- 1Pacific Northwest National Laboratory, Battelle Memorial Institute, Electrochemical Materials and Devices Team, Energy and Environment Directorate, Richland, WA, United States
- 2Department of Chemical and Biological Engineering, Monash University, Clayton South, VIC, Australia
To standardize materials and component characterization for next generation hydrogen production and energy generation solid oxide cell (SOC) technologies, test protocols are being established to facilitate comparison across the numerous laboratories and research institutions where SOC development for application in solid oxide fuel cells (SOFCs) and solid oxide electrolyzes cells (SOEC) is conducted. This paper proposes guiding protocols for fundamental electrical properties characterization of SOC materials, including temperature- and oxygen partial pressure (pO2)-dependent conductivity measurements, and use of the electromotive force for determining the transference numbers, or contributions of each charge carrier (i.e., ions and electrons), to the total conductivity. The protocol for Archimedes density measurements is also provided as an integral technique to both of these methods.
1 Introduction
Solid-state electrochemistry is a continually evolving area of science and technology, with researchers and developers from numerous universities, laboratories, and industries globally carrying out measurements to characterize various materials and processes. As a result, there is a vast variety of experimental protocols, sample preparation methods, test fixtures, and instruments. The Energy Materials Network (ENM) consortium is attempting to bring together researchers and experts from academia, national labs, and industry across the globe to review test procedures and agree on and establish a testing protocol for various routine measurements. This manuscript is part of a series of guidelines and protocols prepared by a cohort of researchers brought together at the HydroGEN Advanced Water Splitting Technology Pathways Benchmarking and Protocols Workshop organized by ENM over the last few years. The aim here is to provide a technical guideline that may better compare the published results where possible and provide much-needed operating procedures for new entrants and students in the field. It is acknowledged that the proposed method may need to be modified to suit particular laboratory equipment and would evolve with the development of new methods and new instruments. However, we believe protocol will be helpful as a starting point to develop globally unified testing approaches. The objective here is not to provide specific experimental results but to share a step-by-step procedure for the techniques discussed in this paper.
Electrical conductivity measurements are essential for characterization of SOC component materials. Electrical charge transport in solid oxide materials involves conduction via ions, electrons, and holes as governed by defect chemistry. The total conductivity (σtotal) is expressed as
and is usually measured using four-probe conductivity measurements, a technique extensively applied to electronic ceramics and electrochemical materials, including SOC cathodes and electrolytes (Badwal et al., 1991; Vladislav, 2009; Jo et al., 2021).
The operating environment, pressure, and temperature affect conductivity mechanisms and dictate dominant conducting species. The theoretical foundations of defect chemistry of solid-state electrochemical systems and the thermodynamics of electronic and ionic charge carriers are presented in the literature (Geller, 1977; Tuller and Balkanski, 2012). The charge carrier contributions govern the suitability of materials for application in SOCs. Thus, once total electrical conductivity is known, it is essential to determine the contribution of each charge carrier (ions, electrons, and holes).
In SOC electrolytes, ionic conductivity should be dominant with minimal electronic conduction to maximize Faradic efficiency. For electrode materials, mixed ionic electronic conduction is desired to extend the electrochemical reaction zone beyond the electrode/electrolyte interface. Furthermore, mixed conductivity in barrier layers or functional interfaces can also significantly affect cell performance (Matsuzaki and Yasuda, 2002). Therefore, accurate ionic and electronic conductivity assessments are essential for SOC development. Common methods for determining ionic transference and separating ionic and electronic conductivity include Wagner-Hebb Polarization (blocking electrodes) (Riess, 1992), electromotive force (EMF) measurement (Norby, 1988), four-probe conductivity measured with varying pO2, and ion permeation measurements.
Selecting methods for deconvoluting ionic and electronic conductivity depends upon the intended use of the materials. For electrolytes, where dominant conductivity should be ionic, the EMF method can determine the transference number and has been used to characterize electrolytes like doped ceria (Ananthapadmanabhan et al., 1990; Kang et al., 2006; Fagg et al., 2009). The EMF method has also been extensively used to measure transference numbers in proton conducting ceramics (Norby, 1988). The method is prone to errors when electronic conductivity is comparable to or higher than ionic conductivity and when interfacial resistance is significant (Liu and Hu, 1996). In SOC electrodes, electronic conductivity is dominant. Thus, for separating their ionic and electronic conductivities, four-probe methods with varying pO2 are more suitable (Yoon et al., 2009; Yang et al., 2013).
Electrochemical characterization of ceramics is complex and specimen preparation, size, equipment, and environmental condition can affect the measurements. Moreover, experimental procedures often cannot be reported in full detail due to manuscript constraints. Thus, this protocol provides detailed procedures for four-probe conductivity and EMF methods as applied to SOCs.
2 Protocol Scope
2.1 Scope and Applicability
Conductivity is measured as a function of temperature and under controlled pO2 or gas compositions of interest and provides the overall conductivity, ionic and electronic together. Separating oxygen ionic and electronic contributions is based upon the relationship between the concentrations of charge carriers (ions, electrons or holes) and pO2 around the specimen. The method applies to measurement of oxygen conductivity based upon certain assumptions described in the Results section.
For more accurate separation of ionic and electronic conductivity in oxygen ionic conductors, additional measurements using the EMF method can more directly determine the transference numbers of contributing charge carriers. Different partial pressures of the gases of interest (e.g., oxygen, hydrogen, or steam) are maintained over the two sides of a solid oxide membrane (typically a disc). As an approximation, the ionic transference number (Ti) corresponds to the ratio between the open circuit voltage (OCV) and the theoretical Nernst voltage (Norby, 1988 and Jasna, 2011). Impedance measurements provide a correction for polarization resistance effects on the measured OCV which causes errors in the determination of Ti (Jasna, 2011). Results from different partial pressure combinations can be averaged to obtain Ti. The emf method is limited to materials with sufficient Ti that electronic conductivity does not prevent a measurable OCV.
For accurate conductivity and transference number measurements, both methods require bulk density measurements. Thus, a density measurement protocol will also be provided. In SOC development, sintered density measurements also provide useful information regarding the suitability of a given processing or fabrication approach to achieve the density/porosity required for a given material application.
2.2 Summary of Method
Four-point conductivity. Four platinum paste electrodes are applied to a bar-shaped specimen with ≥95% relative density. Silver is generally avoided due to its tendency for electromigration, which can artificially inflate the measured conductivity. Platinum wires are connected to the electrodes and the sample is placed in a furnace with a calibrated zirconia oxygen sensor. A gas mixer supplies gas mixtures, such as CO/CO2 or Ar/O2, to accurately control the pO2. Other gas mixtures, including H2/Ar/N2/H2O, can be used to discriminate proton conduction. Another convenient buffer gas system, H2/CO2, does not require handling CO or controlling H2O vapor. Four-point conductivity measurements are performed as a function of oxygen, hydrogen, or steam partial pressure and/or temperature.
EMF method. A sintered disc is prepared with circular screenprinted Pt electrodes on each side. Here again, silver should be avoided due to electromigration. Generally, a single screenprinted layer thickness is sufficient for the electrode. The two electrodes are hermetically isolated from each other using glass, gold or ceramic seals in a test fixture, such as a SOC button cell test fixture. A precision gas mixer supplies gas mixtures to control the partial pressures of gases on the electrodes. The voltage (EMF) across the sample is measured over a range of partial pressures and temperatures to determine ionic transference number using a high precision multi-meter. The background voltage is measured without a chemical gradient. Impedance is measured using a frequency analyzer and potentiostat. Transference numbers are calculated from the measured emf values based on the Nernst equation with corrections for polarization resistance dictated by impedance results.
Density measurement. For bulk specimens, the Archimedes (or saturated-suspended weight) method generally provides the most accurate results, particularly for irregularly shaped specimens.
2.3 Personnel Qualifications/Responsibilities
Ceramic processing, dry-pressing, high-temperature sintering, and use of electrical devices (e.g., direct current (DC) power supply and multi-meter), and gas safety training are required.
2.4 Health and Safety Warning
Only trained persons should operate equipment, fabricate and prepare specimens, and handle chemicals. Safety measures for hazards and risks associated with powders and solvents, electrical equipment, hot surfaces, and flammable and asphyxiant gases are mandatory. Refer to safe working instructions, personal protective equipment guidelines, Safety Data Sheets (SDS), and best health, safety, and environment (HSE) practices in your lab.
Special safety precautions must be observed as CO is a toxic gas (hazardous chemical) and inhalation of only 4,000 ppm in air could prove fatal in less than one hour. Reference the SDS prior to use.
Check all sensors for current calibration. Gas safety interlocks must be fully operational. Check light emitting diode (LED) and other indicators on the gas safety panel before use (refer to manual).
2.5 Equipment and Supplies
• Platinum wire (typical diameter ∼0.25 mm)
• >95% dense bar specimen; typical dimensions are 2–5 mm × 4–5 mm × 40 mm.
• Platinum or gold ink/paste
• Diamond saw
• Small paint brush
• Needle nose pliers
• Micrometer calipers
• Tube furnace
• High purity gas source
• High impedance precision digital multi-meter or potentiostat
• Sintered disc specimen (1 mm thick, 18–27 mm diameter)
• Button cell test fixture
• Sealing material (Gold, ceramic or glass)
• Gas mixer (MIX-2000 Digital or in-house equivalent)
• A pair of hydrogen/oxygen sensors
• Bronkhorst Steam generator-gas mixer or separate humidifier
• Frequency analyzer or electrochemical analyzer capable of electrochemical impedance spectroscopy (EIS) measurements
• High temperature 4-point conductivity test fixture
• Mass balance
• Liquid of known density
• Apparatus for determining the apparent mass of a specimen suspended in liquid (density kits are available for most mass balances)
2.6 Nomenclature and Definitions
AC alternating current
DC direct current
DMM digital multimeter
EIS electrochemical impedance spectroscopy
EMF electromotive force
HSE health, safety, and environment
LED light emitting diode
OCV open circuit voltage
OEM original equipment manufacturer
pH2O water partial pressure
pO2 oxygen partial pressure
SOC solid oxide cell
SOEC olid oxide electrolysis cell
SOFC solid oxide fuel cell
SOP standard operating procedure
XRD x-ray diffraction
YSZ yttria-stabilized zirconia
3 Procedure
3.1 Step-By-Step Procedure
3.1.1 Four-point Conductivity
1) Perform density measurement on the sample using the Archimedes’ method described below. Relative density ≥95% is expected.
2) With a diamond saw, cut thin notches around the bar ∼4 and 9 mm from each lengthwise end (see Figure 1). The distance between the inner notches should be ≥4 times the larger perpendicular (cross-sectional) dimension. The notches should be shallow, only deep enough to keep the wire in the groove from sliding.
3) Using a small paint brush, paint a small band of platinum ink (Engelhard 6082 or equivalent) in the notches. The nominal band thickness is 0.5 mm. Silica-free masking tape may be used to control the thickness.
4) Wrap platinum wire around the platinum bands in the notches and twist to tighten them down with needle nose pliers, taking care not to break the wire.
5) Heat the assembly to 900°C for 30 min in synthetic air to sinter the Pt ink.
6) After cooling, check that the wires are still tight and gently retighten if needed.
7) Use micrometer calipers to measure the width and thickness of the sample bar and distance between the innermost platinum wires.
8) Electrically connect the Pt wires to the potentiostat with the innermost wires connected to voltage leads and the outer wires to current leads. This can be done by spot welding.
9) Place the bar in the furnace with the thermocouple near its center.
10) Alternatively to the steps above, commercial fixtures (e.g., Probostat™—NORECS) are also available. Follow the manufacturer’s instructions for attaching the specimen.
Furnace and potentiostat control software can automate the following:
11) Heat to the desired measurement temperature.
12) Introduce the desired gas atmosphere (if other than air). When gas composition [e.g., pO2 or water partial pressure (pH2O)]is varied, allow a suitable purge time of at least 30 min for equilibration of each gas. Suitable gas sensors can be used where applicable. For example, pO2 could be monitored using a calibrated oxygen sensor or steam could be monitored using an appropriate dew point sensor.
13) Set the potentiostat to a constant current of between 0.5 and 10 mA and measure the voltage, then the same current in the opposite direction (negative value) and measure the voltage. Allowing the measured voltage to stabilize is a good way to confirm equilibration.
14) Repeat steps 12–13 for each gas composition of interest. Do not exceed the range of gas compositions within which the specimen is stable (i.e., avoid sample decomposition.) Measurements should be performed in doublets (i.e., while changing partial pressures in one direction, then while going back in the reverse direction) to observe any hysteresis.
15) Heat to the next temperature of interest and repeat steps 12–14.
3.1.2 Emf Method for Transference Numbers
1) Screen print Pt or Au electrodes (8–15 mm dia) onto both sides of the dense sample disc, using Pt or Au ink (e.g., Engelhard 6082), and fire at 800°C for 1 h.
2) An in-house made or commercial button cell test fixture can be used. It should have springloaded Pt meshes on the electrodes for firm connections. Alternatively, leads can be welded to Au or Pt mesh previously attached to the electrodes with sintered Au or Pt paste. Connect the leads to the frequency analyzer and potentiostat for voltage and EIS measurements.
3) Check the apparatus for mechanical integrity of the alumina tube and test fixture and for thermocouple positioning.
4) Use glass, ceramic, or gold for cell sealing. Follow the appropriate seal application procedures and heating/cooling cycles. (See Appendix for the typical cycles for each seal type.) To avoid contamination, use synthetic air as a purge gas during seal formation.
5) Connect oxygen sensors at the outlet of both chambers to measure pO2. Ideally these sensors would be located near the electrodes, however, such placement is difficult in typical button cell fixtures.
6) After sealing, ramp at 3°C/min to the test temperature, where at least 30 min should be allowed to equilibrate.
7) N2 or another inert gas should be used to flush air out prior to introducing hydrogen in step 8.
8) Introduce hydrogen to one side of the sealed cell using a constant flow rate (e.g., 20 ml/min) to pressure test the seal. After closing the exhaust, drop the hydrogen flow rate to zero. After 30 min, OCV should reach above 1.1 V. The pressure test and OCV will confirm seal formation.
9) With a quality seal, flush both chambers with the same gas mixture. For example, for proton transference number determination, both chambers can be flushed with 45% H2/50% Ar/5% H2O. The mixture can be generated using gas mixers and a Bronkhorst steam generator or humidifier with a heated gas line. Allow 30 min for equilibration. Typical flow rates are 20 ml/min (For oxygen transport number determination, different gas mixtures can be used). Confirm the partial pressures in each chamber using gas sensors at the outlets.
10) After 30 min, the OCV should ideally be zero. Note any deviation from zero voltage. This compensation voltage should be subtracted from subsequent voltage measurements.
11) Vary the partial pressure in one chamber, keeping the other chamber constant.
12) Record the voltage after at least 30 min at each partial pressure (or until the voltage stabilizes).
13) Collect an EIS spectrum covering a range of frequencies that captures the high and low frequency x-axis intercepts in a Nyquist plot, reflective of the ohmic and total resistances of the specimen.
14) Repeat steps 12–13 for at least 4 to 5 different partial pressures.
15) Repeat steps 9–14 for at least 3 different temperatures.
16) Log the data using a Labview interface connected to flow meters, gas sensors, and digital multimeter (DMM), or simply record in a lab book.
3.1.3 Archimedes Density Measurement
1) Measure the dry weight of the specimen (Wd) using a balance.
2) Measure the saturated weight (Wsat) after fully saturating the specimen with a liquid of known density (e.g., water, alcohol, or kerosene). To expedite filling the open pores, place the container holding the immersed sample inside a vacuum chamber and apply a vacuum until the sample no longer outgasses. Remove surface liquid prior to measuring the saturated weight. If volatile liquid is used (e.g., ethanol), conduct the measurement fairly quickly after removal from the bath to avoid evaporation.
3) Measure the weight suspended in the liquid (Wsusp). Commercial “density kits” are available for standard balances to conveniently allow suspended weight measurements.
4) Record the Liquid Temperature
3.2 Sample Preparation and Analysis
Four-probe conductivity samples are typically ≥95% dense 2–5 mm × 4–5 mm × 40 mm rectangular bars with square, flat faces.
Electrolyte discs for the emf method can be prepared by die pressing electrolyte powder into circular discs and sintering to at least 95% relative density, as determined by the Archimedes method. The suggested disc diameter is 18–27 mm, depending on test fixture requirements. Tapecasting or other alternative processes can also be used to fabricate the discs.
Sample bars and discs are best pressed from fine powders that can be obtained from the vendor in the desired particle size or attrition milled from a coarser powder. Generally, powders with an average particle size of less than 5 microns should be used. Prior to introducing the powder into the die, the die should be lubicated by applying a thin layer of zinc stearate solution or oleic acid to the inner walls. After the desired pressure is achieved, the pressure should be held for a few seconds followed by a slow release of the pressure. Both lubrication and gradual pressure release will help avoid springback which can cause the pressed part to crack or fracture. During sintering and subsequent heating of the samples, heating rates should be limited to less than 10°C/min to avoid damage resulting from thermal shock.
Specimens for Archimedes density should be clean and dry.
3.3 Computer Hardware and Software
Data is acquired using an electrochemical workstation, the software interface for the DMM and current source, and/or Labview. Most modern potentiostats have original equipment manufacturer (OEM) software for data monitoring, control, and collection.
3.4 Data Collection, Analysis, and Records Management
Back up data as a text file and in software readable format. Process conditions, dates, and times should be noted. Readouts from gas flow meters and furnace temperature controllers can be integrated into electrochemical measurements using LabVIEW software or an Excel macro.
4 Results
Four-point conductivity. Conductivity (σ) is calculated from current (I), voltage (V), and bar dimensions including cross-sectional area (A) and distance between inner/voltage wire contacts (d) according to:
Plot the results as Log conductivity vs. PO2: For a typical ionic conductor, the electronic conductivity is proportional to PO2. Using defect chemistry, the ionic and electronic conductivity can be separated, and the transference number determined (Kosacki and Tuller, 1995; Riess, 2003). A typical response from a proton conducting oxide measured over a range of temperatures and pO2 is shown in Figure 2.
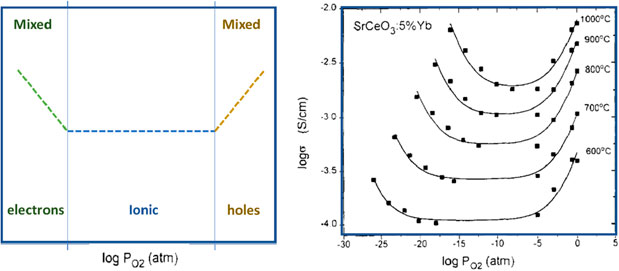
FIGURE 2. Schematic of Conductivity behavior as function of pO2 (LHS), Experimental Data from reference (RHS) showing electrical conductivity of SrCeO:5%Yb vs. pO2. (Figure adapted from Reference 16 with permission from Elsevier).
The method relies on certain assumptions to “separate” ionic and electronic conductivity:
1. The entire specimen responds to changes in the environment.
2. No significant voltage is generated at bar interface.
For more accurate separation, the electromotive force (EMF) method or blocking electrode method (Hebb-Webner) is recommended.
Emf method. For each measurement condition, the ionic transference number, Ti, is calculated using:
where Ro and Rt are the ohmic and total resistance from EIS, respectively, Eoc is the open circuit voltage or emf, and EN is the theoretical Nernst voltage calculated based on a knowledge of the chemical gradients introduced across the cell and electrochemical principles.
Archimedes density. The bulk density, p, (typically expressed in g/cc, although any units may be used if applied consistently) is calculated using:
where Wd, Wsat, and Wsusp were defined previously, and pf is the liquid density at the measured temperature.
Sintered densities are frequently expressed as relative density, pr, obtained simply by dividing the bulk density by the theoretical (i.e., pore-free) density of the material, pt:
The fractional porosity in the specimen is expressed as (1-pr). The theoretical density is obtained from appropriate tables or x-ray diffraction (XRD) analyses.
5 Quality Control and Quality Assurance
Repeated experiments should be performed and statistical methods employed to confirm the data quality and consistency.
5.1 Instrument or Method Calibration and Standardization
Oxygen (or other gas) sensors must be calibrated over the expected range of partial pressures in a separate experiment to determine sensor drift and deviation. Where air is to be used, substitute synthetic air to avoid contaminants.
Calibrate electrochemical equipment using manufacturer provided test circuits.
Periodically test thermocouples and flow meters using manufacturer recommended procedures.
Follow all instrument standard operating procedures (SOPs) and/or calibration procedures.
5.2 Cautions
Check test rigs for mechanical integrity of ceramic tubes and test fixtures, and for thermocouple positioning. Check the seals by pressure testing at 0.5 bar with nitrogen.
Insulating material can be used to avoid short circuiting the Pt lead wires.
Observe special gas safety precautions as CO is a toxic gas (hazardous chemical).
Other precautions: Hot surfaces, flammable/asphyxiant gases, hazardous chemicals.
5.3 Common Issues
Unusual resistance is often attributable to common problems such as poor contacts, a broken sample or wire, or short circuiting.
5.4 Interferences
Electromagnetic interference associated with the main power supply, induction due to lead wires and furnace windings, and/or the Seebeck effect should be compensated using a “dummy cell”. The dummy cell could be a platinum foil or single crystal yttria-stabilized zirconia (YSZ) with sputtered Pt electrodes.
5.5 Troubleshooting
For unusual results, check the gas flows and system temperature, and reset the electrochemical data acquisition system.
If a seal leak is suspected after step 8 of the emf method, repeat the in-situ sealing heat treatment cycle in step 4.
5.6 Error Analysis
See Reference (Singh, 2013) for error sources relating to 4-point measurements.
6 Lessons Learned
1. For four-probe conductivity measurements, machining the bar and its grooves can break the specimens, especially electrode materials or non-zirconia electrolytes. Thus, specimen preparation can be a materials-intensive process if new materials synthesized at lab scales are evaluated.
2. For EMF measurements, hermetic sealing is critical. Pre-mixed sealants like Ceramabond should be well-mixed before use to avoid solids settling. The shelf life of pre-mixed sealants is limited and hermetic sealing is unlikely after their expiration.
3. For EMF measurements, use of house air may lead to erroneous EMFs, hence certified synthetic air must be used.
Data Availability Statement
The original contributions presented in the study are included in the article/supplementary material, further inquiries can be directed to the corresponding author.
Author Contributions
OM directed the effort. JH and AK collaborated to write the 4-point conductivity protocol. AK wrote the EMF method protocol. JS wrote the Archimedes density protocol. JH compiled the writings into a single manuscript.
Conflict of Interest
The authors declare that the research was conducted in the absence of any commercial or financial relationships that could be construed as a potential conflict of interest.
Publisher’s Note
All claims expressed in this article are solely those of the authors and do not necessarily represent those of their affiliated organizations, or those of the publisher, the editors and the reviewers. Any product that may be evaluated in this article, or claim that may be made by its manufacturer, is not guaranteed or endorsed by the publisher.
Appendix
Sealing procedure for glass and gold seals are as follows:
1. For glass sealing: seals may be formed in-situ or pre-formed externally:
1) For in-situ glass sealing, a glass ring or a paste of Schott G018-311 or a similar glass may be used. Such seals are commercially available from Schott. A typical heating cycle is: 100°C/0.5 h (5°C/min), 180°C/0.2 h (3°C/min), 720°C/1 h (10°C/min) used to reach the operating temperature of the cells. During sealing, use either air or argon for purging the fixture. If sealing paste is desired, a glass powder may be mixed with organic binder (e.g., Ferro Corporation/Schott).
2) For pre-formed glass sealing: The glass seal is applied using glass powder slurry prepared with commercial materials such as Schott GM31107 glass powder mixed with organic binder (typically 4:1 wt%) and annealed to obtain a gas tight seal (refer to instructions provided by Schott for pre-formed seals).
2. Alternatively, a ceramic sealant such as Ceramabond® (Aremco) can be used, and the procedure provided by the manufacturer should be followed for pre-formed ceramic sealing.
3. Gold paste or gold rings can be used for sealing, which involves heating the cell close to the melting temperature of gold (1,050°C) using a 2°C/min ramp rate, holding at 1,050°C for 20 min, and cooling to operating temperature (2°C/min). The ramp rates and hold time are indicative and may change with fixture design and gas flow rates.
References
Ananthapadmanabhan, P. V., Venkatramani, N., Rohatgi, V. K., Momin, A. C., and Venkateswarlu, K. S. (1990). Structure and Ionic Conductivity of Solid Solutions in the System 0·9{(ZrO2)1−x-(CeO2)x}-0·1(Y2O3). J. Eur. Ceram. Soc. 6 (2), 111–117. doi:10.1016/0955-2219(90)90044-g
Badwal, S. P. S., Ciacchi, F. T., and Ho, D. V. (1991). A Fully Automated Four-Probe d.C. Conductivity Technique for Investigating Solid Electrolytes. J. Appl. Electrochem. 21, 721–728. doi:10.1007/bf01034052
Fagg, D. P., Pérez-Coll, D., Núñez, P., Frade, J. R., Shaula, A. L., Yaremchenko, A. A., et al. (2009). Ceria Based Mixed Conductors with Adjusted Electronic Conductivity in the Bulk And/or along Grain Boundaries. Solid State Ion. 180 (11–13), 896–899.
Geller, S. (1977). Solid Electrolytes Topics in Applied Physics. Berlin Heidelberg New York: Springer-Verlag.
Jasna, J. (2011). Proton Conductive Ceramic Materials for an Intermediate Temperature Proton Exchange Fuel Cell. Ph.D. Thesis. United Kingdom: The University Of British Columbia.
Jo, K., Ha, J., Ryu, J., Lee, E., and Lee, H. (2021). DC 4-Point Measurement for Total Electrical Conductivity of SOFC Cathode Material. Appl. Sci. 11 (11), 4963. doi:10.3390/app11114963
Kang, C. H. Y., Kusaba, H., Yahiro, H., Sasaki, K., and Teraoka, Y. (2006). Preparation, Characterization and Electrical Property of Mn-Doped Ceria-Based Oxides. Solid State Ion. 177 (19–25), 1799–1802. doi:10.1016/j.ssi.2006.04.016
Kosacki, I., and Tuller, H. L. (1995). Mixed Conductivity in SrCe0.95Yb0.05O3 Protonic Conductors. Solid State Ion. 80 (3–4), 223–229. doi:10.1016/0167-2738(95)00142-s
Liu, M., and Hu, H. (1996). Effect of Interfacial Resistance on Determination of Transport Properties of Mixed‐Conducting Electrolytes. J. Electrochem. Soc. 143, L109–L112. doi:10.1149/1.1836892
Matsuzaki, Y., and Yasuda, I. (2002). Electrochemical Properties of Reduced-Temperature SOFCs with Mixed Ionic-Electronic Conductors in Electrodes And/or Interlayers. Solid State Ionics 152-153, 463–468. doi:10.1016/s0167-2738(02)00373-9
Norby, T. (1988). EMF Method Determination of Conductivity Contributions from Protons and Other Foreign Ions in Oxides. Solid State Ionics 28-30, 1586–1591. doi:10.1016/0167-2738(88)90424-9
Riess, Ilan. (1992). Four Point Hebb-Wagner Polarization Method for Determining the Electronic Conductivity in Mixed Ionic-Electronic Conductors. Solid State Ion. 51 (3–4), 219–229. doi:10.1016/0167-2738(92)90204-3
Riess, I. (2003). Mixed Ionic–Electronic Conductors—Material Properties and Applications. Solid State Ion. 157 (1–4), 1–17. doi:10.1016/s0167-2738(02)00182-0
Singh, Y. (2013). Electrical Resistivity Measurements: a Review. Int. J. Mod. Phys. Conf. Ser. 22, 745–756. doi:10.1142/s2010194513010970
Tuller, H. L., and Balkanski, M. (2012). Science and Technology of Fast Ion Conductors. Berlin: Springer Science & Business Media.
V. K. Vladislav (Editor) (2009). Solid State Electrochemistry I: Fundamentals, Materials and Their Applications (WILEY-VCH Verlag GmbH & Co. KGaA).
Yang, N., Meng, X., Meng, B., Tan, X., Ma, Z.-F., and Sunarso, J. (2013). Effect of Preparation Methods on the Properties of Ni-YSZ Cermets for SOFC Anodes. ECS Trans. 45, 267–277. doi:10.1149/04529.0267ecst
Keywords: conductivity, solid oxide cell, transference number, ionic, electronic, electrode, electrolyte, interconnect
Citation: Hardy JS, Kulkarni AP, Stevenson JW and Marina OA (2022) Conductivity and Transference Number Determination Protocols for Solid Oxide Cell Materials. Front. Energy Res. 10:867783. doi: 10.3389/fenrg.2022.867783
Received: 01 February 2022; Accepted: 25 May 2022;
Published: 28 June 2022.
Edited by:
Muhammad Wakil Shahzad, Northumbria University, United KingdomReviewed by:
Muhammad Ahmad Jamil, Northumbria University, United KingdomChi Zhang, Wuyi University, China
Fahad Noor, University of Engineering and Technology, Lahore, Pakistan
Copyright © 2022 Hardy, Kulkarni, Stevenson and Marina. This is an open-access article distributed under the terms of the Creative Commons Attribution License (CC BY). The use, distribution or reproduction in other forums is permitted, provided the original author(s) and the copyright owner(s) are credited and that the original publication in this journal is cited, in accordance with accepted academic practice. No use, distribution or reproduction is permitted which does not comply with these terms.
*Correspondence: John S. Hardy, am9obi5oYXJkeUBwbm5sLmdvdg==