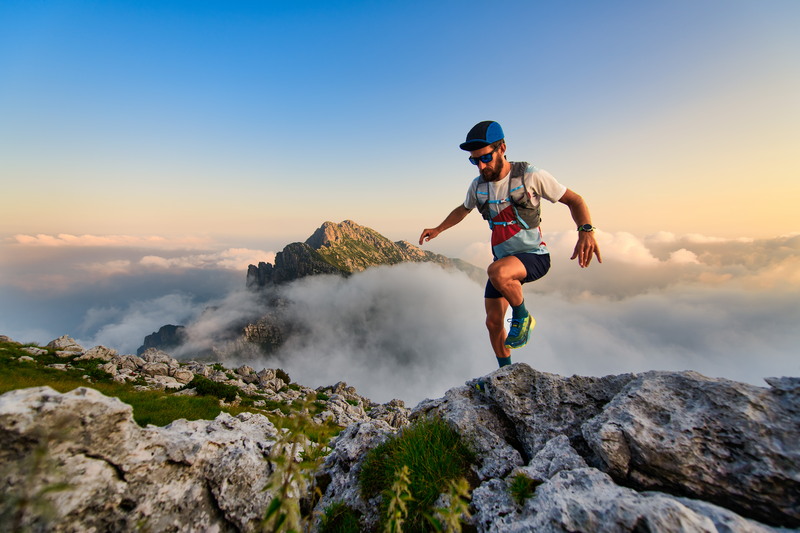
95% of researchers rate our articles as excellent or good
Learn more about the work of our research integrity team to safeguard the quality of each article we publish.
Find out more
ORIGINAL RESEARCH article
Front. Energy Res. , 23 January 2023
Sec. Nuclear Energy
Volume 10 - 2022 | https://doi.org/10.3389/fenrg.2022.1075224
Introduction: To meet the multi-user, cross-time-and-space, cross-platform online demand of work, and professional training teaching in nuclear reactor safety analysis under the normalization of Coronavirus Disease 2019.
Method: Taking the nuclear accident simulation software PCTRAN as an example, this study adopts cloud computing technology to build the NasCloud, a nuclear accident simulation cloud platform based on Browser/Server architecture, and successfully realizes multi-user, cross-time-and-space, cross-platform applications. Targeting the AP1000, a pressurized water reactor nuclear power plant, the simulation of cold-leg Small Break Loss of Coolant Accident and cold-leg Large Break Loss of Coolant Accident were carried out to verify the correctness of the NasCloud’s accident simulation function.
Results: The result shows that the simulation functions and results of the NasCloud in multi-terminal are consistent with the single version of PCTRAN. At the same time, the platform has high scalability, concurrency and security characteristics.
Discussion: Therefore, the nuclear accident simulation cloud platform built in this study can provide solutions for the work and training of nuclear reactor safety analysis, and provide reference for other engineering design and simulation software cloud to computing transformation.
For nuclear power development, nuclear safety is particularly important. Over half a century of nuclear power development, three major nuclear accident (GU, 2017) disasters in history have continuously sounded the alarm to mankind that the current nuclear energy system represented by water reactors is still very flawed in terms of safety, and therefore ensuring nuclear safety is an issue that must be addressed to determine the development of nuclear energy. Reactor safety is an important part of nuclear safety, and for nuclear power plant reactor safety, its accident safety analysis is very important and essential for the design, construction, operation and licensing of nuclear power plant reactors. During service and design, designers ensure reactor safety by performing safety analyses for various accidents. The use of simulation software for nuclear reactor safety analysis is an indispensable way, such as using RELAP5/MOD3.4 to investigate the residual heat removal capability of the emergency passive residual heat removal system and the transient characteristics of the primary loop system in the event of the station blackout accident and study the behavior of Emergency Passive Safety System and the transient characteristics of the primary loop system during the Steam Generator Tube Rupture accident (Wang et al., 2012; Wang et al., 2013a). The computational fluid dynamics (CFD) method has been widely adopted and accepted in the nuclear reactor safety analysis in the recent years. For example, using CFD method to simulate Two-Phase Bubbly Flow (Khan et al., 2020). Furthermore, a combination of RELAP5 and CFD can be used to design the passive decay heat removal system for the integral inherent safety light water reactor (Wang et al., 2020).
The nuclear power plant simulation system is used as one of the important tools for nuclear reactor safety analysis, according to the complexity of the system and the type of simulation, it can be divided into four types: Training simulator; Nuclear power engineering simulator; Nuclear power plant safety analyzer; Nuclear plant analyzer (Yan, 1991). Traditionally, the network environment of nuclear power plant simulation system is an internal local area network composed of independent computers or a limited number of computers (Zhao, 2006; Liu, 2008; Lu, 2015); the distributed architecture is usually used to realize the connection between the trainer’s computer and the student’s computer. It not only can not realize the cross-time-and-space and cross-platform access based on the Internet (Ren and Ren, 2009; Li et al., 2011; Gao et al., 2017), but also the single-machine running nuclear power plant simulation system results in the waste of computing resources.
Under the background of Coronavirus Disease 2019, various cloud-based teaching, office and production platforms have developed rapidly. For example, MOOC platforms, online cloud conferences, CAD modeling software based on cloud architecture (Zhao, 2020) and obstetric imaging diagnostic platforms based on cloud computing technology (Lie et al., 2020). They have greatly improved the efficiency of social education and production. According to the research findings, cloud computing allows employees to complete tasks about 20 percent faster and reduces error rates by about 50 percent (Jia and Wu, 2022). Facebook CEO Mark Zuckerberg announced plans for a “Meta-universe” and renamed the company “Meta.” His fundamental purpose is to construct a virtual world that spans space-time and low cost of living based on cloud computing technology of the Internet (Meta, 2021).
In the study on the application of cloud computing to the nuclear field, Kim and Rizwan (2007) built a web-based nuclear power plant simulator by coupling LabVIEW with RELAP5 software; Cho and Woo (2017) conducted an analysis of the accident at the Fukushima Nuclear Power Plant based on real-time management of cloud computing system; Woo (2014) combined cloud-based analysis with the Internet of Things in 2013 to assess nuclear safety in Fukushima nuclear accident, and real-time analysis of Fukushima nuclear accident atmospheric dispersion by 2020, based on mobile phone cloud computing assessments (Woo and Jang, 2020); the European organization for Nuclear Research (Sadashiv and Kumar, 2011) is developing a mega computing cloud to distribute data to scientists around the world as part of the LHC project; based on cloud computing, FDS Team (Wu, 2019) developed virtual nuclear power plant Virtual4DS in the digital society environment; Wang et al. (2013b) have proposed a cloud-based risk monitor for nuclear power plants; He et al. (2018) have designed and implemented a Thorium-based Molten Salt Reactor cloud simulation system using OpenStack open source platform. Cai et al. (2020) have developed a network-based transient real-time simulation software, NUSOLSIM, for PWR nuclear power plants based on the Client/Server (C/S) architecture; Hui et al. (2013) put forward the idea and implementation scheme of building nuclear power plant design platform based on private cloud architecture by using cloud computing technology; Xin et al. (2018) have developed a cloud quantum computing service “NMRCloudQ”; The concept of a nuclear safety cloud was developed by Ju et al. (2014); Hu et al. (2019), has launched the SuperMC Cloud for nuclear design and safety assessment. The shortcomings of existing international research are highlighted by the following:
(1) Cloud platforms based on the IaaS model have low ease of use and high requirements for non-computer professional in resource allocation.
(2) The flexibility of system architecture is not strong, which leads to the low universality and expansibility of the platform;
(3) C/S-based Cloud Platform, its compatibility is difficult to meet the use of cross-system;
(4) Part of the project is still in the conceptual design or preliminary design stage.
In summary, the trend in nuclear accident simulation software is to implement Internet-based cross-space and cross-platform access and virtualization of computational resources. In response to the high standard and high demand of the nuclear engineering for nuclear reactor safety analysis, this paper takes the nuclear accident simulation software as the object based on the mature cloud computing design model, and the nuclear accident simulation cloud platform with cross terminal, cross platform, multi-user simultaneous availability, low start-up threshold and high scalability is realized. The work of this paper is divided into four parts: the first part is an introduction to the relevant technologies involved, the second part is the architectural design and detailed design of the platform, the third part is the implementation and testing of the platform, and the fourth part is the summary and outlook of the work of this paper.
The system uses the nuclear accident simulation software PCTRAN as the cloud computing object. PCTRAN is a software for simulation and serious accident analysis of nuclear power plants, which Micro-Simulation Technology (MST) Company develops. In 1996, PCTRAN was selected by the International Atomic Energy Agency as the training software for the annual Advanced Reactor Simulation Symposium. As shown in Figure 1, it has a friendly Windows Graphical User Interface and is intuitive and easy to use. In addition to providing a standard run-time display of instrumentation and control, it also provides icons for coolant leaks and containment failures. PCTRAN is influential in function diversity and human-computer interaction. Users can not only stop the pump, switch the safety valve, change the set value of the control system, manual shut-down and other reactor operations at any time, but also can manually set up faster than the actual speed of several times the running state, thus improving the efficiency of the simulation. In 2007, the University of South China purchased three PCTRAN simulation software from MST, such as AP1000 and CPR1000, to meet personnel nuclear reactor safety analysis needs. However, PCTRAN can only run on a single computer under the Windows system, and only using PCTRAN on a single computer will result in a waste of computing resources and cannot realize multi-user real-time operation across space-time and platforms. The stand-alone version of PCTRAN has a serious disconnect with the rapid development of the information age of the Internet.
To make the computer a public resource, like water, electricity and gas in life, provide on-demand computing services for everyone (Kim, 2007; Armbrust et al., 2009). John McCarthy proposed the concept of cloud computing in 1961. Cloud computing is the convergence and development of technologies such as distributed computing, utility computing, virtualization technology, web services and grid computing. Its goal is for users to use the virtual resource pool to the maximum extent through the network at any time and place to deal with large-scale computing problems (Vaquero et al., 2008). Cloud computing provides scalable, inexpensive, distributed computing power over the network (Qiao and Zheng, 2011). The cloud services it offers are three layers of cloud computing: IaaS, Platform as a Server (PaaS) and Software as a Server (SaaS). In this study, a SaaS platform is built to integrate all software services through the system. The nuclear accident simulation software service resources virtualization, the entire service resources scheduling, management, maintenance and other work by specialized personnel responsible for users do not care about the “Cloud” internal implementation, focus on the accident simulation and analysis. The cloud-based platform has the following features:
(1) Service pooling: by virtualization technology, resources such as storage, computing, memory, network, etc., are allocated dynamically according to user needs.
(2) Extensibility: the user can request the service resource quickly and flexibly according to the actual demand at anytime, anywhere, to expand the processing power.
(3) Broadband Network Calls: users use various devices in the browser, through which the network calls cloud computing resources.
(4) Measurability: the use of service resources can be monitored and reported to the background.
(5) Reliability: automatically detect failure nodes, through data redundancy can continue to work normally, provide high-quality services and achieve Service Level Agreement requirements.
With the advent of Web 2.0, the network architecture of the Internet has changed from traditional C/S architecture to a more convenient and efficient B/S architecture. This transformation has simplified the way people access the Internet and accelerated the development of the Internet industry. This platform, based on the B/S architecture, has the following features:
(1) Use the browser as the client. The platform has a UI experience, no installation, just access to the browser. Users can use it anytime, anywhere out of the box, and the application users use will always remain in the latest version. Therefore, for users, using their software reduces the difficulty; For developers, software development and maintenance investment is also reduced.
(2) The server is based on a unified HTTP protocol. HTTP is a stateless connection that disconnects when the request is complete. The HTTP protocol does not persist in sent requests and the corresponding communication state. The goal is to keep the HTTP protocol simple so that many transactions can be processed quickly and efficiently. Internet services worldwide are based on unified communications, which are more convenient and efficient.
Based on the cloud computing design model, the physical resource layer, the virtual resource layer, the resource scheduling layer and the user terminal layer are firstly established. At the same time, considering that NasCloud is oriented towards multi-user real-time parallel operation, it needs high scalability, high concurrency, high availability, and high security. The traditional “Memory-computing integration” architecture in the resource scheduling layer is replaced by a “Memory-computing separation” distributed architecture, which is separated into a “Resource service storage layer” and a “Web service layer.” Finally, the NasCloud is designed into five layers: physical resource layer, virtual resource layer, resource service storage layer, web service layer and user terminal layer, as shown in Figure 2:
Physical resource layer: As the foundation stone of the platform, it should include all hardware resources (server, storage, network, etc.) and be responsible for computing, storage, etc.
Virtual resource layer: It should be generated by each server in the physical resource layer through virtualization technology, which divides the centralized computing resources, storage resources, and network resources into multiple virtual servers with appropriate performance.
Resource service storage layer: When the platform encounters unexpected resource peaks, on the one hand, it should relieve the computation pressure of the web server. On the other hand, it should ensure the consistency of the back-end data of multiple web servers. This layer communicates via the TCP protocol with the web services layer.
Web services layer: This layer must play a top-down role in the platform and ensure the platform security. At the same time, it needs to parse the command and call the corresponding web data to return to the user terminal layer and use the scheduling algorithm to allocate reasonable computing resources for the user.
User terminal layer: The user uses the browser to communicate with the web server through the HTTP protocol; After authentication, the user enters the simulation platform terminal and accesses the cloud computing resources of the virtual resource layer through the WebSocket protocol. At the same time, it also needs to ensure the cross-platform running environment of the screen adaptation and good interaction.
Physical resource layer: The operating system of the computing node still uses the running environment windows supported by PCTRAN; The operating system of the control node adopts the open-source mainstream Linux distribution CentOS 7, reducing the total physical resource footprint and ensure the security and stability of the server.
Virtual resource layer: Use Virtual Box for server virtualization, including Windows, Mac OS, Linux, OpenBSD, Solaris, IBM OS2, Android, iOS, etc. At the same time, the cloud server remote proxy scheme is deployed on the virtual server, and the noVNC is used to communicate the virtual resource layer with the user terminal layer.
Resource services storage layer: Management tools for managing, checking and optimizing database operations are available in MySQL. Therefore, MySQL is a platform database management system to manage web data, compute node real-time load status data and its Uniform Resource Locator.
Web services layer: Based on interactive B/S architecture, in the web backend, choosing the Spring Boot framework to simplify the development of Spring applications, and provides out-of-the-box settings for the Spring platform and third-party libraries, and integrated system monitoring, health detection and other functions to ensure the security and stability of the entire Web environment. To optimize server task scheduling (Liu, 2010), the load least priority algorithm is written in the load balancing component. The computing node uploads the real-time load status data of the system to the database via the HTTP protocol, the web server obtains the server data through Java Data Base Connectivity, normalizes the CPU load α, I/O utilization β, and network utilization η, and gets the system load value F:
The server uses this load value to optimize the allocation of cloud computing resources, and the specific allocation process is shown in Figure 3. Cloud computing security is an important part of cloud computing technology. This layer firstly solves the problem of user identity security by means of account authority control and authentication code, secondly solves the problem of shared business security by binding accounts and resources, and finally solves the problem of user data security by IP access control and access to LAN using firewall.
User terminal layer: using the lightweight cross-screen front-end framework Amaze UI, from small screen to large screen, covering different screen resolutions and finally achieving all screen adaptation. The data transfer and coupling process between the accident analysis data and the platform is shown in Figure 4. The accident parameters obtained and input by the user at the user terminal layer are transformed into a data input stream through the back-end of the cloud platform and transmitted to the nuclear power plant safety analysis software (PCTRAN) through the WebSocket protocol to form the nuclear power plant equipment state input parameters of PCTRAN, which are converted into each equipment sensor transient data and its transient change chart output to the user terminal layer after simulation.
The NasCloud is built using three servers: the control node, the compute node and the data node, all of which are Dell PowerEdge R820. The hardware configuration of each server is the same, as shown in Table 1. According to the different roles of servers, their software environments are shown in Table 2.
Step through the platform deployment flow chart from left to right, as shown in Figure 5.
After the platform is deployed, as shown in Figure 6, users visit the NasCloud platform homepage through the browser, as shown in Figure 7. When the user passes the authentication, they can switch to the simulation service interface, as shown in Figure 8, and click “Start Now” to make the cloud computing resources intelligently allocated by the control node, and the user conducts the simulation of nuclear power plant operation. Different operating system device simulation interfaces are shown in Figures 9–11.
Based on the standard latency testing requirements: uniform timer, accurate to milliseconds, synchronized source time and playback time snapshot. This paper opens a timer accurate to milliseconds on any virtual resource on the server side, and establish communication with it by accessing the NasCloud using a mobile phone, tablet, and PC in turn, and place the original screen displayed on the server side and the screen received by the device in the same camera viewfinder frame for simultaneous photo recording, and calculates the time difference value in the two screens. After several experimental tests, the latency of using the platform is less than 50 ms.
Concurrency testing is performed on NasCloud using the mainstream web stress testing tool Apache Bench. The test results obtained by using the command “ab” and setting the total number of requests “-n” to 10,000 and the concurrency “-c” to 10,000 are shown in Figure 12. From the figure, it can be seen that the server can respond to 99% of the web requests of the platform within 3000 ms, which is a good user experience and meets the request-response criteria.
As a core function of this cloud platform and a necessary requirement for nuclear reactor safety analysis, this paper requires a comprehensive and rigorous testing of the nuclear power plant accident simulation function. The AP1000 nuclear power plant reactor was used to simulate Small Break Loss of Coolant Accident (SBLOCA) and Large Break Loss of Coolant Accident (LBLOCA). The endpoint environments used by users are shown in Table 3. The accident was simulated under NasCloud by multiple users using different environments simultaneously.
Loss of Coolant Accident (LOCA) is the reduction in the reactor coolant system (RCS) charge caused by any pipe rupture or equipment leak that exceeds the charge capacity of the normal water recharge system. The occurrence of LOCA will cause the system to depressurize. The loss of coolant, the rate of system depressurization, the reactor system’s subsequent response to a depressurization accident and the effects caused by the emergency core cooling system are all influenced by the size of the break. For the AP1000 reactor design, RCS line break sizes less than 3/8 in (9.5 mm) in diameter do not cause a water loss incident because the charge flow from one charge pump is sufficient to compensate for the leakage flow at that break diameter and thus maintain the RCS pressure. No safety-related system input is required, and the reactor will shut down normally. Conversely, an RCS pipeline break diameter size greater than 3/8 in (9.5 mm) will cause a water loss incident, when the entire section area greater than or equal to 1 ft2 (929 cm2) is called LBLOCA, and the entire section area less than 1 ft2 (Xiao-jin et al., 2019) is called SBLOCA (Wang, 2011).
The steps for simulating SBLOCA in PCTRAN (Wang, 2011) are shown in Table 4:
The test results are shown in Figure 13, where a break in the cold leg occurs at 5 s of system operation and the RCS pressure drops rapidly. The reactor shutdown signal is triggered at 6 s; The control rods fall and the second circuit turbine trips. 19.5 s one circuit pressure is lower than 11.7 Mpa. g, generate an “S” signal. The 21st s pressurizer level is as low as 5%, triggering a “low 2” protection signal, the core makeup tank (CMT) intervenes, the electric heater of the voltage regulator trips, and the pressure drop trend becomes slower. At 21.5 s, the containment pressure rises to .1 Mpa·g, triggering the passive containment cooling system (PCCS) spray signal. When the RCS pressure drops below 4.8 MPa·g, the system issues a main pump trip signal and the accumulating tank runs automatically. CMT level low to “low 3” protection signal, to ensure passive boron water injection, automatic depressurization system (ADS) level 1, 2, 3 triggered in turn. When the RCS hot leg level falls below 9.7%, the “low 4” protection signal is triggered, the ADS-4 (International Atomic Energy Agency, 2019) is triggered, and the squib valve on the In-Containment Refueling Water Storage Tank (IRWST) injection pipeline is delayed to open, and the pressure drops more slowly. At 145 s, all main pumps are tripped, and RCS provides lateral flow for waste heat export to prevent departure from nucleate boiling (DNB). As the RCS pressure decreases, the coolant leakage rate decreases. As the accident progressed, the rate of coolant leakage at the break leveled off.
The steps for simulating LBLOCA in PCTRAN (Wang, 2011) are shown in Table 5:
The test results are shown in Figure 14. The RCS pressure in LBLOCA drops to 2 Mpa·g in 25 s. Compared with the 265 s required to drop the RCS pressure to the same pressure in SBLOCA, it is evident that the RCS pressure reduction in LBLOCA is much faster. A break occurred in the 5th s. The reactor shutdown signal was generated 1 s later, and the reactor coolant leakage rate was as high as 11,965 kg/s at the beginning. The RCS pressure quickly drops to the highest local saturation pressure of the fluid, and a coolant loop is quickly sprayed and released from the break into the containment. The containment pressure rises to .1 Mpa·g at 6.5 s, triggering the PCCS spray signal. Two “S” signals are generated within 1 s: the reactor building pressure is higher than .2 Mpa·g, and the first circuit pressure is lower than 11.7 Mpa·g. The 8.5st s pressurizer level is as low as 5%, triggering a “low 2” protection signal, the CMT intervenes, the electric heater of the voltage regulator trips, and the pressure drop trend becomes slower, and then stabilized near the reactor building pressure. With the loss of most of the reactor coolant and the depressurization of the RCS, the leak rate decreases rapidly, and the squib valve and check valve on the IRWST injection line open one after another. The gravity injection system of the 2 IRWSTs starts to inject boron water into the reactor pressure vessel, and the level of the IRWST slowly decreases while the level of the containment increases. Trisodium phosphate begins to dissolve when the containment level reaches the pH adjustment baskets position. Eventually, containment recirculation will be established, and the natural circulation of water in the containment provides long-term recirculation cooling for the core (Khan et al., 2021), with the coolant system pressure leveling off. In the 30 s, all main pumps tripped until the 74 s when the passive residual heat removal system (PRHRS) was triggered to close the IRWST catch basin with the steam trap valve.
In the above accident simulation, the entire operation process is easy to understand due to PCTRAN’s graphical interface, which eliminates the need for manual modeling and makes each piece of equipment in the power plant visible to the user. It helps participants quickly and comprehensively acquire knowledge about the operation of nuclear power plants. The data in the accident simulation results of the NasCloud and the stand-alone PCTRAN under the three test environments are precisely the same. The characteristics of the parameter change trends are in line with the standards, which verifies the reliability of the NasCloud, and at the same time, realizes the simultaneous multi-user cross-platform application, expanding the cloud computing capability of PCTRAN and laying a solid foundation for Internet-based cross-time and cross-platform nuclear reactor safety analysis.
Based on the idea of cloud computing, this paper successfully implements the NasCloud, a cross-terminal, cross-platform and multi-user cloud platform for nuclear power plant accident simulation, based on the original stand-alone version of nuclear power plant accident simulation software PCTRAN, using B/S architecture to build a Web client and noVNC solution. The platform is characterized by high scalability, high concurrency and high security through the minimum load priority algorithm and the distributed resource storage structure of “storage and calculation separation”. The platform has been tested with low latency and high concurrency, and its simulation functions have been verified by simulating SBLOCA and LBLOCA of the AP1000. The results are compared and verified to show that the NasCloud and PCTRAN are consistent in accident simulation functions and results. NasCloud also features flexible deployment, high scalability, low maintenance requirements, high performance, low user requirements and strong copyright protection.
On the one hand, the cloud platform developed in this paper can meet the practical needs of nuclear reactor safety analysis on a large scale and with high difficulty, breaking through the restrictions of an epidemic environment. On the other hand, it is also a valuable attempt to use “cloud computing” in the traditional nuclear engineering field to improve the accessibility of nuclear reactor safety analysis while reducing the cost of resources and carbon emissions. In addition, the NasCloud developed in this paper can be applied to the cloud computing of other nuclear engineering design and simulation software.
In the future work, in order to cope with the increase of parallelism and concurrency brought by the growth of the number of users, the underlying framework will be optimized to support the flow peak clipping function on the basis of enhancing the server performance and increasing the number of servers; meanwhile, in order to strengthen the integrity of the platform functions, more nuclear simulation software will be integrated in this platform to finally realize the multi-physics multi-scale coupled analysis cloud platform.
The original contributions presented in the study are included in the article/supplementary material, further inquiries can be directed to the corresponding authors.
PC: Methodology, software, writing—original draft. XC: Validation, data curation. JX: Conceptualization, writing—review and editing, funding acquisition. WX: Formal analysis, investigation. TY: Resources, project administration.
This work is supported by the Science and Technology Innovation Program of Hunan Province (2020RC4053).
The authors declare that the research was conducted in the absence of any commercial or financial relationships that could be construed as a potential conflict of interest.
All claims expressed in this article are solely those of the authors and do not necessarily represent those of their affiliated organizations, or those of the publisher, the editors and the reviewers. Any product that may be evaluated in this article, or claim that may be made by its manufacturer, is not guaranteed or endorsed by the publisher.
Armbrust, M., Fox, A., and Griffith, R. (2009). Above the clouds: A berkeley view of cloud computing[R]. Technical Report UCB/EECS-2009-28. Berkeley: EECS Department, University of California.
Cai, Q., Ge, L., and Shan, J. (2020). Nusolsim: A network-based PWR nuclear power plant simulation software [J]. Nucl. Power Eng. 41 (01), 99–103. doi:10.13832/j.jnpe.2020.01.0099
Cho, H. S., and Woo, T. H. (2017). Real-time management (RTM) by cloud computing system dynamics (CCSD) for risk analysis of Fukushima nuclear power plant (NPP) accident[J]. Atw. Int. Z. fuer Kernenerg. 62 (3), 171–176.
Gao, H., Qu, M., Qin, L., and Jing, Y. (2017). Research and design on virtual DCS process control platform in nuclear power plant [J]. Comput. Simul. 34 (02), 144–149. doi:10.3969/j.issn.1006-9348.2017.02.032
Gu, Z. (2017). Analysis on unprotected transient safety characteristics of lead-based research reactor [D]. China: University of Science and Technology of China.
He, Y., Chen, M., and Dai, Z. (2018). Preliminary design and implementation of TMSR cloud simulation platform [J]. Nucl. Tech. 41 (07), 79–86. doi:10.11889/j.0253-3219.2018.hjs.41.070603
Hu, L., Long, P., Song, J., He, T., Wang, F., Hao, L., et al. (2019). SuperMC cloud for nuclear design and safety evaluation. Ann. Nucl. Energy 134, 424–431. doi:10.1016/j.anucene.2019.07.019
Hui, P., Xiao, A. H., Da-Wei, Y., Wang, Z., and Guan, H. (2013). Study on application of cloud computing technology in nuclear power plant design platform [J]. Nucl. Power Eng. 34 (1), 214–217. doi:10.3969/j.issn.0258-0926.2013.z1.052
International Atomic Energy Agency (2019). PCTRAN generic pressurized water reactor simulator exercise handbook [M/OL], training course series. Available at: https://www.iaea.org/publications/13463/pctran-generic-pressurized-water-reactor-simulator-exercise-handbook.
Jia, D., and Wu, Z. (2022). Development model of enterprise green marketing based on cloud computing. Wirel. Commun. Mob. Comput. 2022, 1–10. doi:10.1155/2022/4931374
Ju, Z., Zhou, T., Li, J., and Xiao, Z. (2014). Research on the application of cloud computing in nuclear safety analysis [J]. Industrial Saf. Environ. Prot. 40 (10), 32–35. doi:10.3969/j.issn.1001-425X.2014.10.012
Khan, I., Wang, M., Zhang, Y., Tian, W., Su, G., and Qiu, S. (2021). CFD study on onset of liquid entrainment through ADS-4 branch line in AP1000. Nucl. Eng. Des. 380, 111299. doi:10.1016/j.nucengdes.2021.111299
Khan, I., Wang, M., Zhang, Y., Tian, W., Su, G., and Qiu, S. (2020). Two-phase bubbly flow simulation using CFD method: A review of models for interfacial forces. Prog. Nucl. Energy 125, 103360. doi:10.1016/j.pnucene.2020.103360
Kim, K. D. (2007). A web-based nuclear simulator using RELAP5 and LabVIEW[J]. Nucl. Eng. Des. 237 (11), 1185–1194. doi:10.1016/j.nucengdes.2007.01.004
Kim, K. D., and Rizwan, U. (2007). A web-based nuclear simulator using RELAP5 and LabVIEW. Nucl. Eng. Des. 237 (11), 1185–1194. doi:10.1016/j.nucengdes.2007.01.004
Li, D., Zheng, L., Pan, Y., Wang, K., and Tang, L. (2011). The improvement of the distributed training system for PCTran/AP1000 [J]. Value Eng. 30 (10), 179–180. doi:10.3969/j.issn.1006-4311.2011.10.134
Lie, W., Jiang, B., and Zhao, W. (2020). Obstetric imaging diagnostic platform based on cloud computing technology under the background of smart medical big data and deep learning. IEEE Access 8, 78265–78278. doi:10.1109/access.2020.2988563
Liu, W. (2008). On-line simulation research on reactor's coolant system of nuclear power plant [D]. China: Harbin Engineering University.
Lu, C. (2015). Design and online simulation of level control system for steam generator [D]. China: Shanghai Jiao Tong University.
Qiao, L., and Zheng, X. (2011). Research survey of cloud computing [J]. Comput. Sci. 38 (04), 32–37. doi:10.3969/j.issn.1002-137X.2011.04.006
Ren, Y., and Ren, X. (2009). Design and development of nuclear power plant training simulator [J]. Syst. Simul. Technol. 5 (02), 125–129. doi:10.3969/j.issn.1673-1964.2009.02.011
Sadashiv, N., and Kumar, S. M. D. (2011). “Cluster, grid and cloud computing: A detailed comparison[C],” in 2011 6th international conference on computer science & education (ICCSE), Singapore, 03-05 August 2011 (IEEE), 477–482.
Vaquero, L. M., Rodero-Merino, L., Caceres, J., and Lindner, M. (2008). A break in the clouds: Towards a cloud definition[J]. ACM sigcomm Comput. Commun. Rev. 39 (1), 50–55. doi:10.1145/1496091.1496100
Wang F., F., Hu, L., and Wang, J. (2013). “A nuclear power plant risk monitor based on cloud computing[C],” in 2013 International Conference on Quality, Reliability, Risk, Maintenance, and Safety Engineering (QR2MSE), Chengdu, China, 15-18 July 2013 (IEEE).
Wang, M., Manera, A., Petrov, V., Memmott, M. J., Qiu, S., and Su, G. (2020). Passive decay heat removal system design for the integral inherent safety light water reactor (I2S-LWR). Ann. Nucl. Energy 145, 106987. doi:10.1016/j.anucene.2019.106987
Wang M., M., Tian, W., Qiu, S., Su, G., and Zhang, Y. (2013). An evaluation of designed passive Core Makeup Tank (CMT) for China pressurized reactor (CPR1000). Ann. Nucl. Energy 56, 81–86. doi:10.1016/j.anucene.2013.01.010
Wang, M., Zhao, H., Zhang, Y., Su, G., Tian, W., and Qiu, S. (2012). Research on the designed emergency passive residual heat removal system during the station blackout scenario for CPR1000. Ann. Nucl. Energy 45, 86–93. doi:10.1016/j.anucene.2012.03.004
Wang, Z. (2011). Research of AP1000 passive core cooling system and system design transient [J]. China Nucl. Power 4 (03), 195–206.
Woo, T. H., and Jang, K. B. (2020). Cloud computing based analysis incorporated with the internet of things (iot) in nuclear safety assessment for fukushima dai-ichi disaster[J]. J. Korea Internet Things Soc. 6 (1), 73–81. doi:10.20465/KIOTS.2020.6.1.073
Woo, T. H. (2014). Real time analysis for atmospheric dispersions for Fukushima nuclear accident: Mobile phone based cloud computing assessment. Ann. Nucl. Energy 63, 255–260. doi:10.1016/j.anucene.2013.07.020
Wu, Y. (2019). Development and application of virtual nuclear power plant in digital society environment. Int. J. Energy Res. 43 (4), 1521–1533. doi:10.1002/er.4378
Xiao-jin, M., Rao, G., and Hua-hu, X. (2019). Research on task scheduling in cloud computing [J]. Comput. Sci. 46 (03), 1–8. doi:10.11896/j.issn.1002-137X.2019.03.001
Xin, T., Huang, S., Lu, S., Li, K., Luo, Z., Yin, Z., et al. (2018). NMRCloudQ: A quantum cloud experience on a nuclear magnetic resonance quantum computer. Sci. Bull. 63 (1), 17–23. doi:10.1016/j.scib.2017.12.022
Yan, J. (1991). Overview of the application of simulation technology in nuclear power plants [J]. Electr. Power Stand. Constr. Cost Control Inf. 21(07), 56–60.
Zhao, F. (2020). Key technologies and applications for cloud CAD software [J/OL]. Comput. Integr. Manuf. Syst. 6, 1–10. doi:10.13196/j.cims.2022.04.001
Keywords: cloud platform, nuclear accident simulation, B/S architecture, LOCA, nuclear reactor safety analysis
Citation: Chen P, Chen X, Xie J, Xiong W and Yu T (2023) Design and implementation of cloud platform for nuclear accident simulation. Front. Energy Res. 10:1075224. doi: 10.3389/fenrg.2022.1075224
Received: 20 October 2022; Accepted: 12 December 2022;
Published: 23 January 2023.
Edited by:
Mingjun Wang, Xi’an Jiaotong University, ChinaReviewed by:
Pengfei Wang, Xi’an Jiaotong University, ChinaCopyright © 2023 Chen, Chen, Xie, Xiong and Yu. This is an open-access article distributed under the terms of the Creative Commons Attribution License (CC BY). The use, distribution or reproduction in other forums is permitted, provided the original author(s) and the copyright owner(s) are credited and that the original publication in this journal is cited, in accordance with accepted academic practice. No use, distribution or reproduction is permitted which does not comply with these terms.
*Correspondence: Jinsen Xie, amluc2VuX3hpZUB1c2MuZWR1LmNu; Tao Yu, eXV0YW8yOUBzaW5hLmNvbQ==
Disclaimer: All claims expressed in this article are solely those of the authors and do not necessarily represent those of their affiliated organizations, or those of the publisher, the editors and the reviewers. Any product that may be evaluated in this article or claim that may be made by its manufacturer is not guaranteed or endorsed by the publisher.
Research integrity at Frontiers
Learn more about the work of our research integrity team to safeguard the quality of each article we publish.