- 1Process and Energy Department, Faculty of 3mE, Delft University of Technology, Delft, Netherlands
- 2Institute of Industrial Science, University of Tokyo, Tokyo, Japan
- 3Centre for Rural Development and Technology, Indian Institute of Technology, Delhi, India
- 4Energy and Sustainability Research Institute Groningen, Faculty of Science and Engineering, University of Groningen, Groningen, Netherlands
- 5Climate Institute, Delft University of Technology, Delft, Netherlands
- 6Water Engineering, CiTG, Delft University of Technology, Delft, Netherlands
Biochar derived from pyrolysis or gasification has been gaining significant attention in the recent years due to its potential wide applications for the development of negative emissions technologies. A new concept was developed for biochar and power co-generation system using a combination of biomass pyrolysis (BP) unit, solid oxide fuel cells (SOFCs), and a combined heat and power (CHP) system. A set of detailed experimental data of pyrolysis product yields was established in Aspen Plus to model the BP process. The impacts of various operating parameters including current density (
1 Introduction
Negative emissions technologies (NETs) have been gaining attention in the recent years, as it can be helpful in reducing CO2 emissions from power plants and industrial sectors to the atmosphere and mitigating climate change. Bioenergy with carbon capture and storage (CCS) technology currently plays a significant role in achieving a negative balance of carbon in the atmosphere (Fuss and Johnsson, 2021). In general, bioenergy conversion technologies can be simply classified into physical, thermal, chemical and biological methods (Ayodele et al., 2019). Among them, the thermal conversion technology such as torrefaction, pyrolysis, gasification of biomass has been widely considered for the purpose of producing syngas, heat, and power (Din and Zainal, 2016; Dechapanya et al., 2020). In addition to the utilization of biomass for energy and electricity production, the by-product biochar has gained considerable attention and is found suitable for various applications as illustrated in Figure 1.
Typically, biochar is produced from a slow pyrolysis process of biomass, which is generally heated in an inert atmosphere maintained below 500°C with a slow heating rate (<10°C min−1) (Yaashikaa et al., 2019; Uroic Štefanko and Leszczynska, 2020). This solid product (biochar) is characterized by its high stability, high porosity, high carbon content, high surface area, and high adsorption properties (Lee et al., 2017; Yaashikaa et al., 2019). Besides its potential application in the environmental and agricultural fields such as carbon sequestration, wastewater treatment process, and soil amendment, biochar can also be utilized as a catalyst for tar reforming during the biomass pyrolysis and gasification processes as well as in biorefineries (Lee et al., 2017; Yaashikaa et al., 2019; Uroic Štefanko and Leszczynska, 2020).
Another prospective and attractive approach to generate eco-friendly and efficient energy is to apply solid oxide fuel cells (SOFCs) technology to the NETs (Thattai et al., 2017). In contrast to the conventional coal-fired power plants or integrated coal gasification combined cycle (IGCC) systems, an integration of various chemical processes or hybrid energy systems with SOFCs for clean electricity production plays a vital role in the energy market and is now attracting significant attention, as it has a number of advantages (Aravind et al., 2009; Liu et al., 2011; Din and Zainal, 2016; Thattai et al., 2017): 1) SOFCs are low-emission, flexible, and modular devices; 2) high fuel flexibility: hydrogen, syngas, biogas, ammonia, etc.; 3) the high operating temperature of SOFCs makes the integration of high temperature chemical systems such as biomass gasification (BG), calcium looping technology, and chemical looping combustion viable; 4) system efficiencies as high as 50–60% or more if combined with gas turbines (GT) using exhaust heat from SOFC; and 5) a wide variety of applications ranging from combined heat and power (CHP) systems to larger power plants. On account of these advantages, the combination of different energy systems with SOFCs is highly promising as an energy-efficient and environment friendly process for decentralized power generation and co-generation.
Reviewing recent works concerning the applications of SOFC technology, there are numerous studies in the literature on the process integration of BG and SOFC system. For instance, Aravind et al. (2009) evaluated the performance of small-scale gasifier-SOFC-GT systems (100 kW) through thermodynamic calculations in terms of energy and exergy efficiencies using Cycle Tempo. They pointed out that an overall electrical efficiency of 54% was achieved. Liu et al. (2011) investigated an integrated biosyngas fueled gasifier-SOFC-CHP system (5 kW) and found that the CHP energy and exergy efficiencies were in the range of 57–66% and 23.9–28.1%, respectively. Baldinelli et al. (2016) conducted the coupling of a pilot downdraft gasifier with a commercial SOFC system and concluded that wood syngas was feasible for SOFCs since no carbon deposition was found on the NiYSZ-anode cell. Thattai et al. (2017) compared the performance of an integrated gasification fuel cell (IGFC) system with full oxy-fuel CO2 capture with a co-gasification of biomass and coal power plant without CO2 capture, and concluded that the energy and exergy efficiencies of the former were 10.8 and 9.8%, respectively, better than those of the latter. In addition, the IGFC system offers a very low specific CO2 emission as compared to the traditional co-gasification power plant. Detchusananard et al. (2019) simulated the integration of the sorption enhanced steam biomass gasification (SEG) with SOFC and a CHP system and they highlighted that a maximum exergy efficiency of 61.2% can be achieved.
In contrast to the BG-SOFC system, a number of studies have been carried out on integrated SOFC with other chemical process in a hybrid system. A literature summary of various energy systems integrated with an SOFC is presented in Table 1. For example, Ozcan and Dincer (2014) studied a chemical looping hydrogen production connected with a SOFC-GT system for trigeneration of power, heat, and hydrogen, and they indicated that the overall energy and exergy efficiencies of such a system were 56.9 and 45.1%, respectively. Chiodo et al. (2015) adopted the Aspen Plus simulator to investigate the feasibility of integrating a biogas reformer with an SOFC. They reported that their proposed system offers high SOFC efficiency (DC) up to 61.76% based on biogas steam reforming at an operating temperature of 800°C. Mehrpooya et al. (2020) designed a biodiesel production power plant integrated with a glycerol steam reforming process and an SOFC using Aspen Hysys. They concluded that the overall electrical and thermal efficiencies were 28.1 and 85.2% respectively. Mojaver et al. (2020a) investigated the optimum operating conditions of SOFCs via various optimization approaches (Taguchi/AHP/TOPSIS) to maximize the electrical efficiency. Meanwhile, they also evaluated an SOFC-supercritical CO2 Brayton- organic Rankine cycle-based power plant and pointed out that the electrical exergy efficiency was 43% after carrying out multi-objective optimization (Mojaver et al., 2020b). These earlier studies prove that SOFC technology is promising in applications to power plants and several industrial processes.
Based on the foregoing review of the literature, it shows that integrated BG-SOFC systems have been investigated extensively both in experiments and simulations, and few examined the use of integrating SOFCs with biogas reforming or chemical looping processes. However, an examination of the recent studies reveal that no research has been done to evaluate an integrated system incorporating biomass pyrolysis (BP) with a SOFC-CHP system for the NETs. Such sort of integrated system seems to be sustainable in nature and hence appropriate for energy and environment focused applications. For the aforementioned reasons, the present study aims to develop a BP-SOFC-CHP system for co-generation of biochar and power using Aspen Plus simulator, and then to examine the influence of operating parameters such as current density and fuel utilization factor (
2 Process design and simulation
2.1 System description
In this study, a simulation model of the co-generation of biochar and power plant is developed in Aspen Plus V8.8. In the simulation, the Peng-Robinson Boston Mathias (PR-BM) equation of state is used as the thermodynamic property (Chiodo et al., 2015). Figure 2 shows the entire process flow diagram for the co-generation of biochar and power system. The overall system is mainly composed of a biomass pyrolysis (BP) reactor, a pyrolysis volatiles reformer, a solid oxide fuel cell (SOFC) system, a combined heat and power (CHP) system, and three steam turbine systems. The key sub-systems in the BP-SOFC-CHP system, such as the BP process, the pyrolysis volatiles reforming, and the SOFC are presented in detail below. On the other hand, the detailed operating conditions of all sub-systems are presented in Table 2.
2.2 Biomass pyrolysis and pyrolysis volatiles reforming processes
In the biomass pyrolysis process (BP), slow pyrolysis of corn stover is considered for the purpose of producing biochar. The chemical and physical properties of corn stover are listed in Table 3. Moreover, the model is established according to the following key assumptions in the development of the BP-SOFC-CHP system: 1) the process is carried out in steady state; 2) the feedstock is at normal conditions (i.e., 25°C and 1 atm); 3) the solid and gaseous phases are in a state of thermodynamic equilibrium; 4) char is assumed as graphitic carbon. Based on the chemical and physical properties of corn stover, the biomass fuels and ash are established and defined as non-conventional components in Aspen Plus. The HCOALGEN model is chosen to estimate the heat of combustion, heat of formation, and heat capacity of biomass fuels. The DCOALIGT model is selected to calculate the density of biomass fuels. When corn stover is fed into the BP-CHP-SOFC system, the first step is the heating and drying to reduce its moisture content. The resulting dried corn stover is then fed to the pyrolysis reactor in which the slow pyrolysis is performed at 500°C and 0.55 MPa. The RYield reactor is used to model the product yields of pyrolysis volatiles, pyrolysis liquid, and biochar based on the experimental system used by Chen et al. (2016) and Manyà et al. (2018). Based on their studies, experimental data such as the product yields and compositions are available, and this can be taken as valid inputs for developing the model in Aspen Plus. The yields of the major products are thus calculated based on the experimental results by a calculator block which is controlled by the FORTRAN statement in accordance with the component characteristics of the feedstock. The main product yields from corn stover slow pyrolysis are presented in Table 2. During corn stover slow pyrolysis at 500°C, approximately 30.6% of the pyrolysis volatiles are released from the feed, while the pyrolysis liquid (including water and organic compounds) and biochar yields are 37.9 and 31.5% respectively. The main components of pyrolysis liquid from corn stover slow pyrolysis are established based on the experimental results of Chen et al. (2016). In terms of GC/MS analysis, furfural accounted for most of the yields of products in the organic phase, followed by, oxiranemethanol acetate, D-allose, Furfuryl alcohol, Phenol, Metacetamol, Butyrolactone, 4-Methoxy-1,2-benzenediol and other components. The pyrolysis gas coming out of the reactor is heated and sent to the volatiles reformer to produce hydrogen-rich gas, while the biochar is taken out from the bottom of the pyrolysis reactor. For the base case system, the biochar split ratio is assigned as zero and hence the entire biochar produced is taken out from the reactor at regular intervals. In contrast to the base case, a splitter unit is used to control the biochar spilt ratio. According to this ratio, a part of the produced biochar will be conveyed to the pyrolysis volatiles reformer to produce more hydrogen. The pyrolysis volatiles reforming is simulated by using an RGibbs reactor which models the major chemical reactions based on the chemical and phase equilibrium calculations by minimizing the Gibbs free energy. The Gibbs free energy minimization equilibrium model (RGibbs) has been widely considered a suitable approach to predict thermodynamic behavior of the gas-char reforming process (AlNouss et al., 2020; Rosha et al., 2022). Six different reforming temperatures of 600, 650, 700, 750, 800, and 850°C are taken into account to find the suitable operating condition for the BP-SOFC-CHP system, and the major chemical reactions occurring in the reformer are summarized in Table 4. Meanwhile, to identify the maximum thermodynamic efficiencies of the system, for simplicity, an ideal separator unit is installed after the reformer to separate hydrogen from the reformed gas, and this hydrogen is heated and fed to the SOFC system.
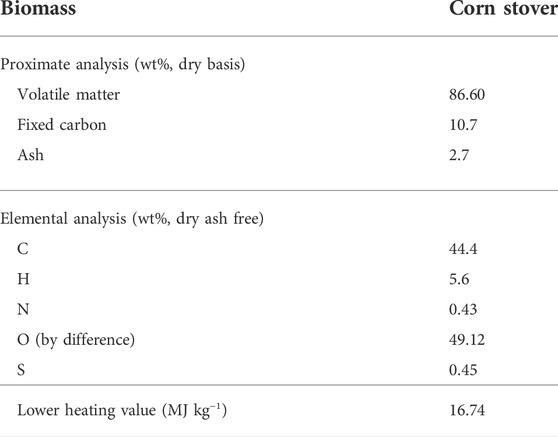
TABLE 3. Proximate and elemental analyses of the biomass used in the simulation (Manyà et al., 2018).
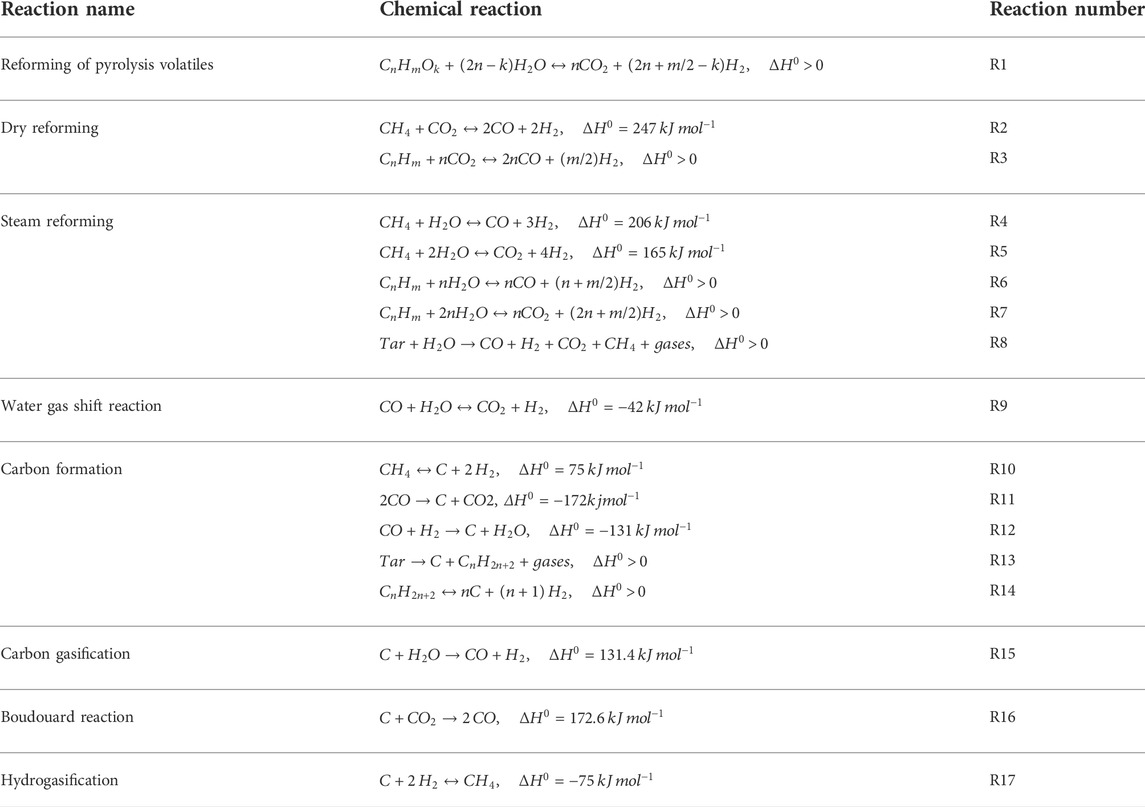
TABLE 4. A list of main chemical reactions occurring during the pyrolysis volatiles reforming unit (Liu et al., 2013; Xu et al., 2015; Arregi et al., 2017).
2.3 Solid oxide fuel cell system
The SOFC model is also established in the Aspen Plus environment. The detailed process flowsheet and the relevant input parameters (geometry, material properties, etc.) are modeled based on the study of Doherty et al. (2010). The following key assumptions are considered in the present SOFC model (Doherty et al., 2010; Taufiq et al., 2015): 1) the entire system is steady-state and zero-dimensional; 2) any pressure drop in the system is neglected; 3) chemical reactions reach the thermodynamic equilibrium at a given reaction temperature; 4) the half-cell reactions are replaced by the overall oxidation of hydrogen, since the process of ions crossing over through the electrolyte cannot be simulated in Aspen Plus. An RGibss reactor based on Gibbs free energy minimization is utilized to model the chemical reactions occurring at the anode, while a separator is used to model oxygen required by the electrochemical reactions (Doherty et al., 2010). To calculate the required amount of oxygen (
where
The Nernst potential, and the operational cell voltage considering the losses due to ohmic, activation, and concentration polarizations are calculated based on Doherty et al. (2010). After the cell voltage (
where
The anode outlet gas of SOFC subsequently enters into the combustor where the oxidation of unreacted hydrogen takes place to release heat. An RStoic reactor which is a stoichiometry-based reactor with specified extents of reaction is utilized to model the combustion reaction. Next, the hot exhaust gas from the combustor flows through a heat exchanger (HE-1) in order to preheat the cathode air and then is sent to a combined heat and power system (CHP), including a heat recovery steam generator (HRSG) and a number of steam turbine (ST) cycles to generate additional electricity.
2.3.1 Validation of the solid oxide fuel cell
The validation of the SOFC model is performed by comparing the current predictions to the results of Doherty et al. (2010). In their work, a syngas composition characteristic of 34% H2, 16% CO, 7.4% CH4, 15.8% CO2, 25.7% H2O, and 1.1% N2, produced after gas cleaning from the Güssing DFB gasifier with an operating temperature of 850°C and a steam/fuel ratio of 0.75 (Doherty et al., 2010), is used as an inlet fuel of the SOFC for generating a DC power of 120 kW. The operating temperature, pressure, and active area of the SOFC were 910°C, 1.09 bar, and 96.1 m2, respectively. The fuel utilization and air utilization factors were fixed at 0.85, and 0.167, respectively. As shown in Table 5, the simulation results are in good agreement with the data presented in the literature. Therefore, it is concluded that the SOFC model used in the present study is reliable.
3 Thermodynamic analysis
In order to investigate the effect of various operating parameters such as
3.1 Energy efficiency ( )
The SOFC energy efficiency (
where
With regard to the overall efficiency of BP-SOFC-CHP system, it can be determined by using the following equations. Basically, the main energy content of the products which can be recovered from the BP-SOFC-CHP system are product gas, biochar and sensible heat. The gross power output from the BP-SOFC-CHP system equals to the sum of electric power of the SOFC and CHP. The energy content of the product gas can be expressed by its lower heating value (LHV, MJ kg−1) (Emun et al., 2010):
where x stands for the mass fraction of gas species in the product gas, and
On the other hand, the energy content of biochar is calculated based on the LHV of biochar (27 MJ kg−1) (Rafiq et al., 2016). Hence, the system energy efficiency for main products (
where
3.2 Exergy efficiency ( )
The overall exergy balance between the inlet and outlet flows can be expressed as (Saidur et al., 2012; Zhang et al., 2012; Ozcan and Dincer, 2014):
where
Basically, the total exergy of the material streams includes physical exergy and chemical exergy, which can be written as follows:
where
In the foregoing equation, the
where
The
where
Meanwhile, the standard chemical exergy of species in the product gas and carbon can be obtained from the studies of Zhang et al. (2012), Saidur et al. (2012), and Ozcan and Dincer (2014). The exergy of heat streams is expressed as follows:
where
For biomass, the specific chemical exergy can be obtained by (Cohce et al., 2010):
where
As a consequence, the SOFC exergy efficiency (
where
Meanwhile, from the aforementioned equations, the exergy efficiency of the products (
4 Results and discussion
In the following discussion, a base case of the performance of overall BP-SOFC-CHP system in terms of energy (
4.1 A base case study of the biomass pyrolysis-solid oxide fuel cell-combined heat and power system
The energy and exergy flow diagrams of the BP-SOFC-CHP system for the base case are shown in Figures 3A,B, respectively. In this base case, the pyrolysis volatiles reforming temperature (
The inlet energy flow, which is the sum of the chemical energy content of the biomass fuel, heat of reaction, and energy requirement of the process, to the BP-SOFC-CHP system is 25.95 MW and most of the useful energy output of products are obtained from biochar and pyrolysis gas, which are 12.68 and 4.59 MW respectively, corresponding to 48.9 and 17.7% of the energy input (i.e.,
4.2 Sensitivity analysis
In order to develop a better understanding of a novel BP-SOFC-CHP system two important SOFC operating parameters, current density (
4.2.1 Effect of current density ( )
Sensitivity analysis of the effect of current density on the BP-SOFC-CHP system is shown in Figure 4, where
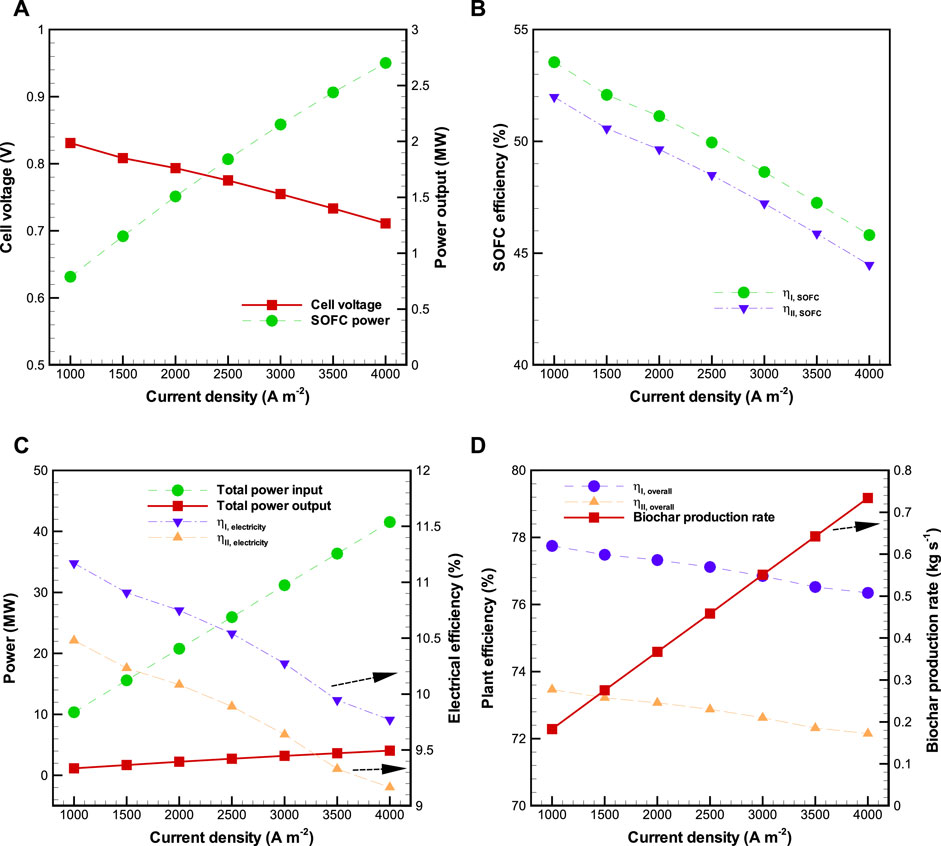
FIGURE 4. Effects of current density (
4.2.2 Effect of fuel utilization factor ( )
The second sensitivity analysis is carried out by varying the utilization factor (
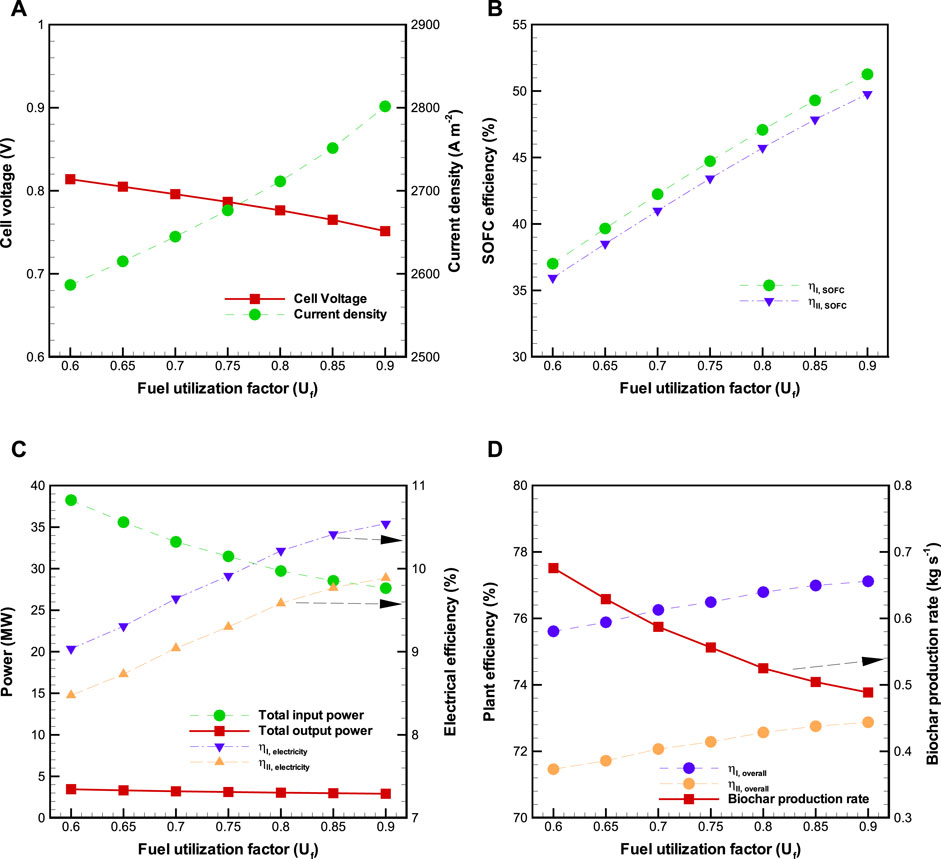
FIGURE 5. Effects of fuel utilization factor (
4.2.3 Effect of reforming temperature ( )
By virtue of the fact that
Figure 6A displays the profiles of concentrations of H2, CO, CH4, and CO2 in the product gas as well as carbon production rate as a function of
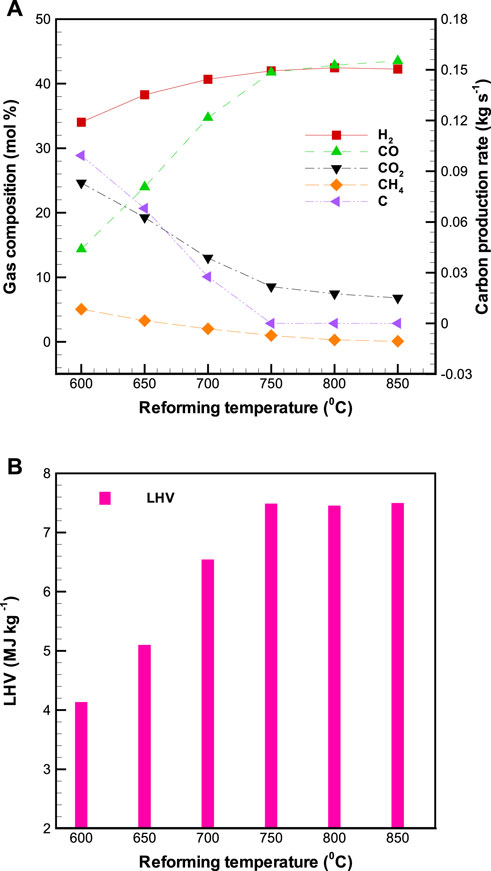
FIGURE 6. Effects of reforming temperature (
With attention paid to carbon formation in the reformer (Figure 6A), it is clear that the carbon production rate declines drastically with increasing
The influence of altered
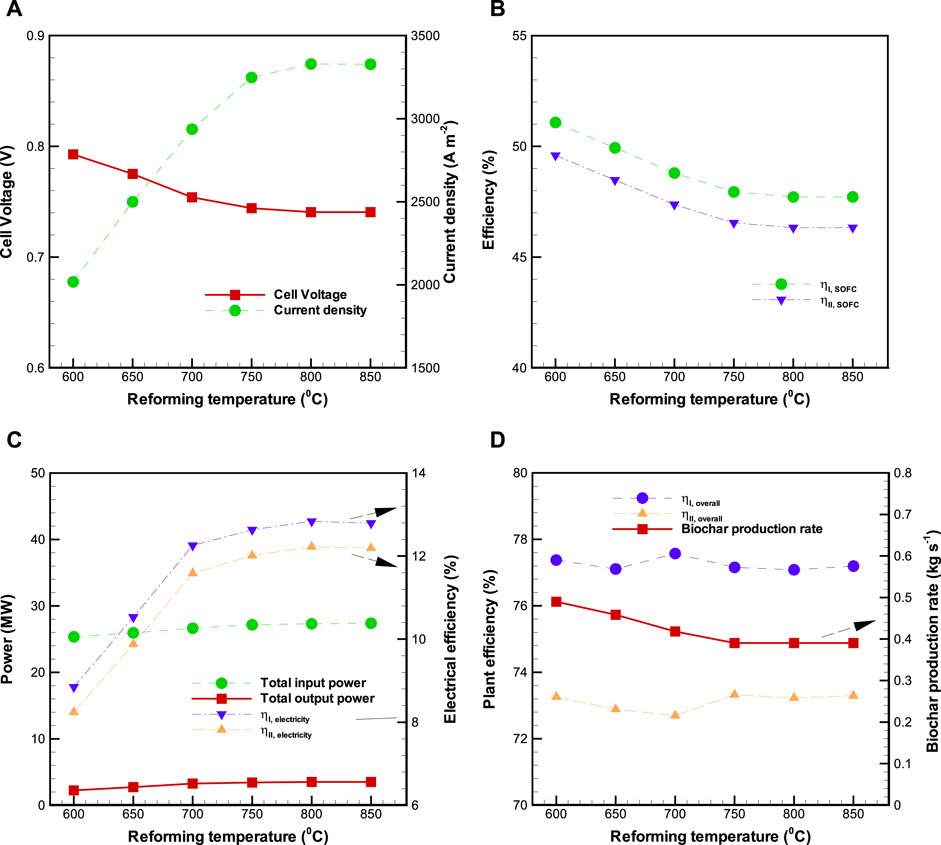
FIGURE 7. Effects of reforming temperature (
4.2.4 Effect of biochar split ratio ( )
The effect of biochar split ratio on the performance of BP-SOFC-CHP system is plotted in Figure 8, where biomass input rate,
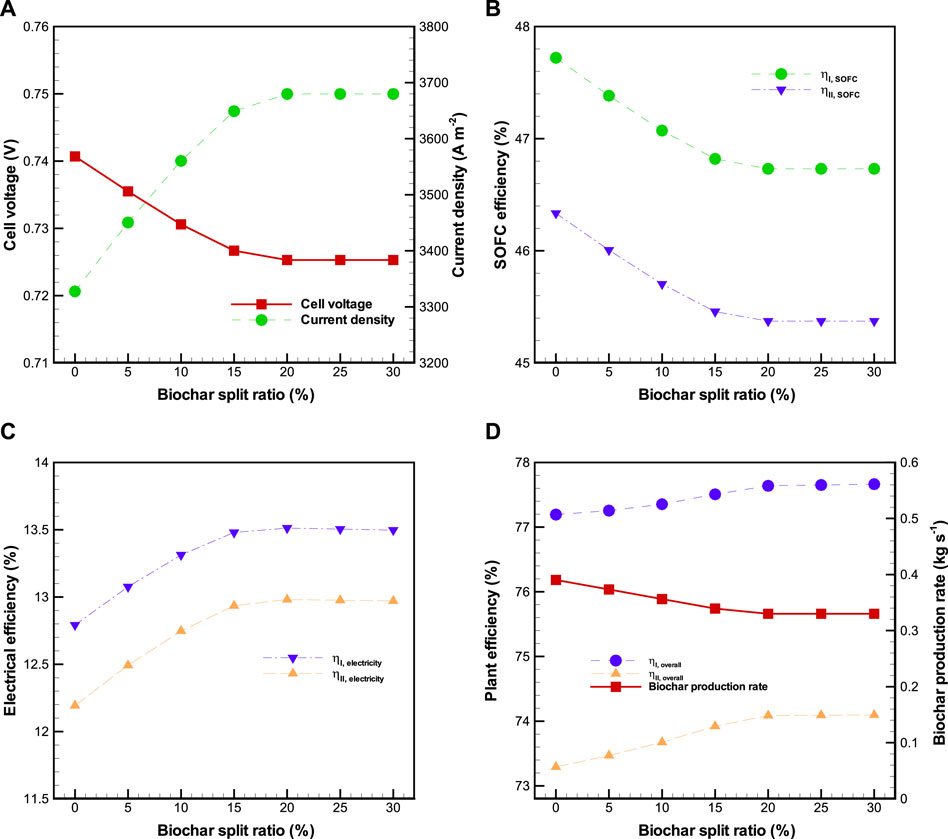
FIGURE 8. Effects of biochar split ratio (
4.3 A stand-alone design of the biomass pyrolysis-solid oxide fuel cell-combined heat and power system
In view of the endothermic reactions during biomass pyrolysis and the pyrolysis volatiles reforming processes, a stand-alone design of the BP-SOFC-CHP system for co-generation of biochar and power is eventually proposed. In order to achieve a self-sustainable process, pyrolysis gas which contained the second-highest energy content in the overall system is sent to a combustor to generate heat for the drying, heating, pyrolysis, and reforming processes. Figure 9 demonstrates the layout of the stand-alone design of the BP-SOFC-CHP system in terms of mass and energy balance, where
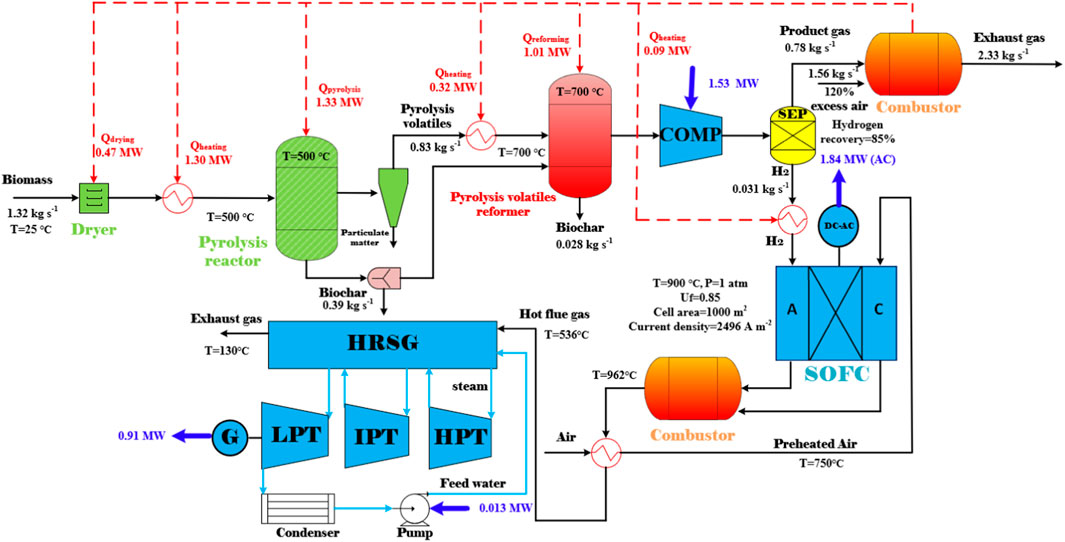
FIGURE 9. The stand-alone design of the BP-SOFC-CHP system for the co-generation of biochar and electricity.
5 Conclusions and future work
A novel integrated BP-SOFC-CHP system for the co-generation of biochar and power is developed and its performance is examined through a thermodynamic analysis. Parametric analysis carried out on the BP-SOFC-CHP system has highlighted the following conclusions:
1) Based on variation in operating parameters including current density (
2) Varying
3) Varying
4) Additional carbon formation from the pyrolysis volatiles reforming unit is observed when the
5) Based on biomass fuel input of 1.32 kg s−1,
6) According to energy balance, with a hydrogen recovery rate of 85% from the hydrogen separation unit, it is possible to operate a stand-alone BP-SOFC-CHP system by burning the pyrolysis gas. Such a self-sustainable design of the BP-SOFC-CHP system can yield the
Based on the above simulation results in view of thermodynamic evaluations, it is concluded that the developed BP-SOFC-CHP system not only offers high system energy efficiency (64%), but also generates a biochar yield of at least 30%, which can be further utilized in various fields. Such a novel integrated system is therefore helpful for developing the negative emissions technologies in the near future. However, to further investigate the technical feasibility of the proposed system, the following remarks should be explored in future work: 1) evaluate and identify a suitable hydrogen separation technology and integrate it with this system, and 2) an in-depth techno-economic analysis and a life cycle analysis from the economic and environmental perspective should be carried out.
Data availability statement
The original contributions presented in the study are included in the article/supplementary material, further inquiries can be directed to the corresponding author.
Author contributions
P-CK and BI: investigation, conceptualization, writing—original draft, writing—review and editing FO: writing—review and editing P-CK, TW, and PA: conceptualization, writing—review and editing, supervision.
Funding
The authors also acknowledge the financial support of Ministry of National Education, Turkey and Japan Society for the Promotion of Science under Grant No. JP-22F21041.
Acknowledgments
The authors would like to thank Chaitanya Joglekar, Energy and Sustainability Research Institute Groningen, University of Groningen, the Netherlands for his extensive support in reviewing the manuscript and fruitful discussions in our research work.
Conflict of interest
The authors declare that the research was conducted in the absence of any commercial or financial relationships that could be construed as a potential conflict of interest.
Publisher’s note
All claims expressed in this article are solely those of the authors and do not necessarily represent those of their affiliated organizations, or those of the publisher, the editors and the reviewers. Any product that may be evaluated in this article, or claim that may be made by its manufacturer, is not guaranteed or endorsed by the publisher.
References
Abrego, J., Plaza, D., Luno, F., Atienza-Martinez, M., and Gea, G. (2018). Pyrolysis of cashew nutshells: Characterization of products and energy balance. Energy 158, 72–80. doi:10.1016/j.energy.2018.06.011
AlNouss, A., Parthasarathy, P., Shahbaz, M., Al-Ansari, T., Mackey, H., and McKay, G. (2020). Techno-economic and sensitivity analysis of coconut coir pith-biomass gasification using ASPEN PLUS. Appl. Energy 261, 114350. doi:10.1016/j.apenergy.2019.114350
Aravind, P. V., Woudstra, T., Woudstra, N., and Spliethoff, H. (2009). Thermodynamic evaluation of small-scale systems with biomass gasifiers, solid oxide fuel cells with Ni/GDC anodes and gas turbines. J. Power Sources 190, 461–475. doi:10.1016/j.jpowsour.2009.01.017
Arregi, A., Amutio, M., Lopez, G., Artetxe, M., Alvarez, J., Bilbao, J., et al. (2017). Hydrogen-rich gas production by continuous pyrolysis and in-line catalytic reforming of pine wood waste and HDPE mixtures. Energy Convers. Manag. 136, 192–201. doi:10.1016/j.enconman.2017.01.008
Ayodele, B. V., Mustapa, S. I., Tuan Abdullah, T. A. R. B., and Salleh, S. F. (2019). A mini-review on hydrogen-rich syngas production by thermo-catalytic and bioconversion of biomass and its environmental implications. Front. Energy Res. 7, 118. doi:10.3389/fenrg.2019.00118
Baldinelli, A., Cinti, G., Desideri, U., and Fantozzi, F. (2016). Biomass integrated gasifier-fuel cells: Experimental investigation on wood syngas tars impact on NiYSZ-anode Solid Oxide Fuel Cells. Energy Convers. Manag. 128, 361–370. doi:10.1016/j.enconman.2016.09.048
Chen, T., Liu, R., and Scott, N. R. (2016). Characterization of energy carriers obtained from the pyrolysis of white ash, switchgrass and corn stover-Biochar, syngas and bio-oil. Fuel Process. Technol. 142, 124–134. doi:10.1016/j.fuproc.2015.09.034
Chiodo, V., Galvagno, A., Lanzini, A., Papurello, D., Urbani, F., Santarelli, M., et al. (2015). Biogas reforming process investigation for SOFC application. Energy Convers. Manag. 98, 252–258. doi:10.1016/j.enconman.2015.03.113
Cohce, M. K., Dincer, I., and Rosen, M. A. (2010). Thermodynamic analysis of hydrogen production from biomass gasification. Int. J. Hydrogen Energy 35, 4970–4980. doi:10.1016/j.ijhydene.2009.08.066
Cong, H., Masek, O., Zhao, L., Yao, Z., Meng, H., Hu, E., et al. (2018). Slow pyrolysis performance and energy balance of corn stover in continuous pyrolysis-based poly-generation systems. Energy fuels. 32, 3743–3750. doi:10.1021/acs.energyfuels.7b03175
Dechapanya, W., Rattanahirun, S., and Khamwichit, A. (2020). Syngas production from palm kernel shells with enhanced tar removal using biochar from agricultural residues. Front. Energy Res. 8, 157. doi:10.3389/fenrg.2020.00157
Detchusananard, T., Sharma, S., Marechal, F., and Arpornwichanop, A. (2019). Multi-objective optimization of sorption enhanced steam biomass gasification with solid oxide fuel cell. Energy Convers. Manag. 182, 412–429. doi:10.1016/j.enconman.2018.12.047
Din, Z. U., and Zainal, Z. A. (2016). Biomass integrated gasification–SOFC systems: Technology overview. Renew. Sustain. Energy Rev. 53, 1356–1376. doi:10.1016/j.rser.2015.09.013
Doherty, W., Reynolds, A., and Kennedy, D. (2010). Computer simulation of a biomass gasification-solid oxide fuel cell power system using Aspen Plus. Energy 35, 4545–4555. doi:10.1016/j.energy.2010.04.051
Emun, F., Gadalla, M., Majozi, T., and Boer, D. (2010). Integrated gasification combined cycle (IGCC) process simulation and optimization. Comput. Chem. Eng. 34, 331–338. doi:10.1016/j.compchemeng.2009.04.007
Fuss, S., and Johnsson, F. (2021). The BECCS implementation gap-A Swedish case study. Front. Energy Res. 8, 553400. doi:10.3389/fenrg.2020.553400
Hanak, D. P., Jenkins, B. G., Kruger, T., and Manovic, V. (2017). High-efficiency negative-carbon emission power generation from integrated solid-oxide fuel cell and calciner. Appl. Energy 205, 1189–1201. doi:10.1016/j.apenergy.2017.08.090
He, X. (2021). A novel hybrid digestion-gasification process integrated with membranes for efficient conversion of biomass to bio-alcohols. Green Energy & Environ. 6, 15–21. doi:10.1016/j.gee.2020.04.003
Hou, Q., Zhao, H., and Yang, X. (2018). Thermodynamic performance study of the integrated MR-SOFC-CCHP system. Energy 150, 434–450. doi:10.1016/j.energy.2018.02.105
Lee, J., Kim, K. H., and Kwon, E. E. (2017). Biochar as a catalyst. Renew. Sustain. Energy Rev. 77, 70–79. doi:10.1016/j.rser.2017.04.002
Lee, K., H., and Strand, R. K. (2009). SOFC cogeneration system for building applications, part 1: Development of SOFC system-level model and the parametric study. Renew. Energy 34, 2831–2838. doi:10.1016/j.renene.2009.04.010
Liu, M., Aravind, P. V., Woudstra, T., Cobas, V. R. M., and Verkooijen, A. H. M. (2011). Development of an integrated gasifier-solid oxide fuel cell test system: A detailed system study. J. Power Sources 196, 7277–7289. doi:10.1016/j.jpowsour.2011.02.065
Liu, M., Kleij, A. van der., Verkooijen, A. H. M., and Aravind, P. V. (2013). An experimental study of the interaction between tar and SOFCs with Ni/GDC anodes. Appl. Energy 108, 149–157. doi:10.1016/j.apenergy.2013.03.020
Manyà, J. J., Azuara, M., and Manso, J. A. (2018). Biochar production through slow pyrolysis of different biomass materials: Seeking the best operating conditions. Biomass Bioenergy 117, 115–123. doi:10.1016/j.biombioe.2018.07.019
Mehrpooya, M., Ghorbani, B., and Abedi, H. (2020). Biodiesel production integrated with glycerol steam reforming process, solid oxide fuel cell (SOFC) power plant. Energy Convers. Manag. 206, 112467. doi:10.1016/j.enconman.2020.112467
Mojaver, P., Abbasalizadeh, M., Khalilarya, S., and Chitsaz, A. (2020b). Co-generation of electricity and heating using a SOFC-ScCO2 Brayton cycle-ORC integrated plant: Investigation and multi-objective optimization. Int. J. Hydrogen Energy 35, 4970–4980.
Mojaver, P., Khalilarya, S., Chitsaz, A., and Assadi, M. (2020a). Multi-objective optimization of a power generation system based SOFC using Taguchi/AHP/TOPSIS triple method. Sustain. Energy Technol. Assessments 38, 100674. doi:10.1016/j.seta.2020.100674
Ozcan, H., and Dincer, I. (2014). Thermodynamic analysis of a combined chemical looping-based trigeneration system. Energy Convers. Manag. 85, 477–487. doi:10.1016/j.enconman.2014.06.011
Rafiq, M. K., Bachmann, R. T., Rafiq, M. T., Shang, Z., Joseph, S., and Joseph, R. (2016). Influence of pyrolysis temperature on physico-chemical properties of corn stover (Zea mays L.) biochar and feasibility for carbon capture and energy balance. PLoS One 11, e0156894. doi:10.1371/journal.pone.0156894
Recalde, M., Woudstra, T., and Aravind, P. V. (2019). Gasifier, solid oxide fuel cell integrated systems for energy production from wet biomass. Front. Energy Res. 7, 129. doi:10.3389/fenrg.2019.00129
Rosha, P., Kumar, S., and Ibrahim, H. (2022). Sensitivity analysis of biomass pyrolysis for renewable fuel production using Aspen Plus. Energy 247, 123545. doi:10.1016/j.energy.2022.123545
Saidur, R., BoroumandJazi, G., Mekhilef, S., and Mohammed, H. A. (2012). A review on exergy analysis of biomass based fuels. Renew. Sustain. Energy Rev. 16, 1217–1222. doi:10.1016/j.rser.2011.07.076
Spallina, V., Nocerino, P., Romano, M. C., Annaland, M. V. S., Campanari, S., and Gallucci, F. (2018). Integration of solid oxide fuel cell (SOFC) and chemical looping combustion (CLC) for ultra-high efficiency power generation and CO2 production. Int. J. Greenh. Gas Control 71, 9–19. doi:10.1016/j.ijggc.2018.02.005
Taufiq, B. N., Kikuchi, Y., Ishimoto, T., Honda, K., and Koyama, M. (2015). Conceptual design of light integrated gasification fuel cell based on thermodynamic process simulation. Appl. Energy 147, 486–499. doi:10.1016/j.apenergy.2015.03.012
Thattai, A. T., Oldenbroek, V., Schoenmakers, L., Woudstra, T., and Aravind, P. V. (2017). Towards retrofitting integrated gasification combined cycle (IGCC) power plants with solid oxide fuel cells (SOFC) and CO2 capture-A thermodynamic case study. Appl. Therm. Eng. 114, 170–185. doi:10.1016/j.applthermaleng.2016.11.167
Uroic Štefanko, A., and Leszczynska, D. (2020). Impact of biomass source and pyrolysis parameters on physicochemical properties of biochar manufactured for innovative applications. Front. Energy Res. 8, 138. doi:10.3389/fenrg.2020.00138
Wang, N., Chen, D., Arena, U., and He, P. (2017). Hot char-catalytic reforming of volatiles from MSW pyrolysis. Appl. Energy 191, 111–124. doi:10.1016/j.apenergy.2017.01.051
Weldekidan, H., Strezov, V., He, J., Kumar, R., Asumadu-Sarkodie, S., Doyi, I. N. Y., et al. (2019). Energy conversion efficiency of pyrolysis of chicken litter and rice husk biomass. Energy fuels. 33, 6509–6514. doi:10.1021/acs.energyfuels.9b01264
Xu, X., Jiang, E., Wang, M., and Xu, Y. (2015). Dry and steam reforming of biomass pyrolysis gas for rich hydrogen gas. Biomass Bioenergy 78, 6–16. doi:10.1016/j.biombioe.2015.03.015
Yaashikaa, P. R., Kumar, P. S., Varjani, S. J., and Saravanan, A. (2019). Advances in production and application of biochar from lignocellulosic feedstocks for remediation of environmental pollutants. Bioresour. Technol. 292, 122030. doi:10.1016/j.biortech.2019.122030
Yang, H., Kudo, S., Kuo, H. P., Norinaga, K., Mori, A., Masek, O., et al. (2013). Estimation of enthalpy of bio-oil vapor and heat required for pyrolysis of biomass. Energy fuels. 27, 2675–2686. doi:10.1021/ef400199z
Zhang, S., Liu, H., Liu, M., Sakaue, E., Li, N., and Zhao, Y. (2017). An efficient integration strategy for a SOFC-GT-SORC combined system with performance simulation and parametric optimization. Appl. Therm. Eng. 121, 314–324. doi:10.1016/j.applthermaleng.2017.04.066
Zhang, Y., Li, B., Li, H., and Zhang, B. (2012). Exergy analysis of biomass utilization via steam gasification and partial oxidation. Thermochim. Acta 538, 21–28. doi:10.1016/j.tca.2012.03.013
Keywords: biochar, SOFC, biomass pyrolysis, process integration, thermodynamic analysis, negative emissions technologies
Citation: Kuo P-C, Illathukandy B, Özdemir F, Woudstra T and Aravind PV (2022) Thermodynamic analysis of a novel integrated biomass pyrolysis-solid oxide fuel cells-combined heat and power system for co-generation of biochar and power. Front. Energy Res. 10:731191. doi: 10.3389/fenrg.2022.731191
Received: 26 June 2021; Accepted: 18 July 2022;
Published: 13 September 2022.
Edited by:
Amornchai Arpornwichanop, Chulalongkorn University, ThailandReviewed by:
Xuezhong He, Guangdong Technion-Israel Institute of Technology (GTIIT), ChinaParisa Mojaver, Urmia University, Iran
Copyright © 2022 Kuo, Illathukandy, Özdemir, Woudstra and Aravind. This is an open-access article distributed under the terms of the Creative Commons Attribution License (CC BY). The use, distribution or reproduction in other forums is permitted, provided the original author(s) and the copyright owner(s) are credited and that the original publication in this journal is cited, in accordance with accepted academic practice. No use, distribution or reproduction is permitted which does not comply with these terms.
*Correspondence: Po-Chih Kuo, cGNrdW8yMjVAZ21haWwuY29t