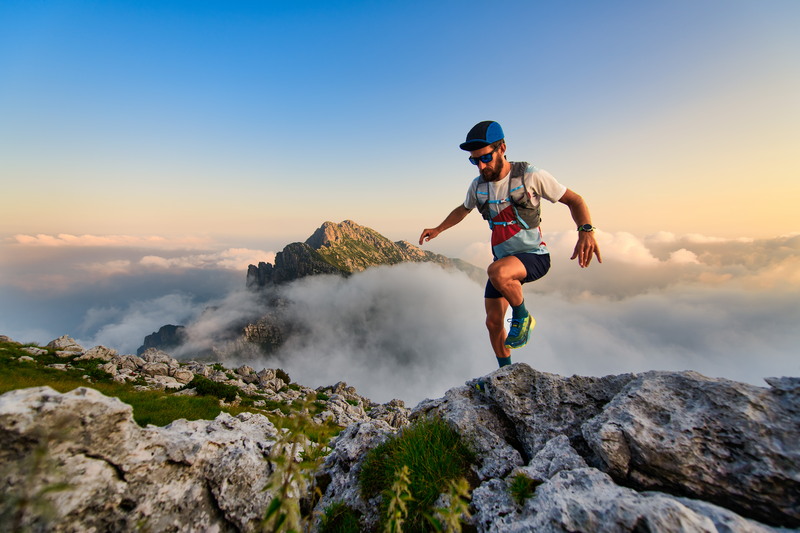
94% of researchers rate our articles as excellent or good
Learn more about the work of our research integrity team to safeguard the quality of each article we publish.
Find out more
REVIEW article
Front. Energy Res. , 01 November 2021
Sec. Advanced Clean Fuel Technologies
Volume 9 - 2021 | https://doi.org/10.3389/fenrg.2021.779476
This article is part of the Research Topic Pollutant Emission Control in Energy Conversion Process View all 12 articles
Spent carbon anode (SCA) is a dangerous solid waste that is continuously discharged from the aluminum electrolysis industry and has a large number of valuable resources and a high risk of environmental pollution. Its safe disposal and resource utilization have become a resource and environmental problem that must be solved urgently. Current methods for SCA disposal include flotation, vacuum metallurgy, physical activation, roasting, bubbling fluidized bed combustion, alkali fusion, alkali leaching, and chemical leaching combined with high temperature graphitization. In this paper, the material composition, resource properties, and environmental risks of SCA are discussed. Working principle, treatment process, advantages and disadvantages of the above methods are also briefly described and compared. Results showed that flotation is the safest disposal and comprehensive utilization technology that is suitable for characteristics of SCA raw materials and has the most large-scale application potential. In addition, characteristics of SCA recovery products are correlated to the recycling of aluminum reduction cells. This technology can alleviate the shortage of high-quality petroleum coke resources in China’s carbon material industry and the high cost of raw materials in aluminum electrolysis industry.
Hall–Heroult method is currently used to produce aluminum. High-purity primary aluminum is produced by electrolysis with aluminum electrolysis cell as the carrier, cryolite (Na3AlF6) as the reaction solvent, and alumina (Al2O3) as the raw material. As a core component, prebaked anode drives the electric current into the electrolytic cell and participates in electrochemical reaction (Yang et al., 2016). However, reactivity differs between aggregate (calcined petroleum coke) and binder coking product (pitch coke), thus leading to the selective oxidation and uneven combustion of prebaked anode during production. In addition, the prebaked anode is washed and eroded by high temperature aluminum liquid and molten electrolytes. Hence, some carbon particles fall off from the prebaked anode, enter the electrolyte, and form spent carbon anode (SCA) (Li et al., 2015; TU, 2017; Hou et al., 2020). When excessive SCA accumulates on the surface of molten electrolytes, the resistance of aluminum reduction cell increases, and the electric energy is excessively consumed (Zhang, 2013; Bai, 2020). SCA can also hinder Al2O3 dissolution and induce the anode effect (GuoHou et al., 2019;GuoHou et al., 2020) and therefore must be salvaged regularly to ensure the normal operation of the aluminum reduction cell. As a result, SCA has become an unavoidable solid waste that is continuously discharged from the aluminum electrolysis industry.
Calcined petroleum coke has a remarkable porous structure and can be used as the prebaked anode aggregate. This material can provide sufficient adsorption and permeation channels for molten electrolytes, resulting in a large amount of electrolytes in the SCA (Zhao and Yang, 2013; Liu and Wu, 2020). When SCA piles up in the open air or is buried unprotected, soluble fluoride with strong solubility and permeability gradually migrates to nearby soil and water sources along with rainwater, thus seriously threatening the ecological balance. Therefore, the SCA produced during electrolytic aluminum production has been classified as toxic hazardous waste (code: 321-025-48, hazardous characteristics: T) in the National List of Hazardous Wastes (2021 Edition). This waste is strictly prohibited to be discarded or stored in the open air and must be harmlessly disposed within the enterprise or by entrusting a third-party institution with hazardous waste treatment qualification.
With the continuous development of electrolytic aluminum industry, the discharge of SCA and the scale of harmless disposal have increased annually. As shown in Figure 1, the growth rate of China’s primary aluminum output was approximately 129.80% from 2010 to 2020 (Wang, 2021). For every 5–15 kg of SCA (Liu et al., 2021) produced per ton of aluminum, its discharge amount exceeded 35,000 tons in 2020. SCA is composed of a large number of high-quality carbon materials and high-value electrolyte components and therefore has high recycling value (Zhang et al., 2018). The safe disposal and comprehensive utilization of SCA is conducive to promoting the green and sustainable development of the aluminum electrolysis industry.
SCA usually comprises 60–70% electrolyte components and 30–40% carbon materials (Zhao et al., 2015; Wei, 2018; Liu, 2020). Table 1 shows the main material components, resource attributes, and environmental risks of SCA.
The safe disposal and comprehensive utilization of SCA has been a major concern of the aluminum electrolysis industry. According to their principle of action, existing technologies for the safe disposal and comprehensive utilization of SCA can be grouped into physical separation and chemical treatment. Physical separation methods include flotation, vacuum metallurgy, and physical activation. Chemical treatment processes involve roasting, bubbling fluidized bed combustion, alkali fusion, and alkali leaching. The co-treatment involving chemical treatment and physical separation includes alkali–acid leaching and high temperature graphitization.
Flotation is currently the most mature and widely used disposal technology of SCA. Its working principle is based on the hydrophobic difference between carbon materials (hydrophobic) and electrolyte components (hydrophilic). With the assistance of flotation reagents, carbon materials floating up with bubbles are collected, and electrolytes are discharged from the bottom of the flotation machine. Thus, the preliminary separation of carbon and electrolyte in SCA is realized. The main processes of this method include crushing, grinding, classification, flotation, and drying (Wang et al., 2019) as shown in Figure 2.
Mei et al. (2016) conducted an experimental study on recovering SCA through flotation. Under the optimized parameters of pulp concentration of 25–33%, SCA size of <200 mesh (<74 μm) accounting for 90%, and flotation machine speed of 1800 r/min, carbon materials with a carbon content of 94.59% were recovered, and the carbon content of electrolyte concentrate decreased from 4.10 to 1.01%. In addition, the flotation effect of SCA was improved through process optimization. Zhou et al. (2019) investigated the effect of flotation conditions on the separation of carbon and electrolytes in SCA. The optimal experimental conditions were obtained by single factor experiment. Carbon materials with a carbon content of 85.23% were retrieved with recovery rate of 81.55% under the optimal flotation parameters of SCA size of 120–140 mesh (106–125 μm), pulp concentration of 30%, stirring speed of 1,600 r/min, and aeration rate of 0.30 m3/h (Li et al., 2021). explored the influence of conventional process conditions (size of SCA, stirring speed, and pulp concentration) on the flotation effect of SCA and studied the effect of pH regulator and collector adding mode. The results showed that pH regulator has minimal influence on SCA flotation, and the flotation effect was remarkably improved through the batch addition of flotation reagents. Finally, the following optimal flotation parameters were obtained: particle size of <200 mesh (<74 μm) accounting for 70%, stirring speed of 1700 r/min, pulp concentration of 25%, collectors added in five batches, and mixing time of 5 min. The carbon content of SCA was increased from 23.30 to 75.60%, and the carbon recovery rate reached 86.90%.
Flotation has the advantages of large treatment capacity per unit time, low cost, simple operation, good working environment, and stable quality of recycled products. However, SCA is usually composed of many components and is infiltrated by electrolytes for a long time, resulting in the complex distribution state among the components. This method also has some disadvantages such as poor separation effect of valuable components, low purity of recovered products (carbon materials and electrolytes), and a large amount of produced fluorine-containing wastewater. Most of the above studies reported that the flotation effect of SCA can be enhanced by optimizing the flotation parameters as shown in Table 2. However, the recycling of recycled products and the safe disposal of flotation wastewater are rarely discussed. Given the characteristics of SCA, raw materials should be pretreated in advance to realize the enhanced separation between carbon materials and electrolytes. New flotation reagent systems such as reagent emulsification and reagent compounding should also be constructed.
Vacuum metallurgy utilizes the volatility difference of valuable components in SCA. The volatile electrolytes are removed from the SCA under high temperature and vacuum conditions to separate the carbon materials and electrolyte components (Luo et al., 2020). The process of SCA treatment via vacuum metallurgy is shown in Figure 3.
Chai et al. (2016) explored the effect of vacuum degree, reaction temperature, SCA particle size, and reaction time on the separation of carbon materials and electrolytes in SCA. Under the optimal parameters of vacuum degree of 5 Pa, reaction temperature of 950°C, raw material size of 0.50 mm, and reaction time of 4 h, the separation rate of electrolytes reached 83%, and the carbon content of SCA was improved from 36 to 74%.
Vacuum metallurgy is used to directly recover high purity electrolyte components (such as Na3AlF6, AlF3, LiF, and KF). However, only carbon materials with low carbon content are recovered because SCA has abundant Al2O3 (boiling point: 2,980°C) and CaF2 (boiling point: 2,500°C), which are stable and difficult to volatilize. In addition, the high treatment temperature and long reaction time for this method are accompanied by high energy consumption and equipment loss, which hinder its industrial application.
Physical activation is used to treat carbon-rich materials by activating media (such as water vapor and CO2) to form porous carbon materials (Geng et al., 2014; Yi et al., 2008). The process of SCA treatment via CO2 activation is shown in Figure 4.
(Liu et al., 2021) used SCA as raw material and CO2 as activation medium to prepare porous carbon materials. The effects of CO2 flow rate, activation temperature, and activation time on the properties of porous carbon were investigated through single factor experiments. The results showed the best adsorption performance of the porous carbon materials (79.75 mg/g) at CO2 flow rate of 200 cc, activation temperature of 650°C, and activation time of 2 h. TEM, Raman, XRD and other analysis results showed that the porous carbon materials are mostly composed of mesopores and macropores. Their crystallization and graphitization degree were remarkably improved.
CO2 activation for SCA treatment is a simple process, and the prepared porous carbon materials show pore structure and good adsorption performance. The application channels and utilization value of SCA are broadened. However, this method has high requirements for the carbon content of raw carbon; hence, the SCA must be deeply pretreated.
Roasting completely burns the carbon materials in SCA at high temperature while keeping the electrolyte components stable (non-volatile and non-decomposed). Only the electrolytes with high purity are recovered (Chen, 2011). The main reaction in roasting is shown in Eq. 1. Its process mainly includes grinding, roasting, and cooling as shown in Figure 5.
Chen et al. (2009) employed roasting for SCA treatment and analyzed the influence of process parameters on roasting reaction efficiency. Electrolytes with content above 99% were recovered under the optimal parameters of roasting temperature of 760°C, addition of combustion improver of 12%, addition of dispersant of 15%, and rotary kiln rotating speed of 1 rpm. Meanwhile, the roasting reaction efficiency of SCA is as high as 95.31%.
Roasting is used to recover high-purity electrolytes that can be directly returned to the aluminum reduction cell for recycling. However, research and demonstration on the suitability of the characteristics of the recovered electrolytes for reuse in aluminum electrolysis are lacking. During this treatment, a large number of high-quality petroleum cokes are burned, and CO2 is released. These problems bring pressure to environmental protection. In addition, its high energy consumption does not meet the requirements of energy conservation and emission reduction.
Bubbling fluidized bed combustion is used to roast SCA in suspension. The electrolyte components in SCA are effectively recovered by burning the carbon materials (Luo et al., 2019). The process of SCA treatment via bubbling fluidized bed is shown in Figure 6.
Zhou et al. (2014) investigated the combustion characteristics of SCA through differential thermal analysis and the influences of technical parameters such as particle size of SCA, initial bed height, air distribution plate structure, and fluidization velocity on the fluidization of SCA. SCA samples were roasted under the optimal parameters of bed diameter of 100 mm, opening rate of air distribution plate of 1.80%, fluidization velocity of 0.40 mm/s, SCA size of 0.40 mm, and roasting temperature of 565–734°C. However, the expected effect was not achieved, and only 66.30% of the carbon materials were removed.
In theory, bubbling fluidized bed combustion has better gas–solid contact effect and higher combustion efficiency and intensity than conventional roasting. However, the melting of Na5Al3F14 with low melting point may lead to the sintering of SCA. As a result, its distribution in the fluidized bed is worsened, thereby reducing the reaction rate and limiting the removal efficiency of carbon materials.
Alkali fusion removes electrolyte components by molten alkaline reagents such as NaOH and Na2CO3. Carbon materials with high content are recovered after water leaching (Wang et al., 2016; Li et al., 2015). The alkaline substance changes from solid state to molten state when the roasting temperature is higher than its melting point. Therefore, the reaction activity and mass transfer conditions with the electrolyte components in the SCA are remarkably improved (Shoppert et al., 2019).
Yang et al. (2020) treated SCA by using NaOH as an additive. The effects of alkali fusion temperature, reaction time, and alkali–material mass ratio on the carbon content of recovered carbon materials were investigated through single factor experiments. Parameters were optimized through orthogonal experiment. Carbon materials with a carbon content of 99.10% were recovered under the optimized parameters of alkali fusion temperature of 600°C, reaction time of 6.50 h, mass ratio of alkali to material of 5.5:1, and acid leaching. The recovered carbon materials had a large reversible capacity (286.80 mAh·g−1) at 1 C and have a good capacity attenuation rate (the attenuation rate of each cycle in 500 cycles is 0.03%) and thus can be used as anode material of lithium-ion batteries. This finding provides a theoretical basis for the high-value utilization of SCA. The process of SCA treatment via NaOH alkali fusion is shown in Figure 7. Tian et al. (2021) used recovered SCA (carbon content >99.00%) and nano-silicon powder as raw materials to prepare Si/C composite materials by mechanical ball milling for lithium-ion battery anode. The Si/C composites exhibited good electrochemical properties under the ball milling speed of 500 r/min, mass ratio of ball to material of 5:1, and ball milling time of 25 h. The specific discharge capacity of Si/C composites reached 382.40 mAh·g−1 after 100 cycles at current density of 120 mA·g−1. This work provides a new idea for the high-value utilization of valuable components in SCA.
Liang et al. (2021) treated SCA with Na2CO3 as an additive. Na2CO3 almost completely reacted with Al2O3, Na3AlF6, and Na5Al3F14 in SCA under the parameters of mass ratio of alkali to SCC of 2.5:1, alkali fusion temperature of 950°C, and reaction time of 2 h. Carbon materials with a carbon content of 89.00% were recovered after repeated water leaching, and Na3AlF6 was prepared by introducing CO2 into the leachate. The process of SCA treatment via Na2CO3 alkali fusion is shown in Figure 8.
Alkali fusion can realize the efficient separation of carbon materials and electrolyte components in SCA. Combined with acid leaching, carbon materials with a carbon content >99.00% and high-value application potential can be recovered. However, given that SCA is composed of a large amount of electrolyte components, this process consumes a large amount of alkaline reagents with extremely high economic cost. A summary of the optimal parameters for SCA treatment with different alkaline agents is shown in Table 3.
Alkali leaching removes the electrolyte components reacting with alkaline solution to recover carbon materials (Yuan et al., 2018; Yuan et al., 2018; Yuan et al., 2018). The specific process is shown in Figure 9.
Li et al. (2021) used NaOH solution to treat SCA and recover the carbon materials. Carbon materials with a carbon content of 98.00% were recovered under the parameters of leaching temperature of 110°C, NaOH solution concentration of 15%, solvent-to-solid ratio of 10:1, leaching time of 120 min, and the NaOH solution dissolved the Na3AlF6 and Al2O3 in SCA. The main chemical reaction equations are shown in Formulas Eqs 2–3.
According to the composition of alkali leaching filtrate (Na+, F−, and AlO2−), Na3AlF6 and Na2CO3 were prepared by introducing CO2 into leachate. The related chemical reaction equations are shown in Formulas Eqs 4–5.
Alkali leaching can realize the complete quantitative recovery of valuable components (carbon materials and electrolyte components) in SCA. When combined with carbonation, this method can generate Na2CO3 and Na3AlF6. Alkali leaching is similar to a closed-loop treatment and has the technical advantages of low energy consumption and high product yield. However, the process is complex and consumes a large amount of alkaline reagents. In addition, CaF2 not be removed by alkali leaching, thus limiting the high-value utilization of recycled carbon materials.
Wang (2021) conducted a co-treatment involving alkali–acid leaching and high temperature graphitization to treat SCA. Na3AlF6 and Al2O3 in SCA were dissolved into the leachate by NaOH solution. The carbon content of SCA was further increased by acid leaching, aiming at removing CaF2 from SCA. The main reaction in acid leaching is shown in formula Eq. 6. Accordingly, Carbon materials with a carbon content of 93.15% were recovered by alkali–acid leaching.
Afterwards, the carbon content of carbon materials was increased from 93.15 to 99.90% by high temperature graphitization (2,800°C). In the process of graphitization, the carbon in SCA undoubtedly converted from disordered structure to graphite crystal structure by thermal activation. The process of SCA treatment via alkali–acid leaching and high temperature graphitization is shown in Figure 10.
Chemical leaching combined with high temperature graphitization can produce carbon materials with high purity and graphitization degree. The application channels and utilization value of carbon materials in SCA are broadened. Nonetheless, the process is complex and consumes a large amount of chemical reagents. In addition, the high treatment temperature is accompanied by high energy consumption and equipment loss.
Physical separation and chemical treatment technologies for SCA can realize the separate/complete quantitative recovery of valuable components (carbon materials and electrolytes). The feasibility of utilizing recycled carbon materials to prepare porous carbon materials and lithium-ion batteries has been widely explored. The principle, advantages, and disadvantages of existing methods for the safe disposal and comprehensive utilization of SCA are shown in Table 4.
TABLE 4. Principle, advantages, and disadvantages of existing methods for the safe disposal and comprehensive utilization of SCA.
SCA is a hazardous solid waste that is inevitably and continuously produced in the aluminum electrolysis industry. Owing to its large number of high-quality carbon materials and high-value electrolyte components, this material has extremely high recycling value. Therefore, the safe disposal and comprehensive utilization of SCA is essential.
1) Roasting and vacuum metallurgy can be used to recover electrolyte components that have high purity and could be directly returned to the aluminum electrolysis cell for recycling. However, these processes are accompanied by a large amount of CO2 emission and energy consumption, which do not meet the strategic needs of “carbon neutrality” and “peak carbon dioxide emissions” promoted by the state. Compared with physical separation, chemical treatment has the advantages of high separation efficiency and high product yield. However, some problems such as large consumption of chemical reagents and high production cost must be addressed.
2) Given the raw material characteristics of SCA, flotation is the most promising technology for the safe disposal and comprehensive utilization of SCA. In future research work, raw materials must be pretreated to further realize the enhanced separation of carbon materials and electrolyte components. Flotation should be combined with chemical treatment to develop a technology with high efficiency, low consumption, and environmental protection.
3) Recycling of valuable resources in SCA should be actively explored. For example, carbon materials can be used as raw materials to prepare carbon anode for aluminum electrolysis. The pressure of low-sulfur petroleum coke resource shortage is alleviated, and the production cost is reduced. The high-value utilization of recycled products in catalysis, adsorption, and new energy should be expanded to build a common key technical system for the safe disposal and comprehensive utilization of SCA.
BL: Methodology, Writing-Original draft preparation. JZ: Conceptualization. ZY: Visualization, Writing-Review and Editing. QP: Investigation, Software. ML: Data Curation. XL: Validation, Formal analysis. WL: Resources, Supervision.
This work was supported by Guizhou Provincial Science and Technology (No. (2020)1Y224, No. (2020)4Y036)).
The authors declare that the research was conducted in the absence of any commercial or financial relationships that could be construed as a potential conflict of interest.
All claims expressed in this article are solely those of the authors and do not necessarily represent those of their affiliated organizations, or those of the publisher, the editors and the reviewers. Any product that may be evaluated in this article, or claim that may be made by its manufacturer, is not guaranteed or endorsed by the publisher.
Bai, Qiong. (2020). Causes and Countermeasures of Carbon Slag in Aluminum Electrolysis Production. Metallurgical Management 17, 158–159. (in Chinese). doi:10.3969/j.issn.1007-1865.2020.17.002
Chai, D. P., Hou, G. H., and Huang, H. B. (2016). Experimental Study on the Treatment of Aluminum Reduction Carbon Residue by Vacuum Metallurgy. Light Met. 4, 25–27. (in Chinese). doi:10.13662./j.cnki.qjs.2016.04.006
Chen, X. P. (2011). Latest Status of Processing Technologies for Spent Potlining from Aluminum Smelters. Light Met. 12, 21–24. (in Chinese). doi:10.13662/j.cnki.qjs.2011.12.011
Chen, X. P., Zhao, L., and Luo, Z. S. (2009). Study on Recycling Process for Electrolyte in Carbon Dust from Reduction Cells. Light Met. 12, 21–25. (in Chinese). doi:10.13662/j.cnki.qjs.2009.12.006
Geng, L. L., Zhang, H. X., Li, X. Q., Liao, S., and Wu, Y. (2014). Research Progress in the Preparation of Biomaterial Activated Carbon. Guangdong Chem. Industry 41, 102–103. (in Chinese). doi:10.3969/j.issn.1007-1865.2014.12.052
Guo, Z. H. (2020). Causes and Countermeasures of Carbon Slag in Aluminum Electrolysis Production. Low Carbon World 10, 16–17. (in Chinese). doi:10.3969/j.issn.2095-2066.2020.05.010
Hou, W., Li, H., Feng, Y., Wang, J., Li, M., Cheng, B., et al. (2020). Effects of the Application of a Perforated Anode in an Aluminum Electrolysis Cell on the Gas-Liquid Two-phase Flow and Bubble Distribution Characteristics. Ind. Eng. Chem. Res. 59, 14522–14530. doi:10.1021/acs.iecr.0c02478
Hou, W., Li, H., Li, M., Zhang, B., Wang, Y., and Gao, Y. (2019). Multi-physical Field Coupling Numerical Investigation of Alumina Dissolution. Appl. Math. Model. 67, 588–604. doi:10.1016/j.apm.2018.11.041
Li, C. L., Ou, Y. J., Xie, G. H., Wang, H. Y., Wang, J. Y., Zhao, L. L., et al. (2021). Cultivating Students' Engineering Awareness and Innovation Ability Based on Internet+College Students' Innovation and Entrepreneurship Competition—Taking Carbon Recovery Process Design of Carbon Powder after Aluminum Electrolysis Carbon Residue Flotation as an Example. Guangdong Chem. Industry 48, 248–250. (in Chinese). doi:10.3969/j.issn.1007-1865.2021.02.115
Li, D., Guo, X., Xu, Z., Tian, Q., and Feng, Q. (2015). Leaching Behavior of Metals from Copper Anode Slime Using an Alkali Fusion-Leaching Process. Hydrometallurgy 157, 9–12. doi:10.1016/j.hydromet.2015.07.008
Li, H., Wang, J., Hou, W., Li, M., Cheng, B., Feng, Y., et al. (2021). The Study of Carbon Recovery from Electrolysis Aluminum Carbon Dust by Froth Flotation. Metals 11, 145. doi:10.3390/met11010145
Li, Q., Cui, X. D., and Gao, W. Y. (2015). Countermeasures and Origins of Carbon Residue in Aluminum Electrolysis Production. Light Met. 11, 36–38. (in Chinese). doi:10.13662/j.cnki.qjs.2015.11.008
Liang, C., Zhao, R. M., Peng, J. P., Di, Y. Z., and Wang, Y. W. (2021). Treatment of Carbon Slag from Aluminum Electrolysis Cell Using Na2CO3. Chin. J. Eng. 7, 1–12. (in Chinese). doi:10.13374/j.issn2095-9389.2020.11.30.007
Liu, C. S., and Wu, S. W. (2020). Discussion on Causes and Treatment for Carbon Residue during Aluminum Reduction Pot Production. World Nonferrous Met. 14, 19–20. (in Chinese). doi:10.3969/j.issn.1002-5065.2020.14.008
Liu, K. (2020). Practice of Recovering Electrolyte in Aluminum Electrolysis Carbon Slag Flotation Process. Resource Regen. 10, 54–56. (in Chinese). doi:10.3390/min10090820
Liu, S. X., Gao, B. F., and Zeng, Z. H. (2021). Preparation of Aluminum Electrolytic Cell Porous Carbon by CO2 Activation and Performance for Adsoption. Guangzhou Chem. Industry 49, 75–77. (in Chinese). doi:10.3969/j.issn.1001-9677.2021.07.025
Liu, Y., Hu, G. Y., Sun, W., Zhang, Y., and Wang, L. (2021). Progress in Comprehensive Utilization of Carbon Solid Waste in Aluminum Electrolytic Cell. Conservation Utilization Mineral. Resour. 41, 166–171. (in Chinese). doi:10.13779/j.cnki.issn1001-0076.2021.01.024
Luo, M. Y., Gu, X. P., Qu, T., Shi, L., and Dai, Y. N. (2020). Separation of Carbon and Electrolyte from Electrolytic Aluminum Spent Cathode Carbon Block by Vacuum Distillation. Nonferrous Met. Eng. 10, 47–52. (in Chinese). doi:10.3969/j.issn.2095-1744.2020.07.08
Luo, Z., Zhao, Y., Lv, B., Fu, Y., Xu, X., and Chen, C. (2019). Dry Coal Beneficiation Technique in the Gas-Solid Fluidized Bed: a Review. Int. J. Coal Preparation Utilization 10, 1–29. doi:10.1080/19392699.2019.1678469
Mei, X. Y., Li, J., and Yu, Z. L. (2016). The Research on Recycling Carbon Residue by Floatation Process. Light Met. 4, 28–30. (in Chinese). doi:10.13662/j.cnki.qjs.2016.04.007
Shoppert, A., Loginova, I., Rogozhnikov, D., Karimov, K., and Chaikin, L. (2019). Increased as Adsorption on Maghemite-Containing Red Mud Prepared by the Alkali Fusion-Leaching Method. Minerals 9, 60. doi:10.3390/min9010060
Tian, Z. L., Gong, Y. P., Xin, X., Yang, K., Deng, C. Y., and Yin, G. (2021). Electrochemical Properties of Si/C Compsite Materials Preparded from Discarded Carbon Anode Residue from Aluminum Electrolysis by ball Milling Method. Mining Metallurgical Eng. 41, 110–113. doi:10.3969/j.issn.0253-6099.2021.03.027
Tu, X. C. (2017). Analysis on the Causes and Preventive Measures of Carbon Residue in Aluminum Electrolysis Production. Shanxi Metall. 40, 126–128. (in Chinese). doi:10.16525/j.cnki.cn14-1167/tf.2017.04.46
Wang, H., Feng, Q., Tang, X., and Liu, K. (2016). Preparation of High-Purity Graphite from a fine Microcrystalline Graphite Concentrate: Effect of Alkali Roasting Pre-treatment and Acid Leaching Process. Separation Sci. Technology 51, 2465–2472. doi:10.1080/01496395.2016.1206933
Wang, Y. R. (2021). Preparation and Electrochemical Performance of Anode Materials for Lithium-Ion Batteries by Spent Carbon Anode from Electrolytic Aluminum. [master’s thesis] (Lanzhou: Lanzhou University of Technology) (in Chinese).
Wang, Z. Q., Wen, T. J., and Zhang, H. T. (2019). Analysis and Research on Resource Utilization Technology of Anode Carbon Slag Disposal in Aluminum Electrolysis Production. World Nonferrous Met. 22, 8–9. (in Chinese). doi:10.3969/j.issn.1002-5065.2019.22.004
Wei, Y. H. (2018). Improvement and Application of Cryolite Regeneration Technology by Carbon Residue Flotation. Light Met. 10, 29–31. (in Chinese). doi:10.13662/j.cnki.qjs.2018.10.007
Yang, K., Gong, P., Xin, X., Tian, Z., and Lai, Y. (2020). Purifying Spent Carbon Anode (SCA) from Aluminum Reduction Industry by Alkali Fusion Method to Apply for Li-Ion Batteries Anodes: from Waste to Resource. J. Taiwan Inst. Chem. Eng. 116, 121–127. doi:10.1016/j.jtice.2020.10.034
Yang, Y., Gao, B., Wang, Z., Shi, Z., and Hu, X. (2016). Study on the Inter-electrode Process of Aluminum Electrolysis. Metall. Materi Trans. B 47, 621–629. doi:10.1007/s11663-015-0508-6
Yi, S. Y., Wang, X. Y., Li, N., Wei, J. L., and Dai, C. L. (2008). Research Progress in Activation Treatment Technology of Activated Carbon. Mater. Guide 3, 72–75. (in Chinese). doi:10.3321/j.issn:1005-023x.2008.03.018
Yuan, J., Xiao, J., Li, F., Wang, B., Yao, Z., Yu, B., et al. (2018). Co-treatment of Spent Cathode Carbon in Caustic and Acid Leaching Process under Ultrasonic Assisted for Preparation of SiC. Ultrason. Sonochem. 41, 608–618. doi:10.1016/j.ultsonch.2017.10.027
Yuan, J., Xiao, J., Tian, Z., Yang, K., and Yao, Z. (2018). Optimization of Spent Cathode Carbon Purification Process under Ultrasonic Action Using Taguchi Method. Ind. Eng. Chem. Res. 57, 7700–7710. doi:10.1021/acs.iecr.7b05351
Yuan, J., Xiao, J., Tian, Z., Yang, K., Yao, Z., Yu, B., et al. (2018). Optimization of Purification Treatment of Spent Cathode Carbon from Aluminum Electrolysis Using Response Surface Methodology (RSM). Asia-pac. J. Chem. Eng. 13, e2164. doi:10.1002/apj.2164
Zhang, B. S. (2013). Harm of Carbon Slag in Aluminum Electrolysis Production. Xinjiang Nonferrous Met. 36, 70–72. (in Chinese). doi:10.16206/j.cnki.65-1136/tg.2013.01.046
Zhang, Y. N., Chai, D. P., Zhou, Y. F., Wang, Y. Fang., Bai, W. G., and Hou, G. H. (2018). Research Progress on Resource Comprehensive Utilization Technology of Carbon Dust in Aluminum Electrolysis. World Nonferrous Met. 7, 1–3. (in Chinese). doi:10.3969/j.issn.1002-5065.2018.07.001
Zhao, D. F., and Yang, Y. Z. (2013). Analysis on the Harmfulness of Carbon Residue in Aluminum Electrolysis Production. Introduction Scientific Technol. Innovation 10, 154 (in Chinese). doi:10.16660/j.cnki.1674-098x.2013.10.028
Zhao, R. M., Yu, Z. L., and Li, S. H. (2015). The Recycling Experimental Study on Aluminum Electrolysis Carbon Residues. Yunnan Metall. 44, 15–18. (in Chinese). doi:10.3969/j.issn.1006-0308.2015.01.004
Zhou, J., Yao, Z., Liu, W., Luo, J., and Xie, Y. S. (2019). Effects of Flotation Conditions on the Separation Effciency of Carbon in Carbon Residue in Aluminum Electrolysis. Carbon Technology 38, 58–61. (in Chinese). doi:10.14078/j.cnki.1001-3741.2019.05.012
Keywords: aluminum electrolysis, hazardous waste, spent carbon anode, safe disposal, comprehensive utilization
Citation: Li B, Zhou J, Yao Z, Peng Q, Liu M, Li X and Liu W (2021) Advances in the Safe Disposal and Comprehensive Utilization of Spent Carbon Anode From Aluminum Electrolysis: Prospects for Extraction and Application of Carbon Resources From Hazardous Waste. Front. Energy Res. 9:779476. doi: 10.3389/fenrg.2021.779476
Received: 18 September 2021; Accepted: 18 October 2021;
Published: 01 November 2021.
Edited by:
Zongliang Zuo, Qingdao University of Technology, ChinaReviewed by:
Jindi Huang, Jiangxi University of Science and Technology, ChinaCopyright © 2021 Li, Zhou, Yao, Peng, Liu, Li and Liu. This is an open-access article distributed under the terms of the Creative Commons Attribution License (CC BY). The use, distribution or reproduction in other forums is permitted, provided the original author(s) and the copyright owner(s) are credited and that the original publication in this journal is cited, in accordance with accepted academic practice. No use, distribution or reproduction is permitted which does not comply with these terms.
*Correspondence: Zhen Yao, eWFvemhlbkBnem51LmVkdS5jbg==; Wei Liu, Y2psd0Bnem51LmVkdS5jbg==
Disclaimer: All claims expressed in this article are solely those of the authors and do not necessarily represent those of their affiliated organizations, or those of the publisher, the editors and the reviewers. Any product that may be evaluated in this article or claim that may be made by its manufacturer is not guaranteed or endorsed by the publisher.
Research integrity at Frontiers
Learn more about the work of our research integrity team to safeguard the quality of each article we publish.