- 1Guangxi Xinfazhan Communication Group Co., Ltd., Nanning, China
- 2Power China Zhongnan Engineering Corporation Limited, Changsha, China
- 3School of Civil Engineering, Changsha University of Science and Technology, Changsha, China
During the tunnel construction process using the drilling and blasting method, the induced blasting vibration always poses a great threat to the stability and safety of the adjacent tunnel supporting structure. To improve the efficiency and safety of tunnel blasting construction, the vibration propagation and peak particle velocity (PPV) distribution of the lining of an excavated tunnel were investigated during the blasting of an adjacent tunnel located in Guangxi province. The evolution process and distribution characteristics of the PPV of the lining of adjacent tunnels were monitored and analyzed. The results show that the maximum blasting vibration velocity of the lining of the adjacent tunnel can be shown as: PPVx > PPVz > PPVy; hence, the PPVx plays a significant role in the vibration of the adjacent tunnel. According to the tensile stress failure criterion, the PPV threshold was determined to be 12.7 cm/s in this study. To control the damage of surrounding rock induced by the blasting vibration, compound wedge-shaped cutting technology, stress wave dislocation superposition technology, and pre-splitting blasting technology were employed to reduce the impact of blasting vibration on the excavated tunnel.
1 Introduction
When a highway is constructed in a mountain area, the neighborhood tunnel is used frequently, and it is restricted by terrain conditions and environmental factors (Editorial department of China Journal of Highway and Transport, 2022). As the most widely used and efficient method for rock excavation in engineering practice, the drilling and blasting technique is widely used in mountain tunnel excavation (Chen et al., 2023; Liang et al., 2023). However, the dynamic load induced by blasting can easily damage the bearing capacity of the surrounding rock and supporting structure, leading to cracking, spalling, and even collapse of existing tunnel (Li et al., 2014; Xue et al., 2019; Liang et al., 2023). For instance, on 10 September 2020, during the construction at 540 m of the left tunnel of Leye Avenue in Leye County, Guangxi, a sudden rock collapse occurred on top of the tunnel. Nine workers who were working on the tunnel were trapped. The blasting vibration caused by the explosion always poses a great threat to the stability and safety of a tunnel structure (Zhou et al., 2020; Cheng et al., 2021; Yu et al., 2021; Xue et al., 2023). Consequently, the influence of blasting on the stability of adjacent tunnels has attracted wide attention.
At present, the research on the vibration characteristics of tunnel induced by blasting load can be divided into three categories: theoretical analysis, field test, and numerical analysis (Cao et al., 2016; Yang et al., 2022; Xu et al., 2023). (1) Theoretical analysis: the stress wave theory and tensile stress criterion are the theoretical basis for the analysis of vibration response of tunnels (Jiang and Zhou, 2012; Xie et al., 2016). Li et al. (2013) established the motion equation of an adjacent tunnel structure according to the propagation of the blasting stress wave and theory of energy conservation, calculating the stress distribution of a tunnel. They then proposed a theoretical method for predicting the dynamic response of this tunnel. Chen et al. (2017) employed the separation of variables method to solve the displacement potential function for the propagation of blasting-induced vibration waves. They discussed the peak particle velocity law in surrounding rock under different blast loads and surrounding rock parameters. Luo et al. (2022) derived the frequency domain expression and vibration velocity spectrum expression for the equivalent blasting load in porous media through theoretical analysis, and the propagation and attenuation of the primary frequency of blasting vibration of multiple cutting holes and caving holes in infinite rock mass were explored. (2) Field test: the vibration characteristics of the tunnel structure can be evaluated by the field blasting vibration monitoring test. Zhang et al. (2008) analyzed the blasting vibration characteristics of middle rock and concrete lining of bifurcation tunnel under different modes of cutting blasting. Fu et al. (2011) carried out vibration monitoring on the vault and side wall near a tunnel working face, analyzing the blasting vibration characteristic of the surrounding rock near the blasting source. Dang et al. (2018) arranged three-dimensional velocity sensors in the bottom foot and arch waist of an adjacent tunnel, obtaining the blasting vibration velocity of the lining. Lin (2011) carried out long-term blasting vibration monitoring, investigating the relationship between the PPV and charge, and the stability of the tunnel, which was disturbed by blasting vibration, was then assessed by the dynamic stress ratio method. (3) Numerical analysis: the numerical analysis method is being gradually applied to investigate tunnel engineering with the rapid development of computing technology. Kim et al. (2006) used the PFC 2D software to simulate the blasting of tunnel contour holes, and numerical models with different joint angles and joint spacing were established to analyze the failure mechanism of tunnel blasting, considering the angle and spacing of discontinuous interfaces. Liang et al. (2013) used the three-dimensional numerical analysis method to comprehensively analyze the influence of tunnel static stress and dynamic stress caused by blasting on the existing tunnel lining. Shin et al. (2011) studied the influence of blasting vibration on the performance of existing tunnels from the perspectives of vibration velocity, displacement, and stress of lining. Yu et al. (2014) used ABAQUS software to analyze the blasting vibration characteristics of adjacent tunnels on soft soil foundation, evaluating the safety of tunnels. Liu et al. (2020) established the three-dimensional numerical model using ANSYS/LS-DYNA, analyzing the distribution characteristics of vibration velocity and stress of adjacent tunnels; the relationship between vibration velocity and tensile stress of the tunnel lining was then established. Yang et al. (2015) conducted a three-dimensional numerical simulation study on rock damage evolution during the excavation of deeply buried tunnels using LS-DYNA software. The impact of practical millisecond delay blasting on damage extension was discussed, and the mechanisms of rock damage and evolution were then explored during the excavation process of deeply buried tunnels. Zhou et al. (2016) established a numerical model for an existing tunnel and an adjacent tunnel under construction at different spacing values, and the vibration response of the existing tunnel to the adjacent blasting construction was analyzed. Yang et al. (2019) employed a three-dimensional dynamic finite element model to validate field monitoring results, and the mechanisms that cause the difference between the surface and inside vibration were discussed in detail.
In general, the vibration criteria of tunnel blasting often simply refers to the degree of safety allowed for the PPV in the tunnel construction process. In the safety regulations for blasting, the allowable range is specified from 10 cm/s to 20 cm/s. However, as research advances, scholars have discovered a critical defect in that the peak vibration velocity is used as the unique criterion for assessing the safety of blasting-induced vibrations in many practical engineering cases (Chen et al., 2023). In fact, the vibration response of the tunnel is determined by objective factors, such as the blasting load and the tunnel’s properties (Ling et al., 2021; Song, 2022). It is difficult to control blasting disasters only by referring to the safety regulations for blasting or similar engineering experiences. Therefore, it is important to analyze the propagation characteristics of blasting vibration and the vibration response law of adjacent tunnels, and it is necessary to explore vibration control technology for reducing blasting vibration. Blasting disasters can be effectively controlled, and the safety construction efficiency can be improved.
2 Engineering condition and blasting vibration monitoring
2.1 Engineering condition
A double-line tunnel was excavated using drilling and blasting method in Guangxi. The maximum width of the excavation section is approximately 16.0 m. The minimum horizontal distance between the tunnels is also approximately 16.0 m. That can be considered a small clear distance tunnel. The layout of tunnels is shown in Figure 1. The tunnel passes through the mountain with thin covering soil, and the large area of bed rock is exposed. The surrounding rock is slightly or moderately weathered limestone. However, the rock is hard and complete, and the unconfined compression strength of part rock sample can exceed 100 MPa. Physical and mechanical tests were carried out on the moderately weathered limestone stones collected from the tunnel, and the main physical and mechanical parameters are summarized in Table 1.
The double-line tunnels were excavated step by step. The right line was excavated, followed by the left tunnel. Therefore, the right-line existing tunnel would be disturbed by the vibration caused by the blasting excavation of the left line. The left tunnel was excavated by the bench method, and the upper bench profile was excavated by smooth blasting. The width and height of the excavation section are 16.0 m and 6.6 m, respectively. The design of the excavation footage is 2.0 m, 2.5 m, and 3.0 m, respectively. Under different footage conditions, the charge of each blast holes increased slightly with the increase of footage, and the main parameters, such as the number of blast holes and delay time, were almost kept the same. The blasting parameters are listed in Table 2 and Figure 2, respectively. The type of hole was defined according to the function of the hole in the tunnel blasting. The symbols of MS1 and x# were used to represent the detonation time. The layout of the blasting holes is shown in Figure 2. Furthermore, to control the blasting vibration, the contour blasting was divided into two parts. The wall was blasted using the MS13, followed by the vault blasting at the MS15.
2.2 Monitoring scheme and technology
Based on the propagation theory of stress wave and the principle of blasting vibration monitoring, the blasting vibration monitoring test was carried out on the adjacent right-line tunnel. The layout of monitoring points is shown in Figure 3. Five monitoring points were arranged on the lining close to the blasting tunnel, which were numbered as 1#, 2#, 3#, 4#, and 5#, respectively. The vertical position of the monitoring points was 1.2 m away from the tunnel floor, and the distance between the monitoring points was 5 m. Monitoring point 3# was parallel to the working face of the excavating tunnel at the tunneling direction. Monitoring points 1# and 2# were located in front of the working face section. The area of the left tunnel parallel to those measuring points is not excavated yet. Monitoring points 4# and 5# were located at the rear of the working face section, where both the tunnels have been excavated, forming the middle rock. Three-dimensional velocity sensors were installed at each monitoring point to monitor the blasting vibration velocity on the lining of the right excavated tunnel.
In order to comprehensively consider the influence of rock characteristics, mountain structure, geological structure, and other factors on blasting vibration, the intelligent blasting vibration meters are shown in Figure 3, which is composed of the NUBOX-8016 acquisition equipment and TP3V-4.5 three-dimensional speed sensor. The measurement range was from 0.0047 cm/s to 35 cm/s, which can simultaneously measure the vibration signals in the X-horizontal radial, Y-horizontal tangential, and Z-vertical direction. In order to obtain accurate and detailed blasting vibration signals, the frequency, trigger level, acquisition time, and delay time of the instrument were set to 5 kHz, 0.1 cm/s, 1s, and 20 ms, respectively. The blasting vibration meter was installed before detonation, as shown in Figure 3, and this must be activated to await the trigger and store the vibration data when the vibration velocity exceeds 0.1 cm/s.
2.3 Monitoring results
Three kinds of field blasting tests with different maximum charge quantities of a single section were carried out. A total of 15 sets of data were obtained. The vibration velocity data of the monitoring points in the nearby tunnel are listed in Table 3.
Taking the blasting vibration results at the section of the ZK356 + 262 as an example, the curve of vibration velocity and time is shown in Figure 4. It can be seen that eight segments of the blasting vibration wave were monitored during the blasting. As the charge amount of the cutting section (MS1) is the maximum, the PPV is also significantly higher than other segments. Hence, the blasting vibration of the MS1 influence on the adjacent tunnel lining is discussed.
In order to analyze the vibration characteristics of the adjacent tunnel, the PPV induced by the maximum charge of 28.8 kg, 36.0 kg, and 42.0 kg have been drawn in Figure 5. The position 0 m on the abscissa represents the blasting working position, the positive value represents the unexcavated direction, and the negative value is the excavated direction. The PPV-x of the adjacent tunnel is the largest, followed by the PPV-z, and the PPV-y is the smallest; these results indicate that the horizontal vibration wave plays a significant role in the vibration of the adjacent tunnel. With the increase of explosive dosage, the PPV of the monitoring points gradually increased. In the longitudinal direction of the adjacent tunnel, the PPV at the blasting location is the largest, and then decays in both directions of the tunnel. However, when the distance from the monitoring section is the same, the PPV on the unexcavated side is slightly higher than that on the excavated side; these results indicate that the PPV attenuation rate on the unexcavated side is slower than that on the excavated side. Therefore, more attention should be paid to the blasting vibration on the unexcavated side.
In order to further analyze the difference of the vibration velocity attenuation characteristic between the unexcavated side and the excavated side of the adjacent tunnel, the fitting formula based on the detonation center distance (R) and the single maximum charge quantity (Q) was used to investigate the PPV of the adjacent tunnel. The fitting formula can be described as follows:
where R is the linear distance from the explosion source to the monitoring point (m), Q is the maximum charge quantity (kg), K and α are the blasting vibration coefficient, which is dependent on rock characteristics and geological conditions, and SD is the scale distance (m/kg1/3).
Taking the logarithms of formula (1), formula (2) can be expressed:
Let
As shown in Figure 6, according to Eqs 1–3, the PPV is fitted with the proportional distance, and the fitting results of the unexcavated side and excavated side are obtained.
The stress wave propagation attenuation parameters of the K and α are determined. The formula of vibration velocity attenuation (4) is described as follows:
The attenuation law of the blasting vibration in the excavating direction and excavating section is different. The values of α are 1.90 and 1.55, respectively. Those are relatively close, indicating that the geological conditions of the rock mass in the tests had tiny differences. The values of K are 487.8 and 340.3, respectively; the difference between the two values is obvious, indicating that the excavation state in the excavating direction and excavated section had a significant impact on the propagation and attenuation of the blasting vibration.
3 Safety criterion of blasting vibration
3.1 The relationship between PPV and tensile stress
During blasting excavation, the blasting disturbance generated by the blasting energy released will eventually propagate outward in the form of elastic waves. On the wave vibration surface, the relationship of the peak vibration velocity of the particle and stress can be expressed as
where
3.2 The PPV threshold
The damage of the adjacent tunnel lining can be judged according to the maximum tensile stress criterion. When the tensile stress on the lining exceeds the tensile strength of the concrete material, it can be judged that the lining structure has been destroyed.
According to the code for the design of concrete structures, the design value of the tensile strength of the C25 concrete is 1.27 Mpa. Considering the strain rate effect, the dynamic tensile strength improvement coefficient of rock is 1.24 (Jiang et al., 2023). The permitted dynamic tensile stress can be obtained using Formula (5), and then, the PPV threshold of the adjacent tunnel is calculated. Hence, the critical value is 12.7 cm/s in this study. In comparison with Table 1, the blasting vibration is smaller than that of the threshold value. Hence, it is necessary to employ useful technology to reduce the vibration.
4 Blasting vibration reduction technology
4.1 Compound wedge-shaped cutting technology
During tunnel blasting, the satisfactory cutting blasting effect can be realized using the single-stage large-wedge cutting blasting method (Zhong et al., 2022). However, the vibration intensity is very strong in the cutting blasting process as a great quantity of explosives is necessary. Moreover, the blasting effect is limited by the impact of stress clamping, and most of the energy is converted into vibration rather than being used to break the rock (Tian et al., 2019). Fortunately, as shown in Figure 7, the compound wedge-shaped cutting can reduce the charge as the additional free surface will be provided by the middle hole. When the middle hole is used to break the rock, the stress of the remaining cutting holes will be released, reducing the clamping effect. The explosive energy will be used to break the rock effectively as the energy of vibration is reduced.
4.2 Stress wave dislocation superposition
From the vibration monitoring analysis of the blasting test area, it could be found that the maximum vibration velocity was caused by the cutting holes. Hence, it is necessary to control the maximum single-segment charge of the cut blasting. As shown in Figure 8, if the stress wave generated by the single blasting hole can be superimposed on the staggered peaks, this can effectively decrease the strength of the seismic waves resulting from the superposition of the total charge of the blasting hole. Fortunately, with the development of electronic detonator technology, the precision of the hole initiation time can be controlled in 1 m (Iwano et al., 2020). The delay time of each cutting blasting hole can be controlled to control the blasting effect.
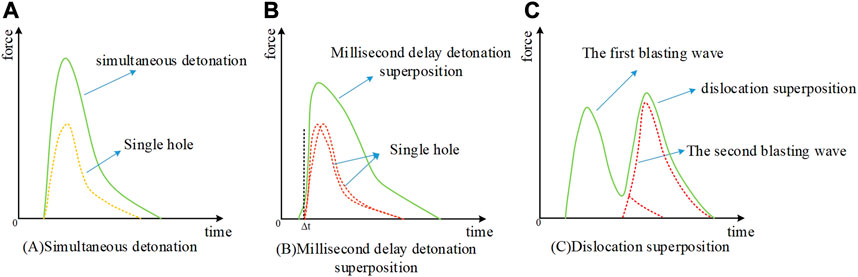
FIGURE 8. Stress wave dislocation superposition mechanism. (A) Simultaneous detonation, (B) Millisecond delay detonation superposition and (C) Dislocation superposition.
4.3 Pre-splitting blasting
The propagation of blasting seismic waves mainly depended on the wave impedance of the medium. As shown in Figure 9, when the tunneling contour is formed with pre-splitting crack, and the blasting vibration wave reaches the crack, the vibration wave will generate reflection and transmission. The tensile wave will return to the blast zone, and a portion of the damped compression wave will be transmitted. The transmitted wave intensity will be weakened, reducing the vibration behind the pre-splitting crack.
4.4 Analysis of damping effect
The blasting vibration reduction technology is provided and used in the blasting control area. When the compound wedge-shaped cutting technology is used, the blasting vibration can be reduced by about 15%. If the delay time of the cutting blasting hole is set from 3 m to 5 m, the blasting vibration can be reduced by about 20%. When the pre-splitting holes are arranged at the wall of the tunnel, the blasting vibration can be reduced by about 20%–30%. This can reach 60% if the all the contour holes are set as pre-splitting holes. In engineering practice, the blasting vibration must be controlled to reduce the risk. It is necessary to analyze the engineering condition and technical level so that the appropriate technical methods can be employed.
5 Conclusion
In this article, the vibration of blasting excavation of a double-line tunnel project in Guangxi is investigated. The blasting vibration propagation is analyzed by field monitoring. The relationship between the maximum stress and the PPV is analyzed, and a reasonable PPV threshold is proposed. Then, blasting vibration reduction technology is provided. The research results have been successfully applied to guide field construction.
(1) The blasting vibration of the adjacent tunnel can be shown as: PPVX > PPVZ > PPVY, in which the PPVX plays a significant role in the vibration of the adjacent tunnel.
(2) When the distance from the blasting center to the monitoring points is the same, the PPV located at the unexcavated side is slightly higher than that of the excavated side, which indicates that the attenuation rate of the PPV of the unexcavated side is slower than that of the excavated side. Attention should be paid to the blasting vibration of the unexcavated side.
(3) The relationship between the maximum tensile stress and PPV of the adjacent tunnel lining is analyzed. According to the ultimate tensile stress failure criterion, the PPV threshold of the adjacent tunnel is determined to be 12.7 cm/s in this study.
(4) Compound wedge-shaped cutting technology, stress wave dislocation superposition technology, and pre-splitting blasting technology are employed to reduce the blasting vibration. The blasting vibration can be reduced from 20% to 60%. The blasting vibration must be controlled to reduce the risk. It necessary to analyze the engineering condition and technical level so that the appropriate technical methods can be employed.
Data availability statement
The original contributions presented in the study are included in the article/supplementary material, further inquiries can be directed to the corresponding authors.
Author contributions
Literature search and manuscript writing: ZQ, YZ, and LC. Monitoring design: HC, LC. Field monitoring: WJ. Verification: ZQ, LZ. Writing–first draft preparation: ZQ, YZ, and LC. Writing–review and editing: HX, LC. All authors contributed to the article and approved the submitted version.
Funding
This research is funded by the national key research and development program (2022yfc2903901), the national natural science foundation of China (52004036, 52104111, 52004080), the national natural science foundation of Hunan province (2021jj40572, 2021jj40579), the key laboratory of advanced engineering materials and structural mechanical behavior and intelligent control for universities in Hunan province (19ka01), the projects of Hunan province department of education (21c0198), and the key science and technology project of Guangxi transportation industry (2020–24).
Conflict of interest
Authors ZQ and WJ were employed by the company Guangxi Xinfazhan Communication Group Co., Ltd. Author YZ was employed by the company Power China Zhongnan Engineering Corporation Limited.
The remaining authors declare that the research was conducted in the absence of any commercial or financial relationships that could be construed as a potential conflict of interest.
Publisher’s note
All claims expressed in this article are solely those of the authors and do not necessarily represent those of their affiliated organizations, or those of the publisher, the editors and the reviewers. Any product that may be evaluated in this article, or claim that may be made by its manufacturer, is not guaranteed or endorsed by the publisher.
References
Cao, W., Li, X., Tao, M., and Zhou, Z. (2016). Vibrations induced by high initial stress release during underground excavations. Tunn. Undergr. Space Technol. 53, 78–95. doi:10.1016/j.tust.2016.01.017
Chen, S.-h., Hu, S.-w., Zhang, Z.-h., and Wu, J. (2017). Propagation characteristics of vibration waves induced in surrounding rock by tunneling blasting. J. Mt. Sci. 14 (12), 2620–2630. doi:10.1007/s11629-017-4364-5
Chen, L., Zhou, Z.-L., Gao, S., Cai, X., Wang, S-F., Nie, S-L., et al. (2023). Research status and prospects of blasting excavation of tunnel under high stress condition. J. Central South Univ. Sci. Technol. 54 (3), 849–865. doi:10.11817/j.issn.1672-7207.2023.03.006
Cheng, R., Chen, W., Hao, H., and Li, J. (2021). A state-of-the-art review of road tunnel subjected to blast loads. Tunn. Undergr. Space Technol. 112, 103911. doi:10.1016/j.tust.2021.103911
Dang, V., Dias, D., Do, N., and Vo, T. (2018). Impact of blasting at tunnel face on an existing adjacent tunnel. Int. J. Geomate 15 (47), 22–31. doi:10.21660/2018.47.04640
Editorial department of China Journal of Highway and Transport (2022). Review on China’s traffic tunnel engineering research: 2022. China J. Highw. Transp. 35 (4), 1–38. doi:10.19721/j.cnki.1001-7372.2022.04.001
Fu, H., Zhao, Y., Xie, J., and Hou, Y. (2011). Study of blasting vibration test of area near tunnel blasting source. Chin. J. Rock Mech. Eng. 30 (02), 335–340.
Iwano, K., Hashiba, K., Nagae, J., and Fukui, K. (2020). Reduction of tunnel blasting induced ground vibrations using advanced electronic detonators. Tunn. Undergr. Space Technol. 105, 103556. doi:10.1016/j.tust.2020.103556
Jiang, N., and Zhou, C. (2012). Blasting vibration safety criterion for a tunnel liner structure. Tunn. Undergr. Space Technol. 32, 52–57. doi:10.1016/j.tust.2012.04.016
Jiang, W., Gao, Q.-D., Wang, Y.-Q., Yang, Y., Fan, Y., and Leng, Z. (2023). Study on blast vibration characteristics and its isolation scheme selection of the existing tunnel in multi-arch tunnel without middle wall. Chin. J. Geotechnical Eng. Available at: http://kns.cnki.net/kcms/detail/32.1124.TU.20230115.1144.009.html.
Kim, S., Jeong, W., Jeong, D., and Seok, J. (2006). Numerical simulation of blasting at tunnel contour hole in jointe rock mass. Tunn. Undergr. Space Technol. 21 (3), 306–307. doi:10.1016/j.tust.2005.12.162
Li, J. C., Li, H. B., Ma, G. W., and Zhou, Y. (2013). Assessment of underground tunnel stability to adjacent tunnel explosion. Tunn. Undergr. Space Technol. 35, 227–234. doi:10.1016/j.tust.2012.07.005
Li, S., Li, K., Lei, G., and Sun, G. (2014). Study of blasting vibration and deformation control for metro construction beneath existing metro tunnel in short distance. Rock Soil Mech. 35 (S2), 284–289. doi:10.16285/j.rsm.2014.s2.048
Liang, Q., Li, J., Li, D., and Ou, E. (2013). Effect of blast-Induced vibration from new railway tunnel on existing adjacent railway tunnel in xinjiang, China. Rock Mech. Rock Eng. 46 (1), 19–39. doi:10.1007/s00603-012-0259-5
Liang, Y. J., Gao, S., and Chen, L. (2023). Research on deformation analysis and treatment technology of shallow buried tunnels in karst areas. J. Transp. Sci. Eng. 39 (2), 49–54. doi:10.16544/j.cnki.cn43-1494/u.20230403001
Lin, D. (2011). The mitigation negative effect of tunnel-blasting-induced vibrations on constructed tunnel and buildings. J. Coal Sci. Eng. (China) 17 (1), 28–33. doi:10.1007/s12404-011-0106-4
Ling, T., OuYang, X., Liu, J., and Zhang, S. (2021). Dynamic response analysis of double tunnel lining under blasting vibration. J. Transp. Sci. Eng. 37 (02), 20–27. doi:10.16544/j.cnki.cn43-1494/u.2021.02.004
Liu, Z., Jiang, N., Sun, J., Xia, Y., and Lyu, G. (2020). Influence of tunnel blasting construction on adjacent highway tunnel: a case study in wuhan, China. Int. J. Prot. Struct. 11 (3), 283–303. doi:10.1177/2041419619888936
Luo, Y., Gong, H., Qu, D., Zhang, X., Tao, Y., and Li, X. (2022). Vibration velocity and frequency characteristics of surrounding rock of adjacent tunnel under blasting excavation. Sci. Rep. 12 (1), 8453. doi:10.1038/s41598-022-12203-7
Shin, J. H., Moon, H. G., and Chae, S. E. (2011). Effect of blast-induced vibration on existing tunnels in soft rocks. Tunn. Undergr. Space Technol. 26 (1), 51–61. doi:10.1016/j.tust.2010.05.004
Song, H. (2022). Blasting vibration control technology based on blasting velocity attenuation law. J. China&Foreign Highw. 42 (02), 188–193. doi:10.14048/j.issn.1671-2579.2022.02.035
Tian, X., Song, Z., and Wang, J. (2019). Study on the propagation law of tunnel blasting vibration in stratum and blasting vibration reduction technology. Soil Dyn. Earthq. Eng. 126, 105813. doi:10.1016/j.soildyn.2019.105813
Xie, L. X., Lu, W. B., Zhang, Q. B., Jiang, Q., Wang, G., and Zhao, J. (2016). Damage evolution mechanisms of rock in deep tunnels induced by cut blasting. Tunn. Undergr. Space Technol. 58, 257–270. doi:10.1016/j.tust.2016.06.004
Xu, M., Li, X., Xu, K., Liu, T., Zhang, Y., and Yang, T. (2023). Influence of the spatial distribution of underground tunnel group on its blasting vibration response. Undergr. Space 10, 248–268. doi:10.1016/j.undsp.2022.10.006
Xue, F., Xia, C., Li, G., Jin, B., He, Y., and Fu, Y. (2019). Safety threshold determination for blasting vibration of the lining in existing tunnels under adjacent tunnel blasting. Adv. Civ. Eng. 2019, 1–10. doi:10.1155/2019/8303420
Xue, Y., Ranjith, P., Gao, F., Zhang, Z., and Wang, S. (2023). Experimental investigations on effects of gas pressure on mechanical behaviors and failure characteristic of coals. J. Rock Mech. Geotechnical Eng. 15, 412–428. doi:10.1016/j.jrmge.2022.05.013
Yang, J., Lu, W., Hu, Y., Chen, M., and Yan, P. (2015). Numerical simulation of rock mass damage evolution during deep-buried tunnel excavation by drill and blast. Rock Mech. Rock Eng. 48 (5), 2045–2059. doi:10.1007/s00603-014-0663-0
Yang, J., Cai, J., Yao, C., Li, P., Jiang, Q., and Zhou, C. (2019). Comparative study of tunnel blast-induced vibration on tunnel surfaces and inside surrounding rock. Rock Mech. Rock Eng. 52 (11), 4747–4761. doi:10.1007/s00603-019-01875-9
Yang, J., Wu, Z., Sun, W., Yao, C., and Wang, Q. h. (2022). Numerical simulation on radiation and energy of blast-induced seismic waves in deep rock masses. J. Central South Univ. 29 (2), 645–662. doi:10.1007/s11771-022-4908-x
Yu, H., Yuan, Y., Yu, G., and Liu, X. (2014). Evaluation of influence of vibrations generated by blasting construction on an existing tunnel in soft soils. Tunn. Undergr. Space Technol. 43, 59–66. doi:10.1016/j.tust.2014.04.005
Yu, W.-j., Li, K., Liu, Z., An, B., Wang, P., and Wu, H. (2021). Mechanical characteristics and deformation control of surrounding rock in weakly cemented siltstone. Environ. Earth Sci. 80 (9), 337. doi:10.1007/s12665-021-09626-2
Zhang, Q., Li, L., Li, S., Ding, W., and Hong, W. (2008). Experimental study of blasting dynamic vibration of closely adjacent tunnels. Rock Soil Mech. 29 (10), 2655–2660+2666. doi:10.16285/j.rsm.2008.10.012
Zhong, H., Liang, Y., Lan, W., Gao, S., and Liu, X. (2022). Research on compound wedge-shaped cutting in mountain hard rock tunnel. J. Transp. Sci. Eng. 38 (03), 72–78+106. doi:10.16544/j.cnki.cn43-1494/u.2022.03.006
Zhou, Y., Wang, S., Wang, J., Wen, J., and Chen, L. (2016). Vascular endothelial growth factor plasma levels before and after treatment of retinopathy of prematurity with ranibizumab. Chem. Eng. Trans. 55, 31–36. doi:10.1007/s00417-015-2996-0
Keywords: blasting vibration, propagation characteristics, vibration control, cutting technology, pre-splitting blasting
Citation: Qin Z, Zhao Y, Chen L, Cao H, Zeng L, Jiao W and Xu H (2023) Propagation characteristics and control technology of blasting vibration in neighborhood tunnel. Front. Earth Sci. 11:1204450. doi: 10.3389/feart.2023.1204450
Received: 12 April 2023; Accepted: 01 August 2023;
Published: 24 August 2023.
Edited by:
Xu Chang, Huaqiao University, ChinaCopyright © 2023 Qin, Zhao, Chen, Cao, Zeng, Jiao and Xu. This is an open-access article distributed under the terms of the Creative Commons Attribution License (CC BY). The use, distribution or reproduction in other forums is permitted, provided the original author(s) and the copyright owner(s) are credited and that the original publication in this journal is cited, in accordance with accepted academic practice. No use, distribution or reproduction is permitted which does not comply with these terms.
*Correspondence: Hongtao Cao, Y2FvQHN0dS5jc3VzdC5lZHUuY24=; Wencan Jiao, andjXzUyNUAxNjMuY29t