- Yunnan Key Laboratory of Internal Combustion Engines, Kunming University of Science and Technology, Kunming, China
Matching characteristics between fuel injection and intake control parameters significantly affect overall performances in diesel engine at variable altitudes. Prior to optimizing the control parameters of diesel engines operating at high altitudes areas, there is a necessity to identify the influence law of fuel injection and intake parameters on engine performance. This study focused on the effects of main injection timing (MIT), fuel injection pressure (FIP), EGR rate, and variable nozzle turbocharger (VNT) opening on the combustion, performances and NOx and smoke emissions in a turbocharged diesel engine at different altitudes (2000, 1,000, and 0 m). Strategies for optimization of engine performance and the coupling relationship between these parameters were analyzed. The results showed that as the altitude increased from 0 m to 2000 m, the engine torque dropped by 2.9%, the BSFC increased by 2.6%, the NOx emissions reduced by 11.8%, and the opacity smoke increased by 26.2%. The effects of MIT, FIP, EGR rate and VNT opening on engine performances were more significant at high altitudes. As the MIT was advanced at 2000 m altitude, the engine torque increased by 5.6%, the BSFC reduced by 5.9%, the opacity smoke decreased by 55%, while the NOx emissions increased by 54%%. Advance the injection timing properly can overcome the altitude effect on engine power. With the FIP increased from 105 to 130 MPa at 2000 m, the engine torque reduced by 1.7%, the BSFC increased by 1.6%, the opacity smoke dropped by 44.5%, and the NOx emissions increased by 17.5%. When the EGR rate increases by 5%, the NOx emission reduces by 16.4%,17.9 and 21.9 respectively at 0, 1,000 and 2000 m altitude. The EGR rate should be properly reduced to obtain the recovery of engine power at plateau. As the VNT vane opening decreased from 40% to 20%, the NOx emission increase by 9.4% and 9.9% at 0 m and 1,000 m respectively, and it reduces by 3.9% at 2000 m, while the opacity smoke reduces by 38.9% at different altitudes. The optimization of VNT vane opening requires a balance between combustion performance and pumping losses. The multi-objective collaborative optimization technique should be applied to optimize these parameters to help improve engine efficiency and emissions at high altitudes.
1 Introduction
The European energy policies for air quality protection has led to the inclusion of type-approval real driving emission (RDE) tests for passenger car and light duty vehicles that must consider the ambient temperature and driving altitude as boundary conditions (Piqueras et al., 2022). The latest China VI emission standard of light-duty diesel vehicles call for a reduction of 86% for nitrogen oxides (NOx) emission, and the RDE tests extended ambient conditions to 2,400 altitude (Zhang H et al., 2020). However, when the altitude increases, the air pressure and density will decrease (Fang et al., 2022; Zhang C et al., 2022). The mismatch between air and diesel quantities caused by the high-altitude atmosphere led to the engine combustion deterioration (Liu et al., 2022). Diesel engines operating at plateau will face problems such as power dropping, higher fuel consumption, and worse emissions due to lower intake mass air flow (Giraldo and Huertas 2019). Worsened spray formation and mixture preparation, together with insufficient and late oxidation at high altitudes, resulting in reduced engine efficiency, increased emissions, and power loss (Liu and Liu, 2022a). And the bulk temperature was higher at high altitudes because of less mass of the mixture trapped in the cylinder (Liu and Liu, 2022b). There are many plateau regions in Latin America with high altitude up to 1,000 m above the sea level. In China, most of the cities are located at high altitude (>1,500 m) and have very high traffic density with high road grades (Wang et al., 2021). Consequently, there are many vehicles, agricultural and construction facilities, military equipment are working in these plateau areas indicate the need to concern engines operating at high altitudes.
Previous work on the high-altitude performances of diesel engines were mainly focused on the power recovery, turbocharger matching and performance optimization. Turbocharged diesel engines can partially compensate the decrease of the intake pressure at high altitude and improve combustion performance (Huang et al., 2020; Liu et al., 2023). Zhang S et al. (2020) found that the regulation ability of two-stage turbocharger increases as altitudes rise and provides less excess air coefficient with constant regulation area. Output torque and fuel consumption can be improved below 2000 m with reasonable regulation area due to greater overall efficiency. Yang et al. (2018) showed that the variable geometry turbocharging (VGT) has the best altitude adaptability that can achieve the highest operational altitude for power recovery and BSFC control. Liu et al. (2019) found that the thermal efficiency of the engine decreased with the increase of VGT vane openings at the altitudes of 0 m and 5,500 m, but the thermal efficiency increased and then decreased at the altitude of 3,500 m; Wang et al. (2019) showed that the rated power at an altitude of 1920 m proved to be recovered to that at sea level though optimizing the injection quantity, injection timing, injection pressure, and variable nozzle turbocharger (VNT) opening. Zhang et al. (2019) showed that the optimal openings of high-pressure and low-pressure VGT vanes decreased with increase in altitudes. The global expansion ratio increased with increase in altitudes and reached 4.9 at 5,500 m. Jia et al. (2022) found that as the flight altitude rises from 0 km to 21 km, the Reynolds number reduces, the working lines approach the surge lines, and the maximum mass flow rate and the efficiency of the engine components gradually decrease. Gu et al. (2021) announced that the altitude adaptability of the engine is notably improved by adapting the proposed method, especially for the two-stage turbocharging system. Zhang Y et al. (2022) found that the maximum intake density, coupled with fuel injection strategy, would achieve the lowest fuel consumption under a part-load condition and the largest torque corresponding to the minimum air-fuel ratio under a full-load condition.
The decreasing air inflow reduces the cylinder air to fuel ratio resulting in deteriorate combustion and worsened emissions. Many studies have been conducted into the performance, emission and combustion characteristics of diesel engines under variable operating conditions. Zhang Z et al. (2022) showed that when the diesel engine was operated at high altitude, the mismatch between fuel and air led to more soot formation but less oxidized. Jing et al. (2021) found that when the altitude increases, the average cylinder pressure and maximum pressure both decrease, the cylinder temperature and maximum temperature both increase, the combustion start point lags, and the combustion duration increases. Wang et al. (2018) showed that at the altitude of 2,990 m, the CO emissions increased by 209% in comparison with that of near sea level. Both particle numbers (PN) and NOx emissions also rose with altitude while NOx emissions at 2,990 m showed a decreasing tendency. Yang et al. (2022) showed that high-altitude environments prolonged combustion duration and reduced in-cylinder pressure, thereby causing power attenuation. Serrano et al. (2019) found that the strategy to keep maximum torque for full-load conditions has evidenced a relevant damage to the exhaust aftertreatment systems performance as the altitude increases due to the increase of the equivalence ratio towards stoichiometric conditions. Jiao et al. (2019) Compared the combustion and emission characteristics of a diesel engine fueled with diesel and methanol-Fischer-Tropsch diesel-biodiesel-diesel blends at various altitudes. The results indicated that the particulate matter for the blends was markedly lower compared with the diesel, while a slightly higher in NOx at various altitudes. Bi et al. (2018) pointed out that the engine power and economy are reduced, the NOx emission is reduced, and the particulate matter emission is increased with the decrease of atmospheric pressure. Meng et al. (2022) suggest that the plateau engines can be optimized by finding strategies to improve spray quality, which may help raise the threshold that causes a sharp decline in performance well above 3,000 m.
The power output and emissions production of a diesel engine are dominated by the formation of homogeneous fuel-air mixture, which may be promoted by a combustion system with a good configuration, including the fuel injection strategies, intake parameters, and combustion chamber (Kang et al., 2022). When the altitude increases, the cylinder pressure and oxygen concentration both decrease because of less mass of mixture trapped in the cylinder. The fuel injection quantity at high altitudes will be lower than the plain environment due to the limitation of smoke limit or exhaust temperature. Therefore, control parameters such as EGR rate and fuel injection timing also need to be adjusted accordingly with the altitude change. Although a limited number of studies examined the effect of altitude, fuel injection events [i.e., injection timing (IT), injection pressure (IP)] and EGR on combustion, performance and emission characteristics of diesel engines. However, investigation on the detailed characterization of overall performance at different altitudes are still insufficient. The underlying causes of engine performance degradation and the combustion and emission control strategies are not fully understood. Moreover, there is not unified conclusion about the variation of NOx emission with respect to altitude. For example, Wang et al. (2018) shows that the NOx emission increased and then gradually decreased as the altitude increases, while Bi et al. (2018) demonstrated the NOx emission drops with the decreases of altitude. The present study focused on the impacts of VNT vane opening, EGR rate, fuel injection timing and pressure on combustion, power output, fuel economy, and emissions characteristics at various altitude. The objective of this work is to identify the effects of fuel injection timing and pressure, EGR rate and VNT opening degree on the combustion processes, performance and NOx emissions at different altitudes. This study provides a basis for the optimization of control parameters to improve the operating and emission performance of diesel engines under high altitude environments.
2 Experiment and methodology
2.1 Experimental setup
The engine used in this study was a four-cylinder diesel engine equipped with a Bosch high-pressure common rail direct injection system, a single-stage variable nozzle turbocharger (VNT) and a high pressure cooled exhaust gas recirculation (EGR) system. The detailed specifications of the engine were shown in Table 1. The load and speed of the test engine were controlled by an AC electric dynamometer. An AVL 622 combustion analyzer was used to sample cylinder pressure and calculate heat release rate (HRR). The CA50 phasing is generally defined as the crank angle position corresponding to 50% heat release, and CA90 means the crank angle positions of 90% heat release. The NOx emission and opacity smoke were measured by an AVL AMA i60 gaseous emissions analyzer and an AVL opacimeter, respectively. This experimental apparatus also included an AVL PUMA OPEN measurement and control system, an air flowmeter, an atmospheric pressure simulation system and an INCA calibration software. The layout of test bench was shown in Figure 1. The parameters of main experimental devices are shown in Table 2.
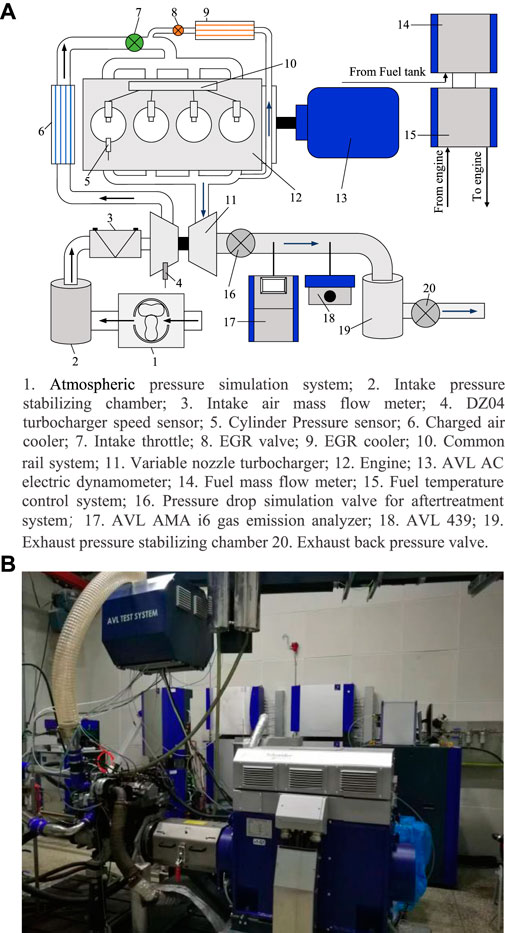
FIGURE 1. Test system for diesel engine at high altitudes. (A) Layout of test system, (B) Experiment test set up.
2.2 Control of altitude
Altitude variation experiments were performed according to the China Standard GB/T 20,969.1–202 (Government of China, 2021) to simulate the ambient pressure of intake and exhaust. The specific control settings in the intake and exhaust pressures depend on the atmospheric pressure level in the local region. Since the local altitude of our laboratory is 2000 m, an atmospheric pressure simulation system and an exhaust back pressure valve were used to adjust the intake and exhaust ambient pressure to simulate 0m and 1000 m altitude. The steady-state pressure control accuracy of the atmospheric pressure simulation system is ±1 kPa. To exclude the influence of intake air temperature and humidity, the intake air temperature and relative humidity at compressor inlet of VNT at different altitudes are controlled within 25°C ± 1.5 °C and 50% ± 5% respectively by the intake air conditioning.
2.3 Settings of control parameters
Experiments were carried out at a constant engine speed of 2000 rpm at full engine loads (300 Nm). At all experimental conditions, the cycle fuel injection quantity was maintained constant (52 mg/cycle) to avoid the variation of fuel quantity affecting the results. The original calibration value of MIT, FIP and EGR rate were −4.5°CA aTDC, 115 MPa and 0% for the selected fuel injection quantity at 0 m altitude, respectively. The variations of MIT and FIP will affect the exhaust temperature resulting in the change of boost pressure and intake air flow, and thus cause a change of in-cylinder mixture and combustion. Therefore, to eliminate the effects of boost pressure and intake air flow, the VNT vane opening was maintained close-loop control mode based on the intake manifold absolute pressure (MAP) during the MIT and FIP sweep tests.
Due to the coupling relationship between EGR and VNT, the control strategy of VNT was an open-loop mode during the EGR rate and VNT vane opening sweep tests. When the VNT vane opening was greater than or equal to 40%, EGR cannot be achieved because the boost pressure was greater than the turbine inlet pressure. Therefore, the initial opening of VNT vane opening was set to 40%, and the VNT vane opening was reduced by 5% step until the turbocharger speed reaches the maximum speed. The smaller VNT vane opening, the greater boost pressure. The initial value of EGR rate was set to 0%, and the EGR rate was gradually increased by 5% step until the EGR valve was fully opened, while the VNT vane opening was maintained at 20%. The detail settings of all parameters at different altitudes were shown in Table 3. At each test condition, experiments were repeated thrice, and the data of these three measurements were averaged to get the experimental data set for further analyses.
3 Results and discussion
3.1 Effects of main injection timing at different altitudes
Direct diesel fuel injection timing has a significant effect on fuel gradient distribution, which affects the combustion characteristics in cylinder. In order to evaluate the main injection timing (MIT) effect on engine performances at different altitudes, a parametric study was carried out for different MIT. All the other engine operating parameters (fuel injection pressure, injected fuel mass, engine speed, engine load and EGR rate) were maintained constant. But the VNT opening was automatically adjusted by the ECU to maintain a constant boost pressure. Table 3 details the settings used for the MIT sweep.
Figure 2 illustrated the in-cylinder pressure and heat release rate (HRR) with different MIT at various altitude conditions. The figure depicts that as the injection timing is advanced from 0 °CA aTDC to 8 °CA aTDC at 2000 rpm, the combustion phasing is advanced, the cylinder pressure and temperature increase significantly. The maximum in-cylinder pressure increased by approximately 38.2% at the altitude of 2000 m. This means that the injection timing can be adjusted to overcome the altitude effect on engine power. As the altitude increases from 0 m to 2000 m, the peak in-cylinder pressure reduce by up to 8.4%, the peak heat release rate decreased as much as 8.2% for 5 different injection timings. The speed of diesel combustion was limited by the mixing between the injected fuel and the air in the combustion chamber. The ignition delay becomes longer when the injection timing is advanced in the compression stroke, resulting in a partially well premixed mixture of fuel and air, and the homogeneity of the mixture increases. These effects can accelerate the combustion rate and improve combustion performance, they are reflected by the increases in the cylinder pressure and temperature. However, an excessively advanced main injection timing leads to very lean distribution of diesel fuel inside the cylinder which results in slower combustion.
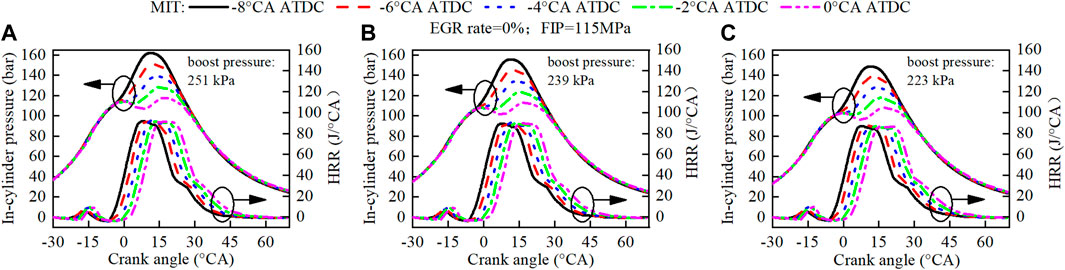
FIGURE 2. Impacts of MIT on in-cylinder pressure and HRR at different altitudes. (A) 0 m, (B) 1000 m, (C) 2000 m.
Figure 3 illustrate the variation of ignition delay, CA50, CA90 and peak in-cylinder temperature at different altitudes and main injection timing (MIT) at 2000 rpm with full load. The ignition delay was defined as the duration of crank angle positions from MIT to start of combustion (SOC). Generally, With MIT advanced, ignition delay increases, combustion phasing advance and peak in-cylinder temperature increases at different altitudes. The differences in combustion characteristics are due to differences in the mixing times of different fuel injection timing. The air-fuel mixing duration becomes longer when the main injection timing was advanced in the compression stroke, resulting in a partially well premixed mixture of diesel and air. When the mixing time duration becomes longer, the local equivalence ratio gradient becomes less, and the homogeneity of the mixture increases. These effects can accelerate the combustion rate and improve combustion performance. Due to the lower intake pressure and temperature at high altitude, the fuel cannot burn rapidly near the top dead center. Consequently, as the altitude increases from 0 m to 2000 m, the CA50 retarded by 2.3%, the CA90 retarded by 4.8%, and the peak in-cylinder temperature increased by 4.9% on average.
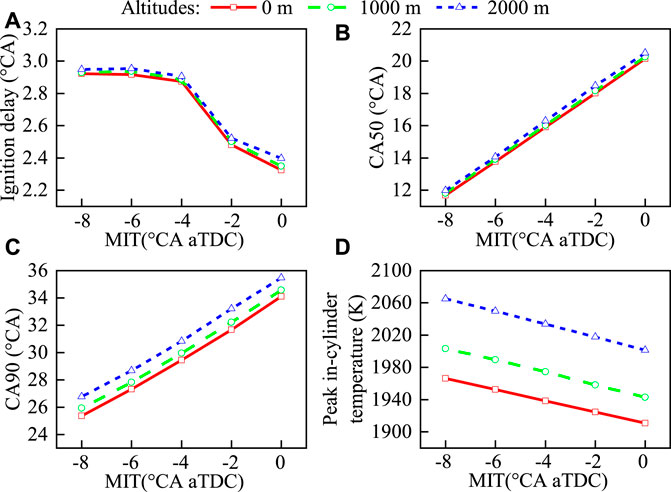
FIGURE 3. Impacts of MIT on combustion parameters at different altitudes, (A) Ignition delay, (B) CA50, (C) CA90 and (D) Peak in-cylinder temperature.
Figure 4 indicates the engine torque, BSFC, NOx emissions and opacity smoke with respect to altitude and MIT. As the MIT was advanced from 0 °CA aTDC to 8 °CA aTDC at 2000 m altitude, the engine torque increased by 5.6%, the BSFC reduced by 5.9%, the opacity smoke decreased by approximately 55%, while the NOx emissions increased by 54%%.
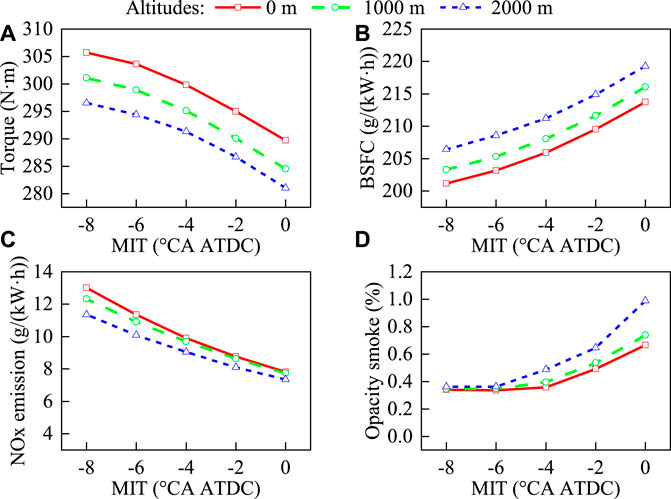
FIGURE 4. Impacts of MIT on engine performance and emissions, (A) torque, (B) BSFC, (C) NOx emission and (D) opacity smoke.
Advanced diesel injection timing leads to a moderate overall equivalence ratio and improved combustion, which results in the engine torque increases, and the BSFC reduces. However, as the altitude increases, the air to fuel ratio decreased due to lower intake air density, which could deteriorate fuel-air mixture quality and combustion process. Deteriorated combustion at higher altitudes resulted in higher fuel consumption rate and lower output torque. As the altitude increases from 0 m to 2000 m, the engine torque reduces by up to 2.9%, and the BSFC increases by up to 2.6%. Therefore, to achieve the power recovery with the same cycle injection quantity at high altitudes to 0 m level, an early injection timing should be used.
Generally, the emissions of NOx increase, and opacity smoke decrease with the advance of MIT at different altitudes. The NOx emissions reduce consistently with the rise of altitude, while the opacity smoke increase with the rise of altitude. When the altitude level increases from 0 m to 2000 m with an interval of 1,000 m, the NOx emissions gradually reduce by 4.3% and 11.8% respectively, and the opacity smoke increases by 7.0% and 26.2% respectively. The atmospheric pressure and air density decreased at high altitudes, then the average air to fuel ratio of the combustible mixture decreases and the maximum combustion temperature increases. However, the reduced oxygen concentration hinders NOx formation. It was found that the latter factor was more prominent at higher altitudes (Bi et al., 2018). Higher combustion temperature and locally rich fuel–air mixture lead to the increase in opacity smoke at high altitudes, especially when the injection timing is retarded.
3.2 Effects of injection pressure at different altitudes
To assess the impact of the fuel injection pressure (FIP) on the overall performance, six different FIP levels were tested 105, 110, 115, 120, 125 and 130 MPa. In this analysis, the diesel MIT, EGR rate, injected fuel mass, intake and exhaust pressures and temperatures were kept constant. Therefore, the differences in the combustion process can be only attributed to FIP variations. Table 3 depicts the settings used during the FIP tests.
Figure 5 present the in-cylinder pressure and heat release rate with different FIP at various altitude conditions. Fuel injection pressure plays a vital role in combustion characteristics and ignition delay of engine. Injecting fuel at higher pressure generates an increase in turbulence within air/fuel mixture, leads to effective fuel atomization, and decreases the cyclic variations results in combustion enhancement (Vallapudi et al., 2018). With the increase of injection pressure, the combustion phasing is advanced, and the maximum combustion pressure and heat release rate increase. But the trend of increasing declined gradually with the increase of altitude. At higher altitudes, intake air density and temperature are lower, which leads to poor atomization and evaporation of diesel droplets in cylinder. When the fuel injection pressure increases by 5 MPa, the maximum combustion pressure increases by 1.22%, 1.32% and 1.47% respectively at 0, 1,000 and 2000 m altitude.
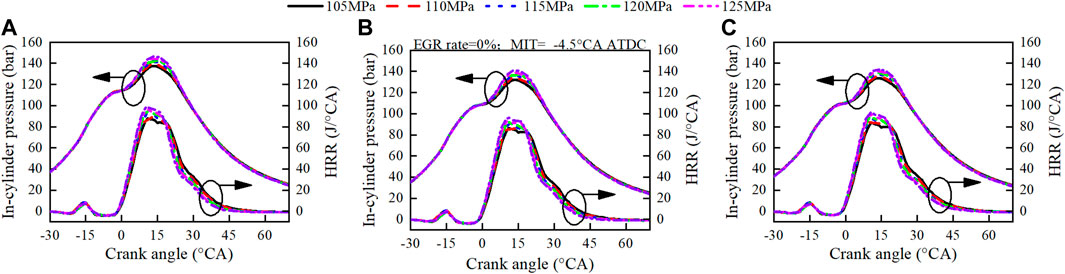
FIGURE 5. Impacts of FIP on in-cylinder pressure and HRR at different altitudes. (A) 0 m, (B) 1000 m, (C) 2000 m.
Figure 6 shows the variation of ignition delay, CA50, CA90 and peak in-cylinder temperature with fuel injection pressure (FIP) and altitudes. As the fuel pressure increases from 105 m to 130 MPa, the ignition delay was reduced, the CA50 and CA90 advanced and the peak in-cylinder temperature slightly increased at different altitudes. Fuel injection pressure affects the atomization, vaporization and dispersion of the injected liquid diesel fuel. Higher fuel injection pressure leads to rapid vaporization and mixing process, which results into more homogeneous mixture and acceleration of the combustion rate. As the altitude increases from 0 m to 2000 m, the CA50 was retarded 3.9°CA, the CA90 was retarded 8.9°CA, and the peak in-cylinder temperature increased by 4.98% with different FIP.
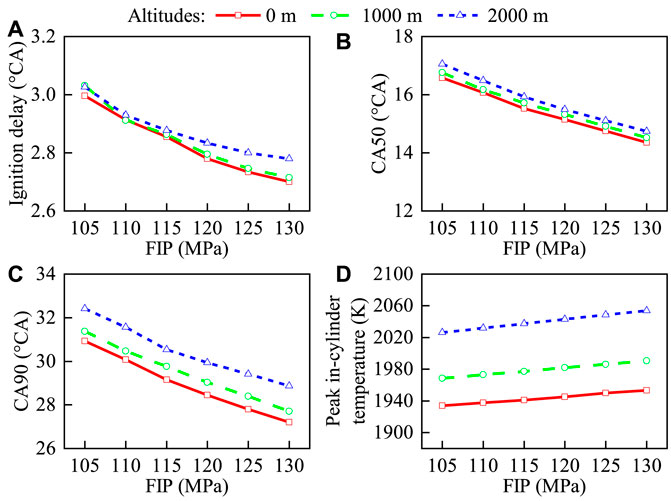
FIGURE 6. Impacts of FIP on combustion parameters at different altitudes, (A) Ignition delay, (B) CA50, (C) CA90 and (D) Peak in-cylinder temperature.
Figure 7 gives the engine torque, BSFC, NOx emissions and opacity smoke with respect to injection pressure and altitude. As the fuel injection pressure increases from 105 m to 130 MPa at 2000 m altitude, the engine torque reduces by up to 1.7%, and the BSFC increases by up to 1.6%. To isolate the effect of FIP on the combustion and emission performances at different altitudes, the boost pressure was fixed when the FIP was varied. As increasing FIP, the ignition delay was reduced, and combustion rate was increased due to improved fuel atomization. Therefore, the exhaust energy is greatly reduced because of the low exhaust temperature due to the reduction of post combustion. Consequently, in order to maintain the same boost pressure, the VNT vane opening was reduced, which may result in reduction in engine torque and higher fuel consumptions due to higher pumping losses. At high altitudes, the air density and pressure in cylinder are lower, which leads to poor atomization and evaporation. To avoid the fuel impingement on cylinder wall, the fuel injection pressure should not be too high.
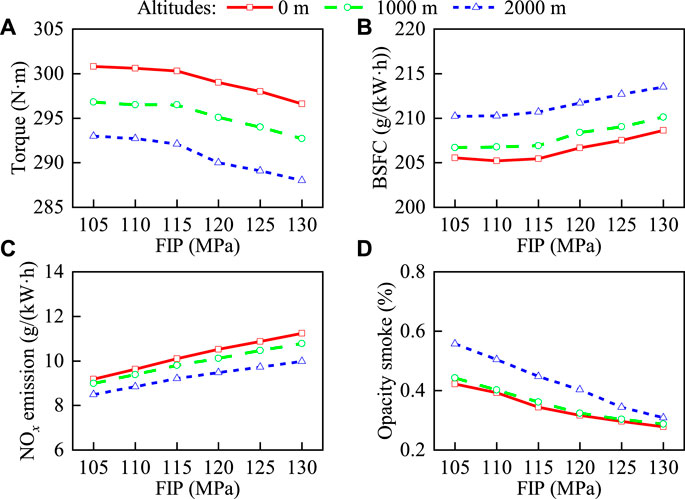
FIGURE 7. Impacts of FIP on engine performance and emissions, (A) torque, (B) BSFC, (C) NOx emission and (D) opacity smoke.
The fuel injection pressure strongly affected the NOx emissions and smoke levels, especially at high altitude conditions. Generally, with the rise of injection pressure, the opacity smoke was obviously decreased, while the NOx emissions increase markedly due to the improvement of premixed combustion. As the fuel injection pressure increased from 105 to 130 MPa at 2000 m, the opacity smoke reduce by approximately 44.5%, the NOx emissions increase by 17.5%. Three main factors are responsible for lower opacity smoke emission with higher injection pressure. First, the residence time in the region with rapid soot formation in the fuel jet is decreased due to higher penetrating speed of the jet at high injection pressure. Second, at higher injection pressure, the spray breakup and fuel-air mixing are more effective in preventing the formation of locally rich regions, which would produce significant amount of soot. Third, the turbulence is increased providing more effective soot oxidization (Maurya 2018). Higher injection pressure brings about higher heat release in premixed phase resulting in higher in-cylinder temperature. Meanwhile, increase in injection pressure leads to decrease in the diameter of atomized fuel droplets and faster vaporization which enhances the rapid combustion rate and increase in combustion temperature resulting in higher NOx emission.
3.3 Effects of EGR rate at different altitudes
To isolate the effect of EGR rate on the combustion process and emissions at different altitudes, only the EGR rates and altitude were changed during the tests. When EGR valve was fully open position, the maximum EGR rate was 21.6%, 17.3% and 13.2% at 0m, 1000m and 2000m with 20% VNT vane opening, respectively. Lower exhaust gas temperature and pressure difference at plateau leads to availability of less exhaust energy available to drive EGR to plain levels. For the convenience of comparison, the multiples of 5% EGR rate were taken as analyzing the cylinder pressure and HHR.
Figure 8 illustrate the variation of cylinder pressure and HRR at varied EGR rates and altitudes. As the EGR rate grows, both the cylinder pressure and temperature reduce, inducing a delay in the starting point of heat release and extending the ignition delay. And the maximum HRR reduces because as EGR rate grows, intake oxygen concentration declines, and the combustion chemical reaction rate of the fuel reduces. This is in accordance with the results of Huang et al. (2019). As the altitude increases, the reduction of the atmospheric pressure leads to the decrease of the intake air density. As a result, the maximum EGR rate should be reduced to improve combustion at high altitude.
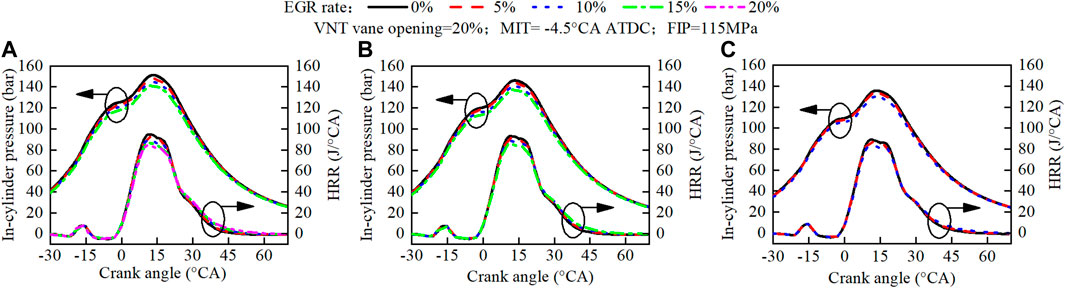
FIGURE 8. Impacts of EGR rate on in-cylinder pressure and HRR at different altitudes. (A) 0 m, (B) 1000 m, (C) 2000 m.
Figure 9 shows the relationship between ignition delay, CA50, CA90 and peak in-cylinder temperature at various EGR rates and altitudes. As EGR rate grows, the inert gas content in cylinder rises, resulting in the fresh charging amount reduces, and the cylinder combustion temperature declines. Therefore, the combustion heat release process of fuel is hindered, and the center of combustion is far away from the top dead center (TDC). Therefore, the CA50 and CA90 retarded, the peak in-cylinder temperature reduced with increases of EGR rate. As the altitude increases, the atmospheric pressure and air density will decrease, resulting in a more significant retarded combustion phasing, which reduces the HRR and maximum cylinder pressure. When the EGR rate increases from 0% to 13% at 2000 m altitude, the CA50 position is retarded from 15.7° CA to 16.5° CA, the CA90 position is retarded from 30° CA to 32° CA, and the peak in-cylinder temperature reduces by 4% 1.4%.
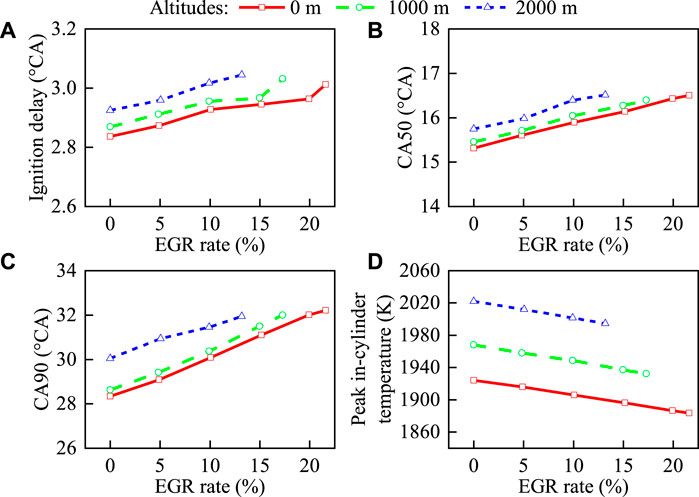
FIGURE 9. Impacts of EGR rate on combustion parameters at different altitudes, (A) Ignition delay, (B) CA50, (C) CA90 and (D) Peak in-cylinder temperature.
Figure 10 presents the variation of engine output torque, BSFC, NOx emissions and opacity smoke with respect to altitudes and the EGR rate. The engine brake torque reduces and the BSFC increases with the growth of the EGR rate at different altitudes. As the altitude increases, the atmospheric pressure and air density will decrease, resulting in a more significant reduction in engine power and fuel economy due to lack of oxygen with the increase of EGR rate. When the altitude increases from 0 to 2000 m, the engine brake torque drops by 2.0%, and BSFC increases by 2.2% with 13.2% EGR rate.
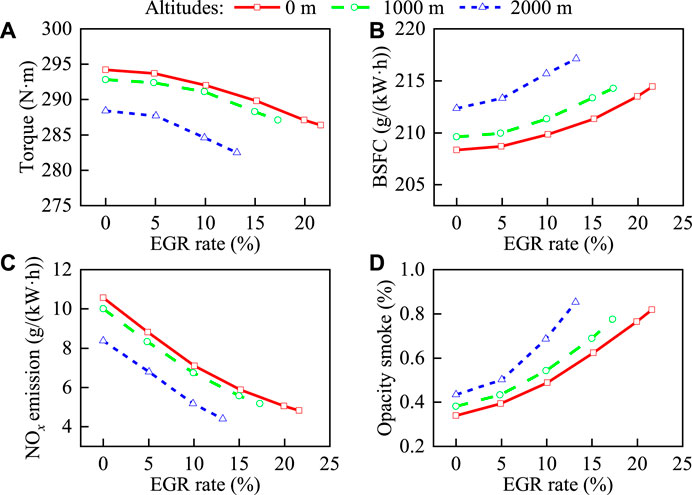
FIGURE 10. Impacts of EGR rate on engine performance and emissions, (A) torque, (B) BSFC, (C) NOx emission and (D) opacity smoke.
Generally, the NOx emission was reduced, while the opacity smoke was increased for higher EGR rate at each altitude. Obviously, the EGR rate has a significant influence on the formation of NOx (Choi et al., 2021). When the EGR rate increases by 5%, the NOx emission reduces by 16.4%,17.9 and 21.9 respectively at 0, 1,000 and 2000 m altitude. With the increase of EGR rate, the EGR flow increases, and the amount of exhaust gases to drive turbine reduces, resulting in the drop of turbocharger power and air intake flow. Furthermore, the inert gases in-cylinder go up with the rise of EGR rate. These two factors cause the fresh charge and air-fuel ratio in the cylinder to decrease, and the NOx emissions cut down at different altitudes. Additionally, the combustion temperature will drop at high EGR and hindering the formation of NOx. When the altitude increases from 0 to 2000 m, the NOx emission reduces by 47%, the opacity smoke increases by 49% with 13.2% EGR rate. The decreasing oxygen concentration at high altitude will further hinder the chemical reaction of NOx formation. However, the shortage of oxygen for higher EGR and altitudes promotes the generation of smoke opacity. Therefore, simultaneous reduction of smoke and NOx emissions is much more difficult at high altitudes due to the inherent trade-off relationship between them.
3.4 Effects of VNT vane opening at different altitudes
The last sweep performed addresses different VNT opening at different altitudes. Table 3 depicts the settings used during the tests as well as the altitude values. There is a strong coupling relationship among EGR and VNT since both the EGR flow and turbine vane are driven by exhaust energy. Therefore, the control strategy of VNT was modified to an open-loop mode during the VNT vane opening sweep tests. The reduction of the atmospheric pressure at plateau leads to a decrease in the turbine outlet pressure and an increase of the turbine expansion ratio. As a result, the increase in the turbine inlet gas temperature and the decrease in the turbine outlet pressure accelerate the turbocharger speed (Huang et al., 2019). When the VNT vane opening was set to 15% at 2000 m altitude, over-speeding of the compressor occurred at 2000 rpm. Consequently, the minimum VNT vane opening is 20% at 2000 m altitude owing to the low intake pressure.
Figure 11 indicates the cylinder pressure and HRR with respect to altitudes and VNT opening degree. With the decrease of VNT opening degree by 5%, the maximum in-cylinder pressure increased by approximately 3.08%, and the maximum instantaneous heat release rate increased by 2.8% at different altitudes. The decrease in VNT vane opening degree resulting into decrease of boost pressure, which leads to the rise of air pressure and the amount of air entered the cylinder. Thus, the combustion process and combustion efficiency were improved owing to the enough oxygen concentration in the combustion chamber when the fuel injection quantity was fixed. Consequently, the peak cylinder pressure and HRR with lower VNT opening degree was increased.
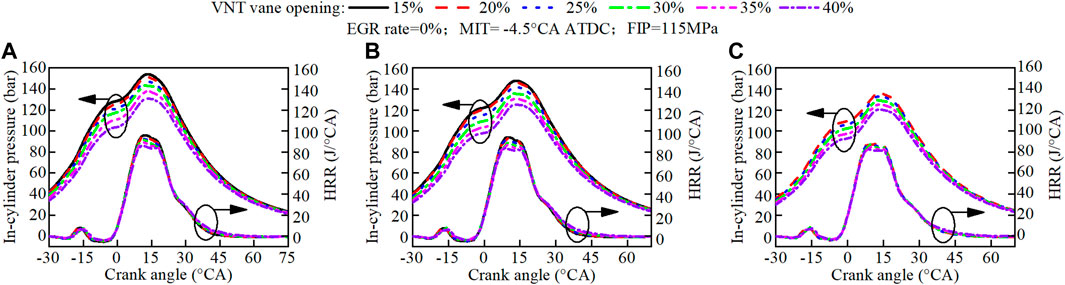
FIGURE 11. Impacts of VNT vane opening on in-cylinder pressure and HRR at different altitudes. (A) 0 m, (B) 1000 m, (C) 2000 m.
Figure 12 shows the relationship between ignition delay, CA50, CA90 and peak in-cylinder temperature with various VNT opening degree at different altitudes. With the decrease of VNT vane opening, the ignition delay and combustion phasing was advanced, and the peak in-cylinder temperature decreased. However, as VNT opening degree or altitude increase, the reduction of intake quantities resulting in a longer ignition delay and slower heat release rate. Therefore, the CA50 and CA90 retarded with increases of VNT vane opening and altitude. When the altitude increases from 0 to 2000 m, the CA50 and CA90 were delayed by .44°CA and 1.74°CA respectively with 20% VNT opening degree.
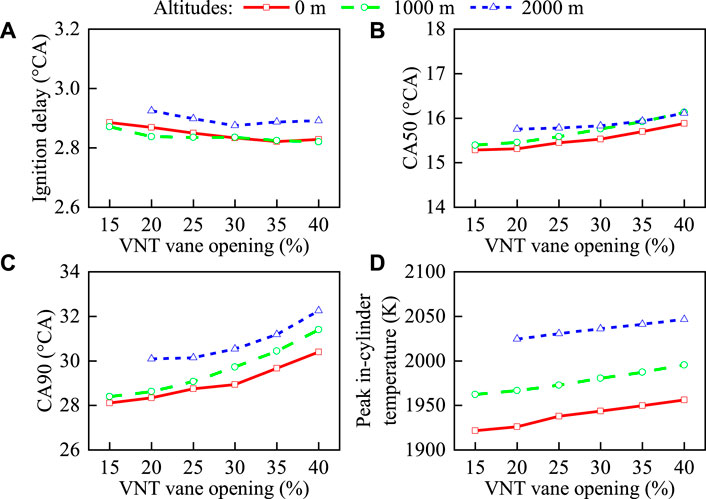
FIGURE 12. Impacts of VNT vane opening combustion parameters at different altitudes, (A) Ignition delay, (B) CA50, (C) CA90 and (D) Peak in-cylinder temperature.
The impacts of VNT vane opening on engine torque, BSFC, NOx emissions and opacity smoke at different altitudes are presented in Figure 13. With the decrease of VNT opening degree, the engine brake torque gradually increased and then decreased, and the BSFC gradually decreased and then increased. When the altitude increases from 0 to 2000 m, the engine brake torque drops by 3.01%, and the BSFC increases by 2.86% with 40% VNT vane opening. But the engine brake torque drops by 1.97%, and the BSFC increases by 1.92% with 20% VNT vane opening as the altitude increases from 0 to 2000 m. As the VNT vane opening decreases, the boost pressure and intake flow mass increase, resulting in higher engine power output and better fuel economy due to the improvement of combustion. However, with the reduction of VNT vane opening, the effective flow area of the turbine decreases, resulting in an increase in the turbine inlet pressure and the turbine expansion ratio, which will lead to the increase of pumping losses owing to the higher exhaust back pressure. Therefore, the VNT vane opening should be optimized synergistically to minimize the pumping losses to improve the fuel economy, and to maximize the air flow to improve the combustion and emission performances. The optimization of VNT control requires a balance between combustion performance and pumping losses. Aiming to the maximum torque output and minimum fuel consumption, the optimum VNT opening of this engine at different altitudes with the given fuel injection parameters is 30%.
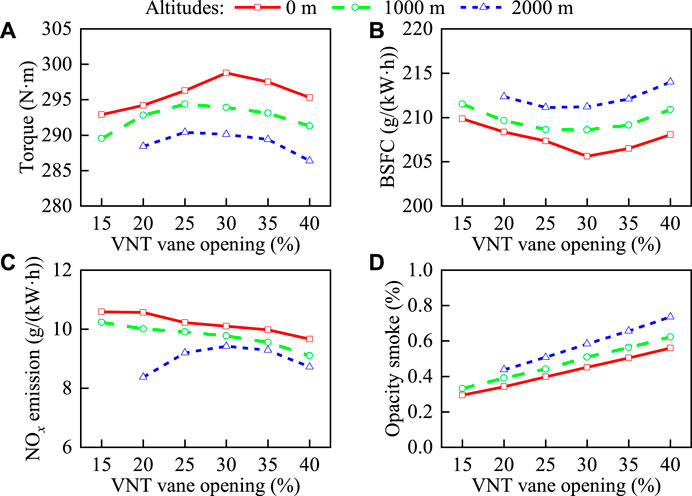
FIGURE 13. Impacts of VNT vane opening on engine performance and emissions, (A) torque, (B) BSFC, (C) NOx emission and (D) opacity smoke.
As the VNT vane opening decreases from 40% to 20%, the NOx emission increase by 9.4% and 9.9% at 0 m and 1,000 m respectively, and it reduces by 3.9% at 2000 m. While the opacity smoke reduces by 38.9% averagely at different altitudes, as shown in Figure 13. When the altitude increases from 0 to 2000 m, the NOx emission declines by 20.7% with 20% VNT opening degree. With the reduction of VNT vane opening, the increase in air-fuel ratio will enhance the combustion, resulting in higher thermal efficiency and lower exhaust temperature. As the altitude increases, the reduction of the atmospheric pressure leads to a decrease of the compressor inlet pressure. As a result, the reduction of intake flow mass and air-fuel ratio will affect the combustion efficiency, emission performances and exhaust energy. The increase of the turbine inlet gas temperature and the decrease of the turbine outlet pressure accelerate the turbocharger speed. The increase of the compressor speed and the decrease of the compressor inlet pressure result in an increase in the compressor pressure ratio. Accordingly, the compressor efficiency may decrease with the increase of the compressor speed, resulting in an increased compressor outlet air temperature and decrease of intake flow mass. If we cut down the cycle injection quantity to keep the air-fuel ratio constant, then the engine power performance will be reduced.
In summary, higher altitude provided a lower density environment for the fuel-air mixture preparation and combustion. As the altitude increase, the intake air mass flow and pressure decrease, which lead to reduction in quality of premixed charge (degree of homogeneity) due to the narrower spray angle and the lower strength of the turbulence kinetic energy in the cylinder (Huang et al., 2020). The lower cylinder pressure during injection extended the ignition delay at high altitudes, which delayed the end of combustion and prolonged the combustion duration. Additionally, the reduction of air-fuel ratio at high altitudes result into poor combustion efficiency and higher soot emission due to incomplete combustion. Although the cylinder pressure decreased with altitude, the combustion temperature was higher due to the reduction in amount of air entered in the cylinder at plateau, which may lead to lower heat transfer loss (Liu et al., 2022). Fuel injection timings and fuel injection pressure are the main fuel injection characteristics, which governed the premixed charge preparation quality and combustion phase. EGR rate and VNT vane opening determined the fuel–air equivalence ratio and thermal atmosphere in the cylinder when the cycle fuel injection quantity is fixed. The response and control of the fuel injection and air system are more comprehensive and complex at high altitudes because too many factors couple with each other. These imbalances between fuel injection and intake parameters of diesel engines operating at different altitudes lead to comparatively poor power performance and higher emissions. Therefore, to improve the combustion performance and obtain the recovery of engine power at higher altitude, it is necessary to optimize the VNT vane opening, EGR rate, fuel injection timing and injection pressure simultaneously to enhance the matching of fuel and gas.
4 Conclusion
To address the challenges of insufficient studies on the synergistic effects law of fuel injection and intake parameters on combustion and emission characteristics and the unclear underlying causes of engine performance degradation at high altitudes. Parametric experiments were performed by changing the MIT, FIP, EGR rate, and VNT opening at 2000, 1,000, and 0 m altitude. The main conclusions are summarized as follows.
1) As the altitude increased from 0 m to 2000 m when the MIT, FIP and EGR rate maintain the original calibration value, the peak in-cylinder pressure reduced by 8.4%, the peak HRR decreased by 8.2%, the peak in-cylinder temperature increased by 4.9%, the engine torque dropped by up to 2.9%, the BSFC increased by 2.6%, the NOx emissions reduced by 11.8%, and the opacity smoke increased by 26.2% respectively. With higher altitudes, the air to fuel ratio decreased due to lower intake air density, which could deteriorate combustion process then resulted in higher fuel consumption and lower output torque. But the decreasing oxygen concentration at high altitude will hinder the formation of NOx.
2) The main injection timing has a significant effect on the performance and emission characteristics at high altitudes. As the MIT was advanced from 0 °CA aTDC to 8 °CA aTDC, the engine torque increased by 5.6%, the BSFC reduced by 5.9%, the opacity smoke decreased by approximately 55%, while the NOx emissions increased by 54%% at 2000 m altitude. Advance the injection timing properly can overcome the altitude effect on engine power.
3) As the FIP increased from 105 to 130 MPa at 2000 m, the combustion phasing advanced, the maximum HRR increased, the peak in-cylinder temperature increased by 4.98%, the engine torque reduced by 1.7%, the BSFC increases by 1.6%, the opacity smoke dropped by approximately 44.5%, and the NOx emissions increased by 17.5%.
4) With the growth of the EGR rate, the cylinder pressure and maximum HRR reduce, the combustion phasing retard, the engine brake torque reduces and the BSFC increases, and NOx emission reduces. The effects of EGR rate on NOx emission is more significant at high altitudes. When the EGR rate increases by 5%, the NOx emission reduces by 16.4%,17.9 and 21.9 respectively at 0, 1,000 and 2000 m altitude. But the EGR rate should be properly reduced to obtain the recovery of engine power at plateau.
5) As the VNT vane opening decreases from 40% to 20%, the NOx emission increase by 9.4% and 9.9% at 0 m and 1,000 m respectively, and it reduces by 3.9% at 2000 m, while the opacity smoke reduces by 38.9% averagely at different altitudes. The optimization of VNT vane opening requires a balance between combustion performance and pumping losses. For the given fuel injection parameters, there is an optimal VNT opening for engine to achieve the maximum power output.
6) At high altitude, the effects of fuel injection parameters and intake parameters on combustion, performances and emissions of diesel engines are more comprehensive and complex because too many parameters couple with each other. Consequently, the next step of our research will be focused on the parameter sensitivity analysis, the synergistic effects of fuel injection timing, injection pressure, EGR rate and VNT vane opening on engine performance, and the collaborative mechanism and optimization of fuel injection parameters, intake parameters and operating parameters to improve power output, fuel economy and emission performances at different altitudes. In addition, the analysis will cover more altitude conditions (0–5,000 m) and engine operating conditions, especially under transient conditions.
Data availability statement
The original contributions presented in the study are included in the article/Supplementary Material, further inquiries can be directed to the corresponding author.
Author contributions
MW: Investigation, Methodology, Writing—Review and Editing. FH: Data curation, Writing—Review and Editing. LS: Validation, Writing—Review and Editing, Supervision. JL: Methodology, Validation, Formal analysis.
Funding
The authors would like to express their gratitude to the National Natural Science Foundation of China (Grant No. 52066008) and Major science and technology projects in Yunnan Province (Grant No.202103AA080002) for their financial support of this study.
Conflict of interest
The authors declare that the research was conducted in the absence of any commercial or financial relationships that could be construed as a potential conflict of interest.
Publisher’s note
All claims expressed in this article are solely those of the authors and do not necessarily represent those of their affiliated organizations, or those of the publisher, the editors and the reviewers. Any product that may be evaluated in this article, or claim that may be made by its manufacturer, is not guaranteed or endorsed by the publisher.
References
Bi, Y., Tang, C., Shen, L., Wen, W., Wang, J., and Song, G. (2018). Effect of VNT and EGR coupling on performance of diesel engine fueled with oxygenated fuel under different atmospheric pressures. Trans. Chin. Soc. Agric. Eng. 34 (17), 38–45. doi:10.11975/j.issn.1002-6819.2018.17.006
Choi, M., Mohiuddin, K., Kim, N., and Park, S. (2021). Investigation of the effects of EGR rate, injection strategy and nozzle specification on engine performances and emissions of a single cylinder heavy duty diesel engine using the two color method. Appl. Therm. Eng. 193, 117036. doi:10.1016/j.applthermaleng.2021.117036
Fang, L., Lou, D. M., Hu, Z. Y., Tan, P. Q., Zhang, Y. H., and Yang, R. (2022). Study on the First-Firing-Cycle combustion characteristics of high-altitude and low-temperature environments during diesel engine cold start. Fuel 322, 124186. doi:10.1016/j.fuel.2022.124186
Giraldo, M., and Huertas, J. I. (2019). Real emissions, driving patterns and fuel consumption of in-use diesel buses operating at high altitude. Transp. Res. Part D Transp. Environ. 77, 21–36. doi:10.1016/j.trd.2019.10.004
Government of China (2021). China standard GB/T 20969.1-2021. Available at: https://openstd.samr.gov.cn/bzgk/gb/newGbInfo?hcno=C5CF540C809DE60021646A624A41092E (Accessed December 31, 2021).
Gu, Y. C., Ma, Z. T., Zhu, S. P., Yang, M. Y., and Deng, K. Y. (2021). A methodology to extend the altitude adaptability of a turbocharged heavy-duty diesel engine. Int. J. Automot. Technol. 22, 837–852. doi:10.1007/s12239-021-0076-5
Huang, F., Lei, J., and Xin, Q. (2020). Study on altitude adaptability of a turbocharged off-road diesel engine. ASME. J. Eng. Gas. Turbines Power 142 (11), 114501. doi:10.1115/1.4047932
Huang, H., Li, Z., Teng, W., Huang, R., Liu, Q., and Wang, Y. (2019). Effects of EGR rates on combustion and emission characteristics in a diesel engine with n-butanol/PODE3-4/diesel blends. Appl. Therm. Eng. 146, 212–222. doi:10.1016/j.applthermaleng.2018.09.126
Jia, Z., Tang, H., Jin, D., Chen, M., Li, S., and Liu, X. (2022). Multifidelity simulation research on the low Reynolds number effect on the engine performance at different altitudes. ASME. J. Eng. Gas. Turbines Power 144 (10), 101011. doi:10.1115/1.4055355
Jiao, Y., Liu, R., Zhang, Z., Yang, C., Zhou, G., Dong, S., et al. (2019). Comparison of combustion and emission characteristics of a diesel engine fueled with diesel and methanol-Fischer-Tropsch diesel-biodiesel-diesel blends at various altitudes. Fuel 243, 52–59. doi:10.1016/j.fuel.2019.01.107
Jing, Q., Luo, Q. G., Gui, Y., and Liu, H. B. (2021). Combustion simulation of variable altitude turbocharged diesel engine using SVM. Int. J. Automot. Technol. 22, 1087–1095. doi:10.1007/s12239-021-0097-0
Kang, Y., Li, X., Shen, H., Chen, Y., Liu, D., and Chang, J. (2022). Effects of combustion chamber diameter on the performance and fuel–air mixing of a double swirl combustion system in a diesel engine. Fuel 324, 124392. doi:10.1016/j.fuel.2022.124392
Liu, J., Li, Y., Zhang, C., and Liu, Z. (2022). The effect of high altitude environment on diesel engine performance: Comparison of engine operations in Hangzhou, Kunming and Lhasa cities. Chemosphere 309 (1), 136621. doi:10.1016/j.chemosphere.2022.136621
Liu, J., Wang, B., Meng, Z., and Liu, Z. (2023). An examination of performance deterioration indicators of diesel engines on the plateau. Energy 262, 125587. doi:10.1016/j.energy.2022.125587
Liu, R., Yang, C., Zhang, Z., Jiao, Y., and Zhou, G. (2019). Experimental study on thermal balance of regulated two-stage turbocharged diesel engine at variable altitudes. J. Therm. Sci. 28 (4), 682–694. doi:10.1007/s11630-019-1151-3
Liu, Z., and Liu, J. (2022a). Effect of altitude conditions on combustion and performance of a turbocharged direct-injection diesel engine. Proc. Institution Mech. Eng. Part D J. Automob. Eng. 236 (4), 582–593. doi:10.1177/09544070211026204
Liu, Z., and Liu, J. (2022b). Investigation of the effect of altitude on in-cylinder heat transfer in heavy-duty diesel engines based on an empirical model. J. Energy Resour. Technol. 144 (11), 112303. doi:10.1115/1.4054136
Maurya, R. K. (2018). Characteristics and control of low temperature combustion engines: Employing gasoline, ethanol and methanol. Berlin, Germany: Springer. doi:10.1007/978-3-319-68508-3
Meng, Z., Liu, Z., and Liu, J. (2022). Investigation of in-cylinder combustion deterioration of diesel engines in plateau regions. Fuel 324, 124824. doi:10.1016/j.fuel.2022.124824
Piqueras, P., Burke, R., Sanchis, E. J., and Diesel, B. (2022). Fuel efficiency optimisation based on boosting control of the particulate filter active regeneration at high driving altitude. Fuel 319, 123734. doi:10.1016/j.fuel.2022.123734
Serrano, J. R., Piqueras, P., Sanchis, E. J., and Diesel, B. (2019). A modelling tool for engine and exhaust aftertreatment performance analysis in altitude operation. Results Eng. 4, 100054. doi:10.1016/j.rineng.2019.100054
Vallapudi, D. R., Makineni, H. K., Pisipaty, S. K., and Venu, H. (2018). Combined impact of EGR and injection pressure in performance improvement and NOx control of a DI diesel engine powered with tamarind seed biodiesel blend. Environ. Sci. Pollut. Res. Int. 25 (36), 36381–36393. doi:10.1007/s11356-018-3540-7
Wang, H., Ge, Y., Hao, L., Xu, X., Tan, J., Li, J., et al. (2018). The real driving emission characteristics of light-duty diesel vehicle at various altitudes. Atmos. Environ. 191, 126–131. doi:10.1016/j.atmosenv.2018.07.060
Wang, J., Shen, L., Bi, Y., and Lei, J. (2021). Modeling and optimization of a light-duty diesel engine at high altitude with a support vector machine and a genetic algorithm. Fuel 285, 119137. doi:10.1016/j.fuel.2020.119137
Wang, J., Shen, L., Bi, Y., Liu, S., and Wan, M. (2019). Power recovery of a variable nozzle turbocharged diesel engine at high altitude by response surface methodology and sequential quadratic programming. Proc. Institution Mech. Eng. Part D J. Automob. Eng. 233 (4), 810–823. doi:10.1177/0954407017753913
Yang, M., Gu, Y., Deng, K., Yang, Z., and Zhang, Y. (2018). Analysis on altitude adaptability of turbocharging systems for a heavy-duty diesel engine. Appl. Therm. Eng. 128, 1196–1207. doi:10.1016/j.applthermaleng.2017.09.065
Yang, Z., Du, Y., Geng, Q., Gao, X., Er, H., Liu, Y., et al. (2022). Performance analysis of a hydrogen-doped high-efficiency hybrid cycle rotary engine in high-altitude environments based on a single-zone model. Energies 15 (21), 7948. doi:10.3390/en15217948
Zhang, C., Li, Y., Liu, Z., and Liu, J. (2022). An investigation of the effect of plateau environment on the soot generation and oxidation in diesel engines. Energy 253, 124086. doi:10.1016/j.energy.2022.124086
Zhang, H., Shi, L., Deng, K., Liu, S., and Yang, Z. (2020). Experiment investigation on the performance and regulation rule of two-stage turbocharged diesel engine for various altitudes operation. Energy 192, 116653. doi:10.1016/j.energy.2019.116653
Zhang, S., Zhao, P., He, L., Yang, Y., Liu, B., He, W., et al. (2020). On-board monitoring (OBM) for heavy-duty vehicle emissions in China: Regulations, early-stage evaluation and policy recommendations. Sci. Total Environ. 731, 139045. doi:10.1016/j.scitotenv.2020.139045
Zhang, Y., Yan, Y. C., Yang, R. M., Wang, Q. F., Zhang, B. W., Gan, Q. L., et al. (2022). Study of in-cylinder heat transfer boundary conditions for diesel engines under variable altitudes based on the CHT model. Front. Energy Res. 10, 828215. doi:10.3389/fenrg.2022.828215
Zhang, Z., Liu, R., Dong, S., Zhou, G., Liu, W., and Peng, Q. (2022). Thermodynamic cycle characteristics of twin-VGT diesel engine and its control method at variable altitudes. Appl. Therm. Eng. 211, 118429. doi:10.1016/j.applthermaleng.2022.118429
Zhang, Z., Liu, R., Zhou, G., Yang, C., Dong, S., Jiao, Y. F., et al. (2019). Influence of varying altitudes on matching characteristics of the Twin-VGT system with a diesel engine and performance based on analysis of available exhaust energy. Proc. Institution Mech. Eng. Part D J. Automob. Eng. 234 (7), 1972–1985. doi:10.1177/0954407019876220
Glossary
AFR = Air-Fuel Ratio
BSFC = Brake specific fuel consumption
bTDC = before Top Dead Centre
aTDC = After Top Dead Centre
CIP = Compressor inlet pressure
CIT = Compressor inlet temperature
CRH = Relative humidity of compressor inlet air
CO = Carbon mono-oxide
CA = Crank angle
CA50 = crank angle position of 50% heat release
CA90 = crank angle positions of 90% heat release
EGT = Exhaust gas temperature
EBT = Engine brake torque
EGR = Exhaust Gas Recirculation
ECU = Engine Control Unit
FIP = Fuel injection pressure
HRR = Heat release rate
HC = Hydrocarbon
MIT = Main injection timing
NOx = Nitrogen Oxides
RDE = real driving emission
TDC = Top Dead Center
VGT = Variable geometry turbocharging
VNT = Variable nozzle turbocharger
Keywords: emissions, exhaust gas recirculation, injection timing, injection pressure, variable nozzle turbocharger opening, altitude
Citation: Wan M, Huang F, Shen L and Lei J (2023) Experimental investigation on effects of fuel injection and intake parameters on combustion and performance of a turbocharged diesel engine at different altitudes. Front. Energy Res. 10:1090948. doi: 10.3389/fenrg.2022.1090948
Received: 06 November 2022; Accepted: 16 December 2022;
Published: 05 January 2023.
Edited by:
Jinlong Liu, Zhejiang University, ChinaReviewed by:
Huachao Yang, Zhejiang University, ChinaJunqing Zhu, ExxonMobil Research and Engineering, United States
Yu Zhang, Zhejiang University City College, China
Copyright © 2023 Wan, Huang, Shen and Lei. This is an open-access article distributed under the terms of the Creative Commons Attribution License (CC BY). The use, distribution or reproduction in other forums is permitted, provided the original author(s) and the copyright owner(s) are credited and that the original publication in this journal is cited, in accordance with accepted academic practice. No use, distribution or reproduction is permitted which does not comply with these terms.
*Correspondence: Fenlian Huang, NDI5MDE5Nzg4QHFxLmNvbQ==, NTk0Njk5NjYxQHFxLmNvbQ==