- 1School of Energy and Mining Engineering, China University of Mining and Technology (Beijing), Beijing, China
- 2CCTEG Wuhan Engineering Company, Wuhan, China
The advance area affected by mining (AAAM) of the Lijiahao coal mine is influenced by the superposition of the side and advance abutment pressure, and the roadway roof is considerably damaged. General support technology and equipment cannot economically and effectively maintain the stability of the roadway roof of AAAM. Through field detection, theoretical analysis, and numerical simulation, this study analyzes the structure of the surrounding rock, the evolution characteristics of the regional stress field, the distribution of the surrounding rock plastic zone, and the influencing factors of the plastic zone in the AAAM of the Lijiahao mine. The results show the following: 1) the direct roof and floor of the roadway comprise coal, siltstone, and sandy mudstone, which has low strength and can be easily broken. 2) The maximum and minimum principal stresses in the AAAM reach 2.3 and 1.5 times of in situ stress, respectively, and the ratio of the two stresses reaches 2–8, which causes the shape of the plastic zone of the surrounding rock to turn into a butterfly shape. 3) The principal stress direction of AAAM deflects at a large angle, which causes the deepest failure direction of the surrounding rock to rotate to the roof and floor of the roadway. Accordingly, a self-moving foldable support system is proposed to support the AAAM of the Lijiahao coal mine. The system will not support the roof repeatedly and is suitable for soft rock stratum. In addition, it can also adapt to the heave of roadway floor and avoid dumping. The mechanized operation of the system makes the roof support in AAAM more efficient and safer.
1 Introduction
In underground mines, the advance areas affected by mining (AAAM) are an important channel for pedestrians, ventilation, and equipment transportation (Du et al., 2014; Kang et al., 2016a). However, due to the superposition influence of the advance and side abutment pressures of the goaf, the roadway is often deformed and seriously damaged, and secondary support is required (Qian et al., 2010; Cai, 2020; Zhang et al., 2020). Numerous scholars have studied the stress evolution and failure characteristics of roadway surrounding rock in detail and have proposed the corresponding control technology and equipment. For example, Ma et al. (2015a, 2015b) and Zhao (2014) studied the partial stress field of deep mining roadways and revealed the asymmetric deformation failure mechanism of roadways. Moreover, they proposed the use of extendable anchor bolts and flexible anchor cables to support the roadways. Based on the stress evolution law of roadways under repeated mining and the asymmetric evolution characteristics of the plastic zone in the Shendong mining area, (Wu, 2018), (Wu, 2020), and Lv et al. (2019) revealed the malignant expansion mechanism of the plastic zone of the roadway surrounding rock and presented a hierarchical stability control system of the roadway surrounding rock. Yu et al. (2021) studied the fracture mode and abutment pressure distribution of a thick and hard rock roof with a weak interlayer. (Kang and Zhong (2016b) studied the influence of working face abutment pressure on the stability of roof rock that was strengthened using a bolt through physical and numerical simulation. Li et al. (2019, 2020) studied the non-uniform failure mechanism of roadways under the influence of secondary mining and presented a roof stability control technology based on plastic zone evolution. Jia et al. (2019) studied the failure mechanism of a soft rock roadway and multi-layer combined rock roadway and determined that the plastic zone has “penetration characteristics,” i.e., the plastic zone can pass through a hard rock stratum and redistribute in the soft rock. Thus, they presented the corresponding control technology. Liu et al. (2021) studied the stress evolution and surrounding rock failure of roadways and coal pillars under the influence of repeated mining in a double-roadway layout system through UDEC (Universal Distinct Element Code) numerical simulation software. Zhu et al. (2022) analyzed the stress distribution law caused by mining under different roof strengths through FLAC 3D (Fast Lagrangian Analysis of Continua) and obtained the influence area range of the working face pressure. Yao et al. (2020) introduced the technical idea of using an active support (reinforced anchor bolt and anchor cable) to replace a passive support (hydraulic powered support, HPS) in AAAM. In terms of the support research of HPS, Xu et al. (2020) analyzed the support resistance and support mode of HPS and proposed that HPS in AAAM should be coordinated with the roadway roof and anchorage system. Zhang (2013) studied a new type of HPS in AAAM, which can not only realize the overall support of the roof up to 12 m but also support the two sides of a roadway. Kang et al. (2019) analyzed the stress distribution characteristics of a roadway in front of the working face, presented the support concepts of “low initial support, high work resistance” and “unequal support,” and realized the automatic control of HPS in AAAM.
The aforementioned analysis shows that few studies currently exist on the stress distribution and plastic zone characteristics of roadway surrounding rock in AAAM and that the research on the advance support scheme is still limited to increasing the support resistance of bolts and cables or expanding the support range of HPS, which does not solve the problem of repeatedly supporting the roof. Furthermore, the support resistance makes it difficult to collapse roofs and increases the support cost.
In the AAAM of the Lijiahao coal mine, surrounding rocks of the roadway are relatively soft and prone to deformation and damage. In this case, the HPS system is easy to dump, and the repeated support of the HPS system to the roof often causes roof fall accidents. In addition, the traditional single hydraulic prop requires a lot of labor to erect and remove support units, which is difficult and unsafe. This study analyzes the advance area affected by the secondary mining of the Lijiahao coal mine, explores failure characteristics of the roadway, reveals its failure mechanism, and puts forward the corresponding support system to provide a reference for AAAM support under similar conditions.
2 Engineering background
2.1 Geological survey of the mining area
The Lijiahao coal mine of the Shenhua Baotou energy group is located in the Dongsheng coalfield, Inner Mongolia, China. The coal seams in the mining area are shallow and geological conditions are complex. Rocks of roof and floor of the coal seam are mainly layered clastic rocks, sandy mudstone, and siltstone. Rock strength is low and its stability is poor. The ratio of the horizontal stress to vertical stress in the regional stress field is about 1.2. Recently, with the continuous increase of the mining intensity, problems of AAAM support are becoming increasingly serious, and it needs to be urgently solved.
2.2 Project profile
Currently, the Lijiahao mine is mining 31# coal seam 31,115 working face, with an average coal thickness of 6 m. The thickness of the coal seam in the entire working face is relatively uniform. The thickness of the overlying loose layer of the coal seam in the working face ranges from 10 to 30 m and that of the overlying bedrock ranges from 150 to 220 m. The strike length of the 31,115 working face under mining is 2,600 m and the dip length is 300 m. It is close to the 31,114 goaf in the north and the 31,116 working face are planned to be arranged in the south. The 31,115 working face adopt a three roadways layout mode, as shown in Figure 1. The ventilation roadway of the 31,115 working face was once an auxiliary roadway of the 31,114 working face, the roadway section is 5.2 m wide × 3.56 m high; the section of the 31,115 haulage roadway is 5.4 m wide × 3.66 m high, and that of the 31,115 auxiliary roadway is 5.2 m wide × 3.56 m high. The coal pillar between the haulage and auxiliary roadways is 20 m in width. According to China’s coal mine safety production regulations, the area within 20 m ahead of the working face is the AAAM, and the roof support equipment needs to be arranged (red area in Figure 1). Currently, the mine adopts HPS for roof support.
2.3 Coal and rock mass structure
Through borehole detection and rock sample analysis, the rock structure of the Lijiahao 31,115 working face was obtained, as shown in Figure 2. The direct roof of the coal seam is mainly siltstone and fine-grained sandstone, wherein the thickness of the siltstone is 5–11 m with an average thickness of 8 m. The thickness of fine-grained sandstone is 6–11 m, with an average thickness of 9 m. The main roof is sandy mudstone, with a thickness of 6–14 m and an average thickness of 9 m. The direct floor is sandy mudstone and siltstone. The thickness of siltstone is 1–3 m, with an average thickness of 2 m. The thickness of sandy mudstone is 12–27 m, with an average thickness of 20 m. According to the mechanical measurement results, the physical and mechanical properties of each rock are shown in Table 1.
3 Methodology
3.1 Analysis of the stress field in AAAM
After the previous working face is mined, the stress in the goaf is relieved, yielding a low-stress area. Furthermore, the abutment pressure on the side of the goaf forms a stress-increasing area. Based on the existing research, the peak stress in the stress-increasing area can reach 3–5 times the in situ rock stress (Guo et al., 2021a; 2021b). As it is far away from the goaf, the stress field is less disturbed by mining, i.e., it is a stress stable area. During the mining process of the working face, the surrounding rock stress will be redistributed. Under the superposition of the lateral abutment pressure of the goaf and the advance abutment stress in front of the working face (Figure 3), AAAM will form a non-uniform stress field called the deviatoric stress field.
3.2 Failure characteristics of roadway surrounding rock under the non-uniform stress field
3.2.1 Asymmetric distribution of plastic zone of surrounding rock
Kastner (1962) conducted an elastic–plastic analysis on the stress and deformation of the roadway surrounding rock under the condition of two-way uniform pressure and obtained the boundary equation of the surrounding rock plastic zone. Later, Guo et al. (2019, 2020) deduced the boundary equation of the surrounding rock plastic zone of a homogeneous circular roadway under the condition of a non-uniform stress field (Eq. (1)) (Zhao et al., 2018). Moreover, based on the hole plane strain model in the theory of elasticity (Figure 4) and taking the Mohr–Coulomb criterion, they proposed that the plastic zone of the roadway surrounding rock generally has three forms, i.e., circle, ellipse, and butterfly (Guo et al., 2019,2020) (Figure 5A). This reveals the failure mechanism of the roadway surrounding rock, such as asymmetric deformation (Zhao, 2014), roof fall (Zhao et al., 2016), and floor heave (Li et al., 2018).
where
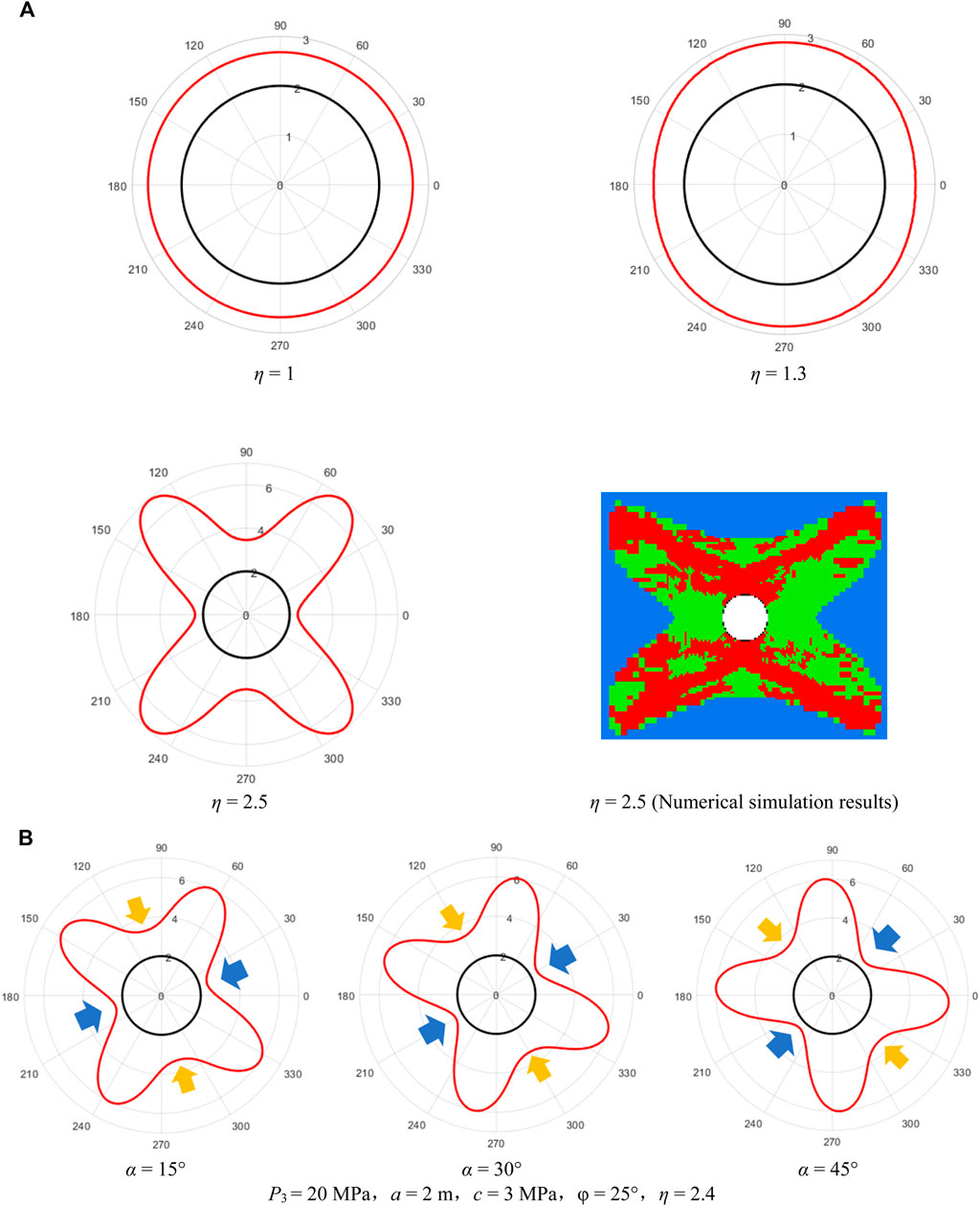
FIGURE 5. Plastic zone shape of the surrounding rock. (A) Shape of the plastic zone under different lateral pressure coefficients. (B) Rotation of the butterfly plastic zone.
Here, P1 and P3 are the maximum and minimum principal stresses, respectively. Additionally, a is the roadway radius, η is the ratio of the maximum principal stress to the minimum principal stress (also known as the lateral pressure coefficient), φ is the friction angle, and R and θ are the polar coordinates of any point in the coordinate system.
3.2.2 Directional rotation of the butterfly plastic zone
According to Eq. (1), when the direction of the maximum and minimum principal stresses of the regional stress field deflects, the plastic zone shape of the roadway surrounding rock rotates at a corresponding angle, as shown in Figure 5B (defining the horizontal direction as 0° and the counterclockwise and clockwise rotations as positive and negative, respectively).
4 Numerical simulation
4.1 Model construction
FLAC 3D can accurately simulate the distribution characteristics of stress and the plastic zone after continuous medium excavation using the dynamic motion equation. Therefore, this study uses FLAC 3D software to simulate and analyze the Lijiahao coal mine. A model X × Y × Z = 840 m × 900 m × 54 m is established, and a 4.15 MPa equivalent load is applied above the model to compensate for the vertical stress of overburden. The grid is 5 m/grid, and the AAAM is refined to 0.5 m/grid. The numerical simulation model is shown in Figure 6 rock stratum parameters are shown in Table 1. The lateral pressure coefficient is 1.2, and the model adopts the Mohr–Coulomb criterion.
4.2 Model excavation and filling
To more truly simulate the on-site engineering environment, the 31,114 working face and its two adjacent roadways are excavated and the goaf is filled with the double yield model. After balancing, the model is saved and named the basic calculation model. Then, the 31,115 working face is excavated in the basic calculation model, and the goaf is filled. After calculation, the axial stress at the ventilation roadway of 31,115 working face is extracted for analysis. Finally, according to the actual engineering excavation process, the 31,114 working face, its two adjacent working roadways, and the 31,114 auxiliary roadway (31,115 ventilation roadway) are re-excavated, and the 31,114 working face and its two adjacent roadways are filled. After the calculation, the 31,115 working face and the roadway on its right side shall be excavated and filled. After the model is balanced, the distribution of the surrounding rock plastic zone at different positions of the mining roadway is obtained by slicing the mining roadway in the model. The parameters of the double yield model in goaf are shown in Table 2.
4.3 Results
4.3.1 Stress distribution characteristics of surrounding rock in mining roadway
The maximum and minimum principal stresses at the roadway centerline under the conditions of different mining distances of the working face are shown in Figures 7A,B. The figure shows that the maximum and minimum principal stresses of the original rock stress field (before being affected by mining) are about 5.9 and 4.9 MPa, respectively. Due to the influence of mining-induced stress (superposition of abutment pressure at the side of goaf and advance abutment pressure at this working face), the maximum and minimum principal stresses reach extreme values near the working face and the open cut hole, respectively. The peak value of the maximum principal stress is about 12–13 MPa, and the peak value of the minimum principal stress is about 6–7.5 MPa. Due to the difference in the spatial distribution of the main roof structure of the coal seam, the peak stress of the roadway is different under different mining distances. With increasing distance from the open cut hole and the working face, the principal stresses exhibit a decreasing trend. The figure also shows that the stress distribution characteristics are independent of the mining distance of the working face.
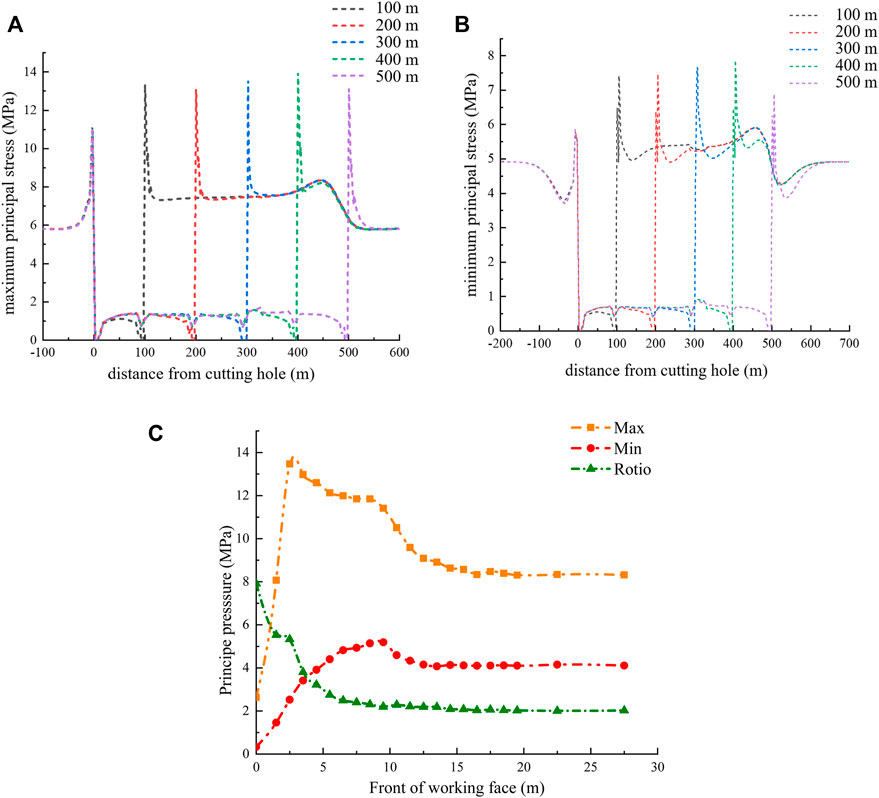
FIGURE 7. Distribution characteristics of the principal stress of surrounding rocks under different mining distances. (A) Maximum principal stress. (B) Minimum principal stress. (C) Maximum principal stress and minimum principal stress in AAAM.
When the coal seam is mined 300 m, the maximum and minimum principal stresses in AAAM are shown in Figure 7C. With the increasing distance from the working face, the maximum and minimum principal stress increase rapidly at first, and then decrease gradually. This is because the stress near the working face is concentrated due to the influence of mining, and surrounding rocks adjacent to the working face have been damaged, where the stress has been released. The maximum and minimum principal stress peaks of surrounding rocks are about 13.5 and 5.5 MPa. It can be seen from Figure 7C that the principal stress ratio gradually decreases from 8.0 to 2.0 as it is away from the working face. At 5, 10, and 20 m in front of the working face, the principal stress ratios are 3, 2.3, and 2.1, respectively.
4.3.2 Failure characteristics of the surrounding rock in the advance area of the working face
The aforementioned analysis shows that the stress variation law of the AAAM is basically the same at different mining distances of the working face. Therefore, taking the 300 m of the working face as an example, the distribution characteristics of the plastic zone of surrounding rocks in the advance area are analyzed.
Figure 8 shows the plastic zone of the roadway surrounding rock at different positions in the advance area of the working face when the mining distance of the working face is 300 m. Near 1 m in front of the working face (Figure 8A), the surrounding rock of the roadway is seriously damaged, the plastic zone exhibits asymmetric deformation characteristics, the right side of the roadway and the roof are penetrated, and the maximum failure depth on the left side of the roadway (coal pillar side) is about 4 m. About 5 m in front of the working face (Figure 8B), the overall range of the plastic zone of the roadway surrounding rock is reduced, the right side of the roadway is still damaged, and the maximum damage depth of the roadway roof is 4.5 m. Near 10 m in front of the working face (Figure 8C), the range of the plastic zone of the roadway surrounding rock decreases, but it still exhibits asymmetric characteristics. The roof of the roadway has the largest failure range, and the failure depth is about 4 m. The failure depth on the left and right sides of the roadway is 4 and 3 m, respectively. At 15 m and 20 m in front of the working face (Figures 8D,E), the failure range and failure characteristics of the roadway surrounding rock are almost identical. The maximum failure position is still the roof, and the failure depth is 4 m. The maximum failure depths on the left and right sides of the roadway are 4 and 2.5 m, respectively. Near 30 m in front of the working face (Figure 8F), the plastic zone of the surrounding rock decreases, but the distribution characteristics of the plastic zone do not change. The plastic zone of the surrounding rock still exhibits an asymmetric distribution. The largest failure part of the roadway is still the roadway roof, and the failure of the left side of the surrounding rock is more serious than that of the right side.
The aforementioned analysis shows that the plastic zone of the roadway surrounding rock near the working face is large and the damage is serious. As the distance from the working face increases, the plastic zone of the roadway surrounding rock gradually decreases, i.e., the failure zone of the roadway gradually decreases. The plastic zone of the roadway surrounding rock exhibits asymmetric distribution characteristics. Although a certain range of the plastic zone is present on the roof, floor, and two sides of the roadway, the plastic zone of the roadway roof is the largest. Furthermore, the plastic zone of the surrounding rock on the left side of the roadway is larger than that on the right side of the roadway.
4.4 Discussion
The shape and distribution characteristics of the roadway plastic zone stem from the interaction between the regional stress field vector and surrounding rock. Therefore, the influence of the size and direction of the regional stress field and the structure and strength of the surrounding rock on the plastic zone needs to be analyzed.
4.4.1 Influence of the stress rotation angle
Taking the working face distance of 300 m as an example, the direction of the maximum principal stress within 20 m in front of the working face (Figure 9A) is determined by using the numerical model. The horizontal direction is defined as 0°, and the counterclockwise and clockwise rotations are defined as positive and negative, respectively. The direction of the stress field in the AAAM considerably changes from the original stress of about 0° to about 85°, then rapidly changes to about −40° with increasing distance from the working face, and finally gradually decreases to about −20°. At about 0–8 m ahead of the working face, due to the influence of the mining of the working face, the overlying strata fracture and collapse, resulting in the change of the stress direction. Therefore, the direction of the maximum principal stress changes from approximately horizontal (about 0°) to approximately vertical (about 85°). Clearly, after 8 m, the surrounding rock of the roadway is less affected by the mining of this working face but is greatly affected by the mining of the previous working face. After the mining of the previous working face, the overburden breaks and collapses, and the abutment stress of the goaf is transmitted to the coal pillar side. Therefore, the stress direction changes from the positive to the negative direction and the angle between the maximum principal stress and the horizontal direction ranges between about −45° and −15°.
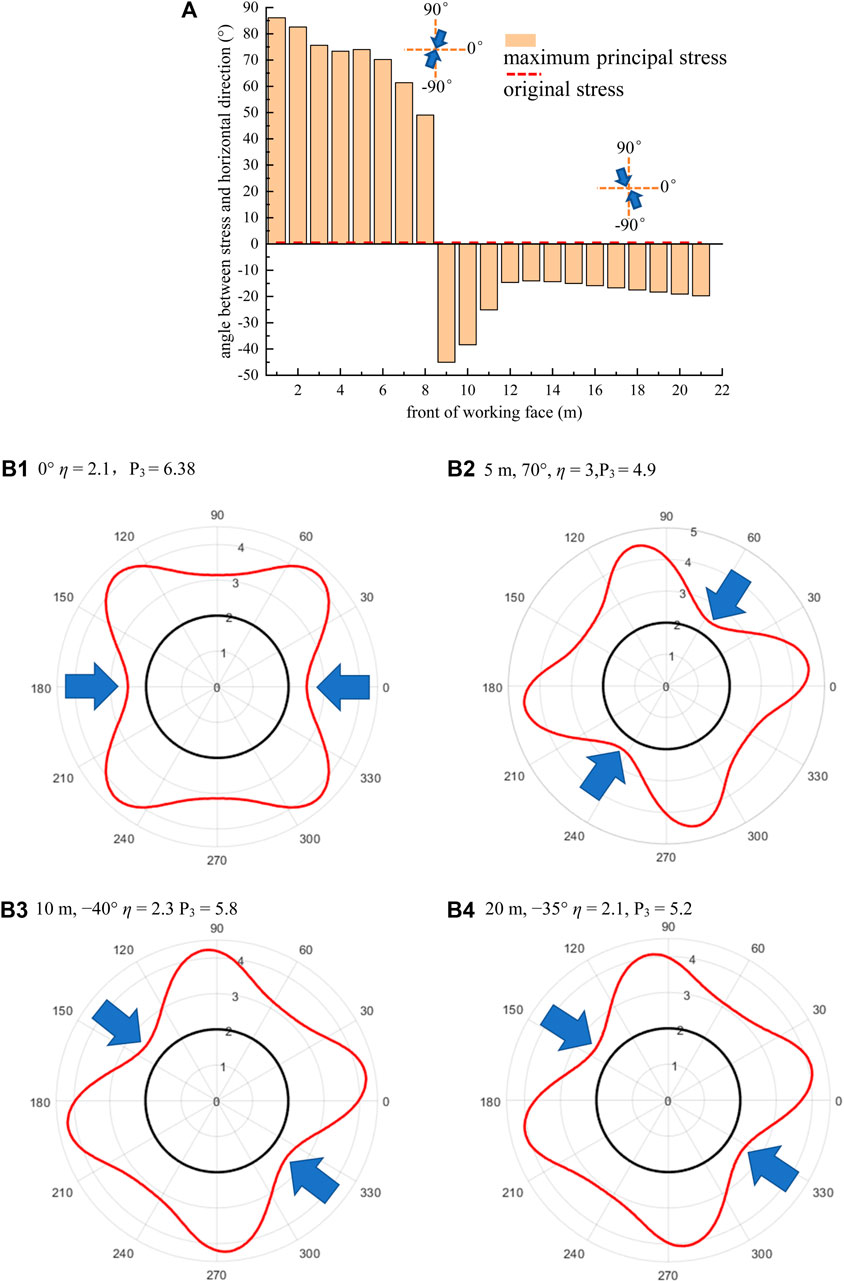
FIGURE 9. (A) Variation of the principal stress direction. (B) Influence of principal stress direction on the plastic zone of the surrounding rock.
When the stress field is not affected by mining, the direction of the maximum principal stress is approximately horizontal while that of the minimum principal stress is approximately vertical. In this case, the shape of the plastic zone of the surrounding rock is shown in Figure 9B1 and the plastic zone in the four corner directions of the roadway is the largest. Taking the mechanical parameters of coal as an example, the boundary of the surrounding rock plastic zone at 5, 10, and 20 m in front of the working face is calculated, as shown in Figures 9B2–B4. The figures show that AAAM is affected by the successive mining of the two working faces and that the direction of the regional stress field dramatically changes, causing the deflection of the plastic zone of the surrounding rock at the corresponding angle. Within 20 m ahead of the working face, the maximum damage direction of the plastic zone changes from the four corners of the roadway to the roof, floor, and both sides of the roadway.
4.4.2 Influence of rock structure and strength
According to the borehole detection results (Figure 2), the direct roof of the coal seam is siltstone, and the direct floor is siltstone and sandy mudstone. Taking the stress environment of 10 m in front of the working face (η = 2.3, P3 = 5.8, the maximum principal stress direction is −40°) as an example, the plastic zone boundary of roadway surrounding rock under different rock stratum conditions is calculated by Eq. (1) (Figure 10). The figure shows that under the same stress conditions, when the surrounding rock of the roadway is coal, the plastic zone is the largest, followed by sandy mudstone, and siltstone affords the smallest plastic zone. When the roadway surrounding rock comprises three lithological rocks, the plastic zone of the roadway surrounding rock is the superposition and combination of three plastic zone forms. The shape of the plastic zone in Figure 10D is basically consistent with that in Figure 8C. The failure range of the roadway roof is the largest, followed by that of the side of the roadway, and the roadway floor affords the smallest failure range. The aforementioned analysis shows that the range of surrounding rock plastic zone will be different due to different rock structures and the strength of each rock stratum. The direct roof and both sides of the roadway are coal, and its strength is small, so the plastic zone is large. The direct floor of the roadway is sandstone, which is stronger than coal, and the range of the plastic zone is relatively small.
4.4.3 Influence of the principal stress ratio
With increasing distance from the working face, the ratio of the maximum to the minimum principal stresses in AAAM gradually decreases from 8 to about 2.1. Similarly, taking the distance of 10 m ahead of the working face as an example (η = 2.5, P3 = 5.8, and the maximum principal stress direction is −40°), the boundary of the surrounding rock plastic zone under different principal stress ratios is analyzed (Figure 11). Under the same conditions, when the stress ratio changes from 2.5 to 3, the range of the butterfly plastic zone sharply increases and the plastic zone of the roadway roof is the largest. When the stress ratio changes from 2.5 to 2.1, the plastic zone of the surrounding rock still exhibits a butterfly shape, but the failure range decreases.
The aforementioned analysis shows that under the same conditions, the ratio of the maximum to minimum principal stresses is positively correlated with the range of the plastic zone of the roadway surrounding rock. When the ratio of principal stress is larger, the range of surrounding rock plastic zone is larger, and the failure range of roadway roof is larger. The magnitude of the stress ratio does not affect the maximum failure direction (position) of surrounding rocks. Under the three conditions, the damage range of the roadway roof is the largest.
In summary, the AAAM of the Lijiahao coal mine is affected by the continuous mining of two working faces, and the rotation angle of the direction of the regional stress field is large, leading to the occurrence of butterfly plastic zone in the roof and floor of the roadway. In addition, the roadway roof strata are relatively soft. What is more, the superposition of goaf advance pressure and side abutment pressure results in the ratio of the maximum to the minimum principal stress exceeding 2, and the plastic zone evolves into a butterfly shape. The aforementioned reasons lead to a large range of plastic zone in the roadway roof.
5 Support strategy and system
5.1 Factors considered in advance support
The roof of AAAM needs to be stable during mining, and it also needs to collapse in time after mining. Therefore, secondary supplementary support of bolt and anchor cable not only increases the cost but also not conducive to roof caving. The roof and floor in the AAAM of the Lijiahao mine are coal and sandstone, with low strength. The plastic zone of the roadway roof is large, and the roadway roof has step subsidence (Figure 12A). Thus, when an HPS system is been used, the broken coal can easily fall (Figure 12B) and cause accidents. The deformation of the roadway floor is large, and HPS may topple when a floor bulge occurs (Figure 12C). Therefore, supplementary supports and HPS in AAAM are not suitable for the Lijiahao coal mine.
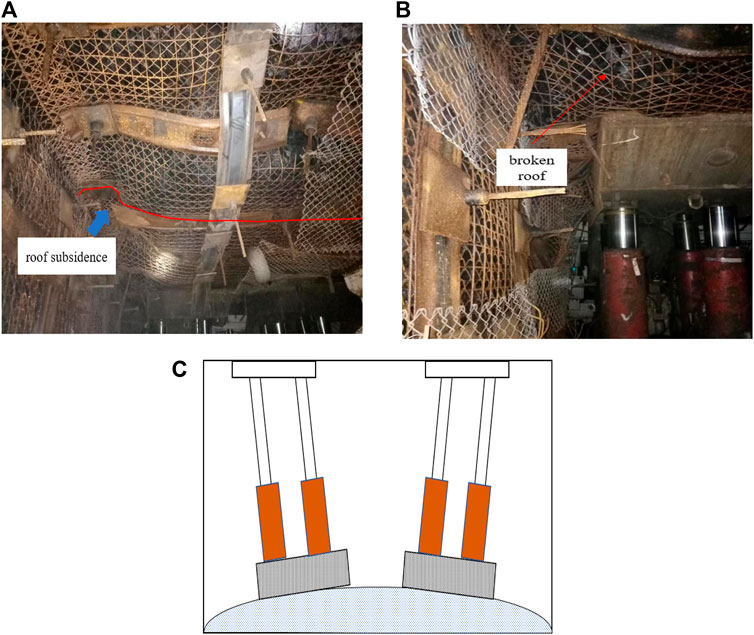
FIGURE 12. Problems faced by the Lijiahao advance support. (A) Roof deformation. (B) Broken roof. (C) Hydraulic support dumping.
5.2 System of advance support
Considering the geological conditions that the roof of the Lijiahao mine is seriously broken and the floor is deformed to a certain extent, a self-moving foldable support system (Figure 13) in AAAM is recommended. The system includes a foldable support unit, an intelligent support and withdrawal platform, a self-driving machine head, and a traction system.
The system includes the following features:
(1) The system does not support the roadway roofs repeatedly and can fully adapt to roofs’ deformation. The foldable support unit is small, so roadway roofs will not be repeatedly supported when the support unit is erected and removed. Furthermore, the direction of the support unit can be adjusted (Figure 14A), which improves its adaptability to the deformation of the roof and prevents damage to the roof bolt, anchor cable, and reinforcement mesh.
(2) It is suitable for roadway floor heave and will not dump. The support system comprises multiple support units, and each support unit is supported by two hydraulic rods. In case of a non-uniform deformation of the roadway floor, the support height can be adjusted by adjusting the lifting of the hydraulic rod to adapt to the deformation of the roadway floor. Additionally, the support unit is small, which can prevent dumping (Figure 14B).
(3) The system operates mechanically, which is safe and efficient. As mining progresses, the support unit is removed from the rear of the system, transported to the front of the system, and then re-erected by an intelligent support and withdrawal platform (Figure 14C). The system is pulled by a driving machine, which can realize the safety and efficiency of the support erection, removal, and transportation.
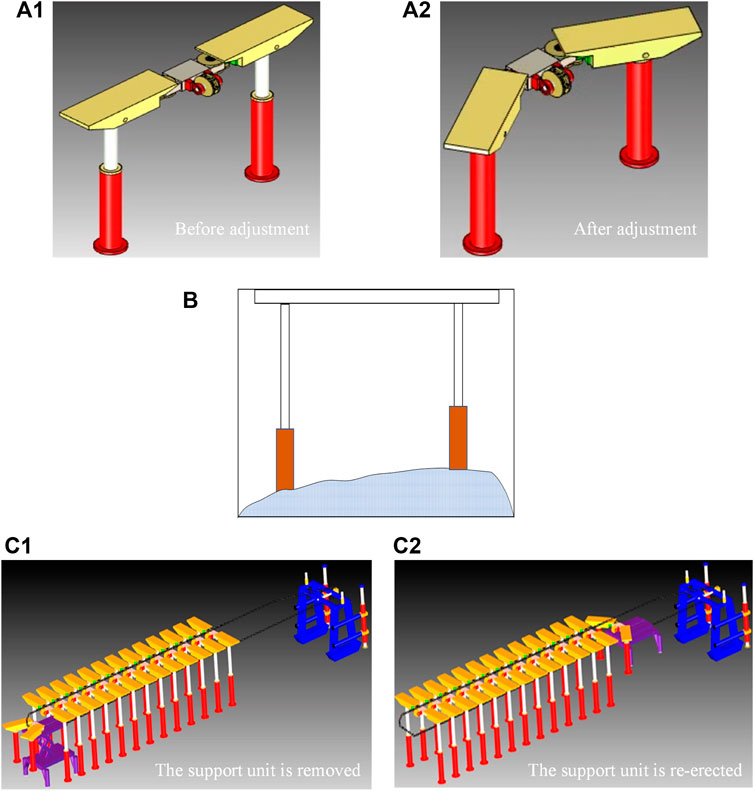
FIGURE 14. Features of the support system. (A) Foldable support unit. (B) Support unit adapted to floor heave. (C) Removal and erection of the support units.
6 Conclusion
(1) The roof and floor of the mining roadway in the Lijiahao coal mine are sandstone and sandy mudstone, which are relatively soft and prone to roof fall and asymmetric deformation. In AAAM, the HPS and the secondary supplementary support of bolt and anchor cable cannot maintain the stability of the roadway roof economically and effectively. These technologies are not suitable for this condition.
(2) Affected by the successive mining of the two working faces, maximum and minimum principal stresses reach 2.3 and 1.5 times the original stress, respectively, and the ratio of the two stresses reaches 2–8. The regional non-uniform stress field makes the shape of the plastic zone of the surrounding rock change from circular to oval and butterfly, and the plastic zone also deflects at a certain angle (the largest part of the plastic zone rotates to the roof and floor of the roadway). These are the reasons for the roof failure in AAAM of the Lijiahao coal mine.
(3) A self-moving foldable support system is proposed for AAAM support in the Lijiahao coal mine. As the working face moves forward, the support unit will not repeatedly support the roof during erection and removal. Furthermore, the support unit can adapt to the floor heave and prevent dumping. The field test shows that the system can better adapt to the geological conditions of roof crushing and floor deformation.
Data availability statement
The original contributions presented in the study are included in the article/supplementary material; further inquiries can be directed to the corresponding author.
Author contributions
All authors listed have made substantial, direct, and intellectual contributions to the work and approved it for publication.
Funding
This work was partially supported by the National Natural Science Foundation of China (Grant Nos. 52004289 and 51704294), and Fundamental Research Funds for the Central Universities (Grant No. 2022YJSNY10).
Conflict of interest
CL was employed by the Wuhan Engineering Company of CCTEG. The remaining authors declare that the research was conducted in the absence of any commercial or financial relationships that could be construed as a potential conflict of interest.
Publisher’s note
All claims expressed in this article are solely those of the authors and do not necessarily represent those of their affiliated organizations, or those of the publisher, the editors, and the reviewers. Any product that may be evaluated in this article, or claim that may be made by its manufacturer, is not guaranteed or endorsed by the publisher.
References
Cai, M. F. (2020). Key theories and technonogies for surrounding rock stability and ground control in deep mining. J. Min. Strat. Control. Eng. 2, 5–13. doi:10.13532/j.jmsce.cn10-1638/td.20200506.001
Du, J. P., and Meng, X. R. (2014). Mining science. Xuzhou, China: China University of mining and Technology Press.
Guo, X. F., Guo, L. F., Ma, N. J., Zhao, Z. Q., and Li, C. (2020). Applicability analysis of the roadway butterfly failure theory. J. China Univ. Min. Technol. 49, 646–653. 660. doi:10.13247/j.cnki.jcumt.001169
Guo, X. F., Li, C., and Huo, T. H. (2021b). A quantitative evaluation method on the stability of roadway surrounding rock in partial con-fining stress based on plastic zone shapes. Geomech. Eng. 25, 405–415. doi:10.12989/gae.2021.25.5.405
Guo, X. F., Li, C., and Huo, T. H. (2021a). Shapes and formation mechanism of the plastic zone surrounding circular roadway under partial confining stress in deep mining. Geomech. Eng. 25, 509–520. doi:10.12989/gae.2021.25.6.509
Guo, X. F., Zhao, Z. Q., Gao, X., Wu, X., and Ma, N. (2019). Analytical solutions for characteristic radii of circular roadway surrounding rock plastic zone and their application. Int. J. Min. Sci. Technol. 29, 263–272. doi:10.1016/j.ijmst.2018.10.002
Jia, H. S., Wang, L. Y., Fan, K., Peng, B., and Pan, K. (2019). Control technology of soft rock floor in mining roadway with coal pillar protection: A case study. Energies 12, 3009. doi:10.3390/en12153009
Kang, H. P., Xu, G., Wang, B. M., Wu, Y. Z., Jiang, P. F., Pan, J. F., et al. (2019). Forty years development and prospects of underground coal mining and strata control technologies in China. J. Min. Strat. Control. Eng. 1, 7–39. doi:10.13532/j.jmsce.cn10-1638/td.2019.02.002
Kang, H. P. (2016a). Sixty years development and prospect of rock bolting technology for underground coal mine roadways in China. J. China Univ. Min. Technol. 45, 1071–1081. doi:10.13247/j.cnki.jcumt.000583
Kang, H. P., Zhong, J., Yang, J., and Gao, F. (2016b). Investigation on the influence of abutment pressure on the stability of rock bolt reinforced roof strata through physical and numerical modeling. Rock Mech. Rock Eng. 50, 387–401. doi:10.1007/s00603-016-1114-x
Li, C., Guo, X. F., Lian, X. Y., and Ma, N. (2020). Failure analysis of a pre-excavation double equipment withdrawal channel and its control techniques. Energies 13, 6368. doi:10.3390/en13236368
Li, C., Zhang, W. L., Wang, N., and Hao, C. (2019). Roof stability control based on plastic zone evolution during mining. J. Min. Saf. Eng. 36, 753–761. doi:10.13545/j.cnki.jmse.2019.04.014
Li, Y. E., Ma, N. J., and Ma, J. (2018). Surrounding rock’s failure characteristic and rational location of floor gas drain-age roadway above deep confined water. J. China Coal Soc. 43, 2491–2500.
Liu, S. G., Bai, J. B., Wang, X. Y., Wang, G. H., Wu, B., Li, Y., et al. (2021). Study on the stability of coal pillars under the disturbance of repeated mining in a double-roadway layout system. Front. Earth Sci. 9, 1–9. doi:10.3389/feart.2021.754747
Lv, K., Feng, Z. G., Feng, J. C., Xuan, Z. T., Xiao, J., and Wu, X. Y. (2019). Surrounding rock failure mechanism of reserved roadway under superimposed mining and its control technology. J. Min. Saf. Eng. 36, 685–695. doi:10.13545/j.cnki.jmse.2019.04.006
Ma, N. J., Li, J., and Zhao, Z. Q. (2015a). Distribution of the deviatoric stress field and plastic zone in circular roadway surrounding rock. J. China Univ. Min. Technol. 44, 206–213. doi:10.13247/j.cnki.jcumt.000309
Ma, N. J., Zhao, X. D., Zhao, Z. Q., Li, Q., and Guo, X. F. (2015b). Stability analysis and control technology of mine roadway roof in deep mining. J. China Coal Soc. 40, 2287–2295. doi:10.13225/j.cnki.jccs.2015.6011
Qian, M. G., Shi, P. W., and Xu, J. L. (2010). Mining pressure and strata control. Xuzhou, China: China University of Mining and Technology Press.
Wu, X. Y. (2018). Evolutionary regularity of plastic zone and stability control in repetitive mining roadway in Shendong mining area. Beijing, Chinna: Doctoral dissertation, China University of Mining and Technology.
Wu, X. Y., Liu, H. T., Li, J. W., Guo, X. F., and Lv, K. (2020). Space-time evolutionary regularity of plastic zone and stability control in repetitive mining roadway. J. China Coal Soc. 45, 3389–3400. doi:10.13225/j.cnki.jccs.2019.1051
Xu, Y. J., Zhang, K., Li, D. Y., and Zhang, D. S. (2020). Theory and application of self-adaptive support for advanced powered support. J. China Coal Soc. 45, 3615–3624. doi:10.13225/j.cnki.jccs.2019.1207
Yao, Q. L., Wang, X. H., Xia, Z., Li, L. H., Zhu, L., and Li, X. H. (2020). Key technology and application of active fore poling for longwall coal mining in coal mine. J. Min. Saf. Eng. 37, 289–297.
Yu, M., Zuo, J., Sun, Y., Mi, C., and Li, Z. (2021). Investigation on fracture models and ground pressure distribution of thick hard rock strata including weak interlayer. Int. J. Min. Sci. Technol. 32, 137–153. doi:10.1016/j.ijmst.2021.10.009
Zhang, P. C. (2013). Doctoral dissertation. Beijing), Beijing, China: China University of Mining and Technology.Research on key technology and equipments for advanced support used in the ends of fully mechanized mine face
Zhang, T., and Wang, Y. L. (2020). Study on deformation evolution law and support technology of surrounding rock in multiple mining roadway. J. Min. Strat. Control. Eng. 2, 66–73. doi:10.13532/j.jmsce.cn10-1638/td.20200106.001
Zhao, Z. Q., Ma, N. J., Guo, X. F., and Zhao, X. D. (2016). Falling principle and support design of butterfly-failure roof in large deformation mining roadways. J. China Coal Soc. 14, 2932–2939. doi:10.13225/j.cnki.jccs.2016.1146
Zhao, Z. Q., Ma, N. J., Liu, H. T., and Guo, X. F. (2018). A butterfly failure theory of rock mass around roadway and its application prospect. J. China Univ. Min. Technol. 47, 969–978. doi:10.13247/j.cnki.jcumt.000922
Zhao, Z. Q. (2014). Doctoral dissertation. Beijing, Beijing, China: China University of Mining and Technology.Mechanism of surrounding rock deformation and failure and control method research in large deformation mining roadway
Keywords: support system, failure mechanism, advance area affected by mining, plastic zone, soft rock stratum
Citation: Li J, Lian X, Li C, Wu Z and Wang J (2022) Failure mechanism and support system of roofs in advance areas affected by mining under the condition of soft rock stratum. Front. Earth Sci. 10:936029. doi: 10.3389/feart.2022.936029
Received: 04 May 2022; Accepted: 30 June 2022;
Published: 04 August 2022.
Edited by:
Zhiqiang Yin, Anhui University of Science and Technology, ChinaReviewed by:
Yuan Benqing, CCTEG Chongqing Research Institute, ChinaChun Wang, Henan Polytechnic University, China
Chao Yuan, Hunan University of Science and Technology, China
Lei Fan, Hunan University of Science and Engineering, China
Copyright © 2022 Li, Lian, Li, Wu and Wang. This is an open-access article distributed under the terms of the Creative Commons Attribution License (CC BY). The use, distribution or reproduction in other forums is permitted, provided the original author(s) and the copyright owner(s) are credited and that the original publication in this journal is cited, in accordance with accepted academic practice. No use, distribution or reproduction is permitted which does not comply with these terms.
*Correspondence: Jun Li, dXN0YmxpanVuQDEyNi5jb20=