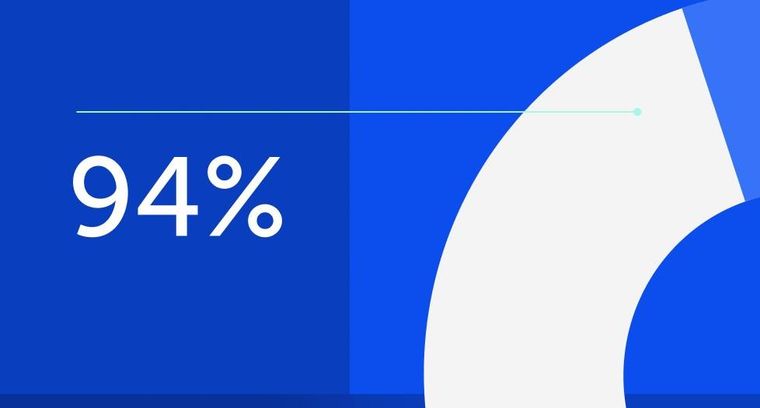
94% of researchers rate our articles as excellent or good
Learn more about the work of our research integrity team to safeguard the quality of each article we publish.
Find out more
ORIGINAL RESEARCH article
Front. Energy Res., 05 October 2020
Sec. Bioenergy and Biofuels
Volume 8 - 2020 | https://doi.org/10.3389/fenrg.2020.575523
This article is part of the Research TopicInnovative Technology and System Integration for Gaseous Biofuels ProductionView all 9 articles
A correction has been applied to this article in:
Expression of Concern: Competing reactions limit production of sugars in hydrothermal hydrolysis of grass silage: an assessment of the effect of temperature on sugar production and parasitic energy demand
Grass represents a major renewable feedstock in temperate climate zones, but its efficient utilization is challenging in biorefineries and advanced biofuels due to its structural recalcitrance. Here hydrothermal hydrolysis (100–180°C, for up to 40 min duration) was investigated to improve sugar yields from grass silage. The optimal conditions (140°C for 20 min duration) showed the highest sugar yield of 0.29 g/g volatile solid (VS) of grass silage. Further increasing the temperature to 180°C favored degradation of sugars (such as glucose, xylose) to by-products (such as furfural, hydroxymethylfurfural). A first-order reaction model confirmed a two-step reaction with the first step hydrolysis and the second step degradation. An energy balance calculation indicated that pre-treatment at 140°C required an energy input of 16.5 kJ/g VS, which could be significantly reduced to 5.1 kJ/g VS through efficient heat recovery. This research assists in understanding of the hydrolysis mechanism and provides a practical solution to produce grass-based sugars for further advanced biofuel and biorefinery applications.
Globally, grass has an irreplaceable role in the agricultural sector; it is primarily utilized for livestock feed. In temperate areas of Europe, grasslands can occupy more than half of the agricultural land (Qi et al., 2017). In Ireland, grassland accounts for approximately 92% of the agricultural land area, with optimal annual grass yields of up to 16 tonnes dry matter per hectare (McEniry et al., 2013). The average annual grassland resource in Ireland has been estimated as approximately 1.7 million tonnes of dry weight available in excess of livestock needs (McEniry et al., 2013). The use of excess grass as a renewable source for bioenergy production (such as biogas, biohydrogen and bioethanol) can contribute to decarbonizing the energy and transport sectors (Batstone and Virdis, 2014; Guragain et al., 2016; Bhatia et al., 2017; Dien et al., 2018). A study by the Sustainable Energy Authority of Ireland (2017) suggests that grass silage resource accounts for 86% of the total renewable gas potential. With respect to the European Union 2020 targets, c. 1% of grassland in Ireland could satisfy the EU renewable energy supply in transport target of 10% allowing for a double credit for advanced biofuels (Wall et al., 2013). Grass-based feedstocks present a significant potential for advanced bioenergy and biorefineries. For example, anaerobic digestion of grass produces biogas (containing c. 60% methane and 40% carbon dioxide), the upgrading of which provides a solution to producing green gas biomethane as an advanced biofuel. Compressed biomethane is technically suitable as transportation fuels for automobiles. However, commercialized biomethane as adopted is primarily sourced from animal slurries and wastes and in some cases Maize (IEA Bioenergy Task 37, 2019). The direct use of grass-based feedstocks in biological processes is not as widely employed and may encounter issues arising from the rigid and complex cellulosic structure of grass, reducing the efficiency of conversion. The question remains as to how to overcome the recalcitrance of grass and improve its subsequent conversion efficiency?
The organic composition of grass primarily constitutes three major types of polymers, including cellulose, hemicellulose and lignin. Cellulose is an unbranched chain of anhydroglucose (C6H10O5) linked by β-glycosidic linkages. Hemicellulose has the capacity to bind strongly to cellulose, while lignin is typically a three-dimensional polymer with branched molecules consisted of phenol units with strong intramolecular bonding (Wang et al., 2017; Ponnusamy et al., 2019). The lignocellulosic structure is bonded together forming a complex structure, making it resistant to hydrolysis. The recalcitrant structure may act as a hurdle to biofuel production. To enhance hydrolysis of lignocellulosic biomass, a range of pre-treatment methods have been established, including physical, biological, chemical, and physicochemical pre-treatments (Ruiz et al., 2013; Behera et al., 2014; Rodriguez et al., 2017). Progress has been made in optimizing biomass pre-treatment methods to achieve higher sugar yields and lower by-product generation.
Physical pre-treatment (such as microwave radiation and ball milling) can reduce biomass particle size and cellulose crystallinity, but they are typically energy-intensive and expensive (Rodriguez et al., 2017; Tsapekos et al., 2017). Biological pre-treatment with cellulose- and lignin-degrading microbes is comparatively energy-saving, nonetheless it requires a high retention time for microbial growth; additionally, some parts of cellulose and hemicellulose are consumed for microbial growth during pre-treatment (Bhatia et al., 2018). Chemical pre-treatments (such as alkaline, acid and hydrothermal) are simple and efficient methods with a high potential for commercialization (Li et al., 2016; Li et al., 2018). Dilute acid pre-treatment can remove a significant amount of hemicellulose and parts of amorphous cellulose. Orozco et al. (2007) investigated acid pre-treatment of grass in a microwave reactor and reported optimal conditions with 2.5% of phosphoric acid at 175°C. The kinetic analysis suggested that microwave acid heating could achieve a high kinetic rate constant at moderate temperatures (Orozco et al., 2007). Alkaline pre-treatments by using ammonia, lime or sodium hydroxide to remove lignin from grass have been reported (Rodriguez et al., 2017). For example, alkaline pre-treatment of grass silage exhibited the best performance at a temperature of 100°C and NaOH concentration of 5% (Xie et al., 2011). Depending on the severity (such as the concentration of acid/alkaline, temperature, and pressure) of the chemical pre-treatment applied, inhibitory by-products, such as furfural, hydroxymethylfurfural and phenolic compounds, have been observed (Jönsson et al., 2013). These inhibitory compounds have been reported as potential inhibitors in the biological processes (Lin et al., 2017; Lin et al., 2018). Therefore, the optimization of pre-treatments should focus on reducing energy demand, addition of chemicals and the generation of inhibitory by-products.
Hydrothermal pre-treatment has received increasing attention for a number of reasons (Ruiz et al., 2013; Zhu et al., 2016; Xiaojian et al., 2017; Brown et al., 2020): 1) less water vapor is generated under hydrothermal conditions, which makes the process more energy efficient; 2) mild pre-treatment conditions reduce the requirement for addition of chemicals; and 3) mild pre-treatment conditions reduce production of inhibitory by-products. In a previous work investigating hydrothermal pre-treatment of Prairie cord grass, the authors found that a 97% yield of glucose was achieved under 210°C for a duration of 10 min (Cybulska et al., 2009). By using CO2 as a catalyst in hydrothermal pre-treatment, a reduction in hemicelluloses of 42% was achieved (Eskicioglu et al., 2017). This reduction in structural integrity further increased the hydrolysis rate by 30% during anaerobic digestion of pretreated sorghum, straws and corn stover (Eskicioglu et al., 2017). Wang et al. demonstrated that hydrothermal temperatures above 190°C significantly destroyed crystalline cellulose and resulted in partial delignification (Wang et al., 2019). These investigations indicated that hydrothermal pre-treatment is a promising method for hydrolysis of grass-based feedstock.
Biomass derived sugars can be further valorized through different technologies in the context of biofuel production and biorefineries. For example, hydrogen, ethanol and volatile fatty acids can be produced through biological acidification (hydrogen fermentation) (Ding et al., 2020). Hydrogen and ethanol have the potential to be used as transportation fuels, whereas volatile fatty acids can be upgraded to platform chemicals in biorefineries. In comparison, it may be more straightforward to covert biomass derived sugars in anaerobic digestion to produce biogas. Biogas or upgraded biogas (biomethane) can be used in a range of sectors such as heat, electricity and transport, thereby significantly contributing to renewable energy targets (Thi et al., 2016).
Use of lignocellulosic biomass to produce biochemicals and biofuels is of great relevance with many commercial opportunities, however, challenges exist. For grass silage to be an effective renewable feedstock, any structural recalcitrance has to be overcome in an efficient way. Although hydrothermal pre-treatment is viewed as a promising technology as stated above, there have been few studies conducted on hydrothermal pre-treatment of grass silage to maximize the yields of reducing sugars. The existing literature is also limited in terms of understanding the competing reaction kinetics between sugar generation and its subsequent degradation. The objectives of this paper are to: 1) Investigate hydrothermal pre-treatment (temperature and time) of grass silage; 2) Develop a kinetic model to describe the competing reactions between sugar generation and decomposition of grass silage; and 3) Determine the energy requirement for hydrothermal hydrolysis with/without heat recovery.
The grass silage used in the experiments was a late-cut perennial ryegrass (Lolium perenne). The late-cut grass typically contained a relatively high lignified fiber content and lower digestibility as compared to early cut grass silage (Wall et al., 2015). This represented relatively high recalcitrance and a challenging feedstock for biofuels and biorefineries. The received silage was dried at 105°C for 24 h to ensure removal of moisture content (Sluiter et al., 2008). The dried grass silage was then pulverized and sieved through a 100-mesh sieve to obtain a particle size of approximately 150 μm. The samples were kept at 4°C in a fridge before use in hydrothermal hydrolysis.
Table 1 presents the ultimate analysis of the dried grass silage. The content of carbon and nitrogen in the grass silage was 41.1 and 1.7% respectively based on total solid (TS); this yields a favorable carbon to nitrogen ratio (C/N) of 24.2 (Chandra et al., 2012). Wall et al. (2013) previously found a C/N of 26.0 for a first cut grass silage with an associated high biodegradability index of 0.90 achieved in batch anaerobic digestion trials. The energy content of late cut grass silage was obtained as 16.3 kJ/g TS or 17.4 kJ/g volatile solid (VS), which is comparable with the energy content of carbohydrate (for instance the energy content of glucose = 15.6 kJ/g). The content of cellulose, hemicellulose, and lignin in the untreated grass silage was previously measured as 31.3, 15.1, and 27.9%, respectively (Deng et al., 2019).
The hydrothermal hydrolysis of grass silage was performed in a batch reactor (500 ml). The hydrolysis trials were conducted for 20 min at 100, 140, and 180°C. Our previous studies have demonstrated that the optimal pre-treatment conditions for a wide range of feedstocks (such as seaweed, cassava residue and food waste) were in processing temperatures of 135–140°C and times of 15–20 min (Ding et al., 2017; Deng et al., 2019; Lin et al., 2019). When performing steam acid pre-treatment, the optimal condition was achieved at 135°C for 15 min with a total reducing sugar yield of 0.33 g/g VS of grass silage (Deng et al., 2019). Similarly, the suggested optimal hydrothermal pre-treatment condition for food waste was 140°C for 20 min (Ding et al., 2017). Therefore, the present study investigated the temperature range from 100 to 180°C.
In each run, 7.5 g VS of silage was fed into the batch reactor; 250 ml dilute sulfuric acid (1.0% v/v) was subsequently added. The pre-treatment time was measured precisely for 20 min, starting from when the solution in the reactor reached the target temperatures. The external heaters surrounding the reactor walls are able to provide rapid and uniform heating and temperature control. The heater used on each reactor produces heating rates up to 15°C/min. The reactor after the hydrolysis trails was subjected to air cooling to room temperature of approximately 25°C.
The analysis of C, H, and N of samples was performed using an elemental analyzer. The oxygen content was determined as the remaining content (not accounted for by C, H, and N) of VS in grass silage. The yield of total reducing sugars from grass silage after hydrothermal hydrolysis was measured by the 3,5-dinitrosalicylic (DNS) acid method with glucose as a standard (Miller, 1959). Typically, 1 ml of the sample and 2 ml of DNS solution were added in a test tube. The mixed solution was then placed in boiling water for 5 min allowing for a complete reaction. The tube was then flushed with water to cool down to room temperature. The absorbance of the derived solution was subsequently measured with a spectrophotometer at 540 nm. Glucose was used to develop a standard curve for further determination of the total reducing sugars concentration.
Typical monosaccharic sugars derived from grass hydrolysis include glucose, xylose, arabinose and galactose. The concentration of each was measured on a high-performance liquid chromatography (HPLC) system (Agilent 1200, United States), which is equipped with a refractive index detector and an Aminex HPX-87P column (Bio-Rad, United States) at 80°C with H2O as mobile phase at 0.6 ml/min. In addition to the presence of sugars, several degradation products, such as furfural and hydroxymethylfurfural, were also found in the hydrolysates. The concentration of furfural and hydroxymethylfurfural was measured on an HPLC system using an ultraviolet detector and an Aminex HPX-87H column (Bio-Rad, United States) at 65°C with 0.005 N H2SO4 as mobile phase at 0.5 ml/min. The above analyses were conducted in duplicate, and the average values were reported.
The organic components of grass silage may decompose into a variety of products, including for reducing sugars, by-products and degradation products during hydrolysis. The complexity of hydrolysis arises from the reactions between two phases, namely the solid substrate and liquid solution. The reaction rate of hydrolysis depends on several variables, such as substrate concentration, substrate composition, temperature and time. To simplify the process, the following considerations and assumptions have been considered: 1) The composition of grass silage is considered a lignocellulosic matrix, assuming no interactions occur between the fractions of cellulose, hemicellulose and lignin. This matrix can be hydrolyzed into reducing sugars, which are further decomposed into degradation products; 2) The overall reactions of hydrolysis and degradation are irreversible and consecutive; and 3) The formation of other intermediates and by-products (such as oligomers, amino acids) are not considered. The simplified process of grass hydrolysis is outlined in Eq. 1, in which k1 and k2 are the constants of formation and decomposition rate of reducing sugars respectively.
Assuming that each reaction is an irreversible first-order reaction, the model presented above can be described through the following differential equations:
where rG is grass degradation rate (g/L/min), [G] is the grass concentration (g/L), k1 is the rate constant for reducing sugars production (min−1), and t is the reaction time (min).
where rR is the reducing sugar production rate (g/L/min), [R] is the reducing sugar concentration (g/L), k2 is the rate constant for degradation products production (min−1). After integration with Eq. 2, the dependence of grass concentration on time is obtained as:
where [G]0 is the initial grass concentration (g/L). By combining Eq. 4 with Eq. 3, the following first-order linear differential equation can be derived:
Taking into account the following boundary condition: when t = 0, [R] = 0, the dependence of reducing sugar concentration on time is obtaining by solving Eq. 5:
The temperature dependence of the rate constants can be described by the Arrhenius equation:
where k is the rate constant (min−1), Ea is the apparent activation energy (kJ/mol), A is the pre-exponential factor (min−1), R is the universal gas constant (8.314 J/mol/K), and T is the reaction temperature (K). By plotting the logarithm of the rate constant against the reciprocal temperature, the results can be illustrated in the form of a straight line. By means of the Arrhenius plot (Eq. 8), the activation energy as well as the pre-exponential factor can be determined:
To assess the energy required for hydrothermal acid hydrolysis, the overall process heat for water, sulfuric acid and grass silage was calculated. Considering that the specific heat of sulfuric acid and grass silage do not vary significantly with temperature, the overall heat requirement for hydrothermal hydrolysis of grass silage can be provided by the following Eq. 9.
where, m and Cp represents the mass and specific heat of water (w), grass silage (g) and sulfuric acid (a) respectively. Texp is the experimental temperatures (namely 100, 140, and 180°C) and T0 is the ambient temperature assumed as 25°C. The mass of sulfuric acid and water were evaluated based on their respective density and volume at the beginning of the experiment. The specific heat of grass silage based on its dry weight is 1.89 kJ/kg K (Borreani et al., 2018), while that of sulfuric acid is 1.34 kJ/kg K (Mafe et al., 2015). The variation of the specific heat of water with temperature is given by the following Eq. 10 (valid between 0.01 and 200°C) (Mafe et al., 2015).
Hydrothermal pre-treatment has become a promising technique that has been widely applied for biomass pre-treatment to achieve selective fractionation of major components (cellulose, hemicellulose, and lignin) with high sugar recovery in subsequent enzymatic hydrolysis. The effectiveness of hydrothermal pre-treatment is dependent on several process factors such as pre-treatment temperature, time, and type/amount of solvent used. The combined effect of hydrothermal reaction temperature and time can be quantified by the severity factor as defined in a previous study (Overend et al., 1987). Typically, the decomposition rate of biomass feedstock increases with increase in treatment severity. Some representative solvent systems have been investigated including water (Ding et al., 2017; Lin et al., 2019), water/acid (Cheng et al., 2019), water/CO2 (Eskicioglu et al., 2017), water/organic acids (Lai et al., 2017), and deep eutectic salts (Yu Q. et al., 2018). When water is used as the solvent, hydrothermal pre-treatment generally requires a higher process severity (4.0 or higher) to achieve effective removal of hemicellulose and structural modification of lignin. In comparison, the addition of acid with low pH values can significantly enhance hemicellulose removal with a lower process severity (<2.0). Novel solvents such as ionic liquids and deep eutectic salts have the advantages of 1) high dissolution for specific biomass compositions, and 2) conducting treatment under mild conditions (<100°C).
The hydrolysis of cellulose and hemicellulose in grass silage to monomeric sugars involves multiple reaction steps, which are simplified in Figure 1. Hydrolysis, the cleavage of chemical bonds in the presence of water, is a reaction, which breaks down cellulose to glucose and hemicellulose to xylose. This is typically the first step in a bioprocess for biofuel/biochemical production. Hydrothermal conditions under high temperature and pressure favor the hydrolysis reaction. Acid (such as sulfuric acid, metal salts, heterogeneous acid) can act as the catalyst that accelerates the hydrolysis reaction (Yuan and Macquarrie, 2015). Deng et al. (2019) showed that after steam acid pre-treatment with 2% H2SO4 at 135°C for 15 min, hemicellulose was completely decomposed, while almost half of cellulose in raw grass silage was removed during the pre-treatment. Hydrothermal pre-treatment under 240°C is efficient in dissolving hemicellulose without removing the majority of the cellulose composition (Li et al., 2017). The modification of lignocellulosic structure increases the accessibility of fermentable cellulose and the subsequent biofuel/chemical production from the substrates. Kang et al. (2020) revealed that as the pre-treatment severity increased to approximately 4.0, the degradation of xylan was 58.0%; this further increased to almost 100% when the temperature increased to 200°C with the severity factor over 4.2. A drawback of an acidic environment is that various by-products (such as hydroxymethylfurfural and furfural) can also be generated, especially with high acid concentrations and process temperatures (Toftgaard Pedersen et al., 2015).
Figure 1. Proposed pathways of hydrolysis of lignocellulosic biomass. Reused with permission from reference Girisuta et al. (2013) Copyright (2013) Chemical Engineering Journal, Elsevier Co.
Figure 2 presents the effect of hydrothermal temperature on the production of total reducing sugars from grass silage. The total sugars yield after hydrothermal hydrolysis was quantified using the DNS method (Miller, 1959), by which the amount of reducing sugars (including all monosaccharides, along with some disaccharides, oligosaccharides, and polysaccharides) can be measured. The initial concentration of grass silage for hydrolysis experimentation was 30.0 g VS/L (in a solution of 1% sulfuric acid). When the hydrothermal temperature was 100°C, the yield of total reducing sugars increased with pre-treatment time, leading to the highest yield of 2.2 g/L at 40 min. The reducing sugars yield of grass silage at 140°C rapidly increased to 5.4 g/L in the first 2 min, indicating that the hydrothermal acid pre-treatment was efficient for decomposing polysaccharides into monosaccharides. The yield of total reducing sugars peaked at 20 min with a value of 8.8 g/L; further increasing the pre-treatment time to 40 min resulted in a decrease in reducing sugar yield to 5.5 g/L. The observed decrease was due to the undesirable degradation of sugars to by-products (such as furfural and hydroxymethylfurfural). The reducing sugars yield at 180°C showed a similar trend to that achieved at 140°C. However, the hydrothermal temperature at 180°C significantly reduced the highest total sugar yield to 4.6 g/L at 20 min. This result suggests that the high temperature at 180°C favored the production of by-products instead of sugars. Kang et al. revealed that the liquid fraction of liquid hot water pretreated grass (hybrid Pennisetum) contained primarily oligosaccharides, monosaccharides (such as glucose, xylose and arabinose) and organic acids (acetic acid, formic acid and levulinic acid) (Kang et al., 2020); the authors claimed that the majority of those components were derived from the hemicellulose composition in grass. When increasing the pre-treatment temperature from 160 to 180°C, the arabinose yield significantly increased (3-fold) (Kang et al., 2020). However, the glucose yield decreased by 60.6%, suggesting the occurrence of a glucose degradation reaction (for example from glucose to hydroxymethylfurfural) (Kang et al., 2020). Furthermore, with elevated temperatures in pre-treatment, some monosugars can react with amino acids, forming nitrogen-containing Maillard compounds, such as 1-azido-4-dimethylaminobenzene (Lin et al., 2018), thereby resulting in a decreased sugar yield.
Figure 2. The yield of total reducing sugars from grass silage under different hydrothermal temperatures.
The major organic components of grass silage comprise cellulose and hemicellulose, both of which can be hydrolyzed to reducing sugars. Cellulose (C6H10O5)n consists of a linear chain of many hundreds of β-(1, 4)-glycosidic bonds linking glucose units (Wang et al., 2017). Hemicellulose (C5H8O4)n is a smaller branched carbohydrate which can be made of different monosaccharides, that contain pentoses (xylose and arabinose), and hexoses (mannose, glucose, and galactose) (Wang et al., 2017). While cellulose is crystalline and resistant to hydrolysis; hemicellulose has an amorphous structure with weak strength. Both cellulose and hemicellulose can be hydrolyzed in dilute acid into monosaccharides. The following reactions describe the production of glucose (C6H12O6) and xylose (C5H10O5) from cellulose and hemicellulose, respectively. and 12 are the favored hydrolysis reactions that directly lead to the production of reducing sugars.
Figure 3 shows the composition of monosaccharic sugars from grass silage under different hydrothermal temperatures (using the HPLC method). This suggests that xylose and arabinose are more likely produced at lower temperature hydrolysis, while glucose is predominately produced at higher temperatures due to cellulose hydrolysis. When grass silage was pretreated at 100°C for 20 min, the yield of monosaccharic sugars was 0.92 g/L, in which arabinose and xylose accounted for 95.6% of total sugar yield. When the hydrothermal temperature increased to 140°C, the yield of monosaccharic sugars increased to 3.2 g/L. Specifically, the xylose yield increased from 0.53 to 2.36 g/L, which was due to the dramatic hydrolysis of hemicellulose (Figure 1). When the hydrothermal temperature increased to 180°C, the xylose yield greatly decreased to 0.13 g/L, while the glucose yield significantly increased to 3.19 g/L. The decrease in xylose yield indicates that a higher temperature favored the degradation of xylose to by-products (Figure 1). However, the increase in glucose yield suggested that a higher temperature resulted in deep hydrolysis of cellulose to glucose (Figure 1). It is noteworthy that the yield of total monosaccharic sugars measured by the HPLC method (Figure 3) was much lower than that measured by the DNS method (Figure 2). This is due to the fact that the DNS method took into account all monosaccharides, some disaccharides, oligosaccharides, and polysaccharides.
Figure 3. Composition of monosaccharic sugars from grass silage under different hydrothermal temperatures.
Depending on the pre-treatment severity of the process, cellulose and hemicellulose in biomass are hydrolyzed to monomer sugars, which can be further decomposed to a variety of inhibitory compounds, such as furfural, hydroxymethylfurfural, levulinic acid, and formic acid (Guragain et al., 2016). Phenolic compounds derived from lignin can also be generated during pre-treatment (Monlau et al., 2014). Figure 4 presents the composition of sugar-derived degradation products under different hydrothermal temperatures. Furan derivatives (namely furfural and hydroxymethylfurfural) were detected as the major sugar-derived by-products. At the hydrothermal temperatures of 100 and 140°C, the concentration of furfural slightly increased from 4.4 to 16.8 mg/L, while no significant amount of hydroxymethylfurfural was detected. It was obvious that high temperatures benefited the sugar dehydration process, leading to higher furfural and hydroxymethylfurfural yields. Redding et al. found that glucose was more stable than xylose under mild acid pre-treatment conditions (0.9% sulfuric acid, 120–140°C for 5–30 min); this explained that only less than 10 mg furans/g raw biomass was generated, in which furfural and hydroxymethylfurfural accounted for around 90 and 10%, respectively (Redding et al., 2011). Hydroxymethylfurfural comes from cellulose which is harder to degrade (and as such needs higher temperatures) than hemicellulose which degrades to furfural. The low concentrations of furans suggest that low temperatures do not favor the production of degradation by-products, indicating the hydrolysis reaction was dominant during hydrothermal hydrolysis. Notably, when the hydrothermal temperature was 180°C, a considerable amount of furan derivatives was produced; the concentration of furfural and hydroxymethylfurfural was 157.2 and 270.0 mg/L, respectively. A high hydrothermal temperature inevitably resulted in further degradation of sugars with furans as by-products. Batista et al. observed that low concentrations of furans were obtained from sugarcane straw at pre-treatment temperature of 170°C, but at 220°C more furans were detected in the liquid phase (Batista et al., 2019). When the pre-treatment temperature increased to 180°C, the furans yield significantly increased to 50 mg/g raw biomass (Redding et al., 2011), this was in agreement with the trend that higher temperatures resulted in higher sugar loss.
Figure 4. Composition of sugar-derived degradation products under different hydrothermal temperatures.
Hydroxymethylfurfural may be obtained from 6-carbon sugars (such as glucose) undergoing acid catalyzed poly-dehydration (Teong et al., 2014; Yu and Tsang, 2017; Yu I. K. M. et al., 2018). Furfural is largely derived from 5-carbon sugars, particularly xylose, through the acid-catalyzed dehydration. The reactions in relation to the formation of hydroxymethylfurfural (C6H6O3) and furfural (C5H4O2) are described in the following equations, which are considered the competing reactions during hydrothermal hydrolysis. The competition between the hydrolysis reactions ( and 12) and degradation reactions ( and 14) need to be balanced to achieve a high reducing sugar yield.
The first-order reaction model was used to describe the competitive reaction kinetics for sugar production from grass silage. The modeling curves and experimental data under different hydrothermal temperatures (100, 140, and 180°C) are presented in Figure 5. The hydrothermal temperature acted as a significant factor that affected sugar production. The theoretical curve of sugar production at 100°C showed a satisfactory fit to the experimental data (R2 = 0.98), showing that the yield of reducing sugar increased with pre-treatment time from 0 to 40 min. This result indicates that low pre-treatment temperatures led to a relatively long time to achieve a higher sugar yield. Increasing the hydrothermal temperature significantly promoted the production of reducing sugars. The modeling curves at both 140°C (R2 = 0.68) and 180°C (R2 = 0.97) exhibited a one-peak trend over pre-treatment time confirming a two-step reaction: first step hydrolysis and second step further degradation. The peak time in relation to the highest sugar yield under 140 and 180°C conditions was shortened to approximately 15 min.
Figure 5. Experimental data and calculated curves for reducing sugar yields from grass silage by hydrothermal hydrolysis at various temperatures.
Table 2 shows the reaction rate constants of sugar production and decomposition by fitting the experimental data to Eq. 1. As the hydrothermal temperature increased from 100 to 140°C, the sugar production rate k1 increased from 0.0017 to 0.0512 min−1. When the pre-treatment temperature was 180°C, the sugar production rate k1 decreased to 0.0296 min−1, whereas the sugar decomposition rate increased to 0.1091 min−1. The kinetic calculation clearly shows that there is a competing relationship between the hydrolysis reaction and further degradation reaction. In the lower temperature range between 100 and 140°C, increasing temperature favors the hydrolysis reaction. In comparison, in the higher temperature range between 140 and 180°C, increasing temperature favors the further degradation reaction. A similar trend was noticed in previous studies using different types of feedstocks, such as rice straw, bamboo, and organic wastes (Zhu et al., 2011; Lin et al., 2015; Mohan et al., 2015). When investigating subcritical water hydrolysis of rice straw, the highest reaction rate (k1) of 0.063 was achieved at 280°C; further increasing the temperature led to generation of more degradation products (Lin et al., 2015). Girisuta et al. (2013) found that the decomposition reaction of glucose to undesired by-products (such as humins) has a high activation energy (161.41 kJ/mol), suggesting that temperature has a significant effect on this reaction. Therefore, undertaking the hydrolysis reaction at high temperatures would favor the formation of by-products from glucose.
Table 2. Reaction rate constants for reducing sugar production and decomposition at different temperatures.
The pre-exponential factors and activation energies for the production and decomposition reactions were calculated and presented in Table 3. It can be seen that the apparent activation energy (5.89 kJ/mol) for the hydrolysis reaction was higher than the one (1.85 kJ/mol) for the decomposition reaction, indicating that the hydrolysis reaction is more difficult to take place than the decomposition reaction in the temperature range used in the experiments. This also suggests that temperature has a more significant effect on this reaction. The result is consistent with the observed biomass hydrolysis under acidic environment (such as formic acid and sulfuric acid) (Girisuta et al., 2013; Kupiainen et al., 2014).
Table 3. Activation energies (Ea) and pre-exponential factors (A) for reducing sugar production and decomposition.
The kinetic results can assist in the understanding of grass silage hydrolysis in hydrothermal pre-treatment. The stability of grass silage and its derived sugars against further degradation is highly dependent on the reaction conditions. However, a disadvantage of the first-order models lies in the limited understanding of the reaction network and mechanisms. Therein, the requirement for sophisticated analytical equipment to shed light on the key intermediates of reaction, remains a main challenge for the application of kinetic modeling. Nonetheless, this study provides a practical solution for the production of sugars, which are a valuable platform precursor for biofuels and biorefineries.
Figure 6 presents the energy consumption for hydrothermal hydrolysis of grass silage at different temperatures. Pre-treatments at 100, 140, and 180°C result in energy consumption of 10.7, 16.5, and 22.3 kJ/g VS of grass silage, respectively. The energy requirement for hydrothermal hydrolysis includes heating of water, sulfuric acid, and grass silage. Of this, over 97.5% of energy consumption was accounted for heating of water under all three pre-treatment conditions. This result indicated that pre-treatment is a significant factor governing the amount of energy consumed in heating especially for wet substrates. Similarly, Mafe et al. (2015) reported that the main energy consumption in acid pre-treatment was associated with water heating. With increasing pre-treatment temperature, an almost linear increase in energy requirement was observed. As a result, the energy needed for hydrolysis at 180°C (22.3 kJ/g VS of grass silage) was higher than the energy content within grass silage (17.4 kJ/g VS). This negates the rationale for pre-treatment at high temperatures, unless efficient downstream heat recovery is conducted. It is inevitable that there will be some form of heat loss. However, the heat loss has been proven to be marginal as compared to the total heating energy; for example, Mafe et al. demonstrated that the heat loss during acid pre-treatment (130°C for 25 min) accounted for only 0.2% of the heating energy required for the whole process (Mafe et al., 2015).
Figure 6. Specific energy requirement for hydrothermal hydrolysis of grass silage with/without heat recovery.
Heat recovery after hydrolysis presents a valuable opportunity to enhance the overall process efficiency. Considering that heating of water accounts for the majority of the energy input in hydrolysis, the recovery of heat from water was considered as the primary source of energy recovery. The recovered energy could be utilized in further processing within a biofuel or biorefinery system or may be utilized in a district heating system. The potential heat recovery was evaluated with the assumption that the hydrolysates at pre-treatment temperatures (namely 100, 140, and 180°C) were cooled down to 50°C with a heat transfer efficiency of 90%. Therefore, the net specific energy required per gram of grass silage (VS basis) for hydrolysis following heat recovery can be observed in Figure 6. Unlike the ascending trend without heat recovery, the recovery of heat under different hydrothermal temperatures resulted in a much lower specific energy requirement, ranging from 4.4 to 5.8 kJ/g VS of grass silage. Indeed, following heat recovery, the net specific energy requirement was similar irrespective of the temperature of hydrolysis. Nonetheless, a significant improvement in the overall energy performance of the system can be achieved. The sugar yield per unit energy expended was the highest at the hydrothermal temperature of 140°C (0.23 g sugar/kJ). Increasing the temperature resulted in a lower value of 0.11 g sugar/kJ. Overall in terms of the parameters of maximum reducing sugar yield and specific sugar yield per energy demand, the pre-treatment at 140°C for 20 min is suggested for further applications in advanced biofuels and biorefineries.
To overcome the recalcitrance of grass silage, hydrothermal hydrolysis was assessed in order to optimize sugar production. The sugar degradation reaction competes with the hydrolysis reaction, and therefore limits total sugar yield. The first-order model suggested that at lower temperatures (100–140°C), increasing temperature favors the hydrolysis reaction, while at higher temperatures (140–180°C), increasing temperature favors further degradation reaction. Heat recovery could significantly reduce energy required from 16.5 kJ/g VS (140°C without heat recovery) to 5.1 kJ/g VS. This study furthers the understanding of optimizing grass hydrolysis for future grass biorefineries.
The raw data supporting the conclusions of this article will be made available by the authors, without undue reservation.
RL designed and conducted the experiments, performed analyses, interpreted data, and drafted the manuscript. CD contributed to data interpretation and edited the manuscript. KR designed the graphical abstract and edited the manuscript. AB performed the energy analysis of the pre-treatment. XK contributed to data interpretation and edited the manuscript. JM provided funding and laboratory facilities, edited the manuscript and approved the final manuscript.
The authors thank the European Union’s Horizon 2020 research and innovation program of Marie Skłodowska-Curie Grant (No. 797259), the Environmental Protection Agency, Ireland (2018-RE-MS-13), Sustainable Energy Authority, Ireland (RDD/00454), and the Science Foundation, Ireland (SFI) through the MaREI Center for Energy, Climate and Marine under Grant No. 12/RC/2302_P2 and 16/SP/3829.
The authors declare that the research was conducted in the absence of any commercial or financial relationships that could be construed as a potential conflict of interest.
Batista, G., Souza, R. B. A., Pratto, B., dos Santos-Rocha, M. S. R., and Cruz, A. J. G. (2019). Effect of severity factor on the hydrothermal pretreatment of sugarcane straw. Bioresour. Technol. 275, 321–327. doi:10.1016/j.biortech.2018.12.073
Batstone, D. J., and Virdis, B. (2014). The role of anaerobic digestion in the emerging energy economy. Curr. Opin. Biotechnol. 27 (Suppl. C), 142–149. doi:10.1016/j.copbio.2014.01.013
Behera, S., Arora, R., Nandhagopal, N., and Kumar, S. (2014). Importance of chemical pretreatment for bioconversion of lignocellulosic biomass. Renew. Sustain. Energy Rev. 36, 91–106. doi:10.1016/j.rser.2014.04.047
Bhatia, S. K., Joo, H.-S., and Yang, Y.-H. (2018). Biowaste-to-bioenergy using biological methods–a mini-review. Energy Convers. Manag. 177, 640–660. doi:10.1016/j.enconman.2018.09.090
Bhatia, S. K., Kim, S.-H., Yoon, J.-J., and Yang, Y.-H. (2017). Current status and strategies for second generation biofuel production using microbial systems. Energy Convers. Manag. 148, 1142–1156. doi:10.1016/j.enconman.2017.06.073
Borreani, G., Tabacco, E., Schmidt, R. J., Holmes, B. J., and Muck, R. E. (2018). Silage review: factors affecting dry matter and quality losses in silages. J. Dairy Sci. 101 (5), 3952–3979. doi:10.3168/jds.2017-13837
Brown, A. E., Finnerty, G. L., Camargo-Valero, M. A., and Ross, A. B. (2020). Valorisation of macroalgae via the integration of hydrothermal carbonisation and anaerobic digestion. Bioresour. Technol. 312, 123539. doi:10.1016/j.biortech.2020.123539
Chandra, R., Takeuchi, H., Hasegawa, T., and Kumar, R. (2012). Improving biodegradability and biogas production of wheat straw substrates using sodium hydroxide and hydrothermal pretreatments. Energy 43 (1), 273–282. doi:10.1016/j.energy.2012.04.029
Cheng, J., Yue, L., Ding, L., Li, Y.-Y., Ye, Q., Zhou, J., et al. (2019). Improving fermentative hydrogen and methane production from an algal bloom through hydrothermal/steam acid pretreatment. Int. J. Hydrog. Energy. 44 (12), 5812–5820. doi:10.1016/j.ijhydene.2019.01.046
Cybulska, I., Lei, H., and Julson, J. (2009). Hydrothermal pretreatment and enzymatic hydrolysis of prairie cord grass. Energy Fuels. 24 (1), 718–727. doi:10.1021/ef9009179
Deng, C., Lin, R., Cheng, J., and Murphy, J. D. (2019). Can acid pre-treatment enhance biohydrogen and biomethane production from grass silage in single-stage and two-stage fermentation processes? Energy Convers. Manag. 195, 738–747. doi:10.1016/j.enconman.2019.05.044
Dien, B. S., Mitchell, R. B., Bowman, M. J., Jin, V. L., Quarterman, J., Schmer, M. R., et al. (2018). Bioconversion of pelletized big bluestem, switchgrass, and low-diversity grass mixtures into sugars and bioethanol. Front. Energy Res. 6, 129. doi:10.3389/fenrg.2018.00129
Ding, L., Cheng, J., Lin, R., Deng, C., Zhou, J., and Murphy, J. D. (2020). Improving biohydrogen and biomethane co-production via two-stage dark fermentation and anaerobic digestion of the pretreated seaweed Laminaria digitata. J. Clean. Prod. 251, 119666. doi:10.1016/j.jclepro.2019.119666
Ding, L., Cheng, J., Qiao, D., Yue, L., Li, Y.-Y., Zhou, J., et al. (2017). Investigating hydrothermal pretreatment of food waste for two-stage fermentative hydrogen and methane co-production. Bioresour. Technol. 241, 491–499. doi:10.1016/j.biortech.2017.05.114
Eskicioglu, C., Monlau, F., Barakat, A., Ferrer, I., Kaparaju, P., Trably, E., et al. (2017). Assessment of hydrothermal pretreatment of various lignocellulosic biomass with CO2 catalyst for enhanced methane and hydrogen production. Water Res. 120, 32–42. doi:10.1016/j.watres.2017.04.068
Girisuta, B., Dussan, K., Haverty, D., Leahy, J. J., and Hayes, M. H. B. (2013). A kinetic study of acid catalysed hydrolysis of sugar cane bagasse to levulinic acid. Chem. Eng. J. 217, 61–70. doi:10.1016/j.cej.2012.11.094
Guragain, Y. N., Wang, D., and Vadlani, P. V. (2016). Appropriate biorefining strategies for multiple feedstocks: critical evaluation for pretreatment methods, and hydrolysis with high solids loading. Renew. Energy. 96, 832–842. doi:10.1016/j.renene.2016.04.099
IEA Bioenergy Task 37 (2019). Country report summaries. Available at: https://task37.ieabioenergy.com/country-reports.html (Accessed June 20, 2020).
Jönsson, L. J., Alriksson, B., and Nilvebrant, N.-O. (2013). Bioconversion of lignocellulose: inhibitors and detoxification. Biotechnol. Biofuels. 6 (1), 16. doi:10.1186/1754-6834-6-16
Kang, X., Zhang, Y., Lin, R., Li, L., Zhen, F., Kong, X., et al. (2020). Optimization of liquid hot water pretreatment on Hybrid Pennisetum anaerobic digestion and its effect on energy efficiency. Energy Convers. Manag. 210, 112718. doi:10.1016/j.enconman.2020.112718
Kupiainen, L., Ahola, J., and Tanskanen, J. (2014). Kinetics of formic acid-catalyzed cellulose hydrolysis. BioResources 9 (2), 2645–2658. doi:10.15376/biores.9.2.2645-2658
Lai, C., Tu, M., Xia, C., Shi, Z., Sun, S., Yong, Q., et al. (2017). Lignin alkylation enhances enzymatic hydrolysis of lignocellulosic biomass. Energy Fuels. 31 (11), 12317–12326. doi:10.1021/acs.energyfuels.7b02405
Li, F., Liu, L., An, Y., He, W., Themelis, N. J., and Li, G. (2016). Hydrothermal liquefaction of three kinds of starches into reducing sugars. J. Clean. Prod. 112, 1049–1054. doi:10.1016/j.jclepro.2015.08.008
Li, G., Sun, Y., Guo, W., and Yuan, L. (2018). Comparison of various pretreatment strategies and their effect on chemistry and structure of sugar beet pulp. J. Clean. Prod. 181, 217–223. doi:10.1016/j.jclepro.2018.01.259
Li, M., Cao, S., Meng, X., Studer, M., Wyman, C. E., Ragauskas, A. J., et al. (2017). The effect of liquid hot water pretreatment on the chemical–structural alteration and the reduced recalcitrance in poplar. Biotechnol. Biofuels. 10 (1), 237. doi:10.1186/s13068-017-0926-6
Lin, R., Cheng, J., Ding, L., Song, W., Qi, F., Zhou, J., et al. (2015). Subcritical water hydrolysis of rice straw for reducing sugar production with focus on degradation by-products and kinetic analysis. Bioresour. Technol. 186, 8–14. doi:10.1016/j.biortech.2015.03.047
Lin, R., Cheng, J., and Murphy, J. D. (2017). Unexpectedly low biohydrogen yields in co-fermentation of acid pretreated cassava residue and swine manure. Energy Convers. Manag. 151, 553–561. doi:10.1016/j.enconman.2017.09.006
Lin, R., Cheng, J., and Murphy, J. D. (2018). Inhibition of thermochemical treatment on biological hydrogen and methane co-production from algae-derived glucose/glycine. Energy Convers. Manag. 158, 201–209. doi:10.1016/j.enconman.2017.12.052
Lin, R., Deng, C., Ding, L., Bose, A., and Murphy, J. D. (2019). Improving gaseous biofuel production from seaweed Saccharina latissima: the effect of hydrothermal pretreatment on energy efficiency. Energy Convers. Manag. 196, 1385–1394. doi:10.1016/j.enconman.2019.06.044
Mafe, O. A. T., Davies, S. M., Hancock, J., and Du, C. (2015). Development of an estimation model for the evaluation of the energy requirement of dilute acid pretreatments of biomass. Biomass Bioenergy. 72, 28–38. doi:10.1016/j.biombioe.2014.11.024
McEniry, J., Crosson, P., Finneran, E., McGee, M., Keady, T. W. J., and O’Kiely, P. (2013). How much grassland biomass is available in Ireland in excess of livestock requirements? Irish J. Agr. Food Res. 52 (1), 67–80.
Miller, G. L. (1959). Use of dinitrosalicylic acid reagent for determination of reducing sugar. Anal. Chem. 31 (3), 426–428. doi:10.1021/ac60147a030
Mohan, M., Banerjee, T., and Goud, V. V. (2015). Hydrolysis of bamboo biomass by subcritical water treatment. Bioresour. Technol. 191, 244–252. doi:10.1016/j.biortech.2015.05.010
Monlau, F., Sambusiti, C., Barakat, A., Quéméneur, M., Trably, E., Steyer, J.-P., et al. (2014). Do furanic and phenolic compounds of lignocellulosic and algae biomass hydrolyzate inhibit anaerobic mixed cultures? A comprehensive review. Biotechnol. Adv. 32 (5), 934–951. doi:10.1016/j.biotechadv.2014.04.007
Orozco, A., Ahmad, M., Rooney, D., and Walker, G. (2007). Dilute acid hydrolysis of cellulose and cellulosic bio-waste using a microwave reactor system. Process Saf. Environ. Prot. 85 (5), 446–449. doi:10.1205/psep07003
Overend, R. P., Chornet, E., and Gascoigne, J. A. (1987). Fractionation of lignocellulosics by steam-aqueous pretreatments. Phil. Trans. Math. Phys. Eng. Sci. 321 (1561), 523–536. doi:10.1098/rsta.1987.0029
Ponnusamy, V. K., Nguyen, D. D., Dharmaraja, J., Shobana, S., Banu, J. R., Saratale, R. G., et al. (2019). A review on lignin structure, pretreatments, fermentation reactions and biorefinery potential. Bioresour. Technol. 271, 462–472. doi:10.1016/j.biortech.2018.09.070
Qi, A., Murray, P. J., and Richter, G. M. (2017). Modelling productivity and resource use efficiency for grassland ecosystems in the UK. Eur. J. Agron. 89, 148–158. doi:10.1016/j.eja.2017.05.002
Redding, A. P., Wang, Z., Keshwani, D. R., and Cheng, J. J. (2011). High temperature dilute acid pretreatment of coastal Bermuda grass for enzymatic hydrolysis. Bioresour. Technol. 102 (2), 1415–1424. doi:10.1016/j.biortech.2010.09.053
Rodriguez, C., Alaswad, A., Benyounis, K. Y., and Olabi, A. G. (2017). Pretreatment techniques used in biogas production from grass. Renew. Sustain. Energy Rev. 68, 1193–1204. doi:10.1016/j.rser.2016.02.022
Ruiz, H. A., Rodríguez-Jasso, R. M., Fernandes, B. D., Vicente, A. A., and Teixeira, J. A. (2013). Hydrothermal processing, as an alternative for upgrading agriculture residues and marine biomass according to the biorefinery concept: a review. Renew. Sustain. Energy Rev. 21, 35–51. doi:10.1016/j.rser.2012.11.069
Sluiter, A., Hames, B., Hyman, D., Payne, C., Ruiz, R., Scarlata, C., et al. (2008). Technical Report No. NREL/TP-510-42621. Determination of total solids in biomass and total dissolved solids in liquid process samples. National Renewable Energy Laboratory, 9.
Sustainable Energy Authority of Ireland (2017). Economic assessment of biogas and biomethane in Ireland. Available at: https://www.seai.ie/ (Accessed June 20, 2020).
Teong, S. P., Yi, G., and Zhang, Y. (2014). Hydroxymethylfurfural production from bioresources: past, present and future. Green Chem. 16 (4), 2015–2026. doi:10.1039/c3gc42018c
Thi, N. B. D., Lin, C.-Y., and Kumar, G. (2016). Waste-to-wealth for valorization of food waste to hydrogen and methane towards creating a sustainable ideal source of bioenergy. J. Clean. Prod. 122, 29–41. doi:10.1016/j.jclepro.2016.02.034
Toftgaard Pedersen, A., Ringborg, R., Grotkjær, T., Pedersen, S., and Woodley, J. M. (2015). Synthesis of 5-hydroxymethylfurfural (HMF) by acid catalyzed dehydration of glucose–fructose mixtures. Chem. Eng. J. 273, 455–464. doi:10.1016/j.cej.2015.03.094
Tsapekos, P., Kougias, P. G., Egelund, H., Larsen, U., Pedersen, J., Trénel, P., et al. (2017). Mechanical pretreatment at harvesting increases the bioenergy output from marginal land grasses. Renew. Energy. 111, 914–921. doi:10.1016/j.renene.2017.04.061
Wall, D. M., O’Kiely, P., and Murphy, J. D. (2013). The potential for biomethane from grass and slurry to satisfy renewable energy targets. Bioresour. Technol. 149, 425–431. doi:10.1016/j.biortech.2013.09.094
Wall, D. M., Straccialini, B., Allen, E., Nolan, P., Herrmann, C., O’Kiely, P., et al. (2015). Investigation of effect of particle size and rumen fluid addition on specific methane yields of high lignocellulose grass silage. Bioresour. Technol. 192, 266–271. doi:10.1016/j.biortech.2015.05.078
Wang, S., Dai, G., Yang, H., and Luo, Z. (2017). Lignocellulosic biomass pyrolysis mechanism: a state-of-the-art review. Prog. Energy Combust. Sci. 62, 33–86. doi:10.1016/j.pecs.2017.05.004
Wang, Z.-W., Zhu, M.-Q., Li, M.-F., Wei, Q., and Sun, R.-C. (2019). Effects of hydrothermal treatment on enhancing enzymatic hydrolysis of rapeseed straw. Renew. Energy. 134, 446–452. doi:10.1016/j.renene.2018.11.019
Xiaojian, D., Yun, H., Qiang, L., Qian, F., Ao, X., Chao, X., et al. (2017). Medium-low temperature hydrothermal hydrolysis kinetic characteristics of concentrated wet microalgae biomass. Int. J. Agric. Biol. Eng. 10 (1), 154–162. doi:10.3965/j.ijabe.20171001.2699
Xie, S., Frost, J. P., Lawlor, P. G., Wu, G., and Zhan, X. (2011). Effects of thermo-chemical pre-treatment of grass silage on methane production by anaerobic digestion. Bioresour. Technol. 102 (19), 8748–8755. doi:10.1016/j.biortech.2011.07.078
Yu, I. K. M., and Tsang, D. C. W. (2017). Conversion of biomass to hydroxymethylfurfural: a review of catalytic systems and underlying mechanisms. Bioresour. Technol. 238, 716–732. doi:10.1016/j.biortech.2017.04.026
Yu, I. K. M., Tsang, D. C. W., Yip, A. C., Su, Z., De Oliveira Vigier, K., Jérôme, F., et al. (2018). Organic acid-regulated Lewis acidity for selective catalytic hydroxymethylfurfural production from rice waste: an experimental–computational study. ACS Sustain. Chem. Eng. 7 (1), 1437–1446. doi:10.1021/acssuschemeng.8b05141
Yu, Q., Zhang, A., Wang, W., Chen, L., Bai, R., Zhuang, X., et al. (2018). Deep eutectic solvents from hemicellulose-derived acids for the cellulosic ethanol refining of Akebia’ herbal residues. Bioresour. Technol. 247, 705–710. doi:10.1016/j.biortech.2017.09.159
Yuan, Y., and Macquarrie, D. J. (2015). Microwave assisted acid hydrolysis of brown seaweed Ascophyllum nodosum for bioethanol production and characterization of alga residue. ACS Sustain. Chem. Eng. 3 (7), 1359–1365. doi:10.1021/acssuschemeng.5b00094
Zhu, G., Zhu, X., Fan, Q., and Wan, X. (2011). Production of reducing sugars from bean dregs waste by hydrolysis in subcritical water. J. Anal. Appl. Pyrol. 90 (2), 182–186. doi:10.1016/j.jaap.2010.12.006
Keywords: grass silage, hydrothermal hydrolysis, kinetic model, reducing sugars, energy requirement
Citation: Lin R, Deng C, Rajendran K, Bose A, Kang X and Murphy JD (2020) Competing Reactions Limit Production of Sugars in Hydrothermal Hydrolysis of Grass Silage: An Assessment of the Effect of Temperature on Sugar Production and Parasitic Energy Demand. Front. Energy Res. 8:575523. doi: 10.3389/fenrg.2020.575523
Received: 23 June 2020; Accepted: 08 September 2020;
Published: 05 October 2020.
Edited by:
Pau Loke Show, University of Nottingham Malaysia Campus, MalaysiaReviewed by:
Kit Wayne Chew, Xiamen University Malaysia, MalaysiaCopyright © 2020 Lin, Deng, Rajendran, Bose, Kang and Murphy. This is an open-access article distributed under the terms of the Creative Commons Attribution License (CC BY). The use, distribution or reproduction in other forums is permitted, provided the original author(s) and the copyright owner(s) are credited and that the original publication in this journal is cited, in accordance with accepted academic practice. No use, distribution or reproduction is permitted which does not comply with these terms.
*Correspondence: Chen Deng, Y2hlbi5kZW5nQHVjYy5pZQ==
Disclaimer: All claims expressed in this article are solely those of the authors and do not necessarily represent those of their affiliated organizations, or those of the publisher, the editors and the reviewers. Any product that may be evaluated in this article or claim that may be made by its manufacturer is not guaranteed or endorsed by the publisher.
Research integrity at Frontiers
Learn more about the work of our research integrity team to safeguard the quality of each article we publish.