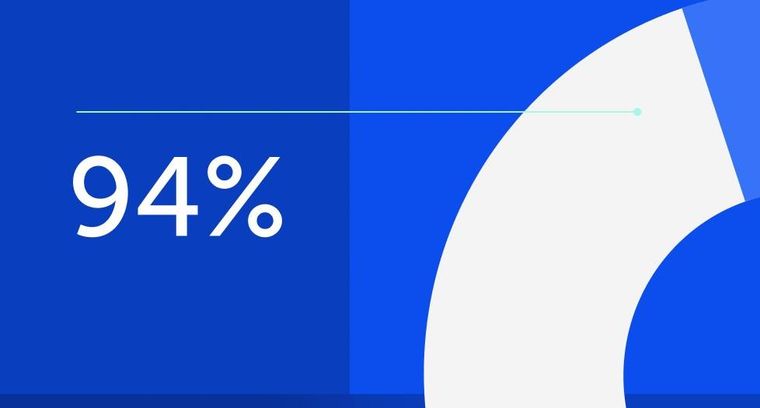
94% of researchers rate our articles as excellent or good
Learn more about the work of our research integrity team to safeguard the quality of each article we publish.
Find out more
ORIGINAL RESEARCH article
Front. Energy Res., 01 September 2021
Sec. Smart Grids
Volume 9 - 2021 | https://doi.org/10.3389/fenrg.2021.721385
This article is part of the Research TopicAdvanced Optimization and Control for Smart Grids with High Penetration of Renewable Energy SystemsView all 49 articles
In the current distribution network, photovoltaic, wind power, energy storage, and other distributed energy are widely connected, and the proportion of generalized DC load is rapidly increasing. With the development of power electronics technology, using multi-port power electronic transformer (PET) to achieve high-efficiency access of large-capacity AC/DC source and load is the current research hotspot, and AC / DC hybrid power supply is inevitable. The introduction of a large number of power electronics and the flexible coordinated control and complementary fault-tolerant advantages of PET bring challenges to the operation and maintenance management of the AC/DC hybrid power system. In this paper, the structure of the AC/DC hybrid power system with the multi-port PET cluster is introduced. Based on the idea of hierarchical and partitioned control, a three-layer and multi-time scale control mode of integrated automation system, PET cluster and PET controller is proposed; Aiming at the problem of reliability evaluation, a sequential Monte Carlo simulation method is proposed to simulate the AC/DC hybrid power system with the multi-port PET cluster. The influence of multi-port PET parallel cluster mode and port capacity limitation on the reliability of the power system is analyzed, and the effectiveness of the model and algorithm is verified. Finally, an example is given to verify that the proposed structure is conducive to improving the utilization level of renewable energy in the distribution network.
With the rapid increase of the proportion of generalized DC load, the long-term coexistence of AC load in a certain period in the future, and the increase of the proportion of new energy, the AC/DC hybrid power system may accept more types of source load and larger capacity in the future. The AC/DC hybrid system needs enough power supply capacity and power supply radius to meet the demand of rapid load growth and realize high-efficiency access of large-capacity AC/DC source and load. The integration of different AC/DC loads and distributed renewable energy makes the power flow direction of the whole system more complex and energy management more challenging. If the energy management of the system and the passive mode switching of the equipment are realized by the system level control, the calculation of the system control is large, the communication delay will greatly affect the energy efficiency of the system, and the system will be paralyzed when the communication is interrupted. With the development of power electronics technology, which provides the hardware foundation for the integration of new energy and different types of loads into the distribution system. Considering the randomness and volatility of distributed generation and the diversity of user side load, it has become an important research direction to integrate AC, DC power, and load into AC/DC hybrid power system through multi-port PET with different voltage level ports.
The traditional operation mode of distribution network is dominated by the supplier and one-way radial power supply. It has a top-down one-way supply-demand relationship with the transmission network, and its function and structure are still relatively single. However, with the high proportion of new energy and electric vehicles with volatility and randomness, and all kinds of controllable AC and DC load access, the traditional distribution network fails to fully consider this factor in the configuration optimization and operation management stage, resulting in the actual operation of the traditional distribution network not being able to well adapt to the user’s requirements for power supply reliability, environmental protection, and power quality of the distribution network (Huang et al., 2011; Pilo et al., 2011; Wang, 2014; Zha et al., 2014).
In order to solve a series of problems caused by distributed renewable energy access, improve the level of power quality, and improve the utilization efficiency of renewable energy, the concept of integrated energy subnet came into being. The integrated energy sub-network includes electricity, heat, cold, gas, and other energy forms, and the power collector constructed by flexible switchgear is used for unified management (Duan et al., 2016; Zhang et al., 2017; Dolatabodi et al., 2018; Miao et al., 2018). Distributed energy access, energy storage control, power quality management, power flow control, and other functions are managed by the power collector, which has the advantages of modularization and centralization. However, multiple energy sources are coupled and interact in the integrated energy sub network, which has different time scales, and its transient characteristics are more complex. Therefore, the integrated energy subnet is a new way to integrate distributed energy access, but the accompanying problems to be solved include optimal operation and fault protection (Dolatabodi et al., 2018).
In addition to the integrated energy sub-grid, it is also an effective method for distributed renewable energy to be connected to the distribution network through the microgrid (Funabashi and Yokoyama, 2006; Barnes et al., 2007; Hatziargyriou et al., 2007; Salonen et al., 2008; He et al., 2020). By integrating the distributed generation, energy storage unit, and local load, an independent microgrid that can be connected to the grid and operated off the grid has been widely studied, and it has been widely used in remote mountainous areas, independent islands, and other areas that are difficult to be covered by the large power grid.
AC distributed generation can be connected to a common coupling point through a grid connected inverter and transformer, and DC distributed generation and energy storage equipment can be connected to the AC/DC microgrid through DC line and rectifier. In Yin et al. (2012), the structure design of the AC/DC hybrid microgrid is studied, and its key technology and development direction are summarized. In Xiang et al. (2017), the influence of distributed generation, energy storage, load, and power converter on the stability of AC/DC microgrid is considered, and the method to improve the system stability is proposed. The control strategy of the AC/DC microgrid is studied in Dragicevic et al. (2014). Due to the existence of multi-level and various types of power conversion devices in AC/DC microgrid, on the one hand, it reduces the energy utilization efficiency of the system and, on the other hand, it makes the control system more complex and difficult to control the power quality, which is not conducive to the unified deployment of the system. Eghtedarpour and Farjah (2014) introduce a design scheme of AC/DC hybrid microgrid using PET and studies its operation mode and the switching strategy between each operation mode. Boroyevich et al. (2010) study the coordinated control strategy of PET and energy storage equipment, which improves the stability of the system.
At the same time, the research on structure design (Wang et al., 2015; Xiao, 2015), stability (Sanchez and Molinas, 2015; Pu et al., 2018; Wan et al., 2019), DC voltage control strategy (Dragicevic et al., 2014; Eghtedarpour and Farjah, 2014; Gao et al., 2017), and energy and power control strategy (Gao et al., 2017) has been widely carried out in the field of microgrid. AC/DC technology can improve the utilization efficiency of new energy to a certain extent but hesitates to limit the access capacity of microgrid. The access capacity of new energy is usually relatively small and does not support the power coordination optimization and adjustment control among multiple regions, which is limited by the popularization of this technology. At the same time, domestic and foreign scholars further proposed the AC/DC hybrid system based on PET (Huang et al., 2011), which can integrate a variety of distributed renewable energy in multiple voltage level systems of multiple AC/DC regions. In Yan et al. (2017), a hierarchical hybrid distribution system structure based on AC/DC converter is proposed. A construction scheme of AC/DC hybrid distribution network is proposed in Ma et al. (2015).
Through PET, a variety of new energy and AC/DC loads are connected to the distribution network to form a flexible and controllable new AC/DC hybrid distribution network, which makes the future distribution network develop into an information physical system with high integration of information and physical power grid for power and information integrated services (Pilo et al., 2011). At the same time, it can meet a variety of energy demands of users and allow new energy and power grid with random and fluctuation energy consumption platform with a high proportion of electric vehicle load and DC load controlled by users and stable operation (Zha et al., 2014).
Compared with the traditional distribution network, AC/DC hybrid distribution system has the advantages of reducing power supply cost, improving power supply reliability, improving power quality and reducing reactive power loss. The reliable operation of the distribution network is the basic guarantee for the stable supply of power.
However, up to now, with the rapid development of the national economy, China’s power load is showing a trend of continuous growth, followed by the increasingly prominent contradiction between power supply and demand, It is very important to study the reliability of power system. In recent years, China has done a lot of research work on the optimal design and reasonable planning of the distribution network, and the reliability management is also carried out in an organized and planned way, in order to promote the development of distribution network reliability research (Liu, 2011; Peng, 2018).
In the reliability evaluation of the distribution network, the reliability analysis methods can be divided into analytical method and Monte Carlo method. The calculation amount of the analytical method will increase rapidly with the increase of system complexity or system accident dimension, so this method is generally only applicable to the reliability analysis of some simple systems. The commonly used reliability analytical methods are divided into the following categories (Zhang and Wang, 2004), such as failure mode and consequence analysis method, network equivalence method, minimum path method, Bayesian network-based evaluation algorithm, fault diagnosis method, fault diagnosis method and so on Vector method and analytic method are intuitive, easy to understand, and easy to solve by computer programming (Zhang and Alabdulwahab, 2017). For single fault or relatively small state space, the analytical method is very effective in most cases. When considering the multi-dimensional events or high failure rate, the computational complexity of the analytical method will be greatly improved. The analytic method can be used to evaluate the expected value and load point of the system reliability index. The main advantages of the analytical method are being easy to understand, clear concept, and strong practicability of the model (Zheng, 2011).
Monte Carlo method, also known as statistical test method or random sampling technique, is based on probability and expected value. When using Monte Carlo method for simulation calculation, the most important thing is to use the computer to randomly sample the fault state of each component, and then accumulate the reliability index of the system (Zhang, 2019). Among them, the sequential Monte Carlo method can accurately simulate the duration of distribution system in different states. Because it does not consider the timing information, compared with sequential Monte Carlo method, its calculation speed is faster and the model is simpler. It is only suitable for short-term field and large-scale circuit system evaluation projects which require higher calculation speed. How to improve the non-sequential Monte Carlo method on the basis of ensuring the convergence speed and storage capacity has become the main research direction of many scholars(Eicha, 2004; Fecci, 2014).
The randomness and volatility of new energy on the power supply side pose a challenge to the reliable power supply of the power grid. On the load side, a large number of data centers will become the typical DC load in the future power grid. The requirements for power supply reliability of the power system are very strict. The scientific research and reasonable planning of distribution network reliability need to be paid enough attention to. At the same time, with the increasing complexity of the urban distribution system, the reliability analysis of the distribution system plays an increasingly important role in the reasonable design and planning of the whole power grid. It is a difficult problem to solve the reliability calculation problem of the AC/DC hybrid distribution system with the multi-port power cluster.
AC/DC hybrid system needs enough power supply capacity and power supply radius to meet the demand of rapid load growth and realize high-efficiency access of large capacity AC/DC source and load. The integration of different AC/DC loads and distributed renewable energy makes the power flow direction of the whole system more complex and energy management more challenging. Based on the above reasons, the coordinated control and flexible complementary fault tolerance of PET can be considered to optimize the AC/DC hybrid system.
As shown in Figures 1A,B, they are typical structures of three-port PET and four-port PET, respectively. They have medium voltage AC port ACM, medium voltage DC port DCM, and low-voltage AC port ACL, respectively. Four-port PET leads out one low-voltage DC port DCL more than three port PET. ACM port is composed of voltage source converter (VSC) and dual active bridge converter (DAB), DCM is composed of DAB, ACL is composed of VSC, and DCL is led out from PET internal common bus to form low-voltage DC port.
FIGURE 1. Equivalent structure model of four-port PET. (A) Equivalent structure model of three-port PET. (B) Equivalent structure model of four-port PET.
Each port of multi-port PET is connected with the external AC/DC new energy power supply, energy storage, load, and traditional distribution network to form an AC/DC hybrid power system with multi-port PET. The external power grid, new energy, and AC/DC load can be connected to the AC/DC hybrid system through the PET port. The structure has abstracted the internal bus structure; the part from bus to each port is replaced by efficiency module, which shows that multi-port PET is easy to realize modularization and expand ports flexibly, which is convenient for different types and voltage levels of power grid access.
For the AC/DC hybrid system, PET is the core equipment to realize energy conversion. The PET based on cascaded H-bridge (CHB) structure can not only meet the demand of high voltage and large capacity but also provide a high voltage DC port. It has the basic demand of multi-port for power routing and can face the flexible networking of energy Internet. Based on the flexible networking features of cascaded H-bridge power electronic transformers, the concept of “cluster” is introduced on the basis of dual power single bus topology.
Each PET operates autonomously with source and load as a “set,” and two or more power electronic transformers are combined with energy ports and interconnected to form a “cluster.” PET cluster control is to make the cluster have the function of flexible power routing and efficient energy management through active coordination control. Through the PET cluster networking and cluster control, the reliability of load power supply, system operation flexibility, and redundancy scalability can be improved.
With PET cluster, the AC/DC hybrid system has the following advantages:
1) Plug and play, increase system power supply capacity and power supply radius
The parallel operation of several power electronic transformers can increase the power supply capacity of the system. After cluster networking, multiple power electronic transformers in different parks are hot standby for each other, and the energy can flow freely in the AC/DC hybrid system, which can increase the power supply radius and reduce the power transmission loss of central power supply, which is in line with the characteristics of plug and play.
2) Enhance capacity scalability and reduce total reserve capacity
The construction of cluster system relies on the combination of energy ports and information interconnection network, and the most basic is the modular design and multi-parallel technology. The power conversion modules of the same type of PET can be combined, which can easily expand or reduce the capacity and reduce the total reserve capacity.
3) Improve the reliability of power supply
N power electronic transformers in different parks are connected by AC/DC bus, with one host and N-1 slaves. If the slave fails, the system can still provide voltage reference by the host. If the total capacity of PET is enough, the whole system can still operate. If the host fails, one of the slaves must change the operation mode to provide voltage reference for the system. When a single PET fails or is overhauled, the power electronic transformers in other parks can provide power support, which can greatly improve the reliability of the power supply.
4) Improve operation economy
The distributed energy management technology can be used to manage the power electronic transformers in different parks, and then the global energy coordination can be realized through the system level controller. The loss and efficiency of a single PET are non-linearly related to its load rate. The power distribution of each PET in the system can be optimized by cluster control to minimize the total loss of n power electronic transformers and make the system run in the optimal condition.
5) Reliable fault tolerance and active mode switching of power electronic transformer
There is direct communication and state feedback between multiple power electronic transformers, and the master-slave mode can be switched online without system level controller.
6) The communication is interrupted and the system is still running
When the system communication is interrupted/failed, the system can turn into non-integrated system operation, and the system operation control is realized by the PET cluster.
Based on the above analysis, a two-stage AC/DC hybrid power distribution system based on PET cluster is proposed, which includes 10 kV AC and 10 kV DC distribution level, and 380 V AC and 380 V DC distribution level ±. The 375 V DC power consumption level is shown in Figure 2.
This structure has the following advantages:
1) Through the PET cluster networking mode, improve the operation reliability and economy;
2) According to the capacity of renewable energy, different voltage levels can be flexibly selected to save cost and reduce loss;
3) Through 10 kV DC, the two stations can operate in a closed loop to improve the reliability of the power supply. At the same time, as a power ride through channel, load balancing can be realized.
The multi-port PET cluster AC/DC hybrid power system, based on the idea of hierarchical control, adopts three-layer control mode: integrated automation system, PET cluster controller and PET controller. The integrated automation system is mainly responsible for the overall scheduling of multiple PET cluster controllers, solving the exchange of power, voltage, frequency and other information between the cluster controller and the external power grid, which can realize power optimization control, voltage dynamic control, frequency secondary regulation, system recovery after failure, etc; PET cluster controller is mainly responsible for coordinating and managing each PET in the cluster, formulating operation strategy and distributing it to the PET in the cluster, which can realize fault-tolerant switching, n-1 load transfer, PET re putting into operation, etc; PET controller is mainly responsible for executing the upper control instructions and completing its own optimization operation. The control architecture adopts multi-layer division of labor, which can improve the control robustness of the system, and simplify the direct information interaction and data processing between the integrated automation system and PET.
As shown in Figure 2, the operation control objective of the AC/DC hybrid power system is generally applicable to the coordinated control of the simple system. However, for the complex AC/DC hybrid power system with multi-bus, multi-port PET cluster, this structure has certain limitations, which lead to the simple system energy management system and the inability to realize the economic operation of the system.
Therefore, the hierarchical control system as shown in Figure 3 is introduced into the control of the AC/DC hybrid distributed system with multi-port PET as shown in Figure 2. The device level control (corresponding to the first level control) and system level control (corresponding to the second and third level control) strategies are implemented at different levels to realize the standardization and scalability of the AC/DC hybrid power system and improve the overall performance of the system.
The first layer mainly realizes the device level control, in which the AC/DC bus voltage control is the core. According to the different AC/DC bus voltage control strategies, this layer can be divided into master-slave control and peer-to-peer control. Taking the DC bus voltage control as an example, in the master-slave control strategy, there is usually only one unit in the system to control DC bus voltage. If the unit fails, the DC sub-network will lose the power balance unit, which may cause the DC bus voltage out of control and system collapse. Therefore, the reliability of the master-slave control strategy is poor, which is more suitable for the application of the simple AC/DC hybrid distributed system.
In order to improve the operation reliability of the bus voltage control system in a complex AC/DC hybrid distributed system, an equivalent control strategy can be adopted for DC bus voltage control. In this control mode, many units or devices are participating in the DC bus voltage control in the system. These units are called the main control unit and have equal status in the control function. The droop control with plug and play characteristics is an effective way to realize the equivalent control strategy. As shown in Figure 4, the two distributed generators adopt DC bus voltage output power (Udc-p) droop control mode and droop control characteristic curve of the main control unit. Each main control unit controls DC bus voltage only by injecting local information such as DC bus power and output port DC voltage. In order to cope with the load change in the DC sub-network and the output power fluctuation of the other distributed generation, even if a main control unit in the system is out of operation due to fault, the DC sub-network can still maintain the system stability through the other main control units, so the power supply reliability of the system is improved.
Due to the steady-state deviation of DC voltage and the power sharing problem of multiple main control units in the AC/DC hybrid power supply unit, the secondary coordination control strategy suitable for the AC/DC hybrid system is introduced, as shown in Figure 5. At present, according to the different communication and control modes, the research on the secondary coordination control strategy of AC/DC hybrid distributed system can be divided into three categories.
In this structure, the secondary coordinated control of the AC/DC hybrid power system is realized by a centralized controller. As shown in Figure 5, the secondary centralized controller detects the DC bus voltage and the output power of each main control unit participating in the DC bus voltage control, then performs the corresponding DC bus voltage recovery and current sharing control algorithm of each unit output, and adjusts the droop curve set point or droop coefficient and other control parameters of the droop control system of each main control unit to achieve the corresponding control purpose. In the secondary control system, PI regulation is used to compensate for the bus voltage drop caused by droop control and improve the bus voltage to normal level. But the biggest defect of centralized control is that if the secondary centralized controller of AC/DC hybrid distributed system fails, the system will not be able to complete the secondary coordinated control function, so the reliability is low.
In order to improve the reliability of the secondary control system, the secondary coordinated control strategy of centralized communication and distributed control is adopted as shown in Figure 6. This method is different from the centralized controller shown in Figure 5. The secondary controller is embedded in the local controller of each main control unit, and the information it receives through the communication bus is no longer the droop control parameter reference value adjustment instruction issued by the centralized controller, but the DC voltage and voltage at the outlet of other main control units in the AC/DC hybrid distributed system output power and other primary measurement information. Although the secondary control also needs to obtain the global information of the DC distributed system, the secondary coordinated control algorithm is implemented in the local controller of each main control unit. Therefore, compared with the centralized control system structure, the reliability of this method will be improved. However, the secondary controller of each main control unit needs to obtain the relevant data information of other main control units in order to realize the secondary control algorithm and provide a reference value for the bottom droop control. Therefore, this method requires high reliability of communication network, and with the increase of the scale of AC/DC hybrid distributed system, the pressure of communication network will increase, which may affect the performance of secondary coordinated control.
Distributed coordination control (DCS) refers to the more complex tasks that each main control unit updates its output state through local control based on its own and neighboring unit data information. Based on the above thought, in order to realize the secondary voltage recovery and current sharing control objectives of the AC-DC hybrid distributed system, each main control unit only communicates with neighboring nodes, and its basic control structure is shown in Figure 7.
In the future AC/DC hybrid distributed system, distributed energy storage unit, controllable distributed generation, even wind and other distributed random intermittent generation may be used as the main control unit to actively participate in the DC bus voltage control. If the interface of different types of power supply or converter adopts the equivalent control mode, in order to achieve economic operation, it often needs to accept the scheduling of the upper energy management system. The upper energy management system can often adjust the voltage reference set point or droop coefficient in the droop control curve of each unit in the AC/DC distributed system, Thus, the output level of different distributed generation or power flow controller can be adjusted to ensure the overall optimal operation of AC/DC hybrid power system.
The third layer control of AC/DC hybrid distributed system is energy optimization operation and integrated monitoring system. The purpose is to make decisions according to different optimal operation objectives and beam conditions according to the data of distributed power output prediction, load demand, operation status of the energy storage system, and market information and make real-time operation scheduling strategy of AC/DC hybrid distributed system. The flexible dispatching of distributed power supply, energy storage system, load output, and AC/DC system switching power is realized to ensure the safe and economic operation of the system. A reasonable energy management strategy is an important guarantee for the effective utilization of renewable energy and the safe and optimized operation of the system in AC DC hybrid distributed system, as shown in Figure 8.
FIGURE 8. schematic diagram of hybrid hierarchical control combining centralized and distributed control.
As the top energy management system, its structure mainly includes centralized and distributed. Centralized energy management system is monitored and controlled by a unified central controller, which is simple in structure and easy to realize, but it lacks redundancy and high dependence on central controller and reliability is not high enough; Distributed control is usually controlled by multi-agent, which is easy to implement plug and play, but lack of unified coordination and management, and requires higher requirements for distributed optimization operation algorithm.
According to different operation control requirements, the control time scales corresponding to different objects are determined, so as to build a multi-scale scheduling system and locate the specific functions of different devices and different levels.
In the third section, the hierarchical control strategy corresponds to the equipment layer, the coordination control layer, and the optimal scheduling layer of the system. Therefore, three levels of time scale control are set.
Considering the operation control requirements of three levels, the corresponding operation control time scales of equipment level, coordination control level, and optimization dispatching level are ≤100 ms, (100 ms, 5s), and (5s, 15 min). Through the organic cooperation of multiple time scales, the overall operation control efficiency can be effectively improved, and the system operation can be optimized. The main function design involved in each layer of control is described in detail as follows.
The main part of equipment layer ≤ 100 ms level control mainly includes distributed renewable energy, energy storage, load, power electronic voltage regulator, fault current controller and other primary equipment. It mainly involves the autonomous operation of primary equipment ontology, ontology protection and master-slave / peer-to-peer control of PET cluster.
The 100 ms-5 s level control in coordination control layer mainly includes multi-functional coordination control system, regional local controller, AC protection device, DC protection device and other equipment. It mainly involves secondary control of voltage and frequency, smoothing filter control of new energy power below second level, multi pet coordination control, power regulation control, tie line control and system start-up and stop control.
The coordination and control layer is mainly responsible for cooperating with the equipment layer to solve the control requirements within the time range of 100 ms-5 s, and coordinating and controlling layer to help the equipment layer complete the transition of emergency. Taking PET cluster control as an example, when the cluster operates in master-slave mode, if the slave machine fails, the system can still provide voltage reference by the host machine. If the total capacity of PET is enough, the whole system can still operate. If the host machine fails, one of the slave machine must change the operation mode to provide voltage reference for the system. When a single PET fails or is overhauled, the PET in other parks can provide power support, which can greatly improve the reliability of power supply.
The 5 s-15 min level control of optimal dispatching layer is mainly the overall optimal dispatching of “source-network-load-storage” of the whole system, which mainly involves planning curve, peak shaving and valley filling, early warning analysis, prediction, power flow optimization and multi energy complementary control. In this paper, the power flow optimization control is mainly realized by adjusting the power of each port of the multi-functional PET, and the power control is realized by adjusting the output of various distributed generation.
The reliable operation of the distribution network is the basic guarantee for the stable supply of power, and it undertakes the important task of transmitting power from the power supply and the grid to the users. How to effectively evaluate the power supply reliability of the AC/DC hybrid distribution network with a multi-port PET cluster is a new problem.
For the reliability modeling of PET, as shown in Figure 9, it has 10 kV AC, 10 kV DC ±. It has four ports of 375 V DC and 380 V AC, which can convert medium voltage AC or DC power into low-voltage DC or AC power. In order to calculate the power supply reliability of the structure PET, we can first analyze the failure rate from the 10 kV AC port to the 10 kV DC port and then calculate the power supply reliability of other ports in the same way.
The topology of 10 kV AC-10 kV DC port is shown in Figure 10, which is composed of six parts in series (Zhang and Wang, 2004):
1) Single phase bridge full control rectifier and inverter circuit (AC/DC, DC/AC);
2) Transformer primary side series inductance L;
3) High frequency transformer (T);
4) Single phase bridge full control rectifier circuit (AC/DC);
5) Filter capacitor C;
6) The reliability evaluation model of C and P is shown in Figure 11.
By calculating the power supply reliability of each module in Figure 11, through series and parallel, the 10 kV AC-10 kV DC port can be calculated. Further, the reliability data of each port can be calculated as shown in Figure 12.
Figure 13 shows a comparison of the calculation of the system reliability for the contained and reliable data.
According to the actual power supply network obtained from the power system of the data center, the use of PET is two PET parallel operations, which form a cluster operation mode and jointly supply power for the load point and energy storage equipment. Figure 14 shows the reliability block diagram of two PET cluster operation.
In Figure 14, L1 is the 10 kV AC bus, L2 is the 10 kV DC bus, L4 is the power supply ±375 DC bus, L3 is 380 three-phase AC bus, T1-1/T2-1 is PET 10 kV AC port, T1-2/T2-2 is PET 10 kV DC port, T1-3/T2-3 is 380 V AC port, T1-4/T2-4 is 375 V DC port, Z1/Z2 is reactor, and DC1/DC2 is load step-down converter.
The reliability solution formula of the system can be deduced from the function logic connection relationship of the components shown in Figure 14.
The sequential Monte Carlo method is used to calculate the power supply reliability of the multi-port PET AC/DC hybrid system with different structures. Combined with the idea of searching the power supply path of load point, the random number with the same number of system components is generated for random sampling to simulate the operation state of the power system, and the second-order fault and load transfer state of the system are accurately described and calculate the reliability of the power system.
According to the main electrical wiring diagram of the demonstration site in the data center, there are n = 26 components in the system. The failure rate and repair time data of all components are obtained, and the failure rate of the ith component is recorded as λ i. The repair rate of the ith component is recorded as μ i, where I = 1, 2, 3, 4, ... ,n.
The main process of simulating the actual operation of the distribution network based on the sequential Monte Carlo method is as follows, and the corresponding flow chart is shown in Figure 15.
1) Input the original parameter data of each component in the distribution network, and complete the initialization work. In this paper, the number of load points is ntrans = 4 and the number of components is n = 26. Table 2 shows the failure rate and repair time data for all components.
The simulation time is set as the actual operation time of distribution network. The initialization work is to initialize the simulation time summttf, fault number ftimes, fault time, annual fault rate, fault duration and annual fault time to 0.
2) The quantity of random numbers is the same as the quantity of components. Due to the second-order fault, 226 random numbers are generated, which are recorded as R1 and R2 respectively
3) According to the generated two groups of random numbers, the corresponding MTTF of two groups of 26 components is obtained.
4) The minimum value of each group of data is found by using the calculated no fault working time, so as to determine two faulty components, and the smaller value of the two is included in the simulation time summttf.
5) Two random numbers are generated again to obtain the repair duration MTTR of the two faulty components. The larger value is obtained by comparing the two, which is used to calculate the repair time and related indicators of the load point.
6) By using the transformed power supply path, the fault type is judged, the first-order fault and the second-order fault are judged respectively, and whether the load transfer conditions are met is classified and calculated.
7) Judge whether the simulation time summttf meets the preset running time requirements. If it is less than the set running time, turn to 2; otherwise, proceed to the next step.
8) The outage indexes of all load points are accumulated, and the reliability indexes of the whole distribution system are calculated.
FIGURE 15. Simulation calculation of power supply reliability based on the sequential Monte Carlo method.
As shown in Figure 13, in the structure diagram of the AC/DC power system, all kinds of components and logic connection modes need to be considered in the process of system reliability analysis. Two four-port power electronic transformers form a cluster group to supply power for a group of DC load and AC load at the same time. Therefore, there are two power supply paths for each load point.
The annual failure rate, repair time, and other reliability data of each power supply module in the AC/DC hybrid system are shown in Table 2 with reference to the statistical data. PET port capacity and load are given in Table 3.
According to the data in the table, in the actual power system, when the load transfer occurs at the low-voltage DC load point due to fault, the capacity of a single PET port can support 100% load normal operation; when the load transfer occurs at the low-voltage AC load point due to fault, the capacity of a single PET port can support 70% load normal operation; then, the power loss percentage is 0.3 of the total load at the load point.
Under the condition that the original parameters of all components, port capacity, and load capacity are known, simulation of 100000 h operation time of distribution network is conducted.
Since the load amount of load transfer due to fault is determined by the maximum capacity of each port, with the minimum of 50% and the maximum of 100%. A total of six groups of power system outage indicators and reliability related data are generated, as shown in Table 4 and Figures 16–19.
By comparing the chart data, it can be concluded that the port capacity has a positive correlation with the reliability indicators. The larger the port capacity is, the higher the system availability ASAI is, and the lower the SAIFI, SAIDI, CAIDI, and other related indicators are. Compared with the results of qualitative analysis, when the port capacity is larger, the power loss caused by a component failure at each load point will be reduced correspondingly, and the number of users who are not affected by the failure due to load transfer continuing to use electricity normally will increase. Therefore, the reliability of the whole system will be higher, and the relevant outage index of each load point will be lower, but the system investment and operation and maintenance cost will be increased. The economic efficiency is reduced.
PET is a new power converter which combines the power electronic converter and high frequency transformer. In addition to the functions of voltage conversion and electrical isolation of traditional transformers, it has high-voltage and low-voltage AC/DC interfaces and is suitable for DC source and load access. Multi-port PET is used as an “energy router” in the AC/DC distribution network with a variety of distributed renewable energy sources. Thus, a variety of distributed renewable energy sources can be connected to the distribution network to improve the efficiency and economy of the power system, improve the economy of power grid operation are beneficial.
Therefore, in order to fully study the advantages of multi-port PET applied in the distribution network, in the traditional AC distribution network, how to select the appropriate node to access PET and realize the integration of new energy not only ensures the new energy consumption rate but also ensures the reliability and economy of system operation.
IEEE 33 node is a 33-node standard distribution network system consisting of 32 lines. The topology structure of the ieee33 node system with multi-port PET is shown in Figure 20. Through the introduction of PET, the access to solar photovoltaic power generation, photothermal, wind power, storage, and heat storage equipment is realized.
In general, the MV AC (10 kV AC) port of PET is connected to the distribution network. This example optimizes the location of PET to IEEE 33 node distribution network and takes the minimum loss of distribution network and the lowest voltage deviation rate of nodes as the target. The constraints include power balance constraint, PET port constraint, and new energy output constraints: two sets of comparison examples are set at the same time: 1) PET medium voltage AC port can send power back to the distribution network, and the upper and lower limit of power transmission are [−2500 kw, 2500 kw]; 2) PET medium voltage AC port cannot send power back to the distribution network, and the upper and lower limit of power transmission are [−2500 kw, 0].
In both cases, the real-time power of PET 10 kV AC port and the optimal access node of 10 kV AC port, PET loss, network loss, voltage deviation rate, waste wind, and light loss are shown in Table 5.
1) under the condition that PET is prohibited from sending power back to the distribution network, PET is only equivalent to the load compared with the distribution network. The optimization result is that the MV AC port of PET is connected to node 2 of the distribution network. Therefore, it is more favorable for the loss and voltage deviation rate of distribution network to prohibit PET from transmitting power back to the distribution network, and PET is connected to the distribution network near the beginning of feeder;
2) PET can be regarded as a power supply when PET is allowed to send power back to the distribution network. The optimized result is to connect the PET medium voltage port to node 8 of the distribution network. The IEEE 33 node distribution network system is observed in the whole. Node 8 is located in the middle of the longest feeder. When PET is sending power back to the distribution network, it is beneficial to improve the voltage of downstream nodes and the loss of the feeder. From Table 5, it can be seen that allowing PET to send back power to the distribution network is beneficial to improve the utilization of renewable energy.
TABLE 5. Index comparison for whether the 10 kV AC port reverses the power of the power grid or not.
In view of the wide access of distributed new energy in the distribution network and the rapid increase of the proportion of generalized DC load in the distribution network, this paper proposes an AC/DC hybrid power system structure based on a multi-port PET cluster. Aiming at the AC/DC hybrid power system, the stable operation and control system are studied, the control objectives of the equipment level and system level of the AC/DC hybrid distributed system are analyzed, the hierarchical operation control architecture of the AC/DC hybrid distributed system is proposed, and the three-layer control mode and multi-time scale control mode of the integrated automation system, PET cluster controller, and PET controller are proposed. A sequential Monte Carlo simulation algorithm is proposed to solve the reliability problem of AC/DC hybrid power system with a multi-port PET cluster. The effectiveness of the reliability calculation model and algorithm is verified by an example. It is concluded that the reliability of the AC/DC hybrid power system can be improved by multi-port PET parallel cluster mode and port capacity increase. The example shows that the AC/DC hybrid power system with a multi-port PET cluster can improve the utilization rate of renewable energy.
The original contributions presented in the study are included in the article/Supplementary Material; further inquiries can be directed to the corresponding author.
XX: wrote the manuscript and overall conception. WH: put forward suggestions on the revision and improvement of the paper. YH: put forward suggestions on the revision and improvement of the paper. NT: put forward suggestions on the revision and improvement of the paper. YJ: put forward the hierarchical control of AC/DC hybrid system. NX: put forward the structure of the AC/DC hybrid power system with the multi-port PET cluster.
This study was supported by: 1) 2017 National Key R and D Program of China, research on key technologies, core equipment and engineering demonstration of AC/DC hybrid distributed renewable energy, Grant No.: 2017YFB0903202, 2) Major Scientific Research and Innovation Project of Shanghai Education Commission in 2019, research on Key Technologies of integrated energy power system based on multi energy flow coupling, Grant No.: 2019-01-07-00-02-E00044.
YJ was employed by Beijing Sifang Jibao Automation Co., Ltd., and NX was employed by Electric Power Research Institute of Guangdong Power Grid Co., Ltd.
The remaining authors declare that the research was conducted in the absence of any commercial or financial relationships that could be construed as a potential conflict of interest.
All claims expressed in this article are solely those of the authors and do not necessarily represent those of their affiliated organizations, or those of the publisher, the editors, and the reviewers. Any product that may be evaluated in this article, or claim that may be made by its manufacturer, is not guaranteed or endorsed by the publisher.
Barnes, M., Kondoh, J., Asano, H., Oyarzabal, J., Ventakaramanan, G., Lasseter, R., et al. (2007). Real-world Microgrids[J]. Proc. Syst. Syst. Eng. (4), 16–18. doi:10.1109/SYSOSE.2007.4304255
Bie, C. H., and Guan, X. H. (2016). Basic Theory of Energy Internet Planning, Operation and Trading [R]. Xi'an: Xi'an Jiaotong University.
Boroyevich, D., Cvetkovic, I., Dong, D., Burgos, R., Wang, F., and Lee, F. (2010). “Future Electronic Power Distribution Systems: A Contemplative view[C],” in 12th International Conference on Optimization of Electrical and Electronic Equipment, OPTIM 2010. Brasov: Transilvania University of Brasov, 1369–1380.
Ding, M., and Li, S. H. (2000). Methods for Accelerating the Convergence Rate of Monte Carlos Simulation in Reliability Calculation [J]. Power Syst. Automation..
Dolatabodi, A., Jadidbonab, M., and Mohammadi, B. (2018). Short-Term Scheduling Strategy for Wind-Based Energy Hub: a Hybrid Stochastic/IGDT Approach[J]. IEEE Trans. Sust. Energ. 10 (1), 438–448. doi:10.1109/TSTE.2017.2788086
Dragicevic, T., Guerrero, J. M., and Vasquez, J. C. (2014). A Distributed Control Strategy for Coordination of an Autonomous LVDC Microgrid Based on Power-Line Signaling. IEEE Trans. Ind. Electron. 61 (7), 3313–3326. doi:10.1109/tie.2013.2282597
Duan, Q., Sheng, W. X., and Meng, X. L. (2016). Research on New Energy Subnet System for Energy Internet [J]. Chin. J. Electr. Eng. 36 (02), 388–398.
Eghtedarpour, N., and Farjah, E. (2014). Power Control and Management in a Hybrid AC/DC Microgrid. IEEE Trans. Smart Grid. 5 (3), 1494–1505. doi:10.1109/tsg.2013.2294275
Eicher, S., Rahimo, M., Tsyplakov, E., Schneider, D., Kopta, A., Schlapbach, U., et al. (2004). “4.5kV Press Pack IGBT Designed for Ruggedness and Reliability [C],” in Conference Record of the 2004 IEEE Industry Applications Conference, 2004 3, 1534–1539.
Facci, A. L., Andreassi, L., and Ubertini, S. (2014). Optimization of CHCP (Combined Heat Power and Cooling) Systems Operation Strategy Using Dynamic Programming. Energy 66, 387–400. doi:10.1016/j.energy.2013.12.069
Funabashi, T., and Yokoyama, R. (2006). “Microgrid Field Test Experiences in Japan[C],” in Proceedings of the Power Engineering Society General Meeting (Canada: IEEE), 18–22.
Gao, Y., Hu, X., Yang, W., Liang, H., and Li, P. (2017). Multi-Objective Bilevel Coordinated Planning of Distributed Generation and Distribution Network Frame Based on Multiscenario Technique Considering Timing Characteristics. IEEE Trans. Sustain. Energ. 8 (4), 1415–1429. doi:10.1109/tste.2017.2680462
Hatziargyriou, N., Asano, H., Iravani, R., and Marnay, C. (2007). Microgrids. IEEE Power Energ. Mag. 5 (4), 78–94. doi:10.1109/mpae.2007.376583
He, X., Chu, L., Qiu, R. C., Ai, Q., Ling, Z., and Zhang, J. (2020). Invisible Units Detection and Estimation Based on Random Matrix Theory. IEEE Trans. Power Syst. 35 (3), 1846–1855. doi:10.1109/tpwrs.2019.2935739
Huang, A. Q., Crow, M. L., Heydt, G. T., Zheng, J. P., and Dale, S. J. (2011). The Future Renewable Electric Energy Delivery and Management (FREEDM) System: The Energy Internet. Proc. IEEE. 99 (1), 133–148.
Liu, Z. R. (2011). Reliability Evaluation of Distribution Network Based on Non Time Series Monte Carlo Simulation Method [D]. Changsha: Hunan University.
Ma, Z., Zhou, X. X., Shang, Y. W., and Zhou, L. M. (2015). Future Distribution System Form and Development Trend [J]. Chin. J. Electr. Eng. 35 (06), 1289–1298. doi:10.13334/j.0258-8013.pcsee.2015.06.001
Miao, J., Zhang, N., Kang, C., Wang, J., Wang, Y., and Xia, Q. (2018). Steady-State Power Flow Model of Energy Router Embedded AC Network and its Application in Optimizing Power System Operation. IEEE Trans. Smart Grid. 9 (5), 4828–4837. doi:10.1109/tsg.2017.2672821
Peng, H. T. (2018). Reliability Analysis Method of Power System[J]. Sci. Tech. Vision. (36), 211–212.
Pilo, F., Pisano, G., and Soma, G. G. (2011). Optimal Coordination of Energy Resources with a Two-Stage Online Active Management [J]. IEEE Trans. Ind. Electron. 10 (58), 4526–4537. doi:10.1109/tie.2011.2107717
Pu, T. J., Li, Y., Chen, N. S., and Sun, Y. Y. (2018). Key Technologies and Research Framework for Optimal Operation Control of AC/DC Hybrid System Based on PET [J]. Power Grid Tech. 42 (09), 2752–2759.
Salonen, P., Kaipia, T., and Nuutinen, P. (2008). “An LVDC Distribution System Concept[C],” in Proceedings of the Nordic Workshop on Power and Industrial Electronics (Espoo, Finland: Helsinki University Department of Electrical Engineering), 1–7.
Sanchez, S., and Molinas, M. (2015). Large Signal Stability Analysis at the Common Coupling Point of a DC Microgrid: A Grid Impedance Estimation Approach Based on a Recursive Method. IEEE Trans. Energ. Convers. 30 (1), 122–131. doi:10.1109/tec.2014.2359993
Wan, Q., Xia, C. J., and Guan, L. (2019). Review on Stability of Independent Microgrid with High Penetration Distributed Generation [J]. Power Grid Tech. 43 (02), 598–612.
Wang, B. Y. (2014). Research on the Loss Calculation Method and Temperature Testing of the IGBTs in AC-DC Converters with Chaotic SPWM Control [D]. Beijing: Beijing Jiaotong University, 21–24.
Wang, P., Jin, C., Zhu, D., Tang, Y., Loh, P. C., and Choo, F. H. (2015). Distributed Control for Autonomous Operation of a Three-Port AC/DC/DS Hybrid Microgrid. IEEE Trans. Ind. Electron. 62 (2), 1279–1290. doi:10.1109/tie.2014.2347913
Xiang, Y., Fu, M., Zhang, A. F., and Dou, X. B. (2017). Small Signal Stability Analysis of AC/DC Hybrid Microgrid in Isolated Island Operation [J]. Electric. pow. construt. 38 (01), 96–105.
Xiao, H. G. (2015). Research on Some Key Technologies of AC/DC Hybrid Microgrid [D]. Changsha: Hunan University.
Xu, S. Y., Ying, Y. L., and Chen, Y. L. (2019). Optimization Method of Integrated Energy System Based on Standardized Matrix Model [J]. Shanghai energy conservation. (01), 29–39.
Yan, X., Jiao, Y. J., and Du, Z. (2017). Feasibility Study of a Hybrid AC/DC Distribution Network Based on Flexible DC Technology [J]. Power Syst. Prot. Control. 45 (13), 110–116. doi:10.7667/PSPC160985
Ye, C. M. (2016). Research on Coordinated Planning Method of Transmission Network and Distribution Network in Large Cities [D]. Shanghai: Shanghai Jiaotong University.
Yin, X. G., Dai, D. Y., Han, Y., and Liao, Z. C. (2012). Research on Key Technologies of AC/DC Hybrid Microgrid [J]. High voltage apparatus. 48 (09), 43–46. CNKI:SUN:GYDQ.0.2012-09-010
Zha, Y. B., Zhang, T., Huang, Z., and Zhang, Y. (2014). Analysis of Key Technologies of Energy Internet [J]. China Sci. Inf. Sci. 44 (06), 702–713. doi:10.1360/N112014-00008
Zhang, H. T., Xu, T. Q., Yang, J., and Ying, F. F. (2019). Research on Key Technologies of Energy Router in Energy Internet [J]. Electr. Tech. (20), 105–107.
Zhang, P., and Wang, S. X. (2004). Interval Algorithm for Reliability Evaluation of Large Scale Distribution System [J]. Chin. J. Electr. Eng. 24 (03), 82–89. doi:10.2116/analsci.20.717
Keywords: AC/DC hybrid, power electronic transformer, reliability, control, new energy access
Citation: Xu X, Huang W, Hu Y, Tai N, Ji Y and Xie N (2021) Power Management of AC/DC Hybrid Distribution Network With Multi-Port PET Considering Reliability of Power Supply System. Front. Energy Res. 9:721385. doi: 10.3389/fenrg.2021.721385
Received: 06 June 2021; Accepted: 16 July 2021;
Published: 01 September 2021.
Edited by:
Bo Yang, Kunming University of Science and Technology, ChinaCopyright © 2021 Xu, Huang, Hu, Tai, Ji and Xie. This is an open-access article distributed under the terms of the Creative Commons Attribution License (CC BY). The use, distribution or reproduction in other forums is permitted, provided the original author(s) and the copyright owner(s) are credited and that the original publication in this journal is cited, in accordance with accepted academic practice. No use, distribution or reproduction is permitted which does not comply with these terms.
*Correspondence: Xinxing Xu, eHV4aW54aW5nMTEyOEBzanR1LmVkdS5jbg==
Disclaimer: All claims expressed in this article are solely those of the authors and do not necessarily represent those of their affiliated organizations, or those of the publisher, the editors and the reviewers. Any product that may be evaluated in this article or claim that may be made by its manufacturer is not guaranteed or endorsed by the publisher.
Research integrity at Frontiers
Learn more about the work of our research integrity team to safeguard the quality of each article we publish.