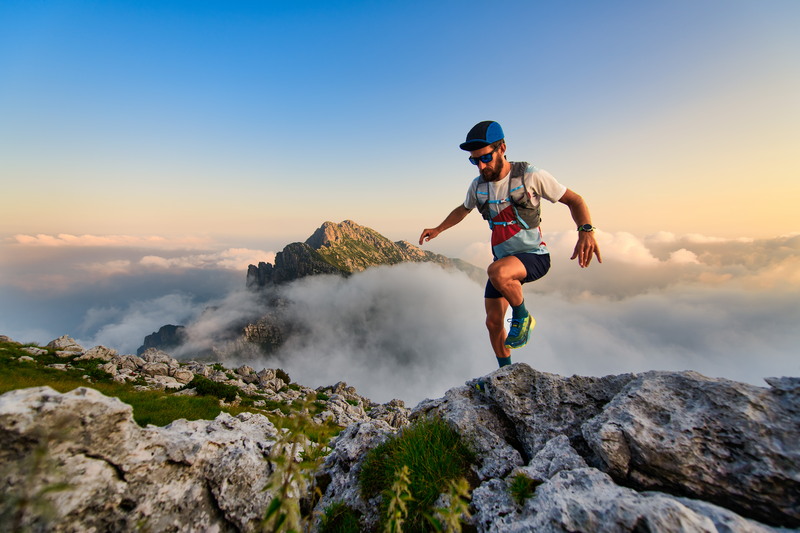
95% of researchers rate our articles as excellent or good
Learn more about the work of our research integrity team to safeguard the quality of each article we publish.
Find out more
ORIGINAL RESEARCH article
Front. Energy Res. , 24 March 2022
Sec. Process and Energy Systems Engineering
Volume 10 - 2022 | https://doi.org/10.3389/fenrg.2022.811648
This article is part of the Research Topic Advanced Hybrid Polygeneration Technologies View all 6 articles
The cooperative control of shearer and scraper conveyors is the prerequisite for the realization of intelligent comprehensive mining equipment and unmanned comprehensive mining workings. However, because of the harsh working face environment, the complex process of comprehensive mining, and the many uncertainties, it is difficult to establish a mathematical model for the cooperative control of shearer and scraper conveyors precisely through the operating mechanism. In the era of big data, the data-driven model has become a popular trend. Therefore, according to the actual production process data, this article proposed a data-driven cooperative control model of shearer–scraper conveyor based on rough set theory. First, the selection method of process monitoring parameters based on rough set theory was proposed to remove redundant parameters and redundant parameter values. Moreover, the decision rule base of cooperative speed regulation of shearer and scraper conveyor was established. Then a collaborative speed regulation decision algorithm based on attribute importance was designed. The algorithm matches the decision rules according to the real-time observation data and then determines the running speed of the shearer. The simulation results show that the proposed data-driven collaborative control model of shearer–scraper conveyor based on rough set theory overcomes the limitations of the mathematical model. It can predict the running speed of shearer well and realize the collaborative speed regulation of shearer–scraper conveyor.
The comprehensive working face is not only the forefront of coal production but also one of the main gathering places for underground coal mine workers. The production environment is poor and the operation risk is high. Therefore, unmanned technology is the key to realize the safe mining of fully mechanized working face (Wang et al., 2019; Liu et al., 2021). The intelligent coordinated speed regulation between shearer and scraper conveyor is one of the key problems to be solved. The change in shearer operation speed directly determines the change in scraper conveyor load (Huang et al., 2020). Unreasonable shearer operation speed often leads to light load operation, load mutation, overload shutdown, and even causes equipment damage and casualties. Therefore, the intelligent adjustment of the shearer running speed can effectively solve the problem of intelligent cooperative operation between shearer and scraper conveyor (Wang, 2014; Sun et al., 2021).
At present, a large number of scholars have studied the shearer speed regulation and the scraper conveyor load prediction. Tiryaki B. studied the application of frequency conversion technology in the shearer speed control system and put forward the shearer speed control method based on the shearer traction load according to the field experiment. Ralston J. C. proposed an automatic adjustment method of the shearer speed based on the recognition of coal–rock interface (Ralston and Strange, 2012). Ou Lulu analyzed the constant power control strategy of shearer. According to the characteristics of shearer speed control system, the shearer speed can be adjusted by the cutting load (Ou, 2008). Quan Ning studied the spatial constraint relationship of the mining equipment, analyzed the relationship between the current of the mining equipment and the shearer traction speed, as well as adjusted the shearer speed based on the current of the mining equipment (Quan, 2011). Murphy C. J. analyzed the dynamic load characteristics of the conveyor and proposed a method to track the load changes of the conveyor (Murphy and Bliss, 1994). Jun C. used the load detector to measure the chain tension of the scraper conveyor under different load states and designed a system that can monitor and control the load state of the scraper conveyor automatically (June 2012). Yang Wei analyzed the influence of coal cutting direction and inertia force on the load of scraper conveyor from the dynamic coal cutting perspective of shearer (Yang, 2011). The above studies have improved the single machine intelligence level of a fully mechanized mining equipment to some extent, but have not solved the problem of coordinated speed regulation of shearer–scraper conveyor.
With the continuous improvement in coal mine production technology, the research of single intelligent fully mechanized mining equipment has been unable to meet the automation and unmanned needs of fully mechanized mining face. The construction of cooperative control mechanism between fully mechanized mining equipment is the basis and key for the future development of intelligent fully mechanized mining face. The cooperative speed regulation between shearer and scraper conveyor has been studied by foreign and domestic scholars. Based on the analysis of the cooperative movement of coal mining, Luo C. M. formulated the action rules of hydraulic support and the adaptive height adjustment strategy of shearer (Luo et al., 2016). Qiao Chunguang analyzed the cooperative motion relationship between the shearer and the scraper conveyor, and established the mathematical model of 3D space shape detection of the scraper conveyor based on the operation posture and position of shearer, in order to obtain the shape of the scraper conveyor in the working face. On this basis, coordinated control of the shearer–scraper conveyor was carried out (Qiao et al., 2018). Fan Q. G. analyzed the mutual constraint law of shearer and scraper conveyor, constructed the constraint set, established the task control model and task coordination mechanism, as well as realized the coordinated operation of comprehensive shearer and scraper conveyor (Fan. et al., 2012). Cui Nannan studied the shearer speed control system based on the cooperative work of fully mechanized mining equipment. The coordinated control technology of shearer and scraper conveyor was used to predict the load, and the specific scheme of the coordinated control was given. Then the shearer speed control system about the load prediction of scraper conveyor was developed (Cui, 2017). Combining with the cutting load characteristics of the shearer equipped with scraper conveyor, Wang Yao obtained the unloading characteristics, that is, the variation curve of coal drop with the traction speed of the shearer, and on this basis established a collaborative control mechanism (Wang and Meng, 2018). These studies have opened up the research field of cooperative control of shearer and scraper conveyor, and made great contributions to the construction of fully mechanized mining intelligence.
However, the above method puts forward some assumptions and conditions for the interference factors of the environment and equipment when establishing the cooperative working model of the shearer and the scraper conveyor. Such as, in the process of coal flow transportation, the size of coal particles cannot be determined. The baffle has been completely covered by coal particles and cannot be measured; in the actual transportation process, the coal flow has a velocity gradient, etc. When building a mathematical model, it is inevitable to make assumptions and conditions for these problems, which have a great impact on the load of the scraper conveyor. Moreover, the established cooperative speed regulation control model of shearer and scraper conveyor cannot adapt to complex and changeable production conditions. With the deep integration of artificial intelligence and big data and other technologies with the traditional coal mining industry, a large amount of historical operation data of fully mechanized mining equipment has been generated. These data contain rich cooperative control strategies and operation logic of shearers and scraper conveyors. Effective use of these data to study the data-driven control method for the cooperative process of the shearer and the scraper conveyor can deal with the problem that the established model cannot adapt to the complex and changeable production conditions. Data-driven research has become a new breakthrough in the research on cooperative speed regulation of shearer and scraper conveyor. Scholars have carried out related research. For example, aiming at the sudden change in working conditions caused by coal–rock inclusions and aiming at reliable operation and efficient production of shearers, Ge Shuaishuai et al. proposed a calculation method for the control target of cutting thickness of the pick based on the rated torque of the cutting motor, and based on the load characteristics of the drum and the rock-breaking ability, the drum speed regulation control strategy and the traction-drum coordinated control strategy for different sudden changes are formulated (Ge et al., 2015). Tan, C. proposed an improved Elman neural network (ENN) based on threshold strategy to predict the operation parameters of shearer. Furthermore, probabilistic neural network (PNN) was used to evaluate the operation state of scraper conveyor, and its collaborative control process was designed and analyzed (Tan et al., 2015). Data-driven control methods have also been investigated in other complex industrial fields. Ding Y. designed a data-driven DNUC method and proposed a collaborative control system based on the real-time monitoring data of all relevant equipment due to the precise plant model required by DNUC (Ding et al., 2015). Santos A.V. used data mining technology to extract relevant information from a large number of monitoring datasets in order to deal with complex industrial wastewater and study the control of membrane fouling (Santos et al., 2018). Asadi Yasin proposed a data-driven adaptive controller to solve the complexity of industrial process modeling and control, which makes the system less dependent on pre-identified models (Asadi et al., 2021). The research results show that the data-driven control method can effectively solve the dependence of the complex industrial system control model on the control object mechanism.
However, some basic problems need to be noticed when the data-driven control method is applied to the cooperative control system of the shearer–scraper conveyor. First, the working environment of the shearer–scraper conveyor is highly complex, and the data of production process are widely distributed in all aspects such as fully mechanized mining equipment, centralized control center of roadway, and ground remote control system (Gao, 2018; Quan et al., 2018). The multisource data of the working face and the error of measuring equipment may lead to inaccurate, inconsistent, or incomplete field data. Second, the field data set attributes have different effective weights related to decision behavior, which should be considered in the data-driven collaborative control model of the shearer–scraper conveyor (Tan et al., 2014; Xing et al., 2021). In order to solve the problem of incomplete data caused by equipment failure or network interruption, Hu Xuguang proposed a generative adversarial network based on trinetworks form (tnGAN) to deal with the problem of incomplete sensor data leakage detection. The proposed method has made great contributions to the recovery of incomplete data in the industrial field (Hu et al., 2021). The rough set theory proposed by Pawlak is also an effective mathematical tool in dealing with incomplete data. It can be utilized to discover hidden knowledge and information from field datasets (Pawlak, 1982; Zhang et al., 2014). The significance of attributes can also be calculated without any prior knowledge. A large number of scholars have conducted in-depth research on this. For example, Ruihua L. established the prediction model of underground coal mine gas by reducing the redundant information based on the improved rough set theory to solve the incomplete data attribute reduction problem existing in the existing online gas early warning model (Li et al., 2021). Elbaz A. H. established a medical diagnosis decision table by using the rough set theory and achieved the diagnosis of the disease by knowledge reduction (El-Baz, 2015). Aiming at the problem of intelligent knowledge expression and decision making of railway traffic dispatching command system, Wang Minghui proposed a method for selecting key indices of railway traffic dispatching based on rough set and applied it to the decision of adjusting train operation order (Wang, 2014). This control method based on the rough set theory has been widely used in coal mine gas prediction, medical diagnosis, decision support, and analysis, but the key technology has not been studied in the cooperation field of the shearer–scraper conveyor.
To this end, this paper proposed a data-driven collaborative control model of the shearer–scraper conveyor based on the rough set theory, which can well simulate the collaborative work process of the shearer–scraper conveyor, as well as predict and control the shearer speed. In this model, the process monitoring parameter selection method based on the rough set theory was used to remove redundant parameters and redundant parameter values. The collaborative speed regulation decision rule library of the shearer–scraper conveyor was established. Then a cooperative speed regulation decision-making algorithm based on attribute importance was designed. According to real-time observation data, the algorithm matches decision rules to determine the operation speed of the shearer. The main contributions of this paper are as follows.
1) A data-driven control method was proposed to realize the cooperative control of the shearer and the scraper, which makes up for the problem that the traditional control model depends on the cooperative working mechanism of the shearer and the scraper.
2) A method for selecting monitoring parameters based on the rough set theory was proposed to deal with the problem that the monitoring parameters are full of uncertainties in the coal mining and scraper processes.
3) A cooperative speed regulation decision algorithm (CSDA) of the shearer–scraper conveyor considering attribute weight was designed.
4) This paper proposed a data-driven cooperative control model of the shearer–scraper conveyor based on the rough set theory, which does not require comprehensive mining equipment and mining process. The decision rule base of the shearer–scraper conveyor cooperative control is established with strong interpretability and generalization performance.
This paper is divided into five parts. Section 2 introduces the rough set theory. Section 3 describes the methods used in this study, including the optimal feature parameter selection method and the shearer–scraper conveyor collaborative speed decision algorithm. The fourth section conducts experimental verification, describes the whole process of obtaining the optimal decision rule set of the shearer–scraper conveyor collaborative speed regulation, and verifies the rule base and decision algorithm. The conclusions of this article are in section 5.
This paper proposes to establish a cooperative speed control rule database for coal shearers and scraper conveyors based on the rough set theory. Even if there are some incomplete or inconsistent data in the original data set, the model can reveal more useful information from the original data, thereby, obtaining the optimal decision rule set. The main process of the proposed shearer self-adaptive control model is shown in Supplementary Figure S1. It is mainly divided into three parts: The first part is to determine the initial characteristic parameters from the field data collected by the Yujialiang automated data acquisition system. The data of the initial characteristics are preprocessed to establish a coal shearer–scraper conveyor coordinated control data set. In the second part, the shearer–scraper conveyor coordinated control data set is discretized and then input into the Rosetta system as the initial decision table, and the redundant attributes contained in the original decision system are removed through attribute reduction and value reduction of the rough set theory. The decision-making system was simplified, and the optimal set of decision-making rules was taken. In the third part, a decision-making algorithm that considers attribute weights is designed to handle different coal flow conditions. The decision-making algorithm selects the most suitable rule for the speed of the shearer by calculating the distance between the real-time data and the optimal decision-making rule set.
The rough set theory was first proposed by Professor Pawlak to deal with the imprecision, ambiguity, and uncertainty of data. Rough sets have important applications in intelligent decision-making systems, and it is suitable for automatically acquired rules because it can deal with inaccurate, inconsistent, and incomplete data (Pawlak, 1982). In the rough set theory, information system is defined as a four-tuple
Definition 1: Given a decision system,
where a(x) represents the value of attribute a of object x.
Definition 2: Given a decision system
Definition 3: Given a decision system
If there is
Definition 4: Given a decision system
where
The collaborative work process of the shearer–scraper conveyor is complex, and the environmental coupling is strong. The data-driven collaborative control model of the shearer–scraper conveyor based on the rough set theory is to speed the shearer according to the operation state of the scraper conveyor. The data source of the collaborative speed regulation includes the operation data and environmental data of the shearer and the scraper. The data types are diverse, including current, voltage, temperature, speed, and other sensing data. During the operation of the scraper conveyor, with the change of coal falling amount of shearer, its motor current, motor speed, and temperature are constantly changing. Although the load of scraper conveyor is not simply a linear relationship with the motor current, the fluctuation of the motor current can reflect the change in the load. The shearer runs repeatedly in the working face, the scraper conveyor runs circularly, and unloading is at the end of the machine, so the direction and position of the shearer and the coal load of the scraper conveyor are also important. At present, the centralized monitoring system of fully mechanized mining can conveniently collect and record these data. According to the requirements of mining technology, the characteristic parameters of the operation state of the shearer–scraper conveyor are selected, as shown in Supplementary Table S1.
In Supplementary Table S1, the two characteristic variables, body pitch angle c1 and body cross-roll angle c2 of the coal miner, reflect the undulating variation of the working face bottom plate and the spatial position state of the scraper conveyor to a certain extent. The height of the coal miner drums c8 and c16 reflects the undulation of the working face top plate. Therefore, Supplementary Table S1 not only characterizes the operating conditions of the shearer–scraper conveyor but also, to some extent, portrays the environmental conditions at the working face.
The rough set theory can only deal with discrete data. Therefore, when using the rough set theory to model the adaptive speed regulation process of the shearer, continuous attributes must be discretized first; otherwise, the computational complexity will exceed the limit. Moreover, discretization belongs to the data preprocessing stage in the whole rough set modeling process, and its effect will greatly affect the final accuracy of the model.
Based on the characteristics of the data collected in this paper, a data discretization method based on an improved K-means clustering algorithm was used in order to overcome the characteristics of different identification target sensor data having a certain degree of differentiation. Different sensor data have different formats and null values, and these collections are susceptible to noise. First, a large number of high-dimensional attribute data points are divided into multiple clusters according to the class cluster indicators, and the class cluster labels for each cluster is extracted. Then labels are employed in discretizing all the data in the clusters to reduce the errors caused by discretization through making full use of the characteristics of the data itself. Based on the improved K-means clustering algorithm, the final number of clusters is chosen as the K value corresponding to the lowest point (minimum value) of the cluster index curve with K value. In order to reduce the computational complexity, the algorithm uses the average center-of-mass distance of the class clusters as the class cluster indicator, taking into account the sample distance and dispersion, in order to reduce the influence of noise and isolated points on the decision recognition results. For the null values in the dataset, interpolation can be performed based on the class cluster density and the upper and lower samples. Taking the coal miner adaptive self-adaptive control dataset as the sample dataset, let the sample dataset be
where K is the number of class clusters, ni is the number of samples in class i of Ci,
The input is the value of the attribute and the maximum value of k. Here the value of k is enumerated by a decreasing counter. The output is the discretized value of the attribute.
Step 1: K-means clustering is performed for all attribute data, and a fixed K value is taken. The results are stored temporarily.
Step 2: Calculate the mean prime distance of the class clusters as the class cluster indicator.
Step 3: Determine whether k is greater than 1. If yes, then k−1, return to Step 1, otherwise go to Step 4.
Step 4: Calculate the minimum value of the attribute’s class cluster indicator with k value, determine the final value of k, and select the clustering result corresponding to k value from the staged data.
Step 5: Discrete the continuous attributes using the class cluster labels instead of the values of the data in the class clusters.
After discretization, it is necessary to perform feature reduction on the adaptive speed regulation dataset of the shearer. Due to the importance of attributes, this paper directly selects the minimum attribute reduction set as the adaptive speed regulation rule set of shearer, and calculates the dependence and importance of each condition attribute in turn, which is an important parameter for subsequent decision making.
In Eqs 7–9, where
After attribute reduction, the decision rule base is generated, and the decision algorithm can select the appropriate rules from the rule base according to real-time data for determining the shearer speed. It is the most important issue in the decision-making process to select the appropriate rules to make decisions on the speed of the shearer at time t + 1. Since different attributes have different influences on the selection of decision rules, it is necessary to consider the weight of each attribute in the decision rule table when making the shearer speed decision, which makes up for the insufficient consideration of attribute importance in the traditional shearer behavior decision-making method.
where c is the attribute in the conditional attribute set RED,
Among them,
Decision algorithm steps are described as follows.
Step 1: Calculate weighted distance
Step 2: Select the rule r satisfying the condition
Step 3: Calculate the number of rules for three decision attributes in the selected rules, and select the decision attribute with the largest number of rules as the final decision result.
The decision algorithm proposed in this paper involves the parameters of weighted distance threshold
The adaptive speed control data set of the shearer used in this paper was collected from 43,101 fully mechanized mining face of Yujialiang Coal Mine in Northern Shaanxi, China. The length of 43,101 working face is 351.4 m, the thickness of coal seam is 1.0–1.7 m, and the average thickness is 1.47 m. The designed mining height of working face is 1.4 m, and the dip angle is 3°–5°. The main mechanized mining equipment and its configuration is ZY9200/09/18D double column shield hydraulic support whose strength is 0.99–1.06 MPa. The shearer is MG2 × 200/890-WD1, the cutting height range is 1.3–2.5 m, and the total installed power is 890 kW. The scraper is SGZ800/1,400, and the installed power is 2 × 700 kW. The layout structure of 43,101 fully mechanized working face in Yujialiang Coal Mine is shown in Supplementary Figure S3.
The original dataset is composed of state monitoring data and control behavior data of the shearer–scraper conveyor. From the initial feature set established in Supplementary Table S1, the adaptive speed regulation dataset of the shearer is established, which includes 25 feature attributes and 1 decision attribute. The sampling period is 1.0 s from 01:00 a.m. to 06:00 a.m. on March 29, 2020 and March 30, 2020. Because the dataset collected by the Yujialiang automatic acquisition system is not displayed in every second, it only shows the time and data when the data changes. Therefore, it is necessary to fill the data set in 1 s. After completion, there are 20,663 samples totally, as shown in Supplementary Table S2.
First, we need to normalize the data in Supplementary Table S2 and use the Z-score normalization method to normalize the data of the initial features. Then based on the improved K-means clustering algorithm proposed in the Section 3.2.1, the normalized data in Supplementary Table S2 are discretized, and the initial maximum value k = 15 is selected. After the improved K-means method is discretized, the data are shown in Supplementary Table S3.
In Supplementary Table S3, each attribute data in the dataset is discretized based on the improved K-means clustering method, and k = 15 is set as the maximum value. The value of k is enumerated through a decreasing counter, and the attribute data with decreasing k values are clustered and discretized, and all cluster indices are calculated. Finally, k = 9 corresponding to the minimum value of the cluster index changing with the k value is selected as the final cluster index. The clustering and discretization of the data not only reduces the influence of noise and outliers in the data on the decision recognition results but also fully solves the problem of large differences in the perception data of different targets.
The feature reduction method introduced in Section 3.2.2 is used to reduce the discrete adaptive speed control decision table of the shearer. The input is shown in Supplementary Table S3. The reduction results are shown in the following table. The initial decision table was reduced using the feature reduction method introduced in section 3.2.2. Its inputs are shown in Supplementary Table S3. The results of the simplification and reduction are shown in Supplementary Table S4.
From the data in Supplementary Table S4, the importance of conditional attributes, c2, c8, c14, c15, and c21, to decision attribute D is 0, and the preliminary reduction result is P = (c1, c3, c4, c5, c6, c7, c8, c9, c10, c11, c12, c13, c16, c17, c18, c19, c20, c22, c23, c24, c25). What is more, the classification ability of each conditional attribute c on P to D is calculated by Eq. 8, and the results are shown in Supplementary Table S5.
It can be seen from the data in Supplementary Table S6 that after removing the conditional attributes, c3, c5, c9, c10, c17, c19, and c24, from the preliminary reduction conditional attribute set P, the classification ability of the conditional attribute set P for decision attribute D is not affected, and the final reduction result is RED = (c1, c4, c6, c7, c8, c11, c12, c13, c16, c18, c20, c22, c23, c25). In order to improve the adaptive speed regulation efficiency of the shearer, it is necessary to reduce the value of the composed rule table. That is, for rule r in the rule table, its attribute ci is taken. If the value of attribute ci is removed, there is no conflict between other rules and ruler, and the value of attribute ci in rule r is redundant. After the value reduction of the decision rule table, the length of the antecedent of each rule has been further reduced. At the same time, each two rules do not conflict with each other and correspond to the complete rules of the original decision table. The reduced rule set is clearer, as shown in Supplementary Table S6.
In the process of cooperative speed regulation decision of the shearer–scraper conveyor, it is an important problem to select appropriate rules to determine the shearer speed. Different attributes in the decision rule set have different significance for the rule selection. After the decision rules are generated, the decision algorithm in the Section 3.5 is used to predict the traction speed of the shearer. Supplementary Table S7 shows the discrimination and weight calculation results of each attribute in the decision rule table. According to each attribute discrimination value in Supplementary Table S7, it can be seen that the attribute traction current, traction temperature, scraper conveyor head horizontal speed, and tail speed have great influence in the decision-making process, which is consistent with the decision-making behavior in the actual shearer traction decision-making process. In this paper, there are 4,276 rules in the decision rule base (Supplementary Table S6). According to the number of rules, given that the threshold of the number of rules is
The data-driven cooperative control model of the shearer–scraper conveyor based on the rough set theory proposed in this paper is verified. The cooperative speed regulation decision of the shearer–scraper conveyor is regarded as a classification model. Through the comparison between the predicted shearer speed of this model and the actual shearer speed, the adaptive speed regulation model of the shearer based on the rough set proposed in this paper is verified.
First, the decision rule base established by the model is verified. The data-driven cooperative control model of the shearer–scraper conveyor based on the rough set theory is established. Different discretization methods correspond to different decision rule bases. The dataset of the cooperative control of the shearer–scraper conveyor established in this paper is discretized by equal width, k-means clustering, and entropy-based discretization methods. After reduction, different rule bases are obtained. According to the cooperative speed regulation decision algorithm of the shearer–scraper conveyor, the speed prediction of the shearer is realized. The decision algorithm needs to be adjusted according to the decision rule base. The prediction accuracy of the model under different rule bases is evaluated by the ROC curve of the classical classification model. The closer the ROC curve is to the upper left corner, the higher the accuracy of the test classification. The area under the ROC curve is defined as the AUC value. The higher the AUC value is, the better and more accurate the classification effect is. The experimental results are shown in Supplementary Figure S4 and Supplementary Table S8.
As can be seen from the chart, the decision factor ICC of the improved K-means clustering rule base selection is 0.35, the decision factor ICC of the equal width discrete rule base selection is 0.4, the decision factor ICC of the equal frequency discrete rule base selection is 0.3, and the decision factor ICC of the entropy discrete rule base selection is 0.3. After the decision factor is determined, the decision attribute with the largest number of supporting rules can be selected by the decision algorithm as the final decision result. The decision results are shown in Supplementary Figure S5.
According to the results of the decision algorithm and the actual decision behavior of the shearer, the decision rule base established by the model is verified. The verification results are shown in Supplementary Figure S5. It is obvious that the predicted shearer speed obtained by the model simulation provided in this paper is basically consistent with the actual shearer speed change trend. The number of matching rules is given in the diagram. Since the model predicts the change trend of the shearer traction speed, the shearer traction speed is adjusted according to the fixed speed change (according to the characteristics of the dataset in this paper, the fixed speed change value is 0.08 m/min), which leads to a small deviation between the simulation results and the actual speed, but does not affect the decision results. In order to verify the superiority of the data-driven collaborative control model of the shearer–scraper conveyor based on the rough set theory (DCCRM), the original data without rough set pretreatment is input into support vector machine (SVM) and extreme learning machine (ELM) for training and testing. The LIBSVM toolkit is used for SVM experiments. Through repeated experiments, with mean square error and correlation coefficient as the standard, the Gaussian kernel function, penalty coefficient C = 151, γ = 0.003, and error control parameter = 0.18 are selected as the training parameters of SVM. For ELM, the number of hidden layer nodes is determined to be 370 by Sin function. The test results are shown in Supplementary Figure S6 and Supplementary Table S9.
It can be seen from the above chart that in the application of the shearer–scraper conveyor cooperative control decision making, compared with elm and SVM, the data-driven shearer–scraper conveyor cooperative control model based on the rough set theory proposed in this paper has better performance, and shows advantages in prediction accuracy, and error range. Although the accuracy of SVM can reach 85.64%, and the error range can be controlled within 0.47, it is difficult to find the optimal parameters accurately, and it takes a lot of time to adjust and train the parameters, which limits its application in the cooperative control decision making of the shearer–scraper conveyor. Although the classification time of elm is very fast, the accuracy is relatively low. Because the influence of different attributes on the decision results is considered, the accuracy of our model is 89.16%, and the error range can be controlled within 0.22. Moreover, the time-consuming part of the model is to obtain the decision rule base by using the rough set theory, and the time spent in the decision part can meet the job requirements.
This paper presented a data-driven shearer–scraper conveyor collaborative control model based on the rough set theory, which can adjust the shearer speed according to real-time production data. The rough set theory is used to deal with the cooperative operation logic of the shearer–scraper conveyor contained in the monitoring parameters of fully mechanized mining face. The redundant attributes were eliminated by feature reduction, and the cooperative control decision rule database of the shearer–scraper conveyor was established. Then a shearer–scraper conveyor collaborative speed regulation decision algorithm based on attribute importance was designed. The algorithm matches the decision rules according to the real-time observation data and determines the shearer running speed. The experimental results show that, compared with the traditional model, the prediction accuracy of our model is higher, reaching about 89.16%, and the error range is relatively small. Our model can well predict the operating speed of the shearer and realize the cooperative control of the shearer–scraper conveyor. In the future, in order to improve the accuracy and generalization performance of our model, we need to collect more monitoring parameters of comprehensive mining face and optimize the decision algorithm of the shearer–scraper conveyor collaborative speed regulation to achieve more accurate prediction results.
The original contributions presented in the study are included in the article/Supplementary Material. Further inquiries can be directed to the corresponding author.
Conceptualization, SZ and JZ; methodology, SZ and JZ; software, JZ; validation, ZL, YM, and HH; formal analysis, JZ and SZ; investigation, JZ; resources, YM; data curation, JZ; writing—original draft preparation, JZ and HH; writing—review and editing, JZ and YM; visualization, ZL; supervision, ZX and HH; project administration, JZ and YM; funding acquisition, SZ and JZ. All authors have read and agreed to the published version of the manuscript.
This study was funded by the Shaanxi Provincial Key Research and Development Program (Project No. 2019ZDLGY03-09-02), Xi’an Science and Technology Plan Project (Project No. 2019113913CXSF017SF027), Xi’an Science and Technology Plan Project (Project No. 2020ZDLGY04-06), and Joint Funds of the Natural Science Foundation of Shaanxi Province (Grant No.2019JLP-06).
The authors declare that the research was conducted in the absence of any commercial or financial relationships that could be construed as a potential conflict of interest.
All claims expressed in this article are solely those of the authors and do not necessarily represent those of their affiliated organizations, or those of the publisher, the editors, and the reviewers. Any product that may be evaluated in this article, or claim that may be made by its manufacturer, is not guaranteed nor endorsed by the publisher.
In this paper, the coordinated speed regulation of the shearer–scraper conveyor was regarded as a rule-based adaptive control behavior decision problem. An adaptive speed regulation method of the shearer based on the rough set theory was proposed to study the relationship between the perception information and the speed regulation decision under the cooperative operation of the scraper conveyor. Based on the rough set theory, considering that different condition attributes have different effective weights related to decision-making behaviors, the shearer–scraper conveyor coordinated speed regulation rule base was established. Then the speed of the shearer was decided based on the attribute discrimination. The research results of this paper can provide a theoretical basis for the coordinated control of the shearer–scraper conveyor and improve the use efficiency of the existing fully mechanized mining equipment. At the same time, the coordinated control of the fully mechanized mining equipment was conducive to automatic production of the fully mechanized mining face, reducing the number of workers in the fully mechanized mining face, reducing casualties when disasters occur, as well as promoting the construction and development of safe, high-yield, and efficient mines in coal mines. Therefore, whether it is considered from the perspective of economic development or social development, the study of this topic has important theoretical and practical significance.
The Supplementary Material for this article can be found online at: https://www.frontiersin.org/articles/10.3389/fenrg.2022.811648/full#supplementary-material
Asadi, Y., Farsangi, M. M., and Bijami, E. (2021). Data-driven Adaptive Control of Wide-Area Non-linear Systems with Input and Output Saturation: A Power System Application. Int. J. Electr. Power Energ. Syst. 133, 107225. 0142-0615. doi:10.1016/j.ijepes.2021.107225
Cui, N. (2017). Shearer Speed Control System Based on Cooperative Work of Fully Mechanized Mining Equipment. Coal 26 (2), 47–49.
Deshpande, V., Chaudhari, J. G., and Jagtap, P. P. (2009). Development and Simulation of SPWM and SVPWM Control Induction Motor Drive. Rock Mech. Rock Eng. 39 (2), 89–120. doi:10.1109/ICETET.2009.78
Ding, Y. S., Xu, N., Ren, L., and Hao, K. (2015). Data-Driven Neuroendocrine Ultrashort Feedback-Based Cooperative Control System. IEEE Trans. Contr. Syst. Technol. 23, 1205–1212. doi:10.1109/TCST.2014.2359386
El-Baz, A. H. (2015). Hybrid Intelligent System-Based Rough Set and Ensemble Classifier for Breast Cancer Diagnosis. Neural Comput. Appl. 26 (2), 437–446. doi:10.1007/s00521-014-1731-9
Fan, Q. G., Li, W., and Luo, C. M. (2012). Error Analysis and Reduction for Shearer Positioning Using the Strapdown Inertial Navigation System. Int. J. Comput. Sci. Issues 9 (5), 49–54.
Gao, G. (2018). Collaborative Control of Shearer Speed Control System Based on Load Adaptive Prediction. Mech. Manage. Dev. 33 (5), 135–136.
Ge, S., Qin, D., and Hu, M. (2015). Research on Speed Regulation Control Strategy of Drum Shearer under Sudden Change Conditions. J. China Coal Soc./Mei Tan Xue Bao 40 (11), 2569–2578. doi:10.13225/j.cnki.jccs.2015.7043
Hu, X., Zhang, H., Ma, D., and Wang, R. (2021). A tnGAN-Based Leak Detection Method for Pipeline Network Considering Incomplete Sensor Data. IEEE Trans. Instrum. Meas. 70, 1–10. doi:10.1109/TIM.2020.3045843
Huang, Z., Wang, F., and Zhang, S-X. (2020). Research on the Architecture and Key Technologies of Intelligent Coal Mining System. J. Coal 45 (06), 1959–1972. doi:10.13225/j.cnki.jccs.zn20.0348
Jun, C. (2012). Dynamic Tension Control System for Chain of Scraper Conveyor and its Application. Indust. Mine Autom. 1, 034.
Li, R. H., Feng, Z. D., Guo, H. B., and Zhao, P. (2021). Online Early Warning Model of Underground Gas Concentration Based on Improved Rough Set. Int. J. Intell. Inf. Manage. Sci. 10 (3), 599–622.
Liu, G.-J., Zhang, H., Zhu, Y.-W., Cao, W.-H., Ji, X.-J., Lu, C.-P., et al. (2021). Investigations of Coal-Rock Parting-Coal Structure (CRCS) Slip and Instability by Excavation. Shock Vibr. 2021 (01), 1–15. doi:10.1155/2021/1715644
Luo, C., Fan, X., Ni, J., Yang, H., Zhang, X., and Li, W.. (2016). Positioning Accuracy Evaluation for the Collaborative Automation of Mining Fleet with the Support of Memory Cutting Technology. IEEE. 4 5764–5775. doi:10.1109/access.2016.2602304
Murphy, C. J., and Bliss, R. E. (1994). Method and Apparatus for belt Conveyor Load Tracking. U.S. Patent 5,335,777. 8–9.
Ou, L. (2008). Research on Frequency Conversion Speed Control System of Coal Mining Machine Based on Direct Torque Control. Anhui University of Technology.
Qiao, C., Wang, X., and Xie, J. (2018). Method for Solving Vertical Plane Shape of Scraper Conveyor Based on Coal Mining Machine Running Track. Chin. J. Eng. Des. 25 (5), 7–14.
Quan, L. M., Yang, C. L., and Qiao, Y. F. (2018). Data-driven Method for Online Self-Organising Control of Dissolved Oxygen Concentration. Acta Automatica Sinica, 1–14. doi:10.16383/j.aas.c210041
Quan, N. (2011). Research on Collaborative Control Technology of Coal Mining Equipment at Comprehensive Mining Face. Indust. Mine Autom. 1, 024.
Ralston, J. C., and Strange, A. D. (2012). Thermal Infrared-Based Seam Tracking for Intelligent Longwall Shearer Horizon Control. 12th Coal Operators’ Conference, 78–85. FEB 16-17.
Santos, A. V., Andrade, L. H. d., Amaral, M. C. S., and Lange, L. C. (2018). Integration of Membrane Separation and Fenton Processes for Sanitary Landfill Leachate Treatment. Environ. Technol. 40, 2897–2905. doi:10.1080/09593330.2018.1458337
Shprekher, D., Babokin, G., Kolesnikov, E., and Zelenkov, A. (2020). Application of the Adaptive PI-Controller in the System of the Load Regulation of the Shearer. Изв.вузов Электромеханика 63, 46–54. doi:10.17213/0136-3360-2020-5-46-54
Sun, C., Jiang, L., and Yuan, G. (2021). Analysis of Coal Supply and Demand Trends in China during the 14th Five-Year Plan. Coal Eng. 53 (05), 193–196.
Tan, C., Wang, Y., Zhou, X., Wang, Z., Zhang, L., and Liu, X. (2014). An Integrated Denoising Method for Sensor Mixed Noises Based on Wavelet Packet Transform and Energy-Correlation Analysis. J. Sens. 2014 (2), 1–11. doi:10.1155/2014/650891
Tan, C., Si, L., Zhou, X., Wang, Z., and Wang, K. (2015). A Cooperative Control Method for Fully Mechanized Mining Machines Based on Fuzzy Logic Theory and Neural Networks. Adv. Mech. Eng. 7, 424070. doi:10.1155/2014/424070
Wang, Y., and Meng, W. (2018). Research on Dynamic Characteristics and Intelligent Control Method of Driving System of Heavy-Duty Scraper Conveyor in Fully Mechanized Mining. Taiyuan University of Science and Technology. Engineering Technology Series 1. TD634.2.
Wang, G., Liu, F., Pang, Y., Ren, H., and Ma, Y. (2019). Intelligent Coal Mine – Core Technology Support for High-Quality Development of Coal Industry. J. Coal 44 (02), 349–357. doi:10.13225/j.cnki.jccs.2018.2041
Wang, M. (2004). Study on the Application of Rough Set Theory in Railway Traffic Dispatching Command System. China Railway Sci. (04), 104–108. doi:10.1007/BF02911033
Wang, G. (2014). Development Direction of Automation, Intelligent and Unmanned Set of Technology and Equipment for Header Mining. Coal Sci. Technol. 4 2 (09), 30–34+39. doi:10.13199/j.cnki.cst.2014.09.007
Xing, Z., Zhao, S., Guo, W., Guo, X., and Wang, Y. (2021). Processing Laser Point Cloud in Fully Mechanized Mining Face Based on DGCNN. ISPRS Int. J. Geo-Inf. 10 (7), 482. doi:10.3390/ijgi10070482
Yang, W. (2011). Stability Analysis of Scraper Conveyor at Working Face. Coal Eng. 2011 (02). doi:10.3969/j.issn.1671-0959.2011.02.004
Keywords: shearer–scraper conveyor, rough set theory, cooperative control, decision rule base, data-driven
Citation: Zhao S, Zhao J, Lu Z, He H, Zhang C, Miao Y and Xing Z (2022) Data-Driven Cooperative Control Model of Shearer-Scraper Conveyor Based on Rough Set Theory. Front. Energy Res. 10:811648. doi: 10.3389/fenrg.2022.811648
Received: 09 November 2021; Accepted: 10 January 2022;
Published: 24 March 2022.
Edited by:
Carlo Roselli, University of Sannio, ItalyReviewed by:
Xuguang Hu, Northeastern University, ChinaCopyright © 2022 Zhao, Zhao, Lu, He, Zhang, Miao and Xing. This is an open-access article distributed under the terms of the Creative Commons Attribution License (CC BY). The use, distribution or reproduction in other forums is permitted, provided the original author(s) and the copyright owner(s) are credited and that the original publication in this journal is cited, in accordance with accepted academic practice. No use, distribution or reproduction is permitted which does not comply with these terms.
*Correspondence: Shuanfeng Zhao, enNmQHh1c3QuZWR1LmNu
Disclaimer: All claims expressed in this article are solely those of the authors and do not necessarily represent those of their affiliated organizations, or those of the publisher, the editors and the reviewers. Any product that may be evaluated in this article or claim that may be made by its manufacturer is not guaranteed or endorsed by the publisher.
Research integrity at Frontiers
Learn more about the work of our research integrity team to safeguard the quality of each article we publish.