- 1Tianjin Branch of CNOOC LTD., Tianjin, China
- 2China Oilfield Services Limited, Tianjin, China
To protect the marine ecological environment of Bohai Bay, the waste drilling fluid in Bohai oilfield have to be treated. In the light of the composition characteristics of Biodrill-A drilling fluid, the compounding method of the inorganic–organic flocculants was adopted to assist the flocculation and solid–fluid separation of Biodrill-A drilling fluid. Through the orthogonal test design, the main factors impacting the flocculation effect on Biodrill-A drilling fluid were found to the concentration of inorganic flocculant CaCl2 and the flocculation pH value. The optimal flocculation treatment was further obtained through single-factor optimization. Specifically, when the inorganic flocculant CaCl2 concentration was 0.9 w/v%, the organic flocculant concentration was 0.01 w/v%, the flocculation pH was 8, and the flocculation time was 7 min. Eventually, the final dewatering rate could reach 84.02%. In the optimized compound flocculants, the inorganic flocculant CaCl2 reduced the zeta potential of clay particles by electric neutralization to decrease the repulsion among particles, and the organic one could absorb and wrap the clay particles through bridging curling and electric neutralization after flocculation destabilization. Both inorganic and organic flocculants facilitated the large flocs and particles of clay particles. The field test showed that the inorganic–organic flocculants were suitable for the on-line flocculation treatment process based on centrifugal machine. The waste drilling fluid was reduced by 82%, and the water content of the separated solid phase was as low as 25.7%.
Introduction
As one of the major offshore oil and gas accumulation areas in China, Bohai Bay is a first-class sea area with slow water exchange rate and a long ecological recovery cycle once water was polluted (Peng, 2008; Zhou et al., 2012). According to relevant regulations, the water-based drilling fluid and drilling cuttings drilled in the oil layer are prohibited from being discharged directly into the ocean (GB4914, 2008). From the perspective of protecting the ecological environment of Bohai Bay, it is imperative to achieve zero discharge of drilling fluid and drilling cuttings involved in all offshore oil and gas drilling (GB4914, 2008). At present, the treatment methods of drilling fluid all over the world include injection, solidification treatment, mud-to-cement fluid (MTC), solid–liquid separation, distillation heat treatment and biodegradation treatment (Xing, 2004; Zhang, 2007; XueYuzhi and LiGongJean, 2008; Xu et al., 2009; Zou et al., 2011; Agwa et al., 2012; Xie et al., 2013; Xu and Dong, 2014; Mao et al., 2016; Jinzhi et al., 2017; Li et al., 2017; Lei et al., 2018; He et al., 2020). Among them, solid–liquid separation is more thorough for the pollution treatment, which is suitable for offshore waste drilling fluid treatment. The treatment effects of solid–liquid separation are mainly affected by flocculant, coagulant aid, sedimentation kinetics, and other factors (Eia, 2006; Zhou et al., 2007; Li et al., 2010; Wang et al., 2021).
Biodrill-A drilling fluid is one of the main drilling fluid systems currently used in Bohai oilfield. The drilling fluid has the advantages of low filtration loss, reasonable rheology, and strong inhibition performance. The drilling fluid system is extremely stable due to high polymer contents, which is not conducive to the solid–liquid separation treatment. For this reason, aiming at the Bohai oilfield waste Biodrill-A drilling fluid, this article formulated the inorganic and organic flocculant compound by orthogonal experiment method and optimized the flocculation conditions. The solid–liquid separation effect was analyzed, and the flocculation mechanism was studied. This work could provide a theoretical support for the design of Biodrill-A drilling fluid field treatment technology and equipment, and also provide an idea for harmless treatment of offshore drilling waste.
Materials and methods
Experimental materials
Biodrill-A drilling fluid was obtained from Bohai oilfield (field sampling). The inorganic flocculants included polyaluminum chloride solution (PAC-1), polyaluminum chloride granules (PAC-2), polymeric ferric chloride (PFC), polymeric ferric sulfate (PFS), polyferric chloride sulfate (SPFS), and calcium chloride (CaCl2). The organic flocculants included polyacrylamide 810 emulsion (20% cationic degree), 815 emulsion (30% cationic degree), 825 emulsion (50% cationic degree), and 830 emulsion (80% cationic degree). All the chemicals are of industrial grade. Additionally, 1 mol/L citric acid solution and 1 mol/L NaOH solution was prepared for pH regulation during flocculation treatment.
Instruments
The instruments used are the following: TA6-3 program-controlled coagulation experimental agitator (Wuhan Hengling Technology Company), PHS-3CT precision table acidity meter (Shanghai Dapu Instrument Company), LG10-2.4A high speed desktop centrifugal Machine (Beijing Times Beili Centrifuge Company), Bettersize 2000 Laser particle size distributor, Brookhaven Zeta potential analyzer, medium pressure water loss instrument (Qingdao Tongchun Petroleum Instrument Company), and ZNN-D68 Electric six-speed viscometer (Qingdao Haitongda Special Instrument Company).
Experimental methods
In the laboratory, the beaker coagulation experiment method was adopted. The program controlled coagulation agitator was used to simulate the field mixing process, and the centrifuge was used to simulate the field centrifuge device. According to the principle of destabilization and flocculation, different concentrations of flocculant solution were added to Biodrill-A drilling fluid under high-speed mixing (450 r/min). The drilling fluid was mixed evenly after 2 min, then stirred for 5 min at a low speed (50 r/min), and made to stand for 30 s. The procedure could ensure the adequate mixing of flocculants and drilling fluid without destruction of flocs. The flocculated and set drilling fluid was placed in an LG10-2.4A type high-speed bench centrifuge for 3 min at a high speed (3,000 r/min), and the supernatant liquid volume was read, and the extraction rate of Biodrill-A drilling fluid was calculated by Eq. 1.
In the formula,
f is the dewatering rate, %;
Flocculant optimization and process parameter optimization
Colloidal stability characteristics of Biodrill-A drilling fluid
The drilling fluid system of Biodrill-A formula is 0.3% NaOH + 0.2% Na2CO3 + 0.4% PF-BIOVIS + 0.12% FLOTROL + 0.4% PF-BIOCAP + 3% PF-BIOTROL + 12% NaCl + 0.2% PAC-LV + Barite (to adjust density). Drilling fluid contains a large number of viscosity enhancers, inhibitors, and lubricants, so that the solid content of surfactant in drilling fluid increases, resulting in increased difficulty in destabilizing flocculation of Biodrill-A drilling fluid. The basic performance and colloid stability characteristics of Biodrill-A drilling fluid were tested, and the experimental results are shown in Table 1. From the appearance of the waste Biodrill-A drilling fluid, the system is quite stable and looks like a viscous fluid. It is a viscous colloid with fine particles, high moisture content, and not easy to dehydrate. Biodrill-A drilling fluid has high solid content, high density, and high viscosity, and the actual solid content differs greatly from the solid content given in the formula, indicating that the on-site drilling fluid contains a lot of poor soil and is seriously polluted.
Factors affecting Biodrill-A drilling fluid flocculation
In the experiment, inorganic flocculant CaCl2 and organic flocculant 30% cationic polyacrylamide 815 emulsion were used as flocculation treatment agents, by selecting four influencing factors, including CaCl2 dosage, 815 emulsion dosage, flocculation stirring time, and flocculation pH value. Each factor corresponded to three levels, and the orthogonal test of four factors and three levels (34) was carried out. The test results are shown in Table 2.
By comparing the dewatering rates of Biodrill-A drilling fluid under different technological conditions, the highest dewatering rate was 80.97%, and the lowest one was 76.31%. Taking the dewatering rate as the optimization index, the order of influence of various factors of flocculation process on the dewatering rate of Biodrill-A drilling fluid was as follows: flocculation pH value > inorganic flocculant dosage > flocculation mixing time > organic flocculant dosage. The results showed that the main factors influencing the flocculation dewatering rate of Biodrill-A drilling fluid were pH value and inorganic flocculant dosage, and the flocculation process should be further optimized through single factor optimization experiment.
Optimization of pH value of flocculation
For Biodrill-A drilling fluid, by fixing other factors and considering the flocculation effect of drilling fluid at different pH values (4, 6, 7, 8, 9), the optimal dosage was optimized. As can be seen from Figure 1, when pH value was 8, the highest dewatering rate of the drilling fluid treated by flocculation was 83.63%, and with the increase in pH value, the overall trend of dewatering rate increased. The results indicate that alkaline conditions are conducive to solid–liquid separation of Biodrill-A drilling fluid. When the pH value was greater than 8, the concentration of OH− in the system was higher, and it was easier to cause clay particle dispersion, so that the system became stable again, the dewatering rate showed a downward trend, and the optimal pH value of flocculation was 8.
Optimization of inorganic flocculant dosage
The pH of Biodrill-A drilling fluid was adjusted to 8, and under the condition of other factors being unchanged, the optimal addition amount was optimized by considering the flocculation effect of drilling fluid under different dosages (0.9 w/v%, 1.2%, 1.5%, 1.8%, 2.1%) of CaCl2. Experimental results are shown in Figure 2. Compared with the dehydrating rate of drilling fluid, the highest dehydrating rate of drilling fluid treated by flocculation was 84.02% when the addition of inorganic flocculant CaCl2 is 0.9%. This is mainly because the addition of Ca2+ neutralizes the negative charge in the Biodrill-A drilling fluid; thus, reducing the negative charge on the surface of clay particles in the drilling fluid, the repulsive force between clay particles decreases when zeta potential decreases. When the amount of CaCl2 exceeded 0.9%, with the increase in the amount of CaCl2, Ca2+ entered the adsorption layer on the particle surface, which made some clay particles positively charged, and the potential changed from negative to positive, resulting in “recharged” clay particles. The drilling fluid was stabilized again, and the liquid extraction rate showed a downward trend; therefore, the optimized inorganic flocculant CaCl2 dosage was 0.9%.
In summary, the optimal flocculation process for Biodrill-A drilling fluid is as follows: 0.9 w/v% of inorganic flocculant CaCl2 + 0.01% of organic flocculant polyacrylamide emulsion (30% cationic degrees), mixing time of 7 min, and flocculation pH 8. The optimized dewatering rate of the drilling fluid treated by flocculation reached a high value of 84.02%.
Flocculation mechanism of Biodrill-A drilling fluid
Effect of inorganic flocculant
We selected aluminum, iron, calcium, and other inorganic flocculants (1.5%) for beaker coagulation experiment of Biodrill-A drilling fluid system. The zeta potential of the flocs was tested to explore the changing rule of particle–particle interactions after treating with different inorganic flocculants. Meanwhile, the particle size distribution of the solid phase at the bottom was measured, and the flocculation mechanism of Biodrill-A drilling fluid was analyzed. As can be seen from Table 3 and Figure 3, the zeta potential of Biodrill-A drilling fluid was relatively high, and the system was relatively stable without natural settlement stratification. The addition of inorganic flocculant reduced the zeta potential of clay particles and the stability of the system. Among them, inorganic flocculant PAC-1 and CaCl2 had the greatest influence on the zeta potential. Due to Al3+ having certain harm to the ecological environment, Ca2+ was selected as the optimal inorganic flocculant.
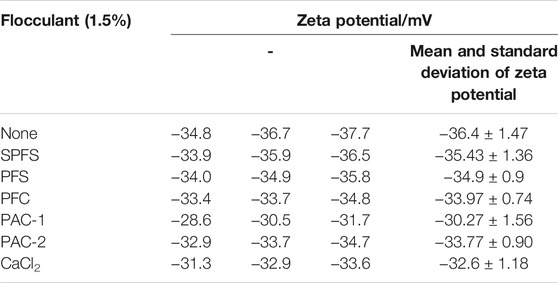
TABLE 3. Influence of the inorganic flocculant on the zeta potential and particle size distribution in Biodrill-A drilling fluid.
Effect of organic flocculant on flocculation of Biodrill-A drilling fluid
Different polyacrylamides with different cation degrees in states of emulsion and dry powder were selected for coagulation treatment on Biodrill-A drilling fluid system. The zeta potential of flocs was tested, and the particle size distribution of the solid phase at the bottom was measured, and the mechanism of destabilization of Biodrill-A drilling fluid by organic flocculant was analyzed.
The experimental results are shown in Table 4 and Figure 4. The effect of polyacrylamide emulsions with different degrees of cation on zeta potential of Biodrill-A drilling fluid system was not obvious, indicating that it was not the main factor affecting the flocculation. It can be seen from the experimental results of particle size distribution that organic flocculants significantly increased the particle size of Biodrill-A drilling fluid, which was more conducive to the flocculation settlement. With the increase in the cation degree of organic flocculant, the medium diameter (D50) became larger. The experimental results are shown in Table 5 and Figure 5. With the increase in emulsion concentration, the overall particle size gradually increased. Within a certain concentration range, with the increase in concentration, the zeta potential of the system had an overall increase trend. Therefore, for Biodrill-A drilling fluid, the amount of organic flocculant should not be too high.

TABLE 4. Influence of the organic flocculant on the zeta potential and particle size distribution in Biodrill-A drilling fluid.
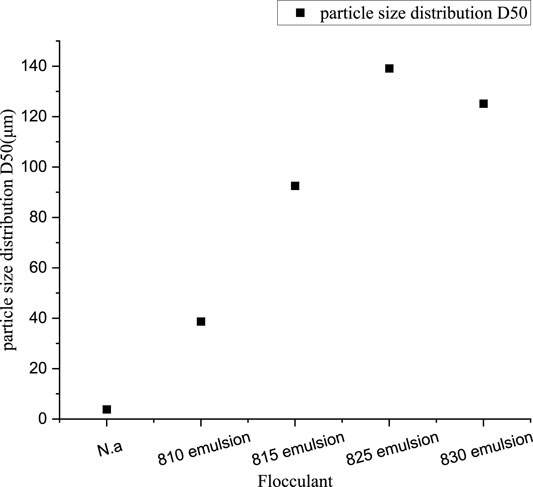
FIGURE 4. Influence of the organic flocculant on the particle size distribution in Biodrill-A drilling fluid (D50).

TABLE 5. Influence of different emulsion concentration on the zeta potential and particle size distribution in Biodrill-A drilling fluid.
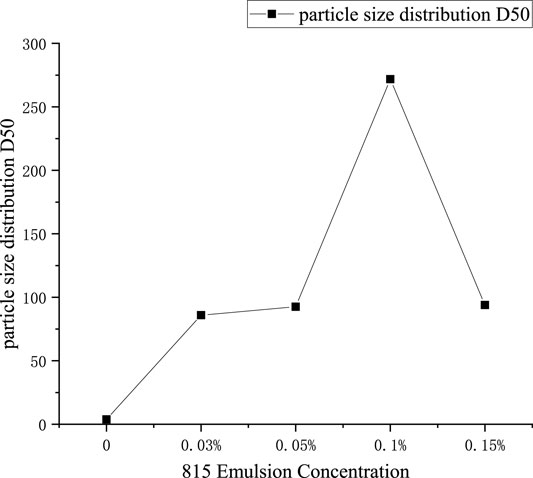
FIGURE 5. Influence of different emulsion concentrations on the particle size distribution in Biodrill-A drilling fluid (D50). (A) Biodrill-A drilling fluid. (B) Biodrill-A drilling fluid treated with organic flocculant.
The solid-phase film at the bottom was placed under a microscope for observation. As shown in Figure 6, the drilling fluid particles were connected to each other and more prone to flocculation and sedimentation. Combined with the results of zeta potential test, the organic flocculant mainly helped the system destabilize by the connection of the adsorption bridging.
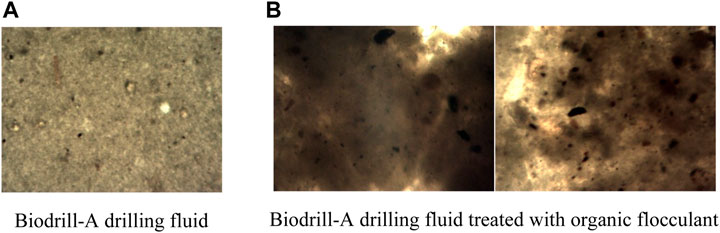
FIGURE 6. Microscopic morphology of Biodrill-A drilling fluid under the microscope after organic flocculant treatment.
Field experiment
The flocculation system and destabilization process obtained from the optimization study were tested on the H platform adjustment well of Qinhuangdao 32–6 Oilfield, Bohai Sea. The centrifugal separation process was set up in the Caofeidian Wharf warehouse. The centrifuge used was type LW550, and the separation factor was 2,772. The drilling fluid used for the H platform adjustment well is the Biodrill A system, and the waste drilling fluid is transported to Caofeidian Wharf. Before the test, the water content and retention rate of the treated waste drilling fluid were 89 and 11%, with no obvious oil layer on the surface. In addition, 100-ml samples were taken for small-scale flocculation test. The optimal dosage of inorganic and organic flocculants were determined by the speed of forming flocs and the size of flocs: 0.9% of inorganic flocculant CaCl2 + 0.01% of polyacrylamide emulsion (30% cationic degree).
Through continuous flocculation centrifuge pilot-scale test, it was found that when the waste drilling fluid was 4.2 square/h, centrifuge speed 2,400/700rpm, difference speed 29.8, while the inorganic flocculant 0.9% CaCl2 solution was added to 0.04 square hours, and the organic flocculant 0.01% polyacrylamide emulsion (30% cationic degree) was added to 0.005 square hours, the proportion of the separated liquid after centrifugation was 1.05, and the solid water content is 25.7%, which can reduce the waste drilling fluid by about 82%, and the treatment effect is good. The treatment process and the separated solid and liquid phases are shown in Figures 7 and 8.
Conclusion
1) The influence order of various factors on the dewatering rate of Biodrill-A drilling fluid during flocculation process is as follows: flocculation pH value > inorganic flocculant dosage > flocculation mixing time > organic flocculant dosage. The most influential factors are pH value and inorganic flocculant dosage.
2) The optimal flocculation conditions for Biodrill-A drilling fluid are as follows: 0.9% of inorganic flocculant CaCl2 + 0.01% of organic flocculant polyacrylamide 815 emulsion (30% cationic degree), stirring time of 7 min, flocculation pH value of 8, and the dewatering rate of drilling fluid could reach 84.02%. The mechanism of the flocculation system is that the cations in the inorganic flocculant reduce the stability of the system through electric neutralization, and the organic flocculant destabilizes the system by adsorption bridging.
3) The experimental results of H platform adjustment well in Qinhuangdao 32–6 Oilfield in Bohai Sea showed that the flocculation destabilization process optimized for Biodrill-A drilling fluid was suitable for the on-line treatment process based on centrifuge, with high reduction of waste drilling fluid and low water content of separated solid phase.
Data Availability Statement
The original contributions presented in the study are included in the article/Supplementary Material. Further inquiries can be directed to the corresponding author.
Author Contributions
MY conceptualized the study, developed the methodology, investigated the study, and wrote the original draft. ZY supervised and validated the study, wrote, reviewed, and edited the manuscript, and acquired the funding. LY supervised the study and acquired the funding. YM performed the formal analysis and acquired the resources. WD and ZX acquired the resources.
Funding
This work was financially supported by CNOOC (China) Co., Ltd. Technology Project (No.: YXKY-2019-TJ-05), the National Natural Science Foundation of China (No. 51974351; No. 51704322; Major Program, No. 51991361), and the National Science and Technology Major Project of China (No. 2016ZX05040-005).
Conflict of Interest
MY, ZY, LY, YM, and WD were employed by Tianjin Branch of CNOOC LTD. ZX was employed by China Oilfield Services Limited
Publisher’s Note
All claims expressed in this article are solely those of the authors and do not necessarily represent those of their affiliated organizations, or those of the publisher, the editors, and the reviewers. Any product that may be evaluated in this article, or claim that may be made by its manufacturer, is not guaranteed or endorsed by the publisher.
References
Agwa, A., Sadiq, R., and Leheta, H. (2012). “Offshore Drilling Waste Discharge: Egyptian Environmental Regulations,” in Paper presented at the Abu Dhabi International Petroleum Conference and Exhibition (Abu Dhabi: UAE). November. doi:10.2118/161446-MS
Eia, J. T. (2006). “Environmental Advances in Drilling Fluids, Completion Fluid and Waste Operations Applying Novel Technology for Fluid Recovery and Recycling,” in Paper presented at the SPE Russian Oil and Gas Technical Conference and Exhibition, Moscow, Russia. October. doi:10.2118/102737-MS
GB4914 (2008). Emission Concentration Limits of Pollutants from Offshore Oil Exploration and Development [S].
He, R., Zhang, Y., Suhui, , Ma, W., Wang, K., Zhang, D., et al. (2020). Research on Disposal Technology of Waste Drilling Fluid at home and Abroad. J. Shandong Chem. Industry 49, 133–134. No.384(14).
Jinzhi, Z., Long, L., Da, Y., Jiaxue, L., Shaojun, Z., Yuping, Y., et al. (2017). “Application of Comprehensive Harmless Waste Treatment Technology to Treat Drilling Cuttings in the Tian Mountain Front Block in Tarim Basin,” in Paper presented at the Abu Dhabi International Petroleum Exhibition & Conference (Abu Dhabi: UAE). November. doi:10.2118/188263-MS
Lei, Z., Chen, Q., and Zhang, P. (2018). Study on Optimization of Water-Based Drilling Fluid System in Bohai Oilfield[J]. Tianjin Sci. Tech. 045 (009), 22–2428.
Li, W., Xiang, X., and Shu, F. (2010). Study on Solid-Liquid Separation Water Coagulation Treatment of PEM Polymer Water-Based Drilling Fluid Waste in Bohai Oilfield [J]. Pet. Nat. gas Chem. industry 39 (1), 75–78.
Li, W., Zhao, X., Cai, B., Liu, J., Yan, C., Guo, W., et al. (2017). “Integrated Treatment and Disposal of Waste Drilling Fluid Onshore China: Laboratory Investigation and Process Design,” in Paper presented at the Abu Dhabi International Petroleum Exhibition & Conference (Abu Dhabi: UAE). November. doi:10.2118/188334-MS
Mao, H., Qiu, Z., Xie, B., Wang, Z., Shen, Z., and Hou, W. (2016). “Development and Application of Ultra-high Temperature Drilling Fluids in Offshore Oilfield Around Bohai Sea Bay Basin, China,” in Paper presented at the Offshore Technology Conference Asia (Malaysia: Kuala Lumpur). March. doi:10.4043/26384-MS
Peng, W. (2008). A Statistical Analysis of Hydrocarbon Pool Characteristics in Bohai sea[J]. Beijing: Offshore Oil and Gas.
Wang, K., Liu, P., Hou, X., Wang, P., Zhu, P., Hao, M., et al. (2021). "Drilling and Completion Waste Reutilization and Zero Discharge Technology Used in China Bohai Bay," in Paper presented at the SPE/IATMI Asia Pacific Oil & Gas Conference and Exhibition (Kuala Lumpur: Virtual). October doi:10.2118/205633-MS
Xie, S., Deng, H., Wang, R., Yue, Y., Wu, B., Liu, G., et al. (2013). “Useful Recycling and Safe Disposal Technology of Waste Oil Based Drilling Fluids and its Application,” in Paper presented at the International Petroleum Technology Conference, Beijing, China. March. doi:10.2523/IPTC-16623-MS
Xing, Y. (2004). Study on Solid-Liquid Separation Technology of Waste Drilling Fluid[J]. Drilling fluid and completion fluid 21 (3), 19–22.
Xu, H., Wang, B., and Qian, S. (2009). HarmLess Treatment of Oilfield Waste Drilling Fluid [J]. Drilling fluid and completion fluid 26 (4), 83–85.
Xu, L., and Dong, H. (2014). Study on Deep Purification Technology of Waste Drilling Fluid[J]. West. Prospecting Works (02), 64–68.
XueYuzhi, M. Y., and LiGongJean, (2008). Study on Treatment of marine Waste Drilling Fluid[J]. Oil Drilling Tech. 36 (5), 12–16.
Zhang, Y. (2007). Research on Harmless Treatment Technology of Waste Drilling fluid[D]. East China): China University of Petroleum.
Zhou, F., Zeng, G., and He, L. (2007). Research Progress on Solid-Liquid Separation Technology of Waste Drilling and Completion Fluid [J]. Drilling fluid and completion fluid 24 (0z1), 59–64.
Zhou, J., Yue, Q., and Yang, L. (2012). Study on Solid-Liquid Separation Technology of Waste Drilling Fluid in Offshore Oil Field[J]. J. Pet. Nat. Gas (09), 148–151.
Keywords: composite flocculation system, solid–fluid separation, biodrill-A drilling fluid, flocculation mechanism, Bohai oilfield
Citation: Ma Y, Zhang Y, Liu Y, Yue M, Wang D and Zhang X (2021) Construction and Application of Flocculation and Destability System of Biodrill-A Drilling Fluid in Bohai Oilfield. Front. Energy Res. 9:796773. doi: 10.3389/fenrg.2021.796773
Received: 17 October 2021; Accepted: 01 November 2021;
Published: 02 December 2021.
Edited by:
Xun Zhong, Yangtze University, ChinaReviewed by:
Zhixiang Cai, China University of Petroleum, ChinaXuan Li, China University of Petroleum, China
Copyright © 2021 Ma, Zhang, Liu, Yue, Wang and Zhang. This is an open-access article distributed under the terms of the Creative Commons Attribution License (CC BY). The use, distribution or reproduction in other forums is permitted, provided the original author(s) and the copyright owner(s) are credited and that the original publication in this journal is cited, in accordance with accepted academic practice. No use, distribution or reproduction is permitted which does not comply with these terms.
*Correspondence: Yingwen Ma, NTUzNDgxNjU5QHFxLmNvbQ==