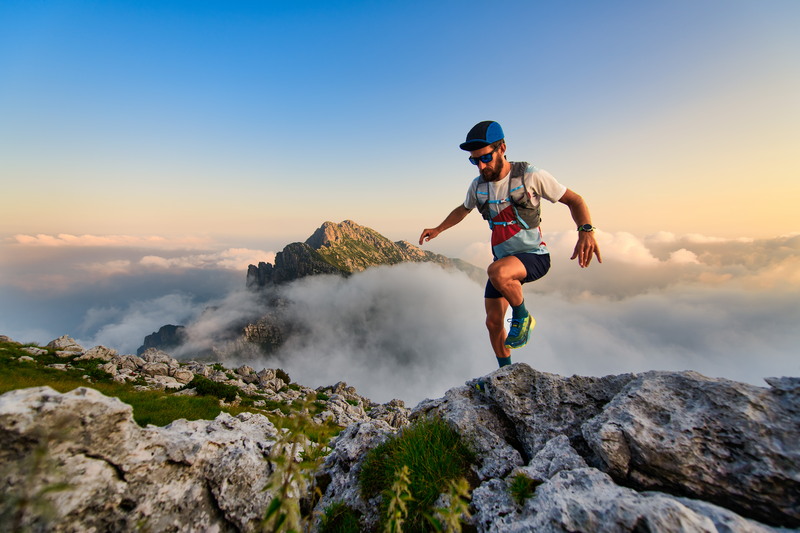
95% of researchers rate our articles as excellent or good
Learn more about the work of our research integrity team to safeguard the quality of each article we publish.
Find out more
REVIEW article
Front. Energy Res. , 11 September 2020
Sec. Electrochemical Energy Storage
Volume 8 - 2020 | https://doi.org/10.3389/fenrg.2020.00170
This article is part of the Research Topic Surface and Interface Engineering for Next-Generation Rechargeable Batteries View all 4 articles
Developing efficient energy conversion and storage technology is gradually becoming more and more necessary with the increasing shortage of fuel resources and the growth of environmental pollution. Demand and applications for the emerging technology such as new-energy vehicles and massive-scale energy storage are also expanding. Therefore, new rechargeable batteries, especially the most promising electrochemical energy storage device, lithium-ion batteries (LIBs), play an important role on the energy storage stage. LIBs have achieved large-scale industrialization, while the various non-negligible problems still exist compared with the demand for the future. Significantly, most electrochemical reactions occur on the electrode-electrolyte interface, and interface components, surface structure and property determine the performance of batteries. Thus, numerous efforts have been made to form or modify the electrode-electrolyte interface. This article reviews recent research about surface-interface modification in electrodes and organic liquid electrolytes in LIBs. Specifically, the basic growth mechanism of electrolyte-electrode interface and SEI layer is referred. The summary and discussion of surface modification and the innovative design of SEI layer are mainly focused on. Finally, future research directions focusing on electrode-electrolyte interface for lithium storage are proposed.
Chemical energy, as a portable energy, is extensively stored and used with biomass and fossil fuels (Cano et al., 2018; Tai et al., 2020). Electrical energy is an important applied energy, largely produced from fossil fuels, and it can be efficiently and remotely transmitted to work via the electrical grid. With the increase of the population and social complexity, we are also more dependent on fossil fuels, even the electrical power station. Alternative energy sources, such as wind, nuclear, and solar energy, are converted into electricity and form part of the large electric grid and the massive electrical energy storage. As one of the energy storage components, the rechargeable battery converts chemical energy into electrical energy to provide an effective storage (Larcher and Tarascon, 2015; Wu et al., 2019). Compared with conventional rechargeable batteries, the rechargeable lithium-ion batteries (LIBs) show superior properties, such as the higher energy density and voltage, long cycle period, satisfactory charge-discharge property, and safety, which indicates its hopeful prospects (Yuan et al., 2011). However, the energy and power density, cycle performance, stability, and conductivity of LIBs can still be improve.
Lithium-ion rechargeable batteries consist of two electrodes-cathodes and an anode, separators and electrolytes containing Li-ions. The electrolyte is basically divided into two kinds of phases: liquid and solid. The solid electrolyte can prominently prevent lithium dendrites and increase the safety of the battery compared with a liquid electrolyte, but the formed solid-solid interface causes many pivotal problems, such as the high interface impedance. In the system of commercial LIBs, the more important interface is the solid-liquid interface and a non-aqueous liquid organic solvent is mostly used as the liquid electrolyte. The liquid electrolyte, made of lithium salt generally, provides the lithium-ion transfer channels as the ion carrier; it isolates the electron conduction, in favor of conductivity in the whole battery as the bridge connecting the cathode and anode. In the LIBs system, lithium-ions transfer freely through the electrolyte solution, accomplishing the charge-discharge process along with the highly reversible de-insertion behavior between the two electrodes in the battery, which is called a “rocking chair battery.” During the process of charge, the electrons in the external circuit shift from cathode to anode, meanwhile, Li-ions migrate as the former inserts the graphite layer, for the formation of lithium, proceeding the combination with the electrodes; it is easy to understand that the discharge behavior is a reversible process. Li-ions migrate through the liquid electrolyte, as well as the flowing of electrons in the external circuit, all of which have travel quickly. However, the permeation from electrolyte to electrode of Li-ions and the solid diffusion within the electrode materials is slower. As a result, the relatively slow mass transportation behavior of Li-ions on the surface and interface plays an important part in the performance of LIBs (Wang et al., 2015).
Toward the key role-interface in energy batteries, the visual interpretation is of “a two-dimensional surface” but it is deeply understood that interface is not just a plane but also represents the inhomogeneous spacial region between two phases in contact (Rajput et al., 2018). As a dynamic space, interface influences most of the reaction processes and parameters determining the battery performance. Furthermore, the side influence usually occurs between the electrode and electrolyte or on the surface of the electrode materials. Additionally, the performance of the whole battery is highly dependent on the quality of the electrolyte interface and the physicochemical properties and characteristics of the interface significantly determines the power and safety of the battery. It is significant that researchers can adjust the interface in many ways to improve the battery performance based on a comprehensive understanding of the chemical properties and the effects of each component within the interface. Significantly, the decomposition of electrolytes and the interactions of electrode-electrolyte lead to the irreversible formation of a solid-electrolyte interface layer which makes a great difference to LIBs. Generally, the interface generated on the negative electrode is named the “solid electrolyte interphase” (SEI) and the interface generated on the positive electrode is called the “cathode electrolyte interphase” (CEI). Therefore, more attention is given to the electrolyte interface by researchers in the field of rechargeable batteries over time. To take a convictive supplement, the statistics about the amount of research into electrolyte interface (only in research titles) are shown in Figure 1 (summarizes the yearly number of scientific papers on Lithium-ion batteries, based on Web of Science) displaying clearly the extremely high status of interface in energy innovation.
Figure 1. Number of publications on electrode/electrolyte interface in LIBs according to Web of Science (accessed: May 12, 2020).
The electrode surface film is also considered to be an SEI film. During the process of charge, the solvent or lithium salt is reduced or oxidized on the electrode surface, and the insoluble part of the products will be deposited on the anode or cathode surface and an SEI layer is formed. The surface film can conduct lithium-ions except insulated electrons and has the characteristics of a solid electrolyte. If the SEI cannot cover the electrode surface in a dense manner or is not an electronic insulator, then the solvent or lithium salt can continue to obtain and lose electrons from the electrode, causing a side redox reaction and consuming the lithium source of the cathode. If the SEI can effectively prevent the subsequent reduction of solvent or lithium electrolyte salt, then it has the property of a passivation film called surface passivating film. An SEI film with superior properties is usually equipped with the follow features: (1) high ionic conductance making the passing of lithium-ions through the SEI easy, (2) a stable morphology and chemical structure, (3) robust binding properties with active substances, (4) superior mechanical performance buffering volume expansion, and (5) superior electrochemical and thermal stability. In simple words, surface and interface modification involves finally coating or forming a thin film on the electrode surface in a variety of ways. By controlling the side reactions in the electrolyte and the structural changes on the surface, modifying the surface lights up the dark region for LIBs. It is observed that appropriately controlling and modifying the electrolyte-electrode interface is necessary for the application of rechargeable LIBs.
In order to improve the performance of LIBs, the surface and interface in the battery can be efficiently modified and tuned. In this review, recent research about surface-interface modification in electrodes and organic liquid electrolytes of LIBs are presented and discussed, and the corresponding modification methods are classified, as shown in Figure 2. Specifically, the basic growth mechanism of the electrolyte-electrode interface and the SEI layer is referred. The summary and discussion of surface modification and the innovative design of the SEI layer are the main topics focused on. In addition, the prospect of surface and interface in LIBs is thoroughly discussed.
Figure 2. Schematic diagram of surface-interface modification strategies and classification in organic liquid electrolytes for LIBs and map of this review.
The SEI layer can generate on the surface of both cathodes and anodes, while the effect of the cathode on the battery is much less than that of the SEI on the anode. Therefore, we focused on the SEI layer on the surface of the anode. For a dual component electrolyte [1.0 M LiPF6 in ethylene carbonate (EC)], Heiskanen et al. (2019) conducted a detailed study on the process of formation and growing of SEI and analyzed vividly the changing process of the SEI film composition. In the beginning, the main components, lithium ethylene dicarbonate (LEDC) and LiF, are produced due to the decomposition of EC on the anode surface. However, LEDC is not stable enough that decomposition reactions can continuously proceed during the process of circulation and storage. These products are almost gas or soluble substances including Li2CO3, LiF, and CO2, which creates the porous structure of SEI film. Additionally, the porous structure can bring about the permeation of electrolyte solutions, that new LEDC and LiF are produced again. This continuous process can accelerate the growth of the SEI film. At the same time, the SEI film also gradually evolves into a bilayer structure that has more inorganic components in the inner layer and more organic components in the outer layer. Thus, the interface model can be distinctly depicted by Figure 3 (Heiskanen et al., 2019). The characteristics of the SEI determine the de-intercalation of Li-ions and the dynamics of the stable electrode-electrolyte interface, which has a profound effect on the performance of the whole battery.
Figure 3. Schematic figure of the interface growth model of initial SEI formed. Reproduced with permission from Ref. Heiskanen et al. (2019). Copyright 2019 Elsevier.
Electrochemical impedance spectroscopy (EIS) is one of the most powerful tools for studying the electrochemical processes occurring at the electrode/electrolyte interface (Zhuang et al., 2010; Pajkossy and Jurczakowski, 2017). It is extensively adopted to investigate the intercalation and expulsion of Li-ions in electrode active materials (Figure 4) (Zhuang et al., 2010; Xu et al., 2011), the mechanism of performance degradation (Abe et al., 2019), and the formation mechanism of SEI (Steinhauer et al., 2017). EIS uses the sine wave potential with a small amplitude as the disturbance electrical signal to produce the response of the electrode system with an approximate linear relationship, it then measures the ratio of alternating potential and current signal in a wide frequency range to study the electrode system (Zhuang et al., 2020). Steinhauer et al. (2017) measured the SEI resistance of the first and second lithiation process by EIS. During the first lithiation measurement, the maximum in SEI resistance is shown and the formation of complete SEI decreases the value of resistance, yet the maximum is not present during the second lithiation which originates from the facilitated desolvation behavior of Li-ions due to the appearance of the ion-conductive SEI layer. This means that desolvation can cause the high activation barrier in the course of the interfacial ion transfer, which is elaborated by Busche et al. (2016). Besides, the SEI behavior analyzed by EIS is at an elevated and lower temperature. At the higher temperature, the overall resistance is increased which can be explained by thermo-dynamics. And the lower temperature environment induces the formation of incomplete SEI.
Figure 4. Model schematic diagram of the physical mechanism of the lithium intercalation process. Reproduced with permission from Ref. Zhuang et al. (2010). Copyright 2010 American Chemical Society.
However, many limitations also occur in the further applications for LIBs. Up to now, the EIS figure usually only consists of a semicircle and a slash, which indicts the ambiguity. Specifically, numerous complex physical and chemical reactions and various steps within each reaction cannot be described independently and clearly in detail. In external conditions, the complex porous electrode structure in LIBs increases the difficulty. Hence, improving the measurement accuracy of the EIS instrument further and developing new impedance spectrum testing techniques are necessary approaches to overcome the above obstructions. And combining the EIS technique with theoretical simulation occupies the important status in the developing direction of LIBs.
During the first charge process, the SEI grows on the solid-liquid interface and covers the electrode surface, efficiently preventing the reduction of the electrolyte. For the graphite anode, the cointercalation of molecules and exfoliation of electrode surface layers are also protected due to the SEI (Ciosek Högström et al., 2013). Changing the component of the electrolyte by adding an effective chemical compound with a special structure, further tunes the composition and properties of SEI. According to the additive added to the solution, such as a representative film-forming additive, a co-solvent additive, or an anion receptor, which would react with electrolyte liquid or electrode surface and further the bonding, growth situation, and chemical property change greatly on the electrode-electrolyte interface.
The electron-withdrawing ability of a film-forming additive active group is an important factor for the potential of the SEI film (Zhao W. et al., 2017; Zhao H. et al., 2019). If its electron-withdrawing ability is strong, a high potential reduction reaction would take place, which can not only restrain the damage to the electrode by solvent co-embedding, but also inhibit the excessive decomposition of the electrolyte to improve the performance of the surface (Zhao W. et al., 2017). An organic film-forming additive, propargyl methanesulfonate (PMS), and LiPF6 were added to the EC/DEC electrolyte. Compared to the cycled battery without PMS, which demonstrated less irreversible capacity loss and had the appearance of a thinner SEI film. At the same time, PMS formed a triple-bonded radical reacting with the electrolyte on reduction (Ciosek Högström et al., 2013). Matsuoka et al. (2002) verified the superior effect of vinylene carbonate (VC) on the electrode. For the formation of SEI on highly oriented pyrolytic graphite (HOPG), VC is in a position to decrease the active site and inhibit the decomposition of the solution. In addition, as the additive on HOPG in Propylene carbonate (PC) solutions, VC is proven to promote the precipitation of the thin SEI film (Jeong et al., 2001). Itagaki et al. (2006) conducted an improvement focusing on the effect of VC on SEI. By improving the permeation of Li-ion in SEI film and decreasing the resistance of it, the VC additive in the electrolyte solution played a significant role in the formation of high quality SEI film. Moreover, Aurbach et al. (2002) emphasized the efficient influence of VC as an additive for a graphite electrode, confirming that VC is able to polymerize on the electrode surface and form polyalkyl lithium-carbonate that held back the reduction between the solvent and salt anion. Pointing to the impact of the film-forming additive on the formation mechanism of SEI, Zhuang’s group utilized vinylethylene carbonate (VEC) (Xu et al., 2013) and fluroethylene carbonate (FEC) (Zhao X. et al., 2015) successively as additives in an EC-based electrolyte. The results demonstrated that the high concentration of FEC can result in the deterioration of electrochemical performance, probably because of the poor cohesion and flexibility of SEI which made the charge transfer resistance and SEI film resistance larger as particularly observed by EIS analysis. For researching the role of inorganic film-forming additives, Zhuang et al. (2013) also evaluated K2CO3 in 1 mol/L LiPF6-ethylene carbonate:dimethyl carbonate (LiPF6-EC:DMC) electrolyte in LIBs. Separately, K2CO3 as the additive suppressed the deposition of EC making SEI thinner and successfully modified SEI to a porous worm mesh structure equipped with better viscoelasticity. Further, the decelerate rise of resistance of the SEI film also makes a contribution to viscoelasticity from the EIS results. The enhanced battery performance is obtained on account of the flexible porous mesh SEI structure that can easily accommodate the volume changes of the electrode.
Anion receptors are specific compound-forming complexes with lithium salt anions which can reduce the interaction between Li+ and anions, increase the migration number of Li+, prevent the oxidation or reduction of anions, and inhibit the formation of side products on the electrode interface. In general, the conductivity of the electrolyte can be improved due to the coordination effect. According to numerous studies, anion receptors proved to be an appropriate electrolyte additive. Tris(pentafluorophehyl)borane (TPFPB), a boron-based anion receptor, is adopted to suppress redundant effects from oxygen species as an electrolyte additive and decrease the side products on the cathode surface (Zheng et al., 2014). As a result, TPFPB reduces the electrolyte decomposition due to its strong coordination ability and high oxygen solubility, and the stability of the electrode-electrolyte interface is enhanced (Zheng et al., 2014). Besides, it was reported that TPFPB dissolving byproducts such as LiF and Li2O in solution can improve the performance of batteries in which graphite and LiMn2O4 are internal active materials (Chen et al., 2006; Chung et al., 2006). For the batteries with the same concentration of TPFPB, the performance is closely related to the amount of electrolytes. So the influence of anion receptors is subject to many factors. In addition, both the concentration of anion receptors and the amount of electrolytes are controlled accurately so as to optimize the performance of the electrode with higher loading.
The co-solvent can change the concentration, temperature, and melting point of electrolyte solutions so choosing the appropriate co-solvent as a special “additive” in electrolytes can modify the electrode surface and change the composition of the electrolyte, meanwhile, the SEI with a high quality will form under the effect of the co-solvent. When nanostructured a-MoO2 is used as the negative electrode, FEC induces some changes in surface reactions of a-MoO2 and tunes the structure of SEI. Park J. et al. (2014) showed that the FEC-derived SEI has the lowest impedance and superior stability due to its thin, flexible, and robust properties. Therefore, the involvement of FEC enables efficient interface control. Numerous reports also focused on FEC as a co-solvent in their research. When silicon nanoparticles (SiNP), prepared by slurry casting, compose the electrodes, the assembled LIBs with a FEC-based electrolyte showed superior capacity retention (Lin et al., 2012). Silicon nanowire (SiNW) as the anodes, modified by the co-solvent FEC, is observed to enhance the electrochemical performance, such as lower impedance. And fresh surface film is much thinner and more compact in FEC-containing electrolyte solutions (Etacheri et al., 2012). In FEC-based electrolytes with the co-solvent propylene carbonate (PC), the Li-ion cell develops well with graphite anodes (McMillan et al., 1999). Additionally, FEC can also change the surface species to get a high quality interface serving as SEI former organic additives (Zhang, 2006). Ideally, for a co-solvent to be effective on an electrolyte, it is necessary to balance the high conductivity, the decreased stability of the electrolyte, and the incompatibility with electrode materials.
Recently, developing new high-safety electrolyte systems is important due to the unstable deposition of conventional electrolytes and the limited application on secondary batteries. To this, localized high concentration electrolytes (LHCE) are formed by adding the “inert” diluent into high concentration electrolytes (HCE), which not only absorb the excellent characteristics of high concentration electrolytes, but also possess the characteristics of low cost and superior wettability. Just as its name implies, the emergence of LHCE evolves from HCE. When the interactions between the cation and anion of electrolyte salts enhances and the solvent moleculars on free state disappear with the increasing concentration of salts (until ≥ 3.5 mol/L) (Wang et al., 2016), a kind of new non-hydrolytic electrolyte with a special structure, called HCE, is formed. In Figure 5A, the solution structure of the electrolyte is studied using a density functional theory molecular dynamics simulation (DFT-MD), and bis(fluorosulfonyl)amide (FSA–) anions connect intensively with Li+ in Figure 5A (right), showing a more reinforced three-dimensional network compared with the less concentrated solution. On the basis of HCE, the dilute as a unique additive which can be mutually soluble with solvents but not with salts is added into the electrolyte, while the special coordination structure [(Li+-solvent)dilute] is unbroken and LHCE is formed (Zheng et al., 2018). Chen et al. (2018b) first coined the name “LHCE.” As shown in Figures 5B,C, the electrolyte solution is diluted with an “inert” diluent leading to lower salt concentration along with the formation of LHCE from HCE. LHCE not only inherits the advantages of HCE: 1. high ion migration; 2. keeps the Al current collector from corrosion; 3. inhibits lithium dendrites; 4. broadens the electrochemical window; 5. improves flame resistance, but also alleviates partial disadvantages that the dissolution of the dilute decreases the viscosity and improves the wettability of the electrode and separator. Before, Chen et al. (2018a) reported a novel “localized-HCE” in high voltage lithium-metal batteries (LMBs): 1.2 mol/L lithium bis(fluorosulfonyl)imide (LiFSI) dissolve in dimethyl carbonate/bis(2,2,2-trifluoroethyl) ether (DMC/BTFE) mixture (1:2 by mol). In this work, the addition of dilute BTFE ensures that the lithium metal anode of Li| | LiNi1/3Mn1/3Co1/3O2 battery circulates at a high coulombic efficiency (99.5%) without producing dendrites, finally the novel electrolyte is highlighted with low concentration, low viscosity, high conductivity, and superior wettability. Up to now, the research into LHCE have mostly focused on lithium metal anodes or the lithium-sulfur battery. Considering the discussion topic of this review, a more specific analysis has not been undertaken here.
Figure 5. The solvated coordinate structure of an electrolyte dependent on salt concentration. (A) The solution structure models under equilibrium trajectories of different solution concentrations by DFT-MD simulations. Reproduced with permission from Ref. Wang et al. (2016). Copyright 2016, Springer Nature. (B) The solvated coordinate structure in high concentrated electrolytes, and the participation of diluent constructing the special coordinate structure. Reproduced with permission from Ref. Zheng et al. (2018). Copyright 2018 American Chemical Society. (C) The addition of dilution by BTFE changes the solution structure to form LHCE. Reproduced with permission from Ref. Chen et al. (2018b). Copyright 2018 Elsevier.
Generally, solid-liquid electrochemical reactions happen on the solid-liquid interface accompanied by mass transportation. The interface property depends on the surface of the electrode material particles to a high degree. Moreover, various problems resulting from particle size, high operating voltage, or instable decomposition of electrolyte are being absorbed by researchers finding out solutions. In this regard, surface coating has been proven to be the correct way to monitor the surface structure of electrodes (Zhao F. et al., 2015). Alternatively, the coating on the surface for modification or functionalization is regarded as an efficient method to help overcome these problems. Modifying the electrode-electrolyte interface using a coating is to help stabilize the surface structure of the electrodes and attenuate the SEI layer. When applying a high operating voltage, the electrode-electrolyte interface undergoes many side reactions causing large structural damage.
At first, metal oxide is commonly used as a coating material, which not only reacts with acid species in electrolytes and prevents electrodes from being destroyed but also blocks the direct contact between two electrodes and improves the safe performance of batteries that can overheat due to its lower electronic conductivity. Among the cathode materials on Li-ion batteries, Li0.5Ni1.5MnO4 (LNMO) gets significant attention as a candidate for high power and next-generation energy storage application, while the operating voltage of it reaches up to 4.7 V, which inevitably brings bulk interface structure deterioration and some bad side effects (Xu et al., 2014; Wang et al., 2017). Surface modification and morphology fabrication can be utilized in solving the above issues. Recently, Gao et al. (2020) adopted a conformally interfacial La2O3 nanocoating layer to modify the LNMO high-potential cathode. The introduction of La2O3 nanocoating, especially in the ratio of 2 wt%, successfully suppresses the deposition of the electrolyte and protects the surface from HF corrosion, which gives the LNMO cathode a stable interface structure, a thin SEI layer, and excellent Li-ions diffusion capacity, just as shown in Figure 6a. To date, the LNMO particle surface has also been modified by various coating materials, for instance, Al2O3 (Kim et al., 2015), FePO4 (Xiao et al., 2015), TiO2 (Tao et al., 2017), and Co3O4 (Deng et al., 2018). Among them, the Al2O3 coating layer used to modify the interface is the most popular and extensively researched. According to a recent study, an Al2O3-modified spinel LNMO cathode material was prepared via a one-step solid-state reaction and modified through a wet chemical technique (Chang et al., 2019). In the modification, an amorphous Al2O3 coating layer was developed on the surface of LNMO. The surface coating alleviated the continuous strike of HF species to active materials which were caused by electrolyte decomposition and suppressed the interfacial reactions. The vivid demonstration is shown in Figure 6b (left) (Wang et al., 2015), meanwhile, it can be observed from the EIS parameter, lower △Rsf value, that the rapid increase of SEI is mitigated, the side reactions are restrained and the surface kinetics behavior is more active. And the buffer effect of the amorphous Al2O3-coating in LiCo0.94Fe0.06VO4 reaction with HF from electrolytes is also found (Landschoot et al., 2004). However, the Al2O3-coated material usually has low conductivity due to the interface. Xiao et al. (2015) prepared a FePO4-coated LNMO presenting similar issues. Thus, through keeping the interface electrochemical potential, the FePO4 coatings have a role as both an electrochemical buffer layer and a lithium diffusion facilitator. Sun et al. (2016) study revealed that LNMO modified by Al-coating and Al3+-doping has a stable interface structure. Moreover, enhancing the disorder degree of the ontology phase to promote sufficient electronic conduction has been proven a valid treatment by Co3O4-coated LNMO materials (Deng et al., 2018). In another study, the same phenomenon was obtained, but the mechanisms point to CEI, which is related to the erosion of LNMO surface and the conductivity (Guo et al., 2019). The Co3O4 modification reduced tremendously the interspace of secondary particles and surface area of LNMO, and even weakened the side reaction, resulting in less CEI film. Similarly, LNMO modified by a thin layer of YPO4 via the same coating method has been looked in to. The mechanism analysis is nearly comparable with an Al2O3-coated LNMO. Deeper analysis revealed that Lewis acid YF3, converted from YPO4 layer, accelerated the ion change on the LNMO surface (Xu et al., 2018). Through the above, the stable interface is built up to eliminate the undesirable side reaction as much as possible.
Figure 6. The functioning mechanism of surface modification-surface coating. (a) Schematic illustrations of the cycled La2O3-coated LNMO and the functioning mechanism of the La2O3 protective layer. Ref. Gao et al. (2020). Copyright 2020 Elsevier. (b) Schematic drawing of the interface between the positive electrode and electrolyte, the functioning difference between metal oxide coating (left) and ion-conductive coating (right). Reproduced with permission from Ref. Wang et al. (2015). Copyright 2015 Wiley-VCH. (c) The functioning process of surface modification to stabilize the surface of the LNMO particle. Reproduced with permission from Ref. Zhao R. et al. (2019). Copyright 2019 American Chemical Society. (d) The high-magnification SEM image (left) and TEM image (right) of the Si@PPy-Fe electrode after 10 cycles, and the Si nanoparticles (red arrow) were coated with a uniform PPy-Fe layer (green arrow). Reproduced with permission from Ref. Zhou et al. (2016). Copyright 2016 American Chemical Society.
However, the metal oxide coating materials are usually insulators which work against the interfacial mass change of electrodes and decrease the ionic conductivity. Hence, a lithium-ion conductive-material is more desirable as it is able to facilitate ion diffusion. Compared with the metal oxide, the coating model difference is clearly illustrated in Figure 6b (right). Amorphous lithium phosphate compounds are excellent lithium-ion conductors. Through the formation of surface-protecting layers, the surface coating by lithium phosphates enhances the ion conductivity and hampers the interfacial side reaction. Cathode material LiFePO4 coated by Li3PO4 is seen as a fast Li-ion conductor that presents enhanced electronic conductivity (Zhao et al., 2013). Another lithium phosphate compound Li0.1B0.967PO4 (LBPO) used as the coating on the cathode surface provides an effective li-ion penetration path and surface protection layer (Yang et al., 2014). The fast ion conductor Li3V2(PO4)3 (LVPO) is also adopted to modify the surface of spinel LNMO via a one-step integrated method. Experiment results show that the 1 wt% LVPO-LNMO exhibits excellent performance. Zhao R. et al. (2019) proposed the enhancement mechanism or interpretation of surface modification in Figure 6c. After the treatment, the dissolution of transition-metal (TM) ions were mitigated, and the TM ions stayed inside the electrode decreasing the destruction to the electrolyte and further avoiding the degradation of the bulk material. More importantly, the vanadium (V) ions generated a transition layer involving V by migrating a certain amount of V ions in LVPO to the surface lattice of LNMO, which can reduce the interfacial impedance. Under a high operating voltage, the LVPO-involved surface becomes an improved interface with desirable kinetics behavior and structural stability (Zhao R. et al., 2019). At the same time another fast Li-ion conductor, calcined lithium vanadate (Li3VO4) has a higher ion conductivity. Cathode materials such as LiMnPO4 (Dong et al., 2014) and Li1.18Co0.15Ni0.15Mn0.52O2 (Fu et al., 2014) present a desirable performance after being modified by Li3VO4 coatings on the surface. For coated LiMnPO4 samples, the thin Li+-conductive Li3VO4 surface coatings can increase the Li+ flux through the LiMnPO4 surface by inhibiting formation of phases on the surface which enhances Li-ions permeation into the surface of the electrode, and all of these are attributed to high ion mobility and a three-dimensional ion transport path of the coating layer (Dong et al., 2014). Similarly, in another study, the Li3VO4 coated Li1.18Co0.15Ni0.15Mn0.52O2 (LCNM) material has a higher ordered layered structure and the interfacial side reactions resulting from the ion mixing are less. And at the electrode-electrolyte interface, the Li3VO4 surface coating improves the activation of Mn4+-ion, prohibits the growth of SEI film, and expedites the charge transfer reaction (Fu et al., 2014). Attracted by the high Li-ion diffusion coefficient of Li3VO4, the layered oxide Li1.2Ni0.2Mn0.6O2 is also modified by the ionic conductor and the new material shows an outstanding performance as well as a more stable SEI film (Liu Y. et al., 2015). Some other unspecified reports disclose the significance of fast Li-ion conductors as surface coating materials in LIBs.
Besides, electronic conductivity is generally low for electrode materials. Except these metal oxides and ion-conductivity materials, the electronic conductive species, such as metal nanoparticles, carbon thin film, and conductive polymers, are employed to modify the surface. Thin-film coatings protect the electrodes surface from attacking the electrolyte solution and suppresses the interfacial side reactions. Further, thin-film coatings with electronic conductivity materials are greatly significant, such as conductive polymer (Zhou et al., 2016), carbon (Shen et al., 2014), and titanium silicide (Park et al., 2013), which also have a desirable application value. Si-based anodes are commonly used as popular electrode materials in LIBs, but the large volume change and low conductivity causes many issues. Based on the silicon anode, a Zhou et al. (2016) study showed a conformal modification alleviating the above problems. A Polypyrrole-Fe (PPy-Fe) coordination complex (Si@PPy-Fe) as the thin-film electronic conduction is prepared by coating the Si powder particles with in situ core-shell coating. The conformal conductive coating by PPy-Fe molecules surrounding the Si nanoparticles close the electronic connection among particles, trapping the Si particles inside and offering a successive pathway for electronic conduction. Meanwhile, SEM and TEM images (Figure 6d) intuitively show that the electrode structure of Si@PPy-Fe has no fractures on account of the conformal modifying and the Si nanoparticles are encapsulated by the PPy-Fe coating. More importantly, the formation of the stable SEI layer is improved. To create crucial SEI layers and Si-based materials as anodes in LIBs, Lee et al. (2015) reports that the Si core is designed with multifunctional coating layers (consisting of LS and LTO) equipped with electrical conductivity which controls the formation process of the optimized SEI layer. Next, for measuring the value change of RS, RSEI, and Rct around the coating modification, in situ galvanostatic electrochemical impedance spectroscopy (GS-EIS) is employed. The characteristics of SEI layer are also displayed by the in situ GS-EIS test, and after the 60th cycle the RSEI value of coated Si-based electrode-Si-multi-50 is lower than the pristine Si nanoparticles electrode due to the more stable SEI layer formation, which also demonstrates the electrical conductivity effect of the multi-functional coating layers to the Si-based anode. For Si-based electrodes, the SEI layer is formed at the lithiated state and is broken at the delithiated state because of the volume expansion of Si. Thus the new SEI layer is formed on the new Si surface. With the continuous consumption of electrolytes and Li+, the SEI becomes thicker on the pristine Si electrode. In contrast, multi-functional coating layers produce a uniform SEI layer and have a great effect on the SEI as mentioned above: preventing the direct contact between electrodes and electrolytes; Li+ ion conductors can suppress the decomposition of the electrolyte and keep the ion diffusion steady; and improve the electronic conductivity and ion diffusion rate.
Surface modification works on behalf of a surface coating or growing nanoscale thin film on the surface of electrode materials. For adapting the various surface structure of basic materials, continuous and conformal modification is necessary. The enhanced ability of surface modification for the whole battery primarily depends on the type, amount, and thickness of coating materials. Thin film deposition is also a kind of effective surface coating technique. In particular, for developing the influence of thin film, the nanoscale confomal thin film deposition is becoming most common (Alaboina et al., 2017). As is known to all, numerous methods of thin film deposition are available, which includes physical vapor deposition (PVD), chemical vapor deposition (CVD), molecular beam epitaxy (MBE), and spin coating. Recently, atomic layer deposition (ALD), a new-fashioned, ultra-thin film deposition technique, has emerged and acquired increasing attention in the development of next-generation LIBs (Knoops et al., 2012; Meng et al., 2012; Nilsen et al., 2014). Due to the precise control and high throughput of the ALD technique, it walks ahead of other film deposition techniques. And it has the ability to form the thin film on power samples and on large surface areas. Meng et al. (2012) demonstrated the mechanism of the ALD process in Figures 7A–E, and for the binary compound Al2O3 as substrate, the four repetitive steps are illustrated. In practice, an ALD-Al2O3 process can be briefly summarized into two cycled steps: the precursors induce the surface reaction with reactive sites to form the intermediate layer and then a purging phase to evacuate the impurities. Thus, the ALD process operates cyclically and regularly. ALD is based on the sequential self-limiting gas-solid chemical reaction on the material surface (Puurunen, 2005). As a powerful technique for solving problems of practical applications, ALD shows a slight advantage in the synthesis and surface engineering of various nanostructures over other film deposition counterparts on account of its exclusive advantages which include: extremely uniform and conformal deposition, even on three-dimensional (3D) substrates (Elam et al., 2003), precisely controlled film thickness, and low operating temperatures. However, it is disclosed that ALD possesses some unfavorable features such as its slow deposition process, and it has to be applied to ultra-clean surfaces due to the stringent demand, instead, which attracts scientists to conduct a mass of studies focusing on this technique, accordingly some satisfactory results can also be successively obtained.
Figure 7. The deposition model of the ALD process for different electrode surfaces. (A–E) The successive model of the ALD deposition process on Al2O3 substrate using TMA and water as precursors. Reproduced with permission from Ref. Meng et al. (2012). Copyright 2012 Wiley-VCH. (F) Schematic illustration for ALD coating, (I) LCO powders, and (II) LCO cathode electrodes. Reproduced with permission from Ref. Li et al. (2014). Copyright 2014 Elsevier. (G) Schematic illustration of proposed hybrid surface coating strategy. Reproduced with permission from Ref. Kalluri et al. (2017). Copyright 2017 Wiley-VCH.
ALD coating on cathode surfaces is the most typical type of surface modification. As referred above, LNMO particles as cathodes are popular due to their unique advantages. Compared with other methods utilized to treat the surface of LNMO electrodes coated by the metal oxide, the ALD method is more widely accepted. Specifically speaking, Kim et al. (2015) reported the positive effects of Al2O3 ALD coated LNMO and discovered that the SEI layer on coated LNMO surface is much thinner and even contains fewer organic species than untreated LNMO. And the LNMO surface coated by ultrathin amorphous FePO4 (Xiao et al., 2015) using ALD is observed to increase interface stability. ALD-derived ultra-thin Al2O3 and LiAlO2 coatings also perform as protective layers on LNMO (Fang et al., 2014; Park J.S. et al., 2014; Kim et al., 2015). In addition, the surface of the LNMO cathode powder particle is deposited by a protective LiF film via an ALD technique. In the process of deposition, the F sources of LiF film are different: Hexafluoroacetylacetone (Hfac) and TiF4, respectively. According to the shielding characteristics and chemical composition of the two coatings with different F sources, it is suggested that the Li diffusion into cathode materials protect against Mn dissolution (Tiurin et al., 2020). Aiming at the effects of interface coatings modification, the rate capability is always overlooked. Just as mentioned before, the ultra-thin amorphous layers develop the significant effects again. The ultra-thin amorphous Al2O3 and TiO2 ALD coatings are used on anatase the TiO2 and LiMn2O4 electrodes. It is found that ALD TiO2 film can prevent the solvent decomposition from forming a smoother electrode surface and the rate capability can be improved because of its lithium conducting properties (Mattelaer et al., 2017). In other studies, according to precisely controlling the various thickness of metal oxide (TiO2, ZrO2 and Al2O3) coatings, ALD technique is employed to modify a LiCoO2 (LCO) material on the surface (Meng et al., 2012; Li et al., 2014; Xie et al., 2016; Teranishi et al., 2018). A dual surface coating strategy is proposed by Kalluri et al. (2017) and employed on Li(Ni,Mn)O2-coated LCO material in Figure 7G. The as-prepared LCO loaded electrodes are surface coated by ALD with an ultrathin Al2O3 layer under optimized condition. Li et al. (2014) reports showed that with increased ALD cycles, the thickness value of the coating layers is increased and the thickness variation of the ZrO2 coatings with different ALD cycles can be observed. And it is visible that the coating layers have become smooth and uniform with high thickness. In short, when the ALD cycle number increases, the amount of metal oxides deposited augment. As depicted in Figures 8a–c from high-resolution TEM (HRTEM) images, on the LCO cathode surface the conformal and nanoscale ALD coating layers with different materials are closely and clearly observed, TiO2 (Figure 8a), ZrO2 (Figure 8b), and Al2O3 (Figure 8c), and the coating layer thickness of these different materials may be evaluated. By the electrochemical measurements, it can be noted that the type of coating materials would affect the electrochemical performance. LCO powders with Al2O3 ALD film show the excellent cycling ability, whereas the one with ZrO2 film displays a better rate performance than others. Moreover, compared with ALD coated LCO powders, the ALD coated prefabricated LCO electrode has remarkable performance. The reason is illustrated in Figure 7F, if the ALD process is totally applied on LCO powders, the lithium diffusion and electronic transport through the interface is very slow, on the contrary, this is the better situation because the conductible contacting area is not deposited by metal oxides. After the ALD process, the cobalt dissolution of LCO and the contact between LCO particles and HF in electrolyte are inhibited, thereby the interface property is enhanced. It is finally concluded that coating materials are functionally specific and each kind of material exerts a different influence on interface structure and property (Li et al., 2014). Also deposits of Al2O3 ALD film on LCO build a protective barrier layer, while on the interface another protective and active oxide material is formed. The Al2O3 shell is absent, instead, aluminum diffused into the bulk LCO leads to the formation of LiCoO2:Al, an oxide material with amorphous region depending on Al content. The cells are also verified to have a satisfactory discharge capacity of ∼100 and ∼35 mAh/g at 50C and 100C, respectively (Teranishi et al., 2018).
Figure 8. The electrochemical performance of modified electrode materials by thin film deposition via ALD. (a–c) HRTEM images of the LiCoO2 cathode by 50-ALD-cycles coating layers: TiO2, ZrO2, and Al2O3, respectively. Reproduced with permission from Ref. Li et al. (2014). Copyright 2014 Elsevier. (d) TEM image of CeO2 ALD coated LiMn2O4 particles after 100 cycles. Reproduced with permission from Ref. Patel et al. (2015). Copyright 2015 Wiley-VCH. (e) SEM images of a 10 nm Al2O3-coated TiO2 nanotube layer. (f) Galvanostatic cycling at 1C rate of ALD Al2O3-coated TiO2 nanotube with different cycling thickness. Reproduced with permission from Ref. Sopha et al. (2017). Copyright 2017 American Chemical Society.
Moreover, Patel et al. (2015) reports that with increased ALD cycles, the thickness value of the coating layers is increased and the thickness variation of the ZrO2 coatings with different ALD cycles can be observed. The study results show that coating an ultrathin conformal cerium dioxide (CeO2) with the ALD technique on the surface of LMO particles generates the optimized LMO particles which exhibits a significant improvement on performance compared with uncoated, Al2O3 coated LMO, and ZrO2 coated LMO samples. The TEM image of CeO2 ALD coated LMO particles after 100 cycles (shown in Figure 8d) is obtained (Patel et al., 2015). It can be seen that the distinctive conformal coating is coated and the thickness of CeO2 film in 100 cycles is thicker. According to electrochemical tests, the capacity of the CeO2 coated samples after 50 ALD cycles is increased by 24% compared to the bare one, and 96% and 95% capacity retention at room temperature and 55°C respectively is displayed with 1C rate after 1,000 cycles. The SEI layer is formed on the surface of anode materials while the cathode can affect the component of SEI. The surface film formed on the cathode particles is called a solid permeable interface (SPI) layer (Edström et al., 2004), as well as CEI mentioned above, which can keep increasing with time. Similar with the formation of SEI, the process of SPI also consumes Li-ions and solution. Notably, the ALD CeO2 coating is regarded as artificial SEI film, thereby further formation of SEI is suppressed. In addition, the thickness of the CeO2 is thicker than that of the initial thin SPI layer, thus further growing of the SPI layer is prevented. By the modification of ALD CeO2 film, the slower rate of impedance rise and the smoother ion transport optimize the LMO cathode (Patel et al., 2015).
Nanoscale modified electrode materials, like hollow nanospheres, nanosheets, nanotubes, and porous nanofiber, have unique advantages including well conductivity, improved specific capacity, and rate performance, which originate from its nanometer level, so coated nanomaterial electrode via ALD is popularly researched. Similarly, nitrogen-doped carbon nanotubes (NCNTs) modified by the amorphous FePO4 ALD coating is studied. After 500 ALD FePO4 cycles, the cathode material on NCNTs delivers a satisfying battery activity and its discharge capacity reaches up to 141 mAh/g at 1C with 100 ALD cycles (Liu J. et al., 2015). In the nanoscope, the nanotubes can be reformed to work as the cathode might as well for the anode. Sopha et al. (2017) suggests ALD Al2O3 coatings of different thickness are utilized to the TiO2 nanotube layer as the anode material and the generated superior interface performance for LIBs. The SEM image of 10 nm Al2O3-coated TiO2 nanotube layer is shown in Figure 8e, thin and uniform layers of Al2O3-coated can be observed on the inside and outside of nanotubes. If the coating is very thin, the formation of SEI is suppressed and side reactions are decreased. It is reported that even when a cycling test was performed at >1 V potential, the ultra-thin SEI layers would be formed on TiO2 anodes. It can be observed from Figure 8f that for the uncoated TiO2 nanotube layers, the first cycle capacity is low due to the form of thin SEI. In contrast, the capacity loss is more pronounced for the thick ALD Al2O3-coated nanotube (>2 nm) layers blocking the electrode surface. Compared to the uncoated one, however, electrodes with ultrathin Al2O3 film (∼1 nm) receive a superior performance. Hence, a thin and conformal coating for interface modification can significantly optimize the TiO2 nanotubes as electrodes (Sopha et al., 2017). Likewise, the nanometer-scale TiN (Kohandehghan et al., 2013) coating and TiO2 (Memarzadeh Lotfabad et al., 2013) coating via ALD can be deposited on silicon nanowire for LIBs anode and limit the growth of SEI.
As mentioned before, 3D materials used as substrates can release tremendous potential which have high chemical activity and are thoroughly contacted with electrolyte liquid due to the integrated conductive network. Performing innovative modifications on 3D-nanoscale electrode surfaces is interesting. Dhara et al. (2017) report a new 3D core-shell structure prepared by conducting carbon nanotube (CNT) with ALD amorphous MoOx coating. Combined with the advanced technology, the plasma enhanced ALD (PEALD) process has been rapidly gaining interest from researchers along with the improvement on controlling the thickness of ultra-thin coating and the enhancement on the uniformity of high deposition rate per cycle (Ji et al., 2015; Dobbelaere et al., 2016, 2017). As a derivative of ALD, the reactants in PEALD are activated by the plasma source that the higher reaction activity can be obtained during deposition. In terms of crystallinity, density, and purity, the film created by PEALD is better compared with the non-plasmatic ALD and is more economically viable (Park et al., 2001; Song et al., 2012). There is a relevant report that introduces the process of the deposited titanium phosphate thin films by PEALD. Utilizing the two techniques, ex situ X-ray reflectometry and in situ spectroscopic ellipsometry, to characterize the complex process and the conformality which manifests on the deposition on micropillars (Dobbelaere et al., 2017). The thickness of coatings deposited by self-limiting ALD cycles can reach up to the sub-nano level and as low as the angstrom level (Alaboina et al., 2017). Although the increasing number of ALD cycles can bring thicker surface coatings, the coatings become thick when the surface impedance is rising and Li-ion diffusion rate is falling. The obtained surface property is mostly determined by the process of ALD and the ALD technique has evident advantages on the homogeneity, coverage, and thickness control of electrode surfaces.
Composite electrode materials including anode and cathode are both increasingly highlighted. For anode materials, the actual volume ratio of the positive electrode is higher than that of the negative electrode. Therefore, in order to further improve the specific energy of the battery, the key point of researching is to improve the performance of lithium embedded in the cathode material. And with the increasing popularity of electronic products, the need for high specific energy batteries is increasing. At present, a single material cannot fully meet the relevant needs. Although carbon materials have good cycling performance, its specific capacity is low. Other electrochemical properties of carbon materials with high specific capacity are also impaired. The alloy material has a high specific energy, however, the cycling performance of the material is far from satisfying the requirements because of the large volume expansion during the lithium embedding process. In this way, it is a reasonable choice to combine the advantages of various materials, purposefully compound all kinds of materials, and avoid their disadvantages, and form composite anode materials. Nowadays, some representative composite anode materials are vigorously studied including Si/C (Hu et al., 2019), Si/graphite (Zhao Q. et al., 2017), and metal oxide/carbon (Yang et al., 2011) material. When the electrode is designed into the composite, the surface of the electrode as well as the electrode-electrolyte interface is correspondingly improved. The chemical properties and interface structure, such as interface energy, surface stability, and pore density, can make a difference. The components and structure of SEI layer are also reconstructed.
Liu Y. et al. (2019) prepared a new SiOx/C composite with a dual interface via a sol-gel method by redox reaction, and the final composite structure exhibits that the dual interface has an intermediate layer and a carbon coating layer outside the SiOx matrix, from the Figure 9a. For exploring the construction process and the most optimized condition, several groups samples are prepared by changing the components of the precursor as comparison. The sample without hydrogen peroxide is labeled as SiOx/C-1; the sample that replaced hydrogen peroxide with an equal amount of ammonia water is labeled as SiOx/C-2; and the influence from the change of sucrose carbon is also researched. Compared with SiOx/C-1 and SiOx/C-2 without the dual interface, the SiOx/C particles were well dispersed and filled with pore channels because the decomposing hydrogen peroxide generated gas prevented agglomeration between particles. From the HRTEM image in Figures 9b,c, the distinct middle layer appeared between the SiOx matrix and carbon coating. The thickness of this layer with unique microstructure is about 10–20 nm and the thickness of the carbon layer is about 3–15 nm. The dual interface layer can provide a strong buffering effect, from the similar values of RSEI in EIS plots, additionally it is obvious that the stable SEI film is formed even after 200 cycles and the interface structure effectively restrains volume expansion.
Figure 9. The details for the preparation and structure of the dual interface SiOx/C composite. (a) Schematic illustration for the preparation of the SiOx/C composite. (b,c) TEM and HRTEM image of the double layer interface structure. Reproduced with permission from Ref. Liu Y. et al. (2019). Copyright 2019 Elsevier.
LiFePO4 is used as a potential cathode material, while the low electronic conductivity and ion diffusion rate of it leads to poor practical application. For designing superior LFP as cathode material in LIBs, many modified methods develop their value as follows. A self-supported ultrahigh-capacity and fire-resistant LiFePO4 (UCFR-LFP) based nanocomposite cathode has been reported recently. Through the synergistic interaction of all building blocks, layer structures with high electronic conductivity and close proximity to liquid electrolytes are reasonably produced rather than randomly stacked together. Compared with conventional LFP (Con-LFP), UCFR-LFP composite cathodes present the improvement in electrochemical performance, mass loading, thermal stability, and high temperature operability of active materials (Li H. et al., 2019). Lin et al. (2008) proposed another composite method based on LFP-carbon coating and the obtained carbon coated LFP (LFP/C) presents increased reaction kinetics and the favorable deinsertion/insertion condition of Li-ions. Under the reductive sintering atmosphere, the iron phosphides highly improve the bulk conductivity generated. The analysis shows that both the reduction of particle size caused by carbon coating and the appropriate amount of iron phosphides commonly determine the quality of LFP/C. Likewise for improving the LiFePO4 nanocomposite cathode, the porous carbon-coated LFP nanocrystals can be efficiently used as new cathode materials. And the activated porous carbon coated LFP (LFP/AC-P4) presents the increased Li-ions diffusion coefficient and low charge transfer resistance (Tian et al., 2020). Hence, it is disclosed that carbon coating is an important method to fabricate composites, which is able to be achieved by introducing a carbon source, such as graphene oxide (GO) (Huo et al., 2017), glucose (Zhang et al., 2017; Li Y. et al., 2019; Wang M. et al., 2019; He et al., 2020), sucrose (Chen et al., 2019; Park et al., 2019), pitch (Hsieh and Liu, 2020), cotton (Deng et al., 2019), ethylene glycol (Lin et al., 2008), and methyl orange (Yan et al., 2019), as raw materials. Besides, in the field of all-solid-state batteries, except the reconstruction of composite electrode materials, the controllable adjustment to composite solid electrolytes can effectively optimize the electrolyte interface. Shi et al. (2020) proposed an “in situ LiF nanodecoration” method to improve the unstable solid interface. More specifically, after solid-state reaction the obtained ultrafine LiF particles can uniformly disperse in the amorphous Li2B12H12 matrix and thereby the nanocomposite electrolyte shows the favorable ion conductivity and electrode compatibility. In Figure 10A, the interface model for the stability mechanism is constructed vividly, which indicates diminishing Li dendrite and the reduction of interfacial resistance produces the stable electrode-electrolyte interface owing to the LiF nanoparticles.
Figure 10. Schematic illustration of electrode-electrolyte interface structure. (A) Schematic illustration for the functioning mechanism of the interface with composite solid electrolyte via in situ LiF nano-decoration of Li2B12H12. Ref. Shi et al. (2020). Copyright 2020 Elsevier. (B) Schematic illustration for the possible LVP-carbon interfacial structure of LVP/C composites. Reproduced with permission from Ref. Huo et al. (2019). Copyright 2019 American Chemical Society.
The surface coating of the carbon layer as a conducting layer not only improves the electrochemical performance of the material, but also inhibits the agglomeration of electrode material particles and improve the utilization rate of active substances. In addition, the carbon layer as a buffer layer can relieve the stress caused by the volume expansion and contraction of the material and decrease the thickness of the SEI layer and electrolyte dissolution. Li3V2(PO4)3 (LVP) as one of the cathode materials in LIBs achieves intense attention due to its higher charge-discharge voltage and thermodynamically stable structure. Huo et al. (2019) designed different phosphate/carbon composites by introducing different carbon sources. In their experiment, citric acid (CA) is the carbon source as well as chelating agent for the composite LVP/CA; the denoted composite LVP/Glu, LVP/GO, LVP/G, and LVP/SP are synthesized with glucose, graphene oxide, graphene, and super P as carbon sources, respectively. The morphology and structure of the LVP-carbon interface are controlled by the electrostatic interaction between the LVP building units and the electronegative groups of carbon source molecules. As shown in Figure 10B, a schematic model of LVP-carbon interfacial structure is put forward. According to this model, on the interface, the LVP particles are coated with three layers/components which are the protective/wetting layer, the conductive layer, and the capacitive/buffering carbon layer respectively, as marked in the figure. The above three components in the carbon layers are described in detail. For a protective/wetting layer, the formation of it can be shown below: the strong attraction effect of -COOH groups in the carbon source makes the species constituting the layer aggregate on the interface. And these species can protect LVP from electrolytes because they are Li-ion conductors inhibiting other ions passing and provide the Li-ion pathway. For a capacitive/buffering layer, it consists of porous carbon layers which can absorb the Li-ion and reduce the potential loss due to fast ion reinsertion. Furthermore, for the key layer generated by graphitization of the carbon source as well as a conductive layer of sp2 carbon, it has a significant effect on fast ion pathway. By carbon coating introducing the carbon source, the carbon-transition metal phosphate interface in the composite cathode is reasonably controlled and designed. On the one hand, carbon coating in composite electrodes can improve the conductivity of the interface. On the other hand, the stable electrochemical reaction interface can be provided by the coating layer. However, the overlarge amount of carbon coating makes the density of composite electrodes light and the overthick or overthin coating layer also deteriorates the overall performance.
The doping method is thought to develop a greater effect in carbon coating. Atom doping is a crucial technique on improving electrode performance for LIBs. After doping the lattice, atoms can make the ion channel larger and enhance the conductivity by changing the lattice and increasing the dislocation (Wang et al., 2014). Combining the technique of carbon coating with atom doping can comprehensively concentrate the two advantages, and the doped atom can form the non-intrinsic and disordered carbon structure improving electrochemical activity of the carbon material, all of which makes a contribution to the electrode performance. Non-metal doping is more common than metal doping because the metals can easily react with the substance of electrode materials, produce lattice defects, and even break the performance. In non-metal doping combined with carbon coating, N doping (Duan et al., 2019; Jiang et al., 2019; Liu X. et al., 2019; Nanthagopal et al., 2019; Park et al., 2019; Sun et al., 2019; Wang Y. et al., 2019) is proven to result in a better effect, followed by P doping (Zhang et al., 2019). Na doping (Yan et al., 2019) as the metal doping is also widely applied. For LFP as typical cathode materials, after the simple surface carbon coating modification, if the charge distribution on the electrode surface is not uniform under the condition of high rate charge and discharge, the utilization efficiency of active substance would decrease. It is indicated that depositing C and N elements on the LFP electrode surface can form a continuous electron conductance layer, which improves the rate performance. Therefore, an N-doped carbon coating layer for LFP cathode attracts more attention. Jiang et al. (2019) exploits a nitrogen-doped carbon (N-C) coating method with dopamine as a nitrogen-carbon source by spray-drying to obtain the N-C@LiFePO4 spherical cathode. Experimental results verify that 5% N-C@LFP delivers a superior performance. In another report, with an in situ plasma method antisite defectless LFP nanoparticles deposited by nitrogen-doped carbon coating and supported by a graphitic nanosheet (LFP@NC-GNS) is produced successfully as a cathode material (Wang Y. et al., 2019). The surface of the LiNi0.8Co0.1Mn0.1O2 cathode is modified by nitrogen-doped carbon coating (NC@NCM811) and dopamine hydrochloride is the NC coating source. A thin N-C layer is coated on the NCM811 surface. From the HR FE-SEM pictures, the modified particles possess a spherical morphology and the surface texture becomes rough with the increasing content of N and C. Through choosing optimal coating of NC, the surface degradation and acid attack are prevented (Nanthagopal et al., 2019). For metal doping, Na-doped carbon-coated Li3–xNaxV2(PO4)3/C as the cathode with a well crystallized structure is obtained. The optimal result displays that the synergetic effect between Na-doping and carbon coating offers enlarged Li+ diffusion channels. The doped Na can substitute the surface active sites and the coated carbon increases the electronic connecting of particles (Yan et al., 2019).
Using carbon coating for surface treatment generates different structures among various composites, such as yolk-shell-structured microspheres (Park et al., 2019) (Figures 11A,B), core-shell structure (Duan et al., 2019; Zhang et al., 2019), sandwich structure (Li Y. et al., 2019) (Figure 11C), double core-shell structure (Hsu et al., 2020), and other nanoscale porous structures (Deng et al., 2019; Zheng et al., 2019; Tian et al., 2020) (Figure 11D). These structures also lead to the change of surface morphology and property of the electrode, so the analysis of surface-interface is extremely necessary. In the numerous nanoscale structures, a carbon coated porous Co3O4 nanosheet is prepared via a cotton template route and at the first cycle a superior capacity of 1,735.4 mAh/g when the current density is 200 mA/g is obtained. As the cycle number increases, the surface morphology of coated Co3O4 would change. After the first cycle, the surface structure gradually appeared to have a coralloid-like morphology and formation of SEI film. After the 50th cycle, the coralloid-like structure of all the porous nanosheets opened to form more enlarged empty spaces and SEI film became more unbroken, additionally, by the analysis of EIS, the surface film is also more stable. The uniform coating layer is around 2 nm thick with porous structure, which possesses a larger specific surface area promoting diffusion rate of Li-ions and increases numerous active sites. Furthermore, the enlarged empty space is conductive to the diffusion between the electrolyte and electrode and the growing of the SEI film on the interface, thereby the superior performance is obtained (Deng et al., 2019). The coating layer has the characteristics of porous nanostructure and carbon ingredients. The porous structure can create the larger surface area and make the ion diffusion distance shorter, and the carbon coating enhances surface conductivity and prevents the inner deterioration as the buffer layer. Therefore, after this contributing equipment, the modified surface of electrode materials can play an important role in the battery.
Figure 11. The structure models and formation mechanism of various composite electrodes by surface carbon coating with representative structure. (A) N-doped carbon coated hollow NiMoO4 nanospheres with yolk-shell structure. Reproduced with permission from Ref. Park et al. (2019). Copyright 2019 Royal Society of Chemistry. (B) Si/C composites with yolk-shell structure. Reproduced with permission from Ref. Hu et al. (2019). Copyright 2018 Elsevier. (C) OM-Si@C composites with core-shell structure. Reproduced with permission from Ref. Duan et al. (2019). Copyright 2019 Elsevier. (D) The nanoscale porous CNFs electrode with successive electron and Li+ transfer channels. Reproduced with permission from Ref. Zheng et al. (2019). Copyright 2019 Elsevier.
In conclusion, the surface and interface of electrode materials are not the basic components but are extremely important functional layers even in the main structure in the batteries. Through the liquid electrolytes, Li-ions transfer smoothly, arriving at the surface of the electrode and embedding in the inner layer structure, making the charge-discharge process proceed successfully. Moreover, most electrochemical reactions develop the effect on the surface and interface along with the generation and growth of SEI film determining the interface property. It can be concluded that surface modification and design has taken us closer to realizing high-enhanced performance LIBs. In this article, we give a brief comprehension about the features and importance of solid-liquid interfaces and introduced SEI film growing on the electrode surface. Focusing on the effort to improve performance of LIBs by the modification of the surface of electrode materials, the design methods are summarized. By adding electrolyte additives, the electrolyte components make a difference conducting a series of interactions with the surface of electrode materials. Among them, film-forming additives can change the SEI film potential and reduce potential due to its strong electron-withdrawing ability, inhibiting the co-embedding of Li-ions and optimizing the formation of surface film. Anion receptors can form complexes with lithium salt anions which reduces the interaction between Li+ and anions and side reactions on the electrolyte interface, making the conductivity of the electrolyte enhanced. Choosing the appropriate co-solvent to adjust the electrolyte is also proven to be efficient in modifying the interface. The interface property depends on the surface of electrode material particles to a high degree, further, surface coating is a proven way to monitor the surface structure of electrodes. Modifying the electrode-electrolyte interface using the coating layer can stabilize the surface structure of electrodes and attenuate the SEI layer. Metal oxide as the surface coating layer, not interacting with active substances, has attracted more attention due to its stability and safety. However, the insulate metal oxide coating suppresses the surface mass transportation and conductivity, so the lithium-ion-conductive-materials and electronic conductive materials are modified on the surface as coating layers. Meanwhile, as an important kind of surface coating, thin-film deposition on the surface of electrodes via the ALD technique particularly is mainly reviewed and the modification of the PEALD method is also briefly referred. Composite electrode materials can be prepared via various approaches that the alteration of inner structure and components on electrode must influence the surface, accordingly the multiple surface structure is created. Among the composite methods as well as the surface coating technique, carbon coating is widely applied, and the obtained porous surface structure not only increases the active sites but also provides the convenient diffusion for Li-ions. Based on the carbon coating, the atom doping carbon-coated layer develops the greater effects represented by the doping of the N element. Combining the respective advantages can prompt the electrode to possess a superior surface and suitable, stable SEI film. Although there is a tremendous amount of studies about surface and interface in LIBs, the relationship and boundary of surface, interface, and SEI film are ambiguous. Specifically, it is a certain distance away from the precise comprehension of SEI that includes its conductivity, mechanical behavior, cover degree, and electrochemical stability. Except the Li-ions batteries, other energy-storage ion batteries emerge and developed recently, such as K-ions batteries, Na-ions batteries, Al-ions batteries, and Ca-ions batteries. For potassium ion batteries (KIBs), due to the high abundance and low cost of potassium in the earth’s crust, they have recently attracted more attention in the field of energy storage. However, the development is still in its infancy. As a result, the research of surface-interface for other secondary batteries are more infrequent than LIBs and it will take time to have a good knowledge of them. So it is necessary to develop surface-interface research with liquid electrolytes for more secondary batteries by exploring electrode materials with good properties and studying the corresponding storage mechanism. Besides, during the charge-discharge cycling process, lithium ions can deposit preferentially at the bulge on the surface of lithium metal to form lithium dendrites, which also poses a greater difficulty in interfacial safety. However, it is the challenges, possibilities, and unknowns of the interface condition of LIBs, that prove that even more energy batteries deserve to be fully explored. Finally, LIBs still present an enormous potential in the field of both scientific research and commercial production, and focusing on a rechargeable battery with a high energy density, high safety, low cost, and long cycling life is significant.
All authors listed have made a substantial, direct and intellectual contribution to the work, and approved it for publication.
This work was supported by the National Natural Science Foundation of China (21975283 and U1730136), the Natural Science Foundation of Jiangsu Province (Grant No. BK20191343), and the CAS Key Laboratory of Carbon Materials (No. KLCMKFJJ2010).
The authors declare that the research was conducted in the absence of any commercial or financial relationships that could be construed as a potential conflict of interest.
Abe, Y., Hori, N., and Kumagai, S. (2019). Electrochemical impedance spectroscopy on the performance degradation of LiFePO4/Graphite Lithium-ion battery due to charge-discharge cycling under different C-Rates. Energies 12:4507. doi: 10.3390/en12234507
Alaboina, P. K., Uddin, M.-J., and Cho, S.-J. (2017). Nanoprocess and nanoscale surface functionalization on cathode materials for advanced lithium-ion batteries. Nanoscale 9, 15736–15752. doi: 10.1039/C7NR02600E
Aurbach, D., Gamolsky, K., Markovsky, B., Gofer, Y., Schmidt, M., and Heider, U. (2002). On the use of vinylene carbonate (VC) as an additive to electrolyte solutions for Li-ion batteries. Electrochim. Acta 47, 1423–1439. doi: 10.1016/S0013-4686(01)00858-1
Busche, M. R., Drossel, T., Leichtweiss, T., Weber, D. A., Falk, M., Schneider, M., et al. (2016). Dynamic formation of a solid-liquid electrolyte interphase and its consequences for hybrid-battery concepts. Nat. Chem. 8, 426–434. doi: 10.1038/nchem.2470
Cano, Z. P., Banham, D., Ye, S., Hintennach, A., Lu, J., Fowler, M., et al. (2018). Batteries and fuel cells for emerging electric vehicle markets. Nat. Energy 3, 279–289. doi: 10.1038/s41560-018-0108-1
Chang, Q., Wei, A., Li, W., Bai, X., Zhang, L., He, R., et al. (2019). Structural and electrochemical characteristics of Al2O3-modified LiNi0.5Mn1.5O4 cathode materials for lithium-ion batteries. Ceram. Int. 45, 5100–5110. doi: 10.1016/j.ceramint.2018.11.213
Chen, S., Duan, H., Zhao, L., Zhao, Y., Gupta, A., Kuang, Q., et al. (2019). Electrochemical performance and Li+ insertion/extraction mechanism of carbon-coated cerium metavanadate as a novel anode for lithium-ion batteries. J. Power Sour. 413, 250–258. doi: 10.1016/j.jpowsour.2018.12.053
Chen, S., Zheng, J., Mei, D., Han, K. S., Engelhard, M. H., Zhao, W., et al. (2018a). High-voltage lithium-metal batteries enabled by localized high-concentration electrolytes. Adv. Mat. 30:1706102. doi: 10.1002/adma.201706102
Chen, S., Zheng, J., Yu, L., Ren, X., Engelhard, M. H., Niu, C., et al. (2018b). High-efficiency lithium metal batteries with fire-retardant electrolytes. Joule 2, 1548–1558. doi: 10.1016/j.joule.2018.05.002
Chen, Z., Wang, Q., and Amine, K. (2006). Understanding the stability of aromatic redox shuttles for overcharge protection of lithium-ion cells. J. Electrochem. Soc. 153:A2215. doi: 10.1149/1.2352048
Chung, K. Y., Yoon, W.-S., Lee, H. S., McBreen, J., Yang, X.-Q., Oh, S. H., et al. (2006). In situ XRD studies of the structural changes of ZrO2-coated LiCoO2 during cycling and their effects on capacity retention in lithium batteries. J. Power Sour. 163, 185–190. doi: 10.1016/j.jpowsour.2005.12.063
Ciosek Högström, K., Malmgren, S., Hahlin, M., Rensmo, H., Thébault, F., Johansson, P., et al. (2013). The influence of PMS-Additive on the electrode/electrolyte interfaces in LiFePO4/Graphite Li-Ion batteries. J. Phys. Chem. C 117, 23476–23486. doi: 10.1021/jp4045385
Deng, J., Lv, X., Zhong, J., and Sun, X. (2019). Carbon coated porous Co3O4 nanosheets derived from cotton fibers as anodes for superior lithium ion batteries. Appl. Surf. Sci. 475, 446–452. doi: 10.1016/j.apsusc.2018.12.232
Deng, M.-M., Tang, Z.-F., Shao, Y., He, X.-D., Wen, Z.-Y., and Chen, C.-H. (2018). Enhancing the electrochemical performances of LiNi0.5Mn1.5O4 by Co3O4 surface coating. J. Alloys Comp. 762, 163–170. doi: 10.1016/j.jallcom.2018.05.245
Dhara, A., Sarkar, S. K., and Mitra, S. (2017). Controlled 3D carbon nanotube architecture coated with MoOx Material by ALD technique: a high energy density lithium-ion battery electrode. Adv. Mater. Interf. 4:1700332. doi: 10.1002/admi.201700332
Dobbelaere, T., Mattelaer, F., Dendooven, J., Vereecken, P. M., and Detavernier, C. (2016). Plasma-enhanced atomic layer deposition of iron and titanium phosphates as electrode materials for 3D-Structured lithium-ion microbatteries. ECS Trans. 75, 35–44. doi: 10.1149/07506.0035ecst
Dobbelaere, T., Mattelaer, F., Roy, A. K., Vereecken, P., and Detavernier, C. (2017). Plasma-enhanced atomic layer deposition of titanium phosphate as an electrode for lithium-ion batteries. J. Mater. Chem. A 5, 330–338. doi: 10.1039/C6TA04179E
Dong, Y., Zhao, Y., Duan, H., and Liang, Z. (2014). Enhanced electrochemical performance of LiMnPO4 by Li+-conductive Li3VO4 surface coatings. Electrochim. Acta 132, 244–250. doi: 10.1016/j.electacta.2014.03.171
Duan, Y.-J., Zhao, D.-L., Meng, W.-J., Yang, H.-X., Han, X.-Y., Tian, X.-M., et al. (2019). Ordered mesoporous Si microspheres with nitrogen-doped carbon coating for advanced lithium-ion battery anodes. J. Alloys Comp. 800, 198–207. doi: 10.1016/j.jallcom.2019.06.009
Edström, K., Gustafsson, T., and Thomas, J. O. (2004). The cathode–electrolyte interface in the Li-ion battery. Electrochim. Acta 50, 397–403. doi: 10.1016/j.electacta.2004.03.049
Elam, J. W., Routkevitch, D., Mardilovich, P. P., and George, S. M. (2003). Conformal coating on ultrahigh-aspect-ratio nanopores of anodic alumina by atomic layer deposition. Chem. Mater. 15, 3507–3517. doi: 10.1021/cm0303080
Etacheri, V., Haik, O., Goffer, Y., Roberts, G. A., Stefan, I. C., Fasching, R., et al. (2012). Effect of fluoroethylene carbonate (FEC) on the performance and surface chemistry of si-nanowire li-ion battery anodes. Langmuir 28, 965–976. doi: 10.1021/la203712s
Fang, X., Ge, M., Rong, J., Che, Y., Aroonyadet, N., Wang, X., et al. (2014). Ultrathin surface modification by atomic layer deposition on high voltage cathode LiNi0.5Mn1.5O4 for lithium ion batteries. Energy Technol. 2, 159–165. doi: 10.1002/ente.201300102
Fu, Q., Du, F., Bian, X., Wang, Y., Yan, X., Zhang, Y., et al. (2014). Electrochemical performance and thermal stability of Li1.18Co0.15Ni0.15Mn0.52O2 surface coated with the ionic conductor Li3VO4. J. Mater. Chem. A 2, 7555–7562. doi: 10.1039/C4TA00189C
Gao, J., Yuan, T., Luo, S., Ruan, J., Sun, H., Yang, J., et al. (2020). Boosting lithium ion storage of lithium nickel manganese oxide via conformally interfacial nanocoating. J. Colloid Interf. Sci. 570, 153–162. doi: 10.1016/j.jcis.2020.02.112
Guo, J., Li, Y., Chen, Y., Deng, S., Zhu, J., Wang, S., et al. (2019). Stable interface Co3O4-coated LiNi0.5Mn1.5O4 for lithium-ion batteries. J. Alloys Comp. 811:152031. doi: 10.1016/j.jallcom.2019.152031
He, F., Xu, Q., Zheng, B., Zhang, J., Wu, Z., Zhong, Y., et al. (2020). Synthesis of hierarchical Sn/SnO nanosheets assembled by carbon-coated hollow nanospheres as anode materials for lithium/sodium ion batteries. RSC Adv. 10, 6035–6042. doi: 10.1039/C9RA08897K
Heiskanen, S. K., Kim, J., and Lucht, B. L. (2019). Generation and evolution of the solid electrolyte interphase of lithium-ion batteries. Joule 3, 2322–2333. doi: 10.1016/j.joule.2019.08.018
Hsieh, C.-C., and Liu, W.-R. (2020). Carbon-coated Si particles binding with few-layered graphene via a liquid exfoliation process as potential anode materials for lithium-ion batteries. Surf. Coat. Technol. 387:125553. doi: 10.1016/j.surfcoat.2020.125553
Hsu, Y.-C., Hsieh, C.-C., and Liu, W.-R. (2020). Synthesis of double core-shell carbon/silicon/graphite composite anode materials for lithium-ion batteries. Surf. Coat. Technol. 387:125528. doi: 10.1016/j.surfcoat.2020.125528
Hu, L., Luo, B., Wu, C., Hu, P., Wang, L., and Zhang, H. (2019). Yolk-shell Si/C composites with multiple Si nanoparticles encapsulated into double carbon shells as lithium-ion battery anodes. J. Energy Chem. 32, 124–130. doi: 10.1016/j.jechem.2018.07.008
Huo, H., Lin, Z., Guo, S., Shao, J., Zhang, G., and Wang, Q. (2017). Roles of coating carbon, conductive additive and binders in lithium vanadium phosphate/reduced graphene oxide composite cathodes. New J. Chem. 41, 14228–14235. doi: 10.1039/C7NJ02821K
Huo, H., Lin, Z., Wu, D., Zhong, G., Shao, J., Xu, X., et al. (2019). Investigating the Structure of an active material–carbon interface in the monoclinic Li3V2(PO4)3/C Composite Cathode. ACS Appl. Energy Mater. 2, 3692–3702. doi: 10.1021/acsaem.9b00410
Itagaki, M., Yotsuda, S., Kobari, N., Watanabe, K., Kinoshita, S., and Ue, M. (2006). Electrochemical impedance of electrolyte/electrode interfaces of lithium-ion rechargeable batteries: effects of additives to the electrolyte on negative electrode. Electrochim. Acta 51, 1629–1635. doi: 10.1016/j.electacta.2005.02.136
Jeong, S.-K., Inaba, M., Mogi, R., Iriyama, Y., Abe, T., and Ogumi, Z. (2001). Surface film formation on a graphite negative electrode in lithium-ion batteries:? atomic force microscopy study on the effects of film-forming additives in propylene carbonate solutions. Langmuir 17, 8281–8286. doi: 10.1021/la015553h
Ji, S., Cho, G. Y., Yu, W., Su, P.-C., Lee, M. H., and Cha, S. W. (2015). Plasma-enhanced atomic layer deposition of nanoscale yttria-stabilized zirconia electrolyte for solid oxide fuel cells with porous substrate. ACS Appl. Mater. Interf. 7, 2998–3002. doi: 10.1021/am508710s
Jiang, Z., Zhang, B., Shen, Q., and Jiang, Z.-J. (2019). In-situ plasma assisted formation of graphitic nanosheet supported N-doped carbon-coated antisite defectless LiFePO4 as a high-performance cathode material for lithium-ion batteries. J. Alloys Comp. 806, 864–873. doi: 10.1016/j.jallcom.2019.07.309
Kalluri, S., Yoon, M., Jo, M., Liu, H. K., Dou, S. X., Cho, J., et al. (2017). Feasibility of cathode surface coating technology for high-energy lithium-ion and beyond-lithium-ion batteries. Adv. Mater. 29:1605807. doi: 10.1002/adma.201605807
Kim, J. W., Kim, D. H., Oh, D. Y., Lee, H., Kim, J. H., Lee, J. H., et al. (2015). Surface chemistry of LiNi0.5Mn1.5O4 particles coated by Al2O3 using atomic layer deposition for lithium-ion batteries. J. Power Sour. 274, 1254–1262. doi: 10.1016/j.jpowsour.2014.10.207
Knoops, H. C. M., Donders, M. E., Sanden, M. C. M. V. D., Notten, P. H. L., and Kessels, W. M. M. (2012). Atomic layer deposition for nanostructured Li-ion batteries. J./ Vacuum Sci. Technol. A 30:010801. doi: 10.1116/1.3660699
Kohandehghan, A., Kalisvaart, P., Cui, K., Kupsta, M., Memarzadeh, E., and Mitlin, D. (2013). Silicon nanowire lithium-ion battery anodes with ALD deposited TiN coatings demonstrate a major improvement in cycling performance. J. Mater. Chem. A 1, 12850–12861. doi: 10.1039/C3TA12964K
Landschoot, N. V., Kelder, E. M., Kooyman, P. J., Kwakernaak, C., and Schoonman, J. (2004). Electrochemical performance of Al2O3-coated Fe doped LiCoVO4. J. Power Sour. 138, 262–270. doi: 10.1016/j.jpowsour.2004.06.046
Larcher, D., and Tarascon, J. M. (2015). Towards greener and more sustainable batteries for electrical energy storage. Nat. Chem. 7, 19–29. doi: 10.1038/nchem.2085
Lee, J.-I., Ko, Y., Shin, M., Song, H.-K., Choi, N.-S., Kim, M. G., et al. (2015). High-performance silicon-based multicomponent battery anodes produced via synergistic coupling of multifunctional coating layers. Energy Environ. Sci. 8, 2075–2084. doi: 10.1039/C5EE01493J
Li, H., Peng, L., Wu, D., Wu, J., Zhu, Y.-J., and Hu, X. (2019). Ultrahigh-capacity and fire-resistant LiFePO4-Based composite cathodes for advanced lithium-ion batteries. Adv. Energy Mater. 9:1802930. doi: 10.1002/aenm.201802930
Li, X., Liu, J., Meng, X., Tang, Y., Banis, M. N., Yang, J., et al. (2014). Significant impact on cathode performance of lithium-ion batteries by precisely controlled metal oxide nanocoatings via atomic layer deposition. J. Power Sour. 247, 57–69. doi: 10.1016/j.jpowsour.2013.08.042
Li, Y., Wang, R., Zhang, J., Chen, J., Du, C., Sun, T., et al. (2019). Sandwich structure of carbon-coated silicon/carbon nanofiber anodes for lithium-ion batteries. Ceramics Int. 45, 16195–16201. doi: 10.1016/j.ceramint.2019.05.141
Lin, Y., Gao, M. X., Zhu, D., Liu, Y. F., and Pan, H. G. (2008). Effects of carbon coating and iron phosphides on the electrochemical properties of LiFePO4/C. J. Power Sour. 184, 444–448. doi: 10.1016/j.jpowsour.2008.03.026
Lin, Y.-M., Klavetter, K. C., Abel, P. R., Davy, N. C., Snider, J. L., Heller, A., et al. (2012). High performance silicon nanoparticle anode in fluoroethylene carbonate-based electrolyte for Li-ion batteries. Chem. Commun. 48, 7268–7270. doi: 10.1039/C2CC31712E
Liu, J., Xiao, B., Banis, M. N., Li, R., Sham, T.-K., and Sun, X. (2015). Atomic layer deposition of amorphous iron phosphates on carbon nanotubes as cathode materials for lithium-ion batteries. Electrochim. Acta 162, 275–281. doi: 10.1016/j.electacta.2014.12.158
Liu, X., Meng, Y., Li, R., Du, M., Zhu, F., and Zhang, Y. (2019). Nitrogen-doped carbon-coated cotton-derived carbon fibers as high-performance anode materials for lithium-ion batteries. Ionics 25, 5799–5807. doi: 10.1007/s11581-019-03146-7
Liu, Y., Ruan, J., Liu, F., Fan, Y., and Wang, P. (2019). Synthesis of SiOx/C composite with dual interface as Li-ion battery anode material. J. Alloys Comp. 802, 704–711. doi: 10.1016/j.jallcom.2019.06.072
Liu, Y., Wang, Q., Wang, X., Wang, T., Gao, Y., Su, M., et al. (2015). Improved electrochemical performance of Li1.2Ni0.2Mn0.6O2 cathode material with fast ionic conductor Li3VO4 coating. Ionics 21, 2725–2733. doi: 10.1007/s11581-015-1484-1
Matsuoka, O., Hiwara, A., Omi, T., Toriida, M., Hayashi, T., Tanaka, C., et al. (2002). Ultra-thin passivating film induced by vinylene carbonate on highly oriented pyrolytic graphite negative electrode in lithium-ion cell. J. Power Sour. 108, 128–138. doi: 10.1016/S0378-7753(02)00012-5
Mattelaer, F., Vereecken, P. M., Dendooven, J., and Detavernier, C. (2017). The influence of ultrathin amorphous ALD alumina and titania on the rate capability of anatase TiO2 and LiMn2O4 lithium ion battery electrodes. Adv. Mater. Interf. 4:1601237. doi: 10.1002/admi.201601237
McMillan, R., Slegr, H., Shu, Z. X., and Wang, W. (1999). Fluoroethylene carbonate electrolyte and its use in lithium ion batteries with graphite anodes. J. Power Sour. 8, 20–26. doi: 10.1016/S0378-7753(98)00201-8
Memarzadeh Lotfabad, E., Kalisvaart, P., Cui, K., Kohandehghan, A., Kupsta, M., Olsen, B., et al. (2013). ALD TiO2 coated silicon nanowires for lithium ion battery anodes with enhanced cycling stability and coulombic efficiency. Phys. Chem. Chem. Phys. 15, 13646–13657. doi: 10.1039/C3CP52485J
Meng, X., Yang, X.-Q., and Sun, X. (2012). Emerging applications of atomic layer deposition for lithium-ion battery studies. Adv. Mater. 24, 3589–3615. doi: 10.1002/adma.201200397
Nanthagopal, M., Santhoshkumar, P., Shaji, N., Praveen, S., Kang, H. S., Senthil, C., et al. (2019). Nitrogen-doped carbon-coated Li[Ni0.8Co0.1Mn0.1]O2 cathode material for enhanced lithium-ion storage. Appl. Surface Sci. 492, 871–878. doi: 10.1016/j.apsusc.2019.06.242
Nilsen, O., Miikkulainen, V., Gandrud, K. B., Østreng, E., Ruud, A., and Fjellvåg, H. (2014). Atomic layer deposition of functional films for Li-ion microbatteries. Phys. Status Solidi A 211, 357–367. doi: 10.1002/pssa.201330130
Pajkossy, T., and Jurczakowski, R. (2017). Electrochemical impedance spectroscopy in interfacial studies. Curr. Opin. Electrochem. 1, 53–58. doi: 10.1016/j.coelec.2017.01.006
Park, G. D., Hong, J. H., Lee, J.-K., and Kang, Y. C. (2019). Yolk–shell-structured microspheres composed of N-doped-carbon-coated NiMoO4 hollow nanospheres as superior performance anode materials for lithium-ion batteries. Nanoscale 11, 631–638. doi: 10.1039/C8NR08638A
Park, J., Choi, I., Lee, M. J., Kim, M. H., Lim, T., Park, K. H., et al. (2014). Effect of fluoroethylene carbonate on electrochemical battery performance and the surface chemistry of amorphous MoO2 lithium-ion secondary battery negative electrodes. Electrochim. Acta 132, 338–346. doi: 10.1016/j.electacta.2014.03.173
Park, J.-S., Lee, M.-J., Lee, C.-S., and Kang, S.-W. (2001). Plasma-enhanced atomic layer deposition of tantalum nitrides using hydrogen radicals as a reducing agent. Electrochem. Solid State Lett. 4:C17. doi: 10.1149/1.1353160
Park, J. S., Meng, X., Elam, J. W., Hao, S., Wolverton, C., Kim, C., et al. (2014). Ultrathin Lithium-Ion conducting coatings for increased interfacial stability in high voltage lithium-ion batteries. Chem. Mater. 26, 3128–3134. doi: 10.1021/cm500512n
Park, O., Lee, J.-I., Chun, M.-J., Yeon, J.-T., Yoo, S., Choi, S., et al. (2013). High-performance Si anodes with a highly conductive and thermally stable titanium silicide coating layer. RSC Adv. 3, 2538–2542. doi: 10.1039/C2RA23365G
Patel, R. L., Xie, H., Park, J., Asl, H. Y., Choudhury, A., and Liang, X. (2015). Significant capacity and cycle-life improvement of lithium-ion batteries through ultrathin conductive film stabilized cathode particles. Adv. Mater. Interf. 2:1500046. doi: 10.1002/admi.201500046
Puurunen, R. L. (2005). Surface chemistry of atomic layer deposition: a case study for the trimethylaluminum/water process. J. Appl. Phys. 97:121301. doi: 10.1063/1.1940727
Rajput, N. N., Seguin, T. J., Wood, B. M., Qu, X., and Persson, K. A. (2018). Elucidating solvation structures for rational design of multivalent electrolytes—a review. Top. Curr. Chem. 376:19. doi: 10.1007/s41061-018-0195-2
Shen, L., Wang, Z., and Chen, L. (2014). Carbon-coated hierarchically porous silicon as anode material for lithium ion batteries. RSC Adv. 4, 15314–15318. doi: 10.1039/C4RA01255K
Shi, X., Pang, Y., Wang, B., Sun, H., Wang, X., Li, Y., et al. (2020). In situ forming LiF nanodecorated electrolyte/electrode interfaces for stable all-solid-state batteries. Mater. Today Nano 10:100079. doi: 10.1016/j.mtnano.2020.100079
Song, S. J., Lee, S. W., Kim, G. H., Seok, J. Y., Yoon, K. J., Yoon, J. H., et al. (2012). Substrate dependent growth behaviors of plasma-enhanced atomic layer deposited nickel oxide films for resistive switching application. Chem. Mater. 24, 4675–4685. doi: 10.1021/cm302182s
Sopha, H., Salian, G. D., Zazpe, R., Prikryl, J., Hromadko, L., Djenizian, T., et al. (2017). ALD Al2O3-Coated TiO2 nanotube layers as anodes for lithium-ion batteries. ACS Omega 2, 2749–2756. doi: 10.1021/acsomega.7b00463
Steinhauer, M., Risse, S., Wagner, N., and Friedrich, K. A. (2017). Investigation of the Solid electrolyte interphase formation at graphite anodes in lithium-ion batteries with electrochemical impedance spectroscopy. Electrochim. Acta 228, 652–658. doi: 10.1016/j.electacta.2017.01.128
Sun, P., Ma, Y., Zhai, T., and Li, H. (2016). High performance LiNi0.5Mn1.5O4 cathode by Al-coating and Al3+-doping through a physical vapor deposition method. Electrochim. Acta 191, 237–246. doi: 10.1016/j.electacta.2016.01.087
Sun, W., Zhang, Y., and Wang, Y. (2019). Nitrogen-doped carbon-coated bimetal selenides for high-performance lithium-ion storage through the self-accommodation of volume change. ChemElectroChem 6, 3736–3741. doi: 10.1002/celc.201900848
Tai, Z., Wei, J., Zhou, J., Liao, Y., Wu, C., Shang, Y., et al. (2020). Water-mediated crystallohydrate–polymer composite as a phase-change electrolyte. Nat. Commun. 11:1843. doi: 10.1038/s41467-020-15415-5
Tao, S., Kong, F., Wu, C., Su, X., Xiang, T., Chen, S., et al. (2017). Nanoscale TiO2 membrane coating spinel LiNi0.5Mn1.5O4 cathode material for advanced lithium-ion batteries. J. Alloys Comp. 705, 413–419. doi: 10.1016/j.jallcom.2017.02.139
Teranishi, T., Yoshikawa, Y., Yoneda, M., Kishimoto, A., Halpin, J., O’Brien, S., et al. (2018). Aluminum interdiffusion into LiCoO2 using atomic layer deposition for high rate lithium ion batteries. ACS Appl. Energy Mater. 1, 3277–3282. doi: 10.1021/acsaem.8b00496
Tian, X., Chen, W., Jiang, Z., and Jiang, Z.-J. (2020). Porous carbon-coated LiFePO4 nanocrystals prepared by in situ plasma-assisted pyrolysis as superior cathode materials for lithium ion batteries. Ionics 26, 2715–2726. doi: 10.1007/s11581-019-03422-6
Tiurin, O., Solomatin, N., Auinat, M., and Ein-Eli, Y. (2020). Atomic layer deposition (ALD) of lithium fluoride (LiF) protective film on Li-ion battery LiMn1.5Ni0.5O4 cathode powder material. J. Power Sour. 448:227373. doi: 10.1016/j.jpowsour.2019.227373
Wang, B., Wang, J., Cao, J., Ge, H., and Tang, Y. (2014). Nitrogen-doped Li4Ti5O12 nanosheets with enhanced lithium storage properties. J. Power Sour. 266, 150–154. doi: 10.1016/j.jpowsour.2014.05.009
Wang, H., Xie, X., Wei, X., Zhang, X., Zhang, J., Huang, Y., et al. (2017). A new strategy to stabilize capacity and insight into the interface behavior in electrochemical reaction of LiNi0.5Mn1.5O4/Graphite system for high-voltage lithium-ion batteries. ACS Appl. Mater. Interf. 9, 33274–33287. doi: 10.1021/acsami.7b08828
Wang, J., Yamada, Y., Sodeyama, K., Chiang, C. H., Tateyama, Y., and Yamada, A. (2016). Superconcentrated electrolytes for a high-voltage lithium-ion battery. Nat. Commun. 7:12032. doi: 10.1038/ncomms12032
Wang, K.-X., Li, X.-H., and Chen, J.-S. (2015). Surface and interface engineering of electrode materials for lithium-ion batteries. Adv. Mater. 27, 527–545. doi: 10.1002/adma.201402962
Wang, M., Yin, L., Li, M., Luo, S., and Wang, C. (2019). Low-cost heterogeneous dual-carbon shells coated silicon monoxide porous composites as anodes for high-performance lithium-ion batteries. J. Colloid Interf. Sci. 549, 225–235. doi: 10.1016/j.jcis.2019.04.076
Wang, Y., Wang, X., Jiang, A., Liu, G., Yu, W., Dong, X., et al. (2019). A versatile nitrogen-doped carbon coating strategy to improve the electrochemical performance of LiFePO4 cathodes for lithium-ion batteries. J. Alloys Comp. 810:151889. doi: 10.1016/j.jallcom.2019.151889
Wu, X., Chen, Y., Xing, Z., Lam, C. W. K., Pang, S.-S., Zhang, W., et al. (2019). Advanced carbon-based anodes for potassium-ion batteries. Adv. Energy Mater. 9:1900343. doi: 10.1002/aenm.201900343
Xiao, B., Liu, J., Sun, Q., Wang, B., Banis, M. N., Zhao, D., et al. (2015). Unravelling the role of electrochemically active FePO4 coating by atomic layer deposition for increased high-voltage stability of LiNi0.5Mn1.5O4 cathode material. Adv. Sci. 2:1500022. doi: 10.1002/advs.201500022
Xie, M., Hu, T., Yang, L., and Zhou, Y. (2016). Synthesis of high-voltage (4.7 V) LiCoO2 cathode materials with Al doping and conformal Al2O3 coating by atomic layer deposition. RSC Adv. 6, 63250–63255. doi: 10.1039/C6RA10531A
Xu, M., Tsiouvaras, N., Garsuch, A., Gasteiger, H. A., and Lucht, B. L. (2014). Generation of cathode passivation films via oxidation of lithium bis(oxalato) borate on high voltage spinel (LiNi0.5Mn1.5O4). J. Phys. Chem. C 118, 7363–7368. doi: 10.1021/jp501970j
Xu, S.-D., Zhuang, Q.-C., Tian, L.-L., Qin, Y.-P., Fang, L., and Sun, S.-G. (2011). Impedance spectra of nonhomogeneous, multilayered porous composite graphite electrodes for li-ion batteries: experimental and theoretical studies. J. Phys. Chem. C 115, 9210–9219. doi: 10.1021/jp107406s
Xu, S.-D., Zhuang, Q.-C., Wang, J., Xu, Y.-Q., and Zhu, Y.-B. (2013). New insight into vinylethylene carbonate as a film forming additive to ethylene carbonate-based electrolytes for lithium-ion batteries. Int. J. Electrochem. Sci. 8, 8058–8076.
Xu, T., Li, Y., Wang, D., Wu, M., Pan, D., Zhao, H., et al. (2018). Enhanced electrochemical performance of LiNi0.5Mn1.5O4 Cathode Material by YPO4 surface modification. ACS Sust. Chem. Eng. 6, 5818–5825. doi: 10.1021/acssuschemeng.7b03935
Yan, X., Xin, L., Wang, H., Cao, C., and Sun, S. (2019). Synergetic effect of Na-doping and carbon coating on the electrochemical performances of Li3–xNaxV2(PO4)3/C as cathode for lithium-ion batteries. RSC Adv. 9, 8222–8229. doi: 10.1039/C8RA10646K
Yang, X., Yang, T., Liang, S., Wu, X., and Zhang, H. (2014). Modification of LiNi0.5Mn1.5O4 high potential cathode from the inner lattice to the outer surface with Cr3+-doping and Li+-conductor coating. J. Mater. Chem. A 2, 10359–10364. doi: 10.1039/C4TA00974F
Yang, Z., Shen, J., and Archer, L. A. (2011). An in situ method of creating metal oxide–carbon composites and their application as anode materials for lithium-ion batteries. J. Mater. Chem. 21, 11092–11097. doi: 10.1039/C1JM10902B
Yuan, L.-X., Wang, Z.-H., Zhang, W.-X., Hu, X.-L., Chen, J.-T., Huang, Y.-H., et al. (2011). Development and challenges of LiFePO4 cathode material for lithium-ion batteries. Energy Environ. Sci. 4, 269–284. doi: 10.1039/C0EE00029A
Zhang, L.-L., Li, Z., Yang, X.-L., Ding, X.-K., Zhou, Y.-X., Sun, H.-B., et al. (2017). Binder-free Li3V2(PO4)3/C membrane electrode supported on 3D nitrogen-doped carbon fibers for high-performance lithium-ion batteries. Nano Energy 34, 111–119. doi: 10.1016/j.nanoen.2017.02.026
Zhang, M., Yu, J., Ying, T., Yu, J., Sun, Y., and Liu, X. (2019). P doped onion-like carbon layers coated FeP nanoparticles for anode materials in lithium ion batteries. J. Alloys Comp. 777, 860–865. doi: 10.1016/j.jallcom.2018.11.060
Zhang, S. S. (2006). A review on electrolyte additives for lithium-ion batteries. J. Power Sour. 162, 1379–1394. doi: 10.1016/j.jpowsour.2006.07.074
Zhao, F., Tang, Y., Wang, J., Tian, J., Ge, H., and Wang, B. (2015). Vapor-assisted synthesis of Al2O3-coated LiCoO2 for high-voltage lithium ion batteries. Electrochim. Acta 174, 384–390. doi: 10.1016/j.electacta.2015.05.180
Zhao, H., Yu, X., Li, J., Li, B., Shao, H., Li, L., et al. (2019). Film-forming electrolyte additives for rechargeable lithium-ion batteries: progress and outlook. J. Mater. Chem. A 7, 8700–8722. doi: 10.1039/C9TA00126C
Zhao, Q., Xiao, W., Yan, X., Qin, S., Qu, B., and Zhao, L. (2017). Effect of pyrolytic polyacrylonitrile on electrochemical performance of Si/graphite composite anode for lithium-ion batteries. Ionics 23, 1685–1692. doi: 10.1007/s11581-017-1992-2
Zhao, R., Li, L., Xu, T., Wang, D., Pan, D., He, G., et al. (2019). One-step integrated surface modification to build a stable interface on high-voltage cathode for lithium-ion batteries. ACS Appl. Mater. Interf. 11, 16233–16242. doi: 10.1021/acsami.9b02996
Zhao, S.-X., Ding, H., Wang, Y.-C., Li, B.-H., and Nan, C.-W. (2013). Improving rate performance of LiFePO4 cathode materials by hybrid coating of nano-Li3PO4 and carbon. J. Alloys Comp. 566, 206–211. doi: 10.1016/j.jallcom.2013.03.041
Zhao, W., Ji, Y., Zhang, Z., Lin, M., Wu, Z., Zheng, X., et al. (2017). Recent advances in the research of functional electrolyte additives for lithium-ion batteries. Curr. Opin Electrochem. 6, 84–91. doi: 10.1016/j.coelec.2017.10.012
Zhao, X., Zhuang, Q.-C., Xu, S.-D., Xu, Y.-X., Shi, Y.-L., and Zhang, X.-X. (2015). A new insight into the content effect of fluoroethylene carbonate as a film forming additive for lithium-ion batteries. Int. J. Electrochem. Sci. 10, 2515–2534.
Zheng, G., Chen, M., Zhang, H., Zhang, J., Liang, X., Qi, M., et al. (2019). Zn-MOFs derived porous carbon nanofiber for high performance lithium-ion batteries. Surface Coat. Technol. 359, 384–389. doi: 10.1016/j.surfcoat.2018.12.075
Zheng, J., Chen, S., Zhao, W., Song, J., Engelhard, M. H., and Zhang, J.-G. (2018). Extremely stable sodium metal batteries enabled by localized high-concentration electrolytes. ACS Energy Lett. 3, 315–321. doi: 10.1021/acsenergylett.7b01213
Zheng, J., Xiao, J., Gu, M., Zuo, P., Wang, C., and Zhang, J.-G. (2014). Interface modifications by anion receptors for high energy lithium ion batteries. J. Power Sour. 250, 313–318. doi: 10.1016/j.jpowsour.2013.10.071
Zhou, J., Qian, T., Wang, M., Xu, N., Zhang, Q., Li, Q., et al. (2016). Core–shell coating silicon anode interfaces with coordination complex for stable lithium-ion batteries. ACS Appl. Mater. Interf. 8, 5358–5365. doi: 10.1021/acsami.5b12392
Zhuang, Q., Yang, Z., Zhang, L., and Cui, Y. (2020). Diagnosis of electrochemical impedance spectroscopy in lithium ion batteries. Prog. Chem. 32, 761–791. doi: 10.7536/PC191116
Zhuang, Q.-C., Li, J., and Tian, L.-L. (2013). Potassium carbonate as film forming electrolyte additive for lithium-ion batteries. J. Power Sour. 222, 177–183. doi: 10.1016/j.jpowsour.2012.08.050
Keywords: lithium-ion batteries, electrode-electrolyte interface, solid electrolyte interphase, interface modification, organic liquid electrolyte
Citation: Guo W, Meng Y, Hu Y, Wu X, Ju Z and Zhuang Q (2020) Surface and Interface Modification of Electrode Materials for Lithium-Ion Batteries With Organic Liquid Electrolyte. Front. Energy Res. 8:170. doi: 10.3389/fenrg.2020.00170
Received: 17 May 2020; Accepted: 03 July 2020;
Published: 11 September 2020.
Edited by:
Jianfeng Mao, University of Wollongong, AustraliaReviewed by:
Shiyou Zheng, University of Shanghai for Science and Technology, ChinaCopyright © 2020 Guo, Meng, Hu, Wu, Ju and Zhuang. This is an open-access article distributed under the terms of the Creative Commons Attribution License (CC BY). The use, distribution or reproduction in other forums is permitted, provided the original author(s) and the copyright owner(s) are credited and that the original publication in this journal is cited, in accordance with accepted academic practice. No use, distribution or reproduction is permitted which does not comply with these terms.
*Correspondence: Zhicheng Ju, anV6Y0BjdW10LmVkdS5jbg==; Quanchao Zhuang, emh1YW5ncXVhbmNoYW9AMTI2LmNvbQ==
Disclaimer: All claims expressed in this article are solely those of the authors and do not necessarily represent those of their affiliated organizations, or those of the publisher, the editors and the reviewers. Any product that may be evaluated in this article or claim that may be made by its manufacturer is not guaranteed or endorsed by the publisher.
Research integrity at Frontiers
Learn more about the work of our research integrity team to safeguard the quality of each article we publish.