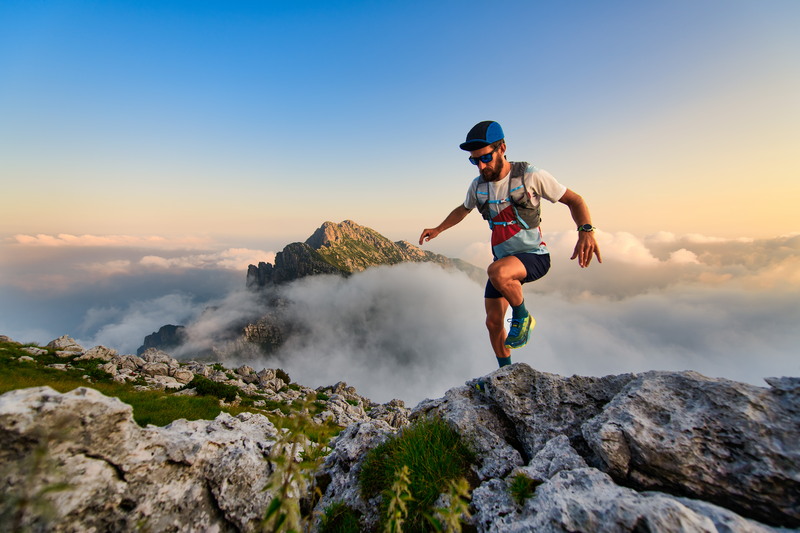
95% of researchers rate our articles as excellent or good
Learn more about the work of our research integrity team to safeguard the quality of each article we publish.
Find out more
ORIGINAL RESEARCH article
Front. Earth Sci. , 14 September 2022
Sec. Geochemistry
Volume 10 - 2022 | https://doi.org/10.3389/feart.2022.983442
This article is part of the Research Topic Mechanisms and Applications of Chemical Techniques for Effective Development of Unconventional Reservoirs View all 13 articles
CO2 injection is a promising method for low-permeability reservoirs. CO2 is much easier to inject underground compared with water. The solubility of CO2 in oil decreases the oil density and viscosity, leading to an enhancement of the oil recovery. CO2 flooding could achieve the dual purpose of developing oil effectively and reducing greenhouse gas. Therefore, this technique has both economic and social benefits and is an essential technology for achieving green development. Natural fractures are widely developed in low-permeability reservoirs, and artificial fractures are often used to improve oil development. These fractures have a significant influence on flow patterns during CO2 flooding. In addition, fractures are also one of the key factors of CO2 channeling. Therefore, the influence of fractures on CO2 flooding pressure distribution, fluid composition, and displacement efficiency needs to be studied. In this work, a CO2 flooding experiment was implemented to test the pressure distribution and outlet composition changes during CO2 flooding under different fracture lengths and apertures. The experiment shows that a long and wide fracture could effectively reduce the injection-production pressure difference. However, fractures also had a negative effect on oil development. Fracture length and aperture had a significant effect on the gas phase composition at the outlet, but had little effect on the oil phase composition.
The development of low-permeability reservoirs and tight-oil reservoirs is often unsatisfactory due to problems such as small pore radius and low permeability. The poor flow conditions lead to difficulties in water injection development. Laboratory experiments and field applications have shown that the injection of CO2 into low-permeability reservoirs has a significant ability to enhance oil. In CO2 injection, oil mixed with CO2 has much increased mobility and reduces the interfacial tension. Therefore, CO2 flooding could greatly improve oil recovery. CO2 injection has been recognized as the second-largest enhanced oil recovery (EOR) process in the world.
CO2 has attracted the attention of experts around the world because of its excellent oil displacement capacity. There is a long research history on CO2 flooding in theory research, and it has been frequently used in applications in the field. Since the 1950s, a large amount of theoretical research and field application research has been carried out (Guo et al., 2002; Jiang et al., 2010; He et al., 2011). In the 1970s, the application of CO2 flooding made great progress (Cao et al., 2020). China started research on CO2 flooding theory and application in the 1960s. This technology has not been widely promoted in China because of the lack of CO2.
Global warming is a major issue for the world, as increased amounts of CO2 and other greenhouse gases in the atmosphere have resulted in increases in sea levels and changes in the climate. Many countries have proposed policies to reduce carbon emissions. In CO2 flooding, the injected CO2 is trapped underground, and it is an important way to reduce carbon emissions. Therefore, CO2 flooding has the dual purpose of oil recovery and CO2 reduction, and has broad application prospects.
Laboratory experiments of CO2 flooding are applied to support the implementation of CO2 flooding in the field (Xie, 1991; Cheng et al., 2008; Ma et al., 2020). Many experts have made great contributions in this field. The influence of CO2 on the viscosity and volume of oil was studied by Hao et al. (2005) through laboratory experiments, and the mechanism of CO2 EOR was researched. Miller and Jones studied the effect of CO2 on the physical properties of heavy oil (Miller and Jones, 1981; Sankur and Emanuel, 1983). Gao et al. (2020) analyzed the influence of development parameters on the CO2 EOR through experiments (Gao et al., 2020). Wang et al. (2016) discussed periodic CO2 injection through experiments in low-permeability porous media, and the influence of injection slug and velocity is revealed in their work (Wang et al., 2016). The differences between miscible flooding and immiscible flooding were compared by Zhao et al. (2018), and field experiments were conducted to support the research. The above works mainly focus on the mechanism of CO2 EOR, and the effect of fractures was not studied.
Oil development of low permeability and tight reservoirs is often affected by fractures. On the one hand, by fracturing the injection well, the injection rate of CO2 is improved and the reservoir energy can be recovered in a short time. On the other hand, the oil production well is usually fractured to improve the production rate in low-permeability reservoirs. As a high-conductivity channel, fractures are closely related to important parameters such as the swept volume and gas channeling during reservoir development. It is necessary to carry out experimental research on the effect of fractures on CO2 flooding. In order to explore the effect of fractures on CO2 flooding, Huang used cores with annulus to represent fractures (Huang et al., 2008). An experimental study of CO2 huff and puff was conducted, showing that fractures had a great influence on the CO2 huff and puff. In order to optimize the injection methods of CO2 flooding after water flooding, CO2 compound flooding experiments with single fracture and complex fracture in a five-spot well pattern were implemented, respectively (Shi et al., 2021). The physical model of fracture radial flow was used in their work. To develop fractured tight reservoirs effectively, Wang (2017) designed a CO2 flooding experiment to analyze pressure transfer in fractured porous media (Wang, 2017). In this experiment, the fractures were formed with different apertures. By comparing the CO2 flooding results with the control experiment, it was shown that the gas channeling caused by fracture was the key factor in the production of oil in the matrix. Existing experiments show that fractures have a significant impact on the development of CO2 flooding in low-permeability and tight reservoirs. However, further research is required on pressure distribution, fluid composition, and fluid displacement.
In this study, artificial cores were made according to the formation parameters in Shengli Oilfield. Fracture length and aperture are the primary factors affecting CO2 flooding. Therefore these fractures were made with different lengths and apertures. During CO2 flooding, the pressure along the core and the components at the outlet was recorded. Then the influence of fractures on CO2 flooding was investigated.
The experimental equipment contained UQT-120-70 high temperature and high pressure long-core test system, Bruker 450 GC, and Agilent 7890A GC as the main components. The pressure was measured with SENEX DG2113-C-70/B. The pressure measurement signal was automatically recorded by the computer data acquisition system and was set to be recorded every 2 min. The cores used in this experiment were artificially produced according to the formation parameters of Shengli Oilfield. After cleaning and drying, the basic parameters of the cores are shown in Table 1. The fractures were made by wire cutting, and quartz sand was used as a filler to support the fractures as shown in Figure 1.
FIGURE 1. Part of cores used in this experiment. (A) Cores before fracture and (B) cores after being fracture.
Since it is difficult to obtain a single core longer than 0.5m, the commonly used method is splicing conventional cores in a certain arrangement. Filter paper was applied to connect short cores to eliminate the terminal effect. The arrangement of each core was as follows.
1) The harmonic mean permeability
where
2) The harmonic mean permeability of the remaining n-1 cores
3) The long cores were obtained using the above method.
Four kinds of cores were considered in this experiment: the control group (without fracture in cores), a core with fracture length 10 cm and aperture 0.05mm, a core with fracture length 20 cm and aperture 0.05 mm, and a core with fracture length 20 cm and aperture 0.1 mm. By carrying out CO2 flooding experiments on different types of cores, the influences of fracture length and aperture on the pressure distribution, composition, and displacement effect during CO2 flooding were studied. The fluid used in this experiment was obtained by compounding the oil and gas samples from the surface separator of a well in the block.
The experimental steps mainly included the following: ① Firstly, the core was cleaned with petroleum ether and dried with nitrogen, then dead oil was injected with a pump to fully saturate the core, and keep the pressure and temperature at formation conditions for some time. After the core was fully saturated, the amount of dead oil was recorded. ② The pressure and temperature at the outlet were set to 20 MPa and 50°C, respectively. Then the prepared live oil was used to displace the dead oil in the core until the gas-oil ratio at the inlet and outlet was the same to ensure that the core was completely saturated with live oil. ③ Industrial-purity CO2 (99.9%) was injected at a constant rate to displace the oil in the core until no more oil was driven out at the outlet. The data record changed over time, including oil production, gas production, pressure at the measuring points, etc. The produced gas and oil samples were collected for chromatographic analysis. ④ After each experiment was finished, the cores were cleaned, dried with nitrogen, evacuated with a vacuum pump, and steps ① to ③ were repeated for the next set of experiments.
Firstly, the CO2 flooding experiment in cores without fractures was carried out as a control experiment. The measuring points were set every 10 cm from the injection point. The outlet pressure remained unchanged, and the CO2 was injected at a constant rate of 0.2 ml/min. The value of the pressure at each measuring point was recorded, as shown in Figure 2.
The pressure at each measuring point gradually decreased with displacement time before CO2 broke through the core. It indicated that in the initial stage of gas injection, high pressure was required to generate a pressure difference between the inlet and outlet. Stable flooding was formed after the experiment had been carried out for a period of time. At this stage, the required injection pressure at the inlet was decreased. The flow resistance was decreased by reducing the unswept area. Therefore the required pressure became smaller with CO2 flooding. The gas-oil ratio in Figure 3 shows that the CO2 broke through the core at 0.77 PV. Before CO2 was detected at the outlet, it can be seen from Figure 2 that the pressure difference was significantly smaller than the initial pressure difference. It shows that, after the gas broke through, the constant-rate flooding could be achieved with a low pressure difference.
Two kinds of cores were considered in this case. One contained a 10-cm fracture and the other a 20-cm fracture. The aperture of both fractures was 0.05 mm. The measuring points were set every 10 cm from the injection point. The outlet pressure remained unchanged, and the CO2 was injected at a constant rate of 0.2 ml/min. The values of the pressure at each measuring point were recorded, as shown in Figure 4. The curves of gas oil ratio for these two cases are shown in Figure 5.
FIGURE 4. Pressure distribution in cores with different fracture lengths. (A) Length of fracture 10 cm and (B) length of fracture 20 cm.
FIGURE 5. Gas oil ratio at outlet with different fracture lengths. (A) Length of fracture 10 cm and (B) length of fracture 20 cm.
Compared with the control experiment, the required injection pressure of the cores with fracture was smaller. Similarly, before CO2 was detected at the outlet, the pressure at each measuring point decreased with the displacement time. The high permeability of the fractures led to low energy loss when fluid flowed through the fracture. Therefore the pressure in the fracture area did not decrease much with distance. But after passing through the fractured area, the descent rate of pressure was faster.
It indicates that fractures can reduce the required injection pressure because of their high permeability. As the experiment continued, the high-viscosity oil area gradually decreased and the flow resistance became smaller simultaneously. Figure 5 shows that the CO2 broke through the core at 0.64 PV and 0.58 PV, respectively. Before CO2 was detected at the outlet, it can be seen from Figure 4 that the pressure distribution had been reduced to 1.2 MPa. When the fracture length was 20 cm, the required injection pressure was lower than when the fracture length was 10 cm. It indicates that the fractures could effectively reduce the pressure difference between the injection and the production point.
The outlet was used as the collection point to record the cumulative production of the cores at different times. The gas-oil ratio at different times was obtained according to the instantaneous production. The component composition under standard conditions was obtained by chromatography. Four time points were selected to analyze the component, including the time before CO2 broke through the core, the time when CO2 broke through the core, the time after CO2 broke through the core, and the later stage of CO2 flooding. The molar composition of each component in the gas phase and the oil phase was obtained according to the chromatographic analysis, as shown in the following Figures 6, 7.
1) Length of fracture 10 cm
2) Lengths of fracture 20 cm
The molar composition of gas and oil are shown in Figures 6, 7. It is obvious that CH4 accounts for the largest proportion in the gas phase before CO2 was detected. Part of the CO2 was separated from the oil, less than 10%. After the CO2 was detected, the proportion of CH4 continued to decrease, and the proportion of CO2 continued to increase, until the gas component at the outlet was mainly CO2.
FIGURE 6. Molar composition at different times. (A) Molar composition of the gas phase at different times and (B) molar composition of the oil phase at different times.
FIGURE 7. Molar composition at different times. (A) Molar composition of the gas phase at different times and (B) molar composition of the oil phase at different times.
It can be seen from the oil phase composition that at the outlet, the proportion of light hydrocarbon components C5-C7 decreased after gas was detected. Meanwhile, the proportion of intermediate components C8-C12 and heavy components C13-C20 increased. This shows that CO2 could extract light components from oil. After the light components were extracted, the viscosity of the oil in the swept area was increased, and it was difficult to bring out the heavy components. Therefore, the proportion of heavy components at the outlet continued to decrease.
The proportion of CO2 in the gas was different, as seen by comparing the gas components in Figures 6, 7. The produced gas contained more CO2 in the core with the 20-cm fracture. It demonstrates that the fracture could exacerbate the gas channeling of CO2. On the other hand, the fracture had little effect on the component of the produced oil. The main difference was in the core with the 20-cm fracture; the final proportion of intermediate components C8-C12 was increased (the molar fraction of C8-C12 in the 10-cm fracture was increased to 0.51, and the mole fraction of C8-C12 in 20 cm fracture was increased to 0.62). It indicates that the fracture could lead to the reduction of the extraction and displacement of CO2.
The results in Figure 8 show that the final oil recovery was closely connected to the fracture length. A longer fracture had a greater influence on the gas channeling during the CO2 flooding process. Therefore, the oil recovery decreased as the fracture length increased.
The fracture with an aperture of 0.1 mm was made and compared with the above fracture with an aperture of 0.05 mm. The lengths of both fractures were 20 cm. The measuring points were set every 10 cm from the injection point. The outlet pressure remained unchanged, and the CO2 was injected at a constant rate of 0.2 ml/min. The pressure distribution is shown in the following Figure 9.
Compared with the 0.05 mm fracture aperture in the previous section, the required pressure was smaller. Similar to the conclusion of fracture length, the larger the fracture aperture, the smoother the pressure change. The fracture aperture led to greater effective permeability to reduce the injection-production pressure difference.
The proportion of CO2 in gas was different in the cores with different apertures as shown in Figure 10. The produced gas contained more CO2 in the core with the 0.1 mm fracture. More than 60% of CO2 was detected at the outlet when the fracture aperture was 0.1 mm. The fracture had little effect on the component of the produced oil.
FIGURE 10. Molar composition at different times. (A) Molar composition of the gas phase at different times and (B) molar composition of the oil phase at different times.
The results in Figure 11 show that although the larger fracture aperture may have reduced the pressure difference between the injection and the production point, the gas was able to flow along the high-permeability fracture; this was not conducive to a balanced displacement.
The pressure before CO2 was detected at the injection and production point is shown in Figure 12.
The results show that before CO2 was detected, a larger pressure difference was required in the control experiment. The pressure difference between the injection and production point was about 1.4 MPa. The pressure difference would drop if there was a fracture, and the longer the fracture, the smaller the injection-production pressure difference. The fracture aperture had a similar influence on the pressure. Comparing the control experiment and experiment with the fracture of 0.1 mm and aperture 20 cm length, the injection-production pressure difference was reduced by 40%.
The outlet molar fraction was taken at the moment of gas being detected under the five conditions for comparison, and the results are shown in Figure 13.
The results show that at the moment of gas being detected, the mole fraction of CO2 was the lowest in the control experiment, which was only 12.7%. With an increase in fracture length and aperture, the proportion of CO2 increased to 62.3% when the CO2 broke through the core. Long and wide fractures shortened the CO2 breakthrough time at the outlet, and the injected CO2 had no chance to contact the oil and improve the condition. Therefore the rapid increase of CO2 affected the displacement efficiency.
The light components C5-C7, intermediate components C8-C12, and heavy components C13-C20 were taken under five conditions for comparison, and the results are shown in Figure 14.
The results show that the increase of fracture aperture and length had little influence on the oil phase composition at the moment of CO2 breaking the core.
Figure 15 shows that the control experiment had the highest oil recovery. The increase in fracture length and aperture aggravated the gas channeling which led to a decrease in oil recovery. Besides this, compared with the fracture width, the fracture length had a greater impact on the CO2 flooding.
A CO2 flooding experiment in a long core was designed. The artificial cores and live oil were prepared according to the reservoir parameters in Shengli Oilfield. The inlet was injected with CO2 at a constant speed of 0.2 ml/min. The pressure distribution along the core and components of the gas phase and oil phase at the outlet was tested. The results demonstrate the following:
1) The CO2 flooding experiments on the matrix cores show that the pressure of each measuring point decreased rapidly with time in the early stage. After CO2 broke through the core, the injection-production pressure difference decreased with the decrease of flow resistance. It indicates that constant speed displacement could be achieved without high injection pressure after the gas broke through. The proportion of CH4 in the gas phase at the outlet exceeded 70% when CO2 broke through the core. Then the proportion of methane continued to decrease, and the proportion of CO2 continued to increase until the gas component at the outlet was mainly CO2. The proportion of light and intermediate components increased after CO2 broke through the core.
2) It shows that the long and wide fracture could effectively reduce the injection-production pressure difference. With the increase in fracture length and aperture, the recovery degree decreased from 72.41% to 48.15%. In general, the fracture length and aperture had obvious effects on the pressure distribution and the displacement efficiency.
3) Fracture length and aperture had a significant effect on the gas phase composition at the outlet. Wide and long fractures shortened the CO2 breakthrough time, and the rapid increase of CO2 at the outlet affected the displacement efficiency. Generally speaking, the increase of fracture aperture and length had little effect on the oil phase composition.
The data analyzed in this study is subject to the following licenses/restrictions: The data are used for scientific analysis. Requests to access these datasets should be directed to ZW1jZ3JvdXBAMTYzLmNvbQ==.
The author confirms being the sole contributor of this work and has approved it for publication.
ZQ-F was employed by Shengli Oilfield Company, SINOPEC.
All claims expressed in this article are solely those of the authors and do not necessarily represent those of their affiliated organizations, or those of the publisher, the editors, and the reviewers. Any product that may be evaluated in this article, or claim that may be made by its manufacturer, is not guaranteed or endorsed by the publisher.
Cao, C., Liu, H., and Hou, Z. (2020). A Review of CO2 Storage in View of Safety and Cost-Effectiveness[J]. Energies 13 (3), 600. doi:10.3390/en13030600
Cheng, J., Lei, Y., and Zhu, W. (2008). Pilot test on CO2 flooding in extra-low permeability Fuyu oil layer in DaQing placanticline. Nat. Gas. Geosci. 19 (3), 402–409.
Gao, M., Ni, J., Wang, X., Ma, B., and Wang, H. (2020). Experimental study on effects of CO2 flooding in ultra-low permeability reservoir under different parameters. J. Xi’an Shiyou Univ. Nat. Sci. Ed. 35 (3), 60–65. doi:10.3969/j.issn.1673-064X.2020.03.008
Guo, P., Li, S., and Du, Z. (2002). Evaluation of enhanced oil recovery by gas injection in low permeability reservoirs. J. Southwest Petroleum Inst. 24 (5), 46–50. doi:10.3863/j.issn.1000-2634.2002.05.015
Hao, Y., Bo, Q., and Chen, M. (2005). Laboratory investigation of CO2 flooding. Petroleum Explor. Dev. 32 (2), 110–112. doi:10.3321/j.issn:1000-0747.2005.02.027
He, Y., Gao, H., and Zhou, X. (2011). Study on method for improving displacement ef-fect of CO2 in extra-low permeability reservoir. Fault-block oil gas field 18 (4), 512–515.
Huang, Q., Zhang, J., and Wang, K. (2008). Laboratory experimental study on CO2 huff and puff flooding in fractured core system. Foreign oilfield Eng. 24 (4), 9–12. doi:10.3969/j.issn.2095-1493.2008.04.003
Jiang, H., Shen, P., and Lu, Y. (2010). Research on the status of CO2 enhanced oil and gas resource recovery in the world. Special Oil Gas Reservoirs 17 (2), 5–10. doi:10.3969/j.issn.1006-6535.2010.02.002
Ma, Q., Hou, S., Lv, B., and Song, S. (2020). Expansion experiment study of CO2 injection in XG oilfield. J. Green Sci. Technol. 16, 222–224.
Miller, J. S., and Jones, R. A. (1981). “A laboratory study of determine physical characteristics of heavy oil after CO2 saturation,” in SPE/DOE Enhanced Oil Recovery Symposium (OnePetro). doi:10.2118/9789-MS
Sankur, V., and Emanuel, A. S. (1983). “A laboratory study of heavy oil recovery with CO2 injection,” in SPE California Regional Meeting (OnePetro). doi:10.2118/11692-MS
Shi, L., Wang, W., Wang, C., and Chen, L. (2021). Study on injection mode of CO2 flooding based on physical model of fracture radial flow. Special oil gas reservoirs 28 (3), 112–117. doi:10.3969/j.issn.1006-6535.2021.03.017
Wang, P. (2017). Experimental study and application of carbon dioxide constant volume miscible-flooding in fractured-tight reservoir. J. Chengde petroleum Coll. 174 (1), 10–14. doi:10.3969/j.issn.1008-9446.2017.01.003
Wang, W., Chen, L., Tang, R., Wang, H., and Yang, H. (2016). Experimental study of cycle CO2 injection for low permeability reservoir. Fault-block oil gas field 23 (2), 206–209. doi:10.6056/dkyqt201602016
Xie, S. (1991). Laboratory study of CO2 flooding in Daqing oilfield. Petroleum Geol. Oilfield Dev. Daqing 10 (4), 51–58.
Keywords: CO2 flooding, low permeability reservoir, fractures, CO2 flooding experiment, greenhouse gas
Citation: Qing-Fu Z (2022) Laboratory investigation of the influence of fractures on CO2 flooding. Front. Earth Sci. 10:983442. doi: 10.3389/feart.2022.983442
Received: 01 July 2022; Accepted: 01 August 2022;
Published: 14 September 2022.
Edited by:
Jianlin Zhao, ETH Zürich, SwitzerlandCopyright © 2022 Qing-Fu. This is an open-access article distributed under the terms of the Creative Commons Attribution License (CC BY). The use, distribution or reproduction in other forums is permitted, provided the original author(s) and the copyright owner(s) are credited and that the original publication in this journal is cited, in accordance with accepted academic practice. No use, distribution or reproduction is permitted which does not comply with these terms.
*Correspondence: Zhang Qing-Fu, emhhbmdxaW5nZnU2MDVAMTYzLmNvbQ==
Disclaimer: All claims expressed in this article are solely those of the authors and do not necessarily represent those of their affiliated organizations, or those of the publisher, the editors and the reviewers. Any product that may be evaluated in this article or claim that may be made by its manufacturer is not guaranteed or endorsed by the publisher.
Research integrity at Frontiers
Learn more about the work of our research integrity team to safeguard the quality of each article we publish.