- Department of Chemical Engineering, National Institute of Technology Durgapur, Durgapur, India
Biodiesel has been adopted in various countries as an alternative to petro-fuels and has been able to cater to transport sector requirements. A wide range of feedstock can be used for many production approaches, some of which are not cost-effective and are obsolete. Since waste biomass usage is an effective approach for resource recirculation, and edible oils cannot be used as feedstock to avoid straining food resources, the current investigation presents the optimization of biodiesel from raw castor oil using carbonized Mesua ferrea linn (MFL) seed shells as a heterogeneous catalyst after steam activation and H2SO4 doping. Proximate analysis of the oil showed high free fatty acid (FFA) content, which meant that acid catalyst was necessary for fuel production. Characterization of the inert char and acid catalyst showed good physical activation and effective doping. A 4-factor central composite design (CCD) experimental matrix was used for optimizing the acid esterification using methanol. Under optimal conditions, an actual yield of 92% as opposed to 86% predicted yield was observed at 60°C when run for 1.5 h with 7% catalyst under 950 rpm at 70% w/w alcohol concentration. Fuel characterization showed that fuel-grade RCME (Ricinus communis methyl esters) has physico-chemical properties within acceptable ASTM limits for biodiesel. gas chromatography analysis of fuel showed that acid esterification was able to convert the FFAs into methyl esters. The process adopted can thus provide a good way of turning waste biomass into an effective catalyst capable of converting non-edible feedstock like castor oil into biodiesel.
Introduction
The demand for energy has been on the rise since the dawn of the first industrial age starting from 1760. What started as a drive for replacement of hand driven tools with power-driven machines, has only become more sophisticated at an exponential rate with vast technological breakthroughs in major areas of daily life. The industrial revolution served as a Pandora’s Box that led to an unprecedented energy revolution with energy demands ever increasing at a rapid pace as various sectors of our feudal lives are advanced daily. One of the most important of these advancements is the transport sector that connects various parts of a city country or the globe. This sector is the largest energy demanding sector and requires 30.8% of the total worldwide energy produced by oils (Monitoring the application of European union law – annual report 2017). From the current predictions it can be surmised that this will likely increase in the next decade or so. The demand for transportation fuels is being maintained by petroleum based fuels, which has led to steep rise of oil process and will culminate in the exhaustion of these finite fuel reserves, if alternative sources of fuel aren’t sought and commercialized. Biodiesel has been steadily gaining popularity as a lucrative alternative to petro-fuels. Sourced from esterification and/or transesterification of vegetable oils, waste oils, animal tallow and other oil rich sources (Karmakar and Halder, 2019), this is an easily accessible form of renewable fuel with replenishable feedstock, and many countries have already implemented usage of biodiesel or biofuels on a commercial scale (Balat, 2011).
The cultivation of non-edible crops or waste oils also reduces strain on food sources (Pimentel et al., 2009). Castor plant can grow very easily in arid areas and can resist hydric stress, which makes it easy to cultivate either in lands that cannot sustain cultivation of food crops or as a decorative plant in roadsides (Canoira et al., 2010; Dias et al., 2013). Being native to most Asian countries and widely grown in India due to favourable climates, it is a promising non-exhaustive source for biodiesel production. In a relatively recent report by the Financial Express, castor bean output was expected to rise from 10.83 lakh tonnes to 20.36 lakh tonnes, the annual output promising a staggering rise by almost 88% (Kasabe, 2020). With above 40%w/w extraction as noted by us prior to purification and degumming, it can be estimated that the potential of this non-edible oil largely remains untapped uin fuel production and thus cannot be ignored. Nagkesar (Mesua ferrea linn), the national tree of Sri Lanka, is a slow-growing tree naïve to the Indian subcontinent (also known as Indian rose chestnut) where it is exclusively grown for timber. Various parts of this tree also find use in Indian herbal medicines. The seeds are rich in an oil that is commonly used for rural lighting. The seed shells are usually treated as waste and discarded; they hold potential after carbonization to be used as carbon support for catalyst development in biodiesel production (Bora et al., 2018).
For optimization of a particular process, the controlling process parameters as well as the levels for each parameter need to be tested in order to establish the optimal reaction conditions for maximum yield. Optimizing one factor while keeping others constant (OFAT) is no longer used because it is tedious with unnecessary repetitions as well as being ineffective at analysing the obtained results mathematically for accuracy against predicted responses. Here response surface (RSM) guided methods like CCD (central composite design) and BBD (Box-Behnken design) are advantageous in that the statistical analyses can be used in a far more sophisticatedly accurate manner for comprehensible model statistics that depict the experimental accuracy and if any problems exist with the design of experiments (DOE) (Medina-Valtierra et al., 2017; Show et al., 2020).
For the production of fuel grade esters, the feedstock needs to be either esterified using an acid catalyst or transesterified using a base catalyst. Since oils with high free fatty acids (FFAs) cannot be converted using bases owing to risk of saponification and rancidity, esterification is the favoured pathway which progresses rapidly using polar alcohols such as methanol and ethanol (Karmakar et al., 2021). Bora et al. (2018) used MFL seed shells in acid esterification of MFL seed oil for biodiesel production with 96% yield using methanol (Bora et al., 2018). Karmakar et al. (2020) also used carbonized flamboyant pods (Delonix regia) as a heterogeneous carbon support to impregnate H2SO4 for acid esterified biodiesel production from Madhuca indica (mahua) oil using methanol with optimal yield of 97% (Karmakar et al., 2020). In another study, they used a two-step conversion optimized through Taguchi L16 matrices for obtaining biodiesel from karanja (Pongamia pinnata) oil using H2SO4 doped Delonix regia as an acid catalyst with methanol for FFA conversion, and KOH doped Delonix regia as a base catalyst with 2–propanol for biodiesel production. Under optimal conditions, FFA conversion maxed at 99%, while highest biodiesel yield noted was 99% (Karmakar et al., 2020). Thus, acid catalyzed conversion remains one of the most common ways for biodiesel production for high-FFA oils (Hidayat et al., 2015). The use of heterogeneous catalysts is preferred over homogeneous systems due to ease of separation and efficient reusability of the recovered catalyst (Yu et al., 2010).
The reported study discusses biodiesel production from castor oil using methanol. Waste MFL seed shells, carbonized and steam activated for surface modification to enhance adsorptive properties were then doped with H2SO4 to develop a heterogeneous catalyst capable of facilitating esterification of the oil to form an ester rich product. Proximate analysis of the raw oil reveals high FFA content, thereby necessitating acid esterification for ester production (Wan Omar et al., 2009). Activated and sulfonated char were characterized using SEM and BET analyses to check surface and pore modification. With a fixed agitation speed, the parameters used for optimizing production were: reaction temperature, reaction duration, methanol concentration and catalyst concentration. Central composite design (CCD) optimization of reaction parameters and analysis of variance (ANOVA) of obtained results ensured accuracy of developed optimization model. The fuel produced was characterized using standard ASTM test procedures to establish its physico-chemical properties. The fuel was also subjected to GC analysis for identification of esters. The fuel yield shows promise for scale-up and commercialization.
Materials and Procedure
Materials Required
MFL seed shells (collected from Jorhat district, Assam, India) were the raw material chosen to prepare a porous carbon support capable of acceptable H2SO4 impregnation. Commercial grade castor oil was selected as the feedstock to produce biodiesel and purified by heating and filtration before use. For the study, methanol and 2-propanol (99.5%), H2SO4 (98%), KOH pellets (85%), and phenolphthalein as indicator were used. All reagents were obtained from Merck, India. KOH, phenolphthalein and 2-propanol were used for titrimetric analysis of acid value and FFA content. For GC chromatographic analysis used in the confirmation of obtained esters, Supelco 37 FAME mix (Sigma Aldrich) was used, with dicloromethane (99.5%) for sample dilution. Deionized water was obtained from an Arium 611 DI ultrapure water system (Gottingen, Germany).
Catalyst Preparation and Characterization
The MFL seed shells were cleaned thoroughly with tap water and deionized water before being dried using a hot air oven. This was followed by grinding for reduction of size, after which the sample was carbonized in a muffle furnace. The temperature for carbonization was set at 500°C and was performed for 1 h under steady N2 flow (Karmakar et al., 2020). The temperature suitable for carbonization had been previously established by Bora et al. (2018), who had used MFL seed shells to develop a carbonaceous support impregnated with H2SO4 serving as acid catalyst (called “sulfonated char” or SC) for production of biodiesel from MFL oil. For the enhancement of surface properties of the carbonized char, physical activation was performed at 350°C for 1.5 h with steam passed at a pressure of 1.5–2 kg/cm2 (Bora et al., 2018). This resulted in the formation of modified char with enhanced surface properties and porosity, dubbed as “activated char” (AC). In order to prepare the acid catalyst (SC), the AC was mixed with conc. H2SO4 at a ratio of 1:5 w/v and was kept for 10 h on a hotplate magnetic stirrer providing agitation of 550 rpm at 120°C (Karmakar et al., 2020). The char was then washed using water for removing the excess H2SO4 and dried for elimination of water molecules. AC and SC had already been evaluated by Bora et al. (2018)for the successful steam activation and sulfonation. Nevertheless for the present study SEM and BET analyses for the prepared sample (carbon support and catalyst) were repeated to study how their surface and pores were modified.
Proximate Analysis
The corrosiveness of oil is measured using acid number (AN), which is the amount of KOH in mg required to neutralize oil in a solvent, with an end point indicator. The AN of an oil can also be used to elucidate the free fatty acid (FFA) content (ASTM D974) and FFA content helps determine which process is suitable for fuel production using the oil. Along with a phenolphthalein indicator, a known quantity of the oil is dissolved in 2-propanol and the end point is indicated by formation of a faint stable pink colour. Titre value t is the amount of KOH of given strength required for complete neutralization. From this value using Eqs. 1 and 2, the AN and FFA can be calculated:
Here mass of oil is denoted by m, N (normality) is the KOH strength used, t is the titre value, molar weight of KOH = 56.1 and weight of oleic acid (in the oil) = 28.2.
Design of Experiments Using CCD Matrix
In the esterification of castor oil to form biodiesel, the reduction in FFA% is impacted by variations in levels of the process controlling parameters, namely, agitation speed, reaction temperature, catalyst concentration and methanol concentration. Hence, it is imperative that these process parameters be optimized using an experimental matrix that uses varying process conditions as experimental runs which is then used to develop a mathematical model equation that can predict the optimal conditions through individual as well as interactive effects of the considered process conditions. The developed quadratic second order model makes repeat runs with slightly varying process conditions focussed around the center point of each process variable and these repetitions are greatly diminished as the values reach the upper and lower extremes set for optimization. The levels for each variable ranges from the lowest (–α) through a center point (0) to the highest (+α). For the presented study, five levels (designated –α, -1, 0, +1, +α) are tested for each parameter. This has also been summarized in Table 1. The number of required experimental runs N is the summation of 3 types of experiments runs required, F = 2n number of factorial runs (16 for this study), E = 2(n) number of axial runs (8 for this study) and C = nc number of center runs (6 for this study), as is given in Eq. 3:
The obtained values from each experiment were used to check the accuracy of the quadratic regression equation depicting optimal biodiesel yield. Sum of squares (SS) of individual parameters and the model is used to calculate the contribution factor of each parameter to check its influence on yield using Eq. (4). Here SSf = factorial SS value and SST = model SS value. This helps analyze the impact of each reaction parameter on the biodiesel yield.
Experimental Procedure
To esterify the castor oil, a three necked round-bottomed reactor was used. One of the two side necks was equipped with a thermometer which measures the temperature of the reaction mixture, while the other side neck is fitted with a reflux condenser that helps in re-routing the vaporised methanol back into the reactor after cooling, thereby preventing methanol loss. Since during the reaction methanol vapours do not react with the oil and catalyst mixture, the condensation of the alcohol helps maintain the methanol concentration well above the amount required stoichiometrically. The middle neck was used to add reagents. A fixed quantity of the oil and methanol was heated to a stable temperature before addition of the required amount of catalyst. In one of our reported works with castor oil and methanol using acid esterification, reaction duration of 1.5 h was noted to be sufficient, and therefore, it was kept constant for this optimization process. Other reaction parameters such as agitation speed, catalyst concentration, methanol to oil ratio and reaction temperature were varied to design an experimental matrix consisting of unique parametric combinations for each run as shown in Table 2, which were then used to carry out experiments. After the desired reaction duration, the reaction mixture was cooled below 20°C to stop further conversion and then filtered to remove catalyst before distillation of methanol for recovery. Washing the fuel with water ensures the separation of formed water (from esterification as depicted in Figure 1) and impurities as well as any leached catalytic functional groups. A separating funnel is used for this process, with washing repeated till the drained water gives a neutral pH. This further followed by ultracentrifugation of the fuel sample to eliminate traces of impurities. The yield of FAME can then be estimated by a simple titrimetric analysis that measures residual FFA concentration as a direct estimation of conversion of FFAs into FAMEs.
Characterization of Methyl Esters
In order to establish suitability of the obtained product, the fuel must be characterized for its physico-chemical properties in accordance with the standards set by ASTM. Thermal stability is important in estimating risks involved in storage and transportation of the fuel, which is measured in terms of flash and fire point, which indicate the temperatures at which a fuel gives off vapours that are sufficient for a brief spark or a sustained flame upon introduction of a flame respectively. Both properties are tested via a Pensky Martens closed cup apparatus. The fuel should be non-corrosive in nature to avoid degradation of the engine block, and a low acid number (corresponding to low FFA content) is thus desirable. These are determined by titrimetric assay as described in Section 2.2. Oils must not contain moisture which can negatively affect combustion performance, and presence of moisture is easily detectable via cloudiness of the oil sample. The oil to be used as fuel must be of good quality, and this is estimated through determination of cetane number (and corresponding diesel index) as well as aniline point, which is indicative of combustion characteristics of the fuel since the aniline point indicates paraffin content in a fuel, with high paraffins leading to clean combustion. Aniline point is estimated by heating a fixed quantity of aniline and the fuel to a temperature at which the mixture becomes miscible in an aniline point apparatus. For the fuel to be energy efficient, a high calorific value is preferable, and this can be estimated in a bomb calorimeter (Karmakar et al., 2020). Kinematic viscosity (KV) is vital in understanding the flow properties of the fuel, and lower values are preferred which indicate fluidity of the product. The KV of the sample is measured using a Redwood viscometer, in which a fixed amount of the sample (oil or fuel) is filled to be drained through an orifice at the bottom with heating provisions for noting viscosity at a certain temperature (Karmakar et al., 2020). The formation of methyl esters was confirmed through GC (gas chromatography) analysis of the fuel sample. Agilent GC system 7820A was used for the analysis, coupled to a flame ionization detector (FID) and the sample was passed through wax column DB-23 using N2 as carrier gas (Karmakar et al., 2018). The components were identified through a comparison of retention times based on the peaks obtained from a Supelco 37 FAME mix standard (Sigma Aldrich).
Results and Discussion
Analysis of Raw Materials and Fuel Obtained
To study the surface morphology of AC and H2SO4 doped acid catalyst (SC), SEM images were studied (Konwar et al., 2014). They show that activation using steam is successful in modification of the ridges and pores throughout the surface of the MFL carbonaceous support (Figure 2A). It is also observed that sulphonation results in the blockage of the developed pores in the catalyst (Figure 2B) resulting in a smooth appearance of the developed catalyst, which is an indication of effective H2SO4 impregnation (Karmakar et al., 2020). This was further confirmed from BET analysis, which showed that AC and SC have surface areas of 850.11 m2/g and 326.03 m2/g respectively with pore volume of 0.3264 cm3/g and 0.0871 cm3/g respectively. The impregnation of HSO3- had also been confirmed by Bora et. al. in their work with usage of MFL shell developed catalyst in the acid esterification of MFL oil with methanol (Bora et al., 2018). According to their reports, the FT-IR studies revealed peaks at 1,198 cm−1 and 1,120 cm−1, indicating the presence of HSO3− groups and O=S=O structures respectively. They also noted deviations in XRD patterns, with the sulfonated catalyst showing characteristic peak deviations between 2θ 15°–25° and 2θ 30°–40°. In their EDAX analysis, they noted the presence of sulphur at 2.4% and oxygen at 28.33%, owing to the efficient adsorption of HSO3− (Bora et al., 2018). The reported observations in the present study as well as in the work reported by Bora et al. (2018) are congruent to those observed by Karmakar et al. (2021) in their work on blends of castor and karanja oil where the oil blend was subjected to a two-step heterogeneous catalyzed conversion using sequential acid and base doped Delonix regia char, with the acid pre-treated oil blend being subjected to base transesterification with blends of methanol and 2-propanol (Karmakar et al., 2021) as well as in another of their works involving a single step heterogeneous acid catalyzed conversion of mahua oil into biodiesel (Karmakar et al., 2020). Fatty acid composition of the oil has been presented in Table 3. It was noted that the oil has high FFA and kinematic viscosity; hence biodiesel production must proceed through acid esterification method. The oil also has a high calorific value, which indicates that an energy rich fuel can be obtained after esterification. Results from the proximate analysis of castor oil and fuel are summarized in Table 4. Through ASTM characterization tests, it is seen that the fuel properties are within acceptable commercial standards for biodiesel. The product after esterification has very low KV, which is indicative of good flow properties indicating ease in atomization during injection (Olubunmi et al., 2020). Cetane number of the fuel is high enough indicating good quality of the fuel, higher aniline point specifies a paraffin rich fuel, indicating clean burning characteristics. High flash point and fire point of the fuel are indicative of the sample’s thermal stability. The low aniline point indicates a high paraffin content, which corresponds to clean burning of the product. The fuel is also seen to be rich in energy content, as evident from a high calorific value. The AN and residual FFA of the fuel are also low, indicative of negligible corrosiveness, therefore the fuel can be used in engines with no damage to the mechanical parts. GC analysis of the biodiesel obtained shows its ester composition which is summarized in Table 5, while the gas chromatogram for the same is shown in Figure 3.
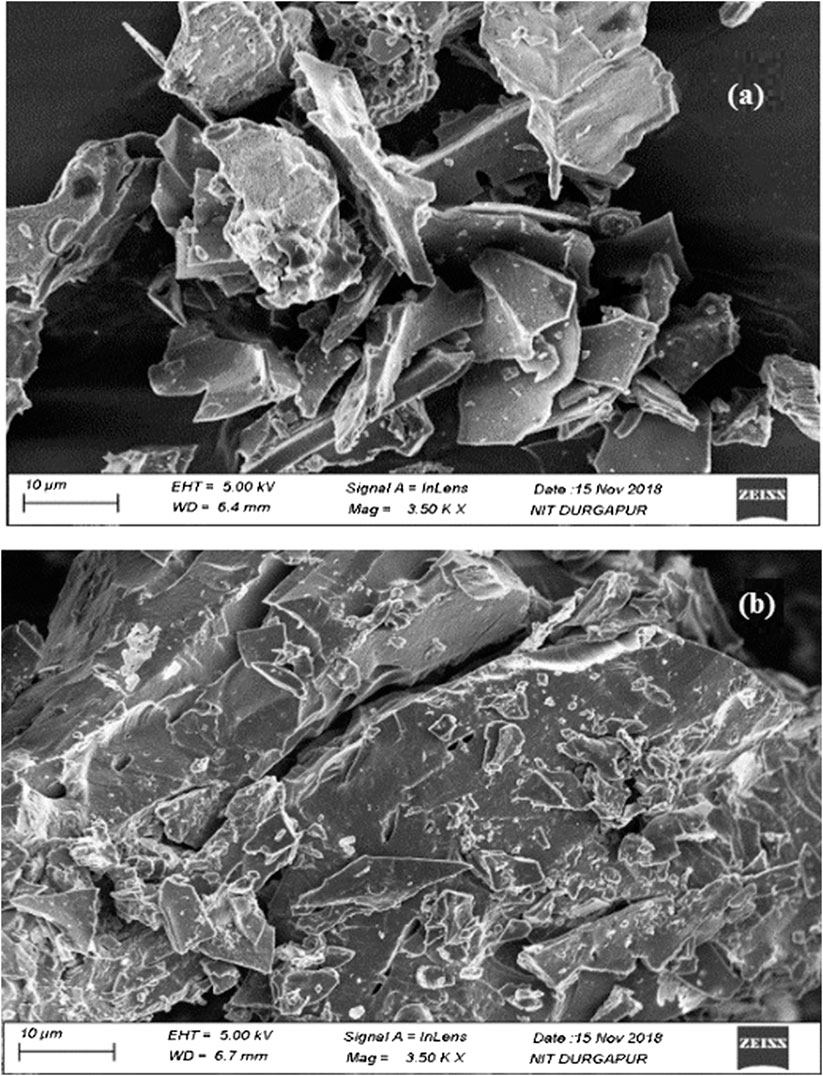
FIGURE 2. SEM image of Mesua ferrea linn (MFL) (A) activated carbon (AC) and (B) sulfonated carbon (SC).
Statistical Analysis Through ANOVA
Through statistical analysis of variance (ANOVA), the results obtained from experimental runs were analyzed and reported in Table 6. Agitation speed is seen to have the lowest impact on the process, while reaction temperature is clearly the most influential parameters evident from the SS values. The regression model developed was seen to have an F-value (Fischer’s exact test) high enough for the model to be significant. Such a high F-value was also assured to be free of errors by a p-value of <0.0001 that indicates that there is only a <0.01% probability that the values in the developed model was obtained due to chance (Mukherjee et al., 2020). From the model comparison statistics and fit statistics it was also noted that the difference between predicted and adjusted R2 values (0.9614 and 0.9827 respectively) is less than 0.2, which indicates good correlation between the experimentally obtained results and the theoretically predicted results, which otherwise would have been indicative of problems with the selected model and the experimentally obtained data. Therefore it was surmised that the chosen model can be used to navigate the design space with accuracy. This is also confirmed by the adequate precision (AP) value of the model (Table 7), noted to be 45.8079, which is much higher than the minimum required value of 4. The AP value is indicative of the signal to noise ratio (SNR), and high AP values indicate that the obtained experimental results are devoid of noise, i.e. accurate (Show et al., 2020).
The final biodiesel (RCME) yield was depicted in the regression model equation as shown in Eq. (5).
Here A, B, C and D refer to reaction temperature, catalyst concentration, methanol concentration and agitation speed respectively. For each term in the equation presented, a “–” sign indicates a detrimental impact on the process relative to the level of the parameter chosen, while a “+” sign denotes a positive impact on yield due to the contribution of a selected level of the process parameter in the final regression equation. The contribution factor of each significant parameter can be summarized as: reaction temperature = 73.35%, catalyst concentration = 1.41%, methanol concentration = 2.73 and agitation speed = 0.19% as shown in Table 8.
Parametric Impact on Yield
Figure 4 shows the mathematically predicted data for the developed model as compared to the experimentally obtained data, and it is seen that there is a good correlation. Hence the developed quadratic model can be considered accurate in optimization of the process variables.
Impact of Reaction Temperature
From Figures 5A,B,C (contour plot) and Figures 6A – 5C (surface plot), it can be seen that the effect of reaction temperature is positive till 60°C, beyond which the yield drops. This finding can be substantiated from the boiling point of methanol (64.7°C), beyond which the alcohol vapours formed in the reaction vessel even under reflux are not sufficiently cooled and transferred back into the reaction mixture, therefore the reaction rate drops. At lower temperatures, the activation energy barrier prevents sufficient reaction between the oil and methanol even in the presence of the catalyst (Alhassan and Uemura, 2016). The findings reported by us are congruent to those obtained by Karmakar et al., (2018) in their works with homogeneous acid esterification of castor oil using methanol as well in their works with castor and karanja oil blend using a two-step heterogeneous Delonix regia catalyzed conversion with methanol and 2-propanol blend (Karmakar et al., 2021). Also, Neeharika et al. (2017), who carried out kinetic studies on the effects of acid catalyst on the esterification of FFAs in jatropha oil found that reaction temperature is greatly influential on the conversion process, playing a crucial part in process kinetics (Neeharika et al., 2017). This was also seen by Karmakar et al. (2021) in their studies on esterification of castor oil using H2SO4 and methanol.
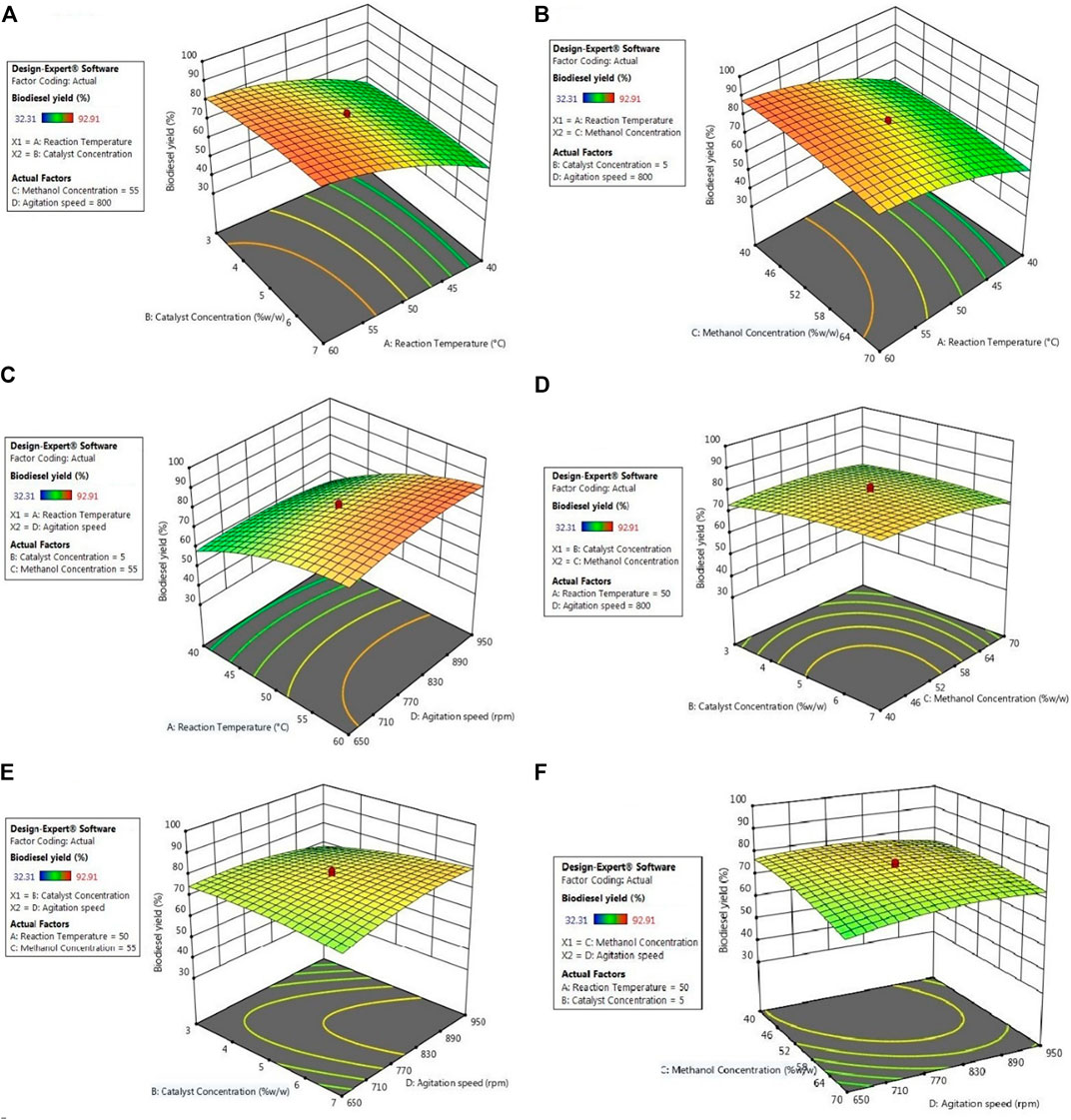
FIGURE 5. Contour plots of interactive impacts on biodiesel yield (A) reaction temperature and catalyst concentration (B) reaction temperature and methanol concentration (C) reaction temperature and agitation speed (D) catalyst concentration and methanol concentration (E) catalyst concentration and agitation speed (F) methanol concentration and agitation speed.
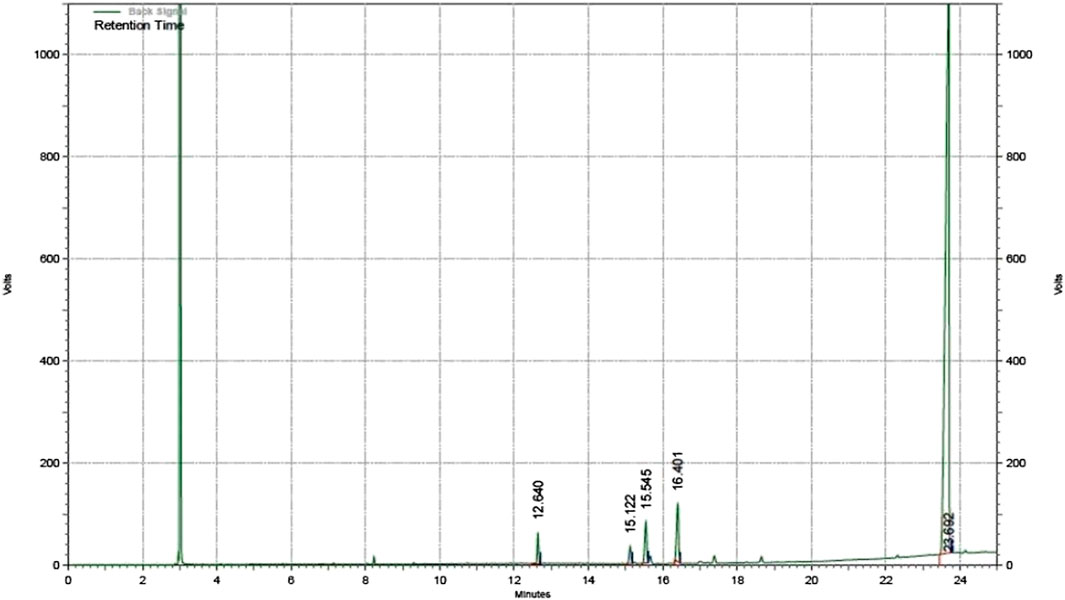
FIGURE 6. Surface plots of interactive impacts on biodiesel yield (A) reaction temperature and catalyst concentration (B) reaction temperature and methanol concentration (C) reaction temperature and agitation speed (D) catalyst concentration and methanol concentration (E) catalyst concentration and agitation speed (F) methanol concentration and agitation speed.
Impact of Catalyst Concentration
Most reactions occurring at room or elevated temperatures cannot proceed at an appreciable rate without the presence of a catalyst. Therefore, the concentration of a catalyst is crucial in obtaining optimal conversion of these catalyzed conversions. In FFA esterification, an acid catalyst is used and hence the sulfonated carbon must be present in an amount high enough for efficient FAME production (Dawodu et al., 2014). For the presented study, SC was maintained between concentrations of 1–9% w/w, out of which maximum conversion was seen at a concentration of 7%. The observations are due to insufficient amounts of catalysts at lower concentrations, an excess of which results in diffusional resistances between the oil and alcohol, since the catalyst is heterogeneous in nature. This can be seen from Figures 5A,D,E (contour plot) as well as Figures 6A,D,E (surface plot). Analogous results had been reported by Banani et al., (2015) on biodiesel synthesis from waste frying oils through acid esterification (Banani et al., 2015), by Goyal et al., (2012) on conversion of high-FFA jatropha oil using RSM (Goyal et al., 2012), by Bora et. al. who used sulfonated waste MFL seed shells for biodiesel synthesis from MFL oil (Bora et al., 2018) and by Karmakar et al. (2020) in their study on two-step conversion of karanja oil (Karmakar et al., 2020), out of which some results noted showed a trivial decline in conversion rates as the temperature exceed the optimum value.
Impact of Methanol Concentration
Polar alcohols are more potent for esterification of the FFAs present in the acidic oils. Since the castor oil used in this study also has a high AN, methanol is the preferred alcohol for conversion of the FFAs into FAME (Jain et al., 2011). The acid esterification step requires 1 mol of methanol for each mole of FFA that is converted into FAME in a reversible reaction. The reversibility of this conversion can be modified by a shift of the reaction equilibrium by adding excess amounts of methanol to favour product formation. Therefore, large amounts of methanol are generally required. This is the case seen in the results obtained from FAME production in the presented study, as 56% w/w of methanol is able to provide the highest FFA conversion under optimal reaction conditions. The effect of methanol concentration is seen in Figures 5B,D,F (contour plot) as well as Figures 5B,D,F (surface plot). It can be reasoned that lower amounts of methanol are insufficient in preventing the backward reaction sufficiently, while beyond optimal levels, the excess methanol will dilute the system resulting in decreased successful interactions between the reactants, resulting in lowered conversion rates. This has also been noted by Ramachandran et al. (2011) in their studies with aluminium hydrogen sulphate as a heterogeneous acid catalyst in the production of biodiesel from mixed waste vegetable oil (Ramachandran et al., 2011), by Neeharika et al. (2017) in their kinetic studies of FFA esterification in jatropha oil (Neeharika et al., 2017), by Karmakar et al. (2020). in their conversion of karanja oil using a two-step heterogeneous catalyzed process (Karmakar et al., 2020), by Dhawane et. al. in their conversion of high-FFA esterification of waste cooking oil using H2SO4 and methanol (Dhawane et al., 2018), by Bora et al. (2018) in their esterification of MFL oil using heterogeneous sulfonated MFL seed shells and methanol (Bora et al., 2018) and by Berrios et al. (2007) in their kinetic studies of the esterification of jatropha oil (Berrios et al., 2007).
Impact of Agitation Speed
For increased interactions between the reactant molecules, the reaction mixture must be agitated at a certain speed. The agitation provided to the reaction mixture results in the mobilization of the reactants and the catalyst, as well as improved heat and mass transfer between the reactants, thereby improving the reaction rate. As seen from Figures 5C,E,F (contour plot) as well as Figures 6C,E,F surface plot), the mixing intensity also affects the reaction, albeit to a lesser extent. It is also seen that increasing the mixing intensity up to 950 rpm improves the FAME yield, beyond which the yield drops. The noted observation can be attributed to the fact that increasing the agitation results in improved heat and mass transfer by eliminating diffusional resistances while also increasing the frequency of productive interactions between the reactants. On the flip side, extreme speeds actually reduce the residence time of the reactant molecules and the catalyst particles that come in close proximity to each other, thereby reducing the time they have to interact and form products. This is close agreement to many other similar works, especially those reported by Aldo et. al. in their works on optimization of biodiesel synthesis from jatropha oil (Aldo et al., 2010), by Karmakar et. al. in various studies involving the heterogeneous catalytic conversion of mahua oil (Karmakar et al., 2020), two step heterogeneopus catalyzed conversion of karanja oil (Karmakar et al., 2020), and H2SO4 catalyzed conversion of castor oil (Karmakar et al., 2018) as well as by Ramachandran et. al. on the production of biodiesel from mixed waste vegetable oil using Al(HSO4)3 (Ramachandran et al., 2011).
Interactive Impacts on Yield
From Figures 5 and 6A,D,E, it is clear that a major improvement in FAME yield is due to the increase in reaction temperature compared to changes in catalyst concentration. This is also the case in Figures 5 and 6A–C, where it is seen that the effect of reaction temperature on the FFA conversion varies to a much larger extent compared to the effects of methanol concentration and agitation speed. In Figures 5D and 6D, changes in catalyst concentration are seen to have a lesser impact on the biodiesel yield compared to methanol concentration, which is inverse of the case seen in Figures 5E and 6E for biodiesel yield variation with respect to changing catalyst concentration and agitation speed shows that agitation peed affects the biodiesel yield to a lesser extent compared to catalyst concentration. Figures 5F and 6F confirm the fact that agitation speed is the least significant of the reaction parameters since it also has a low impact compared to methanol concentration on the biodiesel yield. All of these are also confirmed from Table 8 through the respective contribution factors of the individual parameters.
Catalyst Reusability Studies
The development of a heterogeneous catalyst is a complex process involving significant manual labour, the usage of various equipment for proper support preparation as well as reagents in the catalyst development process. Hence, from an economic point of view, the catalyst support should be structurally stable enough for repeated doping to be efficient while withstanding damage from usage, while the functional group should be doped well enough for the catalyst to remain efficient for a few reuses. For the present study, after filtration of the reaction mixture to separate the catalyst, the latter was washed with acetone to drain the oil and then dried at 80°C in a hot air oven. The dried catalyst was then used for subsequent catalytic conversions under established optimum conditions with varying catalyst concentration to check the efficiency of catalyst under reuse. The results from the catalyst reusability study are reported in Table 9. Summarily, the catalyst showed good catalytic efficiency up to four reuses, after which the drop in biodiesel yield resulting from functional group leaching from the carbon support was deemed significant enough to prompt re-sulfonation as described under Section 2.2. Functional group leaching is mostly due to the agitation provided during the course of the reaction, as well as contact with solvents during the washing stage (Bora et al., 2018; Karmakar et al., 2021). However, after repeating the doping process, the catalyst showed comparable efficiency in catalysis of the esterification process, resulting in comparable biodiesel yield with negligible drop, proving the structural stability of the catalyst support and resistance to mechanical damage from agitation (Karmakar et al., 2020).
Conclusion
Since castor plant is a semi-arid decorative plant with the ability to thrive in tropical climate as well as sustain drought and salinity, it can grow widely in India. Hence the usage of castor oil as feedstock for commercial production of biodiesel. This necessitates the development of a cost-effective process that is able to convert the feedstock into fuel-grade RCME. Also, MFL seed shells are essentially a waste material with the potential to be recycled into an effective precursor material for the development of porous carbon support for catalyst preparation. MFL seed shells proved to be a good catalyst support for the heterogeneous conversion approach, since its surface could be modified by steam activation and then impregnated heavily using H2SO4, as seen in the SEM images and confirmed through BET analysis. In this study a 24 CCD matrix comprised of 30 runs was used to optimize the production process. From the results obtained, the optimum biodiesel yield was 92% under a reaction time of 1.5h, reaction temperature of 60°C, methanol concentration of 70% w/w, agitation speed of 950 rpm and catalyst load of 7 w/w%. Through proximate analysis of the castor oil feedstock it is seen that castor oil with high FFA, calorific value and kinematic viscosity is suitable for ester conversion only through acid catalyzed esterification, while the RCME characterization tests showed that the obtained fuel had very low residual FFA and AV with low kinematic viscosity, high thermal stability and higher calorific value compared to the feedstock. The formation of esters was also confirmed using GC analysis which shows that the process has the potential of commercialization if scaled up appropriately.
Data Availability Statement
The original contributions presented in the study are included in the article/supplementary materials, further inquiries can be directed to the corresponding author/s.
Author Contributions
BK: Conceptualization, methodology, investigation, software, validation. BG: Formal analysis, data curation, writing - original draft preparation. GH: Supervision, project administration, writing - reviewing and editing.
Conflict of Interest
The authors declare that the research was conducted in the absence of any commercial or financial relationships that could be construed as a potential conflict of interest.
Acknowledgments
Sincere gratitude needs to be expressed from the authors to the Department of Chemical Engineering, National Institute of Technology, India for the laboratory facilities provided.
References
Aldo, O., Temu, A. K., Ntalikwa, J. W., and Ogwok, P. (2010). Optimization of biodiesel production from Jatropha oil Int. J. Eng. Res. Afr. 3, 62–73. doi:10.4028/www.scientific.net/JERA.3.62
Alhassan, F. H., and Uemura, Y. (2016). Isopropanolysis of cottonseed oil to biodiesel via potassium hydroxide catalyst Procedia Engineering, 148, 473–478. doi:10.1016/j.proeng.2016.06.475
Balat, M. (2011). Potential alternatives to edible oils for biodiesel production: a review of current work. Energy Conversion and Management. 52, 1479–1492. doi:10.1016/j.enconman.2010.10.011
Banani, R., Youssef, S., Bezzarga, M., and Abderrabba, M. (2015). Waste frying oil with high levels of free fatty acids as one of the prominent sources of biodiesel production. J. Mater. Environ. Sci. 6 (4), 1178–1185.
Berrios, M., Siles, J., Martin, M. A., and Martin, A. (2007). A kinetic study of the esterification of free fatty acids (FFA) in sunflower oil. Fuel. 86, 2383–2388. doi:10.1016/j.fuel.2007.02.002
Bora, A. P., Dhawane, S. H., Anupam, K., and Halder, G. (2018). Biodiesel synthesis from Mesua ferrea oil using waste shell derived carbon catalyst. Renewable Energy. 121, 195–204. doi:10.1016/j.renene.2018.01.036
Canoira, L., García Galeán, J., Alcántara, R., Lapuerta, M., and García-Contreras, R. (2010). Fatty acid methyl esters (FAMEs) from castor oil: production process assessment and synergistic effects in its properties. Renewable Energy. 35, 208–217. doi:10.1016/j.renene.2009.05.006
Dawodu, F. A., Ayodele, O., Xin, J., Zhang, S., and Yan, D. (2014). Effective conversion of non-edible oil with high free fatty acid into biodiesel by sulphonated carbon catalyst. Applied Energy. 114, 819–826. doi:10.1016/j.apenergy.2013.10.004
Dhawane, S. H., Karmakar, B., Ghosh, S., and Halder, G. (2018). Parametric optimisation of biodiesel synthesis from waste cooking oil via Taguchi approach. J. Environ. Chem. Eng. 6, 3971–3980. doi:10.1016/j.jece.2018.05.053
Dias, J. M., Araújo, J. M., Costa, J. F., Alvim-Ferraz, M. C. M., and Almeida, M. F. (2013). Biodiesel production from raw castor oil. Energy. 53, 58–66. doi:10.1016/j.energy.2013.02.018
Goyal, P., Sharma, M. P., and Jain, S. (2012). Optimization of esterification and transesterification of high FFA Jatropha curcas oil using response surface methodology. J. Petrol. Sci. Res. 1, 36–43.
Hidayat, A., Rochmadi, , Wijaya, K., and Budiman, A. (2015). Esterification of free fatty acid on palm fatty acid distillate using activated carbon catalysts generated from coconut shell. Procedia Chem. 16, 365–371. doi:10.1016/j.proche.2015.12.065
Jain, S., Sharma, M. P., and Rajvanshi, S. (2011). Acid base catalyzed transesterification kinetics of waste cooking oil. Fuel Processing Technology, 92, 32–38. doi:10.1016/j.fuproc.2010.08.017
Karmakar, B., and Halder, G. (2019). Progress and future of biodiesel synthesis: advancements in oil extraction and conversion technologies. Energy Conversion and Management, 182, 307–339. doi:10.1016/j.enconman.2018.12.066
Karmakar, B., Dhawane, S. H., and Halder, G. (2018). Optimization of biodiesel production from castor oil by Taguchi design. J. Environ. Chem. Eng. 6, 2684–2695. doi:10.1016/j.jece.2018.04.019 |
Karmakar, B., Ghosh, B., Samanta, S., and Halder, G. (2020). Sulfonated catalytic esterification of Madhuca indica oil using waste Delonix regia: L16 Taguchi optimization and kinetics. Sustainable Energy Technologies and Assessments, 37, 100568. doi:10.1016/j.seta.2019.100568
Karmakar, B., Samanta, S., and Halder, G. (2020). Delonix regia heterogeneous catalyzed two-step biodiesel production from Pongamia pinnata oil using methanol and 2-propanol. J. Cleaner Production. 255, 120313. doi:10.1016/j.jclepro.2020.120313
Karmakar, B., Hossain, A., Jha, B., Sagar, R., and Halder, G. (2021). Factorial optimization of biodiesel synthesis from castor-karanja oil blend with methanol-isopropanol mixture through acid/base doped Delonix regia heterogeneous catalysis. Fuel. 285, 119197. doi:10.1016/j.fuel.2020.119197
Kasabe, N., Castor seed output likely to grow by 88%, (Reported on 25th Feb, 2020; Sourced on 28th Sept., 2020). https://www.financialexpress.com/industry/castor-seed-output-likely-to-grow-by-88/1878127/.
Konwar, L. J., Das, R., Thakur, A. J., Salminen, E., Mäki-Arvela, P., Kumar, N., et al. (2014). Biodiesel production from acid oils using sulfonated carbon catalyst derived from oil-cake waste. J. Mol. Catal. A Chem. 388-389, 167–176. doi:10.1016/j.molcata.2013.09.031
Medina-Valtierra, J., Sánchez-Olmos, L. A., Carrasco-Marin, F., and Sánchez-Cárdenas, M. (2017). Optimization models type Box-Behnken in the obtaining of biodiesel from waste frying oil using a large-acidity carbonaceous catalyst. Int. J. Chem. React. Eng. 15 1–15. doi:10.1515/ijcre-2017-0072.
Monitoring the application of European union law – annual report 2017, European Commision. EU-28 countries factsheet. https://ec.europa.eu/info/sites/info/files/eu28-factsheet-2017_en.pdf.
Mukherjee, A., Karmakar, B., and Halder, G. (2020). Response surface optimized free radical grafting of methyl methacrylate on de-lignified rice straw for evaluating its application potential as flame retardant roofing material. Chem. Eng. J. Adv. 1. doi:10.1016/j.ceja.2020.100007
Neeharika, T. S. V. R., Bhimjiyani, V. H., Dole, B. R., Prasanna Rani, K. N., Karadbhajne, V. Y., and Prasad, R. B. N. (2017). Esterification of free fatty acids present in Jatropha oil: a kinetic study. Industrial Journal of Chemical Technology. 24, 213–217.
Olubunmi, B. E., Karmakar, B., Aderemi, O. M., G., A. U., Auta, M., and Halder, G. (2020). Parametric optimization by Taguchi L9 approach towards biodiesel production from restaurant waste oil using Fe-supported anthill catalyst. J. Environ. Chem. Eng. 8, 104288. doi:10.1016/j.jece.2020.104288
Pimentel, D., Marklein, A., Toth, M. A., Karpoff, M. N., Paul, G. S., McCormack, R., et al. (2009). Food versus biofuels: environmental and economic costs, Hum. Ecol., 37, 1–12. doi:10.1007/s10745-009-9215-8
Ramachandran, K., Sivakumar, P., Suganya, T., and Renganathan, S. (2011). Production of biodiesel from mixed waste vegetable oil using an aluminium hydrogen sulphate as a heterogeneous acid catalyst. Bioresource Tech. 102, 7289–7293. doi:10.1016/j.biortech.2011.04.100
Show, S., Karmakar, B., and Halder, G. (2020). Sorptive uptake of anti-inflammatory drug ibuprofen by waste biomass–derived biochar: experimental and statistical analysis. Biomass Conversion and Biorefinery. https://doi.org/10.1007/s13399-020-00922-8
Wan Omar, W. N. N., Nordin, N., Mohamed, M., and Amin, N. A. S. (2009). A two-step biodiesel production from waste cooking oil: optimization of pre-treatment step. J. Appl. Sci., 9(17), 3098–3103.
Keywords: acid esterification, biodiesel production, heterogeneous catalysis, Mesua ferrea linn, Ricinus communis
Citation: Karmakar B, Ghosh B and Halder G (2020) Sulfonated Mesua ferrea Linn Seed Shell Catalyzed Biodiesel Synthesis From Castor Oil – Response Surface Optimization. Front. Energy Res. 8:576792. doi:10.3389/fenrg.2020.576792
Received: 27 June 2020; Accepted: 08 October 2020;
Published: 30 October 2020.
Edited by:
Eriola Betiku, Obafemi Awolowo University, NigeriaReviewed by:
Nurul Asikin Mijan, National University of Malaysia, MalaysiaAdeyinka Sikiru Yusuff, Afe Babalola University, Nigeria
Copyright © 2020 Karmakar, Ghosh and Halder. This is an open-access article distributed under the terms of the Creative Commons Attribution License (CC BY). The use, distribution or reproduction in other forums is permitted, provided the original author(s) and the copyright owner(s) are credited and that the original publication in this journal is cited, in accordance with accepted academic practice. No use, distribution or reproduction is permitted which does not comply with these terms.
*Correspondence: Gopinath Halder, Z29waW5hdGhoYWxkYXJAZ21haWwuY29t