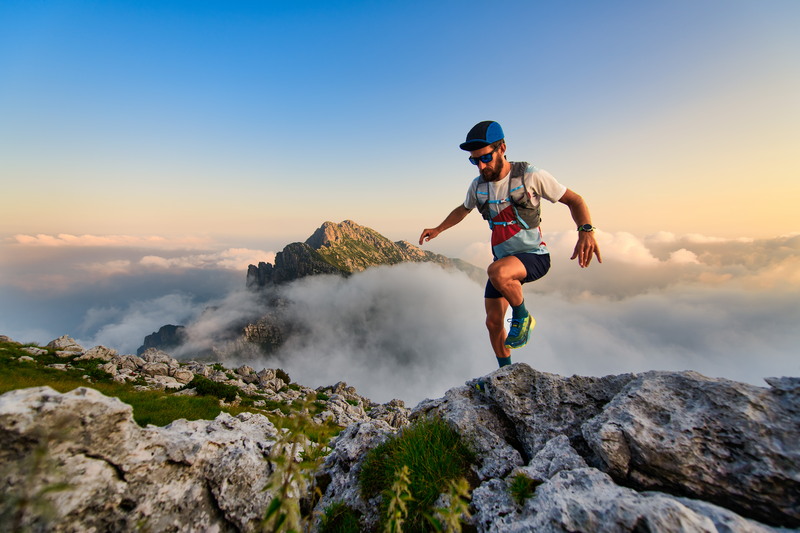
94% of researchers rate our articles as excellent or good
Learn more about the work of our research integrity team to safeguard the quality of each article we publish.
Find out more
PERSPECTIVE article
Front. Energy Res. , 11 May 2021
Sec. Carbon Capture, Utilization and Storage
Volume 9 - 2021 | https://doi.org/10.3389/fenrg.2021.592600
This article is part of the Research Topic Beyond Current Research Trends in CO2 Utilization View all 11 articles
Accelerated carbonation is a carbon utilization option which allows the manufacturing of useful products, employing CO2-concentrated or -diluted emission sources and waste streams such as industrial or other processing solid residues, in a circular economy perspective. If properly implemented, it may reduce the exploitation of virgin raw materials and their associated environmental footprint and permanently store CO2 in the form of Ca and/or Mg carbonates, thus effectively contributing to climate change mitigation. In this perspective article, we first report an overview of the main mineral carbonation pathways that have been developed up to now, focusing on those which were specifically designed to obtain useful products, starting from different alkaline feedstocks. Based on the current state of the art, we then discuss the main critical issues that still need to be addressed in order to improve the overall feasibility of mineral carbonation as a CCUS option, as well as research needs and opportunities.
Achieving the UN target of 1.5–2.0°C maximum temperature increase by 2100, set by the COP 21 Paris Climate Conference, requires the implementation of different actions aimed at mitigating climate change (IPCC et al., 2018; Woodall et al., 2019). A shift to low carbon energy technologies will be required to achieve such stringent targets, but this implies a nontrivial transformation of the status quo, where fossil fuels account for more than 80% of the global primary energy supply (Vinca et al., 2018). This suggests that any pathway aimed at reducing carbon emissions shall include a transition phase, during which fossil fuels will still need to be used but their related emissions should be captured and not released into the atmosphere. Besides, as probably we will need in the future to reduce the CO2 concentration in the atmosphere, carbon capture and storage (CCS) should be applied also to emissions from biomass to energy plants (BECCS) or even directly to air (DACCS), leading effectively to negative carbon emissions (Realmonte et al., 2019). CCS according to some scenarios might represent from 30 to 40% of the primary energy use (Vinca et al., 2018); however, geological storage, already applied at scales of around 1 Mt CO2/y, is still facing concerns about storage sites, public acceptance, costs, and large-scale feasibility (Vinca et al., 2018). In this context, CO2 utilization has been proposed as an alternative or integration to geological storage since it allows conversion of CO2 into a wide variety of end products, including chemicals and fuels (MacDowell et al., 2017). According to the National Academies of Sciences, Engineering, and Medicine (NASEM - National Academies of Sciences, Engineering, and Medicine, 2019), CO2 utilization technologies have a role to play in future carbon management and the circular carbon economy; among these, mineral or accelerated carbonation (MC) is considered the closest option to commercial scale implementation due to its thermodynamic favorability and market size (Woodall et al., 2019). In MC, which is considered a process that can allow the bridging of CO2 storage and CO2 utilization, CO2 reacts with alkaline earth metal oxide-bearing phases, such as Ca/Mg (hydr)-oxides and silicates, forming stable solid carbonates. This process may be tailored to manufacture products for construction applications and high purity Ca- and Mg-based carbonates for different uses (Librandi et al., 2019). Potential alkalinity sources for mineralization include geologically derived feedstock materials such as olivine and serpentine or alkaline industrial residues (Hills et al., 2020). These residues are typically available in the proximity of CO2 source emissions, present a high reactivity even at mild operating conditions, and, differently from natural ores, may also present suitable grain size without pretreatment (Librandi et al., 2019). Despite MC achieving permanent sequestration of CO2 in solid form similarly to other CCS options, the primary driver of MC as a CCU option should be feedstock substitution and the production of materials at a lower cost and with an associated lower fossil carbon footprint rather than locking up CO2 (MacDowell et al., 2017). We share this vision, and this perspective article is focused on the application of MC to manufacture useful products, as we believe that this will allow acceleration of MC deployment at large scale.
Mineral carbonation is a naturally occurring weathering reaction which involves the interaction of carbon dioxide with minerals typically found in mafic and ultramafic rocks (i.e., mainly Mg- and Ca-based silicates), leading to the formation of thermodynamically stable mineral carbonates (such as magnesite, calcite, and dolomite). This reaction is exothermic and contributes to the chemical weathering of continental surfaces, which has been suggested to be enhanced by the current modifications in climate and atmospheric composition and, although presents slow reaction kinetics, could play a role in the evolution of the global carbon cycle over the next centuries (Beaulieu et al., 2012). Weathering of silicates is a multiphase reaction since CO2 dissolves and ionizes in water leading to the formation of carbonic acid (H2CO3) that in turn can partly dissolve the rocks, releasing the CaO/MgO phases that react with HCO3−/CO32−, yielding the final carbonate product.
The exploitation of MC as a CO2 storage option has been investigated through both in situ and ex situ process routes, as reviewed extensively in Sanna et al. (2014) and Kelemen et al. (2019). In situ MC processes basically consist in enhancing mineral trapping of CO2 by weathering through the injection of CO2-rich fluids in reactive geological formations, such as mantle peridotites (Kelemen and Matter, 2008) and basalt deposits (Gislason et al., 2010). In particular, most of the CO2 injected into subsurface pore space in basaltic lavas in Iceland was reported to have mineralized in less than two years (Matter et al., 2016). This approach is at a lower stage of technological readiness compared to geological storage; however, it has been estimated that globally in situ MC has the potential of sequestering up to 60,000,000 GtCO2 if the resource is economically accessible and fully carbonated (Kelemen et al., 2019). As for ex situ MC, several processes have been developed to speed up the reactivity of alkaline feedstocks such as minerals and industrial residues, thus allowing to achieve relevant CO2 storage yields (several GtCO2/y) in industrially feasible time frames (i.e., up to a few hours) (Sanna et al., 2014; NASEM - National Academies of Sciences, Engineering, and Medicine, 2019). Kelemen et al. (2019) actually report a third MC pathway—surficial MC—by which dilute or concentrated CO2 is reacted on-site with the alkaline feedstock, such as mafic and ultramafic mine tailings. This MC option represents an interesting application for offsetting mining CO2 emissions on-site (Wilson et al., 2009; Mervine et al., 2018) and was estimated that may provide in the next decades an increasing capture capacity from hundreds of Mton CO2/y to over 1 Gton CO2/y, depending on the socioeconomic scenario considered (Renforth, 2019). In addition, in situ carbonation of artificial soils (i.e., soils containing calcium-rich materials such as demolition waste or steel slag) was indicated as an option that could allow to sequester globally 290 Mt C/y in construction/development sites (Renforth et al., 2009).
With regard to ex situ MC pathways, which may be applicable also for CO2 utilization besides storage, many different alkalinity feedstocks, process routes, and sets of operating conditions have been tested. The most investigated minerals include worldwide abundant Mg-based silicates such as serpentine and olivine and Ca silicates such as wollastonite, which is much more limited—with global reserves estimated at only 100 Mt (U.S. Geological Survey, 2021)—but presents a greater reactivity with CO2 due to the higher precipitation rate of CaCO3 compared to MgCO3. As for residues, several types of alkaline waste materials, including coal fly ash, cement kiln dust (CKD), concrete waste, paper mill waste, municipal solid waste incineration residues such as bottom ash and air pollution control (APC) residues, steel-making by-products, asbestos, and Ni tailings and red mud (Al extraction waste) have been tested (see e.g., Pan et al., 2012; Sanna et al., 2014). Overall, the amounts of industrial residues suitable for MC treatment, which currently are mostly landfilled or employed only for low-end applications, have been estimated to exceed 2 Gt/y (Hills et al., 2020).
As previously mentioned, at ambient conditions, carbonation proceeds via gas–liquid–solid pathways. Most of the research on accelerated carbonation has focused on the aqueous route, generally mixing the alkaline feedstock with water applying liquid to solid (L/S) ratios above 2 L/kg (slurry-phase) (Baciocchi et al., 2014). This route may be applied directly, that is, alkaline oxide dissolution and carbonate precipitation can be performed in the same reactor in a one-stage process, or indirectly, separating the dissolution and precipitation steps. In this latter process, carbonation can be completed under milder conditions because of the independent optimization of each step, leading to an enhancement of the overall carbonate conversion rate and to a product with a higher purity (Mission Innovation, 2017), as discussed in Paragraph 2.1. With regard to indirect treatment routes, many different types of reagents have been tested for promoting Mg extraction from the feedstock, including, in particular, ammonium salts (e.g., Wang and Maroto-Valer 2011; Zevenhoven et al., 2017). The direct route is best suited to treating concentrated CO2 streams, whereas the indirect approach can be applied also to diluted CO2 streams, including untreated flue gases (Mission Innovation, 2017). Several pretreatments have been applied to enhance the reaction kinetics of minerals, and in particular of serpentine to remove hydroxyl groups including mechanical, chemical, and thermal activation (Sanna et al., 2014). It should be noted, however, that thermal activation may lead to the formation of undesirable side reactions (i.e., the reformation of crystalline serpentine and precipitation of amorphous magnesium silicate hydroxide phases on the surface of reacting particles), resulting in a significant decrease in reaction efficiency (Benhelal et al., 2019). Besides, biochemical enhancement employing the enzyme carbonic anhydrase to catalyze the hydration of aqueous CO2 has been also tested (e.g., Patel et al., 2013; Power et al., 2016). High carbonate conversion yields (above 80%) have been achieved by applying the NETL-Albany direct slurry-phase process to olivine employing a pCO2 of 150 atm, temperatures greater than 90°C, and a 1 M NaCl and 0.64 M NaHCO3 solution (Gerdemann et al., 2007). The reactivity of Ca-bearing minerals, such as labradorite and Ca, and/or Mg-bearing rocks, such as anorthosite and basalt, at reaction conditions similar to those reported above is one to two orders of magnitude lower than that of olivine (Gadikota et al., 2020). The reactivity of residues, which is different from minerals, is mostly related to Ca-based phases and depends upon the abundance and the type of mineral phases. Specifically, free oxide and hydroxide phases, such as lime and portlandite, are typically found in significant amounts only in APC residues, CKD, and paper mill waste, and basic oxygen furnace (BOF) steel slag is highly reactive even at mild operating conditions. As for silicate phases, the most reactive are reported to be tricalcium (alite, Ca3SiO5) and dicalcium (belite, Ca2SiO4) silicates, which are generally retrieved in materials such as concrete demolition waste or steel manufacturing slag (Baciocchi et al., 2014). For residues characterized by the abovementioned types of phases, the aqueous direct route may be run also using very low L/S ratios (typically below 1 L/kg) and in this case is often referred to as the wet or thin film route. This route has been particularly investigated for manufacturing construction materials from industrial residues and for cement curing, as discussed in Paragraphs 2.2–2.3. Alternatively, direct gas–solid pathways have been also tested; residues from thermal treatment processes can be directly contacted with CO2 diluted streams at atmospheric pressure, exploiting the high temperature of the residues and/or of the flue gas, but the reaction involves only calcium oxides or hydroxides phases (Prigiobbe et al., 2009; Santos et al., 2012).
The application of direct and indirect MC processes to minerals and industrial alkaline materials offers the opportunity to produce a range of products and by-products that may find several uses. Applications include construction materials (e.g., cements, concrete, and mortars), aggregates or compacts (e.g., for road-base, erosion, sea, and flood protection barriers), and calcium- and magnesium-based carbonates (specialty products) that may be used for different applications (e.g., as additives for protective coatings such as paints and polymers). Specialty products resulting from carbonation of alkaline materials also include hydrated Mg carbonates that may be employed for thermal energy storage or as CO2 transport medium and other products that may be obtained by selective dissolution of the reacting feedstock, such as silica and metals or metalloids (Mission Innovation, 2017).
As shown in Figure 1, some of the MC products, such as aggregates, may be employed in concrete manufacturing, contributing to further decrease the carbon footprint of this material compared to CO2 curing, which consists already in an improvement versus the traditional steam curing method, as discussed below.
FIGURE 1. Scheme of current CO2 utilization pathways for producing carbonated materials to use in construction or other applications. Solid reagents are reported in green boxes, whereas final products in blue. Turquois boxes highlight MC products that can be used as reagents to manufacture other products.
The main focus of this section is on high purity carbonates which represent the specialty product with the most relevant market potential. The market of high purity carbonates is constituted mainly by precipitated calcium carbonate (PCC), which is used as filler or coating material in various types of applications, comprising paper, paint, plastics, and adhesives, among many others (Jimoh et al., 2018; Zevenhoven et al., 2019). As of 2014, the market for mineral fillers and pigments is about 14 Mt/y with a high value of 375–550 USD/t (Woodall et al., 2019). PCC is made of either fine or very fine nanoparticles that are synthesized either by a lime soda process, a calcium chloride process, or a process based on the carbonation of calcium hydroxide produced after calcination and hydration of a carbonate rock (Teir et al., 2005; Jimoh et al., 2018). The need to manufacture precipitated calcium carbonate with a definite morphology, structure, and particle size is necessary due to its wide application in various industries (Jimoh et al., 2018). The most important crystalline forms of PCC are the rhombohedral calcite type, scalenohedral calcite type, and orthorhombic acicular aragonite type. The scalenohedral form is favoured in most applications. There are several various types of PCC grades, but the purity of PCC is usually over 99% with a density of 2700 kg/m3 (Teir et al., 2005).
Teir et al. (2005) first introduced and modeled different processes for producing PCC from calcium silicate as alkalinity source instead of calcium carbonate. From this work, the so-called Slag2PCC process was developed, in which the alkalinity source is provided by steel slags, in particular BOF slags (Said et al., 2013; Mattila et al., 2014; Zevenhoven et al., 2019). As reported in Figure 2, calcium is first extracted using an ammonia salt (typically chloride), and the obtained Ca-rich slurry is fed to a carbonation section, where PCC is obtained after reaction with CO2, even from a diluted source without the need for a separate CO2 capture step (Zevenhoven, 2020).
FIGURE 2. Flow diagram of the Slag2PCC concept for PCC production from steel-making slags. Reproduced with permission from Zevenhoven et al. (2019).
Despite the process being developed up to pilot scale (Said et al., 2013), achieving product purity above 99.5% using a 1 M ammonium chloride solution for Ca extraction, the scale-up to an industrial size process, for example, ∼25 t/h BOF slag, faces several challenges/drawbacks. These include: the significant amount of water needed to wash the PCC product (to recover the solvent salt), the separation of the solids (slag residue and PCC product) from the aqueous streams, and the low calcium amount extracted from the slag, with a significant amount of residual solids resulting from the process (Zevenhoven et al., 2019). The cradle-to-gate LCA of the process showed that operating at the experimentally tested ammonia concentration in the extraction solution (0.65 M) and at a 0.1 kg/L slag to solution ratio, the Slag2PCC approach suffers from the large amount of process steam required for recycling the washing water, which increases the environmental impact of the process, even compared to traditional PCC manufacturing (Mattila et al., 2014). Operating at a much lower ammonia concentration, that is, 0.01 M, the Slag2PCC process results into negative CO2 emissions, that is, CO2 stored into the PCC product, although in this case, the calcium extraction step must be repeated several times with the same slag to obtain the same total conversion as with an over-stoichiometric solvent concentration (Mattila et al., 2014). Besides PCC, also other specialty products have been recently investigated, namely, Erlund and Zevenhoven. (2019) studied the heat effects and storage capacity for thermal energy storage applications of a composite materialmade by magnesium carbonate hydrate (Nesquehonite) and silica gel, where the former one is produced by carbonation of alkalinematerials with Mg-bearing phases. Carbonation for production of metastable carbonates such as nesquehonite was also recently proposed and tested as carbon growth media for microalgae, for cases in which pure or even diluted CO2 sources may not be available nearby algae production plants (Ye et al., 2019).
Synthetic aggregates may be produced by treating different types of alkaline residues by carbonation through the carbo-granulation pathway (see Figure 3A). This process consists in combining wet-route MC with a cold-bonding granulation process, during manufacturing and/or product curing (Gunning et al., 2011). Alkaline residues may, in fact, present a fine particle size as-produced, for example, fly ash or APC residues, or after grinding for ferrous/nonferrous metals removal, for example, bottom ash or steel slag. Carbo-granulation applied to ground BOF slag allowed to achieve a significant increase in particle size and a CO2 uptake of around 10% by weight (Morone et al., 2014). However, alkaline activation, consisting in the use of a sodium silicate/sodium hydroxide solution instead of water as binder, proved necessary to attain granules with a mechanical strength close to the one typically exhibited by gravel (Morone et al., 2017). Carbon8 Systems have achieved commercial operation of plants that make use of alkaline waste materials, APC residues in particular, concentrated CO2 streams, and other binders and fillers to produce lightweight aggregates for use mainly in concrete. A recent innovation of this process is the development of a mobile plant with a capacity of 12,000 t/y of manufactured aggregates that can directly use flue gas and be located in the proximity of point-source emitters of CO2 and residues, thus avoiding the need for transport and CO2 capture (Hills et al., 2020). Co-location of an aggregate manufacturing plant with CO2 emission sources such as power plants and industries generating solid reactants is also part of the concept of the Blue Planet process that employs alkaline residues such as concrete waste and produces lightweight carbonate-coated aggregates (Blue Planet, 2021). Specifically, as shown in Figure 3B, CO2 from diluted sources is absorbed in an ammonium salt solution; the ammonium carbonated water is then contacted with the residues and synthetic CaCO3 layers are formed over a substrate. A field trial was performed in 2016 in which lightweight carbon-coated aggregates were used as partial replacement of coarse aggregates in the concrete mix employed for building a pedestrian atrium deck at San Francisco airport (Blue Planet, 2021). Another process based on MC to produce aggregates from alkaline residues was reported by Ghouleh et al. (2017); in this process, hydrated BOF slag was first compacted in cylindrical specimens that were cured under 100% CO2; the compacts were then crushed to angular shape in order to achieve a particle size distribution typical of fine aggregates (Figure 3C). Concrete slabs prepared from this waste material displayed comparable strengths to granite-based slabs and better strength than slabs prepared from commercial lightweight aggregates (Ghouleh et al., 2017).
FIGURE 3. Mineral carbonation pathways to produce aggregates or compacts. (A) Carbo-granulaion pathway. (B) Carbonate-coating route. (C) Compacting + accelerated curing route.
Aggregates, including sand, gravel, and crushed stone, represent a low-value commodity with a global market of over 50 Gt/y and a relatively low associated carbon intensity (7.85 kgCO2 eq/t aggregates) (Woodall et al., 2019). This makes it difficult for MC-produced aggregates to be competitive with the traditionally employed ones, unless the former ones present superior properties and/or allow storage of large amounts of CO2. An additional asset, if not the main driver currently for employing industrial residues in aggregate manufacturing, is the payment of gate fees for the treatment of waste such as APC residues, a hazardous waste that presents a high landfilling cost. Another aspect that should also be considered besides the technical properties of the product is its environmental properties since alkaline residues may release significant amounts of metals, metalloids, and salts, and carbonation has shown to be able to improve the chemical stability only of some constituents (see e.g., Costa et al., 2007; Morone et al., 2014). Specific end-of-waste criteria are established at a country or even provincial or regional level and may require the compliance with leaching guidelines also for artificial aggregates employed in bound applications.
Another interesting application of MC, also depicted in Figure 3C, is a patented process that allows manufacturing of blocks or compacts called Carbstone using finely milled steel slags that, by curing with concentrated CO2 streams at elevated temperature and pressure, achieve high mechanical performance without the use of cementitious binders (Quaghebeur et al., 2015). Two MC processes have been developed up to industrial scale: a low-pressure process for the production of common building blocks (compressive strength up to 50 MPa) using 50% dried fine-grained stainless steel slags and 50% fine sand and a high-pressure process for the production of high-strength materials (compressive strength>50 MPa) (Di Maria et al., 2020). LCA of the low-pressure process that includes different capture options for the CO2 to use in the curing step indicates that this technology can be considered carbon-negative since the amount of CO2 stored during the process (around 9% by weight) is higher than the amount of CO2 emitted, considering the whole life cycle of the block. Nonetheless, electricity and heat requirements represent the main environmental burden of this technology in terms of CO2 emissions (Di Maria et al., 2020).
Steam-cured conventional concrete market use amounts currently to over 27 Gt/y and presents an associated carbon intensity around 0.14 tCO2/t concrete (Woodall et al., 2019). It has been estimated that the application of MC to concrete, for example, through early-stage CO2 curing, has a global CO2 avoidance potential of more than 1.5 GtCO2/year (Woodall et al., 2019). CO2 curing has been proposed to manufacture concrete blocks using different binders alternative to Portland cement (OPC) such as binary mixtures of wollastonite–Portland cement (WPC), MgO–Portland cement (MPC), limestone–Portland cement (LPC), and slag–Portland cement (SPC) (Huang et al., 2019). If Portland cement is used as a binder, carbonation curing may lead to a lower pH than in steam-cured concrete, which may limit its use to nonreinforced applications (Zhang et al., 2017). Using nonhydraulic binders may allow avoiding this limitation, but care must be taken in ensuring homogeneous and in-depth carbonation of the block, as the material’s strength relies solely on the carbonation reaction rather than on hydration reactions (Zhang et al., 2017). Cements made with nonhydraulic binders, such as wollastonite and rankinite (Ca3Si2O7), are marketed by Solidia, which claims a reduction of CO2 emissions associated with cement production of up to 30% with respect to traditional cement and a further permanent sequestration of CO2 of up to 300 kg per tonne of cement incorporated in the concrete formulation after CO2 curing (Solidia CementTM, 2013). Carbon dioxide treatment of concrete upstream from product mold is also currently marketed by Carboncure in the United States (Niven et al., 2012) with a claimed number of more than 562,000 trucks of CO2-cured concrete delivered (indicatively a fully loaded truckload holds 10 cubic yards, i.e., 7.5 m3 of concrete) and a net CO2 reduction of 40,000 t achieved in the last year (period March 2020–March 2021) (Carbon Cure, 2021).
Another MC product that may find application in concrete is amorphous silica that can be obtained through indirect routes. In particular, acid-treated silica-enriched residues from serpentine dissolution were found to display pozzolanic activity and hence were suggested as high-quality reactive cement additives (e.g., Sanna et al., 2012; Benhelal et al., 2018).
In 2008, the United Kingdom–based company Novacem, in collaboration with Lafrange, developed a process to manufacture cement, termed as green or carbon-negative, from magnesium silicate rocks (e.g., olivine or serpentine). In this process, these rocks are carbonated with CO2 at 200°C and 180 bar to produce magnesium carbonate, which is then decarbonated at 700°C to produce magnesium oxide. The final Novacem cement composition is a mix of magnesium oxide, hydrated magnesium carbonates, and pozzolans (Naqi and Jang, 2019).
The distinctive feature of carbonation as a CCUS option relies in the long-term carbon storage that can be achieved in most of the manufactured products, the potential of which has been discussed in several studies. Even not considering the development of a tailored mining activity aimed at the extraction of silicate minerals, which could, in principle, lead to a carbonation potential of the same scale of CO2 yearly emissions, the production of ultramafic (and mafic) tailings alone is estimated to be about 200–400 Mt year, thus leading to a carbonation potential approximately between 100 and 200 MtCO2/y, assuming serpentine as the main mineral phase and magnesite as carbonation product (Woodall et al., 2019). The remaining alkaline materials, which include a wide range of industrial waste, may also contribute around 0.97 GtCO2/y (Woodall et al., 2019). Renforth (2019) recently estimated the future trend of the global CO2 carbonation potential of alkaline materials, with figures (excluding carbon absorption by cement) between 0.8 and 1.3 GtCO2 yr−1 in 2050 and 1.4 and 2.7 GtCO2 yr−1 by 2100, depending on the socioeconomic global pathway considered. According to Renforth (2019), these figures represent a theoretical maximum potential, which, in practice, would be difficult to realize. In fact, they are limited by the effective conversion of Ca or Mg mineral phases to carbonates and by the availability of a market for the carbonation products (see again Woodall et al., 2019, for further discussion).
Mineral carbonation has been extensively investigated during the last 25 years. Nevertheless, full-scale applications are still limited in number and in market coverage. A wider diffusion of MC has been hindered so far, mainly by the limited CO2 and alkalinity sources suitable to make the process feasible in terms of energy requirements and by the limited interest of the market for MC products. It should be noted that the direct use of CO2-diluted sources such as flue gas, biogas, or syngas, which allows avoiding a preliminary CO2 capture step, can significantly reduce the energy requirements of the process. However, the direct use of off-gas should not affect the quality and purity of the products; therefore, depending on the characteristics of gas flow and of the targeted product, the use of specific pretreatments for impurity removal should be considered.
Besides, a still insufficient understanding of the fundamental mechanisms and reaction pathways underlying mineral carbonation probably did not allow the development of the most efficient carbonation routes. So far, the applications which have achieved pilot or full-scale stage are based on the more reactive alkalinity sources, that is, alkaline industrial residues (specifically APC residues and steel slag), cement, or even minerals containing Ca-bearing phases rather than Mg-bearing ones.
The reactivity of alkalinity sources must be increased by improving the extraction efficiency of alkaline metals as well as by investigating process integration and industrial symbiosis opportunities to reduce energy requirements.
Besides, we need more effort at a fundamental scale to not only improve the knowledge on the mechanisms underlying the carbonation process but also to increase the extent and quality of experimental data in order to make mass/energy requirement assessment more precise. This will allow to assess in a more comprehensive way the actual contribution of mineral carbonation by detailed and more consistent life cycle assessment (LCA) approaches that should be applied with the same level of detail to evaluate all MC pathways.
Carbonation processes should be developed with the aim of manufacturing improved or new products, which may have a wider market than the current ones. Currently, MC product use in construction is limited to precast building materials and nonreinforced applications. An important step ahead would be if the technology could be adapted to replace the cement binder in ready-mix concrete and in reinforced (concrete) building applications; however, to reach this goal, further improvements in the mechanical behavior and environmental quality of the carbonated products would be necessary (Mission Innovation, 2017).
New ideas include, for instance, the integration of the recovery of rare earth elements during the mineral carbonation treatment to maximize the exploitation and valorization of steel slags, while contributing to the reduction of CO2 emissions and the sustainable utilization of energy.
Besides, new feedstocks need to be explored since aggregates, compacts, and binder manufacturing by MC are constrained by the availability of alkaline residues and not by the market demand for these products. Supplementary feedstocks may include brines from desalination, as first proposed in Ferrini et al. (2009) and Mignardi et al. (2011), or oil and gas extraction fluids that present high concentrations of dissolved Ca and Mg, but require alkali additives to balance the solution acidity that results from CO2 injection, besides the removal of Cl buildup in solution. A recent study reports the development of a closed-loop cyclical process to remove chloride anions from brines by ion exchange with hydrotalcites that release hydroxyl anions, sufficiently raising the pH to enable the precipitation of calcium carbonates (Zhang et al., 2020).
Another opportunity that could be further exploited may be represented by mineral or waste materials bearing Mg-phases, which are widely available worldwide. Nevertheless, in order to make their application feasible, new market opportunities for Mg carbonate products should be investigated, besides novel sustainable pathways to enhance the reactivity of Mg-phases that, as highlighted previously, is lower than that of Ca-bearing materials.
Finally, as for many other circular economy processes, in order to favor the deployment of MC products in place of virgin raw materials, governments should provide ways of addressing financial and nonfinancial barriers. For example, due to concerns related to the release of elements of potential environmental concern from alkaline waste materials, such as metals or metalloids, products obtained from these materials have been typically employed only in limited applications under restricted conditions. In this regard, the Green Deal program of the Netherlands, that has established that waste-derived secondary construction materials can only be employed in unrestricted applications, implies on the one hand that more stringent environmental quality parameters should be met, for example, by applying pretreatments, but also that waste-derived materials presenting suitable properties are substantially equivalent to primary raw material. The issuing of end-of-waste criteria, present currently only in some European countries and only for specific waste-derived materials and uses, will certainly help to promote the recycling of secondary construction materials, presenting adequate technical and environmental properties, by clarifying administrative procedures, thus allowing companies to make more resilient business plans. In addition, to promote the use of these materials in private but also public tenders by green public procurement, environmental product declarations deriving from product-based LCAs, that could allow highlighting of the positive implications deriving from the permanent uptake of CO2 in the product as well as the partial substitution of virgin raw materials, should be achieved.
The original contributions presented in the study are included in the article/Supplementary Material; further inquiries can be directed to the corresponding author.
RB: conceptualization, writing, review, and editing. GC: conceptualization, writing, review, and editing.
The authors declare that the research was conducted in the absence of any commercial or financial relationships that could be construed as a potential conflict of interest.
Baciocchi, R., Costa, G., and Zingaretti, D. (2014). “Accelerated Carbonation Processes for Carbon Dioxide Capture, Storage and Utilisation,” in Transformation and Utilization of Carbon Dioxide. Editors B. M. Bhanage, and M. Arai (Springer), 263–299. doi:10.1007/978-3-642-44988-8_11
Beaulieu, E., Goddéris, Y., Donnadieu, Y., Labat, D., and Roelandt, C. (2012). High Sensitivity of the Continental-Weathering Carbon Dioxide Sink to Future Climate Change. Nat. Clim Change 2, 346–349. doi:10.1038/nclimate1419
Benhelal, E., Rashid, M. I., Holt, C., Rayson, M. S., Brent, G., Hook, J. M., et al. (2018). The Utilisation of Feed and Byproducts of Mineral Carbonation Processes as Pozzolanic Cement Replacements. J. Clean. Prod. 186, 499–513. doi:10.1016/j.jclepro.2018.03.076
Benhelal, E., Rashid, M. I., Rayson, M. S., Brent, G. F., Oliver, T., Stockenhuber, M., et al. (2019). Direct Aqueous Carbonation of Heat Activated Serpentine: Discovery of Undesirable Side Reactions Reducing Process Efficiency. Appl. Energ. 242, 1369–1382. doi:10.1016/j.apenergy.2019.03.170
Blue Planet (2021). Available at: www.blueplanet-ltd.com (Accessed May 3, 2021).
Carbon Cure (2021). Available at: www.carboncure.com (Accessed March 27, 2021).
Costa, G., Baciocchi, R., Polettini, A., Pomi, R., Hills, C. D., and Carey, P. J. (2007). Current Status and Perspectives of Accelerated Carbonation Processes on Municipal Waste Combustion Residues. Environ. Monit. Assess. 135, 55–75. doi:10.1007/s10661-007-9704-4
Di Maria, A., Snellings, R., Alaerts, L., Quaghebeur, M., and Van Acker, K. (2020). Environmental Assessment of CO2 Mineralisation for Sustainable Construction Materials. Int. J. Greenhouse Gas Control. 93, 102882. doi:10.1016/j.ijggc.2019.102882
Erlund, R., and Zevenhoven, R. (2019). Thermal Energy Storage (TES) Capacity of a Lab Scale Magnesium Hydro Carbonates/silica Gel System. J. Energ. Storage 25, 100907. doi:10.1016/j.est.2019.100907
Ferrini, V., De Vito, C., and Mignardi, S. (2009). Synthesis of Nesquehonite by Reaction of Gaseous CO2 with Mg Chloride Solution: Its Potential Role in the Sequestration of Carbon Dioxide. J. Hazard. Mater. 168, 832–837. doi:10.1016/j.jhazmat.2009.02.103
Gadikota, G., Matter, J., Kelemen, P., Brady, P. V., and Park, A.-H. A. (2020). Elucidating the Differences in the Carbon Mineralization Behaviors of Calcium and Magnesium Bearing Alumino-Silicates and Magnesium Slicates for CO2 Storage. Fuel, 277–117900. doi:10.1016/j.fuel.2020.117900
Gerdemann, S. J., O'Connor, W. K., Dahlin, D. C., Penner, L. R., and Rush, H. (2007). Ex situ Aqueous Mineral Carbonation. Environ. Sci. Technol. 41, 2587–2593. doi:10.1021/es0619253
Ghouleh, Z., Guthrie, R. I. L., and Shao, Y. (2017). Production of Carbonate Aggregates Using Steel Slag and Carbon Dioxide for Carbon-Negative Concrete. J. CO2 Utilization 18, 125–138. doi:10.1016/j.jcou.2017.01.009
Gislason, S. R., Wolff-Boenisch, D., Stefansson, A., Oelkers, E. H., Gunnlaugsson, E., Sigurdardottir, H., et al. (2010). Mineral Sequestration of Carbon Dioxide in Basalt: A Pre-injection Overview of the CarbFix Project. Int. J. Greenhouse Gas Control. 4, 537–545. doi:10.1016/j.ijggc.2009.11.013
Gunning, P. J., Hills, C. D., and Carey, P. J. (2011). Production of Lightweight Aggregate from Industrial Waste and Carbon Dioxide. Waste Manag. 29, 2722–2728. doi:10.1016/j.wasman.2009.05.021
Hills, C., Tripathi, N., and Carey, P. J. (2020). Mineralization Technology for Carbon Capture, Utilization, and Storage. Front. Energ. Res. 8, 142. doi:10.3389/fenrg.2020.00142
Huang, H., Wang, T., Kolosz, B., Andresen, J., Garcia, S., Fang, M., et al. (2019). Life-cycle Assessment of Emerging CO2 Mineral Carbonation-Cured Concrete Blocks: Comparative Analysis of CO2 Reduction Potential and Optimization of Environmental Impacts. J. Clean. Prod. 241, 118359. doi:10.1016/j.jclepro.2019.118359
Jimoh, O. A., Ariffin, K. S., Hussin, H. B., and Temitope, A. E. (2018). Synthesis of Precipitated Calcium Carbonate: a Review. Carbonates Evaporites 33, 331–346. doi:10.1007/s13146-017-0341-x
Kelemen, P., Benson, S. M., Pilorgé, H., Psarras, P., and Wilcox, J. (2019). An Overview of the Status and Challenges of CO2 in Minerals and Geological Formations. Front. Clim. 1, 9. doi:10.3389/fclim.2019.00009
Kelemen, P. B., and Matter, J. (2008). In situ carbonation of Peridotite for CO2 Storage. Proc. Natl. Acad. Sci. 105, 17295–17300. doi:10.1073/pnas.0805794105
Librandi, P., Nielsen, P., Costa, G., Snellings, R., Quaghebeur, M., and Baciocchi, R. (2019). Mechanical and Environmental Properties of Carbonated Steel Slag Compacts as a Function of Mineralogy and CO2 Uptake. J. CO2 Utilization 33, 201–214. doi:10.1016/j.jcou.2019.05.028
Mac Dowell, N., Fennell, P. S., Shah, N., and Maitland, G. C. (2017). The Role of CO2 Capture and Utilization in Mitigating Climate Change. Nat. Clim Change 7, 243–249. doi:10.1038/nclimate3231
Matter, J. M., Stute, M., Snæbjörnsdottir, S. Ó., Oelkers, E. H., Gislason, S. R., Aradottir, E. S., et al. (2016). Rapid Carbon Mineralization for Permanent Disposal of Anthropogenic Carbon Dioxide Emissions. Science 352, 312–1314. doi:10.1126/science.aad8132
Mattila, H.-P., Hudd, H., and Zevenhoven, R. (2014). Cradle-to-gate Life Cycle Assessment of Precipitated Calcium Carbonate Production from Steel Converter Slag. J. Clean. Prod. 84, 611–618. doi:10.1016/j.jclepro.2014.05.064
Mervine, E. M., Wilson, S. A., Power, I. M., Dipple, G. M., Turvey, C. C., Hamilton, J. L., et al. (2018). Potential for Offsetting Diamond Mine Carbon Emissions through Mineral Carbonation of Processed Kimberlite: an Assessment of De Beers Mine Sites in South Africa and Canada. Miner. Petrol. 112, 755–765. doi:10.1007/s00710-018-0589-4
Mignardi, S., De Vito, C., Ferrini, V., and Martin, R. F. (2011). The Efficiency of CO2 Sequestration via Carbonate Mineralization with Simulated Wastewaters of High Salinity. J. Hazard. Mater. 191, 49–55.
Mission Innovation (2017). Accelerating the Clean Energy Revolution. Carbon Capture Innovation Challenge. Report of the Carbon Capture, Utilization and Storage Experts’ Workshop. Houston (USA). Available at: https://www.energy.gov/fe/downloads/accelerating-breakthrough-innovation-carboncapture-utilization-and-storage (Accessed September 26–28, 2017).
Morone, M., Costa, G., Georgakopoulos, E., Manovic, V., Stendardo, S., and Baciocchi, R. (2017). Granulation-Carbonation Treatment of Alkali Activated Steel Slag for Secondary Aggregates Production. Waste Biomass Valor. 8 (5), 1381–1391. doi:10.1007/s12649-016-9781-0
Morone, M., Costa, G., Polettini, A., Pomi, R., and Baciocchi, R. (2014). Valorization of Steel Slag by a Combined Carbonation and Granulation Treatment. Minerals Eng. 59, 82–90. doi:10.1016/j.mineng.2013.08.009
Naqi, A., and Jang, J. (2019). Recent Progress in Green Cement Technology Utilizing Low-Carbon Emission Fuels and Raw Materials: A Review. Sustainability 11, 537. doi:10.3390/su11020537
NASEM - National Academies of Sciences Engineering and Medicine (2019). Gaseous Carbon Waste Streams Utilization: Status and Research Needs. Washington, DC: The National Academies Press.
Niven, R., Monkman, G. S., and Forgeron, D. (2012). Carbon Dioxide Treatment of Concrete Upstream from Product Mold. US Patent 8845940B2. Halifax, CA: Applicant: Carbon Cure Tecnologies Inc.
Pan, S.-Y., Chang, E. E., and Chiang, P.-C. (2012). CO2 Capture by Accelerated Carbonation of Alkaline Wastes: A Review on its Principles and Applications. Aerosol Air Qual. Res. 12, 770–791. doi:10.4209/aaqr.2012.06.0149
Patel, T. N., Park, A.-H. A., and Banta, S. (2013). Periplasmic Expression of Carbonic Anhydrase inEscherichia Coli: A New Biocatalyst for CO2hydration. Biotechnol. Bioeng. 110, 1865–1873. doi:10.1002/bit.24863
Power, I. M., Harrison, A. L., and Dipple, G. M. (2016). Accelerating Mineral Carbonation Using Carbonic Anhydrase. Environ. Sci. Technol. 50, 2610–2618. doi:10.1021/acs.est.5b04779
Prigiobbe, V., Polettini, A., and Baciocchi, R. (2009). Gas-solid Carbonation Kinetics of Air Pollution Control Residues for CO2 Storage. Chem. Eng. J. 148, 270–278. doi:10.1016/j.cej.2008.08.031
Quaghebeur, M., Nielsen, P., Horckmans, L., and Van Mechelen, D. (2015). Accelerated Carbonation of Steel Slag Compacts: Development of High-Strength Construction Materials. Front. Energy Res. 3, 52. doi:10.3389/fenrg.2015.00052
Realmonte, G., Drouet, L., Gambhir, A., Glynn, J., Hawkes, A., Koberle, A. C., et al. (2019). An Inter-model Assessment of the Role of Direct Air Capture in Deep Mitigation Pathways-. Nat. Commun. 10, 3277. doi:10.1038/s41467-019-10842-5
Renforth, P. (2019). The Negative Emission Potential of Alkaline Materials. Nat. Commun. 10. doi:10.1038/s41467-019-09475-5
Renforth, P., Manning, D. A. C., and Lopez-Capel, E. (2009). Carbonate Precipitation in Artificial Soils as a Sink for Atmospheric Carbon Dioxide. Appl. Geochem. 24, 1757–1764. doi:10.1016/j.apgeochem.2009.05.005
Said, A., Mattila, H. P., Jarvinen, M., and Zevenhoven, R. (2013). Pilot-scale Experimental Work on Carbon Dioxide Sequestration Using Steelmaking Slag. Appl. Energ. 177, 602–611.
Sanna, A., Dri, M., Wang, X. L., Hall, M. R., and Maroto-Valer, M. (2012). Micro-Silica for High-End Application from Carbon Capture and Storage by Mineralisation. Kem 517, 737–744. doi:10.4028/www.scientific.net/kem.517.737
Sanna, A., Uibu, M., Caramanna, G., Kuusik, R., and Maroto-Valer, M. M. (2014). A Review of Mineral Carbonation Technologies to Sequester CO2. Chem. Soc. Rev. 43, 8049–8080. doi:10.1039/c4cs00035h
Santos, R. M., Ling, D., Sarvaramini, A., Guo, M., Elsen, J., Larachi, F., et al. (2012). Stabilization of Basic Oxygen Furnace Slag by Hot-Stage Carbonation Treatment. Chem. Eng. J. 203, 239–250.
Solidia CementTM (2013). Part One of a Two-Part Series Exploring the Chemical Properties and Performance Results of Sustainable Solidia Cement™ and Solidia Concrete™. Available at: www.solidiatech.com (Accessed August 3, 2020).
Teir, S., Eloneva, S., and Zevenhoven, R. (2005). Production of Precipitated Calcium Carbonate from Calcium Silicates and Carbon Dioxide. Energ. Convers. Manage. 46, 2954–2979.
U.S. Geological Survey (2021). Mineral Commodity Summaries. Available at: https://pubs.usgs.gov/periodicals/mcs2021/mcs2021-wollastonite.pdf (Accessed April 21, 2021).
Vinca, A., Rottoli, M., Marangoni, G., and Tavoni, M. (2018). The Role of Carbon Capture and Storage Electricity in Attaining 1.5 and 2 °C. Int. J. Greenhouse Gas Control. 78, 148–159. doi:10.1016/j.ijggc.2018.07.020
IPCC (2018). Global Warming of 1.5 °C.an IPCC Special Report on the Impacts of Global Warming of 1.5°C above Pre-industrial Levels and Related Global Greenhouse Gas Emission Pathways, in The Context of Strengthening the Global Response to the Threat of Climate Change, Sustainable Development, and Efforts to Eradicate Poverty [Masson-Delmotte, V. P. Zhai, H.-O. Pörtner, D. Roberts, J. Skea, P. R. Shuklaet al. (eds.)]. © 2019 Intergovernmental Panel on Climate Change
Wang, X., and Maroto-Valer, M. M. (2011). Dissolution of Serpentine Using Recyclable Ammonium Salts for CO2 Mineral Carbonation. Fuel 90, 1229–1237. doi:10.1016/j.fuel.2010.10.040
Wilson, S. A., Dipple, G. M., Power, I. M., Thom, J. M., Anderson, R. G., Raudsepp, M., et al. (2009). Carbon Dioxide Fixation within Mine Wastes of Ultramafic-Hosted Ore Deposits: Examples from the Clinton Creek and Cassiar Chrysotile Deposits, Canada. Econ. Geology 104, 95–112. doi:10.2113/gsecongeo.104.1.95
Woodall, C. M., McQueen, N., Pilorgé, H., and Wilcox, J. (2019). Utilization of Mineral Carbonation Products: Current State and Potential. Greenhouse Gas Sc.i Technol. 9, 1096–1113. doi:10.1002/ghg.1940
Ye, Z., Abraham, J., Christodoulatos, C., and Prigiobbe, V. (2019). Mineral Carbonation for Carbon Utilization in Microalgae Culture. Energy Fuels 33, 9, 8843–8851. doi:10.1021/acs.energyfuels.9b01232
Zevenhoven, R., Legendre, D., Said, A., and Järvinen, M. (2019). Carbon Dioxide Dissolution and Ammonia Losses in Bubble Columns for Precipitated Calcium Carbonate (PCC) Production. Energy 175, 1121–1129. doi:10.1016/j.energy.2019.03.112
Zevenhoven, R. (2020). Metals Production, CO2 Mineralization and LCA. Metals 10, 342. doi:10.3390/met10030342
Zevenhoven, R., Slotte, M., Koivisto, E., and Erlund, R. (2017). Serpentinite Carbonation Process Routes Using Ammonium Sulfate and Integration in Industry. Energy Technol. 5, 945–954. doi:10.1002/ente.201600702
Zhang, D., Ghouleh, Z., and Shao, Y. (2017). Review on Carbonation Curing of Cement-Based Materials. J. CO2 Utilization 21, 119–131. doi:10.1016/j.jcou.2017.07.003
Keywords: mineral carbonation, aggregates, compacts, precipitated calcium carbonate, curing, CO2 utilization, CO2 storage
Citation: Baciocchi R and Costa G (2021) CO2 Utilization and Long-Term Storage in Useful Mineral Products by Carbonation of Alkaline Feedstocks. Front. Energy Res. 9:592600. doi: 10.3389/fenrg.2021.592600
Received: 07 August 2020; Accepted: 23 April 2021;
Published: 11 May 2021.
Edited by:
Angela Dibenedetto, University of Bari Aldo Moro, ItalyReviewed by:
Sasha Wilson, University of Alberta, CanadaCopyright © 2021 Baciocchi and Costa. This is an open-access article distributed under the terms of the Creative Commons Attribution License (CC BY). The use, distribution or reproduction in other forums is permitted, provided the original author(s) and the copyright owner(s) are credited and that the original publication in this journal is cited, in accordance with accepted academic practice. No use, distribution or reproduction is permitted which does not comply with these terms.
*Correspondence: Renato Baciocchi, YmFjaW9jY2hpQGluZy51bmlyb21hMi5pdA==
Disclaimer: All claims expressed in this article are solely those of the authors and do not necessarily represent those of their affiliated organizations, or those of the publisher, the editors and the reviewers. Any product that may be evaluated in this article or claim that may be made by its manufacturer is not guaranteed or endorsed by the publisher.
Research integrity at Frontiers
Learn more about the work of our research integrity team to safeguard the quality of each article we publish.