- 1Department of Environmental Science, International Islamic University, Islamabad, Pakistan
- 2Biodiesel Lab, Department of Plant Sciences, Quaid-i-Azam University, Islamabad, Pakistan
- 3Medicinal Aromatic and Poisonous Plants Research Center, College of Pharmacy, King Saud University, Riyadh, Saudi Arabia
- 4Analytical Lab, Department of Chemistry, Quaid-i-Azam University, Islamabad, Pakistan
This study examined the potential of nanocatalyst CuO-CeO2 and Fe2O3 for efficient conversion of Sterculia foetida seed Oil into biodiesel. S. foetida contains 40% oil content and low free fatty acid value (0.18 mg KOH/g). The synthesized nanocatalyst was characterized using X-Ray Diffraction (XRD), Fourier Transform Infrared Spectroscopy (FT-IR), and Scanning Electron Microscopy (SEM) techniques. The maximum conversion was achieved (92% yield) using CuO-CeO2 at 0.25% catalyst loading. The optimized reaction was carried out by experimental variables included molar ratio (1:9), temperature (70°C), reaction time (3 h) and stirring rate (600 rpm) using reflux transesterification method. The XRD results showed the size of crystals with order 54.4 nm for CuO-CeO2 and 31.3 nm for Fe2O3. The SEM images of CuO-CeO2 showed spherical structure having an average particle size of 32.3 nm. SEM images of Fe2O3 showed the size ranges from 46.27 to 28.76 nm having regular morphology, including spherical shape. The FT-IR analysis of this nanocatalyst also reinforced the results of this study. Gas Chromatography Mass Spectroscopy (GC-MS) and Fourier Transform Infrared Spectroscopy (FT-IR) confirmed the efficient conversion of S. foetida seed oil into biodiesel using prepared nanocatalysts. The prepared nanocatalysts are cheaper, readily available and can be used for industrial scale biofuel production assembly, making it economically feasible and more cost effective.
Introduction
Sterculia foetida, commonly known as Bottle tree, Java Olive, Bastard Poon Tree, Jangli Badam, Hazel Sterculia, and Wild Almond tree, belongs to the genus Sterculiae. The family Sterculiaceae is considered one of the non-drying and non-edible oil yielding species. It is considered as a potential non-edible feed stock for biodiesel production amongst the previously studied framework of non-edible seed oil. This family represents 10 genera and 20 species in Pakistan. Most of them are introduced as a decorative plant (Rao et al., 2015). S. foetida is planted in many parts of the world, such as Ethiopia, Australia, Bangladesh, India, Indonesia, Malaysia, Oman, Uganda, Thailand, Somalia, Sri Lanka as well as Pakistan. It is a wild plant that is modified by tropical and sub-tropical areas (30 North Latitude to 35 South Latitude). The plant has an average life span of more than 100 years (Heyne, 1987; Munarso, 2010). S. feotida is a large, straight and deciduous tree which can grow up to 40 m in height and 3 m in width. It is commonly grown across roadsides and in parks for shadow, variegating flashy flowers. The fruit is 10 m long, woody red, nearly smooth in appearance. The single large seed is enclosed by a shell and a thin 1–2 mm layer of pulp. Each fruit contains 10–15 seeds, giving about 250–300 kg seeds annually (Munarso, 2010). Seed collection from the fruit is somewhat problematic due to the presence of harsh curls in it. The main compositions of S. foetida seeds are fats and protein which are 51.78 and 21.61%, respectively (Heyne, 1987; Munarso, 2010).
Alternative fuel has acquired more attention over the past twenty-five years due to fossil fuel depletion, climate change and human health hazards (Gardy et al., 2018). Biodiesel, being eco-friendly, non-toxicity, and biodegradability are gaining popularity. Worldwide, 90% of biodiesel is produced by a homogeneous catalyzed transesterification process, using edible feedstock (Rehan et al., 2018). Substantial amount of fresh water and arable land are required for its cultivation, which could lead to food security problems in developing countries (Salam et al., 2016). The above mentioned issues can be overwhelmed by using non-edible feedstock, such as waste cooking oil, Jatropha oil, Neem, Pongamia, Karanja, Rocket seed oil, Chinese wild tallow tree, Castor beans, Hemp, Milo, etc. (Rashid et al., 2015). This non-edible feedstock contain large amount of Free Fatty Acids (FFA) resulting in soap formation. Therefore, the nanocatalyst is currently used for synthesis of biodiesel to overcome such problems. These materials have significant permeability, high contact area, high thermal stability, and good chemical properties, culminating in a more effective participation in the chemical reactions to produce biodiesel.
To the best of our knowledge based on detail literature reviewed, qualitative, and quantitative analysis of fatty acid methyl esters (FAMESs) profile of non-edible seed oils has been the focus of many advanced publications. This study focused, for the first time, on a detailed investigation on seed oil source of S. feotida as a new addition in the list of non-edible feedstock for biodiesel synthesis using application of nano-catalysts. Biodiesel can be defined as fuel consisting of mono alkyl esters of long chain fatty acids derived from renewable sources. Biodiesel have various reigns over conventional diesel, such as biodegradability, non-toxicity, renewability, environment friendly, high flash point, and lubricity (Kumar et al., 2011; Okitsu et al., 2014). There are several problems related to biodiesel production, i.e., expensive raw material, shortage of food supply and high energy consumption. Recently, an increase in energy consumption causes a steady depletion of conventional petrol-diesel reserves. According to this theory, the higher demand for oil will require its exceeded the supplies, (Fusco, 2006; Ashnani et al., 2014; Datta and Mandal, 2014; Ullah et al., 2015). To fill this gap, it is significant to investigate the potential of appropriate feedstock like S. feotida as non-edible seed oil production which must be increased significantly if biodiesel possesses the potential impact to contribute in solving energy crises.
Different approaches have been used to reduce the viscosity of oil such as dilution, micro emulsions with short chain alcohols, pyrolysis, catalytic cracking, and transesterification (Farobie and Matsumura, 2015). Transesterification is one of the viable processes used for biodiesel synthesis at industrial scale (Edward and Peggy, 2013) because it gives high yield with low temperature and pressure at short reaction time (Shikha and Chauhan, 2012).
Transesterification method is used for biodiesel production. In this process triglycerides first convert into diglycerides followed by the conversion of diglycerides into monoglycerides in presence of methanol and suitable catalyst (Farobie and Matsumura, 2015). Homogeneous catalysts are typically used at large scale for biodiesel production. Although, they show good catalytic activity with several inadequacies, such as high production cost, difficulty in product isolation and requirement of large quantity of water. A new drift in biodiesel production is the use of heterogeneous alkali catalysts. Heterogeneous catalytic methods are time consuming, low catalytic stability with significant escape of catalyst components to the deactivation of the catalyst, incompetent, and robust to mass transfer. In contrast, nanocatalysts are gaining much more attention in biodiesel production due to its latent role to overcome the disadvantages associated with the use of homogeneous and heterogeneous catalyst. Nanocatalysts show several advantages such as large surface to volume ratio, high catalytic efficiency due to its Nano dimension and morphological structure, good rigidity, low separation cost, and reusability, resistance to saponification, simple operational procedures, and decrease in pollution regeneration.
Among nano-catalysts, transition metals catalysts are more effective than alkali or acid catalyst for biodiesel production (Hu et al., 2011). In the development of nanoparticles, transition metals are intensively perused because of their prominence in the field of applications in science and technology (Aparna et al., 2012). The selected metal oxide nanocatalysts CuO-CeO2 and Fe2O3 have high catalytic efficiency, higher stability, and lower cost as compared to noble metals. Due to turbulent flow and shock waves, metal particles can move toward each other at high-speed and may also melt at collision point. The suspension solution occurs because of very quick Inter-particle collisions; as a result, the mass of the particle is formed. Collisions can cause a crushing blow between particles, and so, increased specific surface, and finally to achieve high reactivity and good conversion (Karimi et al., 2013).
In recent years, several mixed oxide catalysts have been practiced for synthesizing biodiesel owing to their highest catalytic activity during transesterification reaction. Since mixed oxides possess strong basic sites that increases catalytic surface area which increases catalytic stability and activity during the process. This also helps in the reutilization of catalysts after the completion of its reaction. For instance, CaCeO3 gives 80% biodiesel yield during transesterification reaction with the reusability of about 5 to 7 times (Okoronkwo et al., 2012). CuO-CeO2 gives 92.59% biodiesel via transesterification of waste cooking oil and proves to be stable during the process (Tajammul Hussain et al., 2013). In the methonolysis of Pistaciachinensis seed oil via CuO-CeO2 gives 91% biodiesel yield and can be used with five times consecutively, while Fe-Zn double metal cyanide gives 92% biodiesel yield with the reusability of five times(Chouhan and Sarma, 2011). On the basis of reported work, transition metal mixed oxide Nano catalysts (CuO-CeO2 and Fe2O3) are therefore, selected for the present work on the basis of its stability, reusability, and highest catalytic performance under mild reaction conditions.
Previously, several mixed oxide catalysts have been practiced for synthesizing biodiesel owing to their highest catalytic activity during transesterification reaction. Since mixed oxides possess strong basic sites that increase the catalytic surface area which increases catalytic stability and activity during the process. This also helps in the reutilization of catalysts after the completion of its reaction. For instance CaCeO3 gives 80% biodiesel yield during transesterification reaction with the reusability of about 5–7 times (Okoronkwo et al., 2012). CuO-CeO2 gives 92.59% biodiesel via transesterification of waste cooking oil and proves to be stable during the process (Tajammul Hussain et al., 2013). In the methonolysis of Pistacia chinensis seed oil via CuO-CeO2 gives 91% biodiesel yield and can be used with five times consecutively, while Fe-Zn double metal cyanide gives 92% biodiesel yield with the reusability of five times (Chouhan and Sarma, 2011). On the basis of reported work transition metal mixed oxide Nanocatalysts (CuO-CeO2 and Fe2O3) is therefore, selected for the present work on the basis of its stability, reusability, and highest catalytic performance under mild reaction conditions.
Several studies focused on the Biodiesel production using nano-catalysts. On the other hand, comparative studies are very limited. In the present study, comparative evaluation has been made to deliberate the effects of two different nano-catalysts (CuO-CeO2, Fe2O3) in terms of their characterization i.e., X-ray powder diffraction (XRD), Scanning Electron Microscopy (SEM), Fourier transfer Infrared spectroscopy (FT-IR), on FAMEs synthesis using non-edible seed oil of S. feotida. In addition to this, synthesized FAMEs have been quantitatively analyzed using analytical techniques such as Gas Chromatography-Mass Spectrometry (GC-MS), FT-IR.
Methods
The experimental work was conducted at Wet Lab, Department of Environmental Science, International Islamic University Islamabad and Nano Science and Technology research lab of the National Centre for Physics, Quad-i-Azam University Islamabad, Pakistan. Shells of S. feotida plant was collected through several field trips across the country. The collected shells were placed in sun light to remove insects and moisture, then processes for seed separation. Seeds were washed with soft warm distilled water to eradicate the dirt then dried in an oven at 55°C. The Soxhlet apparatus was used to determine seed oil contents. Crude oil was extracted using an electric oil expeller (KEK P0015-10127) from Germany.
Equipment and Chemicals
Digital Weighing Balance (GF-3000), Teflon Magnetic Stirrer (AM4, VELP, SCIENTIFICA), Thermometer, pH Paper, Conical Flasks, Beakers (100 and 500 ml), Filter Paper (Wattman 42), Aluminum Foil, Pipette (10 ml), Iron Stand, Electric Oil Expeller (KEK P0015, 10127 Germany), Burette, Soxhlet Assembly (Behr Labor – Technik), Magnetic Stirrers, Pestle mortar, Drying Oven (DHG-9053A), Calcination Furnance (Neycraft), Sodium hydroxide (NaOH), Methanol 99.9% purity, Cerium (IV) oxide, Iron Sulfate, Copper Oxide, Sulfuric acid. All the reagents used were of analytical grade and purchased from Merck (Germany), Scharlau (Spain), and Sigma Aldrich (USA).
Oil Extraction
Soxhlet apparatus was used for solvent extraction. It is a sequence by which chemical constituents are removed from sample by using organic solvent. Dried seeds were wrinkled into fine powder using pestle and mortar. Round bottom flask was filled with 250 ml of n-hexane. Thimble was filled with 5 g of seeds powder and heated up to 60°C for 5 h. In this process, solvent is continually recovered and reused. Oil droplets were also visible in the round bottom flask. The resulting wet sample was again oven dried at 60°C to evaporate the solvent and weigh the sample. The reduction in the sample weight was determined to calculate the amount of oil extracted.
Where W1 = Weight of Empty Flask
W2 = Weight of Empty Flask + powdered Sample
W3 = Weight of Sample Used
W4 = Weight of Extracted Oil
The collected oil was pre-treated by filtration and titrated using acid base titration method to determine its FFAs contents. The resulting crude oil contained 3.7 wt% FFA.
Synthesis of Nanocatalyst (CuO-CeO2) and Fe2O3
CuO-CeO2 composite was synthesized by top down approach through the ball mill method. Equivalent amount of CuO (2 g) and CeO2 (2 g) were weighed through analytical balance and then placed in ball mill apparatus. It was made airtight with the help of a rubber piece. At room temperature the revolution per minute was 200 for 8 h. The powder was subjected to high energy collision from the balls. Then, these processed nanoparticles were calcined for 3 h at 500°C in the muffle furnace. After calcinations, the composite of CuO and CeO2was ready for characterization.
Fe2O3 was prepared by co-precipitation route. 0.1 M solution of FeSO4 was prepared. Then, 0.1 M solution of NaOH was prepared and put into the burette. Take 100 ml of Iron Sulfate into beaker and titrate it against 0.1 M NaOH, to get its basic pH i.e., 10–12. NaOH solution dropped very slowly to produce fine nanoparticles. The color of solution turns to reddish brown Iron (II) oxide, due to oxidation. The solution was frequently stirred at 600 rpm till its pH reached up to 10. When the solution pH reached 10, titration was stopped. The solution was left over night for phase separation then washed with distilled water to remove impurities of NaOH. After washing, the sample was oven dried at 90°C for 10–12 h to evaporate extra water then calcined in muffle furnace for 3 h at 500°C. Following calcination, the FeSO4 nanoparticles were ready for characterization.
Characterization of Nanocatalyst
X-Ray Diffraction
The Nanocatalyst was characterized using XRD Model No. D8 Advance Bruker, to confirm the formation of crystallite size. The Scherer Debye equation was used to calculate crystallite size. XRD measurement was performed at 2θ value between 10 and 80°C.
Scanning Electron Microscopy (SEM)
SEM was performed using scanning electron microscopy Model JEOL JSM-5910 to understand the morphology of nanocatalyst. Field emission electron microscopy with 5 kV accelerating voltage was used to attain SEM image. This allows the qualitative characterization of catalyst and support, to understand the phenomena occurring in calcination and pretreatment.
Fourier Transform Infrared (FT-IR) Analysis
FT-IR spectroscopic technique was used to identify and measure organic functional groups and inorganic ions of S. feotida biodiesel using MODEL BRUKER-TENSOR 27 in the range from 3,500 to 400 cm−1. The resolution was 1 cm−1 and 15 scans for biodiesel analysis. FT-IR of seed oil, biodiesel and catalysts were analyzed.
Biodiesel Synthesis Using Reflux Transesterification
Reflux transesterification method was used for biodiesel production from seed oil. Materials used for transesterification were Nanocatalyst, seed oil, hot plate, magnetic stirrer, thermometer, reflux condenser. The reaction was carried out in a 250 ml round bottom flask equipped with thermometer, reflux condenser and magnetic stirrer. 0.1 g Nanocatalyst was refluxed with 1:3 oil to methanol ratio for 1 h at 70°C. After cooling, preheated oil was added into flask and refluxed again at 70°C for 2 h. Then mixture was allowed to cool down and transferred into separating funnel for phase separation. The upper liquid phase was crude ester and the lower liquid phase was the glycerol. Biodiesel yield was calculated using the equation
Characterization of Synthesized Fatty Acid Methyl Esters/Biodiesel
FT-IR Analysis
FT-IR spectroscopic technique was used to determine structural composition of Sterculia feotida biodiesel using FT-IR MODEL BRUKER-TENSOR 27 in the range of 4,000 to 600 cm−1. The resolution was 1 cm−1 and 15 scans for biodiesel analysis. FT-IR of seed oil, biodiesel, and catalysts were analyzed.
GC-MS Analysis
It was used to determine the chemical composition of fatty acids in S. foetida oil biodiesel. The synthesized biodiesel was subjected to GC-MS model QP 210 ultra (Shimadzu, Japan). A sample volume of 1 ml was dissolved with 5 ml chloroform and stirred for 3 min. One microliter of this sample was injected into GC-MS model using a split mode with split ratio of 1:3. Helium was used as a vector with a flow rate of 1.44 mL/min. The column temperature was set from 50 to 300°C at the rate of 80°C/min. The temperature of detector and injector was set at 250 and 120°C.
Physico-Chemical Properties of Biodiesel
Fuel properties of synthesized biodiesel from Sterculia Oil were determined quantitatively from Pakistan State Oil (PSO) and Rawalpindi, and were compared to ASTM; biodiesel standards. Flash point (°C) was recorded at ASTM D-93,Pour point at ASTM D-97, Cloud Point °C at ASTM D-2500, Density @ 15°C kg/L at D-1298, Kinematic Viscosity @ 40°C at ASTM D-445, Sulfur % ASTM D-4294 and Total Acid Number (mg KOH/mg) at ASTM D-974 (Atabani et al., 2013) was recorded and compared to the ASTM.
Results and Discussion
Biodiesel Synthesis From S. foetida Seed Oil
S. foetida seed oil was converted into biodiesel, and oil content and FFA contents were determined. Based on dry biomass, the extracted oil percentage was 40% which is higher as compared to other edible and non-edible oil sources studied in previous literature, such as Pongamia oil (37%) (Baskar et al., 2016), Melia Azedarch fruit oil (39%) (Stavarache et al., 2008), Rocket seed (35%) (Chakrabarti et al., 2011), Soybean (18–22%) (Williams, 2005; Moser, 2010). Biodiesel quality and yield highly depend upon the FFA contents. As reported in literature, FFA content of crude oil up to 2.5% is suitable for biodiesel synthesis. Efficiency of crude oil gradually decreases outside the prescribed limit, and soap formation occurs which ultimately causes difficulty in separation process (Naik et al., 2010; Shikha and Chauhan, 2012).
Two nano-catalysts CuO-CeO2 and Fe2O3 in different concentrations were used for efficient conversion of S. foetida seed oil (SFSO) into biodiesel. Data presented in Table 1 depicts that conversion rate of oil is mainly dependent on type and amount of catalyst. At 0.25% of said catalysts concentration, the conversion rate is relatively high, up to 92%. While, by increasing the catalyst amount shows declining trends in biodiesel yield, keeping all the variables constant. Loss in biodiesel yield is proportional to the catalyst amount as shown in Table 1. Higher amount of catalyst emulsification which hampers the glycerin separation that results low ester yield (Vicente et al., 1998; Gurunathan and Ravi, 2015). As reported in literature, different nanocatalysts were used for biodiesel production from non-edible feedstock. Hashmi et al. (2016) investigated the use of CaO-Al2O3 nano-catalyst for biodiesel production from Jatropha oil. The highest 82.3 % biodiesel yield was obtained. Baskar et al. (2017) demonstrated the biodiesel production from Pongame oil using magnetic composite of Zinc oxide nano-catalyst. Transesterification of Pongame oil yielded 93% of biodiesel. In this study, CuO-CeO2 showed the highest conversion efficacy of crude oil into FAMEs that is 92%.
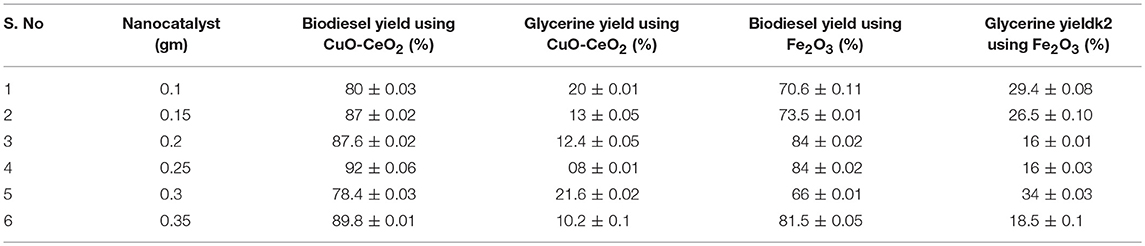
Table 1. Effect of nanocatalyst on biodiesel production of S. foetida oil using molar ratio (1:6), temperature (70°C), reaction time (3 h), and stirring speed (600 rpm).
Characterization of CuO-CeO2 and Fe2O3 Nano-Catalysts
XRD of CuO-CeO2 and Fe2O3
X-Ray Diffraction pattern of CuO-CeO2 nano-catalyst (Figure 1) shows strong diffraction peaks at 2θ angles i.e., 28.6, 33.1, 47.4, and 56.3 with diffraction pattern (1 1 1), (2 0 0), (2 2 0), and (3 1 1), respectively. The peak appears at 2θ angles 28.6, 33.1, 47.4, and 56.3 confirms the cubic fluorite structure of CeO2. The peak observed at 2θ angles 35.7, 38.7 with diffraction pattern (1 1 1), and (0 2 2), respectively shows the hexagonal structure of CuO. The average crystalline size of CuO.CeO2 54.4 nm was determined by Debye-Scherer equation (D=Kλ/βcosθ) (Mustafa et al., 2013). Where D is the crystallite size in nm, λ stands for X-ray wavelength = 0.154095 nm, θ is the half diffraction angle, K stands for the factor shape which takes a value of 0.89 and β stands for full width at half maximum (Pathaka et al., 2017). crystallite size of CuO-CeO2 nano-particles in literature was 40 nm (Amaniampong et al., 2018). XRD pattern of Fe2O3 nano catalyst (Figure 2) shows strong diffraction peaks at 2θ angles 33.1, 35.6, 40.6, 49.5, 54.0, 62.5, and 64.16 with diffraction pattern of (1 0 4), (1 1 0), (1 1 3), (0 2 4), 1 1 6), (2 1 0), and (3 0 0), respectively. These peaks indicate the rhombohedral structure of Fe2O3 which is confirmed from (JCPDS File No. 24-0072) with particle size 32 nm.
Scanning Electron Microscopy (SEM)
SEM was used to see the morphology and particle size of synthesized nano-catalysts. The SEM images have been shown in different magnifications. The SEM results showed that CuO-CeO2 nanoparticles have average crystalline size 32.3 nm. The results showed that the nanoparticles have spherical shape with no agglomeration (Figure 2).
The SEM study of Fe2O3 nano-catalyst demonstrated the average size and morphology. The average size ranged from 46.27 to 28.76 nm. The shape of Iron oxide nanoparticles appeared to be spherical with no agglomeration. The larger iron oxide aggregated particles remained visible may be due to the aggregation of the smaller particles (Figure 3).
FTIR of CuO-CeO2
FT-IR spectroscopic analysis is used to determine characteristic peaks in functional group (4,000–1,400 cm−1) and finger print (400–1,400 cm−1) region. FT-IR spectrum of CuO-CeO2 shows characteristic absorption peaks in functional group region at 3648.13, 3565.93, 1738.54, 1558.63, 1540.72, 1507.07, 1456.98, 1365.10 cm−1 and in finger print region at 1229.86, 1217.11, 715.05, 690.37, 681.98, 668.78 cm−1 which is shown as (Figure 5). The peak observed at 3648.13 and 3565.93 cm−1 due to –OH stretch of water molecule present in sample as a moisture. The peak appears in spectra at 1738.51 and 1558 cm−1 is due to bending vibrations of H-O-H molecule present in sample. The C-H stretching and bending vibration appears at 2,969 and 1456, 1365 cm−1, respectively. The peak appears at 690 and 681 cm−1 is due to of Cu-O particles, but an additional peak is observed at 1,229 cm−1, which is due to stretching mode of Cu+2 and O−2. The peak appearing at 668 cm−1 is due to CeO2 vibration. These peaks confirm the formation of CuO-CeO2 (Karimi et al., 2013) (Figure 4).
FT-IR of Fe2O3
The peak appearing in the spectra of Fe2O3 at 3,375 cm−1 is due to –OH stretching vibration of water molecule present in sample as moisture. The peak observed at 1,635 cm−1 is due to bending vibration of H-O-H. The characteristic peak appears at 674 cm−1 is due to Fe-O stretching vibration mode. An additional stretching mode of Fe-O is observed at 911 cm−1 in spectra.The previous study also supports the results. Farahmandjou and Soflaee (2015) Synthesize and Characterize Fe2O3 nanoparticles by simple co-precipitation method (Farahmandjou and Soflaee, 2015). These peaks confirm the formation of Fe2O3 (Figure 5).
Characterization of Synthesized FAMEs
GC-MS Analysis of S. foetida FAMEs
GC-MS analysis is an extensively used analytical technique to quantify chemical composition, structure and type of FAMEs present in biodiesel. The given hierarchy shows the efficiency of synthesized Nanocatalyst i.e., CuO-CeO2 >Fe2O3 on biodiesel synthesis, the percentage of synthesized methyl esters was in the order of 92 > 84%. The catalytic efficiency of CuO-CeO2 was highest due to its specific characteristics. GC spectrum of CuO-CeO2 catalyzed biodiesel showed 9 different peaks (Figure 6). Each peak corresponds to Methyl Ester and identified from the library match software (NO. NIST II). The major FAMES were found to be tetradecanoic acid, Hexadecanoic acid, 6- Nonezal, 9-Octadecaenoic Acid, Methyl Ester, 7,10-Octadecadienoic Acid, Heptadecanoic Acid, 1-Azuleneethanol, Acetate, Sterculic acid 8-(-2-Octacyclopropen-1-yl) octanoic acid. The retention time of these methyl esters is illustrated in Tables 2A,B. FAMEs were identified by arranging the retention time data; moreover, verification was made by GC internal standards (Figures 7, 8).
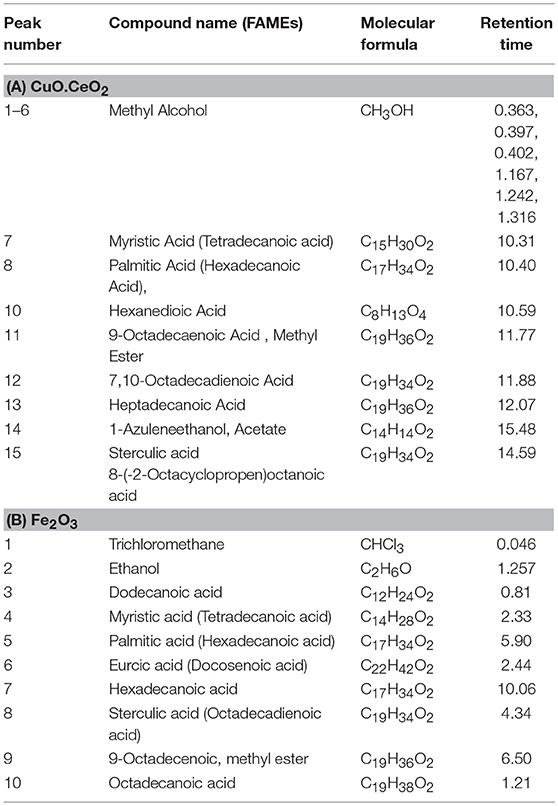
Table 2. Comparative analysis of fatty acid methyl ester profile of S. foetida using nano-catalysts.
FT-IR of S. foetida Seed Oil
FT-IR spectroscopic analysis is used to determine characteristic peaks in functional group (4,000–1,400 cm−1) and finger print (400–1,400 cm−1) region. The peak appearing at 3007.82 cm−1 confirms the presence of aromatic compounds. Strong peaks at 2923.91, 2852.93 cm−1 confirm the (sp3 and sp2C-H) stretch. An intense peak in FT-IR spectrum is observed at 1743.67, 1710.28 cm−1 due to C = O stretching vibrations that confirmed the presence of saturated aliphatic Esters. A medium peak at 1458.49 and 1377.20 cm−1 appears in spectra due to bending vibrations of CH2 and CH3. A peak appeared at 1236.01 cm−1 shows C-H deformation vibration, whereas, at 1162.02 cm−1 stretching vibration of C-C bond was observed. Peak observed at 1099.06 cm−1 confirm the presence of cyclic compound shows C-O stretching vibration as shown in Figure 9.
BIODIESEL Optimization
The conversion rate of Sterculia oil to biodiesel depends on various parameters, such as molar ratio, reaction temperature, reaction time, catalyst loading. A series of experiments were performed to achieve the maximum conversion of crude oil into biodiesel. Five variables were selected to check out their effect on biodiesel yield (Figure 10).
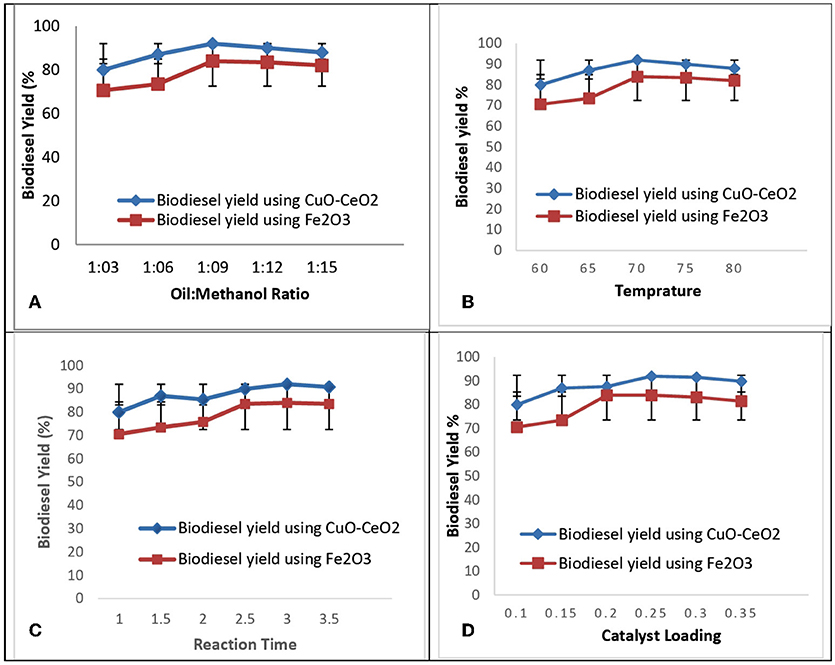
Figure 10. Optimization ofbiodiesel (A) oil-methanol ration, (B) temperature, (C) reaction time, (D) catalyst loading.
Molar Ratio
It is one of the most important variables in biodiesel production. Stoichiometrically 3 mole of methanol is required for 1 mole of triglyceride but practically, a large amount of methanol is required to shift the equilibrium favorably(Khan and El Dessouky, 2009) when other variables were kept constant methanol to all ratio shows positive influence on the biodiesel yield as it increases from 1:3 to 1:9. But as the molar ratio increase from 1:9 to 1:15, the incremental decrease in the yield was observed (Atapour and Kariminia, 2013). The maximum biodiesel yield was obtained at 1:9 oil to methanol ratio. Biodiesel yield was reduced at 1:15 oil to methanol ratio, due to decrease in density difference between the two phases obtained after transesterification reaction. High amount of methanol was used to minimize the contact of triglyceride on the catalyst active sites, ultimately decreasing the catalyst activity.
Reaction Temperature
The reaction temperature is one of the main parameters which affects the biodiesel yield. At certain range, elevated temperatures will speed up the reaction rate. The transesterification proceeded slowly at 45°C because at lower temperatures, only small numbers of molecules were able to get over the required energy barrier. Based off of the literature, the maximum conversion results acquired at the range of 60–70°C were studied (Chelladurai and Rajamanickam, 2014). In this study, the reaction temperature was kept at 60, 65, 70, 75, and 80°C by keeping other variables constant. Maximum conversion of esters was obtained at 70°C. At lower temperature, the energy is not enough to promote the collisions among reactant molecules. Whereas at higher temperature the possibility of collision among reactant molecules becomes greater and the activation energy is easily reached (Sivakumar et al., 2012).
Reaction Time
Reaction time has great influence on the rate of transesterification reaction. Oil must be stirred at constant rate to convert it into biodiesel. The conversion increased progressively with increasing reaction time and then reached a plateau value that represents the equilibrium (Pathaka et al., 2017). By keeping all other variables constant, the reaction time was kept from 1 to 3 h at the optimal reaction conditions. The results show the maximum conversion of biodiesel was obtained at 3 h. After that, further increase in time, up to 5 h, showed the decrease in yield of biodiesel. This decrease in yield is due to the backward reaction. Results show that increasing reaction time has influence on FAME yield production (Feyzi et al., 2013) (Figure 11).
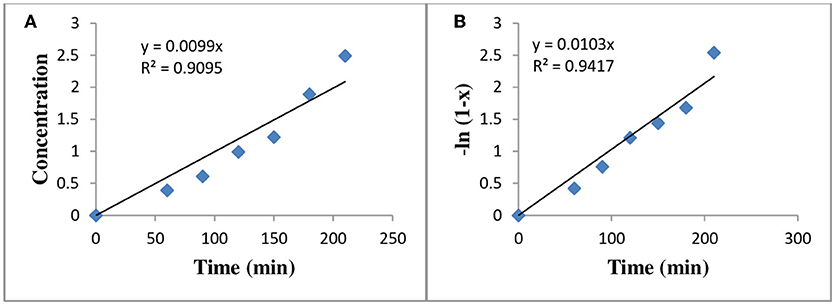
Figure 11. Reaction kinetics for transesterification (A) zero order reaction (Cone. vs. time), (B) Pseudo first order reaction (-ln(l-x) vs. time).
Catalyst Loading
The concentration of fatty acid methyl ester decreases with the increase in catalyst concentration (Gupta and Agrawal, 2015). The catalyst concentration used in transesterification reaction was 0.1, 0.15, 0.2, 0.25, 0.3, and 0.35 gm by keeping other variables such as reaction time, reaction temperature, oil to methanol ratio and catalyst type constant. The results showed a decrease in biodiesel yield with increase in catalyst concentration up to 0.25 gm because emulsification process hampers the glycerine separation and decreases the ester yields. The maximum biodiesel yield is obtained by using low catalyst concentration (Leung et al., 2010).
Physico-Chemical Properties of Sterculia Oil Biodiesel (Sob)
Physico-chemical properties of SOB were quantitatively determined and compared with the American Society for Testing and Materials (ASTM) standards for biodiesel testing (Atadashi et al., 2010). Fuel properties of pure biodiesel was tested where its density, cloud point, viscosity, density, sulfur content, Flash point, and total acid number were determined. The obtained values were then compared with the research and with the standard values of ASTM. The results for B-100 are mentioned in Table 3.
Color
The color of Sterculia biodiesel is on visual 2 according to ASTM standards.
Flash Point°C
The temperature at which fuel can ignite, is known as a flash point. It is the measure of affinity of a material to form a flammable mixture in the presence of air. Fuel having high flash point is safe during handling, transportation and storage (Candeia et al., 2009). Karmee and Chadha (2005) reported the flash point value of Pongamia pinnata i.e., 150°C using ASTM D-93. In this sample, the flash point was recorded as 73°C within the range of ASTM D-93 standards, which makes it safer fuel. High Speed Diesel (HSD) have flash point in the range of 60–80°C.
Density @ 15°C Kg/L
Fuel density is defined as the mass per unit of volume that measures in a vacuum. It plays a vital role in the determination of biodiesel quality. Fuel density has direct effect on fuel efficiency. Cetane number and viscosity are strongly linked with density. Small mass and speed of less viscous fuel make very accurate spray (Candeia et al., 2009). The density of Sterculia Oil Biodiesel was analyzed at ASTM D-1298 and the result was 0.0832 kg/L (Table 3), while High Speed Diesel has a density of 0.834. It confirms that SOB has less density than that of High Speed Diesel (HSD).
Kinematic Viscosity @ 40°C
Kinematic viscosity provides the indication of the ability of a material to flow. Engine efficiency becomes reduced due to the deposition of higher viscosity fuel (Gunstone and Hamilton, 2001; Sarin et al., 2007). Esterification process helped to reduce the viscosity (Sarin et al., 2007). Less viscous oil is easier to pump and to achieve fine droplets of fuel (Goodrum, 2002). (Morshed et al., 2011)studied that rubber oil biodiesel have kinematic viscosity of 4.5 @ 40°C which was greater as compared to HSD viscosity i.e., 4.223. The kinematic viscosity of SOB was analyzed at ASTM D-445 and result was 4.15 @ 40°C which lie within the range of ASTM standards. The value is also higher than that of HSD value i.e., 4.22.
Pour Point°C and Cloud Point°C
The lowest temperature at which the fuel can flow in chilled conditions is known as Pour point. While the cold point is a temperature at which paraffin becomes crystallize or begin to separate from solution. When the fuel is ice cold under suggested conditions, (Rashid et al., 2013) discovered that the Pour point and Cloud Point value of Rocket seed oil was −15 and −3°C, respectively. The Pour point and Cloud point of SOB was analyzed at ASTM D-97 and ASTM D-2500. Pour point value was −8°C which were according to ASTM standards whereas its cloud point value is −13°C which is higher than HSD.
Sulfur Contents % (wt)
Fuel with decreasing number of sulfur contents is ideal for most polluted areas. Low sulfur is considered more effective for the environment and for the engine's life (Candeia et al., 2009). Rashid et al. (2011) found that Muskmelon seed oil biodiesel contains 0.02% sulfated ash. Ahmad et al. (2009) reported that the 0.01% of sulfated ash present in Sesame oil biodiesel. The sulfur contents in SOB were found to be 0.0002% by weight, which was very low by comparing with ASTM D-4294 standard. It is stated that biodiesel is superior to HSD due to its decreasing number of sulfur contents.
Total Acid Number mg KOH/gm
Total acid number or Acid Value is termed as the number of free fatty acids present in fuel samples. It is expressed in mg KOH/gm for neutralizing 1 gm of FAMEs (Raj and Sahayaraj, 2010). Biodiesel is not acidic in nature but presence of FFAs in the diesel can make it acidic. High number of acid value is not good for engine efficiency. It results in severe corrosion in fuel supply system and internal engine combustion (Atabani et al., 2013). Rashid et al. (2011) studied that the acid value of Cotton Seed oil is 0.45 mg KOH/gm. According to ASTM D-974 standard, the acid value of SOB was 0.173 mg/KOH.
Kinetic Study of Biodiesel
Rate of Chemical reaction is the decrease in reactants concentration and increase in product concentration and was calculated experimentally. The order of reaction for the transesterification process to produce biodiesel was calculated by: second order (1/Conc. vs. time), first order (-(ln(conc.) vs. time), zero order (conc. vs. time) (Shu et al., 2011). The R2-values calculated from the graph is given in the table below. The zero order reaction rate of the chemical reaction was calculated from Equation (1);
Where [P] is the product concentration, Kp is reaction rate constant, x is the fraction of biodiesel.
The pseudo first order was calculated from Equation (2);
Where K is the rate constant of pseudo first order of reaction and was calculated from Equation (3);
Where x is the methanol content and the Reaction rate constant of various kinetic study at different temperatures for zero and pseudo first order reaction, are given in Table 4. The activation energy was calculated from Arrhenius equation (Aransiola et al., 2013) and value of R2 calculated from graph of (conc. vs. time) and (-ln (1-x) vs. time) and is given in Table 5. By comparing R2-values of different models via Arrhenius equation, pseudo first order reaction appeared to be well fit with experimental yield because it has greater value of (R2 = 0.9417) as compared to zero order reaction rate.
The reusability of transition metal mixed oxide Nano catalysts (CuO-CeO2 and Fe2O3) was checked by collecting catalyst after each round of reaction through reflux system. It was noted that CuO-CeO2 and Fe2O3 can be used four times without decrease in their catalytic activity. This fact was supported by the literature values, where CuO-CeO2 and Fe-Zn double metal cyanide can be used five times (Chouhan and Sarma, 2011). Therefore, CuO-CeO2 and Fe2O3 are stable and active catalysts for large scale biodiesel synthesis.
Long term use and feasibility of catalysts can be checked by examining the reusability of transition metal mixed oxide Nano catalysts (CuO-CeO2 and Fe2O3) on biodiesel yield at optimum operating conditions. Figure 12 shows the reusability of (CuO-CeO2 and Fe2O3) under optimum conditions of 0.25% catalyst loading with oil to methanol ratio of 1:9 at 70°C for 3 h. After each cycle of catalyst used, it was washed with absolute ethanol followed by oven drying (100°C) for 4 h. The catalysts were found to be active over four times without decrease in their catalytic activity. However, after the fifth round of catalyst testing, their activity significantly decreased. This fact was supported by the literature values where CuO-CeO2 and Fe-Zn double metal cyanide can be used five times (Chouhan and Sarma, 2011). Therefore, CuO-CeO2 and Fe2O3 are stable and active catalysts. The decrease in biodiesel yield might be attributed to the deactivation of active sites and leaching of catalyst in reaction media (Figure 12).
Conclusion
This study focused on the comparative analysis of nano-catalysts on biodiesel production from S. foetida. Nanocatalysts (CuO-CeO2 and Fe2O3) were synthesized chemo-mechanically, then characterized and applied for biodiesel production from SSO to SOB. Among these two catalysts, CuO-CeO2 showed the auspicious results; highest conversion efficiency was achieved 92%, using CuO-CeO2 followed by Fe2O3 at 0.25% catalyst loading. The best optimized variables were: alcohol to oil molar ratio (1:6), reaction time (3 h), temperature (70°C) and stirring rate (600 rpm) using reflux transesterification method. Moreover, pseudo first order reaction appeared fit with experimental yield with greater R2 = 0.9417 as compared to zero order reaction rate. The synthesized nanocatalyst exhibit good stability and reusability during the reaction. The encouraging results of this study strongly recommended S. foetida an economically feasible potential feedstock for biodiesel production as a renewable energy on industrial level.
Author Contributions
MA, RU, MZ, and MTA designed the whole experiment and methodology. AS collected the seeds. MTA, MAs, and SS performed the whole experiment. MM, MS, and AW revised the whole manuscript carefully to its present form, and assisted with checking the consistency of the data. NR and KM drafted manuscript with contribution from all co-authors. All authors read the final manuscript and agreed to its submission.
Conflict of Interest Statement
The authors declare that the research was conducted in the absence of any commercial or financial relationships that could be construed as a potential conflict of interest.
Acknowledgments
The authors extend their appreciation to Deanship of Scientific Research at King Saud University for funding their group through research Group No (RG 1440–100). Authors are also thankful to Chengdu Institute of Biology for providing lab facilities.
References
Ahmad, M., Khan, M., Zafar, M., and Sultana, S. (2009). Environment-friendly renewable energy from sesame biodiesel. Energy Sour Part A 32, 189–196. doi: 10.1080/15567030802467480
Amaniampong, P. N., Trinh, Q. T., Li, K., Mushrif, S. H., Hao, Y., and Yang, Y. (2018). Porous structured CuO-CeO2 nanospheres for the direct oxidation of cellobiose and glucose to gluconic acid. Catal. Today 306, 172–182. doi: 10.1016/j.cattod.2017.01.009
Aparna, Y., Rao, K. E., and Subbarao, P. S. (2012). “Synthesis and characterization of CuO nano particles by novel sol-gel method,” in Proceedings of the 2nd International Conference on Environment Science and Biotechnology (Singapore).
Aransiola, E. F., Daramola, M. O., Ojumu, T. V., Solomon, B. O., and Layokun, S. K. (2013). Homogeneously catalyzed transesterification of Nigerian Jatropha curcas oil into biodiesel: a kinetic study. Modern Res. Catal. 2:83. doi: 10.4236/mrc.2013.23012
Ashnani, M. H. M., Johari, A., Hashim, H., and Hasani, E. (2014). A source of renewable energy in Malaysia, why biodiesel? Renew. Sustain. Energy Rev. 35, 244–257. doi: 10.1016/j.rser.2014.04.001
Atabani, A., Silitonga, A., Ong, H., Mahlia, T., Masjuki, H., Badruddin, I. A., et al. (2013). Non-edible vegetable oils: a critical evaluation of oil extraction, fatty acid compositions, biodiesel production, characteristics, engine performance and emissions production. Renew. Sustain. Energy Rev. 18, 211–245. doi: 10.1016/j.rser.2012.10.013
Atadashi, I., Aroua, M., and Aziz, A. A. (2010). High quality biodiesel and its diesel engine application: a review. Renew. Sustain. Energy Rev. 14, 1999–2008. doi: 10.1016/j.rser.2010.03.020
Atapour, M., and Kariminia, H.-R. (2013). Optimization of biodiesel production from Iranian bitter almond oil using statistical approach. Waste Biomass Valorizat. 4, 467–474. doi: 10.1007/s12649-013-9203-5
Baskar, G., Gurugulladevi, A., Nishanthini, T., Aiswarya, R., and Tamilarasan, K. (2017). Optimization and kinetics of biodiesel production from Mahua oil using manganese doped zinc oxide nanocatalyst. Renew. Energy 103, 641–646. doi: 10.1016/j.renene.2016.10.077
Baskar, G., Soumiya, S., and Aiswarya, R. (2016). Biodiesel production from pongamia oil using magnetic composite of zinc oxide nanocatalyst. Int. J. Modern Sci. Technol. 1, 129–137. doi: 10.1016/j.renene.2016.02.068
Candeia, R., Silva, M., Carvalho Filho, J., Brasilino, M., Bicudo, T., Santos, I., et al. (2009). Influence of soybean biodiesel content on basic properties of biodiesel–diesel blends. Fuel 88, 738–743. doi: 10.1016/j.fuel.2008.10.015
Chakrabarti, M., Ali, M., Baroutian, S., and Saleem, M. (2011). Techno-economic comparison between B10 of Eruca sativa L. and other indigenous seed oils in Pakistan. Process Safety Environ. Protect. 89, 165–171. doi: 10.1016/j.psep.2010.11.006
Chelladurai, K., and Rajamanickam, M. (2014). Environmentally benign neem biodiesel synthesis using nano-Zn-Mg-Al hydrotalcite as solid base catalysts. J. Catal. 2014:326575. doi: 10.1155/2014/326575
Chouhan, A. S., and Sarma, A. (2011). Modern heterogeneous catalysts for biodiesel production: a comprehensive review. Renew. Sustain. Energy Rev. 15, 4378–4399. doi: 10.1016/j.rser.2011.07.112
Datta, A., and Mandal, B. K. (2014). Use of Jatropha biodiesel as a future sustainable fuel. Energy Technol. Policy 1, 8–14. doi: 10.1080/23317000.2014.930723
Edward, N., and Peggy, A. (2013). Optimization of biodiesel production from non-edible seeds of Delonix regia (Gul. Mohr). Int. J. Bioresou. Technol. 1, 2327–7734. Available online at: www.acascipub.com
Farahmandjou, M., and Soflaee, F. (2015). Synthesis and characterization of α-Fe2O3 nanoparticles by simple co-precipitation method. Phys. Chem. Res. 3, 191–196. doi: 10.22036/pcr.2015.9193
Farobie, O., and Matsumura, Y. (2015). A comparative study of biodiesel production using methanol, ethanol, and tert-butyl methyl ether (MTBE) under supercritical conditions. Bioresour. Technol. 191, 306–311. doi: 10.1016/j.biortech.2015.04.102
Feyzi, M., Hassankhani, A., and Rafiee, H. R. (2013). Preparation and characterization of Cs/Al/Fe3O4 nanocatalysts for biodiesel production. Energy Conver. Manage. 71, 62–68. doi: 10.1016/j.enconman.2013.03.022
Fusco, L. (2006). Peak Oil Theory. St. John's: Memorial University of Newfoundland Recuperado de. Available online at: http://www.ucs.mun.ca/õilpower/documents/Peakoil2-1.doc.pdf
Gardy, J., Osatiashtiani, A., Céspedes, O., Hassanpour, A., Lai, X., Lee, A. F., et al. (2018). A magnetically separable SO4/Fe-Al-TiO2 solid acid catalyst for biodiesel production from waste cooking oil. Appl. Catal. B 234, 268–278. doi: 10.1016/j.apcatb.2018.04.046
Goodrum, J. (2002). Volatility and boiling points of biodiesel from vegetable oils and tallow. Biomass Bioenergy 22, 205–211. doi: 10.1016/S0961-9534(01)00074-5
Gunstone, F. D., and Hamilton, R. J. (2001). Oleochemical Manufacture and Applications. Sheffield, UK: CRC Press.
Gupta, G., and Agrawal, M. (2015). “Preparation and Characterization of CaO Nanoparticle for Biodiesel Production,” in 2nd International Conference on Emerging Technologies (AIP Publishing), 1–10. doi: 10.1063/1.4945186
Gurunathan, B., and Ravi, A. (2015). Biodiesel production from waste cooking oil using copper doped zinc oxide nanocomposite as heterogeneous catalyst. Bioresou. Technol. 188, 124–127. doi: 10.1016/j.biortech.2015.01.012
Hashmi, S., Gohar, S., Mahmood, T., Nawaz, U., and Farooqi, H. (2016). Biodiesel production by using CaO-Al2O3 Nano catalyst. Int. J. Eng. Res. Sc. 2:3.
Heyne, K. (1987). The useful Indonesian plants. Res. Dev. Agency Ministry Forestry, Jakarta, Indonesia 845.
Hu, S., Guan, Y., Wang, Y., and Han, H. (2011). Nano-magnetic catalyst KF/CaO–Fe3O4 for biodiesel production. Appl. Energy 88, 2685–2690. doi: 10.1016/j.apenergy.2011.02.012
Karimi, A., Fatehifar, E., and Alizadeh, R. (2013). Synthesis and characterization of nanostructured CuO/CeO2 catalysts via ultrasound assisted techniques used for selective oxidation of CO. Iran. J. Chem. Eng. 10, 51–59.
Karmee, S. K., and Chadha, A. (2005). Preparation of biodiesel from crude oil of Pongamia pinnata. Bioresour. Technol. 96, 1425–1429. doi: 10.1016/j.biortech.2004.12.011
Khan, N. A., and El Dessouky, H. (2009). Prospect of biodiesel in Pakistan. Renew. Sustain. Energy Rev. 13, 1576–1583. doi: 10.1016/j.rser.2008.09.016
Kumar, G., Kumar, D., Johari, R., and Singh, C. (2011). Enzymatic transesterification of Jatropha curcas oil assisted by ultrasonication. Ultrasonics Sonochem. 18, 923–927. doi: 10.1016/j.ultsonch.2011.03.004
Leung, D. Y., Wu, X., and Leung, M. (2010). A review on biodiesel production using catalyzed transesterification. Appl. Energy 87, 1083–1095. doi: 10.1016/j.apenergy.2009.10.006
Morshed, M., Ferdous, K., Khan, M. R., Mazumder, M., Islam, M., and Uddin, M. T. (2011). Rubber seed oil as a potential source for biodiesel production in Bangladesh. Fuel 90, 2981–2986. doi: 10.1016/j.fuel.2011.05.020
Moser, B. R. (2010). Camelina (Camelina sativa L.) oil as a biofuels feedstock: Golden opportunity or false hope? Lipid Technol. 22, 270–273. doi: 10.1002/lite.201000068
Munarso, J. (2010). Plantation of Sterculia feotida. L as vegetable oil. Information technology agriculture. Jakarta: Indonesia Agency for Agricultural Research and Development. 13–15.
Mustafa, G., Tahir, H., Sultan, M., and Akhtar, N. (2013). Synthesis and characterization of cupric oxide (CuO) nanoparticles and their application for the removal of dyes. African J. Biotechnol. 12, 6650–6660. doi: 10.5897/AJB2013.13058
Naik, S. N., Goud, V. V., Rout, P. K., and Dalai, A. K. (2010). Production of first and second generation biofuels: a comprehensive review. Renew. Sustain. Energy Rev. 14, 578–597. doi: 10.1016/j.rser.2009.10.003
Okitsu, K., Maeda, Y., and Bandow, H. (2014). Ultrasound assisted production of fatty acid methyl esters from transesterification of triglycerides with methanol in the presence of KOH catalyst: Optimization, mechanism and kinetics. Ultrasonics Sonochem. 21, 467–471. doi: 10.1016/j.ultsonch.2013.09.015
Okoronkwo, M., Galadima, A., and Leke, L. (2012). Advances in Biodiesel synthesis: from past to present. Elixir Appl. Chem. 43, 6924–6945.
Pathaka, P. K., Rajb, J., Saxena, G., and Uma, S. A. (2017). A review on production of biodiesel by transesterification using heterogeneous nanocatalyst. Int. J. Sci. Res. Dev. 5, 631–636.
Raj, F. R. M. S., and Sahayaraj, J. W. (2010). “A comparative study over alternative fuel (biodiesel) for environmental friendly emission,” in Recent Advances in Space Technology Services and Climate Change (RSTSCC) (Chennai: IEEE), 80–86.
Rao, P., Ramesh, S., and Kumar, S. (2015). Study of CI engine performance with diesel-biodiesel (Sterculia foetida) blend as fuel. Intl. J. Trend Res. Dev. 2, 76–79.
Rashid, U., Anwar, F., Ashraf, M., Saleem, M., and Yusup, S. (2011). Application of response surface methodology for optimizing transesterification of Moringa oleifera oil: Biodiesel production. Energy Conver. Manage. 52, 3034–3042. doi: 10.1016/j.enconman.2011.04.018
Rashid, U., Anwar, F., Yunus, R., and Al-Muhtaseb, A. H. (2015). Transesterification for biodiesel production using Thespesia populnea seed oil: an optimization study. Int. J. Green Energy 12, 479–484. doi: 10.1080/15435075.2013.853177
Rashid, U., Ibrahim, M., Yasin, S., Yunus, R., Taufiq-Yap, Y., and Knothe, G. (2013). Biodiesel from Citrus reticulata (mandarin orange) seed oil, a potential non-food feedstock. Indus. Crops Products 45, 355–359. doi: 10.1016/j.indcrop.2012.12.039
Rehan, M., Gardy, J., Demirbas, A., Rashid, U., Budzianowski, W., Pant, D., et al. (2018). Waste to biodiesel: a preliminary assessment for Saudi Arabia. Bioresour Technol. 250, 17–25. doi: 10.1016/j.biortech.2017.11.024
Salam, K. A., Velasquez-Orta, S. B., and Harvey, A. P. (2016). Surfactant-assisted direct biodiesel production from wet Nannochloropsis occulata by in situ transesterification/reactive extraction. Biofuel Res. J. 3, 366–371. doi: 10.18331/BRJ2016.3.1.6
Sarin, R., Sharma, M., Sinharay, S., and Malhotra, R. K. (2007). Jatropha–palm biodiesel blends: an optimum mix for Asia. Fuel 86, 1365–1371. doi: 10.1016/j.fuel.2006.11.040
Shikha, K., and Chauhan, Y. R. (2012). Biodiesel production from non edible-oils: a review. J. Chem. Pharmaceut. Res. 4, 4219–4230.
Shu, Q., Gao, J., Liao, Y., and Wang, J. (2011). Reaction kinetics of biodiesel synthesis from waste oil using a Carbon-based solid acid catalyst. Chinese J. Chem. Eng. 19, 163–168. doi: 10.1016/S1004-9541(09)60193-2
Sivakumar, P., Parthiban, K. S., Sivakumar, P., Vinoba, M., and Renganathan, S. (2012). Optimization of extraction process and kinetics of Sterculia foetida seed oil and its process augmentation for biodiesel production. Indus. Eng. Chem. Res. 51, 8992–8998. doi: 10.1021/ie300882t
Stavarache, C. E., Morris, J., Maeda, Y., Oyane, I., and Vinatoru, M. (2008). Syringa (Melia azedarach L.) berries oil: a potential source for biodiesel fuel. Revista de Chimie 59, 672–677.
Tajammul Hussain, S., Ahmed, W., Saeed, M., Danish Ali, S., and Asma, M. (2013). Fatty acid methyl ester production from waste cooking oil catalyzed by CuO-CeO2/NiO mixed oxides. J. Renew. Sustain. Energy 5:023104. doi: 10.1063/1.4794437
Ullah, K., Ahmad, M., and Qiu, F. (2015). Assessing the experimental investigation of milk thistle oil for biodiesel production using base catalyzed transesterification. Energy 89, 887–895. doi: 10.1016/j.energy.2015.06.028
Vicente, G., Coteron, A., Martinez, M., and Aracil, J. (1998). Application of the factorial design of experiments and response surface methodology to optimize biodiesel production. Indus. Crops Products 8, 29–35. doi: 10.1016/S0926-6690(97)10003-6
Keywords: Sterculia foetida, biodiesel, nanocatalyst, conversion efficiency, XRD, SEM, FT-IR, GC-MS
Citation: Akhtar MT, Ahmad M, Shaheen A, Zafar M, Ullah R, Asma M, Sultana S, Munir M, Rashid N, Malik K, Saeed M and Waseem A (2019) Comparative Study of Liquid Biodiesel From Sterculia foetida (Bottle Tree) Using CuO-CeO2 and Fe2O3 Nano Catalysts. Front. Energy Res. 7:4. doi: 10.3389/fenrg.2019.00004
Received: 29 October 2018; Accepted: 17 January 2019;
Published: 01 March 2019.
Edited by:
Umakanta Jena, New Mexico State University, United StatesReviewed by:
Mohammad Zain Khan, Aligarh Muslim University, IndiaJunLi Ren, South China University of Technology, China
Jabbar Gardy, University of Leeds, United Kingdom
Copyright © 2019 Akhtar, Ahmad, Shaheen, Zafar, Ullah, Asma, Sultana, Munir, Rashid, Malik, Saeed and Waseem. This is an open-access article distributed under the terms of the Creative Commons Attribution License (CC BY). The use, distribution or reproduction in other forums is permitted, provided the original author(s) and the copyright owner(s) are credited and that the original publication in this journal is cited, in accordance with accepted academic practice. No use, distribution or reproduction is permitted which does not comply with these terms.
*Correspondence: Mushtaq Ahmad, bXVzaHRhcWFobWFkcWF1QGdtYWlsLmNvbQ==