- Jiangxi Key Laboratory of Power Battery and Material, School of Materials Science and Engineering, Jiangxi University of Science and Technology, Ganzhou, China
The precursor material of Ni0.8Co0.1Mn0.1(OH)2 was prepared by a co-precipitation method to obtain the layered cathode materials LiNi0.8Co0.1Mn0.1O2 (811) through roasting with LiOH·H2O. Then the SnO2-modified samples were obtained by adding tin oxide into the ball mill. It was found by XRD characterization of the original and modified samples, that the addition of SnO2 did not change the layered structure of the raw materials. Microstructure and distribution of the SnO2 were analyzed with SEM and EDS. Charge/discharge tests indicated that the SnO2-modified phases improved the cycling stability and rate capability. The results of CV test showed that the polarization of SnO2 modified electrode was smaller. AC impedance showed that SnO2/LiNi0.8Co0.1Mn0.1O2 electrode had smaller Rct and Rf value. The above test results indicate that the modification of SnO2 improves the electrochemical performance of cathode material LiNi0.8Co0.1Mn0.1O2.
Introduction
Layered Ni-based cathode materials have attracted more and more attention due to their high energy density and environmental friendliness. Among these materials, LiNi0.8Mn0.1Co0.1O2 (811) material has become the focus of many pursuits because of its high specific discharge capacity, low material cost, and environmental protection concept. However, the stability and safety problems of this material are more prominent. Researchers have carried out many modification studies to solve the problems existing in LiNi0.8Mn0.1Co0.1O2 (811), in which doping and coating are generally recognized as effective methods. Researchers believe that doping can reduce the probability of phase transition during the cycle, improve the structural stability and contribute to electrochemical performance, doping cations such as Cr3+, Ti4+, Rb+, Al3+, and Mg2+ (Li et al., 2010, 2013; Yuan et al., 2014; Du et al., 2015; Dong et al., 2017; Zhang et al., 2017). Semiconductive or insulating materials are usually adopted to coat the LiMO2 phase because it has the functions of protecting active substances from diffusion and dissolution in electrolyte, improving electronic conductivity, ensuring surface structure stability and avoiding corrosion of anode materials. The materials selected for coating are mainly some substances with relatively stable chemical properties, such as oxides, fluorides, salts and polymers. As previously reported, AlF3, Al2O3, TiO2, ZnO, Li4SiO4, LiAlO2, and SnO2 (Yang et al., 2012; Lee et al., 2013; Wang et al., 2015; Dai et al., 2016; Lai et al., 2016; He et al., 2017; Srur-Lavi et al., 2017; Liua et al., 2018; Zheng et al., 2018; Xie et al., 2019) were used as effective coating materials for lithium battery cathode materials. The coated materials contribute to more stable SEI film, which can slow down the decomposition of electrolyte and protect bulk materials from corrosion during charging and discharging. For instance, SnO2 was adopted to improve the electrochemical properties in many cathode materials with better results such as LiCoO2 (Hudaya et al., 2014), LiFePO4 (Ziolkowska et al., 2013), and LiMn2O4 (Ma et al., 2017), LiNi1/3Co1/3Mn1/3O2 (Luo et al., 2015), Li1.2Mn0.54Co0.13Ni0.13O2 (Li B. et al., 2016), LiNi0.8Co0.15Al0.05O2 (He et al., 2017; Xie et al., 2019). However, the influence of SnO2 modification on electrochemical properties of LiNi0.8Co0.1Mn0.1O2 cathode materials has rarely been researched.
In this work, SnO2/LiNi0.8Co0.1Mn0.1O2 was prepared by facile ball-milling post-treatment. The structure and morphology of LiNi0.8Co0.1Mn0.1O2 with or without SnO2 modification were investigated and the charge transfer resistance and electrochemical properties of SnO2 modification on the LiNi0.8Co0.1Mn0.1O2 material were discussed in detail.
Materials and Methods
Synthesis and Characterization
The layered Ni-rich material of LiNi0.8Co0.1Mn0.1O2 was prepared by LiOH·H2O and Ni0.8Co0.1Mn0.1(OH)2 precursor formed by a simple continuous co-precipitation method through high temperature solid phase reaction. In this preparation process, excessive lithium hydroxide 5% (Li et al., 2012), 550°C for 6 h, 800°C for 12 h, and oxygen is introduced into the whole process. SnO2-modified phases were further obtained by mechanical ball milling treatment. The mass percentage of SnO2 in composites is as follows: 1, 2, 3, and 4 wt%.
The X-ray diffraction was measured on Bruker D8 Advance X-ray Diffractometer. The morphology of the material was examined by ZEISS EVO/MA10 electron microscope. Cyclic voltammetry (CV) and EIS measurements of the cells were collected on Ivium-n-Stat electrochemical workstation.
The cathode materials were assembled into CR2032 type button batteries to detect electrochemical performances. The preparation of cathode active materials slurry and the assembly of batteries can be referred to Reference (Li et al., 2018).
Results and Discussion
XRD Phase
Figure 1 shows the structure of pristine LiNi0.8Co0.1Mn0.1O2 (NCM) materials and its coating process with SnO2. As shown in the figure, the cathode materials are essentially the same and belong to a hexagonal α-NaFeO2 structure with a space group of Rm, the lattice constant are very close which means that the crystal structure of NCM is not affected by coating with nano SnO2. Moreover, the distinct splitting of (006)/(102) and (108)/(110) indicates the products possess well-developed layered structure (Li G. Y. et al., 2016). The XRD plots of SnO2 modification samples also show the diffraction peak at about 27 degree representing for the plane (110) of SnO2, which becomes obvious with the increase of the concentration of SnO2.
Microtopography
The SEM images of pristine and nano SnO2-modified samples are shown in Figure 2. It is clearly seen that the second particles of pristine samples (the diameter is about 10 μm) are made of abundant primary nanoparticles which the surface is smooth. Compared with the pristine sample, the surface of the sample modified by SnO2 appears rough, and some bright white spots can be seen because the nano tin dioxide particles partially cover it. However, when the mass percentage of SnO2 is 4 wt%, the SnO2 nanoparticles begin to aggregate and distribute unevenly on the surface of the original particles which will reduce the electro-chemical performance. The EDS spectra of 3 wt% SnO2 modified specimen are shown in Figure 3 which is also used to confirm the distribution of SnO2 particles on the surface of LiNi0.8Co0.1Mn0.1O2 cathode materials. As can be seen from the figure, the tin element covers the surface of the cathode material relatively evenly.
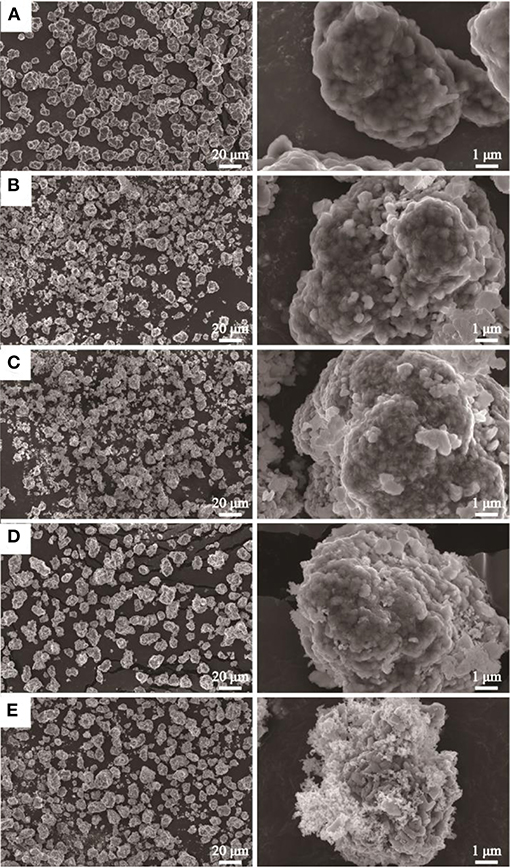
Figure 2. SEM images of 811 (A) and nano SnO2-modified samples (B: 1 wt%; C: 2 wt%; D: 3 wt%; E: 4 wt%).
Electrochemical Performance
The cyclic voltammograms for the first, second, and third cycle were tested in the range of 2.5–4.6 V with a scanning rate of 0.1 mV s−1 to clearly obtain the different redox behaviors of pristine and nano SnO2-modified samples. As shown in Figure 4, there are three redox couples in the cyclic voltammogram curves of 2.5–4.3 V voltage range (Abraham et al., 2003; Belharouak et al., 2006), indicating the polyphase transition from hexagonal to monoclinic (H1/M), monoclinic to hexagonal (M/H2), hexagonal to hexagonal (H2/H3). The major anodic peak of the first cycle is different from the second and third cycle which may be partially attributed to the formation of solid electrolyte inter-phase (Zhong et al., 2015, 2016) or the cation mixing (Zhong et al., 2015) in the first cycle. There is only small shift of the major anodic peak in the second and third cycle. This means that the material has good intercalation and deintercalation reversibility of lithium ions which facilitates the good electrochemical properties. As shown in Table 1, nano SnO2-modified samples exhibit smaller potential difference between anodic peak and cathodic peak (ΔψV) compared to the pristine sample. The value of ΔψV is only 20 mV when the tin oxide content is 3 wt%. It can be seen from the above data that nano SnO2-modification can reduce electrode polarization.
Figures 5A,B are cycling performance curves of pristine and SnO2-modified materials between the voltage of 2.8–4.35 V at 0.2C and 1C rate. The initial specific capacities of pristine and SnO2-modified samples at 0.2C rate (1, 2, 3, and 4 wt%) were, respectively, 185.7, 181.3, 183.375, 187.5, and 179.9 mAh/g. The corresponding capacity was maintained with 85.25%, 90.40%, 91.88%, 90.77%, and 88.72 wt% after 50 cycles. The capacity of each material decreases rapidly at 1C rate, however, compare to the pristine, the capacity retention rate increased from 74.23 to 87.43% when the SnO2 content is 3 wt%. All these results attributed to the fact that the proper addition of SnO2 not only improves the conductivity of the material, but also reduces the corrosion of the electrolyte. However, when the SnO2 content is 4 wt%, the capacity and recyclability of cathode materials will be reduced due to the uneven distribution of SnO2 in the surface of NCM and hinder the migration of lithium ions.
As shown in Figure 6, the rate performances for the pristine and SnO2-modified materials were tested at 0.2C, 0.5C, 1C, 2C, and 5C, respectively. The average discharge specify capacity of pristine and SnO2-NCM (the SnO2 is 1, 2, 3, and 4 wt%) at 0.2C rate are, respectively, 179.6, 174.4, 180.8, 191.8, and 185.8 mAh/g, which, respectively, decreased to 134.3, 141.0, 150.9, 158.2, and 151.1 mAh/g when the current rate raised to 5C rate with the capacity retentions of 74.8, 68.6, 80.8, 83.5, 82.5, and 81.3%. And the discharge capacities almost restored from decay when the rate returned to 0.2C. The results showed that the existence of SnO2 improved the rate performance of the cathode material electrode. The reason may be that the existence of SnO2 in the electrode passivates the reaction between the cathode and the electrolyte which contributes to forming a more stable interface.
Electrochemical impedance spectroscopy measurement (EIS) technology was applied to study the internal resistance change of the five electrodes. The EIS profiles of the 5th cycled electrodes are demonstrated in Figure 7. Rs, Rsf, and Rct calculated from EIS results are tabulated in Table 2. All of the EIS profiles are similar and consist of two semicircles and a line, according to the reported references (Noh et al., 2013), the high-frequency semicircle represent the resistance of Li+ diffusion in the surface layer (Rsf), the mid-frequency semicircle and the low-frequency line should be, respectively, ascribed to the charge transfer resistance (Rct) and the Warburg impedance of solid phase diffusion (Zw). Compared with the original electrode, the SEI film resistance (Rsf) and charge transfer resistance (Rct) of SnO2 modified electrodes are slightly smaller in which the SEI film resistance of 3 wt% SnO2 modified electrode is the smallest. Therefore, the modification of SnO2 greatly improves the ionic conductivity, which improves the electrochemical performance of the material.
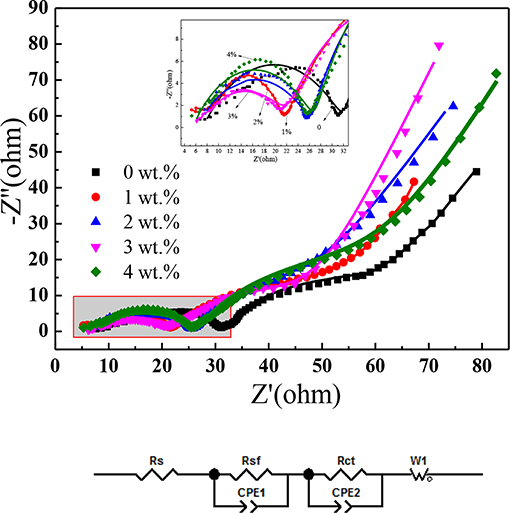
Figure 7. Nyquist plots and equivalent circuit for x wt% SnO2-modified NCM (x = 0, 1, 2, 3, 4) positive electrode materials.
Conclusion
In this paper, the precursor material of Ni0.8Co0.1Mn0.1(OH)2 was prepared by a co-precipitation method then roasted with LiOH·H2O to obtain the layered cathode materials LiNi0.8Co0.1Mn0.1O2. SnO2-modified phases were further obtained by mechanical ball milling treatment. The effect of SnO2 modification on the structure, morphology and electrochemical properties of LiNi0.8Co0.1Mn0.1O2 was mainly studied. Duo to the existence of SnO2 in the surface of LiMO2 active materials, the cycling stability and rate capability are greatly improved. The results of cyclic voltammetry (CV) show that the existence of SnO2 can reduce the polarization of the electrode. When the content of SnO2 is 3 wt%, the sample has the lowest SEI film resistance (Rsf) and best cycling performance performed 0.2C or 1C under the potential of 2.75–4.35 V. In conclusion, this study has potential significance for improving the cyclic and rate properties of nickel-based cathode materials.
Data Availability Statement
The datasets generated for this study are available on request to the corresponding author.
Author Contributions
CW: experimental design, data analysis and discussion, and article writing. WP: battery preparation, electrochemical performance testing, and data discussion. ZL: experimental design, electrochemical performance analysis, and discussion. YL: synthesis of cathode compounds and SnO2 doped modification experiment. SZ: experimental design. QZ: CV performance test, results analysis, and discussion.
Funding
The project was supported by National Natural Science Fund of China (No. 51874151), Jiangxi Province Science and Technology Plan Project (No. 20151BBE50106), and Jiangxi Provincial Education Office Natural Science Fund Project (No. GJJ160202).
Conflict of Interest
The authors declare that the research was conducted in the absence of any commercial or financial relationships that could be construed as a potential conflict of interest.
References
Abraham, D. P., Twesten, R. D., Balasubramanian, M., Kropf, J., Fischer, D., McBreen, J., et al. (2003). Microscopy and spectroscopy of lithium nickel oxide-based particles used in high power lithium-ion cells. J. Electrochem. Soc. 150, A1450–A1456. doi: 10.1149/1.1613291
Belharouak, I., Lu, W., Vissers, D., and Amine, K. (2006). Safety characteristics of Li(Ni0.8Co0.15Al0.05)O2 and Li(Ni1/3Co1/3Mn1/3)O2. Electrochem. Commun. 8, 329–335. doi: 10.1016/j.elecom.2005.12.007
Dai, G., Du, H., Wang, S., Cao, J., Yu, M., Chen, Y., et al. (2016). Improved electrochemical performance of LiNi0.8Co0.15Al0.05O2 with ultrathin and thickness controlled TiO2 shell via atomic layer deposition technology. RSC Adv. 6, 100841–100848. doi: 10.1039/C6RA21903A
Dong, M. X., Li, X. Q., Li, X. H., Guo, H. J., and Huang, Z. J. (2017). Enhanced cycling stability of La modified LiNi0.8−xCo0.1Mn0.1LaxO2 for Li-ion battery LiNi0.8−xCo0.1Mn0.1LaxO2. Trans. Nonferrous Met. Soc. China 27, 1134–1142. doi: 10.1016/S1003-6326(17)60132-8
Du, R., Bi, Y. J., Yang, W. C., Peng, Z., Liu, M., Liu, Y., et al. (2015). Improved cyclic stability of LiNi0.8Co0.1Mn0.1O2 via Ti substitution with a cut-off potential of 4.5V. Ceram. Int. 41, 7133–7139. doi: 10.1016/j.ceramint.2015.02.026
He, X., Du, C., Shen, B., Chen, C., Xu, X., Wang, Y., et al. (2017). Electronically conductive Sb-doped SnO2 nanoparticles coated LiNi0.8Co0.15Al0.05O2 cathode material with enhanced electrochemical properties for Li-ion batteries. Electrochim. Acta 236, 273–279. doi: 10.1016/j.electacta.2017.03.215
Hudaya, C., Park, J. H., Lee, J. K., and Choi, W. (2014). SnO2-coated LiCoO2 cathode material for high-voltage applications in lithium-ion batteries. Solid State Ionics 256, 89–92. doi: 10.1016/j.ssi.2014.01.016
Lai, Y. Q., Xu, M., Zhang, Z., Gao, C., Wang, P., and Yu, Z. (2016). Optimized structure stability and electrochemical performance of LiNi0.8Co0.15Al0.05O2 by sputtering nanoscale ZnO film. J. Power Sources 309, 20–26. doi: 10.1016/j.jpowsour.2016.01.079
Lee, S. H., Yoon, C. S., Amine, K., and Sun, Y. K. (2013). Improvement of long-term cycling performance of Li[Ni0.8Co0.15Al0.05] O2 by AlF3 coating. J. Power Sources 234, 201–207. doi: 10.1016/j.jpowsour.2013.01.045
Li, B., Wang, J., Cao, Z. L., Zhang, P., and Zhao, J. B. (2016). The role of SnO2 surface coating in the electrochemical performance of Li1.2Mn0.54Co0.13Ni0.13O2 cathode materials. J. Power Sources 325, 84–90. doi: 10.1016/j.jpowsour.2016.06.027
Li, G. Y., Zhang, Z. J., Wang, R. N., Huang, Z. L., Zuo, Z. C., and Zhou, H. H. (2016). Effect of trace Al surface doping on the structure, surface chemistry and low temperature performance of LiNi0.5Co0.2Mn0.3O2 cathode. Electrochim. Acta 212, 399–407. doi: 10.1016/j.electacta.2016.07.033
Li, L. J., Chen, Z. Y., Long, X. B., Jin, W. F., and Xia, Q. (2013). Synthesis of cation-substituted LiNi0.8Co0.1Mn0.1O2 from laterite. Ionics 19, 1215–1222. doi: 10.1007/s11581-013-0957-3
Li, L. J., Li, X. H., Wang, Z. X., Guo, H. J., Yue, P., Chen, W., et al. (2010). Synthesis, structural and electrochemical properties of LiNi0.79Co0.1Mn0.1Cr0.01O2 via fast co-precipitation. J. Alloy Comp. 507, 172–177. doi: 10.1016/j.jallcom.2010.07.148
Li, Z., Chernova, N. A., Feng, J., Upreti, S., Omenya, F., and Whittingham, M. S. (2012). Stability and rate capability of Al substituted lithium-rich high-manganese content oxide materials for Li-ion batteries. J. Electrochem. Soc. 159, A116–A120. doi: 10.1149/2.044202jes
Li, Z. F., Luo, C. Y., Wang, C. X., Jiang, G. X., Chen, J., Zhong, S. W., et al. (2018). Effects of Nb substitution on structure and electrochemical properties of LiNi0.7Mn0.3O2 cathode materials. J. Solid State Electr. 22, 2811–2820. doi: 10.1007/s10008-018-3975-2
Liua, W., Lia, X., Xiong, D., Hao, Y., Li, J., Kou, H., et al. (2018). Significantly improving cycling performance of cathodes in lithium ion batteries: the effect of Al2O3 and LiAlO2 coatings on LiNi0.6Co0.2Mn0.2O2. Nano Energy 44, 111–120. doi: 10.1016/j.nanoen.2017.11.010
Luo, Z. M., Sun, Y. G., and Liu, H. Y. (2015). Electrochemical performance of a nano SnO2-modified LiNi1/3Co1/3Mn1/3O2 cathode material. Chin. Chem. Lett. 26, 1403–1408. doi: 10.1016/j.cclet.2015.06.007
Ma, F., Geng, F., Yuan, A., and Xu, J. Q. (2017). Facile synthesis and characterization of a SnO2-modified LiNi0.5Mn1.5O4 high-voltage cathode material with superior electrochemical performance for lithium ion batteries. Phys. Chem. Chem. Phys. 19, 9983–9991. doi: 10.1039/C7CP00943G
Noh, H. J., Youn, S., Yoon, C. S., and Sun, Y. K. (2013). Comparison of the structural and electrochemical properties of layered Li[NixCoyMnz]O2 (x = 1/3, 0.5, 0.6, 0.7, 0.8 and 0.85) cathode material for lithium-ion batteries. J. Power Sources 233, 121–130. doi: 10.1016/j.jpowsour.2013.01.063
Srur-Lavi, O., Miikkulainen, V., Markovsky, B., Grinblat, J., Talianker, M., Fleger, Y., et al. (2017). Studies of the electrochemical behavior of LiNi0.8Co0.15Al0.05O2 electrodes coated with LiAlO2. J. Electrochem. Soc. 164, A3266–A3275. doi: 10.1149/2.1631713jes
Wang, J., Du, C., Yan, C., He, X., Song, B., Yin, G., et al (2015) Al2O3 Coated concentration-gradient Li[Ni0.73Co0.12Mn0.15]O2 cathode material by freeze drying for long-life lithium ion batteries. Electrochim. Acta 174, 1185–1191. doi: 10.1016/j.electacta.2015.06.112.
Xie, Z. C., Zhang, Y. Y., Yuan, A. B., and Xu, J. Q. (2019). Effects of lithium excess and SnO2 surface coating on the electrochemical performance of LiNi0.8Co0.15Al0.05O2 cathode material for Li-ion batteries. J. Alloy Comp. 787, 429–439. doi: 10.1016/j.jallcom.2019.02.127
Yang, K., Fan, L. Z., Guo, J., and Qu, X. H. (2012). Significant improvement of electrochemical properties of AlF3-coated LiNi0.5Co0.2Mn0.3O2 cathode materials. Electrochim. Acta 63, 363–368. doi: 10.1016/j.electacta.2011.12.121
Yuan, S., Liu, L. B., Tang, Y. P., Wang, J. H., and Guo, Y. Z. (2014). Synthesis and electrochemical properties of cathode material LiNi0.8Co0.1Mn0.1O2 via Li, Mg, Al dopping. Adv. Mater. Res. 1058, 302–306. doi: 10.4028/www.scientific.net/AMR.1058.302
Zhang, Z. L., Chen, D. H., and Chang, C. (2017). Improved electrochemical performance of LiNi0.8Co0.1Mn0.1O2 cathode materials via incorporation of rubidium cations into the original Li sites. Rsc Adv. 7, 51721–51728. doi: 10.1039/C7RA10053A
Zheng, J., Yang, Z., He, Z., Tong, H., Yu, W., and Zhang, J. (2018). In situ formed LiNi0.8Co0.15Al0.05O2@Li4SiO4 composite cathode material with high rate capability and long cycling stability for lithium-ion batteries. Nano Energy 53, 613–621. doi: 10.1016/j.nanoen.2018.09.014
Zhong, S., Chen, P., and Yao, W. (2015). Ni-rich layered oxide Li1.05(Ni0.7Mn0.3)O2 as a highly reversible cathode material for lithium-ion batteries. ECS Electrochem. Lett. 4, A45–A48. doi: 10.1149/2.0041506eel
Zhong, S. W., Lai, M. Z., Yao, W. L., Li, Z, and Li, Z. C. (2016). Synthesis and electrochemical properties of LiNi0.8CoxMn0.2−xO2 positive-electrode material for lithium-ion batteries. Electrochim Acta 212, 343–351. doi: 10.1016/j.electacta.2016.07.040
Keywords: Li-ion battery, Ni-based cathode materials, SnO2 modification, electrochemical performances, lower electrode polarization
Citation: Wang C, Peng W, Li Z, Liang Y, Zhong S and Zhang Q (2019) Synthesis and Characterization of Nano SnO2 Modification on LiNi0.8Mn0.1Ni0.1O2 Cathode Materials for Lithium Ion Batteries. Front. Energy Res. 7:125. doi: 10.3389/fenrg.2019.00125
Received: 20 September 2019; Accepted: 25 October 2019;
Published: 26 November 2019.
Edited by:
Yutao Li, University of Texas at Austin, United StatesReviewed by:
Biyi Xu, University of Texas at Austin, United StatesNan Wu, Beijing Institute of Technology, China
Yijie Liu, Nanjing University, China
Copyright © 2019 Wang, Peng, Li, Liang, Zhong and Zhang. This is an open-access article distributed under the terms of the Creative Commons Attribution License (CC BY). The use, distribution or reproduction in other forums is permitted, provided the original author(s) and the copyright owner(s) are credited and that the original publication in this journal is cited, in accordance with accepted academic practice. No use, distribution or reproduction is permitted which does not comply with these terms.
*Correspondence: Shengwen Zhong, anh1c3R6c3cmI3gwMDA0MDsxMjYuY29t; Zhifeng Li, anhsemZlbmcmI3gwMDA0MDsxNjMuY29t