- 1Department of Agricultural and Biosystems Engineering, Iowa State University, Ames, IA, United States
- 2Faculty of Industrial Sciences and Technology, Universiti Malaysia Pahang, Kuantan, Malaysia
Lignin and hemicellulose structures in cellulosic materials serve as a barrier for enzyme reactions. A pretreatment step is often needed to break these components to allow the biomass to be utilized as a source of value-added products. Various available pretreatment methods possess common drawbacks of the high amount of liquid and chemical requirements, harsh process conditions, and the high amount of waste produced, which driving up the production costs of bioproducts. Low moisture anhydrous ammonia (LMAA) pretreatment capable of eliminating those drawbacks. In this study, Distillers Dried Grains with Solubles (DDGS), corn gluten feed (CGF), corn fiber (CF), and oil palm frond (OPF) with different moisture contents were subjected to LMAA pretreatment at the specific ammonia loading rate, 1 h ammoniation, and 75°C incubation temperature. This pretreatment successfully decreased the lignin content of the materials, increased their percentage of α-cellulose, and improved enzymatic digestibility for most of the materials tested. The effect of moisture content (30 and 50% db) was found to be more significant than that of incubation time (24 and 72 h).
Introduction
Pretreatment is a crucial step in any type of lignocellulosic-based bioproduct production. Through pretreatment, the recalcitrant structure of lignocellulosic materials is loosened and disrupted, thus enhancing enzyme penetration and hydrolysis of the biomass crystalline backbone structure. However, pretreatment has also been found to potentially increase the production cost of the lignocellulosic-based bioproducts, either because of the cost of intensive processing or the amount of chemicals required. Conventional pretreatment methods such as chemical and mechanical pretreatment essentially require high chemical loading, high energy consumption, a large amount of water, and a need for waste treatment. Other pretreatment approaches have been developed to eliminate these drawbacks; one of them, physicochemical pretreatment, combines the advantages of chemical pretreatment and physical pretreatment. Typical physical pretreatment would require an energy cost of approximately >20% of operating cost (Baruah et al., 2018). Nuruddin et al. (2016) highlighted that the tandem operation of physical and chemical pretreatment could significantly reduce the energy cost from the reduction of intensity of each single pretreatment (Nuruddin et al., 2016). Chemical pretreatment incurs not only high operating cost from the large volume of chemical used and waste produced, formation of undesired inhibitor compounds and severe cellulose degradation but also from high capital cost due to high corrosion level of equipment as in acid pretreatment (Taylor et al., 2019; Stoklosa et al., 2021). Therefore, physicochemical pretreatment is seen as a viable way to increase the value of some underutilized materials.
Ammonia-based physicochemical pretreatments have been among those most explored by researchers because of the attractive properties of ammonia (NH3) as a pretreatment agent, including the effects of swelling, delignification, and preservation (Li and Kim, 2011; Yoo et al., 2011). Among these pretreatment methods include ammonia fiber explosion (AFEX), ammonia recycle percolation (ARP), and low liquid ammonia (LLA) pretreatment. These pretreatments still require either high consumption of energy or liquids, thus are not considered feasible for commercial application. AFEX, ARP and LLA run at approximately 60–120, 150–210, and 30°C, respectively. While the high amount of water washing requirement is essential to reduce the alkalinity of the materials, which will then generate a large sum of wastewater in addition to the use of aqueous pretreatment chemical itself (Kim et al., 2016). Not long ago, low moisture anhydrous ammonia (LMAA) pretreatment was introduced, which employs gaseous ammonia (NH3) as the pretreatment agent at nearly ambient operating conditions (Yoo et al., 2011). The use of gaseous NH3 results in a substantial reduction of liquid requirements and also since it is gas, it could easily be removed from the materials with the aid of vacuum or slight increase in temperature, eliminating the need for additional water washing step to remove the residual NH3. The study on LMAA pretreatment is still limited with most works focused on specific biomass such as corn stover (Yoo et al., 2011; Cheng and Rosentrater, 2016; Guo et al., 2017; Yang and Rosentrater, 2017), sweet sorghum bagasse (Stoklosa et al., 2021), ryegrass (Yasuda et al., 2015) and napiergrass (Yasuda et al., 2013), limiting the feasibility evaluation for its wider application. Regardless, LMAA pretreatment of corn stover has yielded promising results in a large scale reactor, suggesting the possibility of effectively using LMAA pretreatment for larger-scale application (Cheng and Rosentrater, 2016; Yang and Rosentrater, 2017).
This study subjected distillers dried grains with solubles (DDGS), corn gluten feed (CGF), corn fiber (CF), and oil palm fronds (OPF), which are undervalued and underutilized materials, to the LMAA pretreatment process. DDGS, CGF, and CF are generated in abundance from corn processing plants as co-products and currently have relatively low economic value. The current market for these materials is primarily in animal feed manufacturing and only a small proportion as low-cost food additives. In 2019–2020, U.S. DDGS and CGF exports were down by 7 and 26% respectively compared to the previous year (Richman, 2021). CF is often mixed with corn gluten feed therefore rarely been exported. Similarly, oil palm fronds (OPF) are abundantly generated throughout the year in palm oil plantation areas. In Malaysia, between 44 and 51 × 106 t of OPF is annually produced (Goh et al., 2010; Awalludin et al., 2015), with the amount higher during replanting periods. There is no current commercial application of OPF. Attempts to utilize it in ruminants feed production and wood manufacturing did not yield promising results (Bals et al., 2006).
Revenues from these materials are not comparable to those of the primary manufacturing products, i.e., ethanol from corn wet and dry milling, and oil from palm oil mills. The growth of the palm oil industry has resulted in continuous generation of OPF (Ooi et al., 2017; Rizal et al., 2018), and the relatively slow current ethanol market (2020) has resulted in a greater desire of corn processing industries to increase their co-products value and market (Cooper et al., 2021).
The similarity of these materials is the high content of non-fermentable polysaccharides (cellulose, and hemicellulose), which is of important polymer feedstock for biorefinery and other bio-based structural product. The LMAA pretreatment has the potential to make these polysaccharides more available by removal or disruption of the recalcitrant lignin. It is important to ensure that the utilization of these waste materials to be at the lowest economic effect possible to increase the whole life-cycle value of the primary product. Hence, this study proposed a way to utilize such co-products and other waste materials in a possibly lower-cost approach using LMAA pretreatment (Mahmud and Rosentrater, 2020). The study focused on investigating the effects of LMAA pretreatment on DDGS, CGF, CF, and OPF. The efficiencies of LMAA pretreatment were evaluated in terms of the reduction in lignin content, increase in available cellulose, and also improvement in the percentage of enzymatic digestibility, which could indicate its suitability especially for a biochemical process for generation of higher value compounds.
Materials and Methods
Materials
DDGS was obtained from Absolute Energy, L.L.C. (St. Ansgar, IA, United States), CGF was obtained from Grain Processing Corporation (Muscatine, IA, United States), and CF was obtained from Honeyville, Inc. (North Ogden, UT, United States). OPF was obtained from an oil palm plantation site in Malaysia. OPF was cleaned, dried, and chopped into 1 cm pieces. The compositions of each of the raw materials are summarized in Table 1. The moisture content of all raw materials was determined according to the NREL LAP standard method (Sluiter et al., 2008). The moisture content of the raw materials was adjusted to 30% dry basis (db) and 50% dry basis (db) by addition of water and steeped for 24 h.
Enzyme
Cellulase enzyme (Celluclast® 1.5 L) used was purchased from Sigma Aldrich Corp. (St. Louis, MO, United States) with a determined activity of 65 FPU/ml.
Low Moisture Anhydrous Ammonia Pretreatment
LMAA pretreatment was conducted in a 0.9 L reactor (Parr Instrument Co., Moline, IL, United States). Anhydrous ammonia (NH3) loading was 0.09 g/g biomass for DDGS, CGF, and CF, and 0.18 g/g biomass for OPF. This was based on a previous study, which highlighted that materials with higher lignin content should be treated with a higher dosage of ammonia loading (Cheng and Rosentrater, 2016). In this regard, OPF used in this work contains similar lignin content compared to corn stover used in their work. NH3 was introduced into the reactor filled with raw materials while monitoring the pressure (Figure 1). The reactor was held for 1 h after which the lid was removed in the fume hood for 15 min to enable evaporation of the NH3. The ammoniated raw materials were transferred into glass bottle with screw cap and subjected to incubation at 75°C for 24 and 72 h in a convection oven. When the incubation process had been completed, the glass bottle caps were removed for 1 h to allow surplus NH3 to evaporate. The whole pretreatment procedure was according to (Cheng and Rosentrater, 2016; Yang and Rosentrater, 2017).
Compositional Analyses
Holo-, Alpha-, and Hemicellulose Determination
Holocellulose and α-cellulose content of the pretreated samples were determined using the Wise method (Wise et al., 1946). Hemicellulose content obtained by subtracting the holocellulose content with the α-cellulose content.
Lignin and Carbohydrate Determination
Lignin content determination was according to the NREL LAP standard method (Sluiter et al., 2012). The acid-insoluble lignin (AIL) content was determined based on a gravimetric method while the acid-soluble lignin (ASL) content was determined at 320 nm using Cary 8454 UV/Vis Diode Array Spectrophotometer (Agilent Technologies, Santa Clara, CA, United States). Absorptivity at lambda max value (ε) of 30 L/g cm was used to calculate the percentage of soluble lignin for all types of raw materials (Noureddini and Byun, 2010; Nomanbhay et al., 2013). The glucose content was determined using HPLC equipped with Bio-Rad Aminex HPX-87H column (Bio-Rad Laboratories, Hercules, CA, United States), Varian 356-LC refractive index detector (Varian, Inc., CA, United States), guard column and autosampler based on the following conditions: injection volume—10 μl; mobile phase—0.01 N HPLC grade sulfuric acid; flow rate—0.6 ml/min; column temperature—65°C; detector temperature—as close as possible the column temperature; detector—refractive index; run time—20 min. A set of sugar recovery standards (SRS) was prepared to determine degradation losses, which is used to compensate for degradation losses of the samples.
Equations 1–4 were used to calculate the percentage of lignin and glucose in the sample after hydrolysis, where AIR, acid-insoluble residue; ODW, oven dry weight; Wt.C, weight of crucible; Wt.P, weight of protein; V, volume; correction factor = 0.9. The protein content of each raw materials was assumed at 31.4% (Pedersen et al., 2014), 25.1% (Miron et al., 2001), 9.9% (Noureddini and Byun, 2010), and 5.3% (Khalil et al., 2012) for DDGS, CGF, CF, and OPF, respectively.
Enzymatic Digestibility Test
Enzymatic digestibility test was conducted according to the NREL LAP standard method (Selig et al., 2008). The cellulase enzyme loading was 60 FPU/g cellulose. The mixture was incubated at 50°C and 150 rpm in an incubator shaker (Excella E24 Incubator Shaker Series, New Brunswick Scientific, Edison, NJ, United States). Samples were taken at 24 h intervals for up to 120 h. Percentage of digestions were calculated in term of glucan digestibility based on Eq. 5, where 0.9 is a correction factor for calculating 6-cabon polymeric sugars from corresponding monomeric sugars.
Non-linear changes in percentage digestibility over time were modeled by developing a regression trendline using the Hanes-Woolf approach, where the kinetic rate constants were determined by linear regression on a time over digestibility versus time plot.
Experimental Design and Data Analysis
The independent variables tested for each feedstock were moisture content (30% db and 50% db) and LMAA incubation time (untreated (UT), 24, and 72 h). Untreated samples of each feedstock were subjected to the same analyses and served as a control. The measured dependent variables were α-cellulose (wt. %), hemicellulose (wt. %), AIL (wt. %), ASL (wt. %), and glucan contents (wt. %), along with enzymatic digestibilities percentages. All experimental procedures were run in triplicate and average data with standard deviation were presented.
Statistical analyses were conducted using JMP Pro 13.1.0 (SAS Institute, Cary, NC, United States) statistical software. Comparisons amongst mean values of results from the moisture content factor were conducted using paired Student’s t-test. Tukey’s Honestly Significant Difference (HSD) test was used for multiple pairwise comparisons amongst mean values of results from the incubation time factor, as well as the interaction between factors. The analyses were conducted at α = 0.05.
Results and Discussions
Effect of Moisture Content and Incubation Time on Biomass Compositions
Variations in incubation time and moisture content have resulted in different amounts of α-cellulose, hemicellulose, AIL, and ASL for all types of materials tested. Table 2 summarizes the p-values of each factor at α = 0.05. Results for main and interaction effects of factors on materials compositions after LMAA pretreatment are shown in Tables 3, 4, respectively.
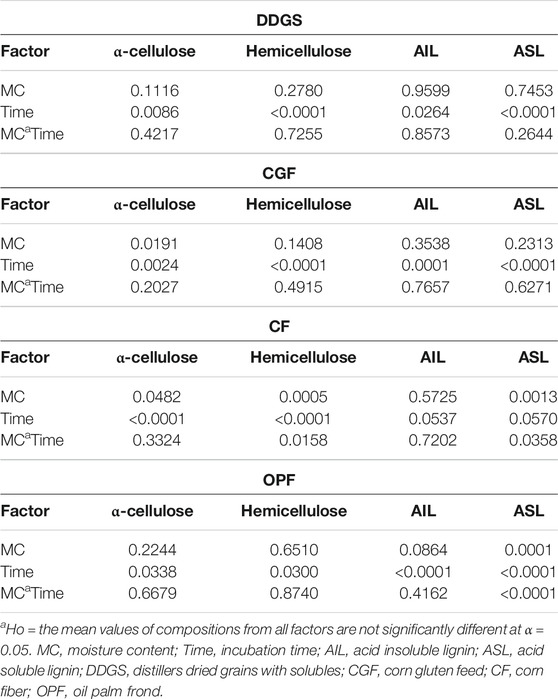
TABLE 2. p-values of individual and interaction effects after LMAA pretreatmenta.
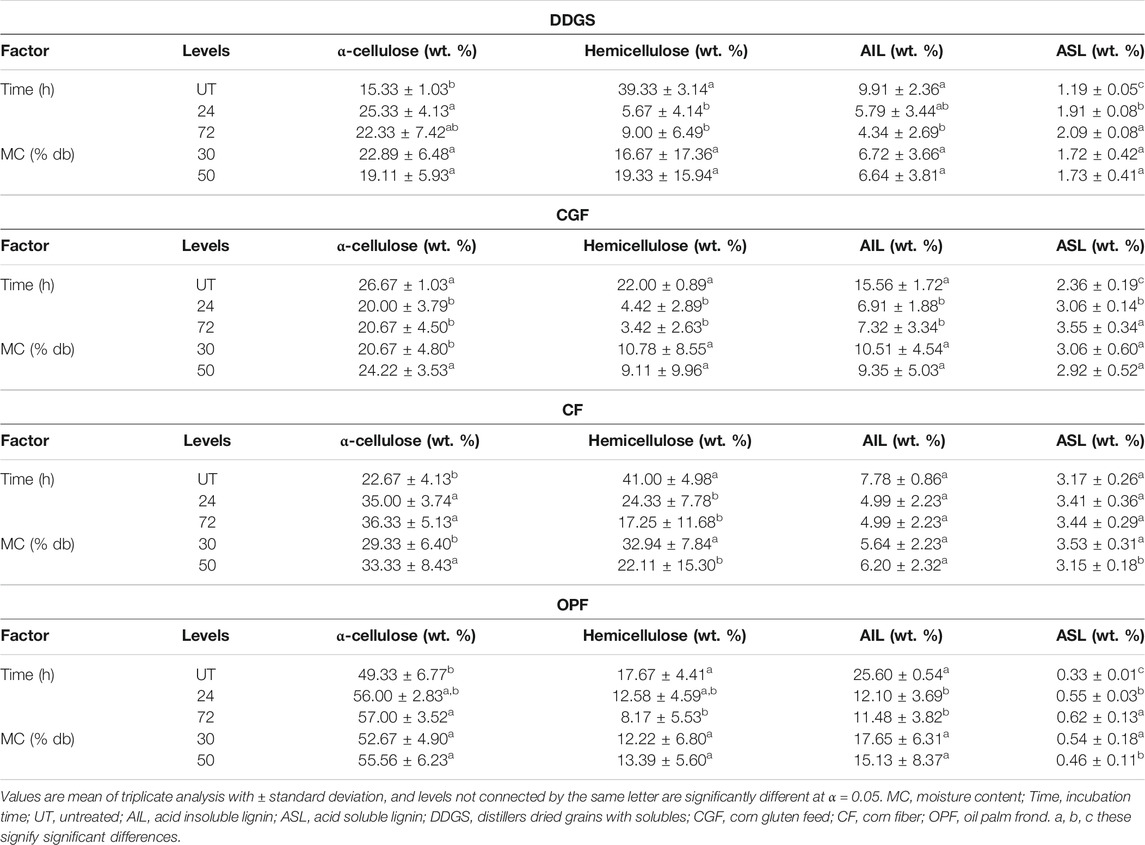
TABLE 3. Main effects of factors on biomass compositions after LMAA pretreatment. a, b, c these signify significant differences.
Distillers Dried Grains With Solubles
Incubation time had a significant effect on DDGS compositions (Table 2). There was no significant difference in the compositions at the moisture contents tested, suggesting that working at lower MC will insignificantly affect sample compositions. The results (mean values) for the main effect (Table 3) and the interaction effect (Table 4) show that different incubation times resulted in significant differences in mean values of compositions between level UT and the others but not always significantly different between levels 24 and 72, suggesting that 24 h is a sufficient incubation time for DDGS.
The highest cellulose content recorded was 27.33 wt. % from 30% MC DDGS treated for 24 h (Table 4). Similarly, the same parameters resulted in no significant differences in the mean of hemicellulose and AIL, but not for ASL. It could be observed that cellulose in DDGS was slightly decreased as incubation time increased to 72 h, suggesting that a longer incubation period might enhance cellulose degradation, either partially into glucose or fully into the carbon unit. The latter is undesirable in the biochemical process because it would decrease the substrate available for the fermentation process. Results of glucan content (Figure 2) show that total glucan in the sample was not decreased, perhaps eliminating the possibility of occurrence for the latter scenario mentioned above.
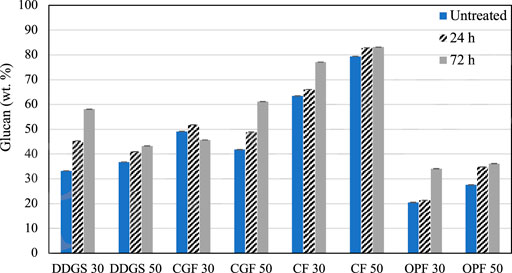
FIGURE 2. Glucan content in the biomass after LMAA pretreatment. Error bars represent ± standard deviations. DDGS, distillers dried grains with solubles; CGF, corn gluten feed; CF, corn fiber; OPF, oil palm frond. Numbers in the x-axis indicate moisture content designation.
Corn Gluten Feed
In CGF, p-values of <0.05 were recorded with respect to a time factor, indicating that different times resulted in significantly different compositions. In spite of this, based on the results in Tables 3, 4, significant differences in compositions were recorded only between levels UT and 24, and levels UT and 72 but not always between levels 24 and 72. Varying the MC resulted in no significant difference in mean values of compositions (except for α-cellulose content). α-cellulose content in CGF was decreased after the pretreatment compared to that of untreated samples, possibly indicating that the pretreatment conditions applied were too much for CGF, causing degradation of α-cellulose.
Analysis of glucan content (Figure 2) shows a slight reduction of total glucan in 30% MC CGF, possibly indicating sugar degradation. This effect was not observed in 50% MC CGF. Pretreatment conducted on 50% MC CGF recorded a significantly less α-cellulose degradation than that of 30% MC CGF. However, the results between 24 and 72 h incubation times were not significantly different.
Corn Fiber
The effect of MC on CF compositions was more apparent than those of DDGS and CGF, with a significant difference in the results except for AIL content. Sample with 50% MC recorded significantly higher α-cellulose, lower hemicellulose, and lower ASL. Conversely, there was no statistically significant difference in mean values of compositions between levels 24 and 72 of the incubation time, suggesting that 24 h LMAA incubation time might be sufficient for CF. The α-cellulose content recorded for 50% MC CF treated for 24 h (38 wt. %) were not significantly different from those of 72 h (39.33 wt. %) (Table 4). Other compositions exhibited similar trends. There was a statistically significant interaction between all factors for hemicellulose and ASL content (Table 2).
Oil Palm Frond
For OPF, there was no significant difference of α-cellulose recorded for the different MC tested. This was also true for hemicellulose and AIL content, but not for ASL content. Different incubation time was mostly giving a significant difference of results at levels 0 and 24, and between levels 0 and 72, but not always between levels 24 and 72. Only the mean of ASL content has recorded a statistically significant interaction between all factors (Table 2). The cellulose content recorded for 50% MC OPF treated for 24 h (58 wt. %) was insignificantly different from those of 72 h (59.33 wt. %), possibly indicating that these parameters (50% MC and 24 h) are sufficient for LMAA pretreatment of OPF.
From the results, lower MC (30%) in the DDGS and OPF was observed to not giving a statistically significant difference in α-cellulose content after LMAA pretreatment from those for 50% MC biomass, suggesting its suitability for future use. For CGF and CF, significantly higher α-cellulose content was recorded at higher MC (50%). According to Yang and Rosentrater (2017), LMAA pretreatment performance was optimum at 50% MC for corn stover, in comparison to the same materials at 20 and 80% MC. In this regard, looking more detail into the structure and compositions of each material used in this work, OPF is more closely resembles that of corn stover, however, corn stover required a higher MC requirement might be due to slightly higher cellulose content in it (Mensah et al., 2021). In other aspect, this also proves the requirement of moisture in LMAA pretreatment, although it varies with the cellulose content of materials (Kim et al., 2016; Yang and Rosentrater, 2017; Stoklosa et al., 2021). The difference in MC requirement could also be attributed to the difference in water absorption behavior that somehow related to the compositional difference in materials, which will be described in the following paragraph. α-cellulose content was assumed to be the most critical component because it gives the most sugar (glucose) for the fermentation process and is a high purity material for bio-based structural as such nanocellulose development (Phanthong et al., 2018), this was used to decide the most effective parameters for the LMAA pretreatment process. Following α-cellulose, hemicellulose also potentially can supply sugar (xylose) to the system (Mahmud and Rosentrater, 2020). It was observed that hemicellulose contents at the selected MC (30% for DDGS and OPF, and 50% for CGF and CF) were slightly less than those of the other MC, although the reason for the trend is unclear.
In the LMAA pretreatment process, it was hypothesized that water molecules present in the biomass bind with NH3 molecules during ammoniation and form ammonium ions (NH4+) and hydroxyl ions (OH−) that react with lignin (Yoo et al., 2011). Water molecules can also form hydrogen bonds with cellulose, which causes swelling of the cellulose crystalline structure, resulting in micro-cracks and later increasing accessibility of enzymes (Yoo et al., 2011; Célino et al., 2014). For CGF and CF, for which a significant amount of starch is part of their compositions, water might be absorbed into the starch in addition to that absorbed into the other cellulosic structure. Therefore, in total, more amount of water was absorbed as bound water, providing more sites for NH3-H2O reactions, justifying the requirement of higher MC by these materials. For OPF, although the presence of high cellulose might enhance water absorption and therefore potentially produce a higher α-cellulose content after the pretreatment, no significant differences were found between 50 and 30% MC samples. For DDGS, which consists of a low amount of starch and cellulose, only a small amount of water was retained in its structure to provide the pretreatment effect. The addition of more water to DDGS might result in its only being kept in the structure as free water and thus not contribute to any reaction with NH3 (Yoo et al., 2011).
Several previous studies have reported that water absorption capacity was less in protein than in starch and cellulose, explaining the results of this study (Greer and Stewart, 1959; Wang et al., 2007). The approximate starch content in DDGS, CGF, and CF, are 6% (Pedersen et al., 2014), 20% (Schroeder, 2012), and 17.77% (Noureddini and Byun, 2010), respectively. For the incubation time factor, longer time (72 h) resulted in no significant overall effect on the materials, especially in terms of α-cellulose content, which was in contrast to the previous study (Yang and Rosentrater, 2017). This might be attributed to the higher NH3 loading applied during ammoniation, which might be suitable for materials used in this work, speeding up the digestion reaction within the structural materials.
Other than increasing the α-cellulose available in the materials compared to that in untreated materials (except for CGF), the LMAA pretreatment decreased the hemicellulose and AIL content for all materials. While the ASL content for all materials after pretreatment was increased, this was not particularly valuable information in biochemical processing, because this fraction would be removed from the system either during filtration or evaporated by the drying process (a moisture reduction process that is required before the waste can be fed into the boiler).
The p-values from statistical analysis (Table 2) support the results described. p-values lower than 0.05 indicated no evidence that varying the associated factors would lead to a different mean value. Most interaction effects of the factors in all type of materials tested reflected insignificant results at α = 0.05, showing no evidence that effects of time differed with different materials MC, as reported by Cheng and Rosentrater (2016), Yang and Rosentrater (2017). Only several compositions for several types of materials, the mean of ASL content for CF and OPF, and the mean of hemicellulose content for CF, exhibited a significant interaction effect. It was rather weak supporting data for the selection of the best working conditions. Table 5 summarizes the comparison of materials compositions after the pretreatment process recorded in this study with the available results from others for DDGS, CF, and OPF. No previous research on CGF pretreatment was available for comparison. It has been proven that LMAA provides a competitive way of biomass pretreatment at a potentially lower cost than other pretreatment approaches (Yoo et al., 2011; Mahmud and Rosentrater, 2019).

TABLE 5. Biomass compositions after LMAA pretreatment and comparison with other published pretreatment processes.
Effect of Moisture Content and Pretreatment Time on Enzymatic Digestibility
Figures 3–6 show the results for enzymatic digestibility tests. The percentage digestibility of all LMAA pretreated materials was higher than that of untreated materials (UT), indicating that LMAA pretreatment was successful in allowing more penetration of hydrolysis enzyme to the cellulose. The highest digestibility values recorded at the end of hydrolysis for DDGS, CGF, and CB were from those with 30% MC and treated for 24 h, with 76.02%, 62.87%, and 80.28% digestibility, respectively. The highest digestibility percentage recorded for OPF was 54.15%, from those with 50% MC and treated for 24 h. These equivalents to about 32%, 28%, 82% and 81% increase in digestibility compared to those of UT samples for DDGS, CGF, CF and OPF, respectively. As a comparison (Yang and Rosentrater, 2017), recorded a 64% increase in digestibility of LMAA pretreated corn stover, whereas 80%, 6.4% increase in digestibility were recorded for corn stover pretreated with other ammonia pretreatments, which were aqueous ammonia and AFEX pretreatment, respectively (Kim and Lee, 2007; Baruah et al., 2018). While (Jung et al., 2012) recorded ∼64% digestibility of aqueous pretreated OPF. The percentages of digestibilities generally increased as digestion time increased. For the commercial application of the process, from an economic standpoint, 24 h of reaction would be considered sufficient for all type of biomass tested, since there was no significant difference between the percentage digestibility values at 24 and 72 h (Table 6). However, this is dependent on the concentration of enzyme used, with comparison (Yang and Rosentrater, 2017) required longer digestibility time due to low concentration of cellulase (45 FPU/ml).
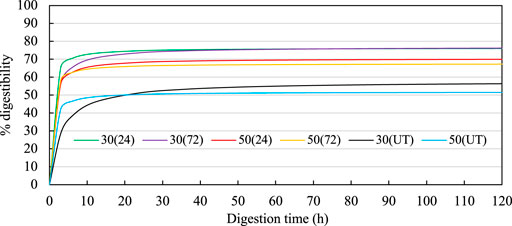
FIGURE 3. Enzymatic digestibility curves for treated DDGS. In the legend, the first numbers indicate the MC (%db), the numbers in the parentheses indicate the incubation time (h). Hanes-Woolf linear regressions used to estimate the digestibilites over time were 30 (24): Y = 0.0131x + 0.0065; 30 (72): Y = 0.013x + 0.0138; 50 (24): Y = 0.0142x + 0.0106; 50 (72): Y = 0.0148x + 0.0071; 30(UT): Y = 0.0173x + 0.0529; 50(UT): Y = 0.0193x + 0.0131. UT indicates untreated DDGS.
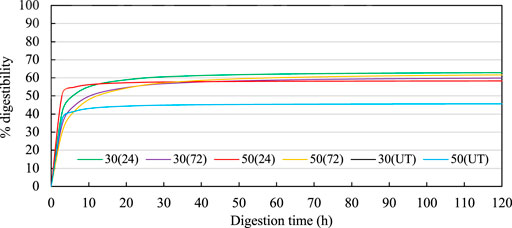
FIGURE 4. Enzymatic digestibility curves for treated CGF. In the legend, the first numbers indicate the MC (%db), the numbers in the parentheses indicate the incubation time (h). Hanes-Woolf linear regressions used to estimate the digestibilites over time were 30 (24): Y = 0.0157x + 0.0248; 30 (72): Y = 0.0164x + 0.0372; 50 (24): Y = 0.0171x + 0.007; 50 (72): Y = 0.0158x + 0.051; 30(UT): Y = 0.0218x + 0.0144; 50(UT): Y = 0.0218x + 0.0144. UT indicates untreated CGF.
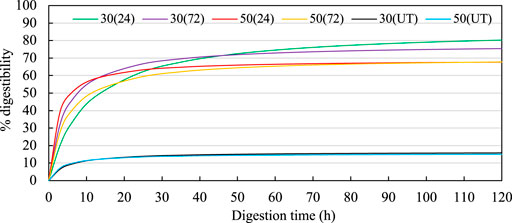
FIGURE 5. Enzymatic digestibility curves for treated CF. In the legend, the first numbers indicate the MC (%db), the numbers in the parentheses indicate the incubation time (h). Hanes-Woolf linear regressions used to estimate the digestibilites over time were 30 (24): Y = 0.0115x + 0.1147; 30 (72): Y = 0.0128x + 0.055; 50 (24): Y = 0.0145x + 0.0328; 50 (72): Y = 0.0142x + 0.0659; 30(UT): Y = 0.0609x + 0.2771; 50(UT): Y = 0.0647x + 0.2278. UT indicates untreated CF.
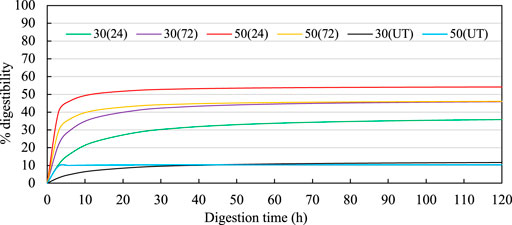
FIGURE 6. Enzymatic digestibility curves for treated OPF. In the legend, the first numbers indicate the MC (%db), the numbers in the parentheses indicate the incubation time (h). Hanes-Woolf linear regressions used to estimate the digestibilites over time were 30 (24): Y = 0.0262x + 0.2085; 30 (72): Y = 0.0212x + 0.0752; 50 (24): Y = 0.0183x + 0.0199; 50 (72): Y = 0.0214x + 0.038; 30(UT): Y = 0.0798x + 0.7621; 50(UT): Y = 0.0964x + 0.0235. UT indicates untreated OPF.
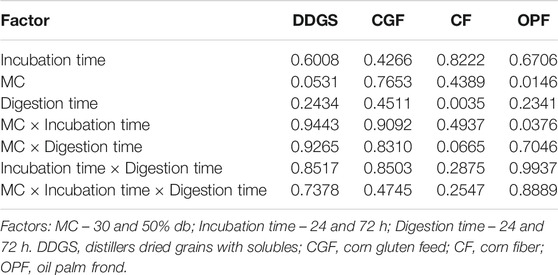
TABLE 6. p-values of main and interaction effects on enzymatic digestibilities of the LMAA-treated biomass.
p-values of the main effects revealed no significant difference in digestibility resulting from most of the factors tested. The exception was observed in the main effect of MC for OPF and the main effect of digestion time for CF, in which the digestion of 50% MC OPF was significantly higher than that of 30% MC, and the digestion of CF at 72 h was significantly higher than that at 24 h. With respect to the most significant parameters giving the best yield of α-cellulose, the highest percentage digestibility recorded for DDGS was 73.66% (30% MC and 24 h incubation), for CGF was 57.50% (50% MC and 24 h incubation), for CF was 66.26% (50% MC and 24 h incubation), and for OPF was 52.28% (50% MC and 24 h incubation).
Conclusion
In this study, DDGS, CGF, CF, and OPF were treated using LMAA pretreatment. DDGS required lesser MC (30%) for the process, while the other biomass candidates exhibited better results (increase in α-cellulose and enzymatic digestibilities) from pretreatment at 50% MC. The two LMAA incubation times tested produced statistically insignificant differences in results for all materials tested, leading to a conclusion of 24 h pretreatment is the best. Enzymatic hydrolysis conducted after the LMAA pretreatment process increased the digestibility of the biomass compared to those not treated; DDGS - 76.02%, CGF - 62.87%, CF - 80.28%, and OPF - 54.15%. These results have proven the potential of LMAA-treated materials for value-added product production especially in the production of higher value compounds through biochemical conversion. OPF is a major agricultural waste in oil palm plantation shown a promising future in increasing profits of the plantation owner. This study also highlights the potential of corn milling co-products to be used in a variety of applications other than in the feed manufacturing market. Additionally, some published techno-economic analyses have concluded significantly lower operating cost for biorefineries that adopt LMAA treatment. This justifies continued work in this area to ensure more concrete findings. Future studies should include more variety in ammonia loadings to determine the effect of higher concentrations on digestion, of which the analysis could be conducted in more detail through chromatography analysis. Moreover, this study concluded that 24 h digestion time was sufficient for enzyme digestion, potentially giving more yield to the biorefinery. It is worth investigations the correlation of enzyme concentration and ammonia loading with enzyme digestibility performance.
Data Availability Statement
The raw data supporting the conclusions of this article will be made available by the authors, without undue reservation.
Author Contributions
KR conceived and supervised the research, and revised and edited the manuscript. NM conducted the research, conducted the analysis, and drafted the manuscript.
Conflict of Interest
The authors declare that the research was conducted in the absence of any commercial or financial relationships that could be construed as a potential conflict of interest.
References
Awalludin, M. F., Sulaiman, O., Hashim, R., and Nadhari, W. N. A. W. (2015). An Overview of the Oil Palm Industry in Malaysia and its Waste Utilization Through Thermochemical Conversion, Specifically via Liquefaction. Renew. Sust. Energ. Rev. 50, 1469–1484. doi:10.1016/j.rser.2015.05.085
Bals, B., Dale, B., and Balan, V. (2006). Enzymatic Hydrolysis of Distiller's Dry Grain and Solubles (DDGS) Using Ammonia Fiber Expansion Pretreatment. Energy Fuels 20, 2732–2736. doi:10.1021/ef060299s
Baruah, J., Nath, B. K., Sharma, R., Kumar, S., Deka, R. C., Baruah, D. C., et al. (2018). Recent Trends in the Pretreatment of Lignocellulosic Biomass for Value-Added Products. Front. Energ. Res. 6, 1–19. doi:10.3389/fenrg.2018.00141
Célino, A., Fréour, S., Jacquemin, F., and Casari, P. (2014). The Hygroscopic Behavior of Plant Fibers: A Review. Front. Chem. 1, 43. doi:10.3389/fchem.2013.00043
Cheng, M., and Rosentrater, K. A. (2016). “Optimization of Low Moisture Anhydrous Ammonia (LMAA) Pretreatment for Corn Stover Enzymatic Digestibility during Hydrolysis Process”, in 2016 ASABE Annual International Meeting, Orlando, FL, July 17-20, 2016.
Cooper, G., McCaherty, J., Huschitt, E., Schwarck, R., and Wilson, C. (2021). 2021 Ethanol Industry Outlook. Washington, DC. Available at: www.ethanolrfa.org.
Gáspár, M., Juhász, T., Szengyel, Z., and Réczey, K. (2005). Fractionation and Utilisation of Corn Fibre Carbohydrates. Process Biochem. 40, 1183–1188. doi:10.1016/j.procbio.2004.04.004
Goh, C. S., Tan, K. T., Lee, K. T., and Bhatia, S. (2010). Bio-Ethanol From Lignocellulose: Status, Perspectives and Challenges in Malaysia. Bioresour. Technol. 101, 4834–4841. doi:10.1016/j.biortech.2009.08.080
Greer, E. N., and Stewart, B. A. (1959). The Water Absorption of Wheat Flour: Relative Effects of Protein and Starch. J. Sci. Food Agric. 10, 248–252. doi:10.1002/jsfa.2740100409
Guo, M., Jin, T., Nghiem, N. P., Fan, X., Qi, P. X., Jang, C. H., et al. (2017). Assessment of Antioxidant and Antimicrobial Properties of Lignin From Corn Stover Residue Pretreated with Low-Moisture Anhydrous Ammonia and Enzymatic Hydrolysis Process. Appl. Biochem. Biotechnol. 184, 350–365. doi:10.1007/s12010-017-2550-0
Jung, Y. H., Kim, S., Yang, T. H., Lee, H. J., Seung, D., Park, Y.-C., et al. (2012). Aqueous Ammonia Pretreatment, Saccharification, and Fermentation Evaluation of Oil Palm Fronds for Ethanol Production. Bioproc. Biosyst. Eng. 35, 1497–1503. doi:10.1007/s00449-012-0739-8
Khalil, H. P. S. A., Jawaid, M., Hassan, A., Paridah, M. T., and Zaidon, A. (2012). “Oil Palm Biomass Fibres and Recent Advancement in Oil Palm Biomass Fibres Based Hybrid Biocomposites,” in Composites and Their Applications. 1st Edn, Editor Hu, N. (London, United Kingdom: Intech Publication), 187–220.
Kim, J. S., Lee, Y. Y., and Kim, T. H. (2016). A Review on Alkaline Pretreatment Technology for Bioconversion of Lignocellulosic Biomass. Bioresour. Technol. 199, 42–48. doi:10.1016/j.biortech.2015.08.085
Kim, T. H., and Lee, Y. Y. (2007). Pretreatment of Corn Stover by Soaking in Aqueous Ammonia at Moderate Temperatures. Appl. Biochem. Biotechnol. 137–140, 81–92. doi:10.1007/s12010-007-9041-7
Li, X., and Kim, T. H. (2011). Low-Liquid Pretreatment of Corn Stover With Aqueous Ammonia. Bioresour. Technol. 102, 4779–4786. doi:10.1016/j.biortech.2011.01.008
Mahmud, N., and Rosentrater, K. A. (2019). Techno-Economic Analysis of Low Moisture Anhydrous Ammonia (LMAA) Pretreatment for Butanol Production From Oil Palm Frond. Biomass. Convers. Biorefin. Available at 14 December 2019. doi:10.1007/s13399-019-00564-5
Mahmud, N., and Rosentrater, K. A. (2020). Techno-Economic Analysis (TEA) of Different Pretreatment and Product Separation Technologies for Cellulosic Butanol Production From Oil Palm Frond. Energies 13, 181. doi:10.3390/en13010181
Mensah, M. B., Jumpah, H., Boadi, N. O., and Awudza, J. A. M. (2021). Assessment of Quantities and Composition of Corn stover in Ghana and Their Conversion into Bioethanol. Scientific Afr. 12, e00731. doi:10.1016/j.sciaf.2021.e00731
Miron, J., Yosef, E., and Ben-Ghedalia, D. (2001). Composition and In Vitro Digestibility of Monosaccharide Constituents of Selected Byproduct Feeds. J. Agric. Food Chem. 49, 2322–2326. doi:10.1021/jf0008700
Myat, L., and Ryu, G.-H. (2014). Characteristics of Destarched Corn Fiber Extrudates for Ethanol Production. J. Cereal Sci. 60, 289–296. doi:10.1016/j.jcs.2014.06.006
Nomanbhay, S. M., Hussain, R., and Palanisamy, K. (2013). Microwave-Assisted Alkaline Pretreatment and Microwave Assisted Enzymatic Saccharification of Oil Palm Empty Fruit Bunch Fiber for Enhanced Fermentable Sugar Yield. J. Sustain. Bioenergy Syst. 3, 7–17. doi:10.4236/jsbs.2013.31002
Noureddini, H., and Byun, J. (2010). Dilute-Acid Pretreatment of Distillers' Grains and Corn Fiber. Bioresour. Technol. 101, 1060–1067. doi:10.1016/j.biortech.2009.08.094
Nuruddin, M., Hosur, M., Uddin, M. J., Baah, D., and Jeelani, S. (2016). A Novel Approach for Extracting Cellulose Nanofibers From Lignocellulosic Biomass by Ball Milling Combined With Chemical Treatment. J. Appl. Polym. Sci. 133, 42990. doi:10.1002/app.42990
Ooi, Z. X., Teoh, Y. P., Kunasundari, B., and Shuit, S. H. (2017). Oil Palm Frond as a Sustainable and Promising Biomass Source in Malaysia: A Review. Environ. Prog. Sustain. Energy 36, 1864–1874. doi:10.1002/ep.12642
Pedersen, M. B., Dalsgaard, S., Knudsen, K. E. B., Yu, S., and Lærke, H. N. (2014). Compositional Profile and Variation of Distillers Dried Grains With Solubles From Various Origins With Focus on Non-starch Polysaccharides. Anim. Feed Sci. Technol. 197, 130–141. doi:10.1016/j.anifeedsci.2014.07.011
Phanthong, P., Reubroycharoen, P., Hao, X., Xu, G., Abudula, A., and Guan, G. (2018). Nanocellulose: Extraction and Application. Carbon Resour. Convers. 1, 32–43. doi:10.1016/j.crcon.2018.05.004
Rizal, N., Ibrahim, M., Zakaria, M., Abd-aziz, S., Yee, P., and Hassan, M. (2018). Pre-Treatment of Oil palm Biomass for Fermentable Sugars Production. Molecules 23, 1381. doi:10.3390/molecules23061381
Sabiha-Hanim, S., Noor, M. A. M., and Rosma, A. (2011). Effect of Autohydrolysis and Enzymatic Treatment on Oil Palm (Elaeis Guineensis Jacq.) Frond Fibres for Xylose and Xylooligosaccharides Production. Bioresour. Technol. 102, 1234–1239. doi:10.1016/j.biortech.2010.08.017
Schroeder, J. W. (2012). Corn Gluten Feed: Composition, Storage, Handling, Feeding, and Value. North Dakota State University. Available at: https://library.ndsu.edu/ir/bitstream/handle/10365/4796/as1127.pdf?sequence=1.
Richman, S. (2021). 2020 U.S. Distillers Grains Exports & Imports Statistical Summary. Ellisville, MO. Available at: www.ethanolrfa.org.
Selig, M., Weiss, N., and Ji, Y. (2008). Enzymatic Saccharification of Lignocellulosic Biomass. Available at: www.doe.gov.
Siti Sabrina, M. S., Roshanida, A. R., and Norzita, N. (2013). Pretreatment of Oil Palm Fronds for Improving Hemicelluloses Content for Higher Recovery of Xylose. J. Teknol. 62, 39–42. doi:10.11113/jt.v62.1877
Sluiter, A., Hames, B., Hyman, D., Payne, C., Ruiz, R., Scarlata, C., et al. (2008). Determination of Total Solids in Biomass and Total Dissolved Solids in Liquid Process Samples. Technical Report: NREL/TP-510-42621. Available at: www.doe.gov.
Sluiter, A., Hames, B., Ruiz, R., Scarlata, C., Sluiter, J., Templeton, D., et al. (2012). Determination of Structural Carbohydrates and Lignin in Biomass. Available at: www.doe.gov.
Stoklosa, R. J., Moore, C., Latona, R. J., and Nghiem, N. P. (2021). Butyric Acid Generation by Clostridium tyrobutyricum From Low-Moisture Anhydrous Ammonia (LMAA) Pretreated Sweet Sorghum Bagasse. Appl. Biochem. Biotechnol. 193, 761–776. doi:10.1007/s12010-020-03449-w
Taylor, M., Alabdrabalameer, H., and Skoulou, V. (2019). Choosing Physical, Physicochemical and Chemical Methods of Pre-treating Lignocellulosic Wastes to Repurpose into Solid Fuels. Sustainability 11, 3604. doi:10.3390/su11133604
Wang, L. Z., Liu, L., Holmes, J., Kerry, J. F., and Kerry, J. P. (2007). Assessment of Film-Forming Potential and Properties of Protein and Polysaccharide-Based Biopolymer Films. Int. J. Food Sci. Tech. 42, 1128–1138. doi:10.1111/j.1365-2621.2006.01440.x
Wise, L. E., Murphy, M., and Adieco, A. A. D. (1946). A Chlorite Holocellulose, its Fractionation and Bearing on Summative Wood Analysis and Studies on the Hemicelluloses. Pap. Trade J. 122, 35–43.
Yang, M., and Rosentrater, K. A. (2017). Small-Scale Low-Moisture Anhydrous Ammonia (LMAA) Pretreatment of Corn stover. Biomass Bioenergy 97, 38–42. doi:10.1016/j.biombioe.2016.12.013
Yasuda, M., Takenouchi, Y., Nitta, Y., Ishii, Y., and Ohta, K. (2015). Italian Ryegrass (Lolium multiflorum Lam) as a High-Potential Bio-Ethanol Resource. Bioenerg. Res. 8, 1303–1309. doi:10.1007/s12155-015-9582-5
Yasuda, M., Takeo, K., Nagai, H., Uto, T., Yui, T., Matsumoto, T., Ishii, Y., and Ohta, K. (2013). Enhancement of Ethanol Production From Napiergrass (Pennisetum purpureum Schumach) by a Low-Moisture Anhydrous Ammonia Pretreatment. J. Sustain. Bioenergy Syst. 3, 179–185. doi:10.4236/jsbs.2013.33025
Keywords: lignocellulose, biomas, LMAA pretreatment, ammonia, biorefinery and biofuel, bioproducts, pretreatment, lignin removal
Citation: Mahmud N and Rosentrater KA (2021) Low Moisture Anhydrous Ammonia Pretreatment of Four Lignocellulosic Materials—Distillers Dried Grains With Solubles, Corn Gluten Feed, Corn Fiber, and Oil Palm Frond. Front. Energy Res. 9:682522. doi: 10.3389/fenrg.2021.682522
Received: 18 March 2021; Accepted: 01 June 2021;
Published: 11 June 2021.
Edited by:
Ana Somoza-Tornos, University of Colorado Boulder, United StatesReviewed by:
Ernesto Mura, Indipendent Researcher, GermanyMohamad Nasir Mohamad Ibrahim, Universiti Sains Malaysia, Malaysia
Copyright © 2021 Mahmud and Rosentrater. This is an open-access article distributed under the terms of the Creative Commons Attribution License (CC BY). The use, distribution or reproduction in other forums is permitted, provided the original author(s) and the copyright owner(s) are credited and that the original publication in this journal is cited, in accordance with accepted academic practice. No use, distribution or reproduction is permitted which does not comply with these terms.
*Correspondence: Kurt A. Rosentrater, a2Fyb3NlbnRAaWFzdGF0ZS5lZHU=