- 1Department of Chemical and Biological Engineering, College of Engineering, University of Saskatchewan, Saskatoon, SK, Canada
- 2University of Saskatchewan, Saskatoon, SK, Canada
- 3Saskatoon Research and Development Centre, Agriculture and Agri-Food Canada, Saskatoon, SK, Canada
- 4Saskatchewan Polytechnic, Saskatoon, SK, Canada
Microwave (MW)-assisted torrefaction and pelleting could enhance biomass fuel properties and energy applications. Plastic wastes are considered as a replacement source binder in pellets to minimize their effect on the environment as pollutants. High-density polyethylene (HDPE), an extractable plastic from recycling waste, was investigated as a binder for torrefied wheat and barley straw pellets. Fuel pellet characteristics, such as durability, density, tensile strength, and water absorption, were used to evaluate the pellets produced from a single pelleting test. The results showed that the addition of HDPE as a binder significantly increased the pellet quality in terms of density (686.12–982.93 kg/m3), tensile strength (3.68 and 4.53 MPa) for wheat and barley straw, and reduced ash content of the pellet from 10.34 to 4.59% for barley straw pellet and 10.66 to 3.88% for wheat straw pellets. The higher heating value (HHV) increased with increasing biochar mix and HDPE binder blend. The highest HHV value observed for barley straw was 28.34 MJ/kg, while wheat straw was 29.78 MJ/kg. The study further indicated that MW torrefaction of biomass-biochar mix with HDPE binder reduced the moisture adsorption of wheat and barley straw pellets, which can significantly improve their storage capability in humid locations. The moisture uptake ratio for MW-torrefied barley straw pellets was 0.10–0.25 and wheat straw pellets 0.11–0.25 against a moisture uptake ratio of 1.0 for untreated biomass. MW torrefaction of wheat and barley straw with biochar and HDPE binder addition during pelleting is a promising technique to improve biomass fuel pellet properties.
Introduction
Herbaceous biomass is estimated to contribute between 10 and 14% of the world’s energy supply (Liu et al., 2014), and energy demand prediction is globally expected to grow more than 50% by 2025 due to increasing demand from rapidly developing countries (Ragauskas et al., 2006). Commercial production of wood-based pellets is done globally in large scale compared to agricultural biomass-based pellets, which have limited production (Spelter and Toth. (2009). Canadian biomass magazine (2017) reported that global wood pellets for heating and industrial applications had shown continuous growth in the past decade compared to agricultural biomass-based pellets. The growth is estimated at 10% annually, ranging from 19.5 metric tons in 2012 to about 28 million tons in 2015. Consequently, agricultural biomass-based pellets are mostly produced through torrefaction, and there would be triple production growth from 2020. The adoption of agricultural biomass-based fuel pellets is influenced by government/private policy and financial incentives (Agu, 2018). However, reducing fossil fuel prices in the future will increase productivity in an increasingly competitive biomass pellet market (Canadian biomass magazine, 2012).
Herbaceous biomass (wheat, barley, oat, canola, and camelina straw) is abundant and available within Western Canada. If utilized adequately, biomass is advantageous over fossil fuels because it is renewable and has lower greenhouse gas (GHG) emissions (Whalen et al., 2017). Thus, it can provide the solution to the shortage of raw material in the wood pellet industry, making herbaceous biomass an alternative material for biofuel (Mupondwa et al., 2016; Emadi et al., 2017; Li et al., 2018). To an extent, nonuniform physical properties, low energy density, high moisture content, and hydrophilicity of biomass have posed huge challenges in efficient and economic transportation, handling, and storage, including conversion into valuable bioproducts (Wang et al., 2013). Therefore, effective pretreatment of biomass is needed to open channels for lignocellulose conversion reactivities and modify biomass chemical and physical properties to improve biomass quality for efficient energy conversion (Bergman et al., 2005; Chaturvedi and Verma, 2013; Wang et al., 2013; Agu et al., 2017).
Torrefaction is a mild pyrolysis carried out at a temperature range of 200–300°C at atmospheric pressure in the absence of oxygen (Chen, 2015). Torrefaction has the potential to increase biomass quality and make it suitable for fuel applications (Satpathy et al., 2014; Chai and Saffron, 2016). Generally, the torrefaction process depends on variables such as temperature, residence time, influence of the particle size distribution, and reactor configuration. The torrefaction process can be accomplished at different temperatures, namely, light (200–230°C), mild (230–275°C), and severe/destructive (275–300°C) (Chen et al., 2015; Tumuluru, 2016). The increase in residence time (heating duration) from several minutes to hours results in loss of volatiles, high carbon content, and energy intensity (Tumuluru et al., 2011; Wannapeera et al., 2011; Chen, 2015). Lin. (2015) reported the effects of MW-induced torrefaction on waste straw upgrading. Based on thermogravimetric analysis (TGA) and differential thermal gravimetric analysis (DTG) of torrefied straw, the increase in MW power (250–450 W) and reaction time (10–30 min) increased fixed carbon content, ash content, higher heating value (HHV), and energy density. The MW torrefaction temperature of 275°C and heating time of 30 min combined with the pyrolysis of corn stover resulted in high yields and improved pyrolytic oil quality (Ren et al., 2014). It was reported that during the torrefaction process, heat breaks the inter- and intra-molecular hydrogen, C-O, and C-H bonds (Tumuluru et al., 2011) and prevents hydrogen bonds from forming (Bergman and Kiel, 2005). Many studies reported that the torrefaction process increases heating value and hydrophobicity, reduces grinding energy, improves particle size distribution, intensifies combustion (with less smoke), and improves biological decay resistance (Phanphanich and Mani, 2011).
Combining microwave and torrefaction is a promising technology, and several studies have reported that this combined technology can improve the quality of biofuel pellets (Wang et al., 2012; Ren et al., 2014; Lin 2015; Emadi et al., 2017; Huang et al., 2017). The method has the potential to be an alternative to conventional electric heaters used for the torrefaction of biomass (Xu, 2015). MW torrefaction is widely used in processing herbaceous biomass, wood, and municipal solid wastes to produce high-energy biofuels and other applications such as digestion, extraction, and stabilization (Wang et al., 2012; Ren et al., 2014; Emadi et al., 2017). Additionally, torrefied pellets release the same amount of emissions as conventional pellets. At longer distances such as 400 km using a lorry, 1850 km by rail, or 25,500 km by ship, torrefied pellets have lower emissions than conventional pellets (Emadi et al., 2017). Several pieces of literature have reported many findings on the application of MW using various techniques. Still, studies are limited on the economic implications of MW torrefaction for commercial processing of herbaceous biomass. Mosqueda and Tabil. (2017) results indicated that more investigations are required on distillers’ dried grain costs with solubles (DDGS) production to have an favorable investment opportunity in MW-drying technology. Wang et al. (2015) assessment indicated that MW-assisted pyrolysis is profitable. Also, the coproducts from the MW-assisted pyrolysis have the potential to increase the return of investment (ROI) significantly with a strong impact on bio-oil yield and selling price. Huang et al. (2017) showed that MW-torrefied Leucaena could replace fuel or co-fire with coal and be competitive when commercially scaled up. Currently, there are many future directions of MW torrefaction for promoting biofuel production, also challenges of large-scale applications (Richard, 2010; Ciolkosz and Wallace, 2011; Batidzirai et al., 2013; Bundhoo, 2018). Some of the challenges are supply chain management, MW irradiation penetration inability through a large amount of feedstock, utilization of different feedstocks, and reactor optimization (Ciolkosz and Wallace, 2011; Bundhoo, 2018).
Densification increases the density of the biomass pellet product to 600–1,200 kg/m3 (Kashaninejad and Tabil 2011) for efficient transportation and low moisture for safe storage (Mani et al., 2006). High heating value, good water-resistivity, and durability of torrefied wood pellets have been used to describe the economics of torrefied pellets, which can serve as an alternative replacement for coal in thermal power plants and metallurgical processes (Chen et al., 2015). Torrefied biomass particles show poor binding characteristics and will produce low-quality pellets (Ghiasi et al., 2014). Binders or additives can be liquid or solid, forming a matrix to make strong inter-particle bonding (Kaliyan and Morey, 2006). The choice of binders mainly depends on cost and environmental considerations in biomass pelletizing (Tabil, 1996). The amount of added binders depends directly on the level of torrefaction. Severe torrefaction conditions adversely affect the lignin that helps bind torrefied biomass. Thus, more binders will be required during densification (Obernberger and Thek, 2010; Peng et al., 2012). The binding capacity of torrefied biomass can be improved by directly applying binders via improving the strength or durability of densified material (Soleimani et al., 2017). Whittaker and Shield (2017) reported that the use of binders in pelleting could help to reduce the net GHG emissions and decrease the energy requirement of the pelleting process. Recycled polymer plastic, which can be sourced from municipal solid waste, has an excellent binding capability. Using recycled plastics as binders for biomass pellets at high pelleting temperatures (120–150°C) has shown positive results on biomass pellet quality. Recycled plastics as binders have good potential in achieving sustainable energy production (Emadi et al., 2017).
In the present study, biochar is used as an additive during biomass torrefaction, and recycled polymer plastic (high-density polyethylene) is used as a binder before biomass densification. Researchers extend their investigation on the new material biochar to evaluate its potential use as an additive in MW torrefaction of biomass. The anticipation is to investigate the reduction in energy consumption during MW torrefaction and increase the efficiency of the MW torrefaction process. Khelfa et al. (2020) reported that microwave-assisted pyrolysis of pinewood sawdust mixed with activated carbon improved biomass heating, reduced energy consumption, and coproduct quality after the treatment. Also, Ethaib et al. (2020) reported that microwave absorbers could adjust product distribution, improve bio-oil, biochar, and bio-gas at different treatment conditions, including the energy efficiency of the process. Biochar is a solid material produced from the thermochemical decomposition or carbonization of biomass. Biochar is inexpensive, environmentally friendly, and can be applied in different ways for waste management, greenhouse gas reduction, energy production, and soil remediation (Cha et al., 2016). It is also be used in agriculture as a soil amendment and for nutrient retention (Hu et al., 2021). Research studies on the use of biochar are ongoing for a variety of purposes, and this current study on MW torrefaction process is a part of it. Improvement of biochar will contribute to enhancing global sustainability via the carbon cycle (Ramesh et al., 2015).
There is a lack of information on the effect of the addition of biochar in biomass MW torrefaction and the use of high-density polyethylene (HDPE) as a binder for torrefied biomass. The objective of the study is to investigate the effect of biochar added during MW torrefaction of wheat and barley straw, and the effect of HDPE as an additive binder for pelleting torrefied wheat and barley straw on the physical quality of biofuel pellets.
Materials and Methods
Material Collection, Preparation, and Conditioning
Wheat and barley straw were obtained from an experimental farm near Saskatoon, Saskatchewan, Canada (Emadi et al., 2017). The straws were ground in a knife mill (Retsch GmbH, 5657 HAAN, West Germany) using a screen size of 3 mm. The initial moisture contents of wheat and barley straw were 7.45 and 9.14% wet basis (w.b.). The moisture content was determined using ASABE Standard S358.2 (2006) replicated three times. Commercial biochar from forest residues (Soil-matrix, Aitterra, Calgary, AB) (3 mm screen size) was mixed with the biomass before the MW torrefaction process. The moisture and ash contents of the biochar were determined and found to be 15.35% w.b. and 7.67%, respectively. Recycled polymer plastic (HDPE) was used as an additive/binder for torrefied straw with or without biochar. The HDPE from municipal solid waste was collected from SARCAN Recycling (Saskatoon, SK, Canada). The moisture content of the MW-torrefied wheat and barley straw-biochar mix was adjusted and conditioned to the required two levels, 8 and 10% w.b., before the densification process. This was done by carefully and uniformly spraying the samples with a calculated percent of water based on mass balance. The samples were placed in Ziploc bags and stored in a controlled environment chamber at 4°C for at least 72 h for moisture equilibrium prior to experiments.
Experimental Setup of Microwave-Torrefaction and Pelletization of Ground Microwave-Torrefied Wheat and Barley Straw Biochar-Mix
The experimental setup carried out using a benchtop MW oven with 2.45 GHz (LBM 1.2A/7296, Cober Electronics Inc., Stamford, CT). The MW torrefaction temperature was set to 250°C, and the residence time was set at 15 min. The temperature sensor was covered with a Teflon tube throughout the experiment and inserted in the middle port to measure the heat distribution in the reactor. The MW temperature data were recorded continuously on a laptop computer using the real-time graphing and data logging software (OSENSA Innovations Corp. Coquitlam, BC). Before MW torrefaction, the ground wheat straw or barley straw was mixed with biochar at four mass ratios of 0:0, 1:9, 1:5.7, and 1:3. A custom-made cylindrical quartz container, 140 mm in diameter and 108 mm in height, was used as the reactor. A lid was put on top of the container using a close-fitting rubber “O” ring in between making it airtight. The container has one exhaust port on top of the lid and one port by its side for nitrogen purging. About 100 ± 0.02 g biomass-biochar mixture was placed in the reactor for each experiment. Nitrogen gas was purged through the side port of the reactor at a constant rate of 50 ml/min using a flow meter for about 20 min before the start of each experiment and continued throughout the process. Purging of the nitrogen gas continued until the solid residues cooled down to 80°C before removal and placement in the desiccator (Satpathy et al., 2014). The torrefaction experiments were done in triplicate. After the MW torrefaction treatment, the samples were cooled to room temperature. The samples were stored in plastic Ziploc bags at room temperature until preparation for pelleting. The MW-torrefied wheat and barley straw biochar-mix at 8 and 10% (w.b.) moisture were subjected to the pelletization process. The pelletization process followed the procedure reported by Agu et al. (2017). Seven pellets were produced from wheat or barley straw biochar-HDPE mix and were followed by evaluating the pellet physical quality. A scanning electron microscope (SEM Phenom-World, Eindhoven, Netherlands) and stereoscope (Wild M3Z, Wild Heerbrugg, Gais, Switzerland) with a magnification of ×16, Paxcam3 camera (Midwest Information Systems, Villa Park, IL) and Intralux 500 light source were used to investigate the structural and surface transformation of the MW-torrefied biomass pellet.
Experimental Design
The independent variables are biomass-biochar ratio (expressed in percent weight) during torrefaction (1:9, 1:5.7, and 1:3) and HDPE added to the torrefied biomass-biochar mixture (6, 10, 20, and 25%) during pelletizing. The experiment was designed with Design Expert Statistical software (Version 8.0.7.1, Stat-Ease Inc., Minneapolis, MN, United States, 2010) using response surface methodology (RSM) based on user-defined design (UDD), an efficient and economical type of RSM (Agu et al., 2018; Agu et al., 2017). The collected data were further analyzed with Design Expert using analysis of variance (ANOVA) for response surface quadratic model to investigate the effect of the biomass-biochar mix and the HDPE binder in compaction of wheat and barley straw. A polynomial quadratic was fitted to evaluate the effect of each independent variable on the response:
where Y is the response studied by UDD (ash content, pellet density, tensile strength, and dimensional stability), β0 the offset term, X1 and X2 are the real variables (biomass-biochar and HDPE), β1 and β2 the linear coefficients, β11 and β12 the quadratic coefficients, and β12 and β13 the interaction effects between X1 and X2 on the response.
Thermochemical/Fuel Properties
In order to evaluate the effect of MW torrefaction on the fuel properties of biomass pellets, elemental compositional analysis of untreated and MW-torrefied wheat and barley straw (with or without biochar-mix) pellets, biochar, and HDPE was determined. The measurement was carried out using an elemental analyzer (Elementar-Vario EL III, Germany) to determine the mass percentages of C, H, N, O, and S. Volatile matter was determined according to ASTM D5142. HHV is the amount of energy produced by the complete combustion of the unit mass. HHV of the torrefied biomass (with or without biochar-mix) and torrefied biomass HDPE mixture (with or without biochar-mix) were calculated from the correlations based on elemental analysis (Chen, 2015).
Mass and Energy Yield of Microwave Torrefaction
Mass/solid and energy yields are parameters in the evaluation of the torrefaction process. The parameters are important factors in indicating how biomass resists thermal degradation. The maximization of solid yield after the heating process is a significant motivation for biomass conversion to biofuel (Chen et al., 2015). Solid and energy yields were evaluated using the following equations (Chen 2015), Bach and Skreiberg (2016), and Bai et al. (2017):
where SY = solid yield (%), MTB and MRB are the masses of torrefied biomass (with or without biochar-mix) and raw biomass (g), EY = energy yield (%), C, H, S, O, N are the carbon, hydrogen, sulfur, oxygen and nitrogen, respectively (%), EDR = energy densification ratio, HTB = HHV of torrefied biomass (with or without biochar-mix), and HRB = HHV of raw biomass, FC = fixed carbon (%), MC = moisture content (%), VC = volatile mater (%), A = ash content (%).
Moisture Adsorption Test
Torrefied wheat and barley straw (mixed with biochar and HDPE) pellets were dried in an oven at 105°C for 24 h and then placed in a humidity and temperature chamber (SH-641, Serial No. 92005408, ESPEC Corp., Kyoto, Japan) with an accuracy of ±0.1°C. The temperature and humidity of the chamber were set at 6°C and 95%, respectively (Satpathy et al., 2014; Iroba et al., 2017a), to simulate storage conditions of the pellets during humid and cold seasons of the year. The initial mass of the torrefied pellets and 2 g ground biomass were measured and placed in the chamber. The mass was measured at 1 h interval for 10 h, and the weight change was evaluated (Iroba et al., 2017a). The moisture uptake ratio was calculated by dividing the moisture content of the MW-torrefied sample by the moisture content of untreated samples after the hydrophobicity test.
Results and Discussions
Physical Characteristics of Non-torrefied and Microwave-Torrefied Biochar-Mix
The physical characteristics of raw and torrefied wheat and barley straw mixed with biochar at different ratios are listed in Table 1. The particle size distribution of torrefied biomass is used to evaluate the flow ability and utility of fuel via reactivity of the fuel pellet (Chen, 2015). The geometric mean particle diameter of torrefied biomass decreased with an increase in biochar weight fraction. The torrefied barleybiochar mix has slightly smaller particle sizes compared to the torrefied wheat straw-biochar mix. Torrefied barley straw biochar-mix (BS 75-25) was the finest among the ground-torrefied and untreated samples. The geometric mean particle diameter of the samples varies and could be attributed to moisture content variation and differences in the mechanical properties of the biomass samples (Mani et al., 2006).
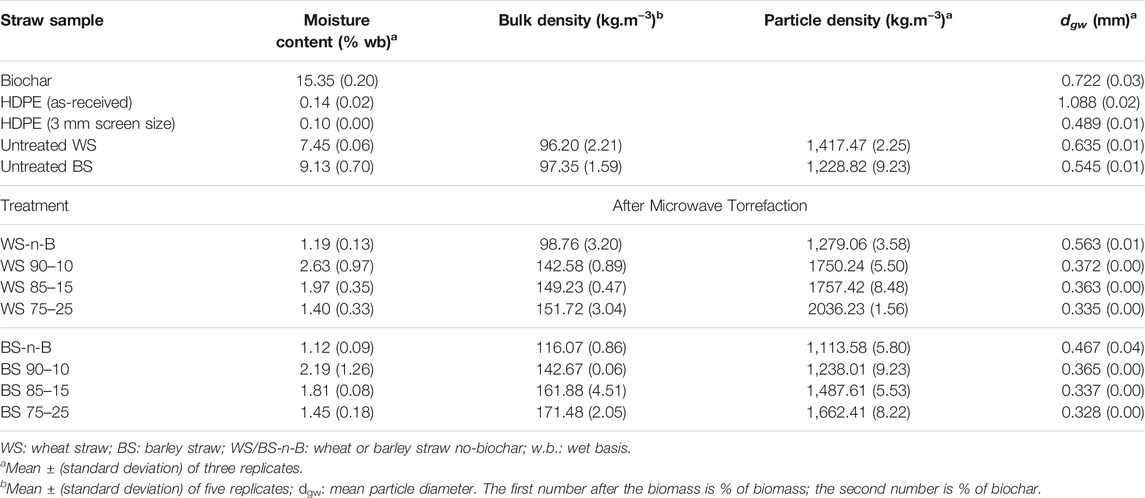
TABLE 1. Physical characteristics of raw and microwave-torrefied wheat and barley straw biochar-mix.
Figure 1 shows that the MW torrefaction effect leads to a charcoal-like formation as the end product. The biochar weight fraction into the mixture indicated moisture content reduction after MW torrefaction of both samples. The decrease in moisture content resulted due to water evaporation from the samples and dehydration of organic molecules (Iroba et al., 2017b). All torrefied samples showed more mass retained on the pan compared to raw biomass. As the particle size decreased, both bulk and particle density increased after the MW torrefaction process. This is due to a reduction in both inter- and intra-particle voids produced after milling (Phanphanich and Mani, 2011). Torrefied and untreated barley straw had the highest values of bulk and particle density. In addition, the moisture content of the biomass was decreased after the torrefaction process, and biomass no-biochar-mix had the lowest moisture content after MW torrefaction. Tumuluru. (2016) reported a similar result on deep drying and torrefaction of ground lodgepole pine. The moisture content decreased with an increase in torrefaction temperature and time. Pang and Mujumdar. (2010) reported that moisture content reduction after torrefaction increases energy efficiency, improves energy product quality, and reduces emissions during the thermochemical energy conversion process.

FIGURE 1. Raw and microwave-torrefied wheat and barley straw biochar-mix (A) ground biomass; (B) torrefied biomass without biochar; (C) torrefied biomass with 10% biochar; (D) torrefied biomass with 15% biochar; (E) torrefied biomass with 25% biochar.
Solid and Energy Yields of Wheat and Barley Straw Biochar-Mix
Solid and energy yields of torrefied mixtures decreased with an increase in biochar weight fraction. Table 2 shows the thermochemical properties of MW-torrefied wheat and barley straw biomass-mix. The decrease in solid yield could be because of microwave power and volatile components, and moisture loss to the surrounding environment. Remarkably, as the biomass carbonized after microwave heating, the torrefied material became lighter in weight and darker in color compared to the original mix. The effect of biochar on solid yield was low, and the loss of mass was attributed to the thermal decomposition of hemicellulose and some short-chain lignin compounds (Bergman et al., 2005). Energy yield is an important factor in biofuel quality and indicates HHV improvement of biomaterials via the torrefaction process (Iroba et al., 2017a; Bai et al., 2017). The energy and solid yields decreased with increasing biochar addition while the HHV increased. The observed increase in HHV of the biomass-biochar mix was due to volatile matter removal and an increased degree of carbonization during MW torrefaction. According to Chen et al. (2015), a decrease in solid yield linearly decreases biomass energy yield at increasing HHV. Also, Bai et al (2017) reported a similar trend while studying the co-pelletizing torrefied wheat straw with a peanut shell. At equal HHV (WS/BS 75-25), the solid and energy yields (WS: 45.47 and 73.75%; and BS: 45.07 and 71.72%) of MW-torrefied biomass-biochar mix decreased at the same rate. The results suggest that biomass torrefaction with a mild MW power level and a residence time of ≤15 min results in good fuel property.
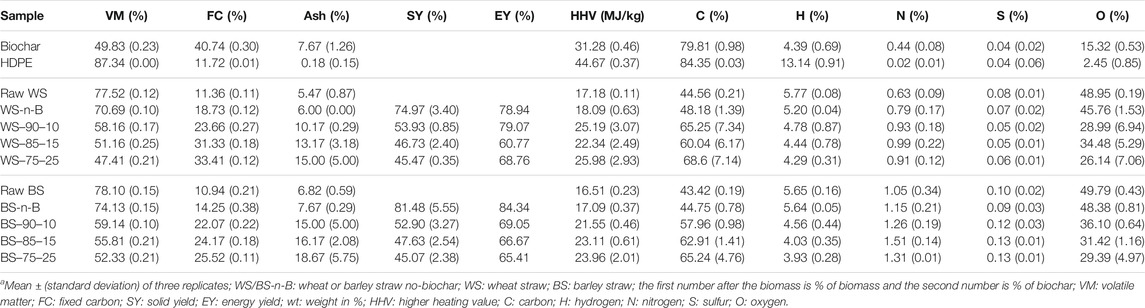
TABLE 2. Thermochemical properties of MW-torrefied and non-torrefied wheat and barley straw (dry basis)a.
An increase in ash content of torrefied biomass-biochar mixture was observed in both samples; however, it may be due to the mass loss of the biomass during torrefaction treatment. The carbon and nitrogen contents increased in both samples, whereas hydrogen content decreased with an increase in biomass-biochar mix after 250°C MW torrefaction at 15 min residence time. The MW-torrefied samples have higher nitrogen content compared to the non-torrefied samples. Iroba et al. (2017b) highlighted that the increase in nitrogen content after torrefaction suggests that such material could be used as a potential soil improvement additive for soil nutrient replenishment. Also, both biomaterials carbonize more under MW heating, and a similar observation was reported by Satpathy et al. (2014).
Fuel Quality Characteristics of Microwave-Torrefied and Non-Torrefied Pellets
Higher Heating Value of Wheat and Barley Straw Biochar-Mix Pellets
Figure 2 shows the impact of HDPE addition at different weight fractions on the HHV of torrefied biomass-biochar mixtures. Biochar and HDPE addition significantly (p < 0.05) affected the thermochemical properties of MW-torrefied and non-torrefied wheat and barley straw biochar-mix pellets. HHV is an important property for fuel energy applications. HHV of torrefied biomass pellets significantly increased with an increase in biochar addition and HDPE at different levels. Chen (2015) reported that the torrefaction objective is to increase energy density, and the HHV of torrefied biomass is approximately 16–29 MJ/kg, closer to coal HHV 25–35 MJ/kg. Overall, the highest HHV values (29.85 MJ/kg and 30.51 MJ/kg, and 27.96 MJ/kg and 28.63 MJ/kg) were obtained as the HDPE levels increased from 6–25% in both torrefied pellet samples. Emadi et al. (2017) reported similar results mixing linear low-density polyethylene (LLDPE) with MW-torrefied wheat and barley straw. The increase in HHV MW-torrefied biomass pellets could be due to decreased oxygen to carbon (O/C) and hydrogen to carbon (H/C) ratios of the biomass samples after the torrefaction process. Yu-Fong Huang et al. (2017) studied the MW torrefaction of Leucaena to produce biochar. The HHV was estimated at 30 MJ/kg at MW power of 250 W for 30 min. Overall, the HHV values obtained (29.85 MJ/kg and 30.51 MJ/kg, and 27.96 MJ/kg and 28.63 MJ/kg), which are closer to coal HHV (25–35 MJ/kg), demonstrate the potential of MW-torrefied wheat/barley straw pellets in replacing fuel, co-firing with coal in power plants, and residential use when commercially scaled up.
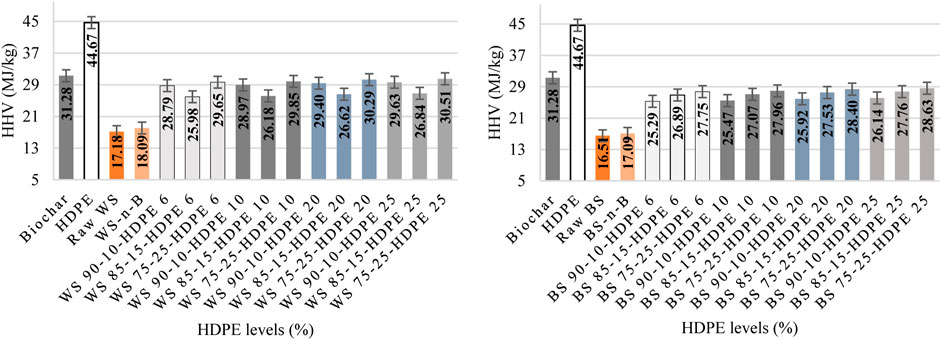
FIGURE 2. Heating value of MW-torrefied wheat and barley straw-biochar pellets at different HDPE levels including biochar, high-density polyethylene, and wheat and barley straw.
Ash Content and Dimensional Stability of Microwave-Torrefied Wheat and Barley Straw Biochar-Mix Pellets
Ash content is a fraction of minerals of the pellet in oxidized form (Obernberger and Thek, 2010). The biochar used in the present study had an ash content value of 7.67%, and the mass loss in wheat straw and barley straw contributed to the high ash content after torrefaction (Table 2). Increasing the biochar mixture (10–25%) increased the ash content of MW-torrefied wheat and barley straw with MW-torrefied barley straw having the highest ash content value. The results could be because of the high ash content of biochar, and further investigation is ongoing.
The ash content of wheat and barley straw biochar-mix pellets at 8 and 10% moisture content in different HDPE binder levels is presented in Table 3. The ash content of the pellets slightly decreased with increased HDPE addition for both samples. Quality wood pellets have a low ash content below 0.7%, and industrial wood pellets have over 3% (Wood Energy 2006). Emadi et al. (2017) reported a similar trend of results using the same biomass but a different binder, LLDPE. The low ash content of wheat and barley straw pellets may produce clean and stable fuel for co-firing purposes, causing less cleaning activities in the burners and filters of combustion units. Increasing the biochar-mix from 10 to 25% contributed to a high ash content at the initial level of HDPE addition for both types of biomass. Nilsson et al. (2011) reported that pellets produced from agricultural crop residues have the potential to yield high ash content. However, the results from this study have shown the high potential of recycled polymer plastic to decrease the ash content of MW-torrefied biomass pellets. The effect of biochar-mix and HDPE additives was significant (p < 0.05) on the dimensional stability of biomass pellets. The change in the pellet diameter, height, and mass after 2 weeks was measured to calculate the dimensional stability of the pellets. The HDPE binder’s addition gave more dimensional stability to the barley straw pellet than the wheat straw pellet after 2 weeks of producing the pellets. The decrease in dimensional stability can also be attributed to biochar ash quality. Torrefied barley straw no-biochar pellet at 10% moisture content showed the highest dimensional stability close to 0.
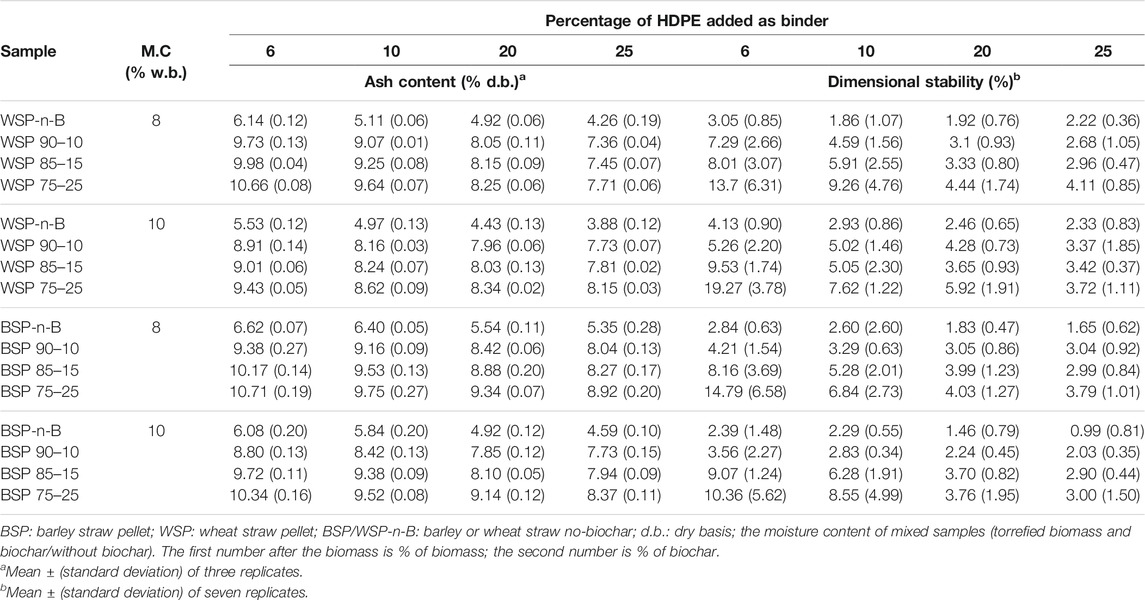
TABLE 3. Pellets ash content and dimensional stability characteristics of microwave-torrefied wheat and barley straw biochar at different HDPE blends.
Pellet Density and Tensile Strength of Microwave-Torrefied Wheat and Barley Straw Biochar-Mix
The effect of biochar-mix and HDPE additives was significant (p < 0.05) on the pellet density of MW-torrefied biomass (Table 4). Results obtained for both MW-torrefied pellets at different moisture contents showed low pellet density wherein the acceptable standard range is 1,000–1,400 kg/m3 for a single pellet density (Agu et al., 2017). The low pellet density could be because of biochar ash quality. A similar study was done by Emadi et al. (2017) but did not use biochar during torrefaction. Using different levels of linear low-density polyethylene (LLDPE), the results reported a pellet density range of 1,046–1,126 kg/m3. The highest pellet density was obtained in MW-torrefied barley straw pellet-HDPE 25% without biochar (982.93 kg/m3). Increasing the biochar-mix decreased the pellet density, whereas adding 6–25% HDPE-binder levels increased the pellet density in both samples. Generally, wheat and barley straw MW-torrefied biochar-mix pellets produced at 10% moisture content resulted in high pellet density compared to 8% pellets.
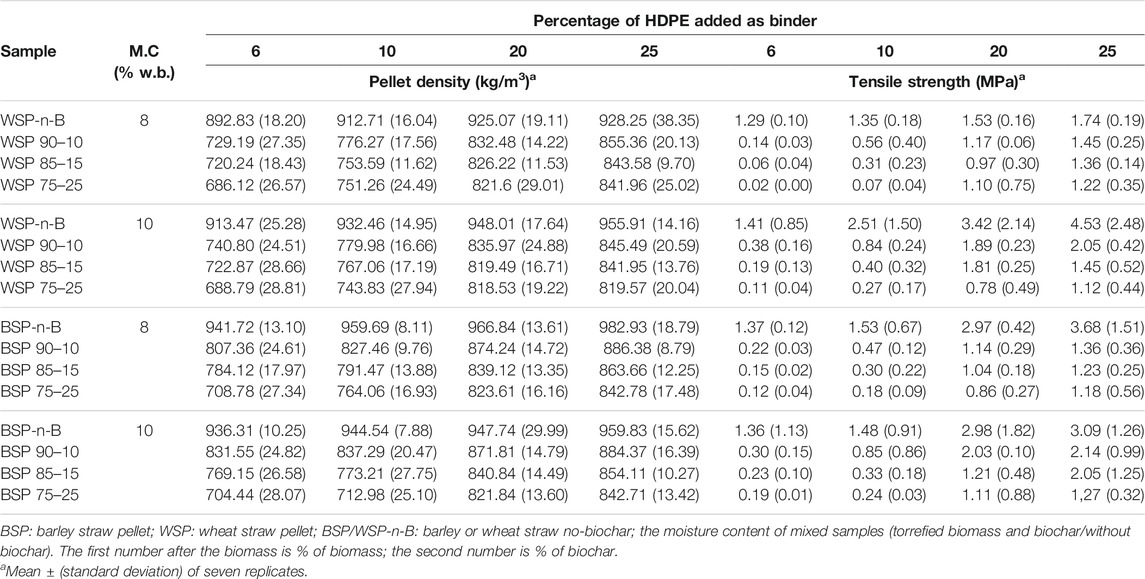
TABLE 4. Pellets density and tensile strength characteristics of microwave-torrefied wheat and barley straw biochar at different HDPE blends.
Table 4 presents the results of diametral compression for pellets produced from MW-torrefied straw of wheat and barley biochar-mix with different levels of the HDPE binder. Adding HDPE binder to the MW-torrefied wheat and barley straw pellets showed a significantly higher (3.68 and 4.53 MPa) tensile strength value. The highest pellet tensile strength was obtained in MW-torrefied wheat straw pellet-HDPE 25%.
The results showed a positive effect of HDPE as a binder to create mechanical interlocking for MW-torrefied biomass. Also, the biochar quality affected the pellet strength, but the HDPE binder has the potential to reduce dust generation during handling and storage. Adding 20–25% HDPE to the MW-torrefied samples increased the tensile strength and durability of wheat and barley straw pellets.
Statistical and Experimental Verification of Predictive Models
The matrix of user-defined design determined the interaction of independent factors affecting wheat and barley straw biochar pellets. Tables 5 and 6 summarize the results obtained for the ANOVA study. The data generated using ANOVA for the response surface quadratic model was significant for pellet density (p < 0.0001), tensile strength (p < 0.0001), and dimensional stability. The quadratic regression model in both moisture conditions of samples indicated that the models were significant. The F-values suggest that the models were highly significant. The p-value serves as a check of the significance of coefficients, including the interaction power of each independent variable. The R2 values close to 1, the better the correlation between the predicted and actual experimental values (Senol et al., 2020). The R2 values of 0.9917 and 0.9926 for BS-ash content and tensile strength at 8% moisture content showed the highest values for the accuracy of the models. The results indicated that the model could explain the variation of 99.17% of ash content and 99.26% of tensile strength, and only about 0.83 and 0.74% showed out of scope.
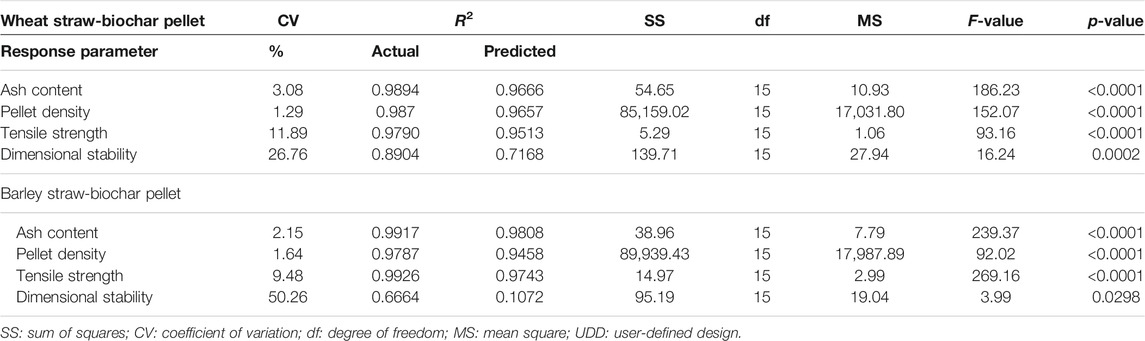
TABLE 5. Analysis of variance for the quadratic model of UDD responses of wheat and barley straw-biochar pellet at 8% (w.b).
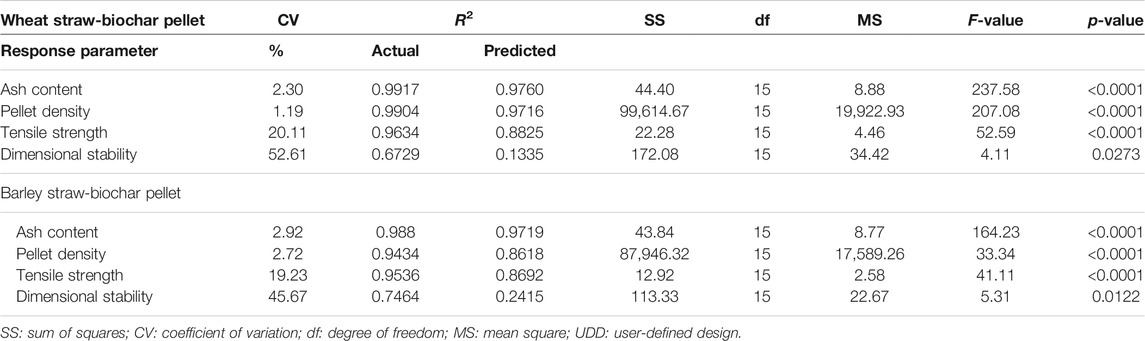
TABLE 6. Analysis of variance for the quadratic model of UDD responses of wheat and barley straw-biochar pellet at 10% (w.b).
Also, the predicted R2 0.9808 ash content and tensile strength 0.9743 of BS-biochar pellet at 8% moisture content indicated good agreement with the actual R2 experimental values. RSM’s objective is to detect which experimental variables generate signals, which are large compared to any noise. According to Safari et al. (2018), precision adequacy (precisionadeq.) measures the signal-to-noise ratio. A ratio greater than 4 is desirable. The ratio in all the models indicated values greater than 4, showing adequate signals (values not included in this paper). The coefficient of variation (CV %) measures the residual variation of data relative to the average. The higher the CV, the lower is the reliability of the experiment (Das et al., 2015). In the present study, pellet density showed very low CV values in WS/BS 8% moisture content and WS 10% moisture content, indicating sufficient precision and reliability on the experimental results.
Figures 3 and 4 show a representative relationship between predicted and actual responses and perturbation plots of the effects on the center points describing wheat and barley straw biochar pellets. The relationship indicates that the distribution of residuals is randomly scattered around zero, with no grouped data and autocorrelations also, and the ability to simulate response changes between predicted and actual values. Most experimental results lie on the 45-degree line, meaning that the models are feasible and can be subsequently applied in the prediction stages, indicating a good agreement between experimental and predicted values. In addition, the red and blue colored points stand for the highest and the lowest individual variables data. The ANOVA presented in Tables 5 and 6 showed that the biochar and HDPE significantly affected pellet density and tensile strength at p < 0.05. The perturbation plots imply that the combination of biochar-mix “A” with HDPE blend “B” showed that the response variables are sensitive to its changes. The interaction effects of the response parameters on the biomass-biochar and HDPE in describing wheat and barley straw-biochar pellets are studied using 3D dimensional plots, a representative plot of the samples (Figures 5, 6A,B). The response surface plot generally helps to visualize and understand the interactive effect of selected factors (ash content, pellet density, tensile strength, and dimensional stability). The pellet density surface plot of wheat and barley straw-biochar pellets at 10% moisture content demonstrates the nature of the response surface and fitness of the obtained model. Increasing biochar-mix decreased pellet density while HDPE binder addition (6–25%) increased the pellet density (Figures 5A, B). The HDPE addition (6–25%) to the wheat and barley straw biochar affected the tensile strength of pellets showing interaction with response to surface shape (Figures 6A, B). The surface plots indicated that higher pellet tensile strength was obtained at HDPE 25% by decreasing the biochar.
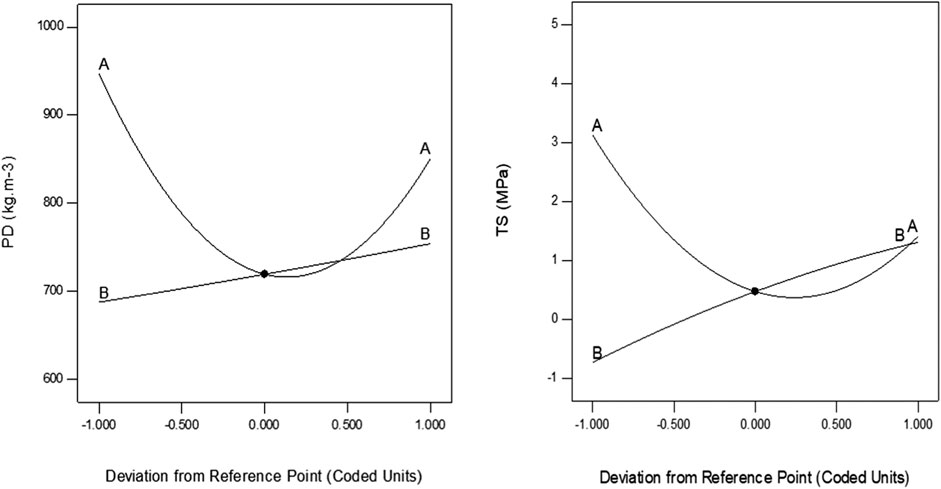
FIGURE 4. Wheat and barley straw-biochar pellets perturbation plot for pellet density and tensile strength.
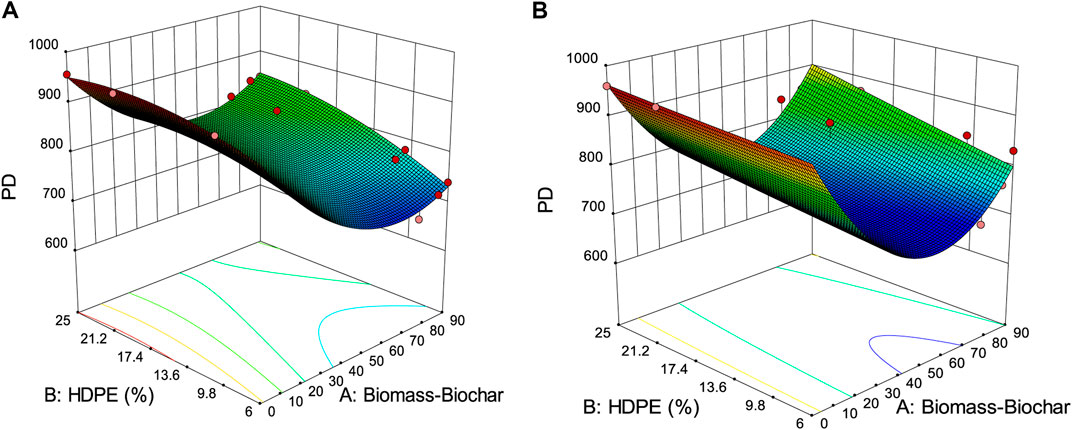
FIGURE 5. Effect of 3D dimensional response surface plots for (A) wheat and (B) barley straw-biochar pellets for pellet density (PD).
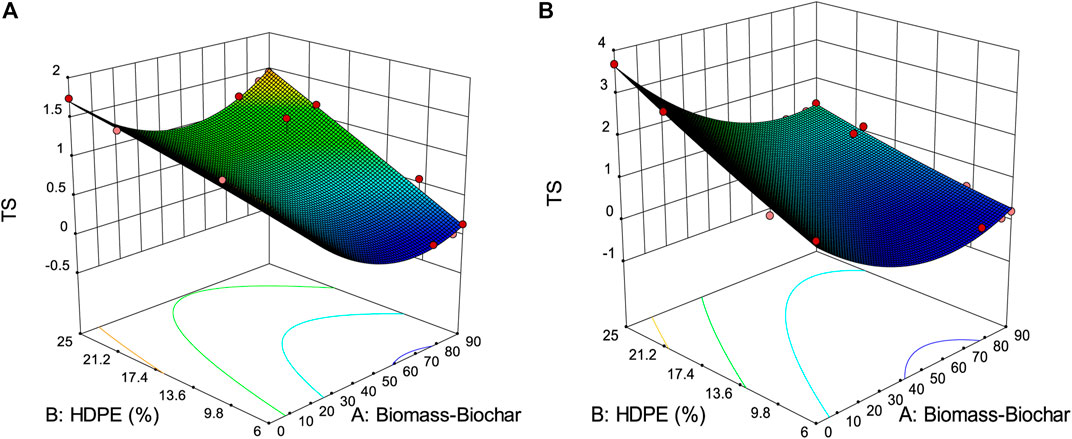
FIGURE 6. Effect of 3D dimensional response surface plots for (A) wheat and (B) barley straw-biochar pellets for tensile strength (TS).
Moisture Adsorption Characteristics of Microwave-Torrefied and Non-torrefied Wheat and Barley Straw-Biochar Pellets
Moisture content (MC) is the main challenge attributed to densified biomass. Kaliyan and Morey (2009) highlighted that the exposure of biomass pellets to rain or high humidity conditions (short-term) might affect pellet quality during transportation and storage. Hydrophobicity is the water-repellent property of biomass fuel (Bach and Skreiberg 2016). The moisture uptake of the MW-torrefied wheat and barley straw-biochar-mix pellets placed in a humidity and temperature chamber at 6°C and 95% relative humidity (RH) was measured and presented in Figures 7, 8. The moisture uptake decreased with an increase in biochar-mix for both samples. As the biochar and HDPE increased, inflection points are observed in Figures 7, 8A-D, showing that the release of volatiles could also increase (Chen, 2015). The initial moisture uptake for with and without biochar-mix wheat and barley straw pellets started between 15 and 33% w.b. after 1 h. Both samples got saturated and reached equilibrium moisture conditions (EMC) within 4–6 h of subjecting samples to humid conditions. The moisture ratio was calculated by dividing the moisture content of the MW-torrefied sample by the moisture content of the untreated sample after the hydrophobicity test (Iroba et al., 2017a). The moisture uptake ratio for MW-torrefied barley straw pellets was found to be 0.10–0.25 and wheat straw pellets 0.11–0.25 against a moisture uptake ratio of 1.0 for untreated biomass pellets. The values of moisture uptake of the produced pellets are similar to the values (0.32–0.96) reported by Iroba et al. (2017a) and Satpathy et al. (2014). The hydrophobic characteristic significantly improves fuel pellet storage capability in humid locations. The results indicated that MW torrefaction has the potential to solve the problem of moisture adsorption of biomass pellets during outdoor storage, and pellet decomposition will not pose any problem. Biochar-mixed with biomass during the MW torrefaction process may have contributed to low moisture uptake of the pellets indicating a highly hydrophobic characteristic. To an extent, biochar has shown effective results in various research applications such as adsorbent, catalyst, soil amendment, fuel cells, and supercapacitors (Cha et al., 2016). Furthermore, both the final EMC and the moisture uptake rate of the pellets are important from a transport and storage perspective (Iroba et al., 2017; Chen, 2015). More research work on biochar utilization in producing fuel pellets is ongoing within our research team.
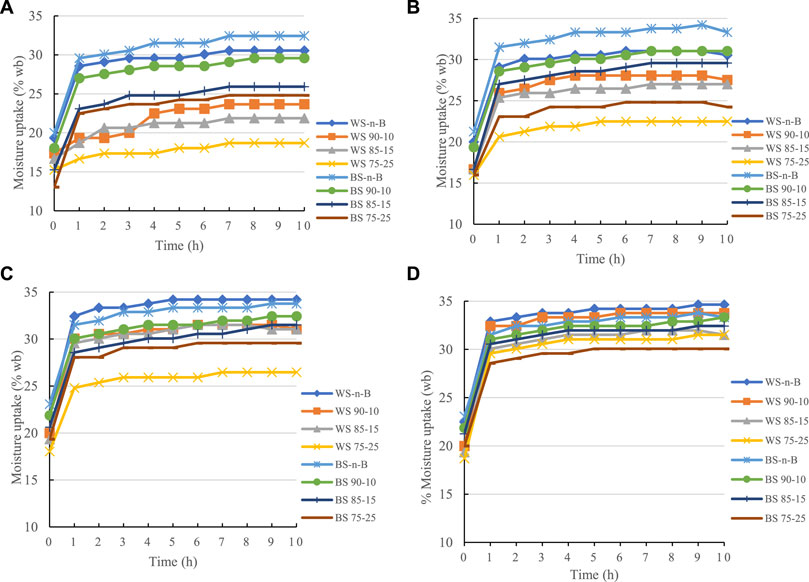
FIGURE 7. Moisture adsorption of pellets made of MW-torrefied (wheat straw biochar and barley straw biochar) at 8% moisture content for different HDPE binder levels (A) 6%; (B) 10%; (C) 20%, and (D) 25% at 6°C and 95% RH.
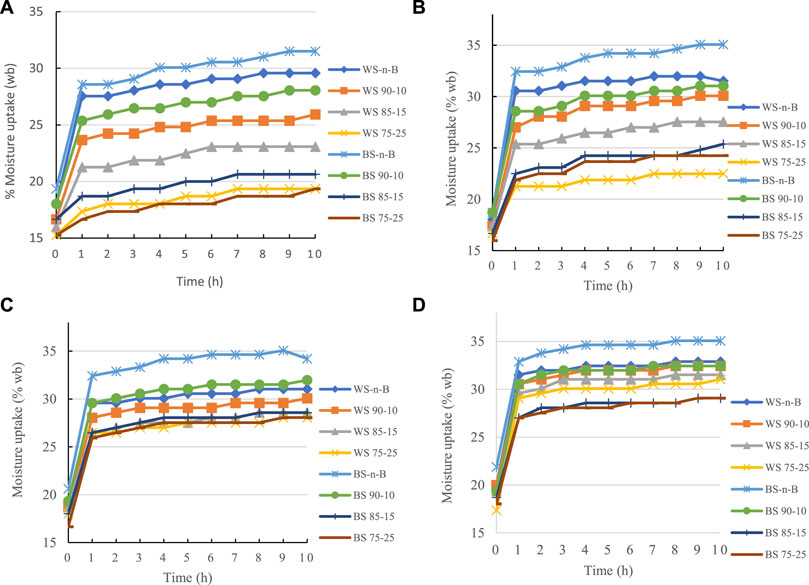
FIGURE 8. Moisture adsorption of pellets made of MW-torrefied (wheat straw biochar and barley straw biochar) pellets at 10% moisture content for different HDPE binder levels (A) 6%; (B) 10%; (C) 20%, and (D) 25% at 6°C and 95% RH.
Micrographs in Figure 9 are SEM images for the cross-sectional area of MW-torrefied wheat and barley straw with and without biochar-HDPE pellets at ×200 magnification. The image analysis provided a deeper insight into the binding mechanisms and an obvious interface on the surface of the pellets. According to the surface images of torrefied wheat and barley straw pellets without biochar mixing and HDPE blend (Figure 9A-B), inter-particle spaces between the particles show a good cohesive and tight bonding without any added binder. Figures 9C and 9D clearly show the HDPE-binder (Figure 9C: HDPE 6% and Figure 9D: HDPE 25%) interface on the surface of wheat/barley straw pellet particles. The wheat/barley straw-biochar-HDPE particles stuck to each other, allowing low void spaces. It implies that binder and biomass polymers (hemicellulose and lignin), having reached the glass transition temperatures during densification, have formed solid bridges between the particles (Tilay et al., 2015).
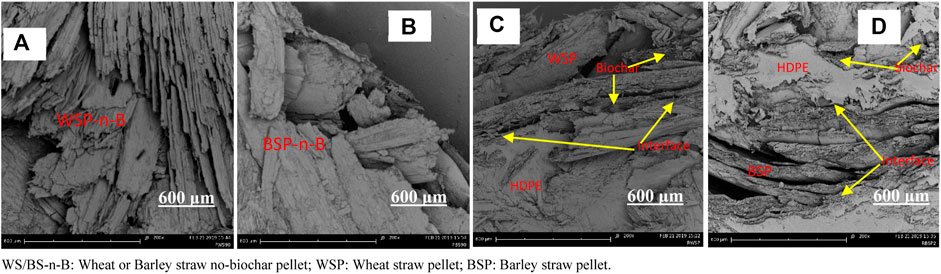
FIGURE 9. SEM surface images of microwave-torrefied wheat and barley straw-biochar-mix pellets at different HDPE levels and viewed at ×200 magnification (A) WSP-n-B; (B) BSP-n-B; (c) WSP with biochar-HDPE blend; and (D) BSP with a biochar-HDPE blend.
The formation of biomassHDPE binder interface could be affected by the release of volatile matter from wheat/barley straw, biochar, and HDPE. Also, the nature of the interface is expected to be dependent on the binder, which could be the reason for the difference in the pellet strength of wheat/barley straw biochar with or without the HDPE binder. Therefore, the results indicated that the HDPE binder improved MW-torrefied wheat and barley straw biochar-mix pellet properties.
Figure 10 shows the various morphological surface arrangements of wheat and barley straw pellet particles examined using the stereoscope technique. The images provide useful insights into the inter-particle binding mechanisms using different HDPE levels. Increasing the HDPE levels and biochar-mix developed a solid bridge binding between the particles without any visible cracks. Also, visuals from the stereoscope images illustrate differences in pellet microstructure and higher plastic deformation as the biochar and HDPE increase.
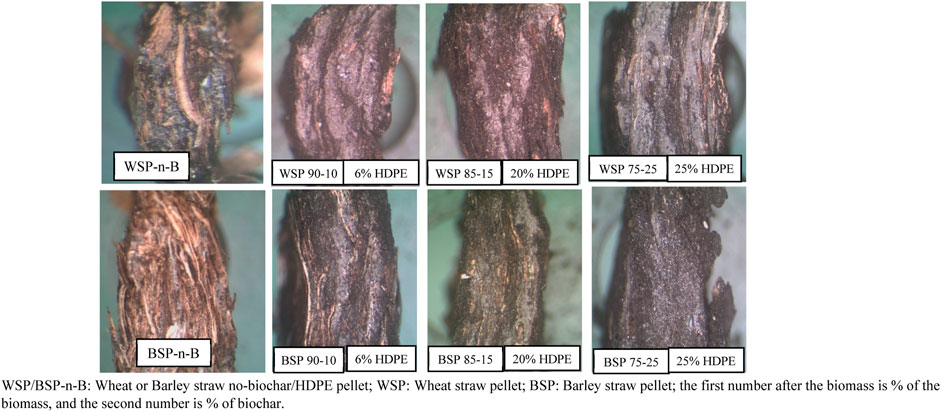
FIGURE 10. Cross-sectional surface of microwave-torrefied wheat and barley straw pellets with biochar-HDPE blend at ×16 magnification.
The wheat and barley straw pellets without biochar-mix show a visibly inter-particle bonding with the HDPE blend. Consequently, the pellet’s binding mechanism increased as indicated in the pellet density, tensile strength, and durability results. Further investigation is ongoing using the differential interference contrast microscopy to understand differences in microstructure, porosity, and impact of different surface treatments while increasing the biochar-mix at various HDPE levels.
Conclusion
Microwave torrefaction of wheat and barley straw biochar-mix with HDPE-added binder shows promising results in producing fuel pellets for the bioenergy industry. Biochar mixed with biomass during MW torrefaction treatment improved the bulk density and particle density and reduced the moisture content of the biomass (wheat and barley straw) after torrefaction. Increasing the biochar added during torrefaction could reduce the quality of wheat and barley straw pellets for storage and transportation. The addition of HDPE to MW-torrefied biomass during pelleting significantly affected the quality of pellet produced in terms of the tensile strength (3.68 and 4.53 MPa). The HDPE binder addition (6–10%) increased the HHV (28.24 MJ/kg and 29.78 MJ/kg) and decreased the ash content of the pellets. The biochar/HDPE blend showed the potential of reducing moisture uptake in both biomass pellets during storage. This study shows that recycled polymer plastic and biochar have potential value as a additional or substitute material for bio-pellet production for co-firing in power-generating plants and residential use. The morphological examination of pellets showed the extent of interfacial adhesion of particles of the biomass-biochar-HDPE blend. Wheat and barley straw, biochar, and recycled polymer plastic could significantly reduce greenhouse gas emissions since they are environmentally sustainable. More investigation is ongoing to examine biochar addition during torrefaction and other biochar utilization in this research study, including environmental impact assessment and techno-economic analysis of utilizing the materials and MW torrefaction process.
Data Availability Statement
The raw data supporting the conclusions of this article will be made available by the authors, without undue reservation.
Author Contributions
All authors listed have made a substantial, direct, and intellectual contribution to the work and approved it for publication.
Conflict of Interest
The authors declare that the research was conducted in the absence of any commercial or financial relationships that could be construed as a potential conflict of interest.
Publisher’s Note
All claims expressed in this article are solely those of the authors and do not necessarily represent those of their affiliated organizations, or those of the publisher, the editors and the reviewers. Any product that may be evaluated in this article, or claim that may be made by its manufacturer, is not guaranteed or endorsed by the publisher.
Acknowledgments
The authors would like to acknowledge the funding received from the Natural Sciences and Engineering Research Council of Canada (NSERC), Agricultural and Agri-Food Canada–Saskatoon Research and Development Centre (AAFC-SRDC), Enugu State University of Science and Technology (ESUT) Nigeria, and BioFuelNet Canada.
References
Agu, O. S., Tabil, L. G., Emadi, B., and Mupondwa, E. (2018). “Microwave-assisted Torrefaction of Biomass: Effect of Biochar and Recycled Polymer Plastic (HDPE) on the Physical Quality of Fuel Pellets,”. ASABE Paper No. 1801398. doi:10.13031/aim.201801398
Agu, O. S. (2018). Techno-economic Analysis of Biomass Torrefaction and Densification: A Review. Saskatoon: University of Saskatchewan. [Unpublished-Biological Engineering]. [Saskatoon (SK)].
Agu, O., Tabil, L., and Dumonceaux, T. (2017). Microwave-Assisted Alkali Pre-treatment, Densification and Enzymatic Saccharification of Canola Straw and Oat Hull. Bioengineering 4, 25. doi:10.3390/bioengineering4020025
ASABE Standard S358.2 (2006). Moisture Measurement – Forages. St. Joseph, MI: American Society of Agricultural and Biological Engineers.
ASTM Standard D5142 (2009). A. Standard Test Methods for Proximate Analysis of the Analysis Sample of Coal and Coke by Instrumental Procedures. West Conshohocken, PA, USA: ASTM International. http://www.astm.org/Standards/D5142 (2021-01-16.
Bach, Q.-V., and Skreiberg, Ø. (2016). Upgrading Biomass Fuels via Wet Torrefaction: a Review and Comparison with Dry Torrefaction. Renew. Sust. Energ. Rev. 54, 665–677. doi:10.1016/j.rser.2015.10.014
Bai, X., Wang, G., Gong, C., Yu, Y., Liu, W., and Wang, D. (2017). Co-pelletizing Characteristics of Torrefied Wheat Straw with Peanut Shell. Bioresour. Technol. 233, 373–381. doi:10.1016/j.biortech.2017.02.091
Batidzirai, B., Mignot, A. P. R., Schakel, W. B., Junginger, H. M., and Faaij, A. P. C. (2013). Biomass Torrefaction Technology: Techno-Economic Status and Future Prospects. Energy 62, 196. doi:10.1016/j.energy.2013.09.035
Bergman, P. C. A., Boersma, A. R., Zwart, R. W. R., and Kiel, J. H. A. (2005). Torrefaction for Biomass Co-firing in Existing Coal-Fired Power Stations “Biocoal”. Research Centre of Netherlands, Petten, NL: ECNC-05-013. Google Scholar.
Bergman, P. C. A., and Kiel, J. H. A. (2005). “Torrefaction for Biomass Upgrading,” in Proceeding of the 14th European Biomass conference and exhibition, Paris, France, 17-21 October 2005 (Petten, Netherlands: ECN-RX-05-180). [Google Scholar].
Bundhoo, Z. M. A. (2018). Microwave-assisted Conversion of Biomass and Waste Materials to Biofuels. Rene. Sust. Energ. Rev. 82. doi:10.1016/j.rser.2017.09.066
Canadian biomass magazine (2012). Global Pellet Demand Rises. Available at: https://www.canadianbiomassmagazine.ca/global-pellet-demand-rises-3253 (2021-04-21.
Canadian biomass magazine (2017). Global Pellet Market Outlook. Available at: https://www.canadianbiomassmagazine.ca/pellets/growing-demand-for-pellets-6074 (2021-04-21.
Cha, J. S., Park, S. H., Jung, S. C., Ryu, C., Jeon, J. K., Shin, M. C., et al. (2016). Production and Utilization of Biochar: a Review. J. Ind. Eng. Chem. 40, 1. doi:10.1016/j.jiec.2016.06.002
Chai, L., and Saffron, C. M. (2016). Comparing Pelletization and Torrefaction Depots: Optimization of Depot Capacity and Biomass Moisture to Determine the Minimum Production Cost. Appl. Energ. 163, 387–395. doi:10.1016/j.apenergy.2015.11.018
Chaturvedi, V., and Verma, P. (2013). An Overview of Key Pretreatment Processes Employed for Bioconversion of Lignocellulosic Biomass into Biofuels and Value Added Products. 3 Biotech. 3, 415–431. doi:10.1007/s13205-013-0167-8
Chen, W.-H. (2015). “Torrefaction,” in Pretreatment of Biomass – Processes and Technologies. Editors A. Pandey, S. Negi, P. Binod, and C. Larroche (Netherlands: Elsevier), 173–192. doi:10.1016/b978-0-12-800080-9.00010-4
Chen, W. H., Peng, J., and Bi, X. T. (2015). A State-Of-The-Art Review of Biomass Torrefaction, Densification and Applications. Renew. Sust. Energ. Rev. 44, 847. doi:10.1016/j.rser.2014.12.039
Ciolkosz, D., and Wallace, R. (2011). A Review of Torrefaction for Bioenergy Feedstock Production. Biofuels, Bioprod. Bioref. 5, 317–329. doi:10.1002/bbb.275
Das, S., Bhattacharya, A., Haldar, S., Ganguly, A., Gu, S., Ting, Y. P., et al. (2015). Optimization of Enzymatic Saccharification of Water Hyacinth Biomass for Bio-Ethanol: Comparison between Artificial Neural Network and Response Surface Methodology. Sust. Mater. Tech. 3, 17–28. doi:10.1016/j.susmat.2015.01.001
Emadi, B., Iroba, K. L., and Tabil, L. G. (2017). Effect of Polymer Plastic Binder on Mechanical, Storage and Combustion Characteristics of Torrefied and Pelletized Herbaceous Biomass. Appl. Energ. 198, 312–319. doi:10.1016/j.apenergy.2016.12.027
Ethaib, S., Omar, R., Kamal, S. M. M., Biak, D. R. A., and Zubaidi, S. (2020). Microwave-assisted Pyrolysis of Biomass Waste: a Mini Review. Processes 8, 1190. doi:10.3390/pr8091190
Ghiasi, B., Kumar, L., Furubayashi, T., Lim, C. J., Bi, X., Kim, C. S., et al. (2014). Densified Biocoal from Woodchips: Is it Better to Do Torrefaction before or after Densification? Appl. Energ. 134, 133–142. doi:10.1016/j.apenergy.2014.07.076
Hu, X., Huang, X., Zhao, H., Liu, F., Wang, L., Zhao, X., et al. (2021). Possibility of Using Modified Fly Ash and Organic Fertilizers for Remediation of Heavy-Metal-Contaminated Soils. J. Cl. Prod. 284, 124713. doi:10.1016/j.jclepro.2020.124713
Huang, Y-F., Sung, H-T., Chiueh, P-T., and Lo, S-L. (2017). Microwave Torrefaction of Leucaena to Produce Biochar with High Fuel Ratio and Energy Return on Investment. Energ. Proced. 105, 35. doi:10.1016/j.egypro.2017.03.276
Iroba, K. L., Baik, O.-D., and Tabil, L. G. (2017b). Torrefaction of Biomass from Municipal Solid Waste Fractions I: Temperature Profiles, Moisture Content, Energy Consumption, Mass Yield, and Thermochemical Properties. Biomass and Bioenergy 105, 320–330. doi:10.1016/j.biombioe.2017.07.009
Iroba, K. L., Baik, O.-D., and Tabil, L. G. (2017a). Torrefaction of Biomass from Municipal Solid Waste Fractions II: Grindability Characteristics, Higher Heating Value, Pelletability and Moisture Adsorption. Biomass and Bioenergy 106, 8–20. doi:10.1016/j.biombioe.2017.08.008
Kaliyan, N., and Morey, R. V. (2009). Factors Affecting Strength and Durability of Densified Biomass Products. Biomass and Bioenergy 33, 337–359. doi:10.1016/j.biombioe.2008.08.005
Kashaninejad, M., and Tabil, L. G. (2011). Effect of Microwave-Chemical Pre-treatment on Compression Characteristics of Biomass Grinds. Biosyst. Eng. 108, 36–45. doi:10.1016/j.biosystemseng.2010.10.008
Khelfa, A., Rodrigues, F. A., Koubaa, M., and Vorobiev, E. (2020). Microwave-Assisted Pyrolysis of Pine Wood Sawdust Mixed with Activated Carbon for Bio-Oil and Bio-Char Production. Processes 8 (8), 1437. doi:10.3390/pr8111437
Li, X., Mupondwa, E., and Tabil, L. (2018). Technoeconomic Analysis of Biojet Fuel Production from Camelina at Commercial Scale: Case of Canadian Prairies. Bioresour. Technol. 249, 196–205. doi:10.1016/j.biortech.2017.09.183
Lin, Y.-L. (2015). Effects of Microwave—Induced Torrefaction on Waste Straw Upgrading. Ijcea 6, 401–404. doi:10.7763/IJCEA.2015.V6.518
Liu, T., McConkey, B., Huffman, T., Smith, S., MacGregor, B., Yemshanov, D., et al. (2014). Potential and Impacts of Renewable Energy Production from Agricultural Biomass in Canada. Appl. Energ. 130, 222–229. doi:10.1016/j.apenergy.2014.05.044
Mani, S., Tabil, L. G., and Sokhansanj, S. (2006). Effects of Compressive Force, Particle Size and Moisture Content on Mechanical Properties of Biomass Pellets from Grasses. Biomass and Bioenergy 30, 648–654. doi:10.1016/j.biombioe.2005.01.004
Mosqueda, M. R. P., and Tabil, L. G. (2017). Techno-economic Evaluation of Microwave Drying of Wheat Distiller’s Grain with Solubles in Saskatchewan. Can. Biosyst. Eng. 59, 23. doi:10.7451/cbe.2017.59.8.23
Mupondwa, E., Li, X., Tabil, L., Falk, K., and Gugel, R. (2016). Technoeconomic Analysis of Camelina Oil Extraction as Feedstock for Biojet Fuel in the Canadian Prairies. Biomass and Bioenergy 95, 221–234. doi:10.1016/j.biombioe.2016.10.014
Nilsson, D., Bernesson, S., and Hansson, P.-A. (2011). Pellet Production from Agricultural Raw Materials - A Systems Study. Biomass and Bioenergy 35, 679–689. doi:10.1016/j.biombioe.2010.10.016
N. Kaliyan, N., and Morey, R. V. (2006). Densification Characteristics of Corn stover and Switchgrass. ASABE Paper No.066174. doi:10.13031/2013.27380
Obernberger, J., and Thek, G. (2010). The Pellet Handbook: The Production and thermal Utilization of Biomass Pellets. London: Earthscan Ltd.
Pang, S., and Mujumdar, A. S. (2010). Drying of Woody Biomass for Bioenergy: Drying Technologies and Optimization for an Integrated Bioenergy Plant. Drying Tech. 28, 690–701. doi:10.1080/07373931003799236
Peng, J. H., Bi, H. T., Sokhansanj, S., and Lim, J. C. (2012). A Study of Particle Size Effect on Biomass Torrefaction and Densification. Energy Fuels 26, 3826–3839. doi:10.1021/ef3004027
Phanphanich, M., and Mani, S. (2011). Impact of Torrefaction on the Grindability and Fuel Characteristics of forest Biomass. Bioresour. Tech. 102, 1246–1253. doi:10.1016/j.biortech.2010.08.028
Ragauskas, A. J., Williams, C. K., Davison, B. H., Britovsek, G., Cairney, J., Eckert, C. A., et al. (2006). The Path Forward for Biofuels and Biomaterials. Science 311, 484–489. doi:10.1126/science.1114736
Ramesh, T., Rajalakshmi, N., and Dhathathreyan, K. S. (2015). Activated Carbons Derived from Tamarind Seeds for Hydrogen Storage. J. Energ. Storage. 4, 89. doi:10.1016/j.est.2015.09.005
Ren, S., Lei, H., Wang, L., Yadavalli, G., Liu, Y., and Julson, J. (2014). The Integrated Process of Microwave Torrefaction and Pyrolysis of Corn stover for Biofuel Production. J. Anal. Appl. Pyrolysis 108, 248–253. doi:10.1016/j.jaap.2014.04.008
Richard, T. L. (2010). Challenges in Scaling up Biofuels Infrastructure. Science 329, 793–796. doi:10.1126/science.1189139
Safari, M., Abdi, M., Adi, M., and Kafashan, J. (2018). Optimization of Biogas Productivity in Lab-Scale by Response Surface Methodology. Renew. Energ. 118, 368. doi:10.1016/j.renene.2017.11.025
Satpathy, S. K., Tabil, L. G., Meda, V., Naik, S. N., and Prasad, R. (2014). Torrefaction of Wheat and Barley Straw after Microwave Heating. Fuel 124, 269–278. doi:10.1016/j.fuel.2014.01.102
Senol, H., Ersan, M., and Gorgun, E. (2020). Optimization of Temperature and Pretreatments for Methane Yield Hazelnut Shells Using the Response Surface Methodology. Fuel 271, 117585. doi:10.1016/j.fuel.2020.117585
Shankar Tumuluru, J., Sokhansanj, S., Hess, J. R., Wright, C. T., and Boardman, R. D. (2011). REVIEW: A Review on Biomass Torrefaction Process and Product Properties for Energy Applications. Ind. Biotechnol. 7, 384–401. doi:10.1089/ind.2011.7.384
Soleimani, M., Tabil, X. L., Grewal, R., and Tabil, L. G. (2017). Carbohydrates as Binders in Biomass Densification for Biochemical and Thermochemical Processes. Fuel 193, 134–141. doi:10.1016/j.fuel.2016.12.053
Spelter, H., and Toth, D. (2009). “North America’s wood Pellet Sector,”. Paper No. FPL-RP-656 (Washington, DC: U.S. Department of Agriculture, Forest Services, Forest Products Laboratory). doi:10.2737/FPL-RP-656
Tabil, L. G. (1996). Binding and Pelleting Characteristics of Alfalfa. [Ph.D. thesis]. [Saskatoon (SK)] (Saskatoon: University of Saskatchewan).
Tilay, A., Azargohar, R., Drisdelle, M., Dalai, A., and Knozinski, J. (2015). Canola Meal Moisture-Resistant Fuel Pellets: Study O the Effects of Process Variables and Additives on the Pellet Quality and Compression Characteristics. Ind. Crops Prod. 63, 337. doi:10.1016/j.indcrop.2014.10.008
Tumuluru, J. (2016). Effect of Deep Drying and Torrefaction Temperature on Proximate, Ultimate Composition, and Heating Value of 2-mm lodgepole pine (Pinus contorta) Grind. Bioengineering 3, 16. doi:10.3390/bioengineering3020016
Wang, C., Peng, J., Li, H., Bi, X. T., Legros, R., Lim, C. J., et al. (2013). Oxidative Torrefaction of Biomass Residues and Densification of Torrefied Sawdust to Pellets. Bioresour. Technol. 127, 318–325. doi:10.1016/j.biortech.2012.09.092
Wang, M. J., Huang, Y. F., Chiueh, P. T., Kuan, W. H., and Lo, S. L. (2012). Microwave-induced Torrefaction of rice Husk and Sugarcane Residues. Energy 37, 177–184. doi:10.1016/j.energy.2011.11.053
Wannapeera, J., Fungtammasan, B., and Worasuwannarak, N. (2011). Effects of Temperature and Holding Time during Torrefaction on the Pyrolysis Behaviours of Woody Biomass. J. Anal. App Pyrolysis 92, 99. doi:10.1016/j.jap.2011.04.010
Whalen, J., Xu, C., Shen, F., Kumar, A., Eklund, M., and Yan, J. (2017). Sustainable Biofuel Production from Forestry, Agricultural and Waste Biomass Feedstocks. Appl. Energ. 198, 281–283. doi:10.1016/j.apenergy.2017.05.079
Whittaker, C., and Shield, I. (2017). Factors Affecting wood, Energy Grass and Straw Pellet Durability - A Review. Renew. Sust. Energ. Rev. 71, 1–11. doi:10.1016/j.rser.2016.12.119
Wood Energy (2006). Simple Ways to Check wood Pellet Quality. Available at: http://www.woodenergy.ie/keywords/woodpellets/(Accessed July 13, 2021).
Xu, J. (2015). “Microwave Pretreatment,” in In Pretreatment of Biomass: Processes and Technologies. Editor A. Pandey (Waltham, MA, USA: Elsevier), 157–172. doi:10.1016/b978-0-12-800080-9.00009-8
Keywords: wheat straw, barley straw, plastic binder, densification, microwave torrefaction, solid fuel
Citation: Agu OS, Tabil LG, Mupondwa E and Emadi B (2021) Torrefaction and Pelleting of Wheat and Barley Straw for Biofuel and Energy Applications. Front. Energy Res. 9:699657. doi: 10.3389/fenrg.2021.699657
Received: 23 April 2021; Accepted: 02 August 2021;
Published: 28 September 2021.
Edited by:
Wasif Farooq, King Fahd University of Petroleum and Minerals, Saudi ArabiaReviewed by:
Paola Brachi, Istituto di ricerche sulla combustione (IRC), ItalyImtiaz Ali, King Abdulaziz University, Saudi Arabia
Copyright © 2021 Agu, Tabil, Mupondwa and Emadi. This is an open-access article distributed under the terms of the Creative Commons Attribution License (CC BY). The use, distribution or reproduction in other forums is permitted, provided the original author(s) and the copyright owner(s) are credited and that the original publication in this journal is cited, in accordance with accepted academic practice. No use, distribution or reproduction is permitted which does not comply with these terms.
*Correspondence: Lope G. Tabil, bG9wZS50YWJpbEB1c2Fzay5jYQ==