- 1School of Mechanical and Vehicle Engineering, Linyi University, Linyi, Shandong, China
- 2The 38th Research Institute of China Electronic Technology Corporation, Hefei, Anhui, China
- 3Key Laboratory of Energy Thermal Conversion and Control of Ministry of Education, School of Energy and Environment, Southeast University, Nanjing, Jiangsu, China
- 4School of Electronics, Southeast University, Nanjing, Jiangsu, China
Introduction
With the thrust of science and technology as well as higher performance requirements, the assembly density and power consumption of radar equipment are getting higher (Ping et al., 2009). Unlike ground-based radars, airborne radars are almost applied in controlling and guiding weapons, but also for aerial vigilance and reconnaissance to navigate accurately and fly safely. Moreover, due to the limitation of aircraft carrying capacity, the miniaturization and lightening of airborne radars have become an urgent need (Tang et al., 2011). The rapid development of electronic component integration technology has contributed to the miniaturization and lightness of airborne radars (Wang et al., 2021). For example, in 1990s, the heat flux of integrated circuits was only 20–30 W/cm2 (Ping et al., 2009), but now it has exceeded 100 W/cm2, and this development trend is still expanding. However, the miniaturization of radar also increases the heat flux density, making the thermal management of airborne radars more difficult. In view of the increasing heat flux of airborne radar equipment, harsh environmental conditions, and high reliability requirements, it is urgent to carry out in-depth and systematic research on cooling technology of radar equipment.
Thermal management of airborne radars is an important guarantee for its long-term stable and reliable operation (Wang et al., 2018). As common thermal management methods, forced air cooling (Khalaj, A et al., 2017) and single-phase liquid cooling technologies (Flouris, A et al., 2006) have been widely used to cool airborne radars. However, as the heat flux density of airborne radars continues to rise, conventional cooling technologies (i.e., forced air cooling and single-phase liquid cooling) are reaching their bottlenecks (Chen et al., 2015). Consequently, cooling technologies with higher heat dissipation capacity need to be sought to meet the cooling requirements of the next-generation airborne radars. To comprehensively understand the thermal management development of airborne radars, the investigational status of conventional cooling technologies is firstly reviewed. On this basis, the feasibility of the new cooling technologies is also analyzed and discussed. Moreover, the future development of airborne radar cooling technology is also prospected, providing guidance and reference for the future innovation of thermal management technology for airborne radars, which is summarized in Figure 1A.
Conventional cooling technologies for airborne radars
Forced air cooling
Forced air cooling technology is a widely used way for the heat dispassion of airborne radars (Wei et al., 2014), whose basic principle is to carry away the heat generated by airborne radars via forced cold air. It has the advantages of simple equipment, reliable performance, convenient operation, and maintenance (Zhang et al., 2021). Moreover, cold air is easily accessible in forced air cooling systems and avoids the issues of icing and leakage that are common in single-phase liquid cooling systems. Cheng et al. (2018) introduced the design and optimization of forced air cooling systems for a radar transmitter in detail. Figure 1B shows the working principle of the forced air-cooling system for a radar transmitter. As shown in the figure, the radar transmitter is arranged in a closed electronic chassis to improve its ability to resist harsh environments. Given this, the heat dissipation mode herein is the combination of heat conduction and forced convection. Moreover, the experimental results indicated that the optimized forced air-cooling system meets the cooling requirements of the radar transmitter even when operating continuously at the maximum permissible ambient temperature. Considering the environmental features of airborne radar, Liu et al. (2016) carried out the thermal design of a closed airborne radar. Simulation analysis and test results indicated that the forced air cooling technology could guarantee the normal running of the radar in the airplane at high temperatures. However, the cooling effect of air is easily affected by the environment. Moreover, the specific heat capacity of air is small and the temperature control response speed is slow, leading to the phenomenon that the temperature in the engine room keeps rising.
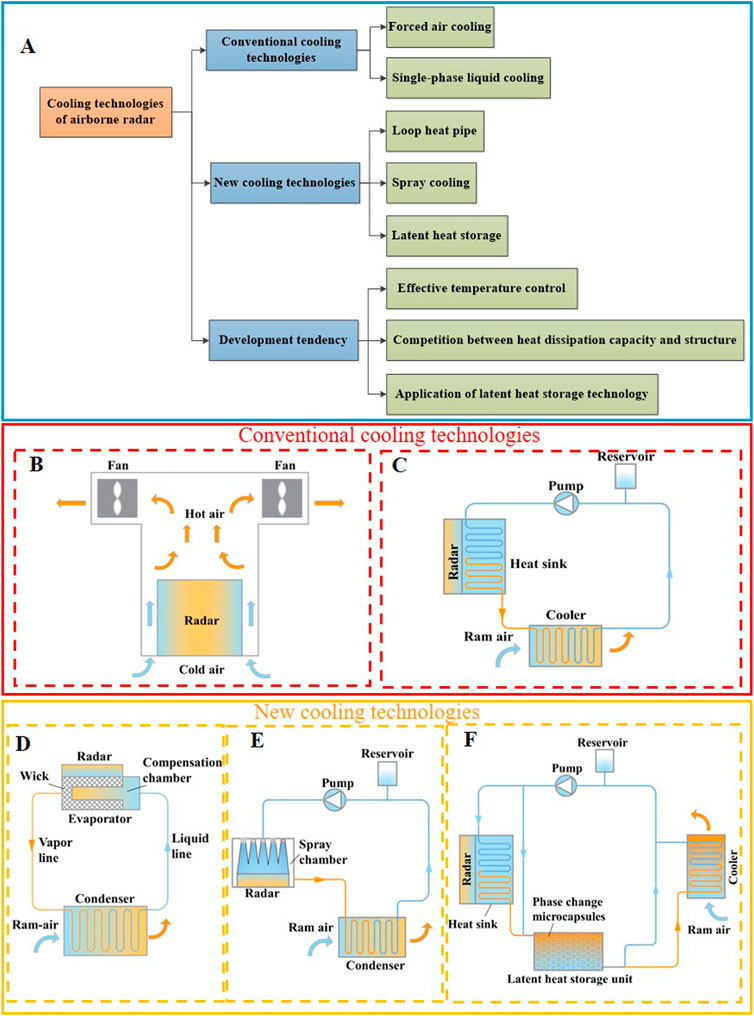
FIGURE 1. Cooling technologies of airborne radars: (A) Classification of airborne radar cooling modes, (B) Forced air cooling, (C) Single-phase liquid cooling, (D) Loop heat pipe cooling, (E) Spray cooling, (F) Latent heat storage.
Single-phase liquid cooling
Compared with traditional air-cooling technology, single-phase liquid cooling has significant advantages in heat dissipation capacity and response speed. Moreover, the improvement in convective heat transfer efficiency contributes to the more compact structure of liquid cooling systems. Hence, it can effectively alleviate the contradiction between the limited space and the increasing power consumption of current airborne radars. In addition, single-phase liquid cooling technology allows airborne radars to be designed as confined spaces, avoiding the risk of loss of life and reliability caused by dust, particles, and salt spray erosion of airborne radars.Gao et al. (2022) designed a new liquid cooling heat exchanger. The test and application results indicated that the heat-sinking capacity of the equipment is greatly enhanced. The automatic control of the liquid temperature is realized and the support efficiency of airborne radars is greatly improved. Wang et al. (2018) introduced a compact liquid cooling model for airborne radars, as presented in Figure 1C. Compared with other cooling methods, the volume is reduced by 8.6% and the weight is reduced by 26% under the same working condition. This paper has a practical reference for the compact design of liquid cooling systems for airborne radars and other electronic equipment. With the further requirement of heat dissipation, the single-phase liquid cooling has been difficult to meet the cooling demand of the new generation of airborne radars, so it is urgent to look for some new cooling technologies (Zhang et al., 2021).
New cooling technologies for airborne radars
Throughout the current cooling technologies for electronic devices, there are also several new cooling technologies with excellent application prospects, mainly including loop heat pipe, spray cooling and latent heat storage technology.
Loop heat pipe
A loop heat pipe is a heat transfer equipment that driven by the capillary force, whose heat transfer capacity can reach up to 30 W/cm2 (Xue, Qu et al., 2020). The loop heat pipe system has the advantages of long transmission distance, anti-gravity operation, autonomous start, and adaptive temperature control (Liu et al., 2013). Moreover, the loop heat pipe is highly reliable because it does not contain mechanical moving parts (Sohel et al., 2017). For the thermal management of airborne radars, a new cooling method of loop heat pipe was proposed by Wei et al. (2014), which is presented in Figure 1D. As shown in the figure, the evaporator absorbs heat from the airborne radar to evaporate the working fluid in capillary tubes. As the steam pressure increases, a pressure differential is created along the capillary tube length, driving the two-phase flow of working fluid towards the condenser where it is condensed into a liquid phase. Since the liquid saturation in the evaporator decreases, self-compensation of working fluid is produced by the capillary action of capillary cores. Simultaneously, the condensate is pumped or returned to the evaporator by gravity. Therefore, an automatic circulation system of evaporation, condensation, and liquid reflux is formed, providing a solution for the heat dispassion of airborne radars.
Spray cooling
Spray cooling relies on the process of vapor-liquid phase change. Atomized droplets are sprayed upon the heat exchange and the heat is taken away by the evaporation phase change of the medium. Although spray cooling has the disadvantages of large volume and high cost, it has an excellent heat transfer performance, low superheat and large critical heat flux. Therefore, spraying cooling is a competitive thermal control technology for airborne radars in the long run. The schematic diagram of a spray cooling system is presented in Figure 1E (Wang et al., 2017). As plotted in the figure, the liquid coolant is quickly atomized into small droplets through the interaction with air after ejecting from the pressurized nozzle, and then moves to the heat source surface of airborne radars. In this context, the flow and evaporation of the liquid film take away part of the heat consumption. Simultaneously, the violent movement of the liquid film also excites the creation of numerous bubbles, resulting in nucleation boiling on the airborne radar surface and heat dissipation to the environment.
Latent heat storage
Latent heat storage technology can absorb heat from airborne radars and use the isothermal latent heat storage capacity to extend the release time of heat load. Latent heat storage unit can be existed in a manner of fin tube, single phase-change capsule (Chen et al., 2015; Chen et al., 2017), multiple phase-change capsule (Gao et al., 2019), heat pipe coupled with latent heat storage. Since the latent heat storage technology breaks through the mismatch of energy supply and demand in time and space through the melting and solidification of PCMs, it ensures that the heat load of airborne radars can be reasonably and effectively utilized. Due to the advantages of high energy density, almost constant phase change temperature, and high controllability, the latent heat storage technology is extensively applied in area of electricity peak shaving and valley filling (Haupt et al., 2020), waste heat recovery (Sun et al., 2019), building energy saving and thermal management of electronic devices (Zhang et al., 2010). The application of latent heat storage units in the thermal management of airborne radars is presented in Figure 1F. The heat from the airborne radar is stored in the latent heat storage unit and then taken away by the cooling circuit. This cooling method is mainly applied for airborne radars in intermittent operation mode.
Opportunities and challenges
How to achieve efficient heat dissipation for airborne radars has become one of the key research points in the development of future thermal management systems for airborne radars. The traditional cooling method has reached the technical bottleneck, which limits the further development of airborne radars. Driven by economic and social benefits, it is urgent to innovate the cooling technology for airborne radars to guarantee the reliable, and efficient running of airborne radars. Wang, 2018.
1. Conventional heat-sinking technologies, including forced air cooling as well as single-phase liquid cooling, cannot satisfy the heat dissipation demands of high-power airborne radars. Loop heat pipe and spray cooling, which can realize large heat load under limited temperature difference, has gradually become the main research direction. However, there are still some problems to be studied and solved, such as the effective temperature control for airborne radars via loop heat pipe cooling technology.
2. With the development of existing cooling technologies develop from passive to active and single-phase to multiphase flow, the cooling system’s heat dissipation capability has increased substantially. Although the introduction of new heat dissipation modes may lead to changes in the overall structure, as long as the improvement in heat dissipation capability is significant, it is important for developing thermal management technology of airborne radars.
3. The application of latent heat storage technology can effectively mitigate the impact of short-term high heat flux on the thermal management system of airborne radars. Moreover, the constant temperature during the phase change process can also be applied to electronic devices with temperature control requirements. The application of this technology in the thermal management system of airborne radars is an inevitable development trend.
Author contributions
PL: Supervision, CZ: Conceptualization. YY and ZZ: Investigation, Writing—Original Draft, Writing—Review, and Editing. XZ and XL: Investigation. HJ: Validation.
Conflict of interest
ZZ and HJ is employed by the The 38th Research Institute of China Electronic Technology Corporation.
The remaining authors declare that the research was conducted in the absence of any commercial or financial relationships that could be construed as a potential conflict of interest.
Publisher’s note
All claims expressed in this article are solely those of the authors and do not necessarily represent those of their affiliated organizations, or those of the publisher, the editors and the reviewers. Any product that may be evaluated in this article, or claim that may be made by its manufacturer, is not guaranteed or endorsed by the publisher.
References
Chen, Y. P., and Deng, Z. L. (2017). Hydrodynamics of a droplet passing through a microfluidic T-junction. J. Fluid Mech. 819, 401–434. doi:10.1017/jfm.2017.181
Chen, Y. P., Liu, X. D., Zhang, C. B., and Zhao, Y. J. (2015). Enhancing and suppressing effects of an inner droplet on deformation of a double emulsion droplet under shear. Lab. Chip 15 (5), 1255–1261. doi:10.1039/c4lc01231c
Chen, Y. P., Liu, X. D., and Zhao, Y. J. (2015). Deformation dynamics of double emulsion droplet under shear. Appl. Phys. Lett. 106 (14), 141601. doi:10.1063/1.4916623
Cheng, H., and Zhang, X. (2018). Design and analysis of forced air cooling for a weather radar transmitter. Appl. heaven earth 37 (10). doi:10.19652/j.cnki.femt.180999
Flouris, A., and Cheung, S. (2006). Design and control optimization of microclimate liquid cooling systems underneath protective clothing. Ann. Biomed. Eng. 34 (3), 359–372. doi:10.1007/s10439-005-9061-9
Gao, T., and Yang, H. (2022). New type liquid-cooled heat exchanger for aircraft radar. Hydraulics pneumatics seals (7). doi:10.3969/j.issn.1008-0813.2022.07.013
Gao, W., and Chen, Y. P. (2019). Microencapsulation of solid cores to prepare double emulsion droplets by microfluidics. Int. J. Heat Mass Transf. 135, 158–163. doi:10.1016/j.ijheatmasstransfer.2019.01.136
Haupt, L., Schoepf, M., Wederhake, L., and Weibelzahl, M. (2020). The influence of electric vehicle charging strategies on the sizing of electrical energy storage systems in charging hub microgrids. Appl. Energy 273, 115231. doi:10.1016/j.apenergy.2020.115231
Khalaj, A., and Halgamuge, S. (2017). A Review on efficient thermal management of air- and liquid-cooled data centers: From chip to the cooling system. Appl. Energy 205, 1165–1188. doi:10.1016/j.apenergy.2017.08.037
Liu, X. D., Chen, Y. P., and Shi, M. H. (2013). Dynamic performance analysis on start-up of closed-loop pulsating heat pipes (CLPHPs). Int. J. Therm. Sci. 65, 224–233. doi:10.1016/j.ijthermalsci.2012.10.012
Liu, X., and Zhao, D. (2016). Thermal design of closed cabinet for airborne radar. Electro-Mechanical Eng. 32 (6). doi:10.19659/j.issn.1008-5300.2016.06.015
Ping, L. (2009). Current status and development trends of thermal control technology for phased array radar system. Mod. Radar 31 (5). doi:10.16592/j.cnki.1004-7859.2009.05.004
Sohel, M., and Castro, C. (2017). A critical review of traditional and emerging techniques and fluids for electronics cooling. Renew. Sustain. Energy Rev. 78, 821–833. doi:10.1016/j.rser.2017.04.112
Sun, L., Jin, Y., Pan, L., Shen, J., and Lee, K. Y. (2019). Efficiency analysis and control of a grid-connected PEM fuel cell in distributed generation. Energy Convers. Manag. 195, 587–596. doi:10.1016/j.enconman.2019.04.041
Tang, A., and Xiang, H. (2011). Thermal design of an airborne radar box and its simulation-based optimization. Electro-Mechanical Eng. 27 (2). doi:10.19659/j.issn.1008-5300.2011.02.005
Wang, J. (2018). Study of the compact liquid cooling unit designed for an airborne radar. Electro-Mechanical Eng. 34 (3). doi:10.19659/j.issn.1008-5300.2018.03.011
Wang, J., Gao, W., Zhang, H., Zou, M. H., Chen, Y. P., and Zhao, Y. J. (2018). Programmable wettability on photocontrolled graphene film. Sci. Adv. 4 (9), eaat7392. doi:10.1126/sciadv.aat7392
Wang, J., Li, Y., Xiong, K., and Ning, X. (2017). Investigation of a gravity-immune chip-level spray cooling for thermal protection of laser-based wireless power transmission system. Int. J. Heat Mass Transf. 114, 715–726. doi:10.1016/j.ijheatmasstransfer.2017.06.111
Wang, J., Li, Y., Liu, X., Shen, C., Zhang, H., and Xiong, K. (2021). Recent active thermal management technologies for the development of energy-optimized aerospace vehicles in China. Chin. J. Aeronautics 34 (2), 1–27. doi:10.1016/j.cja.2020.06.021
Wei, T., and Qian, J. (2014). Thermal simulation of an airborne millimeter-wave radar antenna. Electro-Mechanical Eng. 30 (3).
Xue, Z. H., Qu, W., and Xie, M. H. (2020). High performance loop heat pipe with flat evaporator for energy-saving cooling systems of supercomputers. J. Heat Transf. 142 (3). doi:10.1115/1.4045730
Zhang, C. (2021). Review on the cooling technology of wind turbine systems. J. East China Jiaot. Univ. 38 (5). doi:10.16749/j.cnki.jecjtu.20211026.005
Keywords: airborne radar, cooling technology, loop heat pipe, latent heat storage, spraying cooling, thermal management
Citation: Yin Y, Zhu Z, Li P, Zhang X, Liu X, Jiang H and Zhang C (2022) Opinions on the research status and development trend of airborne radar cooling technology. Front. Energy Res. 10:1047600. doi: 10.3389/fenrg.2022.1047600
Received: 18 September 2022; Accepted: 31 October 2022;
Published: 11 November 2022.
Edited by:
Ang Li, Suzhou University of Science and Technology, ChinaReviewed by:
Zhenying Zhang, North China University of Science and Technology, ChinaCopyright © 2022 Yin, Zhu, Li, Zhang, Liu, Jiang and Zhang. This is an open-access article distributed under the terms of the Creative Commons Attribution License (CC BY). The use, distribution or reproduction in other forums is permitted, provided the original author(s) and the copyright owner(s) are credited and that the original publication in this journal is cited, in accordance with accepted academic practice. No use, distribution or reproduction is permitted which does not comply with these terms.
*Correspondence: Peizhen Li, bGlwZWl6aGVuQGx5dS5lZHUuY24=