- 1Department of Chemical & Environmental Engineering, Faculty of Engineering, Universiti Putra Malaysia, Serdang, Malaysia
- 2Sustainable Process Engineering Research Centre, Faculty of Engineering, Universiti Putra Malaysia, Serdang, Malaysia
- 3Department of Chemistry, Faculty of Science, Universiti Putra Malaysia, Serdang, Malaysia
The conversion of biomass into hydrogen-rich syngas has been getting attention recently, as it has potential sustainability benefits of agricultural residues. In this study, gasification of empty fruit bunch (EFB) was performed using various calcined Malaysian dolomite catalysts, which were denoted as P1, P2, and P3. The physicochemical properties of the catalysts were examined using X-ray fluorescence (XRF), X-ray diffraction (XRD), Brunauer–Emmett–Teller (BET), and scanning electron microscopy (SEM). The effect of various catalyst to biomass (C/B) ratios (varied in the range of 0.05–0.3 in an increment of 0.05) of P1, P2, and P3 catalyst in EFB gasification was evaluated at a gasifier temperature of 850°C. The gas produced was analyzed by gas chromatography (GC). The effect of various C/B ratios on tar conversion was also examined. The result showed that, with lower impurities in calcined dolomites and high content of active sites (CaO–MgO), improved characteristics of P1 and P2 in crystalline structure contributes to a significant reduction in tar cracking (~78 and 75%, respectively) and higher H2 yield (32.25 mg H2/g EFB).
Introduction
Syngas can be obtained from various sources, such as coal, natural gas, and petroleum distillate through thermochemical processes (Shen et al., 2018). Syngas technology is a well-known alternative process to produce valuable chemical products. The main components of syngas are hydrogen and carbon monoxide. Hydrogen is a clean and efficient energy source, also known as a safe source because it can be stored as a gas or a liquid, and it has good properties in fueling automobile engines (Mohammed et al., 2011). Dependence on fossil fuels as the main source has led to price instability, excessive carbon dioxide emissions, and unprecedented global warming (Li and Chen, 2018). Owing to the ever-increasing demand of energy for modern civilization and rapid depletion of fossil fuel, there is a need to find for alternative energy sources (González-Vázquez et al., 2018). The production of hydrogen not only accomplish the growing demand energy but also is economically feasible and a sustainable development of the world by utilizing the same infrastructure without any major modification to replace fossil fuel (Shahbaz et al., 2019).
Biomass gasification is regarded to be one of the viable routes for a sustainable future in hydrogen gas production. Biomass is a cheap, abundant, carbon-neutral energy source and has good synergy with current fossil fuel power plants (Li and Chen, 2018). Malaysia has produced a huge amount of palm oil wastes ~54.1 Mt/year. The palm oil wastes, also known as biomass, consists of empty fruit bunch (EFB), palm kernel shell (PKS), palm oil fronds (POFs), trunks, and fiber (Abdulrazik et al., 2017). Malaysia has implemented a biofuel program and embarked on renewable energy growth to ensure sustainable development in the energy sector. In line with government policy, it has led to strong interest among researchers to utilize biomass for green biofuels (Mohammed et al., 2011). Till now, many works have been reported on the transformation of solid biomass into combustible gases, such as the mixture of hydrogen, methane, carbon monoxide, carbon dioxide, light hydrocarbon, and char, through gasification (Mutlu and Yucel, 2018). Nevertheless, many reported works have shown low conversion efficiency of syngas, which is low H2/CO ratio, hence resulting in higher tar formation and reduction in gas yield. To achieve high-quality syngas, high gas yield, suitable gas components, low tar yield, and low content of impurities must be obtained (Shen et al., 2018). Many studies have been conducted to produce high-quality syngas by various techniques, such as high-temperature gasification, gasification agent, bio-oil reforming, inline reforming, and type of catalysts.
Nonetheless, high tar yield can cause several operational issues, such as corrosion in equipment and pipeline blockage and high maintenance cost on the filtration system (Tian et al., 2018). Tars can be removed by several ways, such as collection and disposal of tars (non-catalytic), catalytic tar conversion, and cogasification of biomass and coal (Tian et al., 2018). Tar can be eliminated by a catalytic pathway to convert it into the lower molecular weight of hydrocarbon. Tar conversion reaction during gasification in the presence of the catalyst can be shown in Equation (1) (Aydin et al., 2018):
The use of catalyst has proven to benefit the gasification process in terms of the economic point of view. According to Shahbaz et al. (2019), the use of a catalyst can augment the quantity of the desired product, lower the gasification temperature condition, and capable of converting tar into gases, although it has a minor problem in sintering as well as regeneration. However, some catalyst can be easily deactivated during the process due to high tar contamination and particle agglomeration after several sorption–desorption cycles (Xu et al., 2017).
There is strong interest to use low-cost and abundantly available sources, such as dolomite as catalyst for EFB gasification as well as tar cracking (Waheed et al., 2016). Quitete and Souza (2017) stated that they evaluated the three dolomites from different origins and Ni-based mixed metal oxides containing Ce and La for tar removal. Mixed metal oxide showed a higher toluene conversion than dolomites due to hydration and carbonation. They also mentioned that dolomites can retain a portion of H2S and HCl and promote tar cracking and are significantly active above 800°C. Herein, this study aimed to evaluate the tar cracking efficiency in EFB gasification reaction using various calcined Malaysian dolomite catalysts as the primary catalyst. Moreover, the effect of different catalyst to biomass (C/B) ratios on product yield and selectivity, the performance of gasification reaction, and tar conversion efficiency were determined in the study.
Materials and Methods
Materials
The feedstock used was dried EFB, ~0.3–0.5 mm in diameter. The properties of the dried EFB are shown in Table 1. Silica sand was used as the bed material in the gasifier with a mean size of 0.10–0.15 mm. Three types of natural Malaysian dolomite stones (P1, P2, and P3) were used as catalysts. All dolomites were ground and sieved with an average diameter of 0.5–1.0 mm. Then, the dolomites were calcined at 900–1,000°C with nitrogen purging for 4 h before being used in the gasification process. Analytical-grade solvents and reagents were used for sample preparation and chemicals for the preparation of calibration and internal standards. All chemicals as follows were received in minimum purity of 98–99% (Sigma–Aldrich, United States): dichloromethane (DCM), isopropanol (IPA), N, O-bis(trimethylsilyl) trifluoroacetamide (BSTFA), p-ethoxyphenol (PEP), and 2-promonaphthalene. Solid-phase extraction (SPE) tubes (VARIAN, United States) used for tar sampling and sample preparation were loaded with 500 mg of aminoporpylsilane (NH2) phase (surface area, ~460–520 m2/g) bonded to a silica gel (average particle size of 47–60 μm and average pore diameter of 60–87 Å).
Catalyst Characterization
The chemical composition of catalysts was estimated using wavelength-dispersive X-ray fluorescence (WDXRF) (model BRUKER, S8 TIGER, United States). The fused-bead technique was used to prepare the samples for XRF analysis. Approximately 0.5 g of the sample was mixed with 5.0 g of spectra-flux LT-110 (Li2B4O7 = 66.5%, LiBO2 = 33.5%) and placed in a platinum crucible. The mixture was then fused at temperatures between 900 and 1,250°C and cast in a platinum casting dish. The samples were subjected to precise control of the cooling process to ensure the reproducibility of the flat glass disks and to avoid cracking or crystallization.
To examine the structural changes induced by the calcination process, the samples were characterized using a diffractrometer X-ray diffraction (XRD) system (model Shimadzu XRD6000, Japan), using Cu Kα (at wavelength of 1.5406 Å) radiation, fitted with a Cu filter on the secondary optics and operated under 40 kV power and 30 mA current. The scanning 2θ range was from 20 to 90°, at a scan rate of 3°/min.
The physical properties of the dolomites, such as specific surface area, total pore volume, and pore size distribution, were obtained by measuring their nitrogen adsorption–desorption isotherm at 77 K using a Quantachrome instrument (model Atosorb-1, United States). The Brunauer–Emmet–Teller (BET) surface area was estimated from the adsorption–isotherm data using the relative pressure (p/po) range of 10−6-1. The total pore volume was assessed by converting the amount of nitrogen gas adsorbed at relative pressure to the volume of the liquid adsorbate. The analytical method consisted of three steps, including dehydration, degassing under low vacuum pressure, and nitrogen gas adsorption at 77 K. The resulting isotherm was analyzed using the BET adsorption method, and the pore-size distributions were derived by the Barret–Joyner–Halena (BJH) desorption method.
The surface and microstructure analysis of the catalysts was carried out using a scanning electron microscopy (SEM) instrument (model HITACHI, S-3400N, Japan). The catalyst powder was mounted onto the SEM stubs (layered with sticky carbon tape). The stub was then placed in a sputter coater (EMITECH, K550X, United States) for 5 min for coating with gold to provide high reflectivity during the scanning process. The samples were then placed at 40°C in an oven before SEM analysis.
Catalytic Gasification
The catalysis experiments were performed to inspect the effect of the catalyst on the EFB gasification process when it was directly dry mixed with EFB samples as primary catalyst. The weight ratio of C/B varied in the range of 0.05–0.3 in increments of 0.05 at a gasifier temperature of 850°C. The experimental setup for a primary catalyst is illustrated in Figure 1. The results were compared with the results published previously (Mohammed et al., 2011), in which non-catalytic gasification was performed to assess the influence of gasification temperature, the equivalence ratio (ER), and feedstock particle size.
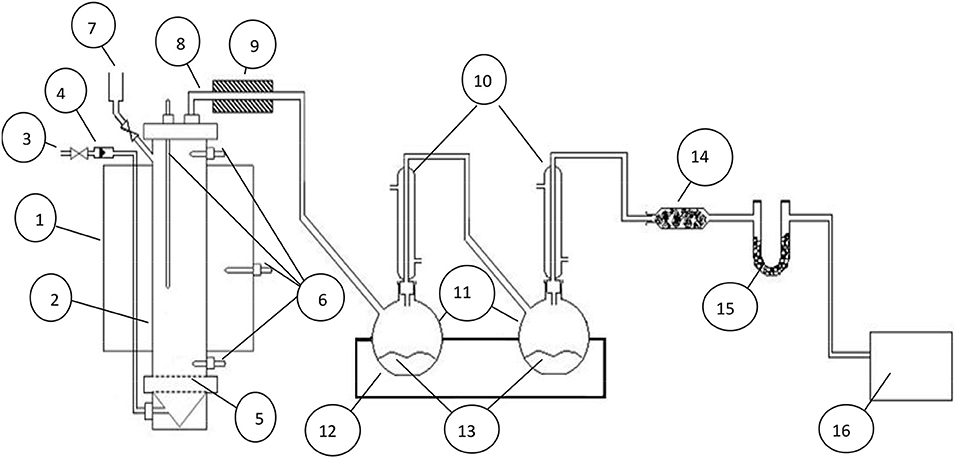
Figure 1. A schematic diagram of the gasification setup: (1) gasifier, (2) electric furnace, (3) air inlet, (4) air flow meter, (5) air distributor, (6) thermocouples, (7) feeder, (8) gas outlet, (9) heating tape, (10) condenser, (11) neck flask, (12) ice path, (13) dichloromethane, (14) fiber-glass wool filter, (15) silica gel, and (16) gas bag.
Tar Analysis Using Solid-Phase Adsorption Method
The sampling and analysis of tar compounds were achieved using the solid-phase adsorption (SPA) method. In this paper, tar was referred to as major gas chromatography (GC)-detectable aromatic and phenolic compounds. In this method, 100 ml of gas product was withdrawn from the sampling gas line through the SPE tube using a syringe within ~1 min. The sampling point was kept at 250°C using a heating tape to prevent or minimize any tar condensation. Subsequently, the SPE tubes were eluted using 1.5 ml DCM to get an aromatic fraction, and then with 1 ml of IPA-DCM (1:1 v/v) and 0.5 ml of IPA to get a phenolic fraction. The fractions were collected in vials (1.5 ml) and closed with a septum cap. The known amounts of 2-bromonaphthalene and p-ethoxyphenol were added as internal standards for aromatic and phenolic fractions, respectively. Phenols were derivatized to form trimethylsilyl ethers by the addition of 50 μl BSTFA to the phenolic fractions and allowed for the reaction to occur for 1 h before GC analysis. The aromatic and phenolic fractions were analyzed using a GC (model Agilent Technologies, 7890A, United States) equipped with a flame-ionization detector (FID) operated at 300°C and an Agilent HP-5 column with 30 m length, 0.325 mm internal diameter, and 0.25 μm film thickness. The splitter/splitless injector port was operated in a split mode at 280°C. A constant flow of helium at 0.8 ml/min through the column was automatically maintained using electronic pressure control programming (60–100 kPa) to follow the temperature program. The sample size was 1 μl. The oven temperature was programmed from 50°C isothermally for 5 min and then at 8°C/min to 280°C with 5-min final delay time.
Gas Product Analysis Using Gas Chromatography
The gas product was qualitatively and quantitatively analyzed using GC (model Agilent technology, HP6890N, United States) equipped with a thermal conductive detector (TCD) and a capillary column HP Molesieve (J&W Scientific, United States) to measure the volume fraction of permanent gas. The length, internal diameter, and film thickness of the column were 30 m, 0.53 mm, and 50 μm, respectively. The oven temperature was set at 70°C, and the carrier gas flowrate (argon) was 3.4 ml/min. The splitless inlet temperature was 60°C, while the detector temperature was 200°C. The TCD was calibrated using a standard gas (Air Products, Singapore) mixture containing CO, CO2, H2, and CH4 in N2 at periodic intervals.
Results and Discussion
Physicochemical Properties of Activated Dolomite Catalysts
The catalysts were characterized before and after calcination using XRD to analyze the effect of the calcination process on the catalyst structure. From Figure 2, XRD patterns for natural dolomites show that all peaks correspond to those of dolomite CaMg(CO3)2 [Joint Committee on Powder Diffraction Standards (JCPDS) 36-0426]. The XRD pattern for calcined dolomites, however, changes drastically compared to that of natural dolomites. New dominant peaks that belong to CaO (JCPDS 04-0777) and MgO (JCPDS 87-0652) are observed. Natural P3 sample (Figure 3C) shows three additional peaks between 2θ = 20° and 2θ = 30°, which belongs to Fe2O3 (JCPDS 26-1319), TiO2 (JCPDS 71-1169), and SiO2 (JCPDS 83-0539), occurring at 2θ = 25.2, 26.7, and 28°, respectively. The changing in the peaks illuminates the calcination of Malaysian dolomites, resulting in the formation of MgO–CaO, which is the active component.
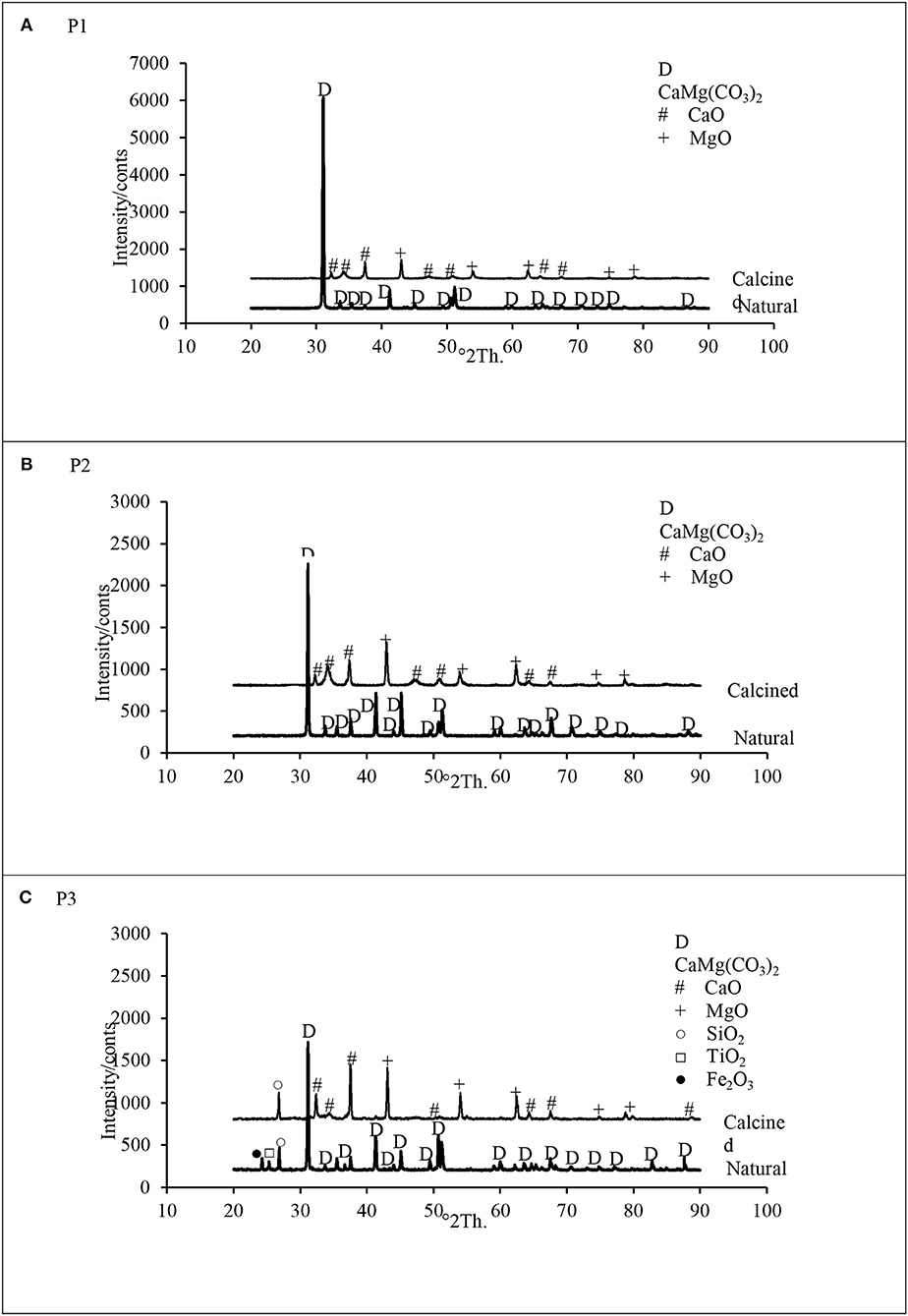
Figure 2. X-ray diffraction (XRD) diffractogram of natural and calcined dolomite catalyst for (A) P1, (B) P2, and (C) P3.
The chemical composition of the dolomite in addition to its physical properties (i.e., surface area, pore volume, and average pore diameter) is an important factor in evaluating the tar cracking capacity of the dolomite. Calcined dolomite is a porous catalyst; its large surface area and the presence of CaO and MgO in its matrix make it an active catalyst concerning tar reduction. The BET surface area, pore volume, and average pore size for dolomites are summarized in Table 2. A comparison of the surface area and pore volume (17–3,000 Å) shows that the P1 and P2 catalysts has the highest surface area and pore volume compared to P3. The pore size distribution of P1 and P2 dolomites differs from that of P3. The pore size of P1 and P2 catalysts is mainly in the 400-Å region, whereas the major pore size of P3 is in the 150-Å region.
Catalyst micrographs before and after calcination process are shown in Figure 3. The SEM images of the calcined dolomites are significantly different from those of the dolomites before calcination. As illustrated in Figure 3, the SEM images of natural dolomite show a rough and disorderly surface with low-porosity grains, whereas the calcined dolomite samples show high-porosity surface, especially in the case of P1 and P2 catalysts. The pores are homogeneous and well-pronounced, which confirms the structural transformation of dolomites.
The Influence of Calcined Dolomite Catalysts on Tar Cracking
Figure 4A shows the effect of different amounts of calcined dolomite catalysts on tar conversion in the EFB gasification process. The tar content decreased with the use of dolomites in the gasifier due to the cracking of tar by wet- and dry-reforming reaction. Further reductions were achieved by increasing the amount of catalyst in the reaction. P1 and P2 catalysts showed higher catalytic activity for tar reduction compared to P3 dolomite. It might be due to the higher surface area and pore volume that contributes to higher tar cracking efficiency, as shown in Table 2. On the contrary, P3 contains low quantities of CaO and MgO with high amounts of impurities, such as SiO2, Al2O3, and TiO2, which strongly reduced its catalytic activity. In the presence of P1 dolomite, the total tar content in the produced gas decreased from 41.2 mg/g obtained with zero catalyst addition in the gasification to 8.8 mg/g obtained at 850°C with 30% catalyst, while under the same conditions, the total tar reduced to 10.2 and 12.2 mg/g in the case of P2 and P3, respectively. The tar conversion efficiencies of all calcined dolomite catalysts are shown in Figure 4B. The calculated tar reduction (%) relative to that obtained with zero catalyst for P1, P2, and P3 were ~78, 75, and 70%, respectively (Mohammed et al., 2011).
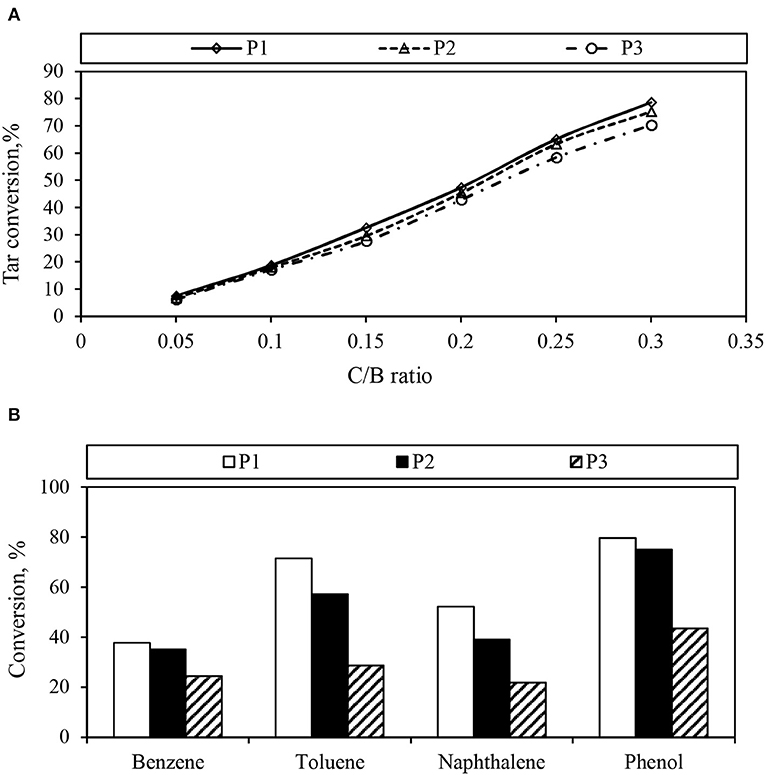
Figure 4. Effect of different catalyst to biomass (C/B) ratio on (A) tar conversion and (B) gas conversion.
Analysis of the characteristics of tar content in the produced gas from EFB gasification were performed before and after decomposition with PI, P2, and P3 catalysts for their aromatic and phenolic compounds using the SPA method. As can be seen in Figure 4B, P1 dolomite showed the highest activity for the decomposition of the total light aromatics and naphthalene compared to P2 and P3 catalysts, while for the decomposition of phenolic compounds, P1 and P2 dolomites showed similar activity. Besides, the naphthalene conversion for P1, P2, and P3 were ~52, 39, and 21%, respectively.
The Influence of Calcined Dolomite Catalysts on Overall Product Yields and Syngas Composition
The results for the EFB gasification yields and performance using calcined dolomite, which are P1, P2, and P3 catalysts, are shown in Figure 5. All dolomites conferred more positive influence on the gas yield. The gas product increased with increasing the C/B ratio, whereas the char and tar yields decreased. The results indicate that the dolomite catalyst tends to produce a larger quantity of gas with a smaller amount of tar. This contributes to a significant effect on gasification yields and performance. As shown in Figure 5, the P1 catalyst appeared to have a stronger catalytic effect than other types of dolomites used in the EFB gasification reaction. As the C/B ratio of P1 increased from 0.05 to 0.30, the total gas yield increased ~8% (1.57 N m3/kg) compared to non-catalytic gasification (1.46 N m3/kg), whereas the total tar yield dramatically decreased approximately by 78% (8.8 mg/g) compared to the former process (non-catalytic, 41.2 mg/g). Char yield also decreased from 51.5 mg/g with zero catalyst addition to 15.4 mg/g with the addition of P1 at a C/B ratio of 0.30 (Mohammed et al., 2011).
Figure 6 shows the specific gas composition for the EFB gasification under the influence of the different C/B ratios of P1, P2, and P3 catalysts. The percentage in volume of produced gas components had a marked change with the increasing C/B ratio. As for the individual gases, dolomites had a noticeable effect of favoring the production of H2 and CO at higher C/B ratios, whereas the CO2 formation was reduced. These results could be explained by the effect of shifting reactions (Mohammed et al., 2011) and tar destruction (by reforming, cracking) reaction.
The presence of dolomites as primary catalyst favored the production of H2, although different effects could be observed. The product yield and gas species distributions were quite similar for both additions of P1 and P2 catalysts, and they were slightly different in the case of adding the P3 catalyst. This can be explained by the fact that the chemical compositions of the dolomites (Table 3) are different from each other. The chemical composition of P3 dolomite differed significantly from that of P1 and P2. The CaO and MgO contents of P1 and P2 dolomites were very close, whereas in the case of P3, these contents were relatively low. Furthermore, P1 and P2 had a much lower content of impurities than P3, whereas P3 had a higher level of impurities, especially silica (SiO2, 15.37%) and alumina (Al2O3, 1.69%).
As shown in Figure 6, the P1 catalyst shows a higher catalytic activity for gas yield and a better selectivity for H2 production than P2 and P3 dolomites. The highest H2 content of 36.87% (32.25 mg H2/g EFB) was obtained with P1 as the primary catalyst at an C/B ratio of 0.30 compared to 27.31% (21.55 mg H2/g EFB) obtained from gasification process with zero catalyst addition. Besides, the CO and CH4 contents were increased from 33.08 to 36.56% and from 13.76 to 16.26%, respectively. The CO2 content significantly decreased from 25.63%, obtained from non-catalytic gasification process, to 9.93% with the presence of P1 dolomite.
The Influence of Dolomite on Gasification Performance
As the gas yield increased with increasing the loading of catalyst to EFB, the cold gas efficiency and carbon conversion were also increased accordingly. The increasing trend in the higher heating value (HHV) of produced gas was also observed due to increment in H2, CO, and CH4 contents. As can be seen in Figure 7, the cold gas efficiency, carbon conversion, and HHV of produced gas were higher in the presence of dolomites. In case of P1 catalyst, an increase in C/B ratio from 0.05 to 0.30 improved the gas HHV from 8.38 to 9.96 MJ/N m3 compared to 8.20 MJ/N m3 for the non-catalytic gasification process. In addition, the carbon conversion was improved due to the improvement of water–gas and Boudouard reactions (Mohammed et al., 2011) through which more carbon was converted to gaseous products. The presence of P1 dolomite in the gasification system increased the cold gas efficiency from 55.80 to 70.90% at a C/B ratio of 0.30 due to the high gas yield and heating value.
Conclusion
Calcined dolomites denoted as PI, P2, and P3 catalysts are an effective catalyst for reducing tar in EFB gasification for syngas production. The results indicate that besides chemical composition, the dolomites' surface properties are also important factors for efficient tar cracking capacity. Higher surface area and pore volume contribute to higher tar reduction and catalytic activity when using P1 and P2 catalysts as compared to P3 catalysts. P3 contains low quantities of actives sites (CaO–MgO) with high amounts of impurities, which strongly reduced its catalytic activity. The calculated tar reduction (%) relative to that obtained with zero catalyst for P1, P2, and P3 were ~78, 75, and 70%, respectively. The PI catalyst increased the total yield by 8% (1.57 N m3/kg), reduced the char to 15.4 mg/g, and significantly reduced tar by 78% (8.8 mg/g) as compared to EFB gasification without a catalyst. The P1 catalyst showed higher selectivity of H2 production (32.25 mg H2/g EFB), cold gas efficiency, and carbon conversion than P2 and P3.
Data Availability Statement
The datasets generated for this study are available on request to the corresponding author.
Author Contributions
MM: carried out the main experimental activities and wrote the first draft of the manuscript. IS: carried out validation of the work and revised the manuscript. AS: designed the methodology of the work, supervision of the work, validation, and revised the manuscript. WW and YT-Y: supervision, conceptualization, and validation of the work.
Funding
The authors would like to acknowledge the financial support for this work by Universiti Putra Malaysia under the project 05/01/07/0210RU.
Conflict of Interest
The authors declare that the research was conducted in the absence of any commercial or financial relationships that could be construed as a potential conflict of interest.
References
Abdulrazik, A., Elsholkami, M., Elkamel, A., and Simon, L. (2017). Multi-products productions from Malaysian oil palm empty fruit bunch (EFB): analyzing economic potentials from the optimal biomass supply chain. J. Clean. Prod. 168, 131–148. doi: 10.1016/j.jclepro.2017.08.088
Aydin, E. S., Yucel, O., and Sadikoglu, H. (2018). Numerical and experimental investigation of hydrogen-rich syngas production via biomass gasification. Int. J. Hydrogen Energy 43, 1105–1115. doi: 10.1016/j.ijhydene.2017.11.013
González-Vázquez, M. P., García, R., Gil, M. V., Pevida, C., and Rubiera, F. (2018). Comparison of the gasification performance of multiple biomass types in a bubbling fluidized bed. Energy Convers. Manag. 176, 309–323. doi: 10.1016/j.enconman.2018.09.020
Li, Y. H., and Chen, H. H. (2018). Analysis of syngas production rate in empty fruit bunch steam gasification with varying control factors. Int. J. Hydrogen Energy 43, 667–675. doi: 10.1016/j.ijhydene.2017.11.117
Mohammed, M. A. A., Salmiaton, A., Wan Azlina, W. A. K. G., Mohammad Amran, M. S., and Fakhru'L-Razi, A. (2011). Air gasification of empty fruit bunch for hydrogen-rich gas production in a fluidized-bed reactor. Energy Convers. Manag. 52, 1555–1561. doi: 10.1016/j.enconman.2010.10.023
Mutlu, A. Y., and Yucel, O. (2018). An artificial intelligence based approach to predicting syngas composition for downdraft biomass gasification. Energy 165, 895–901. doi: 10.1016/j.energy.2018.09.131
Quitete, C. P. B., and Souza, M. M. V. M. (2017). Application of Brazilian dolomites and mixed oxides as catalysts in tar removal system. Appl. Catal. A Gen. 536, 1–8. doi: 10.1016/j.apcata.2017.02.014
Shahbaz, M., Taqvi, S. A., Minh Loy, A. C., Inayat, A., Uddin, F., Bokhari, A., et al. (2019). Artificial neural network approach for the steam gasification of palm oil waste using bottom ash and CaO. Renew. Energy 132, 243–254. doi: 10.1016/j.renene.2018.07.142
Shen, Y., Liu, Y., and Yu, H. (2018). Enhancement of the quality of syngas from catalytic steam gasification of biomass by the addition of methane/model biogas. Int. J. Hydrogen Energy 43, 20428–20437. doi: 10.1016/j.ijhydene.2018.09.068
Tian, Y., Zhou, X., Lin, S., Ji, X., Bai, J., and Xu, M. (2018). Syngas production from air-steam gasification of biomass with natural catalysts. Sci. Total Environ. 645, 518–523. doi: 10.1016/j.scitotenv.2018.07.071
Waheed, Q. M. K., Wu, C., and Williams, P. T. (2016). Pyrolysis/reforming of rice husks with a Ni–dolomite catalyst : in fl uence of process conditions on syngas and hydrogen yield. J. Energy Inst. 89, 657–667. doi: 10.1016/j.joei.2015.05.006
Keywords: empty fruit bunch, gasification, Malaysian dolomite, hydrogen yield, tar cracking
Citation: Mohammed MAA, Shafizah IN, Salmiaton A, Wan Azlina WAKG and Taufiq-Yap YH (2020) The Evaluation on Three Types of Malaysian Dolomites as a Primary Catalyst in Gasification Reaction of EFB and Tar Cracking Efficiency. Front. Energy Res. 8:38. doi: 10.3389/fenrg.2020.00038
Received: 19 November 2019; Accepted: 25 February 2020;
Published: 24 March 2020.
Edited by:
Su Shiung Lam, University of Malaysia Terengganu, MalaysiaReviewed by:
C. K. Cheng, Universiti Malaysia Pahang, MalaysiaMuhammad Aziz, The University of Tokyo, Japan
Jude Onwudili, Aston University, United Kingdom
Copyright © 2020 Mohammed, Shafizah, Salmiaton, Wan Azlina and Taufiq-Yap. This is an open-access article distributed under the terms of the Creative Commons Attribution License (CC BY). The use, distribution or reproduction in other forums is permitted, provided the original author(s) and the copyright owner(s) are credited and that the original publication in this journal is cited, in accordance with accepted academic practice. No use, distribution or reproduction is permitted which does not comply with these terms.
*Correspondence: A. Salmiaton, bWllQHVwbS5lZHUubXk=