- 1Department of Mechanical Engineering, Xi’an Jiaotong University City College, Xi’an, Shaanxi, China
- 2Engineering Research Center of Robot and Intelligent Manufacturing, University of Shaanxi Province, Xi’an, Shaanxi, China
With the rapid development of high-speed rotating machinery, diaphragm couplings are widely used in energy equipment such as compressors, generators, drilling equipment, and turbine drives by virtue of their high sensitivity, oil resistance and corrosion resistance. However, the theoretical research of this product mainly focuses on the design of diaphragm profile, the combination form between diaphragms, the overall structural form of diaphragm coupling and the axial dynamic characteristics of diaphragm coupling. Therefore, this paper analyzes and summarizes the current research status of diaphragm couplings in the world, and puts forward the problems that need to be solved in the field of diaphragm coupling research, and proposes a new direction for the subsequent research.
Introduction
Metal diaphragm coupling is a high-tech coupling element of modern power equipment with multi span rotor system. It has the following advantages in realizing the basic function of transmitting power and torque (Mancuso, 1896; Mancuso et al., 1990; Piotrowski, 2007): It currently has advantages in achieving the basic functions of transmitting power and torque, which can be described in the following eleven aspects: 1) No lubrication required; 2) It has high torque transmission ability without increasing coupling size; 3) Great compensation for misalignment; 4) Maximum axial offset compensation capability; 5) Suitable for high temperature operation; 6) Suitable for all types of joints: splines, tapered shafts, flanges, etc; 7) Produce lower reaction moment and force; 8) Generate foreseeable moments and forces; 9) Easy to balance; 10) Years of operation without maintenance, no fault; 11) Vibration of the lower input equipment.
Therefore, it is widely used in various types of gas turbines, such as aeroengine, warship or ship engine, high efficiency gas turbine unit for power generation and small and micro gas turbine of distributed energy supply system. In rotating equipment, the center line of two or more rotating shafts is not in the right direction due to the existence of manufacturing and installation errors. Especially in high speed rotating machinery and rigid coupling system of multi span rotor, the system problems such as super second critical speed operation, excessive vibration, serious rotor/stator friction and bearing damage are often encountered, which are difficult to overcome in the short term. Because of the metal diaphragm coupling has two or more core parts of elastic diaphragm, it has excellent axial, transverse and angular misalignment compensation. If it is applied to the connection of multi span rotors, it can effectively reduce the critical speed of the system, control it below the second or even first critical speed, which significantly reduces the difficulty of modern high-tech power equipment development, as shown in Figure 1. Therefore, the research of metal diaphragm coupling is of great significance to the national defense and the consolidation and development of the important technology industry related to people’s livelihood.
The structure of metal diaphragm coupling
Metal diaphragm coupling can be divided into bolt connection and interference connection by its different forms of connection with shaft. The diaphragms are key parts to keep nice property for the coupling, so there are different structure profiles, which are usually linear profile, conical profile (Uniform centrifugal stress) and curved profile (Uniform shear stress), as Figure 2. In order to adapt to high temperature conditions and have greater misalignment compensation ability, its elastic elements are often made of materials with better strength and fatigue characteristics, such as titanium alloy (Ti-6Al-4V) (Editorial board of China Aviation Materials Manual, 2002), 17-4PH Stainless steel (Stewart et al., 1999), etc.
Bolted diaphragm coupling (Calistrat, 1980) was designed and developed by Goodrich company (former Bendix company) in the late 1940s. It is commonly used in medium and large gas turbines. It is easy to install. There are two main design forms: single diaphragm (Figures 3, 4) and multi diaphragm (Figure 5). Especially in the case of multi diaphragm, it has very good misalignment compensation characteristics, and the working speed can reach 60000r/min. As shown in Figure 3, the single diaphragm coupling with one diaphragm disk (consisting of flange, film and hub) is provided on the left and right. The membrane plate and flange are connected by bolts on the outer edge of the membrane disc. The two membrane plates are connected together by interference assembly or welding through an intermediate shaft. The size and shape of flange and diaphragm plate on both sides are identical. The flange on both sides is connected with the rotating shaft by key to form transmission structure. The physical figure is shown in Figure 4. Figure 5 shows the connection positions and style (electron beam weld) of multi membrane diaphragm coupling, the outer diaphragms are usual more thicker than inner diaphragms.
Interference coupling type diaphragm coupling (Stewart et al., 1999; Stewart et al., 2000) was designed by capstone company in the beginning of 2000, and is often used in small and micro gas turbines. It is more concise in structure than bolt coupling diaphragm coupling, and further improves the performance of flexible coupling. The maximum speed can reach 96000r/min, as shown in Figure 6. The diaphragm coupling is mainly composed of one coupling cup and intermediate shaft (also called spacer shaft) on the left and right sides. The coupling cup can be divided into two parts:the coupling unit (connecting cup wall) and the membrane disk (the bottom of the cup). In order to reduce the pre stress of assembly, the interference fit of the outer surface of the drive end of the two coupling units, the interference fit of the inner surface of the driven end side, and the size of the two diaphragm plates are generally different.
The two coupling types of diaphragm disc are core elastic elements, and they often have the same thickness, cone, hyperbolic or waveform, and the intermediate shaft can be hollow or solid. Considering the structures of two coupling types and according to the available literatures (Calistrat, 1980; Stewart et al., 1999; Stewart et al., 2000), the interference coupling type has the following advantages compared with the bolt type diaphragm coupling for the applications:
1) Interference coupling makes the coupling have good adaptive performance.
2) When the size of the two diaphragm plates is equal, the interference coupling has higher compensation capacity of the anisotropy.
3) It has a higher maximum allowable speed.
4) Compact structure and high spatial utilization.
Development and application of diaphragm coupling
Membrane disc couplings are a product of the development of modern rotor systems operating at high speeds. As early as the late 1940s, due to the emergence of small gas turbine, the application demand of diaphragm coupling has been generated, which has been used in aviation. However, due to the failure to compensate the high misalignment at the initial stage, the application of diaphragm coupling in aviation and navigation has been seriously hindered, and it was once replaced by gear coupling. However, with the requirements of higher power, higher speed and the increase of operating temperature, many problems are exposed in gear coupling. At the same time, due to the increasing demand for low reaction torque, reaction force and low noise, the development and application of membrane disc coupling are greatly promoted. In the 1970s, Rexnord research and Development Laboratory of the United States carried out the experimental research on the axial vibration characteristics of the diaphragm coupling for the first time (Landon and Counter, 1976). So far, the diaphragm coupling has been gradually successfully applied to high-performance gas turbine. In 1978, Wildhaber (Wildhaber et al., 1978) of Bendix company proposed a hyperbolic (cone-like) single diaphragm coupling, as shown in Figure 7. Its structure is relatively simple and with a protective film. Because it is only a single diaphragm, its ability of compensating misalignment is limited. It is generally used in the shipbuilding industry rather than the aviation industry. In 1980, Calister (Calistrat, 1976) of Koppers company designed a single diaphragm coupling with equal thickness. Because of its linear diaphragm surface, its stress condition is not as good as the former.
From 1880s to the beginning of the 20th century, J.R Mancuso (Mancuso, 1986a; Mancuso, 1986b; Mancuso et al., 1989; Mancuso J., 1994; Mancuso J. R., 1994; Mancuso, 2000; Mancuso, 2003) published a series of articles and monographs, introduced the structure and performance of Bendix diaphragm coupling in detail, gave several design indexes of diaphragm coupling from the perspective of Engineering selection, and pointed out the design standards of four design theories (maximum principal stress theory, maximum shear stress theory, maximum distortion energy theory and fatigue failure theory), including Soderberg criteria and Goodman criteria Criteria, modified Goodman criteria and constant life fatigue diagram, described the common failure causes and manifestations of the membrane disk coupling, that is, the radial and circumferential rupture of the membrane disk caused by the design not meeting the misalignment requirements and torque requirements (Figure 8), as well as some precautions in the actual safe use.
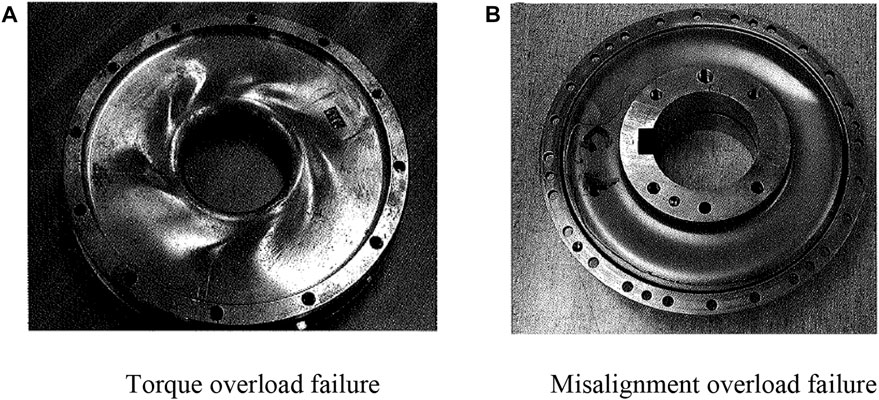
FIGURE 8. Failure styles of the diaphragm. (A) Torque overload failure (B) Misalignment overload failure.
Up to now, the membrane disc coupling has been widely used in developed countries, and its performance is excellent, and it is mostly used in important equipment related to national defense and security. For example, Bendix membrane disk couplings in the United States are widely used in flexible power transmission systems of more than 60 aircraft types, such as fighters (af-101, F-102, f-106, f-5a, f-5b, F-15, F-16, Saab, yf-17, g8a, etc.), bombers (B-1,B-52, cf-5a, XB-70, KC-135, etc.), vertical landing aircraft (fh-100, m-5, xc-142), and helicopter (BO-105, ch-3c, ho-5ch-6, oh-6a), Including power output shaft, main drive shaft, tail drive shaft, auxiliary power drive shaft and so on (Lin, 2005). In addition, it is also used in tanks, ships power plants (Kop-Flex Inc, 2003), such as lm2500, ft-4, Olympus engine, etc., as well as power transmission in other fields of the national economy. It is reported that there are more than 1700 specifications and more than 2,020,000 coupling products successfully applied in aviation alone. At present, the main manufacturers of membrane disc coupling are: Goodrich company (formerly Bendix company of the United States), Koppers company, NSO company of Japan, ZURN company of the United States, Cincinnati, etc. Literature (Zhao et al., 2002) points out that the maximum value of the composite diaphragm coupling of Cincinnati gear coupling company can reach 80,000 r/min, that of the laminated disc coupling of American coupling association can also reach 40,000 r/min, and that of the double diaphragm composite coupling of Capstone company can reach 96,000 r/min.
Membrane disc coupling started relatively late in China. The research of 703 Research Institute of China Shipbuilding Industry Group Co., Ltd. Imitating Bendix’s high-tech membrane disc coupling was successful for the first time in the 1980s (Zhao et al., 2002; The 703rd Research Institute of China Ship building Industry Corporation, 2008), and it was mainly used in fighter planes, ships and other important strategic equipment. At the same time, Bi Chengwu of 703 Institute published several papers on the design of diaphragm coupling (Chengwu, 1980; Chengwu and Wang, 1982; Chengwu and Lin, 1984; Chengwu et al., 1988), pointed out several loads and key points to be considered in the design of diaphragm coupling, and put forward ideas, principles and notes for the design of diaphragm coupling from an overall point of view. By the end of the 1980s, Hua Jiashou officially published his book (Hua, 1989), which described the structural features, excellent characteristics and design concerns of the diaphragm coupling in detail. Since the 1990s, the membrane disc coupling has gradually realized the transformation from military to civilian, and has been applied to power generation equipment (Mao et al., 2019), metallurgical equipment (Li et al., 2019), petrochemical equipment (Pan and Wang, 1994), etc. This change has greatly promoted the development of the design and application industry of membrane disc coupling. At the beginning of the 21st century, several influential companies producing and marketing membrane disc coupling have emerged in China, such as Wuxi Chuangming Transmission Engineering Co., Ltd. (formerly transmission engineering company of China Aviation Industry 614 Research Institute), Tianshuo coupling Co., Ltd., etc.
From 2010 to 2020, with the advancement of the modernization of national defense industry, the integration of military and civil affairs, and the development of military to civil affairs, the relevant national research institutes (703 and 704 research institutes of China Shipbuilding Industry Corporation, Sichuan Gas Turbine Research Institute of China Aviation Development Corporation, China aeronautical power Research Institute, etc.), colleges and universities (Xi’an Jiaotong University, Chinese Academy of Sciences Northeast University, etc.) and enterprises (Wuxi Chuangming Transmission Engineering Co., Ltd., Tianshuo coupling Co., Ltd., Harbin Guanghan Power Co., Ltd., Harbin Dong’an Engine Co., Ltd.) have further increased the research and development efforts to improve the performance of membrane disc coupling, and a large number of patents (Tao et al., 2011; Tao et al., 2012; He, 2015; Li et al., 2015; Song et al., 2016; Wang et al., 2018a; Chen et al., 2018; Qiu et al., 2020; Zhao et al., 2020) have emerged, which focus on membrane disc surface, overall structure, material, connection form, etc. The design of disc coupling has been improved, which not only promotes the performance of important equipment in China, but also further expands the commercial application scope of disc coupling. At present, China’s membrane disc coupling has reached the advanced level of foreign similar products, with the highest working speed of 30,000–60000 r/min, and has five series of 90 varieties applied in all walks of life. Comparatively speaking, there is still a certain gap in the overall performance of membrane disc coupling between China and foreign countries, and the specifications and varieties are relatively small, so the commercialization degree still needs to be further improved.
Research status of diaphragm coupling
In the course of development and application of membrane disc coupling in the world, scientists have done a lot of targeted research work, and achieved obvious results, but there are also shortcomings. Throughout its research status, it mainly focuses on the following two aspects: First, the design study of the force and deformation of the diaphragm disc; second, the analysis of the dynamic characteristics of the diaphragm coupling.
Design research based on analysis of force and deformation of membrane disk
As for the design and research of membrane disk, the following aspects are generally considered:
1) Research on the design of membrane disk surface;
2) The centrifugal force of the disc and its adjacent parts on the disc;
3) The stress, deformation, over torsion and torsional stiffness of the membrane disk under torsion are analyzed;
4) Under the action of bending stress and axial deformation of the membrane plate;
5) Misalignment, deflection, bending deformation, angular stiffness and additional bending moment of membrane disk;
As early as 1951, W.P.H Wolff (Wolff, 1951) proposed a general differential equation of disc deflection in cylindrical coordinate system by considering the deformation and balance of a tiny element on the disc. Under the assumption of small deformation of disc bending, given the surface equation of the disc, the deflection and rotation angle of the inner and outer diameter of the disc in the case of misalignment and alignment were taken as the boundary conditions, respectively, to derive the deflection and deflection of the disc The results show that with the increase of the surface coefficient n, the distribution of the torsional shear stress tends to be uniform, and when n = 2, the distribution of the torsional shear stress on the hyperbolic membrane plate is equal The relationship between the radial stress and bending stiffness of the disk under oblique bending and umbrella bending with respect to the ratio of inner diameter to outer diameter and the surface coefficient of the membrane is studied. Firstly, it is pointed out that when the ratio of inner diameter to outer diameter of the membrane is constant, with the increase of n value, the stress concentration at the inner diameter of the membrane tends to decrease, and the stress at the outer diameter of the membrane tends to increase, and the decrease of stress is slower than the increase of stress The deflection bending stiffness increases obviously. It can be seen that from the point of view of stress balance, under the condition of oblique bending, when the stress at the outer diameter and inner diameter of the membrane is equal, the value n of the profile can be taken, and the increase of the value n is conducive to improving the critical speed of the coupling system. Secondly, it is pointed out that when the surface coefficient n is fixed, the stresses at the inner and outer diameters of the membrane and the bending stiffness of the membrane disk increase with the increase of the ratio of the inner and outer diameters of the membrane, so it is better to have a smaller ratio of the inner and outer diameters of the membrane. In this paper, the deformation, stress and stiffness characteristics of a single diaphragm of bolted diaphragm coupling are calculated and analyzed in detail, and the requirements of surface shape, inner and outer diameter ratio in the design of diaphragm coupling are pointed out, which has important reference value for the establishment of the design theory of diaphragm coupling. However, it is only a theoretical calculation, lack of experimental verification; and in the design of membrane disk coupling, the performance of membrane disk is also affected by its connecting parts and working conditions, these factors are not considered in the paper.
In 1976, M.M. Calister (Calistrat, 1976) of Koppers company pointed out that the performance of diaphragm coupling largely depends on the fatigue limit of diaphragm, and the fatigue limit depends on the angular misalignment and axial deformation of diaphragm. The fatigue S-N curves of the membrane disk under various extreme conditions are tested comprehensively. The research shows that the membrane disk coupling is quite safe under rated conditions. Only when the angle misalignment is increased to at least three times of the rated value can the fatigue failure be induced. Under the condition of alternating stress, fatigue failure will occur no matter in the case of no axial displacement or large axial displacement. However, the cracks in the former are circumferential and almost no buckling, while the cracks in the latter are randomly and irregularly distributed with severe buckling. In addition, the failure curve of the membrane disk is drawn under the coordination of different axial deformation (stress) and different angular deformation (stress). According to the failure curve, the plane is divided into two parts (failure area and safety area). The closer the failure curve is, the worse the safety stability of the membrane disk is. Therefore, the failure curve is translated to the safety area, and the safety factor and its safety factor are formed The safety design area of the corresponding membrane disk. This method provides convenience for failure judgment and design based on fatigue failure.
In 1980, Bi Chengwu (Chengwu, 1980) made a more detailed analysis on the relationship between bending stress, torsional shear stress, angular stiffness, bending stiffness and disc size and surface coefficient of single disc of Bendix like membrane disc coupling in combination with the previous research results and the experimental research results of 703 Institute, which is clearer than w.p.h Wolff’s. It is recommended that the ratio of inner diameter to outer diameter of the membrane should be between 0.4 and 0.5 under the condition that the stiffness of the membrane disk (hopefully higher) and the strength of the connecting bolt of the membrane disk at the hub are considered to limit the size of the hub. However, in the given surface equation
In 1988, Wang Xinfeng (Wang, 1988) analyzed the axial bending stress, deflection bending stress, torsion stress and centrifugal stress of membrane disk, and gave the calculation method of safety factor of membrane disk coupling by comparing the working stress with Goodman curve, and solved the equivalent stiffness and critical speed of membrane disk coupling under axial vibration, transverse vibration and conical vibration. The objective optimization method to minimize the maximum stress or weight of the membrane disk coupling under a given load is analyzed by an example, which has important reference significance for the design of membrane disk.
In 1993, Guo Xiaoming (Guo et al., 1993) used the finite element method to analyze the stress and flexibility of the membrane disk under the action of axisymmetric bending, non-axisymmetric bending and torque, and verified it through the experimental test. It shows that the distribution of the membrane disk surface thickness is the main factor affecting the membrane disk flexibility and the stress concentration inside and outside the surface, and the bending stress level of the surface is the main reference basis for the membrane disk design. Based on this, by comparing with four types of membrane disc coupling of Eagle company in Japan, a kind of folded line membrane disc surface with equivalent stress level is designed.
In 2004, Xuan qi (Xue and Guo, 2008) analyzed and compared the stress characteristics of several diaphragm couplings and the stress calculation formulas given in relevant literature, and gave some modified formulas. Through checking and calculating the diaphragm of an imported device, it was verified that the calculation results of the modified formula were closer to the reality. The formula correction proposed in this paper is based on practice, and only one kind of membrane disc coupling is calculated and checked, so the application area is narrow.
In 2008, AI Pinggui (Ai and Zhu, 2008) used APDL language to model the membrane disk, and solved the stress analysis and modal analysis under centrifugal force, torsion and axial force of coupling separately. However, the model established in this paper is a fully symmetric conical disk structure, which is not suitable for asymmetric multi disk analysis even through parameter adjustment, and cannot be used for wavy disk analysis. In addition, the actual operation of the coupling is multi force comprehensive action, which has little practical significance for the analysis of single force or torque action. In the same year, Zhu Keke (Zhu and Zhu, 2008a; Zhu and Zhu, 2008b) gave the analytical solution of shear strain by using the principle of energy variation under the assumption that the radius of the middle plane remains unchanged before and after deformation.
In 2013, Yue Peng (Yue et al., 2013) took linear, pyramid and hyperbolic 3 typical membrane surfaces as an example. Through finite element analysis, the stress distribution of each type of mask tray under the single condition of axial displacement, angular deviation and torsion was compared with the three composite working conditions, and the stress distribution of each type of mask disc was summarized. The applicable conditions of the contract. This paper provides a theoretical basis for the design and application of membrane disk coupling according to different working conditions, and provides a new idea for further improving the performance index of membrane disk.
Similarly, in 2016, Li Bo (Bo et al., 2016) took the n-type double diaphragm (hyperbolic surface) diaphragm coupling as the research object, and analyzed its stress under centrifugal load, torque load and misalignment load by using ANSYS software, which provided a certain reference for the structural modification of coupling diaphragm.
In 2017, Cao Angang (Cao et al., 2017a) took the commonly used cone-shaped membrane disk as an example, and used ANSYS software to analyze the stress and safety factor distribution of membrane disk under the combined action of multiple loads. According to the analysis results, the original conical profile is improved and designed as a thin profile in the middle and thick at both ends (Figure 9), and multi parameter optimization is carried out by using the optimization module of ANSYS. After optimization, the stress on the surface of the membrane disc is reduced and the minimum safety factor is increased. In the same year, based on the stress-strain distribution of membrane disk under the action of isotropic load, the axial stiffness, angular stiffness and torsional stiffness were calculated (Cao et al., 2017b). In (Cao et al., 2019) of 2019, ANSYS was used to analyze the influence of profile parameters (profile thickness, profile amplitude and profile period) on the safety factor of the coupling. It was found that under the selected unit conditions, the profile thickness of the corrugated membrane disk was 0.4 mm, the profile amplitude was 5 mm, and the profile period was a sine curve period. The safety factor is determined by comparing the combined stress of dynamic and static stress with the modified Goodman curve, which provides a stress analysis method for membrane disk design of membrane disk coupling.
All of the above are based on the analysis of the stress and deformation of the diaphragm, according to the influence of the stress, strain and stiffness of the diaphragm on the coupling, the design suggestions of the diaphragm coupling or the improvement of the structure of the diaphragm are put forward, and most of them are based on the software simulation research, which cannot consider the internal role between the components of the diaphragm coupling and the external multi physical environment as a whole Moreover, the research contents are static or quasi-static, which is far from enough for the design of diaphragm coupling under the actual high temperature and high speed operation conditions.
Analysis of dynamic characteristics of diaphragm coupling
With the increasing use of metal diaphragm couplings, people have realized the necessity of overall research and the importance of its dynamic characteristics. At present, the research on the dynamics of membrane disk coupling is mainly reflected in the following aspects:
1) Research on the dynamic parameters of the diaphragm coupling, including the stiffness and damping of the coupling.
2) Under the condition of misalignment in all directions (Figure 10), the dynamic characteristics of the membrane disk coupling are analyzed, including the critical speed and response analysis of transverse vibration, axial vibration and torsional vibration.
3) Test and Research on dynamic fatigue characteristics of coupling.
4) The influence of diaphragm coupling on the dynamic characteristics of bearing rotor system is studied.
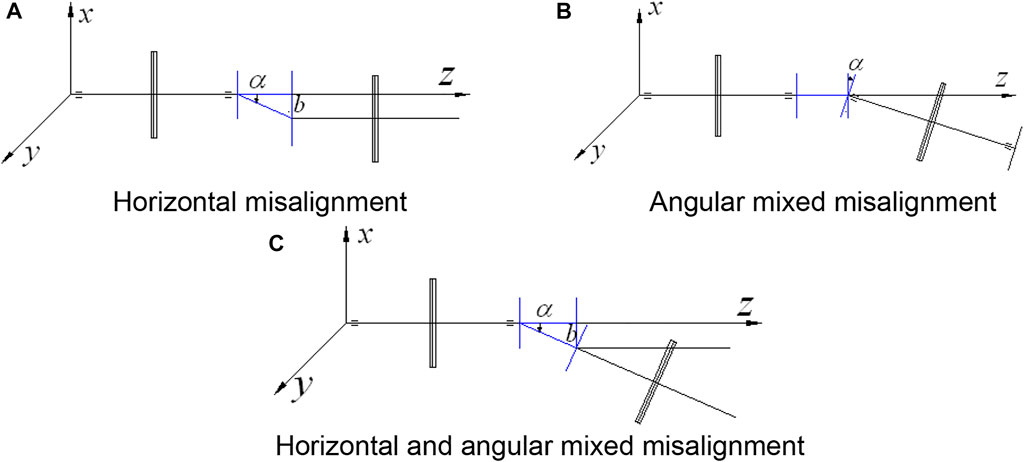
FIGURE 10. Various misalignment states of diaphragm coupling. (A) Horizontal misalignment (B) Angular mixed misalignment (C) Horizontal and angular mixed misalignment.
In 1976, F.K. Landon (Landon and Counter, 1976) of the United States first studied the axial vibration characteristics of Bendix type metal diaphragm coupling in theory, taking into account the relative sliding damping of diaphragm which is only available in multi diaphragm group. M. M. Calister (Calistrat, 1976) carried out a full range of fatigue tests on Bendix diaphragm coupling under various extreme conditions (angular misalignment, axial misalignment, high torque, etc.), determined its operation limit and reference pictures that can be used to identify the failure forms of diaphragm coupling, and fully realized the high reliability of diaphragm coupling far exceeding rated parameters. C. B. Gibbons (Gibbons, 1976) analyzed the force and torque of Bendix diaphragm coupling acting on the connecting shaft under the condition of horizontal misalignment, and gave the calculation examples of reaction force and torque of several diaphragm couplings with different diaphragm shapes. In the early 1980s in China, Bi Chengwu (Chengwu, 1980) first proposed that the overall strength of the diaphragm coupling should be calculated, and briefly analyzed the connection parts, the selection of the diaphragm material and the force of the coupling on the support. Taking the bolted double diaphragm coupling as an example, the general design steps, the overall design ideas and the factors to be considered are introduced in detail and systematically. The simplified physical model of the coupling and the critical speed estimation formula of transverse vibration and axial vibration under the model are given, and the finite element method is pointed out the method of accurate calculation. In 1982 (Chengwu and Wang, 1982) and 1988 (Chengwu et al., 1988), Mr. Bi made further finite element analysis and Experimental Research on the overall structural strength of the double diaphragm coupling. Through the comparative analysis of the overall stress of the diaphragm coupling under six different connection flange forms, he pointed out the relationship between the connection flange structure of the coupling and the performance of the diaphragm coupling, and proposed that the stiffness should be selected in the design At the same time, according to the practical application of the coupling, it is suggested that the intermediate shaft should be designed as a hollow shaft with long hollow length, and the stiffness requirements should be taken into account. In 1984, Mr. Bi introduced his platform (Chengwu and Lin, 1984) to carry out the experimental research on the membrane disc coupling, and carried out experimental research on the static performance and dynamic performance of the membrane disc coupling. The static test includes the torsion bearing capacity test, umbrella deformation test and deflection bending test of the single membrane disc; the dynamic test includes the performance test of the coupling system under the condition of axis alignment and misalignment; the two focus on their respective characteristics The published theoretical calculation of membrane disk coupling design has been verified well, which provides support for the popularization and application of its design theory. However, it is limited to the strength analysis based on membrane disk stress under static and dynamic conditions, and the research on the influence of coupling design on the system performance of its connected shafting is less.
In 1995, A.S. Sekhar (Sekhar and Prabhu, 1995) proposed to use high-order finite element method to solve the mass unbalance response of rotating shaft under the condition of horizontal and angular misalignment of Bendix diaphragm coupling. The result shows that the synchronous response amplitude is less affected by misalignment, while the frequency doubling amplitude is heavily dependent on misalignment.
In 2000, H. Birkholz (Birkholz et al., 2000) carried out a lot of numerical calculation and Experimental Research on the stress response and deformation response of n-type double diaphragm coupling under the action of torque, bending moment and axial force. The research shows that the torsional stiffness is constant, while the bending stiffness is nonlinear. It has good torque transmission characteristics. The test results also confirm its excellent torsional stiffness.
In 2009, S. Ganesan (Ganesan and Pandmanabhan, 2009) estimated the influence of rotational speed on the rotor system with a diaphragm coupling. The paper used Abaqus software to calculate the diaphragm stiffness in different rotational speed and lumped as a stiffness matrix for the rotor model. The results indicated that the bending critical speeds of the rotor system vary depending on angular velocity due to centrifugal stiffening and gyroscopic couple. However, the influence of the diaphragm coupling on rotor system is not studied in this paper.
In 2010, under the assumption of plane stress, Chen Wenpin (Chen and Ma, 2010) and others studied the axial stiffness of membrane disk coupling under axial symmetrical load by using tensor analysis and energy variational method, and analyzed the influence of membrane disk thickness, profile shape, radius ratio and transmission torque on the axial stiffness. Through the comparison with the simulation results, the correctness of the assumptions and conclusions was verified, which is a reference for membrane disk coupling It provides a reference method for the calculation of dynamic parameters of disc coupling.
In 2011, Wang (Wang et al., 2011) took the interference type membrane disc coupling as the research object. Under certain mechanical assumptions, the calculation method of axial misalignment compensation was given theoretically, and the calculation example was solved. Then, according to the characteristics of the tight fit diaphragm coupling, the coupling is simplified as a mass spring model in the axial direction, and its axial dynamic equation is established. Through the combination of analytical calculation and ANSYS simulation, the axial modal and dynamic response are solved (Guo et al., 2013), and the results are in good agreement.
In 2012, Yang Shang (Shang, 2012) took the Huake coupling as the research object, established its discrete equivalent system model, and combined with the transfer matrix method, established the bending torsion shaft vibration model and mathematical expression of the coupling under the condition of rigid support, and solved it. Then, the three-dimensional finite element models of flexible diaphragm coupling with different thickness of diaphragm are established in ANSYS and ABAQUS respectively, and the vibration characteristics of flexible diaphragm coupling under four different working conditions are analyzed respectively. The static stress analysis, steady-state dynamic stress analysis, transient dynamic stress analysis and harmonic response analysis of the 0.85 thickness model are carried out to obtain the mechanical characteristics of the coupling under rated conditions. By comparing the natural frequencies and mode shapes of the coupling obtained by the transfer matrix method and the finite element method, the rationality of the bending torsion shaft vibration model of the coupling is verified, which provides a theoretical reference for the research and analysis of the complex vibration forms of the flexible diaphragm coupling and the improvement and optimization of the product in the next step. Wang Wei (Wang et al., 2012) et al. Established a simplified calculation model for the rotor structure of an aircraft accessory transmission system with diaphragm coupling in a research institute, calculated and analyzed its critical speed through the transfer matrix method and the finite element method, discussed the influence of different modeling methods and different simplified forms on the critical speed, and made more accurate analysis and Analysis on the diaphragm coupling using the finite element software The research can be used for reference.
In 2015, Li Bobo (Li, 2015; Li et al., 2017) used the commercial software ABAQUS to carry out the modal analysis and dynamic stress solution of the membrane disk coupling under the rated condition, limit condition, axial overload, transverse overload and other conditions, and obtained the vibration displacement, stress, velocity and acceleration characteristics of the nodes in the important area of the membrane disk with time. In addition, under the condition of ensuring the static strength, the author optimizes the topology of the intermediate shaft of the diaphragm coupling, and realizes the lightweight design of the diaphragm coupling.
In 2017, Liu Guoping (Liu and Fang, 2017) and others analyzed the axial tensile stiffness, axial compression stiffness and axial natural frequency of a metal diaphragm coupling by finite element method. The axial vibration test was carried out under the operation condition. The results show that the axial tension stiffness and compression stiffness of the metal diaphragm coupling show obvious nonlinear characteristics, and there is axial vibration natural frequency in the working speed range.
In 2018, Wang Chuanqi (Wang and Yang, 2018) analyzed the characteristics of the dynamic balance characteristics of the diaphragm coupling and the causes of its deflection characteristics, gave the dynamic balance method of the diaphragm coupling, found the key points of the dynamic balance of the diaphragm coupling through the dynamic balance test, and solved the dynamic balance of the diaphragm coupling by optimizing the tooling, changing the dynamic balance speed and changing the allowable dynamic imbalance value It provides a balance scheme for the dynamic balance of components with flexure characteristics at high speed. In the same year, Wang Guoping (Wang et al., 2018b) studied the fitting pressure distribution of the coupling element of small-size closed interference type diaphragm disc coupling, constructed the deformation higher-order differential equation of the coupling element by using the plate shell theory, and gave the numerical solution of the fitting pressure according to the general form of the general solution, the second kind of Volterra integral and the segmented trapezoidal method, which was in good agreement with the calculation results of the finite element software The consistency of the system. In 2019 (Wang et al., 2020), on the basis of the previous paper, the author constructed the analytical calculation formula of the pressure distribution of the thin-walled closed interference fit, solved the undetermined coefficients, and gave the solution method of the bending moment and shear force at the joint of the coupling element and the diaphragm disc, which realized the analytical expression of the large nonlinear interference fit pressure, and provided a theoretical basis for the design of the interference joint diaphragm disc coupling.
In 2019, Zhen man (Man, 2019; Man et al., 2019) the numerical simulation of coupled rotor system of gas turbine generator set is carried out by MATLAB, and the motion differential equation is solved by Newmark-β method. Considering the stiffness nonlinearity of diaphragm coupling caused by large deformation, the effects of critical speed, modal shape, unbalance response and coupling stiffness on the dynamic characteristics of coupled rotor system are analyzed. The results show that the critical speed and unbalanced vibration response of the coupled rotor system are higher than that of the single rotor system. The increase of the coupling stiffness will increase the critical speed of the coupled rotor system, and the unbalanced vibration response will also increase. Moreover, the difference between the nonlinear stiffness model and the linear stiffness model is 16.77%. Li Xuezhi (Li et al., 2019) studied the structure and dynamic performance of the redundant diaphragm coupling, aiming at the problem of fatigue failure and fracture failure caused by the sudden change of load in the working process of the high-speed diaphragm coupling. The overall structure of the redundant diaphragm coupling is designed, the finite element analysis model of the diaphragm is established, and the optimal thickness of the diaphragm meeting the design requirements is calculated. The dynamic performance of the coupling is studied and the amplitude frequency response curve under the unit harmonic excitation is obtained. This research can provide a reference for the further improvement of the performance of the diaphragm coupling and the redundant design.
According to the above literature on the dynamics of diaphragm coupling, the current research mainly focuses on the static and axial dynamic characteristics of bolted diaphragm coupling. The research on the torsional vibration, lateral vibration and misalignment of the rotor vibration system of diaphragm coupling is obviously insufficient, and the multi physical field coupling problem under working conditions is almost not involved. As for the interference coupling, the number of research literature is less. However, there are articles in the direction of evolutionary optimization (Ma et al., 2021a; Ma et al., 2021b) research showing that some methods can interfere with the coupling relationship. Perhaps this will help to advance the next research.
Conclusion
In summary, although the diaphragm coupling has a commercial scale, it is obvious that the theoretical research lags behind seriously, and the literatures on the theoretical research mainly focus on the design, analysis and optimization of diaphragm profile, the research on the combination form between the membrane discs and the overall structure form of the membrane disc coupling, and the research on the axial dynamic characteristics of the membrane disc coupling. The research on the overall dynamic performance parameters of the membrane disk coupling, the dynamic characteristics of the coupling bearing rotor system and the multi field coupling effect is insufficient. In the current research literature, there are various forms of diaphragm coupling, however, there is no unified design standard or criterion, which is not conducive to the development of the industry.
Therefore, we should continue to carry out in-depth and systematic research on the design theory of diaphragm coupling, mainly including:
1) Influence of connection form of membrane disk coupling on static and dynamic performance of membrane disk coupling.
2) Study on the stiffness and damping characteristics of diaphragm coupling and shaft.
3) Study on dynamic parameters of diaphragm coupling.
4) Study on the whole dynamic model of diaphragm coupling.
5) Study on dynamics of membrane disk coupling bearing rotor system (including alignment and misalignment).
6) Research on the compensation ability of membrane disk coupling misalignment in all directions.
7) Research on the influence of coupling structure parameters on static and dynamic performance of coupling.
8) Research on the influence of multi physical fields on the diaphragm coupling and coupling bearing rotor system.
In order to obtain the design criteria of diaphragm coupling and promote the design and application of diaphragm coupling.
Author contributions
GW, JL, and SC contributed to conception and design of the study. GW organized the database. GW wrote the first draft of the manuscript. FY, QJ and HH wrote sections of the manuscript. All authors contributed to manuscript revision, read, and approved the submitted version.
Funding
This research was supported by National Major Scientific Research Instrument Development Project (Grant No. 22127803), Special program for scientific research of Shaanxi Provincial Department of Education (Grant No. 17JK1022), Key Project of Scientific Research Plan of Xi’an Jiaotong University City College (Grant No. 2021Z03).
Conflict of interest
The authors declare that the research was conducted in the absence of any commercial or financial relationships that could be construed as a potential conflict of interest.
Publisher’s note
All claims expressed in this article are solely those of the authors and do not necessarily represent those of their affiliated organizations, or those of the publisher, the editors and the reviewers. Any product that may be evaluated in this article, or claim that may be made by its manufacturer, is not guaranteed or endorsed by the publisher.
References
Ai, P. G., and Zhu, R. P. (2008). Stress and modal analysis of diaphragm coupling based on ANSYS. Mech. Eng. 1, 124–125. (in Chinese).
Birkholz, H., Dietz, P., Dehner, E., and Garzke, M. (2000). “Diaphragm couplings for turbo machines,” in International Design Conference - Design 2000 Dubrovnik, Croatia, Dubrovnik, May 23–26, 2000.
Bo, L., Lu, B., and Liu, C. (2016). Surface design and finite element analysis of n-type membrane disc coupling. Mech. Electr. Eng. 33 (8), 955–959.
Calistrat, M. M. (1976). Metal diaphragm coupling performance, in Proceeding of the fifth turbomachinery symposium, Gas turbine laboratories. Texas A & M University, College Station, Texas, 1976, 117–123.
Cao, A., Chang, S., Ding, C., and Li, S. (2017). Optimization of membrane disk surface structure and size. Mech. Transm. 41 (7), 83–87. doi:10.16578/j.issn.1004.2539.2017.07.018
Cao, A., Changshan, S., Ding, C., and Liu, X. (2017). Stress and stiffness analysis of diaphragm disc coupling. Ship Sci. Technol. 39 (10), 155–158. doi:10.3404/j.issn.1672-7649.2017.10.031
Cao, A., Ding, J., and Xu, W. (2019). Study on the optimization of the profile of corrugated membrane tray. Therm. power Eng. 34 (1), 120–124. doi:10.16146/j.cnki.rndlgc.2019.01.020
Chen, w., and Ma, Y. (2010). Analysis of axial stiffness performance of diaphragm coupling. Mar. Eng. 32 (1), 33–36. doi:10.13788/j.cnki.cbgc.2010.01.010
Chen, H., Li, X., Zhang, L., Xia, J., Pan, D., and Li, G. (2018). A membrane disc coupling with overload protection. Sichuan: CN108240399A.
Chengwu, B., and Lin, W. (1984). Experimental study on diaphragm coupling. Ship Sci. Technol. 5, 55–63. (in Chinese).
Chengwu, B., and Wang, H. (1982). Finite element analysis of integral strength of diaphragm coupling. Ship Sci. Technol. 1, 10–22. (in Chinese).
Chengwu, B., Lin, W., and Jin, J. (1988). Design of diaphragm coupling from an overall point of view. Therm. power Eng. 3 (4), 43–49. (in Chinese).
Editorial board of China Aviation Materials Manual (2002). China aviation materials manual. Beijing: China Standards Press. (In Chinese).
Ganesan, S., and Pandmanabhan, C. (2009). “Influence of centrifugal stiffening on a rotor system with a flexible diaphragm coupling,” in The fifth international conference on vibration engineering and technology of machinery, Wuhan, P. R. China, August 26–28, 2009.
Gibbons, Cb (1976). “Coupling misalignment forces,” in Proceedings of the fifth turbomachinery symposium, Gas turbine laboratories, Texas A & M University, College Station, Texas, 1976, 111–116.
Guo, X., Wang, S., and Gong, J. (1993). Research on mechanical properties and optimal design of membrane disk coupling. J. Southeast Univ. 6, 138–142.
Guo, W., Chen, H., Qi, S., and Yu, L. (2013). Axial vibration characteristics of a metal diaphragm coupling. Appl. Mech. Mater. 239-240, 443–451. doi:10.4028/www.scientific.net/amm.239-240.443
Hua, J. S. (1989). New type coupling and clutch. Shanghai: Shanghai Science and Technology Press. (in Chinese).
Kop-Flex Inc (2003). Flexible diaphragm coupling: MS marine style. Eden Prairie, MN, United States: Emerson Industrial Automation.
Landon, F. K., and Counter, L. F. (1976). “Axial vibration characteristics of metal-flexing couplings,” in Proceedings of the Fifth Turbomachinery Symposium, Gas Turbine Laboratories, Texas A&M University, College Station, Texas, 1976, 125–131.
Li, S., Cao, A., Zong, H., Liu, X., Xing, L., Song, D., et al. (2019). Structural analysis and dynamic performance research of redundant diaphragm coupling. Mech. Transm. 43 (3), 123–125. doi:10.16578/j.issn.1004.2539.2019.03.023
Li, G., Zhuang, T., Dai, H., Fan, H., Chen, T., Wang, Y., et al. (2015). A membrane disc coupling. Heilongjiang: cn104405784A.
Li, B., Yuan, H., Wang, G., and Ren, J. (2017). “Study on dynamic characteristics of integrated structure of new flexible diaphragm coupling,” in Proceedings of the 12th National Conference on vibration theory and application, NanNing, China, October 20, 2017.
Li, S., Cao, A., Zong, H., et al. (2019). A membrane disc coupling for connecting BPRT variable speed clutch. Heilongjiang Province: CN110005724A. (in Chinese).
Li, B. (2015). Simulation study on dynamic characteristics and structural optimization of flexible diaphragm coupling. China: Northeastern University.
Lin, J. S. (2005). The mechanical system design of aero-gas turbine engine. Beijing: Aviation Industry Press. (in Chinese).
Liu, G., and Fang, J. (2017). Study on axial vibration characteristics of metal diaphragm coupling. Aeroengine 43 (3), 14–18. doi:10.13477/j.cnki.aeroengine.2017.03.004
Ma, L., Wang, X., Wang, X., Wang, L., Shi, L., and Huang, M. (2021). TCDA: Truthful combinatorial double auctions for mobile edge computing in industrial internet of things. IEEE Trans. Mob. Comput., 1. doi:10.1109/TMC.2021.3064314
Ma, L., Li, N., Guo, Y., Huang, M., Yang, S., Wang, X., et al. (2021). Learning to optimize: Reference vector reinforcement learning adaption to constrained many-objective optimization of industrial copper burdening system. IEEE Trans. Cybern., 1–14. doi:10.1109/TCYB.2021.3086501
Man, Z., Sun, T., Tian, Y., Zhang, H., and Tan, C. (2019). Dynamic analysis of rotor system of diaphragm coupling gas turbine generator. Gas. turbine Technol. 32 (2), 44–51. doi:10.16120/j.cnki.issn1009-2889.2019.02.008
Man, Z. (2019). Analysis of misalignment dynamic characteristics of a two span rotor system with membrane disk coupling. China: University of Chinese Academy of Sciences.
Mancuso, J. R., Gibbons, C. B., and Munyon, R. E. (1989). “The application of flexible couplings for turbomachinery,” in Proceedings of the 18th Turbomachinery Symposium, Texas A&M University, United States, 1989, 141–164.
Mancuso, J. R., Gibbons, Cb, and Munyon, Re (1990). “The application of flexible couplings for turbomachinery,” in Proceeding of the eighteenth turbomachinery symposium, Gas Turbine Laboratories, Texas A&M University, College Station, Texas, September 1989, 141–164.
Mancuso, J. R. (1896). Couplings and joints, design, selection, and applications. New York: Marcel Dekker.
Mancuso, J. R. (1986). Disc vs diaphragm couplings. Machine design. Braintree, MA, United States: Altra Industrial Motion.
Mancuso, J. R. (1986). Couplings and joints, design, selection, and applications. New York: Marcel Dekker.
Mancuso, J. (1994). “General purpose vs special purpose couplings [C],” in Proceedings of the twenty-third turbomachinery symposium. Texas A&M university. Turbomachinery laboratories, Texas A&M University, United States, September 1994, 167–177.
Mancuso, J. R. (2000). Just how flexible is your flexible coupling in reality? World Pumps 2000, 46. doi:10.1016/S0262-1762(00)80208-4
Mancuso, J. R.(2003). What are the differences in high performance flexible couplings for turbomachinery? Proceeding of the thirty-second turbomachinery symposium, Texas A&M University, the United States, September 1989: 189–207.
Mao, Y., Yao, P., and Hou, W. (2019). Shafting alignment method of aero modified gas turbine generator set. Shanghai: CN110587285A. (in Chinese).
Piotrowski, J. (2007). Shaft alignment handbook. Third edition. New York: Taylor & Francis Group, LLC: CRC Press, 137–178.
Qiu, Z., Qiqi, H., Han, Z., and Zhang, F. (2020). A kind of perforated diaphragm coupling and its design method. Liaoning Province: CN110953257A.
Sekhar, A. S., and Prabhu, B. S. (1995). Effects of coupling misalignment on vibrations of rotating machinery. J. Sound Vib. 185 (4), 655–671. doi:10.1006/jsvi.1995.0407
Shang, Y. (2012). Study on dynamic characteristics of flexible diaphragm coupling. China: Northeast University.
Song, S., Xin, L., Liu, S., Fang, H., and Nie, J. (2016). Assembly and disassembly tooling of membrane disc coupling. Hunan: CN105345427A.
Stewart, M. J., Roberts, K. G., Bosley, R., and Weissert, D. (1999). Double diaphragm compound shaft. US, 5964663.
Stewart, M. J., Roberts, K. G., Bosley, R., and Weissert, D. (2000). Double diaphragm compound shaft. US, 6037687.
Tao, y., Qiu, B., Yan, d., et al. (2011). A combined structure of stainless steel diaphragm coupling. Jiangsu: CN201714861U.
Tao, y., Qiu, B., and Shen, b. (2012). Membrane disk coupling with low additional bending moment. Jiangsu: CN202251509U.
The 703rd Research Institute of China Ship building Industry Corporation (2008). Transmission research office of the 703rd research institute of China ship building industry corporation. Therm. power Eng. 23 (4). (in Chinese). Available at: http://qikan.cqvip.com/Qikan/Article/Detail?id=28278941.
Wang, C., and Yang, H. (2018). Research on dynamic balance of diaphragm coupling. Mech. Eng. 329 (11), 118–121.
Wang, G., Chen, H., Qi, S., Wu, J., and Yu, L. (2011). “Study on compensatory magnitude of axial misalignment for flexible couplings assembled by interference fit,” in Proceedings of ASME Turbo Expo 2011: Microturbines & Small Turbomachinery, Vancouver, Canada, June 6–10, 2011.
Wang, W., Wang, X., and Luo, G. (2012). Calculation of critical speed of rotor with diaphragm coupling. Vib. shock 31, 151–154.
Wang, G., Cheng, S., and Huaning, H. (2018). Research on fit pressure of small size closed interference fit. Mech. strength 40 (5), 163–166. doi:10.16579/j.issn.1001.9669.2018.05.023
Wang, G., Cheng, S., Liu, J., Men, J., and Zhang, C. (2020). Research on analytic expression construction of fit pressure of small size closed interference type diaphragm coupling. Mech. Des. 37 (11), 21–26. doi:10.13841/j.cnki.jxsj.2020.11.003
Wang, X. (1988). Design and optimization of flexible diaphragm coupling. Therm. power Eng. 5, 37–43.
Wolff, W. P. H. (1951). The design of flexible disk misalignment couplings. Proc. Institution Mech. Eng. 12, 165–175. doi:10.1243/pime_proc_1951_165_018_02
Xue, Q., and Guo, H. (2008). The relationship between the force analysis and the torque stress of the flexible diaphragm coupling. Mech. Des. Manuf. 4, 85–87. (in Chinese).
Yue, P., Zhao, Y., and Liu, X. (2013). Analysis of the characteristics of different mask dishes. Nav. Sci. Technol. 35 (12), 83–87. doi:10.3404/j.issn.1672-7649.2013.12.018
Zhao, Y. B., Xue, Z. H., and Wang, S. P. (2002). Flexible coupling characteristics analysis. Therm. power Eng. 17 (99), 308–309. (in Chinese).
Zhao, H., Hu, X., and Zuo, S. (2020). A super high speed diaphragm coupling. Jilin Province: CN111322319A.
Zhu, K., and Zhu, R. (2008). An analytic solution to asymmetrical bending problem of diaphragm coupling. Appl. Math. Mech. 29 (12), 1643–1649. doi:10.1007/s10483-008-1212-y
Keywords: mechanical design, energy equipment, mechanical characteristics, gas turbine, diaphragm coupling
Citation: Wang G, Liu J, Cheng S, Yan F, Jia Q and Han H (2022) The diaphragm coupling in energy equipment: A review. Front. Energy Res. 10:1001315. doi: 10.3389/fenrg.2022.1001315
Received: 23 July 2022; Accepted: 05 August 2022;
Published: 12 September 2022.
Edited by:
Lianbo Ma, Northeastern University, ChinaReviewed by:
Hongjiang Wang, Shenyang Institute of Engineering, ChinaTian Zhang, Northeastern University, China
Copyright © 2022 Wang, Liu, Cheng, Yan, Jia and Han. This is an open-access article distributed under the terms of the Creative Commons Attribution License (CC BY). The use, distribution or reproduction in other forums is permitted, provided the original author(s) and the copyright owner(s) are credited and that the original publication in this journal is cited, in accordance with accepted academic practice. No use, distribution or reproduction is permitted which does not comply with these terms.
*Correspondence: Guoping Wang, d2FuZ2dwQHhqdHVjYy5lZHUuY24=