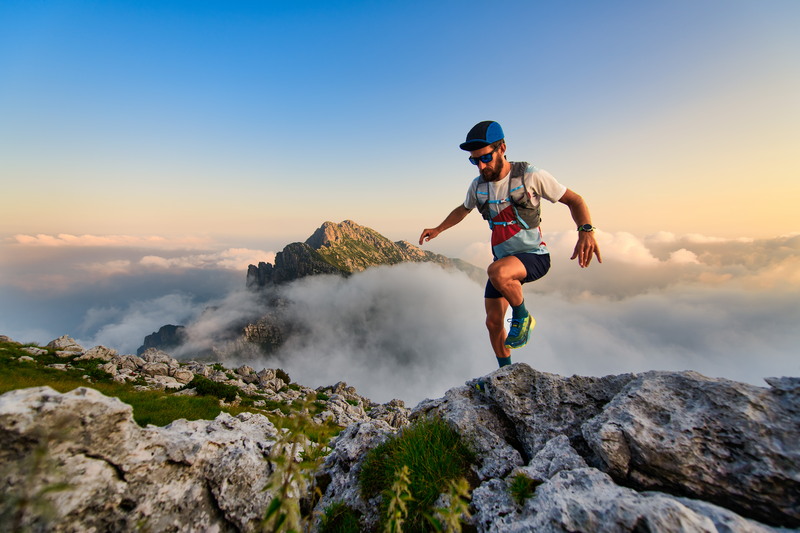
94% of researchers rate our articles as excellent or good
Learn more about the work of our research integrity team to safeguard the quality of each article we publish.
Find out more
MINI REVIEW article
Front. Energy Res. , 04 October 2021
Sec. Sustainable Energy Systems
Volume 9 - 2021 | https://doi.org/10.3389/fenrg.2021.703106
Environmentally enhanced turbines (EETs) have gained attention in the past two decades in order to reduce environmental impacts of hydropower plants on fish communities and on water quality. In this mini-review the main EETs are discussed, focusing on the Alden and Minimum Gap Runner turbines to reduce fish injury and on self-aerating and self/free-lubricant turbines to improve water quality. The review shows that EETs can be efficiently adopted instead of traditional turbines: EETs are cost-effective, efficient in terms of energy generation and have shown to reduce environmental impacts. Scientific gaps are also highlighted and case studies reported to better support refurbishment and new projects.
Hydropower, accounting for 1,308 GW of installed power (International Hydropower Association (IHA), 2020), is the main renewable energy source. It provides renewable energy, flexibility of the electric grid and ancillary services, water storage and flood control (Shuai et al., 2021). On the other side, the alteration of aquatic ecosystems is perceived as the main cause of hydropower-related impacts, with risks imposed on migrating fish and water quality. For example, the turbine may affect water quality (oil pollution and oxygen content) and disrupt the natural pathways for fish migration. (Nguyen et al., 2018; Geist, 2021). Therefore, it is essential to find the optimal trade-off between benefits and impacts, and to implement those hydropower technologies with limited or no conflict with the environmental objectives of water policies.
With the aim of reducing these impacts, environmentally enhanced turbines (EETs) have gained attention in the past 2 decades to reduce fish mortality. EETs are herein classified into fish friendly turbines, FFTs (although this term does not imply these facilities would have beneficial effects on fish), and ecological turbines, ETs, in particular self-aerating turbines and self-lubricated turbines.
In addition to the improvement of the hydropower unit design to facilitate fish passage and survival, another increasingly important strategy consists of interpreting fish-monitoring data for steering turbine operations in order to achieve a specific environmental goal, namely, the reduction of overall risks of mortal injury of fish through the hydropower station. The work of KlopriesElena-Maria and Schüttrumpf (2020) implemented a procedure for evaluating risks of mortal injury of European eels through turbines based on flow simulation and fish trajectory modeling. This is better known as “fish friendly operations and management.” This strategy has been pursued in observance to the migratory behavior of fishes and can be implemented as part of upgrading actions (Quaranta et al., 2021) whenever stricter biological goals are set for the station in question (Schwevers and Adam, 2020).
The impacts of traditional turbines on fish migration have been widely studied in literature, and strictly depend on turbine type (Pracheil et al., 2016). Some examples are: Ferguson et al. (2008) for Francis and Kaplan turbines, Fu et al. (2016) for Francis turbines and Deng et al. (2007) for Kaplan turbines. Pelton turbines are not generally considered, due to their intrinsically high-mortality behavior.
Amaral et al. (2011), Cada et al. (1997) and Cook et al. (2003) defined some criteria to design FFTs. The main damage mechanisms that fish may undergo while passing through a turbine are: mechanical injury (strike, grinding), decreased pressure and sudden pressure decrease, shear stresses and turbulence, and cavitation, which can cause external and internal injury (Mueller et al., 2020). The pressure-related effects take precedence when a greater biodiversity is considered, since most migratory fish are prone to mortality due to barotrauma caused by the rapid decompression affecting the size of the swimming bladder almost instantly. Rapid change in barometric pressure, or barotrauma, is a potential cause of injury and mortality for juvenile salmonids passing through hydro turbines (Brown et al., 2012; Richmond et al., 2014). Richmond et al. (2014) presented a literature review on barotrauma studies and a method to estimate the biological performance of hydro turbines (BioPA) to bridge the gap between field and laboratory studies on fish injury and turbine engineering design. Barotrauma can lead to rupture of the swim bladder and exopthalmia (popped out eyes). In addition, gas bubbles can form in the blood and internal organs, leading to emboli (Brown et al., 2014). The quantification of low pressures leading to barotrauma and its prevention by geometric modifications of the runner constitute a major research activity in academic institutions and industry.
Industry partners report a stronger drive in Europe for the protection of the European eels (Anguilla anguilla), which has prioritized the mitigation of collision-related effects. Furthermore, mechanical injuries are considered dominant and the main cause of fish mortality passing through a turbine (Amaral et al., 2011). Mechanical injury depends on fish dimensions, flow velocity and direction, and on turbine characteristics. The relation between these factors can be explained by the blade strike model (Deng et al., 2007), in particular by a dimensionless time T*, that expresses the ratio between the time employed by the fish to pass through the turbine and the time of a blade passage : the higher T* is, and the higher is the injury risk (Figure 1, Quaranta and Wolter, 2021). To estimate the mortality probability Pm with respect to the injury probability P, the regression equation of Turnpenny et al. (2000), as in Ferguson et al. (2008), can be used, Pm = P (0.15 ln L + 0.0125), with L the fish length in cm. However, Deng et al. (2007) found that predictions from stochastic models are generally closer to experimental data than predictions from the blade strike model, because the stochastic models consider the aspects of fish approaching to the leading edges of turbine runner blades.
FIGURE 1. Injury and mortality probability versus the dimensionless time T* for water wheels (Quaranta and Wolter, 2021).
In order to emphasize the novel strategies for fish protection via the redesign of turbines, a review work (Hogan et al., 2014) about the first generation of FFTs thoroughly described the conceptual development and implementation of two relevant technologies designed for better fish passage conditions, namely the Minimum Gap Runner (MGR) and the Alden turbine Table 1 shows a comparison on the performances and dimensions. The Alden and MGR turbines can be currently used between 10 and 40 m head, and for flow rates above 17 m3/s, but it is expected that they will be able to work up to 50 m head up to 325 m3/s (Nielson et al., 2015; Twaróg, 2015). For hydropower applications below 10 m head, in order to ensure a good ecological behavior, the free surface hydraulic machines can be used (typically below 2.5 m, Bozhinova et al., 2013). Due to their large dimensions, free surface operation and low rotational speed (<100 rpm), they intrinsically exhibit a good environmental behavior in relation to fish passage. FFTs used in the very low head context are, for example, water wheels (Quaranta and Wolter, 2021), the Vortex turbine (Müller et al., 2018), the Archimedes screw (Brackley, 2016; Piper et al., 2018), hydrokinetic turbines (Hammar et al., 2013), and the Very Low Head (VLH) turbine (Bozhinova et al., 2013). Further improvements in the latest decade seek to accommodate a larger biodiversity of fish present in migratory corridors, while at the same time enhancing the hydraulic performance of the machines. The Alden and MGR turbines are the focus of this paper and better described below.
TABLE 1. Comparison of Various Turbines for Fish Survivability (based on a 13.6 MW unit, Nielson et al., 2015).
The Alden turbine is an evolution of the Francis turbine, with three blades, wrapped around the shaft, to reduce fish injury. The Alden turbine was initially conceptualized and studied using Computational Fluid Dynamic (CFD) simulations and experimental tests at a pilot scale in the Alden research laboratory (EPRI and DOE, 2011). The obtained results showed a maximum hydraulic efficiency of 93.6% and fish passage survival rates greater than 98% for fish less than 20 cm long (Timothy et al., 2014). The current Alden turbine design rotates at a slower speed than conventional turbines in the same context. Table 1 shows a comparison between an Alden turbine and a 13-blade Francis turbine that rotates at 190 rpm. In a similar context, a five-blade Kaplan-Bulb turbine that rotates at 267.9 rpm could be used. The cost of the electro-mechanical equipment of the Alden turbine costs 39% more than the analogous cost of a Francis turbine, and 35% more than a MGR Kaplan-Bulb unit. Nevertheless, the global cost of a power plant equipped with the Alden turbine is lower than the cost of a Francis turbine hydropower plant (Dixon and Hogan, 2015), because the following cost reduction has to be considered: the powerhouse excavation is reduced by about 17% than a comparable Kaplan-Bulb turbine, and overall civil works are reduced by approximately 12% with respect to those of a comparable Kaplan-Bulb turbine; fishways for downstream migrating fish may no longer be needed if the passage survival through the turbine is high, making available more flows for generation; finally, O&M and capital costs of downstream fish bypass systems are reduced (Nielson et al., 2015). In order to further improve the performance, the variable rotational speed allows to maintain the blades always in their maximum opening position reducing the strike probability with fish and avoiding dangerous gaps between the blades and other parts of the machine. The DIVE turbine is an example of this application.
The Minimum Gap Runner turbine (MGR) is the optimization of the Kaplan-Bulb turbine. The gaps between the adjustable runner blade and the hub, and the gaps between the blades and the discharge ring, are minimized, reducing fish injury and mortality, and improving turbine efficiency (Timothy et al., 2014). The first field test of the MGR was done in Oregon at the Bonneville dam. The injury rate was 1.5%, smaller that the injury rate of 2.5% occurring at the adjacent Kaplan-Bulb turbine. The design and manufacture of the MGR is very similar to a standard Kaplan-Bulb turbine. Therefore, both turbines exhibit the same operating range in terms power output, flow capacity and hydraulic head, and the same dimensions. However, the higher efficiency and survival rate of a MGR turbine is compensated by a higher cost (Nielson et al., 2015). The U.S. Army Corps of Engineers (USACE) installed an optimized MGR turbine at the Ice Harbor Lock and Dam, located in Washington State (27 m head, power slightly above 100 MW, depending on the unit), achieving a survival rate of more than 98% (Quaranta et al., 2020).
As another example, a rehabilitation project at the Eddersheim hydropower plant (km 15.55 in the River Main, Germany) replaced the original Kaplan-type runner (4.1 m diameter, 2 MW nominal capacity) with a new 3-blade machine with thicker leading edges and minimized runner gaps. In addition to an enhanced flow environment for fish passage, the hydraulic performance of the new machine was in general 1–3% greater than the original one over most of the operating range (near the best efficiency point, the improvement is ∼1%, and at part load the new machine exhibits the greatest improvementsin the order of 3% at 50% of best efficiency point). The direct survival testing and validation of the design strategies are currently taking place (early 2021) with deployments of live and sensor fish samples at equivalent operating points between the two units. One of the 10 Kaplan-Bulb turbines of Wanapum Dam was replaced in 2005 with a new MGR Kaplan-Bulb turbine (Sale et al., 2006). After the first 3,000 h of operation, the turbine generation increased by 14%, and a fish survival rate of 97% was achieved. Based on these results, the Federal Energy Regulatory Commission (FERC) of the United States approved the replacement of the remaining 9 Kaplan-Bulb turbines with MGR turbines. The upgrade work finished in March 2020.1
The water of many reservoirs at the lower reaches is often oxygen deficient and the passage of this water causes damage to the ecosystems downstream (Pleizier et al., 2020). Hydropower plants that generally suffer of oxygen deficit exhibit the following characteristics: reservoir depth greater than 15 m, installed power higher than 10 MW, reservoir volume greater than 61 Mm 3, densimetric Froude number below 7, and a retention time greater than 10 days (EPRI, 1990). In order to minimize oxygen deficit problems, low pressure regions below the runner can be utilized to draw atmospheric air into the turbine during operation. Turbines where this system is implemented are called auto-venting turbines (AVT). AVTs allow distributed, central and peripheral aeration depending on the customer’s requirements. This sustainable technology maximizes bubble distribution in draft tube and tailrace while minimizing the impact on the turbine. Air injection is also an emerging technology for the flow control in the draft tube at off-design conditions (Kougias et al., 2019).
The aeration solution can be implemented both for Francis and for Kaplan and Pelton turbines. In March and Jacobson (2015) a review was presented, along with a database, showing that, in United States, the aerated turbines were 153 Francis turbines, 11 Deriaz turbines, 10 Bulb-Propeller and 4 Kaplan turbines.
Foust and Coulson (2011) described peripheral aeration system for a Kaplan turbine, where the bottom of the discharge ring was located up to 1.8 m below the tailwater elevation, due to cavitation constraints. The peripheral aeration system provided up to 3 mg/l of dissolved oxygen uptake, satisfying the water quality requirements at the plant. Dorena Lake Plant is equipped with a 4.4 MW vertical Kaplan turbine and a 1.2 MW horizontal Francis turbine, both turbines with peripheral aeration in the draft tubes, and additional diffusers in the tailrace (Douglas and Tong, 2012). March (2011) reported an efficiency increase of 2%/1% without/with aeration with an aerating turbine with peripheral aeration, and of 3.8%/1% without/with aeration with an aerating turbine with distributed aeration, with respect to the original turbine. In another project, March (2011) reported the same efficiency with a new aerating turbine with central aeration, and a capacity increase of 21%/11% without/with aeration. Both March and Fisher (1999) and March (2011) showed some efficiency curves from which it is possible to assess the efficiency difference at part load with respect to the original turbine for different aerating turbine technologies. With peripheral aeration, the efficiency at part load increased by 5% with respect to the original turbine which had no aeration system. McIntosh et al. (2010) presented the replacement of a Francis turbine with central aeration, showing that the plant efficiency improved by 3.7%, the power output increase by 14%, and over 1.5 mg/l of dissolved oxygen could be provided.
The aeration inside the casing of Pelton turbines is also very important in order to minimize oxygen deficit downstream, to minimize the negative effects at the tail race, e.g., corrosion and transport capacity (Kramer et al., 2017), especially when they have to be operated with a backpressure. It is worth noting the installation of Bieudron, the world’s largest Pelton turbines, with net head of 1,869 m and 25 m3/s of flow. At full load, with a maximum turbine discharge of 25 m3/s, the natural aeration system delivers 6 m3/s of air to the turbine casing (Keck et al., 2000). A case study worth mentioning on a Pelton turbine working in pressurized conditions is that developed at the Kopswerk II pumped storage hydropower plant in Austria, with a 180 MW Pelton turbine and a gross head ranging from 737 to 804 m. The pump power is 155 MW. Based on the lower reservoir water level, the Pelton turbine is below the water level of the lower reservoir of 1–16 m. When the vertical distance between the Pelton runner and the water level is 16 m, the casing was pressurized at 3 bar, and 1 bar when the distance is 1 m Hirtenlehner (2008).
Another topic to be considered to make turbines more environmentally acceptable is the lubrication. Adjustable blade runner hubs are typically filled with pressurized oil. This oil lubricates runner blade trunnion bearing and sliding parts of the operating mechanism in the hub. However, as explained by St. Germain (2018), oil leakage from hydraulic turbines does not only have a negative impact on the environment, but also causes some operational and maintenance problems. For both Kaplan-Bulb and Francis turbines (but especially for the former), there is thus a challenge related to the oil leakage from the turbine bearings and seals. Many of these turbines were designed, installed and commissioned by using pressurized oil to lubricate the turbine bearings. To date, several Kaplan-Bulb and Francis turbines have been upgraded so as to make them work free from oil (Värlind, 2002; Falkenhem et al., 2011; Auger and Ren, 2017), and new materials and lubricants are being developed (Quaranta and Davies, 2021). Ingram and Ray (2010) stated that water-lubricated guide bearings contribute to increase the overall plant efficiency by reducing friction losses by about 50% and that their maintenance is limited in comparison to oil-lubricated ones. Oil leakage can be an issue in hydropower plants equipped with Pelton turbines as well. However, the number of cases reported in the literature is very limited. Zulović (2014) reported the case of Poatina hydropower plant where 250 L of oil from the turbine guide bearing were released to the river. Oguma et al. (2013) described the performance of a water-lubricated guide bearing that was specifically designed for a multi-nozzle vertical Pelton unit. Kirejczyk et al. (2000) presented in turn the main technical data of three oil-free Deriaz pump-turbines that were installed at Naussac 2 pumped-storage power plant at the end of past century. Oil-free hubs are a widely installed technology in Europe, particularly in the Scandinavian countries.
Environmentally enhanced turbines are continuously improving to yield greater improvements in fish survival and water quality, and to accommodate a larger biodiversity of fish present in the migratory corridor. However, the existing FFTs are limited to the low head applications, and the associated mortality risk is not totally reduced to zero, so that fish passages for the downstream migration remain essential. Self-aerating turbines allow to improve water quality, but their internal fluid dynamic behavior complicates due to the multiphase flow, while novel materials and lubricant are being developed to minimize the use of oil-based lubricant.
Therefore, further efforts should be spent in this context. The more the turbine industry understands the environmental goals set by environmental agencies, the more effective the turbine design strategies at early stages of development will be. The greater the willingness of environmental agencies and operators to prioritize fish-related improvements, the greater the improvement will be. While the scientific research in the field of environmentally enhanced turbines has contributed considerably to the development of the next generation of Kaplan-type turbines to minimize turbine-passage mortality, a considerable effort must be made for bringing Francis-type machines at the same level of development. Furthermore, valves may indirectly influence fish mortality. For instance, valves can set the flows at part load conditions which give rise to greater likelihood of collision-related injuries, but at the same time reduce the likelihood of barotrauma (pressure-related injury). Here the influence comes from the flows deriving from the valve operation but not from the structure itself. To the best of our knowledge, there is no field evidence of effect of penstock/valve flows on fish mortality and more studies should be performed.
Additional research questions that should be addressed are detailed performance and fluid dynamic analyses. Research should also be carried out to improve numerical models for predicting the decrease in turbine efficiency due to fluid dynamic effects in the draft tube (e.g., vortex rope) under non-aerating and aerating conditions, and for predicting gas transfer and dissolved oxygen. Tools to assess the biological performance of turbines are instead already in place. More cost-effective and low maintenance methods to measure dissolved oxygen in reservoirs and reservoir releases should be studied.
EQ coordinated and conducted the review. PR-G and JP-D helped and revised. AP supervised and revised.
This work was conducted within the exploratory activity SustHydro under the project Water4EU at the Joint Research Centre of the European Commission.
Author PR-G was employed by the company Andritz Hydro.
The remaining authors declare that the research was conducted in the absence of any commercial or financial relationships that could be construed as a potential conflict of interest.
All claims expressed in this article are solely those of the authors and do not necessarily represent those of their affiliated organizations, or those of the publisher, the editors and the reviewers. Any product that may be evaluated in this article, or claim that may be made by its manufacturer, is not guaranteed or endorsed by the publisher.
1https://www.grantpud.org/blog/final-unit-at-wanapum-dam-nears-full-rehab
Amaral, S. V., Hecker, G. E., and Dixon, D. A. (2011). “Designing Leading Edges of Turbine Blades to Increase Fish Survival from Blade Strike,”. EPRI Report, No. 1024609 in EPRI-DOE, Conference on Environmentally-Enhanced Hydropower Turbines, 19–20 May 2011 (California, CA, USA: EPRI).
Auger, G., and Ren, G. (2017). Reducing Maintenance with Water Lubricated Turbine Guide Bearings-Design Principles & Case Studies, Tribodays, 28-29 November 2017. Älvkarleby, Sweden: Hydropower and Dams.
Bozhinova, S., Hecht, V., Kisliakov, D., Müller, G., and Schneider, S. (2013). Hydropower Converters with Head Differences below 2·5 M. Proc. Inst. Civil Eng. - Energ. 166 (3), 107–119. doi:10.1680/ener.11.00037
Brackley, R. (2016). Interactions between Migrating Salmonids and Low-Head Hydropower Schemes. Glasgow: University of Glasgow. PhD thesis.
Brown, R. S., Carlson, T. J., Gingerich, A. J., Stephenson, J. R., Pflugrath, B. D., Welch, A. E., et al. (2012). Quantifying Mortal Injury of Juvenile Chinook Salmon Exposed to Simulated Hydro‐Turbine Passage. Trans. Am. Fish. Soc. 141 (1), 147–157. doi:10.1080/00028487.2011.650274
Brown, R. S., Colotelo, A. H., Pflugrath, B. D., Boys, C. A., Baumgartner, L. J., Deng, Z. D., et al. (2014). Understanding Barotrauma in Fish Passing Hydro Structures: a Global Strategy for Sustainable Development of Water Resources. Fisheries 39, 108–122. doi:10.1080/03632415.2014.883570
Cada, G. F., Coutant, C. C., and Whitney, R. R ( (1997). Development of Biological Criteria for the Design of Advanced Hydropower Turbines. No. DOE/ID-100578. Washington, DC, USA: EERE Publication and Product Library.
Cook, T. C., Hecker, G. E., Amaral, S. V., Stacy, P. S., Lin, F., and Taft, E. P. (2003). Final Report-Pilot Scale Tests Alden/Concepts NREC Turbine. Washington, DC, USA: US Department of Energy.
Deng, Z., Carlson, T. J., Ploskey, G. R., Richmond, M. C., and Dauble, D. D. (2007). Evaluation of Blade-Strike Models for Estimating the Biological Performance of Kaplan Turbines. Ecol. Modellin 208 (2-4), 165–176. doi:10.1016/j.ecolmodel.2007.05.019
Dixon, D., and Hogan, T. (2015). “Session B3: Alden Fish-Friendly Hydropower Turbine: History and Development Status,” in International Conference on Engineering and Ecohydrology for Fish Passage, Groningen, Netherlands, 22–24 June. 30
Douglas, J., and Tong, K. (2012). Building 7.5-MW Dorena Lake at an Existing Dam. Renewable Energy World. Hydro Review, 16–19. Available at: https://www.renewableenergyworld.com/storage/new-development-building-7-5-mw-dorena-lake-at-an-existing-dam/#gref.
EPRI and DOE (2011). Fish Friendly Hydropower Turbine Development and Deployment. Alden Turbine Preliminary Engineering and Model Testing. Palo Alto, CAWashington, DC: EPRIand U.S. Department of Energy.
EPRI (1990). Assessment and Guide for Meeting Dissolved Oxygen Water Quality Standards for Hydroelectric Plant Discharges, Report No. GS-7001. Palo Alto, California: Electric Power Research Institute EPRI.
Falkenhem, R., Nakagawa, N., and Havard, D. (2011). Technologies for Eliminating Oil in Kaplan-Bulb Turbines Canals, Tunnels and Penstocks, Rehabilitation and Repair, Technology and Equipment. HydroReview, 6. Available at: https://www.hydroreview.com/world-regions/technologies-for-eliminating-oil-in-kaplan/#gref.
Ferguson, J. W., Ploskey, G. R., Leonardsson, K., Zabel, R. W., and Lundqvist, H. (2008). Combining Turbine Blade-Strike and Life Cycle Models to Assess Mitigation Strategies for Fish Passing Dams. Can. J. Fish. Aquat. Sci. 65 (8), 1568–1585. doi:10.1139/f08-078
Foust, J. M., and Coulson, S. (2011). “Using Dissolved Oxygen Prediction Methodologies in the Selection of Turbine Aeration Equipment,” in EPRI-DOE Conference on Environmentally Enhanced Hydropower Turbines: Technical Papers (Palo Alto, California: Electric Power Research Institute EPRI. Report No. 1024609, December 2011.
Fu, T., Deng, Z. D., Duncan, J. P., Zhou, D., Carlson, T. J., Johnson, G. E., et al. (2016). Assessing Hydraulic Conditions through Francis Turbines Using an Autonomous Sensor Device. Renew. Energ. 99, 1244–1252. doi:10.1016/j.renene.2016.08.029
Geist, J. (2021). Editorial: Green or Red: Challenges for Fish and Freshwater Biodiversity Conservation Related to Hydropower. Aquat. Conserv: Mar Freshw Ecosyst 31, 1551–1558. doi:10.1002/aqc.3597
Hammar, L., Andersson, S., Eggertsen, L., Haglund, J., Gullström, M., Ehnberg, J., et al. (2013). Hydrokinetic Turbine Effects on Fish Swimming Behaviour. PLoS One 8 (12), e84141. doi:10.1371/journal.pone.0084141
Hirtenlehner, K. (2008). The Initial Experience of the Start-Up and the First Opearation of Pelton Turbine in Back Pressure Operation. ZR Hirtenlehner.
Hogan, T. W., Cada, G. F., and Amaral, S. V. (2014). The Status of Environmentally Enhanced Hydropower Turbines. Fisheries 39 (4), 164–172. doi:10.1080/03632415.2014.897195
Hogan, T. W., Cada, G. F., and Amaral, S. V. (2014). The Status of Environmentally Enhanced Hydropower Turbines. Fisheries 39 (4), 164–172. doi:10.1080/03632415.2014.897195
Ingram, E., and Ray, R. (2010). Bearings & Seals: Examples of Innovations and Good Ideas. Available at: Renewable Energy Worlds, available at https://www.renewableenergyworld.com/storage/bearings-amp-seals/#gref.
International Hydropower Association (IHA) (2020). Hydropower Status Report Sector Trends and Insights. United Kingdom: IHA Central Office.
Keck, H., Vullioud, G., and Joye, P. (2000). “Commissioning and Operation Experience with the World’s Largest Pelton Turbines Bieudron,” in Proceedings of HydroVision 2000 Conference Charlotte, USA, 1–12.
Kirejczyk, J., Verzeroli, J. M., and Taulan, J. P. (2000). Nonpolluting Pump-Turbines: Naussac 2. Charlotte, USA: Hydrovision, 2000.
KlopriesElena-Maria, E.-M., and Schüttrumpf, H. (2020). Mortality Assessment for Adult European Eels (Anguilla Anguilla) during Turbine Passage Using CFD Modelling. Renew. Energ. 147, 1481–1490. doi:10.1016/j.renene.2019.09.112
Kougias, I., Aggidis, G., Avellan, F., Deniz, S., Lundin, U., Moro, A., et al. (2019). Analysis of Emerging Technologies in the Hydropower Sector. Renew. Sustain. Energ. Rev. 113, 109257. doi:10.1016/j.rser.2019.109257
Kramer, M., Wieprecht, S., and Terheiden, K. (2017). Minimising the Air Demand of Micro-hydro Impulse Turbines in Counter Pressure Operation. Energy 133, 1027–1034. doi:10.1016/j.energy.2017.05.043
March, P. A., and Fisher, R. K. (1999). IT'SNOTEASYBEINGGREEN: Environmental Technologies Enhance Conventional Hydropower's Role in Sustainable Development. Annu. Rev. Energ. Environ. 24 (1), 173–188. doi:10.1146/annurev.energy.24.1.173
March, P. (2011). “Hydraulic and Environmental Performance of Aerating Turbine Technologies,” in EPRI Conference on Environmentally Enhanced Hydropower Turbines, Washington DC, 19–20 May 2011, 1–32.
March, P., and Jacobson, P. (2015). Industry Experience with Aerating Turbines. Poetland, Oregon, USA: HydroVision International 2015.
McIntosh, D., Cherwinski, D., and Kahl, T. (20102010). Hardy Unit No. 3 Turbine Rehabilitation,” Proceedings of HydroVision 2010. Tulsa, Oklahoma: PennWell Corporation.
Mueller, M., Sternecker, K., Milz, S., and Geist, J. (2020). Assessing Turbine Passage Effects on Internal Fish Injury and Delayed Mortality Using X-ray Imaging. PeerJ 8, e9977. doi:10.7717/peerj.9977
Müller, S., Cleynen, O., Hoerner, S., Lichtenberg, N., and Thévenin, D. (2018). Numerical Analysis of the Compromise between Power Output and Fish-Friendliness in a Vortex Power Plant. J. Ecohydraulics 3 (2), 86–98. doi:10.1080/24705357.2018.1521709
Nguyen, T., Everaert, G., Boets, P., Forio, M., Bennetsen, E., Volk, M., et al. (2018). Modelling Tools to Analyze and Assess the Ecological Impact of Hydropower Dams. Water 10 (3), 259. doi:10.3390/w10030259
Nielson, N. M., Brown, R. S., and Deng, Z. D. (2015). Review of Existing Knowledge of the Effectiveness and Economics of Fish-Friendly Turbines. Vientiane, Lao PDR: Phnom Penh, Mekong River Commission. Technical Paper No. 57.
Oguma, T., Nakagawa, N., Mikami, M., Thantrong, L., Kizaki, Y., and Takimoto, F. (2013). Water Lubricated Guide Bearing with Self-Aligning Segments. Int. J. Fluid Machinery Syst. 6 (2), 49–55. doi:10.5293/IJFMS.2013.6.2.049
Piper, A. T., Rosewarne, P. J., Wright, R. M., and Kemp, P. S. (2018). The Impact of an Archimedes Screw Hydropower Turbine on Fish Migration in a lowland River. Ecol. Eng. 118, 31–42. doi:10.1016/j.ecoleng.2018.04.009
Pleizier, N. K., Nelson, C., Cooke, S. J., and Brauner, C. J. (2020). Understanding Gas Bubble Trauma in an Era of Hydropower Expansion: How Do Fish Compensate at Depth. Can. J. Fish. Aquat. Sci. 77 (3), 556–563. doi:10.1139/cjfas-2019-0243
Pracheil, B. M., DeRolph, C. R., Schramm, M. P., and Bevelhimer, M. S. (2016). A Fish-Eye View of Riverine Hydropower Systems: the Current Understanding of the Biological Response to Turbine Passage. Rev. Fish. Biol. Fish. 26, 153–167. doi:10.1007/s11160-015-9416-8
Quaranta, E., Aggidis, G., Boes, R. M., Comoglio, C., De Michele, C., Ritesh Patro, E., et al. (2021). Assessing the Energy Potential of Modernizing the European Hydropower Fleet. Energ. Convers. Manag. 246, 114655. doi:10.1016/j.enconman.2021.114655
Quaranta, E., Bonjean, M., Cuvato, D., Nicolet, C., Dreyer, M., Gaspoz, A., et al. (2020). Hydropower Case Study Collection: Innovative Low Head and Ecologically Improved Turbines, Hydropower in Existing Infrastructures, Hydropeaking Reduction, Digitalization and Governing Systems. Sustainability 12 (21), 8873. doi:10.3390/su12218873
Quaranta, E., and Davies, P. (2021). Emerging and Innovative Materials for Hydropower Engineering Applications: Turbines, Bearings, Sealing, Dams and Waterways, and Ocean Power Engineering. Elsevier.
Quaranta, E., and Wolter, C. (2021). Sustainability Assessment of Hydropower Water Wheels with Downstream Migrating Fish and Blade Strike Modelling. Sustainable Energ. Tech. Assessments 43, 100943. doi:10.1016/j.seta.2020.100943
Richmond, M. C., Serkowski, J. A., Ebner, L. L., Sick, M., Brown, R. S., and Carlson, T. J. (2014). Quantifying Barotrauma Risk to Juvenile Fish during Hydro-Turbine Passage. Fish. Res. 154, 152–164. doi:10.1016/j.fishres.2014.01.007
Sale, M. J., Cada, G. F., Acker, T. L., Carlson, T., Dauble, D. D., and Hall, D. G. (2006). DOE Hydropower Program Biennial Report for FY 2005-2006 (No. ORNL/TM-2006/097). Oak Ridge, USA: Oak Ridge National Laboratory.
Schwevers, U., and Adam, B. (2020). “Fish-Friendly Operational Management,” in Fish Protection Technologies and Fish Ways for Downstream Migration (Cham: Springer), 211–228. doi:10.1007/978-3-030-19242-6_7
Shuai, H., Yue, X., Hua, L. J., and Yong, L. J. (2021). A Two-Stage Dispatching Method for A Wind-Hydropower-Pumped Storage Integrated Energy System. Front. Energ. Res. 9, 65. doi:10.3389/fenrg.2021.646975
St Germain, F. (2018). Addressing Pressure Loss and Oil Leakage in Kaplan-Bulb Turbines and the Impact on Efficiency, BBA, Mont-Saint-Hilaire. Québec, Canada. Available at: https://www.bba.ca/publication/addressing-pressure-loss-issues-for-the-kaplan-turbine-runner-blade-and-impact-on-efficiency/.
Turnpenny, A., Clough, S., Hanson, K., Ramsay, R., and McEwan, D. (2000). Risk Assessment for Fish Passage through Small, Low Head Turbines. UK: Final Report. Energy Technical Support Unit, Harwell.
Twaróg, B. (2015). An Analysis of the Application of the Alden Turbine‒a Case Study of the Dobczyce Hydroelectric Power Plant. Czasopismo Techniczne, 147–156. doi:10.4467/2353737XCT.15.193.4398
Zulović, E. (2014). Preventing Problems through Past Experience. Renew. Energ. World 22 (6). online at: https://www.renewableenergyworld.com/baseload/preventing-problems-through-past-experience-2/#gref.
Keywords: Alden, fish-friendliness, ecological turbine, minimum gap runner, sustainable hydropower
Citation: Quaranta E, Pérez-Díaz JI, Romero–Gomez P and Pistocchi A (2021) Environmentally Enhanced Turbines for Hydropower Plants: Current Technology and Future Perspective. Front. Energy Res. 9:703106. doi: 10.3389/fenrg.2021.703106
Received: 30 April 2021; Accepted: 15 September 2021;
Published: 04 October 2021.
Edited by:
Muhammad Imran Khan, CECOS University of Information Technology and Emerging Sciences, PakistanReviewed by:
Ram Adhikari, University of Calgary, CanadaCopyright © 2021 Quaranta, Pérez-Díaz, Romero–Gomez and Pistocchi. This is an open-access article distributed under the terms of the Creative Commons Attribution License (CC BY). The use, distribution or reproduction in other forums is permitted, provided the original author(s) and the copyright owner(s) are credited and that the original publication in this journal is cited, in accordance with accepted academic practice. No use, distribution or reproduction is permitted which does not comply with these terms.
*Correspondence: Emanuele Quaranta, ZW1hbnVlbGUucXVhcmFudGFAZWMuZXVyb3BhLmV1, cXVhcmFudGFlbWFudWVsZUB5YWhvby5pdA==
Disclaimer: All claims expressed in this article are solely those of the authors and do not necessarily represent those of their affiliated organizations, or those of the publisher, the editors and the reviewers. Any product that may be evaluated in this article or claim that may be made by its manufacturer is not guaranteed or endorsed by the publisher.
Research integrity at Frontiers
Learn more about the work of our research integrity team to safeguard the quality of each article we publish.