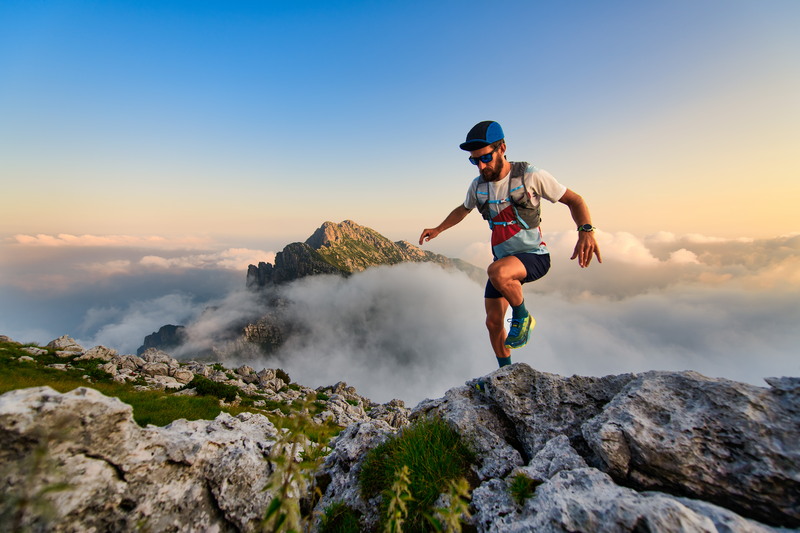
95% of researchers rate our articles as excellent or good
Learn more about the work of our research integrity team to safeguard the quality of each article we publish.
Find out more
ORIGINAL RESEARCH article
Front. Energy Res. , 11 October 2022
Sec. Process and Energy Systems Engineering
Volume 10 - 2022 | https://doi.org/10.3389/fenrg.2022.1000796
This article is part of the Research Topic Modern World Heat Transfer Problems: Role of Nanofluids and Fractional Order Approaches View all 18 articles
Background: The main aim of this article heat transfer in thermal engineering deals with the production, use, transformation, and transfer of thermal energy. Engineering and industrial fields including food packaging, the production of food additives, electronic cooling, microturbines, etc. Heavily rely on heat transmission. Due to its intriguing potential in industries like the production of polymers, paper, crystal glass, etc., scientists from all over the world have endeavored to investigate the effect of heat transmission on fluid flows past an expandable surface.
Purpose: The use of a single-phase technique to assess Newtonian nanofluid flow along stretched surfaces with heat transfer convective models is emphasized in this research. A mathematical formulation is used to do the numerical computations for copper oxide (CuO), aluminum oxide (Al2O3), and titanium dioxide (TiO2) nanoparticles using water (H2O) as the base fluid.
Formulation: The fifth-order Runge-Kutta shooting method procedure with shelling performance are used to solve non-linear ordinary differential equations with boundary conditions numerically. Researched and analyzed for changes in several parameters, plots illustrating the effects of motivated and non-motivated MHD are given to explain the physical values.
Finding: Dispersion of solid items in the working fluid is reported to significantly improve thermal performance. The Biot number determines how convective the border is. With an increase in the Biot number, the fluid’s temperature drops significantly. It has been demonstrated that Copper oxide (CuO), nanoparticles are more efficient than Titanium Dioxide (TiO2) and Aluminum Oxide for thermal enhancement (Al2O3).
Novelty: As far as the authors are aware, no studies have been done on the steady MHD flow and convective heat transfer of nanofluids over a nonuniform stretched surface under the influence of a heat source and viscous dissipation.
Many scientists who study the design of thermal systems are continuously thinking of new ways to build thermal systems that are more effective. The recent technique dispersion of metallic nano-structures in base fluid is the most popular and several aspects of this technique have been discussed so far. Using both theory and experiment, it has been demonstrated that a base fluid’s thermal properties can be improved by the addition of nanostructures, improving the base fluid’s efficiency as a working fluid. Nanofluids are just such fluids. The development of nanofluids has inspired researchers, and as a result, several papers have been published up to this point. As an illustration, Sheikholeslami et al. (2019a) and Sheikholeslami et al. (2019b). The effects of alumina nanoparticle dispersion on momentum and heat energy transfer, as well as an increase in wall heat flux caused by increased thermal conductivity in a magnetohydrodynamic fluid, were all the subjects of investigations. Li et al. (2019) investigated a rising behavior of thermal energy transfer in the fluid which conducts electricity when subjected to a magnetic field and computed the governing issues using the Lattice Boltz Mann method to better comprehend the underlying physics (LBM). The effect of metallic nano-structure addition on the working fluid’s capacity for thermal conduction was theoretically examined by Sadiq et al. (2019). Saleem et al. (2019a) mathematical models for improving mixed convective heat and mass transmission were based on Water’s B rheology. They researched a range of topics using numerical simulations. The working fluid’s thermal performance significantly improved as a result of Ramzan et al. (2019) examination of the transport process in a 3D flow of MHD fluid including nanoparticles. Saleem et al. (2019b) discussed the best analytical technique in regard to the thermal performance of nanomaterials. The influence of heat dissipation on the temperature profile in nanoparticle was also examined, and it was discovered that the presence of metallic nanostructures improved the performance of the working fluid. Dogonchi et al. (2019a) looked at natural convection in addition to the impact of nano-solid formations on the working fluid’s thermal effectiveness of an elliptic heater in a cavity. The effects of heat radiation and porous media on momentum and energy transmission in fluids containing solid nanoparticles were examined by Dogonchi et al. (2019b). Hosseinzadeh et al. (2019) investigated instantaneous effects of nonlinear thermal radiation and porous media on thermal characteristics of fluid subjected to dispersion of nano-structures in the presence of mass transport under the influence of chemical reaction. Gholinia et al. (2019) during mass transportation MHD, created mathematical models for homogeneous-heterogeneous chemical interactions over a revolving disk, Erying-Powell fluid is poured. Chamkha et al. (2019) formulated a mathematical model to investigate the hybridity of metallic nano-particles on the heat transfer properties of the working fluid when provided an external magnetic field. Afridi et al. (2018) used mathematical models to examine how the hybridity of nanoparticles affects the efficiency of fluid thermal conductivity over moving surfaces when there is significant heat dissipation. To investigate an improvement in fluid thermal performance, they solved the developed challenges. Zangooee et al. (2019) performance hydrothermal analysis for magnetohydrodynamic flow over rotating disk subjected to thermal radiations and external magnetic field.
Electrically conducting fluid performs entirely different from electrically nano-conducting fluid, when provided magnetic field, because of the Lorentz effect, which changes the flow and distribution of heat energy. Such magnetic-field-exposed fluid flows are known as MHD flows, and they have been extensively studied. For instance, Ghadikolaei et al. (2018a) and Ghadikolaei et al. (2018b) examined at how the magnetic field affected how heat and velocity were transferred in a convective fluid including nanostructures. Hatami et al. (2014) lnumerical.’s simulation of two-phase MHD flow between nanoparticle-containing plates was completed. Hall and ion slip effects in three-dimensional flow with a magnetic field and nanoparticles were investigated by Nawaz et al. (2018a). Nawaz et al. (2018b) investigated using computers how to increase heat transmission in MHD flow over a moving surface. Alharbi et al. (2019) investigated heat transfer in an MHD flow of fluid over a cylinder exposed to a magnetic field. In a chamber containing liquid and exposed to an external magnetic field, Saleem et al. (2019c) looked at heat transport in the liquid.
The flows of fluids in porous medium are encountered in several daily life applications, such as seepages of fluid through sands and rocks, movement of oil in soil etc. Thereby, various studies on the effects of heat transfer and fluid flow have been conducted. For example, Hayat et al. (2017) addressed governing issues for the impact of magnetic and thermal radiation on heat transfer in a Maxwellian fluid under a permeable channel field. Sheikholeslami and Zeeshan (2018) performed numerical simulations to enhance the thermal conduction properties of nanofluids containing iron oxide nanoparticles with a porous medium. Darcy’s law is followed by the flow resistance caused by porous media. Maghsoudi and Siavashi (2019) investigated the optimization of pore diameters in a heterogeneous porous media with different convection in a lid-driven cavity with two sides. Vo et al. (2019) investigated the effect of nano-particles on the transmission of heat energy in magnetohydrodynamic flow during convective heat transfer under the influence of sinusoidal resistive force due to porous media. In a cadmium telluride nanofluid, Hanif et al. (2019) examined the effects of a cone inserted into a porous media on MHD natural convection. Khan and Aziz (2011) investigated the impact of nanoparticles and porous media on mas and heat transmission during heterogeneous-homogeneous chemical processes.
The Shooting method RK-5 method is utilized to solve initial value problems Along with the Newton-Raphson approach in the application of nanofluids. The higher order nonlinear ordinary differential equations are resolved by the shooting method (Rohni et al., 2012; Olatundun and Makinde, 2017; Nawaz and Shoaib Arif, 2019). The purpose of this study, which is motivated by the aforementioned sources of inspiration, is to investigate The effects of MHD, porous media, viscosity dissipation, Joule heating, and boundary layer restrictions on the heat flux and flow of Newtonian nanofluid. It was possible to complete the mathematical flow modeling of the nanofluid using a phase flow nanofluid model. It has been suggested that the nanoparticles in water (H2O) base fluid are comprised of copper oxide (CuO), aluminum oxide (Al2O3), and Titanium Dioxide (TiO2) nanoparticles. A quantitative model is created, which is then transformed into an ODE system by making the necessary similar modifications. The shooting method was used to resolve the nondimensional system of equations. The aftereffects of velocity and temperature distributions are shown and displayed using the MATLAB program for a lengthy period of time. Visual and numerical analyses of drag force and heat transfer rates are performed. The numerical results of the current study are also contrasted with those of earlier studies for comparison’s sake. As far as we can tell, there are no other publications in the literature that compare this model to it; it is novel and unique.
The results of this study will be useful for many power production and industries. So, (Hassan, 2018; Goud, 2020; Goud et al., 2020; Pramod Kumar et al., 2020; Hassan et al., 2021a; Kumar et al., 2021a; Bejawada et al., 2021; Hassan et al., 2021b; Kumar et al., 2021b; Goud and Nandeppanavar, 2021; Srinivasulu and Goud, 2021; Zhang et al., 2021; Hassan et al., 2022; Rizwan and Hassan, 2022; Shankar Goud et al., 2022) are a chosen number of the important determinants.
This paper is divided into five parts. The second segment has extensive modeling. Section 3 of the article covers the solution approach. Section 5 presents and discusses the results. The results of this investigation are described near the end.
To investigate the rise in heat conductivity, let’s explore how three various nanometallic structures, namely CuO, Al2O3 and TiO2 disperse in water. Nano-water is exposed to a magnetic field. When heated, vertical surfaces are coated with a nano-water mixture, convection happens. Additionally, it is anticipated that this nano-water mixture generates heat. A Boussinesq calculation shows that the buoyancy force is significant.
The ensuing standards, together with the requirements, be relevant to the stream framework:
In Figure 1, the geometry of the flow model is shown as:
Since fluid is moving through a porous media, it is subject to a resistive force. Simplified PDEs are
The given BCs are
Where,
Table 1 below lists nanoparticle correlations.
TABLE 1. Nanofluid thermophysical properties are (Goud, 2020).
Equations 1–4 become dimensionless by adding new variables.
and as a result, one can
Dimensioless BCs (boundary conditions) are
The derivatives mentioned above relate to the variable
Divergent velocity is (Hafeez et al., 2021)
Nusselt number is
Local Reynolds number is
Thermo physical properties water and nanoparticles are presented in Table 3.
TABLE 3. Thermo physical properties water and nanoparticles (Jamshed and Aziz, 2018; Jamshed, 2021; Khashi’ie et al., 2020).
Shooting method is used to solve the higher order nonlinear ordinary differential equations (ODEs). It is an iterative technique that transforms the original boundary value problems (BVPs) into initial value problems (IVPs). The differential equations of IVPs are integrated numerically through RK-5 method Table 4. The formulated problem needs the IVP with arbitrarily chosen initial conditions to approximate the boundary conditions. If the boundary conditions are not fulfilled to the required accuracy, with the new set of initial conditions, which are modified by Newton’s method. The process of Newton method is repeated until the require accuracy is achieved. The flow chart of the shooting method is as follows in Figure 2.
For a structure of two coupled first ODEs.
•
•
• Set
• Solve the ODE using IVP technique (RK-5), and compared the result at
• Make another guess.
• If solution at
Different techniques are used by researchers for solving ordinary differential equations and this always remain area of interest. Linear differential equation is easy to solve by analytical method but solving non-linear ODEs by systematic method is difficult to solve. So researchers used other techniques to find approximate solutions for these equations. The two most popular Runge-Kutta techniques are Ruge-Kutta 4 and Ruge-Kutta 5. Runge-Kutta method is also iterative technique and includes well known routine called Euler method. In this thesis we used RK-5 method and algorithm for RK-5 method is given below.
Suppose the following problem with given initial conditions
Then, RK-5 Method for the above initial valued problem is given by
In above expression,
Where, h is the size of time interval.
The correctness of the computational strategy was established by comparing the heat transfer magnitude from the current approach with the verified results of prior investigations (Jamshed et al., 2021a; Qureshi, 2021). The results of the current investigation were quite accurate and comparable.
Initial value problems are built using normalized governing boundary-value problems with correlations for thermally factors. Utilizing starting circumstances, the shooting method with Runge-Kutta 5th order is used to solve problems with changed beginning value. Using parametric simulations, the dynamics of the flow low variables are examined in Table 1. To choose the best nanoparticles from CuO, Al2O3 and TiO2 for the system, simulations are done. When
Table 5 displays the local friction coefficient and Nusselt number for a nanofluid containing Cu for different nanoparticle factors.
TABLE 5. For nanofluid with copper oxide nanoparticles with several nanoparticle factors, Nusselt number and local skin friction coefficient are equal to 0.2.
1) Convection heat transfer in Newtonian fluid exposed to magnetic field and having nano-solid metallic structures is being explored to look into the improvement in thermal conductivity. Then, for an efficient thermal system like car engines, dispersion of nano-particles among nanofluids CuO, Al2O3 and TiO2 may be suggested. Key studies are listed below, along with the numerical solutions to the governing problems.
2) The favorable Buoyancy force assists the flow and magnetohydrodynamic boundary layer thickness has shown are rising trend when Grashof number is increased. This study is noted for all types of nanoparticles;
3) The variation of Biot number has shown decreasing trend on the flow of fluid. Hence flow is decelerated when Biot number is increased;
A significant restriction to fluid flow results from increasing the magnetic field’s intensity. As a result, as the magnetic field increases, the boundary layer’s thickness decreases.
Future applications of the fifth-order Runge-Kutta shooting technique could include a range of physical and technological difficulties (Adnan et al., 2021; Adnan, 2022; Adnan and Ashraf, 2022; Khan et al., 2022a; Khan et al., 2022b). According to (Jamshed et al., 2021b; Jamshed, 2021; Jamshed and Nisar, 2021), there have been several recent advancements that explore the importance of the research domain under consideration.
The raw data supporting the conclusions of this article will be made available by the authors, without undue reservation.
MB and MK formulated the problem. MB and WJ solved the problem. MB, MK, WJ, ET, HE-W, and FA, computed and scrutinized the results. All the authors equally contributed in writing and proof reading of the paper. All authors reviewed the manuscript.
The researchers would like to thank the Deanship of Scientific Research, Qassim University for funding the publication of this project.
The authors declare that the research was conducted in the absence of any commercial or financial relationships that could be construed as a potential conflict of interest.
All claims expressed in this article are solely those of the authors and do not necessarily represent those of their affiliated organizations, or those of the publisher, the editors and the reviewers. Any product that may be evaluated in this article, or claim that may be made by its manufacturer, is not guaranteed or endorsed by the publisher.
Adnan, U. K., Ahmed, N., Manzoor, R., Mohyud-Din, S. T., and Mohyud-Din, S. T. (2021). Impacts of various shaped Cu-nanomaterial on the heat transfer over a bilateral stretchable surface: Numerical investigation. Adv. Mech. Eng. 13, 168781402110674. doi:10.1177/16878140211067420
Adnan, W. A., and Ashraf, W. (2022). Numerical thermal featuring in γAl2O3-C2H6O2 nanofluid under the influence of thermal radiation and convective heat condition by inducing novel effects of effective Prandtl number model (EPNM). Adv. Mech. Eng. 14 (6), 168781322211065. doi:10.1177/16878132221106577
Adnan, W. A. (2022). Thermal efficiency in hybrid (Al2O3-CuO/H2O) and ternary hybrid nanofluids (Al2O3-CuO-Cu/H2O) by considering the novel effects of imposed magnetic field and convective heat condition. Waves in Random and Complex Media, 1–16.
Afridi, M. I., Qasim, M., and Saleem, S. (2018). Second law analysis of three dimensional dissipative flow of hybrid nanofluid. J. nanofluids 7 (6), 1272–1280. doi:10.1166/jon.2018.1532
Alharbi, S. O., Nawaz, M., and Nazir, U. (2019). Thermal analysis for hybrid nanofluid past a cylinder exposed to magnetic field. AIP Adv. 9 (11), 115022. doi:10.1063/1.5127327
Bejawada, S. G., Khan, Z. H., and Hamid, M. (2021). Heat generation/absorption on MHD flow of a micropolar fluid over a heated stretching surface in the presence of the boundary parameter. Heat. Transf. 50 (6), 6129–6147. doi:10.1002/htj.22165
Chamkha, A. J., Dogonchi, A. S., and Ganji, D. D. (2019). Magneto-hydrodynamic flow and heat transfer of a hybrid nanofluid in a rotating system among two surfaces in the presence of thermal radiation and Joule heating. AIP Adv. 9 (2), 025103. doi:10.1063/1.5086247
Dogonchi, A. S., Armaghani, T., Chamkha, A. J., and Ganji, D. D. (2019). Natural convection analysis in a cavity with an inclined elliptical heater subject to shape factor of nanoparticles and magnetic field. Arab. J. Sci. Eng. 44, 7919–7931. doi:10.1007/s13369-019-03956-x
Dogonchi, A. S., Waqas, M., Seyyedi, S. M., Hashemi-Tilehnoee, M., and Ganji, D. D. (2019). Numerical simulation for thermal radiation and porous medium characteristics in flow of CuO-H 2 O nanofluid. J. Braz. Soc. Mech. Sci. Eng. 41 (6), 249. doi:10.1007/s40430-019-1752-5
Ghadikolaei, S. S., Hosseinzadeh, K., and Ganji, D. D. (2018a). RETRACTED: MHD raviative boundary layer analysis of micropolar dusty fluid with graphene oxide (go)- engine oil nanoparticles in a porous medium over a stretching sheet with joule heating effect. Powder Technol. 338, 425–437. doi:10.1016/j.powtec.2018.07.045
Ghadikolaei, S. S., Hosseinzadeh, K., Ganji, D. D., and Hatami, M. (2018b). Fe3O4–(CH2OH)2 nanofluid analysis in a porous medium under MHD radiative boundary layer and dusty fluid. J. Mol. Liq. 258, 172–185. doi:10.1016/j.molliq.2018.02.106
Gholinia, M., Hosseinzadeh, K., Mehrzadi, H., Ganji, D. D., and Ranjbar, A. A. (2019). Investigation of MHD Eyring–Powell fluid flow over a rotating disk under effect of homogeneous–heterogeneous reactions. Case Stud. Therm. Eng. 13, 100356. doi:10.1016/j.csite.2018.11.007
Goud, B. S. (2020). Heat generation/absorption influence on steady stretched permeable surface on MHD flow of a micropolar fluid through a porous medium in the presence of variable suction/injection. Int. J. Thermofluids 7, 100044. doi:10.1016/j.ijft.2020.100044
Goud, B. S., and Nandeppanavar, M. M. (2021). Ohmic heating and chemical reaction effect on MHD flow of micropolar fluid past a stretching surface. Partial Differ. Equations Appl. Math. 4, 100104. doi:10.1016/j.padiff.2021.100104
Goud, B. S., Srilatha, P., Bindu, P., and Krishna, Y. H. (2020). Radiation effect on MHD boundary layer flow due to an exponentially stretching sheet. Adv. Math. Sci. J. 9 (12), 10755–10761. doi:10.37418/amsj.9.12.59
Hafeez, M. B., Amin, R., Nisar, K. S., Jamshed, W., Abdel-Aty, A. H., and Khashan, M. M. (2021). Heat transfer enhancement through nanofluids with applications in automobile radiator. Case Stud. Therm. Eng. 27, 101192. doi:10.1016/j.csite.2021.101192
Hanif, H., Khan, I., and Shafie, S. (2019). MHD natural convection in cadmium telluride nanofluid over a vertical cone embedded in a porous medium. Phys. Scr. 94 (12), 125208. doi:10.1088/1402-4896/ab36e1
Hassan, M., Ali, S., Aich, W., Khlissa, F., Ayadi, B., and Kolsi, L. (2022). Transport pattern of Non-Newtonian mass and thermal energy under two diverse flow conditions by using modified models for thermodynamics properties. Case Stud. Therm. Eng. 29, 101714. doi:10.1016/j.csite.2021.101714
Hassan, M., Al‐Khaled, K., Khan, S. U., Tlili, I., and Chammam, W. (2021). Assessment of boundary layer for flow of non‐Newtonian material induced by a moving belt with power law viscosity and thermal conductivity models. Numer. Methods Partial Differ. Equ., num.22743. doi:10.1002/num.22743
Hassan, M., El‐Zahar, E. R., Khan, S. U., Rahimi‐Gorji, M., and Ahmad, A. (2021). Boundary layer flow pattern of heat and mass for homogenous shear thinning hybrid‐nanofluid: An experimental data base modeling. Numer. Methods Partial Differ. Equ. 37 (2), 1234–1249. doi:10.1002/num.22575
Hassan, M. (2018). Impact of iron oxide particles concentration under a highly oscillating magnetic field on ferrofluid flow. Eur. Phys. J. Plus 133 (6), 230–234. doi:10.1140/epjp/i2018-12045-7
Hatami, M., Hosseinzadeh, K., Domairry, G., and Behnamfar, M. T. (2014). Numerical study of MHD two-phase Couette flow analysis for fluid-particle suspension between moving parallel plates. J. Taiwan Inst. Chem. Eng. 45 (5), 2238–2245. doi:10.1016/j.jtice.2014.05.018
Hayat, T., Khan, M. I., Waqas, M., Alsaedi, A., and Farooq, M. (2017). Numerical simulation for melting heat transfer and radiation effects in stagnation point flow of carbon–water nanofluid. Comput. methods Appl. Mech. Eng. 315, 1011–1024. doi:10.1016/j.cma.2016.11.033
Hosseinzadeh, K., Gholinia, M., Jafari, B., Ghanbarpour, A., Olfian, H., and Ganji, D. D. (2019). Nonlinear thermal radiation and chemical reaction effects on Maxwell fluid flow with convectively heated plate in a porous medium. Heat. Trans. Res. 48 (2), 744–759. doi:10.1002/htj.21404
Jamshed, W., and Aziz, A. (2018). Entropy analysis of TiO2-CuO/EG casson hybrid nanofluid via cattaneo-christov heat flux model. Appl. Nanosci. 08, 01–14.
Jamshed, W., Devi, S. U., and Nisar, K. S. (2021). Single phase-based study of Ag-Cu/EO Williamson hybrid nanofluid flow over a stretching surface with shape factor. Phys. Scr. 96, 065202. doi:10.1088/1402-4896/abecc0
Jamshed, W., and Nisar, K. S. (2021). Computational single‐phase comparative study of a Williamson nanofluid in a parabolic trough solar collector via the Keller box method. Int. J. Energy Res. 45 (7), 10696–10718. doi:10.1002/er.6554
Jamshed, W., Nisar, K. S., Mohamed Isa, S. S. P., Batool, S., Abdel-Aty, A. H., and Zakarya, M. (2021). Computational case study on tangent hyperbolic hybrid nanofluid flow: Single phase thermal investigation. Case Stud. Therm. Eng. 27, 101246. doi:10.1016/j.csite.2021.101246
Jamshed, W. (2021). Numerical investigation of MHD impact on maxwell nanofluid. Int. Commun. Heat Mass Transf. 120, 104973. doi:10.1016/j.icheatmasstransfer.2020.104973
Khan, U. A., Ullah, B., Abdul Wahab, H., Ullah, I., Almuqrin, M. A., and Khan, I. (2022). Comparative thermal transport mechanism in Cu-H2O and Cu-Al2O3/H2O nanofluids: Numerical investigation. Waves in Random and Complex Media, 1–16.
Khan, U., Ahmed, N., and Khan, I. (2022). Heat transfer evaluation in MgZn6Zr/C8H18 [(Magnesium-Zinc-Zirconium)/Engine oil] with non-linear solar thermal radiations and modified slip boundaries over 3-dimensional convectively heated surface. Front. Energy Res. 351.
Khan, W. A., and Aziz, A. (2011). Double-diffusive natural convective boundary layer flow in a porous medium saturated with a nanofluid over a vertical plate: Prescribed surface heat, solute and nanoparticle fluxes. Int. J. Therm. Sci. 50 (11), 2154–2160. doi:10.1016/j.ijthermalsci.2011.05.022
Khashi'ie, N. S., Arifin, N. M., Pop, I., and Wahid, N. S. (2020). Flow and heat transfer of hybrid nanofluid over a permeable shrinking cylinder with joule heating: A comparative analysis. Alexandria Eng. J. 59 (3), 1787–1798. doi:10.1016/j.aej.2020.04.048
Kumar, M. A., Reddy, Y. D., Goud, B. S., and Rao, V. S. (2021). Effects of soret, dufour, hall current and rotation on MHD natural convective heat and mass transfer flow past an accelerated vertical plate through a porous medium. Int. J. Thermofluids 9, 100061. doi:10.1016/j.ijft.2020.100061
Kumar, M. A., Reddy, Y. D., Rao, V. S., and Goud, B. S. (2021). Thermal radiation impact on MHD heat transfer natural convective nano fluid flow over an impulsively started vertical plate. Case Stud. Therm. Eng. 24, 100826. doi:10.1016/j.csite.2020.100826
Li, Z., Sheikholeslami, M., Mittal, A. S., Shafee, A., and Haq, R. U. (2019). Nanofluid heat transfer in a porous duct in the presence of Lorentz forces using the lattice Boltzmann method. Eur. Phys. J. Plus 134 (1), 30.
Maghsoudi, P., and Siavashi, M. (2019). Application of nanofluid and optimization of pore size arrangement of heterogeneous porous media to enhance mixed convection inside a two-sided lid-driven cavity. J. Therm. Anal. Calorim. 135 (2), 947–961. doi:10.1007/s10973-018-7335-3
Nawaz, M., Rana, S., and Qureshi, I. H. (2018). Computational fluid dynamic simulations for dispersion of nanoparticles in a magnetohydrodynamic liquid: A galerkin finite element method. RSC Adv. 8 (67), 38324–38335. doi:10.1039/c8ra03825b
Nawaz, M., Rana, S., Qureshi, I. H., and Hayat, T. (2018). Three-dimensional heat transfer in the mixture of nanoparticles and micropolar MHD plasma with Hall and ion slip effects. AIP Adv. 8 (10), 105109. doi:10.1063/1.5050670
Nawaz, Y., and Shoaib Arif, M. (2019). Keller-Box shooting method and its application to nanofluid flow over convectively heated sheet with stability and convergence. Numer. Heat. Transf. Part B Fundam. 76 (3), 152–180. doi:10.1080/10407790.2019.1644924
Olatundun, A. T., and Makinde, O. D. (2017). “Analysis of Blasius flow of hybrid nanofluids over a convectively heated surface,” in Defect and diffusion forum (Trans Tech Publications Ltd), 377, 29–41.
Pramod Kumar, P., Shankar Goud, B., and Malga, B. S. (2020). Finite element study of Soret number effects on MHD flow of Jeffrey fluid through a vertical permeable moving plate. Partial Differ. Equ. Appl. Math. 1, 100005. doi:10.1016/j.padiff.2020.100005
Qureshi, M. A. (2021). Thermal capability and entropy optimization for Prandtl-Eyring hybrid nanofluid flow in solar aircraft implementation. Alexandria Eng. J. 61 (7), 5295–5307. doi:10.1016/j.aej.2021.10.051
Ramzan, M., Sheikholeslami, M., Saeed, M., and Chung, J. D. (2019). On the convective heat and zero nanoparticle mass flux conditions in the flow of 3D MHD Couple Stress nanofluid over an exponentially stretched surface. Sci. Rep. 9 (1), 562. doi:10.1038/s41598-018-37267-2
Rizwan, M., and Hassan, M. (2022). Feature of metallic oxide nanoparticles in the thermal efficiency and flow structure of non-Newtonian homogeneous nanofluid: Experimental data-based mathematical approach. Waves in Random and Complex Media, 1–20.
Rohni, A. M., Ahmad, S., and Pop, I. (2012). Flow and heat transfer over an unsteady shrinking sheet with suction in nanofluids. Int. J. Heat Mass Transf. 55 (7-8), 1888–1895. doi:10.1016/j.ijheatmasstransfer.2011.11.042
Sadiq, M. A., Khan, A. U., Saleem, S., and Nadeem, S. (2019). Numerical simulation of oscillatory oblique stagnation point flow of a magneto micropolar nanofluid. RSC Adv. 9 (9), 4751–4764. doi:10.1039/c8ra09698h
Saleem, S., Firdous, H., Nadeem, S., and Khan, A. U. (2019). Convective heat and mass transfer in magneto Walter’s B nanofluid flow induced by a rotating cone. Arab. J. Sci. Eng. 44 (2), 1515–1523. doi:10.1007/s13369-018-3598-z
Saleem, S., Nadeem, S., Rashidi, M. M., and Raju, C. S. (2019). An optimal analysis of radiated nanomaterial flow with viscous dissipation and heat source. Microsyst. Technol. 25 (2), 683–689. doi:10.1007/s00542-018-3996-x
Saleem, S., Shafee, A., Nawaz, M., Dara, R. N., Tlili, I., and Bonyah, E. (2019). Heat transfer in a permeable cavity filled with a ferrofluid under electric force and radiation effects. AIP Adv. 9 (9), 095107. doi:10.1063/1.5120439
Shankar Goud, B., Pramod Kumar, P., and Malga, B. S. (2022). Induced magnetic field effect on MHD free convection flow in nonconducting and conducting vertical microchannel walls. Heat. Trans. 51 (2), 2201–2218. doi:10.1002/htj.22396
Sheikholeslami, M., Mehryan, S. A., Shafee, A., and Sheremet, M. A. (2019a). Variable magnetic forces impact on magnetizable hybrid nanofluid heat transfer through a circular cavity. J. Mol. Liq. 277, 388–396. doi:10.1016/j.molliq.2018.12.104
Sheikholeslami, M., Saleem, S., Shafee, A., Li, Z., Hayat, T., Alsaedi, A., et al. (2019b). Mesoscopic investigation for alumina nanofluid heat transfer in permeable medium influenced by Lorentz forces. Comput. Methods Appl. Mech. Eng. 349, 839–858.
Sheikholeslami, M., and Zeeshan, A. (2018). Numerical simulation of Fe3O4-water nanofluid flow in a non-Darcy porous media. Int. J. Numer. Methods Heat. Fluid Flow. 28 (3), 641–660. doi:10.1108/hff-04-2017-0160
Srinivasulu, T., and Goud, B. S. (2021). Effect of inclined magnetic field on flow, heat and mass transfer of Williamson nanofluid over a stretching sheet. Case Stud. Therm. Eng. 23, 100819. doi:10.1016/j.csite.2020.100819
Vo, D. D., Hedayat, M., Ambreen, T., Shehzad, S. A., Sheikholeslami, M., Shafee, A., et al. (2019). Effectiveness of various shapes of Al2O3 nanoparticles on the MHD convective heat transportation in porous medium. J. Therm. Anal. Calorim. 139, 1345–1353. doi:10.1007/s10973-019-08501-4
Zangooee, M. R., Hosseinzadeh, K., and Ganji, D. D. (2019). Hydrothermal analysis of MHD nanofluid (TiO2-GO) flow between two radiative stretchable rotating disks using AGM. Case Stud. Therm. Eng. 14, 100460. doi:10.1016/j.csite.2019.100460
Keywords: thermal performance, magnetohydrodynamic flow, porous medium, nanoparticles, thermal jump conditions
Citation: Bilal Hafeez M, Krawczuk M, Jamshed W, Tag El Din ESM, El-Wahed Khalifa HA and Aziz ElSeabee FA (2022) Thermal energy development in magnetohydrodynamic flow utilizing titanium dioxide, copper oxide and aluminum oxide nanoparticles: Thermal dispersion and heat generating formularization. Front. Energy Res. 10:1000796. doi: 10.3389/fenrg.2022.1000796
Received: 22 July 2022; Accepted: 16 August 2022;
Published: 11 October 2022.
Edited by:
Adnan, Mohi-ud-Din Islamic University, PakistanReviewed by:
B. Shankar Goud, Jawaharlal Nehru Technological University, Hyderabad, IndiaCopyright © 2022 Bilal Hafeez, Krawczuk, Jamshed, Tag El Din, El-Wahed Khalifa and Aziz ElSeabee. This is an open-access article distributed under the terms of the Creative Commons Attribution License (CC BY). The use, distribution or reproduction in other forums is permitted, provided the original author(s) and the copyright owner(s) are credited and that the original publication in this journal is cited, in accordance with accepted academic practice. No use, distribution or reproduction is permitted which does not comply with these terms.
*Correspondence: Wasim Jamshed, d2FzaWt0a0Bob3RtYWlsLmNvbQ==
Disclaimer: All claims expressed in this article are solely those of the authors and do not necessarily represent those of their affiliated organizations, or those of the publisher, the editors and the reviewers. Any product that may be evaluated in this article or claim that may be made by its manufacturer is not guaranteed or endorsed by the publisher.
Research integrity at Frontiers
Learn more about the work of our research integrity team to safeguard the quality of each article we publish.