- 1School of Chemical Engineering, Yeungnam University, Gyeongsan, South Korea
- 2Department of Chemical Engineering Technology, College of Applied Industrial Technology, Jazan University, Jazan, Saudi Arabia
- 3School of Energy and Chemical Engineering, Ulsan National Institute of Science and Technology, Ulsan, South Korea
- 4Department of Mechanical Engineering, FET, International Islamic University, Islamabad, Islamabad, Pakistan
- 5Center of Excellence in Environmental Studies, King Abdulaziz University, Jeddah, Saudi Arabia
- 6Sustainable Development Study Center, Government College University Lahore, Lahore, Pakistan
- 7Bioenergy & Environmental Sustainable Technology (BEST) Research Group, Department of Chemical Engineering, COMSATS University Islamabad (CUI), Lahore, Pakistan
The organic Rankine cycle (ORC) has recently emerged as a practical approach for generating electricity from low-to-high-temperature waste industrial streams. Several ORC-based waste heat utilization plants are already operational; however, improving plant cost-effectiveness and competitiveness is challenging. The use of thermally efficient and cost-competitive working fluids (WFs) improves the overall efficiency and economics of ORC systems. This study evaluates ORC systems, facilitated by biogas combustion flue gases, using n-butanol, i-butanol, and methylcyclohexane, as WFs technically and economically, from a process system engineering perspective. Furthermore, the performance of the aforementioned WFs is compared with that of toluene, a well-known WF, and it is concluded that i-butanol and n-butanol are the most competitive alternatives in terms of work output, exergy efficiency, thermal efficiency, total annual cost, and annual profit. Moreover, the i-butanol and n-butanol-based ORC systems yielded 24.4 and 23.4% more power, respectively, than the toluene-based ORC system; in addition, they exhibited competitive thermal (18.4 and 18.3%, respectively) and exergy efficiencies (38 and 37.7%, respectively). Moreover, economically, i-butanol and n-butanol showed the potential of generating 48.7 and 46% more profit than that of toluene. Therefore, this study concludes that i-butanol and n-butanol are promising WFs for high-temperature ORC systems, and their technical and economic performance compares with that of toluene. The findings of this study will lead to energy efficient ORC systems for generating power.
Introduction
The global energy demand has been increasing because of economic and population growth and lifestyle improvements in the developing world. Fossil fuels have been used as a primary energy source to fulfill current energy demands and account for around 85.5% of the global energy production (Ediger, 2019). However, fossil fuel consumption leads to environmental pollution, including waste heat and greenhouse gas (GHG) emissions, resulting in climate change (Ediger, 2019). To reduce GHG emissions and meet the globally increasing energy demand, effective utilization of waste heat through power generation is critical. The organic Rankine cycle (ORC) is the most promising technology for utilizing waste heat for power generation, leading to decreasing fossil fuel consumption and GHG emissions. For example, recovering waste heat from a midsize cement industry plant can decrease the annual CO2 emissions by 10 kt (Mahmoudi et al., 2018).
The ORCs have been studied extensively in the past decades. Several studies have evaluated working fluids (WFs) and ORC system configurations from a thermo-economic perspective (Imran et al., 2018; Blondel et al., 2019; Anastasovski et al., 2020). Mudasar et al. (2017) studied a biogas-fueled high-temperature ORC (HT-ORC) system using toluene as the WF and reported that the maximum power generated and thermal efficiency were 156 kW and 19%, respectively. Shu et al. (2016) studied several ORC systems, including a toluene-based HT-ORC system, and demonstrated that this system generated less power (152.3 kW) than steam and double ORC systems (153.8 and 158.6 kW, respectively). Mahmoudi et al. (2018) summarized the effects of WFs on waste heat recovery and exergy efficiency in different ORC configurations and concluded that toluene was one of the most studied WFs for internal combustion engines. Moreover, they presented that the electricity production cost, depreciated payback period, and savings-to-investment ratio of toluene-fueled ORC systems were the lowest (0.27 $/kWh), shortest (7.8 years), and highest (1.6), respectively, compared with those of ORC systems using other WFs (Mahmoudi et al., 2018). Moreover, (Maraver et al., 2014) have investigated conventional WFs, including toluene, and evaluated results after optimization. The results show that the thermal efficiency of toluene based ORC systems ranges from 5.2 to 21% (Maraver et al., 2014). In another study by Song and Gu (2015), toluene is studied as WF where it shows a thermal efficiency of 21%. A latest study has been conducted on the thermodynamics performance analysis of an ORC. A total of 64 combinations of WFs have been examined for the dual cycle. Propane and R245fa were selected for the ORC (Khatoon et al., 2021). A multi-objective optimization work has been performed for an ORC and heat pump system for waste heat recovery in waste-to-energy combined heat and power plant. Various WFs have been investigated, however, butane and ammonia are the most suitable working fluids (Pan et al., 2020). In a study by Touaibi et al. (2020a, b), the authors have evaluated three WFs including toluene, R245fa and R123 on parametric basis. Their results show that toluene has highest efficiency (14.38%) among all WFs.
To date, only a few researchers have evaluated ORC systems and WFs from a process systems engineering (PSE) perspective. Bruno et al. (2008) have simulated an ORC system using the Aspen Plus software and have calculated its thermal efficiency for different WFs; however, they have not performed a detailed thermodynamic evaluation based on parametric and composite curve analyses. Furthermore, (Lee et al., 2017) have studied an ORC system using liquefied natural gas cold energy utilizing the Aspen Plus software and have optimized the proposed process using a genetic algorithm. Their optimized results revealed that the thermal efficiency of the analyzed ORC system was 26%. Moreover, they have analyzed the proposed process using composite curve analysis but have not evaluated the WFs using a parametric study. Barse and Mann (2016) evaluated the performance of 12 conventional WFs used in ORC systems using the Aspen HYSYS software from technical (thermodynamic and exergy analysis) and economic (cost analysis) viewpoints. However, they have not focused on the selection and detailed parametric evaluation of WFs. Similarly, (Rowshanaie et al., 2015) performed a simulation of conventional WFs-based ORC systems in Aspen HYSYS. They have evaluated WFs (R245fa, NOVEC7000, R141b) based on thermal efficiency and UA in which R245fa shows better performance. However, detailed PSE perspective based analysis is not considered in their study (Rowshanaie et al., 2015). Another study by Yu et al. (2013) has evaluated ORC systems in Aspen Plus. In their ORC system, R245fa was evaluated as a WF in a diesel engine combusted flue gases under varying evaporation pressure. The results show that the engine’s thermal efficiency can be improved by 6.1% after combining ORC with it (Yu et al., 2013).
A detailed analysis of ORC systems from a PSE perspective is critical to evaluate overall process performance. Moreover, the thermodynamic and parametric study of WFs is critical, particularly for unconventional WFs. Therefore, this study presents a detailed PSE consideration to evaluate the ORC systems under varying WFs at constant heating and cooling mediums. The proposed ORC systems are facilitated by biogas combustion flue gases. The major contribution of this study can be summarized as follows:
• Three unconventional WFs, namely i-butanol, n-butanol, and methylcyclohexane (MCH), are investigated compared to a well-known conventional WF, i.e., toluene.
• Detailed parametric and thermodynamic analysis for selecting and evaluating the prospective WFs for high temperature ORC systems are performed from a PSE viewpoint.
• The composite curves with detailed exergy analysis are analyzed for ORC systems with chosen prospective WFs.
• The economic benefits of selected unconventional WFs are also determined in comparison with toluene.
Materials and Methods
Prospective Working Fluids
Toluene is one of the most promising WFs for HT-ORC applications (Shu et al., 2016; Mudasar et al., 2017) mainly because of its desirable thermo-physical parameters. Several researchers have studied the behavior of toluene using its thermo-physical properties (Mahmoudi et al., 2018). For instance, (Yagli et al., 2016) analyzed that the thermal efficiency of toluene (17.08%) was higher than that of cyclohexane (16.62%). The selection of optimal WFs is challenging because of the low thermal and exergy efficiency, low power output, and lack of commercial availability of WFs. Considering these constraints, the prospective WFs in this study, namely MCH, n-butanol, and i-butanol, were studied from technical and economic perspectives. These WFs were evaluated because their thermo-physical properties are competitive to those of toluene and their thermodynamic efficiency is far better then toluene which make them viable to be used commercially.
The most important thermo-physical properties of the proposed WFs and toluene, which is a widely used WF, are presented in Table 1. The critical temperatures of n-butanol, i-butanol, and MCH are comparable to that of toluene. Moreover, critical temperatures of prospective WFs are similar to source temperatures and thus are likely responsible for the high cycle efficiency of these WFs. Furthermore, the critical pressures of n-butanol and i-butanol are higher than that of toluene, whereas the critical pressure of MCH is lower. In addition, the molecular weight of MCH is higher than that of toluene, and the molecular weights of n-butanol and i-butanol are lower. Lastly, the boiling point of n-butanol is higher than that of toluene, whereas those of i-butanol and MCH are lower. Because the properties of the prospective WFs are comparable to those of toluene, comprehensive thermodynamic and economic analyses should be performed to analyze the tradeoff between these WFs carefully.
To achieve cost-effective ORC operation, dry and isentropic WFs are recommended (Mudasar et al., 2017), mainly because wet WFs must be superheated before entering turbines. When wet fluids enter a turbine as saturated vapor, they can corrode the turbine blades. Furthermore, additional equipment is required for superheating, which increases operation costs. However, superheating is not required when dry and isentropic fluids are used. The slope of the saturated vapor curve of the temperature–entropy (T–s) diagram (dT/ds) is used to determine whether fluids are wet, dry, or isentropic. Because dT/ds = ∞ for isentropic fluids, the inverse slope (ds/dT) was used in this study; ds/dT is positive, negative, and equal to zero for dry, wet, and isentropic fluids, respectively. Like toluene, the prospective WFs were dry fluids, as illustrated in Table 1.
Evaluation of Working Fluids
The prospective WFs were evaluated based on the energy recovery efficiency from the waste heat source, which depended on the optimum selection of WFs and the heat exchange mode between the WF and the heat source. The optimal WF was selected by evaluating its technical parameters, as mentioned in section “Materials and Methods.” The thermal and exergy efficiencies of the prospective WFs were calculated based on their thermo-physical properties and power output. The economic evaluation was subsequently conducted to determine the most optimal alternative WF for toluene. Furthermore, heat exchange between the waste gases and the WF can occur directly or through a thermal oil, which serves as an intermediate heat-transfer fluid. The heat-transfer fluid presents high thermal capacity, high-temperature stability, low melting temperature, low viscosity, low corrosion, high safety profile, and low environmental impact (Macchi, 2016). Therminol VP-1, which consists of 26.5% biphenyl and 73.5% diphenyl ether (molar percentages), presents most of the aforementioned properties and was selected as the heat-transfer fluid in this study. Moreover, the auto-ignition temperature of Therminol VP-1 is considerably higher than that of other thermal oils. The properties of Therminol VP-1 have been described in detail (Eastman, 2020). Moreover, (Abdel-Hadi, 2009) reported that Therminol VP-1 was suitable for biogas-fueled ORC power generation systems when the biogas’ methane content exceeded 54.5%.
Cycle Details
The proposed ORC system consisted of four major components: a feed pump, an evaporator or a boiler, a turbine or an expander, and a condenser (Sun et al., 2017). The WF passed through the pump, where it was pressurized and was subsequently transferred to the evaporator/boiler. The evaporator/boiler increased the WF’s temperature to form saturated or superheated vapor by exchanging heat with Therminol VP-1, which is a heat transfer fluid. The heat source was selected to be flue gases generated through biogas combustion. The heat source may vary depending upon heat utilization requirements. After heat exchange, the high-pressure WF vapor were expanded in the turbine to generate desired mechanical energy. The turbine is a key component that determines the efficiency of ORC systems. The superheated WF from the turbine was converted into a saturated liquid after cooling in the condenser. Water is used as a cooling medium in the condenser. Thereafter, the condensed WF was compressed by the pump to restart the cycle in a closed loop. To convert waste heat into electricity, the mechanical power produced by the turbine/expander was converted into electrical energy using a generator. The ORC system’s main components and the heat sources and sinks connected with the evaporator/boiler and condenser are illustrated in Figure 1.
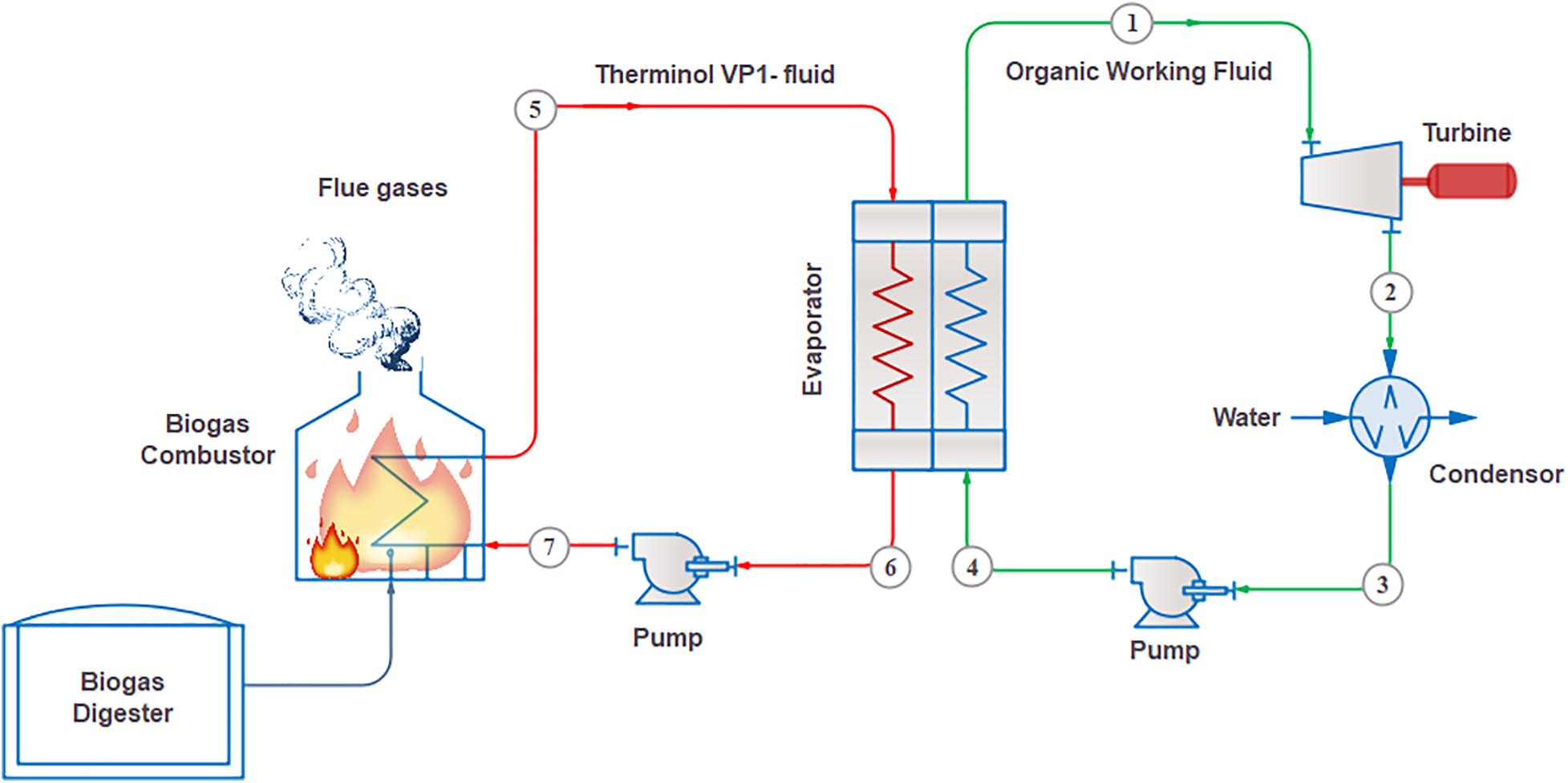
Figure 1. Schematic diagram of biogas-fueled organic Rankine cycle (ORC) system for power generation.
Cycle Design and Simulation
In this study, the ORC system was designed and simulated using the Aspen HYSYS® V10 commercial simulator using toluene as the conventional WF (Mudasar et al., 2017) and MCH, n-butanol, and i-butanol as the proposed WFs. The proposed process design conditions are summarized in Table 2. The design parameters were maintained constant for all four cycle designs, and the generated power and efficiencies were compared. The pump and turbine with isentropic efficiencies of 65 and 85%, respectively, were used as reported in the literature (Saleh et al., 2007). The following assumptions were made during the simulation:
1. The WF was a saturated liquid when it entered the pump.
2. The isentropic efficiencies of the pump and turbine were known.
3. The components were treated under adiabatic conditions.
4. The pressure drops in the evaporator, condenser, pipes, and tubes were negligible.
5. All equipment were operated in steady state.
6. The toluene, MCH, i-butanol, and n-butanol were pumped to 34, 32, 40, and 40 bar, respectively. These pressures were less than their critical pressures.
Results and Discussion
Parametric Analysis
Typically, the optimum WF is selected based on thermo-physical parameters, such as critical temperature and pressure, latent heat of vaporization (LHv), fluid density, degree of superheating, heat capacity, and viscosity. These properties and the thermal efficiencies of the WFs analyzed in this study are listed in Table 3. Table 3 illustrates that critical pressure of the WFs is directly related to their thermal efficiency. For example, MCH presents the lowest thermal efficiency (15.8%), highest back-work ratio, and lowest turbine power output (185 kW) among all analyzed WFs because operating and critical pressures are lower than those of the other WFs. Conversely, n-butanol and i-butanol, which presented high operating and critical pressures (18.3 and 18.4%, respectively), exhibited high thermal efficiencies. Similarly, LHv and density are the other major thermodynamic parameters used to analyze the thermodynamic efficiency of ORC systems. WFs with high LHv and high density are preferred because fluids with high LHv absorb more heat and reduce moisture during expansion. Conversely, WFs with high mass density require low flow rates to absorb more heat, increasing equipment capacity. The LHv of n-butanol and i-butanol (558.5 and 541.8 kJ/kg, respectively) are higher than that of toluene (367 kJ/kg); therefore, n-butanol and i-butanol absorbed more heat than toluene in the evaporator, which in turn decreased the exit temperature of the thermal oil. In contrast, WFs with high LHv increase the cooling load on the condenser, and a large condenser duty is required to remove the LHv. Therefore, n-butanol and i-butanol presented high condenser duties (1070 and 1074 kW, respectively).

Table 3. Comparison of thermodynamic parameters of toluene, methylcyclohexane, n-butanol, and i-butanol.
A high degree of superheating causes a large condenser duty. Therefore, a low degree of superheating at the exhaust of the evaporator for dry fluids is preferred. The superheating degrees of n-butanol and i-butanol were lower than that of MCH, but their condenser duties were higher. This was ascribed to the lower density of MCH than those of n-butanol and i-butanol. Typically, WFs with high density causes high heat absorption, which results in high cooling loads. Heat capacity is another criterion used for WF selection. Heat capacity is defined as the energy required by a given mass of material to increase its temperature by 1°C. WFs with low liquid heat capacity and high latent heat are preferred so that maximum heat is absorbed during phase change without requiring a high degree of preheating. Among the WFs in this study, MCH presented the lowest heat capacity in the liquid phase. In contrast, the liquid heat capacities of n-butanol and i-butanol were comparable (2.78 and 2.74 kJ/kg°C, respectively). However, the heat capacities of the WFs in vapor phase were higher than those in the liquid phase. This was attributed to the superheated fluid leaving the evaporator, and therefore, requiring more heat to increase temperature. Viscosity also plays a vital role in reducing power consumption and increasing heat transfer. More viscous fluids require more power to pump, making the process less efficient. Furthermore, viscosity and heat transfer are inversely related. A WF with low viscosity and high density requires a high heat-transfer capacity.
Thermodynamic Analysis
Thermodynamic analysis of the ORC systems was conducted using T–s diagram and CCs, and the details are presented in the subsequent subsections.
T–s Diagram Analysis
The T–s diagrams of the thermodynamic processes in a simple ORC system using toluene, MCH, i-butanol, and n-butanol as the WFs are illustrated in Figure 2.
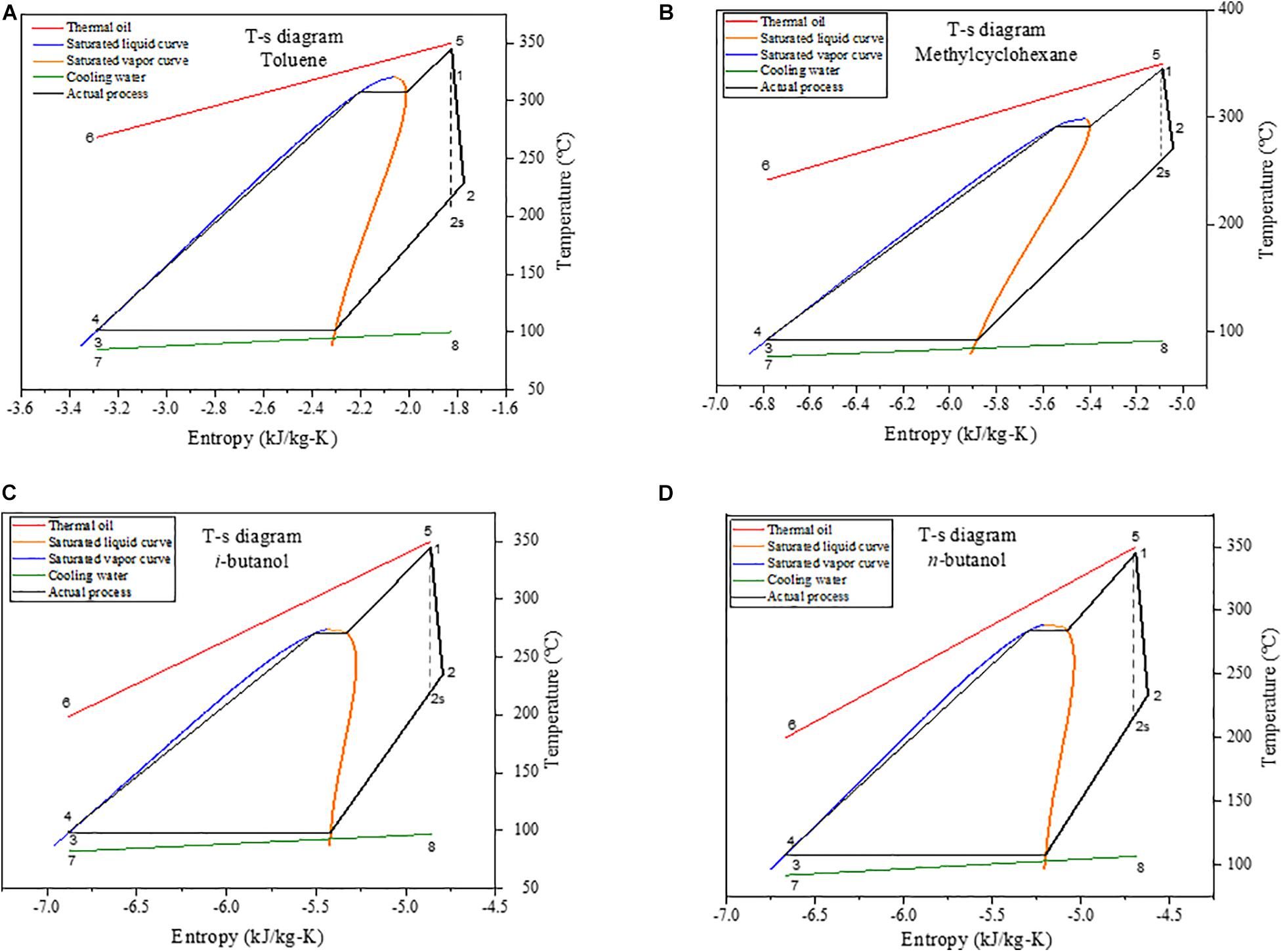
Figure 2. Temperature–entropy diagrams of organic Rankine cycle (ORC) systems using (A) toluene, (B) methylcyclohexane, (C) i-butanol, and (D) n-butanol as the working fluid.
As depicted in the T–s diagrams (Figure 2), the heat source at high temperature (state 5) exchanged heat with the WF in the evaporator, and the heat source was cooled to state 6. Moreover, the low-temperature WF in state 4 was heated to the highest cycle temperature in state 1. The heat transferred to the WF included sensible heat, which increased the temperature of the WF until the fluid reached saturated liquid state, latent heat transferred to the WF at constant temperature and pressure until it reached saturated vapor state, and superheated to increase temperature to the required turbine inlet temperature at state 1. Subsequently, the WF expanded from state 1 to state 2 in the turbine to generate work output. State 2s in Figure 2 illustrates an isentropic or ideal process, with no irreversibility; hence, the entropy did not change, and the entropy at state 1 was equal to the entropy at state 2s. However, real processes are not isentropic; hence, entropy increased from state 1 to state 2. Thereafter, the WF condensed in the condenser from state 2 to state 3, which occurred in two steps. In the first step, the fluid was cooled to a saturated vapor state, whereas during the second step, heat was released at a constant temperature until the WF reached saturated liquid state. Lastly, the fluid entered the pump in saturated liquid state, its pressure was increased to the required evaporator inlet pressure, and the cycle continued.
Composite Curve Analysis
Composite curves (CC) provide a holistic overview of heat recovery in a heat exchanger. These curves demonstrate the relation of hot fluid (i.e., Therminol VP-1) and cold fluid (i.e., WF) with respect to approach temperature and heat flow along the length of heat exchanger. Hot and cold fluid is depicted in terms of hot and cold CCs, respectively. Figure 3 illustrates approach temperature and temperature relation in terms of temperature difference composite curves (TDCCs). Figure 4 visualizes temperature–heat flow composite curves (THCCs) for the ORC system. An ORC system’s performance can be predicted from the peak of cold and hot CCs in the TDCC profiles over a certain temperature range, as illustrated in Figure 3. Accordingly, it is noted that the peak of hot and cold CCs is mainly located at the cold end (below 320°C) of heat exchanger in all ORC systems. This peak of CCs is observed with respect to approach temperature, also referred to as the minimum internal temperature approach (MITA). In Figure 3, the MITA value reaches at 147, 90 and 98.5°C in MCH, n-butanol, and i-butanol cases, whereas in the case of toluene, it reaches at 165°C. This MITA value should follow the specified value i.e., 5°C throughout the length of the exchanger. A large variation in obtained and specified value is mainly because of the large difference between stream temperatures. This difference can be reduced either by enhancing heat recovery or by the optimal selection of WFs based on their thermo-physical properties. For instance, toluene shows MITA value of 165°C, which is the highest in all cases. The lowest value i.e., 90°C, is observed in the case of n-butanol. In n-butanol case, the outlet temperature of Therminol VP-1 is 199.9°C, where the inlet temperature of WF is 109.9°C. This large difference depicts that more heat can be recovered. Amongst proposed WFs, MCH shows the highest peak indicating the least efficient process.
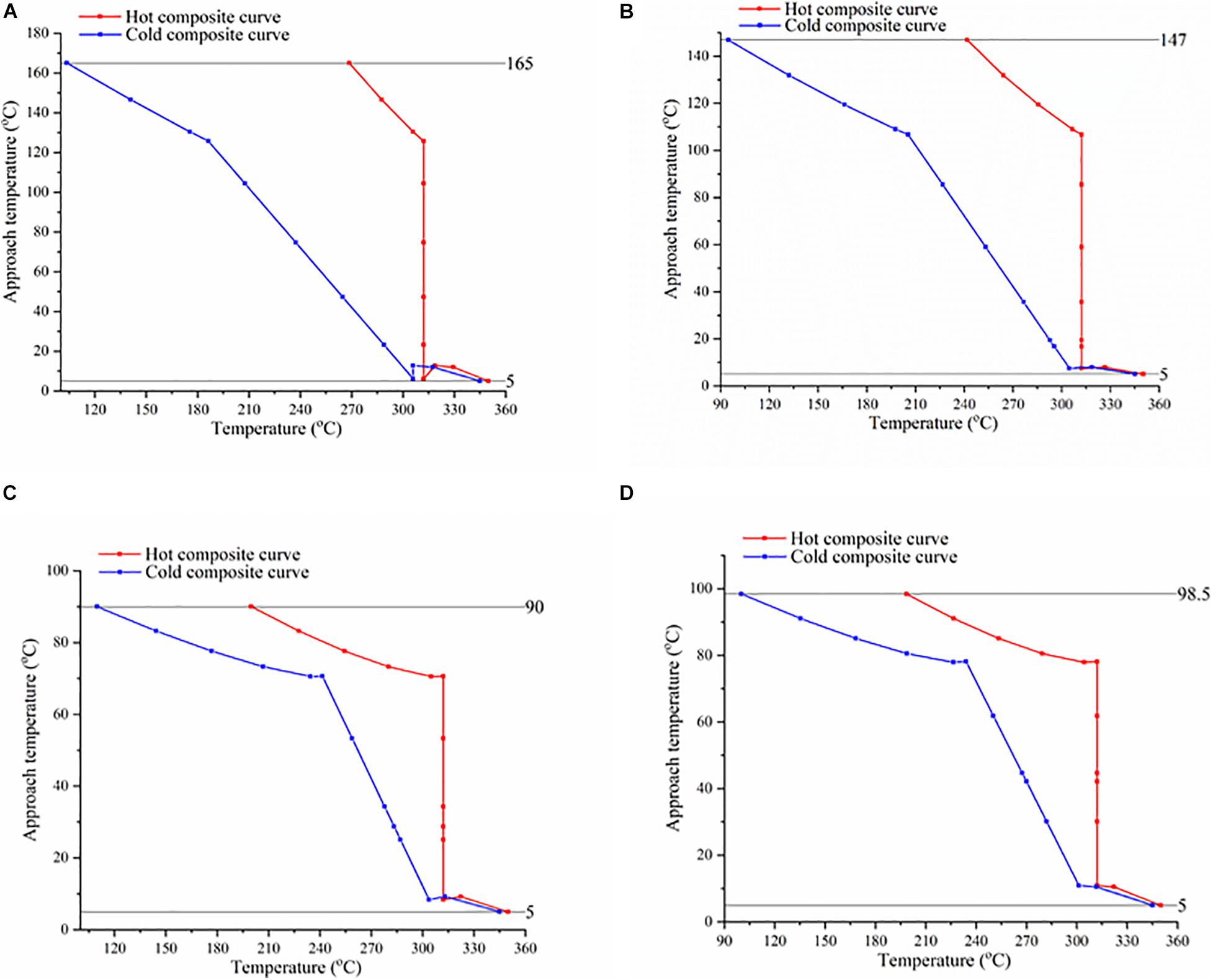
Figure 3. Temperature difference composite curves of organic Rankin cycle (ORC) systems using (A) toluene, (B) methylcyclohexane, (C) n-butanol, and (D) i-butanol as the working fluid.
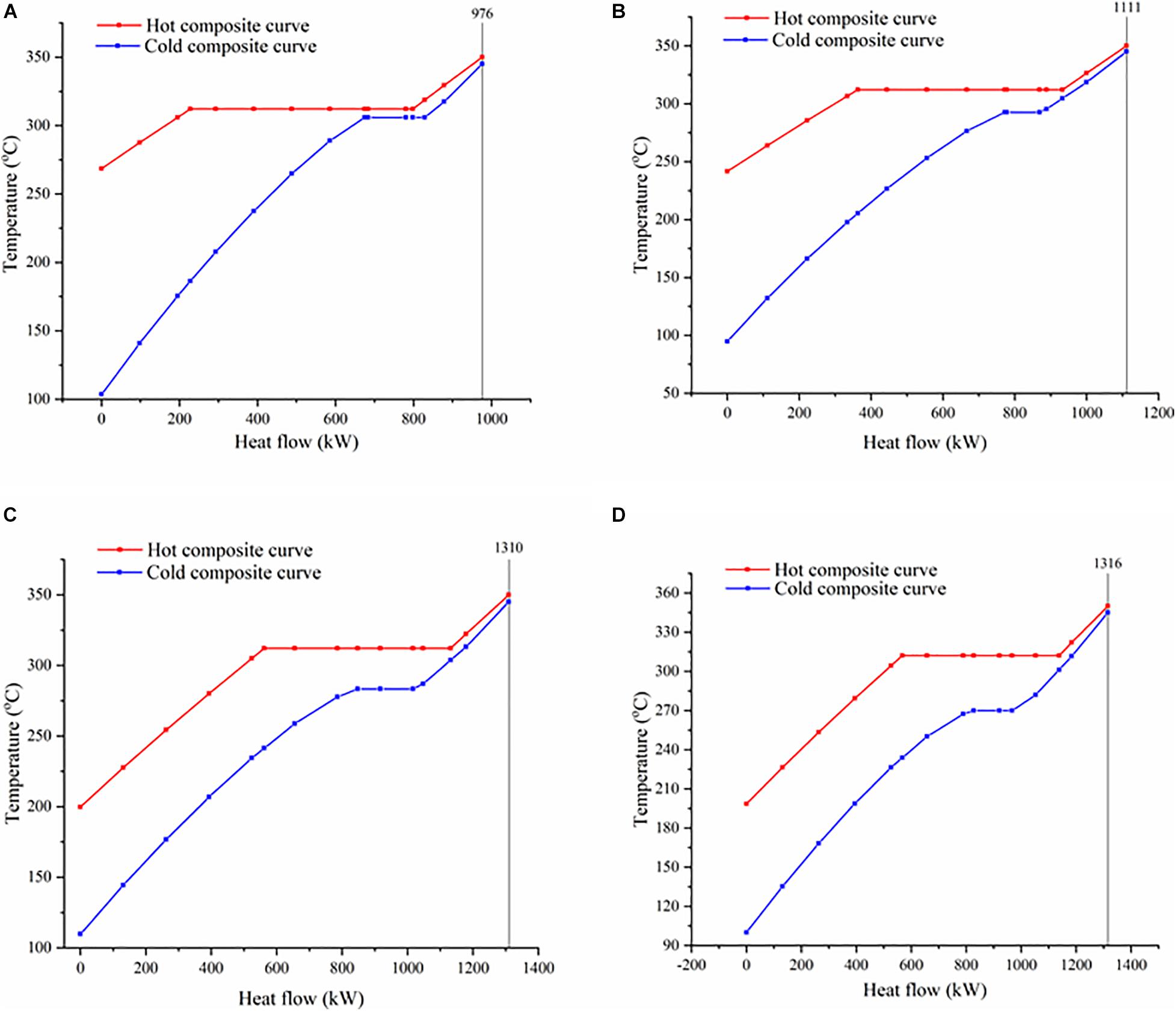
Figure 4. Temperature–heat flow composite curves of organic Rankine systems using (A) toluene, (B) methylcyclohexane, (C) n-butanol, (D) i-butanol as working fluids.
Figure 4 demonstrates THCCs of toluene and proposed WFs. THCCs propose a visualized trend of heat flow inside a heat exchanger. A wide gap between hot and cold CCs depicts low heat recovery, whereas the narrow gap shows more heat recovery and high thermodynamic efficiency. The gap between these curves also depicts MITA value. This gap is prominent at the cold end, which should be low, meeting the criteria of MITA 5°C. In Figure 4, toluene shows the largest gap, whereas n-butanol shows the lowest gap. A large gap tends to increase entropy generation, which consequently increases exergy destruction and decreases process efficiency. This gap can be reduced by optimal WF selection. In that case, n-butanol is most efficient than toluene and proposed WFs mainly because of the lowest temperature gap. Moreover, it is noted that the n-butanol and i-butanol show high heat flow i.e., approx. 1300 kW, whereas toluene shows the lowest heat flow (approx. 980 kW). High heat flow generates more power in the turbine because of large heat capacity. For instance, i-butanol has a large heat capacity (2.94 kJ/kg°C), and due to which it generates more power in the turbine i.e., 253 kW. The T–s diagrams of all studied WFs are summarized and given in Figure 5. Less entropy is generated when the ORC systems were operated at low temperatures. The proposed WFs are operated at lower temperatures than toluene, thus generating less entropy than toluene.
Exergy Analysis
Energy analysis alone is not sufficient to evaluate an energy conversion system’s performance from a heating source to output work. Energy analysis only quantifies the work delivered by the system. However, it does not provide information related to the potential ability of a system to deliver work (Souza et al., 2020). The irreversibility must be accounted for during the evaluation of the system ability (Liu et al., 2020). Therefore, the exergy destruction in different components of the system must be evaluated. Exergy analysis provides information regarding the location and source of irreversibilities (Khaljani et al., 2015).
Exergy is the theoretical maximum useful work that maintains a thermodynamic equilibrium between systems and the environment. Assuming the control volume approach for each component, the exergy balance equation can be expressed as follows:
where, , and are the inlet and outlet exergy streams, respectively, and is the exergy destruction.
The specific exergy equation can be written as follows:
where the subscript “o” denotes the dead state.
Exergy analysis is useful to establish strategies and procedures for more effective use of energy, and it has been applied to different thermal processes, such as power generation, heating, and regeneration (Nami et al., 2018). Exergy can be divided into four components: physical, chemical, kinetic, and potential (Venkatarathnam and Timmerhaus, 2008). In this study, the last three types of exergy were neglected because of no change in composition, speed, and height. The important formulas used to calculate exergy destruction are listed in Table 4. The exergy destruction of the ORC systems using the WFs in this study is illustrated in Figure 6.
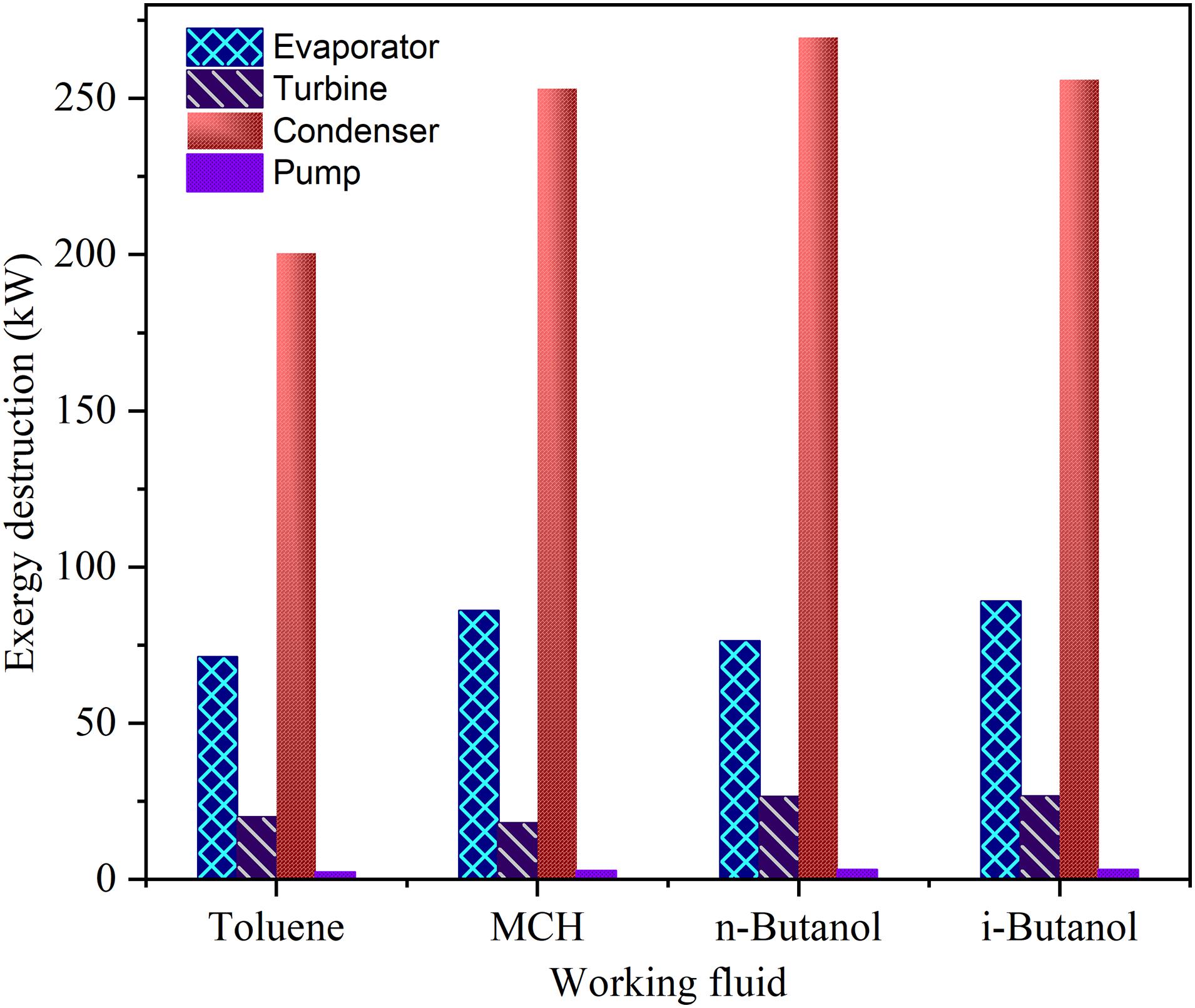
Figure 6. Equipment wise exergy destruction values of toluene, methylcyclohexane, n-butanol, and i-butanol.
The exergy destruction values of the ORC systems using MCH, n-butanol, and i-butanol were higher than that of the ORC system using toluene. Maximum exergy destruction were detected in the condenser for all WFs, where the losses were three times higher than the evaporator. The large temperature difference between the cooling water and the stream exiting the turbine is a source of this high exergy destruction in the condenser. This exergy destruction can be minimized by decreasing this temperature difference or by heat recovery from the turbine exit stream to minimize condenser heat load.
Economic Analysis
Economic analysis is a useful approach to verify proposed designs’ viability (Zhang et al., 2019). In this study, cost estimation for each design using the proposed WFs was performed by analyzing the power and revenue generation of each ORC system. A constant flow rate for each proposed WF was maintained for a fair comparison among the configurational analyses. The cost relations were retrieved from Nelson et al. (1989) and Turton et al. (2008), in which the total capital investment (TCI) and operating cost were the main contributors to the total annual cost (TAC). For a fair comparison, a payback period of 3 years was considered when analyzing the TAC. The TCI of the proposed design was calculated for the evaporator, condenser, turbine, and pump, and the operating cost was accounted only for pumping and condensing the WF. A water condenser was used to condense the fluid used for recycling to ensure the process’s continuity. The electricity cost was adjusted to 0.2 $/kWh based on recent literature-retrieved trends (Turton et al., 2008). All cost relations are presented in the following equations:
where A is a size parameter that corresponds to the power generated in different equipment parts, such as the turbine and heat exchanger, and K is a constant used to calculate the base module cost. The value of this constant is different for each design, as presented in Table 5.
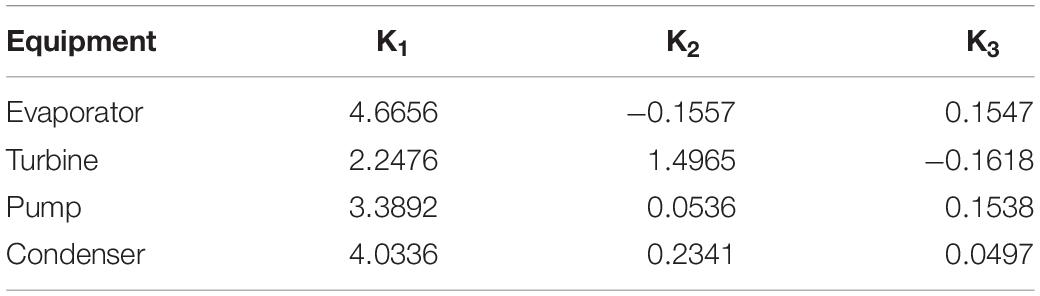
Table 5. Values of constant K used to calculate the base module cost (Turton et al., 2008).
Table 6 summarizes the economic evaluation of the ORC system using the proposed WFs. It is interesting to note that the power generation of ORC systems are directly related to fluid costs. Both i-butanol and n-butanol are expensive than toluene and generate more power than toluene. Similarly, MCH was the least expensive of the prospective WFs and generated the lowest power of all ORC systems. The ORC system using i-butanol generated the highest power (253.3 kW) followed by the ORC system using n-butanol (250.5 kW). The power generated by the ORC systems using n-butanol and i-butanol as WFs was 4.67 and 5.7% higher, respectively, than that of the ORC system using toluene. The economic analysis data in Table 6 reveals that the capital costs of the ORC systems using the prospective WFs were slightly higher than that of the toluene-based ORC system. Similarly, the operating costs of the butanol-based ORC systems were higher than that of the toluene-based ORC system, owing to the high condenser duty and pump power associated with the butanol-based WFs. Hence, the overall TACs of the ORC systems using i-butanol and n-butanol were 6.4 and 7.94% higher, respectively, than that of the ORC system using toluene. Nevertheless, the overall efficiency in terms of cash flow and revenue generation of the ORC systems using the prospective WFs was higher than that of the ORC system using toluene. The data in Table 6 demonstrate that the butanol-based ORC systems were remarkably profitable because the maximum revenues were obtained when i-butanol ($206 634) and n-butanol ($196 470.6) were used as the WFs, which were 48.7 and 46% higher, respectively, than those of the toluene-based ORC system. Hence, it was concluded that conventional WFs could be successfully replaced with i-butanol because of their high capacity, low cost, and high power generation capacity.
Working Fluids Selection: Tradeoff Analysis
The tradeoff of the ORC systems using the prospective WFs was analyzed, and the results were compared with those of the toluene-based ORC system. Both n-butanol and i-butanol were more competitive than MCH in terms of power generation. The power output of the n-butanol– and i-butanol-based ORC systems were 30 and 32% higher, respectively, than that of the toluene-based ORC system. Conversely, the power generated by the MCH-based ORC system was 3.5% lower than that generated by the toluene-based ORC system. However, the thermal efficiencies of MCH, n-butanol, and i-butanol were 16, 2.6, and 2.1% lower, respectively, than that of toluene. Among the prospective WFs, i-butanol presented the highest thermal efficiency (18.4%), as seen in Figure 7. The exergy efficiency of the ORC systems provided a better understanding of thermodynamic inefficiency between heat transfer and work. The exergy efficiencies of n-butanol (37.6%) and i-butanol (38%) were higher than that of toluene (37.2%), whereas that of MCH (32%) was lower. Moreover, the economic analysis data indicated that the operating costs of the ORC systems using MCH, n-butanol, and i-butanol were much higher than those of the toluene-based ORC system because the prospective WFs were more expensive than toluene; however, i-butanol was more economical, and the ORC system using i-butanol generated an annual profit of 48.7%. Therefore, a tradeoff existed between the prospective WFs, and i-butanol over performed the other prospective WFs.
Impact of WFs Flowrate on Orc Performance
The ORC performance has been further evaluated by considering WFs flowrate as a design variable considering the MITA constraint as suggested by one of the reviewers. This is done by increasing the WF flowrate, keeping MITA at 5°C, till no further flowrate can be increased. Initially, the WFs flowrate has been kept fixed and process performance is evaluated for a fair comparison among proposed WFs. This assessment was named as Case-I whereas, upon reviewer’s suggestion, the process performance is evaluated at maximum WFs flowrate to draw maximum potential. This was named as Case-II. The comparison of both cases is presented in Table 7.
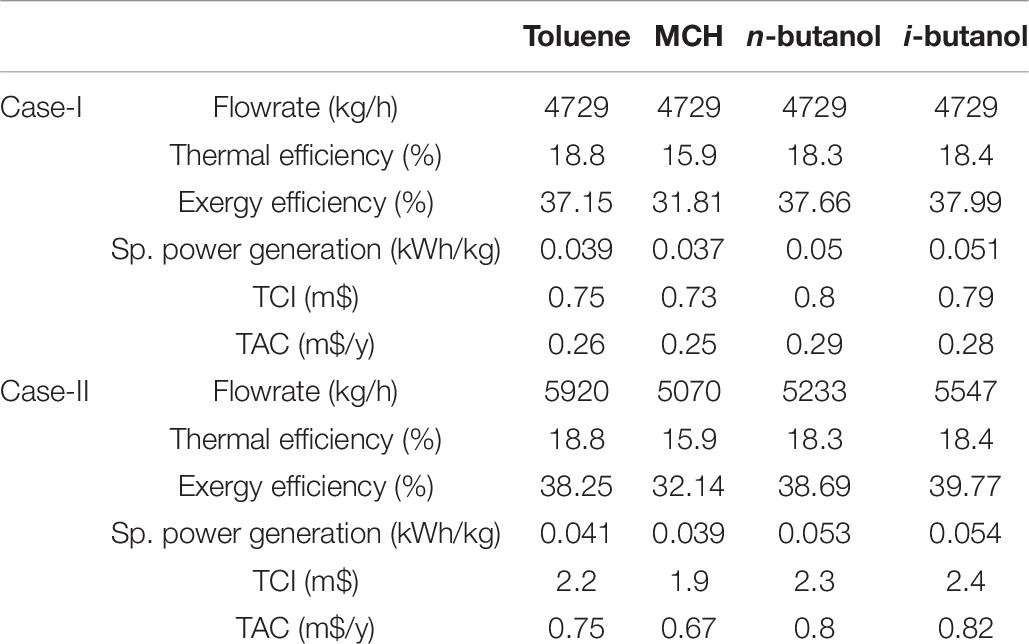
Table 7. Organic Rankine cycle (ORC) performance comparison with same flowrate (case-I) and with different flowrate (case-II) of working fluids.
It can be seen from Table 7 that toluene consumes maximum flowrate among all WFs i.e., 5920 kg/h, however, it has low power generation and low exergy efficiency. On the contrary, i-butanol has highest specific power generation (0.054 kWh/kg) at approx. 24% higher than that of toluene. Similarly, the exergy efficiency (39.77%) of i-butanol is highest amongst all WFs. MCH shows better economic performance with lowest TCI and TAC mainly due to lowest fluid cost. It is interesting to note that despite changing WFs flowrate, the thermal efficiency remains same in both cases. In authors’ understanding, this is because when the flowrate is increased, the heat transfer between hot and cold fluid increased alongside with increased work output. The overall ratio of work output and heat flow remains same in both cases. Therefore, the thermal efficiency remains same in both cases.
Conclusion
In this study, three dry unconventional WFs (n-butanol, i-butanol, and MCH) were analyzed from a PSE perspective. The thermodynamic properties of the prospective WFs were comparable with those of toluene, which is the most widely used WF. Among the proposed WFs, i-butanol is a potential replacement for toluene owing to its high heat capacity (2.9 kJ/kg), high power generation (253 kW), and high exergy efficiency (38%). Conversely, the MCH-based ORC system generated the lowest power (176 kW). In addition to the slightly higher TAC, the annual profit generated by the ORC system using i-butanol was 48.7% higher than that of the toluene-based ORC system. Therefore, i-butanol can successfully replace toluene as a WF. Moreover, ORC systems can be further improved by using sensible heat, which can effectively reduce condenser duty. Furthermore, recuperation technology can be implemented to use sensible heat and also enhance power generation.
Data Availability Statement
The original contributions presented in the study are included in the article/supplementary material, further inquiries can be directed to the corresponding author/s.
Author Contributions
All authors listed have made a substantial, direct and intellectual contribution to the work, and approved it for publication.
Funding
This research was supported by the Priority Research Centers Program through the National Research Foundation (NRF) of Korea funded by the Ministry of Education (2014R1A6A1031189).
Conflict of Interest
The authors declare that the research was conducted in the absence of any commercial or financial relationships that could be construed as a potential conflict of interest.
Abbreviations
CC, composite curve; GHG, greenhouse gas; HT-ORC, high-temperature organic Rankine cycle; LHv, latent heat of vaporization; MCH, methylcyclohexane; MITA, minimum internal temperature approach; ORC, organic Rankine cycle; PSE, process system engineering; TDCC, temperature difference composite curves; THCC, temperature–heat flow composite curves; T–s, temperature entropy; TAC, total annual cost; TCI, total capital investment; WF, working fluid.
References
Abdel-Hadi, M. A. (2009). Determination of methane content by measurements of flame temperature and voltage from biogas burner. Misr J. Agric. Eng. 26, 498–513.
Anastasovski, A., Rasković, P., and Guzović, Z. (2020). A review of heat integration approaches for organic rankine cycle with waste heat in production processes. Energy Convers. Manag. 221:113175. doi: 10.1016/j.enconman.2020.113175
Barse, K. A., and Mann, M. D. (2016). Maximizing ORC performance with optimal match of working fluid with system design. Appl. Therm. Eng. 100, 11–19. doi: 10.1016/j.applthermaleng.2016.01.167
Blondel, Q., Tauveron, N., Caney, N., and Voeltzel, N. (2019). Experimental study and optimization of the organic rankine cycle with pure NovecTM649 and zeotropic mixture NovecTM649/HFE7000 as working fluid. Appl. Sci. 9:1865. doi: 10.3390/app9091865
Bruno, J. C., López-Villada, J., Letelier, E., Romera, S., and Coronas, A. (2008). Modelling and optimisation of solar organic rankine cycle engines for reverse osmosis desalination. Appl. Therm. Eng. 28, 2212–2226. doi: 10.1016/j.applthermaleng.2007.12.022
Eastman (2020). Therminol VP-1 Heat Transfer Fluid. Technical Bulletin TF9141. Kingsport, TN: Eastman.
Ediger, V. (2019). An integrated review and analysis of multi-energy transition from fossil fuels to renewables. Energy Procedia 156, 2–6. doi: 10.1016/j.egypro.2018.11.073
Imran, M., Haglind, F., Asim, M., and Zeb Alvi, J. (2018). Recent research trends in organic Rankine cycle technology: a bibliometric approach. Renew. Sustain. Energy Rev. 81, 552–562. doi: 10.1016/j.rser.2017.08.028
Khaljani, M., Khoshbakhti Saray, R., and Bahlouli, K. (2015). Comprehensive analysis of energy, exergy and exergo-economic of cogeneration of heat and power in a combined gas turbine and organic Rankine cycle. Energy Convers. Manag. 97, 154–165. doi: 10.1016/j.enconman.2015.02.067
Khatoon, S., Almefreji, N. M. A., and Kim, M.-H. (2021). Thermodynamic study of a combined power and refrigeration system for low-grade heat energy source. Energies 14:410. doi: 10.3390/en14020410
Lee, U., Jeon, J., Han, C., and Lim, Y. (2017). Superstructure based techno-economic optimization of the organic rankine cycle using LNG cryogenic energy. Energy 137, 83–94. doi: 10.1016/j.energy.2017.07.019
Liu, X., Yang, X., Yu, M., Zhang, W., Wang, Y., Cui, P., et al. (2020). Energy, exergy, economic and environmental (4E) analysis of an integrated process combining CO2 capture and storage, an organic Rankine cycle and an absorption refrigeration cycle. Energy Convers. Manag. 210:112738. doi: 10.1016/j.enconman.2020.112738
Mahmoudi, A., Fazli, M., and Morad, M. R. (2018). A recent review of waste heat recovery by Organic Rankine Cycle. Appl. Therm. Eng. 143, 660–675. doi: 10.1016/j.applthermaleng.2018.07.136
Maraver, D., Royo, J., Lemort, V., and Quoilin, S. (2014). Systematic optimization of subcritical and transcritical organic Rankine cycles (ORCs) constrained by technical parameters in multiple applications. Appl. Energy 117, 11–29. doi: 10.1016/j.apenergy.2013.11.076
Mudasar, R., Aziz, F., and Kim, M. H. (2017). Thermodynamic analysis of organic Rankine cycle used for flue gases from biogas combustion. Energy Convers. Manag. 153, 627–640. doi: 10.1016/j.enconman.2017.10.034
Nami, H., Ertesvåg, I. S., Agromayor, R., Riboldi, L., and Nord, L. O. (2018). Gas turbine exhaust gas heat recovery by organic Rankine cycles (ORC) for offshore combined heat and power applications - energy and exergy analysis. Energy 165, 1060–1071. doi: 10.1016/j.energy.2018.10.034
Nelson, D. A., Kirkwood, R. L., and Douglas, J. M. (1989). Conceptual design of chemical processes. Simul. Ser. 20, 180–184.
Pan, M., Lu, F., Zhu, Y., Huang, G., Yin, J., Huang, F., et al. (2020). Thermodynamic, exergoeconomic and multi-objective optimization analysis of new ORC and heat pump system for waste heat recovery in waste-to-energy combined heat and power plant. Energy Convers. Manag. 222:113200. doi: 10.1016/j.enconman.2020.113200
Rowshanaie, O., Mustapha, S., Ahmad, K. A., and Rowshanaie, H. (2015). Simulation of organic rankine cycle through fluegas to large scale electricity generation purpose. J. Teknol. 77, 9–18. doi: 10.11113/jt.v77.6878
Saleh, B., Koglbauer, G., Wendland, M., and Fischer, J. (2007). Working fluids for low-temperature organic Rankine cycles. Energy 32, 1210–1221. doi: 10.1016/j.energy.2006.07.001
Shu, G., Wang, X., and Tian, H. (2016). Theoretical analysis and comparison of rankine cycle and different organic rankine cycles as waste heat recovery system for a large gaseous fuel internal combustion engine. Appl. Therm. Eng. 108, 525–537. doi: 10.1016/j.applthermaleng.2016.07.070
Song, J., and Gu, C. W. (2015). Analysis of ORC (Organic Rankine Cycle) systems with pure hydrocarbons and mixtures of hydrocarbon and retardant for engine waste heat recovery. Appl. Therm. Eng. 89, 693–702. doi: 10.1016/j.applthermaleng.2015.06.055
Souza, R. J., Dos Santos, C. A. C., Ochoa, A. A. V., Marques, A. S., Neto, L. M. J., and Michima, P. S. A. (2020). Proposal and 3E (energy, exergy, and exergoeconomic) assessment of a cogeneration system using an organic Rankine cycle and an absorption refrigeration system in the Northeast Brazil: thermodynamic investigation of a facility case study. Energy Convers. Manag. 217:113002. doi: 10.1016/j.enconman.2020.113002
Sun, W., Yue, X., and Wang, Y. (2017). Exergy efficiency analysis of ORC (Organic Rankine Cycle) and ORC-based combined cycles driven by low-temperature waste heat. Energy Convers. Manag. 135, 63–73. doi: 10.1016/j.enconman.2016.12.042
Touaibi, R., Koten, H., and Boydak, O. (2020a). An energy investigation of an Organic Rankine Cycle utilizing three organic fluids. Hittite J. Sci. Eng. 7, 41–44. doi: 10.17350/hjse19030000170
Touaibi, R., Koten, H., and Boydak, O. (2020b). Parametric study of an organic rankine cycle using different fluids. Emerg. Sci. J. 4, 122–128. doi: 10.28991/esj-2020-01216
Turton, R., Bailie, R. C., Whiting, W. B., and Shaeiwitz, J. A. (2008). Analysis, Synthesis and Design of Chemical Processes. London: Pearson Education.
Venkatarathnam, G., and Timmerhaus, K. D. (2008). Cryogenic Mixed Refrigerant Processes. Berlin: Springer.
Yagli, H., Koc, A., Karakus, C., and Koc, Y. (2016). Comparison of toluene and cyclohexane as a working fluid of an organic Rankine cycle used for reheat furnace waste heat recovery. Int. J. Exergy 19, 420–438. doi: 10.1504/IJEX.2016.075677
Yu, G., Shu, G., Tian, H., Wei, H., and Liu, L. (2013). Simulation and thermodynamic analysis of a bottoming Organic Rankine Cycle (ORC) of diesel engine (DE). Energy 51, 281–290. doi: 10.1016/j.energy.2012.10.054
Keywords: i-butanol, n-butanol, methylcyclohexane, toluene, Aspen HYSYS®, thermo-economic evaluation, high temperature ORC
Citation: Qyyum MA, Naquash A, Ali W, Haider J, Noon AA, Rehan M, Nizami A-S, Yasin M and Lee M (2021) Process Systems Engineering Evaluation of Prospective Working Fluids for Organic Rankine Cycles Facilitated by Biogas Combustion Flue Gases. Front. Energy Res. 9:663261. doi: 10.3389/fenrg.2021.663261
Received: 02 February 2021; Accepted: 16 March 2021;
Published: 12 April 2021.
Edited by:
Su Shiung Lam, University of Malaysia Terengganu, MalaysiaReviewed by:
Hasan Köten, Istanbul Medeniyet University, TurkeyYoungsub Lim, Seoul National University, South Korea
Anindita Roy, Pimpri Chinchwad College of Engineering (PCCOE), India
Copyright © 2021 Qyyum, Naquash, Ali, Haider, Noon, Rehan, Nizami, Yasin and Lee. This is an open-access article distributed under the terms of the Creative Commons Attribution License (CC BY). The use, distribution or reproduction in other forums is permitted, provided the original author(s) and the copyright owner(s) are credited and that the original publication in this journal is cited, in accordance with accepted academic practice. No use, distribution or reproduction is permitted which does not comply with these terms.
*Correspondence: Muhammad Abdul Qyyum, bWFxeXl1bUB5dS5hYy5rcg==; Muhammad Yasin, bXlhc2luQGN1aWxhaG9yZS5lZHUucGs=; Moonyong Lee, bXlubGVlQHl1LmFjLmty