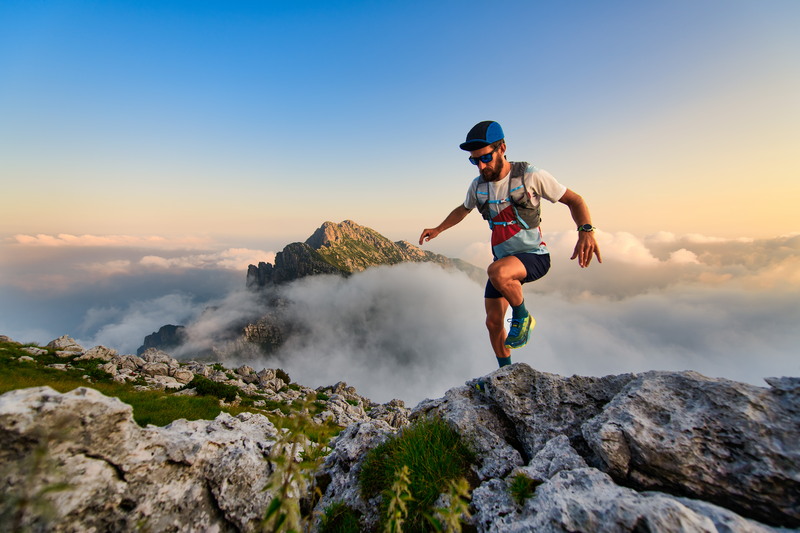
95% of researchers rate our articles as excellent or good
Learn more about the work of our research integrity team to safeguard the quality of each article we publish.
Find out more
ORIGINAL RESEARCH article
Front. Energy Res. , 19 March 2021
Sec. Nuclear Energy
Volume 9 - 2021 | https://doi.org/10.3389/fenrg.2021.651339
This article is part of the Research Topic Advanced Nuclear Fuel Technology View all 11 articles
UO2–Gd2O3 fuel is mostly used as a burnable absorber fuel in the form of a homogenous mixture of Gd2O3 and UO2. More effective reactivity control can be achieved by lumping Gd2O3 within the UO2 because this enhances the spatial self-shielding factor of the burnable absorber fuel. The fabrication of lumped burnable absorber fuel containing lumped Gd2O3 spherical particles or compacts has been experimentally demonstrated using yttrium-stabilized zirconia (YSZ) as a UO2 fuel surrogate. Interfacial cracks or gaps forming under the interfacial stress that develops during the fabrication of the fuel can be eliminated by controlling the initial density of the lumped Gd2O3. In this study, this interfacial stress during the fabrication process was simulated using finite element methods. The effect of the size, shape, and initial density of the lumped Gd2O3 on the distribution and magnitude of the interfacial stress was investigated. The addition of Gd2O3 spherical particles resulted in a lower and more uniform interfacial stress distribution than the addition of cylindrical Gd2O3 compacts. The interfacial stress was increased with increasing Gd2O3 size and initial density. The calculated interfacial stress was compared with experimental results to estimate the threshold stress for crack development in a lumped burnable absorber fuel.
The potential use of Gd as a burnable absorber was recognized many years ago, considering its extremely high thermal neutron absorption cross-section. Gd is usually used in the form of Gd2O3 uniformly mixed with UO2 as a fuel matrix. Owing to the relatively high thermal neutron absorption cross-section, few fuel rods must contain Gd2O3. However, the main limitations of Gd2O3 are the significant end-of-cycle penalty due to the existence of Gd isotopes with higher thermal neutron absorption cross-sections (i.e., 155Gd and 157Gd) (Grossbeck et al., 2001) and the degradation of the fuel’s thermophysical properties (IAEA, 1995; Durazzo et al., 2013; Choe et al., 2016a). One possible way to overcome these limitations is changing the design of the UO2–Gd2O3 mixed fuel.
Several burnable absorber fuel designs have been developed for small modular pressurized water reactors (SMPWRs) in order to eliminate the use of soluble boron and improve the reactor performance in terms of increasing the fuel cycle length while maintainig a flat power distribution. Choe et al. (2016b) have proposed the use of a thin-layer of Zr-167Er (∼ 0.1–0.2 mm) on the inner side of the cladding as a new burnable absorber fuel design. A low burn-up swing of 548 pcm and cycle length of 26.5 months can be obtained for SMPWRs loaded with this burnable absorber fuel design. Another advanced burnable absorber fuel design integrated four azimuthally B4C pads, with a thickness up to 90 μm and span up to 70o, in the guide-thimble ring (Yahya and Kim, 2017a). This burnable absorber fuel design achieved a cycle length of about 53 months and a burnup swing between 634 and 800 pcm. Recently, a new design for burnable absorber fuel, called centrally shielded burnable absorber (CSBA), was developed (Nguyen et al., 2019). The CSBA comprises lumped Gd2O3 in the center of a UO2 fuel pellet. The lumping of Gd2O3 results in a slower burn-out rate and longer suppression of the excess of reactivity due to spatial self-shielding effect (Galperin et al., 1986; Yahya and Kim, 2017b). It was found that the spherically lumped burnable absorber has a higher self-shielding factor than other lumped burnable absorber designs like cylindrical or slab due to the its higher volume-to-surface-area ratio (Fleming, 1982). Nguyen et al. (2019) studied the effect of the size and number of spherically lumped Gd2O3, and found that a more excess reactivity subression and flat power distribution can be obtained by increasing the Gd2O3 sphere radius from 1 mm to 1.3 mm or the number of Gd2O3 sphere (radius = 1 mm) from 1 to 3. They found that a low burn-up swing (∼1100 pcm), long cycle length (∼37 months), and higher burnup (∼30 GWd/tU) can be obtained for a small modular reactor loaded with one Gd2O3 sphere (radius = 1.69 mm) in the center, two Gd2O3 spheres (radius = 1.26 mm) in the intermediate region, three Gd2O3 spheres (radius = 0.7 mm) in the outer region (Nguyen et al., 2019). The fabrication of CSBA using yttria-stabilized zirconia (YSZ) as a surrogate for UO2 and either lumped Gd2O3 pellets, spherical particles, or rods was recently demonstrated (Mistarihi et al., 2018).
One of the major challenges in CSBA fuel design is the formation of interfacial cracks that may form under the stress mismatch developed during the sintering or cooling processes. This may arise from mismatches in the densification and thermal expansion coefficients (TECs), as well as phase transformations, of the sintered materials (Sglavo and Bellettati, 2017). The existence of these interfacial cracks can increase the intensity of fuel cracking during reactor operation and eventually limit fuel performance. In our previous study (Mistarihi et al., 2018), we concluded that interfacial cracks were not formed in YSZ pellets containing lumped Gd2O3 because of the TEC mismatch or the phase transformation of Gd2O3. The TECs of YSZ and Gd2O3 are similar and interfacial cracks were absent from Gd2O3 mini-pellets pre-sintered at temperatures below the phase transformation temperature. Thus, interfacial cracks could be mainly attributed to the sintering stresses resulting from the shrinkage rate mismatch.
Several factors control the sintering stresses that develop during the processing of composites, including shrinkage rate mismatch, volume fraction, and the shape and size of inclusions (Davidge and Green, 1968). The results of our previous study (Mistarihi et al., 2018) showed that, in YSZ oxide pellets containing lumped Gd2O3 mini-pellets, interfacial cracks were formed only when using mini-pellets with high initial densities. However, no interfacial cracks were observed in the case of YSZ oxide pellets containing lumped Gd2O3 spherical particles with high initial densities. The fabricated Gd2O3 spherical particles and mini-pellets had similar relative densities, but they differed in size and shape. Therefore, the effect of the shape, size, and shrinkage rate of the lumped Gd2O3 on the formation of interfacial cracks during the manufacturing of YSZ oxide pellets containing lumped Gd2O3 is investigated in this study.
One method to investigate interfacial crack formation during the processing of composites is to determine the stress distribution. By determining the stress distribution, areas of high stress concentration can be located. These areas are important for the integrity of composites because failure, signified by the formation of interfacial cracks, begins in them (Agarwal, 1972). Several analytical studies based on the theory of elasticity have been performed to determine stress distributions in composites using simplified physical models such as spherical particles (Selsing, 1961) or fibers (Delale, 1988) distributed in infinite matrices. However, the behaviors of powder compacts during sintering are not elastic, and the relationship between the stress and deformation during the sintering process is complex. Nonetheless, the finite-element analysis (FEA) method allows the implementation of complex stress–deformation relationships and the analysis of complex geometries.
Because powder compacts exhibit viscoelastic behaviors, several phenomenological models have been developed to describe their behaviors during sintering. Riedel et al. (1993), using a simple 2D hexagonal grain structure with pores at the triple points, developed an isotropic linear viscous constitutive equation to describe sintering-dominated grain boundary diffusion. Olevsky (1998) developed a phenomenological model based on the continuum theory of sintering by determining the sintering parameters from the rheological behaviors of porous materials during sintering. This model was implemented in an FEA code (COMSOL) and used to study the sintering behavior of different powder compacts (Al2O3 and YSZ) processed by spark plasma sintering (Olevsky et al., 2012) and microwave sintering (Manière et al., 2017). In these studies (Olevsky et al., 2012; Manière et al., 2017), FEA was mostly used to predict the shrinkage rate and temperature distribution of the powders during sintering. Li et al. (2020) used the finite element software (ABAQUS) to study the stress distribution in the cladding of dispersed plate-type fuel as a function of irradiation time and temperatures by implementing nuclear fuel correlation as a subroutine.
In this study, the Olevsky model for sintering was implemented in the COMSOL Multiphysics code and used to understand the stress distribution formed during the manufacturing of YSZ oxide pellets containing lumped Gd2O3. In addition, the applicability of the CSBA to UO2 was investigated, and the stress distribution in UO2 containing lumped Gd2O3 was determined and compared with that of the YSZ-based pellets. The novelty of this study is to estimate the stress distribution and magnitude in the lumped burnable absorber fuel design during the fabrication process.
Thermal, mechanical (linear elastic and sintering), and densification models were coupled by the FEA method (COMOSOL Multiphysics 5.4 code) and used to study the temperature, stress, and density distributions during the manufacturing of YSZ or UO2 oxide pellets containing either lumped Gd2O3 spheres or mini-pellets. The heat-transfer model applied to the entire pellet is expressed by the following equation:
where ρ is the material density (g.cm–3), Cp is the heat capacity (J.kg–1K–1), T is the temperature (K), t is the time (s), and k is the thermal conductivity of the material (W.m–1.K–1).
The Gd2O3 spherical particle or mini-pellet was assumed to exhibit pure elastic behavior, wherein the relationship between the stress and deformation is expressed by Hooke’s law:
where σij is the stress tensor (N.m–2), is the strain tensor (s–1), and C is a fourth-order tensor that is a function of the shear modulus (G) and Young’s modulus (E) of the material.
The YSZ and UO2 powder compact was assumed to exhibit a non-linear viscous behavior expressed by Olevsky (1998) phenomenological model (Eqs 3–6) based on the continuum theory of sintering:
where A(T) is the creep rate factor having the form of an Arrhenius-type equation, Q is the activation energy for deformation, A is a pre-exponential factor, φ is the shear viscosity (Pa.s), Ψ is the bulk viscosity (Pa.s), is the shrinkage rate (s–1), δij is the identity tensor, S is the effective sintering stress (Pa), P is the porosity, α is the surface energy (J.m–2), Q is the activation energy (J.mol–1), R is the gas constant 8.314 (J.mol–1.K–1), and r is the average particle radius (m).
The densification of YSZ and UO2 during the manufacturing process is expressed as the evolution of density during the fabrication process. The density can be related to porosity using the following expression:
where ρeff is the effective density of the material during the sintering process and ρt is the theoretical density of the material. Therefore, the densification of YSZ and UO2 during the fabrication process can be calculated by the evolution of the porosity, which evolves according to the equation of mass conservation:
For Gd2O3, the experimentally measured densities of the 1400 °C, 1500 °C, and 1600 °C pre-sintered Gd2O3 were obtained from our previous study (Mistarihi et al., 2018) and used in the simulation. These densities were approximately 6.29 ± 0.13, 7.10 ± 0.04, and 7.75 ± 0.0.6 g/cm3, corresponding to relative densities (RDs) of 75.5 ± 1.5, 85.2 ± 0.5, and 93.4 ± 0.8%, respectively. The RD equals to the experimentally measured density divided by the theoretical density.
The elastic and shear moduli of Gd2O3 as functions of temperature for samples with an RD of 96.75% were measured by Dole and Hunter (1976). Haglund and Hunter (1973) measured the elastic properties of polycrystalline Gd2O3 with different initial porosities ranging from 2.5% to 36.7% as functions of temperature. The elastic properties were found to decrease linearly with the initial porosity of the sintered samples. The initial porosity of the sintered samples was varied by changing the sintering temperature (Haglund and Hunter, 1973). The reported values of E and G of Gd2O3 as functions of T and RD were fitted to first-degree polynomials; the determined parameters of the fitting function are shown in Eqs 9 and 10.
Using the experimentally measured RDs of the 1400 °C, 1500 °C, and 1600 °C pre-sintered Gd2O3, E and G as functions of T were calculated using Eqs 9 and 10.
The thermal conductivity of the fully sintered Gd2O3 as a function of temperature was experimentally measured using the laser flash method, and the results are shown in Figure 1. The thermal conductivity of fully dense Gd2O3 at temperatures higher than 800 °C was extrapolated from the experimentally measured data.
Figure 1. Thermal conductivity of fully dense Gd2O3 with increases in sintering temperature from 25 °C to 800 °C.
The thermal conductivities of the 1400 °C, 1500 °C, and 1600 °C pre-sintered Gd2O3 as functions of T were calculated from the thermal conductivity of the fully densified Gd2O3 using a modified Maxwell–Eucken correlation (Eq. 11):
where K100 and Kp are the thermal conductivities of fully dense and porous Gd2O3, respectively.
For YSZ, the thermal conductivity and heat capacity as a function of T and density were provided by Manière et al. (2017) and used in the simulation (Eqs 12-13). The surface energy was provided by Tsoga and Nikolopoulos (1996) as given by Eq. 14. The density was calculated from the determined porosity. The average particle radius of 700 nm (Sigma Aldrich) was used in the simulation. The creep factor (Eq. 15) was determined by fitting the experimentally determined density of YSZ with those predicted by the FEA of YSZ oxide pellets without Gd2O3 spheres or mini-pellets. The density of YSZ was determined from the experimentally measured shrinkage of YSZ after correcting its TEC (9.75 × 10–6 K–1) (Song et al., 2011).
For UO2, the surface energy as a function of T from 273 to 3120 K was provided by Hall and Mortimer (1986). Fink (2000) summarized this reported data and provided a correlation for the mean value of the surface energy of UO2 as a function of T (Eq. 16):
The heat capacity of the stoichiometric UO2 was measured by Kerrisk and Clifton (1972) over the temperature range 483–3107 K. These data were summarized and fitted to Eq. 17 in MATPRO (Siefken et al., 2001):
where Y is the oxygen-to-metal ratio (equal to 2), R is the universal gas constant (8.3143 J/mol⋅K), and M is the Einstein constant (535.285). The constants K1, K2, K3, and ED are equal to 296.7, 2.43 × 10–2, 8.745 × 107, and 1.577 × 105.
Lucuta et al. (1996) summarized the thermal conductivity of non-irradiated and fully dense UO2 and fitted the data to a function comprising a hyperbolic term for the lattice contribution through phonon–defect and phonon–phonon scattering processes and an exponential term for polaron contributions. The exponential term becomes dominant for high temperatures T > 1900 K.
The creep factor of UO2 was generated in a similar way to that of YSZ and is expressed by Eq. 19.
An average particle radius of 2400 nm was used for the simulation of UO2 (Yeo et al., 2013).
The shrinkage rates of the green YSZ, UO2, and Gd2O3 compacts and the 1400 °C, 1500 °C, and 1600 °C pre-sintered pellets were measured by a dilatometer (DIL 402C) up to 1600 °C in an air atmosphere with a heating rate of 10 °C/min and a holding time of 3 h. The results are shown in Figure 2.
Figure 2. Shrinkage behaviors of Gd2O3 compact, sintered Gd2O3 pellet, YSZ compact, and UO2 compact.
2-D axisymmetric simulation models were developed to study the sintering stress distributions during the fabrication process of YSZ pellets containing lumped Gd2O3 mini-pellets or spherical particles. The geometrical models used in the FEA simulations are shown in Figure 3.
Figure 3. Geometrical models of YSZ oxide pellet containing (A) lumped Gd2O3 spherical particle and (B) mini-pellet.
In order to determine the critical sintering stress for cracking, simulation models of YSZ oxide pellets with a Gd2O3 mini-pellet pre-sintered at 1400 °C, 1500 °C, or 1600 °C having the average measured dimensions of the pre-sintered pellets (see Table 1) and the measured shrinkage rates of the pellets sintered at 1400, 1500, and 1600 °C (see Figure 2) were developed. Simulation models of YSZ oxide pellets containing either lumped Gd2O3 spherical particles or mini-pellets of the same size and the shrinkage rate of the 1400 °C pre-sintered pellets were also developed to understand the effect of the lumped Gd2O3 shape on the formation of interfacial cracks. In addition, simulation models of YSZ oxide pellets with lumped Gd2O3 spherical particles of 1.5, 2, or 3 mm in diameter and the shrinkage rate of the pellets pre-sintered at 1400 °C were developed to determine the critical size of the lumped Gd2O3 spherical particles. Finally, simulation models of YSZ oxide pellets with a Gd2O3 spherical particle having the shrinkage rate of the pellet at 1400 °C, 1500 °C, or 1600 °C and the size of 1.5 mm were developed to understand the effect of the shrinkage rate on the formation of interfacial cracks.
The simulation models were assumed to have an initial temperature of 25 °C. The outer surfaces of the simulation models of the YSZ oxide pellets containing a lumped Gd2O3 sphere or mini-pellet were heated from 25 °C to 1500 °C or 1600 °C for the case of YSZ or UO2 with a heating rate of 10 °C/min, in accordance with the experimental procedures.
Figure 4 shows the FEA simulation results for the maximum sintering stress in YSZ oxide pellets containing a lumped Gd2O3 mini-pellet pre-sintered at 1400 °C, 1500 °C, or 1600 °C during heating from 25 °C to 1500 °C.
Figure 4. FEA-predicted maximum sintering stresses in YSZ oxide pellet containing a lumped Gd2O3 mini-pellet pre-sintered at 1400 °C, 1500 °C, or 1600 °C.
As shown in Figure 4, the maximum sintering stress in the YSZ oxide pellets containing a lumped Gd2O3 mini-pellet was almost constant in the temperature range 25–1100 °C and began increasing almost exponentially at approximately 1150 °C, corresponding to the temperature at which the YSZ pellet started to shrink (see Figure 2). As the pre-sintering temperature increased from 1400 °C to 1600 °C, the maximum sintering stress increased, which could be attributed to the increase in the shrinkage rate mismatch (see Figure 2). Previous experimental observations (Mistarihi et al., 2018) showed no interfacial cracks in YSZ pellets containing lumped Gd2O3 mini-pellets pre-sintered at 1400 °C, while cracks appeared in the YSZ oxide pellets containing lumped Gd2O3 mini-pellets pre-sintered at 1500 °C or higher. The maximum sintering stress in the YSZ oxide pellet containing a lumped Gd2O3 mini-pellet pre-sintered at 1400 °C during the fabrication process was calculated by FEA as approximately 120 MPa; that with the mini-pellets pre-sintered at 1500 °C was approximately 150 MPa. This indicates that sintering stresses in the range 120–150 MPa would result in the formation of interfacial cracks in the YSZ oxide pellet containing lumped Gd2O3. The flexural strength of the fully dense YSZ at room temperature is approximately 1000 MPa (Masaki, 1986) and it decreases almost linearly with increasing porosity to 170 MPa for YSZ with an RD of 40% (Gain et al., 2006). However, simulation studies of the residual stresses during the fabrication of ceramic composites have shown that residual stresses as low as 25 kPa (Schoenberg et al., 2006) or 90 MPa (DeHoff et al., 2008) can cause the formation of interfacial cracks in ceramic composites.
Figure 5 shows the stress distribution in the YSZ oxide pellet containing either a lumped Gd2O3 sphere (r = 0.75 mm) or mini-pellet (r = h = 0.83 mm) with the same volume of approximately 1.77 mm3 and the shrinkage rate of the 1400 °C pre-sintered Gd2O3 at a sintering temperature of 1300 °C.
Figure 5. Stress distributions in YSZ oxide pellets containing lumped Gd2O3 (A) sphere (r = 0.75 mm) or (B) mini-pellet (r = h = 0.83 mm). (r is the radius of the sphere or mini-pellet and h is the height of the mini-pellet).
As shown in Figure 5, the addition of Gd2O3 spheres resulted in the formation of symmetric stresses around the interface. Meanwhile, the Gd2O3 mini-pellet caused the formation of localized stresses at the edges of the mini-pellet. The formation of these localized stresses indicates that cracks would form in these areas, which is in good agreement with the experimental observation presented in our previous study (Mistarihi et al., 2018), where interfacial cracks in YSZ pellets containing lumped Gd2O3 mini-pellets were observed at the mini-pellet edges.
The FEA-calculated maximum sintering stresses in YSZ oxide pellets containing either a lumped Gd2O3 sphere (r = 0.75 mm) or mini-pellet (r = h = 0.83 mm) with equal volume and shrinkage rates during the sintering process are shown in Figure 6. In order to investigate the effect of the dimensions of the Gd2O3 mini-pellets on the sintering stresses developed during the manufacturing of YSZ oxide pellets containing lumped Gd2O3 mini-pellets, simulation models were also developed with Gd2O3 mini-pellets of equal volume to the spheres but the reduced r/h ratio of 0.5. The maximum sintering stresses developed during the manufacturing of the YSZ oxide pellet containing a lumped Gd2O3 mini-pellet (r = 1/2h = 0.65 mm) as calculated by FEA are also shown in Figure 6.
Figure 6. FEA-calculated maximum sintering stress in YSZ oxide pellets containing lumped Gd2O3 spheres and mini-pellets of the same volume and shrinkage rate.
The addition of mini-pellets yielded higher sintering stress over the entire temperature range, which can be attributed to the localized stresses at the edges of the mini-pellets. These higher localized sintering stresses are mainly caused by the outward bending of the Gd2O3 mini-pellet due to the shrinkage of the YSZ. The temperature gradient caused uniform shrinkage of the Gd2O3 spheres, yielding lower and symmetric sintering stresses in the YSZ oxide pellet containing a lumped Gd2O3 sphere. DeHoff et al. (2008) studied the stress distributions of bilayer open-ended cylindrical ceramics and spherical-core ceramics and found that the open-ended cylinder ceramics showed localized stresses at the upper edges of the cylinders, whereas the spherical-core ceramics had symmetric stress distributions around the core–shell interface. This indicates that the use of spherical Gd2O3 is better than that of mini-pellets to maintain the integrity of the CSBA fuel during fabrication. The localized stresses developed in the YSZ pellet containing a lumped Gd2O3 mini-pellet can be reduced by decreasing the aspect ratio of the mini-pellet because this diminishes the outward bending caused by the temperature gradient.
Figure 7 shows the FEA-calculated maximum sintering stress in YSZ oxide pellets containing lumped Gd2O3 spheres of equal size (r = 0.75 mm) but the shrinkage rates of Gd2O3 sintered at 1400 °C, 1500 °C, and 1600 °C. As shown in Figure 7, the maximum sintering stress during fabrication was increased with increases in the pre-sintering temperature of the lumped Gd2O3, which could be attributed to the increases in the shrinkage rate mismatch.
Figure 7. FEA-calculated maximum sintering stress in YSZ oxide pellets containing lumped Gd2O3 spheres of equal size (r = 0.75 mm) but different shrinkage rates.
According to the experimental observation in our previous study (Mistarihi et al., 2018), interfacial cracks were observed in YSZ oxide pellets containing lumped Gd2O3 mini-pellets pre-sintered at 1500 °C or higher, but not in YSZ containing lumped Gd2O3 spherical particles pre-sintered at 1600 °C. As can be seen from Figure 7, the calculated maximum sintering stress in the YSZ pellet containing a 0.75-mm-radius lumped Gd2O3 sphere pre-sintered at 1600 °C is approximately 105 MPa. The maximum calculated sintering stress in the YSZ pellet containing the 1500 °C pre-sintered mini-pellet was approximately 150 MPa (Figure 4). Therefore, the absence of interfacial cracks in the case of the YSZ pellet containing Gd2O3 spherical particles pre-sintered at 1600 °C could be attributed to the reduced symmetric sintering stress relating to their smaller sizes and spherical shapes, compared to those of the 1500 °C pre-sintered mini-pellet.
The effect of the Gd2O3 sphere size on the maximum sintering stress in YSZ oxide pellets containing lumped Gd2O3 spheres with the shrinkage rate of the 1400 °C sintered Gd2O3 during sintering is shown in Figure 8. As shown, the maximum sintering stress was increased with increases in the size of the Gd2O3 spheres. However, the increase was much smaller than that observed with increases in the Gd2O3 shrinkage rates. This indicates that the sintering stresses developed in the YSZ oxide pellets containing lumped Gd2O3 spheres are mostly controlled by the Gd2O3 shrinkage rate.
Figure 8. FEA-calculated maximum sintering stress in YSZ oxide pellets containing lumped Gd2O3 spheres of different sizes but equal shrinkage rates.
Experimental studies using UO2 are expensive and present high levels of radiotoxicity. In an experimental demonstration (Mistarihi et al., 2018) of the fabrication of oxide pellets containing lumped Gd2O3 spherical particles, mini-pellets, or rods, YSZ was used as a surrogate for UO2 because it has a similar crystal structure, high melting temperature, and sintering kinetics. However, for fabrication studies, the shrinkage rate and TEC of YSZ and UO2 must be similar, as well as the diffusivity of Gd3+ in the YSZ and UO2 matrices.
Figure 9 shows the FEA-calculated maximum sintering stress in UO2 pellets containing a lumped Gd2O3 sphere with a shrinkage rate of 1400 °C pre-sintered Gd2O3 but different sizes (r = 0.75, 1, 1.5 mm). As shown in Figure 9, the maximum sintering stress during the fabrication process was increased with increases in the size of the lumped Gd2O3. However, the calculated maximum sintering stresses in the UO2 fuel pellets were higher than those reported for YSZ pellets. The maximum sintering stresses in UO2 containing lumped Gd2O3 sphere with a radius of 1.5 mm at 1300 °C, 1400 °C, and 1500 °C were about 45.2, 80.3, and 101 MPa, respectively, whereas the maximum sintering stresses determined in YSZ pellet containing the same Gd2O3 sphere and at the same sintering temperatures were about 11.4, 29.2, and 68.8 MPa, respectively (see Figure 8). This could be attributed to the greater mismatch in the shrinkage rates of UO2 and Gd2O3 relative to that of YSZ and Gd2O3 (see Figure 2).
Figure 9. FEA-calculated maximum sintering stress in UO2 pellets containing lumped Gd2O3 spheres of different sizes but equal shrinkage rates.
The stress distribution in the UO2 pellet containing a lumped Gd2O3 sphere (r = 0.75 mm) with the shrinkage rate of 1400 °C pre-sintered Gd2O3 at the sintering temperature of 1300 °C is shown in Figure 10. The stress distribution was symmetric, similar to that in the YSZ pellet with the same conditions; however, the stress values were higher than those reported in YSZ, which can again be attributed to the higher shrinkage rate mismatch between UO2 and Gd2O3 relative to that between YSZ and Gd2O3 (see Figure 2).
Owing to the absence of sufficient experimental data for CSBA fuel using UO2, it is difficult to set threshold stress values for the formation of interfacial cracks in UO2-based CSBA. However, the fabrication of UO2 oxide pellets containing lumped Gd2O3 spherical particles pre-sintered at 1400 °C was reported by Oh et al. (2017) using the conventional fabrication conditions for UO2 of pressing under 3 ton/cm2 followed by sintering at 1700 °C for 4 h in an H2 atmosphere at approximately 5 °C/min. Similar results were observed regarding the absence of interfacial cracks and the formation of the gadolinium urinate phase at the interface between UO2 and Gd2O3.
The sintering stresses developed in the YSZ oxide pellets containing either lumped Gd2O3 spheres or mini-pellets during fabrication from 25 °C to 1500 °C were simulated using the FEA method. Thermal and linear elastic models were used to simulate the sintering stresses in lumped Gd2O3, while thermal and sintering models based on the continuum theory of sintering were used to simulate those in the YSZ powder compact. These models were coupled and implemented using COMSOL Multiphysics code.
The critical sintering stresses for the formation of interfacial cracks in YSZ oxide pellets containing lumped Gd2O3 were determined by comparing the FEA-calculated stresses in YSZ oxide pellets containing lumped Gd2O3 mini-pellets with the shrinkage rates of 1400 °C, 1500 °C, and 1600 °C sintered Gd2O3 with experimental observations. It was found that sintering stresses in the range of 120–150 MPa could cause the formation of interfacial cracks in these pellets.
The effects of the shape, shrinkage rate, and size of lumped Gd2O3 on the formation of cracks during fabrication were studied. It was found that the addition of cylindrical Gd2O3 mini-pellets resulted in localized and higher stresses at the mini-pellet edges. In contrast, the addition of Gd2O3 spherical particles yielded symmetric and lower stresses at the interface between the Gd2O3 and YSZ. Increases in the shrinkage rate and size of Gd2O3 resulted in higher sintering stresses in the YSZ oxide pellets containing lumped Gd2O3.
The sintering stresses developed during the fabrication of UO2 containing lumped Gd2O3 spheres were also estimated. Similar behaviors to those of YSZ were observed. However, the magnitude of the sintering stress was higher because of the higher shrinkage rate mismatch between UO2 and Gd2O3 relative to that between YSZ and Gd2O3.
The original contributions presented in the study are included in the article/supplementary material, further inquiries can be directed to the corresponding author.
QM did the finite element simulation and wrote the article. HR supervised and reviewed the written article. Both authors contributed to the article and approved the submitted version.
This study was supported by the KAI-NEET Institute of KAIST and the National Research Foundation (NRF) of Korea grant funded by the Korean Government (Ministry of Science, ICT and Future Planning) (NRF-2016R1A5A1013919, NRF-2018M2A8A1083889, and NRF-2019M2D1A1067210).
The authors declare that the research was conducted in the absence of any commercial or financial relationships that could be construed as a potential conflict of interest.
Agarwal, B. D. (1972). Micromechanics Analysis of Composite Materials Using Finite Element Methods. Ph.D. thesis, Illinois Institute of Technology, Chicago.
Choe, J., Shin, H. C., and Lee, D. (2016a). New burnable absorber for long-cycle low boron operation of PWRs. Ann. Nucl. Energy 88, 272–279. doi: 10.1016/j.anucene.2015.11.011
Choe, J., Zheng, Y., Lee, D., and Shin, H. C. (2016b). Boron-free small modular pressurized water reactor design with new burnable absorber. Int. J. Energy Res. 40, 2128–2135. doi: 10.1002/er
Davidge, R. W., and Green, T. J. (1968). The strength of two-phase ceramic glass materials. J. Mater. Sci. 3, 629–634. doi: 10.1007/BF00757910
DeHoff, P. H., Barrett, A. A., Lee, R. B., and Anusavice, K. J. (2008). Thermal compatibility of dental ceramic systems using cylindrical and spherical geometries. Dent. Mater. 24, 744–752. doi: 10.1016/j.dental.2007.08.008
Delale, F. (1988). Critical fiber size for microcrack suppression in ceramic-fiber ceramic-matrix compoistes. Eng. Fract. Mech. 31, 145–155.
Dole, S. L., and Hunter, O. (1976). Elastic properties of some Gd2O3-HfO2 compositions. J. Nucl. Mater. 59, 207–214.
Durazzo, M., Saliba-Silva, A. M., Urano De Carvalho, E. F., and Riella, H. G. (2013). Sintering behavior of UO2-Gd2O3 fuel: pore formation mechanism. J. Nucl. Mater. 433, 334–340. doi: 10.1016/j.jnucmat.2012.09.033
Fink, J. (2000). Thermophysical properties of uranium dioxide. J. Nucl. Mater. 279, 1–18. doi: 10.1016/S0022-3115(99)00273-1
Fleming, R. F. (1982). Neutron self-shielding factors for simple geometrics. Int. J. Appl. Radiat. Isot. 33, 1263–1268. doi: 10.1016/0020-708X(82)90247-2
Gain, A. K., Song, H. Y., and Lee, B. T. (2006). Microstructure and mechanical properties of porous yttria stabilized zirconia ceramic using poly methyl methacrylate powder. Scr. Mater. 54, 2081–2085. doi: 10.1016/j.scriptamat.2006.03.009
Galperin, A., Segev, M., and Radkowsky, A. (1986). Substitution of the Soluble boron reactivity control system of a pressurized water reactor by gadolium burnable poisons. Nucl. Technol. 75, 127–133. doi: 10.13182/NT86-A33855
Grossbeck, M. L., Renier, J.-P. A., and Grossbeck, M. L. (2001). Development of improved Burnable Poisons for Commercial Nuclear Power Reactors. Oak Ridge, TN: Oak Ridge National Laboratory.
Haglund, J. A., and Hunter, O. (1973). Elastic properties of polycrystalline monoclinic Gd2O3. J. Am. Ceram. Soc. 56, 327–330. doi: 10.1111/j.1151-2916.1973.tb12506.x
Hall, R. O. A., and Mortimer, M. J. (1986). A critical review of the surface energy of UO2. J. Less Common Met. 121, 341–345. doi: 10.1097/00152193-198306000-00031
Kerrisk, J. F., and Clifton, D. G. (1972). Smoothed values of the enthalpy and heat capacity of UO2. Nucl. Tech. 16, 531–535. doi: 10.13182/NT72-6
Li, C., Wu, Y., Wang, Y., Wang, K., Wang, M., Tian, W., et al. (2020). Analysis on the behavior of dispersed plate-type fuel based on fluid-solid coupling method. Prog. Nucl. Energy 126:103398. doi: 10.1016/j.pnucene.2020.103398
Lucuta, P. G., Matzke, H., and Hastings, I. J. (1996). A pragmatic approach to modelling thermal conductivity of irradiated UO2 fuel: review and recommendations. J. Nucl. Mater. 232, 166–180. doi: 10.1016/S0022-3115(96)00404-7
Manière, C., Zahrah, T., and Olevsky, E. A. (2017). Fully coupled electromagnetic-thermal-mechanical comparative simulation of direct vs hybrid microwave sintering of 3Y-ZrO2. J. Am. Ceram. Soc. 100, 2439–2450. doi: 10.1111/jace.14762
Masaki, T. (1986). Mechanical properties of toughened ZrO2-Y2O3 ceramics. J. Am. Ceram. Soc. 69, 638–640. doi: 10.1111/j.1151-2916.1986.tb04823.x
Mistarihi, Q. M., Park, W., Nam, K., Yahya, M.-S., Kim, Y., and Ryu, H. J. (2018). Fabrication of oxide pellets containing lumped Gd2O3 using Y2O3-stabilized ZrO2 for burnable absorber fuel applications. Int. J. Energy Res 42, 2141–2151. doi10.1002/er.3995
Nguyen, X. H., Kim, C. H., and Kim, Y. (2019). An advanced core design for a soluble-boron-free small modular reactor ATOM with centrally-shielded burnable absorber. Nucl. Eng. Technol. 51, 369–376. doi: 10.1016/j.net.2018.10.016
Oh, J. S., Mistarihi, Q., Ryu, H. J., and Kim, D.-J. (2017). “Fabrication of Gadolinia-containing UO2 fuel pellet,” in Proceedings of the 42nd International Conference and Expo on Advanced Ceramics and Composites, Daytona Beach, FL.
Olevsky, E. A. (1998). Theory of sintering: from discrete to continuum. Mater. Sci. Eng. R Rep. 23, 41–100. doi: 10.1016/S0927-796X(98)00009-6
Olevsky, E. A., Garcia-Cardona, C., Bradbury, W. L., Haines, C. D., Martin, D. G., and Kapoor, D. (2012). Fundamental aspects of spark plasma sintering: II. Finite element analysis of scalability. J. Am. Ceram. Soc. 95, 2414–2422. doi: 10.1111/j.1551-2916.2012.05096.x
Riedel, H., Meyer, D., Svoboda, J., and Zipse, H. (1993). Numerical simulation of die pressing and sintering — development of constitutive equations. Int. J. Refract. Met. Hard Mater. 12, 55–60. doi: 10.1016/0263-4368(93)90016-9
Schoenberg, S. E., Green, D. J., Segall, A. E., Messing, G. L., Grader, A. S., and Halleck, P. M. (2006). Stresses and distortion due to green density gradients during densification. J. Am. Ceram. Soc. 89, 3027–3033. doi: 10.1111/j.1551-2916.2006.01182.x
Selsing, J. (1961). Internal stresses in ceramics. J. Am. Ceram. Soc. 44, 419–419. doi: 10.1111/j.1151-2916.1961.tb15475.x
Sglavo, V. M., and Bellettati, N. (2017). Ceramic laminates with improved mechanical reliability by tailoring the porosity of the constituting layers. J. Eur. Ceram. Soc. 37, 1643–1650. doi: 10.1016/j.jeurceramsoc.2016.11.022
Siefken, L. J., Coryell, E. W., Harvego, E. A., and Hohorst, J. K. (2001). MATPRO-A Library of Materials Properties for Light-Water-Reactor Accident Analysi. Idaho Falls, ID: Idaho National Engineering and Environmental Laboratory.
Song, X., Lu, J., Zhang, T., and Ma, J. (2011). Two-stage master sintering curve approach to sintering kinetics of undoped and Al2O3-doped 8 Mol% yttria-stabilized cubic zirconia. J. Am. Ceram. Soc. 94, 1053–1059. doi: 10.1111/j.1551-2916.2010.04199.x
Tsoga, A., and Nikolopoulos, P. (1996). Surface and grain-boundary energies in yttria-stabilized zirconia (YSZ-8 mol%). J. Mater. Sci. 31, 5409–5413. doi: 10.1007/BF01159310
Yahya, M.-S., and Kim, Y. (2017a). An innovative core design for a soluble-boron-free small pressurized water reactor. Int. J. Energy Res. 41, 1–9. doi: 10.1002/er.3792
Yahya, M.-S., and Kim, Y. (2017b). “Centrally-shielded burnable absorber for LWR fuel,” in Proceedings of the International Congress on Advances in Nuclear Power Plants (Fukui and Kyoto: American nuclear society).
Keywords: finite element analysis, sintering stress, lumped burnable absorber fuel, interfacial cracks, shrinkage mismatch
Citation: Mistarihi Q and Ryu HJ (2021) Finite-Element Simulation of Residual Stresses During the Processing of Lumped Burnable Absorber Fuel. Front. Energy Res. 9:651339. doi: 10.3389/fenrg.2021.651339
Received: 09 January 2021; Accepted: 02 March 2021;
Published: 19 March 2021.
Edited by:
Mingjun Wang, Xi’an Jiaotong University, ChinaReviewed by:
Wenzhong Zhou, Sun Yat-sen University, ChinaCopyright © 2021 Mistarihi and Ryu. This is an open-access article distributed under the terms of the Creative Commons Attribution License (CC BY). The use, distribution or reproduction in other forums is permitted, provided the original author(s) and the copyright owner(s) are credited and that the original publication in this journal is cited, in accordance with accepted academic practice. No use, distribution or reproduction is permitted which does not comply with these terms.
*Correspondence: Ho Jin Ryu, aG9qaW5yeXVAa2Fpc3QuYWMua3I=
Disclaimer: All claims expressed in this article are solely those of the authors and do not necessarily represent those of their affiliated organizations, or those of the publisher, the editors and the reviewers. Any product that may be evaluated in this article or claim that may be made by its manufacturer is not guaranteed or endorsed by the publisher.
Research integrity at Frontiers
Learn more about the work of our research integrity team to safeguard the quality of each article we publish.