- School of Environmental and Municipal Engineering, Qingdao University of Technology, Qingdao, China
In order to study the effect of biomass on the pyrolysis characteristics of urea-formaldehyde resin, the thermogravimetric experiments were carried out respectively using urea-formaldehyde resin (UF), rice straw (RS), and their mixed pellets with different proportions. The pyrolysis kinetics analysis was conducted. The results showed that the pyrolysis process of UF resin and mixed pellets could be divided into three stages: the drying and dehydration of the material, the rapid decomposition of volatile matter, and residue decomposition. The reaction order of UF resin and mixed pellets was discussed using the Coats–Redfern method, the activation energy of UF resin was 54.27 kJ/mol, and this value decreased with the addition of rice straw. As the mass ratio of UF resin to rice straw was 3:1, the activation energy achieved the lowest value, which means that the addition of rice straw was beneficial to the pyrolysis process of UF. In the process of pellet preparation, the falling strength and compressive strength of UF resin pellets can be improved by adding an appropriate proportion of rice straw. In this test, the yield of pyrolytic carbon reached the highest value of 23.93%, as the mass ratio of UF resin to rice straw was 3:2. When the mass ratio was 4:1, the highest liquid product yield of 43.21% was achieved.
1 Introduction
Because it is the main building material of wood products such as furniture, the production of the wood-based panel in China has reached 299.09 million m3 in 2018 (NFGA, 2019). Specifically, adhesives account for about 10% of wood substrates. These adhesives include urea-formaldehyde resin (UF), phenol-formaldehyde resin (PF), and melamine-formaldehyde resin (MF), among which UF resin is the most commonly used adhesive (Gu, 2015). Moreover, UF resin was listed as the 13th category of hazardous wastes according to the National Hazardous Waste List in 2016. Improper handling of UF resin can cause serious environmental pollution.
Pyrolysis technology can convert particleboard into value-added chemicals, such as improved biochar for fuel combustion (Ying et al., 2022). These studies provide a more valid basis for the recycling of urea-formaldehyde resin. In terms of practical engineering application, in order to reduce the difficulty of pretreatment, many researchers try to pyrolysis the mixture of UF resin and biomass to study the effect of UF resin on biomass pyrolysis. Feng et al. (2012) used TG and DTG analysis to evaluate the influence of UF resin on waste particleboards during the co-pyrolysis process and found that the thermal stability of particleboard was enhanced by UF resin, and the degradation was inhibited, especially for the second stage of pyrolysis. Zhang et al. (2014) analyzed the pyrolysis characteristics of eucalyptus, eucalyptus added with 10 %UF resin, eucalyptus added with 10% MUF resin, UF resin, and MUF resin and found that UF resin and MUF resin can reduce the energy required for eucalyptus pyrolysis. Meanwhile, Zhang et al. (2016) studied the pyrolysis process and product characteristics of poplar, UF resin, and particleboard. The result showed that the effect of UF resin on particleboard cracking fluid was mainly reflected in nitrogen compounds. There are more nitrogen compounds in particleboard cracking fluid than poplar cracking fluid. Li et al. (2014) found that more nitrogen elements in UF resin were fixed by cellulose and into the solid products of cellulose pyrolysis. For lignin, UF resin combined with lignin during pyrolysis to generate thermally unstable compounds and continued pyrolysis to release large amounts of compounds, including nitrogen compounds and carbon oxides, which promoted the decomposition of lignin and directly affected the generation of products. However, there are some controversial statements about the effects of adhesives on wood pyrolysis (Xu et al., 2020).
In this article, thermogravimetric and kinetics analyses were performed using a thermogravimetric analyzer to analyze the activation energy. At the same time, the mixture of UF resin and biomass was pelletized to improve its strength and study the effect of mixing ratio on the pyrolysis characteristics and the distribution of pyrolysis products.
2 Experimental
2.1 Materials
The urea-formaldehyde resin (UF) was obtained from the waste wood-based panels produced by a building decoration company in Jinan city, Shandong province, China. Rice straw (RS) was obtained from Shanxi province, China. The original samples were crushed in a high-speed grinder and sieved to obtain a size fraction <74 μm and then dried in a drying oven at 105°C until the quality was constant. Then, UF resin and RS mixed ratios of 1:0, 5:1, 4:1, 3:1, and 3:2 were pelleted.
2.2 Experimental Method
2.2.1 Thermogravimetric Test
Each mixed sample weighed 30 mg. The sample was thereafter placed in a microcomputer thermobalance (HTG-1) and heated up from 20°C to 600°C at a rate of 20°C/min under a nitrogen atmosphere with a flow rate of 100 ml/min. TG data of the reaction process were recorded automatically by the data acquisition system.
2.2.2 Strength Test and Pyrolysis Experiment
Preparation of Urea-Formaldehyde Resin and Rice Straw Mixed Pellets
Take about 5 g of the mixed powder and put it into the designated ball mold. Keep it below 15 MPa for 10 min in the pelletizer machine to eliminate intermolecular pressure and strengthen molecular bonds (Wang et al., 2020). The diameter of the prepared pellet is between 10 and 12 mm.
Test Procedure of Falling Strength
The falling strength tester was used to test the falling strength of samples. The green pellets with a diameter of 10.0–12.5 mm were dropped freely on the steel plate from an altitude of 500 mm. This process was repeated several times until the pellets were broken. In the aspect of data processing, the maximum and the minimum values of falling times were deleted, and the arithmetic mean value was recorded as the falling strength index (times/pellet).
Test Procedure of Compressive Strength
The compressive strength was tested using the compressive strength tester. In the aspect of data processing, the maximum and the minimum values of falling times were deleted, and the arithmetic mean value was recorded as the falling strength index (N/pellet).
Pyrolysis Process
Tests were performed at atmospheric pressure, and the pyrolysis reactor was surrounded by an electric furnace. The schematic lab-scale configuration is illustrated in Figure 1. The effective height of the pyrolysis reactor was 800 mm. Samples were fed into the furnace through the top of the pyrolysis reactor. A thermocouple was used to monitor the temperature profile in the middle of the pyrolysis reactor.
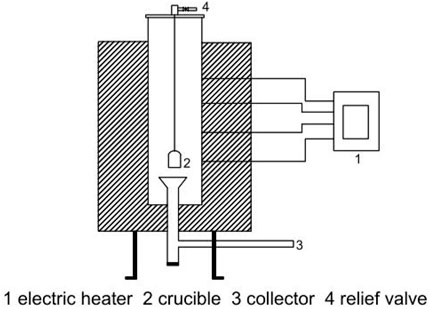
FIGURE 1. Schematic diagram of the pyrolysis device. 1. Electric heater. 2. Crucible. 3. Collector. 4. Relief valve.
Initially, 5 g of sample was put into the center of the reactor, and the electric heater was turned on. Under vacuum, the mixture was heated up to 550°C and kept for 60 min. Then, the reaction mixture was cooled to room temperature. The gas products were collected by a sampling bag and measured by the water drainage method. The liquid products were collected by syringe, and the pyrolysis char was retained in the crucible.
3 Experimental Results and Discussion
3.1 Pyrolysis Characteristics
Figures 2A,B, respectively, show the TG curves and the DTG curves of five samples.
As shown in Figure 2, the pyrolysis process can be divided into three stages, which have similar pyrolysis rules but have their own characteristics. This is consistent with the research of GIRODS P (Girods et al., 2008a; Girods et al., 2008b; Girods et al., 2009).
The first stage (20°C–239°C) is the drying and dehydration stage of the material. It is mainly caused by the evaporation of water in the material and the release of free formaldehyde in UF; the reduction of polymerization degree caused by chain break of macromolecular compounds in straw; and the formation of hydroxyl group, carbonyl group, and hydrogen peroxide group (Lowell and Zhengtian, 1988; Feng et al., 2012; Thao and Yuh, 2021).
The second stage (239°C–340°C) is the main pyrolysis stage, which is the pyrolysis of volatiles in UF resin and decomposition and volatilization of cellulose, hemicellulose, and lignin in RS. In particular, cellulose is massively pyrolyzed in the process (Zhang et al., 2021). After the addition of RS, the TG curve of UF resin shifted to high temperature region and the maximum weight loss rate decreased obviously. Therefore, it is speculated that the addition of straw improves the thermal stability and inhibits the rapid pyrolysis process of UF resin.
The third stage (340°C–600°C) is residue decomposition. The mass of samples is no longer changed, and the pyrolytic char is eventually formed. The content of RS affects the yield of pyrolytic charcoal, which is mainly affected by the high thermal stability of lignin (Ma et al., 2015). When the mass ratio is 3:2, the yield of pyrolytic char reaches a maximum.
3.2 Kinetic Analysis
Generally, the thermal degradation of the solid materials may be assumed to occur after following Eq. 1:
The reaction rate can be expressed as Eq. 2, (Hu and Shi, 2008):
where k is the reaction rate constant; t is the reaction time, s; and
where
The relationship between reaction rate constant K and reaction temperature T can be expressed by the Arrhenius equation:
where
For non-isothermal heating at a constant heating rate, the reaction rate β is
Equation 6 can be obtained:
where
where
Equation 7 can be simplified as
Through calculation and comprehensive consideration of the kinetic correlation coefficients of five samples, the best fitting is obtained using the first-order reaction kinetic model in this study. Therefore, the selected mechanism function form is
The obtained dynamic factors are shown in Table 1, and the linear fitting effect is shown in Figure 3.
As can be seen from Table 1, the activation energy of UF resin is the highest, and the activation energy is the lowest when the mass ratio is 3:1. The activation energy of samples with added biomass was lower than that of UF resin. Because RS has the characteristics of low density and loose structure, it is found that the surface structure of blended power is looser after adding RS, which facilitates the occurrence of pyrolysis reaction and reduces the activation energy.
3.3 The Falling Strength and Compressive Strength of Pellet
By testing the falling strength and compressive strength of the pellets, the falling strength is 6.6, 9.3, 28.1, 27.8, and 10.3, and the compressive strength (N/pellet) is 47.0, 151.6, 174.7, 204.4, and 430.9, respectively corresponding to the following five mixing ratio pellets, UF:RS = 1:0, UF:RS = 5:1, UF:RS = 4:1, UF:RS = 3:1, and UF:RS = 3:2. It can be seen that the drop strength and compressive strength of UF resin were minimum when it was pelleted alone. With the addition of RS, the falling intensity of mixed pellets increased first and then decreased. When the mass ratio of UF to RS varied from 5:1 to 3:1, the falling intensity increased significantly. However, when the mass ratio of UF to RS continued to increase to 3:2, the falling intensity of the pellet decreased sharply. Therefore, the increase of RS ratio could not increase the pellet falling intensity continuously. As the ratio of RS increased, the compressive strength continued to increase.
The pellet quality has a significant impact on subsequent processes, which is mainly manifested in the dropping of raw pellets during transportation and blasting during oxidizing roasting. The proper compressive strength is conductive to the pyrolysis of pellets. The pellets tend to be pulverized when the compressive strength is low. The high compressive strength is not conducive to the complete progress of the reaction (Kaikai et al., 2017). According to relevant literature, the quality requirements of green balls are as follows: falling strength >7 times/piece and compressive strength >12 N/piece (Lv, 2018). It can be seen from the experimental data that the proper addition of RS is beneficial in increasing the compressive strength and falling strength of the blend pellet.
3.4 The Pyrolysis Product Distribution of Pellet
The pyrolysis products distribution of mixed pellets is shown in Figure 4.
As shown from Figure 4, the yields of pyrolysis products of mixed pellets are significantly different. The liquid yield is the lowest during the pyrolysis process of UF resin pellets. When the mass ratio of UF resin to RS is 4:1, the mass fraction of pyrolysis oil is the highest (43.21%). When the mass ratio of UF resin to RS is 3:1, the mass fraction of pyrolysis gas was the highest, which is 50.97%. When the mass ratio of UF resin to RS is 3:2, the mass fraction of pyrolytic char is 23.93%. The cellulose in the biomass promotes the retention of nitrogen during the pyrolysis of the UF resin (Zongyuan et al., 2018) and exerts a positive effect on reducing the release of nitrogen-containing compounds. The mass ratios of UF to RS have a great influence on product distribution. Therefore, the doping ratio of biomass can be modulated according to the actual needing for the various phase products.
4 Conclusion
The TG method was used to study the co-pyrolysis of UF and RS. The conclusion was obtained that incorporating RS greatly improved the thermal stability of UF in the main pyrolysis. Further kinetic analysis showed that the reaction is of first order. After RS is added, the activation energy required for the UF resin reaction is reduced. In the process of pellet preparation, the falling strength and compressive strength of UF resin pellets can be improved by adding an appropriate proportion of RS. During the co-pyrolysis process of UF resin and RS, the ratio of RS has a significant effect on the distribution of three-phase products. The mass fraction of pyrolytic carbon is the highest (23.93%) when the mass ratio of UF resin to RS is 3:2. When the ratio of UF resin to RS is 4:1, the liquid product yield reaches the maximum value, which is 43.21%.
Data Availability Statement
The raw data supporting the conclusion of this article will be made available by the authors without undue reservation.
Author Contributions
SL and ZZ proposed research concepts and experimental design. XL contributed to the analysis of data and articles. HB conducted experiments. WZ and DR made constructive comments on the revision of the article.
Funding
This research was supported by the Natural Science Foundation of China (52104397), the Natural Science Foundation of Shandong Province (ZR2020QE150, ZR2019MEE015), and the 2020 Science and Technology Project of Qingdao West Coast New Area (2020-99).
Conflict of Interest
The authors declare that the research was conducted in the absence of any commercial or financial relationships that could be construed as a potential conflict of interest.
Publisher’s Note
All claims expressed in this article are solely those of the authors and do not necessarily represent those of their affiliated organizations or those of the publisher, editors, and reviewers. Any product that may be evaluated in this article, or claim that may be made by its manufacturer, is not guaranteed or endorsed by the publisher.
References
Feng, Y. S., Huang, Z. Y., and Mu, J. (2012). Pyrolysis Characteristics of poplar Particleboards Containing UF Resins. J. Beijing For. Univ. 34 (1), 119–122. doi:10.13332/j.1000-1522.2012.01.005
Foong, S. Y., Liew, R. K., Lee, C. L., Tan, W. P., Peng, W., Sonne, C., et al. (2022). Strategic hazard Mitigation of Waste Furniture Boards via Pyrolysis: Pyrolysis Behavior, Mechanisms, and Value-Added Products. J. Hazard. Mater. 421, 126774. doi:10.1016/J.JHAZMAT.2021.126774
Girods, P., Dufour, A., Rogaume, Y., Rogaume, C., and Zoulalian, A. (2009). Comparison of Gasification and Pyrolysis of thermal Pre-treated wood Board Waste. J. Anal. Appl. Pyrolysis 85 (1-2), 171–183. doi:10.1016/j.jaap.2008.11.014
Girods, P., Dufour, A., Rogaume, Y., Rogaume, C., and Zoulalian, A. (2008b). Thermal Removal of Nitrogen Species from wood Waste Containing Urea Formaldehyde and Melamine Formaldehyde Resins. J. Hazard. Mater. 159 (2-3), 210–221. doi:10.1016/j.jhazmat.2008.02.003
Girods, P., Rogaume, Y., Dufour, A., Rogaume, C., and Zoulalian, A. (2008a). Low-temperature Pyrolysis of wood Waste Containing Urea-Formaldehyde Resin. Renew. Energ. 33 (4), 648–654. doi:10.1016/j.renene.2007.03.026
Gu, J.-Y. (2015). Present Situation and Development Trend of wood Adhesives in China. Adhesion 36, 28–31. doi:10.3969/j.issn.1001-5922.2015.02.005
Kaikai, Y. E., Xing, P., Wang, J., Xinghong, D. U., Metallurgy, S. O., and University, N. (2017). Study on the Optimum Pelleitizing Condition of Preparing High Purity Silicon Using Carbide rice Husk. Ferro-Alloys 48 (11), 26–29. doi:10.16122/j.cnki.issn1001-1943.2017.11.006
Lai, Z., Li, S., Zhang, Y., Li, Y., and Mu, J. (2018). Influence of Urea Formaldehyde Resin on the Pyrolysis of Biomass Components: Cellulose, Hemicellulose, and Lignin. BioResources 13 (2). doi:10.15376/biores.13.2.2218-2232
Li, S. J., Mu, J., and Zhang, Y. (2014). Influence of Urea Formaldehyde Resin on Pyrolysis of Biomass: a Modeling Study by TG-FTIR. Guang Pu Xue Yu Guang Pu Fen Xi 34 (6), 1497–1501. doi:10.3964/j.issn.1000-0593(2014)06-1497-05
Lowell, R., and Zhengtian, L. (1988). Solid Wood Chemistry. Beijing: China Forestry Publishing House
Lv, T. (2018). Analysis of Chromite Ore Fine Pelletizing Pretreatment. Metallurgical Equipment 2018 (3), 35–41. doi:10.3969/j.issn.1001-1269.2018.03.010
Ma, Z., Chen, D., Gu, J., Bao, B., and Zhang, Q. (2015). Determination of Pyrolysis Characteristics and Kinetics of palm Kernel Shell Using TGA-FTIR and Model-free Integral Methods. Energ. Convers. Management 89, 251–259. doi:10.1016/j.enconman.2014.09.074
NFGA (2019). The National Forestry and Grassland Development Statistical Bulletin. Beijing: National Forestry and Gressland Administration
Ngo, T. N. L. T., and Chiang, K.-Y. (2021). Co-thermal Degradation Characteristics of rice Straw and Sewage Sludge. Sustain. Environ. Res. 31 (1). doi:10.1186/s42834-021-00096-6
Wang, T., Meng, D., Zhu, J., and Chen, X. (2020). Effects of Pelletizing Conditions on the Structure of rice Straw-Pellet Pyrolysis Char. Fuel 264, 116909. doi:10.1016/j.fuel.2019.116909
Xu, D., Yang, L., Zhao, M., Zhang, J., Syed-Hassan, S. S. A., Sun, H., et al. (2021). Conversion and Transformation of N Species during Pyrolysis of wood-based Panels: A Review. Environ. Pollut. 270, 116120. doi:10.1016/J.ENVPOL.2020.116120
Zhang, X., Xue, W., and Zhang, X. (2021). Pyrolysis Characteristics and Knietics Analysis of Mixed rice and Corn Straw. Acta Energiae Solaris Sinica 42 (11), 410–414. doi:10.19912/j.0254-0096.tynxb.2019-1347
Zhang, Y., He, Z. B., Xue, L., Chu, D. M., and Mu *, J. (2016). Influence of a Urea-Formaldehyde Resin Adhesive on Pyrolysis Characteristics and Volatiles Emission of poplar Particleboard. RSC Adv. 6 (16), 12850–12861. doi:10.1039/C5RA18068F
Keywords: urea-formaldehyde resin, pyrolysis, rice straw, kinetics analysis, pellet strength
Citation: Li X, Bing H, Luo S, Zhang W, Zuo Z and Ren D (2022) Study on the Pyrolysis Behaviors of Urea-Formaldehyde Resin and Rice Straw Mixed Pellets. Front. Energy Res. 9:813114. doi: 10.3389/fenrg.2021.813114
Received: 11 November 2021; Accepted: 24 December 2021;
Published: 17 January 2022.
Edited by:
Bamidele Victor Ayodele, Universiti Tenaga Nasional, MalaysiaReviewed by:
Jun Mu, Beijing Forestry University, ChinaMay Ali Alsaffar, University of Technology, Iraq, Iraq
Copyright © 2022 Li, Bing, Luo, Zhang, Zuo and Ren. This is an open-access article distributed under the terms of the Creative Commons Attribution License (CC BY). The use, distribution or reproduction in other forums is permitted, provided the original author(s) and the copyright owner(s) are credited and that the original publication in this journal is cited, in accordance with accepted academic practice. No use, distribution or reproduction is permitted which does not comply with these terms.
*Correspondence: Siyi Luo, bHVvc2l5aTY2NkAxMjYuY29t