- 1Guoneng Shendong Coal Group Co, Ltd, Ordos, China
- 2Emergency Science Research Institute, Chinese Institute of Coal Science, Beijing, China
- 3School of Environmental and Municipal Engineering, North China University of Water Resources and Electric Power, Zhengzhou, China
Hydraulic fracturing creates slots on the coal surface through the impact of high-pressure water jets, resulting in stress gradients in the surrounding coal, thereby inducing stress release and increasing gas extraction efficiency. It is an effective measure to prevent coal and gas outbursts. Numerical simulations demonstrate that high-pressure water jets generate slots in the coal, leading to stress gradients in the surrounding coal. These stress gradients drive the coal to move gradually towards the slots, thereby releasing stress. The stress unloading degree in the Y direction is greater than that in the X and Z directions. Damage occurs in the coal near the slots, causing a significant increase in the number of fractures within the coal, which improves gas extraction efficiency. The study reveals the variation in stress unloading of coal between hydraulic fracturing boreholes and extraction boreholes in adjacent positions. By cross-referencing various factors in numerical simulations, the extent of damage in different directions caused by slot formation under different factor combinations is determined. A mathematical model for the range of coal damage surrounding the slots is obtained through MATLAB fitting. The research findings provide references for on-site testing and applications of high-pressure water jet technology.
1 Introduction
The mechanism of coal and gas outbursts has been extensively studied in the academic community, leading to a comprehensive and widely accepted explanation known as the integrated action hypothesis (Taylor, 1852; Halbaum, 1899; Jou, 2000; Li and Lin, 2010). Conducting research and applications on the intensified unloading and permeability enhancement of low-permeability coal seams contributes to finding solutions and preventive measures for coal and gas outburst accidents (Liu et al., 2014; Zarrouk and Moore, 2009; Liu et al., 2011; Soliman, 1999).
Hydraulic fracturing exhibits significant effects on relatively hard coal formations. By subjecting the coal to high-pressure water jet impacts, slots are formed, leading to unloading and permeability enhancement in the surrounding coal, thereby increasing gas extraction efficiency. Therefore, hydraulic fracturing is an effective measure for preventing outbursts. Zheng et al. (2014) proposed two hydraulic fracturing methods, namely, “strong water rapid cutting” and “fine water slow cutting.” They investigated the effects of different fracturing methods on borehole jets through numerical simulations and field experiments. Li et al. (2014) conducted multiple experiments to explore the characteristics of pressure-flow during the transition process, clarifying the systemic energy characteristics and energy dissipation rules in this process. Yuan et al. (2013) addressed the difficulty of controlling transient pressure and flow during the operational transition of hydraulic fracturing systems. They tested the transient pressure and flow for different nozzle and valve core structural parameters, studying the impact of nozzle and valve core structural parameters on transient pressure and flow. Tang et al. (2012) conducted theoretical and numerical simulation studies on the effectiveness of hydraulic fracturing. Song et al. (2011) analyzed the stress changes induced by hydraulic fracturing in terms of stress variation angles. They employed theoretical analysis and numerical simulation methods, based on the permeation mechanics theory of planar radial flow, to conduct in-depth analysis and exploration of the permeability enhancement principles of hydraulic fracturing. Feng et al. (2001) conducted large-scale coal sample experiments to study the phenomenon of coal and gas outbursts during hydraulic fracturing. They investigated the outburst mechanism of coal and gas during hydraulic fracturing using a combination of experimental and simulation approaches. Zhang et al. (2013) studied the hydraulic fracturing process, proposing that slots formed through hydraulic fracturing in the coal release gas from the outburst coal seam, leading to the release of geological stress. Li et al. (2015) studied the permeability enhancement principle of the combined hydraulic fracturing and hydraulic fracturing techniques used during pre-drainage of coal seam gas. They conducted comparative experiments in the field. Duan et al. (2002) demonstrated that fracturing can increase gas extraction through experiments on the permeability enhancement of coal using large-scale hydraulic fracturing. Wu et al. (2009) analyzed the “bottleneck effect” caused by stress concentration around boreholes and investigated the influence of stress perpendicular to the slot plane, maximum principal stress, and the angle between the slot and stress on unloading through numerical simulations. Zhao and Feng, 2001 studied the methods to enhance the permeability of low-permeability coal seams under the solid-gas coupling effect through experiments. Wang et al. (2015) studied the spatial relationship between coal galleries and bottom drawing galleries, determined the reasonable layout area for bottom drawing galleries, and established a mathematical model for calculating the length of boreholes. Huang et al. (2011) investigated the generation of coal fractures during the hydraulic fracturing process through theoretical research. Long et al. (2011) developed a rapid coal cutting technique using combined deep hole pre-split blasting and high-pressure hydraulic fracturing. They optimized the borehole layout and hydraulic parameters of high-pressure hydraulic fracturing. Fu et al. (2014) studied a water hydraulic integrated technology based on regional gas control, including drilling, fracturing, pressurization, unloading, and injection processes.
Due to the complexity of the coal fracturing process, there are research gaps in understanding the unloading and destructive effects of slots formed by hydraulic fracturing on surrounding coal, as well as the range of damage in different directions. In this study, based on rock mechanics and elastoplastic mechanics, FLAC3D numerical simulation software was employed to investigate the stress-strain and fracture characteristics of the coal surrounding the slots formed by high-pressure water jets. Numerical simulations were conducted to analyze the mutual influence of unloading effects among multiple fracturing boreholes, and the synergistic unloading effects between slots were studied under different borehole arrangement scenarios. Finally, a mathematical model was established to describe the range of coal fracturing caused by hydraulic fracturing.
2 Influence law of slitting on the pressure relief of coal around the slit
2.1 Numerical model construction
The parameters of the numerical calculation model were set based on the actual conditions of Coal Seam No. 6 in Tanjiachong. A rectangular model was established, with a cylindrical outer layer surrounding the surrounding rock in a radial grid. Due to the far distance from the borehole and the predominance of stress effects, it is less prone to deformation and failure, thus a larger grid size was set. The numerical model units were set to 1 m in the X and Z-axes, and 0.05 m in the Y-axis. The inner surrounding rock was modeled as a cylindrical shell, considering its proximity to the borehole and the likelihood of deformation and failure. Therefore, a smaller grid size was used, with unit dimensions of 0.5 m in the X-axis, 0.05 m in the Y-axis, and 0.5 m in the Z-axis. The core part of the model was the borehole model, which had a cylindrical shape. The unit dimensions were set to 0.25 m in the X-axis, 0.05 m in the Y-axis, and 0.25 m in the Z-axis. The model was established with dimensions of 17 m in strike, 10 m in dip, and 17 m in height, and considering the hardware limitations, the slot depth was set to 1 m. The numerical calculation model consisted of a total of 53,600 elements. According to the site conditions, the strike direction of the working face was set as the X-axis, and the dip direction was set as the Y-axis. The material assignment parameters for the numerical model are shown in Table 1.
The model materials were treated as elastic, and the numerical simulation adopted the Mohr-Coulomb constitutive model. The calculation precision was set to 10−5. The shear modulus and bulk modulus in the material parameters were assigned with large values to prevent plastic failure during stress initialization. Finally, an initial stress field was applied to the model after stress initialization. The stress distribution after stress initialization is shown in Figure 1.
2.2 Stress variation law of coal mass around the slot
The basic parameters of the numerical model were set as follows: slot depth of 1m, slot width of 0.2m, and water jetting pressure of 30 MPa. For observation convenience, the model was sliced after the simulation, as shown in Figure 2. Panel a represents a slice perpendicular to the Y-axis, panel b represents a slice perpendicular to the Z-axis, and panel c represents a slice perpendicular to the X-axis. Panels a, b, and c show the stress distribution cloud maps in the respective directions. Panels d, e, and f are enlarged views of the research area, with the left side of the cloud maps removed. From the stress cloud maps, it can be observed that the stress distribution around the coal mass near the slot follows a trend of gradually decreasing stress in the X and Y directions. Additionally, a symmetric distribution can be observed, with the symmetry center located at the midpoint of the slot. The stress distribution around the slot shows a decreasing trend in the Y direction. Furthermore, a symmetric distribution can be observed, with the symmetry center also located at the midpoint of the slot. The difference from the stress distribution in the X direction is that it exhibits a “butterfly” shape on the cross-section. The stress distribution in the Z direction is similar to that in the X direction. It decreases gradually from near the slot towards the outside and exhibits a symmetric distribution centered at the midpoint of the slot. Outside the influence area of the slot until the model boundary, the coal mass remains unaffected by the slot. Additionally, from the stress cloud maps in panels d to f of Figure 2, it can be seen that the coal mass around the slot experiences positive stress, indicating that it is subjected to tensile stress. Furthermore, the decreasing trend of tensile stress is significant. This trend is attributed to the slot depth being much greater than its width due to hydraulic slot cutting, resulting in a higher degree of stress relief in the Y direction compared to the X and Z directions.
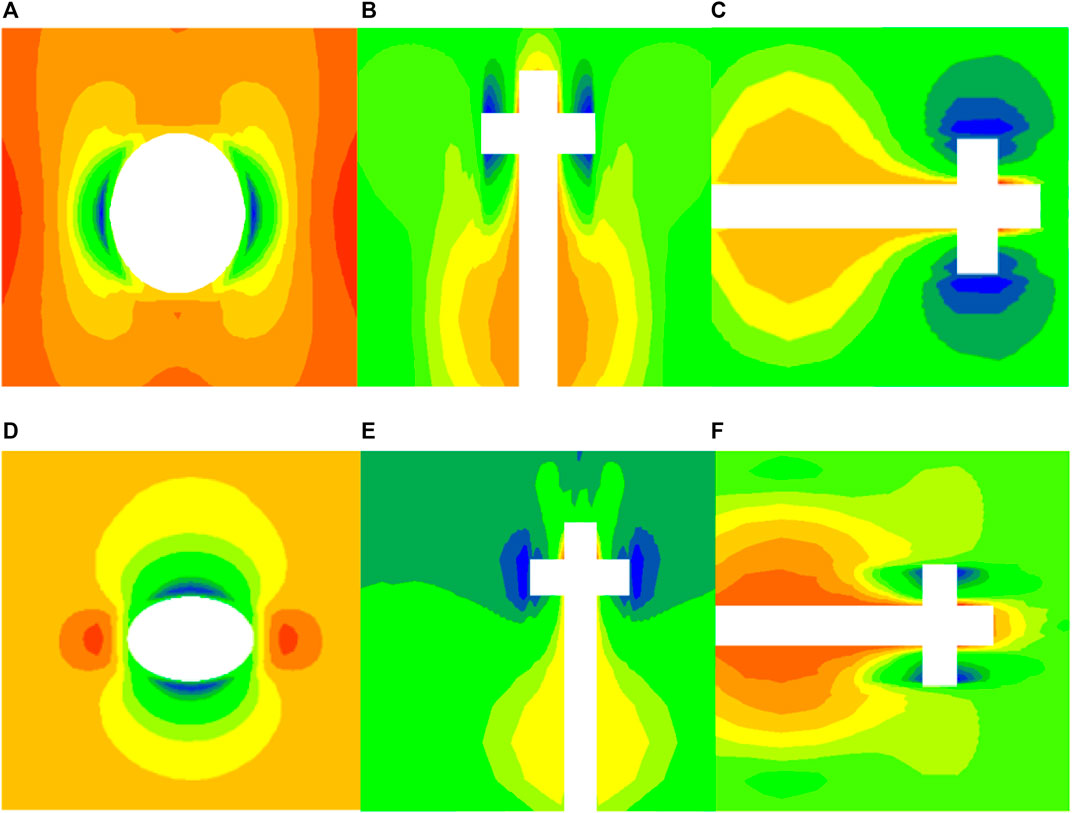
FIGURE 2. Stress distribution cloud of the single slotting: (A,D) Slice perpendicular to the Y-axis; (B,E) Slice perpendicular to the Z-axis; (C,F) Slice perpendicular to the X-axis.
For quantitative analysis, observation points were set at different distances from the center of the slot within the model to obtain the stress values at these points after numerical simulation. The corresponding stress concentration factors were calculated, as shown in Table 2. The table also reflects the same stress variation pattern as the cloud maps, that is, for the same distance from the center of the slot, the stress relief in the Y direction is much greater than in the X and Z directions.
The volumetric stress unloading variation of the coal mass in the X, Y, and Z directions corresponding to different stress concentration factors is shown in Figure 3. Within the entire range of stress concentration factors, for larger stress concentration factors, the corresponding volumetric stress unloading is smaller, consistent with the previously studied stress distribution patterns. Furthermore, when the stress concentration factor is relatively large, it can be observed from the graph that the stress concentration factor in the Y direction is greater than in the other two directions. This is due to the slot depth being much larger than the slot width, resulting in greater stress relief in the Y direction. Conversely, when the stress concentration factor is relatively small, the stress relief in the Y direction is smaller than in the X direction. This is because the hydraulic slot cutting produces a much larger slot depth in the X direction compared to the Y direction, leading to better stress relief in the X direction. From Figure 3, it can be seen that the rate of increase in volumetric stress unloading varies for each direction. As the stress concentration factor increases, the rate of decrease in volumetric stress unloading accelerates for each direction. When the stress concentration factor is large, the rate of decrease in volumetric stress unloading is slower in the Y direction compared to the other directions, indicating that the stress relief effect is better in the Y direction when the hydraulic slot width is much smaller than its depth.
After the implementation of hydraulic slotting measures, the stress at the edge of the slot where coal has been ejected is zero. From the edge to the deep part of the coal mass, the pressure gradient forces the coal to move. When the distance from the slot is far, the stress concentration factor is low, indicating that for coal closer to the slot, the slot plays a crucial role in stress relief, although the stress relief effect diminishes rapidly with increasing distance. Additionally, as analyzed earlier, due to the geometric characteristics of the slot, the stress concentration factor in the Y direction is greater than in the other directions, indicating that the stress relief effect in the Y direction is better.
2.3 Destruction law of coal mass around slots
After hydraulic slotting, based on the previous research, different stress distributions exist at different distances from the slot, resulting in varying stress concentration factors. When the stress exceeds the ultimate strength limit of the coal mass, the coal will be crushed and enter a plastic state. Coal in a plastic state is highly unstable and forms numerous cracks internally, while its strength rapidly decreases. The development and extension of internal cracks in the coal mass lead to a sharp increase in permeability, enabling gas migration channels within the coal mass to connect. As a result, the gas moves more quickly towards the slot space, and when gas drainage is conducted, it significantly improves the efficiency of gas extraction, ultimately eliminating the risk of outbursts. Compared to other areas, coal mass in a plastic state has minimal outburst risk because it possesses very little elastic potential energy and gas kinetic energy, lacking the conditions for dynamic phenomena to occur. The range of coal mass around the slot in the plastic state is shown in Figure 4.
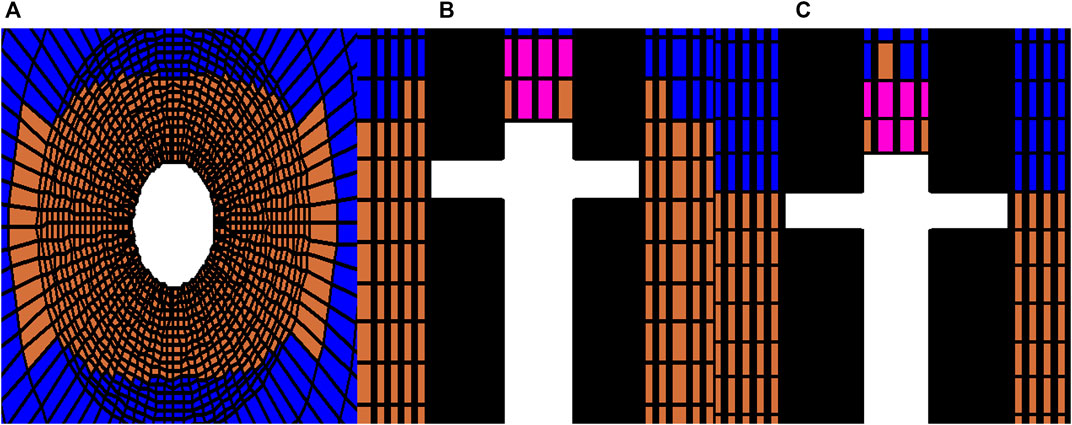
FIGURE 4. The map of plastic zone: (A) Slice perpendicular to the Y-axis; (B) Slice perpendicular to the Z-axis; (C) Slice perpendicular to the X-axis.
For observation convenience, the model was sliced after the simulation, as shown in Figure 4. Panel a represents a slice perpendicular to the Y-axis, panel b represents a slice perpendicular to the Z-axis, and panel c represents a slice perpendicular to the X-axis. From Figure 4A, it can be observed that the plastic zone distribution in the vertical direction (Y-axis) presents an elliptical shape, with a larger horizontal extent of plastic damage compared to the vertical extent. This is because the horizontal stress applied to the borehole is greater than the vertical stress, making the coal mass more susceptible to horizontal damage. From Figure 4B, it can be seen that the impact of the slot on the surrounding coal mass is much greater than that of the hydraulic slotting borehole, indicating that hydraulic slot cutting is more effective in gas extraction compared to solely drilling holes. Due to the much greater depth of the slot compared to its width, the area of the coal mass in the plastic failure zone is much larger in the direction parallel to the borehole than in the direction perpendicular to the borehole. From a three-dimensional perspective, the distribution of coal mass in the plastic zone is similar to that of the slot model, but with a larger diameter. As concluded earlier, the stress unloading in the Y direction is greater than in the other directions, and this can also be observed from the plastic zone diagram. The plastic zone in the Y direction is larger than in the other directions. By examining the stress unloading level at the boundary of the plastic zone, observation points were set at different distances from the center of the slot to determine the stress unloading at the boundary of the plastic zone. It can be concluded that the stress unloading is significant at the boundary of the plastic zone for all coal masses within the plastic zone. For practical application, the range of the slot’s influence can be determined by the radius of the plastic zone, avoiding blind areas in gas extraction and thus preventing outbursts.
3 The law of synergistic pressure relief between slits
This section investigates the mutual influence of stress relief under three different arrangements: parallel placement of slot cutting and gas extraction boreholes, parallel placement of slot cutting boreholes, and intersecting placement of slot cutting boreholes. The stress relief mutual interaction patterns in the case of multiple slot cutting boreholes are summarized. The numerical model parameters were set as follows: coal seam depth of 400 m, water jet pressure of 30 MPa, slot depth of 1 m, slot width of 0.2 m, and slot spacing of 3 m.
3.1 Influence of slotted drilling on gas drainage drilling
A new model was established with a distance of 3 m between the slot cutting boreholes and the gas extraction boreholes. Figure 5 shows the stress-strain cloud map of the coal mass between the slot cutting boreholes and the gas extraction boreholes, and Figure 6 shows the plastic zone distribution.
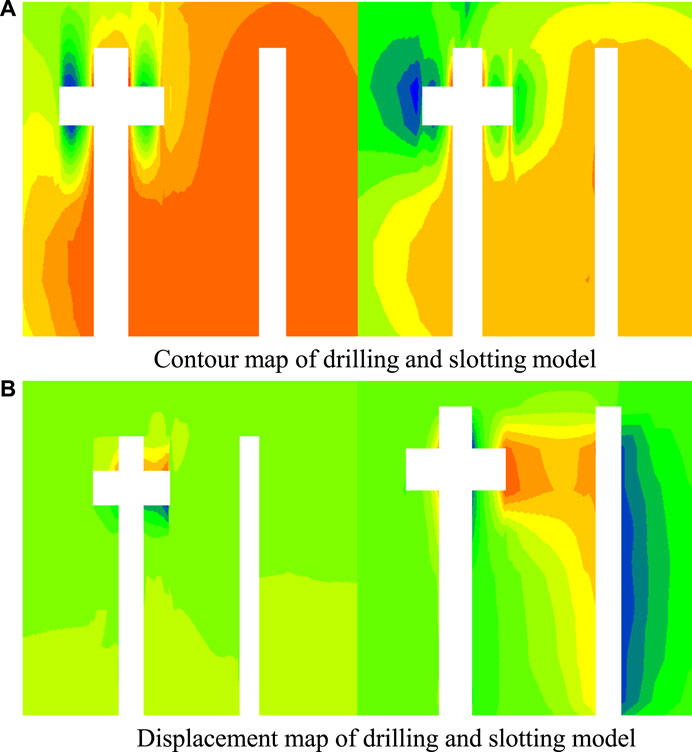
FIGURE 5. Contour and displacement map of drilling and slotting model: (A) Contour map of drilling and slotting model; (B) Displacement map of drilling and slotting model.
The distance between the center of the slot cutting borehole and the center of the gas extraction borehole was set to 3 m. As revealed by the previous numerical simulation, the gas extraction borehole falls within the effective range of hydraulic slot cutting. From the stress distribution cloud map, it can be observed that there is a small stress relief area around the gas extraction borehole after its construction. After hydraulic slot cutting, the coal mass on the left side of the gas extraction borehole falls within the effective range of hydraulic slot cutting, resulting in significant deformation and noticeable stress relief. The influence of hydraulic slot cutting gradually reduces the stress relief range in the X direction on the left side of the gas extraction borehole, while the changes in stress relief range in other directions are not significant. The comparison of stress relief effects on both sides of the gas extraction borehole is evident. The plastic damage zone map shows that the coal mass between the slot cutting borehole and the gas extraction borehole has undergone complete plastic deformation due to the effect of slot cutting. Therefore, when arranging slot cutting boreholes, if the distance between two boreholes is smaller than the effective stress relief range of hydraulic slot cutting, it is possible to construct only one hydraulic slot cutting borehole to effectively reduce the workload.
3.2 Influence of parallel arrangement between kerf boreholes for pressure relief
The previous section examined the influence of hydraulic slot cutting boreholes on the stress relief of adjacent gas extraction boreholes. This section simulates the mutual influence of stress relief in the coal seam when two hydraulic slot cutting boreholes are placed in parallel. A new model was established with a distance of 5 m between adjacent slot cutting boreholes. The stress variation cloud map of the coal mass is shown in Figure 7, and the plastic zone distribution is shown in Figure 8.
From the stress distribution cloud map, it can be observed that when two hydraulic slot cutting boreholes are placed horizontally with a distance of 5 m, the stress relief range gradually increases from the start of hydraulic slot cutting, and the displacement range of the coal mass also expands. The coal mass in the middle is affected by the deformation of the coal masses on both sides due to the synergistic stress relief effects. The stress relief range in the middle is greater than that of a single hydraulic slot cutting measure. The simulation was conducted for 5,000 steps, and after the numerical simulation, the coal mass between the horizontally adjacent hydraulic slot cutting boreholes has undergone complete stress relief.
From the plastic damage zone map, it can be observed that the coal mass is significantly affected by the hydraulic slot cutting measures on both sides, resulting in greater plastic damage compared to a single hydraulic slot cutting borehole. After the numerical simulation, the coal mass between the horizontally adjacent hydraulic slot cutting boreholes has completely undergone plastic deformation, confirming the synergistic stress relief effects when slot cutting boreholes are arranged in parallel.
3.3 Influence of pressure relief on cross-arrangement of kerf drilling
This section focuses on the mutual stress relief effects of intersecting hydraulic slot cutting boreholes. Two slot cutting boreholes were placed with a center-to-center distance of 5 m in the X-axis direction and 2 m in the Y-axis direction. The coal mass between the two boreholes is affected by the intersecting placement of the slot cutting boreholes. The stress cloud map is shown in Figure 9, and the plastic zone is shown in Figure 10.
From the stress distribution cloud map, it can be observed that when two hydraulic slot cutting boreholes are placed in an intersecting pattern, the coal mass between the two slots is subjected to stress relief not only in the X direction but also in the Y direction. When affected by stress relief from two different directions, the stress relief is greater than that of a single hydraulic slot cutting borehole. After the numerical simulation, the coal mass between the two hydraulic slot cutting boreholes has undergone complete stress relief.
From the plastic damage zone map, it can be seen that the coal mass is significantly affected by the two intersecting slots, resulting in greater plastic damage compared to a single hydraulic slot cutting borehole. After the numerical simulation, the coal mass between the two hydraulic slot cutting boreholes has completely undergone plastic damage due to the effects of the intersecting slot cutting measures. Therefore, the implementation of intersecting slot cutting boreholes can effectively increase the stress relief range and reduce the engineering workload.
4 Research on mathematical model of coal damage radius
The depth of the slot cutting has a greater influence on the plastic zone in the Y direction, while its impact on the X and Z directions is smaller. The width of the slot cutting has a greater influence on the plastic zone in the X and Z directions, while its effect on the Y direction is smaller. Therefore, a simplified mathematical model is derived based on the geometric characteristics of the slot. The failure radius of the disc-shaped slot cutting in each direction is given by:
Here,
The in-situ stress is represented by the coal seam depth
Substituting Eq. 2 into Eq. 1, the failure radius of the slot cutting in each direction can be determined as:
With the aid of this mathematical model, the failure range of the slot cutting in each direction can be quickly determined based on the slot parameters, providing reference for the layout of hydraulic slot cutting boreholes in practical applications.
5 Conclusion
A numerical model of coal mass subjected to high-pressure water jet slot cutting was established using FLAC3D software. The model parameters were determined based on the analysis of the regional coal seam conditions. The stress-strain behavior and failure characteristics of the surrounding coal mass after slot cutting were investigated, as well as the synergistic stress relief effects under different slot cutting layouts. The main conclusions are as follows.
(1) Numerical simulations of the stress variation in the coal mass surrounding the slot cutting revealed that the construction of hydraulic slot cutting in the coal seam resulted in the formation of slots through the impact of high-pressure water jets. This created stress gradients in the surrounding coal mass, driving the coal mass to gradually move towards the slots and release stress. Due to the significantly greater depth of the slots compared to their width, the stress relief in the Y direction was greater than in the X and Z directions. Plastic deformation zones were observed in the coal mass near the slots, indicating damage to the coal mass and an increase in the number of cracks, thereby enhancing gas extraction efficiency.
(2) The stress relief variations in the coal mass between adjacent hydraulic slot cutting boreholes and gas extraction boreholes were obtained. The synergistic stress relief effects between the slots can enhance the stress relief in the coal mass between them. When hydraulic slot cutting boreholes were arranged in a crossed pattern, the stress relief in the coal mass between the slots was more significant compared to parallel arrangements. Therefore, the use of crossed arrangements can appropriately increase the spacing between slots to improve engineering efficiency.
(3) The failure range of the coal mass surrounding the slots under different combination conditions was determined through simulation studies. Based on the simulation results, a mathematical model for the failure range of the coal mass surrounding the slots was obtained by curve fitting using MATLAB. This model can provide a reference for practical applications in the field.
Data availability statement
The original contributions presented in the study are included in the article/supplementary material, further inquiries can be directed to the corresponding author.
Author contributions
All authors listed have made a substantial, direct, and intellectual contribution to the work and approved it for publication.
Funding
The authors gratefully acknowledge the support provided by the National Natural Science Foundation of China (52204220, 52174188), and the China Coal Technology and Engineering Group Co., Ltd. (2022-QN001).
Conflict of interest
Authors LJ and JL were employed by the company Guoneng Shendong Coal Group Co, Ltd.
The authors declare that this study received funding from the China Coal Technology and Engineering Group Co., Ltd. The funder had the following involvement in the study: provide the numerical simulation software.
Publisher’s note
All claims expressed in this article are solely those of the authors and do not necessarily represent those of their affiliated organizations, or those of the publisher, the editors and the reviewers. Any product that may be evaluated in this article, or claim that may be made by its manufacturer, is not guaranteed or endorsed by the publisher.
References
Duan, K. L., Feng, Z. C., Zhao, Y. S., Zhao, Y. Q., and Yang, D. (2002). Testing study of methane drainage by bore and hydraulic-cutting seam from low permeability coal seam. J. China Coal Soc. 1, 50–53. doi:10.3321/j.issn:0253-9993.2002.01.011
Feng, Z. C., Kang, J., and Duan, K. L. (2001). Experimental and mechanism study of coal and gas burst in the process of hydraulic cutting seam. J. Liaoning Tech. Univ. Nat. Sci. 4, 443–445.
Fu, J. W., Fu, X. H., Sun, M. C., and Guo, Q. W. (2014). Gas control technology based on the hydraulic measures of "drilling cutting pressuring releasing and injecting. Saf. Coal Mines 5, 47–51. doi:10.13347/j.cnki.mkaq.2014.05.013
Halbaum, W. H. (1899). Discussion of J Gerrard's paper Instantaneous outbursts of fire-damp and coal. Broad Oak Colliery. Inst. Min. Eng. 10522, 258–265.
Huang, B. X., Cheng, Q. Y., and Liu, C. Y. (2011). Hydraulic fracturing theory of coal-rock mass and its technical framework. J. Min. Saf. Eng. 2, 167–173. doi:10.3969/j.issn.1673-3363.2011.02.001
Jou, M. (2000). Analysis of the stability of water-jet cutting with linear theory. J. Mater. Process. Technol. 104, 17–20. doi:10.1016/S0924-0136(00)00583-5
Li, X. H., Wang, X. C., and Kang, Y. (2014). Energy characteristic and dissipation in transient process of hydraulic cutting seams system in coal seam. J. China Coal Soc. 39, 1404–1408. doi:10.13225/j.cnki.jccs.2014.9014
Li, X. J., and Lin, B. Q. (2010). Status of research and analysis on coal and gas outburst mechanism. Coal Geol. Explor. 1, 7–13. doi:10.3969/j.issn.1001-1986.2010.01.002
Li, Z. F., Sun, D. F., Chen, J. F., Lei, H. B., and Xiao, S. Q. (2015). Application of permeability improving technology combined with hydraulic pressure fracturing and hydraulic slotting. Coal Sci. Technol. 10, 72–76. doi:10.13199/j.cnki.cst.2015.10.014
Liu, F. F., Huang, Y. Y., Xu, Q., Xie, G. M., Sun, J. l., and Wu, B. (2014). Influence of advance and retreat high-pressure water jet slotting on coal seam depressurization antireflection effect. Saf. Coal Mines 9, 165–168. doi:10.13347/j.cnki.mkaq.2014.09.049
Liu, J., Wang, H., Yuan, Z., and Xiaogang, F. (2011). Experimental study of pre-splitting blasting enhancing pre-drainage rate of low permeability heading face. Procedia Eng. 26, 818–823. doi:10.1016/j.proeng.2011.11.2242
Long, J. M., Li, W. S., Chen, J. F., Zhou, S. C., and Li, Z. F. (2011). Research on rapid seam opening of cross-cut technology in songzao mine. Coal Sci. Technol. 7, 35–38. doi:10.13199/j.cst.2011.07.41.longjm.013
Soliman, M. (1999). Use of oriented perforation and new gun system optimizes fracturing of high permeability, unconsolidated formations. Latin American and Caribbean Petroleum Engineering Conference. doi:10.2523/53793-MS
Song, W. Y., Wang, Z. F., and Tang, J. P. (2011). Principle of gas extraction by increasing permeability of coal seam with hydraulic cutting and its application. China Saf. Sci. J. 4, 78–82. doi:10.16265/j.cnki.issn1003-3033.2011.04.014
Tang, J. P., Yang, S. L., and Li, L. P. (2012). Numerical simulation of effects of different hydraulic cutting arrangement on pressure relief and gas outburst prevention. Chin. J. Geol. Hazard Control 1, 61–66. doi:10.16031/j.cnki.issn.1003-8035.2012.01.011
Taylor, T. J. (1852). Proofs of subsistence of the firedamp of coal mines in a state of high tension in situ. North Engl. Inst. Min. Mech. Eng. 1, 275–299.
Wang, N. B., Lin, B. Q., and Gao, Y. B. (2015). Optimized design and application of borehole slotting drilling through floor of high outburst seam. Coal Sci. Technol. 5, 62–66. doi:10.13199/j.cnki.cst.2015.05.016
Wu, H. J., Lin, B. Q., Yang, W., Yao, J., and Di, C. (2009). Numerical analysis of the pressure relief effect on slot at different initial stresses. J. Min. Saf. Eng. 2, 194–197.
Yuan, B., Kang, Y., and Li, X. H. (2013). Experimental study on transient characteristics of hydraulic cutting seams system in coal seam. J. China Coal Soc. 12, 2153–2157. doi:10.13225/j.cnki.jccs.2013.12.020
Zarrouk, S. J., and Moore, T. A. (2009). Preliminary reservoir model of enhanced coalbed methane (ECBM) in a subbituminous coal seam, Huntly Coalfield, New Zealand. Int. J. Coal Geol. 77, 153–161. doi:10.1016/j.coal.2008.08.007
Zhang, L. J., Lin, B. Q., and Gao, Y. M. (2013). Quick eliminating outburst technology of coal mine based on high-pressure hydraulic slotting process. Saf. Coal Mines 3, 64–66. doi:10.13347/j.cnki.mkaq.2013.03.014
Zhao, L., and Feng, Z. C. (2001). Testing study of improving seepage flow laws of low seepage coalbed by hydatic-cutting seams. J. TaiYuan Univ. Technol. 2, 109–111.
Keywords: water jet, hydraulic slitting, coal breaking characteristics, coordinated pressure relief, numerical simulation
Citation: Jia L, Sun Z, Lu J and Gu B (2023) Coal breaking characteristics of high pressure water jet and the law of coordinated pressure relief of slits. Front. Earth Sci. 11:1211117. doi: 10.3389/feart.2023.1211117
Received: 24 April 2023; Accepted: 05 June 2023;
Published: 14 June 2023.
Edited by:
Yingfeng Sun, University of Science and Technology Beijing, ChinaReviewed by:
Tengteng Li, Jiangsu University, ChinaFeng Du, China University of Mining and Technology, China
Kedi Wang, Tsinghua University, China
Copyright © 2023 Jia, Sun, Lu and Gu. This is an open-access article distributed under the terms of the Creative Commons Attribution License (CC BY). The use, distribution or reproduction in other forums is permitted, provided the original author(s) and the copyright owner(s) are credited and that the original publication in this journal is cited, in accordance with accepted academic practice. No use, distribution or reproduction is permitted which does not comply with these terms.
*Correspondence: Zuo Sun, c3VuenVvQG1haWwuY2NyaS5jY3RlZy5jbg==