- Energy and Power Engineering, School of Environment and Municipal Engineering, Qingdao University of Technology, Qingdao, China
Copper slag, an important by-product of the copper smelting process, is mainly composed of 2FeO SiO2, Fe3O4, and SiO2. Due to the sufficient metal oxides, copper slag is regard as a potential oxygen carrier (OC), which can be applied in chemical looping technology. This research proposed to use the granulated copper slag particles as precursor to produce oxygen carrier. Through this method, waste heat of the high-temperature slag can be fully recovered, eliminating the complicated copper slag pretreatment process. In this paper, the reactivity of granulated copper slag after redox calcination was studied by X-ray diffractometer (XRD) and Scanning Electron Microscope (SEM), the highest reactivity occurred at 1,000°C. In addition, the oxygen release and absorption performance of OC were tested in thermal-gravimetric (TG). According to theoretical calculations, the mass loss caused by oxygen release accounts for 70.57% of the total loss and the mass reached by 4.2% at 1,000°C in oxygen absorption experiment. The copper slag modified through calcining in redox condition was proved to be a promising oxygen carrier in chemical looping process. Furthermore, the performance research on OC also provided theoretical references for the operating paraments of OC circulating between air reactor and fuel reactor in practical chemical looping processes.
Introduction
Chemical looping technology is an emerging combustion technology which expected to achieve 100% CO2 capture efficiency with a low energy consumption (Abuelgasim et al., 2021). Oxygen carrier (OC) is used to transfer lattice oxygen between air and fuel reactors and plays an essential role in chemical looping processes. The high oxygen carrying capacity, redox activity, gas selectivity, mechanical strength as well as sintering resistance of OC determine the speed and efficiency of reactors in chemical looping conversions (Li et al., 2009). Therefore, a suitable OC has received particular interest in recent years.
There have been significant advances in metal oxide OC such as Fe, Ni, Cu, and Mn for chemical looping applications (Kang et al., 2010; Gu et al., 2015; Jiang et al., 2017). Among these materials, Fe-based OC has attracted increasing attention because of its high oxygen release capacity (Cheng et al., 2018), cost benefits (He et al., 2013; Mayer et al., 2018) as well as environmental compatibility (Luo et al., 2014; Chen et al., 2021). In addition, due to their sulfur tolerance, Fe-based oxygen carriers can react with acid gases or even solid sulfur fuels without affecting its reactivity and phase (Garcia-Labiano et al., 2014; Garcia-Labiano et al., 2016). In general, the application of Fe-based oxygen carriers is a promising research direction in the field of chemical looping technology.
Tones of oxygen carriers will be used in a commercial chemical looping process, and in this case, the cost of materials should be considered. Therefore, the low-cost Fe-based materials such as copper slag, a solid by-product from copper smelting plants, will be an attractive OC to further reduce costs. It has been estimated that about 2–3 tons of slag generated for every ton of copper produced (Alp et al., 2008). Copper slag contains large amount of heat and some valuable metals, in which the content of iron could reach to 45% (Shi et al., 2008) along with other trace elements like Cu, Ni, and Zn. From this aspect, copper slag may be regarded as a source of costless Fe-based oxygen carrier. At the same time, Cu in the copper slag may lead to a synergistic improvement in the reactivity, and SiO2, the second most abundant compound, could improve the mechanical strength as a support material (Durmaz et al., 2020). It is found the copper slag increases the content of CO2 and the carbon conversion rate in the chemical looping gasification of sewage sludge process (Fang et al., 2021). Copper slag, doped with K metal, exhibits the highest carbon conversion efficiency (Yonghao et al., 2020). In summary, copper slag is a candidate for OC in chemical looping technology.
Copper slag used as a precursor for OC preparation generally has a relatively uniform particle size distribution. However, the initial copper slags from copper smelting plants are lumpy, needing pretreatment processes like crushing and screening before being made into a precursor. In order to eliminate the complicated pretreatment process, this paper put forward to using granulated copper slags as precursor, which fully utilizes the waste heat of the high-temperature slag and provides a new idea to recover thermal energy from copper slag. In previous work, the dry granulation method has been proved to be a feasible way to produce copper slag particles with uniform particle diameter distribution (Zuo et al., 2020b; Zuo et al., 2021a).
In general, the original copper slag has a little redox activity. Modifying is necessary to improve the reactivity of OC. At present, most of studies have proposed to modify the OC by doping alkali metals (Bao et al., 2013) or metal (Gu et al., 2012; Dong et al., 2021) and have indeed improved the surface reactivity of OC. However, these modification progresses are usually cumbersome. In order to solve above issues, this paper proposed to calcinate the copper slag to modify OC. There are some studies demonstrate that calcination is a promising method to further improve the redox reactivity and mechanical properties (Gorai et al., 2003).
This work aims to study the characteristics of OC using granulated copper slag as precursor. In this paper, oxidation and reduction calcination of copper slag both took place in a pipe-typed furnace at different temperatures. Then the phase characterization and element detection of OC were measured by X-ray diffractometer (XRD). Multiple experiments were conducted to find the optimal redox calcination temperature. Additionally, in order to verify the oxygen release and absorption performance of OC, experiments were conducted by thermal-gravimetric (TG) method.
Methods
Materials
Copper slag was obtained from Jinchuan Company from Gansu province, China. The mineral phase of initial copper slag was analyzed by X-ray Diffractometry (XRD)with a scanning rate of 4°/min from range of 2θ = 10º–90º and the elements composition was tested by X-ray Fluorescence (XRF). The XRD results are shown in Figure 1, the main mineral phases of initial copper slag are fayalite, magnetite and silicon oxide. Fayalite is 2FeO·SiO2 in copper slag composed of net-like tetrahedrons. The XRF analysis are as follows: 37.3% of Fe2O3, 12.9% of SiO2, 12.2% of CaO, 6.6% of Al2O3, 12.1% of ZnO as well as some minor elements like K, Cu, Pb, and Co.
Coal is a kind of lignite from Fuxin City, Liaoning Province, China. The compositions are as follows: 35.1% of moisture, 25% of ash, 20.5% of volatile, and 19.4% of fixed carbon. Coal samples were dried at 105°C in a constant temperature oven for 2 h, then sieved into powder with a size of 0.15 mm. The coal powder was used as a reducer for the next experiments.
Copper Slag Calcination
Fe3O4/Fe2O3 species decomposed from calcinated copper slag can provide the lattice oxygen for chemical looping process (Gorai et al., 2003; Deng et al., 2019). There also were some results have indicated the redox reactivity and the initial oxygen transport capacity of calcined ilmenite were better than fresh ilmenite (Adnez et al., 2010). Therefore, calcination is a promising method to improve the lattice oxygen transfer ability and the reaction activity of copper slag. Hence, in this study, to improve the lattice oxygen transport capacity, granulated copper slag was calcinated at different temperature under redox conditions. Furthermore, the performance research on OC can provide theoretical references for the operating characteristics and paraments of OC circulating between air reactor and fuel reactor in practical chemical looping processes.
The oxidation calcination process is as follows: copper slag particles heated in a tube furnace (SHKGL-1200 horizontal high temperature furnace) in an air atmosphere at a heating rate of 10°C/min before 600°C then changed the rate to 5°C/min until the temperature reaches 900, 1,000, and 1,100°C. The above samples are marked as 900 (OX), 1,000 (OX), and 1,100 (OX), respectively.
The reduction modification process is as follows: the mixture of copper slag, coal and CaO at a mass ratio of 1:1:1 was made into 4 g pellet by a hydraulic pelletizer. CaO not only played the role of an adhesive, but also played the role of a slagging agent and had a promotion influence on the reduction reactions of copper slag by a large margin (Zuo et al., 2020b). Then heated to 800–1,000°C in N2 atmosphere with the heating rate same as the oxidation conditions to obtain 800 (RE), 900 (RE), and 1,000 (RE). Finally, the modified copper slag magnetically separated was selected as OC. Coal is a reducer of copper slag with the main contents of fixed carbon, which reduction temperature is lower than gaseous reducers H2 (Zuo et al., 2020b), and thus it decreases the heat consumption of reduction process.
Thermo Gravimetric Experiments
In order to verify the oxygen release and absorption characteristics of OC, experiments were conducted using thermo gravimetric (TG). It was turned out 1,000 (OX) and 1,000 (RE) were the most suitable oxygen carriers according to XRD analysis. With respect to the oxygen release experiment, 20 mg mixture of 1,000 (OX) and coal powder heated to 1,000°C at a heating rate of 10°C/min and kept 1 h under a N2 flow of 30 ml/min. As for oxygen absorption test, 20 mg 1,000 (RE) heated to 1,000°C at a heating rate of 10°C/min in N2 atmosphere, then N2 was switched to air and kept 2 h. As a blank control experiment, 10 mg coal was heated under the same condition. In this experiment, the degree of mass reduction can reflect the degree of oxygen release capacity of OC.
Results and Discussion
Phase Transformation of Copper Slag by Oxidation
As shown in Figure 2, fayalite was decomposed into main phases (Fe3O4, Fe2O3, and SiO2) in the air (Gyurov et al., 2011), the intensity of Fe2O3 in the calcined sample gradually increased and Fe3O4 phase decreased as the calcined temperature increased from 900°C to 1,100°C. It indicates that the transformation rule of iron phase in copper slag during calcination process is “2FeO·SiO2→Fe3O4→αFe2O3” shown in R1-R2 (Gorai et al., 2003). At a relatively low temperature (900°C), the calcined reaction R1 dominated and more fayalite was decomposed into Fe3O4 and Fe2O3 (Deng et al., 2019). At 900°C, the XRD pattern shows characteristic peaks of magnetite, accompanied by weak characteristic peaks of hematite. Most of fayalite (Fe2+) was decomposed into magnetite (Fe8/3+), indicating that the oxygen carrier has a poor oxidability under this circumstance. With the increase of temperature, the proportions of the characteristic peaks of Fe3O4 and Fe2O3 at 1,000°C are almost same because most of the Fe3O4 has been oxidized to Fe2O3 as R2 describes. At 1,100°C, although the Fe3O4 phase becomes weaker, it did not completely disappear, revealing that the copper slag has not been completely oxidized to Fe3+ at this temperature. This phenomenon may be caused by the calcination temperature which is not enough to complete the conversion of magnetite, or the oxidation of fayalite still proceed at this temperature, in other words, R1 and R2 take place simultaneously.
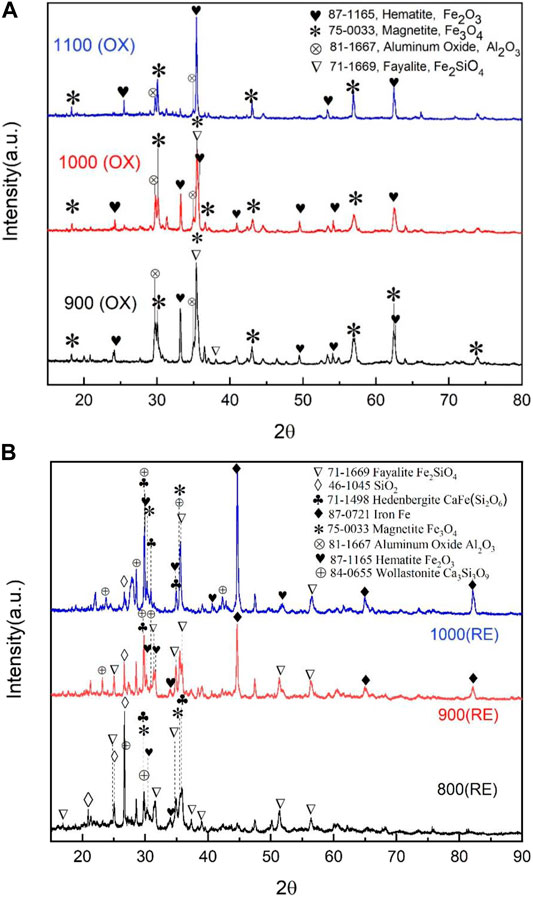
FIGURE 2. XRD patterns of oxidized and reduced copper slag. (A) XRD pattern of oxidized copper slag. (B) XRD pattern of reduced copper slag.
In summary, the higher the calcination temperature, the higher the degree of oxidation of the copper slag. However, Scanning Electron Microscope (SEM) results were shown in Figure 3, which indicated the most severe sintering occurred at 1,100°C. Based on this, it is better to control the calcined temperature at 1,000°C to ensure OC has more lattice oxygen and to avoid serious sintering in chemical looping process.
Phase Transformation of Copper Slag by Reduction
The calcined copper slag in reduction condition is shown in Figure 2. It was shown that the Fe+8/3 in Fe3O4 phase gradually disappeared, while the Fe2+ existing in CaFeSi2O6 and Ca3Si3O9 enhanced with the increasing of reduction temperature. The reduction processes are carried out step by step respectively: FeO·SiO2→FeO→Fe, Fe3O4→FeO→Fe (Yang et al., 2011). During the reduction process, coal powder as a reductant reacted with various iron oxides in the copper slag to produce CO and further generate CO2, and simultaneously yield wollastonite Ca3Si3O9 and hedenbergite CaFeSi2O6 (Yang et al., 2011). The reduction of iron oxide with C is called direct reduction (R3-R4) and with CO is called indirect reduction (R5-R6) (Bafghi et al., 1993). In the gas phase, the conversion reaction of CO2, CO, and C is a Boudouard reaction (R7) (Zuo et al., 2020a).
In this study, the Reaction Equations part of the HSC6.3 simulation software was used to confirm the initial reduction reaction temperature based on Gibbs free energy calculation. It was found that the initial temperature for R3, R4, and R6 are approximately 800, 700, and 790°C. If temperature higher than 800°C, these reactions occur spontaneously, moreover, the reduction reactions of C are easier than the reduction reactions of CO for iron oxide in solid copper slag. However, The Gibbs free energy for reduction reactions of CO and 2FeO·SiO2 can’t take place spontaneously. In summary, the reduction temperature of C and copper slag should be set above 800°C. The above reactions are all endothermic reactions, which demonstrates that improving the temperature will promote the reduction reaction. Therefore, the copper slag calcined at 1,000°C has higher reduction degree and is more suitable as an oxygen carrier to a certain extent. This simulation conclusion is consistent with the results shown in the XRD plot.
The XRD results Figure 2 show that in addition to the three main phases of 2FeO·SiO2, Fe3O4, and SiO2, there is a weaker CaFeSi2O6 characteristic peak at a reduction temperature of 800°C. Since the CaFeSi2O6 is a silicate composed of Ca2+, Fe2+ and Si2O6, Fe2+ has relatively strong reducibility. To a certain extent, the appearance of characteristic peak of CaFeSi2O6 indicates the improvement of reduction degree. When the reduction temperature increased to 900 °C, the diffraction peaks of 2FeO·SiO2 and Fe3O4 gradually weakened and decomposed into the characteristic peaks of FeO and Fe, there was simultaneously a large amount of 2FeO·SiO2 in the oxygen carrier. Until the temperature rose to 1,000°C, almost all the iron phase was converted to iron metal.
At 1,000°C, the oxygen carrier has the deepest reduction degree and excellent reduction performance, which provides theoretical references for the operating characteristics and paraments of OC.
The Analysis of Thermal-Gravimetric
To further test the release and absorption oxygen performance of the calcined copper slag, two experiments were conducted by TG method:
1) The oxygen release characteristics of 1,000 (OX) was tested in a N2 atmosphere.
2) The oxygen absorption of 1,000 (RE) was tested in an air atmosphere.
The TG curve of 1,000 (OX) oxygen release is shown in Figure 4. There are two obvious weight loss stages, 25–600 and 600–1,000°C. The stage 1 is mainly caused by the pyrolysis of coal powder. In the stage 2, pyrolysis of coal powder is basically completed and the reduction reaction between the coal powder and 1,000 (OX) lead the mass loss. It was calculated that the mass loss caused by the oxygen release process accounts for 70.57% of the total loss. The curve of oxygen release as shown in Figure 3, the surface lattice oxygen of OC was captured by C element in the pulverized coal to produce CO/CO2, meanwhile the oxygen vacancies generated by the outer lattice oxygen enforce the inner lattice oxygen move to the surface quickly to provide more lattice oxygen and to achieve the purpose of releasing oxygen (Zeng et al., 2012). Thus, the degree of mass loss reflects the reduction degree of oxygen release performance. In general, this curve has two vividly mass loss region, the result is consistent with Zuo (Zuo et al., 2021b). In first region, pyrolysis reactions of coal take place; The second region is the oxygen release reaction of OC, taking place at 600–1,000°C, which is the main reaction stage causes the loss of mass. Moreover, it is calculated that the mass loss caused by the oxygen release process accounts for 70.57% of the total loss. From this aspect, the granulated copper slag after calcination has a good oxygen release performance.
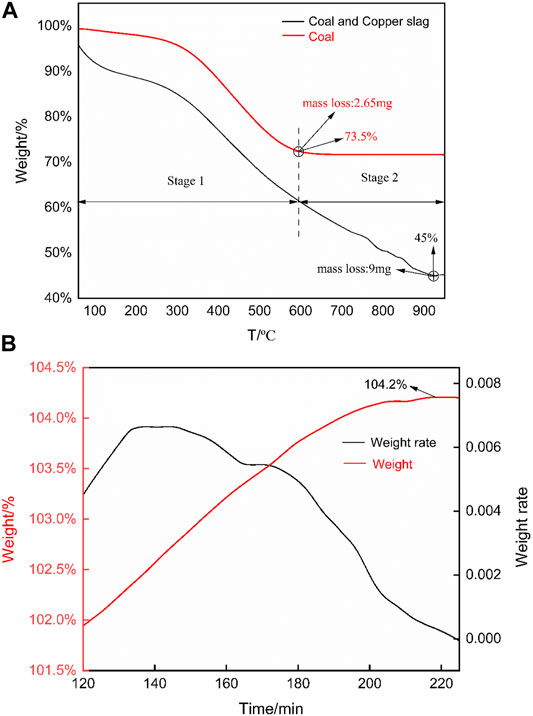
FIGURE 4. TG curves of oxygen release and absorption. (A) TG curve of oxygen release. (B) TG curve of oxygen absorption.
Figure 4 shows the oxygen absorption process of 1,000 (RE). The oxygen absorption is an isothermal process. OC was heated in an inert gas N2 before 120 min, then N2 was switched to air and kept 2 h to accomplish oxygen absorption. In other words, the actual oxygen absorption process took place between 120 and 240 min, so the x-axis of TG curve starts from 120. The longer the oxidation process, the heavier the OC, eventually the mass of OC increased by 4.2%. This phenomenon indicates the OC after redox calcination has an ability to absorb oxygen.
In summary, granulated copper slag as a precursor makes full use of waste heat resources. OC calcinated at 1,000°C has the best redox reactivity and has a fine ability of oxygen release and absorption. This study provided a reference for the operating temperature of OC in the chemical looping technology, as well as offered a new idea for the comprehensive utilization of metal oxide-containing metallurgical slag.
Conclusions
This paper proposed the preparation of oxygen carriers using granulated copper slag as a precursor. and the main findings have been summarized below:
1) Copper slag calcined at different temperatures was tested through XRD and TG method to analyze the iron phase transition mechanism and the lattice oxygen transport performance of the oxygen carrier. The oxygen carrier showed excellent performance at 1,000°C.
2) There were obvious quality changes of OC during the TG experiment indicating the fine lattice oxygen transfer ability. At the same time, this research also provided theoretical temperature range of OC circulating between two reactors in practical chemical looping applications.
Data Availability Statement
The original contributions presented in the study are included in the article/Supplementary Material, further inquiries can be directed to the corresponding authors.
Author Contributions
ZZ proposed the concept of the research; SL designed the experiment; YF contributed significantly to analysis and article writting; QY performed the experiment; DR and LH helped performing the analysis with constructive discussions.
Funding
This research has been supported by the Natural Science Foundation of China (52104397), the Natural Science Foundation of Shandong Province (ZR2020QE150, ZR2019MEE015).
Conflict of Interest
The authors declare that the research was conducted in the absence of any commercial or financial relationships that could be construed as a potential conflict of interest.
Publisher’s Note
All claims expressed in this article are solely those of the authors and do not necessarily represent those of their affiliated organizations, or those of the publisher, the editors and the reviewers. Any product that may be evaluated in this article, or claim that may be made by its manufacturer, is not guaranteed or endorsed by the publisher.
References
Abuelgasim, S., Wang, W., and Abdalazeez, A. (2021). A Brief Review for Chemical Looping Combustion as a Promising CO2 Capture Technology: Fundamentals and Progress. Sci. Total Environ. 764, 142892. doi:10.1016/j.scitotenv.2020.142892
Adánez, J., Cuadrat, A., Abad, A., Gayán, P., de Diego, L. F., and García-Labiano, F. (2010). Ilmenite Activation during Consecutive Redox Cycles in Chemical-Looping Combustion. Energy Fuels 24 (2), 1402–1413. doi:10.1021/ef900856d
Alp, İ., Deveci, H., and Süngün, H. (2008). Utilization of Flotation Wastes of Copper Slag as Raw Material in Cement Production. J. Hazard. Mater. 159 (2-3), 390–395. doi:10.1016/j.jhazmat.2008.02.056
Bafghi, M. S., Fukuda, M., Ito, Y., Yamada, S., and Sano, M. (1993). Effect of CO Gas Formation on Reduction Rate of Iron Oxide in Molten Slag by Graphite. ISIJ Int. 33 (11), 1125–1130. doi:10.2355/isijinternational.33.1125
Bao, J., Li, Z., and Cai, N. (2013). Promoting the Reduction Reactivity of Ilmenite by Introducing Foreign Ions in Chemical Looping Combustion. Ind. Eng. Chem. Res. 52 (18), 6119–6128. doi:10.1021/ie400237p
Chen, W-H., Chem, K-H., Ubando, , A. T., Lee, W-J., and Chio, M-H. (2021). Redox Degrees of Iron-Based Oxygen Carriers in Cyclic Chemical Looping Combustion Using Thermodynamic Analysis. Chem. Eng. J. 426, 130834. doi:10.1016/j.cej.2021.130834
Cheng, Z., Qin, L., Fan, J. A., and Fan, L.-S. (2018). New Insight into the Development of Oxygen Carrier Materials for Chemical Looping Systems. Engineering 4 (3), 343–351. doi:10.1016/j.eng.2018.05.002
Deng, Z., Huang, Z., He, F., Zheng, A., Wei, G., Meng, J., et al. (2019). Evaluation of Calcined Copper Slag as an Oxygen Carrier for Chemical Looping Gasification of Sewage Sludge. Int. J. Hydrogen Energ. 44 (33), 17823–17834. doi:10.1016/j.ijhydene.2019.05.039
Dong, N., Huo, R., Liu, M., Deng, L., Deng, Z., Chang, G., et al. (2021). Chemical Looping Gasification of Sewage Sludge Using Copper Slag Modified by NiO as an Oxygen Carrier. Chin. J. Chem. Eng. 29, 335–343. doi:10.1016/j.cjche.2020.09.007
Durmaz, M., Dilmaç, N., and Dilmaç, Ö. F. (2020). Evaluation of Performance of Copper Converter Slag as Oxygen Carrier in Chemical-Looping Combustion (CLC). Energy 196, 117055. doi:10.1016/j.energy.2020.117055
Fang, S., Deng, Z., Lin, Y., Huang, Z., Ding, L., Deng, L., et al. (2021). Investigation of the Nitrogen Migration Characteristics in Sewage Sludge during Chemical Looping Gasification. Energy 216, 119247. doi:10.1016/j.energy.2020.119247
García-Labiano, F., de Diego, L. F., Gayán, P., Abad, A., Cabello, A., Adánez, J., et al. (2014). Energy Exploitation of Acid Gas with High H2S Content by Means of a Chemical Looping Combustion System. Appl. Energ. 136, 242–249. doi:10.1016/j.apenergy.2014.09.041
García-Labiano, F., de Diego, L. F., Cabello, A., Gayán, P., Abad, A., Adánez, J., et al. (2016). Sulphuric Acid Production via Chemical Looping Combustion of Elemental sulphur. Appl. Energ. 178, 736–745. doi:10.1016/j.apenergy.2016.06.110
Gorai, B., Jana, R. K., and Premchand, (2003). Characteristics and Utilisation of Copper Slag—A Review. Resour. Conserv. Recycl. 39 (4), 299–313. doi:10.1016/s0921-3449(02)00171-4
Gu, H., Shen, L., Xiao, J., Zhang, S., Song, T., and Chen, D. (2012). Iron Ore as Oxygen Carrier Improved with Potassium for Chemical Looping Combustion of Anthracite Coal. Combust. Flame 159 (7), 2480–2490. doi:10.1016/j.combustflame.2012.03.013
Gu, H., Shen, L., Zhong, Z., Zhou, Y., Liu, W., Niu, X., et al. (2015). Interaction between Biomass Ash and Iron Ore Oxygen Carrier during Chemical Looping Combustion. Chem. Eng. J. 277, 70–78. doi:10.1016/j.cej.2015.04.105
Gyurov, S., Kostova, Y., Klitcheva, G., and Ilinkina, A. (2011). Thermal Decomposition of Pyrometallurgical Copper Slag by Oxidation in Synthetic Air. Waste Manag. Res. 29 (2), 157–164. doi:10.1177/0734242X10379495
He, F., Galinsky, N., and Li, F. (2013). Chemical Looping Gasification of Solid Fuels Using Bimetallic Oxygen Carrier Particles - Feasibility Assessment and Process Simulations. Int. J. Hydrogen Energ. 38 (19), 7839–7854. doi:10.1016/j.ijhydene.2013.04.054
Jiang, S., Shen, L., Wu, J., Yan, J., and Song, T. (2017). The Investigations of Hematite-CuO Oxygen Carrier in Chemical Looping Combustion. Chem. Eng. J. 317, 132–142. doi:10.1016/j.cej.2017.01.091
Kang, K.-S., Kim, C.-H., Bae, K.-K., Cho, W.-C., Kim, S.-H., and Park, C.-S. (2010). Oxygen-carrier Selection and thermal Analysis of the Chemical-Looping Process for Hydrogen Production. Int. J. Hydrogen Energ. 35 (22), 12246–12254. doi:10.1016/j.ijhydene.2010.08.043
Li, F., Kim, H. R., Sridhar, D., Wang, F., Zeng, L., Chen, J., et al. (2009). Syngas Chemical Looping Gasification Process: Oxygen Carrier Particle Selection and Performance. Energy Fuels 23 (8), 4182–4189. doi:10.1021/ef900236x
Luo, M., Wang, S., Wang, L., and Lv, M. (2014). Reduction Kinetics of Iron-Based Oxygen Carriers Using Methane for Chemical-Looping Combustion. J. Power Sourc. 270, 434–440. doi:10.1016/j.jpowsour.2014.07.100
Mayer, K., Schanz, E., Pröll, T., and Hofbauer, H. (2018). Performance of an Iron Based Oxygen Carrier in a 120 kWth Chemical Looping Combustion Pilot Plant. Fuel 217, 561–569. doi:10.1016/j.fuel.2018.01.014
Shi, C., Meyer, C., and Behnood, A. (2008). Utilization of Copper Slag in Cement and Concrete. Resour. Conserv. Recycl. 52 (10), 1115–1120. doi:10.1016/j.resconrec.2008.06.008
Yang, H., Jing, L., and Dang, C. (2011). Direct Reduction and Magnetic Separation Recovery of Iron Components in Copper Slag. Chin. J. Nonferrous Met. 21 (05), 1165–1170. doi:10.19476/j.ysxb.1004.0609.2011.05.034
Yonghao, W., Ming, L., Nanhang, D., Yan, L., Guozhang, C., Guoqiang, W., et al. (2020). Chemical Looping Gasification of High Nitrogen wood Waste Using a Copper Slag Oxygen Carrier Modified by Alkali and Alkaline Earth Metals. Chem. Eng. J. 410, 128344. (prepublish). doi:10.1016/j.cej.2020.128344
Zeng, L., Kathe, M. V., Chung, E. Y., and Fan, L.-S. (2012). Some Remarks on Direct Solid Fuel Combustion Using Chemical Looping Processes. Curr. Opin. Chem. Eng. 1 (3), 290–295. doi:10.1016/j.coche.2012.05.001
Zuo, Z., Luo, S., Zhang, J., Yu, Q., Guo, J., Bi, X., et al. (2020a). C and CO Reduction Proportional Fraction with Copper Slag by a Phase Equilibrium Calculation Model (PECM). Energy Fuels 34 (1), 698–708. doi:10.1021/acs.energyfuels.9b03384
Zuo, Z., Yu, Q., Luo, S., Zhang, J., and Zhou, E. (2020b). Effects of CaO on Two-step Reduction Characteristics of Copper Slag Using Biochar as Reducer: Thermodynamic and Kinetics. Energy Fuels 34 (1), 491–500. doi:10.1021/acs.energyfuels.9b03274
Zuo, Z., Feng, Y., Li, X., Luo, S., Ma, J., Sun, H., et al. (2021a). Thermal-Chemical Conversion of Sewage Sludge Based on Waste Heat Cascade Recovery of Copper Slag: Mass and Energy Analysis. Energy 235, 121327. doi:10.1016/j.energy.2021.121327
Keywords: copper slag, granulation, oxygen carrier, calcination, redox
Citation: Feng Y, Yang Q, Zuo Z, Luo S, Ren D and Lin H (2021) Study on Preparation of Oxygen Carrier Using Copper Slag as Precursor. Front. Energy Res. 9:781914. doi: 10.3389/fenrg.2021.781914
Received: 23 September 2021; Accepted: 22 October 2021;
Published: 22 November 2021.
Edited by:
Chuang Wen, University of Exeter, United KingdomReviewed by:
Roman Jaskulski, Warsaw University of Technology, PolandDuygu Yilmaz, Chalmers University of Technology, Sweden
Copyright © 2021 Feng, Yang, Zuo, Luo, Ren and Lin. This is an open-access article distributed under the terms of the Creative Commons Attribution License (CC BY). The use, distribution or reproduction in other forums is permitted, provided the original author(s) and the copyright owner(s) are credited and that the original publication in this journal is cited, in accordance with accepted academic practice. No use, distribution or reproduction is permitted which does not comply with these terms.
*Correspondence: Zongliang Zuo, enVvem9uZ2xpYW5nbmV1QDE2My5jb20=; Siyi Luo, bHVvc2l5aTY2NkAxMjYuY29t