- 1Consiglio per la Ricerca in Agricoltura e l’analisi dell’Economia Agraria (CREA)-Centro di Ricerca Ingegneria e Trasformazioni Agroalimentari, Monterotondo, Italy
- 2ENEA Centro Ricerche Trisaia, Rotondella, Italy
- 3NOVAMONT SpA, Novara, Italy
Inulin is accumulated as a reserve carbohydrate in the roots and tubers of many plants belonging to the Asteraceae family. At present, most of the inulin for nutraceutical purposes is produced from Jerusalem artichoke (Helianthus tuberosus L.) and Chicory (Cichorium intybus L.), and cardoon is proved to synthetize and store a high quantity of inulin in roots. Inulin in the roots of cardoon reaches the maximum content before the beginning of flowers formation in May. Due to the limited favorable period for harvesting the roots, storage plays a key role in the supply chain. The complete drying of cardoon roots before the storage has been proved to prevent the degradation of inulin up to 6 months of storage. Because drying is a costly operation, in the present study, energy-saving and the effect on percentage inulin content in cardoon roots dried at different moisture contents before storage were assessed. From 48.2% inulin retrievable at the beginning of the investigated period (100% dry matter), after 1 month of storage, about 2% reduction was recorded on average in H0 and H12.5 treatments, while about 10% reduction was shown (with no statistical differences) in treatments at higher moisture contents (TQ, H50, and H25). These values remained constant until the end of storage, except for TQ treatment, where inulin content decreased progressively up to 38.7% w/w. From an economic point of view, limiting the drying time and storing roots at a moisture content higher than 0% leads to an income loss of 2,000–3,000 €/t of roots. Therefore, full drying is the most cost-effective solution in the optic of producing the highest possible amount of inulin and could be avoided just in the case of immediate roots extraction and processing in a few days.
Introduction
One of the most important issues in the bioeconomy concept is producing biomaterials from sustainable and renewable feedstocks (von Cossel, 2020; Pędzik et al., 2021; Kahar et al., 2022). In this optic, industrial crops, better if multipurpose ones, represent an interesting solution (Cossel et al., 2019; Panoutsou and Alexopoulou, 2020).
Among these crops, Cardoon (Cynara cardunculus L.) properly represents a promising resource to produce biomaterials and biobased molecules because it offers a wide spectrum of potential applications (Fernández et al., 2006; Barracosa et al., 2019; Caporusso et al., 2021). Cynara cardunculus L. is common in central-southern Italy and generally in the regions bordering the Mediterranean Sea. This perennial crop has shown suitability to grow on marginal, drought soils and requires minimal nutrients (Raccuia and Melilli, 2004; Crognale et al., 2019; Von Cossel et al., 2019; Galletti et al., 2021). Because several molecules with a high added value could be obtained from the whole cardoon, the use of this crop finds an advantageous use in a biorefinery approach. In fact, oils are produced from the seeds for food, bioplastics, and biodiesel supply chains (Cabiddu et al., 2019; Mirpoor et al., 2021). However, after pretreatment of the lignocellulosic stems, carbohydrates could be enzymatically valorized and other chemicals could be obtained from lignin depolymerization processes (Liuzzi et al., 2019; Di Fidio et al., 2021). Last but not least, the roots are rich in inulin, valuable by-products obtained at the end of the crop cycle (Zayed et al., 2020).
Cardoon is a perennial species with an annual growth cycle, and more than ten-year-old crops have been reported in the literature (Gominho et al., 2018). However, decreased yields in biomass and seeds from the sixth year onward are reported (Angelini et al., 2009). Therefore, the exploitation of Cardoon seeds and lignocellulosic stems is indicated for medium long-time cropping systems until the fifth season (Mauromicale et al., 2014). On the contrary, considering that the removal of the root is a costly and necessary operation, the extraction of inulin is a useful option at the end of the productive cycle.
Inulin is a reserve carbohydrate accumulated in the roots and tubers of many plants belonging mainly to the Asteraceae family, including Cardoon (Cynara cardunculus L.). At present, most of the inulin for nutraceutical purposes is produced from Jerusalem artichoke (Helianthus tuberosus L.) and Chicory (Cichorium intybus L.) (Lattanzio et al., 2009; Ramos et al., 2014; Malik and Rehman, 2021). In detail, inulin is an oligosaccharide, a polymer of β-D-fructose, with β-1,2-glycosidic bonds. The level of polymerization (DP) of standard inulin varies from 2 to 100 depending on species, harvesting time, or extraction processes (Li et al., 2015). Due to the β (2,1) bonds, inulin is generally not digested by the human body and is therefore used to increase dietary fiber and prebiotic activities. Thanks to these characteristics, these fibers allow regulating the metabolism of glucose, lipids, and cholesterol (Kalyani Nair et al., 2010). Inulin can also be chemically or enzymatically hydrolyzed to fructose. By dehydration, fructose produces 5-HMF, one of the most coveted monomers in green chemistry, as a precursor of numerous molecules with high added value that can be used as plasticizers in the pharmaceutical field and polymers in general (Hanover and White, 1993; Lima et al., 2011; Dibenedetto et al., 2015).
The amount of inulin in cardoon species varies depending on the seasonality of the harvest and the age of the crop. The normal of the genotypes comes to up to around 400 g of sugars per kg of the dry root, and more than 80% is inulin (Raccuia and Melilli, 2010). Inulin reaches its maximum in cardoon roots in spring, particularly between full blossom and fruit ripening. It peaks in May, while the inulin content at the seed harvesting phase, usually in August, comes down to about one-fifth of its peak value (Raccuia and Melilli, 2010). Therefore, storage plays a key role in supply chain as industries need to harvest and store cardoon roots during a limited favorable period.
Frozen storage (−18°C) has been demonstrated to maintain the stability of the inulin content and composition in tubers and roots of different crops containing inulin during long-term storage. On the contrary, storage of Jerusalem artichoke tubers performed at 4°C caused significant degradation of inulin to soluble sugars after 4 weeks (Saengthongpinit and Sajjaanantakul, 2005), while during storage at ambient temperature, a significant decrease in inulin content occurred just at the 15th day of storage (Maicaurkaew et al., 2017).
Moreover, it has been proven that, in addition to temperature, moisture allows microorganisms to start the degradation of the sugar-based component of dry matter, including inulin, to carry out their metabolism (Löhmar and Theurillat, 2003). In this framework, artificial drying technologies are gaining interest for storage purposes.
While freezing is an effective storage approach, it is a costly process. On the contrary, artificial drying can reduce the overall costs of the supply chain. The machinery required for drying is easier to run and cheaper to buy (e.g., ventilated ovens), with an enormous advantage for the transportation that does not require a longer ice chain (Chung et al., 2008; Mujumdar and Law, 2010).
Drying is considered the easiest way to preserve biomass for food and non-food applications (Chua et al., 2019; Yu et al., 2021). Obviously, the lower the moisture reached after drying, the lower the possibility of product loss during storage (Kurozawa et al., 2012). On the contrary, it is needed to reach 0% of moisture for proper product conservation (not in all cases) (Chen et al., 2021).
Considering what was written above, the drying process performed before the storage of cardoon roots has been recently investigated. The complete drying of cardoon roots before storage has been proved to prevent the degradation of inulin at least up to 6 months of storage (Pari et al., 2021). Moreover, chipping before drying did not affect the inulin content during the storage. Furthermore, chipping reduced the time needed for drying by 33.3%, with a consequent reduction in the direct cost of drying (Pari et al., 2021).
However, the influence of cardoon roots artificial drying has not been widely investigated. In detail, there is missing information regarding the balance between the time of roots drying and the cost of the process. Indeed, previous research highlighted that complete drying of cardoon roots is an effective way to conserve inulin. However, there is no information regarding the effectiveness of partial drying and an economic balance between drying cost, residual moisture of the roots after drying, and final inulin content.
Considering the current lack of knowledge on this particular topic, the present study, developed within the Italian Project Cometa-Autoctone Mediterranean crops and their valorization with advanced green chemistry technologies (funded by the Ministry of Education, Universities and Research), was addressed to identify the threshold of moisture for storing cardoon roots without a significant loss in inulin content, in order to reduce the drying time, the energy required, and its costs.
Authors hypothesized that complete drying is not the most cost-effective alternative and that stopping the drying process before full drying can lead to increased earn for the industry thanks to the reduced energy costs of artificial drying.
Materials and Methods
Plant Material: Cultivation and Root Sampling
Cardoon plants were grown in an open experimental field in Maccarese (Fiumicino, Lazio, Italy) (WGS84-UTM33T coordinate 271167 E, 4633933 N; 0 m a.s.l.). The soil was classified as silty clay loam soil. Plants had been grown from seeds, and sowing took place in February 2019 at the rate of 3 kg/ha via a pneumatic drill. At the sowing, the intra- and inter-row spacing was 0.18 × 0.75 m, approximately eight seeds per square meter. Fertilization was applied in February 2020, providing 160 kg/ha of slow-release nitrogen fertilizer (corresponding to 73 N-unit per hectare). Application of pendimethalin and mechanical weed management was carried out in March and May 2019, respectively.
In April 2021, roots from 50 randomly chosen plants were manually uprooted, put in sealed bags, and brought to the laboratory of the Research Centre for Engineering and Agro-Food Processing of the Council for agricultural research and economics (CREA) in Monterotondo, Central Italy (42 10019″ N latitude 12 62066″ E longitude) for sampling. Roots were cleaned from the residual soil and sampled for fresh weight, dry weight, and residual moisture content assessment (EN ISO 18134-2:2017, 2017).
Chipping, Drying, and Storage
After cleaning, roots were fresh chipped using an electric 2.0 kW bio-shredder (Zanon, mod. BIO 3). About 10 kg of the chipped material was divided into five samples (treatments) to monitor inulin and dry matter content during 6-month storage. The first sample was made of undried chipped roots (TQ treatment), with the initial humidity (Hi), as received. The other four samples were put into a thermo-ventilated oven (Memmert, mod. 100–800) for drying at 60°C until they reached the target humidity (Ht), respectively: 50%, 25%, 12.5%, and 0%. For doing this, the weight of the samples was monitored until reaching the respective target weight (Wt). Wt was obtained from the following equation:
where Wi and Hi were, respectively, the initial weight and the initial humidity of the samples before drying and Wt and Ht were the target weight and the target humidity.
At each weighing, the electricity consumption of the oven was recorded with an electricity meter (ORNO, mod.OR-WE-520) to identify the relations between the loss of humidity, the drying time, and the energy consumption. When the samples (treatments) achieved the target weight, they were removed from the oven and were collocated in the storage site. Each treatment was divided into eight subsamples, then weighed, and labeled (replicates).
An indoor and not artificially heated site was chosen for the storage. During the entire storage period of 6 months, temperature and air humidity inside the storage site were recorded with a thermometer-hygrometer (GOVEE, mod. H5075) (temperature accuracy: ±0.3°C, humidity accuracy: ±3%) located in the proximity of the samples. Data recorded are shown in Figure 1.
Monthly, approximately 200 g of each treatment were sent to the ENEA laboratory for inulin determination, while a representative subsample from each treatment was kept for dry matter assessment.
Dry Matter and Inulin Content Determination
Monthly, the dry matter content (% w/w) of three replicates for each treatment was assessed according to
where Wm and Hm were, respectively, the weight and the humidity achieved from month 1 (M1) to month 6 (M6), while W0 and Ht were the values at the beginning of the storage (M0). Regarding inulin, the monthly collected samples were ground by a Retsch Zm200 Ultracentrifugal Mill (Retsch GmbH and Co. KG, Haan, Germany), with a 0.5 mm sieve, and stored in a dryer until the extraction procedure.
Before the extraction of the inulin, the determination of the ashes was carried out to avoid errors in the calculation of the extraction yield due to the residual inorganic soil not completely removed, although the roots have been thoroughly washed after harvesting. The ashes content was measured by organic-matter overnight degradation in a muffle furnace at 540°C, and the results were between 9.5% and 16.1%. These values were used to calculate the initial organic matter for each sample.
The inulin was extracted in demineralized water in a 5% (s/L) ratio suspension. In particular, for each sample, 50 ml flasks containing the suspension were stirred at 500 rpm in a Benchmark Scientific (South Plainfield, NJ, United States) Multi-Therm Heat-Shake at 100°C for 1 h (Raccuia et al., 2016).
After the extraction step, acid hydrolysis followed to convert the inulin and fructo-oligosaccharides into fructose. This procedure was clearly detailed in the previous work (Pari et al., 2021).
HPIC DX 300 chromatographic system (Dionex, Sunnyvale, CA, United States) was coupled with a Shodex RI101 refractive index (Showa Denko, Japan). A Nucleogel® Ion 300 OA column (Macherey–Nagel, Düren, Germany) was used with sulphuric acid 10 mN as eluent. The sample was pre-filtered with a 0.45 µm membrane before injection. The volume of the sample injected was 100 μL. The flow rate was set at 0.4 ml/min, and the temperature of the column was set at 60°C. D-fructose with a purity of 99% was purchased from Sigma-Aldrich (St. Louis, MO, United States) and used as standard. Calibration curves were obtained by preparing five fructose concentrations in water ranging from 0.2 to 1.0 mg/ml. The extraction and hydrolysis processes were conducted in triplicate for each sample.
The inulin content % was determined as solubilized monomers after extraction and hydrolysis process per 100 g of organic substance subjected to the process (Pari et al., 2021).
Economic Analysis
An economic quantification of energy-saving achievable by reducing the drying times from a side and the corresponding income achievable from the amount of inulin maintained in the different treatments during storage was performed.
A net income loss index was built as a difference between the potential income achievable per treatment (lower cost for drying) and the net income in the case of complete drying (more inulin expected).
The price of electricity was taken as 0.2 €/kWh averaging the values provided by the Italian Regulatory Authority for Energy, Networks and Environment (ARERA) in the last 5 years (https://www.arera.it/it/dati/eep35.htm#).
On the contrary, 30.10 €/kg was the economic value of inulin assumed by referring to the cost of pure inulin extracted from Jerusalem artichoke tubers (Kriukova et al., 2018).
Statistical Analysis
Statistical analysis was performed to assess significant differences among the mean values of dry matter, inulin content, and the net income loss index. A two factorial designs were considered with variation factors: five humidity classes (TQ, H50, H25, H12.5, H0) and six storage periods (from M1 to M6). The normality of the data was previously measured by the Shapiro–Wilk test (p < 0.05). The sphericity of data was checked with the Mauchly test. Thus, the effect of the various factors was observed after the repeated measures analysis of variance (ANOVA). Being the assumption of sphericity rejected by the dedicated test, the results of the repeated measures ANOVA were corrected by applying the Greenhouse–Geisser correction. Bonferroni mean test (p < 0.05) was applied as a post hoc test. All data were analyzed in the R statistical software environment (R Development Core Team, 2017).
Results and Discussions
Biomass Availability, Drying Process, and Energy Consumption
The assessed potential harvestable biomass from cardoon roots was 17.2 tdm/ha after 2 years of cultivation. This result is higher than what is presented in the current literature. Raccuia and Melilli (2010) reported 9.8 tdm/ha (Raccuia and Melilli, 2010), while Pari et al. (2021) found a harvestable roots biomass of 10.6 tdm/ha (Pari et al., 2021).
Focusing on the average weight of roots, the value obtained in the present trial was 0.23 ± 0.17 kgdm with a moisture content of 66.6% w/w. Data from literature reported 0.14 kgdm for Pari et al. (2021), while a higher value of about 0.37 kgdm was reported by Raccuia and Melilli (2010).
Therefore, the difference in roots biomass yield between the present study and the ones previously carried out on a similar topic may have a double explanation. The yield of Raccuia and Melilli (2010) was probably influenced by the lower plant density, which was three-time lower than the one of the present study. Instead, the difference with Pari et al. (2021), considering that both trials have a similar plant density, is probably related to some differences in the growing conditions (climate, fertilization, etc.), whose evaluation is outside the scope of this manuscript. However, future trials are needed to have more and more reliable data on cardoon roots biomass for inulin production. These data would indeed be fundamental for designing an efficient value chain.
By dealing with roots moisture, the obtained data are instead consistent with literature ones, considering that Pari et al. (2021) reported a moisture content of 70% w/w in line with the 66.6% w/w value of the present trial.
Data on the process of biomass drying are reported in Figure 2. As it is possible to notice, the residual moisture content in chipped roots of cardoon reached 50%, 25%, 12.5%, and 0% after 6, 16, 21, and 26 h of ventilation at constant 60°C. On the contrary, energy consumption increased over time, from 4.34 kWh in H50 to 13.84 kWh in H0 following a linear equation (R2 0.9861).
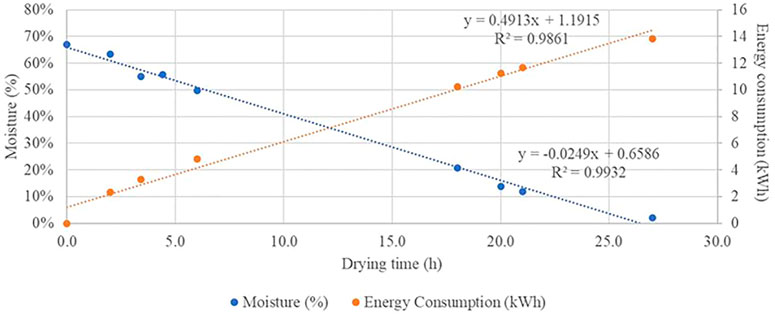
FIGURE 2. Energy consumption (orange) and moisture content (blue) during the cardoon roots drying process.
The energy consumption to fully dry 1 kg of roots was 1.52 kWh/kg, which, considering the biomass yield of 51.4 tfm/ha, corresponds to 78.13 MWh/ha.
Such results should be utilized, keeping in mind that they refer to the lab-scale oven, where ideal conditions are guaranteed, such as optimal air circulation and homogeneous biomass drying. Therefore, if these ideal conditions are also maintained on an industrial scale, the energy spent to dried biomass ratio found on a small scale can also be applied to the industrial scale. Further investigation on a larger-scale trial is needed to confirm this hypothesis.
Effect of Storage on Dry Matter and Inulin Content
During the first month of storage (M1), a significant reduction (p < 0.01 according to the results of Repeated measures ANOVA) in dry matter content was recorded in all the treatments. At M1, the loss of dry matter was just 1.4% in the H0 treatment, while it was higher than 15% in the not fully dried treatments (Figure 3).
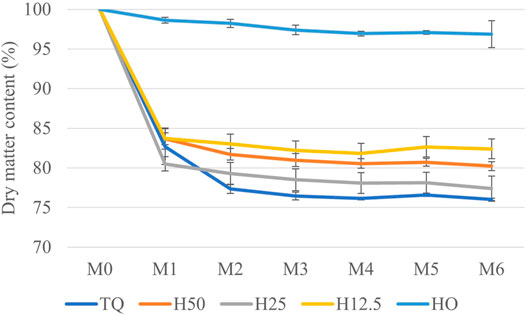
FIGURE 3. Dry matter content in the treatments (TQ, H50, H25, H12.5, and H0) during storage, from M0 (April) to M6 (October).
The dry matter content remained constant during the following months in all the treatments, except for a significant reduction in month 2 in TQ. This behavior was justified by the natural drying of the samples. During the first month of storage, the moisture content reached about 10% in all the treatments, except for the TQ treatment, reaching it in month 2. Such value of moisture content, maintained during the following months, is generally thought to be low enough to prevent microbial degradation (Towey et al., 2019).
From these results, it is possible to highlight the first major outcome of this study. In other words, in the condition of indoor storage of cardoon roots, the dry matter loss is concentrated in the first one maximum 2 months for each initial moisture of biomass. These findings are in line with the results of a study on storage of different biomass (i.e., corn stover) at different moisture contents, which reported that the great major part of dry matter loss is concentrated in the first month of storage for moisture lower than 40%, while in the first 2 months for biomass with moisture higher than 50% (Smith et al., 2020).
At the end of storage (M6), the dry matter loss was about 3% in the H0 treatment, 18% in H12.5, and 22% on average (with no statistical differences) in TQ, H50, and H25 treatments. Despite the substantial loss of dry matter in the not fully dried treatments, the indoor conditions still ensured better storage with respect to the losses that normally occur in the open-air storage of biomass (Lenz et al., 2016; Whittaker et al., 2016; Pari et al., 2017). Focusing on the effects of storage in inulin content, repeated measures ANOVA highlighted the presence of statistically significant differences among the treatments (p < 0.01) for percentage inulin content in cardoon roots. In detail, at the beginning of storage (April), the inulin content was 48.2 ± 0.6 w/w. A similar value (47.1 ± 1.30% w/w) was found in cardoon roots harvested 1 month later (May) in the trial performed in 2020 (Pari et al., 2021). After 1 month of storage, about 2% reduction was recorded on average (with no statistical differences) in H0 and H12.5 treatments. In contrast, about a 10% reduction was shown (with no statistical differences) in treatments at higher moisture contents (TQ, H50, and H25). These values remained constant until the end of storage, except for TQ treatment, where inulin content decreased progressively up to 38.7% w/w. The data represented in Figure 4 show that limiting the drying at 12.5% does not lead to a significant reduction of percentage inulin content. This represents the second major finding of the present study. Moreover, as happened for dry matter loss, percentage inulin loss is also concentrated in the first month, except for the TQ treatment, where the loss is progressive over time.
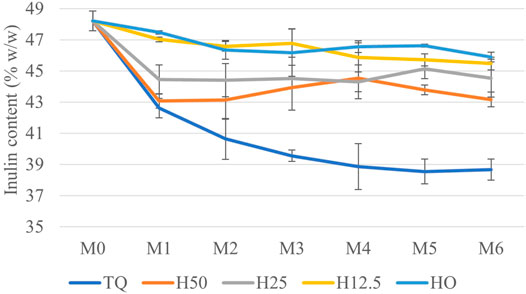
FIGURE 4. Inulin content in the treatments (TQ, H50, H25, H12.5, and H0) during storage, from M0 (April) to M6 (October).
In contrast, in terms of the potential quantity of inulin retrievable from the roots of cardoon, given by the inulin contained in the dry matter preserved during the storage (inulin content × dry matter content), only the complete drying allowed retrieving almost entirely the initial content, while the other treatments showed statistically significant negative differences (p < 0.01 according to repeated measures ANOVA). From 48.2% inulin retrievable at the beginning of storage (100% dry matter), after 1 month, about 2% significant reduction occurred in H0 treatment, about 9% in H12.5 treatment, and about 12% in the treatments at higher moisture contents (Figure 5).
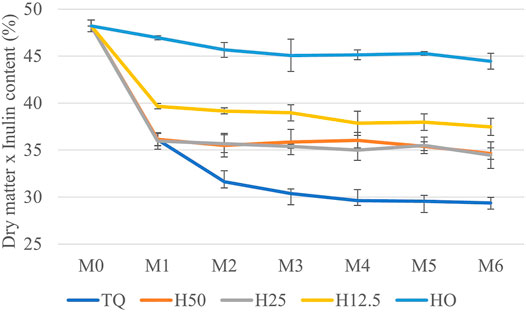
FIGURE 5. Inulin retrievable from the roots of cardoon (dry matter content x inulin content) in the treatments (TQ, H50, H25, H12.5, and H0) during storage, from M0 (April) to M6 (October).
According to these results, it is possible to suggest that if the roots are processed within 1 month of storage, in the case, the industry will accept 12% inulin loss, the roots do not need any drying, while from the second month onward, it is sufficient to dry up to 50%, achieving the corresponding energy saving. On the contrary, if the industry is interested in recovering the maximum amount of inulin, renouncing any energy-saving, roots should be completely dried before storage because H0 was the only treatment able to maintain almost the total amount of retrievable inulin. Obviously, all these considerations are related to the economic balance between energy-saving and the cost of inulin loss in the various drying scenarios, as presented in the following part of the manuscript.
Economic Analysis
Analyzing the obtained results from the economic point of view, it is evident that energy-saving achievable by reducing the drying times does not compensate for the loss of potential income linked to the inulin loss during storage. Therefore, the hypothesis that full drying is not the most cost-effective alternative is rejected.
On average, the net income loss with respect to the complete drying ranges from 2,000 € to 4,000 € per ton of roots, respectively, in the case of drying until 12.5% and no drying (Figure 6). Limiting the analysis at the first month (considering that this is the period in which there is a great major part of product loss), the income loss ranges between 2,000 €/t in H12.5 treatment and 3,000 €/t on average in TQ, H50, and H25 treatments. This outcome is mostly related to the very high price of inulin (30.1 €/kg), which leads to the need to try preserving the maximum possible amount of this carbohydrate.
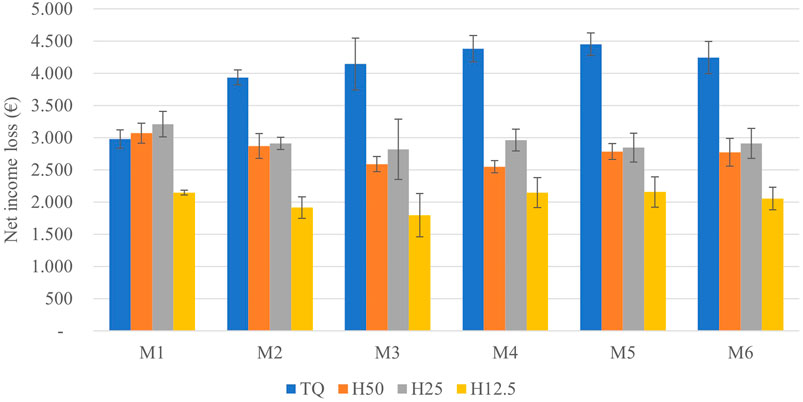
FIGURE 6. Net income loss (€) during the storage of 1 ton of roots per treatment with respect to H0 treatment.
These results suggest two possible alternative management strategies for developing a value chain of inulin production from cardoon roots. In the case the biorefinery can process all the biomass obtainable from the fields (between 9 and 17 tdm/ha of roots) in a very short time, i.e. some days, the storage phase could be avoided. Thus, simplifying the industrial process also limits some additional costs (biomass handling and purchasing of the instruments for drying). In the case storage is needed, drying is a suitable alternative to preserve inulin, but the process has to be fully applied, allowing the roots to reach 0% moisture.
Conclusion
Processing the whole crop to obtain useful products meets the sustainability goals of the circular bioeconomy. In this framework, the exploitation of cardoon roots for inulin production at the end of the crop cycle, after the exploitation of seeds and stalks for the production of further high added-value raw materials, is a very interesting option.
Inulin content in cardoon roots peaks just before flower formation. Therefore, storage is an important step because industries need to harvest and store many roots in a limited favorable period.
The obtained findings suggest that the complete drying of roots before the storage preserves the inulin content for up to 6 months of storage. Reducing the drying time and storing roots with higher initial moisture contents determined a significant loss of the retrievable inulin. Energy-saving by the reduction of the drying time did not compensate for the potential income loss for the reduction of obtainable inulin.
In the case the biorefinery would be able to process all the biomass in a few days, drying and storage could be avoided. However, in the case a storage operation would be necessary, drying should be carried out until 0% residual moisture in roots to save the highest amount of inulin.
From the perspective of the biorefinery approach, it would be interesting to make an overview of the mass balances and economics of the different useful products obtainable from the whole cardoon. Depending on many factors related to industrial processes adopted along the value chain and the market prices of non-conventional raw materials, such analysis should be performed in a future dedicated study.
Data Availability Statement
The original contributions presented in the study are included in the article/Supplementary Material, further inquiries can be directed to the corresponding author.
Author Contributions
VA, WS, and FLa designed the research objective. VA and FLi wrote the draft manuscript. VA, WS, and FLa performed data analysis and revised the manuscript. FLi and EV performed laboratory analysis. AC revised the manuscript. LP and ID acquired funding and supervised the research. All authors read and approved the final manuscript.
Funding
This research was performed within the Italian Project COMETA-Autoctone Mediterranean crops and their valorization with advanced green chemistry Technologies and supported by the European project “BeCool” (grant agreement No. 744821), financed by the EU H2020 programme.
Conflict of Interest
The authors declare that the research was conducted in the absence of any commercial or financial relationships that could be construed as a potential conflict of interest.
Publisher’s Note
All claims expressed in this article are solely those of the authors and do not necessarily represent those of their affiliated organizations or those of the publisher, the editors, and the reviewers. Any product that may be evaluated in this article, or claim that may be made by its manufacturer, is not guaranteed or endorsed by the publisher.
References
Angelini, L. G., Ceccarini, L., Nassi o Di Nasso, N., and Bonari, E. (2009). Long-term Evaluation of Biomass Production and Quality of Two Cardoon (Cynara Cardunculus L.) Cultivars for Energy Use. Biomass and Bioenergy 33, 810–816. doi:10.1016/j.biombioe.2008.12.004
Barracosa, P., Barracosa, M., and Pires, E. (2019). Cardoon as a Sustainable Crop for Biomass and Bioactive Compounds Production. Chem. Biodiversity 16, e1900498. doi:10.1002/cbdv.201900498
Cabiddu, A., Contini, S., Gallo, A., Lucini, L., Bani, P., Decandia, M., et al. (2019). In Vitro fermentation of Cardoon Seed Press Cake - A Valuable Byproduct from Biorefinery as a Novel Supplement for Small Ruminants. Ind. Crops Prod. 130, 420–427. doi:10.1016/J.INDCROP.2018.12.095
Caporusso, A., De Bari, I., Valerio, V., Albergo, R., and Liuzzi, F. (2021). Conversion of Cardoon Crop Residues into Single Cell Oils by Lipomyces Tetrasporus and Cutaneotrichosporon Curvatus: Process Optimizations to Overcome the Microbial Inhibition of Lignocellulosic Hydrolysates. Ind. Crops Prod. 159, 113030. doi:10.1016/j.indcrop.2020.113030
Chen, C., Liao, C., Wongso, I., Wang, W., Khir, R., Huang, G., et al. (2021). Drying and Disinfection of Off-Ground Harvested Almonds Using Step-Down Temperature Hot Air Heating. LWT 152, 112282. doi:10.1016/J.LWT.2021.112282
Chua, L. Y. W., Chong, C. H., Chua, B. L., and Figiel, A. (2019). Influence of Drying Methods on the Antibacterial, Antioxidant and Essential Oil Volatile Composition of Herbs: a Review. Food Bioproc. Technol 12, 450–476. doi:10.1007/S11947-018-2227-X
Chung, L. L., Waje, S. S., Thorat, B. N., and Mujumdar, A. S. (2008). Advances and Recent Developments in thermal Drying for Bio-Origin and Agricultural Products. Stewart Postharvest Rev. 4, 1–23. doi:10.2212/spr.2008.1.1
Cossel, M. (2020). Renewable Energy from Wildflowers-Perennial Wild Plant Mixtures as a Social‐Ecologically Sustainable Biomass Supply System. Adv. Sust. Syst. 4, 2000037. doi:10.1002/ADSU.202000037
Crognale, S., Liuzzi, F., D'Annibale, A., de Bari, I., and Petruccioli, M. (2019). Cynara Cardunculus a Novel Substrate for Solid-State Production of Aspergillus tubingensis Cellulases and Sugar Hydrolysates. Biomass and Bioenergy 127, 105276. doi:10.1016/J.BIOMBIOE.2019.105276
Di Fidio, N., Timmermans, J. W., Antonetti, C., Raspolli Galletti, A. M., Gosselink, R. J. A., Bisselink, R. J. M., et al. (2021). Electro-oxidative Depolymerisation of Technical Lignin in Water Using Platinum, Nickel Oxide Hydroxide and Graphite Electrodes. New J. Chem. 45, 9647–9657. doi:10.1039/D1NJ01037A
Dibenedetto, A., Aresta, M., Pastore, C., Di Bitonto, L., Angelini, A., and Quaranta, E. (2015). Conversion of Fructose into 5-HMF: A Study on the Behaviour of Heterogeneous Cerium-Based Catalysts and Their Stability in Aqueous media under Mild Conditions. RSC Adv. 5, 26941–26948. doi:10.1039/C5RA03358F
EN ISO 18134-2:2017 (2017). Solid Biofuels - Determination of Moisture Content - Oven Dry Method - Part 2: Total Moisture - Simplified Method (ISO 18134-2:2017).
Fernández, J., Curt, M. D., and Aguado, P. L. (2006). Industrial Applications of Cynara Cardunculus L. For Energy and Other Uses. Ind. Crops Prod. 24, 222–229. doi:10.1016/j.indcrop.2006.06.010
Gominho, J., Curt, M. D., Lourenço, A., Fernández, J., and Pereira, H. (2018). Cynara Cardunculus L. As a Biomass and Multi-Purpose Crop: A Review of 30 Years of Research. Biomass and Bioenergy 109, 257–275. doi:10.1016/j.biombioe.2018.01.001
Hanover, L. M., and White, J. S. (1993). Manufacturing, Composition, and Applications of Fructose. Am. J. Clin. Nutr. 58, 724S–732S. doi:10.1093/AJCN/58.5.724S
Kahar, P., Rachmadona, N., Pangestu, R., Palar, R., Triyono Nugroho Adi, D., Betha Juanssilfero, A., et al. (2022). An Integrated Biorefinery Strategy for the Utilization of palm-oil Wastes. Bioresour. Tech. 344, 126266. doi:10.1016/J.BIORTECH.2021.126266
Kalyani Nair, K., Kharb, S., and Thompkinson, D. K. (2010). Inulin Dietary Fiber with Functional and Health Attributes-A Review. Food Rev. Int. 26, 189–203. doi:10.1080/87559121003590664
Kriukova, Y., Jakubiak-Augustyn, A., Ilyinska, N., Krotkiewski, H., Gontova, T., Evtifeyeva, O., et al. (2018). Chain Length Distribution of Inulin from Dahlia Tubers as Influenced by the Extraction Method. Int. J. Food Properties 20, S3112–S3122. doi:10.1080/10942912.2017.1357043
Kurozawa, L. E., Hubinger, M. D., and Park, K. J. (2012). Glass Transition Phenomenon on Shrinkage of Papaya during Convective Drying. J. Food Eng. 108, 43–50. doi:10.1016/J.JFOODENG.2011.07.033
Lattanzio, V., Kroon, P. A., Linsalata, V., and Cardinali, A. (2009). Globe Artichoke: A Functional Food and Source of Nutraceutical Ingredients. J. Funct. Foods 1, 131–144. doi:10.1016/J.JFF.2009.01.002
Lenz, H., Pecenka, R., Hartung, E., and Idler, C. (2016). Development and Test of a Simplified Method to Calculate Dry Matter Loss during Open-Air Storage of poplar wood Chips by Analysing Ash Contents. Biomass and Bioenergy 94, 258–267. doi:10.1016/J.BIOMBIOE.2016.09.011
Li, W., Zhang, J., Yu, C., Li, Q., Dong, F., Wang, G., et al. (2015). Extraction, Degree of Polymerization Determination and Prebiotic Effect Evaluation of Inulin from Jerusalem Artichoke. Carbohydr. Polym. 121, 315–319. doi:10.1016/J.CARBPOL.2014.12.055
Lima, D. M., Fernandes, P., Nascimento, D. S., Ribeiro, R., and Assis, S. A. (2011). Fructose Syrup: A Biotechnology Asset. Croatia: Faculty of Food Technology and Biotechnology.
Liuzzi, F., Mastrolitti, S., and De Bari, I. (2019). Hydrolysis of Corn Stover by Talaromyces cellulolyticus Enzymes: Evaluation of the Residual Enzymes Activities through the Process. Appl. Biochem. Biotechnol. 188, 690–705. doi:10.1007/S12010-018-02946-3
Löhmar, K., and Theurillat, V. (2003). “CHICORY BEVERAGES,” in Encyclopedia of Food Sciences and Nutrition (Elsevier), 1144–1149. doi:10.1016/b0-12-227055-x/00210-8
Maicaurkaew, S., Jogloy, S., Hamaker, B. R., and Ningsanond, S. (2017). Fructan:fructan 1-fructosyltransferase and Inulin Hydrolase Activities Relating to Inulin and Soluble Sugars in Jerusalem Artichoke (Helianthus Tuberosus Linn.) Tubers during Storage. J. Food Sci. Technol. 54, 698–706. doi:10.1007/s13197-017-2508-9
Malik, B., and Rehman, R. U. (2021). Chicory Inulin: A Versatile Biopolymer with Nutritional and Therapeutic Properties. Med. Aromat. Plants, 373–390. doi:10.1007/978-3-030-58975-2_16
Mauromicale, G., Sortino, O., Pesce, G. R., Agnello, M., and Mauro, R. P. (2014). Suitability of Cultivated and Wild Cardoon as a Sustainable Bioenergy Crop for Low Input Cultivation in Low Quality Mediterranean Soils. Ind. Crops Prod. 57, 82–89. doi:10.1016/j.indcrop.2014.03.013
Mirpoor, S. F., Giosafatto, C. V. L., and Porta, R. (2021). Biorefining of Seed Oil Cakes as Industrial Co-streams for Production of Innovative Bioplastics. A Review. Trends Food Sci. Tech. 109, 259–270. doi:10.1016/J.TIFS.2021.01.014
Mujumdar, A. S., and Law, C. L. (2010). Drying Technology: Trends and Applications in Postharvest Processing. Food Bioproc. Technol 3, 843–852. doi:10.1007/s11947-010-0353-1
Panoutsou, C., and Alexopoulou, E. (2020). Costs and Profitability of Crops for Bioeconomy in the EU. Energies 13, 1222. Page 1222 13. doi:10.3390/EN13051222
Pari, L., Scarfone, A., Santangelo, E., Gallucci, F., Spinelli, R., Jirjis, R., et al. (2017). Long Term Storage of poplar Chips in Mediterranean Environment. Biomass and Bioenergy 107, 1–7. doi:10.1016/j.biombioe.2017.09.007
Pari, L., Alfano, V., Stefanoni, W., Latterini, F., Liuzzi, F., De Bari, I., et al. (2021). Inulin Content in Chipped and Whole Roots of Cardoon after Six Months Storage under Natural Conditions. Sustainability 202113, 3902. Page 3902 13. doi:10.3390/SU13073902
Pędzik, M., Janiszewska, D., and Rogoziński, T. (2021). Alternative Lignocellulosic Raw Materials in Particleboard Production: A Review. Ind. Crops Prod. 174, 114162. doi:10.1016/J.INDCROP.2021.114162
Raccuia, S. A., Genovese, C., Leonardi, C., Bognanni, R., Platania, C., Calderaro, P., et al. (2016). Fructose Production by Cynara Cardunculus Inulin Hydrolysis. Acta Hortic. 1147, 309–314. doi:10.17660/ACTAHORTIC.2016.1147.43
Raccuia, S. A., and Melilli, M. G. (2004). Cynara Cardunculus L., a Potential Source of Inulin in the Mediterranean Environment: Screening of Genetic Variability. Aust. J. Agric. Res. 55, 693. doi:10.1071/AR03038
Raccuia, S. A., and Melilli, M. G. (2010). Seasonal Dynamics of Biomass, Inulin, and Water-Soluble Sugars in Roots of Cynara Cardunculus L. Field Crops Res. 116, 147–153. doi:10.1016/j.fcr.2009.12.005
Ramos, P. A. B., Santos, S. A. O., Guerra, Â. R., Guerreiro, O., Freire, C. S. R., Rocha, S. M., et al. (2014). Phenolic Composition and Antioxidant Activity of Different Morphological Parts of Cynara Cardunculus L. Var. Altilis (DC). Ind. Crops Prod. 61, 460–471. doi:10.1016/j.indcrop.2014.07.042
Raspolli Galletti, A. M., Licursi, D., Ciorba, S., Di Fidio, N., Coccia, V., Cotana, F., et al. (2021). Sustainable Exploitation of Residual Cynara Cardunculus L. To Levulinic Acid and N-Butyl Levulinate. Catalysts 202111, 1082. Page 1082 11. doi:10.3390/CATAL11091082
Saengthongpinit, W., and Sajjaanantakul, T. (2005). Influence of Harvest Time and Storage Temperature on Characteristics of Inulin from Jerusalem Artichoke (Helianthus Tuberosus L.) Tubers. Postharvest Biol. Tech. 37, 93–100. doi:10.1016/j.postharvbio.2005.03.004
Smith, W. A., Wendt, L. M., Bonner, I. J., and Murphy, J. A. (2020). Effects of Storage Moisture Content on Corn Stover Biomass Stability, Composition, and Conversion Efficacy. Front. Bioeng. Biotechnol. 8, 1–11. doi:10.3389/fbioe.2020.00716
Towey, R., Webster, K., and Darr, M. (2019). Influence of Storage Moisture and Temperature on Lignocellulosic Degradation. AgriEngineering 1, 332–342. doi:10.3390/agriengineering1030025
Von Cossel, M., Lewandowski, I., Elbersen, B., Staritsky, I., Van Eupen, M., Iqbal, Y., et al. (2019). Marginal Agricultural Land Low-Input Systems for Biomass Production. Energies 12, 3123. doi:10.3390/EN12163123
Von Cossel, M. Von., Wagner, M., Lask, J., Magenau, E., Bauerle, A., Von Cossel, V. Von., et al. (2019). Prospects of Bioenergy Cropping Systems for A More Social-Ecologically Sound Bioeconomy. Agronomy 9, 605. doi:10.3390/agronomy9100605
Whittaker, C., Yates, N. E., Powers, S. J., Misselbrook, T., and Shield, I. (2016). Dry Matter Losses and Greenhouse Gas Emissions from outside Storage of Short Rotation Coppice Willow Chip. Bioenerg. Res. 9, 288–302. doi:10.1007/S12155-015-9686-Y
Yu, Q., Wang, Y., Van Le, Q., Yang, H., Hosseinzadeh-Bandbafha, H., Yang, Y., et al. (2021). An Overview on the Conversion of Forest Biomass into Bioenergy. Front. Energ. Res. 9, 348. doi:10.3389/FENRG.2021.684234/BIBTEX
Keywords: Cynara cardunculus L., supply chain, biomass, bioeconomy, drying, circular economy
Citation: Alfano V, Stefanoni W, Latterini F, Liuzzi F, De Bari I, Viola E, Ciancolini A and Pari L (2022) Inulin Content in Chipped Roots of Cardoon Stored at Different Initial Moisture Contents After Six-Month Storage. Front. Energy Res. 10:834443. doi: 10.3389/fenrg.2022.834443
Received: 13 December 2021; Accepted: 25 March 2022;
Published: 25 April 2022.
Edited by:
Marcin Debowski, University of Warmia and Mazury in Olsztyn, PolandReviewed by:
Ludo Diels, Flemish Institute for Technological Research (VITO), BelgiumSomnath D. Shinde, Conagen Inc., United States
Copyright © 2022 Alfano, Stefanoni, Latterini, Liuzzi, De Bari, Viola, Ciancolini and Pari. This is an open-access article distributed under the terms of the Creative Commons Attribution License (CC BY). The use, distribution or reproduction in other forums is permitted, provided the original author(s) and the copyright owner(s) are credited and that the original publication in this journal is cited, in accordance with accepted academic practice. No use, distribution or reproduction is permitted which does not comply with these terms.
*Correspondence: Walter Stefanoni, d2FsdGVyLnN0ZWZhbm9uaUBjcmVhLmdvdi5pdA==