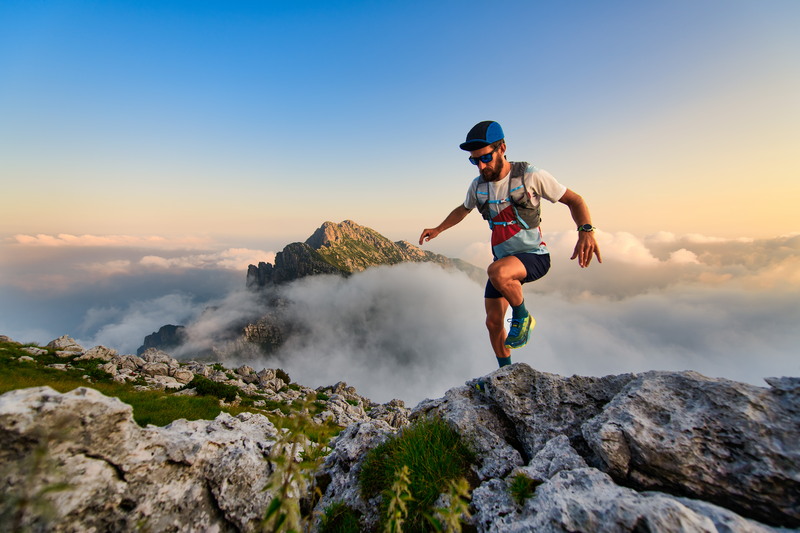
94% of researchers rate our articles as excellent or good
Learn more about the work of our research integrity team to safeguard the quality of each article we publish.
Find out more
ORIGINAL RESEARCH article
Front. Energy Res. , 06 October 2021
Sec. Advanced Clean Fuel Technologies
Volume 9 - 2021 | https://doi.org/10.3389/fenrg.2021.729919
This article is part of the Research Topic Pollutant Emission Control in Energy Conversion Process View all 12 articles
The double-effect Ni-based catalysts, modified with Ce, Mg, and Fe and synthesized by the coprecipitation method, were applied into the enhanced steam reforming process of real tar. The effects of the catalysts with different doping mass proportions (3, 6, 9, and 12%) of Ce, Mg, and Fe on the H2 yield, and H2 and CO2 concentrations were studied. The results revealed that the tar reforming efficiency was improved with appropriate proportions of the additives added. The Ce- or Mg-doped catalyst could change the distribution or morphology of the active component Ni. The modified catalyst with 6% Ce or 3% Mg doping showed the best catalytic activity in the reforming experiment, with the H2 yield reaching 86.84% or 85.22%, respectively. The Fe-doped catalyst could form an Ni–Fe alloy and improve the stability of the catalyst, and the better catalytic activity can be obtained at 9 and 12% Fe doping, with the H2 yield reaching 85.54 and 85.80%, respectively.
Coal gasification plays an important role in the coal chemical industry, while tar is the main by-product of this process. In China, the total output of coke was 473.1 million tons in 2019, with about 19 million tons of tar as the by-product. The composition of tar is complex, and it is estimated to include more than ten thousand compounds. Distinguish by boiling point, tar includes light oil, phenol oil, naphthalene oil, washing oil, onion oil, and coal tar pitch (Li and Suzuki, 2010; Li et al., 2013; Duan et al., 2017). Tar is gaseous at high temperature and liquid at low temperature, which will easily corrode the pipeline equipment. In addition, it can cause harm to the ecology and the human body if discharged into the environment (Xie et al., 2016a; Zeng et al., 2018; Li et al., 2021; Zuo et al., 2021). The methods of tar removal include physical and chemical methods. The physical method is to remove the tar from the syngas through the principle of absorption and adsorption, such as water washing, oil washing to absorb tar, or using porous media to adsorb tar onto its surface. The physical method has the advantages of simple operation and a low equipment cost, but there are some disadvantages such as secondary pollution and low removal efficiency (Xie et al., 2016c). The chemical method mainly includes the pyrolysis method and reforming method (partial oxidation reforming and steam reforming). The pyrolysis method refers to the tar cracking at high temperature to produce non-condensable small molecules of gas, which increases the cost due to the need of adding additional heat sources (Torres et al., 2007). The partial oxidation reforming method can effectively convert tar into small molecular gases such as H2 and CO, but the process is mainly conducted at a higher temperature (about 1,200°C), by consuming a large amount of pure oxygen and additional fuel to supply heat (Onozaki et al., 2006). The steam reforming method prefers to obtain hydrogen-rich gas under the action of steam and catalyst. Compared with the partial oxidation reforming method, the temperature of this method is lower (about 800°C), with no additional O2 and less heat. Thus, steam reforming of tar and its model compounds for hydrogen production has received extensive attention in recent years (Furusawa et al., 2013; Duan et al., 2015; Li et al., 2015; Dou et al., 2016; Duan et al., 2018; Xie et al., 2018).
Catalysts are key to steam reforming of tar, and many catalysts have been studied so far. The commonly used catalysts mainly include dolomite (Gusta et al., 2009; Sarıoğlan, 2012), olivine (Virginie et al., 2012), alkali metal (Jiang et al., 2015), Ni-based catalysts (Richardson et al., 2010; Chan and Tanksale, 2014; Xie et al., 2015), and noble metal catalysts (Furusawa et al., 2013; Mei et al., 2013). Considering the catalyst efficiency and cost, the Ni-based catalyst is one of the most promising catalysts for tar reforming. However, inhibiting its carbon formation and improving its catalytic stability are the urgent problems to be solved (Yue et al., 2010; Gao et al., 2015). As a carrier, Ca12Al14O33 can improve the reactivity and the anti-carbon property of the Ni-based catalyst. It itself can also be used as a catalyst for cracking tar, and the synergistic with Ni addition can further inhibit the carbon formation (Li et al., 2009). However, common steam reforming reactions yield only 70% (volume fraction) H2 and more than 20% CO2, limiting the use of such a hydrogen-containing gas (Xie et al., 2016d). So, researchers try to add adsorption components to the original catalyst and combine the catalytic reforming process with the CO2 adsorption process. The adsorbent components can break the balance of the original reforming reaction, improving the quality and concentration of H2, and the carbon deposition on the catalyst can be effectively reduced (Kinoshita and Turn, 2003; Dou et al., 2016; Xie, et al., 2016b; Zuo et al., 2020). In the adsorption-enhanced process, CaO is widely used as the CO2 adsorbent due to its low cost and easy accessibility. However, CaO is easy to be sintered at high temperatures, resulting in a decrease in the adsorption capacity (Zamboni et al., 2011). As mentioned above, as a carrier, Ca12Al14O33 has a special free oxygen storage structure, which can also effectively inhibit the sintering of CaO when carried within Ca12Al14O33 (Li et al., 2009). Thus, the double-effect Ni/CaO–Ca12Al14O33 catalyst was prepared and applied to the steam reforming process of 1-methylnaphthalene (C11H10) as a tar model component in our previous study, showing a good catalytic activity and CO2 adsorption capacity (Zhang et al., 2021a; Zhang et al., 2021b). However, the double-effect catalyst has not been applied in the reforming of real tar, and because of its component’s complexity, the catalytic performance on the reforming process of real reforming may be decreased compared to that on the model component. According to the literature, the catalytic activity and anti-carbon property of the Ni-based catalyst can be improved by adding additives such as precious metals (Pt, Rh, Ru, etc.) (Mei et al., 2013; Cai et al., 2014), rare earth metals (La, Ce, etc.) (Kimura et al., 2006; Tomishige et al., 2007; Mazumder and Lasa., 2015), alkali earth metals (Ca, Mg, etc.) (Wang et al., 2006; Ashok et al., 2015; Nakhaei and Mousavi, 2015), and transition metals (Fe, Co, etc.) (Wang et al., 2011; Koike et al., 2012; Wang et al., 2013). Considering the cost, Ce (rare earth metal), Mg (alkali earth metal), and Fe (transition metal) were studied in this article.
In this article, modified double-effect Ni-based catalysts were prepared and applied to the enhanced reforming process of real tar. The double-effect Ni-based catalysts with different additives (Ce, Mg, and Fe) of different doping mass proportions (3, 6, 9, and 12%) were synthesized by the coprecipitation method and were characterized by X-ray diffraction (XRD) and scanning electron microscopy (SEM). Then, the effects of different modified double-effect catalysts on the hydrogen production from the enhanced reforming of tar were studied, and the result was compared with that over the unmodified double-effect Ni-based catalyst.
The raw tar sample came from a coking plant in Liaoning province, China. The sample was preheated by distillation to remove moisture and solid-phase impurities prior to the chemical composition analysis. Elementar (vario MACRO cube, Germany) was used for the elemental analysis of tar, and the results show that the molar content of C is 54.50%, H is 39.27%, O is 5.32%, N is 0.70%, and S is 0.21%. The chemical formula of the sample can be simplified to C10H7.21O0.98, ignoring nitrogen and sulfur that were too low compared with other elements. Therefore, the steam reforming (SR) reaction of tar can be expressed by the following equation:
and following the water–gas shift (WGS) reaction, we obtain
Thus, the total steam reforming reaction can be written as follows:
GC-MS (Agilent 5975–7890A, Shanghai Tianmei) was used for the composition analysis of tar. Specific operating conditions are as follows: 1) Chromatographic conditions: Hp-5 chromatographic column; oven temperature program was as follows: maintain 1 min at 60°C as the starting temperature, heat to 280°C with the heating rate of 15 C/min, and maintain for 5 min; and He as the carrier gas with the shunt ratio of 1:100. 2) Mass spectrometry conditions: solvent delay for 4 min; ionization source: EI; electron bombardment energy: 70 eV; electronic multiplier voltage: 1200 V; and quality range: 30–600 amu, with the scanning interval of 0.5 s. Through the GC-MS analysis, a total of 22 major compounds were detected, among which the naphthalene content was the highest (given in Table 1).
The modified double-effect Ni-based catalysts were prepared by the coprecipitation method, with the mass proportion of Ni (catalytic component):CaO (adsorption component):Ca12Al14O33 (carrier component) being 15:70:15. Meanwhile, Ce (Mg or Fe) was doped as the additive, with mass proportions of 3, 6, 9, or 12%. The catalyst preparation process needed to undergo a series of dissolving, stirring, drying, and calcination processes as follows: First, Ca(CH3COO)2 was calcined at 900°C for 2 h, to obtain high-activity CaO. Second, a certain quality of CaO, Al(NO3)3 9H2O, Ni(NO3)2 6H2O, and Ce (or Mg, Fe) were mixed with deionized water to form a suspension. Then, the suspension was stirred for 3 h, dried for 12 h at 120°C, and then calcined at 500°C for 3 h. Afterward, the calcined solid was cooled and formed into a suspension by adding deionized water again, followed by stirring and drying. Finally, the dried solid was calcined at 1,000°C for 4 h to obtain a catalyst.
The experimental apparatus for the reforming experiment is shown in Figure 1. The modified double-effect catalyst was kept in a three-stage temperature control tube furnace. The tar and deionized water were pumped into the stainless-steel downstream reactor drop by dropping through an injection pump and a peristatic pump with 600 ml/min N2 carrier gas. To ensure the good fluidity of tar, the syringe was wrapped with a heating belt, keeping the wall temperature above 50°C. The product gas in the reactor was cooled and dried successively, and finally detected by a gas meter and a gas analyzer.
In this article, the catalytic performances of the modified double-effect catalysts were assessed under the optimal experimental condition based on the previously enhanced reforming experiment result with the unmodified catalyst (temperature = 740°C, S/C (the mole ratio of steam to carbon in tar) = 15, and WHSV (weight hourly space velocity) = 0.0447 h−1).
The experimental process of the tar reforming can be divided into two stages: enhanced reforming stage and common reforming stage (shown in Figure 2). For the enhanced reforming stage, CO2 generated via the WGS reaction (Eq. 2) was adsorbed by CaO in the double-effect catalyst (adsorption reaction, Eq. 4). Then, the equilibriums of the steam reforming reactions of tar were transferred to the direction of hydrogen production, with the CH4 and CO concentrations being very low and the H2 concentration being quite high. As the time went by, the concentration of CO2 was increased and that of H2 was decreased because the CO2 adsorption capacity of the double-effect catalyst tended to be saturated. Finally, the H2 and CO2 concentrations tended to be stable, about 70 and 25%, respectively, which were similar with those of the dry reformed gas without adding any CO2 adsorbent, and thus, such a stage was considered as a common reforming stage (Xie et al., 2018; Zhang et al., 2021b),
The main indicators in this article were as follows.
H2 yield (YH2) was defined as the ratio of the output of H2 (QH2, out) in the reformed gas to the theoretical output of H2 (QH2) when all the input tar is converted completely via Eq. 3.
The dry reformed gas (Qtotal, out) was considered to be composed of H2, CO, CO2, and CH4. The concentration of the reformed gas (Ci,i was H2, CO, CO2, or CH4) was defined as the ratio of the output of i (Qi, out) to the total output of the reformed gas (Qtotal, out). In this article, only the concentrations of H2 and CO2 were studied in consideration of the extremely low concentrations of CO and CH4,
Prior to characterization, the prepared catalysts were activated at 800°C with 10% mol H2/N2 stream for 3 h. The structure of the catalysts was characterized by XRD (Shimazu, Japan, XRD-7000) using Cu Kα radiation operated at 30 kV and 40 mA, with the scanning angle of 10–80 rad and the scanning speed of 2 rad/min. The morphology of the catalysts was observed by SEM with the aid of a Hitachi su-8010 microscope.
Figure 3 shows the XRD patterns of Ce-modified catalysts with different doping mass proportions. As shown in the figure, the Ce-modified catalysts include the active components, Ni and CeO2; adsorption component, Ca(OH)2 (formed by CaO absorbing water in the air); and carrier component, Ca12Al14O33. As the doping proportion increases, the peak value of CeO2 significantly increased. Figure 4 shows the SEM spectra of Ce-modified catalysts as well as the undoped sample (shown in Figure 4A). In the spectra, the bright part is mainly the active component Ni (shown by arrows 1, 3, 4, and 6), and the gray part is the adsorption component CaO and the carrier component Ca12Al14O33 (shown by arrows 2, 5, and 7); the element contents of the different parts are shown in Table 2. The different particles were based on a CaO–Ca12Al14O33 matrix, with Ni and CeO2 dotting on the surface of the matrix by small spherical particles. Proper addition of Ce can improve the distribution of Ni, which showed that part of Ni no longer relied on or just relied on a small amount of the CaO–Ca12Al14O33 matrix after Ce doping, with the small particles of Ni–CeO2 also slightly increased.
FIGURE 4. SEM spectra of Ce-modified catalysts with different doping mass proportions: (A) 0%, (B) 3%, (C) 6%, and (D) 9%.
CeO2 generally has a strong oxygen storage capacity due to its face-centered cubic structure. CeO2 can provide oxygen atoms to the adjacent nickel metal and promote the oxidation reaction of carbon intermediate products on nickel metal, thus improving the catalyst reactivity and reducing the formation of carbon deposition (Kimura et al., 2006; Tomishige et al., 2007).
Figure 5A shows the H2 yields of tar reforming over the catalysts with different Ce doping mass proportions. Overall, the catalysts, H2 yields, and concentrations at the enhanced reforming stage were higher than those at the common reforming stage. It could also be seen that Ce doped in the catalyst could improve the H2 yield at both the stages. As the doping proportion rose, the H2 yields in the two stages first increased, then decreased, and finally reached the highest at the doping proportion of 6% (86.84% for the enhanced reforming). It was corroborated that a small amount of Ce doping made the active component no longer completely rely on the CaO–Ca12Al14O33 matrix, and the active component distribution was more uniform, thus promoting the SR reaction (Eq. 1), with the increase in the H2 yield. However, the excessive Ce (>6%) doping produced more Ni and CeO2 aggregated particles, which reduced the effective catalytic activity area, with the decrease in the H2 yield. Figures 5B,C show the H2 and CO2 concentrations obtained over the catalysts with different Ce doping proportions. Due to the in-situ CO2 adsorption, the H2 concentrations of the enhanced reforming all over the catalysts with Ce doping were >90%, and among them, the sample with 6% Ce had the highest H2 concentration (95.44%) and a very little CO2 concentration, on some extent indicating that proper Ce addition can also improve the dispersion of CaO. After the adsorption saturation, i.e., at the common reforming stage, the H2 concentrations were all about 72% and CO2 concentrations were about 23–24%.
FIGURE 5. Effect of the Ce-modified catalysts: (A) H2 yield, (B) H2 concentration, and (C) CO2 concentration.
Figure 6 shows the XRD patterns of Mg-modified catalysts with different doping mass proportions. With the rise of the doping proportion, the peak value of Ni decreased, while those of MgO and MgNiO2 spinels increased significantly. From Figure 7 and Table 3, we can see that the CaO–Ca12Al14O33 matrix was still the main composition in the catalyst (shown by arrows 2, 4, and 6), and the active components (shown by arrows 1, 3, 5, 7, and 8) on the matrix were changed from the original globular particles to spiny pellets, caused by the formation of MgNiO2. With the rise of the doping proportions, the Mg-modified catalysts also showed the phenomenon that the active components detached from the CaO–Ca12Al14O33 matrix and then aggregated alone, resulting in the decrease in the catalytic area (shown by arrows 7 and 8).
FIGURE 7. SEM spectra of Mg-modified catalysts with different doping mass proportions: (A) 3%, (B) 6%, (C) 9%, and (D) 12%.
Mg is a common additive in the process of steam reforming. MgO has a certain catalytic property and can also promote the oxidation of CO. For the Ni-based catalyst, the doping of Mg enables the catalyst to form one Ni–Mg–O solid solution, which has good stability and resistance to carbon deposition (Wang et al., 2006).
Figure 8 shows the H2 yield and concentrations over the catalysts at different Mg doping proportions. For the two reforming stages, the addition of Mg can improve the SR reactions, with the increase in the H2 yield. However, for the Mg-doped samples, the H2 yield gradually decreased with the increase in the doping proportion. For the enhanced reforming, the H2 yield reached the highest, 85.62%, at the doping proportion of 3%, and the H2 concentration also decreased gradually with the rise of the Mg doping proportion in the enhanced reforming stage, and reached 93.20% at the doping proportion of 3%. Compared with the undoped catalyst, the increase in the H2 yield and concentration corroborated that the increase in the catalytic area, causing the active components to change from the original globular particles to spiny pellets, promoted the SR reaction. Then, the decrease in the H2 yield and concentration was because too much of the Mg-doped catalyst caused the active components to detach and aggregate, reducing the catalytic area. In the enhanced reforming stage, the CO2 concentration gradually increased with the rise of the Mg doping proportion, to some extent corroborating the result found in the literature that doping Mg in the catalyst could promote the oxidation of CO (Wang et al., 2006). For the common reforming, Mg addition showed a slight increase in the H2 concentration and a slight decrease in the CO2 concentration with the increase in the doping proportion, which almost had no effect.
FIGURE 8. Effect of the Mg-modified catalyst: (A) H2 yield, (B) H2 concentration, and (C) CO2 concentration.
Figure 9 shows the XRD patterns of Fe-modified catalysts with different doping mass proportions. The XRD spectra of Fe-modified catalysts were similar to those of unmodified catalysts, and the peak value of Fe2O3 was weak and nearly did not change with the rise of the doping proportion. The SEM spectra and EDS results of Fe-modified catalysts are shown in Figure 10 and Table 4. It could be seen that Ni (shown by arrows 1, 3, 5, 7, and 8) adhered to the surface of the CaO–Ca12Al14O33 matrix (shown by arrows 2, 4, 6, and 8) in a granular form. Fe was uniformly distributed in the CaO–Ca12Al14O33 matrix (shown by arrows 6 and 7), and different doping mass proportions of Fe had little effect on the distribution of the active component Ni.
FIGURE 10. SEM spectra of Fe-modified catalysts with different doping mass proportions: (A) 3%, (B) 6%, (C) 9%, and (D) 12%.
The oxide of Fe can be used as a catalyst for the reforming reaction, and its catalytic activity is lower than that of the Ni-based catalyst. For example, the active component of olivine is mainly Fe2O3. Ni and Fe can closely combine to form a Ni–Fe alloy and improve the stability of the catalyst. In addition, Fe doping in the catalyst can provide oxygen to neighboring nickel species and promote the oxidation of carbon, reducing the amount of carbon formation (Wang et al., 2011).
The effects of the modified catalysts on the H2 yield and concentration are shown in Figures 11A,B. From the figure, it is clear that the H2 yield and concentration gradually increased with the rise of the Fe doping proportion and then flattened out when the Fe doping proportion was over 9%. The H2 yield of the enhanced reforming can reach 85.54 and 85.80% at the doping proportions of 9 and 12%, respectively. The result corroborated that Fe doping in the catalyst (forming a Ni–Fe alloy) could improve the catalyst stability, which promoted the SR reaction for the hydrogen production. For the common reforming, the concentrations of the products were relatively stable over the catalysts with different Fe loads, around 73% for H2 and around 24% for CO2. However, for the enhanced reforming, the CO2 concentration showed an increasing trend with the increase in the Fe load, like the H2 yield, to some extent corroborating that doping Fe in the catalyst could promote the oxidation of CO.
FIGURE 11. Effect of the Fe-modified catalysts: (A) H2 yield, (B) H2 concentration, and (C) CO2 concentration.
In this article, the double-effect Ni-based catalysts, modified with Ce, Mg, and Fe and synthesized by the coprecipitation method, were applied into the enhanced steam reforming process of real tar. The effects of the catalysts with different doping mass proportions (3, 6, 9, and 12%) of Ce, Mg, and Fe on the H2 yield, and H2 and CO2 concentrations contrasted with those of the unmodified catalyst. The results revealed that the tar reforming efficiency was improved with appropriate proportion of the additives added. The Ce-doped catalyst, existing in the form of CeO2, could change the distribution of the active component Ni and promote the thermal cracking and SR reactions. The modified catalyst with 6% Ce doping The Mg-doped catalyst, existing in the form of MgO and MgNiO2, could change the morphology of Ni, increasing the catalytic area, which promoted the SR reaction. The best catalytic activity was obtained at 3% Mg doping, with the H2 yield reaching 85.22%. The Fe-doped catalyst, existing in the form of Fe2O3, could form a Ni–Fe alloy and improve the stability of the catalyst, and the modified catalyst with 9 and 12% Fe doping showed the better catalytic activity, with the H2 yield reaching 85.54 and 85.80%, respectively.
The original contributions presented in the study are included in the article/Supplementary Material; further inquiries can be directed to the corresponding authors.
PW and WZ conducted the experiments and wrote the manuscript. HX and ZY have corrected and edited the manuscript. MZ and ZW supported the project technically.
This research was financially supported by the Fundamental Research Funds for the Central Universities (N2025029), the National Natural Science Foundation of Liaoning Province (2019-MS-133), and the Open Project Program of Key Laboratory of Metallurgical Emission Reduction and Resources Recycling, Ministry of Education (Anhui University of Technology) (JKF19-06).
The authors declare that the research was conducted in the absence of any commercial or financial relationships that could be construed as a potential conflict of interest.
All claims expressed in this article are solely those of the authors and do not necessarily represent those of their affiliated organizations, or those of the publisher, the editors and the reviewers. Any product that may be evaluated in this article, or claim that may be made by its manufacturer, is not guaranteed or endorsed by the publisher.
Ashok, J., Kathiraser, Y., Ang, M. L., and Kawi, S. (2015). Bi-functional Hydrotalcite-Derived NiO-CaO-Al2O3 Catalysts for Steam Reforming of Biomass And/or Tar Model Compound at Low Steam-To-Carbon Conditions. Appl. Catal. B: Environ. 172-173, 116–128. doi:10.1016/j.apcatb.2015.02.017
Cai, W.-J., Qian, L.-P., Yue, B., and He, H.-Y. (2014). Rh Doping Effect on Coking Resistance of Ni/SBA-15 Catalysts in Dry Reforming of Methane. Chin. Chem. Lett. 25, 1411–1415. doi:10.1016/j.cclet.2014.06.016
Chan, F. L., and Tanksale, A. (2014). Review of Recent Developments in Ni-Based Catalysts for Biomass Gasification. Renew. Sust. Energ. Rev. 38, 428–438. doi:10.1016/j.rser.2014.06.011
Dou, B., Wang, C., Song, Y., Chen, H., Jiang, B., Yang, M., et al. (2016). Solid Sorbents for In-Situ CO 2 Removal during Sorption-Enhanced Steam Reforming Process: A Review. Renew. Sust. Energ. Rev. 53, 536–546. doi:10.1016/j.rser.2015.08.068
Duan, W., Yu, Q., Wang, K., Qin, Q., Hou, L., Yao, X., et al. (2015). ASPEN Plus Simulation of Coal Integrated Gasification Combined Blast Furnace Slag Waste Heat Recovery System. Energ. Convers. Manage. 100, 30–36. doi:10.1016/j.enconman.2015.04.066
Duan, W., Yu, Q., Wang, Z., Liu, J., and Qin, Q. (2018). Life Cycle and Economic Assessment of Multi-Stage Blast Furnace Slag Waste Heat Recovery System. Energy 142, 486–495. doi:10.1016/j.energy.2017.10.048
Duan, W., Yu, Q., Xie, H., and Qin, Q. (2017). Pyrolysis of Coal by Solid Heat Carrier-Experimental Study and Kinetic Modeling. Energy 135, 317–326. doi:10.1016/j.energy.2017.06.132
Furusawa, T., Saito, K., Kori, Y., Miura, Y., Sato, M., and Suzuki, N. (2013). Steam Reforming of Naphthalene/benzene with Various Types of Pt- and Ni-Based Catalysts for Hydrogen Production. Fuel 103, 111–121. doi:10.1016/j.fuel.2011.09.026
Gao, N., Liu, S., Han, Y., Xing, C., and Li, A. (2015). Steam Reforming of Biomass Tar for Hydrogen Production over NiO/ceramic Foam Catalyst. Int. J. Hydrogen Energ. 40, 7983–7990. doi:10.1016/j.ijhydene.2015.04.050
Gusta, E., Dalai, A. K., Uddin, M. A., and Sasaoka, E. (2009). Catalytic Decomposition of Biomass Tars with Dolomites. Energy Fuels 23, 2264–2272. doi:10.1021/ef8009958
Jiang, L., Hu, S., Wang, Y., Su, S., Sun, L., Xu, B., et al. (2015). Catalytic Effects of Inherent Alkali and Alkaline Earth Metallic Species on Steam Gasification of Biomass. Int. J. Hydrogen Energ. 40, 15460–15469. doi:10.1016/j.ijhydene.2015.08.111
Kimura, T., Miyazawa, T., Nishikawa, J., Kado, S., Okumura, K., Miyao, T., et al. (2006). Development of Ni Catalysts for Tar Removal by Steam Gasification of Biomass. Appl. Catal. B: Environ. 68, 160–170. doi:10.1016/j.apcatb.2006.08.007
Kinoshita, C. M., and Turn, S. Q. (2003). Production of Hydrogen from Bio-Oil Using CaO as a CO Sorbent. Int. J. Hydrogen Energ. 28 (10), 1065–1071. doi:10.1016/s0360-3199(02)00203-3
Koike, M., Li, D., Nakagawa, Y., and Tomishige, K. (2012). A Highly Active and Coke-Resistant Steam Reforming Catalyst Comprising Uniform Nickel-Iron alloy Nanoparticles. ChemSusChem 5, 2312–2314. doi:10.1002/cssc.201200507
Li, C., Hirabayashi, D., and Suzuki, K. (2009). A Crucial Role of O2− and O22− on Mayenite Structure for Biomass Tar Steam Reforming over Ni/Ca12Al14O33. Appl. Catal. B: Environ. 88, 351–360. doi:10.1016/j.apcatb.2008.11.004
Li, C., and Suzuki, K. (2010). Resources, Properties and Utilization of Tar. Resour. Conservation RecyclingConservation Recycling 54, 905–915. doi:10.1016/j.resconrec.2010.01.009
Li, D., Ishikawa, C., Koike, M., Wang, L., Nakagawa, Y., and Tomishige, K. (2013). Production of Renewable Hydrogen by Steam Reforming of Tar from Biomass Pyrolysis over Supported Co Catalysts. Int. J. Hydrogen Energ. 38, 3572–3581. doi:10.1016/j.ijhydene.2013.01.057
Li, D., Tamura, M., Nakagawa, Y., and Tomishige, K. (2015). Metal Catalysts for Steam Reforming of Tar Derived from the Gasification of Lignocellulosic Biomass. Bioresour. Technol. 178, 53–64. doi:10.1016/j.biortech.2014.10.010
Li, J., Tao, J., Yan, B., Jiao, L., Chen, G., and Hu, J. (2021). Review of Microwave-Based Treatments of Biomass Gasification Tar. Renew. Sust. Energ. Rev. 150, 111510. doi:10.1016/J.RSER.2021.111510
Mazumder, J., and de Lasa, H. I. (2015). Fluidizable La 2 O 3 Promoted Ni/γ-Al 2 O 3 Catalyst for Steam Gasification of Biomass: Effect of Catalyst Preparation Conditions. Appl. Catal. B: Environ. 168-169, 250–265. doi:10.1016/j.apcatb.2014.12.009
Mei, D., Lebarbier, V. M., Rousseau, R., Glezakou, V.-A., Albrecht, K. O., Kovarik, L., et al. (2013). Comparative Investigation of Benzene Steam Reforming over Spinel Supported Rh and Ir Catalysts. ACS Catal. 3, 1133–1143. doi:10.1021/cs4000427
Nakhaei Pour, A., and Mousavi, M. (2015). Combined Reforming of Methane by Carbon Dioxide and Water: Particle Size Effect of Ni-Mg Nanoparticles. Int. J. Hydrogen Energ. 40, 12985–12992. doi:10.1016/j.ijhydene.2015.08.011
Onozaki, M., Watanabe, K., Hashimoto, T., Saegusa, H., and Katayama, Y. (2006). Hydrogen Production by the Partial Oxidation and Steam Reforming of Tar from Hot Coke Oven Gas. Fuel 85, 143–149. doi:10.1016/j.fuel.2005.02.028
Richardson, Y., Blin, J., Volle, G., Motuzas, J., and Julbe, A. (2010). In Situ generation of Ni Metal Nanoparticles as Catalyst for H2-Rich Syngas Production from Biomass Gasification. Appl. Catal. A: Gen. 382, 220–230. doi:10.1016/j.apcata.2010.04.047
Sarıoğlan, A. (2012). Tar Removal on Dolomite and Steam Reforming Catalyst: Benzene, Toluene and Xylene Reforming. Int. J. Hydrogen Energ. 37, 8133–8142. doi:10.1016/j.ijhydene.2012.02.045
Tomishige, K., Kimura, T., Nishikawa, J., Miyazawa, T., and Kunimori, K. (2007). Promoting Effect of the Interaction between Ni and CeO2 on Steam Gasification of Biomass. Catal. Commun. 8, 1074–1079. doi:10.1016/j.catcom.2006.05.051
Torres, W., Pansare, S. S., and Goodwin, J. G. (2007). Hot Gas Removal of Tars, Ammonia, and Hydrogen Sulfide from Biomass Gasification Gas. Catal. Rev. 49, 407–456. doi:10.1080/01614940701375134
Virginie, M., Adánez, J., Courson, C., De Diego, L. F., García-Labiano, F., Niznansky, D., et al. (2012). Effect of Fe-Olivine on the Tar Content during Biomass Gasification in a Dual Fluidized Bed. Appl. Catal. B: Environ. 121-122, 214–222. doi:10.1016/j.apcatb.2012.04.005
Wang, L., Li, D., Koike, M., Koso, S., Nakagawa, Y., Xu, Y., et al. (2011). Catalytic Performance and Characterization of Ni-Fe Catalysts for the Steam Reforming of Tar from Biomass Pyrolysis to Synthesis Gas. Appl. Catal. A: Gen. 392, 248–255. doi:10.1016/j.apcata.2010.11.013
Wang, L., Li, D., Koike, M., Watanabe, H., Xu, Y., Nakagawa, Y., et al. (2013). Catalytic Performance and Characterization of Ni-Co Catalysts for the Steam Reforming of Biomass Tar to Synthesis Gas. Fuel 112, 654–661. doi:10.1016/j.fuel.2012.01.073
Wang, T., Chang, J., Cui, X., Zhang, Q., and Fu, Y. (2006). Reforming of Raw Fuel Gas from Biomass Gasification to Syngas over Highly Stable Nickel-Magnesium Solid Solution Catalysts. Fuel Process. Technol. 87, 421–428. doi:10.1016/j.fuproc.2005.10.006
Xie, H., Yu, Q., Yao, X., Duan, W., Zuo, Z., and Qin, Q. (2015). Hydrogen Production via Steam Reforming of Bio-Oil Model Compounds over Supported Nickel Catalysts. J. Energ. Chem. 24, 299–308. doi:10.1016/S2095-4956(15)60315-1
Xie, H., Yu, Q., Zhang, J., Liu, J., Zuo, Z., and Qin, Q. (2016a). Preparation and Performance of Ni-Based Catalysts Supported on Ca12 Al14 O33 for Steam Reforming of Tar in Coke Oven Gas. Environ. Prog. Sust. Energ. 36, 729–735. doi:10.1002/ep.12509
Xie, H., Yu, Q., Zuo, Z., Han, Z., Yao, X., and Qin, Q. (2016b). Hydrogen Production via Sorption-Enhanced Catalytic Steam Reforming of Bio-Oil. Int. J. Hydrogen Energ. 41, 2345–2353. doi:10.1016/j.ijhydene.2015.12.156
Xie, H., Yu, Q., Zuo, Z., Zhang, J., Han, Z., and Qin, Q. (2016c). Thermodynamic Analysis of Hydrogen Production from Raw Coke Oven Gas via Steam Reforming. J. Therm. Anal. Calorim. 126, 1621–1631. doi:10.1007/s10973-016-5638-9
Xie, H., Zhang, J., Yu, Q., Zuo, Z., Liu, J., and Qin, Q. (2016d). Study on Steam Reforming of Tar in Hot Coke Oven Gas for Hydrogen Production. Energy Fuels 30, 2336–2344. doi:10.1021/acs.energyfuels.5b02551
Xie, H., Zhang, W., Zhao, X., Chen, H., Yu, Q., and Qin, Q. (2018). Sorption-enhanced Reforming of Tar: Influence of the Preparation Method of CO2 Absorbent. Korean J. Chem. Eng. 35, 2191–2197. doi:10.1007/s11814-018-0136-3
Yue, B., Wang, X., Ai, X., Yang, J., Li, L., Lu, X., et al. (2010). Catalytic Reforming of Model Tar Compounds from Hot Coke Oven Gas with Low Steam/carbon Ratio over Ni/MgO-Al2O3 Catalysts. Fuel Process. Technol. 91, 1098–1104. doi:10.1016/j.fuproc.2010.03.020
Zamboni, I., Courson, C., and Kiennemann, A. (2011). Synthesis of Fe/CaO Active Sorbent for CO2 Absorption and Tars Removal in Biomass Gasification. Catal. Today 176, 197–201. doi:10.1016/j.cattod.2011.01.014
Zeng, X., Wang, F., Sun, Y., Zhang, J., Tang, S., and Xu, G. (2018). Characteristics of Tar Abatement by thermal Cracking and Char Catalytic Reforming in a Fluidized Bed Two-Stage Reactor. Fuel 231, 18–25. doi:10.1016/j.fuel.2018.05.043
Zhang, W., Xie, H., Wang, P., Li, R., Yu, Z., and Yu, Q. (2021a). Steam Reforming of Tar from Raw Coke Oven Gas over Bifunctional Catalysts: Effects of Preparation Parameters on CO 2 Adsorption Performance. Environ. Prog. Sust. Energ. 40, e13506. doi:10.1002/ep.13506
Zhang, W., Xie, H., Yu, Z., Wang, P., Wang, Z., and Yu, Q. (2021b). Steam Reforming of Tar from Raw Coke Oven Gas over Bifunctional Catalysts: Reforming Performance for H 2 Production. Environ. Prog. Sust. Energ. 40, e13501. doi:10.1002/ep.13501
Zuo, Z., Luo, S., Liu, S., Zhang, J., Yu, Q., and Bi, X. (2021). Thermokinetics of Mass-Loss Behavior on Direct Reduction of Copper Slag by Waste Plastic Char. Chem. Eng. J. 405, 126671. doi:10.1016/j.cej.2020.126671
Keywords: tar, double-effect catalyst, CO2 adsorption, enhanced reforming, hydrogen production
Citation: Wang P, Zhang W, Yu Z, Xie H, Zhou M and Wang Z (2021) Enhanced Reforming of Tar Based on Double-Effect Ni/CaO–Ca12Al14O33 Catalysts: Modified by Ce, Mg, and Fe. Front. Energy Res. 9:729919. doi: 10.3389/fenrg.2021.729919
Received: 24 June 2021; Accepted: 06 September 2021;
Published: 06 October 2021.
Edited by:
Akshat Tanksale, Monash University, AustraliaCopyright © 2021 Wang, Zhang, Yu, Xie, Zhou and Wang. This is an open-access article distributed under the terms of the Creative Commons Attribution License (CC BY). The use, distribution or reproduction in other forums is permitted, provided the original author(s) and the copyright owner(s) are credited and that the original publication in this journal is cited, in accordance with accepted academic practice. No use, distribution or reproduction is permitted which does not comply with these terms.
*Correspondence: Huaqing Xie, aHVhcWluZ18yMDA4QDE2My5jb20=; Mi Zhou, emhvdW1AbWFpbC5uZXUuZWR1LmNu
Disclaimer: All claims expressed in this article are solely those of the authors and do not necessarily represent those of their affiliated organizations, or those of the publisher, the editors and the reviewers. Any product that may be evaluated in this article or claim that may be made by its manufacturer is not guaranteed or endorsed by the publisher.
Research integrity at Frontiers
Learn more about the work of our research integrity team to safeguard the quality of each article we publish.