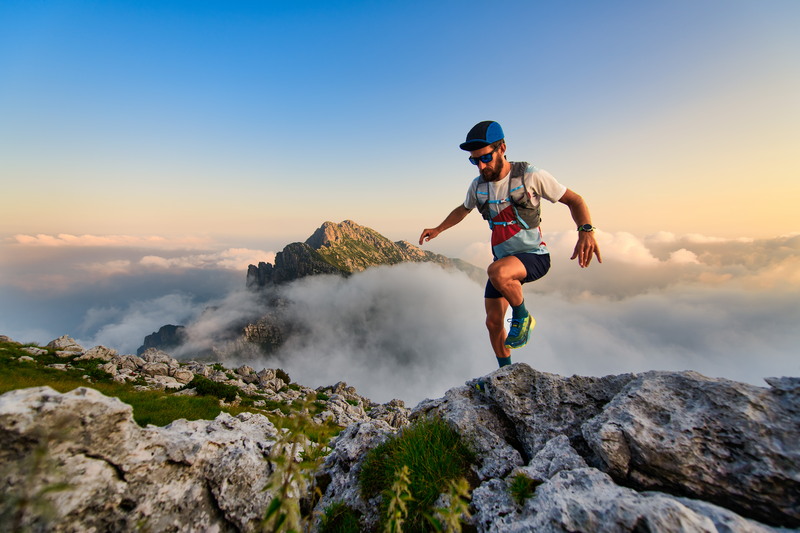
95% of researchers rate our articles as excellent or good
Learn more about the work of our research integrity team to safeguard the quality of each article we publish.
Find out more
ORIGINAL RESEARCH article
Front. Energy Res. , 30 October 2018
Sec. Electrochemical Energy Storage
Volume 6 - 2018 | https://doi.org/10.3389/fenrg.2018.00110
This article is part of the Research Topic Lithium Ion Battery Safety: Trends and Developments View all 4 articles
The electrochemical performance and thermal stability of Li(Ni0.5Co0.2Mn0.3)O2, LiMn2O4, and LiFePO4 are investigated by the multi-channel battery cycler, electrochemical workstation, thermogravimetric analysis (TGA) and C80 instrument in this work. For electrochemical performance, Li(Ni0.5Co0.2Mn0.3)O2 shows the highest specific capacity but the worst cycle stability. For the thermal stability, the experimental results of thermogravimetry and C80 indicate that the charged Li(Ni0.5Co0.2Mn0.3)O2 has the worst thermal stability compared with charged LiFePO4 and LiMn2O4. It is also testified by calculating the chemical kinetic parameters of cathode materials based on the Arrhenius law. The pure Li(Ni0.5Co0.2Mn0.3)O2 starts to self-decompose at around 250°C with total heat generation of −88 J/g. As for a full battery, the total heat generation is −810 J/g with exothermic peak temperature of 242°C. The present results show that thermal runaway is more likely to occur for Li(Ni0.5Co0.2Mn0.3)O2 with the full battery.
Lithium-ion batteries (LIBs) are widely used in a variety of areas for their high-energy density, such as portable telephones, computers and electric vehicles (EVs) (Sun et al., 2009; Hannan et al., 2017). However, the safety issue cannot be ignored because there are so many accidents for fires and explosions that occur frequently due to the potential hazard of batteries (Wang et al., 2012). Meanwhile, as an important part of battery, cathode materials such as Li(Ni0.5Co0.2Mn0.3)O2 (NCM523), LiMn2O4 (LMO) and LiFePO4 (LFP) have received much attention recently. The characteristics of cost, performance and safety should be taken into consideration.
For LiMn2O4 cathode material, it is cheap and with good thermal stability. Whereas LiMn2O4 belongs to spinel-type structure with worse cycle performance, which is affected by Jahn-Teller distortion accompanied with structural transformation during charge-discharge process (Ouyang et al., 2009). A lots of work has been conducted to improve the performance of LiMn2O4 by doping with diverse elements, such as F (Chen et al., 2010; Feng et al., 2010), Cr (Xu et al., 2011), Nb (Yi et al., 2013), Mg (Susanto et al., 2015). LiFePO4 is more stable but the conductivity is poor. Zaghib et al. enhanced the thermal safety and high power performance of LiFePO4 with coated carbon (Zaghib et al., 2012). While Li(Ni0.5Co0.2Mn0.3)O2 has high-energy density but fragile structural stability, some modifications have been made to improve the cycle performance and thermal stability, such as graphene oxide with V2O5 coating (Luo and Zheng, 2017), AlF3 coating (Yang et al., 2012). Gong et al. analyzed the total exothermic heat of nickel cobalt lithium manganese with various nickel content and it increased as nickel content increased (Gong et al., 2017). In addition, Pang et al. reviewed the application of MnO (Chen et al., 2018), FeOx (Ma et al., 2018), and MxSy (M = Cu, Ag, Au) (Lu et al., 2017) in LIBs.
Although the improvement of these cathode materials has been investigated (Julien et al., 2014b; Du et al., 2016), however, an elaborate comparison of the electrochemical performance and thermal stability were rare reported in previous work. In this work, the electrochemical performance and thermal stability of charged Li(Ni0.5Co0.2Mn0.3)O2, LiMn2O4 and LiFePO4 are analyzed and compared.
The positive electrodes contain commercial cathode materials including Li(Ni0.5Co0.2Mn0.3)O2, LiMn2O4, and LiFePO4, acetylene black and polyvinylidene fluoride, and the mass ratio of the active material, acetylene black and polyvinylidene fluoride is 8:1:1. The commercial organic electrolyte with 1.0 M LiPF6 salt and the mixture solvent of ethylene carbonate (EC) and diethyl carbonate (DEC) (1:1, w:w) and the separator being made of Celgard 2,400 polyethylene were used. The CR2032 type coin half-cell was assembled in the glove box filled with argon atmosphere (SG2400/750TS, Vigor, Suzhou, China, O2 < 1 ppm, H2O < 1 ppm). Galvanostatic charge and discharge tests at 0.7 C were conducted on a multi-channel battery cycler (Neware, BTS-6V 10 mA, China) with the voltage range from 2.5 to 4.2 V at room temperature and 55°C, respectively. The AC impendence and cyclic voltammetry were measured by a CHI 604A electrochemical workstation.
In order to evaluate the thermal stability of the cathode material in the most dangerous state of charge, the half-cell with the three kinds of cathode materials were pre-cycled three times and then fully charged to 4.2 V. After this, the fully charged cathode materials were disassembled in the argon atmosphere. The obtained cathodes were rinsed by dimethyl carbonate (DMC) solvent to defuse the residual electrolyte. The weight loss of materials was tested by a STA490C thermal analyzer at a heating/cooling rate of 10°C/min with 200 mL/min flow of N2 in the temperature range of 30–800°C. The heat flow of the materials was measured by a C80 instrument filled with argon atmosphere at 0.2°C/min in the temperature range of room temperature to 300°C. The thermal effects of each sample were thus recorded automatically, and the C80 calculations were based on dry film weight of the electrode material.
X-ray diffraction (XRD) (Cu Kα, MXPAHF) information and scanning electron microscopy (SEM, FEI Sirion200) images of Li(Ni0.5Co0.2Mn0.3)O2, LiMn2O4, and LiFePO4 before and after thermal treatment were conducted.
Figure 1A shows the long cycle performance of the three kinds of cathode materials at 0.7 C charge rate. It can be seen that LiFePO4 shows the best cycle performance. The first coulomb efficiency of LiFePO4 is 87% which is higher than Li(Ni0.5Co0.2Mn0.3)O2 and LiMn2O4 (84%). The present results also show that the capacity retention rate after 100 cycles of Li(Ni0.5Co0.2Mn0.3)O2 is 57%, while the capacity retention rate after 100 cycles of LiMn2O4 and LiFePO4 is higher, 82 and 95%, respectively. Therefore, the cycling stability of Li(Ni0.5Co0.2Mn0.3)O2 is relatively poor. As shown in Figure 1B, the rate performance of LiFePO4 keeps well at low charge and discharge rate, and the rate performance of Li(Ni0.5Co0.2Mn0.3)O2 is consistent with cycle performance, but large capacity loss occurs in high rate region. Figure 1C presents the charge-discharge cycle of the three kinds of cathode materials for the first time. The charge-discharge platform of LiMn2O4 is higher than others. The electrolyte tends to decompose at high charge-discharge platform. Thus, the high charge-discharge platform has an influence on both the electrochemical performance and the safety of the battery. In order to further compare the cycle performance of the three cathode materials at higher temperature, long cycle tests with 0.7 C rate at 55°C were conducted. As shown in Figure 1D, the cycle performance of the three kinds of cathodes are obviously influenced and the capacity of LiMn2O4 drops quickly at the higher temperature, and the LiFePO4 still shows a better performance than LiMn2O4 and Li(Ni0.5Co0.2Mn0.3)O2.
Figure 1. (A) Long cycle performance of Li(Ni0.5Co0.2Mn0.3)O2, LiMn2O4 and LiFePO4 at 0.7 C charge rate at room temperature. (B) Rate performance of Li(Ni0.5Co0.2Mn0.3)O2, LiMn2O4 and LiFePO4 at room temperature. (C) Charge and discharge curves of Li(Ni0.5Co0.2Mn0.3)O2, LiMn2O4, and LiFePO4 at 0.2 C. (D) Long cycle performance of Li(Ni0.5Co0.2Mn0.3)O2, LiMn2O4 and LiFePO4 at 0.7 C charge rate at 55°C.
The comparison of the AC impedance resistance and cyclic voltammetry are presented in the Figure 2. The results of AC impedance resistance test are shown in Figure 2A, according to the formula presented in previous study (Wang et al., 2011), the calculated lithium-ion diffusion coefficients of Li(Ni0.5Co0.2Mn0.3)O2, LiMn2O4 and LiFePO4 are 6.85 × 10−9, 3.22 × 10−8, and 2.12 × 10−7, respectively. Thus, the better rate and cycle performance of LiFePO4 may attribute from the higher lithium ion diffusion coefficient. Figures 2B–D display the cyclic voltammetry of Li(Ni0.5Co0.2Mn0.3)O2, LiMn2O4, LiFePO4, respectively. Consistent with the charge and discharge curves which are shown in Figure 1C, the LiFePO4 shows the lowest voltage platform and the best reversibility which contribute to a better cycle performance, while the voltage platforms of LiMn2O4 and Li(Ni0.5Co0.2Mn0.3)O2 are high and the reversibility is not as good as LiFePO4.
Figure 2. (A) The electrochemical impedance spectra of the three kinds of cathode materials. Cyclic voltammetry plot of (B) Li(Ni0.5Co0.2Mn0.3)O2, (C) LiMn2O4 and (D) LiMn2O4.
The variation of weight percent of the charged cathode materials are showed in Figure 3. The three materials are stable before around 150°C, thereafter the weight of them decreases at different levels as material decomposition produces gas. In detail, LiFePO4 begins to decompose at around 245°C and a total weight loss approaches 10% during the whole process. There are three stages of weight loss for LiMn2O4, which are represented by I (before 260°C), II (from 260° to 462°C) and III (after 462°C), respectively. Before 260°C, the weight loss may be attributed to the loss of LiPF6 or other contaminants. In stage II, PVDF degrades with elimination of hydrogen fluoride in an appreciable quantity along with small amount of C4H3F3 (Li et al., 2007). In the stage III, the weight loss is mainly caused by acetylene carbon black and PVDF. As to Li(Ni0.5Co0.2Mn0.3)O2, the weight decreases at stage I and drops to almost 71% of original value. The present results show that LiFePO4 has better thermal stability than Li(Ni0.5Co0.2Mn0.3)O2 at high-temperature stage. Based on the data of weight loss and the previous studies (Zaghib et al., 2012; Julien et al., 2014a), LiFePO4 is stable enough, and the decomposition process of the Li(Ni0.5Co0.2Mn0.3)O2 and LiMn2O4 can be speculated as follows:
Another thermal experiment was performed by a C80 calorimeter, and the heat flow curves are presented in Figure 4A. According to integrate the heat flow, the total heat production of Li(Ni0.5Co0.2Mn0.3)O2, LiMn2O4, LiFePO4 are −405, −240, and −100 J/g, respectively. In this plot, the exothermic peak of LiFePO4 around 80 and 160°C may belong to the decomposition of the surface films, but with neglected enough heat production. The decomposition of LiFePO4 starts to react after 250°C with −38 J/g. While LiMn2O4 and Li(Ni0.5Co0.2Mn0.3)O2 only have one exothermic peak at 229 and 258°C, respectively. Although the exothermic temperature of LiMn2O4 lowers about 20°C compared with Li(Ni0.5Co0.2Mn0.3)O2, the Li(Ni0.5Co0.2Mn0.3)O2 has a specially sharp exothermic peak with heat generation of −405 J/g. It can be seen that the LiFePO4 has the best thermal stability among the experimental materials while Li(Ni0.5Co0.2Mn0.3)O2 has the worst thermal stability among them. As shown in Figure 4B, the pure Li(Ni0.5Co0.2Mn0.3)O2 starts to self-decompose at around 250°C, which is more safer than mixed with the electrolyte. The heat generation of the pure Li(Ni0.5Co0.2Mn0.3)O2 is totally −88 J/g. The heat flow curve of Li(Ni0.5Co0.2Mn0.3)O2 –Li4Ti5O12 full battery is displayed in Figure 4C. The total heat generation is −810 J/g with exothermic peak temperature of 242°C. The whole process can be divided into three stages. The first stage belongs to the decomposition of anode material with small heat release at around 78°C. Then the melting of membrane occurs at around 171°C with endothermic reaction due to the heat accumulation in the first stage. Finally, reactions between cathode materials and electrolyte in the third stage generate the most heat in the whole process. Furtherly, in order to better understand the structure changes after thermal treatment of the three cathodes, XRD and SEM tests were carried out to compare the three cathodes materials before and after thermal treatment. Figure 5 gives the XRD test results, by comparing the result of each sample before and thermal treatment, it can be seen that there is no obvious crystal structure changes of LiFePO4 material and the SEM test result in Figures 6E,F is almost the same. But for Li(Ni0.5Co0.2Mn0.3)O2 and LiMn2O4 materials, new diffraction peaks appear and some old diffraction peaks disappear, and the crystallinity decreases which all explain that the crystal structure of Li(Ni0.5Co0.2Mn0.3)O2 and LiMn2O4 materials have been destroyed. Furtherly, in Figures 6A–D, it presents clearly the change in structures and the appearance of agglomerated particles. These results are consistent with the test results of thermal analysis.
Figure 4. The heat flow curves of (A) the charged cathode materials, and (B) pure Li(Ni0.5Co0.2Mn0.3)O2, and (C) charged Li(Ni0.5Co0.2Mn0.3)O2 –Li4Ti5O12 full battery.
Figure 5. XRD information of Li(Ni0.5Co0.2Mn0.3)O2, LiMn2O4 and LiFePO4 before and after C80 thermal treatment.
Figure 6. SEM images of Li(Ni0.5Co0.2Mn0.3)O2, LiMn2O4 and LiFePO4 before and after C80 thermal treatment. (a) Li(Ni0.5Co0.2Mn0.3)O2 before thermal treatment. (b) Li(Ni0.5Co0.2Mn0.3)O2 after thermal treatment. (c) LiMn2O4 before thermal treatment. (d) LiMn2O4 after thermal treatment. (e) LiFePO4 before thermal treatment. (f) LiFePO4 after thermal treatment.
In order to further analyze and compare the thermal stability of the three cathode materials, the chemical kinetic parameters of cathode materials are calculated with C80 data based on the Arrhenius law, which can be written as Wang et al. (2006).
where the dH/dt is the heat flow, ΔH the total heat of reaction, M0 the initial mass of the reactant, E the activation energy, R the gas constant, T the temperature, and A the pre-exponential factor. As shown in Figure 7, the fitted line of Li(Ni0.5Co0.2Mn0.3)O2 were taken as an example by plotting the curve of ln(dH/dt/ΔHM0) vs. inverse temperature (1/T). The activation energy of Li(Ni0.5Co0.2Mn0.3)O2-electrolyte system is 539 kJ/mol, and the pre-exponential factor is 7.48 × 1053 s−1. The thermal kinetic parameters for other experimental materials are listed in Table 1 by the same method. The results show that LiFePO4 has the minimum activation energy for the sake of the decomposition of surface films. However, it is unsuitable to choose the activation energy to judge the thermal stability of LiFePO4 as this parameter is not calculated according to the decomposition of the material itself.
Figure 7. Thermal-kinetic parameters of charged Li(Ni0.5Co0.2Mn0.3)O2 estimated from ln(dH/dt/ΔHM0) vs. T−1.
The comparison of electrochemical performance and thermal stability among charged Li(Ni0.5Co0.2Mn0.3)O2, LiMn2O4, and LiFePO4 were investigated in this paper. With the help of charge-discharge cycling and impedance measurement, it can be seen that cycle performance of Li(Ni0.5Co0.2Mn0.3)O2 is not as stable as LiMn2O4 and LiFePO4. Furthermore, the comparison and analysis of thermal stability is conducted by the thermogravimetric (TG) instrument and C80 instrument. The present results show that LiFePO4 has the best thermal stability with the heat generation of −100 J/g among the tested materials, whereas Li(Ni0.5Co0.2Mn0.3)O2 produces the heat of −405 J/g. Finally, the thermal stability of these materials is further evaluated by calculating the thermal kinetic parameters based on the Arrhenius law. The present results reveal that Li(Ni0.5Co0.2Mn0.3)O2 full battery has a high risk of thermal runaway.
All authors listed have made a substantial, direct and intellectual contribution to the work, and approved it for publication.
GZ, CW, and KX were employed by company Electric Power Research Institute of Guangdong Power Grid Co., Ltd.
The remaining authors declare that the research was conducted in the absence of any commercial or financial relationships that could be construed as a potential conflict of interest.
This work is supported by the Science and Technology Project from China Southern Power Grid (No. GDKJQQ20152008).
Chen, L., Guo, X., Lu, W., Chen, M., Li, Q., Xue, H., et al. (2018). Manganese monoxide-based materials for advanced batteries. Coordinat. Chem. Rev. 368, 13–34. doi: 10.1016/j.ccr.2018.04.015
Chen, Y.-B., Hu, Y., Lian, F., and Liu, Q.-G. (2010). Synthesis and characterization of spinel Li1.05Cr0.1Mn1.9O4−zFz as cathode materials for lithium-ion batteries. Int. J. Min. Metal. Mater. 17, 220–224. doi: 10.1007/s12613-010-0217-8
Du, Y., Huang, X., Zhang, K., Liang, F., Li, Q., Yao, Y., et al. (2016). Thermal stability of LiFePO4/C-LiMn2O4 blended cathode materials. Sci. China Technol. Sci. 60, 58–64. doi: 10.1007/s11431-016-0329-7
Feng, C., Li, H., Zhang, P., Guo, Z., and Liu, H. (2010). Synthesis and modification of non-stoichiometric spinel (Li1.02Mn1.90Y0.02O4−yF0.08) for lithium-ion batteries. Mater. Chem. Phys. 119, 82–85. doi: 10.1016/j.matchemphys.2009.07.049
Gong, J., Wang, Q., and Sun, J. (2017). Thermal analysis of nickel cobalt lithium manganese with varying nickel content used for lithium ion batteries. Thermochim. Acta 655, 176–180. doi: 10.1016/j.tca.2017.06.022
Hannan, M.A., Lipu, M.S.H., Hussain, A., and Mohamed, A. (2017). A review of lithium-ion battery state of charge estimation and management system in electric vehicle applications: challenges and recommendations. Renew. Sustain. Energy Rev. 78, 834–854. doi: 10.1016/j.rser.2017.05.001
Julien, C.M., Mauger, A., Groult, H., and Zaghib, K. (2014a). Surface modification of positive electrode materials for lithium-ion batteries. Thin Solid Films 572, 200–207. doi: 10.1016/j.tsf.2014.07.063
Julien, C.M., Mauger, A., Zaghib, K., and Groult, H. (2014b). Comparative issues of cathode materials for Li-ion batteries. Inorganics 2, 132–154. doi: 10.3390/inorganics2010132
Li, L., Zhu, Z.H., Yan, Z.F., Lu, G.Q., and Rintoul, L. (2007). Catalytic ammonia decomposition over Ru/carbon catalysts: the importance of the structure of carbon support. Appl. Catalysis A Gen. 320, 166–172. doi: 10.1016/j.apcata.2007.01.029
Lu, Y., Li, B., Zheng, S., Xu, Y., Xue, H., and Pang, H. (2017). Syntheses and energy storage applications of MxSy (M = Cu, Ag, Au) and their composites: rechargeable batteries and supercapacitors. Adv. Funct. Mater. 27:1703949. doi: 10.1002/adfm.201703949
Luo, W., and Zheng, B. (2017). Improved electrochemical performance of LiNi0.5Co0.2Mn0.3O2 cathode material by double-layer coating with graphene oxide and V2O5 for lithium-ion batteries. Appl. Surface Sci. 404, 310–317. doi: 10.1016/j.apsusc.2017.01.200
Ma, J., Guo, X., Yan, Y., Xue, H., and Pang, H. (2018). FeOx-based materials for electrochemical energy storage. Adv Sci (Weinh) 5:1700986. doi: 10.1002/advs.201700986
Ouyang, C.Y., Shi, S.Q., and Lei, M.S. (2009). Jahn–Teller distortion and electronic structure of LiMn2O4. J. Alloys Compounds 474, 370–374. doi: 10.1016/j.jallcom.2008.06.123
Sun, Y.K., Myung, S.T., Park, B.C., Prakash, J., Belharouak, I., and Amine, K. (2009). High-energy cathode material for long-life and safe lithium batteries. Nat. Mater. 8, 320–324. doi: 10.1038/nmat2418
Susanto, D., Kim, H., Kim, J.-Y., Lim, S., Yang, J., Choi, S.A., et al. (2015). Effect of (Mg, Al) double doping on the thermal decomposition of LiMn2O4 cathodes investigated by time-resolved X-ray diffraction. Curr. Appl. Phys. 15, S27–S31. doi: 10.1016/j.cap.2015.01.027
Wang, Q., Ping, P., Zhao, X., Chu, G., Sun, J., and Chen, C. (2012). Thermal runaway caused fire and explosion of lithium ion battery. J. Power Sources 208, 210–224. doi: 10.1016/j.jpowsour.2012.02.038
Wang, Q., Sun, J., Yao, X., and Chen, C. (2006). Micro calorimeter study on the thermal stability of lithium-ion battery electrolytes. J. Loss Prevent. Process Ind. 19, 561–569. doi: 10.1016/j.jlp.2006.02.002
Wang, X., Hao, H., Liu, J., Huang, T., and Yu, A. (2011). A novel method for preparation of macroposous lithium nickel manganese oxygen as cathode material for lithium ion batteries. Electrochim. Acta 56, 4065–4069. doi: 10.1016/j.electacta.2010.12.108
Xu, W., Yuan, A., Tian, L., and Wang, Y. (2011). Improved high-rate cyclability of sol–gel derived Cr-doped spinel LiCryMn2−yO4 in an aqueous electrolyte. J. Appl. Electrochem. 41, 453–460. doi: 10.1007/s10800-011-0255-6
Yang, K., Fan, L.-Z., Guo, J., and Qu, X. (2012). Significant improvement of electrochemical properties of AlF3-coated LiNi0.5Co0.2Mn0.3O2 cathode materials. Electrochim. Acta 63, 363–368. doi: 10.1016/j.electacta.2011.12.121
Yi, T.-F., Yin, L.-C., Ma, Y.-Q., Shen, H.-Y., Zhu, Y.-R., and Zhu, R.-S. (2013). Lithium-ion insertion kinetics of Nb-doped LiMn2O4 positive-electrode material. Ceramics Int. 39, 4673–4678. doi: 10.1016/j.ceramint.2012.10.256
Keywords: lithium ion battery safety, cathode materials, electrochemical analysis, thermal analysis, thermal runaway
Citation: Zhong G, Gong J, Wang C, Xu K and Chen H (2018) Comparison of the Electrochemical Performance and Thermal Stability for Three Kinds of Charged Cathodes. Front. Energy Res. 6:110. doi: 10.3389/fenrg.2018.00110
Received: 15 July 2018; Accepted: 02 October 2018;
Published: 30 October 2018.
Edited by:
Qingsong Wang, University of Science and Technology of China, ChinaCopyright © 2018 Zhong, Gong, Wang, Xu and Chen. This is an open-access article distributed under the terms of the Creative Commons Attribution License (CC BY). The use, distribution or reproduction in other forums is permitted, provided the original author(s) and the copyright owner(s) are credited and that the original publication in this journal is cited, in accordance with accepted academic practice. No use, distribution or reproduction is permitted which does not comply with these terms.
*Correspondence: Haodong Chen, bGluZ2hhb0B1c3RjLmVkdS5jbg==
Disclaimer: All claims expressed in this article are solely those of the authors and do not necessarily represent those of their affiliated organizations, or those of the publisher, the editors and the reviewers. Any product that may be evaluated in this article or claim that may be made by its manufacturer is not guaranteed or endorsed by the publisher.
Research integrity at Frontiers
Learn more about the work of our research integrity team to safeguard the quality of each article we publish.