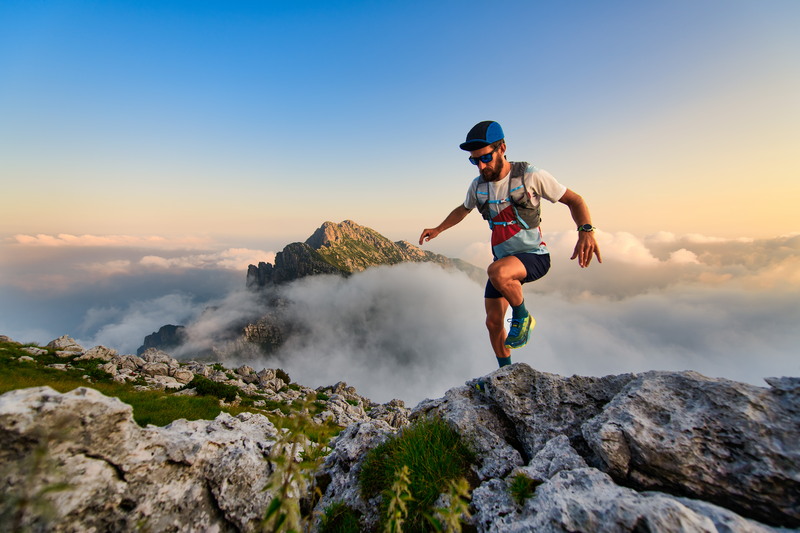
95% of researchers rate our articles as excellent or good
Learn more about the work of our research integrity team to safeguard the quality of each article we publish.
Find out more
ORIGINAL RESEARCH article
Front. Energy Res. , 23 November 2021
Sec. Nuclear Energy
Volume 9 - 2021 | https://doi.org/10.3389/fenrg.2021.751654
This article is part of the Research Topic Radiation Protection and Measurement in Nuclear Reactors View all 9 articles
An optimization design and application of high temperature–resistant shielding material was carried out according to the nuclear power plant source characteristics and special protection requirements such as loss-of-coolant accident (LOCA). The composition of lead–boron polyethylene shielding composite was optimized based on the genetic algorithm and Monte Carlo methods and then realized by blending modification and graft copolymerization to improve its high temperature–resistant, shielding, and mechanical properties. Then comprehensive properties such as mechanical, neutron shielding, damp heat aging, irradiation resistance, and high temperature resistance were tested. These experiments proved that the high temperature–resistant lead–boron polyethylene shielding composite has excellent performance; especially, as it is able to keep a complete structure in a high-temperature environment of up to 190°C for 48 h. Finally, the shielding composite was applied to the shielding door design of a reactor pit chamber. When the shield thickness is 60 mm, the level of the neutron dose rate was reduced by 10 times, and that of the γ dose rate was reduced by 5 times, which meets all the requirements of radiation protection safety for nuclear power plants.
The Hualong One reactor chamber adit requires effective shielding against neutrons and γ to reduce radiation from radiation sources such as reactor pressure vessels and main circuit systems so that the radiation dose rate of typical positions inside and outside the shielding door meets the requirements of the radiation zoning to ensure the safety of the staff, equipment, and environment. Commonly used shielding materials for the shielding doors of nuclear power plants include lead–boron polyethylene, boron steel, epoxy resin, etc. (Lu and Chen, 1994; Yasin and Khan, 2008; Guo et al., 2010; Li et al., 2015; Xu et al., 2017). However, because the shielding door of the reactor chamber adit is installed very close to the reactor pit, it is subject to a much higher temperature, high humidity level, and more severe irradiation conditions. Therefore, the shielding material used should not only have good mechanical properties, shielding performance, and hydrothermal and irradiation aging resistance in the whole 20-year service life but also be able to withstand the extreme conditions of atmospheric temperatures up to 190°C when a LOCA occurs. After a 48-h simulated LOCA test, the structure of the shielding board sample inside the shielding door should remain intact without significant deformation, the performance indicators of all aspects should be within the acceptable range, and it should be easy to repair and replace.
According to the interaction between neutrons and materials (Li, 1982), iron, lead, and other materials with high atomic numbers absorb and scatter γ-rays through the photoelectric effect, Compton effect, electron pair effect, etc., and at the same time, slow down fast neutrons to intermediate energy neutrons through inelastic scattering. Polyethylene with high hydrogen content could further moderate the intermediate energy neutrons into thermal neutrons through elastic scattering, which are finally absorbed by 10B of boron carbide. Therefore, to obtain the best shielding design against neutrons and γ, it is generally necessary to combine or compound the materials mentioned above. However, whether it is the combination of lead with boron-containing polyethylene or lead–boron polyethylene shielding composite, they are all polyethylene-based shielding materials with a lower heat deformation temperature of 85°C and a lower melting temperature of 130°C. Therefore, in general, they cannot work normally in an environment with a temperature above 100°C. This limits their application in high-temperature environments. Especially when a LOCA occurs, high temperatures (about 190°C) will cause problems such as softening, deformation, and splashing of the shielding materials, leading to a reduction in shielding effectiveness and risk of radiation exposure. Since they are effective heat conductors, even when they are fitted with steel structures or lead plates the temperature transferred to the surface of the polyethylene-based shielding material is still as high as 140°C (Nie et al., 2019).
Therefore, in this study, a lead–boron polyethylene shielding composite was developed to meet the protection requirements of the reactor pit chamber. The shielding effect and high temperature resistance of the material are further improved by means of composition optimization design and raw material modification. Sample trial production and comprehensive performance tests were also completed on the shielding door design. The results show that this design can ensure the radiation safety of the reactor chamber adit of the Hualong One nuclear power plant under normal and accident conditions.
The composition design of the lead–boron polyethylene shielding composite is a constrained multi-objective optimization problem. As an effective random search method, the genetic algorithm (Holland, 1975) has the characteristics of global optimality, good consistency, and convergence. It has good adaptability for solving multi-objective optimization problems with constraints and has been widely used in many fields and achieved good results. In this work, GENOCOPⅢ (Michalewicz and Nazhiyath, 1995; Michalewicz and Janikow, 1996) based on the genetic algorithm and MCNP 5 (X-5 Monte Carlo Team, 2003) and the Monte Carlo method are applied to the optimization design of the lead–boron polyethylene shielding composite according to the radiation field source terms of the Hualong One reactor pit chamber. The design process is as follows: first, initializing the material ratio and selecting appropriate genetic parameters, such as the material density region and the element composition region, as the constraints and then running the GENOCOPⅢ program. Second, according to the preliminary calculated results of the composition ratio of the elements, editing and converting the density, calculation model, and other information into an MCNP input file which is used to calculate the equivalent dose rate of neutrons and γ passing through the shielding material and obtaining the total dose equivalent rate. Then, calculating, combining, and feeding back each sub-target value separately. If the design target is not satisfied, the proportioning, calculation, and comparison are redesigned until the results coincide with the conditions.
Source terms of the reactor pit chamber: the fast neutron fluence rate is 1.6 × 105n/cm2 s; the thermal neutron fluence rate is 1.4 × 106n/cm2 s; the γ dose rate is 2 Gy/h. Both neutron and γ energy spectra use the 235U induced fission energy spectrum (Jaffey and Lerner, 1970; Schaeffer, 1973); the neutron energy spectrum distribution is shown in Eq. 1, and the γ photon energy spectrum distribution is in Eq. 2.
The composition ratio design of the lead–boron polyethylene shielding composite has been initially completed, as shown in Table 1.
TABLE 1. Optimization design results of the element composition ratio of the lead–boron polyethylene shielding composite (mass ratio).
Modification refers to the use of physical, chemical, and mechanical methods to improve the original properties of the material in the present molding process to meet different needs. The modification of plastics such as polyethylene can be divided into physical modification and chemical modification. Physical modification mainly refers to the modification by filling and blending, and chemical modification includes graft and block copolymerization. Based on literature on this subject (Huang et al., 2007; Ma and Huang, 2010; Ding et al., 2012; Hao, 2014; Li et al., 2020; Ye et al., 2020), blending and graft copolymerization are widely used methods to improve the high temperature resistance of polyolefin-based shielding composites.
Blending modification adds one or several polymers to keep the molecular structure unchanged during the molding process, providing the raw materials with new properties. To impart no effect on the neutron shielding property of the lead–boron polyethylene shielding composite, an ultrahigh–molecular weight polyethylene with the same hydrogen content as the ordinary high-density polyethylene is selected. It has high melt strength and is extremely insensitive to thermal shear. Hence, this property can be used to modify ordinary polyethylene. During the blending process, the shear force can separate the macromolecular chains of the material to form free radicals, and some block and graft copolymerization will occur (Chen and Peng, 2011) so that the high-density polyethylene is suspended in the liquid phase of the blended material. This can effectively improve the material’s ability to withstand high temperatures, making the melt of the improved lead–boron polyethylene shielding composite in a gel state at high temperatures and not producing softening deformation without an external force. The content ratio of ultrahigh–molecular weight polyethylene added is a key factor. Through sample trial production with different content ratios and high temperature tests, it was found that when the proportion is in the range of 30–50%, the lead–boron polyethylene shielding composite sample has both excellent high temperature resistance and processing performance.
The graft copolymerization modification is used to improve the mixing uniformity and the mechanical properties of the shielding composite. Owing to the non-polar structure of its molecular chain, polyethylene lacks affinity with inorganic and metal fillers. Especially, the lead–boron polyethylene, which is designed through the composition ratio optimization, has a lead and boron content of more than 80%. The large difference in density of several elements and the high content of lead and boron makes it difficult for the shielding composite to mix uniformly, and the mechanical strengths such as tensile strength and elongation at break are greatly reduced. Thus, in this study, maleic anhydride (MAH) with high reactivity and strong polarity was selected as the modification molecules, which could be graft copolymerized with polyethylene chains to improve the processability and increase the properties of polyethylene. The specific method is as follows: a twin-screw extruder is used as a continuous reactor, at a certain screw speed, the mixture of polyethylene, MAH, peroxide, and other additives is subjected to reactions such as plasticization, melting, dispersion mixing, grafting, and melt transportation, and finally, the extrudate is cooled, dried, and then cut into particles. After the particles are ground into powder, they are used as the base material for preparing the lead–boron polyethylene shielding composite. This effectively improves the blending uniformity and bonding strength of the lead–boron polyethylene shielding composite.
According to the composition ratio of the lead–boron polyethylene shielding composite optimized and designed in Optimization Design of Composition, the modified polyethylene raw materials, lead powder, and boron carbide powder, are weighed separately and then put into a high-speed mixer for full mixing. In order to ensure the uniformity of the mixing of the raw materials, they are then put into a twin-screw mixer and are fully heated, squeezed, and sheared to complete the extrusion granulation. Finally, the lead–boron polyethylene particles are added to the mold and then hot pressed. Figure 1 is a sample of prepared lead–boron polyethylene shielding composite.
According to the environmental conditions of a nuclear power plant, comprehensive tests on mechanical properties, neutron and γ shielding performance, hydrothermal and irradiation aging resistance, and the performance in a LOCA simulation of the lead–boron polyethylene shielding composite have been conducted. The specific test process is shown in Figure 2.
The test results show (see Table 2 for details) that the performance of the lead–boron polyethylene shielding composite studied meets or exceeds the technical index requirements. In particular, it has excellent high temperature resistance: the lead–boron polyethylene shielding composite board is settled in the LOCA test device for the simulation test with the atmosphere temperature up to 190°C and the test time longer than 48 h. After the test, the material maintains a complete shielding structure without softening, collapse, significant deformation, or weight loss. Although the size of the board has undergone a certain amount of deformation due to thermal expansion and contraction, it does not stick to the structural components or experience other problems, so it is easy to unload and replace. In contrast, the softening and deformation of ordinary lead–boron polyethylene are serious, there is a significant plasticizing flow, and it is stuck to the steel structure and cannot be taken out. The parameters of the LOCA test are shown in Figure 3, and the results are shown in Figure 4.
The source terms of the reactor chamber adit are as described in Optimization Design of Composition. The surface source model is adopted. The ray direction is perpendicular to the reactor chamber adit along the radial direction of the reactor. A simplified MCNP calculation geometric model (as shown in Figure 5) is established, including the main structures such as a reactor chamber adit shielding wall (composed of concrete and boron-containing polyethylene shielding composite) and a reactor chamber adit shielding door (composed of a steel structure and lead–boron polyethylene shielding composite).
The mesh tally model is used to evaluate the shielding effect of each part of the shielding door. Through MCNP simulation calculation, the labyrinth design of the reactor chamber adit and the shielding wall effectively blocked and absorbed most of the neutrons and γ-rays. Finally, the maximum dose rate of neutrons that reach the inner surface of the shielding door is 810 μSv/h, the maximum γ dose rate is 265 μSv/h, and the average total dose rate is about 950 μSv/h. When the 60-mm-thick lead–boron polyethylene shielding composite developed in this study is installed inside the shielding door, the maximum neutron dose rate outside the shielding door of the reactor chamber adit is 75 μSv/h, and the maximum γ dose rate is 48 μSv/h. The neutron dose rate level is reduced by 10 times on average, and the γ dose rate level is reduced by 5 times. The average total dose rate after shielding is about 92 μSv/h, within the design dose rate limit of the discontinuous work area, namely, Yellow zone B, which meets the relevant requirements of the radiation zoning of the Hualong One nuclear power plant and can guarantee the radiation safety of radioactive workers.
In this study, according to the radiation field source term characteristics and protection requirements of the reactor chamber adit shielding door of the Hualong One nuclear power plant, a lead–boron polyethylene shielding composite with an optimized composition ratio was designed by using the genetic algorithm and the Monte Carlo method. The method of blending modification is adopted to add an ultrahigh–molecular weight polyethylene, and block and graft copolymerizations that occur through the mixing process to improve the material’s ability to withstand high temperatures and ensure the maximum shielding effect. The method of graft copolymerization is used to graft polyethylene with MAH to improve the uniformity and mechanical properties of lead, boron carbide, and other elements mixed with polyethylene. This research also carries out comprehensive nuclear power plant environmental tests on the mechanical properties, neutron shielding performance, hydrothermal and irradiation aging resistance, and the performance in a LOCA of the prepared high temperature–resistant lead–boron polyethylene shielding composite. The results show that the material developed in this study shows an excellent performance in every aspect. Especially in the high-temperature environment up to 190°C, it can maintain the shielding structure integrity and the shielding effectiveness. Finally, the material is applied to the reactor chamber adit shielding door. The 60-mm-thick shielding material can reduce the neutron dose rate level by 10 times and the γ dose rate level by 5 times, which meets the zoning requirements for the reactor chamber adit shielding door of the Hualong One nuclear power plant, and can ensure radiation safety for personnel under normal and accident conditions.
The raw data supporting the conclusions of this article will be made available by the authors, without undue reservation.
LX-L and WR-J contributed to the conception and design of the study. XX-H, ZD-F and YM contributed to comprehensive tests. All authors contributed to manuscript revision and read and approved the submitted version.
The authors declare that the research was conducted in the absence of any commercial or financial relationships that could be construed as a potential conflict of interest.
All claims expressed in this article are solely those of the authors and do not necessarily represent those of their affiliated organizations, or those of the publisher, the editors, and the reviewers. Any product that may be evaluated in this article, or claim that may be made by its manufacturer, is not guaranteed or endorsed by the publisher.
Chen, X., and Peng, S. (2011). Blending Modification of polymer[M]. Beijing: Chemical Industry Press.
Ding, H., Yuan, J., Zhong, G., and Wang, N. (2012). Polymer Materials and applications[M]. Beijing: Chemical Industry Press.
Guo, P., Dong, L., Wang, C., et al. (2010). Preparation of boron Carbide/ultra-High Molecular Weight Polyethylene Composites for Neutron Shielding[J]. J. Mater. Eng. Z2, 337–340. (in Chinese).
Hao, H. (2014). Heat Resistance Modification of Ultra-high Molecular Weight Polyethylene, A Thesis Submitted for the Degree of Master. Wuhan Institute of Technology. (in Chinese).
Holland, J. H. (1975). Adaptation in Natural and Artificial Systems [M]. Ann Arbor: University of Michigan Press.
Huang, A., Zhu, B., and Jia, J. (2007). Progress in Modification of Ultra High Molecular Weight Polyethylene [J]. Gansu Shiyou He Huagong 6 (2), 20–23.
Jaffey, A. H., and Lerner, J. L. (1970). Measurement of Prompt Neutron Fission Yield (V̄p) in thermal Neutron Fission of 232U, 238Pu, 241Pu, 241Am, 242mAm, 243Cm, 245Cm and in Spontaneous Fission of 244Cm. Nucl. Phys. A 145 (1), 1–27. doi:10.1016/0375-9474(70)90307-6
Li, F., Xiao, L. R., and Cao, C. L. (2020). Research Progress on Blending Modification of Ultra High Molecular Weight Polyethylene/Polypropylene [J]. Chem. Eng. Equipment 2 (2), 199–201.
Li, X., Yu, F., Sun, L., et al. (2015). Multi-objective Optimization Design of lead-boron Polyethylene Shielding Composite [J]. Ship Sci. Technol. 37 (12), 148–154. (in Chinese).
Lu, J., and Chen, J. (1994). High Effective Shielding Material lead-boron Polyethylene[J]. Nucl. Power Eng. 15 (4), 370–374. (in Chinese).
Ma, Y., and Huang, Li. (2010). Heat Resistance of Ultra High Molecular Weight Polyethylene Composites Modified by Hollow Glass Bead[J]. J. Beijing Univ. Chem. Technol. 37 (2), 49–53. (in Chinese).
Michalewicz, Z., and Janikow, C. (1996). GENOCOP:A Genetic Algorithm for Numerical Optimization Problem with Linear Constrains[J]. Commun. ACM 39 (12), 175–201. doi:10.1145/272682.272711
Michalewicz, Z., and Nazhiyath, G. (1995). GenocopIII: A Co-evolutionary Algorithm for Numerical Optimization Problems with Nonlinear Constraints. Australia: IEEE International Conference Evolutionary Computation. Perth, 647–651.
Nie, L., Jia, J., Wu, R., et al. (2019). Research on High Temperature Resistance on the Typical Biological Shielding Structure and Biological Shielding Materials. J. Ship Sci. Technol. 41 (10), 103–107.
Schaeffer, N. (1973). Reactor Shielding for Nuclear engineers[C]. United States: US Atomic Energy Commission Office of Information Services.
X-5 Monte Carlo Team (2003). MCNP: A General Monte Carlo N-Particle Transport Code, Version 5[M]. California: Los Alamos National Laboratory.
Xu, H., Li, X., Wu, R., et al. (2017). Optimization Design and Application Study of Epoxy Resin Shielding Putty Based on Monte Carlo Method[J]. At. Energ. Sci. Technol. 51 (7), 1328–1335. (in Chinese).
Yasin, T., and Khan, M. N. (2008). High Density Polyethylene/boron Carbide Composites for Neutron Shielding. E-Polymers 8 (1), 670–676. doi:10.1515/epoly.2008.8.1.670
Ye, C., Ding, X., Li, L., et al. (2020). Radiation Preparation and Properties of Low-Density Polyethylene Grafted Maleic Anhydride[J]. J. Radiat. Res. Radiat. Process. 38 (1), 1–9.
Keywords: high temperature resistance, shielding material, optimization design, loss-of-coolant accident, shielding design
Citation: Xiao-ling L, Rong-jun W, Xiao-hui X, Duo-fei Z and Ming YU (2021) Study of a High Temperature–Resistant Shielding Material for the Shielding Doors of Nuclear Power Plants. Front. Energy Res. 9:751654. doi: 10.3389/fenrg.2021.751654
Received: 01 August 2021; Accepted: 23 September 2021;
Published: 23 November 2021.
Edited by:
Guang Hu, Xi’an Jiaotong University, ChinaReviewed by:
Chunhuan Guo, Harbin Engineering University, ChinaCopyright © 2021 Xiao-ling, Rong-jun, Xiao-hui, Duo-fei and Ming. This is an open-access article distributed under the terms of the Creative Commons Attribution License (CC BY). The use, distribution or reproduction in other forums is permitted, provided the original author(s) and the copyright owner(s) are credited and that the original publication in this journal is cited, in accordance with accepted academic practice. No use, distribution or reproduction is permitted which does not comply with these terms.
*Correspondence: LI Xiao-ling, bGl4bDAwNUAxNjMuY29t
Disclaimer: All claims expressed in this article are solely those of the authors and do not necessarily represent those of their affiliated organizations, or those of the publisher, the editors and the reviewers. Any product that may be evaluated in this article or claim that may be made by its manufacturer is not guaranteed or endorsed by the publisher.
Research integrity at Frontiers
Learn more about the work of our research integrity team to safeguard the quality of each article we publish.