting Technologies Development: Best Practices and Protocols View all 20 articles
Accurate and reproducible screening of the electrocatalytic activity of novel materials for Oxygen Evolution Reaction (OER) and Hydrogen Evolution Reaction (HER) requires establishing an easily adoptable harmonized testing protocol. Herein, we describe a robust, instrumentation-independent testing technique utilizing a three-electrode cell with a fully immersed working electrode. Compared to rotating disk electrode (RDE) techniques, this protocol produces current densities close to those obtained in real electrolyzers and eliminates the usage of the expensive RDE apparatus.
The number of novel electrocatalysts for low-temperature water electrolysis is dramatically increasing annually. Having a tremendous amount of OER/HER performance data associated with various catalyst formulations makes comparison of their activity extremely complicated and convoluted. It is well known that most activity data is obtained under different conditions, usually based on legacy parameters used within each individual research groups to compare data with a previous dataset.
This situation makes establishing baseline state-of-the-art (SoA) electrocatalysts complex, impedes the selection of future material development for low-temperature water electrolysis, and overall slows down progress in the field of green hydrogen production.
We note that the electrochemical activity of electrocatalysts is evaluated primarily in RDE experiments (McCrory et al., 2013), which may not be the best comparison for electrolysis, especially for OER (Hartig-Weiss et al., 2020). The low loading of Platinum Group Metal (PGM)-free oxides on the RDE (typically 0.2–0.6 mg cm−2) makes the evaluation of these catalysts complicated, as these oxides usually have very low electrical conductivity and thus low activity at low loading. The electrochemical activity of low-conductivity catalysts in Gas Diffusion Electrodes (GDEs) or Catalyst Coated Membranes (CCMs) at loadings of 2–8 mg cm−2 will be substantially different than that in a conventional RDE (Kroschel et al., 2019). Additionally, the substrate for catalyst loading in the RDE instrument is very small (usually <0.5 cm2), which is hundreds of times below in the electrode geometric surface area in real electrolyzers. The smooth, nonporous (typically glassy carbon) catalyst support in an RDE is substantially different from the textured, high-porosity GDEs in an electrolyzer. Finally, the RDE is an expensive instrument, and not accessible widely.
A static electrode can be used to compare the electrochemical activity of catalysts without the need for an RDE (Du et al., 2014). Herein, we describe a robust, instrumentation-independent testing technique utilizing a three-electrode cell with a fully immersed working electrode. The protocol’s advantages compared to RDE testing include the ability to test low-conductivity catalysts at higher loading and thus increased current densities, eliminating the usage of expensive RDE equipment, and easier bubble management in OER, more versatility in substrate. This protocol with fully immersed working electrode allows for rapid catalyst screening in conditions that are closer to those in an electrolyzer than the conditions in an RDE.
This protocol describes a standard method for screening HER/OER electrocatalysts using fully immersed electrodes covered with an aqueous electrolyte. The methods described here are optimized for use in room temperature alkaline solutions with a high loading of electrocatalyst (up to 4 mg cm−2) and can be used for both PGM and PGM-free catalysts.
This protocol allows the user to quickly and easily measure an electrocatalyst’s HER/OER activity. The electrochemical performance datasets from electrocatalysts characterized using these methods can be directly compared. This protocol enables rapid screening of newly developed electrocatalyst materials before incorporating them into a full electrolyzer membrane electrode assembly (MEA). In this protocol, users will perform linear sweep voltammetry (LSV) and bulk electrolysis via chronoamperometry (CA) in a standard three-electrode electrochemical cell with an aqueous electrolyte.
Following proper safety training on the electrical equipment used in this protocol, these experiments can be done by technicians, undergraduate students, graduate students, postdoctoral researchers, or other scientists.
Do not touch the electrochemical cell, wires, or potentiostat while the experiment is in progress (active potentiostat) to prevent electrical shock. Be aware of all hazards listed in the safety data sheet (SDS) for the electrolyte used in the electrochemical cell.
To complete the procedure properly, researchers need a potentiostat, electrolyte, and electrodes. A standard potentiostat with 5 V and 5 A capability is sufficient for this protocol. The electrolyte consists of de-ionized (DI) water and an electrolyte salt. The electrolyte salt—commonly potassium hydroxide (KOH)—should be at least 95% purity. Typical electrolyte concentrations are 0.1–1 M. Here, we use different KOH concentrations (0.1, 0.5, and 1 M) as an example. The electrolyte needs to be sparged through with an inert gas such as argon to remove any dissolved reactive gases.
For the three-electrode measurement described here, a working, counter, and reference electrode are needed. The working electrode is the electrode of interest; typically, the catalyst of interest is deposited on a conductive substrate with low electrochemical activity such as stainless-steel mesh, glassy carbon, or carbon paper. A platinum (Pt) wire or sheet of at least 99% purity should be used as the counter electrode if the working electrode contains PGMs. If the working electrode is PGM-free, a graphite rod should be used as the counter electrode. Finally, a standard reference electrode is needed. A mercury/mercury oxide (Hg/HgO) reference is recommended for basic solutions. Optionally, researchers can use a multimeter and a second reference electrode of the same type as the first to check the stability and accuracy of the reference electrode that will be used in the electrochemical cell. This second electrode should be unused other than for periodic checks against the reference electrode used in testing and should be stored properly per the manufacturer’s directions.
For general electrochemical theory, we recommend reading the following textbook chapters: 1) the introduction and chapters on potential sweep and bulk electrolysis methods in Bard, A. J.; Faulkner, L. R. Electrochemical Methods: Fundamentals and Applications, second ed.; John Wiley and Sons, Inc, New York, 2001. and 2) the introduction and chapter on reference electrodes in Newman, J.; Thomas-Alyea, K. E. Electrochemical Systems, third ed.; Wiley: Hoboken, NJ, 2004.
Prepare the three-electrode cell and perform electrochemical measurements on the working electrode according to the steps below.
1) Prepare electrolyte solution with different KOH concentrations (0.1, 0.5, and 1 M). The volume of electrolyte prepared should be enough to fill the beaker or specialized electrochemical cell.
2) Rinse the electrochemical cell, electrodes, and inert gas feed tube with DI water.
3) Add electrolyte solution to the electrochemical cell.
4) Sparge the electrolyte with inert gas for at least ten minutes before starting an electrochemical experiment and continue to bubble gas through the electrolyte during electrochemical measurements.
5) Measure and record the temperature of the electrolyte.
6) Add electrodes to the cell and connect them to the appropriate leads on the potentiostat. Use the HER or OER catalyst of interest as the working electrode (WE), a counter electrode (CE), and a reference electrode (RE). Make sure that none of the electrodes are in contact with each other above or in the electrolyte. Make sure that none of the alligator clips used to connect the electrodes to the potentiostat are in contact with the electrolyte or each other, and that the electrode wires and alligator clips do not show any signs of corrosion or mechanical failure. Cell components and the final cell assembly are shown in Figure 1. Measure the geometric area of the working electrode that is exposed to the electrolyte (1 cm × 1 cm is recommended).
7) Condition the catalyst for electrochemical testing.
8) A) For OER catalysts, e an LSV between 1.4 and 2.2 V vs. reversible hydrogen electrode (RHE) at 10 mV/s.Figure 2 shows an example for OER with stainless-steel mesh WE, Pt wire CE, and Ag/AgCl RE in different concentrations of KOH electrolytes. B) For HER catalysts, perform an LSV between 0 and −0.5 V vs. RHE at 10 mV s−1. Measure the resistance between the WE and the RE by impedance spectroscopy between 100 kHz and 0.1 Hz. The obtained resistance from the lowest x-intercept in a Nyquist plot is used for IR correction.
9) Measure and determine the electrochemically active surface area (ECSA) of the immersion WE using double-layer capacitance (McCrory et al., 2013; Shao et al., 2013; Cossar et al., 2020).
10) Perform bulk electrolysis using CA. Hold at 0 A for 3 s for the induction period followed by 20 mA for 1 h for the electrolysis period. End with 0 A for 1 s in the relaxation period.
FIGURE 2. The performance of stainless-steel WE for OER in different concentrations of KOH electrolytes.
Working electrodes with the catalyst of interest can be prepared in a variety of ways. Here, we discuss the preparation of a working electrode using a stainless-steel mesh as a support for the catalyst of interest. Put a stainless-steel mesh into pure ethanol and sonicate in an ultrasonic bath for 10 min. Dry in air for 15 min. Measure the mass of the mesh. Deposit desired amount of catalyst ink (typically consisting of a catalyst and a polymer binder) on the surface of the mesh using a commercial airbrush or other method. (Ensure deposition methods used are repeatable among samples). Dry at 50°C for 25 min. Measure the mass of the coated electrode to ensure the correct loading of electrocatalyst (e.g., 1, 2, or 3 mg cm−2). Stainless steel can be electrochemically activated to form NiFe-hydroxides on the surface; thus, a control experiment with the uncoated stainless steel is required.
Rinse electrodes and electrochemical cell in DI water and allow to air dry after electrochemical testing.
A standard laptop or desktop with corresponding potentiostat connection (available in USB and wireless connections as of 2021) is required to operate the potentiostat record electrochemical data. Software to operate the potentiostat is supplied with the instrument from the manufacturer (e.g., Biologic, Pine Instruments, Gamry, or other vendors).
Divide the current measured during the experiments by the ECSA of the working electrode exposed to the electrolyte to calculate current density. Collected polarization curves from LSV measurements can be used to determine either the current density at a given potential or the potential at an operational current density (e.g., 0.2 A/cm2 @ 1.8 V vs. RHE).
Results from this protocol include LSV (current density plotted against potential) and chronoamperograms (current density plotted against time). In order for data to be compared reliably with results from other publications, it is important to include the composition, pH, temperature, and concentration of electrolyte and to reference the voltage reported to a particular standard reference electrode. To compare results from different reference electrodes, consult a conversion table. The Tafel slope of the catalyst can be obtained from LSV data (Hu et al., 2019; YANG et al., 2021). Additionally, the effect of IR correction can be critical in low concentration electrolytes. The stainless steel mesh is used to connect the active area of the WE and the clip from the equipment, and the ECSA of the immersion area (active area of the electrode) is determined to make sure that the active area is constant among different experiments. The current density needs to be normalized if the ECSA is not constant.
Electrochemical testing must be repeated for each working electrode type at least once for a total of two measurements. If the difference in current density is more than 10%, repeat the measurements for a third trial to achieve data consistency.
Reference electrodes are used because they have a stable and known potential. However, the potential of the reference electrode can drift due to improper reference electrode storage or long duration usage in an electrolyte different from the reference electrode storage solution. Ensure that the reference electrode is in working order by checking it against a fresh, unused reference electrode or by preparing a hydrogen reference electrode.
1) Fresh reference method: Immerse the reference electrode and another fresh, unused reference electrode of the same type into an unused electrolyte solution. Use a multimeter to measure the potential between the electrical leads on the two reference electrodes. The magnitude of the difference should be < 5 mV for the reference to pass the calibration check.
2) Hydrogen electrode method: Assemble a 3-electrode cell with a platinum working electrode, any compatible counter electrode, the desired reference electrode, and an acidic electrolyte with a 1 M proton concentration [(H+)]. Run a CV in which the current switches from cathodic to anodic (or vice versa), adjusting the voltage extrema until this condition is met. The potential corresponding to 0 current should be ± 5 mV from the theoretical potential of the reference electrode versus the standard hydrogen electrode (SHE).
Do not allow any electrodes or exposed wires to touch while an electrochemical measurement is running. Always store reference electrodes in the standard solution appropriate for the reference type. Do not allow reference electrode to dry out.
Always follow the manufacturer’s guidance on electrolyte compatibility with the desired reference electrode. Reference electrodes should always be stored in the manufacturer-recommended storage solution and never be allowed to dry out. A dry reference electrode can lead to crystallization of salts in the porous frit, clogging the pores and changing the potential of the reference electrode.
Be sure to convert the current reported by the potentiostat software to current density so that results from differently sized electrodes can be compared. Only the portion of the electrodes that are submerged in electrolyte are electrochemically active, so only the submerged area of the working electrode should be used to calculate current density. Reporting the catalyst areal loading (mass of catalyst per electrode area) allows researchers to account for differences in catalyst activity resulting from different loadings.
Check the potentiostat manual and software settings to be sure the correct cables are used to connect each of the three electrodes to the potentiostat.
The main issues with the three-electrode method are related to poor electrical contact between wires connected from the potentiostat to the working electrode, reference electrode, and counter electrode and the connection from the potentiostat to the computer. These should be checked before starting the experiment. Open circuit voltages are typically less than 10 mV but greater than 2 mV.
Potentiostats arrive pre-calibrated from the manufacturer, but many are supplied with a dummy cell to use in checking the potentiostat function. Repeated experiments with fresh working electrode and electrolyte should be used to determine repeatability and standard deviation.
Any analytical methods applied to the data generated by the protocol must be referenced or described. Results must be replicable.
The original contributions presented in the study are included in the article/supplementary material, further inquiries can be directed to the corresponding author.
AS, XL, and GM—protocol design, experimentation EC and RO—data analysis, protocol discussion AS, XL, EC, RO, and GM—manuscript preparation
This manuscript has been authored by UT-Battelle, LLC, under contract DE-AC05-00OR22725 with the US Department of Energy (DOE). The US government retains and the publisher, by accepting the article for publication, acknowledges that the US government retains a nonexclusive, paid-up, irrevocable, worldwide license to publish or reproduce the published form of this manuscript, or allow others to do so, for US government purposes. DOE will provide public access to these results of federally sponsored research in accordance with the DOE Public Access Plan (http://energy.gov/downloads/doe-public-access-plan).
Author GM is employed by Pajarito Powder, LLC. Author RO is employed by Nel Hydrogen.
The remaining authors declare that the research was conducted in the absence of any commercial or financial relationships that could be construed as a potential conflict of interest.
All claims expressed in this article are solely those of the authors and do not necessarily represent those of their affiliated organizations, or those of the publisher, the editors and the reviewers. Any product that may be evaluated in this article, or claim that may be made by its manufacturer, is not guaranteed or endorsed by the publisher.
The authors EC, XL, and AS acknowledge funding support from DOE H2NEW consortium and DOE DE-EE0008081 “High Efficiency PEM Water Electrolysis Enabled by Advanced Catalysts, Membranes, and Processes” project. GM acknowledged funding support from DE-AR0000688 project. RO acknowledges funding support from DOE-DE-EE0008092 “Benchmarking Advanced Water Splitting Technologies: Best Practices in Materials Characterization” project.
Cossar, E., Houache, M. S. E., Zhang, Z., and Baranova, E. A. (2020). Comparison of Electrochemical Active Surface Area Methods for Various Nickel Nanostructures. J. Electroanal. Chem. 870, 114246. doi:10.1016/j.jelechem.2020.114246
Du, C., Tan, Q., Yin, G., and Zhang, J. (2014). “Rotating Disk Electrode Method,” in Rotating Electrode Methods and Oxygen Reduction Electrocatalysts (Elsevier), 171–198. doi:10.1016/b978-0-444-63278-4.00005-7
Hartig-Weiss, A., Tovini, M. F., Gasteiger, H. A., and El-Sayed, H. A. (2020). OER Catalyst Durability Tests Using the Rotating Disk Electrode Technique: the Reason Why This Leads to Erroneous Conclusions. ACS Appl. Energy Mat. 3, 10323–10327. doi:10.1021/acsaem.0c01944
Hu, X., Tian, X., Lin, Y.-W., and Wang, Z. (2019). Nickel Foam and Stainless Steel Mesh as Electrocatalysts for Hydrogen Evolution Reaction, Oxygen Evolution Reaction and Overall Water Splitting in Alkaline Media. RSC Adv. 9, 31563–31571. doi:10.1039/c9ra07258f
Kroschel, M., Bonakdarpour, A., Kwan, J. T. H., Strasser, P., and Wilkinson, D. P. (2019). Analysis of Oxygen Evolving Catalyst Coated Membranes with Different Current Collectors Using a New Modified Rotating Disk Electrode Technique. Electrochimica Acta 317, 722–736. doi:10.1016/j.electacta.2019.05.011
McCrory, C. C. L., Jung, S., Peters, J. C., and Jaramillo, T. F. (2013). Benchmarking Heterogeneous Electrocatalysts for the Oxygen Evolution Reaction. J. Am. Chem. Soc. 135, 16977–16987. doi:10.1021/ja407115p
Shao, M., Odell, J. H., Choi, S.-I., and Xia, Y. (2013). Electrochemical Surface Area Measurements of Platinum- and Palladium-Based Nanoparticles. Electrochem. Commun. 31, 46–48. doi:10.1016/j.elecom.2013.03.011
Yang, X.-m., Li, Z.-p., Qin, J., Wu, M.-x., Liu, J.-l., Guo, Y., et al. (2021). Preparation of Ni-Fe Alloy Foam for Oxygen Evolution Reaction. J. Fuel Chem. Technol. 49, 827–834. doi:10.1016/s1872-5813(21)60084-1
A ampere
cm2 centimeter squared
mg milligram
mV millivolt
s second
V volt
CA chronoamperometry
CE counter electrode
CV cyclic voltammetry
DI de-ionized
ECSA electrochemically active surface area
HER hydrogen evolution reaction
Hg/HgO mercury: mercury oxide
KOH potassium hydroxide
LSV linear sweep voltammetry
MEA membrane electrode assembly
OER oxygen evolution reaction
OCP open circuit potential
PGM platinum group metal
Pt platinum
RDE rotating disk electrode
RE reference electrode
RHE reversible hydrogen electrode
SDS safety data sheet
SHE tandard hydrogen electrode
SoA state-of-the-art
WE working electrode
Keywords: oxygen evolution reaction, hydrogen evolution reaction, electrochemistry, electrolysis, water splitting
Citation: Creel EB, Lyu X, McCool G, Ouimet RJ and Serov A (2022) Protocol for Screening Water Oxidation or Reduction Electrocatalyst Activity in a Three-Electrode Cell for Alkaline Exchange Membrane Electrolysis. Front. Energy Res. 10:871604. doi: 10.3389/fenrg.2022.871604
Received: 08 February 2022; Accepted: 12 May 2022;
Published: 26 May 2022.
Edited by:
Olga A. Marina, Pacific Northwest National Laboratory (DOE), United StatesReviewed by:
Mike Lyons, Trinity College Dublin, IrelandCopyright © 2022 Creel, Lyu, McCool, Ouimet and Serov. This is an open-access article distributed under the terms of the Creative Commons Attribution License (CC BY). The use, distribution or reproduction in other forums is permitted, provided the original author(s) and the copyright owner(s) are credited and that the original publication in this journal is cited, in accordance with accepted academic practice. No use, distribution or reproduction is permitted which does not comply with these terms.
*Correspondence: Alexey Serov, c2Vyb3ZhQG9ybmwuZ292
Disclaimer: All claims expressed in this article are solely those of the authors and do not necessarily represent those of their affiliated organizations, or those of the publisher, the editors and the reviewers. Any product that may be evaluated in this article or claim that may be made by its manufacturer is not guaranteed or endorsed by the publisher.
Research integrity at Frontiers
Learn more about the work of our research integrity team to safeguard the quality of each article we publish.