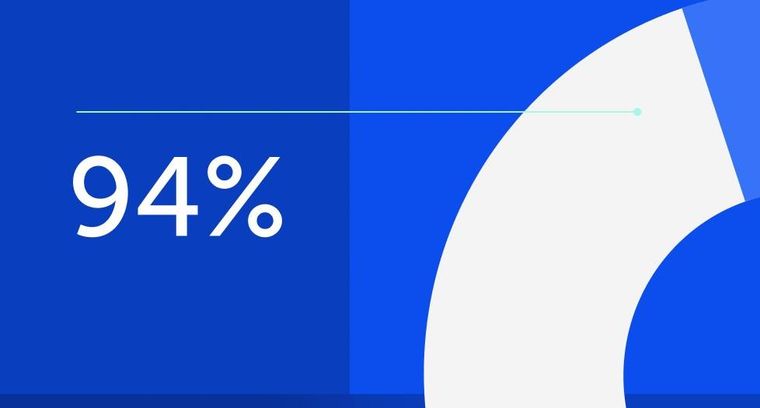
94% of researchers rate our articles as excellent or good
Learn more about the work of our research integrity team to safeguard the quality of each article we publish.
Find out more
ORIGINAL RESEARCH article
Front. Earth Sci., 06 March 2024
Sec. Geohazards and Georisks
Volume 12 - 2024 | https://doi.org/10.3389/feart.2024.1375979
This article is part of the Research TopicEvolution Mechanism and Control Method of Engineering Disasters Under Complex EnvironmentView all 30 articles
Introduction: This study focuses on investigating the characteristics of overburden failure and ground pressure behavior in shallow coal seam mining beneath a gully. The research is conducted at the 135201 working face of Shaliang Coal Mine in the Shenfu Mining Area.
Methods: The study employs physical similarity simulation tests, theoretical analysis, and field measurements to analyze the ground pressure and overburden failure characteristics at the working face.
Results: The research findings indicate that the ground pressure is stronger in the uphill section compared to the gully bottom and downhill sections. The weighting interval in the uphill section is the smallest. A mechanical analysis model for the failure structure of the key stratum in the uphill section is established based on monitored ground pressure data and physical simulation test results. A calculation formula for the weighting interval in the uphill section is derived. The relationship between the caving interval, the thickness of the key stratum in the uphill section, and the gully slope is also analyzed. The on-site measurements align well with the theoretical results.
Discussion: The study proposes a prediction method for ground pressure and suggests hazard prevention and control measures for shallow coal seam mining beneath a gully based on the research findings.
In the mining area of western China, there exists a significant number of shallow buried coal seams with large surface fluctuations, particularly in gully development areas. These areas exhibit more complex geological conditions compared to general terrains. The mining of shallow buried coal seams in gully terrains is susceptible to geological hazards, including landslides, surface subsidence, and dynamic load pressure, with the latter being particularly prominent (Yang et al., 2021; Feng et al., 2022; Miao et al., 2022). The diversified occurrence of gully slopes contributes to more severe mine pressure behavior for shallow buried coal seams in comparison to general terrains, as observed in production practice and related research. Specifically, the working face experiences shorter pressure durations, accompanied by greater and more destructive pressure levels. Consequently, serious geological disasters, such as frame crushing, roof fall, and rib spalling, occur within the working face, significantly endangering mine safety and production (Huang, 2002; Xu et al., 2009; Zhang et al., 2017; Dai et al., 2018; Dai et al., 2020; Dai et al., 2022; Wang Q. et al., 2023; Zhang B. et al., 2023; Dai et al., 2023; Liu et al., 2023; Pan and Wang, 2023). Hence, urgent research efforts are required to mitigate the occurrence of sudden disasters.
To address the intricate geological issue of abnormal pressure on the working face resulting from mining shallow buried coal seams in gully terrains, scholars in the field have conducted the following research studies. Zhang et al. (Zhang et al., 2011) and Ma and Kang (Ma and Kang, 2022) studied the ground pressure law at the working face for shallow coal seam mining underneath the gully through the on-site measurement and the theoretical analysis, and they concluded that the support resistance at the working face increased significantly in the uphill section. Wang et al. (Wang et al., 2010) studied the structural evolution law of the mining slope underneath the gully with the physical simulation and theoretical analysis, and then established a mechanical analysis model for initial failure of the main roof of shallow coal seam underneath the gully. The research results indicated that the failed rock blocks in the overburden occurred rotary sinking with the advancement of the working face, and that the larger the slope angle, the more obvious the ground pressure behavior. Li et al. (Li J. et al., 2016; Li et al., 2019) conducted an in-depth study on the factors affecting the ground pressure behavior in shallow coal seams, and concluded that the thickness of key stratum was the most important factor affecting the weighting interval. Zhao et al. (Zhao et al., 2018) investigated the ground pressure law during the shallow and thick coal seam mining underneath the gully through the numerical simulation, and discovered that the influence zone of original rock stress field on the mining pressure law at the working face underneath the gully could be divided into significant, attenuated, and unaffected zones according to the depth of the coal seam. Li et al. (Li et al., 2020), through theoretical analysis and physical simulation, explored the influence of slope angle, height, and direction on the stability of masonry beam structures. Wang et al. (Wang X. et al., 2023) argued that gully topography modifies the original stress field of the rock mass and leads to significant stress concentration during coal seam mining.
Yang et al. (Yang et al., 2020) investigated the overburden structure and mining pressure law in the shallow fully-mechanized top-coal caving face. The findings revealed that the high-level key stratum masonry beam structure and the low-level key stratum cantilever beam structure were destabilized by the influence of mining, resulting in strong ground pressure at the working face. Based on the variations of the support resistance at the mining working face underneath the gully, Xiao et al. (Xiao and Yao, 2021) concluded that the main and secondary factors affecting the working resistance of the support at the working face were the gully cutting coefficient and the slope foot, respectively. Zhang et al. (Zhang et al., 2019; Zhang et al., 2021) studied the dynamic loading problem of the working face underneath the gully through physical simulation, and they constructed the “non-uniformly loaded beam structure”, and revealed the mechanism of the dynamic ground pressure generated by the non-uniform loads. Through numerical analysis and physical simulation, Huang et al. (Huang and Du, 2018) studied the relationship between the stress concentration of coal pillars in multi-coal seam mining and the staggered distance of section coal pillars and the development of overburden fractures. The research shows that the mechanism of slowing down the concentrated stress of coal pillar group and realizing the uniform settlement of ground surface. Yu et al. (Yu et al., 2020) conducted a study using PFC2D to investigate the impact of coal mining on the deformation and failure characteristics of high and steep slopes. Xu et al. (Xu et al., 2016) examined the influence of underground mining on the rock strata and surface of open-pit slopes through discrete element numerical simulation. Zhao et al. (Zhao et al., 2023) focused on the effect of coal mining on the stability of loess slopes using physical simulation, identifying the slope angle and height as crucial factors for slope stability. Tang et al. (Tang et al., 2019) developed a fracture model for bedding rock slopes and verified its reliability through physical simulation. Zhang et al. (Zhang D. et al., 2023) investigated the impact of different gully topographies on working face pressure using optical fiber and digital image technology. Dai et al. (Dai et al., 2021) obtained through physical simulation that the failure mode of the bedding rock slope under mining disturbance is the landslide form of the initial traction later stage. The breaking characteristics and movement law of rock strata are of great significance for revealing the law of mine pressure in working face. Researchers have put forward many hypotheses of rock fracture structure (Li Z. et al., 2016; Yiouta-Mitra and Sofianos, 2018). Among them, the key stratum hypothesis proposed by Chinese academician Qian has been widely used to reveal the relationship between the fracture structure of overburden rock and the law of mine pressure in working face. However, this hypothesis simplifies the load of key stratum to uniform load. For coal seams with large buried depth and small surface fluctuation, this hypothesis is very suitable. However, for shallow coal seams with gully surface, if the surface load is simplified to uniform load, it will produce large errors. Therefore, in this study, the load of key stratum of shallow coal seam under gully terrain is simplified to linear load.
The existing research mainly focuses on the factors affecting the stability of the slope and the analysis of the stability of the slope (He et al., 2015a), and the control method of the stability of the slope (He et al., 2015b; Lai et al., 2024; Lu et al., 2024). The research methods mainly include field measurement, theoretical analysis, physical simulation and numerical simulation. The above research results and research methods are very important, but due to the diversity of geological occurrence conditions, it is difficult to achieve individual cases to guide the safe and efficient mining of the mine in this paper. Therefore, with reference to the terrain and ground pressure features of the research area as well as the on-site operating conditions, this paper took the 135,201 working face of Shaliang Coal Mine in Shenfu Mining Area as the research object to analyze the overburden failure characteristics and ground pressure law of the working face underneath the gully. A mechanical calculation model of the key stratum for mining underneath the gully was established, and the key stratum caving and its influencing factors were analyzed. The results of the study can provide meaningful guidance for the prevention and control of ground pressure-related hazards in the working face for shallow coal seam mining underneath the gully.
Shaliang Coal Mine is located in Shenfu mining area, Shaanxi Province, China, with a length of 8.4 km from east to west and a width of 5.9 km from north to south, and the depth of the coal seams ranges from 40 to 150 m. There are 5 layers of recoverable coal seams, where the 5-2 coal seam featured by a relatively stable thickness and an uncomplicated structure is mainly mined at present.
The terrain of the mine field is a typical gully and valley landform, with numerous gullies and ridges forming natural watersheds along the north-east to south-west direction. There are Daxi Gully, Maimai Gully, and Luancai Gully developed from west to east in the mine field. The depth of the gully in the Shaliang Coal Mine area is generally 10–60 m, with an average depth of 35 m. The width of the gully is 34–780 m, with an average width of 407 m. The gully slope is 8°–38°, with an average slope of 23°.
There is only one working face (i.e., 135,201 working face) in Shaliang Coal Mine, whose coal seam thickness ranges from 2.90 to 3.34 m, with an average of 3.12 m, and the dip angle of the coal seam ranges from 0° to 2°. Its immediate roof is siltstone with a thickness of 4.75 m, and its main roof is medium-grained sandstone with an average thickness of 9.1 m. Its immediate floor is sandy mudstone with an average thickness of 3.4 m, and its main floor is fine-grained sandstone with an average thickness of 10 m.
The ground surface above 135,201 working face is undulating, which is low in the middle and high on both sides. The maximum elevation is 1,248 m, which is 1,320 m away from the open-off cut of the working face. The minimum elevation is 1,168 m, which is located in the 795 m section of the return airway of the 135,201 working face, i.e., it is in the gully at the northwestern part of Yangye village. The location of the working face and the development of surface fractures are illustrated in Figure 1.
When the 135,201 working face passed through the gully, the ground pressure monitoring was conducted on the upper, middle, and lower regions of a total of 21 supports at the working face by means of the KJ440 Coal Mine Roof Pressure Monitoring System. The pressure distribution characteristic of each support during working face advancement was drawn according to the monitoring data. The difference between the ground pressures in the downhill and uphill sections of the gully was analyzed to understand the pressure pattern when the working face passed through the gully terrain.
Figure 2 presents the distribution characteristic of the support resistances at the working face. It was observed that the average periodic weighting interval in the downhill section of the gully terrain was 16.95 m. The support resistance during the weighting was 20–22 kN, with an average of 20.5 kN. The ground pressure behavior at the working face in the downhill section was more moderate. The ground pressure was characterized by the fact that the weighting firstly occurred in the head or tail region of the working face, and then shifted to the middle part as the working face advanced. The resistance of the supports accounted for about 78% of the rated working resistance. During the weighting, the coal wall of the working face experienced flaking, which was mainly concentrated in the region of 60#-110# supports in the middle, and the depth of flaking was generally 500 mm.
The average periodic weighting interval in the uphill section of the gully terrain was 16.95 m, which indicated that the overburden transport at the working face in the uphill section was stronger than that in the downhill section. During the weighting, the support resistances were 20–22 kN, with an average of 21 kN. The flaking was observed in 40–126# supports when the weighting occurred in the working face, with the depth of flaking being 300–800 mm, and there were occasional roof leakage in front of the individual supports.
When the 135,201 working face in Shaliang Coal Mine crossed the gully terrain, the weighting in the uphill section was stronger than that in the downhill section. The weighting was occasionally accompanied by flaking and roof leakage, but the overall depth of flaking was not large, and the safety valve of the support had not been opened. No dynamic loading ground pressure occurred in the section of the working face crossing the gully, which was obviously different from the existing dynamic loading ground pressures at the working face crossing the gully. The main reason for this was that the main key stratum was covered by loess when the 135,201 working face passed through the gully terrain. The working face that was not affected by weathering and stripping did not experience dynamic loading during the passage through the gully terrain, which ensured the recovery safety of the working face.
A similarity simulation test was conducted to study overburden caving and failure characteristics when the working face passed through the gully, and to analyze the influence of fracture development on the recovery safety of the working face. The design diagram of the similarity simulation test is presented in Figure 3. According to the geological conditions of the 135,201 working face, a 3 m × 1.3 m planar simulation experiment platform was designed to study the terrain conditions such as downhill scenario, gully scenario, and uphill scenario, respectively. Based on the physical similarity constants, the similarity ratios of geometry, stress, and time of the model were taken as 1:100, 1:80 and 1:4, respectively, and the similarity ratios of dimensionless physical parameters (e.g., internal friction angle, strain, Poisson’s ratio, coefficient of friction, etc.) were all set to be 1.
The LY-350 pressure sensor was used to monitor the floor pressure during the advancement of the working face, and the AD-36 pressure computer data collector was used to collect the pressure data. The 128-channel data analysis system was adopted to process the data. These data were used to investigate the ground pressure behavior in the uphill, gully bottom, and downhill sections. The displacement monitoring system mainly consists of PENTAXR-322NX optical total station and GOM ARAMIS system. A total of three roof displacement observation lines were embedded in the model, which were labeled as R1-R3.
With consideration of the lithology of the roof and floor of Shaliang Coal Mine as well as the experimental demand, the parameters of the roof and floor of the 135,201 working face were simplified, and the physical and mechanical parameters of each stratum were determined according to the similarity theory. The similar material used river sand as aggregate, gypsum and calcium carbonate as cement, and a layer of mica as the lamination was laid at the interface of rock layers. The mixing ratios of similar materials are summarized in Table 1.
The first weighting occurred in the downhill section when the working face advanced to 42 m, and the failure length of the main roof was 32 m. When the working face advanced to 80 m, the caving occurred in the lower part of the main roof, forming a hinge structure with the coal wall ahead of the working face. The second periodic weighting happened in the working face, with a weighting interval of 19 m, as depicted in Figure 4A. When the working face advanced to 115 m, 140 m, and 170 m respectively, three times of periodic weighting occurred in the gully bottom mining section, with the weighting intervals of 35.2 m, 25.0 m, and 29.8 m, and the average weighting interval of 30.0 m. The surface at the gully experienced stepwise subsidence, as displayed in Figure 4B. When the working face advanced from the gully bottom mining section to the uphill mining section, the working face in the uphill section underwent four times of periodic weighting at 185 m, 200 m, 215 m, and 230 m, with the weighting intervals of 15.3 m, 15.2 m, 14.9 m, and 15.4 m, respectively, and the average weighting interval of 15.2 m. The overburden fractures were mainly tensile fractures when the working face advanced to the uphill section, and the width of surface fractures was 1.5 m, with a vertical stagger of 1 m, as illustrated in Figure 4C. When the working face advanced to the convex terrain mining section, two times of periodic weighting occurred when the working face advanced to 245 m and 260 m. The weighting intervals were 17.5 m and 19.8 m, with an average weighting interval of 18.7 m. With the advancement of the working face, the fractures in the uphill section were closed, and new fractures were formed on the right side of the convex terrain, and the loess layer at the slope top was formed into a V-shape structure, as illustrated in Figure 4D. Due to the different thicknesses of the loose layer in each section, the average periodic weighting was also different, where the order of the weighting interval was the gully bottom section > downhill section > uphill section. The damage to the slope surface was more severe.
FIGURE 4. Characteristics of overburden caving during the advancement of working face. The number marked in the diagram is the key layer collapse distance.
It was observed from the overburden displacement nephogram in Figure 5 that the vertical displacement of the bedrock was larger than that of the surface. When the working face advanced to the downhill section, the maximum subsidence of the bedrock and the surface was 2.36 m and 1.54 m, respectively, and the surface subsidence coefficient was 0.62 m.
Bedrock and surface subsidence gradually increased as the working face advanced from the downhill mining section to the gully bottom mining section. The subsidence at the gully bottom was larger at 40 m and 110 m, with the maximum bedrock and surface subsidence at 110 m. The maximum bedrock and surface subsidence was 2.37 m and 2.13 m, respectively, and the surface subsidence coefficient was 0.75.
When the working face advanced from the gully bottom mining section to the uphill mining section, the maximum bedrock and surface subsidence was at 110 m. The maximum bedrock and surface subsidence was 2.37 m and 2.14 m, respectively, and the surface subsidence coefficient was 0.86.
Figure 6 presents the distribution characteristics of the displacements obtained from observation lines embedded in the overburden. When the 135201working face of Shaliang Coal Mine advanced underneath the gully terrain, the bedrock load changed obviously due to the different thicknesses of the loose layer in each section. The maximum subsidence coefficients of bedrock and surface were also different, in which the maximum subsidence coefficients were in the order of gully bottom section > uphill section > downhill section.
FIGURE 6. Distribution characteristics of the displacements obtained from observation lines embedded in the overburden. Among them, 90, 13, 170, 210, 250 and 270 m are the advancing distance of the working face.
The change rule of the floor pressure during the advancement of the working face is illustrated in Figure 7. Due to the different bedrock loads, the floor pressure varied significantly when recovering underneath the gully terrain. The advanced abutment pressure of the working face in the downhill section was 750–870 kN, with an average of 810 kN. The ground pressure behavior of the working face was relatively moderate throughout the mining in the downhill section. As the working face continued to advance from the downhill mining section to the gully bottom mining section, the advanced abutment pressure during the advancement of the working face ranged from 421 to 1,140 kN, with an average of 780 kN. As the working face continued to advance from the gully bottom mining section to the uphill mining section, the advanced abutment pressure during the advancement of the working face ranged from 1,370 to 1,990 kN, with an average of 1,680 kN. When the working face was mined in the gully bottom section and the uphill section, the rotational deformation of the overburden easily led to the stress concentration at the slope foot. The distribution patterns of the floor pressure during the advancement of the working face was: uphill section > downhill section > gully bottom section.
Since the ground pressure behavior was intense when the working face advanced to the uphill section, the mechanical mechanism of the key stratum failure of the overburden in the uphill section was analyzed. According to the failure characteristics of the key stratum of the overburden in the uphill section revealed by the physical similarity simulation test, the force characteristics of the key stratum in the uphill mining section underneath the gully terrain were simplified to a problem of a cantilever beam subjected to the linear loads, as illustrated in Figure 8.
In Figure 8, θ is the gully slope in the uphill section, with a unit of °; q(x) is the load applied to the key stratum of the overburden, with a unit of MPa; q(x)=xρgtanθ; h is the thickness of the key stratum, with a unit of m; L is the length of the rock block of the key stratum, with a unit of m; Fs is the shear force at the fixed-end, with a unit of MPa; and Ms is the bending moment at the fixed-end, with a unit of kN⋅m.
According to the plane stress equation, the stress boundary condition of the cantilever beam in this mechanical model can be derived as shown in Eq. 1:
where σx and σy are the positive stresses of the rock block of the key stratum in the x and y directions, respectively, with a unit of MPa; τxy is the stress of the rock block of the key stratum in the xy direction, with a unit of MPa; ρg is the volumetric force of rock mass, with a unit of MN/m3.
Setting σy=f(y)x, According to Saint-Venant’s theorem, the stress distribution expression in the key strata can be solved as shown in Eq. 2:
where x and y are the amounts of change in the thickness and length of the rock block of the key stratum, with a unit of m.
The shear force Fs and the bending moment Ms at the fixed end of the cantilever beam subjected to linear loads could be solved from the mechanics of materials as Eqs 3, 4:
The analysis of the mechanical model of the key stratum indicated that the danger point of the cantilever beam was at the fixed end, and its failure modes were tensile failure and shear failure. Firstly, the ultimate span of cantilever beam in tension failure was analyzed. The analysis of the stress distribution and bending moment of the cantilever beam determined that the danger point of tensile failure was at (L,-h/2), and the maximum tensile stress at this point was Eq. 5:
where (σx)man is the maximum tensile stress at the fixed end of the rock block of the key stratum, with a unit of m; LT is the caving interval of the key stratum in tension failure, with a unit of m.
When (σx)man=Rt, i.e., the positive stress in the rock mass at this point reached the ultimate tensile strength of the rock mass, the rock mass would be fractured at this point. The ultimate span of the beam when it broke is Eq. 6:
where Y1 and Y2 are shown in Eq. 7
where σt is the ultimate tensile strength of the rock block of the key stratum, with a unit of MPa.
When (τxy)max=Rs, the ultimate caving interval formed when the beam was sheared is Eq. 8:
where (τxy)max is the maximum tensile stress at the fixed end of the rock block of the key stratum, with a unit of MPa; Ls is the caving interval of the key stratum in tension damage, with a unit of m; Rs is the shear strength of the rock block of the key stratum, with a unit of MPa.
In summary, the expression of the limit collapse step of the key stratum is Eq. 9
According to the theoretical analysis and physical simulation experiment, the relationship between the limit caving distance of the key stratum and the slope toe in the uphill stage of the 135,201 working face of Shaliang Coal Mine is shown in Figure 9. When the gully slope angle is greater than 46°, the key stratum rock mass shows shear fracture, and the broken rock block slides and loses stability. When the gully slope angle is less than 46°, the key stratum rock mass shows tensile fracture, and the broken rock block rotates and loses stability.
The main roof of the 135201working face in Shaliang Coal Mine was 9.1 m thick medium-grained sandstone. The physical and mechanical test results of the key stratum confirmed that the ultimate tensile strength Rt and the shear strength Rs, of the rock block of the key stratum were 2.5 MPa, 3.7 MPa, respectively, and the volume force ρg of the key stratum was 0.024 MN/m3. On this basis, the relationship among the caving interval L, the thickness of the key stratum h, and the gully slope θ could be obtained, as displayed in Figure 10.
FIGURE 10. Relationship among the overburden failure span, the thickness of key stratum, and the gully slope.
In case of mining under the gully, the ultimate caving interval of the overburden was closely related to both the thickness of the key stratum and the gully slope. The ultimate span increased as the thickness of the key layer increased in the uphill section. When the thickness of the key stratum remained unchanged, the ultimate span decreased with the increase of the gully slope.
The calculation model for mine pressure in the working face of the uphill section under valley terrain is illustrated in Figure 11. The linear load applied by the overlying strata of the key stratum is represented by q(x), while the hinge point of the key stratum rock block is denoted by point M The mine pressure, Pm, at the working face is mainly comprised of two components.
The first component is the pressure, R2, exerted by the immediate roof rock mass. The second component is the pressure, R1, applied once the key stratum rock mass has become broken and unstable. By conducting a mechanical analysis of Figure 11, we can derive the expression for the support pressure at the working face, as follows Eq. 10:
In the formula: γ0 is the average bulk density of the immediate roof strata above the support. b and Lk are the width of the hydraulic support and the length of the control roof, respectively. h0 is the thickness of immediate roof strata.
According to the above analysis, it can be concluded that the working face pressure is proportional to the cubic and slope angle of the limit collapse distance of the key strata in the uphill mining stage. Obviously, the mine pressure of the working face is more affected by the change of slope angle.
(1) Prediction of ground pressure pattern for gully-crossing mining
To verify the reliability and accuracy of the research results, the monitoring of the ground pressure was carried out on the gully-crossing section of the 135,202 working face of Shaliang Coal Mine. A total of 118 sets of ZY9200/15/29 type powered supports were used at the 135,202 working face. Three powered supports were respectively selected from the upper, middle, and lower parts of the working face, and the average values of their monitoring data were taken as the final support resistances. The monitoring section was from 35 m of the open-off cut to the departure of gully, with a length of 290 m. The change curves of the support resistances at the 135,202 working face in the gully-crossing section are displayed in Figure 12.
The monitored support resistances indicated that three times of weighting occurred at the working face in the downhill section. The interval of the first weighting was about 32 m, the periodic weighting intervals were about 16 m and 20 m, respectively, with an average periodic weighting interval of 18 m and a maximum pressure of 41 MPa. Four times of periodic weighting occurred in the gully bottom section, and the weighting intervals were about 18 m, 34 m, 26 m, and 30 m, respectively, with an average weighting interval of 27 m and a maximum pressure of 37 MPa. Three times of the weighting occurred in the uphill section, and the weighting intervals were 17 m, 16 m, and 15 m, respectively, with an average weighting interval of 16 m and a maximum pressure of 41 MPa. There were three times of weighting occurred in the convex terrain section, and the weighting intervals were 16 m, 17 m, and 19 m, respectively, with an average weighting interval of 17.3 m and a maximum pressure of 38 MPa. The location of the maximum weighting was in the uphill section. The weighting intervals were ordered from largest to smallest as: gully bottom section, downhill section, convex terrain section, and uphill section. The monitoring results were in good agreement with the experimental and theoretical results, which indicated that the current study provided valuable theoretical support for shallow coal seam mining underneath the gully.
(2) Hazard prevention measures for shallow coal seam mining underneath the gully
According to this study, the preliminary idea of prediction and prevention of mining pressure law in shallow coal seam is put forward. When the working face is mined through the ditch, the dynamic pressure dangerous area and the mine pressure law of the working face should be pre-dicted first, so as to put forward targeted preventive measures to prevent and control the mine pressure disaster. The previous research shows that the thickness of the key stratum and the slope of the valley are the key factors affecting the pressure law, and the dangerous area of the later section can be identified accordingly. For the area where the key layer is missing, the support resistance should be increased, the advance speed should be accelerated appropriately, the mining height should be reduced locally, the support should be moved with pressure and supported in time; in the case of large gully slope angle of thick loose layer, the loose layer can be stripped in advance to reduce the load of the key layer, so as to effectively ensure the safe mining of the working face when crossing the gully.
(1) The weighting in the uphill section was stronger than that in the downhill section during the 135,201 working face of Shaliang Coal Mine passed though the gully terrain. The weighting was occasionally accompanied by flaking and roof leakage, but the overall depth of flaking was not large, and the safety valve of the support had not been opened. No dynamic loading ground pressure occurred in the section of the working face crossing the gully, which was obviously different from the existing dynamic loading ground pressures at the working face crossing the gully.
(2) The model test results confirmed that the average periodic weighting varied due to the different thickness of the loose layer in each section. The weighting intervals were in the order of gully bottom section > downhill section > uphill section. The bedrock loads varied significantly, and the maximum subsidence coefficients of bedrock and surface were also different. The order of the maximum bedrock subsidence coefficients was: gully bottom section > uphill section > downhill section. When the working face was mined in the gully bottom section and the uphill section, the rotational deformation of the overburden easily led to the stress concentration at the slope foot. The distribution pattern of the floor pressure during the advancement of the working face was: uphill section > downhill section > gully bottom section.
(3) Based on the monitored ground pressure law in the field and the overburden failure characteristics of shallow coal seam underneath the gully obtained by physical similarity simulation test, a mechanical analysis model for failure structure of key stratum in the uphill section was established, and the calculation formula for weighting interval in the uphill section was deduced. The ultimate span increased as the thickness of the key stratum increased and the gully slope decreased.
(4) The ground pressure monitoring on the gully-crossing section of the 135,202 working face of Shaliang Coal Mine revealed that the weighting intervals in the uphill section were 17 m, 16 m, and 15 m, respectively, with an average weighting interval of 16 m. The location of the maximum weighting was in the uphill section. The weighting intervals were ordered from largest to smallest as: gully bottom section, downhill section, convex terrain section, and uphill section. The monitoring results were in good agreement with the experimental and theoretical results, which could provide valuable theoretical support for shallow coal seam mining underneath the gully.
The original contributions presented in the study are included in the article/Supplementary material, further inquiries can be directed to the corresponding author.
JZ: Writing–review and editing, Conceptualization, Project administration. LW: Data curation, Methodology, Writing–original draft. TY: Methodology, Supervision, Writing–review and editing. SG: Data curation, Investigation, Writing–review and editing. YH: Validation, Writing–review and editing. JW: Validation, Writing–review and editing.
The author(s) declare that no financial support was received for the research, authorship, and/or publication of this article.
The authors declare that the research was conducted in the absence of any commercial or financial relationships that could be construed as a potential conflict of interest.
All claims expressed in this article are solely those of the authors and do not necessarily represent those of their affiliated organizations, or those of the publisher, the editors and the reviewers. Any product that may be evaluated in this article, or claim that may be made by its manufacturer, is not guaranteed or endorsed by the publisher.
Dai, L., Pan, Y., Li, Z., Wang, A., Xiao, Y., Liu, F., et al. (2023). Quantitative mechanism of roadway rockbursts in deep extra-thick coal seams: theory and case histories. Tunn. Undergr. Space Technol. 111, 103861–107798. doi:10.1016/j.tust.2021.103861
Dai, L., Pan, Y., and Wang, A. (2018). Study of the energy absorption performance of an axial splitting component for anchor bolts under static loading. Tunn. Undergr. Space Technol. 81, 176–186. doi:10.1016/j.tust.2018.07.009
Dai, L., Pan, Y., Zhang, C., Wang, A., Canbulat, I., Shi, T., et al. (2022). New criterion of critical mining stress index for risk evaluation of roadway rockburst. Rock Mech. Rock Eng. 55, 4783–4799. doi:10.1007/s00603-022-02888-7
Dai, L., Xiao, Y., Pan, Y., Wang, A., Fan, C., and Guo, J. (2020). Mechanical behavior and factors influencing axial splitting energy absorbers and optimized application for rock bolts. Tunn. Undergr. Space Technol. 102, 103427–107798. doi:10.1016/j.tust.2020.103427
Dai, Z., Zhang, L., Wang, Y., Jiang, Z., and Xu, S. (2021). Deformation and failure response characteristics and stability analysis of bedding rock slope after underground adverse slope mining. Bull. Eng. Geol. Environ. 80, 4405–4422. doi:10.1007/s10064-021-02258-7
Feng, D., Hou, E., Xie, X., Che, X., Hou, P., and Long, T. (2022). Prediction and treatment of water leakage risk caused by the dynamic evolution of ground fissures in gully terrain. Front. Earth Sci. 9, 803721. doi:10.3389/feart.2021.803721
He, Y., Hazarika, H., Yasufuku, N., and Han, Z. (2015a). Evaluating the effect of slope angle on the distribution of the soil-pile pressure acting on stabilizing piles in sandy slopes. Comput. Geotechnics 69, 153–165. doi:10.1016/j.compgeo.2015.05.006
He, Y., Hazarika, H., Yasufuku, N., Teng, J., Jiang, Z., and Han, Z. (2015b). Estimation of lateral force acting on piles to stabilize landslides. Nat. Hazards 79, 1981–2003. doi:10.1007/s11069-015-1942-0
Huang, Q. (2002). Ground pressure characteristics of shallow coal seam and definition of shallow coal seam. J. Rock Mech. Eng. 21, 1174–1177. doi:10.3321/j.issn:1000-6915.2002.08.014
Huang, Q., and Du, J. (2018). Study on coupling control of section coal pillar stress and surface crack in shallow coal seam group mining. J. Coal 03, 591–598. doi:10.13225/j.cnki.jccs.2017.0462
Lai, X., Xu, H., Shan, P., Hu, Q., Ding, W., Yang, S., et al. (2024). Research on mechanism of rockburst induced by mined coal-rock linkage of sharply inclined coal seams. Int. J. Miner. Metall. Mater. doi:10.1007/s12613-024-2833-8
Li, J., Liu, C., Wang, W., and Wang, C. (2019). Linkage-induced mechanism and control technology of pressure bump and surface geological damage in shallow coal seam mining of gully area. Arabian J. Geosciences 12, 349. doi:10.1007/s12517-019-4511-0
Li, J., Liu, C., and Zhao, J. (2016a). Sensitivity analysis of influencing factors of mining pressure behavior in shallow coal seam mining. J. Min. Saf. Eng. 05, 853–859. doi:10.13545/j.cnki.jmse.2016.05.014
Li, Z., Dou, L., Cai, W., Wang, G., Ding, Y., and Kong, Y. (2016b). Mechanical analysis of static stress within fault-pillars based on a voussoir beam structure. Rock Mech. Rock Eng. 49, 1097–1105. doi:10.1007/s00603-015-0754-6
Li, Z., Yu, S., Zhu, W., Feng, G., Xu, J., Guo, Y., et al. (2020). Dynamic loading induced by the instability of voussoir beam structure during mining below the slope. Int. J. Rock Mech. Min. Sci. 132, 104343. doi:10.1016/j.ijrmms.2020.104343
Liu, C., Li, J., Zhao, J., Chen, Y., Zhang, H., and Yu, X. (2023). Mechanism of dynamic mine pressure and distribution characteristics of gas-conducting fractures in overlying strata of shallow-buried thick coal seam mining in gully area. J. Min. Saf. Eng. 40, 965–971. doi:10.13545/j.cnki.jmse.2023.0256
Lu, B., Sheil, B., Zhao, W., Jia, P., Bai, Q., and Wang, W. (2024). Laboratory testing of settlement propagation induced by pipe-roof pre-support deformation in sandy soils. Tunn. Undergr. Space Technol. 146, 105645. doi:10.1016/j.tust.2024.105645
Ma, S., and Kang, Y. (2022). Characteristics of mining-induced slope movement and ground behavior under gully landforms. Sustainability 14, 13941. doi:10.3390/su142113941
Miao, K., Tu, S., Tu, H., Liu, X., Li, W., Zhao, H., et al. (2022). Research on fractal evolution characteristics and safe mining technology of overburden fissures under gully water body. Fractal Fract. 6, 486. doi:10.3390/fractalfract6090486
Pan, Y., and Wang, A. (2023). Disturbance response instability theory of rock bursts in coal mines and its application. Geohazard Mech. 1, 1–17. doi:10.1016/j.ghm.2022.12.002
Tang, J., Dai, Z., Wang, Y., and Zhang, L. (2019). Fracture failure of consequent bedding rock slopes after underground mining in mountainous area. Rock Mech. Rock Eng. 52, 2853–2870. doi:10.1007/s00603-019-01876-8
Wang, Q., Wang, Y., Jiang, B., Jiang, Z., and Xue, H. (2023a). Geomechanics model test research on large deformation control mechanism of roadway disturbed by strong dynamic pressure. Geohazard Mech. 1, 140–152. doi:10.1016/j.ghm.2023.06.002
Wang, X., Cai, L., Zhang, B., Wu, J., Zhu, Q., and Cui, Z. (2023b). Simulation study on surface deformation of shallow buried coal seam mining in a gully area. Front. Earth Sci. 11, 1287981. doi:10.3389/feart.2023.1287981
Wang, X., Zhang, D., Lu, X., Xu, M., and Qiu, X. (2010). Mining pressure behavior characteristics of shallow buried coal seam under sandy gully slope. Coal Sci. Technol. 06, 18–22. doi:10.13199/j.cst.2010.06.24.wangxf.008
Xiao, G., and Yao, W. (2021). Mine pressure behavior law of shallow buried coal seam in valley terrain of Madiliang Coal Mine. J. Min. Strata Control Eng. 04, 96–103. doi:10.13532/j.jmsce.cn10-1638/td.20210610.001
Xu, J., Zhu, W., Wang, X., and Yi, M. (2009). Classification of key strata structure of overlying strata in shallow coal seam. Coal J. 34 (7), 865–870. doi:10.13225/j.cnki.jccs.2009.07.00
Xu, N., Zhang, J., Tian, H., Mei, G., and Ge, Q. (2016). Discrete element modeling of strata and surface movement induced by mining under open-pit final slope. Int. J. Rock Mech. Min. Sci. 88, 61–76. doi:10.1016/j.ijrmms.2016.07.006
Yang, T., Yang, Y., Zhang, J., Gao, S., and Li, T. (2021). Study on development law of mining-induced slope fracture in gully mining area. Adv. Civ. Eng. 2021, 1–9. doi:10.1155/2021/9990465
Yang, Z., Guo, R., and Yang, Y. (2020). Study on mine pressure behavior law and control of shallow buried deep fully mechanized caving face. Industrial Min. automation 09, 44–50. doi:10.13272/j.issn.1671-251x.2020060003
Yiouta-Mitra, P., and Sofianos, A. I. (2018). Μulti-jointed stratified hard rock roof analysis and design. Int. J. Rock Mech. Min. Sci. 106, 96–108. doi:10.1016/j.ijrmms.2018.03.021
Yu, J., Zhao, J., Yan, H., Lai, Q., Huang, R., Liu, X., et al. (2020). Deformation and failure of a high-steep slope induced by multi-layer coal mining. J. Mt. Sci. 17, 2942–2960. doi:10.1007/s11629-019-5941-6
Zhang, B., Liu, G., Li, Y., and Lin, Z. (2023a). Experimental study on the seepage mutation of natural karst collapse pillar (KCP) fillings over mass outflow. Environ. Sci. Pollut. Res. 30, 110995–111007. doi:10.1007/s11356-023-30230-3
Zhang, D., Huang, Z., Ma, Z., Yang, J., and Chai, J. (2023b). Research on similarity simulation experiment of mine pressure appearance in surface gully working face based on BOTDA. Sensors 23, 9063. doi:10.3390/s23229063
Zhang, D., Li, W., Lai, X., Fan, G., and Liu, W. (2017). Research progress on basic theory of water resources protection in coal mining in northwest China. Coal J. 42, 36–43. doi:10.13225/j.cnki.jccs.2016.5045
Zhang, J., Li, H., Yang, S., Wang, X., Bai, W., He, Y., et al. (2021). Study on mine pressure law and support adaptability of working face under very close gully terrain. Min. Res. Dev. 12, 48–51. doi:10.13827/j.cnki.kyyk.2021.12.025
Zhang, J., Long, J., Yang, T., Wang, B., and Zhou, F. (2019). Study on dynamic load mechanism of mining under gully in shallow coal seam. J. Min. Saf. Eng. 06, 1222–1227. doi:10.13545/j.cnki.jmse.2019.06.019
Zhang, Z., Xu, J., Wang, L., and Zhu, W. (2011). Study on the influence of gully slope angle on ground pressure of shallow coal seam working face. J. Min. Saf. Eng. 28, 560–565. doi:10.3969/j.issn.1673-3363.2011.04.011
Zhao, B., Guo, Y., Wang, W., and He, S. (2023). Impact of underground coal seam mining on stability and slippage of the loess slope. Sustainability 15, 6485. doi:10.3390/su15086485
Keywords: shallow coal seams, gully terrain, failure characteristic, key stratum, ground pressure law
Citation: Zhang J, Wang L, Yang T, Gao S, He Y and Wu J (2024) Study on overburden failure characteristics and ground pressure behavior in shallow coal seam mining underneath the gully. Front. Earth Sci. 12:1375979. doi: 10.3389/feart.2024.1375979
Received: 24 January 2024; Accepted: 20 February 2024;
Published: 06 March 2024.
Edited by:
Pengjiao Jia, Soochow University, ChinaCopyright © 2024 Zhang, Wang, Yang, Gao, He and Wu. This is an open-access article distributed under the terms of the Creative Commons Attribution License (CC BY). The use, distribution or reproduction in other forums is permitted, provided the original author(s) and the copyright owner(s) are credited and that the original publication in this journal is cited, in accordance with accepted academic practice. No use, distribution or reproduction is permitted which does not comply with these terms.
*Correspondence: Li Wang, MjEyMDMwNzcwMTdAc3R1Lnh1c3QuZWR1LmNu
Disclaimer: All claims expressed in this article are solely those of the authors and do not necessarily represent those of their affiliated organizations, or those of the publisher, the editors and the reviewers. Any product that may be evaluated in this article or claim that may be made by its manufacturer is not guaranteed or endorsed by the publisher.
Research integrity at Frontiers
Learn more about the work of our research integrity team to safeguard the quality of each article we publish.