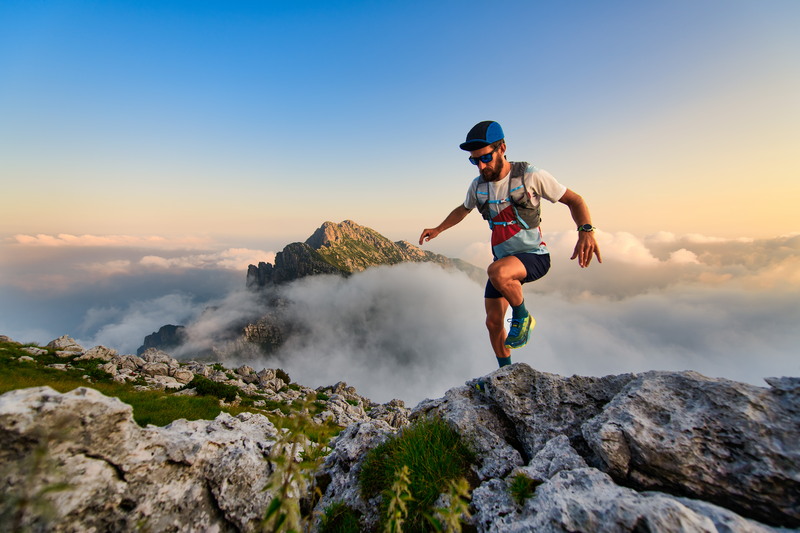
94% of researchers rate our articles as excellent or good
Learn more about the work of our research integrity team to safeguard the quality of each article we publish.
Find out more
ORIGINAL RESEARCH article
Front. Energy Res. , 16 July 2020
Sec. Electrochemical Energy Storage
Volume 8 - 2020 | https://doi.org/10.3389/fenrg.2020.00154
This article is part of the Research Topic Energy Storage Systems Beyond Li-Ion Intercalation Chemistry View all 11 articles
Copper sulfides (CuxS) with different stoichiometry are considered as prospective cathode materials for lithium batteries owing to their large energy storage capability. In this work, three-dimensional CuxS cathodes were synthesized via introducing commercially available copper foam into the solution of dimethyl sulfoxide (DMSO) and sulfur powder. The synthesis procedures were straightforward and ultrafast and did not require additional reagents, high temperature, or long processing time and can be considered as a facile one-step method. Copper sulfide materials with different stoichiometry (x = 1.8, 1.96) were obtained by changing the temperature and the residence time of the copper foam in the DMSO solution. The effects of the temperature and time on phase and morphology of CuxS were characterized by X-ray diffraction and scanning electron microscopy coupled with energy dispersive X-ray spectroscopy. Electrochemical tests resulted in a stable cyclability of Cu1.8S cathode with 100% Coulombic efficiency and capacity of approximately 250 mAh g–1.
Currently, primary energy sources (i.e., fossil fuels such as oil, coal, and natural gas) are depleting at an increasing rate; thus, energy storage devices that suggest offering both rate performance and greater capacity are always of high interest. In addition to this, non-renewable energy sources are responsible for environmental hazards such as “greenhouse gas” emissions and contamination (Armaroli and Balzani, 2007). For the last three decades, lithium-ion batteries (LIBs) have been known as one of the superior technologies to store energy and are already used in portable electronics. Recently, LIBs made its progressive way into the field of electric vehicles, grid energy storage, and plug-in hybrid vehicles (Chung and Sohn, 2002). However, traditional LIBs are still not satisfying the needs for the high capacity, energy density, and, most importantly, safety aspects. For instance, a traditional LIB cell consists of a transition metal oxide (e.g., LiCoO2) as the cathode material and graphite as the anode material. Today, their energy density has reached its limits of <260 Wh kg–1 and is not able to cope with the required energy demands of modern society (Meng et al., 2012; Manthiram et al., 2017). Furthermore, inherent defects of LIBs such as safety concerns limit their development, with incidents ranging from Hewlett Packard’s recall of hundreds of thousands of laptop batteries in 2009 due to overheating and fire, to the Samsung Galaxy Note 7 explosion in 2017 (Liu et al., 2018). Additionally, LiCoO2 is expensive as well as toxic (Blomgren, 2017).
Alternatively, scholars have been investigating new electrode materials to solve these issues. Compared to conventional candidate materials, conversion-based materials [e.g., metal fluorides (Cabana et al., 2010; Wang et al., 2011), sulfides (Meng et al., 2014; Lu et al., 2017), phosphides, and nitrides (Cabana et al., 2010)] present an essential class that has not been well researched. Conversion-based materials have been suggested for LIBs because of their higher specific capacities and preferably cost-effectiveness. Over the past decades, copper sulfides (CuxS) have attracted considerable attention in the field of LIBs because of their different valence states and stoichiometric compositions (Chung and Sohn, 2002). The latest studies have shown that CuxS (1 ≤ x ≤ 2) are an upcoming cathode candidate for interaction with lithium metal (i.e., Li-CuxS, 1 ≤ x ≤ 2) with long cyclic performance and high rate capability.
Copper sulfide is known to have five stable phases starting from chalcocite “copper-rich” Cu2S to the covellite “copper-deficient” CuS. The excellent properties such as high electronic conductivity of 10–3 S cm–1 and theoretical capacities of 337–560 mAh g–1 make them attractive electrode material for large-scale applications in secondary lithium, magnesium, and sodium batteries because of their abundance and inexpensiveness (Lu et al., 2017; Xiao et al., 2018; Wang et al., 2019). It has been reported that the electrochemical and electronic properties of the CuxS system depend greatly on both the Cu/S ratios and crystalline structures. An increase in the bandgap occurs with an increase in the x value in bulk CuxS (i.e., 1.2 eV for Cu2S, 1.5 eV for Cu1.8S, and 2.0 eV for CuS). This implied that CuxS with the composition closer to Cu2S will demonstrate higher electronic conductivity than that of CuS electrodes (Grozdanov and Najdoski, 1995; Zhao et al., 2009).
Thus far, many studies have been devoted to the synthesis of 1–3D structured CuS and Cu2S electrodes by hydrothermal (Tao et al., 2014), solvothermal (Han et al., 2011; Liu and Xue, 2011), microwave (Xiao et al., 2016; Yuan et al., 2016; Wang et al., 2019), spray pyrolysis (Madarasz et al., 2001; Kalimuldina and Taniguchi, 2016a, b), and other methods. However, only a few have focused on the preparation of freestanding 3D structured CuxS electrodes (Ni et al., 2013; Tang et al., 2017). In this research, we investigate a facile way to prepare a 3D structured freestanding cathode material at a low temperature via a straightforward one-step method that does not require expensive apparatus and additional chemical agents compared to the conventional and complex ways of cathode preparation.
To develop a better battery with sufficient volumetric and power densities, the fabrication of freestanding cathodes is being considered as a reasonable approach. Therefore, the preparation of freestanding CuxS with high active mass loading by an ultrafast and low-cost method could benefit the simplification of cell packaging configurations as binders, and current collectors can be omitted (Zeng et al., 2015).
The materials utilized in this work were commercialized copper foam (Cu foam; MTI Corp., United States), sulfur powder (S, LenReaktiv), and dimethyl sulfoxide (C2H6OS, DMSO; Sigma–Aldrich, Germany). Materials were analytical grade and were used as received without further purification. First, to assess the solubility of S powder in DMSO, different amounts of S powder were dissolved in 20 mL DMSO at a heating temperature of 80°C. It was found that more than 0.1 g of powder cannot be fully dissolved in the solution. Afterward, an optimized amount of 0.1 g was used in further experiments. The effect of temperature on the formation of CuxS phases was investigated by varying the reaction temperature from 80°C to 110°C with the help of a heater while keeping the time constant at 30 s. After finding the desired favorable temperature for the synthesis, time was varied from 10 s to 1 min to optimize the reaction time.
In a typical synthesis procedure, 0.1 g of S powder was weighed and added into 20 mL of DMSO solution under vigorous stirring with a magnetic stirrer at the above-stated temperatures. For the preparation of the copper foam, it was cut into small rectangular pieces, washed with acetone, and dried in a vacuum oven at 60°C for 1 h. After the total dissolution of S powder, the prepared copper foam pieces were soaked into the solution as seen in Figure 1. Subsequently, blackened copper foam pieces were then dried in a vacuum oven at 60°C for 24 h. The masses of the obtained CuxS active materials were calculated based on the fact that the Cu element from the Cu foam directly reacts with the S in the solution. First, the mass of the deposited S was calculated by subtracting the pristine Cu foam mass from the obtained Cu/CuxS material mass. After, the electrode’s mass was calculated considering the molar masses of CuxS by the cross-multiplying method.
Obtained CuxS materials were characterized by X-ray powder diffraction (XRD; Rigaku SmartLab® X-ray diffraction system, Japan) to investigate the phases of CuxS. The scanning electron microscope Crossbeam 540 coupled with energy-dispersive X-ray spectroscopy (SEM-EDS; Zeiss, Germany) was employed to observe the morphologies and distribution of separate components of obtained materials. CR2032 type coin cells were assembled and tested to assess the electrochemical performances of the synthesized electrodes. Copper foam pieces were cut into 16 mm in diameter disks and were used as cathodes without any binders and additives in half-cells with Li metal. The mass loading of CuxS active material varied between 8.7 and 10.4 mg cm–2, depending on the synthesis time. Glovebox (MBraun, Germany) was used to assemble the half-cells, where the role of the separator was served by the Celgard 2400, and 1 M LiTFSI in DOL/DME was utilized as an electrolyte. The cells were then tested in the multichannel battery test system Arbin in the voltage range between 1.0 and 3.0 V with a constant current in the form of a C/5 rate (1C = 7–7.3 mAh).
X-ray powder diffraction patterns and SEM pictures of CuxS samples obtained at different temperatures with a constant time of 30 s are shown in Figure 2. The main diffraction peaks located at 43.5° and 50.7° for all samples can be assigned to the (1 1 1) and (2 0 0) crystal faces of the Cu foam, respectively. All other peaks could be indexed to Cu1.8S and Cu1.96S phases with the trace of very weak peaks (35°–38°) that could correspond to monoclinic Cu2S (Potter and Evans, 1976). At lower temperatures of 80 and 90°C, phases of Cu1.96S prevail, whereas at slightly higher temperatures of 100 and 110°C, formation of more Cu1.8S can be noticed. Also, one can observe from the SEM results (Figures 2b–e) that the temperature had a considerable effect on the morphologies and structures of the CuxS phases. In essence, at 80°C, the only formation of two-dimensional irregular CuxS plates can be observed, whereas increasing the temperature only by 10°C results in a surface with rough structures that resemble flowers-like humps. Going up to 100°C leads to the formation of homogenous hierarchical petals. Eventually, at 110°C, petals assemble themselves in flower-like spherical structures.
Figure 2. X-ray powder diffraction patterns (a) and SEM pictures of CuxS samples obtained at different temperatures with the constant time of 30 s: (b) 80°C, (c) 90°C, (d) 100°C, and (e) 110°C.
Figure 3 represents the XRD results and SEM images of CuxS on Cu foam obtained at 90°C at different times. The time had a significant influence on the phases and morphologies of the formed material as well. The samples prepared at the time of 10, 20, and 30 s showed a similar tendency of Cu1.96S formation. However, material obtained at 10 s showed the purest phase of Cu1.96S among them.
Figure 3. X-ray powder diffraction patterns (a) and SEM pictures of CuxS samples obtained at different times with the constant temperature of 90°C: (b) 10 s, (c) 20 s, (d) 30 s, and (e) 1 min.
On the other hand, 1-min synthesis triggered the formation of a flower-like Cu1.8S phase. As shown in Figures 3b–e, the morphology evolution of CuS from irregular form to the flower-like structure can be seen, involving several growth stages. The introduction of copper foam into a sulfur solution for 10 s resulted in the formation of irregular pieces (Figure 3b), whereas changing the time for 20 s enhanced the size of that particle (Figure 3c). After 30 s, pieces transformed into the sheets, and they became geometrically regular (Figure 3d). The time increase to 1 min affected significantly the structure of composites, forming a flower-like structure of CuxS (mainly Cu1.8S) (Figure 3e).
The phase evolution of CuxS is depicted in Figure 4, and several steps are suggested: first, after the Cu foam is soaked in the solution, instant adsorption of sulfur molecules takes place on the surface of the foam. Then, after several seconds, the adsorbed sulfur molecules react with the copper molecules in the surface of the Cu foam, resulting in a copper-rich Cu1.96S phase. Subsequently, increasing the reaction time leads to the reaction of the Cu1.96S phase with the sulfur again causing the formation of sulfur-rich Cu1.8S phase. Also, it is worth to mention that the main transformation of Cu1.96S to the Cu1.8S phase is due to the large surface area of the nanocrystals (Figures 3b–d), which allowed the rapid diffusion of Cu ions out of the crystal, thereby increasing the surface oxidation which possibly accelerated the djurleite formation (Green et al., 2012).
The scanning electron microscope–EDS images of Cu1.8S (Figure 5) indicated that the distribution of Cu and S elements on the copper foam’s surface was uniform, and the coverage was even. Although the reaction between Cu1.96S and S continues on the surface of the Cu foam in a gradient pattern, the composition distribution of the main elements is homogenous throughout the 3D material.
Figure 5. Scanning electron microscope–EDS mappings of obtained Cu1.8S on Cu foam: (a) pristine sample, (b) EDS spectra, (c) Cu and (d) S element mapping images.
The electrochemical characterization of Cu1.96S and Cu1.8S as cathode materials in lithium half-cells is presented in Figure 6. Galvanostatic tests were carried out at a rate of C/5 based on the mass of CuxS. Figure 6A shows charge–discharge profiles of Cu1.96S freestanding electrodes. It can be observed that the first discharge profile exhibits short and prolonged plateaus at 2.0 and 1.73 V, respectively. The reaction mechanism for Cu2S was reported as the initial discharge plateau should be at 1.73 V and corresponded to Cu2S + 2Li+ + 2e– → Li2S + 2Cu during the first cycle (Kalimuldina and Taniguchi, 2016b). However, for Cu1.96S, additional small peaks at 2.0 V can be seen, which is a more typical discharge plateau to CuS electrode (Kalimuldina and Taniguchi, 2017). That difference might come from some impurities residing in the obtained Cu1.96S electrode. After the fifth cycle, the discharge profile showed almost disappeared plateau at 2.2 V and much prolonged at 1.75 V with a capacity of 100 mAh g–1. Those changes might indicate the phase transformation of Cu1.96S with some impurities into pure Cu1.96S with the increase in the cycle number. The impurities could be the insignificant trace of copper-rich phases (Fu and Manthiram, 2013; Jache et al., 2014; Foley et al., 2018).
Figure 6. Charge–discharge profiles of (A) Cu1.96S (90°C, 10 s) and (B) Cu1.8S (90°C, 1 min) cathodes between 1.0 and 3.0 V at C/5.
The first charge voltage profiles are depicted at 1.85 and 2.25 V, respectively. Furthermore, after five cycles, we can observe previously reported flattening of the charge plateau to 1.85 V (Jache et al., 2014). Consequently, we can write the reversible electrochemical reaction accordingly from the obtained charge–discharge profiles as Li2S + 2Cu Û Cu1.96S + 0.04Cu + 2Li+ + 2e– (Debart et al., 2006; Kalimuldina and Taniguchi, 2016b, 2017). The similar charge–discharge profile of Cu1.8S electrode is demonstrated in Figure 6B. However, the change in the discharge plateaus at 2.1 and 1.65 V can be seen as there longer 2.1 V discharge plateau than that of in Figure 6A for Cu1.96S. However, after the fifth cycle, both charge and discharge show single plateaus at 1.75 and 1.85 V with about 250 mAh g–1, respectively. This implies that the richer the sulfur content in the composition of CuxS, the more its electrochemical properties get closer to the behavior of the covellite CuS electrode (Jianga et al., 2019).
Cycling performance of both Cu1.96S and Cu1.8S is demonstrated in Figure 7. The residue time of 10 s to obtain Cu1.96S at 90°C released a low but stable capacity of 100 mAh g–1 for 20 cycles with 100% Coulombic efficiency. On the contrary, when the reaction residue time was increased up to 1 min to achieve Cu1.8S, the significant capacity increase was observed. The capacity of Cu1.8S electrode with a mass loading of 10.4 mg cm–2 without any binders and additives achieved 250 mAh g–1 for 20 cycles with 100% Coulombic efficiency. It is well known that CuS is more attractive in the term of theoretical capacity (560 mAh g–1); however, the electrode with higher copper content is more electrically conductive (Grozdanov and Najdoski, 1995). Based on the theoretical capacities of Cu1.96S and Cu1.8S, the latter will deliver higher value. That can be considered as one of the reasons for such differences in the capacity between those electrodes.
Figure 7. Cycle performance of Cu1.96S (90°C, 10 s) and Cu1.8S (90°C, 1 min) cathodes between 1.0 and 3.0 V at C/5 over 20 cycles.
The ultrafast and straightforward method of preparation of 3D CuxS electrodes on Cu foam showed very prospective electrochemical properties as an applicable compartment in the future LIBs. The work confirms that other phases of CuxS are also electrochemically stable and have reversible charge–discharge processes even at high active mass loading conditions.
Different phases of CuxS as Cu1.96S and Cu1.8S were successfully prepared by a simple method of soaking Cu foam in an S/DMSO solution for a short period of time. The effect of temperature and synthesis time on the tendency for the reaction between Cu foam and S were studied. The morphology of CuxS samples was cubic-type irregular shapes at 80°C and grew further to the nanoflower-like structures at 110°C. The reaction activity of formed CuxS on the surface of Cu foam with remaining S in the DMSO solution was enhanced with the increase in the soaking time.
Electrochemical properties of Cu1.96S formed at 90°C and 10-s synthesis time showed only 100 mAh g–1 at 5/C rate, whereas the sample of Cu1.8S that was obtained by holding Cu foam up to 1 min at 90°C in S/DMSO solution reached stable cycling performance at 250 mAh g–1 with extremely high mass loading. This allows us to study the phase change of CuxS materials, depending on the time and temperature and its influence on the electrochemical properties of the cathode material.
The original contributions presented in the study are included in the article, further inquiries can be directed to the corresponding author.
AA, AN, and GK contributed to the synthesis, characterization, and manuscript writing. GK, DA, ZB, and IT contributed to the characterization, interpretation, and discussion of obtained results. All authors contributed to the article and approved the submitted version.
This work was supported by the research grant 091019CRP2114 “Three-Dimensional All Solid State Rechargeable Batteries,” 240919FD3914 “Self-Charging Rechargeable Lithium-ion Battery” from Nazarbayev University and AP05133706 “Innovative high-capacity anodes based on lithium titanate for a next generation of batteries”, AP08052143 “Development of wearable self-charging power unit” from the Ministry of Education and Science of the Republic of Kazakhstan.
The authors declare that the research was conducted in the absence of any commercial or financial relationships that could be construed as a potential conflict of interest.
Armaroli, N., and Balzani, V. (2007). The future of energy supply: challenges and opportunities. Angew. Chem. Int. Ed. 46, 52–66.
Blomgren, G. E. (2017). The development and future of lithium ion batteries. J. Electrochem. Soc. 164, A5019–A5025.
Cabana, J., Monconduit, L., Larcher, D., and Palacín, M. R. (2010). Beyond intercalation-based Li-ion batteries: the state of the art and challenges of electrode materials reacting through conversion reactions. Adv. Mater. 22, E170–E192.
Chung, J.-S., and Sohn, H.-J. (2002). Electrochemical behaviors of CuS as a cathode material for lithium secondary batteries. J. Power Sources. 108, 226–231. doi: 10.1016/s0378-7753(02)00024-1
Debart, A., Dupont, L., Patrice, R., and Tarascon, J.-M. (2006). Reactivity of transition metal (Co, Ni, Cu) sulphides versus lithium: the intriguing case of copper sulphide. Solid State Sci. 8, 640–651. doi: 10.1016/j.solidstatesciences.2006.01.013
Foley, S., Geaney, H., Bree, G., Stokes, K., Connolly, S., Zaworotko, M. J., et al. (2018). Copper Sulfide (CuxS) Nanowire-in-Carbon Composites Formed from Direct Sulfurization of the Metal-Organic Framework HKUST-1 and Their Use as Li-Ion Battery Cathodes. Adv. Funct. Mater. 28, 1–8.
Fu, A., and Manthiram, A. (2013). Electrochemical properties of Cu2S with ether-based electrolyte in Li-ion batteries. Electrochim. Acta 109, 716–719. doi: 10.1016/j.electacta.2013.07.160
Green, M., Pattrick, R., Corr, S., Imai, H., Haigh, S., Young, R., et al. (2012). Nanoscience: Volume 1: Nanostructures Through Chemistry. London: Royal Society of Chemistry.
Grozdanov, I., and Najdoski, M. (1995). Optical and electrical properties of copper sulfide films of variable composition. J. Solid State Chem. 114, 469–475. doi: 10.1006/jssc.1995.1070
Han, Y., Wang, Y., Gao, W., Wang, Y., Jiao, L., Yuan, H., et al. (2011). Synthesis of novel CuS with hierarchical structures and its application in lithium-ion batteries. Powder Techn. 212, 64–68. doi: 10.1016/j.powtec.2011.04.028
Jache, B., Mogwitz, B., Klein, F., and Adelhelm, P. (2014). Copper sulfides for rechargeable lithium batteries: linking cycling stability to electrolyte composition. J. Power Sources 247, 703–711. doi: 10.1016/j.jpowsour.2013.08.136
Jianga, K., Chen, Z., and Menga, X. (2019). A Review on CuS and Cu2S as Cathode Materials for Lithium Batteries. ChemElectroChem 19, 2825–2840. doi: 10.1002/celc.201900066
Kalimuldina, G., and Taniguchi, I. (2016a). High performance stoichiometric Cu2S cathode on carbon fiber current collector for lithium batteries. Electrochim. Acta 224, 329–336. doi: 10.1016/j.electacta.2016.12.058
Kalimuldina, G., and Taniguchi, I. (2016b). Synthesis and electrochemical characterization of stoichiometric Cu2S as cathode material with high rate capability for rechargeable lithium batteries. J. Power Sources 331, 258–266. doi: 10.1016/j.jpowsour.2016.09.047
Kalimuldina, G., and Taniguchi, I. (2017). Electrochemical properties of stoichiometric CuS coated on carbon fiber paper and Cu foil current collectors as cathode material for lithium batteries. J. Mater. Chem. A 5, 6937–6946. doi: 10.1039/c7ta00614d
Liu, F., and Xue, D. (2011). CuS hierarchical Architectures by a combination of bottom-up and top-down method. Nanosci. Nanotechnol. Lett. 3:440. doi: 10.1166/nnl.2011.1172
Liu, K., Liu, Y., Lin, D., Pei, A., and Cui, Y. (2018). Materials for lithium-ion battery safety. Adv. Sci. 4:9820.
Lu, Y., Li, B., Zheng, S., Xu, Y., Xue, H., and Pang, H. (2017). Syntheses and energy storage applications of MxSy (M = Cu, Ag, Au) and their composites: rechargeable batteries and supercapacitors. Adv. Funct. Mater. 27:1703949. doi: 10.1002/adfm.201703949
Madarasz, J., Okuya, M., and Kaneko, S. (2001). Preparation of covellite and digenite thin films by an intermittent spray pyrolysis deposition method. J. Eur. Ceram. Soc. 2, 2113–2116. doi: 10.1016/s0955-2219(01)00183-2
Manthiram, A., Song, B., and Li, W. (2017). A perspective on nickel-rich layered oxide cathodes for lithium-ion batteries. Energy Storage Mater. 6, 125–139. doi: 10.1016/j.ensm.2016.10.007
Meng, X., He, K., Su, D., Zhang, X., Sun, C. J., Ren, Y., et al. (2014). Gallium sulfide–single-walled carbon nanotube composites: high-performance anodes for lithium-ion batteries. Adv. Funct. Mater. 24, 5435–5442. doi: 10.1002/adfm.201401002
Meng, X., Yang, X.-Q., and Sun, X. (2012). Emerging applications of atomic layer deposition for lithium-ion battery studies. Adv. Mater. 24, 3589–3615. doi: 10.1002/adma.201200397
Ni, S., Lv, X., Li, T., and Yang, X. (2013). Fabrication of Cu2S cathode for Li-ion battery via a low temperature dry thermal sulfuration method. Mater. Chem. Phys. 143, 349–354. doi: 10.1016/j.matchemphys.2013.09.008
Potter, R. W. II, and Evans, H. T. Jr. (1976). Definitive X-ray powder data for covellite, anilite, djurleite and chalcocite. J. Res. U. S. Geol. Surv. 4, 205–212.
Tang, J., Ni, S., Chen, Q., Zhang, J., and Yang, X. (2017). CuS@Cu freestanding electrode via electrochemical corrosion for high performance Li-ion batteries. Mater. Lett. 201, 13–17. doi: 10.1016/j.matlet.2017.04.120
Tao, H. C., Yang, X. L., Zhang, L. L., and Ni, S. B. (2014). One-pot facile synthesis of CuS/graphene composite as anode materials for lithium ion batteries. J. Phys. Chem. Solids 75, 1205–1209. doi: 10.1016/j.jpcs.2014.06.010
Wang, F., Robert, R., Chernova, N. A., Pereira, N., Omenya, F., Badway, F., et al. (2011). Conversion reaction mechanisms in lithium ion batteries: study of the binary metal fluoride electrodes. J. Am. Chem. Soc. 133, 18828–18836. doi: 10.1021/ja206268a
Wang, Z., Rafai, S., Qiao, C., Jia, J., Zhu, Y., Ma, X., et al. (2019). Microwave-assisted synthesis of CuS hierarchical nanosheets as the cathode material for high-capacity rechargeable magnesium batteries. ACS Appl. Mater. Interfaces 11, 7046–7054. doi: 10.1021/acsami.8b20533
Xiao, S., Li, X., Sun, W., Guan, B., and Wang, Y. (2016). General and facile synthesis of metal sulfide nanostructures: in situ microwave synthesis and application as binder-free cathode for Li-ion batteries. Chem. Eng. J. 306, 251–259. doi: 10.1016/j.cej.2016.05.068
Xiao, Y., Su, D., Wang, X., Wu, S., Zhou, L., Shi, L., et al. (2018). CuS microspheres with tunable interlayer space and micropore as a high-rate and long-life anode for sodium-ion batteries. Adv. Energy Mater. 8:1800930. doi: 10.1002/aenm.201800930
Yuan, D., Huang, G., Zhang, F., Yin, D., and Wang, L. (2016). Facile synthesis of CuS/rGO composite with enhanced electrochemical lithium-storage properties through microwave-assisted hydrothermal method. Electrochim. Acta 203, 238–245. doi: 10.1016/j.electacta.2016.04.042
Zeng, L., Jiang, Y., Xu, J., Wang, M., Li, W., and Yu, Y. (2015). Flexible copper-stabilized sulfur–carbon nanofibers with excellent electrochemical performance for Li-S batteries. Nanoscale 7, 10940–10949. doi: 10.1039/c5nr01861g
Keywords: lithium-ion batteries, copper foam, sulfur, one-step method, copper sulfide
Citation: Adylkhanova A, Nurpeissova A, Adair D, Bakenov Z, Taniguchi I and Kalimuldina G (2020) Facile Synthesis of Binder-Free Three-Dimensional CuxS Nanoflowers for Lithium Batteries. Front. Energy Res. 8:154. doi: 10.3389/fenrg.2020.00154
Received: 14 April 2020; Accepted: 17 June 2020;
Published: 16 July 2020.
Edited by:
Jun Yan, Harbin Engineering University, ChinaReviewed by:
Yurong Ren, Changzhou University, ChinaCopyright © 2020 Adylkhanova, Nurpeissova, Adair, Bakenov, Taniguchi and Kalimuldina. This is an open-access article distributed under the terms of the Creative Commons Attribution License (CC BY). The use, distribution or reproduction in other forums is permitted, provided the original author(s) and the copyright owner(s) are credited and that the original publication in this journal is cited, in accordance with accepted academic practice. No use, distribution or reproduction is permitted which does not comply with these terms.
*Correspondence: Gulnur Kalimuldina, Z2thbGltdWxkaW5hQG51LmVkdS5reg==
Disclaimer: All claims expressed in this article are solely those of the authors and do not necessarily represent those of their affiliated organizations, or those of the publisher, the editors and the reviewers. Any product that may be evaluated in this article or claim that may be made by its manufacturer is not guaranteed or endorsed by the publisher.
Research integrity at Frontiers
Learn more about the work of our research integrity team to safeguard the quality of each article we publish.