- School of Energy and Environmental Engineering, University of Science and Technology Beijing, Beijing, China
To be consistent with the actual production, this paper establishes the 2-D steady-state mathematical model of the porous media to numerically analyze influences of structural and operational parameters on the vertical cooling process by applying particle characteristic parameters, and heat transfer and resistance correlations of the multi-size sinter. Considering comprehensive effects of the temperature and pressure drop, the operating and structural parameters are optimized with the objective of the maximum income exergy of the gas. Results show that the numerical model established in this paper can well predict the gas-solid heat transfer process in the sinter bed with the maximum error of 7%. Besides, the income exergy of the gas increases and decreases with the sinter outlet temperature and gas outlet temperature increasing, respectively. The reduction in the equivalent particle diameter is conducive to improving the income exergy. What’s more, the income exergy of the gas first ascends and then descends with the increase of the flow rate ratio of gas to sinter and the height of the sinter layer. Therefore, optimal values of the flow rate ratio of the gas to sinter and the height of the sinter layer are 1,050–1,540 m3·h−1 and 7–11.5 m within the scope of this study, respectively.
Introduction
With the formulation of the double carbon strategy (Xiong et al., 2022), the industrial production should take some necessary measures, such as improving the utilization rate of the clean energy and the combustion efficiency of fossil fuels (Xu et al., 2020a; Xu et al., 2021). As the energy consumption of the iron and steel industry accounts for about 20% of the whole industry, it has become an important focus of the low-carbon development of the economy. With the gradual optimization of various processes, the efficient recovery of the waste heat has become an important way to achieve the green development for the iron and steel industry (Xu et al., 2020b), especially in the sintering process (Zhang et al., 2021a). The energy consumption of the sintering process accounts for 10–15% of the whole iron and steel industry (Zhang et al., 2013). As the horizontal structure, the sinter annular cooling process has inevitable shortcomings, making the utilization rate of the waste heat less than 30% (Zhang, 2022). Therefore, the sinter vertical cooling process is proposed by imitating the coke dry quenching process (Sun et al., 2015), as shown in Figure 1. The new process as the vertical structure not only reduces the air leakage rate, but also improves the gas-solid heat transfer efficiency. Thus, the recovery rate and the quality of the waste heat are improved from 30% to 80% and from 150 to 350°C to 450–550°C, respectively (Zhang, 2022).
At present, the test run indicates that the improvement effect of the waste heat recovery is lower than the expected target (Bi and Sun, 2018), which is attributed to the unreasonable design of operating parameters and structural parameters. To popularize the new technology in the iron and steel field, a lot of researches have been done on pressure drop characteristics, heat transfer characteristics and the numerical optimization of the new process. Moreover, the research on pressure drop characteristics and heat transfer characteristics of the sinter has been very mature, fitting the corresponding empirical correlations. In previous studies, the pressure drop correlation of the sinter was modified by considering the effects of the particle shape (Feng et al., 2015a; Tian et al., 2016a), bed voidage (Feng et al., 2015b), equivalent particle diameter (Feng et al., 2014), confined wall (Tian et al., 2016b; Feng et al., 2019; Zhang et al., 2022a) and particle size distribution (Pan et al., 2015; Tian et al., 2016c; Zhang et al., 2021b). The results showed that the pressure drop had a linear relationship with the height of the material layer, increased in a quadratic relationship with the increase of the gas velocity, and declined exponentially with the increase of the equivalent particle diameter and bed voidage or the decrease of the shape factor. In addition, Tian et al. (Tian et al., 2016b) found that the influence of the confined wall can be neglected when the diameter ratio of bed to particle was larger than 19. When the diameter ratio of bed to particle was less than 19, the wall effect played a dominant role, reducing the pressure drop of the gas in the bed. Zhang et al. (Zhang et al., 2022a) also found that the wall effect would only reduce the pressure drop no matter what the gas flow state was. Moreover, the more irregular the sinter particles were, the weaker the wall effect was. What’s more, the research of Tian et al. (Tian et al., 2016c) showed that the resistance coefficient of the binary-size sinter was larger than that of the mono-size sinter, and the turbulent degree of the gas flow was more significant. Furthermore, Pan et al. (Pan et al., 2015) found that the 17% increase in the proportion of small particles (0–10 mm) in the sinter mixture caused the pressure drop to increase by 2–3 times. The study of Zhang et al. (Zhang et al., 2021b) also indicated that the change of the pressure drop in the multi-size sinter bed with the equivalent particle diameter was completely different from that in the mono-size sinter bed. The decreasing amplitude of the pressure drop for the multi-size sinter ascended first and then descend with the increase of the equivalent particle diameter. Also, the bed permeability of the multi-size sinter was lower than that of the mono-size sinter under the same equivalent particle diameter. In addition, the layered distribution mode of dividing the wide particle size into the narrow particle size was conducive to reducing the pressure drop (Zhang, 2022).
What’s more, previous studies (Jang and Chiu, 2009; Pan et al., 2015; Feng et al., 2016a; Liu et al., 2016; Zheng et al., 2019; Zhang, 2021; Zhang et al., 2022b) showed that the gas-solid heat transfer intensity increased with the increase of the gas velocity, bed height and sinter velocity or the decrease of the particle size. Among them, the gas velocity and the particle size had the most significant influence (Zheng et al., 2019). Additionally, Zheng et al. (Zheng et al., 2019) obtained the heat transfer coefficient of the mono-size sinter by the logarithmic mean temperature difference method based on the moving bed, and fitted it into the heat transfer correlation by the dimensionless method. It was also found that the change trend of the measured heat transfer coefficient with the Reynolds number was similar to that of the predicted value calculated by Wakao et al. (Wakao et al., 1979). However, the irregular shape of the sinter led to the large deviation in the value. Besides, Feng et al. (Feng et al., 2016a) measured the gas temperature at the inlet and outlet of the sinter fixed bed. The arithmetic mean value of them was taken as the mean temperature of the whole bed. Then the logarithmic mean temperature difference method was used to obtain the heat transfer correlation of the mono-size sinter. Based on the heat-mass transfer analogy method, Liu et al. (Liu et al., 2016) applied the naphthalene sublimation technology to obtain the heat transfer coefficient of the mono-size sinter, and found that it was about 40% lower than the predicted value of previous correlations (Wakao et al., 1979). By combining experimental and numerical methods, Jang et al. (Jang and Chiu, 2009) fitted the heat transfer correlation of the mono-size sinter for the cross-flow heat transfer mode of the annular cooling process. In addition, Pan et al. (Pan et al., 2015) showed that the heat transfer performance of the sinter mixture with 17% small particles was lower than that of the sinter mixture without small particles. This indicated that widening the range of the particle size distribution was not conducive to the gas-solid heat transfer. Therefore, Zhang et al. (Zhang, 2021) considered the influence of the particle size distribution to obtain the heat transfer correlation of the multi-size sinter by using the inverse problem method (Zhang et al., 2022b), which was more consistent with the actual heat transfer law. Besides, the heat transfer performance of the multi-size sinter was lower than that of the mono-size sinter, which was attributed to the heterogeneous stacking structure (Zhang, 2021).
The above experimental studies on pressure drop and heat transfer characteristics lay a foundation for the numerical study of the sinter vertical cooling process. First of all, Dong et al. (Dong et al., 2012) showed that the flow rate ratio of gas to sinter and the height of the material layer were the most significant parameters affecting the waste heat recovery. It was also found that the gas exergy had a maximum value with the change of the flow rate ratio of gas to sinter and the height of the material layer. This indicated that these two parameters had an optimal value. However, the empirical correlation of the coke was used for the calculation of the heat transfer coefficient. The meaning of the gas exergy and geometric parameters of the sinter were not also clarified. Considering the combined effect of the temperature and pressure drop, Zhang et al. (Zhang et al., 2019) found that the most significant parameter affecting the dimensionless exergy consumption was the bed diameter, followed by the gas flow rate, bed height and sinter flow rate. However, the pressure drop and temperature fields were numerically predicted by the pressure drop and heat transfer correlations and particle characteristic parameters of the mono-size sinter. Feng et al. (Feng et al., 2016b; Feng et al., 2020) also only applied the heat transfer and pressure drop correlations of the mono-size sinter to optimize the structural and operating parameters of the vertical cooling process. When only considering the influence of the temperature on the gas exergy, the optimal values of the bed diameter, bed height, and gas flow rate for the sinter with an annual output of 3.9 million tons were 10 m, 8 m, 150 kg·s−1, respectively (Feng et al., 2016b). Based on the comprehensive influence of the temperature and pressure drop, the optimal values of the bed diameter, bed height, and gas flow rate for an annual output of 3.9 million tons are 9 m, 8 m, 180 kg·s−1, respectively (Feng et al., 2020). This indicated that the optimization results would change with different optimization objectives. However, the pressure drop determined the energy consumption and gas flow characteristics, which affected the gas-solid heat transfer process and the gas outlet temperature. Moreover, the heights of the material layer in the vertical cooler and the annular cooler were 7–10 m (Feng et al., 2016b; Zhang et al., 2019; Feng et al., 2020) and .8–1.5 m (Liu et al., 2014; Feng et al., 2016c), respectively. The difficulty of the gas flowing through the vertical cooler was much higher than that of the annular cooler. It further indicated that the effect of the pressure drop on the waste heat recovery could not be ignored.
It can be seen that previous numerical studies did not consider the influence of the particle size distribution, and only applied pressure drop and heat transfer correlations of the mono-size sinter to investigate the vertical cooling process. This was inconsistent with the multi-size distribution characteristic in the actual production (Tian et al., 2016a; Zhang et al., 2021b). Moreover, previous studies (Pan et al., 2015; Tian et al., 2016c; Zhang et al., 2021b; Zhang, 2021) showed that the heat transfer performance and pressure drop of the multi-size sinter were lower and higher than those of the mono-size sinter, respectively. In addition, Koekemoer et al. (Koekemoer and Luckos, 2015) and Rong et al. (Rong et al., 2014) showed that the wide particle size distribution enhanced the inhomogeneity of the local structure and gas flow. Byon et al. (Byon and Kim, 2013) found that the permeability decreased in a quasi-linear relationship with the particle size range broadening. Keyser et al. (Keyser et al., 2006) also indicated that the wider the particle size distribution, the greater the pressure drop in the bed, and the more uneven the distribution of the gas flow. Wu et al. (Wu et al., 2016) found that the viscous and inertial resistance coefficients were totally different under the uniform and non-uniform particles. What’s more, Yang et al. (Yang et al., 2016) showed that the flow and temperature fields under the uniform and non-uniform particles were different. Besides, the heat transfer performance of non-uniform particles was significantly lower than that of uniform particles (Yang et al., 2012). This was attributed to that the pressure drop and heat transfer performance under the ordered packing mode was lower and better than those under the disordered packing mode, respectively (Wang et al., 2018).
The above studies prove that the particle size distribution affects the uniformity of the packed structure and gas flow, determining heat transfer and pressure drop characteristics. Therefore, this paper established a 2-D steady-state porous medium model to numerically analyze the influence of operating and structural parameters on the outlet temperature and pressure drop by using the heat transfer and pressure drop correlations of the multi-size sinter. Considering the comprehensive influence of the temperature and pressure drop, the optimization is carried out with the objective of the maximum income exergy of the gas, providing the theoretical reference for the engineering practice.
Establishment of numerical methods
Assumptions and physical models
During the sinter cooling process, the countercurrent convection heat transfer between the hot sinter and the cooling air is essentially carried out in the porous medium formed by the accumulation of sinter particles. To facilitate the study, the following assumptions are made (Feng et al., 2016b).
(1) Under the stable operation, the temperature in the vertical furnace basically does not change with the time, which can be regarded as a steady heat transfer process.
(2) As the size of the sinter is much smaller than that of the vertical furnace, the sinter layer can be seen as the homogeneous porous media.
(3) On the basis of ignoring the air hood, it is considered that the inner diameters of the inlet and outlet of the cooling section are the same.
(4) The sinter and gas only flow evenly along the vertical direction, ignoring the circumferential and radial velocities and the circumferential heat transfer.
(5) There is the local thermal non-equilibrium between the sinter and gas, which transfers the heat through the forced convection.
Based on the above assumptions, the cooling section of the vertical furnace can be simplified as a two-dimensional physical model, as shown in Figure 2.
Mathematical model
Based on the reasonable assumptions, this paper establishes a two-dimensional steady-state mathematical model of the porous media.
(1) Energy equation of the gas
where r and z are the axial direction and radial direction of the material layer, respectively, m;
(2) Energy equation of the sinter
where
where
where
where
The boundary conditions set for the gas-solid energy equation are described as:
(i) Boundary conditions of the gas
where
(ii) Boundary conditions of the sinter
where
(3) Momentum equation
In our previous work (Zhang et al., 2021b), the empirical correlation of the pressure drop for the multi-size sinter was obtained through the experimental method. Based on the above assumptions, this paper uses the pressure drop equation instead of the momentum equation, as follows:
where
Solution method and verification of the mesh independence
The solution method of the numerical model consists of three steps, which are the discretization of meshes, discretization of the differential energy equation and solution of the algebraic equation system, respectively (Zhang et al., 2022b). Firstly, the physical model is meshed by the external node method to determine the node position and mesh element. What’s more, the differential energy equations of the gas and solid for each mesh element are discretized into the algebraic equation by using the control volume method. By sorting out the discrete equation of each mesh element, two sets of tridiagonal algebraic equation systems on the gas temperature and solid temperature can be obtained. The initial value of the gas and solid temperature is assigned by reasonable assumptions. Based on the assumptions, two sets of algebraic equation systems are solved by the tridiagonal matrix algorithm, obtaining the new value of the temperature. Based on the new value, the tridiagonal matrix algorithm is used to solve the algebraic equation system repeatedly until the temperature difference between the two results is less than 10−3. Finally, this paper uses the computer language C# to write the program to realize the above algorithm and calculation process.
To obtain the solution independent of meshes, two limiting conditions are selected in this paper with the equivalent particle diameter
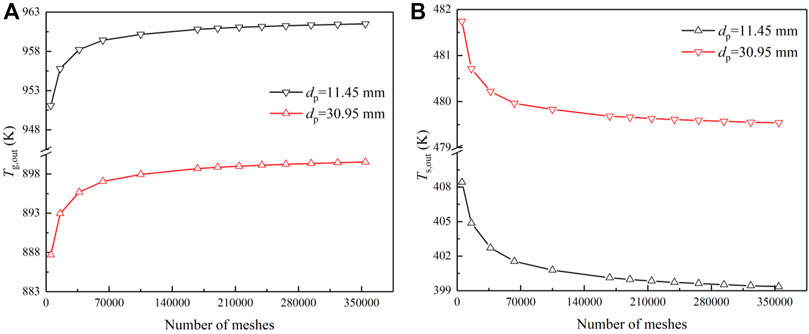
FIGURE 3. Variation of the temperature with the number of meshes: (A) Outlet temperature of the gas
Verification of the numerical model
At present, there are few successful cases of the sinter vertical cooling technology applied in the engineering. Therefore, this paper applies the pilot experimental data of three kinds of the mono-size sinters in Ref (Dong, 2015). to verify the accuracy of the numerical model. The particle sizes of three kinds of the mono-size sinter are 5–10 mm, 10–15 mm and 15–20 mm, respectively. The height of the material layer is 0.4 m. The inlet temperatures of the sinter and gas are 873 K and 293 K, respectively. The moving speed of the sinter is 0.95 mm s−1. The gas flow velocities are 1.38, 1.58, 1.73 and 1.92 m s−1, respectively. According to the above conditions, the sinter outlet temperature
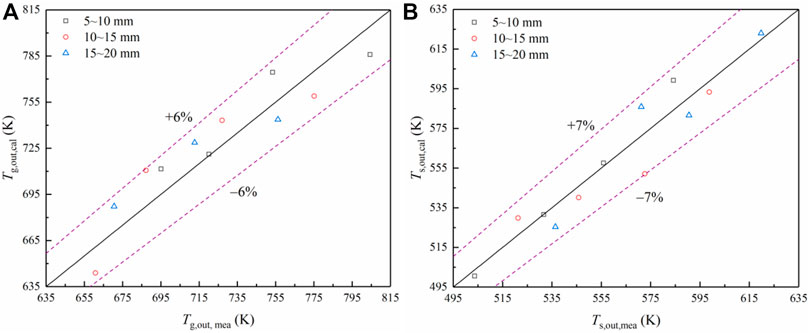
FIGURE 4. (A) Comparison between predicted values
Basic parameters and optimization criteria of the vertical cooling process
Basic parameters of the vertical cooling process
Based on the production site, the process parameters and particle characteristic parameters applied in the numerical model are designed and measured so as to provide the effective guidance. First of all, the structure parameters and operating parameters set in the numerical study are from the production site of HBIS Group Co., Ltd., as shown in Table 1. Moreover, five batches of the sinter mixture are selected from the sintering production site. From our previous work (Zhang et al., 2021b), it can be seen that the sinter with the particle size of 5–60 mm accounts for more than 85% of the total weight. Therefore, this paper studies the multi-size sinter mixture with this typical particle size, as shown in Figure 5. To adapt to the production fluctuation, six types of the multi-size sinter composed of 11 kinds the mono-size sinter are designed based on the original particle size distribution (Zhang et al., 2021b), as shown in Figure 6.
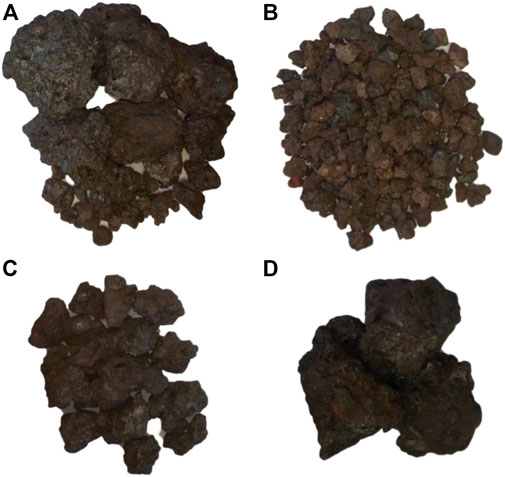
FIGURE 5. (A) Multi-size sinter of 5–60 mm; (B) Mono-size sinter of 5–10 mm; (C) Mono-size sinter of 20–25 mm; (D) Mono-size sinter of 55–60 mm.
To obtain accurate particle characteristic parameters, the thermophysical and geometric properties of the sinter are measured, respectively. First of all, the specific heat and thermal conductivity of the sinter at different temperatures are measured by the simultaneous thermal analyzer (DSC 404F3) and laser thermal conductivity instrument (LFA 467HT), which are fitted into the following equation:
For the multi-size particle composed of various mono-size irregular particles, the equivalent particle diameter
where
where
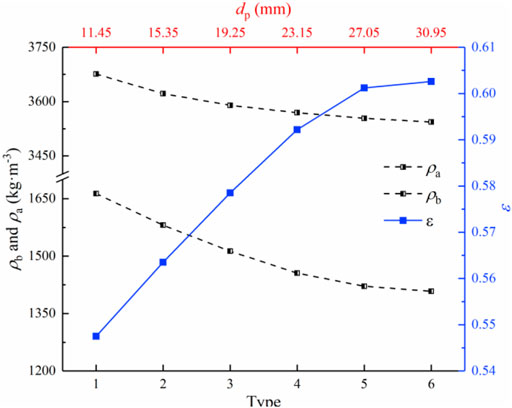
FIGURE 7. Equivalent particle diameter
In addition, Figure 8 compares the bed voidage of the mono-size and multi-size sinters under the same equivalent particle diameter. First of all, the bed voidage of the multi-size sinter is lower than that of the mono-size sinter. For the multi-size sinter, the small particles will fill the gaps between large particles, making the packing denser. In addition, the voidage difference reduces with
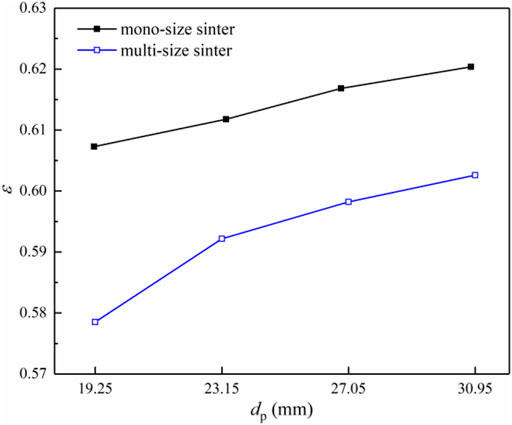
FIGURE 8. Comparison of the bed voidage
Optimization criteria of the vertical cooling process
In this paper, the exergy is applied to analyze the effect of the process parameter based on the quantity and quality of the waste heat. From the inlet to the outlet of the vertical furnace, the change of the gas exergy includes the temperature exergy
where
Based on the comprehensive influence of the temperature and pressure drop, the process parameters are numerically optimized based on the income exergy of the gas, as follows (Feng et al., 2020):
where
Results and discussion
Analysis of temperature fields in the sinter bed
The sinter vertical cooling process is calculated by the numerical model. Taking the multi-size sinter with the equivalent particle diameter of 11.45 mm as an example, Figure 9 analyses the temperature field of the sinter and gas. First of all, it is observed that the gas temperature increases from 293 K to 935.79 K from the bottom to the top of the bed. Moreover, the sinter temperature decreases from 973 K to 341.10 K from the bed top to the bed bottom. There exists the temperature difference between the gas and solid, leading to the convection heat transfer. Therefore, the cooling gas gains the amount of the heat, increasing the gas temperature. While the hot sinter loses the amount of the heat, making the sinter temperature reduce.
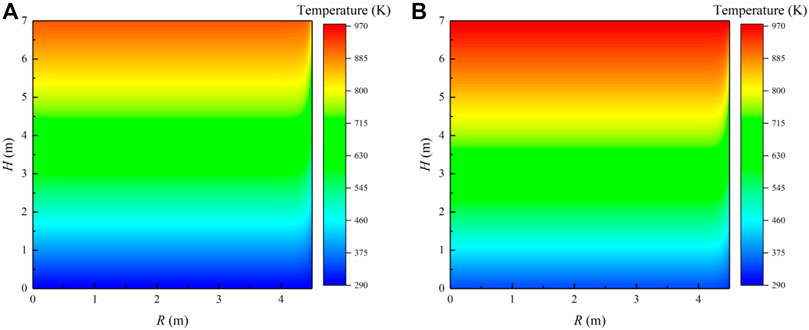
FIGURE 9. Temperature fields of the multi-size sinter bed with the equivalent particle diameter of 11.45 mm: (A) Gas; (B) Sinter.
Effect of the sinter inlet temperature on the cooling process
Figure 10 illustrates the influence of the sinter inlet temperature
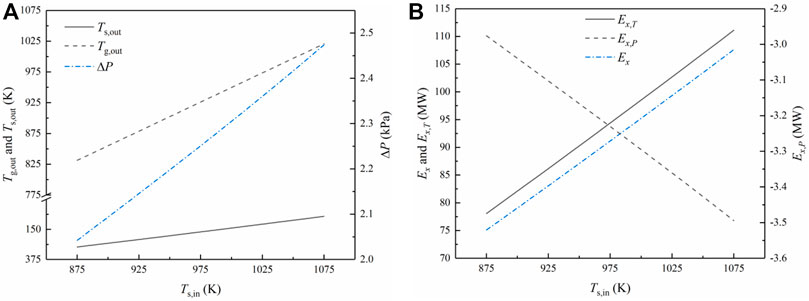
FIGURE 10. Influences of the sinter inlet temperature
Moreover, the increase of
Effect of the gas inlet temperature on the cooling process
Figure 11 illustrates the influence of the gas inlet temperature
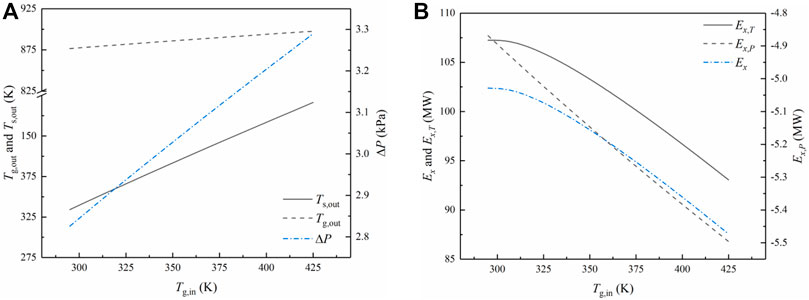
FIGURE 11. Influences of the gas inlet temperature
In addition, Figure 11B shows that the temperature exergy
Effects of the equivalent particle diameter on the cooling process
Figure 12 shows the change of the sinter outlet temperature

FIGURE 12. The influence of the equivalent particle diameter
Additionally, Figure 12B indicates that both the temperature exergy
Effect of the flow rate ratio of gas to sinter on the cooling process
The influence factors of the sinter cooling process also include the sinter flow rate and gas flow rate. Moreover, both of them have a significant impact on the gas flow rate per ton of the sinter. Thus, Figure 13 analyses the influence of the flow rate ratio of gas to sinter
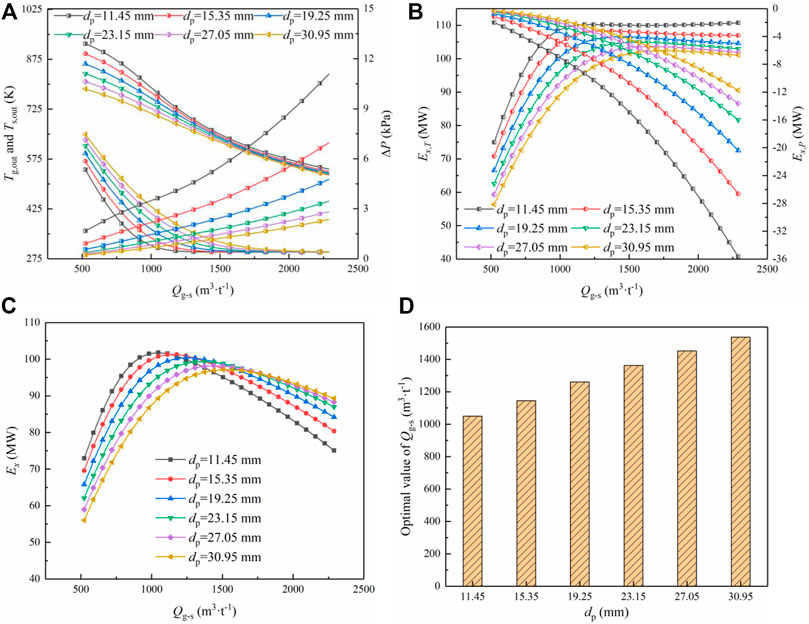
FIGURE 13. The influence of the flow rate ratio of gas to sinter
Also, the pressure drop
Figure 13B shows that the temperature exergy
Moreover, Figure 13C indicates that the income exergy
Effect of the height of the sinter layer on the cooling process
The height of the material layer also has a significant impact on the waste heat recovery. Firstly, the height of the material layer determines the time of the gas-solid heat transfer, affecting the quality and quantity of the waste heat. Secondly, the height of the material layer significantly influences the pressure drop of the gas through the bed, determining the pressure and energy consumption of the fan. Thirdly, the height of the material layer determines the height of the cooling section, affecting the construction cost. Thus, Figure 14 studies the influence of the height of the material layer H on the sinter outlet temperature
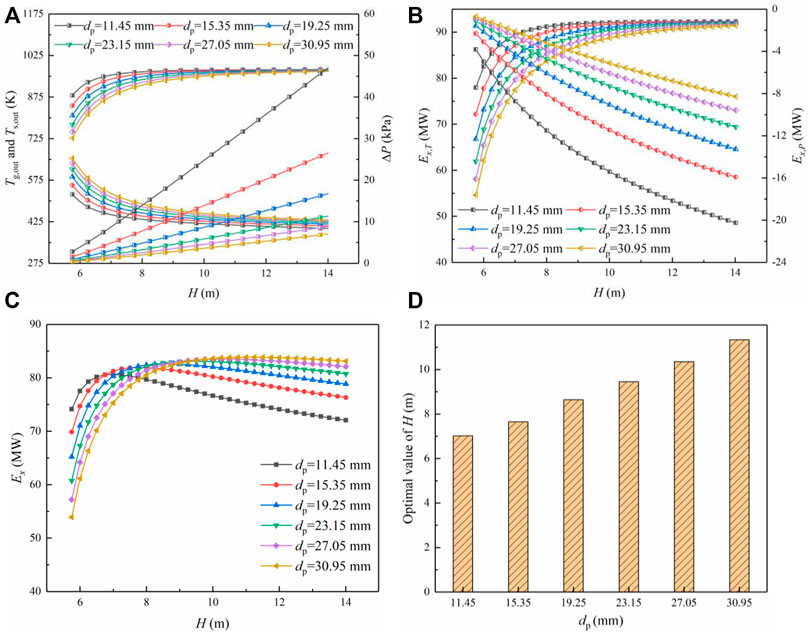
FIGURE 14. The influence of the height of the sinter layer H on the vertical cooling process under different multi-size sinters: (A) Change of the sinter outlet temperature
Figure 14A shows that both
It can be also discovered from Figure 14B that the temperature exergy
Figure 14D shows that the optimal value of H is 7–11.5 m within the scope of this study, and declines with the reduction of the equivalent particle diameter
Conclusion
To realize the dual carbon strategy in the iron and steel industry, it is necessary to study the vertical waste heat recovery technology of the sinter. At present, previous numerical studies are inconsistent with the non-uniform particle size distribution in the actual production. Therefore, a 2-D steady-state numerical model is established to analyze the gas-solid heat transfer process by using the heat transfer and pressure drop correlations, and particle characteristic parameters of the multi-size sinter. Considering the effects of the pressure drop and temperature, the operating parameters and structural parameters are optimized with the objective of the income exergy.
With the increase in the sinter inlet temperature
With the flow rate ratio of gas to sinter
Data availability statement
The original contributions presented in the study are included in the article/Supplementary Material, further inquiries can be directed to the corresponding author.
Author contributions
SZ: Writing-Original Draft, Investigation. LH: Writing-Review and Editing. XL: Supervision. HW: Conceptualization.
Acknowledgments
This work is supported by Fundamental Research Funds for the Central Universities (FRF-TP-22-077A1).
Conflict of interest
The authors declare that the research was conducted in the absence of any commercial or financial relationships that could be construed as a potential conflict of interest.
Publisher’s note
All claims expressed in this article are solely those of the authors and do not necessarily represent those of their affiliated organizations, or those of the publisher, the editors and the reviewers. Any product that may be evaluated in this article, or claim that may be made by its manufacturer, is not guaranteed or endorsed by the publisher.
References
Bi, C., and Sun, J. (2018). Application of process to recycle sensible heat of sinter using vertical cooling furnace in Meisteel. Sinter. Pelletizing 43 (4), 69. (in Chinese). doi:10.13403/j.sjqt.2018.04.061
Byon, C., and Kim, S. J. (2013). The effect of the particle size distribution and packing structure on the permeability of sintered porous wicks. Int. J. Heat. Mass Transf. 61, 499–504. doi:10.1016/j.ijheatmasstransfer.2013.02.025
Dong, H. (2015). Experimental study on gas-solid heat transfer coefficient of layer in vertical tank for recovering sintering waste heat in some working conditions. Shenyang: Northeastern University. (Dissertation of Master Degree).
Dong, H., Li, L., Cai, J., and Li, J. (2012). Numerical simulation of heat exchange in vertical tank of waste heat recovery. J. Northeast. Univ. Nat. Sci. 33 (9), 1299–1302. (in Chinese). doi:10.12068/j.issn.1005-3026.2012.09.020
Feng, H., Chen, L., Liu, X., Xie, Z., and Sun, F. (2016). Constructal optimization of a sinter cooling process based on exergy output maximization. Appl. Therm. Eng. 96, 161–166. doi:10.1016/j.applthermaleng.2015.11.089
Feng, J., Dong, H., and Dong, H. (2015). Modification of Ergun’s correlation in vertical tank for sinter waste heat recovery. Powder Technol. 280, 89–93. doi:10.1016/j.powtec.2015.04.033
Feng, J., Dong, H., Gao, J., Li, H., and Liu, J. (2016). Numerical investigation of gas-solid heat transfer process in vertical tank for sinter waste heat recovery. Appl. Therm. Eng. 107, 135–143. doi:10.1016/j.applthermaleng.2016.06.175
Feng, J., Dong, H., Gao, J., Liu, J., and Liang, K. (2016). Experimental study of gas-solid overall heat transfer coefficient in vertical tank for sinter waste heat recovery. Appl. Therm. Eng. 95, 136–142. doi:10.1016/j.applthermaleng.2015.11.058
Feng, J., Dong, H., Li, M., and Cai, J. (2014). Resistance characteristics of fixed bed layer in vertical tank for recovering sinter waste heat. J. Central South Univ. Sci. Technol. 45 (8), 2566–2571. (in Chinese).
Feng, J., Dong, H., Liu, J., Liang, K., and Gao, J. (2015). Experimental study of gas flow characteristics in vertical tank for sinter waste heat recovery. Appl. Therm. Eng. 91, 73–79. doi:10.1016/j.applthermaleng.2015.07.050
Feng, J., Zhang, S., Dong, H., and Pei, G. (2019). Frictional pressure drop characteristics of air flow through sinter bed layer in vertical tank. Powder Technol. 344, 177–182. doi:10.1016/j.powtec.2018.12.013
Feng, J., Zhao, L., Zhang, S., and Dong, H. (2020). Exergy analysis and parameter optimization of sinter cooling process in vertical moving bed for waste heat recovery. Appl. Therm. Eng. 175, 115370. doi:10.1016/j.applthermaleng.2020.115370
Jang, J., and Chiu, Y. (2009). 3-D Transient conjugated heat transfer and fluid flow analysis for the cooling process of sintered bed. Appl. Therm. Eng. 29, 2895–2903. doi:10.1016/j.applthermaleng.2009.02.012
Keyser, M. J., Conradie, M., Coertzen, M., and Van Dyk, J. C. (2006). Effect of coal particle size distribution on packed bed pressure drop and gas flow distribution. Fuel 85, 1439–1445. doi:10.1016/j.fuel.2005.12.012
Koekemoer, A., and Luckos, A. (2015). Effect of material type and particle size distribution on pressure drop in packed beds of large particles: Extending the Ergun equation. Fuel 158, 232–238. doi:10.1016/j.fuel.2015.05.036
Liu, Y., Wang, J., Cheng, Z., Yang, J., and Wang, Q. (2016). Experimental investigation of fluid flow and heat transfer in a randomly packed bed of sinter particles. Int. J. Heat. Mass Transf. 99, 589–598. doi:10.1016/j.ijheatmasstransfer.2016.03.107
Liu, Y., Yang, J., Wang, J., Cheng, Z., and Wang, Q. (2014). Energy and exergy analysis for waste heat cascade utilization in sinter cooling bed. Energy 67, 370–380. doi:10.1016/j.energy.2013.11.086
Pan, L., Wei, X., Peng, Y., Shi, X., and Liu, H. (2015). Experimental study on convection heat transfer and air drag in sinter layer. J. Cent. South Univ. 22, 2841–2848. doi:10.1007/s11771-015-2816-z
Rong, L. W., Dong, K. J., and Yu, . A. B. (2014). Lattice-Boltzmann simulation of fluid flow through packed beds of spheres: Effect of particle size distribution. Chem. Eng. Sci. 116, 508–523. doi:10.1016/j.ces.2014.05.025
Sun, K., Tseng, C., Wong, D. S., Shieh, S., Jang, S., Kang, J., et al. (2015). Model predictive control for improving waste heat recovery in coke dry quenching processes. Energy 80, 275–283. doi:10.1016/j.energy.2014.11.070
Tian, F., Huang, L., Fan, L., Qian, H., Gu, J., Yu, Z., et al. (2016). Pressure drop in a packed bed with sintered ore particles as applied to sinter coolers with a novel vertically arranged design for waste heat recovery. J. Zhejiang Univ.-SCI A 17, 89–100. doi:10.1631/jzus.A1500088
Tian, F., Huang, L., Fan, L., Qian, H., and Yu, Z. (2016). Wall effects on the pressure drop in packed beds of irregularly shaped sintered ore particles. Powder Technol. 301, 1284–1293. doi:10.1016/j.powtec.2016.07.073
Tian, F., Huang, L., Fan, L., Yu, Z., and Hu, Y. (2016). Experimental study on pressure drop of packed beds with binary sintered ore particle mixtures. J. Zhejiang Univ. Eng. Sci. 50 (11), 2077–2086. (in Chinese). doi:10.3785/j.issn.1008-973X.2016.11.006
Wakao, N., Kaguei, S., and Funazkri, T. (1979). Effect of fluid dispersion coefficients on particle-to-fluid heat transfer coefficients in packed beds: Correlation of nusselt numbers. Chem. Eng. Sci. 34 (3), 325–336. doi:10.1016/0009-2509(79)85064-2
Wang, J., Yang, J., Cheng, Z., Liu, Y., Chen, Y., and Wang, Y. (2018). Experimental and numerical study on pressure drop and heat transfer performance of grille-sphere composite structured packed bed. Appl. Energy 227, 719–730. doi:10.1016/j.apenergy.2017.07.140
Wu, G., Xing, Y., Lü, Y., Qi, H., and Li, D. (2016). Experimental analysis of resistance coefficient of oil and water flow in porous media. Exp. Technol. Manag. 33 (10), 34–37. (in Chinese). doi:10.16791/j.cnki.sjg.2016.10.010
Xiong, Y., Yao, C., Ren, J., Wu, Y., Xu, Q., Nie, B., et al. (2022). Waste semicoke ash utilized to fabricate shape-stable phase change composites for building heating and cooling. Constr. Build. Mat. 361, 129638. doi:10.1016/j.conbuildmat.2022.129638
Xu, Q., Liu, L., Feng, J., Qiao, L., Yu, C., Shi, W., et al. (2020). A comparative investigation on the effect of different nanofluids on the thermal performance of two-phase closed thermosyphon. Int. J. Heat. Mass Transf. 149, 119189. doi:10.1016/j.ijheatmasstransfer.2019.119189
Xu, Q., Wang, K., Zou, Z., Zhong, L., Akkurt, N., Feng, J., et al. (2021). A new type of two-supply, one-return, triple pipe-structured heat loss model based on a low temperature district heating system. Energy 218, 119569. doi:10.1016/j.energy.2020.119569
Xu, Q., Zou, Z., Chen, Y., Wang, K., Du, Z., Feng, J., et al. (2020). Performance of a novel-type of heat flue in a coke oven based on high-temperature and low-oxygen diffusion combustion technology. Fuel 267, 117160. doi:10.1016/j.fuel.2020.117160
Yang, J., Wang, J., Bu, S., Zeng, M., and Wang, Q. (2012). Experimental study of forced convective heat transfer in structured packed porous media of particles. J. Eng. Thermophys. 33 (5), 851–855. (in Chinese).
Yang, J., Wu, J., Zhou, Z., and Wang, Q. (2016). Computational study of fluid flow and heat transfer in composite packed beds of spheres with low tube to particle diameter ratio. Nucl. Eng. Des. 300, 85–96. doi:10.1016/j.nucengdes.2015.10.030
Zhang, S. (2022). Effects of the layered distribution pattern on the gas flow resistance through the bed with the multisize irregular particle for the waste heat recovery. Int. J. Photoenergy 2022, 1–15. doi:10.1155/2022/3727937
Zhang, S. (2021). Study on flow and heat transfer characteristics in the sinter vertical cooling process. Beijing: University of Science and Technology Beijing. (Dissertation of Doctor Degree).
Zhang, S., Wen, Z., Liu, X., Liu, X., Wang, S., and Zhang, H. (2021). Experimental study on the permeability and resistance characteristics in the packed bed with the multi-size irregular particle applied in the sinter vertical waste heat recovery technology. Powder Technol. 384, 304–312. doi:10.1016/j.powtec.2021.02.027
Zhang, S., Wen, Z., Liu, X., Xing, Y., and Zhang, H. (2022). Gas flow characteristics through irregular particle bed with the vertical confined wall for waste heat recovery. Int. J. Photoenergy 2022, 1890541–1890616. doi:10.1155/2022/1890541
Zhang, S., Wen, Z., Liu, X., Zhang, H., Liu, X., and Wang, S. (2021). Effects of particle shape on permeability and resistance coefficients of sinter packed bed. 52(4), 1066–1075. doi:10.11817/j.issn.1672-7207.2021.04.003(in Chinese)
Zhang, S., Wen, Z., Wang, G., Lou, G., and Liu, X. (2021). Kinetic analyses of coke combustion and thermal decompositions of limestone and dolomite based on the sintering atmosphere. Fuel 289, 119870. doi:10.1016/j.fuel.2020.119870
Zhang, S., Wen, Z., Xing, Y., Liu, X., Zhang, H., and Xiong, Y. (2022). Experimental study on gas-solid heat transfer characteristics for the vertical waste heat recovery using the inverse problem method. Int. J. Photoenergy 2022, 1–21. doi:10.1155/2022/4053105
Zhang, S., Zhao, L., Feng, J., Luo, X., and Dong, H. (2019). Thermal analysis of sinter vertical cooler based on waste heat recovery. Appl. Therm. Eng. 157, 113708. doi:10.1016/j.applthermaleng.2019.04.118
Zhang, X., Chen, Z., Zhang, J., Ding, P., and Zhou, J. (2013). Simulation and optimization of waste heat recovery in sinter cooling process. Appl. Therm. Eng. 54, 7–15. doi:10.1016/j.applthermaleng.2013.01.017
Keywords: operational parameter, structural parameter, multi-size, optimization, waste heat
Citation: Zhang S, Huang L, Liu X and Wang H (2023) Optimization of structural and operational parameters for the multi-size sinter vertical waste heat recovery with the objective of the income exergy. Front. Energy Res. 10:1114270. doi: 10.3389/fenrg.2022.1114270
Received: 02 December 2022; Accepted: 16 December 2022;
Published: 05 January 2023.
Edited by:
Yaxuan Xiong, Beijing University of Civil Engineering and Architecture, ChinaReviewed by:
Songhua Hao, Sichuan University, ChinaKai Xie, Weifang University of Science and Technology, China
Copyright © 2023 Zhang, Huang, Liu and Wang. This is an open-access article distributed under the terms of the Creative Commons Attribution License (CC BY). The use, distribution or reproduction in other forums is permitted, provided the original author(s) and the copyright owner(s) are credited and that the original publication in this journal is cited, in accordance with accepted academic practice. No use, distribution or reproduction is permitted which does not comply with these terms.
*Correspondence: Sizong Zhang, NTEzODY1OTA5QHFxLmNvbQ==